DOI:
10.1039/D3RA06701G
(Paper)
RSC Adv., 2024,
14, 2983-2992
Synthesis and characterization of ZrO2–ZnO heterojunction composite for isopropanol detection
Received
2nd October 2023
, Accepted 23rd December 2023
First published on 18th January 2024
Abstract
We prepared ZrO2–ZnO heterojunction composites by a simple hydrothermal method as materials sensitive to isopropanol gas. The 5% ZrO2–ZnO sample presented a uniform rod-like structure. The optimum operating temperature, sensitivity and response/recovery times were measured to investigate the response of ZrO2–ZnO composites to isopropanol. The sensor based on 5% ZrO2–ZnO composites at an optimum temperature of 260 °C had a response to 100 ppm isopropanol of up to 172.46, which was about 3.6 times higher than that of pure ZnO. The sensor also exhibited fast response and recovery times of 5 s and 11 s, respectively. The gas-sensitive properties can be attributed to the rod-like structure, heterojunction structure and catalytic activity of ZrO2. These results would contribute in expanding the application of ZrO2 in gas sensors.
1. Introduction
Isopropanol belongs to the category of volatile organic compounds(VOC), which is an organic, colorless, and flammable liquid.1 It is commonly used as a solvent in paint, cosmetic and pharmaceutical industries2 and as a detergent to remove oil, grease and other treatment dirt from printed circuit boards.3,4 However, isopropanol is a risk to human health and will slightly irritate the airways at concentrations >400 ppm.5 If people are exposed to an environment with high concentrations of isopropanol, they may experience dizziness, lung damage and even coma.6,7 The World Health Organization's International Agency for Research on Cancer published a preliminary compilation of references to their list of carcinogens in 2017. Isopropanol was affirmed as one of the three carcinogens that can be used for early diagnosis of lung cancer by detecting changes in their concentrations in exhaled breath.8,9 The accurate detection of isopropanol will therefore contribute to protecting life.10 Therefore, a series of isopropanol sensors are designed, such as gas chromatography and spectroscopy, which are expensive and exhibit low portability;11 the practice applications are limited. The metal oxide semiconductor (MOS) gas sensors attracts much interesting because of their lower power, high sensitivity, small volume and easy integration.12 Hu et al. have synthesized SnO2 nanorods through the chemical precipitation method, and the response of sensor to 100 ppm isopropanol is about 17.13 Cai et al. have prepared ZnO–CdO composites with a response of about 3.5 to 100 ppm isopropanol.14 Thus, designing high sensitivity isopropanol sensor based on MOS materials is an important research field.
It is well known that common MOS materials, such as In2O3, SnO2, WO3, NiO, Fe2O3 and ZnO, have been used as gas-sensitive materials.15–18 Among them, ZnO is an n-type semiconductor with a 3.7 eV band gap. According to previous reports, ZnO-based gas sensors have the advantages of a high response, short response-recovery time and good selectivity for the detection of toxic and combustible gases.19–22 However, the gas-sensitive performance of ZnO-based sensors is still far from satisfactory in industrial settings.23 Some strategies have been proposed to improve the gas-sensitive properties of semiconductor materials, such as enhancing the specific surface, doping with noble metals and designing heterostructures.24,25
ZrO2, with a wide bandgap of 5.0–5.85 eV, has unique catalytic activities.26,27 ZrO2 possesses four surface properties: acidic, basic, oxidizing and reducing. A series of binary oxide semiconductors, such as (ZrO2–SnO2, ZrO2–In2O3, ZrO2–TiO2 and ZrO2–Al2O3) have been designed for their catalytic activity.26–29 In recent years, binary oxide semiconductors based on ZrO2 and other MOSs have been applied to gas sensing.
Song et al. synthesized In2O3–ZrO2 nanowires via a facile electrospinning strategy. The In2O3–ZrO2 heterojunction showed a fast response to 100 ppm acetone gas with a response time of ∼1 s.26 Jin et al. reported a solution combustion technique to synthesize coral-like macro-/mesoporous ZnO–ZrO2 composites for the detection of isopropanol.7 Shen et al. reported the development of ZrO2-doped ZnO gas-sensitive films via an inkjet printing method; the 3% ZrO2–ZnO film showed the highest sensitivity to 180 ppm acetone, about 2.3 times that of the pure ZnO film.30 Li et al. prepared ZrO2–ZnO nanocomposites via electrostatic spinning. The sensors showed a response of 107 to 100 ppm butanol.31 Wang et al. prepared ZrO2 and ZnO hybrid nanocomposites for designing electrochemical sensors.32 The sensor was highly selective and ultrasensitive for epinephrine, uric acid and folic acid. However, few studies have been conducted to prepare ZrO2–ZnO composites via a facile hydrothermal route for the detection of isopropanol.
We synthesized ZrO2–ZnO heterojunction materials by a simple hydrothermal method and investigated their response to isopropanol. The gas-sensitive mechanisms are discussed based on the catalytic activity of ZrO2, ZrO2–ZnO heterojunction structure and specific surface enhancement of ZnO.
2. Experimental
2.1 Material preparation
The raw materials included zinc nitrate hexahydrate (Zn(NO3)2·6H2O, 99.99%, Sinopharm Chemical Reagent Co), zirconium nitrate pentahydrate (Zr(NO3)4·5H2O, 99.99%, Tianjin Comio Chemical Reagent Co.) and sodium hydroxide (NaOH, 99.9%, Tianjin Fuchen Chemical Reagent Factory Co). Pristine ZnO and ZrO2–ZnO materials were synthesized via a hydrothermal method. The synthetic route of the samples is shown in Fig. 1. First, 1.8 mmol Zn(NO3)2·6H2O(0.535 g), x g Zr(NO3)4·5H2O (x = 0.007 g, 0.023 g, 0.038 g, 0.085 g) and 4 mmol NaOH (0.16 g) were put into 40 mL of deionized water. The precursor solution was obtained after magnetic stirring for about 30 min. Then, the solution was transferred to a 50 mL Teflon-lined autoclave, sealed and heated to 150 °C for 12 h. After the hydrothermal reaction was complete, the reactant was removed from the autoclave and cooled naturally to room temperature. The precipitate was filtered and washed three times with deionized water and anhydrous ethanol and finally dried in an oven at 60 °C for 10 h. At last, the samples were placed in a muffle furnace and calcined to 400 °C at 2 °C min−1 for 2 h. Pristine ZnO and x% ZrO2–ZnO (x = 3, 5 and 7) nanocomposites were thus obtained.
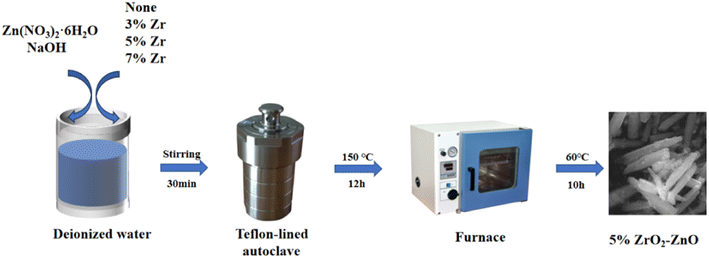 |
| Fig. 1 Flow diagram of the preparation method for ZnO-based sensor materials. | |
2.2 Characterization of materials
The crystalline structures of the samples were analyzed by X-ray diffraction (XRD, Rigaku Ultima IV X-ray diffractometer) with Cu Kα radiation (λ = 1.541 Å; 40 kV, 40 mA). The morphology of the prepared samples was characterized by field-emission scanning electron microscopy (SEM, FEI QUANTA FEG 450), transmission electron microscopy (TEM, JEM-F200) and high-resolution transmission electron microscopy (HRTEM, JED-2300T) with selected-area electron diffraction (SAED). The relative chemical compositions and distributions of different elements were evaluated by X-ray photoelectron spectroscopy (XPS, Thermo Scientific K-Alpha spectrometer, Al Kα source, 1486.6 eV) and X-ray energy spectrometry (Oxford X-MAX50). The gas-sensitive properties of the samples were measured with a chemical gas sensor-8 type intelligent gas analysis system (CGS-8, SINO AGGTECH).
2.3 Sensor manufacturing characteristics
Fig. 2 shows the composition of the gas sensor and test procedure. The gas sensor consists of a pair of ceramic tubes with gold electrodes. The layer of sensitive material is put on the surface of the ceramic tubes. The nichrome alloy coil heater is used for temperature regulation. An appropriate amount of sample is mixed with a 9
:
1 mixture of deionized water and anhydrous ethanol to form a paste, which is then coated on the ceramic tube. After drying, the ceramic tube with the sensing material is placed in a muffle furnace and annealed at 400 °C for 2 h to obtain a gas sensor. The sensor is aged in air at 200 °C for 7 days. The sensing response is defined as the relative change in the resistance of the sensing material in air and gas: S = Rg/Ra, where Ra and Rg are the resistance values of the sensor in air and in the target gas, respectively. The process of gas testing is shown in Fig. 2. First, the corresponding concentration of gas is pumped into a glass bottle using a syringe. The sensor is then quickly put into the glass bottle and the response is observed.
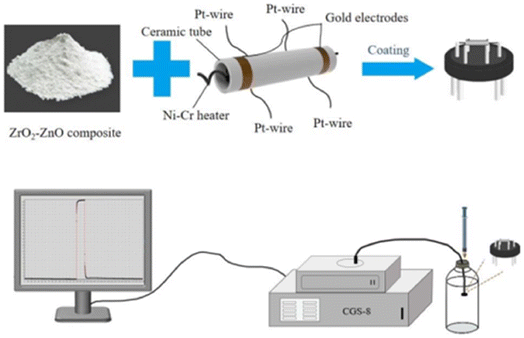 |
| Fig. 2 Schematic diagram of sensor fabrication and gas testing. | |
3. Result and discussion
3.1 Structure and morphology
The XRD patterns of pure ZnO and ZrO2–ZnO nanocomposites are shown in Fig. 3(a). The phase composition and lattice constants of the samples were analyzed through the XRD data. As seen in Fig. 3(a), pure ZnO and ZrO2–ZnO nanocomposites showed clear diffraction peaks at 31.8°, 34.4°, 36.2°, 47.5°, 56.6°, 62.9°, 66.4°, 67.9°, 69.1°, 72.5°, and 77.0°, corresponding to (100), (002), (101), (102), (110), (103), (200), (112), (201), (004) and (202) crystal planes. According to the standard card JCPDS no. 36-1451, all diffraction peaks correspond to hexagonal fibrillated ZnO. No additional peak appears in the XRD spectrum, which indicates that ZnO and ZrO2–ZnO nanocomposites are pure phase. In addition, no diffraction peak of ZrO2 is observed in the XRD patterns, which may be due to the better dispersion of elemental Zr in ZnO or low doping concentration of ZrO2.
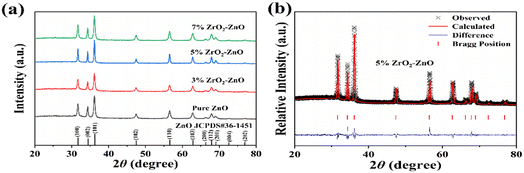 |
| Fig. 3 (a) XRD patterns of the pure ZnO and x% ZrO2–ZnO (x = 3, 5, 7) samples. (b) Rietveld plots with 5% ZrO2–ZnO. | |
XRD Rietveld refinement of the 5% ZrO2–ZnO sample was performed using the visualized electronic structure analysis (VESTA) procedure. The calculated patterns and Bragg position difference plots are shown in Fig. 3(b). In addition, pure ZnO and 3% and 7% ZrO2–ZnO were also calculated. The lattice parameters and feasibility factors (χ2, GOF and Rwp/%) are given in Table 1. The results of feasibility factors satisfied the reasonable value interval, and therefore, the calculated lattice parameters were reliable. The lattice volumes of pure ZnO and ZrO2–ZnO samples were very similar, and therefore, the Zr4+ ions do not substitute at the location of Zn2+. ZrO2 is distributed on the surface of ZnO, and the ZrO2–ZnO junction forms a p–n heterostructure.
Table 1 Refinement lattice parameters of pure ZnO and x% ZrO2–ZnO (x = 3, 5, 7) samples
Sample |
a, Å |
b, Å |
c, Å |
V, Å3 |
α = β |
γ |
Z |
χ2 |
GOF |
Rwp, % |
ZnO |
3.2516 |
3.2516 |
5.210040 |
47.706 |
90° |
120° |
2 |
1.65 |
1.29 |
6.381 |
3% ZrO2–ZnO |
3.2480 |
3.2480 |
5.2040 |
47.544 |
90° |
120° |
2 |
1.50 |
1.23 |
6.169 |
5% ZrO2–ZnO |
3.25178 |
3.25178 |
5.21096 |
47.7190 |
90° |
120° |
2 |
2.28 |
1.51 |
7.563 |
7% ZrO2–ZnO |
3.2454 |
3.2454 |
5.1988 |
47.420 |
90° |
120° |
2 |
0.98 |
0.99 |
7.236 |
The morphologies of ZnO, 3% ZrO2–ZnO, 5% ZrO2–ZnO and 7% ZrO2–ZnO are shown in Fig. 4. The particle morphology of pure ZnO shows a non-uniform sheet-like structure. The particle morphology of ZrO2–ZnO is influenced by the dopant concentration of ZrO2. The particle morphology of the sample is very similar to that of ZnO. However, the particle morphology of the 5% ZrO2–ZnO sample presents a uniform elongated rod-like structure. The length of a single rod reaches about 1.2 μm. Once the dopant concentration of ZrO2 reaches 7%, the rod-like structure still exists, but the length of a single rod is short. Therefore, ZrO2 acts as a catalyst in the ZrO2–ZnO system and affects the growth of ZnO.7
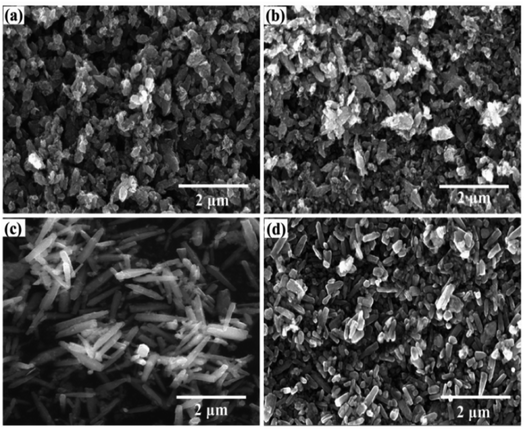 |
| Fig. 4 (a) SEM images of pure ZnO, (b) 3% ZrO2–ZnO2, (c) 5% ZrO2–ZnO2, and (d) 7% ZrO2–ZnO2. | |
Fig. S2 shows the EDS of the 5% ZrO2–ZnO sample. It can be seen that the sample is composed of three elements (Zn, Zr and O), which further indicates that ZrO2 was successfully doped into ZnO with a uniform distribution.
The morphology and structure of the 5% ZrO2–ZnO complexes were investigated using the TEM images to further understand the morphology of the ZrO2–ZnO sample. The composite consists of nanorods about 1.2 μm long (Fig. 5), in agreement with the SEM results. The SAED map (Fig. 5(c), inset) shows that composite oxides have a polycrystalline structure with ring diffraction spots corresponding to ZnO and ZrO2. The high-resolution TEM image in Fig. 5(d) shows lattice stripes with an adjacent spacing of 0.260 nm, which correspond to the (002) facet of fibrillated ZnO, and lattice stripes with an adjacent spacing of 0.284 nm, which may correspond to the (100) face of Zr.33,34 This indicates that ZnO and ZrO2 are tightly connected in the composite. Only two lattice spacings and no other crystalline phase are seen, indicating that the composite oxide is well crystallized.
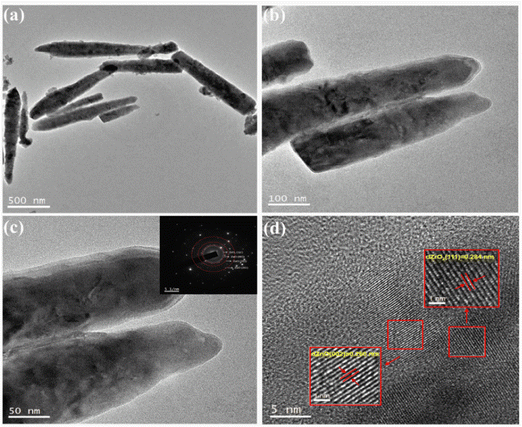 |
| Fig. 5 TEM and HRTEM images of 5% ZrO2–ZnO. Insets are the corresponding selected area electron diffraction (SAED) patterns. | |
To further analyze the elemental composition and chemical morphology of ZrO2–ZnO, the XPS of 5% ZrO2–ZnO was measured (Fig. 6). The Cls peak at 284.8 eV is used as a reference to correct all binding energy positions. Zn, O and Zr peaks were obtained, with no other impurities (Fig. 6(a)). The Zn 2p3/2 peak at 1021.9 eV and the Zn 2p1/2 peak at 1044.9 eV can be observed in the detailed spectra of Zn (Fig. 6(b)), which proves the presence of Zn in the Zn2+ state in the 5% ZrO2–ZnO composite.35–37 Fig. 6(c) shows lattice oxygen (Olat, 530.20 eV), oxygen vacancies (Odef, 531.85 eV) and chemisorbed oxygen species (Oabs, 533.16 eV) in the detailed spectra of O.37–39 Fig. 6(d) clearly shows Zr 3d5/2 and Zr 3d3/2 peaks at 182.26 and 184.64 eV, respectively. The difference between the two peaks is about 2.38 eV, which is in good agreement with the literature values for the Zr4+ state in ZrO2.40,41
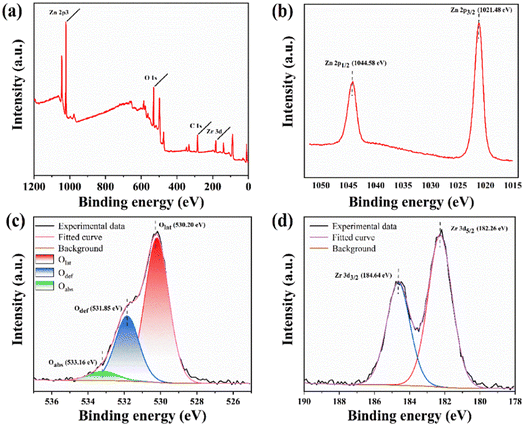 |
| Fig. 6 (a) XPS survey spectrum and detailed spectra of (b) Zn 2p, (c) O 1s and (d) Zr 3d for 5% ZrO2–ZnO. | |
3.2 Gas sensing characteristics
We investigated the gas-sensitive properties of pure ZnO and ZrO2ZnO samples for isopropanol in detail. First, the response values of ZnO and x% ZrO2–ZnO (x = 3, 5, 7) nanocomposites to 100 ppm isopropanol were measured at 240–340 °C (Fig. 7). The responses of all sensors present a pyramidal pattern with increasing operating temperature. It is well known that more energy is available to activate the reaction between the isopropanol molecule and adsorbed oxygen with increasing temperature. The gas response of the sensor therefore increases with temperature. However, desorption of surface oxygen species will occur when the operating temperature exceeds a certain value, which hinders the interaction between the adsorbed oxygen and isopropanol. The gas response therefore decreases at higher temperatures.
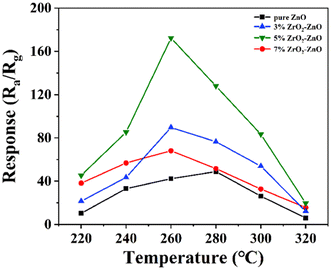 |
| Fig. 7 Response of ZnO doped with different amounts of Zr to 100 ppm isopropanol at different operating temperatures. | |
The pure ZnO sensor exhibits the maximum response of 48.89 to 100 ppm isopropanol at an operating temperature of 280 °C. The sensors with 3% and 7% ZrO2–ZnO composites present a much higher response to 100 ppm isopropanol at 260 °C (89.68 and 68.12, respectively). The sensor with the 5% ZrO2–ZnO composite has the highest response of 172.34 at 260 °C. The response is enhanced 3.53 times compared with pure ZnO, and the operating temperature decreases by 20 °C. The results may be explained by three reasons: (1) the 5% ZrO2–5% ZrO2–ZnO composite with a uniform rod structure exhibits a higher specific surface area than the pure ZnO composite, which produces more adsorbed oxygen and increases the gas response; (2) ZrO2 plays a catalytic role in promoting gas-sensitive reactions; and (3) the ZrO2–ZnO heterojunction structure also plays an important role in enhancing the gas response.42,43 In addition, the responses of all ZrO2–ZnO sensors over the whole temperature range are higher than those of pure ZnO sensors, which indicates that the formed ZrO2–ZnO heterojunction is beneficial to the response of ZnO sensors to isopropanol, and the content of ZrO2 in ZrO2–ZnO affects the response.
The response and recovery times are also key parameters of gas sensors. Fig. 8(a) and (b) show the response-recovery curves of pure ZnO and 5% ZrO2–ZnO in a 100 ppm isopropanol atmosphere at 280 °C and 260 °C, respectively. It can be seen that the response and recovery times of pure ZnO are 9 s and 5 s, respectively, while those of 5% ZrO2–ZnO are 5 s and 11 s, respectively. This indicates that the response time of 5% ZrO2–ZnO is less than that of pure ZnO. The result also proves that the codoped ZrO2 material enhances the isopropanol response rate. The catalytic effect of ZrO2, uniform rod structure and ZrO2–ZnO heterojunction also contribute to a decrease in the response time.
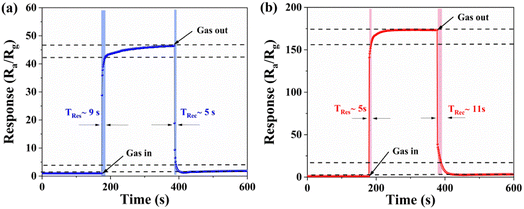 |
| Fig. 8 Dynamic response-recovery curves of the (a) pure ZnO and (b) 5% ZrO2–ZnO sensors to 100 ppm isopropanol at 280 °C and 260 °C. | |
Repeatability is an important performance parameter for gas sensors. The sensor with the 5% ZrO2–ZnO composite was tested several times with 100 ppm isopropanol at an optimum operating temperature of 260 °C. As is shown in Fig. 9(a), the response to isopropanol was almost equal over four cycles, which indicates the good repeatability of the sensor. Each time the sensor returned to the initial value. This will benefit the practical applications of the gas sensor.
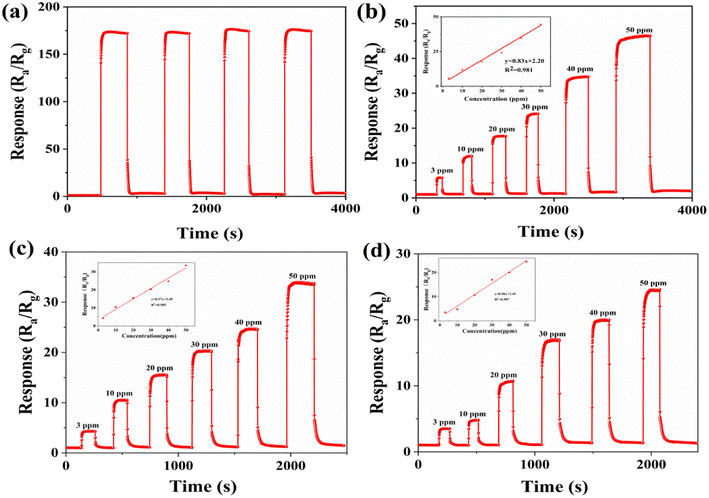 |
| Fig. 9 (a) Dynamic response-recovery curves of the 5% ZrO2–ZnO sensor for a 100 ppm concentration of isopropanol gas. Dynamic response-recovery curves of the (b) 5%, (c) 3% and 7% ZrO2–ZnO sensors for different concentrations of isopropanol gas at the optimum operating temperature. | |
The dynamic response and recovery curves of the 5% ZrO2–ZnO sensor for different concentrations of isopropanol (3–50 ppm) were investigated at 260 °C (Fig. 9(b)). The response of the 5% ZrO2–ZnO sensor reached 5.78 for 3 ppm isopropanol, which indicates that the isopropanol sensor has low detection limit and high sensitivity. The linear relationship between the response values and isopropanol concentrations was fitted (Fig. 9(b)). The least-squares conforming equation was Y = 2.20 + 0.83X (R2 = 0.981). This result shows that a good linear relationship was obtained in the concentration range 3–50 ppm isopropanol. In addition, the 3% and 7% ZrO2ZnO sensor responses for different concentrations of isopropanol were investigated (Fig. 9(c) and (d)). The least-squares conforming of the 3% ZrO2–ZnO sensor was Y = 3.45 + 0.57X (R2 = 0.985) and that of the 7% ZrO2–ZnO sensor was Y = 0.46X + 1.41 (R2 = 0.987). This indicates that all the sensors had a relatively good linearity.
Selectivity is an important parameter of gas sensors. To further evaluate the selectivity of the sensor with the 5% ZrO2–ZnO nanocomposite, the response values of pure ZnO and 5% ZrO2–ZnO sensors were tested for 100 ppm of different gases, including isopropanol (CH3CHOHCH3), methanol (CH3OH), formaldehyde (HCHO), toluene (C7H8) and xylene (C8H10). As shown in Fig. 10, the 5% ZrO2–ZnO nanocomposite sensor had the highest response (172.46) to isopropanol. The sensitivities for other gases was <10. Therefore, the 5% ZrO2–ZnO nanocomposite sensor presents a good selectivity for isopropanol.
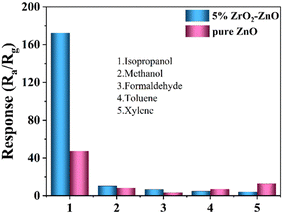 |
| Fig. 10 Selectivity of the 5% ZrO2–ZnO sensor to 100 ppm isopropanol, methanol, formaldehyde, toluene, and xylene. | |
In addition, the prepared sensors were compared with other sensors, and the results are shown in Table 2. It can be found that the ZrO2–ZnO isopropanol sensor prepared in this work had the highest response when compared with previous ZnO gas sensors.
Table 2 Comparison of the gas sensing performance of our sensor and those reported in previous literature
Material |
Temp. (°C) |
Target gas |
Conc. (ppm) |
Response (Ra/Rg) |
Ref. |
Au–ZnO |
300 |
Isopropanol |
100 |
160 |
44 |
SnO2–ZnO |
300 |
Isopropanol |
500 |
98 |
45 |
CdS NP–ZnO PNs |
320 |
Isopropanol |
100 |
33 |
46 |
NiO–ZnO |
280 |
Isopropanol |
100 |
57 |
47 |
ZnO |
320 |
Ethanol |
100 |
3.3 |
48 |
Co–ZnO |
300 |
Ethanol |
100 |
90.71 |
49 |
Fe–ZnO nanostructure |
370 |
Ethanol |
100 |
45 |
50 |
ZrO2–ZnO |
260 |
Isopropanol |
100 |
172.46 |
This work |
3.3 Gas sensing mechanisms
Generally, the gas-sensitive mechanism of n-type MOSs can be explained based on the electron depletion layer, which mainly involves three components: gas adsorption, electron transfer, and gas desorption.7,31,50 As shown in Fig. 11(a), the oxygen in the air is adsorbed onto the surface of the material when ZnO is exposed to air, which traps free electrons in the conduction band and forms oxygen ions. The process can be described by the following reactions: |
O2(ads) + e− → O2−(ads) (T < 100 °C)
| (2) |
|
O2−(ads) + e− → 2O−(ads) (100 °C < T < 300 °C)
| (3) |
|
O−(ads) + e− →O2−(ads) (T > 300 °C)
| (4) |
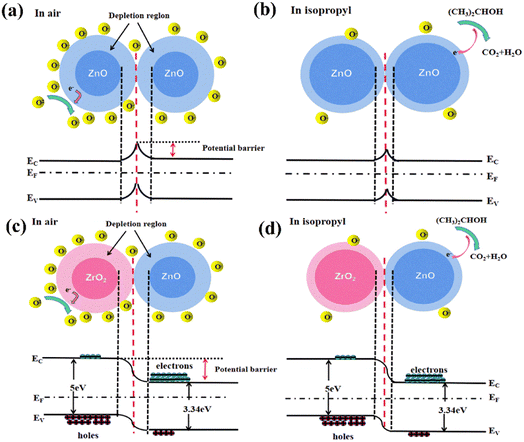 |
| Fig. 11 Sensing mechanism of ZrO2–ZnO composites in air and isopropanol atmosphere. | |
The loss of electrons on the oxide surface results in the formation of a depletion layer and an increase in the potential barrier, which, in turn, results in a higher resistance. When the sensor is exposed to isopropanol, the isopropanol reacts with the oxygen anions on the surface and releases electrons back into the material. The isopropanol is decomposed into oxygen and water, causing the surface depletion layer to decrease and the resistance to decrease; this process can be seen in Fig. 11(b) and described using the following reactions51,52:
|
(CH3)2CHOHgas → (CH3)2CHOHads
| (5) |
|
2(CH3)2CHOHads + 18Oads− → 6CO2 + 8H2O + 18e−
| (6) |
|
(CH3)2CHOHads + 9O2−→ 3CO2 + 4H2O + 18e−
| (7) |
It has previously been reported that the response of gas-sensitive materials is related to the specific surface area. Generally, a large specific surface area produces more absorbed oxygen and the number of active sites involved in the redox reaction will increase,43,48 enhancing the response of the sensitive material. In contrast to pure ZnO, the 5% ZrO2–ZnO nanocomposite with a uniform rod-like structure has a larger specific surface area, which leads to a higher response for isopropanol. All ZrO2–ZnO materials showed a higher response than pure ZnO.
The catalytic effect of ZrO2 should also be considered. Tanabe reported that a methyl group of the absorbed isopropanol and a surface OH group of ZrO2 generate a hydrogen exchange reaction.53 ZrO2 has a role as an acid-based bifunctional catalyst in the activation of the methyl group. Therefore, ZrO2–ZnO samples show a higher response and a faster response time.
The ZrO2–ZnO heterojunction structure also contributes to the increase in the gas response. ZnO is a typical n-type semiconductor, and ZrO2 presents as a p-type semiconductor.40 As shown in Fig. 11(c), the ZrO2–ZnO composites form a p–n heterojunction structure. The electrons in the n-type ZnO and the holes in the p-type ZrO2 move in opposite directions to form built-in power plants, equalizing the Fermi energy levels and bending the energy band. A further increase in resistance is caused by the creation of heterojunctions. The sensor resistance of pure ZnO is 501.04 kΩ in air at 260 °C, while that of 5% ZrO2–ZnO reaches 97.65 MΩ under the same conditions. Consequently, ZrO2–ZnO sensor is exposed to reduced isopropanol, and the combination of the released electrons and holes in ZrO2 will lead to a narrowing of the depletion layer. The sensor resistance of ZrO2–ZnO decreases, and the response is further enhanced.
4. Conclusion
In this paper, pure ZnO and ZrO2–ZnO composites are prepared by a simple hydrothermal method and their structure and morphology is characterized. The morphology of pure ZnO is sheet-like, while the ZrO2–ZnO morphology presents as rod-like. The catalytic effects of ZrO2 may be the key factor in the formation of the rod-like structure. We investigated the gas-sensitive properties of the material to isopropanol. The sensor with 5% ZrO2–ZnO showed good gas-sensitive properties to isopropanol. Compared with pure ZnO, the 5% ZrO2–ZnO sensor achieved the highest response of 172.46 for 100 ppm isopropanol with an optimum operating temperature of 260 °C. The larger specific surface area, the catalytic effect of ZrO2 and the ZrO2–ZnO heterojunction structure are possible reasons for the increased gas response of ZnO materials. These results confirmed that doping with ZrO2 enhances the gas response of MOS materials and provides a new route toward developing gas-sensitive materials.
Conflicts of interest
There are no conflicts to declare.
Acknowledgements
This work was supported by the Natural Science Foundation of China (Grant No. 61705077); Project of Jilin Provincial Science and Technology Department (No. 20200403072SF, 20230508055RC); and Project of Jilin Province Development and Reform Commission (2019C048-4, 2020C021-5)
References
- T. Yang, S. Ma, P. Cao, X. Xu, L. Wang, S. Pei, T. Han, X. Xu, P. Yun and H. Sheng, Synthesis and characterization of ErFeO3 nanoparticles by a hydrothermal method for isopropanol sensing properties, Vacuum, 2021, 185, 110005 CrossRef CAS.
- C. Dong, X. Liu, X. Xiao, G. Chen, Y. Wang and I. Djerdj, Combustion synthesis of porous Pt-functionalized SnO2 sheets for isopropanol gas detection with a significant enhancement in response, J. Mater. Chem. A, 2014, 2, 20089–20095 Search PubMed.
- K. R. Jawaher, R. Indirajith, S. Krishnan, S. K. K. Pasha, K. Deshmukh, D. Sastikumar and S. J. Das, A high sensitivity isopropanol vapor sensor based on Cr2O3-SnO2 heterojunction nanocomposites via chemical precipitation route, J. Nanosci. Nantechnol., 2018, 18, 5454–5460 CrossRef CAS PubMed.
- W. Bi, W. Xiao and S. Liu, Synthesis of Pt-doped SnO2 flower-like hierarchical structure and its gas sensing properties to isopropanol, J. Mater. Sci., 2021, 56, 1–15 CrossRef.
- N. Jayababu, M. Poloju, J. Shruthi and M. V. R. Reddy, NiO decorated CeO2 nanostructures as room temperature isopropanol gas sensors, RSC Adv., 2019, 9, 13765–13775 RSC.
- J. Zhang, G. Li, J. Liu, Y. Liu, R. Yang, L. Li, Q. Zhao, J. Gao, G. Zhu, B. Zhu and H. Lu, Metal–organic framework-derived mesoporous rGO-ZnO composite nanofibers for enhanced isopropanol sensing properties, Sens. Actuators, B, 2023, 378, 133108 CrossRef CAS.
- Q. Jin, W. Wen, S. Zheng and J. Wu, Enhanced isopropanol sensing of coral-like ZnO-ZrO2 composites, Nanotechnology, 2020, 31, 195502 CrossRef CAS PubMed.
- Z. Zheng, Y. Li, Y. Luo, M. Debliguy and C. Zhang, Facile synthesis of bismuth ferrite nanoparticles for ppm-level isopropanol gas sensor, J. Mater. Sci. Mater. El., 2022, 33, 18507–18521 Search PubMed.
- Z. Khatoon, H. Fouad, O. Y. Alothman, M. Hashem, Z. A. Ansari and S. A. Ansari, Doped SnO2 nanomaterials for e-nose based electrochemical sensing of biomarkers of lung cancer, ACS Omega, 2020, 5, 27645–27654 CrossRef CAS PubMed.
- C. Zhang, Y. Huan, Y. Li, Y. Luo and M. Debliquy, Low concentration isopropanol gas sensing properties of Ag nanoparticles decorated In2O3 hollow spheres, J. Adv. Ceram., 2022, 11, 379–391 CrossRef CAS.
- W. Wang, J. Han, C. Liu, J. Zhou, Y. Ma, X. Li and S. Ruan, An isopropanol sensor based on MOF-derived NiO/NiCoxFe2-xO4 porous nanocube with improved response and selectivity, J. Alloys Compd., 2023, 933, 167734 CrossRef CAS.
- D. Meng, T. Qiao, G. Wang, Y. Shen, X. San, R. Li and F. Meng, Rational design of CuO/In2O3 heterostructures with flower-like structures for low temperature detection of formaldehyde, J. Alloys Compd., 2022, 896, 162959 CrossRef.
- D. Hu, B. Han, R. Han, S. Deng, Y. Wang, Q. Li and Y. Wang, SnO2 nanorods based sensing material as an isopropanol vapor sensor, New J. Chem., 2014, 38, 2443–2450 Search PubMed.
- X. Cai, D. Hu, S. Deng, B. Han, Y. Wang, J. Wu and Y. Wang, Isopropanol sensing properties of coral-like ZnO–CdO composites by flash preparation via self-sustained decomposition of metal–organic complexes, Sens. Actuators, B, 2014, 198, 402–410 CrossRef CAS.
- K. Zhang, S. Qin, P. Tang, Y. Feng and D. Li, Ultra-sensitive ethanol gas sensors based on nanosheet-assembled hierarchical ZnO-In2O3 heterostructures, J. Hazard. Mater., 2020, 391, 122191 CrossRef CAS PubMed.
- S. U. Din, M. Haq, M. Sajid, R. Khatoon, X. Chen, L. Li, M. Zhang and L. Zhu, Development of high-performance sensor based on NiO/SnO2 heterostructures to study sensing properties towards various reducing gases, Nanotechnology, 2020, 31, 395502 CrossRef CAS PubMed.
- C. Dong, R. Zhao, L. Yao, Y. Ran, X. Zhang and Y. Wang, A review on WO3 based gas sensors: Morphology control and enhanced sensing properties, J. Alloys Compd., 2020, 820, 153194 CrossRef CAS.
- B. Salah and A. I. Ayesh, Fabrication of H2S sensitive gas sensors formed of SnO2-Fe2O3 composite nanoparticles, Mater. Chem. Phys., 2021, 266, 124597 CrossRef CAS.
- S. K. Gupta, A. Joshi and M. Kaur, Development of gas sensors using ZnO nanostructures, J. Chem. Sci., 2010, 122, 57–62 CrossRef CAS.
- L. Zhu and W. Zeng, Room-temperature gas sensing of ZnO-based gas sensor: A review, Sens. Actuators, A, 2017, 267, 242–261 CrossRef CAS.
- L. Bie, X. Yan, J. Yin, Y. Duan and Z. Yuan, Nanopillar ZnO gas sensor for hydrogen and ethanol, Sens. Actuators, B, 2007, 126, 604–608 CrossRef CAS.
- T. Gao and T. H. Wang, Synthesis and properties of multipod-shaped ZnO nanorods for gas-sensor applications, Appl. Phys. A: Mater. Sci. Process., 2005, 80, 1451–1454 CrossRef CAS.
- C. Wang, Y. Li, F. Gong, Y. Zhang, S. Fang and H. Zhang, Advances in doped ZnO nanostructures for gas sensor, Chem. Rec., 2020, 20, 1–16 CrossRef.
- Y. Kang, F. Yu, L. Zhang, W. Wang, L. Chen and Y. Li, Review of ZnO-based nanomaterials in gas sensors, Solid State Ionics, 2021, 360, 115544 CrossRef CAS.
- J. Liu, L. Zhang, J. Fan, B. Zhu and J. Yu, Triethylamine gas sensor based on Pt-functionalized hierarchical ZnO microspheres, Sens. Actuators, B, 2021, 331, 129425 CrossRef CAS.
- G. Feng, Y. Che, S. Wang, S. Wang, J. Hu, J. Xiao, C. Song and L. Jiang, Sensitivity enhancement of In2O3/ZrO2 composite based acetone gas sensor: A promising collaborative approach of ZrO2 as the heterojunction and dopant for in-situ grown octahedron-like particles, Sens. Actuators, B, 2022, 367, 132087 CrossRef CAS.
- C. Lou, Z. Li, C. Yang, X. Liu, W. Zheng and J. Zhang, Rational design of ordered porous SnO2/ZrO2 thin films for fast and selective triethylamine detection with humidity resistance, Sens. Actuators, B, 2021, 333, 129572 CrossRef CAS.
- B. Neppolian, Q. Wang, H. Yamashita and H. Choi, Synthesis and characterization of ZrO2–TiO2 binary oxide semiconductor nanoparticles: Application and interparticle electron transfer process, Appl. Catal., A, 2007, 333, 264–271 Search PubMed.
- G. Li, W. Li, M. Zhang and K. Tao, Characterization and catalytic application of homogeneous nano-composite oxides ZrO2–Al2O3, Catal. Today, 2004, 93, 595–601 CrossRef.
- W. Shen, Y. Zhao and C. Zhang, The preparation of ZnO based gas-sensing thin films by ink-jet printing method, Thin Solid Films, 2005, 483, 382–387 CrossRef CAS.
- W. Li, Y. Ren and Y. Guo, ZrO2/ZnO nanocomposite materials for chemiresistive butanol sensors, Sens. Actuators, B, 2020, 308, 127658 CrossRef CAS.
- Q. Wang, H. Si, L. Zhang, L. Li, X. Wang and S. Wang, A fast and facile electrochemical method for the simultneous detection of epinephrine, uric acid and folic acid based on ZrO2/ZnO nanocomposites as sensing material, Anal. Chim. Acta, 2020, 1104, 69–77 CrossRef CAS PubMed.
- F. Meng, N. Hou, Z. Jin, B. Sun, W. Li, X. Xiao, C. Wang, M. Li and J. Liu, Sub-ppb detection of acetone using Au-modified flowerlike hierarchical ZnO structures, Sens. Actuators, B, 2015, 219, 209–217 CrossRef CAS.
- J. Zhang, L. Li, Z. Xiao, D. Liu, S. Wang, J. Zhang, Y. Hao and W. Zhang, Hollow sphere TiO2–ZrO2 prepared by self-assembly with polystyrene colloidal template for both photocatalytic degradation and H2 evolution from water splitting, ACS Sustainable Chem. Eng., 2016, 4, 2037–2046 CrossRef CAS.
- B. Han, X. Liu, X. Xing, N. Chen, X. Xiao, S. Liu and Y. Wang, A high response butanol gas sensor based on ZnO hollow spheres, Sens. Actuators, B, 2016, 237, 423–430 CrossRef CAS.
- Y. Gong, X. Wu, X. Li, M. Zhang and Y. Chen, Enhanced acetone sensing properties of Pt@Al-doped ZnO core-shell nanoparticles, Sens. Actuators, B, 2020, 329, 129153 CrossRef.
- Q. Li, D. Chen, J. Miao, S. Lin, Z. Yu, D. Cui, Z. Yang and X. Chen, Highly sensitive sensor based on ordered porous ZnO nanosheets for ethanol detecting application, Sens. Actuators, B, 2021, 326, 128952 CrossRef CAS.
- Y. Mao, S. Ma, X. Li, C. Wang, F. Li, X. Yang, J. Zhu and L. Ma, Effect of Mn doping on the microstructures and sensing properties of ZnO nanofibers, Appl. Surf. Sci., 2014, 298, 109–115 CrossRef CAS.
- M. Chen, X. Wang, Y. Yu, Z. Pei, X. Bai, C. Sun, R. Huang and L. Wen, X-ray photoelectron spectroscopy and auger electron spectroscopy studies of Al-doped ZnO films, Appl. Surf. Sci., 2000, 158, 134–140 CrossRef CAS.
- G. Poungchan, B. Ksapabutr and M. Panapoy, One-step synthesis of flower-like carbon-doped ZrO2 for visible-light-responsive photocatalyst, Mater. Des., 2016, 89, 137–145 CrossRef CAS.
- Y. Pan, Y. Gao, D. Kong, G. Wang, J. Hou, S. Hu, H. Pan and J. Zhu, Interaction of Au with thin ZrO2 films: Influence of ZrO2 morphology on the adsorption and thermal stability of Au nanoparticles, Langmuir, 2012, 28, 6045–6051 Search PubMed.
- H. Tian, H. Fan, G. Dong, L. Mao and J. Ma, NiO/ZnO p–n heterostructures and gas sensing properties for reduced operating temperature, RSC Adv., 2016, 6, 109091–109098 RSC.
- D. Y. Nadargi, M. S. Tamboli, S. S. Patil, R. B. Dateer, I. S. Mulla, H. Choi and S. S. Suryavanshi, Microwave-Epoxide-Assisted hydrothermal synthesis of the CuO/ZnO heterojunction: a highly versatile route to develop H2S gas sensors, ACS Omega, 2020, 5, 8587–8595 Search PubMed.
- G. Wang, P. Wu, L. Guo, W. Wang, W. Liu, Y. Wang, T. Chen, H. Wang, Y. Xu and Y. Yang, Preparation of Au@ZnO nanofilms by combining magnetron sputtering and post-annealing for selective detection of isopropanol, Chemosensors, 2022, 10, 10060211 Search PubMed.
- M. Poloju, N. Jayababu, E. Manikandan and M. V. R. Reddy, Enhancing the isopropanol gas sensing performance of SnO2/ZnO core/shell nanocomposites, J. Mater. Chem. C, 2017, 10, 2662–2668 RSC.
- H. Zhang, Z. Jin, M. Xu, Y. Zhang, J. Huang, H. Cheng, X. Wang, Z. Zheng and Yi. Ding, Enhanced isopropanol sensing
performance of the CdS nanoparticle decorated ZnO porous nanosheets based gas sensors, IEEE Sens. J., 2021, 21, 13041–13047 CAS.
- X. San, M. Li, D. Liu, G. Wang, Y. Shen, D. Meng and F. Meng, A facile one-step hydrothermal synthesis of NiO/ZnO heterojunction microflowers for the enhanced formaldehyde sensing properties, J. Alloys Compd., 2017, 739, 260–269 CrossRef.
- L. Wang, Y. Kang, X. Liu, S. Zhang, W. Huang and S. Wang, ZnO nanorod gas sensor for ethanol detection, Sens. Actuators, B, 2012, 162, 237–243 CrossRef CAS.
- U. T. Nakate, R. Ahmad, P. Patil, Y. Wang, K. S. Bhat, T. Mahmoudi, Y. T. Yu, E. Suh and Y. Hahn, Improved selectivity and low concentration hydrogen gas sensor application of Pd sensitized heterojunction n-ZnO/p-NiO nanostructures, J. Alloys Compd., 2019, 799, 456–464 CrossRef.
- J. Zhao, T. Yang, Y. Liu, Z. Wang, X. Li, Y. Sun, Y. Du, Y. Li and G. Lu, Enhancement of NO2 gas sensing response based on ordered mesoporous Fe-doped In2O3, Sens. Actuators, B, 2014, 191, 806–812 CrossRef CAS.
- J. Ma, Y. Ren, X. Zhou, L. Liu, Y. Zhu, X. Cheng, P. Xu, X. Li, Y. Deng and D. Zhao, Pt nanoparticles sensitized ordered mesoporous WO3 semiconductor: gas sensing performance and mechanism study, Adv. Funct. Mater., 2018, 7, 1705268 CrossRef.
- Y. Wang, L. Yao, L. Xu, W. Wu, W. Lin, C. Zheng, Y. Feng and X. Gao, Enhanced NO2 gas sensing properties based on Rb-doped hierarchical flower-like In2O3 microspheres at low temperature, Sens. Actuators, B, 2021, 332, 129497 CrossRef CAS.
- K. Tanabe, Surface and catalytic properties of ZrO2, Mater. Chem. Phys., 1985, 13, 347–364 Search PubMed.
|
This journal is © The Royal Society of Chemistry 2024 |
Click here to see how this site uses Cookies. View our privacy policy here.