DOI:
10.1039/D1MA00354B
(Review Article)
Mater. Adv., 2021,
2, 4497-4531
Recent advances on the removal of dyes from wastewater using various adsorbents: a critical review†
Received
17th April 2021
, Accepted 2nd June 2021
First published on 7th June 2021
Abstract
The rapid increase in toxic dye wastewater generated from various industries remains a severe public health issue and prime environmental protection concern, posing a major challenge to existing conventional water treatment systems. Consequently, various physicochemical and biological treatment processes have been studied, which exhibit varying removal abilities depending on their experimental constraints. Among them, adsorption is considered to be the most efficient due to its high removal efficiency, easy operation, cost-effectiveness, and recyclability of the adsorbents. Considering this, the present review article focused on presenting a comprehensive summary of the various types of adsorbents such as commercial activated carbon, metal oxide-based, carbon-based, metal–organic framework, and polymer-based adsorbents used in dye remediation of contaminated water. The effects of several critical factors such as initial dye concentration, solution pH, temperature, and adsorbent dose on the dye adsorption performance are also described. In addition, the adsorption mechanisms responsible for dye removal are explained based on electrostatic attraction, ion exchange, surface complexation, and π–π interactions. Finally, critiques, future perspectives, and a summary of the present article are given. Various adsorbents such as carbon-based materials, metal oxides, bio-adsorbents, and polymer-based materials, have been shown to be efficient for the removal of dye pollutants from wastewater. Thus, it is anticipated that dye removal by adsorption can provide a feasible solution for the treatment of dye-laden water.
1. Introduction
The rapid growth of the global population, climate change, and industrial development has significantly affected water quality, resulting in an increasing freshwater crisis worldwide. Considering this, various consumers and polluters of freshwater significantly contribute to freshwater depletion.1,2 Among them, the increasingly used dyes including methylene blue (MB), rhodamine B (RhB), methyl orange (MO), Congo red (CR), Disperse Violet 26, methyl red, and crystal violet are the most important sources of industrial pollutants originating from different industries such as the textile, cosmetic, leather, food, pharmaceutical, paint and varnish, and pulp and paper industries (Table 1).3–16 According to a recent estimate, about 70 lakh tons of dyes are produced annually worldwide.17 The release of this industrial waste dye into water jeopardizes human health and the environment. Consequently, research in this area is ongoing, which is obvious from the drastic upsurge in the number of research articles published on ‘Dye Removal’ in 2016–2020, as displayed schematically in Fig. 1.
Table 1 Classification, examples, applications, solubility in water, and ecotoxicological effects of dyes
Type of dye |
Example of chemical structure of dye |
Examples of dyes |
Dye application |
Solubility in water |
Ecotoxicological effects |
Ref. |
Acid dye |
|
Acid yellow 36, Acid orange 7, Acid blue 83, Acid blue 7 |
Textile, leather, and pharmaceutical industries; nylon, wool, silk, and modified acrylics |
Water soluble |
Vomiting, nausea, diarrhea, carcinogenic and mutagenic effects |
3 and 72–75
|
Basic dye |
|
Methylene blue (MB), Basic red 1 or rhodamine 6G, Basic yellow 2 |
Paper, polyacrylonitrile modified nylons, and modified polyesters |
Water soluble |
Altering the chemical and physical properties of water bodies and causing detrimental effects to the flora and fauna |
3, 72, 76 and 77
|
Direct dye |
|
Congo red (CR), Direct red 28, Direct black 38 |
Coloring paper products |
Water soluble |
Toxic to aquatic animals and plants; carcinogenic; mutagenic, and dermatitis |
3, 72 and 78–80
|
Vat dye |
|
Vat blue 1, Vat acid blue 74 |
Insoluble pigment, indigo, and natural fibers, cellulosic fibers |
Water insoluble |
Severely affects the quality and clearness of water resources such as lakes and rivers; dermatitis, allergic conjunctivitis, rhinitis, and other allergic reactions |
3, 72, 73, 76, 81 and 82
|
Disperse dye |
|
Disperse red 9, Disperse violet 1, Disperse red 60 |
Polyester, nylon, cellulose acetate, and acrylic fibers |
|
Mutagenic; carcinogenic; causes soil and water pollution |
3, 72 and 83
|
Nitro dye |
|
Naphthol yellow (II) |
Dye wool |
|
Decreases light penetration and photosynthetic activity; carcinogenic and mutagenic |
3, 72 and 84
|
Mordant dye |
|
Mordant red 11, Mordant Black 17 |
Textile fibres such as wool, silk, and leather |
|
Shows allergic reactions |
3, 72, 85 and 86
|
Reactive dye |
|
C.I. reactive red 120, C.I. reactive red 147, C.I. reactive blue 19 |
Dyeing cellulosic, silk, and wool fibres |
|
High and unwanted levels of dissolved solids in the effluent |
3 and 72
|
Allergic reaction in eyes, skin, mucous membrane, and the upper respiratory tract |
Sulphur dye |
|
Sulfur brilliant green, Sulfur blue, Sulfur Black 1, Leuco Sulfur Black 1, Phthalic anhydride |
Dyeing cellulosic fibres and cotton |
Water insoluble |
Skin irritation; itchy or blocked noses; sneezing and sore eyes; carcinogenic |
3, 72 and 76
|
Azo dyes |
|
Direct Black 22, Disperse Yellow 7, Acid Orange 20, Methyl red, Methyl orange (MO), Trypan blue |
Textile industry for dyeing process and food coloring |
|
Causes carcinogenicity in humans and animals. If inhaled or swallowed, it affects the eye, skin, and digestive tract. Affects aquatic life if present in excess. |
3, 15, 72, 73 and 87–90
|
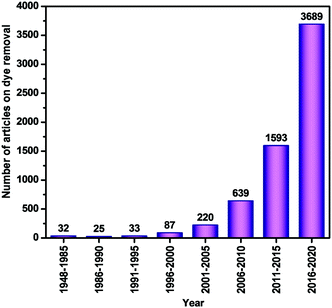 |
| Fig. 1 Frequency of publications on dye removal with selected keyword ‘Dye Removal’ (details are given in Section A of the ESI†). | |
The direct disposal of untreated dye-containing effluent into natural water bodies has an adverse effect on the photosynthetic activity in aquatic ecosystems.18 It creates mutagenic or teratogenic effects on aquatic organisms and fish species due to the existence of metals19 and aromatics.20 Further, the presence of dyes in the environment has mild to severe toxic effects on human health, including carcinogenic, mutagenic, allergic, and dermatitis effects, kidney disease.21 It has been reported that chromium-based dyes are generally complex in structure and cause carcinogenic effects on human health.22 Thus, the disposal of dyes in the environment contaminates the water bodies, subsequently affecting the water quality, aquatic life, and human health. Table 1 also describes the ecotoxicological effects of dyes on living organisms. The sources and pathways of various dye pollutants in water bodies are depicted in Fig. 2.
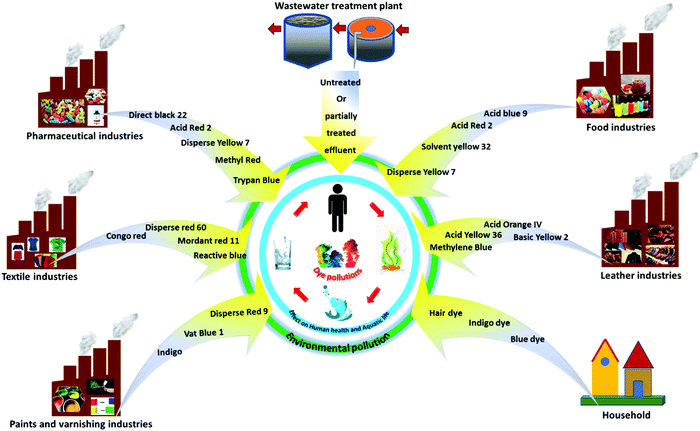 |
| Fig. 2 Sources and pathways of dyes in the environment. | |
Accordingly, researchers have focused on the remediation of dye wastewater using coagulation/flocculation, electrocoagulation, filtration, adsorption, ion-exchange, advanced oxidation processes (AOPs), activated sludge processes (ASP), sequencing batch reactors (SBR), membrane bioreactors (MBR), moving bed biofilm reactors (MBBR), and constructed wetlands (CW).23–30 The coagulation process involves the destabilization of charged suspended and colloidal impurities.31,32 The electrocoagulation method employs a direct current source between metal electrodes containing iron or aluminum submerged in dye-contaminated water. Metal ions create a wide range of coagulated species and metal hydroxides at a certain pH, which destabilize and agglomerate suspended particles or precipitates and adsorb dye molecules.23,33 In the filtration techniques, the separation of dissolved and suspended particles is carried out by sieving and particle capturing mechanisms.32,34,35 Adsorption methods involve the movement of solids from the bulk liquid to the surface of the adsorbent.26,36 The ion-exchange method involves the removal of dyes through the strong interactions between the functional groups on ion exchange resins and charged dye molecules. The formation of strong linkages between the resins and the dye molecules results in the separation of dyes from wastewater.29 The use of AOPs, such as ozonation, ultraviolet/hydrogen peroxide (UV/H2O2), Fenton, ultrasound, anodic oxidation, and photocatalytic processes, have been efficiently employed to treat dye wastewater. AOPs involve the formation of active radicals, which degrade targeted contaminants.35,37–43 The suspended and/or attached growth of bacterial systems (i.e., ASP, MBBR, SBR, CW, and MBR) have been employed in the biodegradation of dye molecules.44,45 The number of articles on various existing physicochemical and biological treatment techniques is shown in Fig. 3a, which confirms that among these technologies, adsorption is considered to be one of the most important and useful decontamination processes. It is considered to be a fast, low cost, simple, sludge-free process, having high efficiency and/or selectivity, mechanical stability, and recycling facilities.14,46–51 The adsorption process is widely used for the remediation of different pollutants from wastewater, including heavy metals, arsenic, and dyes.52–59 Additionally, a pie chart displaying the percentage of literature available on dye removal using various adsorption techniques is shown in Fig. 3b. Considering this, the present study aims to review dye removal from polluted water via the adsorption process using various types of adsorbents. Specifically, several adsorbents, including activated carbon, metal oxide-based, carbon-based, bio-adsorbent, metal–organic framework (MOF), and polymer-based materials, are widely applied for the adsorption of dye from polluted water.13,14,60–67 These adsorbents possess the advantages of easy fabrication, high effective surface area, multi-functionalities, high surface volume ratio, high reactivity, large number of active sites, reusability, low cost, and high efficiency to treat recalcitrant compounds.68,69
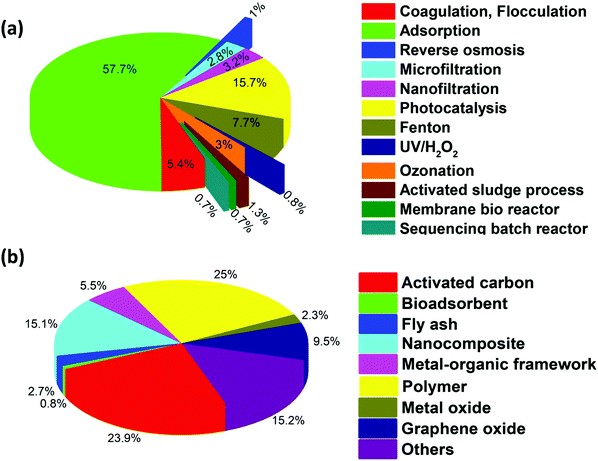 |
| Fig. 3 Pie-chart showing the percentage of literature available on dye removal for (a) various physicochemical and biological techniques. Keywords: dye, water, treatment, and name of each technique, as mentioned in the plot. (b) Adsorption techniques using different adsorbents. Keywords: dye, water, adsorption, and the type of each adsorbent as mentioned in the plot. (Details are given in Section B and C of the ESI,† respectively). | |
According to the available literature, several techniques such as chemical oxidation, coagulation, filtration with coagulation, precipitation, adsorption, and biological treatments have been frequently used to remove dyes from industrial and domestic effluents. However, the use of each of these methods in separation has merits and disadvantages. For example, coagulation is most commonly used method in industry, which does not involve the formation of harmful and toxic intermediates. However, inherent sludge formation and its disposal remain its biggest drawback. Further, the choice of method is also guided by operational costs. Considering this, the adsorption process is considered to be one of the most effective and inexpensive treatment processes to remove dyes in wastewater. Accordingly, the present article presents a review of the challenges and opportunities of the adsorption methodology available as the current state of the art in the removal of dyes from contaminated water. This covers the classification of dye effluents released from various industries, their solubility in water, chemical structures, and impact of these toxic compounds on the environment and human health, and the types of adsorbents used in the remediation of dyes are reviewed. This is followed by an updated review on the removal of different dyes using a variety of adsorbents. In addition, the adsorptive separation of dyes is also assessed in terms of the critical factors influencing dye separation, maximum adsorption capacity, adsorption mechanisms, and adsorption kinetics. It is anticipated that the current review will be helpful in identifying cost-effective and efficient adsorption methods for the remediation of industrial dyes in wastewater. Finally, the present review also targets various research gaps and their possible solution.
2. Dyes: sources, classifications, and ecotoxicological effects
A dye is generally described as substances capable of imparting color through physical/chemical binding on a substrate to which it is applied. The presence of chromophores in dye accounts for the development of color, which auxochromes are attached to.65Table 1 describes the classification of dyes based on their physicochemical properties, applications, ecotoxicological effects, and water solubility. These dyes exhibit aromatic molecular structures originating from hydrocarbons, such as benzene, toluene, naphthalene, anthracene, and xylene.70 Dyes are mainly derived from two significant sources, including natural and anthropogenic. The natural sources include plants, different insects, animals, and minerals, whereas synthetic dyes are man-made or manufactured using various organic molecules.3,71 However, the multifaceted applications of dyes in daily life involve their release together with other toxic organic/inorganic chemicals from industrial effluents, resulting in detrimental effects on the environment.71 Therefore, it is necessary to protect the environment from these toxic dye/dye effluents released in water by subjecting them to various physical, chemical, biological treatments or their combinations. Fig. 2 shows the sources and pathways of different dyes originating from various sources, such as industry, wastewater treatment plants and households, contributing to environmental pollution. Dyes can be classified considering their chemical structure, physicochemical attributes, origin, and applications.22 This classification also considers the extremely hazardous/toxic industrial effluents that are carcinogenic to human health and the environment.1,21 Accordingly, Table 1 describes acid, basic, reactive, nitro, vat, disperse, azo, mordant dyes, etc.
3. Existing treatment processes for the remediation of dyes
Previously, conventional treatment processes were employed using proper regulatory guidelines for the treatment of dyes in wastewater.91 However, advanced dye removal processes have been established considering the discharge limit. They include several biological (e.g., ASP, MBR, SBR, MBBR, and CW), coagulation/flocculation, and advanced physicochemical processes (such as adsorption, filtration, photocatalysis, Fenton reaction, ozonation, UV/H2O2, and anodic oxidation) reported for the purification of dye-contaminated wastewater.29,36,92–95 Biological processes use attached and suspended growth systems for the removal of dyes using aerobic and anaerobic or facultative bacteria.96 In the coagulation/flocculation process, various coagulants are employed to destabilize the charged suspended and colloidal impurities.32 The advanced physicochemical processes are based on the principle of the sieving process, solid–liquid separation, attraction–repulsion, free radical reactions, catalytic oxidation, and electrochemical reactions. Adsorption is another simple facile process extensively used in the treatment of industrial dye effluents. This process involves the movement of dye molecules present in the liquid phase to a solid surface of various adsorbents.26,36 Membrane processes such as reverse osmosis (RO), nanofiltration (NF), and microfiltration (MF) have also been successfully employed in the treatment of dye–laden water (more than or about 90% removal efficiency). However, pore blockage and membrane fouling during these processes are still major drawbacks.93,97–99 In AOPs, active radicals are generated, mainly hydroxyl radicals, which play an important role in degrading persistent dye compounds. However, the high cost/energy requirements and the formation of toxic by-products are a few major constraints in their practical application.35,100
In addition, biological processes, such as ASP, MBR, SBR, and MBBR, have shown good efficacy for dye removal. However, the good removal efficiency of dyes by biological processes is overshadowed by their limitations such as space requirements, low removal rate, and inefficiency to treat recalcitrant dye components. The number of articles published on various existing physicochemical and biological processes are compared and shown in Fig. 3a, which presents that adsorption is the most studied process for dye removal. Overall, it can be inferred that in comparison to the existing advanced oxidation, filtration, and biological treatment processes, the adsorption process is beneficial for treating dye wastewater owing to its easy operation, low cost, high efficiency, recycling of the adsorbents, suitability for the treatment of persistent dye compounds and applicability.40,101
4. Overview of various adsorbents for the removal of dyes
At present, various adsorbents such as bio-sorbents, carbon-based nano-adsorbents, transition metal-based oxides, MOFs, and polymer-based adsorbents are used to treat dye-containing wastewater. The pie-chart in Fig. 3b displays the percentage of the literature available on dye removal using various adsorbents, where it can be observed that adsorbents such as polymer-based materials and activated carbon are studied more for the removal of dyes.
Table 2 Activated carbon (AC) as an adsorbent in dye removal
Source of AC |
Dyes |
Experimental conditions |
Adsorption capacity/removal efficiency |
Adsorption kinetics; isotherm; and mechanisms |
C
0: initial dye concentration; T: temperature; and λmax: maximum wavelength detected for the analysis of dye. |
Commercial activated carbon |
Saw-dust105 |
Direct Blue 2B and Direct Green B |
Time: 120 min |
518 and 327.9 mg g−1, respectively |
Pseudo-second-order kinetics; Langmuir isotherm model; chemisorption |
pH: 3 |
Apricot stones and commercial activated carbon106 |
Methylene blue (MB) and methyl orange (MO) |
C
0: 10 mg L−1 |
Activated carbon prepared from apricot stones (ASAC): 36.68 and 32.25 mg g−1, respectively. |
Pseudo-second-order kinetics; Langmuir isotherm; chemisorption and intraparticle diffusion |
T: 298 K |
Commercial activated carbon (CAC): 199.60 mg g−1 and 35.43 mg g−1, respectively. |
Dose: 0.5 g/50 mL |
|
pH: 4.85 (MB) and 4.87 (MO) |
|
Time: 60–180 min |
|
λ
max: 665 and 465 nm, respectively |
|
Mesoporous carbon material62 |
MO |
Time: 60 min |
294.1 mg g−1 |
Pseudo-second-order kinetics; Langmuir isotherm; chemisorption |
C
0: 1000 mg L−1 |
Dose: 50 mg in 25 mL |
pH: 3–9 |
λ
max: 465 nm |
Red Oak (Quercus rubra)107 |
MB |
C
0: 10 mg L−1 |
97.18% |
— |
Dose: 0.25 g/50 mL |
pH: 10 |
T: 318 K |
Agitation speed: 175 rpm |
Time: 2 h |
λ
max: 660 nm |
Norit Darco 12 × 20 (DARCO), Norit R008 (R008), and Norit PK 1-3 (PK13)108 |
Reactive Black 5 |
pH: 10 |
348, 527, and 394 mg g−1, respectively |
Pseudo-second-order kinetics; Langmuir or Langmuir–Freundlich model; intraparticle diffusion |
Dose: 1 g L−1 |
C
0: 500 mg L−1 |
Time: 24 h |
λ
max: 603 nm |
|
Activated carbon from waste materials |
Lemongrass leaf110 |
Methyl red |
pH: 2 |
76.923 mg g−1 |
Pseudo-first-order kinetics; Koble–Corrigan isotherm (R2: 0.997); physisorption |
Time: 5 h |
λ
max: 520 nm |
Rice husk111 |
Rhodamine B (RhB) |
Time: 5 h |
478.5 mg g−1 |
Pseudo-second-order kinetics; Langmuir isotherm; chemisorption |
pH < 3.20 |
T: 303 K |
λ
max: 554 nm |
Orange peel112 |
Malachite green (MG) |
C
0: 1 mg mL−1 |
28.5 mg g−1 |
— |
λ
max: 617 nm |
Coconut leaves115 |
MB |
C
0: 30–400 mg L−1 |
149.3 mg g−1 |
Pseudo-second-order kinetics; Langmuir isotherm; physisorption |
pH: 3–11 |
Guava leaf117 |
Congo red (CR) |
C
0: 10–50 mg L−1 |
39.70 mg g−1 |
Pseudo-second-order kinetics; Freundlich isotherm; multilayer adsorption |
λ
max: 497 nm |
Brazilian low-cost agriculture waste118 |
Basic Blue 26, Basic Green 1, Basic Yellow 2, and Basic Red 1 |
C
0: 250 mg L−1 |
10–76, 26–83, 27–83, and 21–70 mg g−1, respectively. |
Electrostatic interactions |
Dose: 0.3 g in 100 mL |
Time: 24 h |
λ
max: 618 nm, 625 nm, 433 nm, and 530 nm, respectively |
Spent tea leaves109 |
MG |
C
0: 220 mg L−1 |
256.4 mg g−1 |
Pseudo-second-order kinetics; Langmuir isotherm; chemisorption |
Dose: 0.02 g/25 mL |
Time: 180 min |
λ
max: 617 nm |
Lemon peels/sodium alginate119 |
MB |
C
0: 25 – 300 mg L−1 |
841.37 mg g−1 |
Pseudo-first-order and pseudo-second-order kinetics; Langmuir isotherm; electrostatic interaction and external surface adsorption |
λ
max: 664 nm |
Table 3 Non-conventional adsorbents in dye removal
Examples of adsorbents |
Dyes |
Experimental conditions |
Adsorption capacity/removal efficiency |
Adsorption kinetics; isotherm; and mechanisms |
C
0: initial dye concentration; T: temperature; and λmax: maximum wavelength detected for the analysis of dye. |
Waste materials from agricultural |
Raw maize cob122 |
Bromophenol blue and bromothymol blue |
C
0: 10–100 mg L−1 |
96.53%, and 94.39%, respectively |
Pseudo-second-order kinetics; Temkin isotherm; chemisorption |
Dose: 0.5–4.0 g |
Time: 125 and 110 min, respectively |
λ
max: 591.22 and 430.9 nm, respectively |
Exhausted coffee ground powder60 |
Rhodamine (Rh) dye (Rh B and Rh 6G) |
Dose: 50 mg/50 mL |
5.255 and 17.369 μmol g−1 |
Pseudo-first-order kinetics and pseudo-second-order kinetics; Langmuir isotherm; chemisorption |
Time: 3 h |
λ
max: 554 and 526 nm, respectively |
NaOH treated saw dust121 |
Brilliant green |
Time: 3 h |
55.86 mg g−1 |
Pseudo-second-order kinetics; Temkin and Redlich–Peterson isotherm; physisorption and boundary layer diffusion |
Dose: 4 g L−1 |
C
0: 100 mg L−1 |
T: 303 K |
Nigella sativa seed-based nanocomposite-MnO2/BC123 |
MB |
Dose: 1.0 g L−1 |
185.185 mg g−1 |
Pseudo-second-order kinetics; Freundlich isotherm; intraparticle diffusion, and film diffusion action |
C
0: 10 mg L−1 |
λ
max: 660 nm |
Neem leaf powder124 |
Brilliant green |
C
0: 10–50 mg/dm3 |
0.149 to 0.554 mmol g−1 |
First-order kinetics; Langmuir isotherm; external surface and pore diffusion |
Time: 4 h |
T: 300 K |
λ
max: 624 nm |
Pineapple leaf125 |
Basic green 4 (BG4) |
C
0: 50 mg L−1 |
48.72 mg g−1 |
Pseudo-second-order kinetics; Langmuir isotherm; chemisorption |
pH: 9.0 |
Time: 150 min |
Dose: 5 g L−1 |
T: 298 K |
λ
max: 618 nm |
Pine tree leaves126 |
Basic Red 46 (BR 46) |
C
0: 20–100 mg L−1 |
71.94 mg g−1 |
Pseudo-second-order kinetics; Langmuir isotherm; physisorption |
Dose: 1–6 g L−1 |
T: 298–318 K |
Time: 0–120 min |
λ
max: 530 nm |
Platanusorientalis leaf127 |
MB |
C
0: 20–180 mg L−1 |
114.94 mg g−1 |
Pseudo-second-order kinetics; Langmuir isotherm; endothermic adsorption |
Dose: 80 mg/50 mL |
T: 25–60 °C |
Time: 0–70 min |
λ
max: 664 nm |
Microwave-assisted spent black tea leaves113 |
Eriochrome black T (EBT) |
C
0: 10–400 mg L−1 |
242.72 mg g−1 |
Pseudo-second-order kinetics; Langmuir isotherm; physicochemical interaction |
Dose: 0.25–5.0 g L−1 |
T: 298–338 K |
Time: 24 h |
λ
max: 518 nm |
Rice husk148 |
MB |
C
0: 100 mg L−1 |
1350 mg g−1 |
Pseudo-first-order kinetics; Freundlich and Sips isotherm; electrostatic interaction |
Dose: 250 mg L−1 |
pH: 10 |
T: 298 K |
λ
max: 664 nm |
Waste materials from industry |
Steel and fertilizer industries wastes128 |
Ethyl orange, metanil yellow, and Acid Blue 113 |
Time: 3 h |
198 mg g−1, 211 mg g−1, and 219 mg g−1, respectively |
Pseudo-first-order kinetics; Langmuir isotherm; physisorption |
pH: 7 ± 0.5 |
λ
max: 475 nm, 432 nm, and 532 nm, respectively |
Coal fly ash129 |
MB and crystal violet (CV) |
Dose: 0.08 g L−1 |
CV: >90% MB: <85% |
Pseudo-second-order kinetics; Langmuir isotherm; endothermic adsorption for CV and exothermic reaction for MB dye. |
Time: 24 h |
λ
max: 665 nm and 590 nm, respectively |
Amine-functionalized biomass fly ash149 |
Alizarin red S (ARS) and bromothymol blue (BTB) |
Time: 10 min and 5 min, respectively |
13.42 and 15.44 mg g−1, respectively |
Linear pseudo-second-order kinetics; modified Langmuir–Freundlich isotherm; electrostatic interaction |
λ
max: 422 nm and 432 nm, respectively |
Carbonaceous slurry waste130 |
RhB and Bismark Brown R |
pH: 5.5–6.5 |
91.1 mg g−1 and 85 mg g−1, respectively |
First-order and pore-diffusion; Langmuir isotherm; physisorption |
Time: ∼25 min |
λ
max: 554 nm and 460 nm, respectively |
Industrial waste coal gangue131 |
Cationic Red X-5GN (CR) and Cationic Blue X-GRRL (CB) |
Time: 3 h |
1.044 mg g−1 and 2.170 mg g−1, respectively |
Pseudo-second-order and Elovich kinetics; Freundlich isotherm for CR and Langmuir isotherm for CB dye; electrostatic attraction, n–π interactions, and hydrogen bonding |
pH: 2–12 |
Industrial waste shells of egg132 |
MB and CR |
C
0: 50–1000 mg L−1 |
94.9 mg g−1 and 49.5 mg g−1, respectively |
Pseudo-second-order kinetics; Freundlich isotherm; Electrical double layer mechanism, and electrostatic attraction for MB and CR dye, respectively |
T: room temperature |
Time: 10–120 min |
|
Natural and synthetic materials |
Green clay minerals150 |
MB |
Time: 60 min |
241.96 mg g−1 |
Langmuir isotherm; single-layer adsorption |
300 rpm |
Dose: 200 mg/250 mL |
T: 293 K |
λ
max: 665 nm |
Natural clay151 |
Basic Red 46 |
Dose: 10 mg/100 mL |
594 mg g−1 |
Pseudo-second-order kinetics; Langmuir isotherm; electrostatic interactions, including hydrogen bonding |
pH: 7 |
λ
max: 530 nm |
Sodium montmorillonite137 |
RhB |
pH: 7 |
42.19 mg g−1 |
Pseudo-second-order kinetics; Langmuir isotherm; high electrostatic attraction |
λ
max: 554 nm |
Sepiolite134 |
Astrazon Red (Basic Red 46) and Sirius Blue (Direct Blue 85) |
C
0: 75 mg L−1 and 150 |
108 mg g−1 and 454 mg g−1, respectively |
Langmuir isotherm and Freundlich isotherm; physisorption |
mg L−1, respectively |
pH: 8 and 3.5, respectively |
T: 313 K and 303 K, respectively. |
λ
max: 525 nm and 590 nm, respectively |
Acid-treated palygorskite136 |
Crystal violet (CV), cationic light yellow (7GL), MB, and MO |
C
0: CV, 7GL, MB, and MO, were 500, 500, 200, 500, and 200 mg dm−3, respectively. |
CV: 223.43 mg g−1 |
Sips and Langmuir isotherm; bridging effect mechanism |
λ
max: 581, 415, 662, 463, and 642 nm, respectively |
7GL: 290.86 mg g−1 |
|
MB: 86.53 mg g−1 |
|
MO: 276.11 mg g−1 |
Palygorskite modified by 3-aminopropyl triethoxysilane135 |
Reactive red 3BS, reactive blue KE-R, and reactive black GR |
Time: 20 min |
34.23 mg g−1, 38.59 mg g−1, and 60.13 mg g−1, respectively |
Pseudo-second-order kinetics; Langmuir isotherm; electrostatic attraction |
C
0: 20–600 mg L−1 |
pH: 2–12 |
λ
max: 546 nm, 620 nm, and 602 nm, respectively |
Saklikent mud138 |
Brilliant green |
C
0: 1–20 mg L−1 |
1.18 mg g−1 |
Pseudo-first-order kinetics and intra-particle model at 25 °C and pseudo-second-order kinetics at the higher temperature. |
Dose: 0.1 g/50 mL |
Langmuir isotherm; electrostatic attraction |
λ
max: 625 nm |
|
Flower-like LDH139 |
MO |
C
0: 100 mg L−1 |
500.6 mg g−1 |
Pseudo-second-order kinetics; Langmuir isotherm; chemisorption |
Dose: 1 g |
pH: 3 |
T: 298 K |
Time: 10 min |
Hollow LDH nanowires140 |
MO |
C
0: 5–40 mg L−1 |
210 mg g−1 |
Langmuir isotherm |
Dose: 0.5 g L−1 |
Time: 90% removal at <10 min |
|
Bio-adsorbents |
Spirulina platensis
141
|
Acid blue 9 and FD&C Red No. 40 |
pH: 2 |
1653.0 mg g−1 and 400.3 mg g−1, respectively, 95% for both |
Avrami kinetic; electrostatic attraction |
Agitation speed: 400 rpm and 225 rpm for Acid Blue 9 and FD&C Red No. 40, respectively. |
Time: 20–100 min |
λ
max: 408 and 500 nm, respectively. |
Shrimp shell142 |
Acid blue 25 |
pH: 2 |
1093 mg g−1 |
Pseudo-second-order kinetics; Langmuir, Freundlich and Temkin isotherm; physisorption |
Dose: 0.1–0.4 g L−1 |
Time: 30 min |
λ
max: 600 nm |
Neem sawdust147 |
CV, MB, MG, and RhB |
C
0: 6–12 mg L−1 |
2.197, 2.120, 2.038, 1.480 mg g−1, respectively |
|
Dose: 0.5 g in 100 mL |
T: 25–45 °C |
pH: 7.2 |
Time: 30 min |
λ
max: 592 nm, 664 nm, 616 nm, and 555 nm, respectively |
Cellulose nanocrystal-reinforced keratin143 |
Reactive Black 5 and Direct Red 80 |
C
0: 200 mg L−1 |
1201 mg g−1 and 1070 mg g−1, respectively |
Pseudo-second-order kinetics; Langmuir isotherm; electrostatic interaction |
Time: 3 h |
pH: 3 |
Dose: 0.1 g/200 mL |
λ
max: 595 nm and 543 nm, respectively |
Spent substrate of Ganodormalucidum144 |
MG, safranine T, and MB |
C
0: 10–120 mg L−1 |
40.65 mg g−1, 33 mg g−1, and 22.37 mg g−1, respectively |
Pseudo-second-order kinetics; Freundlich isotherm; chemisorption |
pH: 6 |
Time: 4 h |
λ
max: 617 nm, 530 nm, and 664 nm, respectively |
Carbohydrate polymeric biodegradable adsorbent of wheat flour145 |
Rhodamine B (RhB) |
C
0: 5.0 mg L−1 |
142.26 mg g−1 |
Langmuir adsorption; electrostatic interaction, π–π conjugation, and hydrogen bonding conjugation |
pH: 5.5 |
Wood-based colloidal cellulose nanocrystals152 |
Auramine O (AO) |
pH: not adjusted |
20 mg g−1 |
Pseudo-second-order kinetics; Freundlich isotherm; electrostatic interactions and hydrogen bonding |
C
0: 2.5–30 mg L−1 |
λ
max: 430 nm |
Egg shell membrane153 |
Basic Fuchsin (BF) |
pH: 6 |
48 mg g−1 |
Pseudo-second-order kinetics; Freundlich isotherm; electrostatic interactions |
Time: 25 min |
T: 298 K |
Arginine-modified starch resin154 |
Acid fuchsin (AF) and Acid Orange G (AOG) |
C
0: 0.25 mmol/L |
AF: 21.326 mg g−1 |
Pseudo-second-order kinetics; Langmuir isotherm; electrostatic attractions, prevalent hydrogen bonds, and hydrophobic interactions (van der Waals force) |
Dose: 0.1 g/20 mL |
AOG: 23.485 mg g−1 |
Time: 1 h |
|
T: 298 K |
|
Table 4 Hybrid nanomaterial as adsorbents for dye removal
Adsorbent |
Dyes |
Experimental conditions |
Adsorption capacity/removal efficiency |
Adsorption kinetics, isotherm, and mechanisms |
C
0: initial dye concentration; T: temperature; and λmax: maximum wavelength detected for the analysis of dye. |
Carbon-based hybrid nanocomposite |
Ultrafine Ni/C156 |
RhB and MB |
Dose: 2 g L−1 |
5.269 and 7.415 mg g−1, respectively |
Pseudo-second-order kinetics; Freundlich isotherm; chemisorption process |
C
0: 5 mg L−1 |
Time: 2 h |
λ
max: 554 and 664 nm, respectively |
Iron–carbon hybrid magnetic nanosheets157 |
CR and MB |
Time: 24 min |
531.9 and 185.2 mg g−1, respectively |
Pseudo-second-order kinetics; Langmuir isotherm; chemisorption |
pH: 2 and 8, respectively |
Dose: 6 mg/15 mL |
λ
max: 662 and 664 nm, respectively. |
Hierarchically porous silicon–carbon–nitrogen hybrid materials158 |
Methyl blue and acid fuchsin |
C
0: 300 mg L−1 and 200 mg L−1, respectively |
1327.7 mg g−1 and 1084.5 mg g−1 respectively |
Pseudo-second-order kinetics; Langmuir isotherm; Chemisorption |
Ni/porous carbon-CNT159 |
MG, CR, RhB, MB, and MO |
C
0: 20 mg L−1 |
898 mg g−1, 818 mg g−1, 395 mg g−1, 312 mg g−1, and 271 mg g−1, respectively |
Pseudo-second-order kinetics; Langmuir isotherm; multilayer adsorption mechanism |
Time: 60 min |
|
Activated carbon-based hybrid nanocomposites |
Konjac glucomannan/activated carbon aerogel160 |
MB |
C
0: 140 mg L−1 |
416.67 mg g−1 |
Pseudo-second-order kinetics; Langmuir isotherm; density gradient force and hydrogen bond interaction |
Dose: 10 mg/20 mL |
T: 313 K |
ZnO-NP-loaded Parthenium weed activated carbon (ZnONPs-PWAC)161 |
MB |
C
0: 100 mg L−1 |
∼99% |
— |
pH: 6 |
Dose: 50 mg/100 mL |
Time: 60 min |
λ
max: 670 nm |
Sulfonic acid-modified activated carbon (MTLAC-SA) and MTLAC162 |
RhB and Orange G |
C
0: 200–800 mg L−1 |
757.6 mg g−1 using MTLAC-SA and 318.5 mg g−1 using MTLAC, respectively |
Pseudo-second-order kinetics; Langmuir isotherm; homogeneous adsorption |
λ
max: 664 nm and 476 nm, respectively |
Finger-citron-residue-based activated carbon163 |
MO and MB |
C
0: 50–500 mg L−1 |
934.58 and 581.40 mg g−1, respectively |
Pseudo-second-order kinetics; Langmuir isotherm; π–π stacking interaction and electrostatic attraction |
λ
max: 464 nm and 664 nm, respectively |
Carbon nanotubes166 |
Procion Red MX-5B (CI reactive red 2) |
Dose: < 0.25 g L−1 |
44.64 mg g−1 |
Pseudo-second-order kinetics; Langmuir isotherm; physisorption |
pH: 6.5 |
T: 291 K |
λ
max: 538 nm |
Calcium alginate/multi-walled carbon nanotubes168 |
MB and MO |
pH: 4–12 for MB and <2 for MO |
606.1 and 12.5 mg g−1, respectively |
Pseudo-second-order kinetics; Langmuir isotherm; Opposite charge attraction |
Magnetic multi-wall carbon nanotube70 |
MB, neutral red, and brilliant cresyl blue |
C
0: 1.4–37.4 mg L−1 |
15.74 mg g−1, 20.33 mg g−1, and 23.55 mg g−1, respectively |
Pseudo-second-order kinetics; Freundlich isotherm; van der Waals interactions occurring |
Dose: 0.5 g L−1 |
pH: ∼7 |
Multi-wall carbon nanotubes167 |
MO |
C
0: 20 mg L−1 |
51.74 mg g−1 |
Pseudo-second-order kinetics; Langmuir isotherm; external diffusion, boundary layer diffusion, and intra-particle diffusion |
T: 25 °C |
pH: ∼7 |
Time: 2 h |
Dose: 15 mg/50 mL |
λ
max: 460 nm |
Magnetite-loaded multi-walled carbon nanotubes170 |
MB |
C
0: 20 mg L−1 |
48.06 mg g−1. |
Pseudo-second-order kinetics; Langmuir isotherm; electrostatic attraction and π–π stacking interactions |
Dose: 0.02 g/50 mL |
T: 25 ± 1 °C |
pH: 7 |
Magnetite/MWCNTs169 |
MB |
C
0: 10–70 mg L−1 |
55 mg g−1 |
Pseudo-second-order kinetics; Langmuir isotherm; electrostatic interactions, π–π dispersion interaction, hydrogen bonding, and electron donor–acceptor complex formation. |
Dose: 0.02 g/25 mL |
Time: 0–11 min |
pH: 1 |
|
Graphene oxide, reduced graphene oxide, and their nanocomposites |
3D hierarchical GO–NiFe LDH composite178 |
CR and MO |
Time: 225 min and 135 min, respectively |
489 and 438 mg g−1, respectively |
Pseudo-second-order kinetics; Langmuir isotherm; electrostatic attraction, ions exchange, and π–π stacking interaction |
Graphene/PANI/Fe3O4179 |
CR |
C
0: 100 mg L−1 |
248.76 mg g−1 |
Pseudo-second-order kinetics; Langmuir isotherm; electrostatic interaction, hydrogen bond, and π–π stacking interaction |
Time: 2 h |
Dose: 25 mg/25 mL |
λ
max: 625 nm and 498 nm, respectively |
Graphene oxide174 |
MB |
C
0: < 250 mg L−1 |
714 mg g−1 |
Freundlich isotherm; exothermal adsorption reaction, and π–π stacking interaction |
λ
max: 664 nm |
Layered graphite oxide180 |
MB and MG |
Dose: 10 mg/500 mL |
351 mg g−1 and 248 mg g−1, respectively |
Pseudo-second-order kinetics; Langmuir isotherm; electrostatic attraction |
λ
max: 663 nm and 617 nm, respectively |
Graphene oxide/magnesium oxide nanocomposites181 |
MB |
C
0: 5–100 mg L−1 |
833 mg g−1 |
Pseudo-second-order kinetics; Langmuir isotherm; electrostatic attraction, hydrogen bonding, and π–π interaction |
Time: 5–60 min |
Dose: 0.1–1 g L−1 |
pH: 11 |
λ
max: 664 nm |
GO/Fe3O4 nanohybrids183 |
MB |
C
0: 20 mg L−1 |
∼100% |
Adsorption mechanism followed by π–π interaction |
Dose: 3 mg/5 mL |
pH: 6 |
λ
max: 664 nm |
Sandwiched Fe3O4/carboxylate graphene oxide nanostructures182 |
MB and RhB |
C
0: 10 mg L−1 MB and 5 mg L−1 RhB |
36 mg g−1 and 22.1 mg g−1, respectively |
Pseudo-second-order kinetics; electrostatic attraction |
pH: 6 |
λ
max: 632 nm and 554 nm, respectively |
Magnetic GO/poly(vinyl alcohol) composite gels207 |
MB and methyl violet (MV) |
Dose: 20 mg/5 mL |
270.94 and 221.23 mg g−1, respectively |
Pseudo-second-order kinetics, Langmuir isotherm; strong electrostatic attraction and complexation |
C
0: 0.2 mM |
Time: 0.5 h |
λ
max: 662 nm and 583 nm, respectively |
|
Hybrids of natural and synthetic clay |
Cross-linked chitosan/sepiolite clay composite194 |
MB and Reactive orange 16 |
C
0: 100 mg L−1 |
40.986 mg g−1 and 190.965 mg g−1, respectively |
Pseudo-second-order kinetics; Freundlich isotherm; physisorption |
Dose: 2 g L−1 |
Time: 30 h |
pH: >9 for MB and 3 for reactive orange 16 |
λ
max: 665 nm and 496 nm, respectively |
MgAl-layered double hydroxide supported MOF195 |
MO |
Time: 20 min |
99% and 600 mg g−1 |
Pseudo-first-order kinetics; electrostatic attraction |
C
0: 5–50 mg L−1 |
λ
max: 463 nm |
Mg–Al-layered double hydroxide196 |
Reactive Red, Congo red, and Acid Red 1 |
Time: 60 min |
59.49 mg g−1, 37.16 mg g−1, and 108.0 mg g−1, respectively |
Pseudo-second-order kinetics; Langmuir isotherm; electrostatic attraction and ion exchange |
pH: 9–10 |
λ
max: 543 nm, 500 nm, and 532 nm, respectively |
Nanohybrid layered double hydroxides197 |
Amaranth, diamine Green B, and brilliant green |
T: Room temperature |
0.8 mmol g−1, 1.089 mmol g−1, and 1.418 mmol g−1, respectively |
Pseudo-second-order kinetics; ion exchange |
pH: 7–9.5 |
λ
max: 520 nm, 623 nm, and 624 nm, respectively |
|
Hybrids of fly ash |
Biomass fly ash geopolymer monoliths199 |
MB |
C
0: 1–50 mg L−1 |
15.4 mg g−1 |
Freundlich isotherm; electrostatic attraction |
Time: 30 h |
Reused up to five cycles |
λ
max: 664 nm |
|
Porous biomass fly ash-based geopolymer spheres198 |
MB |
C
0: 10–125 mg L−1 |
79.7 mg g−1 |
Freundlich isotherm; multilayer adsorption |
Time: 30 h |
Reused up to eight cycles |
λ
max: 664 nm |
|
Fly ash–TiO2 composite201 |
Mixture of bemacid red and bemacid blue |
C
0: 10 mg L−1 each |
4.003 and 1.194 mg g−1 |
Pseudo-second-order kinetics; hydrogen abstraction, redox reactions, also the π-bonds |
pH: 10.6 |
λ
max: 444 nm and 652 nm, respectively |
Ca(OH)2/Na2FeO4 modified fly ash202 |
Orange II |
C
0: 50 mg L−1 |
24.8 mg g−1 |
Pseudo-second-order kinetics; Langmuir isotherm; electrostatic interaction, hydrogen bonding |
Dose: 2000 mg L−1 |
|
Hybrids of bio adsorbents |
Cellulose-g-poly(acrylic acid-co-acrylamide)204 |
Acid blue 93 (AB93) and MB |
C
0: 200 mg L−1 |
1602 and 1814 mg g−1, respectively |
Pseudo-second-order kinetics, Freundlich isotherm; electrostatic interaction |
Time: 90 min. |
pH: 7 |
Dose: 0.4 g L−1 |
λ
max: 664 and 607 nm, respectively |
Sulphonated bio-adsorbent from waste hawthorn kernel205 |
MB |
C
0: 25–400 mg L−1 |
151.5 mg g−1 |
Pseudo-second-order kinetics; Langmuir isotherm; ion exchange process |
Time: 0–360 min |
T: 25–60 °C |
Dose: 0.1 g in 50 mL |
λ
max: 665 nm |
Cross-linked beads of activated oil palm ash zeolite/chitosan203 |
MB and acid blue 29 |
C
0: 50–400 mg L−1 |
199.2 mg g−1 and 270.27 mg g−1, respectively |
Pseudo-second-order kinetics; Freundlich isotherm; physisorption |
T: 50 °C |
pH: 3–13 |
λ
max: 668 and 602 nm, respectively |
Agricultural waste/graphene oxide 3D206 |
MB |
C
0: 1000 mg L−1 |
414.03 mg g−1 |
Pseudo-second-order kinetics; Temkin isotherm; multimolecular layers of coverage and heterogeneous adsorption |
T: 25 °C |
The removal was >90% after five cycles |
pH: 12 |
|
λ
max: 663 nm |
|
Table 5 Metal oxide-based hybrid (magnetic and non-magnetic) nanocomposite materials for dye removal
Adsorbent |
Dyes |
Experimental conditions |
Adsorption capacity/removal efficiency |
Adsorption kinetics, isotherm, and mechanisms |
C
0: initial dye concentration; T: temperature; and λmax: maximum wavelength detected for the analysis of dye. |
Pure magnetic materials |
Fe3O4211 |
Rhodamine 6G |
pH ∼ 7 |
150–600 mg g−1 |
Fluorescence resonance energy transfer between the dye molecules and Fe3O4 magnetic nanoparticle |
Dose: 2.5–10 mg L−1 |
Time: 30 min |
λ
max: 525 nm |
γ-Fe2O3215 |
Acid red 27 |
pH < 5.5 |
0.027 mmol g−1 |
Pseudo-second-order kinetics; Langmuir and Freundlich isotherm; physisorption and electrostatic attraction |
Time: 4 min |
λ
max: 520 nm |
Magnetic-carbon-based nanocomposite |
Magnetic graphene oxide modified by chloride imidazole ionic liquid224 |
Anionic: Glenn Black R (GR) and Orange IV (OIV) cationic: acridine orange (AO) and crystal violet (CV) |
C
0: 40 mg L−1 |
GR, OIV, AO, and CV were 588.24, 57.37, 132.80, and 69.44 mg g−1, respectively |
Pseudo-second-order kinetics; Langmuir isotherm; electrostatic interaction |
pH: 4 |
Dose: 0.01 g/25 mL |
λ
max: 520 nm, 440 nm, 490 nm, and 580 nm, respectively |
Magnetic graphene oxide freeze-dried225 |
RhB |
Dose: 0.007 g/50 mL |
126.58 mg g−1 |
Pseudo-second-order kinetics; Langmuir isotherm; electrostatic interaction |
C
0: 30–80 mg L−1 |
T: 25 °C |
λ
max: 553 nm |
Humic acid–Fe3O4226 |
Malachite green (MG) |
Dose: 50 mg/50 mL |
79.3 mg g−1 |
Pseudo-second-order kinetics; Freundlich isotherm; electrostatic attraction, π–π interaction, and hydrogen bonding |
λ
max: 618 nm |
Magnetic graphene oxide227 |
MB and orange G |
Dose: 20 mg/20 mL |
64.23 mg g−1 and 20.85 mg g−1, respectively |
Pseudo-second-order kinetics; Langmuir isotherm; electrostatic interaction |
C
0: 90 and 60 mg L−1 |
Time: 405 min |
λ
max: 667 and 475 nm, respectively |
Fe3O4/GO189 |
MB and MO |
C
0: 1 mg L−1 |
666.7 and 714.3 mg g−1, respectively |
Langmuir isotherm; electrostatic interaction |
pH: 6 |
λ
max: 644 and 466 nm, respectively |
|
Magnetic-based metal oxides |
Fe3O4/CeO2210 |
Azo dye (Acid Black 210 (AB210)) |
Dose: 50 mg/50 mL |
93.08 mg g−1 |
Pseudo-second-order kinetics; Langmuir isotherm; chemisorption |
C
0: 20–400 mg L−1 |
λ
max: 461 nm |
Iron oxide–alumina216 |
CR |
pH: 7 |
416.66 mg g−1 |
Pseudo-second-order kinetics; Freundlich isotherm; multilayer adsorption |
Fe–Mn–Zr metal oxide217 |
MO and eosin yellow (EY) |
Time: 62 min |
196.07 and 175.43 mg g−1, respectively |
Pseudo-second-order kinetics; Langmuir isotherm; surface adsorption and pore diffusions |
Dose: 0.45 g L−1 |
C0 (MO): 11 mg |
L−1, C0 (EY): 25 mg L−1 |
λ
max: 464 and 517 nm, respectively |
TiO2/SiO2/Fe3O4 hollow magnetic microspheres228 |
MB |
C
0: 20 mg L−1 |
147 mg g−1 |
Pseudo-second-order kinetics; Langmuir isotherm; electrostatic interaction |
Dose: 0.5 g L−1 |
Time: 50 min |
Al cation-doped MgFe2O4229 |
MO |
Time: 120 min |
274.6 mg g−1 |
Pseudo-second-order kinetics; Langmuir isotherm; electrostatic interaction |
Dose: 1 g L−1 |
CNT/MgO/CuFe2O4230 |
Methyl violet dye and Nile blue dye |
Dose: 1 g L−1 |
36.46 mg g−1 and 35.60 mg g−1, respectively |
Pseudo-second-order kinetics; Langmuir isotherm; electrostatic interaction |
C
0: 10 mg L−1 |
λ
max: 584 and 638 nm, respectively |
Magnetic Fe3O4@UiO-66231 |
MB and MO |
Dose: 20 mg/100 mL |
205 mg g−1 and 244 mg g−1, respectively. |
Pseudo-second-order kinetics; Langmuir isotherm; electrostatic attraction and π–π stacking interactions |
C
0: 20 mg L−1 |
λ
max: 631 and 463 nm, respectively |
MgFe2O4213 |
Methyl green (MG) and basic fuchsin (BF) |
C
0: 30 mg L−1 |
1.231 and 2.545 mg g−1, respectively |
Pseudo-second-order kinetics; Langmuir isotherm (MG) and Freundlich isotherm (BF); electrostatic interaction (MG) and hydrogen-bond interaction (BF) |
Dose: 0.8 g L−1 |
λ
max: 632 and 541 nm, respectively |
MgFe2O4232 |
MO |
C
0: 100 mg L−1 |
181.34 mg g−1 |
Pseudo-second-order kinetics; Freundlich isotherm; electrostatic forces |
Dose: 1 g L−1 |
λ
max: 464 nm |
|
Magnetic-based bio-adsorbents |
Fe3O4–wheat straw214 |
MB |
Dose: 0.01–0.2 g/100 mL |
1374.6 mg g−1 |
Pseudo-second-order kinetics; Freundlich isotherm; complexation formation and ion exchange |
pH: 7 |
λ
max: 668 nm |
Fe3O4-loaded protonated amine-modified hydrochar233 |
MB and MO |
Dose: 40 mg/50 mL |
148.84 mg g−1 (pH 11) and 202.02 mg g−1 (pH 5.0), respectively |
Pseudo-second-order kinetics; Langmuir isotherm; electrostatic interaction |
C
0: 100 mg L−1 |
T: 303 K |
λ
max: 664 and 464 nm, respectively |
|
Magnetic-based polymers |
Core@double-shell structured magnetic halloysite nanotube218 |
MB |
C
0: 70–130 mg L−1 |
714.29 mg g−1 at 318.15 K |
Pseudo-second-order kinetics; Langmuir isotherm; complexes formation, electrostatic interaction and π–π stacking interaction |
T: 298 K |
Time: 3 h |
Chitosan–Fe(III) hydrogel234 |
C. I. Acid Red 73 (AR 73) |
pH: 12 |
294.5 mg g−1 |
Pseudo-second-order kinetics; Langmuir–Freundlich isotherm; chemisorption |
Time: <10 min |
C
0: 50 mg L−1 |
Fe3O4@C@polyaniline trilaminar core–shell235 |
MO |
Dose: 8 mg/20 mL |
120.2 mg g−1 |
Pseudo-second-order kinetics; Langmuir isotherm; chemisorption followed by electrostatic attraction and π–π interaction |
C
0: 60 mg L−1 |
Fe3O4@sodium alginate–Fe(III) polymer gel beads236 |
CR and Direct red 23 (DR 23) |
Time: 30 min for CR and 60 min for DR 23 |
3333 and 1429 mg g−1, respectively |
Pseudo-second-order kinetics; Langmuir isotherm; electrostatic adsorption, hydrogen bonding, and surface complexation besides van der Waals forces |
λ
max: 498 nm and 502 nm, respectively |
Magnetic halloysite-based molecularly imprinted polymer237 |
Sunset yellow (SY) |
pH: 2 |
46.43 μmol g−1 |
Pseudo-second-order kinetics; Langmuir isotherm; electrostatic attraction |
Dose: 0.005 g/0.01 L |
λ
max: 482 nm |
Sulfonic acid-modified polyacrylamide magnetic composite238 |
Crystal violet (CV) and MB |
pH: 10 |
2106.37 mg g−1 and 1462.34 mg g−1, respectively. |
Pseudo-second-order kinetics; Langmuir isotherm; electrostatic interaction, hydrogen bonding, and hydrophobic interaction |
C
0: 100–4000 mg L−1 |
Dose: 0.5 g L−1 |
Time: 360 min |
Fe3O4/graphite oxide nanosheet/citric acid-crosslinked β-cyclodextrin polymer239 |
MB |
C
0: 50 mg mL−1 |
173 mg g−1 |
Pseudo-first-order or the intraparticle diffusion model; Sips isotherm; electrostatic attraction, the Lewis acid–Lewis base interaction, the host–guest interaction, and the π–π interaction |
Dose: 10 mg/25 mL |
Chitosan-fly ash/Fe3O4240 |
Reactive Orange 16 (RO16) |
pH ∼ 4 |
66.9 mg g−1 |
Pseudo-second-order kinetics; Freundlich isotherm; electrostatic attraction, dipole–dipole hydrogen bonding interactions, H-bonding, and n–π stacking interactions |
Dose: 0.08 g |
T: 303 K |
Time: 55 min |
λ
max: 493 nm |
|
Miscellaneous magnetic-based materials |
Magnetic chelated silica particles241 |
Naphthol blue black (NBB) and Eriochrome blue black R (EBBR) |
C
0: 0.1 mmol L−1 |
3.76 and 1.83 mmol g−1 |
Pseudo-second-order kinetics; Langmuir isotherm; electrostatic attraction |
λ
max: 618 nm and 569 nm, respectively |
Ionic liquid grafted-magnetic nanoparticles242 |
Reactive Black 5 |
C
0: 100 mg L−1 |
161.29 mg g−1 |
Pseudo-second-order kinetics; Langmuir isotherm; electrostatic attraction and hydrogen bonding |
Magnetic silica nanocomposite-immobilized Pseudomonas fluorescens243 |
Rhodamine B |
C
0: 50 mg L−1 |
229.6 mg g−1 |
Pseudo-second-order kinetics; Langmuir isotherm; electrostatic attraction and hydrogen bonding |
Dose: 1 g L−1 |
pH: 6 |
λ
max: 558 nm |
Water-based ferro fluid244 |
Ponceau S |
Ferrofluid dose: 20 mg mL−1 |
140.26 mg g−1 |
Pseudo-second-order kinetics; Langmuir isotherm; electrostatic interaction |
Clay/starch/Fe3O4245 |
Methyl violet (MV) |
C
0: 10 mg L−1 |
29.67 mg g−1 |
Pseudo-second-order kinetics; Freundlich isotherm; electrostatic interactions |
Dose: 1.5 g L−1 |
pH 9 |
Time: 150 min |
T: 298 K |
Activated carbon/bentonite/Fe3O4246 |
Reactive Red 198 |
Dose: 2 g L−1 |
4.86 mg g−1 |
Pseudo-second-order kinetics; Langmuir isotherm |
C
0: 5 mg L−1 |
pH: 8 |
Time: 50 min |
Amine/Fe3O4-resin212 |
Anionic dye: MO, Reactive Brilliant Red K-2BP, and Acid Red 18 |
Time: 180 min |
RBR: 101.0 mg g−1 |
Pseudo-second-order kinetics; Langmuir isotherm; chemisorption involved ion exchange |
T: 25 °C |
MO: 222.2 mg g−1 |
pH 2.5, 5.5, and 7.0 respectively |
AR: 99.4 mg g−1 |
|
Non-magnetic oxide nanocomposites |
Co/Cr-codoped ZnO219 |
MO |
Dose: 10 mg |
1057.90 mg g−1 |
Pseudo-second-order kinetics; Langmuir isotherm; chemisorption and electrostatic interaction. |
Time: 120 min |
λ
max: 200 nm |
ZnO-Al2O3220 |
CR |
C
0: 50 mg L−1 |
397 mg g−1 |
Pseudo-second-order kinetics; Langmuir isotherm; chemisorption |
Dose: 10 mg/100 mL |
Time: 12 h |
T: 303 K |
Mesoporous MgO247 |
CR |
C
0: 250 mg L−1 |
689.7 mg g−1 |
Pseudo-second-order kinetics; Langmuir isotherm; electrostatic interaction. |
Dose: 0.02 g/50 mL |
Time: 60 min |
MgO/SiO2248 |
CR |
Dose: 10 mg/50 mL |
∼4000 mg g−1 |
Pseudo-second-order kinetics; Langmuir isotherm; electrostatic attractions and surface complexation |
C
0: 100 mg L−1– |
1000 mg L−1 |
T: 25 °C |
λ
max: 498 nm |
MgO–graphene oxide249 |
CR |
C
0: 50 mg L−1 |
237 mg g−1 |
Pseudo-second-order kinetics; Langmuir isotherm; electrostatic and π–π interactions |
Dose: 10 mg/50 mL |
Ni–MgO221 |
Methyl blue |
C
0: 375 mg L−1 |
367 mg g−1 |
Langmuir isotherm; electrostatic attraction and surface complexation |
Dose: 0.1–0.5 g L−1 |
λ
max: 600 nm |
NiO–Al2O3222 |
CR |
C
0: 10–100 mg L−1 |
357 mg g−1 |
Pseudo-second-order kinetics; Langmuir isotherm; positive negative charge attraction |
Dose: 10 mg/50 mL |
Time: 12 h |
T: 303 K |
pH: 7 |
ZnV2O4 hollow spheres223 |
MB |
C
0: 10 mg L−1 |
96% and 153.14 mg g−1 |
Pseudo-second-order kinetics; Freundlich isotherm; electrostatic attraction |
Time: 40 min |
λ
max: 664 nm |
Table 6 Metal–organic frameworks (MOFs) for dye removal
MOF |
Dyes |
Experimental conditions |
Adsorption capacity/removal efficiency |
Adsorption kinetics, isotherm, and mechanisms |
C
0: initial dye concentration; T: temperature; and λmax: maximum wavelength detected for the analysis of dye. |
MIL-53(Al)-NH2256 |
MB and MG |
C
0: 5 mg L−1 |
208.3 mg g−1 and 164.9 mg g−1, respectively |
Langmuir (R2 ∼ 0.99) and Freundlich isotherm (R2 ∼ 0.97); electrostatic attraction or repulsion. |
Dose: 10 mg/100 mL |
λ
max: 663 and 619 nm, respectively |
MIL-Ti257 |
Basic Red 46, basic blue 41, and MB |
Time: 30 min |
1250, 1428, and 833 mg g−1, respectively |
Pseudo-second-order kinetics; Langmuir isotherm; π–π interaction, hydrogen bonding, electrostatic interactions, and acid–base interactions |
pH: 6.3 |
λ
max: 530, 605, and 665 nm, respectively |
Porous MOF material-based on chromium-benzene dicarboxylate258 |
MO |
C
0: 30–50 mg L−1 |
194 mg g−1 |
Pseudo-second-order kinetics; Langmuir isotherm; electrostatic interaction |
λ
max: 464 nm |
MIL-100 (Fe,Cr)259 |
MO and MB |
C
0: 400 mg L−1 |
MIL-100(Cr): MO 211.8 mg g−1 |
Pseudo-second-order kinetics; Langmuir isotherm; electrostatic interaction |
MIL-100(Fe): MO 1045.2 mg g−1 |
MIL-100(Cr): MB 645.3 mg g−1 |
MIL-100(Fe): MB 736.2 mg g−1 |
(Fe3O4/Cu3(BTC))260 |
MB |
C
0: 300 mg L−1 |
245 mg g−1 |
Pseudo-second-order kinetics; Freundlich isotherm; electrostatic interaction and π–π stacking interaction and/or hydrophobic interactions |
λ
max: 660 nm |
Zeolitic imidazolate framework (ZIF) ZIF-8, ZIF-8@CNT, ZIF-8@GO261 |
MG |
Dose: 0.062, 0.031, and 0.018 g L−1 ZIF-8, ZIF-8@CNT, ZIF-8@GO, respectively. |
ZIF-8: 1667 mg g−1 |
Pseudo-second-order kinetics; Langmuir isotherm; electrostatic interaction |
Time: 240 min |
ZIF-8@CNT: 2034 mg g−1 |
C
0: 50 mg L−1 |
ZIF-8@GO: 3300 mg g−1 |
λ
max: 618 nm |
|
Zirconium-based MOFs262 |
CV and RhB |
C
0: 10 mg L−1 |
63.38 mg g−1 and 67.73 mg g−1, respectively |
Pseudo-second-order kinetics; chemisorption |
pH: 11 and 7, respectively. |
λ
max: 585 and 554 nm, respectively. |
Table 7 Polymers and their nanocomposites for dye removal
Adsorbent |
Dyes |
Experimental conditions |
Adsorption capacity/removal efficiency |
Adsorption kinetics, isotherm, and mechanisms |
C
0: initial dye concentration; T: temperature; and λmax: maximum wavelength detected for the analysis of dye. |
Pure polyaniline and polypyrrole |
PANI and PPY61 |
CR |
C
0: 20 mg L−1 |
250.01 and 66.66 mg g−1, respectively |
Pseudo-second-order kinetics; Langmuir isotherm; chemisorption |
pH: 6.55 |
T: 298 K |
Dose: 0.4 g L−1 and 1.73 g L−1, respectively |
λ
max: 495 nm |
PPY and PANI272 |
Azo dyes: sunset yellow and CR |
pH: 2 |
212.1 and 147 mg g−1, respectively |
π–π electron donor–acceptor interaction and electrostatic attraction |
λ
max: 470 and 497 nm, respectively |
PANI powder273 |
MB |
C
0: 3.9 mg L−1 |
13.854 mg g−1 |
Pseudo-second-order kinetics; Langmuir isotherm; chemisorption. |
λ
max: 664 nm |
PANI274 |
MO |
pH: 3 |
92% |
|
Time: 5 h |
λ
max: 498 nm |
PANI HNTs275 |
MB and acid green |
pH: 3–11 |
69.44 and 57.87 mg g−1, respectively |
Pseudo-second-order kinetics; Langmuir isotherm; chemisorption involved electrostatic interaction |
λ
max: 664 nm and 642 nm, respectively |
|
Polyaniline and polypyrrole based nanocomposites |
PANI/GO and PANI/RGO280 |
MB |
Time: 270 min |
14.2 and 19.2 mg g−1, respectively |
Pseudo-first-order kinetics; Langmuir isotherm; the presence of imine groups and π–π stacking interactions |
C
0: 50 mg L−1 |
λ
max: 660 nm |
PANI-modified rice husk composite281 |
Acid red 18 |
C
0: 40–120 mg L−1 |
100 mg g−1 |
Pseudo-second-order kinetics; Langmuir isotherm; chemisorption |
λ
max: 523 nm |
PANI/Fe3O4263 |
Acid Blue 40 |
C
0: 50 mg L−1 |
216.9 mg g−1 |
Pseudo-second-order kinetics; Freundlich isotherm; electrostatic interaction and H-bond formation |
λ
max: 620 nm |
Alpha-cellulose/magnetite/PPY282 |
Reactive Black 5 |
pH: 3 |
62.31 mg g−1 |
Langmuir isotherm; π–π* interactions, hydrogen bond formation |
Starch/polyaniline278 |
Reactive Black and Reactive Violet 4 |
λ
max: 597 and 577 nm, respectively |
811.30 and 578.39 mg g−1, respectively |
Pseudo-second-order kinetics; Toth model; electrostatic interaction |
pH: 3 |
PANI/TiO2283 |
MB |
Dose: 2 g L−1 |
458.10 mg g−1 |
Pseudo-second-order kinetics; Temkin isotherm; chemisorption involves membrane diffusion, and intraparticle diffusion |
C
0: 400 mg L−1 |
λ
max: 664 nm |
PANI/Starch279 |
MB |
C
0: 1–2 × 10−5 M |
6.8 × 106 mol g−1 |
Electrostatic interaction |
Dose: 1.2 g L−1 |
|
Chitosan-based adsorbents |
Chitosan nanoparticles immobilized on a fibrous carrier297 |
Direct blue-86, photosens, theraphthal, and C.I. Reactive Blue 21 |
pH: 4–6 |
1097 ± 55, 1049 ± 43, 367 ± 22, and 296 ± 18 mg g−1, respectively |
Pseudo-second-order kinetics; Langmuir isotherm; Ion-exchange processes and hydrophobic binding |
C
0: 10–130 mg L−1 |
λ
max: 665, 679, 675, and 664 nm, respectively |
Chitosan-based magnetic-adsorbent64 |
Acid orange 7 |
T: 298 K |
45.019 mg g−1; 98.01% |
Pseudo-second-order kinetics; Sips and Redlich–Peterson isotherm; ion-exchange process |
pH: 6.2 ± 0.2 |
Dose: 2 g L−1 |
C
0: 50 mg L−1 |
λ
max: 485 nm |
Fe2O3–chitosan–bamboo sawdust298 |
Bromothymol blue |
Time: 30 min |
217.39 mg g−1 |
Pseudo-second-order kinetics; Langmuir isotherm; liquid-film and intraparticle diffusion mechanisms |
Dose: 0.5 g L−1 |
pH < 7 |
λ
max: 453 nm |
Chitosan–ethylenediaminetetraacetic acid–magnetic graphene oxide301 |
RhB |
Dose: 0.07–0.18 g L−1 |
1085.3 mg g−1 |
Pseudo-second-order kinetics; Langmuir isotherm; chemisorption and physisorption |
C
0: 50–250 mg L−1 |
λ
max: 554 nm |
Chitosan hydrogel/SiO2 and chitin hydrogel/SiO2299 |
Remazol black B, erythrosine B, neutral red, and gentian violet |
C
0: 0.05–100 mmol L−1 |
0.081 mmol g−1, 0.08 mmol g−1, 0.88 mmol g−1, and 0.17 mmol g−1, respectively for chitosan hydrogel/SiO2, whereas, 0.0062 mmol g−1, 0.15 mmol g−1, 1.06 mmol g−1, and 0.14 mmol g−1, respectively for chitin hydrogel/SiO2 |
Freundlich isotherm; physical adsorption |
|
Miscellaneous polymer adsorbents |
Polyvinyl alcohol300 |
Bromothymol blue (BTB) and MB |
pH: 6 |
276.2 mg g−1 and 123.3 mg g−1, respectively |
Pseudo-second-order kinetics; Langmuir isotherm; chemisorption |
Time: 10 min |
98.65% and 61.32%, respectively |
λ
max: 616 and 664 nm, respectively |
|
Poly(phenylenediamine) grafted electrospun carbon nanofibers63 |
Coomassie brilliant blue (CBB) |
C
0: 100 mg L−1 |
141 mg g−1 |
Elovich kinetic; Redlich–Peterson isotherm; electrostatic interaction, π–π interactions, and intermolecular H-bonding |
Dose: 5 mg/10 mL |
Time: 5 h |
pH: 3 |
λ
max: 555 nm |
The possible responsible mechanisms (i.e., surface complexation, electrostatic interaction, and van der Waals force) and processes (i.e., surface diffusion and intraparticle pore diffusion) for the adsorption of dyes are discussed and shown in Tables 2–7. The detection wavelengths for the targeted dyes in the reported studies are also mentioned in Tables 2–7, which may be helpful for readers to measure the concentrations of these dyes. In the following sections, the above-mentioned adsorbents are discussed in detail. The classes of dye molecules, their ecotoxic effects, adsorptive removal of dyes using various classes of adsorbents together with their sub-categories, the critical influencing factors, and responsible adsorption mechanisms are displayed as a flow chart in Fig. 4.
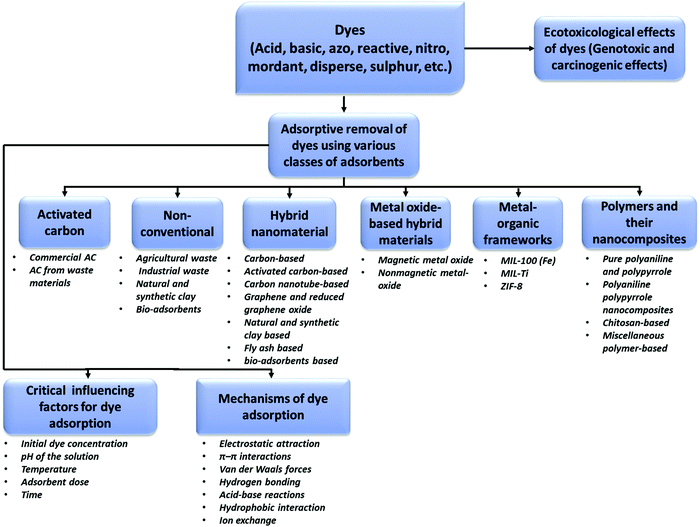 |
| Fig. 4 Flow chart showing the classes of dye molecules, their ecotoxic effects, removal using different classes of adsorbents together with their sub-categories, critical influencing factors, and probable adsorption mechanisms. | |
4.1. Activated carbon
Activated carbon-based adsorbents are widely studied in the field of adsorption owing to their robust chemical stability, low density, structural diversity, and suitability for field-scale applications. These unique characteristics generally originate from their internal pore morphology, surface characteristics, porosity, pore volume, chemical structure, and presence of functional groups from their source material, including their activation.102–104 The commercial activated carbon and activated carbon synthesized from various waste materials are discussed in the subsequent section.
4.1.1 Commercial activated carbon.
Researchers have reported the use of various commercial activated carbons as adsorbents for the separation of different dyes from wastewater.62,105,106 For instance, Malik (2004) developed an effective carbon-based adsorbent from mahogany sawdust and directly applied it to adsorb dyes. The experimental data well correlated with the Langmuir model, exhibiting an adsorption capacity of 518 and 327.9 mg g−1 for Direct Blue 2B and Direct Green B dyes, respectively.105 In another study, Mohammadi et al. reported the removal of an anionic dye (i.e., MO) using mesoporous carbon CMK-3 (i.e., carbon material kinetic-3) as an adsorbent and observed the extraction of the dye within 60 min. Further, their studies indicated that acidic media facilitated the removal of the dye more than basic media. An increase in the initial dye concentration also has a positive effect on the adsorption capacity. The analyzed equilibrium data well fitted the Langmuir isotherm, following monolayer adsorption (adsorption capacity at 25 °C: 294.1 mg g−1).62 In another study, Djilani et al. used activated carbon prepared from apricot stones and achieved an adsorption capacity of 36.68 and 32.25 mg g−1 for MB and MO at a pH of 4.85 and 4.87, respectively. The corresponding adsorption data was found to be well correlated with the Langmuir isotherm.106 In another study, Rahman (2021) used activated carbon synthesized from red oak (i.e., Quercus rubra) for the adsorption of MB and observed adsorption efficiency of 97.18%.107 According to Giannakoudakis et al., the adsorption of Reactive Black 5 dye on the three different forms of commercials activated carbon, namely, Norit Darco 12 × 20 (DARCO), Norit R008 (R008), and Norit PK 1-3 (PK13) followed the Langmuir, Freundlich, and Langmuir–Freundlich models, achieving an adsorption capacity of 348, 527, and 394 mg g−1 in 24 h by the corresponding commercial activated carbon as adsorbents, respectively.108 Activated carbon was also produced from spent tea leaves (STAC) to remove malachite green (MG), which showed an adsorption capacity of 256.4 mg g−1 at 45 °C. These studies showed an increment in the adsorption of MG from aqueous solution up to pH 4 and then became more or less unaltered at higher pH.109
4.1.2 Activated carbon from waste materials.
Different waste materials such as lemongrass leaf, rice husk, orange peel, and spent tea leaves have been reported as important sources for deriving activated carbon, which can be effectively applied as adsorbents in dye remediation.110–114 For example, Ahmad et al. utilized lemongrass leaf-based activated carbon to remediate methyl red from contaminated water. Their findings showed an optimum dye adsorption capacity of 76.923 mg g−1 at pH 2 within 5 h. An increase in the adsorption rate of methyl red dye was mainly observed with an increase in temperature, dye concentration, and contact time. Their thermodynamic study indicated that the adsorption of methyl red dye is endothermic and follows a physisorption process.110 In addition, Ding et al. treated rhodamine B using activated carbon obtained from treated rice husk and achieved its equilibrium removal (478.5 mg g−1) within 5 h. The initial solution pH was found to have an insignificant effect on the adsorption of rhodamine B on the activated carbon.111 In another work, Lam et al. reported an adsorption capacity of 28.5 mg g−1 while investigating the adsorption of MG cationic dye using activated carbon prepared from orange peel.112
Jawad et al. prepared sulfuric acid-treated activated carbon derived from coconut leaves, exhibiting rough and irregular surfaces along with cavities, which was found to be a very effective adsorbent for MB dye (adsorption capacity: 149.3 mg g−1). It is also found that the adsorption capacity increased with an increase in the initial concentration of MB.115 In another study, chemical activated carbon (ACC) prepared from jute sticks (morphological image is shown in Fig. 5) showed an adsorption capacity of 480 mg g−1 for brilliant green dye.116 Guava leaf-based activated carbon exhibited a maximum adsorption capacity of 39.7 mg g−1 to remove CR dye.117 Low-cost activated carbon derived from Brazilian agriculture waste was also used for the adsorption of dyes, including Basic Blue 26, Basic Green 1, Basic Yellow 2, and Basic Red 1, which exhibited an adsorption capacity in the range of 10–76 mg g−1, 26–83 mg g−1, 27–83 mg g−1, and 21–70 mg g−1, respectively.118 The adsorption performance of commercial activated carbon and activated carbon derived from various waste materials for the treatment of dye-contaminated water is presented in Table 2.
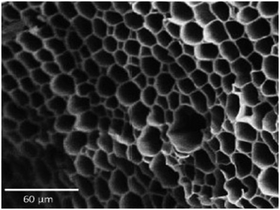 |
| Fig. 5 Morphological image of chemical activated carbon (ACC) prepared from jute sticks [Reprinted with permission from ref. 116. Copyright 2010, Elsevier]. | |
4.2. Non-conventional adsorbents
In recent years, several non-conventional adsorbents have been gaining substantial attention as potential economic alternatives of costly adsorbent materials to remove toxic pollutants.120 This includes the utilization of abundantly available agricultural, industrial, natural resources, bio wastes, etc. as waste materials. These waste materials prior to their application as adsorbents are subjected to various processes such as chemical treatment, conversion to powder form, and decomposition.60,121–123 Considering this, different waste materials to adsorb toxic dyes from contaminated water are described below.
4.2.1 Agricultural waste materials.
Agricultural waste materials, such as raw maize cob, exhausted coffee ground powder, saw-dust, black cumin, neem leaf, pineapple leaf, and pine tree leaves, have been used by many researchers in dye remediation of contaminated water.60,121–125 Abubakar and Ibrahim (2019) used raw maize cob for the adsorption of bromophenol blue (96.5%) and bromothymol blue (94.4%) present in wastewater at the equilibrium time of 125 and 110 minutes, respectively. The effect of increasing the initial dye concentration on dye adsorption showed positive effects, and the dye adsorption followed the Temkin isotherm model.122 In another work, the adsorption of rhodamine B and rhodamine 6G on exhausted coffee ground powder achieved an adsorption capacity of up to 5.3 and 17.4 μmol g−1, respectively.60 It was proposed that electrostatic, hydrophobic, and intermolecular interactions account for the adsorption of Rhodamine dye onto the adsorbent surface (Fig. 6). Sodium hydroxide-treated sawdust exhibited an adsorption capacity of 55.86 mg g−1 for brilliant green dye in 3 h.121 In a study by Siddiqui et al., an antimicrobial Nigella sativa seed-based manganese dioxide/black cumin (MnO2/BC) nanocomposite was used for the adsorption of MB (adsorption capacity: 185.19 mg g−1 at pH 7.0 and 318 K). The process of adsorption was endothermic and best described by the Langmuir isotherm. The adsorption mechanism involved hydrogen bonding and electrostatic interactions of MB onto the surface of MnO2/BC.123 Pineapple leaf powder,125 pine tree leaves,126 and Platanus orientalis leaf powder127 as adsorbents achieved the maximum removal capacities of 48.72, 71.94, and 114.94 mg g−1, corresponding to the contact time of 150, 120, and 70 min in the removal of Basic green 4, Basic red 46, and MB dye, respectively. Neem leaf powder was also used for the adsorption of brilliant green dye,124 which showed 0.554 mmol g−1 adsorption capacity within 240 min. Microwave-assisted spent tea leaves exhibited a maximum adsorption capacity of 242.72 mg g−1 for Eriochrome black-T adsorption in a contact time of 24 h.113
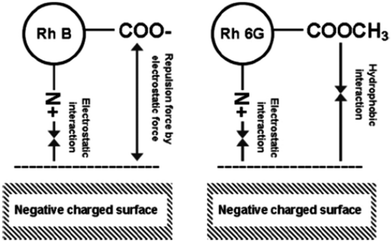 |
| Fig. 6 Possible adsorption mechanisms on the surface of exhausted coffee ground powder [Reprinted with permission from ref. 60. Copyright 2017, Elsevier]. | |
4.2.2 Industrial waste materials.
Various industrial wastes, including fly ash, slurry, and ceramic wastes, have been regularly used as adsorbents for dye removal from contaminated water.128–131 Jain et al. used steel and fertilizer industrial waste as an adsorbent material for the adsorption of ethyl orange, metanil yellow, and Acid Blue 113 dyes. In this process, they achieved an adsorption capacity of 198, 211, and 219 mg g−1, respectively.128 Coal fly ash exhibited maximum removal efficiencies of more than 90% and up to 85% in 24 h for MB and crystal violet dyes, respectively.129 Bhatnagar and Jain (2005) used carbonaceous slurry waste as an adsorbent to remove RhB and Bismark Brown R dye. They achieved an adsorption capacity of 91.1 and 85 mg g−1 at a contact time of nearly 25 min for RhB and Bismarck Brown R dye, respectively.130 Ceramic adsorbents derived from industrial waste coal gangue achieved an adsorption capacity of 1.044 and 2.170 mg g−1 for Cationic Red X-5GN and Cationic Blue X-GRRL dyes at a contact time of 180 min, respectively.131 The possible mechanisms displayed in Fig. 7 suggest electrostatic attraction, H-bonding, etc., playing an essential role in the adsorption of the X-5GN and X-GRRL dyes. Furthermore, industrial waste shells of eggs showed an adsorption capacity of 94.9 and 49.5 mg g−1 in removing MB and CR, respectively.132
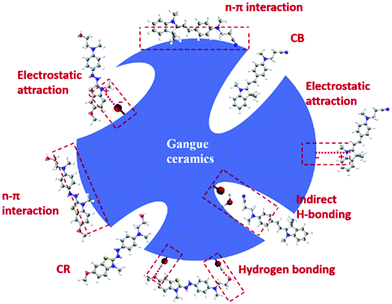 |
| Fig. 7 Possible adsorption mechanisms of adsorption of cationic dyes by gangue ceramics [Reprinted with permission from ref. 131. Copyright 2019, Elsevier]. | |
4.2.3 Natural and synthetic clay.
The easy availability, low cost, high porosity, high potential for ion exchange, and non-toxicity of several natural and synthetic clays have resulted in their significant use as adsorbents for dye removal from aqueous solution.133–136 For example, sulfuric acid-treated coal bearing kaolinite achieved a maximum adsorption capacity of MB dye corresponding to 101.5 mg g−1.133 In another work, the adsorptive behavior of RhB on sodium montmorillonite clay showed an adsorption capacity of 42.19 mg g−1.137 The adsorption process involved electrostatic attraction between the negatively charged adsorbent surfaces and positively charged cationic dye. Santos and Boaventura (2008) used sepiolite to remove Basic Red 46 and Direct Blue 85 dyes, achieving an adsorption capacity of 108 and 454 mg g−1, respectively.134 Acid-treated palygorskite was employed to remove crystal violet, cationic light yellow (7GL), MB, and MO dyes, exhibiting adsorption capacities of 223.43, 290.86, 86.53, and 276.11 mg g−1, respectively.136 Palygorskite modified by 3-aminopropyl triethoxysilane was successfully employed to remove reactive red 3BS, reactive blue KE-R, and reactive black GR dyes in 20 min with adsorption capacities of 34.23, 38.59, and 60.13 mg g−1, respectively.135 Kismir and Aroguz (2011) reported an adsorption capacity of 1.18 mg g−1 for the adsorption of brilliant green dye on Saklikent mud as an adsorbent.138 Flower-like139 and hollow LDH140 exhibited an adsorption capacity of 500.6 and 210 mg g−1 in less than 10 min for methyl orange, respectively.
4.2.4 Bio-adsorbents.
Significant advancement has been made in the field of dye removal from polluted water using biosorbents, such as Spirulina platensis, Penaeus indicus shrimp, cellulose, Ganoderma lucidum, wheat flour, and Graham flour.141–146 According to Dotto et al., Acid Blue 9 and FD&C Red No. 40 were effectively adsorbed on the biosorbent synthesized from Spirulina platensis. The scanning electron microscopy (SEM) image of the Spirulina platensis biomass in Fig. 8 shows the presence of pores and cylindrical filaments on its surface, revealing the adsorption capability of Spirulina platensis. The experimental analysis showed a biosorption capacity of 400.3 and 1653.0 mg g−1 for FD&C Red No. 40 and Acid Blue 9 dye, respectively, at initial solution pH of 2 and contact time of 100 min.141 The shell of Penaeus indicus shrimp was also found to be an effective adsorbent for Acid Blue 25, and dye biosorption fitted well with the pseudo-second-order model.142 The optimum condition of this dye adsorption corresponds to pH 2 and 0.1 g L−1 dose, resulting in an adsorption capacity of 1093 mg g−1. The adsorption capacities of 2.197, 2.120, 2.038, and 1.480 mg g−1 were achieved on neem sawdust for the removal of crystal violet, MB, MG, and RhB dyes, respectively, from contaminated water in 30 min.147 The adsorption capacities of 1201 and 1070 mg g−1 were observed within 3 h on cellulose nanocrystal-reinforced keratin for the adsorption of Reactive Black 5 and Direct Red 80, respectively.143 The adsorption process of both the dyes was well correlated with the Langmuir isotherm. Wu et al. used the spent substrate of Ganoderma lucidum for removing MG, safranine T, and MB dyes and observed the adsorption capacities of 40.65, 33, and 22.37 mg g−1, respectively, in 4 h.144 The adsorption performances of various non-conventional adsorbents are listed in Table 3.
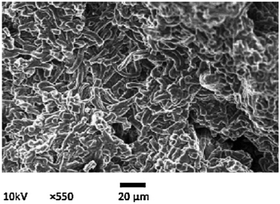 |
| Fig. 8 Scanning electron microscopy image of Spirulina platensis biomass [Reprinted with permission from ref. 141. Copyright 2012 Elsevier]. | |
4.3. Hybrid nanomaterials
Nanomaterials have been extensively used for water treatment applications because of their enhanced surface area and high adsorption-to-mass ratio. Accordingly, the combination of two or more nanomaterials, which is referred to as hybrid nanomaterials, exhibits multi-functionalities found to be very effective to remove dyes from contaminated water, as described below.155
4.3.1 Carbon-based hybrid nanocomposite.
Carbon-based hybrid nanocomposites are associated with easy synthesis, cost-effectiveness, availability, non-toxicity, high porosity, etc., similar to other carbon-based nanocomposites. Ultrafine nickel/carbon (dose: 2 g L−1) on treatment with RhB and MB showed an adsorption capacity of 5.269 and 7.415 mg g−1, respectively.156 Manippady et al. investigated the adsorption of CR and MB dye onto iron–carbon hybrid magnetic nanosheets and achieved an adsorption capacity of 531.9 and 185.2 mg g−1, respectively, in 24 min.157 In another study, a porous silicon–carbon–nitrogen (Si–C–N) hybrid was employed to remove methyl blue and acid fuchsin dyes, achieving an adsorption capacity of 1327.7 and 1084.5 mg g−1, respectively.158 The possible mechanism displayed in Fig. 9 suggests the presence of electrostatic interactions and van der Waals forces between the adsorbent and dye. An Ni/porous carbon nanotube nanocomposite was used to remove MG, CR, RhB, MB, and MO dye, exhibiting adsorption capacities of 898, 818, 395, 312, and 271 mg g−1, respectively.159
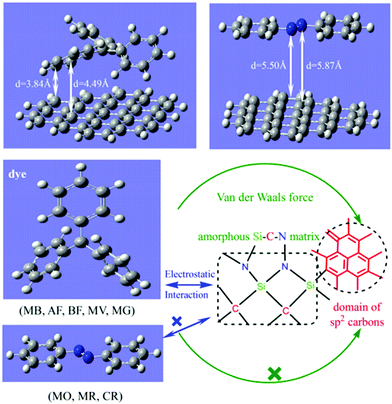 |
| Fig. 9 Adsorption mechanisms for porous Si–C–N hybrid material [Reprinted with permission from ref. 158. Copyright 2015, Nature Research]. | |
4.3.2 Activated carbon-based hybrid nanocomposites.
Activated carbon-based hybrid nanocomposites have been widely used in the purification of contaminated water. Wang et al. observed an adsorption capacity of 416.67 mg g−1 (303 K) using activated carbon aerogel immobilized with konjac glucomannan for the removal of MB.160 In another study, ZnO nanoparticles loaded on Parthenium weed activated carbon achieved more than 99% removal of MB in 60 min.161 The adsorption of RhB and Orange G using sulfonic acid-modified activated carbon resulted in an adsorption capacity of 757.6 and 318.5 mg g−1, respectively.162 Gong et al. used activated carbon synthesized from finger citron residue as a new type of adsorbent for the removal of harmful dyes, namely, anionic dyes such as MO and cationic dyes such as MB, from contaminated water, achieving an adsorption capacity of 934.58 (MO) and 581.40 mg g−1 (MB).163
4.3.3 Carbon nanotube-based hybrid nanomaterials.
Recently, carbon nanotube (CNT)-based nanohybrid materials have receive tremendous attention because of their high specific surface area, small sizes, and hollow structures.164,165 According to Gong et al., these hybrids are more efficient for the adsorption of organic contaminants compared to even activated carbon.70 Thus, the unique features of carbon nanotubes have been supplemented in the formation of several nanocomposites for dye removal from contaminated water. CNTs exhibited an adsorption capacity of 44.64 mg g−1 for CI Reactive Red 2 dye.166 Magnetic multi-walled CNT (MMWCNT) exhibited a poor adsorption performance for MB, neutral red, and brilliant cresyl blue dyes.70 In another study, Yao et al. achieved a maximum adsorption capacity of 51.74 mg g−1 MO dye on MMWCNT from wastewater.167 Further, Sui et al. studied the adsorption of MB and MO on a synthesized calcium alginate/MWCNT hybrid and reported the maximum adsorption capacity of 606.1 and 12.5 mg g−1, respectively.168 HNO3/NaClO/MWCNT nanohybrid169 and magnetite/MWCNT170 hybrid materials showed a maximum adsorption capacity of 55 and 48.06 mg g−1 for the removal of bromothymol blue and MB dyes, respectively.
4.3.4 Graphene and reduced graphene oxide nanocomposites.
Graphene oxide (GO) has been used as an adsorbent for dye removal from wastewater, such as Direct Red 81 and Indosol SFGL direct blue,171 crystal violet and methyl orange,172 and methylene blue.173–176 The adsorption mechanism involves strong interactions between graphene oxide (functionalized with hydroxyl and carboxylic groups) and active functional groups present in the dye.171,177 In addition, several studies have also been reported on GO and reduced graphene oxide (rGO)-based nanocomposites for the adsorption of dye from contaminated water. Zheng et al. prepared a 3D hierarchical GO–NiFe layered double hydroxide (LDH) sandwich hybrid as an adsorbent for the removal of CR and MO dye. Fig. 10 shows that the GO–NiFe-LDH is comprised of a hierarchically well-ordered structure, and both sides of GO is fully protected by ultrathin NiFe-LDH nanosheets, resulting in a sandwich-like architecture. The hybrid exhibited higher adsorption phenomena for CR and MO, as evident from the adsorption capacity values of 489 and 438 mg g−1, respectively. This was ascribed to the presence of electrostatic attraction and ion exchange reactions between the dye molecules and hybrid adsorbents.178 In another work, graphene/polyaniline (PANI)/Fe3O4 was used as a nanoadsorbent for the removal of CR from dye contaminated water.179 It showed an excellent adsorption performance (adsorption capacity: 248.76 mg g−1) for CR dye. MB dye (initial concentration: 250 mg L−1) on treatment with GO showed an adsorption capacity of about 714 mg g−1.174 In another work, graphite oxide was used as an adsorbent to separate MB and MG dyes, with maximum adsorption capacities of 351 and 248 mg g−1, respectively.180 Heidarizad and Şengör (2016) used GO/magnesium oxide nanocomposites for the removal of MB dye and achieved an adsorption capacity of 833 mg g−1 in a contact time up to 60 min.181 Investigations have also been reported using a combination of magnetic Fe3O4/carboxylate GO182 and GO/Fe3O4183 nanostructures as adsorbents in dye removal. It was inferred that GO/Fe3O4 and Fe3O4/carboxylate GO achieved complete removal (MB) and maximum adsorption capacity of 36 mg g−1 (MB) and 22.1 mg g−1 (RhB), respectively.
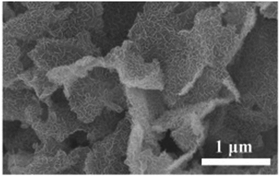 |
| Fig. 10 FE-SEM image of GO–NiFe LDH [Reprinted with permission from ref. 178. Copyright 2019, Elsevier]. | |
Further, GO-based nanocomposites have been reported for dye removal such as porous core–shell graphene/SiO2 nanocomposites for the removal of cationic neutral red dye,184 whereas GO-shielded Mg–Al-LDH,185 Au nanorod-doped Cu2O core–shell nanocube-embedded rGO composite,186 and GO-fabricated Fe–Al bimetal oxide composite187 were reported for the for removal of MB. Several other GO-based nanocomposites have also been reported to adsorb various classes of dyes, for example, the removal of MB using impregnated graphene in porous wood filters,188 Fe3O4/GO composite,189 Fe3O4 nanoparticle-functionalized GO/g-C3N4 nanocomposite,190 and metal ferrite-enabled GO191 and PANI–GO–Fe3O4 hybrid nanocomposite192 for the removal of CR and MO.
4.3.5 Hybrids of natural and synthetic clay.
Hybrids adsorbents comprised of natural and synthetic clay-based materials possess several advantages, such as low cost, non-toxicity, thermal resistance, porosity, ion exchange ability, and the possibility of modification with various functionalities.193 Consequently, nanohybrids of natural and synthetic clay have been harnessed as adsorbents to remove dyes from wastewater. According to Marrakchi et al., the maximum adsorption capacity of 40.97 and 190.97 mg g−1 was achieved in 30 h on cross-linked chitosan/sepiolite clay for MB and reactive orange, respectively.194 The removal efficiency of MO dye on an Mg–Al-layered double hydroxide supported MOF exceeded 99% at the onset of 20 min.195 The adsorptive removal of reactive red, CR, and Acid Red 1on an Mg–Al-layered double hydroxide fitted well with the Langmuir model.196 The layered double hydroxide nanohybrid (Mg–Al–NO3) exhibited a maximum adsorption capacity of 0.8, 1.089, and 1.418 mmol g−1 for the adsorption of amaranth, diamine green B, and brilliant green dyes, respectively.197
4.3.6 Hybrids of fly ash.
Fly ash is generally considered a by-product from coal-based industries and is often used either alone or in combination with other materials as a hybrid adsorbent in water purification.198,199 This is mainly attributed to its high porosity, economic viability, and easy availability.200 The adsorption study on MB dye using fly ash geopolymer monoliths attained a maximum adsorption capacity of 15.4 mg g−1 in 30 h and the absorbent could be reused for up to five cycles.199 Novais et al. reported the adsorption of MB dye on porous biomass fly ash-based geopolymer spheres. The findings showed an adsorption capacity of 79.7 mg g−1 in 30 h and reusability for up to eight cycles.198 Further, Duta and Visa (2015) conducted a study on the adsorption of a mixture of bemacid red and bemacid blue dye on fly ash–TiO2 and noted the adsorption capacity of 4.0 and 1.2 mg g−1, respectively.201 In another study, a maximum adsorption capacity of 24.8 mg g−1 was reported for the adsorption of Orange II dye on Ca(OH)2/Na2FeO4 modified fly ash.202
4.3.7 Hybrids of bio-adsorbents.
Bio-adsorbents can be easily modified and blended with other components, making them suitable as adsorbents for the removal of dyes from contaminated water. Cross-linked beads of an activated oil palm ash zeolite/chitosan composite showed an adsorption capacity of 199.2 and 270.27 mg g−1 for MB and acid blue dye, respectively.203 Liu et al. reported that cellulose-g-poly(acrylic acid-co-acrylamide) exhibited an adsorption capacity of 1602 and 1814 mg g−1 for of Acid Blue 93 and MB dye, respectively.204 A sulphonated bio-adsorbent from waste hawthorn kernel as adsorbent attained a maximum adsorption capacity of 151.5 mg g−1 for MB dye with a contact time of up to 6 h.205 In another work, an adsorption study was conducted for the removal of MB dye on agricultural waste/GO.206 This study revealed a maximum adsorption capacity of 414.03 mg g−1 (pH = 12) with the successful reuse of the adsorbent for up to five cycles. Further, the dye adsorption was well correlated with the Temkin isotherm. The performance of various hybrid materials as adsorbents for the treatment of dyes is presented in Table 4.
4.4. Metal oxide-based (magnetic and non-magnetic) hybrid materials
In recent years, metal oxide-based nano-adsorbents have been widely applied in wastewater treatment due to their unique attributes such as large surface area, nano-size, high reactivity, high ability to blend, and robust solution mobility.1,208 Considering this, the performance of various metal oxide-based hybrid materials as adsorbents in dye removal is reviewed below.
4.4.1 Magnetic metal oxide nanocomposites.
Magnetic nanomaterials exhibit additional advantages in the separation of the catalyst/adsorbent by applying an external magnetic field.209 Gao et al. used Fe3O4/CeO2 as a magnetic composite for the removal of Acid Black 210. The maximum adsorption capacity (93.1 mg g−1) achieved was six times higher than of the commercial CeO2. The corresponding experimental data fitted well with the Langmuir isotherm.210 Fe3O4 magnetic nanoparticles, due to their large surface-to-volume ratio and pore size, showed an adsorption capacity of 150–600 mg g−1 of Rhodamine 6G in 30 min.211 At room temperature, the adsorption of MO, Reactive Brilliant Red K-2BP, and Acid Red 18 in contaminated water on an amine/Fe3O4-functionalized biopolymer magnetic resin correlated well with the Langmuir adsorption isotherm.212 The corresponding adsorption capacity values were found to be 222.2, 101.0, and 99.4 mg g−1, respectively. This high adsorption capacity was attributed to the presence of amine groups and the enhanced surface area of amine/Fe3O4-resin. In another study, Mg-ferrite magnetic nanoparticles exhibited relatively low adsorption capacity in the removal of methyl green (1.23 mg g−1) and basic fuchsin (2.55 mg g−1).213 NaOH-treated wheat straw impregnated with Fe3O4 nanoparticles achieved a maximum adsorption capacity of 1374.6 mg g−1 in the removal of MB from contaminated water.214 The adsorption process (endothermic) was likely to be dependent on pH and temperature. The adsorption mechanisms were proposed considering the formation of a surface complex and ion exchange between the MB molecules and adsorbent. Further, a γ-Fe2O3 nanoadsorbent exhibited equilibrium adsorption of Acid Red 27 dye within 4 min at a low pH (<5.5), and a decrease in the dye removal efficiency was observed with an increase in temperature.215 The adsorption of Acid Red 27 dye on γ-Fe2O3 followed both the Langmuir and Freundlich isotherms.
Mahapatra et al. reported a maximum adsorption capacity of 416.66 mg g−1 at pH 7 for the adsorptive decolorization of CR dye on an Fe2O3–Al2O3 nanohybrid. This higher adsorption capacity was primarily due to the interaction of the amine functional group of the CR dye molecules with the oxy-hydroxide group of the nanohybrid material.216 An Fe–Mn–Zr metal oxide nanocomposite showed a maximum adsorption capacity of 196.07 and 175.43 mg g−1 for the adsorption of MO and eosin yellow dyes, respectively.217 The saturation magnetization of the adsorbent was found to be enough for its rapid magnetic separation from water. Further, the maximum adsorption capacity of 714.29 mg g−1 with a contact time of 3 h was achieved by a core@double-shell-structured HNTs/Fe3O4/poly(DA + KH550) adsorbent in the removal of MB dye.218
4.4.2 Nonmagnetic metal-oxide nanocomposites.
Various nonmagnetic oxide hybrid nanomaterials have been applied as adsorbents in the removal of dyes from the contaminated water. According to Li et al., the adsorption capacity of MO on nano-dimensional Co/Cr-codoped ZnO was 1057.9 mg g−1 due to its high specific surface area and positive charge on its surface.219 Lei et al. noted a maximum adsorption capacity of 397 mg g−1 on ZnO–Al2O3 for the removal of CR dye in 12 h. This adsorbent consisted of microspheres a diameter in the range of 12–16 μm, which were assembled by nanosheets with a thickness of nearly 60 nm.220 The maximum adsorption capacity of 367 mg g−1 for methyl blue dye on Ni–MgO hybrid is attributed to the hydrogen bonding between the N-atoms (which have high electron affinity and smaller atom radius) of methyl blue and OH group on the surface of MgO.221 According to Lei et al., a maximum adsorption capacity of 357 mg g−1 was achieved in 12 h for CR dye on NiO–Al2O3. This was ascribed mainly to the synergistic effect, high specific surface area, and positive surface charge (at pH 7) of the adsorbent.222 ZnV2O4 hollow spheres comprised of a flower-like structure and a large number of compacted nanosheets, as depicted in the SEM image (Fig. 11), exhibited an adsorption capacity of 153.14 mg g−1 in 40 min for MB.223Table 5 presents the performance of metal and metal oxide-based hybrid (magnetic and non-magnetic) nanocomposites as adsorbents used in dye removal.
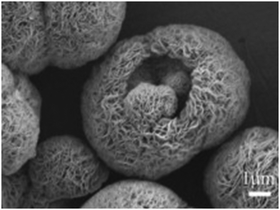 |
| Fig. 11 Morphology of a metal oxide-based adsorbent, ZnV2O4 hollow spheres [Reprinted with permission from ref. 223. Copyright 2011, Elsevier]. | |
4.5. Metal–organic frameworks
Metal–organic frameworks (MOFs) have attracted much attention as adsorbents due to their fine tuneable pore structures and controllable structures/confined geometries. Besides, the large surface areas, multi-functionality, polar/polarisable bonds, and the possibility of the presence of host–guest interactions through the chemical modification of the organic ligands and/or the inorganic sub-units are also likely to play a unique role.250–255 According to Li et al., MIL-53(Al)-NH2 could rapidly bind with MB (208.3 mg g−1) and MG (164.9 mg g−1) due to the hydrogen bonding between the amino groups of the dyes and MOF. Further, MIL-Ti MOFs aided the ultrasound adsorption Basic Red 46, Basic blue 41, and MB from single and binary systems, exhibiting the maximum adsorption capacity of 1250, 1428, and 833 mg g−1, respectively.257 This high adsorption capacity of MIL-Ti MOFs was attributed to π–π interaction, H-bonding, and electrostatic interaction between the dye molecules and MOFs (Fig. 12). Further, the SEM image of the synthesized NH2-MIL-125(Ti) having circular plates exhibited the transformation of its morphology due to the effect of the reactant concentration (Fig. 13), which also confirmed the excellent distribution of the nanomaterials. Haque et al. developed highly porous MIL-101 MOFs to study the adsorption of MO. The high adsorption capacity of 194 mg g−1 depicted the significance of pore size and porosity in the adsorption of MO, following the mechanism of electrostatic interaction on MIL-101.258
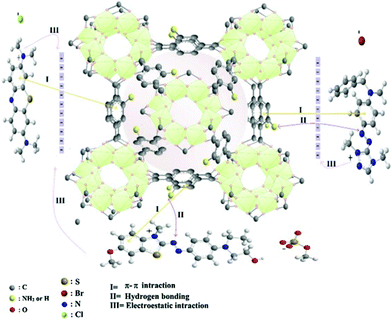 |
| Fig. 12 Multiple dye adsorption mechanisms on MOFs [Reprinted with permission from ref. 257. Copyright 2018, Elsevier]. | |
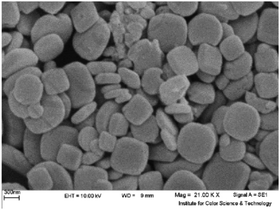 |
| Fig. 13 Morphology of NH2-MIL-125(Ti) with circular plate [Reprinted with permission from ref. 257. Copyright 2018, Elsevier]. | |
Further, MIL-100(Fe) and MIL-100(Cr)-derived MOFs were also found to be efficient adsorbents in capturing MO and MB dye molecules from aqueous solution. MIL-100(Fe) showed an adsorption capacity of 1045.2 and 736.2 mg g−1, while that of MIL-100(Cr) was 211.8 and 645.3 mg g−1 for MO and MB, respectively.259 Further, magnetic MOFs have also been used for the adsorption of MB from dye-contaminated water. The adsorption mechanism involves hydrophobic interactions and/or π–π interactions between the MB molecules and MOF. It was also noted that the adsorption capacity of a magnetic MOF increased from 84 to 245 mg g−1 on increasing the concentration of MB from 30 to 300 mg L−1, respectively.260 In addition, the adsorption capacity of the zeolitic imidazolate framework comprising ZIF-8, ZIF-8@CNT, and ZIF-8@GO depicted stable and high reusability for over four cycles for the adsorption of MG, corresponding to an adsorption capacity of 1667, 2034, and 3300 mg g−1, respectively.261 Zhao et al. used a zirconium-based metal–organic framework (Zr-MOF) as an adsorbent for the removal of crystal violet and RhB dyes with the maximum adsorption capacity corresponding to 63.38 and 67.73 mg g−1, respectively.262Table 6 describes various MOFs used as adsorbents in dye remediation from wastewater.
4.6. Polymers and their nanocomposites
Polymer-based adsorbents, such as polyaniline (PANI), polypyrrole (PPY), PANI/PPY copolymer, PANI/GO, PANI-modified rice husk composites, polymeric rice and Graham flour, polymeric turmeric powder, and chitosan, have found enormous applications in the field of dye treatment due to their easy fabrication, high effective surface area, high selectivity, interesting doping/de-doping chemistry, electrical transport characteristics, strong binding affinities, and porous surface texture.263–266 For most of the conducting polymer composites, the adsorption of dyes follows the mechanism of physisorption, hydrogen bonding, π–π interactions, and electrostatic interaction.267 Further, the presence of active groups (i.e., amine and imine) in the polymer facilitates the adsorption process. Many researchers have proposed the applications of polymer-based adsorbents to remediate dyes originating from industrial effluent (Table 7).
4.6.1 Pure polyaniline and polypyrrole.
Polyaniline is one of the most studied conducting polymers due to its many advantages, such as simple synthesis, presence of –NH– groups, capability of doping, excellent physicochemical properties, mechanical flexibility, stability, low cost, and easy availability of its monomer.101,268 Alternatively, polypyrrole is another polymer studied for the removal of dyes from wastewater.61 Accordingly, Tanzifi et al. studied the adsorption of methyl orange on nano polyaniline at 298 and 338 K. They inferred that an increase in temperature enhanced the adsorption capacity for the dye from 3.34 to 32.04 mg g−1 and 3.28 to 30.28 mg g−1 corresponding to the initial dye concentration of 10 and 100 mg L−1, respectively. The kinetics and isothermal studies established the pseudo-second-order model and validity of the Langmuir model (maximum monolayer adsorption capacity: 75.9 mg g−1).269 PANI nanoparticles have also been utilized for the ultrasonication-assisted adsorption of crystal violet dye.270 The adsorption data fitted well with the Freundlich and Dubinin-Radushkevich isotherms. According to Sharma et al., hyper crosslinked polyaniline (specific surface area: 1083 m2 g−1) achieved the maximum adsorption capacity of 245 and 220 mg g−1 in 60 min for cationic crystal violet and anionic MO dyes in aqueous medium, respectively. These studies also predicted the fitting of the Langmuir adsorption isotherm for both dyes.271 In another study, the adsorption of CR on PANI and PPY exhibited a maximum adsorption capacity of 250.01 and 66.66 mg g−1, respectively.61 Further, the experimental results revealed an increase in the adsorption efficiency with reaction time and adsorbent dosage. The kinetic data fitted well with the pseudo-second-order model, while thew equilibrium adsorption findings best correlated with the Langmuir isotherm model. In another study, the adsorption of sunset yellow and CR on a PPY–MWCNT composite achieved an adsorption capacity of 212.1 and 147 mg g−1, respectively.272 The adsorption mechanism involved electrostatic attraction and π–π electron donor–acceptor interaction. According to Ayad and Zaghlol (2012), cross-linked PANI exhibited an adsorption capacity of 13.85 mg g−1 for cationic dyes such as MB (surface area: 349 m2 g−1). The SEM image of crosslinked polyaniline at high magnification revealed a sponge-like structure, indicating the presence of pores (Fig. 14).273 Smita et al. used PANI to achieve a removal efficiency of 92% in 5 h for a toxic textile dye (MO) present in wastewater. The mechanistic study revealed that the electrostatic interaction between the counterions of the dye molecules and adsorbent was responsible for the adsorption of the dye.274 The adsorption of MB and acid green dye on PANI hollow nanotubes (internal diameter: 50–60 nm and outer diameter: 5–10 nm) followed the Langmuir model, and their maximum adsorption capacity corresponded to 69.4 and 57.87 mg g−1, respectively.275Fig. 15 schematically represents the proposed chemical interaction between PANI hollow nanotubes with MB and acid green dyes at pH of 9 and 3, respectively. MB completely adsorbed on the nanotubes of PANI within 20 min, and the adsorption process well fitted the Langmuir isotherm (maximum adsorption capacity: 9.21 mg g−1).276 Bhaumik et al. reported that the maximum monolayer adsorption capacity of Reactive Black 5 in aqueous solutions (pH 6) was 434.7 mg g−1 (318 K) on polyaniline nanofibers (diameter: 50–80 nm). The equilibrium isotherm data fitted the Langmuir isotherm.277
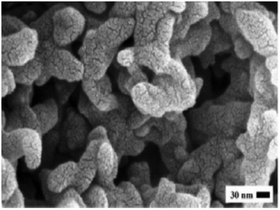 |
| Fig. 14 Scanning electron microscopy image of crosslinked PANI [Reprinted with permission from ref. 273. Copyright 2012, Elsevier]. | |
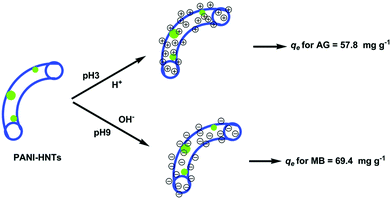 |
| Fig. 15 Schematic illustration of PANI-HNTs at pH 3 and 9 (blue color: PANI-HNTs and green color: AG) [Reprinted with permission from ref. 275. Copyright 2018, The Royal Society of Chemistry]. | |
4.6.2 Polyaniline and polypyrrole-based nanocomposites.
Recently, polymeric nanohybrid materials have attracted significant attention in the field of wastewater treatment due to their high adsorption ability. For example, starch/polyaniline was used to treat reactive black and Reactive Violet 4 dyes, showing an adsorption capacity of 811.30 and 578.39 mg g−1, respectively.278 The Toth isotherm model better described the single-component equilibrium adsorption, whereas the modified Freundlich model well fitted dye removal. In one study, PANI/starch was used to adsorb MB dye, which shown an adsorption capacity of 6.8 × 106 mol g−1.279 Further, El-Sharkaway et al. studied the removal of MB using PANI/GO and PANI/rGO nanocomposites. The adsorption capacity of PANI/GO and PANI/rGO for MB dye was 14.2 and 19.2 mg g−1, respectively, in 270 min.280 Besides, Shabandokht et al. investigated the adsorption of Acid Red 18 dye using a PANI/HCl-modified rice husk composite, which showed an adsorption capacity of 100 mg g−1.281 This study suggested that the Langmuir adsorption isotherm and pseudo-second-order kinetic model were compatible with the experimental results. In another work, Muhammad et al. removed Acid Blue 40 dye using polyaniline, Fe3O4, and their composites and the corresponding adsorption capacity was found to be 130.5, 264.9, and 216.9 mg g−1, respectively. The experimental result was better described by the Freundlich isotherm model and the mechanism involved electrostatic interactions and the significant amount of H-bonds present in PANI.263
In another study, the adsorption of RB5 dye-cellulose coated with magnetite nanoparticles and conducting PPY followed at pH 3 fitted the Langmuir model well (maximum adsorption capacity: 62.31 mg g−1).282 Further, Wang et al. also used PANI/TiO2 to remove MB dye with a maximum adsorption capacity of 458.10 mg g−1, and the Langmuir adsorption isotherm well correlated with the experimental results. Chemical adsorption, membrane diffusion, and intraparticle diffusion were the responsible adsorption processes, while H-bonding, electrostatic interaction, and coordination interaction were the responsible adsorption mechanisms (Fig. 16). The attachment of MB on the surface of PANI mainly occurs on amino groups by electrostatic interaction and hydrogen bonding.283 Thus, a PANI zirconium oxide nanocomposite,284 PANI nanocomposite functionalized with zirconium(IV) and silicophosphate285 and PANI α-zirconium phosphate286 acted as efficient adsorbents for the removal of methylene blue and methyl orange dyes. The adsorption process for the cationic methylene blue dye287 and Acid Green 25288 on PANI nanotube/silica was best described by the pseudo-second-order kinetic model and Langmuir adsorption isotherm with the maximum monolayer adsorption capacity of 10.31 and 6.896 mg g−1, respectively. Studies have also been reported using PANI/silver,289 PANI/alumina,290 PANI/nickel ferrite,291 and PANI/zinc ferrite292 composites for the adsorption of brilliant green dye, anionic dyes (reactive red, Acid Blue 62, and Direct Blue 199), MB, and RhB, respectively.
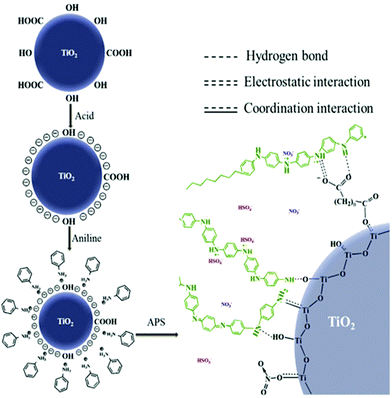 |
| Fig. 16 Schematic showing the adsorption mechanisms of PANI/TiO2 [Reprinted with permission from ref. 283. Copyright 2019, Elsevier]. | |
4.6.3 Chitosan-based adsorbents.
Chitosan is considered one of the most economical bio-polymers for dye removal, which can be extracted from natural resources. In comparison to other commercial adsorbents, it has attained great interest due to its unique properties such as cationic charge, high adsorption capacity, macromolecular structure, abundance, and cost-effectiveness.293,294 Chitosan is also an attractive source of natural polymers for the adsorption of pollutants from wastewater due to its biocompatibility, biodegradability, antibacterial properties, and nontoxicity.101 However, owing to its poor mechanical properties, low surface area, pH sensitivity, and low porosity, it is generally used in the form of a composite. Considering this, Janaki et al. reported that a PANI/chitosan composite efficiently removed Congo red, Coomassie brilliant blue, and Remazol brilliant blue R sulfonated anionic dye with a removal efficiency of 95.4%, 98.2%, and 99.8%, respectively. In contrast, it showed a removal efficiency of only 10.6% for the nonsulfonated cationic dye methylene blue.295
The adsorptive removal of Reactive Orange 16 on chitosan/PANI/ZnO agreed well with the Langmuir isotherm and corresponded to a maximum monolayer adsorption capacity of 476.2 mg g−1.296 In another work, the removal of anionic dyes, namely Direct Blue 86, photosens, theraphthal, and C.I. Reactive Blue 21m was studied on chitosan supported on a fibrous carrier.297 The experimental data fitted the Langmuir isotherm and showed the maximum adsorption capacity of anionic dye in the range of 300–1050 mg g−1 depending on the type, molecular size, and number of anionic groups in the dye. According to Cojocaru et al., spinel ferrite (15%) dispersed in the matrix of chitosan inter-linked with glutaraldehyde, showing an adsorption capacity of 45.02 mg g−1 for Acid Orange 7 dye. The hydrogen bonding and hydrophobic interaction between the dye molecules and composite were responsible for the adsorption mechanism.64 An Fe2O3/chitosan-bamboo saw-dust composite efficiently removed the acid dye bromothymol blue.298 The experimental data well correlated with the Langmuir isotherm model with an adsorption capacity of 217.39 mg g−1 achieved in 30 min contact time using 0.5 g L−1 adsorbent dose. Copello et al. treated Remazol black B, Erythrosine B, neutral red, and gentian violet dyes with chitosan hydrogel/SiO2 and achieved the maximum adsorption capacity of 0.081, 0.08, 0.88, and 0.17 mmol g−1, respectively.299
4.6.4 Miscellaneous polymer-based adsorbents.
Agarwal et al. used polyvinyl alcohol (PVA) as an adsorbent for the removal of bromothymol and MB from wastewater. The corresponding adsorption isotherms were well fitted with both the Langmuir and Freundlich models. The adsorbent attained the maximum adsorption capacity in 10 min, corresponding to 276.2 and 123.3 mg g−1, respectively.300 For the adsorption of Coomassie brilliant blue R 250 dye on poly(para-, ortho- and meta-phenylenediamine (PPDA)) grafted electrospun carbon nanofibers, the effective adsorption capacity of 141 mg g−1 was achieved and the adsorption kinetics and isotherm data were well correlated with the Elovich kinetic and Redlich–Peterson isotherm models respectively.63 The adsorption mechanism study suggested electrostatic interaction, π–π interactions, and intermolecular H-bonding controlled the dye sorption. Table 7 shows the removal of dye from contaminated water using conducting polymer, copolymer, and their nanocomposite-based adsorbents. Fig. 17 shows a schematic representation of dye pollution in water and its adsorptive removal using different adsorbents.
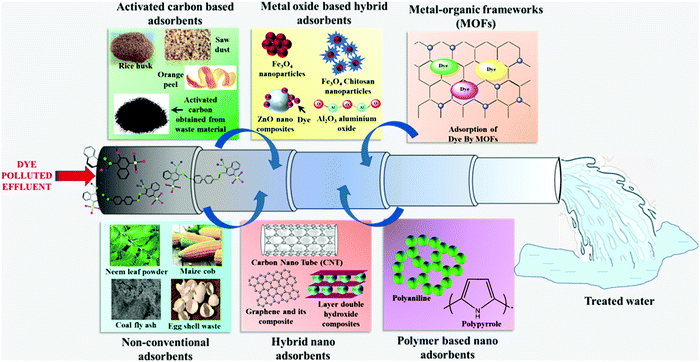 |
| Fig. 17 Schematic presentation of water pollution from dye wastewater, their adsorptive removal using various adsorbents, and the production of treated water. | |
5. Critical factors influencing dye adsorption
Critical factors such as initial dye concentration, solution pH, temperature, adsorbent dose, and time play a significant role in the adsorptive removal of dyes (Table 8). In this regard, the initial dye concentration makes substantial contributions to the adsorption phenomena. It should be noted that an increase in dye concentration shows positive effects up to a certain limit. Further, the increasing tendency of adsorption for high levels of dye contaminants is directly related to the available active sites on the surface of the adsorbent. The enhanced adsorption capacity is initially accelerated due to the presence of unsaturated active sites in the adsorbent. As the surface of the adsorbent becomes saturated, a considerable reduction in the adsorption of dye occurs.14,302 According to Mane and Babu (2011), for brilliant green dye with an initial concentration of 100 mg L−1, sodium hydroxide treated saw-dust exhibited an adsorption capacity of 55.86 mg g−1.121 In another work, the adsorption capacities of 1602 and 1814 mg g−1 were recorded on cellulose-g-poly(acrylic acid-co-acrylamide) as an adsorbent for the initial concentration of acid blue and MB of 200 mg L−1, respectively.204 These observations suggest, in general, a high initial concentration results in a high adsorption capacity. In addition, the solution pH also plays an essential role in the adsorption of dye from contaminated water. According to Zhou et al., a variation in pH can affect the possible reactions between dye molecules and adsorbents due to the change in the ionization level and surface charge of the adsorbent.14 In general, low and high solution pH favor the adsorption of anionic and cationic dyes, respectively.303 This was substantiated by Daneshvar et al. and Phoemphoonthanyakit et al., where they reported an adsorption capacity of 1093 mg g−1 at pH 2 for Acid Blue 25 and 600 mg g−1 at pH 7 for Rhodamine 6G.142,211 Further, the temperature has a prominent effect on the adsorption of dyes. Additionally, a variation in temperature is also helpful in identifying if adsorption process is endothermic or exothermic. In an exothermic process, the adsorption capacity decreases an increase in temperature, whereas it increases with an increase in temperature in an endothermic process.304
Table 8 Critical influencing factors affecting the adsorption process
Critical influencing factor |
Salient features |
Influence on adsorption |
Remarks |
Ref. |
Initial dye concentration |
Showing the dissolved amount of dye in aqueous solution and the amount of dye adsorption are directly related to the active sites present on the surface of the adsorbent. |
Increased dye concentration causes an increment in adsorption capacity until the unsaturated active sites of the adsorbent become saturated. |
In an aqueous environment, the initial concentration of dye may vary from trace level to mg L−1 or even more. |
14 and 302
|
pH of the solution |
Has a prominent role in dye adsorption. |
A variation in pH affects the reaction between dye molecules and adsorbents because of the change in the ionization level and surface charge of the adsorbents. |
The pH of the dye effluent may vary depending on the presence of different types of salts (acidic and basic). |
14 and 303
|
Controls the degree of electrostatic charges provided by ionized dye molecules and causes the varying rate of adsorptions with changing pH. |
In the literature, it has been found that low and high pH favor the adsorption of anionic and cationic dyes, respectively. |
Adsorbent dose |
Showing the amount of adsorbent used to remove dye particles. |
Generally, an increment in dose provides more active sites, which causes an increase in adsorption capacity. |
High dose affects the economy of the treatment process. |
95 and 303
|
Directly related to the number of active sites available on the surface of the adsorbent. |
However, a high dose causes congestion in active sites. |
Temperature |
Shows the adsorption nature, whether it is endothermic or exothermic. |
An increase in adsorption capacity with an increase in temperature shows the endothermic nature, whereas a decrease in adsorption capacity an increase in temperature shows the exothermic nature of reactions. |
In general, an increase in temperature increases the adsorption capacity, but a higher temperature is not desirable. |
95 and 304
|
Reaction time |
Shows the contact time between adsorbent and adsorbate. |
An increase in contact time causes positive effects on the adsorption until equilibrium among active sites of adsorbent and dye molecules is established. |
High reaction time affects the economy of the treatment processes due to an increase in energy requirements. |
95
|
In general, an increase in the adsorbent dose has positive effects on the adsorptive removal of dyes, mainly due to the increment in the active sorption sites.303 In contrast, a higher dose may cause congestion in active sites of the adsorbent. Khan and Nazir (2015) achieved an adsorption capacity of 217.39 mg g−1 for bromothymol blue at a dose of 0.5 g L−1 using an Fe2O3/chitosan–bamboo saw-dust composite.298 In contrast, Ebrahimian Pirbazari et al. reported an adsorption capacity of 1374.6 mg g−1 for MB at a dose of 1.0 g L−1 NaOH-treated wheat straw impregnated with Fe3O4 nanoparticles.214 These findings clearly demonstrate the positive effects manifested by an increased adsorbent dosage. Finally, an increase in contact time may have a negative and/or positive effects on the adsorptive removal of dyes. When equilibrium is established between the active sites of the adsorbent and dye molecules, a further increment in the reaction time has no involvement in the adsorption. Khan and Nazir (2015) have observed an adsorption capacity of 217.39 mg g−1 for bromothymol blue in 30 min on an Fe2O3/chitosan–bamboo saw-dust composite.298 In contrast, an adsorption capacity of 1057.90 mg g−1 for MO dye was achieved on a nano-dimensional Co/Cr-codoped ZnO adsorbent in 120 min, indicating that an increase in reaction time has positive effects on the adsorption process.219
6. Mechanisms of dye adsorption
The adsorption of dye from contaminated water on the surface of an adsorbent is achieved via various adsorption mechanisms, as schematically shown in Fig. 18 and displayed in Tables 2–7. It should be noted that the adsorption of water pollutants on adsorbents is mainly guided by electrostatic attraction, π–π interactions, van der Waals forces, hydrogen bonding, acid–base reactions, and hydrophobic interaction.1 Shen and Gondal reported that electrostatic and intermolecular interactions govern the adsorption of Rhodamine dye on the surface of the adsorbent.60 According to Zheng et al., the adsorption of anionic dyes, such as CR and MO on GO–NiFe-LDH, is achieved by electrostatic attraction and ion exchange phenomena.178
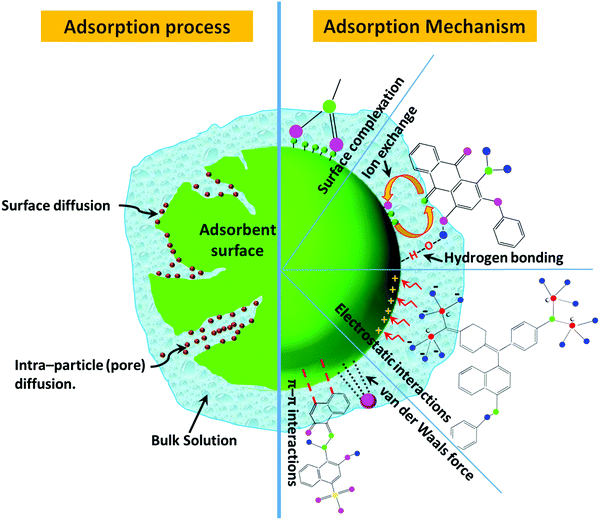 |
| Fig. 18 Adsorption processes and mechanisms for dye removal from bulk liquid. | |
Furthermore, the ion exchange mechanism involves the exchange of ions between a liquid (dye solution) and solid phase (adsorbent). Ebrahimian Pirbazari et al. suggested that two principal mechanisms are involved in removing the MB dye on NaOH-treated wheat straw impregnated with Fe3O4, namely the formation of a surface complex and ion exchange between the dye molecule and adsorption surfaces.214 The formation of a surface complex is a mechanism associated with the adsorption process, which is described by the binding of ions to various surface functional groups available onto the surface of the adsorbent and electrostatic interaction between the adsorbent–adsorbate surfaces. Cojocaru et al. proposed that the formation of hydrogen bonds between Acid Orange 7 dye and adsorbents accounts for the adsorption process.64 According to Siddiqui et al., H-bonds between MB and MnO2/BC arise due to the interaction between the –OH groups present in MnO2/BC and the acceptor present in MB molecules.123 Similarly, π–π bonding/π-effects/π-interactions (non-covalent) involve π systems, where similar to electrostatic interactions, positively charged molecules interact with negatively charged surfaces. Further, the adsorption process can follow more than one mechanism simultaneously. For example, the adsorption of Coomassie Brilliant Blue R 250 dye on the surface of adsorbents is governed by electrostatic interactions, π–π interactions, and intermolecular H-bonding.63 The probable adsorption mechanisms involved in dye removal are shown in Fig. 18, together with the various adsorption processes.
7. Critiques, future perspectives, and summary
7.1. Critiques and future perspectives
Adsorption is the most preferred technique for dye removal due to its ease of operation, high efficiency, recyclability, and cost-effectiveness. This is also one of the most suitable methods employed for both pilot and field-scale wastewater treatment facilities. The adsorption ability depends on the type of adsorbent used in the removal of dyes from contaminated water. Therefore, adsorbents should have easy availability, cost-effectiveness, high porosity, recycling ability, and abundant active sites on its surface. Recently, commercial adsorbents, such as industrial waste-based adsorbents for the treatment of dyes, pesticides, pharmaceuticals, etc., have received considerable attention due to their involvement in waste minimization. Besides, metal oxide-based adsorbents are also preferred on a large scale due to their unique properties, such as highly active sites and ability to blend with other sorbents. Furthermore, metal–organic framework- and polymer-based adsorbents have also been explored as adsorbents in the treatment of dye-contaminated water owing to their enhanced surface activity and porosity. Considering this, future studies could target the better utilization of commercial and natural bio-adsorbents having good adsorption and desorption capabilities, recyclability, and cost-effectiveness. MOFs and polymer-based adsorbents can be widely researched for wastewater treatment. The adsorption techniques can also be explored in the field of micropollutant remediation such as dyes, pharmaceuticals, and other emerging contaminants at the field scale.
Continuing research is focused on adsorption as one of the prime strategies in the separation of dye from wastewater. However, challenges still exist in developing low-cost, high-performing adsorbents with significantly enhanced activity and long-term stability. In this regard, integrating agro-industrial waste, several naturally existing materials, and eco-friendly industrial waste materials with other biodegradable nanomaterials with no risk to human health and environmental sustainability may be the best alternative. Further, the choice of nanomaterials as adsorbents in wastewater treatment is guided by their high surface area and high adsorption capacity. However, the production cost of nano-adsorbents needs to be considered for their commercial use in any industrial effluent treatment. Despite this, the separation of nanomaterials after adsorption and their disposal are complex and costly processes.305
Additionally, cost-effectiveness in terms of reusability of the spent adsorbent should also be considered. Spent adsorbents need to be regenerated and activated by treating them with acid or alkali for their safe and effective reuse.306 Further, the economical and safe disposal or reuse of spent/exhausted adsorbents need to be considered.307,308 Dye-loaded spent adsorbents can be utilized to produce biochar materials, fuel cells, for energy production purposes, and also in landfilling.307,309 Simultaneously, the difficulties and limitations in the scale-up of the treatment technology at the commercial level need to be considered in terms of economic aspects and energy-related issues.
7.2. Summary
The disposal of colored dye wastewater in the environment has depleted freshwater resources and compelled scientists to rethink the availability of clean and safe water. It has been reported that the presence of toxic and colored compounds in dye-containing wastewater results in carcinogenic, mutagenic, allergic, and dermatitis effects on living organisms. This review article reported various classes of dyes and their applications, ecotoxic effects, and sources of dye-contaminated water. The textile, leather, and cosmetic industries were found to be the primary sources of dye-polluted water. Different existing treatment techniques were reviewed and compared for dye removal. Among them, adsorption was selected as a potential technique to treat dye wastewater due to its easy application, simple and scalable synthesis of adsorbents, high removal efficiency, and cost-effectiveness. In this direction, the various adsorbents reported for the removal of dyes from aqueous solution were highlighted. In addition, investigations revealing the adsorption kinetics and fitting of the adsorption isotherm were also presented. MOFs, metal-oxides, and hybrids of bio-adsorbents and carbon show significant adsorption ability for dye contaminants. Various critical factors, such as solution pH, adsorbent dosage, initial dye concentration, temperature, and equilibrium time, were identified as essential factors influencing the adsorption process. Besides, the driving forces responsible for the adsorption of dye molecules are electrostatic interactions, van der Waals forces, hydrogen bonding, and π–π interactions. Thus, the high removal efficiency and field applicability of the adsorption technique make this process suitable for the treatment of dye-contaminated water.
Conflicts of interest
There are no conflicts of interest to declare.
Acknowledgements
S. Dutta and B. Gupta are grateful to the Indian Institute of Technology Kharagpur, India, for financial support.
References
- F. Lu and D. Astruc, Coord. Chem. Rev., 2020, 408, 213180 CrossRef CAS.
- J. K. H. Wong, H. K. Tan, S. Y. Lau, P. S. Yap and M. K. Danquah, J. Environ. Chem. Eng., 2019, 7, 103261 CrossRef CAS.
- S. Benkhaya, S. M’rabet and A. El Harfi, Inorg. Chem. Commun., 2020, 115, 107891 CrossRef CAS.
- J. Chen, Y. Xiong, M. Duan, X. Li, J. Li, S. Fang, S. Qin and R. Zhang, Langmuir, 2020, 36, 520–533 CrossRef CAS PubMed.
- C. Sahoo, A. K. Gupta and A. Pal, Desalination, 2005, 181, 91–100 CrossRef CAS.
- C. Sahoo and A. K. Gupta, J. Environ. Sci. Health, Part A: Toxic/Hazard. Subst. Environ. Eng., 2015, 50, 1333–1341 CrossRef CAS PubMed.
- H. Znad, K. Abbas, S. Hena and M. R. Awual, J. Environ. Chem. Eng., 2018, 6, 218–227 CrossRef CAS.
- C. Sahoo, A. K. Gupta and I. M. S. Pillai, J. Environ. Sci. Health, Part A: Toxic/Hazard. Subst. Environ. Eng., 2012, 47, 2109–2119 CrossRef CAS PubMed.
- E. Guerra, M. Llompart and C. Garcia-Jares, Cosmetics, 2018, 5, 47 CrossRef.
- N. R. J. Hynes, J. S. Kumar, H. Kamyab, J. A. J. Sujana, O. A. Al-Khashman, Y. Kuslu, A. Ene and B. Suresh Kumar, J. Cleaner Prod., 2020, 272, 122636 CrossRef CAS.
- M. Rafatullah, O. Sulaiman, R. Hashim and A. Ahmad, J. Hazard. Mater., 2010, 177, 70–80 CrossRef CAS PubMed.
- C. Sahoo, A. K. Gupta and I. M. Sasidharan Pillai, J. Environ. Sci. Health, Part A: Toxic/Hazard. Subst. Environ. Eng., 2012, 47, 1428–1438 CrossRef CAS PubMed.
- S. Senapati, S. K. Srivastava, S. B. Singh and A. R. Kulkarni, Environ. Res., 2014, 135, 95–104 CrossRef CAS PubMed.
- Y. Zhou, J. Lu, Y. Zhou and Y. Liu, Environ. Pollut., 2019, 252, 352–365 CrossRef CAS PubMed.
-
A. Gičević, L. Hindija and A. Karačić, IFMBE Proceedings, Springer Verlag, 2020, vol. 73, pp. 581–587 Search PubMed.
- A. Ghosal, J. Shah, R. K. Kotnala and S. Ahmad, J. Mater. Chem. A, 2013, 1, 12868–12878 RSC.
- C. J. Ogugbue and T. Sawidis, Biotechnol. Res. Int., 2011, 2011, 1–11 CrossRef PubMed.
- A. Nasar and F. Mashkoor, Environ. Sci. Pollut. Res., 2019, 26, 5333–5356 CrossRef CAS PubMed.
- K. Deering, E. Spiegel, C. Quaisser, D. Nowak, S. Rakete, M. Garí and S. Bose-O’Reilly, Environ. Res., 2020, 184, 109271 CrossRef CAS PubMed.
- E. Von Lau, S. Gan, H. K. Ng and P. E. Poh, Environ. Pollut., 2014, 184, 640–649 CrossRef PubMed.
- B. Lellis, C. Z. Fávaro-Polonio, J. A. Pamphile and J. C. Polonio, Biotechnol. Res. Innov., 2019, 3, 275–290 CrossRef.
- M. T. Yagub, T. K. Sen, S. Afroze and H. M. Ang, Adv. Colloid Interface Sci., 2014, 209, 172–184 CrossRef CAS PubMed.
- N. Nippatla and L. Philip, Process Saf. Environ. Prot., 2019, 125, 143–156 CrossRef CAS.
- K. Meerbergen, S. Crauwels, K. A. Willems, R. Dewil, J. Van Impe, L. Appels and B. Lievens, J. Biosci. Bioeng., 2017, 124, 668–673 CrossRef CAS PubMed.
- B. Dong, H. Chen, Y. Yang, Q. He and X. Dai, Desalin. Water Treat., 2014, 52, 4562–4567 CrossRef CAS.
- K. Rachna, A. Agarwal and N. Singh, Mater. Today: Proc., 2019, 12, 573–580 CAS.
- A. Ahmadi Zahrani and B. Ayati, J. Electroanal. Chem., 2020, 873, 114456 CrossRef CAS.
- M. Shaban, M. R. Abukhadra, A. Hamd, R. R. Amin and A. Abdel Khalek, J. Environ. Manage., 2017, 204, 189–199 CrossRef CAS PubMed.
- S. Samsami, M. Mohamadi, M. H. Sarrafzadeh, E. R. Rene and M. Firoozbahr, Process Saf. Environ. Prot., 2020, 143, 138–163 CrossRef CAS.
- H. C. Tee, P. E. Lim, C. E. Seng, M. A. Mohd Nawi and R. Adnan, J. Environ. Manage., 2015, 147, 349–355 CrossRef CAS PubMed.
- S. Sonal, D. Ugale and B. K. Mishra, Mine Water Environ., 2021, 1, 3 Search PubMed.
- B. Gupta, T. Priya and B. Kumar Mishra, Environ. Eng. Res., 2020, 26, 200234 Search PubMed.
- N. Daneshvar, A. Oladegaragoze and N. Djafarzadeh, J. Hazard. Mater., 2006, 129, 116–122 CrossRef CAS PubMed.
- T. Priya, A. Tarafdar, B. Gupta and B. K. Mishra, J. Environ. Sci., 2018, 70, 1–10 CrossRef PubMed.
- A. Majumder, B. Gupta and A. K. Gupta, Environ. Res., 2019, 176, 108542 CrossRef CAS PubMed.
- C. Manera, A. P. Tonello, D. Perondi and M. Godinho, Environ. Technol., 2019, 40, 2756–2768 CrossRef CAS PubMed.
- B. Gupta, A. K. Gupta, C. S. Tiwary and P. S. Ghosal, Environ. Res., 2020, 110390 Search PubMed.
- B. Gupta, A. K. Gupta, P. S. Ghosal and C. S. Tiwary, Environ. Res., 2020, 109154 CrossRef CAS PubMed.
- S. K. Kuila, D. K. Gorai, B. Gupta, A. K. Gupta, C. S. Tiwary and T. K. Kundu, Chemosphere, 2020, 128780 Search PubMed.
- K. G. Pavithra, P. Senthil Kumar, V. Jaikumar and P. Sundar Rajan, J. Ind. Eng. Chem., 2019, 75, 1–19 CrossRef CAS.
- C. Sahoo, A. K. Gupta and A. Pal, Dyes Pigm., 2005, 66, 189–196 CrossRef CAS.
- A. K. Gupta, A. Pal and C. Sahoo, Dyes Pigm., 2006, 69, 224–232 CrossRef CAS.
- C. Sahoo and A. K. Gupta, J. Hazard. Mater., 2012, 215–216, 302–310 CrossRef CAS PubMed.
- CPHEEO, Manual on Sewerage and Sewage Treatment Systems – 2013:Central Public Health & Environmental Engineering Organisation (CPHEEO), Govt of India, 2013.
- T. H. Kim, Y. Lee, J. Yang, B. Lee, C. Park and S. Kim, Desalination, 2004, 168, 287–293 CrossRef CAS.
- S. Dutta, K. Manna, S. K. Srivastava, A. K. Gupta and M. K. Yadav, Sci. Rep., 2020, 10, 1–14 CrossRef PubMed.
- G. Xiong, B. Bin Wang, L. X. You, B. Y. Ren, Y. K. He, F. Ding, I. Dragutan, V. Dragutan and Y. G. Sun, J. Mater. Chem. A, 2019, 7, 393–404 RSC.
- Y. Xiong, Q. Wang, M. Duan, J. Tan, S. Fang and J. Wu, Langmuir, 2018, 34, 7612–7623 CrossRef CAS PubMed.
- Y. Tong, P. J. McNamara and B. K. Mayer, Environ. Sci.: Water Res. Technol., 2019, 5, 821–838 RSC.
- K. Dutta and S. De, J. Mater. Chem. A, 2017, 5, 22095–22112 RSC.
- M. R. Awual, Chem. Eng. J., 2015, 266, 368–375 CrossRef CAS.
- S. A. El-Safty, M. A. Shenashen, M. Ismael, M. Khairy and M. R. Awual, Analyst, 2012, 137, 5278–5290 RSC.
- M. R. Awual, Mater. Sci. Eng., C, 2019, 101, 686–695 CrossRef CAS PubMed.
- M. R. Awual, Composites, Part B, 2019, 172, 387–396 CrossRef CAS.
- M. R. Awual, J. Environ. Chem. Eng., 2019, 7, 103124 CrossRef CAS.
- M. R. Awual, M. M. Hasan, M. M. Rahman and A. M. Asiri, J. Mol. Liq., 2019, 283, 772–780 CrossRef CAS.
- M. R. Awual, J. Environ. Chem. Eng., 2019, 7, 103378 CrossRef CAS.
- M. R. Awual, T. Yaita, T. Kobayashi, H. Shiwaku and S. Suzuki, J. Environ. Chem. Eng., 2020, 8, 103684 CrossRef CAS.
- M. K. Yadav, D. Saidulu, A. K. Gupta, P. S. Ghosal and A. Mukherjee, J. Environ. Chem. Eng., 2021, 9, 105203 CrossRef CAS.
- K. Shen and M. A. Gondal, J. Saudi Chem. Soc., 2017, 21, S120–S127 CrossRef CAS.
- H. Chafai, M. Laabd, S. Elbariji, M. Bazzaoui and A. Albourine, J. Dispersion Sci. Technol., 2017, 38, 832–836 CrossRef CAS.
- N. Mohammadi, H. Khani, V. K. Gupta, E. Amereh and S. Agarwal, J. Colloid Interface Sci., 2011, 362, 457–462 CrossRef CAS PubMed.
- B. M. Thamer, A. Aldalbahi, M. Moydeen A, H. El-Hamshary, A. M. Al-Enizi and M. H. El-Newehy, Mater. Chem. Phys., 2019, 234, 133–145 CrossRef CAS.
- C. Cojocaru, P. Samoila and P. Pascariu, Int. J. Biol. Macromol., 2019, 123, 587–599 CrossRef CAS PubMed.
- V. K. Gupta, Suhas, I. Ali and V. K. Saini, Ind. Eng. Chem. Res., 2004, 43, 1740–1747 CrossRef CAS.
- S. K. Srivastava, S. Senapati, S. B. Singh and P. K. Raul, RSC Adv., 2016, 6, 113424 RSC.
- A. K. Sahoo, S. K. Srivastava, P. K. Raul, A. K. Gupta and R. Shrivastava, J. Nanopart. Res., 2014, 16, 1–17 CrossRef CAS.
- P. Basnet and Y. Zhao, J. Mater. Chem. A, 2014, 2, 911–914 RSC.
- C. B. Godiya, L. A. Martins Ruotolo and W. Cai, J. Mater. Chem. A, 2020, 8, 21585–21612 RSC.
- J. L. Gong, B. Wang, G. M. Zeng, C. P. Yang, C. G. Niu, Q. Y. Niu, W. J. Zhou and Y. Liang, J. Hazard. Mater., 2009, 164, 1517–1522 CrossRef CAS.
- D. A. Yaseen and M. Scholz, Int. J. Environ. Sci. Technol., 2019, 16, 1193–1226 CrossRef CAS.
- Pubchem, Home – PubChem Compound – NCBI, https://www.ncbi.nlm.nih.gov/pccompound, (accessed 3 February 2021).
- K. Yamjala, M. S. Nainar and N. R. Ramisetti, Food Chem., 2016, 192, 813–824 CrossRef CAS PubMed.
- L. C. Davies, G. J. M. Cabrita, R. A. Ferreira, C. C. Carias, J. M. Novais and S. Martins-Dias, Ecol. Eng., 2009, 35, 961–970 CrossRef.
- M. Kashefialasl, M. Khosravi, R. Marandi and K. Seyyedi, Int. J. Environ. Sci. Technol., 2006, 2, 365–371 CAS.
-
K. Jain, D. Madamwar and O. Tiwari, Mapping of Research Outcome on Remediation of Dyes, Dye Intermediates and Textile Industrial Waste, 2019 Search PubMed.
- S. Shakoor and A. Nasar, J. Taiwan Inst. Chem. Eng., 2016, 66, 154–163 CrossRef CAS.
- H. Xiao, T. Zhao, C. H. Li and M. Y. Li, J. Cleaner Prod., 2017, 165, 1499–1507 CrossRef CAS.
- A. C. Jalandoni-Buan, A. L. A. Decena-Soliven, E. P. Cao, V. L. Barraquio and W. L. Barraquio, Philipp. J. Sci., 2010, 139, 71–78 Search PubMed.
- D. T. Sponza and M. Işik, Process Biochem., 2005, 40, 2735–2744 CrossRef CAS.
- S. M. Burkinshaw and Y. A. Son, Dyes Pigments, 2010, 87, 132–138 CrossRef CAS.
- G. Muthuraman and T. T. Teng, Prog. Nat. Sci., 2009, 19, 1215–1220 CrossRef CAS.
- G. L. Baughman and E. J. Weber, Dyes Pigm., 1991, 16, 261–271 CrossRef CAS.
- C. D. Raman and S. Kanmani, J. Environ. Manage., 2016, 177, 341–355 CrossRef CAS PubMed.
- A. A. Shalaby and A. A. Mohamed, RSC Adv., 2020, 10, 11311–11316 RSC.
- K. R. Millington, K. W. Fincher and A. L. King, Sol. Energy Mater. Sol. Cells, 2007, 91, 1618–1630 CrossRef CAS.
- M. Berradi, R. Hsissou, M. Khudhair, M. Assouag, O. Cherkaoui, A. El Bachiri and A. El Harfi, Heliyon, 2019, 5, e02711 CrossRef PubMed.
- M. F. Abid, M. A. Zablouk and A. M. Abid-Alameer, J. Environ. Health Sci. Eng., 2012, 9, 1–9 CrossRef PubMed.
- B. Manu and S. Chaudhari, Bioresour. Technol., 2002, 82, 225–231 CrossRef CAS.
- A. K. Yadav, C. K. Jain and D. S. Malik, J. Sustainable Environ. Res., 2014, 3, 95–102 Search PubMed.
- T. Robinson, G. McMullan, R. Marchant and P. Nigam, Bioresour. Technol., 2001, 77, 247–255 CrossRef CAS.
- J. Garvasis, A. R. Prasad, K. O. Shamsheera, P. K. Jaseela and A. Joseph, Mater. Chem. Phys., 2020, 251, 123040 CrossRef CAS.
- M. F. Abid, M. A. Zablouk and A. M. Abid-Alameer, Iran. J. Environ. Health Sci. Eng., 2012, 9, 1–9 CrossRef PubMed.
- R. Singh, M. K. Sinha and M. K. Purkait, Sep. Purif. Technol., 2020, 250, 117247 CrossRef CAS.
- V. Katheresan, J. Kansedo and S. Y. Lau, J. Environ. Chem. Eng., 2018, 6, 4676–4697 CrossRef CAS.
- D. Saidulu, B. Gupta, A. K. Gupta and P. S. Ghosal, J. Environ. Chem. Eng., 2021, 105282 CrossRef CAS.
- N. Al-Bastaki, Chem. Eng. Process., 2004, 43, 1561–1567 CrossRef CAS.
- S. K. Nataraj, K. M. Hosamani and T. M. Aminabhavi, Desalination, 2009, 249, 12–17 CrossRef CAS.
- G. Moradi, S. Zinadini and L. Rajabi, Process Saf. Environ. Prot., 2020, 144, 65–78 CrossRef CAS.
- S. Senapati, S. K. Srivastava and S. B. Singh, Nanoscale, 2012, 4, 6604–6612 RSC.
- A. Nasar and F. Mashkoor, Environ. Sci. Pollut. Res., 2019, 26, 5333–5356 CrossRef CAS PubMed.
- K. Y. Foo and B. H. Hameed, Desalin. Water Treat., 2010, 19, 255–274 CrossRef CAS.
- S. Sonal, P. Prakash, B. K. Mishra and G. C. Nayak, RSC Adv., 2020, 10, 13783–13798 RSC.
- X. W. Liu, T. J. Sun, J. L. Hu and S. D. Wang, J. Mater. Chem. A, 2016, 4, 3584–3616 RSC.
- P. K. Malik, J. Hazard. Mater., 2004, 113, 81–88 CrossRef CAS PubMed.
- C. Djilani, R. Zaghdoudi, F. Djazi, B. Bouchekima, A. Lallam, A. Modarressi and M. Rogalski, J. Taiwan Inst. Chem. Eng., 2015, 53, 112–121 CrossRef CAS.
- M. S. Rahman, Water, Air, Soil Pollut., 2021, 232, 1–14 CrossRef CAS.
- D. A. Giannakoudakis, G. Z. Kyzas, A. Avranas and N. K. Lazaridis, J. Mol. Liq., 2016, 213, 381–389 CrossRef CAS.
- E. Akar, A. Altinişik and Y. Seki, Ecol. Eng., 2013, 52, 19–27 CrossRef.
- M. A. Ahmad, N. B. Ahmed, K. A. Adegoke and O. S. Bello, Chem. Data Collect., 2019, 22, 100249 CrossRef.
- L. Ding, B. Zou, W. Gao, Q. Liu, Z. Wang, Y. Guo, X. Wang and Y. Liu, Colloids Surf., A, 2014, 446, 1–7 CrossRef CAS.
- S. S. Lam, R. K. Liew, Y. M. Wong, P. N. Y. Yek, N. L. Ma, C. L. Lee and H. A. Chase, J. Cleaner Prod., 2017, 162, 1376–1387 CrossRef CAS.
- A. Khan, X. Wang, K. Gul, F. Khuda, Z. Aly and A. M. Elseman, Egypt. J. Basic Appl. Sci., 2018, 5, 171–182 Search PubMed.
- B. Szczęśniak, J. Phuriragpitikhon, J. Choma and M. Jaroniec, J. Mater. Chem. A, 2020, 8, 18464–18491 RSC.
- A. H. Jawad, R. A. Rashid, M. A. M. Ishak and L. D. Wilson, Desalin. Water Treat., 2016, 57, 25194–25206 CrossRef CAS.
- M. Asadullah, M. Asaduzzaman, M. S. Kabir, M. G. Mostofa and T. Miyazawa, J. Hazard. Mater., 2010, 174, 437–443 CrossRef CAS PubMed.
- A. T. Ojedokun and O. S. Bello, Appl. Water Sci., 2017, 7, 1965–1977 CrossRef CAS.
- T. N. V. de Souza, S. M. L. de Carvalho, M. G. A. Vieira, M. G. C. da Silva and D. do S. B. Brasil, Appl. Surf. Sci., 2018, 448, 662–670 CrossRef.
- A. Aichour, H. Zaghouane-Boudiaf, C. V. Iborra and M. S. Polo, J. Mol. Liq., 2018, 256, 533–540 Search PubMed.
- G. Crini, Bioresour. Technol., 2006, 97, 1061–1085 CrossRef CAS PubMed.
- V. S. Mane and P. V. V. Babu, Desalination, 2011, 273, 321–329 CrossRef CAS.
- S. I. Abubakar and M. B. Ibrahim, Bayero J. Pure Appl. Sci., 2019, 11, 273 CrossRef.
- S. I. Siddiqui, O. Manzoor, M. Mohsin and S. A. Chaudhry, Environ.
Res., 2019, 171, 328–340 CrossRef CAS PubMed.
- K. G. Bhattacharyya and A. Sarma, Dyes Pigm., 2003, 57, 211–222 CrossRef CAS.
- S. Chowdhury, S. Chakraborty and P. Saha, Colloids Surf., B, 2011, 84, 520–527 CrossRef CAS PubMed.
- F. Deniz and S. Karaman, Chem. Eng. J., 2011, 170, 67–74 CrossRef CAS.
- M. Peydayesh and A. Rahbar-Kelishami, J. Ind. Eng. Chem., 2015, 21, 1014–1019 CrossRef CAS.
- A. K. Jain, V. K. Gupta, A. Bhatnagar and Suhas, J. Hazard. Mater., 2003, 101, 31–42 CrossRef CAS PubMed.
- L. Li, S. Wang and Z. Zhu, J. Colloid Interface Sci., 2006, 300, 52–59 CrossRef CAS PubMed.
- A. Bhatnagar and A. K. Jain, J. Colloid Interface Sci., 2005, 281, 49–55 CrossRef CAS PubMed.
- L. Zhou, H. Zhou, Y. Hu, S. Yan and J. Yang, J. Environ. Manage., 2019, 234, 245–252 CrossRef CAS PubMed.
- M. A. Abdel-Khalek, M. K. Abdel Rahman and A. A. Francis, J. Environ. Chem. Eng., 2017, 5, 319–327 CrossRef CAS.
- W. Gao, S. Zhao, H. Wu, W. Deligeer and S. Asuha, Appl. Clay Sci., 2016, 126, 98–106 CrossRef CAS.
- S. C. R. Santos and R. A. R. Boaventura, Appl. Clay Sci., 2008, 42, 137–145 CrossRef CAS.
- A. Xue, S. Zhou, Y. Zhao, X. Lu and P. Han, Appl. Clay Sci., 2010, 48, 638–640 CrossRef CAS.
- R. Yang, D. Li, A. Li and H. Yang, Appl. Clay Sci., 2018, 151, 20–28 CrossRef CAS.
- P. P. Selvam, S. Preethi, P. Basakaralingam, N. Thinakaran, A. Sivasamy and S. Sivanesan, J. Hazard. Mater., 2008, 155, 39–44 CrossRef CAS PubMed.
- Y. Kismir and A. Z. Aroguz, Chem. Eng. J., 2011, 172, 199–206 CrossRef CAS.
- K. El Hassani, B. H. Beakou, D. Kalnina, E. Oukani and A. Anouar, Appl. Clay Sci., 2017, 140, 124–131 CrossRef CAS.
- L. Chen, C. Li, Y. Wei, G. Zhou, A. Pan, W. Wei and B. Huang, J. Alloys Compd., 2016, 687, 499–505 CrossRef CAS.
- G. L. Dotto, V. M. Esquerdo, M. L. G. Vieira and L. A. A. Pinto, Colloids Surf., B, 2012, 91, 234–241 CrossRef CAS PubMed.
- E. Daneshvar, M. S. Sohrabi, M. Kousha, A. Bhatnagar, B. Aliakbarian, A. Converti and A. C. Norrström, J. Taiwan Inst. Chem. Eng., 2014, 45, 2926–2934 CrossRef CAS.
- K. Song, H. Xu, L. Xu, K. Xie and Y. Yang, Bioresour. Technol., 2017, 232, 254–262 CrossRef CAS PubMed.
- J. Wu, T. Zhang, C. Chen, L. Feng, X. Su, L. Zhou, Y. Chen, A. Xia and X. Wang, Bioresour. Technol., 2018, 266, 134–138 CrossRef CAS PubMed.
- M. M. Hasan, M. A. Shenashen, M. N. Hasan, H. Znad, M. S. Salman and M. R. Awual, J. Mol. Liq., 2021, 323, 114587 CrossRef CAS.
- K. T. Kubra, M. S. Salman, H. Znad and M. N. Hasan, J. Mol. Liq., 2021, 329, 115541 CrossRef CAS.
- S. D. Khattri and M. K. Singh, Water, Air, Soil Pollut., 2000, 120, 283–294 CrossRef CAS.
- M. P. Da Rosa, A. V. Igansi, S. F. Lütke, T. R. Sant’anna Cadaval, A. C. R. Do Santos, A. P. De Oliveira Lopes Inacio, L. A. De Almeida Pinto and P. H. Beck, J. Environ. Chem. Eng., 2019, 7, 103504 CrossRef CAS.
- S. Dogar, S. Nayab, M. Q. Farooq, A. Said, R. Kamran, H. Duran and B. Yameen, ACS Omega, 2020, 5, 15850–15864 CrossRef CAS PubMed.
- A. Amari, H. Gannouni, M. I. Khan, M. K. Almesfer, A. M. Elkhaleefa and A. Gannouni, Appl. Sci., 2018, 8, 2302 CrossRef CAS.
- L. C. Paredes-Quevedo, C. González-Caicedo, J. A. Torres-Luna and J. G. Carriazo, Water, Air, Soil Pollut., 2021, 232, 1–19 CrossRef.
- A. H. Pinto, J. K. Taylor, R. Chandradat, E. Lam, Y. Liu, A. C. W. Leung, M. Keating and R. Sunasee, J. Environ. Chem. Eng., 2020, 8, 104187 CrossRef CAS.
- W. Bessashia, Y. Berredjem, Z. Hattab and M. Bououdina, Environ. Res., 2020, 186, 109484 CrossRef CAS PubMed.
- H. Zhang, P. Wang, Y. Zhang, B. Cheng, R. Zhu and F. Li, RSC Adv., 2020, 10, 41251–41263 RSC.
-
S. K. Srivastava and V. Mittal, Hybrid Nanomaterials: Advances in Energy, Environment and Polymer Nanocomposites, John Wiley & Sons, Inc., Hoboken, NJ, USA, 2017 Search PubMed.
- T. S. Kim, H. J. Song, M. A. Dar, H. J. Lee and D. W. Kim, Appl. Surf. Sci., 2018, 439, 364–370 CrossRef CAS.
- S. R. Manippady, A. Singh, B. M. Basavaraja, A. K. Samal, S. Srivastava and M. Saxena, ACS Appl. Nano Mater., 2020, 3, 1571–1582 CrossRef CAS.
- L. Meng, X. Zhang, Y. Tang, K. Su and J. Kong, Sci. Rep., 2015, 5, 1–16 Search PubMed.
- L. Jin, X. Zhao, X. Qian and M. Dong, J. Colloid Interface Sci., 2018, 509, 245–253 CrossRef CAS PubMed.
- Y. Wang, Y. Li, H. Li, H. Zheng and Q. Du, J. Polym. Environ., 2019, 27, 1342–1351 CrossRef CAS.
- M. Kamaraj, N. R. Srinivasan, G. Assefa, A. T. Adugna and M. Kebede, Environ. Technol. Innov., 2020, 17, 100540 CrossRef.
- M. Goswami and P. Phukan, J. Environ. Chem. Eng., 2017, 5, 3508–3517 CrossRef CAS.
- R. Gong, J. Ye, W. Dai, X. Yan, J. Hu, X. Hu, S. Li and H. Huang, Ind. Eng. Chem. Res., 2013, 52, 14297–14303 CrossRef CAS.
- B. Pradhan, S. Roy, S. K. Srivastava and A. Saxena, J. Appl. Polym. Sci., 2015, 132, 41818 CrossRef.
- B. Bhuyan, S. K. Srivastava and J. Pionteck, Polym. Technol. Mater., 2019, 58, 537–546 CAS.
- C. H. Wu, J. Hazard. Mater., 2007, 144, 93–100 CrossRef CAS PubMed.
- Y. Yao, H. Bing, X. Feifei and C. Xiaofeng, Chem. Eng. J., 2011, 170, 82–89 CrossRef CAS.
- K. Sui, Y. Li, R. Liu, Y. Zhang, X. Zhao, H. Liang and Y. Xia, Carbohydr. Polym., 2012, 90, 399–406 CrossRef CAS PubMed.
- M. Ghaedi, H. Khajehsharifi, A. H. Yadkuri, M. Roosta and A. Asghari, Toxicol. Environ. Chem., 2012, 94, 873–883 CrossRef CAS.
- L. Ai, C. Zhang, F. Liao, Y. Wang, M. Li, L. Meng and J. Jiang, J. Hazard. Mater., 2011, 198, 282–290 CrossRef CAS PubMed.
- L. K. De Assis, B. S. Damasceno, M. N. Carvalho, E. H. C. Oliveira and M. G. Ghislandi, Environ. Technol., 2019, 41, 2360–2371 CrossRef PubMed.
- V. Sabna, S. G. Thampi and S. Chandrakaran, Water Sci. Technol., 2018, 78, 732–742 CrossRef CAS PubMed.
- C. M. Bezerra de Araujo, G. Filipe Oliveira do Nascimento, G. Rodrigues Bezerra da Costa, K. Santos da Silva, A. M. Salgueiro Baptisttella, M. Gomes Ghislandi and M. Alves da Motta Sobrinho, Chem. Eng. Commun., 2019, 206, 1375–1387 CrossRef.
- S. T. Yang, S. Chen, Y. Chang, A. Cao, Y. Liu and H. Wang, J. Colloid Interface Sci., 2011, 359, 24–29 CrossRef CAS PubMed.
- M. Sivakumar, S. Yadav, W. S. Hung and J. Y. Lai, J. Cleaner Prod., 2020, 263, 121498 CrossRef CAS.
-
P. Ranjan, J. Balakrishnan and A. D. Thakur, Materials Today: Proceedings, Elsevier Ltd, 2019, vol. 11, pp. 833–836 Search PubMed.
- H. Kalita, H. Tyagi and M. Aslam, Environ. Sci.: Water Res. Technol., 2020, 6, 963–975 RSC.
- Y. Zheng, B. Cheng, W. You, J. Yu and W. Ho, J. Hazard. Mater., 2019, 369, 214–225 CrossRef CAS PubMed.
- B. Mu, J. Tang, L. Zhang and A. Wang, Sci. Rep., 2017, 7, 1–12 CrossRef CAS PubMed.
- P. Bradder, S. K. Ling, S. Wang and S. Liu, J. Chem. Eng. Data, 2011, 56, 138–141 CrossRef CAS.
- M. Heidarizad and S. S. Şengör, J. Mol. Liq., 2016, 224, 607–617 CrossRef CAS.
- R. Guo, T. Jiao, R. Li, Y. Chen, W. Guo, L. Zhang, J. Zhou, Q. Zhang and Q. Peng, ACS Sustainable Chem. Eng., 2018, 6, 1279–1288 CrossRef CAS.
- T. Jiao, Y. Liu, Y. Wu, Q. Zhang, X. Yan, F. Gao, A. J. P. Bauer, J. Liu, T. Zeng and B. Li, Sci. Rep., 2015, 5, 1–10 Search PubMed.
- J. Wang, T. Chen, B. Xu and Y. Chen, Appl. Sci., 2020, 10, 8529 CrossRef CAS.
- L. Dhar, S. Hossain, M. S. Rahman, S. B. Quraishi, K. Saha, F. Rahman and M. T. Rahman, J. Phys. Chem. A, 2021, 125, 965 CrossRef PubMed.
- H. Mahajan, S. K. Arumugasamy, A. Panda, V. Sada, M. Yoon and K. Yun, ACS Omega, 2020, 5, 24799–24810 CrossRef CAS PubMed.
- S. Haque, S. Gain, K. Gupta and U. C. Ghosh, Water Qual. Res. J. Can., 2019, 54, 57–69 CrossRef CAS.
- S. M. Goodman, R. Bura and A. B. Dichiara, ACS Appl. Nano Mater., 2018, 1, 5682–5690 CrossRef CAS.
- M. Khajeh and A. Barkhordar, J. Appl. Spectrosc., 2020, 87, 701–707 CrossRef CAS.
- S. K. Sahoo, S. Padhiari, S. K. Biswal, B. B. Panda and G. Hota, Mater. Chem. Phys., 2020, 244, 122710 CrossRef CAS.
- A. R. B. Bayantong, Y. J. Shih, D. C. Ong, R. R. M. Abarca, C. Di Dong and M. D. G. de Luna, Chemosphere, 2021, 274, 129518 CrossRef CAS PubMed.
- C. Lv, J. Zhang, G. Li, H. Xi, M. Ge and T. Goto, Colloids Surf., A, 2020, 585, 124147 CrossRef CAS.
- E. Ruiz-Hitzky, P. Aranda, M. Darder and G. Rytwo, J. Mater. Chem., 2010, 20, 9306–9321 RSC.
- F. Marrakchi, W. A. Khanday, M. Asif and B. H. Hameed, Int. J. Biol. Macromol., 2016, 93, 1231–1239 CrossRef CAS PubMed.
- A. Chakraborty and H. Acharya, Colloids Interface Sci. Commun., 2018, 24, 35–39 CrossRef CAS.
- R. R. Shan, L. G. Yan, Y. M. Yang, K. Yang, S. J. Yu, H. Q. Yu, B. C. Zhu and B. Du, J. Ind. Eng. Chem., 2015, 21, 561–568 CrossRef CAS.
- K. Abdellaoui, I. Pavlovic and C. Barriga, ChemEngineering, 2019, 3, 41 CrossRef CAS.
- R. M. Novais, J. Carvalheiras, D. M. Tobaldi, M. P. Seabra, R. C. Pullar and J. A. Labrincha, J. Cleaner Prod., 2019, 207, 350–362 CrossRef CAS.
- R. M. Novais, G. Ascensão, D. M. Tobaldi, M. P. Seabra and J. A. Labrincha, J. Cleaner Prod., 2018, 171, 783–794 CrossRef CAS.
- M. Attari, S. S. Bukhari, H. Kazemian and S. Rohani, J. Environ. Chem. Eng., 2017, 5, 391–399 CrossRef CAS.
- A. Duta and M. Visa, J. Photochem. Photobiol., A, 2015, 306, 21–30 CrossRef CAS.
- M. Gao, Q. Ma, Q. Lin, J. Chang and H. Ma, Appl. Surf. Sci., 2017, 396, 400–411 CrossRef CAS.
- W. A. Khanday, M. Asif and B. H. Hameed, Int. J. Biol. Macromol., 2017, 95, 895–902 CrossRef CAS PubMed.
- L. Liu, Z. Y. Gao, X. P. Su, X. Chen, L. Jiang and J. M. Yao, ACS Sustainable Chem. Eng., 2015, 3, 432–442 CrossRef CAS.
- Y. Akköz, R. Coşkun and A. Delibaş, J. Mol. Liq., 2019, 287, 110988 CrossRef.
- S. Liu, H. Ge, C. Wang, Y. Zou and J. Liu, Sci. Total Environ, 2018, 628–629, 959–968 CrossRef CAS PubMed.
- Z. Cheng, J. Liao, B. He, F. Zhang, F. Zhang, X. Huang and L. Zhou, ACS Sustainable Chem. Eng., 2015, 3, 1677–1685 CrossRef CAS.
- M. Khan, M. N. Tahir, S. F. Adil, H. U. Khan, M. R. H. Siddiqui, A. A. Al-Warthan and W. Tremel, J. Mater. Chem. A, 2015, 3, 18753–18808 RSC.
- K. Manna and S. Kumar Srivastava, ACS Sustainable Chem. Eng., 2017, 5, 10710–10721 CrossRef CAS.
- S. Gao, W. Zhang, H. Zhou and D. Chen, J. Rare Earths, 2018, 36, 986–993 CrossRef CAS.
- S. Phoemphoonthanyakit, P. Seeharaj, P. Damrongsak and K. Locharoenrat, J. Spectrosc., 2019, 2019, 1–5 CrossRef.
- W. Song, B. Gao, X. Xu, L. Xing, S. Han, P. Duan, W. Song and R. Jia, Bioresour. Technol., 2016, 210, 123–130 CrossRef CAS PubMed.
- X. Liu, S. An, X. Zhou, L. Zhang, Y. Zhang, W. Shi and J. Yang, J. Dispersion Sci. Technol., 2014, 35, 1727–1736 CrossRef CAS.
- A. Ebrahimian Pirbazari, E. Saberikhah and S. S. Habibzadeh Kozani, Water Resour. Ind., 2014, 7–8, 23–37 CrossRef.
- N. N. Nassar, Sep. Sci. Technol., 2010, 45, 1092–1103 CrossRef CAS.
- A. Mahapatra, B. G. Mishra and G. Hota, Ceram. Int., 2013, 39, 5443–5451 CrossRef CAS.
- N. H. Singh, K. Kezo, A. Debnath and B. Saha, Appl. Organomet. Chem., 2018, 32, e4165 CrossRef.
- X. Wan, Y. Zhan, Z. Long, G. Zeng and Y. He, Chem. Eng. J., 2017, 330, 491–504 CrossRef CAS.
- Z. Li, Y. Sun, J. Xing, Y. Xing and A. Meng, J. Hazard. Mater., 2018, 352, 204–214 CrossRef CAS PubMed.
- C. Lei, M. Pi, D. Xu, C. Jiang and B. Cheng, Appl. Surf. Sci., 2017, 426, 360–368 CrossRef CAS.
- R. M. Mohamed, A. Shawky and I. A. Mkhalid, J. Phys. Chem. Solids, 2017, 101, 50–57 CrossRef CAS.
- C. Lei, X. Zhu, Y. Le, B. Zhu, J. Yu and W. Ho, RSC Adv., 2016, 6, 10272–10279 RSC.
- F. Duan, W. Dong, D. Shi and M. Chen, Appl. Surf. Sci., 2011, 258, 189–195 CrossRef CAS.
- H. Wang and Y. Wei, RSC Adv., 2017, 7, 9079–9089 RSC.
- A. Faghihi, M. H. Vakili, G. Hosseinzadeh, M. Farhadian and Z. Jafari, Desalin. Water Treat., 2016, 57, 22655–22670 CrossRef CAS.
- G. Y. Abate, A. N. Alene, A. T. Habte and Y. A. Addis, J. Polym. Environ., 2020, 29, 967–984 CrossRef.
- J. H. Deng, X. R. Zhang, G. M. Zeng, J. L. Gong, Q. Y. Niu and J. Liang, Chem. Eng. J., 2013, 226, 189–200 CrossRef CAS.
- H. Zhang, X. Li, G. He, J. Zhan and D. Liu, Ind. Eng. Chem. Res., 2013, 52, 16902–16910 CrossRef CAS.
- H. Nayebzadeh, F. Naderi and B. Rahmanivahid, J. Inorg. Organomet. Polym. Mater., 2020, 31, 776–789 CrossRef.
- R. Foroutan, S. J. Peighambardoust, Z. Esvandi, H. Khatooni and B. Ramavandi, J. Environ. Chem. Eng., 2020, 104752 Search PubMed.
- S. Ahmadipouya, M. Heidarian Haris, F. Ahmadijokani, A. Jarahiyan, H. Molavi, F. Matloubi Moghaddam, M. Rezakazemi and M. Arjmand, J. Mol. Liq., 2021, 322, 114910 CrossRef CAS.
- B. Rahmanivahid, F. Naderi and H. Nayebzadeh, J. Water Environ. Nanotechnol., 2020, 5, 1–16 CAS.
- J. L. Liu, W. C. Qian, J. Z. Guo, Y. Shen and B. Li, Bioresour. Technol., 2021, 320, 124374 CrossRef CAS PubMed.
- C. Shen, Y. Shen, Y. Wen, H. Wang and W. Liu, Water Res., 2011, 45, 5200–5210 CrossRef CAS PubMed.
- W. Yao, C. Shen and Y. Lu, Compos. Sci. Technol., 2013, 87, 8–13 CrossRef CAS.
- T. Lv and B. Li, J. Polym. Environ., 2020, 29, 1576–1590 CrossRef.
- S. Foroughirad, V. Haddadi-Asl, A. Khosravi and M. Salami-Kalajahi, Polym. Adv. Technol., 2021, 32, 803–814 CrossRef CAS.
- X. Zheng, H. Zheng, R. Zhao, Z. Xiong, Y. Wang, Y. Sun and W. Ding, J. Mol. Liq., 2020, 319, 114161 CrossRef CAS.
- L. W. Jiang, F. T. Zeng, Y. Zhang, M. Y. Xu, Z. W. Xie, H. Y. Wang, Y. X. Wu, F. A. He and H. L. Jiang, Adv. Powder Technol., 2021, 32, 492–503 CrossRef CAS.
- A. H. Jawad, N. N. A. Malek, A. S. Abdulhameed and R. Razuan, J. Polym. Environ., 2020, 28, 1068–1082 CrossRef CAS.
- S. A. Ahmed and E. M. Soliman, Appl. Surf. Sci., 2013, 284, 23–32 CrossRef CAS.
- T. Poursaberi and M. Hassanisadi, Clean: Soil, Air, Water, 2013, 41, 1208–1215 CAS.
- G. J. Joshiba, P. S. Kumar, M. Govarthanan, P. T. Ngueagni, A. Abilarasu and F. Carolin C, Environ. Pollut., 2021, 269, 116173 CrossRef CAS PubMed.
- J. Chen, Q. Cao and X. Han, J. Cleaner Prod., 2021, 287, 125003 CrossRef CAS.
- A. Ansari Mojarad, S. Tamjidi and H. Esmaeili, Int. J. Environ. Anal. Chem., 2020, 00, 1–22 CrossRef.
- P. Mirzapour, B. Kamyab Moghadas, S. Tamjidi and H. Esmaeili, Sep. Sci. Technol., 2020, 00, 1–15 CrossRef.
- L. Ai, H. Yue and J. Jiang, Nanoscale, 2012, 4, 5401–5408 RSC.
- M. Hu, X. Yan, X. Hu, J. Zhang, R. Feng and M. Zhou, J. Colloid Interface Sci., 2018, 510, 111–117 CrossRef CAS PubMed.
- J. Xu, D. Xu, B. Zhu, B. Cheng and C. Jiang, Appl. Surf. Sci., 2018, 435, 1136–1142 CrossRef CAS.
- E. Haque, V. Lo, A. I. Minett, A. T. Harris and T. L. Church, J. Mater. Chem. A, 2014, 2, 193–203 RSC.
- Z. Wang, J. H. Zhang, J. J. Jiang, H. P. Wang, Z. W. Wei, X. Zhu, M. Pan and C. Y. Su, J. Mater. Chem. A, 2018, 6, 17698–17705 RSC.
- L. L. Liu, J. Chen, Y. Zhang, C. X. Yu, W. Du, X. Q. Sun, J. Lou Zhang, F. L. Hu, Y. Mi and L. F. Ma, J. Mater. Chem. A, 2021, 9, 546–555 RSC.
- S. Begum, Z. Hassan, S. Bräse and M. Tsotsalas, Langmuir, 2020, 36, 10657–10673 CrossRef CAS PubMed.
- E. M. Dias and C. Petit, J. Mater. Chem. A, 2015, 3, 22484–22506 RSC.
- W. Xiang, Y. Zhang, Y. Chen, C. J. Liu and X. Tu, J. Mater. Chem. A, 2020, 8, 21526–21546 RSC.
- C. Li, Z. Xiong, J. Zhang and C. Wu, J. Chem. Eng. Data, 2015, 60, 3414–3422 CrossRef CAS.
- M. Oveisi, M. A. Asli and N. M. Mahmoodi, J. Hazard. Mater., 2018, 347, 123–140 CrossRef CAS PubMed.
- E. Haque, J. E. Lee, I. T. Jang, Y. K. Hwang, J. S. Chang, J. Jegal and S. H. Jhung, J. Hazard. Mater., 2010, 181, 535–542 CrossRef CAS PubMed.
- M. Tong, D. Liu, Q. Yang, S. Devautour-Vinot, G. Maurin and C. Zhong, J. Mater. Chem. A, 2013, 1, 8534–8537 RSC.
- X. Zhao, S. Liu, Z. Tang, H. Niu, Y. Cai, W. Meng, F. Wu and J. P. Giesy, Sci. Rep., 2015, 5, 1–10 CAS.
- J. Abdi, M. Vossoughi, N. M. Mahmoodi and I. Alemzadeh, Chem. Eng. J., 2017, 326, 1145–1158 CrossRef CAS.
- J. Zhao, L. Xu, Y. Su, H. Yu, H. Liu, S. Qian, W. Zheng and Y. Zhao, J. Environ. Sci., 2021, 101, 177–188 CrossRef PubMed.
- A. Muhammad, A. ul H. A. Shah and S. Bilal, Materials, 2019, 12, 2854 CrossRef CAS PubMed.
- S. Dutta, S. K. Srivastava and A. K. Gupta, Mater. Adv., 2021, 2, 2431–2443 RSC.
- K. T. Kubra, M. S. Salman and M. N. Hasan, J. Mol. Liq., 2021, 328, 115468 CrossRef CAS.
- H. Md. Munjur, M. N. Hasan, M. R. Awual, M. M. Islam, M. A. Shenashen and J. Iqbal, J. Mol. Liq., 2020, 319, 114356 CrossRef CAS.
- P. Bober, I. M. Minisy, U. Acharya, J. Pfleger, V. Babayan, N. Kazantseva, J. Hodan and J. Stejskal, Synth. Met., 2020, 260, 116266 CrossRef CAS.
- S. Acharya, S. Sahoo, S. Sonal, J. H. Lee, B. K. Mishra and G. C. Nayak, Composites, Part B, 2020, 193, 107913 CrossRef CAS.
- M. Tanzifi, S. H. Hosseini, A. D. Kiadehi, M. Olazar, K. Karimipour, R. Rezaiemehr and I. Ali, J. Mol. Liq., 2017, 244, 189–200 CrossRef CAS.
- M. Saad, H. Tahir, J. Khan, U. Hameed and A. Saud, Ultrason. Sonochem., 2017, 34, 600–608 CrossRef CAS PubMed.
- V. Sharma, P. Rekha and P. Mohanty, J. Mol. Liq., 2016, 222, 1091–1100 CrossRef CAS.
- R. S. Aliabadi and N. O. Mahmoodi, J. Cleaner Prod., 2018, 179, 235–245 CrossRef CAS.
- M. Ayad and S. Zaghlol, Chem. Eng. J., 2012, 204–205, 79–86 CrossRef.
- J. Smita, J. Dipika and K. Shraddha, Int. J. Sci. Eng. Manage., 2016, 1, 1–6 Search PubMed.
- W. A. Amer, M. M. Omran, A. F. Rehab and M. M. Ayad, RSC Adv., 2018, 8, 22536–22545 RSC.
- M. M. Ayad and A. A. El-Nasr, J. Phys. Chem. C, 2010, 114, 14377–14383 CrossRef CAS.
- M. Bhaumik, R. I. McCrindle, A. Maity, S. Agarwal and V. K. Gupta, J. Colloid Interface Sci., 2016, 466, 442–451 CrossRef CAS PubMed.
- V. Janaki, K. Vijayaraghavan, B. T. Oh, K. J. Lee, K. Muthuchelian, A. K. Ramasamy and S. Kamala-Kannan, Carbohydr. Polym., 2012, 90, 1437–1444 CrossRef CAS PubMed.
- M. Bin Yeamin, M. M. Islam, A. N. Chowdhury and M. R. Awual, J. Cleaner Prod., 2021, 291, 125920 CrossRef.
- E. A. El-Sharkaway, R. M. Kamel, I. M. El-Sherbiny and S. S. Gharib, Environ. Technol., 2020, 41, 2854–2862 CrossRef CAS PubMed.
- M. Shabandokht, E. Binaeian and H. A. Tayebi, Desalin. Water Treat., 2016, 57, 27638–27650 CAS.
- P. E. Díaz-Flores, C. J. Guzmán-Álvarez, V. M. Ovando-Medina, H. Martínez-Gutiérrez and O. González-Ortega, Desalin. Water Treat., 2019, 155, 350–363 CrossRef.
- N. Wang, J. Chen, J. Wang, J. Feng and W. Yan, Powder Technol., 2019, 347, 93–102 CrossRef CAS.
- S. Agarwal, I. Tyagi, V. K. Gupta, F. Golbaz, A. N. Golikand and O. Moradi, J. Mol. Liq., 2016, 218, 494–498 CrossRef CAS.
- V. K. Gupta, D. Pathania, N. C. Kothiyal and G. Sharma, J. Mol. Liq., 2014, 190, 139–145 CrossRef CAS.
- L. Wang, X. L. Wu, W. H. Xu, X. J. Huang, J. H. Liu and A. W. Xu, ACS Appl. Mater. Interfaces, 2012, 4, 2686–2692 CrossRef CAS PubMed.
- M. M. Ayad, A. Abu El-Nasr and J. Stejskal, J. Ind. Eng. Chem., 2012, 18, 1964–1969 CrossRef CAS.
- M. M. Ayad and A. A. El-Nasr, J. Nanostruct. Chem., 2012, 3, 1–9 CrossRef.
- M. A. Salem, R. G. Elsharkawy and M. F. Hablas, Eur. Polym. J., 2016, 75, 577–590 CrossRef CAS.
- H. Javadian, M. T. Angaji and M. Naushad, J. Ind. Eng. Chem., 2014, 20, 3890–3900 CrossRef CAS.
- M. R. Patil and V. S. Shrivastava, Desalin. Water Treat., 2016, 57, 5879–5887 CrossRef CAS.
- K. Rachna, A. Agarwal and N. B. Singh, Environ. Nanotechnol., Monit. Manage., 2018, 9, 154–163 Search PubMed.
- M. Vakili, M. Rafatullah, B. Salamatinia, A. Z. Abdullah, M. H. Ibrahim, K. B. Tan, Z. Gholami and P. Amouzgar, Carbohydr. Polym., 2014, 113, 115–130 CrossRef CAS PubMed.
- R. A. A. Muzzarelli, J. Boudrant, D. Meyer, N. Manno, M. Demarchis and M. G. Paoletti, Carbohydr. Polym., 2012, 87, 995–1012 CrossRef CAS.
- V. Janaki, B. T. Oh, K. Shanthi, K. J. Lee, A. K. Ramasamy and S. Kamala-Kannan, Synth. Met., 2012, 162, 974–980 CrossRef CAS.
- P. Kannusamy and S. Thambidurai, Colloids Surf., B, 2013, 108, 229–238 CrossRef CAS PubMed.
- I. M. Lipatova, L. I. Makarova and A. A. Yusova, Chemosphere, 2018, 212, 1155–1162 CrossRef CAS PubMed.
- T. A. Khan and M. Nazir, Environ. Prog. Sustainable Energy, 2015, 34, 1444–1454 CrossRef CAS.
- G. J. Copello, A. M. Mebert, M. Raineri, M. P. Pesenti and L. E. Diaz, J. Hazard. Mater., 2011, 186, 932–939 CrossRef CAS PubMed.
- S. Agarwal, H. Sadegh, M. Monajjemi, A. S. Hamdy, G. A. M. Ali, A. O. H. Memar, R. Shahryari-Ghoshekandi, I. Tyagi and V. K. Gupta, J. Mol. Liq., 2016, 218, 191–197 CrossRef CAS.
- N. Nekouei Marnani and A. Shahbazi, Chemosphere, 2019, 218, 715–725 CrossRef CAS PubMed.
- Z. Eren and F. N. Acar, Desalination, 2006, 194, 1–10 CrossRef CAS.
- M. A. M. Salleh, D. K. Mahmoud, W. A. W. A. Karim and A. Idris, Desalination, 2011, 280, 1–13 CrossRef CAS.
- A. E. Ofomaja and Y. S. Ho, Dyes Pigm., 2007, 74, 60–66 CrossRef CAS.
- S. A. Mazari, E. Ali, R. Abro, F. S. A. Khan, I. Ahmed, M. Ahmed, S. Nizamuddin, T. H. Siddiqui, N. Hossain, N. M. Mubarak and A. Shah, J. Environ. Chem. Eng., 2021, 9, 105028 CrossRef CAS.
- S. Homaeigohar, Nanomaterials, 2020, 10, 1–42 CrossRef PubMed.
- D. Harikishore Kumar Reddy, K. Vijayaraghavan, J. A. Kim and Y. S. Yun, Adv. Colloid Interface Sci., 2017, 242, 35–58 CrossRef CAS PubMed.
- S. Lata, P. K. Singh and S. R. Samadder, Int. J. Environ. Sci. Technol., 2015, 12, 1461–1478 CrossRef CAS.
- Y. Feng, D. D. Dionysiou, Y. Wu, H. Zhou, L. Xue, S. He and L. Yang, Bioresour. Technol., 2013, 138, 191–197 CrossRef CAS PubMed.
Footnote |
† Electronic supplementary information (ESI) available. See DOI: 10.1039/d1ma00354b |
|
This journal is © The Royal Society of Chemistry 2021 |
Click here to see how this site uses Cookies. View our privacy policy here.