DOI:
10.1039/C9RA04623B
(Paper)
RSC Adv., 2019,
9, 22295-22301
Mechanical and self-recovery properties of supramolecular ionic liquid elastomers based on host–guest interactions and correlation with ionic liquid content†
Received
20th June 2019
, Accepted 10th July 2019
First published on 18th July 2019
Abstract
Supramolecular materials have received considerable attention due to their higher fracture energy and self-recovery capability compared to conventional chemically cross-linked materials. Herein, we focus on the mechanical properties and self-recovery behaviours of supramolecular polymeric elastomers swollen with ionic liquid. We also gained insight into the correlation between ionic liquid content and mechanical properties. These supramolecular polymers with ionic liquid can be easily prepared from bulk copolymerization of the host–guest complex (peracetylated cyclodextrin and adamantane derivatives) and alkyl acrylates and subsequent immersion in ionic liquid such as 1-ethyl-3-methylimidazolium bis(trifluoromethylsulfonyl)imide. The supramolecular polymeric elastomers showed a self-recovery ability, which the conventional chemically cross-linked elastomers with ionic liquid cannot achieve.
1. Introduction
Supramolecular materials1–3 have attracted attention for their characteristic properties. Several types of non-covalent bonds such as hydrogen bonds,4 π–π stacking,5,6 electrostatic interactions,7 metal–ligand interactions,8,9 and hydrophobic interactions10 have been used to prepare supramolecular materials. Among those non-covalent bonds, host–guest interaction is one of the most fascinating to construct supramolecular materials. They are especially favourable for self-healing materials.11,12 Crown ethers,13,14 calixarenes,15,16 cucurbiturils,17,18 pillararenes,19,20 and cyclodextrins (CDs)21,22 are typical macrocyclic molecules used as host molecules. We prepared supramolecular materials by polymerization of CD and guest monomers; these materials showed enhanced mechanical properties comparable with covalently cross-linked materials.23
Recently, ionic liquids have been used as solvent in polymer network gels because of their characteristic physicochemical properties, such as negligible volatility, high thermal and electrochemical stability, non-flammability, and great ionic conductivity at room temperature.24–26 The use of ionic liquids in polymer networks prevents leakage of the ionic liquids during practical application.27 There are several methods to incorporate ionic liquids into the polymer networks, such as polymerizing the monomers,28,29 using as polymerization solvents,30–34 and swelling the elastomeric films.35–41
Several reports of ionic gels based on supramolecular chemistry were reported by using ionic bonds,42,43 hydrogen bond,44,45 block copolymers,46,47 and small gelators.48–50 We reported supramolecular materials with self-healing and tough properties,51,52 but most of these materials are hydrogels, which are hard to be applied as electrochemical materials because water in the hydrogels possibly causes short circuit. Here, to overcome this problem, we prepared supramolecular host–guest polymeric elastomers swollen with ionic liquid (A-Acrylate-x). Peracetylated acrylamide-methyl ether-modified γCD host molecules (PAcγCD, Fig. 1a) and 2-ethyl-2-adamanthyl acrylate (Ad) guest molecules were used in the presence of alkyl acrylates to form supramolecular polymeric materials, that is, poly(alkyl acrylate)s tethering the host and guest units as the side chains. 1-Ethyl-3-methylimidazolium bis(trifluoro-methylsulfonyl)imide (EMIm TFSI) was used as ionic liquid for swelling the supramolecular polymeric materials (Fig. 1b).
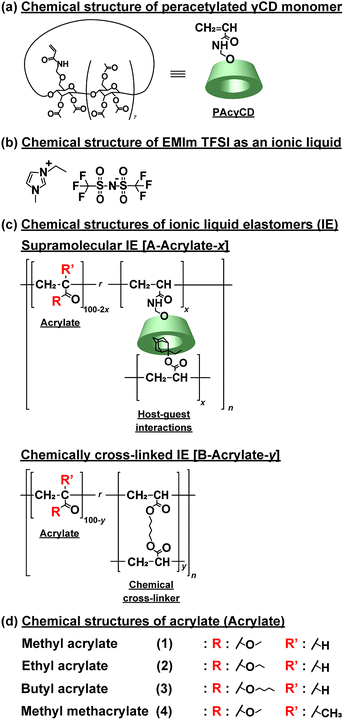 |
| Fig. 1 Chemical structures of (a) peracetylated 6-acrylamido methylether-γCD monomer (PAcγCD) as the host monomer, (b) 1-ethyl-3-methylimidazolium bis(trifluoromethylsulfonyl) imide (EMIm TFSI) as an ionic liquid, and (c) supramolecular polymeric elastomer swollen with EMIm TFSI (A-Acrylate-x) and chemically cross-linked elastomer swollen with EMIm TFSI (B-Acrylate-y). (d) Group of side chain monomers (acrylate): methyl acrylate (1), ethyl acrylate (2), butyl acrylate (3), and methyl methacrylate (4). x and y respectively indicate the mol% content of cross-linking unit of the host–guest inclusion complex (PAcγCD and Ad) and BDA units. | |
Previously, we discussed about the relation between host–guest cross-linking and the ionic conductivity in supramolecular elastomers swollen by ionic liquid (IEs).53 Herein, we focus on the mechanical properties and self-recovery behaviour of supramolecular IEs. We investigated the mechanical properties of these supramolecular IEs with several types of alkyl acrylate side chain polymers (Fig. 1c and d). The A-Acrylate-x showed a lower Young's modulus but a higher fracture energy than chemically cross-linked IEs. The A-Acrylate-x also showed self-recovery properties which cannot be achieved by chemically cross-linked IEs. These self-recovery properties also are a new finding in polymeric ionic liquid materials.
2. Experimental section
2.1. Materials
Methyl acrylate (1), ethyl acrylate (2), n-butyl acrylate (3), and methyl methacrylate (4) were purchased from Toagosei Co., Ltd. γ-Cyclodextrin (γCD) was obtained from Junsei Chemical Co. Ltd. 1-Hydroxy cyclohexyl phenyl ketone (Ciba, IRGACURE 184) was purchased from BASF Japan Co., Ltd. 2-Ethyl-2-adamantyl acrylate (Ad) was obtained from Osaka Organic Chemical Industry Ltd. 1,4-Butanediol diacrylate (BDA), acetic anhydride, and bromoethane were purchased from Nacalai Tesque Inc. Lithium bis(trifluoromethanesulfonyl)imide (LiTFSI) was purchased from Tokyo Chemical Industry Co., Ltd. PAcγCD was prepared according to Scheme S1 in ESI (Fig. S1–S3†). EMIm TFSI was prepared according to Scheme S2 and S3 in ESI (Fig. S4–S8†). Pyridine and CDCl3 were purchased from Wako Pure Chemical Industries, Ltd. DMSO–d6 was obtained from Merck & Co., Inc. Water used for the preparation of the aqueous solutions was purified with a Millipore Elix 5 system. Other reagents were used without further purification.
2.2. Characterization
1H, 13C, and 19F nuclear magnetic resonance (NMR) spectra were recorded at 500 MHz (for 1H), 125 MHz (for 13C), and 470 MHz (for 19F), with a JEOL JNM-ECA 500 spectrometer at 25 °C. 19F NMR spectra were calibrated using the external standard CFCl3 (δ = 0 ppm). Solid-state 1H field gradient magic angle spinning (FGMAS) NMR spectra was recorded at 400 MHz with a JEOL JNM-ECA 400 NMR spectrometer with a sample spinning rate of 7 kHz. In all the solid-state NMR measurements, the chemical shifts were referenced to residual protons values of the deuterated solvent [1H NMR: δ = 0 ppm for tetramethylsilane (TMS) and 2.49 ppm for DMSO-d6; 13C NMR: δ = 0 ppm for TMS and 39.52 ppm for DMSO-d6]. Positive-ion matrix-assisted laser desorption/ionization time-of-flight mass spectrometry (MALDI-TOF MS) experiments were performed using a Bruker autoflex speed mass spectrometer using 2,5-dihydroxybenzoic acid as matrix. The mass number was calibrated by four peptides, i.e., angiotensin II ([M + H]+ 1046.5418), angiotensin I ([M + H]+ 1296.6848), substance P ([M + H]+ 1347.7354), and bombesin ([M + H]+ 1619.8223). The mechanical properties of the IEs were measured using Autograph AG-X plus (Shimadzu Co.) equipped with a 50 N load cell at a specific deformation rate (1.0 mm s−1). The conductivity of the IEs was measured by a Hewlett-Packard 4284A Precision LCR (inductance (L), capacitance (C), and resistance (R)) metre at a frequency of 20 Hz to 1 MHz using a stainless-steel electrode with a sample diameter of 20 mm.
3. Results and discussion
3.1. Preparation of the supramolecular ionic liquid elastomer
The supramolecular polymeric IEs based on CD with guest unit (A-Acrylate-x) were prepared according to our previous report (Scheme S4†).53 Ad as a guest monomer and PAcγCD as a host monomer were mixed and sonicated in an alkyl acrylate monomer to form inclusion complex. Then, bulk radical copolymerization was carried out by using IRGACURE 184 with irradiation of 365 nm UV to produce the supramolecular elastomer. The resulting elastomer was readily immersed in the EMIm TFSI to obtain the supramolecular elastomer swollen with EMIm TFSI, A-Acrylate-x (Table S9†). As control samples, chemically cross-linked IEs (B-Acrylate-y, Fig. 1c and Table S10†), were prepared by the same manner.
The composition ratio in the IEs is indicated by x and y in A-Acrylate-x and B-Acrylate-y, which respectively represent the mol% content of cross-linking unit of the host–guest inclusion complex (PAcγCD and Ad) or BDA. Solid-state 1H FGMAS NMR measurements were carried out to determine the amount of PAcγCD and Ad unit in A-Acrylate-x elastomer and A-Acrylate-x. These amounts coincided with the predefined ratio of the corresponding monomers, indicating that the copolymerization proceeded, quantitatively (Fig. S9–S16†).
3.2. Mechanical properties of the ionic liquid elastomers
The mechanical properties of the A-Acrylate-x were investigated via universal tensile strength test, and the results were compared with the B-Acrylate-y. The stress and strain curves of the A-Acrylate-x and B-Acrylate-y (Fig. S17–S20†) were evaluated while stretching at a tensile speed of 1.0 mm s−1. Then, the Young's modulus and fracture energy were calculated from the stress–strain curve (Table 1, Fig. S21 and S22†).
Table 1 Mechanical properties of supramolecular ionic liquid elastomer (A-Acrylate-1) and chemically cross-linked elastomer (B-Acrylate-1). Acrylate: methyl acrylate (1), ethyl acrylate (2), butyl acrylate (3), and methyl methacrylate (4)
Chemical structures |
Strength/MPa |
Young's modulus/MPa |
Fracture energy/kJ m−2 |
A-1-1 |
0.060 |
0.08 |
180 |
A-2-1 |
0.10 |
0.01 |
310 |
A-3-1 |
0.50 |
0.01 |
3200 |
A-4-1 |
8.0 |
34 |
870 |
B-1-1 |
0.40 |
1.4 |
98 |
B-2-1 |
0.20 |
0.80 |
22 |
B-3-1 |
0.20 |
0.90 |
43 |
B-4-1 |
8.0 |
66 |
750 |
Table 1 shows mechanical properties (ultimate strength, Young's modulus, and fracture energy) of the A-Acrylate-1 and B-Acrylate-1. First, we investigated the relationship between ultimate strength and Young's modulus. Different acrylate groups also showed different ultimate strengths and Young's modulus results. The A-4-1 showed Young's modulus (34 MPa) and ultimate strength (8 MPa) which almost comparable with the chemically cross-linked B-4-1 (Young's modulus: 66 MPa and ultimate strength: 8 MPa).
Another acrylate groups (A-2-1) tended to be more elastic with lower Young's modulus: 0.01 MPa and ultimate strength: 0.1 MPa compared to the chemically cross-linked B-2-1 (Young's modulus: 0.81 MPa and ultimate strength: 0.18 MPa). These results are caused by the apparent lower cross-linking density in the A-Acrylate-x, because the cross-linking points by the CD and Ad units can associate and dissociate freely.
The relationship between the fracture energy and Young's modulus for the A-Acrylate-1 and B-Acrylate-1 also investigated. The A-4-1 showed Young's modulus and fracture energy values comparable with the chemically cross-linked B-4-1. As for fracture energy, the A-3-1 showed a higher fracture energy (3200 kJ m−2) compared to the chemically cross-linked B-3-1 (43 kJ m−2), however they showed lower Young's modulus. Same trends were observed in the A-1-1 and A-2-1. These results showed that the host–guest interactions in the A-Acrylate-x is important to increase the fracture energy of the IEs.
Interestingly, the EMIm TFSI content also takes part in the fracture energy. Fig. 2a shows the relationship between the fracture energy and EMIm TFSI content (wt%) for A-Acrylate-x, and Fig. 2b shows those for B-Acrylate-y. The higher ionic liquid content often lowered the mechanical property values, but at a certain point around 20–60%, local maxima of the fracture energy were observed. Comparison between Fig. 2a and b also shows that in every EMIm TFSI content, A-Acrylate-x shows higher fracture energy than B-Acrylate-y.
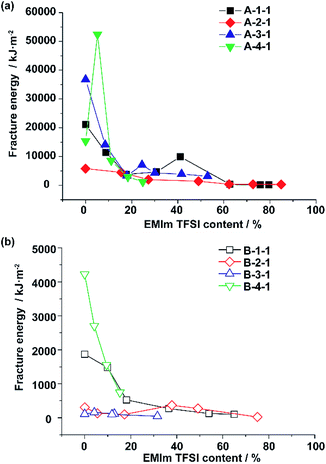 |
| Fig. 2 Relationship between the fracture energy and ionic liquid (EMIm TFSI) content for (a) supramolecular ionic liquid elastomer (A-Acrylate-1) and (b) chemically cross-linked ionic liquid elastomer (B-Acrylate-1). [■: Methyl acrylate (1), : ethyl acrylate (2), : butyl acrylate (3), and : methyl methacrylate (4)]. | |
The A-4-1 showed a local peak of the fracture energy at a 5% ionic liquid content. Additionally, whereas the fracture energy of A-1-1 and A-3-1 also decreased during the addition of ionic liquid content, the fracture energy increased again to show peaks at a 41% and a 24% ionic liquid content, respectively. These results indicate that the host–guest interactions act as noncovalent cross-linkers that associate and dissociate depending on the amounts of EMIm TFSI.
3.3. Stress relaxation behaviour of the ionic liquid elastomers
The behaviour of the CD/Ad host–guest interactions in the IEs was observed using stress relaxation tests for both A-Acrylate-x and B-Acrylate-y. In the stress relaxation test, the IEs were stretched using a universal tensile test machine to a 5% strain and observe the stress relaxation with keeping the strain (5%) for 1 hour. All stress values recorded during the tests were plotted as normalized stress values, in which the initial stresses are normalized as 1 (Fig. 3a).
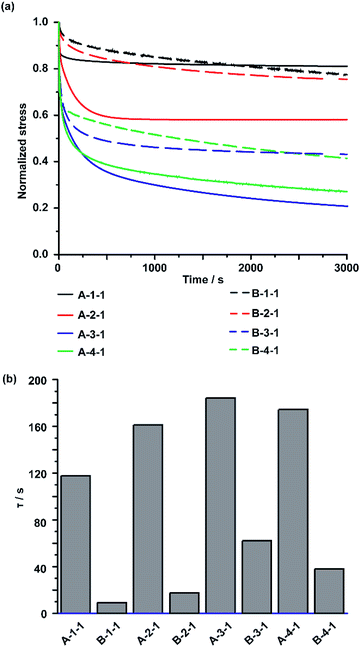 |
| Fig. 3 (a) Stress relaxation behaviour of the supramolecular ionic liquid elastomer (A-Acrylate-1, solid lines) and chemically cross-linked ionic liquid elastomer (B-Acrylate-1, dashed lines) with a 5% strain for 1 hour. (b) Slow relaxation time constant of the A-Acrylate-1 and B-Acrylate-1. Acrylate: methyl acrylate (1), ethyl acrylate (2), butyl acrylate (3), and methyl methacrylate (4). | |
The stress relaxation time constants (τ) were calculated from the curve fitting of the stress relaxation curve profile for exponential decreasing model (ESI section 9†). The A-Acrylate-x showed two relaxation modes. On the other hand, B-Acrylate-y showed single relaxation mode.
Fig. 3b summarizes the τ values. The τ of the slow relaxation mode of A-Acrylate-x (A-1-1: 120 s, A-2-1: 160 s, A-3-1: 180 s, and A-4-1: 170 s) were approximately one order higher than those of the chemically cross-linked B-Acrylate-y (B-1-1: 9.2 s, B-2-1: 17 s, B-3-1: 62 s, and B-4-1: 38 s). These results suggested the presence of slower molecular motions for the A-Acrylate-x due to host–guest interactions. The τ values indicated that A-Acrylate-1 with a smaller size of side chain, such as A-1-1 and A-2-1 showed faster stress relaxation compared to longer size of side chain like A-3-1 and bulky size of side chain like A-4-1, respectively.
As for the other rapid relaxation mode of A-Acrylate-x (shown as τ′ in Fig. S23†), the short τ′ of the A-Acrylate-x supposed to be achieved by the fast association and dissociation of host–guest interactions between PAcγCD and Ad in the elastomer, which should contribute to the effective stress dispersion mechanism of the A-Acrylate-x.
3.4. Correlation between EMIm TFSI content and ionic conductivity of the ionic liquid elastomers
One of the most significant point in utilizing an ionic liquid is that these materials show ionic conductivity properties. The ionic conductivity (σ) was measured using a computer-controlled Hewlett-Packard 4284 Precision LCR metre with a frequency range of 20 Hz to 1 MHz at a temperature of 25 °C, and then σ was calculated using Jonscher's Universal Power Law54,55 (Fig. S24†). The σ of EMIm TFSI as a native ionic liquid, the A-Acrylate-x, and the B-Acrylate-y are shown at Fig. S25.† Herein, we focus on the dependency of EMIm TFSI content on the σ in the A-Acrylate-1 (Fig. 4). We found that there was a critical point, approximately 60% of the EMIm TFSI content, where the σ value drastically increased. This drastic increase only occur in supramolecular polymeric IEs but chemically cross-linked IEs did not show significant increase of σ. Some chemically cross-linked IEs cannot even contain EMIm TFSI at high content (<60%). EMIm TFSI could percolate through the A-1-1 and A-2-1 with a maximum content of over 60%, which makes A-1-1 and A-2-1 show high σ values, whereas the A-3-1 and A-4-1 only contained maximum of 53% and 25% of EMIm, respectively. Therefore, the A-3-1 and A-4-1 showed lower σ values.
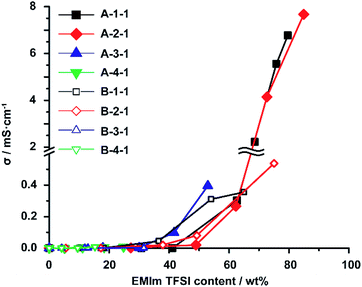 |
| Fig. 4 Relationship between the ionic conductivity (σ) and ionic liquid (EMIm TFSI) content for supramolecular ionic liquid elastomer (A-Acrylate-1) and chemically cross-linked ionic liquid elastomer (B-Acrylate-1). [■: Methyl acrylate (1), : ethyl acrylate (2), : butyl acrylate (3), and : methyl methacrylate (4)]. | |
Fig. 4 also shows that at 65% EMIm TFSI content, A-1-1 (σ = 2.1 mS cm−1) showed higher σ than B-1-1 (σ = 0.40 mS cm−1) and also for around 75% EMIm TFSI content A-2-1 (σ = 4.1 mS cm−1) showed higher σ than B-2-1 (σ = 0.50 mS cm−1). This result proved that A-1-1 and A-2-1 showed higher σ compared to chemically cross-linked B-1-1 and B-2-1 even in the same EMIm TFSI content. This phenomena is caused by reversible and elastic cross-linker in supramolecular polymeric IE makes mobility of substituents of EMIm TFSI are faster compared to mobility of substituents of EMIm TFSI inside the chemically cross-linked IE.
3.5. Self-recovery properties of supramolecular ionic liquid elastomers
Host–guest interactions are popular for their capability as self-recovery material. We also investigated the self-recovery of the A-Acrylate-1. Fig. 5a shows the test procedure for the self-recovery properties. Calculation of recovery ratio (see in Fig. S26 and S27 in ESI†) showed the results obtained from test procedure for the self-recovery properties. The etching method of the self-recovery test was performed using a protocol from our previous report.56 For the first cycle, the A-Acrylate-1 was stretched into half of the plastic deformable region and then rested to the initial state. The A-Acrylate-1 was placed either at room temperature or 80 °C to investigate the temperature dependency on the self-recovery. After 12 hours, for the second cycle, the A-Acrylate-1 was stretched again with the same strain value as the first cycle.
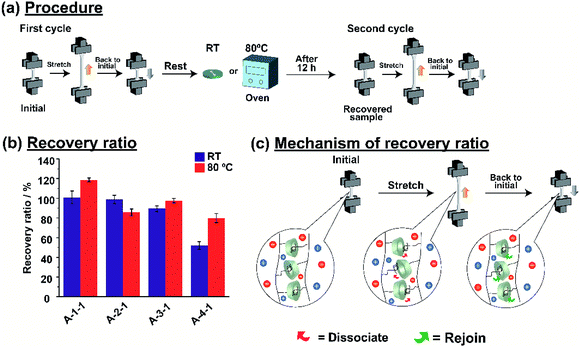 |
| Fig. 5 (a) Procedure for the self-recovery calculation. (b) Recovery ratio for supramolecular ionic liquid elastomer (A-Acrylate-1) after 12 h at room temperature (blue coloured bar) and 80 °C (red coloured bar). (c) Schematic illustration of the self-recovery mechanism. Acrylate: methyl acrylate (1), ethyl acrylate (2), butyl acrylate (3), and methyl methacrylate (4). | |
Fig. 5b shows the recovery ratio of the A-Acrylate-1 after two cycles at room temperature (RT) or 80 °C. The A-1-1 and A-2-1 showed full recovery results (100% and 99%, respectively) after 12 hours at room temperature and at 80 °C, but the A-3-1 and A-4-1 were almost fully recovered (98% and 80%, respectively) only at 80 °C. These results show that A-1-1 and A-2-1 with smaller size of the side chain acrylate show faster stress relaxation compared to B-3-1 and B-4-1, respectively. This phenomena is caused by longer size of side chain like BA and bulky size of side chain like MMA make the inclusion complex of PAcγCD and Ad units harder to re-join again after dissociation.
A-1-1 showed more than 100% recovery ratio after placed at 80 °C, because methyl acrylate is the smallest size of side chain which made self-recovery easier than bigger side chain. This result was also supported by Young's modulus of A-1-1 during self-recovery test (Fig. S28†). After first cycle, A-1-1 showed Young's modulus of 0.07 MPa. For the same sample rested in RT, it showed similar Young's modulus. But, for the sample rested at 80 °C, it showed higher Young's modulus (0.08 MPa) than in the first cycle. These results confirmed that the A-Acrylate-1 shows self-recovery properties.
Fig. 5c illustrates the schematic mechanism of the self-recovery. While the A-Acrylate-1 materials were stretched, several host–guest interactions dissociated. This behaviour contributes to the stress dispersion of the material, resulting in the high fracture energy. During a rest period, those host and guest units re-joined through host–guest interactions to recover the cross-linking again. Thus, the material returned to its original state to show the self-recovery.
4. Conclusions
Supramolecular polymeric IEs were successfully prepared from the bulk copolymerization of host–guest elastomer containing PAcγCD and Ad with immersion in EMIm TFSI. The Young's moduli of the A-Acrylate-x were lower than those of the chemically cross-linked IEs, indicating that the A-Acrylate-x have a flexible cross-linking points. Although low Young's modulus materials are generally soft and brittle with showing low fracture energy, however the fracture energy of the A-Acrylate-x with a low Young's modulus is higher than that of the chemically cross-linked IEs. We concluded that host–guest interactions are an important part of the supramolecular polymeric IEs for preparing flexibly cross-linked materials with a high fracture energy, and these materials can also be self-recovered. A-1-1 and A-2-1 show full recovery results after 12 hours at room temperature and at 80 °C. In the near future, supramolecular polymeric IEs based on host–guest interactions are promising for applications in electrochemical materials.
Conflicts of interest
There are no conflicts to declare.
Acknowledgements
This research was funded by a Grant-in-Aid for Scientific Research (B) (18H02035, 17H03115, 17H03416, and MJMI18E3) from the MEXT of Japan, the Mazda Foundation, and Research Grant Program of the Asahi Glass Foundation (2015 and 2018). We wish to thank Prof. T. Inoue and Dr O. Urakawa of Osaka University for access to the conductivity measurements. We also wish to acknowledge the technical assistance of Dr N. Inazumi for the NMR measurements.
References
- L. Brunsveld, B. J. B. Folmer, E. W. Meijer and R. P. Sijbesma, Chem. Rev., 2001, 101, 4071–4098 CrossRef CAS.
- A. Harada, Supramolecular Polymer Chemistry, Wiley-VCH Verlag & Co. KGaA, Weinheim, 2012 Search PubMed.
- J.-M. Lehn, Polym. Int., 2002, 51, 825–839 CrossRef CAS.
- P. Cordier, F. Tournilhac, C. Soulié-Ziakovic and L. Leibler, Nature, 2008, 451, 977 CrossRef CAS.
- S. Burattini, H. M. Colquhoun, J. D. Fox, D. Friedmann, B. W. Greenland, P. J. F. Harris, W. Hayes, M. E. Mackay and S. J. Rowan, Chem. Commun., 2009, 6717–6719 RSC.
- J. Fox, J. J. Wie, B. W. Greenland, S. Burattini, W. Hayes, H. M. Colquhoun, M. E. Mackay and S. J. Rowan, J. Am. Chem. Soc., 2012, 134, 5362–5368 CrossRef CAS.
- Q. Wang, J. L. Mynar, M. Yoshida, E. Lee, M. Lee, K. Okuro, K. Kinbara and T. Aida, Nature, 2010, 463, 339 CrossRef CAS.
- M. Burnworth, L. Tang, J. R. Kumpfer, A. J. Duncan, F. L. Beyer, G. L. Fiore, S. J. Rowan and C. Weder, Nature, 2011, 472, 334 CrossRef CAS.
- R. J. Wojtecki, M. A. Meador and S. J. Rowan, Nat. Mater., 2010, 10, 14 CrossRef.
- D. C. Tuncaboylu, M. Sari, W. Oppermann and O. Okay, Macromolecules, 2011, 44, 4997–5005 CrossRef CAS.
- X. Chen, M. A. Dam, K. Ono, A. Mal, H. Shen, S. R. Nutt, K. Sheran and F. Wudl, Science, 2002, 295, 1698 CrossRef CAS.
- N. Roy, B. Bruchmann and J.-M. Lehn, Chem. Soc. Rev., 2015, 44, 3786–3807 RSC.
- C. J. Pedersen, J. Am. Chem. Soc., 1967, 89, 7017–7036 CrossRef CAS.
- C. J. Pedersen, J. Am. Chem. Soc., 1967, 89, 2495–2496 CrossRef CAS.
- C. D. Gutsche, B. Dhawan, K. H. No and R. Muthukrishnan, J. Am. Chem. Soc., 1981, 103, 3782–3792 CrossRef CAS.
- X. Yan, F. Wang, B. Zheng and F. Huang, Chem. Soc. Rev., 2012, 41, 6042–6065 RSC.
- W. A. Freeman, W. L. Mock and N. Y. Shih, J. Am. Chem. Soc., 1981, 103, 7367–7368 CrossRef CAS.
- J. Kim, I.-S. Jung, S.-Y. Kim, E. Lee, J.-K. Kang, S. Sakamoto, K. Yamaguchi and K. Kim, J. Am. Chem. Soc., 2000, 122, 540–541 CrossRef CAS.
- T. Ogoshi, T.-a. Yamagishi and Y. Nakamoto, Chem. Rev., 2016, 116, 7937–8002 CrossRef CAS.
- M. Xue, Y. Yang, X. Chi, Z. Zhang and F. Huang, Acc. Chem. Res., 2012, 45, 1294–1308 CrossRef CAS.
- K. Kato, Y. Okabe, Y. Okazumi and K. Ito, Chem. Commun., 2015, 51, 16180–16183 RSC.
- C. Koopmans and H. Ritter, Macromolecules, 2008, 41, 7418–7422 CrossRef CAS.
- A. Harada, Y. Takashima and M. Nakahata, Acc. Chem. Res., 2014, 47, 2128–2140 CrossRef CAS.
- M. Armand, F. Endres, D. R. MacFarlane, H. Ohno and B. Scrosati, Nat. Mater., 2009, 8, 621–629 CrossRef CAS PubMed.
- R. D. Rogers and K. R. Seddon, Science, 2003, 302, 792–793 CrossRef.
- T. Welton, Chem. Rev., 1999, 99, 2071–2083 CrossRef CAS.
- A. Wu, F. Lu, P. Sun, X. Qiao, X. Gao and L. Zheng, Langmuir, 2017, 33, 13982–13989 CrossRef CAS.
- H. Ohno and K. Ito, Chem. Lett., 1998, 27, 751–752 CrossRef.
- J. Y. Yuan and M. Antonietti, Polymer, 2011, 52, 1469–1482 CrossRef CAS.
- A. J. Carmichael, D. M. Haddleton, S. A. F. Bon and K. R. Seddon, Chem. Commun., 2000, 1237–1238 RSC.
- S. Harrisson, S. R. Mackenzie and D. M. Haddleton, Chem. Commun., 2002, 2850–2851 RSC.
- S. Harrisson, S. R. Mackenzie and D. M. Haddleton, Macromolecules, 2003, 36, 5072–5075 CrossRef CAS.
- J. L. Kaar, A. M. Jesionowski, J. A. Berberich, R. Moulton and A. J. Russell, J. Am. Chem. Soc., 2003, 125, 4125–4131 CrossRef CAS.
- A. Noda and M. Watanabe, Electrochim. Acta, 2000, 45, 1265–1270 CrossRef CAS.
- K. Fujii, H. Asai, T. Ueki, T. Sakai, S. Imaizumi, U.-i. Chung, M. Watanabe and M. Shibayama, Soft Matter, 2012, 8, 1756–1759 RSC.
- J. M. Harner and D. A. Hoagland, J. Phys. Chem. B, 2010, 114, 3411–3418 CrossRef CAS.
- J. C. Jansen, K. Friess, G. Clarizia, J. Schauer and P. Izák, Macromolecules, 2011, 44, 39–45 CrossRef CAS.
- M. A. Klingshirn, S. K. Spear, R. Subramanian, J. D. Holbrey, J. G. Huddleston and R. D. Rogers, Chem. Mater., 2004, 16, 3091–3097 CrossRef CAS.
- K. Matsumoto and T. Endo, Macromolecules, 2008, 41, 6981–6986 CrossRef CAS.
- S. Seki, A. B. H. Susan, T. Kaneko, H. Tokuda, A. Noda and M. Watanabe, J. Phys. Chem. B, 2005, 109, 3886–3892 CrossRef CAS.
- M. A. Susan, T. Kaneko, A. Noda and M. Watanabe, J. Am. Chem. Soc., 2005, 127, 4976–4983 CrossRef CAS PubMed.
- X. Li, H. Charaya, G. M. Bernard, J. A. W. Elliott, V. K. Michaelis, B. Lee and H.-J. Chung, Macromolecules, 2018, 51, 2723–2731 CrossRef CAS.
- T. L. Sun, T. Kurokawa, S. Kuroda, A. B. Ihsan, T. Akasaki, K. Sato, M. A. Haque, T. Nakajima and J. P. Gong, Nat. Mater., 2013, 12, 932 CrossRef CAS.
- A. Noro, Y. Matsushita and T. P. Lodge, Macromolecules, 2009, 42, 5802–5810 CrossRef CAS.
- Y. J. Kim, J. H. Kim, M. S. Kang, M. J. Lee, J. Won, J. C. Lee and Y. S. Kang, Adv. Mater., 2004, 16, 1753–1757 CrossRef CAS.
- D. F. Miranda, C. Versek, M. T. Tuominen, T. P. Russell and J. J. Watkins, Macromolecules, 2013, 46, 9313–9323 CrossRef CAS.
- S. P. Zhang, K. H. Lee, C. D. Frisbie and T. P. Lodge, Macromolecules, 2011, 44, 940–949 CrossRef CAS.
- S. Chen, N. Zhang, B. Zhang, B. Zhang and J. Song, ACS Appl. Mater. Interfaces, 2018, 10, 44706–44715 CrossRef CAS PubMed.
- N. Mohmeyer, D. Kuang, P. Wang, H.-W. Schmidt, S. M. Zakeeruddin and M. Grätzel, J. Mater. Chem., 2006, 16, 2978–2983 RSC.
- W. Zhang, C. Yuan, J. N. Guo, L. H. Qiu and F. Yan, ACS Appl. Mater. Interfaces, 2014, 6, 8723–8728 CrossRef CAS PubMed.
- M. Nakahata, Y. Takashima and A. Harada, Macromol. Rapid Commun., 2016, 37, 86–92 CrossRef CAS.
- T. Kakuta, Y. Takashima, M. Nakahata, M. Otsubo, H. Yamaguchi and A. Harada, Adv. Mater., 2013, 25, 2849–2853 CrossRef CAS.
- G. Sinawang, Y. Kobayashi, Y. Zheng, Y. Takashima, A. Harada and H. Yamaguchi, Macromolecules, 2019, 52, 2932–2938 CrossRef CAS.
- M. Greenhoe Brian, K. Hassan Mohammad, S. Wiggins Jeffrey and A. Mauritz Kenneth, J. Polym. Sci., Part B: Polym. Phys., 2016, 54, 1918–1923 CrossRef.
- A. K. Jonscher, Nature, 1977, 267, 673 CrossRef CAS.
- T. Kakuta, Y. Takashima and A. Harada, Macromolecules, 2013, 46, 4575–4579 CrossRef CAS.
Footnote |
† Electronic supplementary information (ESI) available: Preparation and characterization of PAcγCD, EMIm TFSI, and elastomers. Strain and stress curve for A-Acrylate-x and B-Acrylate-y. See DOI: 10.1039/c9ra04623b |
|
This journal is © The Royal Society of Chemistry 2019 |
Click here to see how this site uses Cookies. View our privacy policy here.