DOI:
10.1039/D1RA05037K
(Paper)
RSC Adv., 2021,
11, 25943-25950
Bio-synthesis of itaconic acid as an anti-crease finish for cellulosic fiber fabric
Received
29th June 2021
, Accepted 21st July 2021
First published on 27th July 2021
Abstract
Itaconic acid is an organic acid with a wide range of applications in the fields of polymer chemistry, pharmacy, agriculture, textile industry, etc. A bio-synthetic process of itaconic acid production in this study was carried out with Aspergillus terreus K17 having empty palm oil fruit bunches as a feedstock. Bio-synthesis of itaconic acid was compared with commercial maleic acid, itaconic acid and 1, 2, 3, 4-butanetetracarboxylic acid (BTCA) as anti-crease agents with sodium hypophosphate (SHP) as an esterification catalyst for cotton fabric finishing. The results showed that mechanical properties of cotton fabrics treated with bio-synthesized itaconic acid were better than those treated with the commercial ones whereas their whiteness index was lower. The best conditions for crease recovery were obtained from 8% w/v itaconic acid with 8% w/v SHP applied on cotton fabrics with a technique of 2-dip-2-nip, dried at 85 °C for 3 min and cured at 180 °C for 2 min. Even though the anti-crease properties of cotton fabrics treated with bio-synthesized itaconic acid were still lower than those treated with commercial maleic acid and BTCA, the finished cotton fibers retain the mechanical properties of cotton fabric. This study would be beneficial in producing itaconic acid as an eco-friendly anti-crease agent for cotton fabrics from waste empty palm oil fruit bunches by a bio-synthesis process.
1. Introduction
Itaconic acid is one of the 12 building block chemicals that can be produced from either a chemical process or biological process through biological fermentation. Fermentation of carbohydrate or lignocellulose has the potential to be developed into value added chemicals.1 Since the decade of the 1960s, production of itaconic acid by Aspergillus terreus in a biological fermentation process using sugar as a raw material was a success.2 Even though other microorganisms have found to be able to produce itaconic acid, A. terreus is still the most outstanding species. This is because only the A. terreus species can provide the highest production yield, up to 80–86 g L−1.3,4 On the other hand, itaconic acid production by a chemical process can also be carried out in many ways. However, chemical methods usually create environmental problems and cause a reduction in fossil resources. Therefore, if itaconic acid can be produced by a biological process using sugar as its raw material in the production, this could substitute for the chemical process. This would not only reduce environmental problems, but would also reduce production cost and lead to sustainability.
Itaconic acid is used in many industries as it has the potential to be substituted for chemicals derived from fossil resources. In general, it is frequently used in the coating industry5 in the form of polymers, both homopolymers and heteropolymers. Itaconic acid is also used in the property improvement of certain materials such as hydrogels and fibers.6,7 In the textile industry, itaconic acid has been attempted to use as an anti-crease agent for cellulose fibers.8 Cellulose fibers such as cotton, linen and hemp have been popular fibers for a long time as they have many excellent properties, e.g. they are comfortable to wear from their good ventilation, able to absorb moisture well, strong, and durable. In addition, cellulose fibers can be easily dyed with various types of dyes, while their odor fastness depends on the dye used. However, cellulose fibers have a low level of crease recovery or can easily crease and possibly shrink after water absorption. As a result, there have been tremendous studies to improve these weakness properties of cellulose fibers. The approach to improve anti-crease properties of cellulose is usually by crosslinking between cellulose chains, which will give good dimension stability to the fabric. In the past, anti-crease agents commonly used were formaldehyde-based compounds. However, it has been revealed that there are health effects from using formaldehyde in many products. Carboxylic acid compounds were thus used as substitutes for formaldehyde as anti-crease agents.8
The purpose of this study is to produce bio-synthesized itaconic acid from empty palm oil fruit bunches (EPOFB) by separating the acid from the fermentation solution and then applying the acid as an anti-crease finish for cotton fabrics. Itaconic acid is a di-carboxylic compound with a potential of being a crosslink agent in the same manner as 1,2,3,4-butanetetracarboxylic acid (BTCA), a compound that is widely used in the industry.9 However, itaconic acid has an advantage, that is, it can be produced from natural raw materials, which is more environmentally sustainable. Furthermore, it can create many different forms of crosslink bonds resulting in having many different properties, depending on its application with other compounds. The results indicated that agriculture waste EPOFB have the potential to be an alternative substrate to produce itaconic acid that could be effectively utilized as an anti-crease finish for cotton fabrics.
2. Experimental
2.1 Microorganisms and culture
Aspergillus terreus K17 isolated from the soil in Nakorn Ratchasima, Thailand, was stored on Potato Dextrose Agar (PDA). Spore suspension of 1 mL (1 × 107 spores per mL) volume was inoculated into 100 mL of seed medium in 250 mL Erlenmeyer flasks and incubated at 30 °C for 24 h in a rotary shaker at 150 rpm for seed culture preparation. A polyurethane foam cube (0.5 × 0.5 × 0.5 cm3) was prepared for immobilized device and put into 250 mL Erlenmeyer flask. The seed culture was transferred to 250 mL Erlenmeyer flask which contains a culture medium of 50 mL and incubated at 30 °C for 24 h on a rotary shaker at 150 rpm. Afterward, immobilized device was separated by washing it twice with sterile distilled water and transferred into a new culture medium which was operated at 30 °C for 1 h on a rotary shaker at 150 rpm. This would result in a starting culture of immobilized cells of A. terreus K17 to be further used in the fermentation process.
2.2 Preparation of itaconic acid
2.2.1 Preparation of raw materials and sugar solution from empty palm oil fruit bunches. Empty palm oil fruit bunches (EPOFB) obtained from oil extraction plant of Suksomboon Palm Oil Co., Ltd. were used as a raw material in this study. EPOFB were cut by a shredder to obtain a size of 2.5 mm and then were pretreated by a steam explosion machine (Model: FD-97137, KUMAKAI) to eliminate lignin and obtain cellulose according to the method of the previous study.10 Main component analysis, such as cellulose, hemicellulose, lignin and extractive matters was performed according to the TAPPI standard. Afterward, pretreated EPOFB was carried out to the saccharification process to obtain sugar solution10 which was used as reactant in the production of itaconic acid.
2.2.2 Production of itaconic acid. The optimum conditions for itaconic acid production were already investigated by our previous study.10 Fermentation was performed in 3 L air-lift fermenter tank using 60 g L−1 of sugar solution containing 60 g glucose, 0.95 g MgSO4·7H2O, 0.03 g NH4NO3 and 0.004 g CuSO4 at 30 °C, pH 2.5, and aeration rate of 2.0 vvm for 72 h. A high-performance liquid chromatograph (HPLC) with a Bio-Rad Aminex HPX-87H column (300 by 7.8 mm) was used for the quantitative measurement of itaconic acid. The mobile phase was 0.005 N sulfuric acid at a flow rate of 1 mL min−1 and a temperature of 60 °C. Samples were filtered through a 0.25 μm filter prior to HPLC analysis. The standard solution of itaconic acid with 99% purity (Sigma-Aldrich, St. Louis, MO) was prepared for HPLC calibration curve.
2.2.3 Separation of itaconic acid from fermented extract. Itaconic acid produced in the air-lift fermenter tank was separated from the fermented solution by a solvent extraction method, according to the approach of Kaur et al.11 Fermented extract was filtered using filter paper (Whatman) with a pore size of 0.2 μm. Solid phase remaining on filter paper was washed with the de-ionized water in the same volume as fermented extract. The whole volume of acid solution phase was secondly filtered using a syringe filter with a pore size of 0.2 μm. After that n-butanol was added in acid solution with the volume ratio of n-butanol
:
acid solution of 1
:
3 and mixed thoroughly by using a magnetic stirrer for 45 min. The mixture was allowed to settle at room temperature by means of a separatory funnel, resulted in a separation of aqueous and organic phases. The amount of itaconic acid in both phases was quantified by titration with 0.1 M NaOH using a phenolphthalein indicator. Degree of extraction (%E) was also calculated.12
2.2.4 Separation of itaconic acid from fermented extract. Itaconic acid produced in the air-lift fermenter tank was separated from the fermented solution by a solvent extraction method, according to the approach of Kaur et al.11 Fermented extract was filtered using filter paper (Whatman) with a pore size of 0.2 μm. Solid phase remaining on filter paper was washed with the de-ionized water in the same volume as fermented extract. The whole volume of acid solution phase was secondly filtered using a syringe filter with a pore size of 0.2 μm. After that n-butanol was added in acid solution with the volume ratio of n-butanol
:
acid solution of 1
:
3 and mixed by using magnetic stirrer for 45 min. After the separating funnel allowed for 1 h, the mixture was separated into aqueous phase and organic phase. The amount of itaconic acid in two phases was quantified by titration with 0.1 M NaOH using phenolphthalein indicator. Degree of extraction (%E) was calculated.12
2.3 Application of itaconic acid as an anti-crease finish on cotton fabric
2.3.1 Study of the optimum concentration of sodium hypophosphite (NaH2PO2, SHP). Cotton fabrics with fabric weight of 23.81 g m−2 were applied with different anti-crease agents i.e. maleic acid, commercial and bio-synthesized itaconic acid from a laboratory scale at a concentration of 8% w/v with SHP solution at three different concentrations (2, 8 and 18% w/v). Then, the cotton fabric was padded using a dry cure padder (Beijing Textile Equipment Institute, MU504A, China) with a technique of 2-dip-2-nip and was wet picked up to 90%. The padded cotton fabric was dried at 85 °C for 3 min and cured at 160 °C for 2 min. Afterward, characteristic tests of fabrics with and without finishing of anti-crease agents were conducted.
2.3.2 Study of the optimum temperature in curing cotton fabric with anti-crease agents. A solution of maleic acid, commercial and bio-synthesized itaconic acid at a concentration of 8% w/v, mixed with SHP solution at the above-mentioned optimum concentration level. After that, a pad dry cure process was applied for cotton fabric finishing by a dry cure padder with a technique of 2-dip-2-nip using the same wet pick up and drying conditions as the previous section. The curing temperatures at 140, 160, and 180 °C for 2 min were investigated. The characteristic tests of cotton fabrics with and without treatment of anti-crease agents were performed.
2.3.3 Application of BTCA as a commercial anti-crease finish. A solution of 6% w/v BTCA was prepared following the method of Hezavehi et al.13 and mixed with 6% w/v SHP. Then the cotton fabric was finished with a solution of BTCA according to the above padding and drying method followed by curing at 170 °C for 2 min. Characteristics of the treated cotton fabrics were evaluated.
2.4 Characteristics of cotton fabrics finished with anti-creasing finishes
2.4.1 Wrinkle recovery angle (WRA). WRA was calculated according to the standard method of AATCC-66. Cotton fabric was folded and compressed under controlled conditions of time and force to create a folded wrinkle using a WRA instrument. To prepare fabric samples for WRA evaluation, six fabric samples in the warp direction (three face-to-face folds, three back-to-back folds) and six fabric samples in the weft direction (three face-to-face folds, three back-to-back folds) were used totally for 12 specimens. Then folded fabric was suspended in a WRA instrument for a controlled recovery period, after which the recovery angles were recorded and averaged.
2.4.2 Breaking force. Breaking force of the treated cotton fabric was characterized according to ISO 13934-1: 1999 with a tensile testing machine (Shimadzu AGS-J, Japan). Samples were cut into 160 mm × 25 mm and the speed of testing was at 300 mm min−1 with a gauge length of 75 mm.
2.4.3 Tearing strength. Tearing strength was analyzed by a tensile testing machine (Shimadzu AGS-X 10N-10 kN, Japan) according to ISO 13937-2: 2000 standard. Fabric samples were cut into 160 mm × 25 mm. Each sample was cut a 100 mm notch parallel to the length direction from the middle of width direction. Evaluation was settled at the speed of testing at 100 mm min−1 with a gauge length of 100 mm.
2.4.4 Whiteness and yellowness index. The whiteness index (WI) and yellowness index (YIE) of treated cotton fabrics were determined according to AATCC Testing Method 11-2005. The average values from three-time measurement were reported for each sample using an odor measurement equipment (HunterLab MiniScan EZ, USA).
2.4.5 Fourier Transform Infrared spectroscopy. The functional groups of cotton fabric surface were determined by Fourier Transform Infrared spectrophotometer (FTIR) (Thermo Scientific Nicolet IR200, USA) using attenuated total reflection (ATR) mode at wavelength 4000–400 cm−1 and a resolution of 4 cm.
2.4.6 SEM. A scanning electron microscope (SEM) (Hitachi SU8020, Germany) with accelerating voltage of 15 kV was used to observe layer of anti-creasing agent on cotton fibers after finishing and compared with the control cotton.
2.4.7 Water contact angle. The cotton fabrics before and after finishing with bio-synthesized itaconic acid were measured for their water contact angles using a contact angle goniometer (Dataphysics OCA20, Germany) equipped with a camera and using the image capture program of the SCA20 software. Samples were cut into rectangles (1 cm × 5 cm) and then 0.5 μL water droplets from a micro syringe to drop were dropped on the fabric samples. Contact angles were calculated by defining a circle around the drop and recording the tangent angle formed at the fabric surface.
3. Results and discussion
3.1 Itaconic acid production and purification
Itaconic acid with a concentration of 30.45 g L−1 was obtained at aeration rate of 2.0 vvm, initial pH of 2.5 and a temperature of 30 °C within 72 h of fermentation according to previously report.10 The yield and productivity were 0.39 g g−1 and 0.41 g L−1 h−1, respectively. The HPCL chromatogram of bio-synthetic organic acids after filtration in Fig. 1 shows that the main peak is itaconic acid. Purification of itaconic acid was done using a mixture of n-butanol and acid solution at 1
:
3 by volume. Itaconic acid concentration and degree of extraction after purification was 40 g L−1 and 82.42% respectively. This result was consistent with the research by Kaur et al.11 They reported that after purification using n-butanol and acid solution at ratio of 1
:
3, the degree of extraction of itaconic acid produced from corn starch, maize flour, waste potatoes and glucose were 91.95, 42.05, 33.64, and 97.65, respectively.
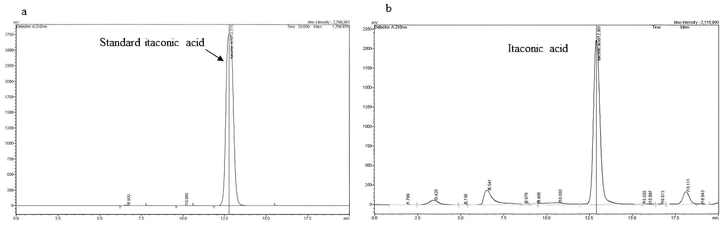 |
| Fig. 1 Chromatogram of organic acid with the main component of commercial (a) and bio-synthetic itaconic acids (b). Sample was injected through Aminex HPX-87H (300 mm × 7.8 mm) columns. Conditions: mobile phase, 0.005 N sulfuric acid; flow rate, 1 mL min−1; column temperature, 60 °C; and detection, refractive index. | |
In this study, carboxylic acid containing compounds which are maleic acid, commercial and bio-synthesized itaconic acids from EPOFB were examined to be used as anti-crease agents for cotton fabrics. They can form ester crosslinking with hydroxyl groups of cellulose fibers and reduce fiber deformation after washing.14 SHP was used as a catalyst for the crosslinking reaction and the optimum amount needs to be investigated.
3.2 The optimum concentration of SHP
The optimum concentration of SHP used in the crosslinking reaction between anti-crease agents and cellulose fibers was considered from characteristics of treated cotton fabrics as shown in Table 1. From WRA results, cotton fabrics treated with maleic acid and SHP gave greater WRA than the control cotton fabric. WRA values from using 2% and 8% SHP were higher than the one from using 18% SHP with a significant difference at a confidence level of 95%. Similar WRA results were obtained when using commercial and bio-synthesized itaconic acids with SHP as a catalyst. Cotton fabrics treated with itaconic acid had higher WRA than the ones without anti-crease agent treatment. When 8% SHP was applied, higher values of WRA were obtained as compared with 18% SHP (p ≤ 0.05). The increase of WRA was a result of crosslinks between maleic acid, commercial and bio-synthesized itaconic acids with cellulose fibers. The mechanism of crosslinking by anti-crease agents can be explained here. The pentagon structure of the anhydride was firstly formed and followed by an esterification reaction forming ester bonds with cellulose fibers15 SHP would act as a catalyst for crosslink forming at 160 °C, resulting in the improvement of anti-crease resistance as shown in Fig. 2.16
Table 1 Characteristics of cotton fabrics treated by different anti-crease agents at various concentrations of sodium hypophosphitea
Test methods |
Control |
8% w/v Maleic acid |
8% w/v Commercial itaconic acid |
8% w/v Bio-synthesized itaconic acid |
SHP (% w/v) |
SHP (% w/v) |
SHP (% w/v) |
2 |
8 |
18 |
2 |
8 |
18 |
2 |
8 |
18 |
The different letters (a, b, c) in the same row mean that the results are significantly different at p ≤ 0.05 by Duncan's multiple-range test. |
Wrinkle recovery angle (degree) |
W + F |
103.92 ± 4.17c |
166.75 ± 10.08a |
159.67 ± 7.30a |
133.33 ± 6.87b |
127.58 ± 8.91ab |
130.42 ± 7.38a |
120.25 ± 7.08b |
113.30 ± 3.77a |
118.88 ± 4.50a |
112.50 ± 8.45a |
Breaking force (N) |
Warp |
276.49 ± 18.28a |
197.06 ± 5.76b |
197.33 ± 8.60b |
206.31 ± 5.99b |
231.84 ± 6.47b |
238.10 ± 4.30b |
259.63 ± 10.83a |
249.16 ± 9.44b |
272.66 ± 6.16a |
234.34 ± 6.50c |
Filling |
151.58 ± 1.81a |
96.03 ± 7.26c |
95.32 ± 8.78c |
113.92 ± 5.84b |
92.06 ± 7.96c |
118.20 ± 8.80b |
112.05 ± 6.60b |
113.28 ± 7.16b |
120.38 ± 8.13b |
122.19 ± 4.31b |
Tear force (N) |
Warp |
6.84 ± 0.18a |
3.78 ± 0.13c |
4.13 ± 0.29bc |
4.79 ± 0.82b |
4.37 ± 0.11c |
4.75 ± 0.13b |
5.24 ± 0.21d |
4.75 ± 0.18c |
5.16 ± 0.32bc |
5.68 ± 0.27b |
Filling |
5.31 ± 0.49a |
2.59 ± 0.09c |
2.65 ± 0.13c |
3.44 ± 0.07b |
3.37 ± 0.23b |
3.53 ± 0.09b |
3.72 ± 0.05b |
3.48 ± 0.18c |
3.61 ± 0.06c |
4.20 ± 0.34b |
Whiteness index |
WIE |
126.32 ± 0.63b |
111.69 ± 3.37c |
109.74 ± 0.95c |
130.14 ± 0.47a |
99.37 ± 0.97d |
119.97 ± 1.62c |
132.84 ± 0.75a |
57.54 ± 4.68d |
76.36 ± 3.61c |
87.46 ± 3.44b |
YIE |
−18.84 ± 0.15b |
−13.11 ± 1.29c |
−12.00 ± 0.51c |
−20.99 ± 0.23a |
−8.13 ± 0.23d |
−16.38 ± 0.59c |
−22.55 ± 0.32a |
12.04 ± 1.77d |
5.33 ± 1.64c |
0.65 ± 1.07b |
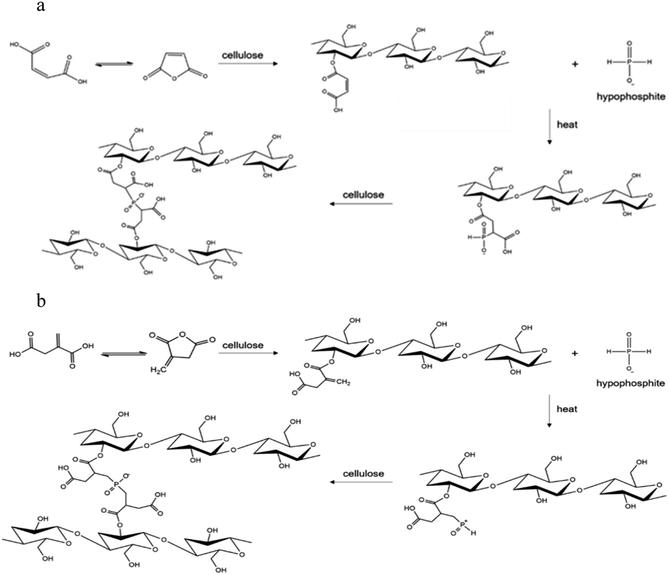 |
| Fig. 2 Crosslinking of cellulose fibers using maleic acid (a), itaconic acid (b) in the presence of hypophosphite. | |
Cotton fabrics treated with anti-crease agents had a lower value of breaking force and tear strength than cotton fabrics without anti-crease agents. This could be because the acidity of these three carboxylic acids containing compounds diminished cotton fiber strengths by hydrolysis of the glycosidic linkage, resulting in de-polymerization of cellulose chains.17 Cotton fabrics before and after anti-crease finishing had a pH of 5.2 and 4.0, respectively. The increase of acidity after finishing indicates that there were some itaconic acids remaining on cotton. However, the values of their strengths tended to increase when the concentration of SHP was higher. The results of itaconic acid were in consistent with other research works. It was found that cotton fabrics with crosslinking from itaconic acid and SHP were able to withstand tearing and breaking forces better than cotton fabrics with crosslinking from formaldehyde-based compounds.17
3.3 The optimum curing temperature of cotton fabrics treated with anti-crease finishes
Cotton fabrics finished with 8% maleic acid and 2% SHP and 8% itaconic acid with 8% SHP were investigated. Table 2 shows that WRA values of finished cotton fabrics increased in order of increasing curing temperatures from 140, 160 and 180 °C and were higher than fabrics without anti-crease agents. This indicates that the higher curing temperatures promoted the esterification reaction between anti-crease agents and cellulose,15 resulting in more effective crosslink forming between SHP and cellulose fibers. However, tearing strength and breaking strength at 180 °C were lower than that at 140 and 160 °C. This suggests that higher temperatures lowered the strength of cotton fabrics. When comparing whiteness index and yellowness index at three different curing temperatures, the whiteness index at 140 °C was highest followed by that at 160 and 180 °C, respectively. For the yellowness index, a curing temperature at 140 °C gave a lower value than that at 160 and 180 °C. The finished cotton fabrics had a higher yellowness index than the ones without. Therefore, it can be proved that when the curing temperature increased, cotton fabrics with anti-crease finishes would have a lower value of whiteness index and a higher value of yellowness index. An increase in yellowness of fabrics finished with itaconic acid when the curing temperature increased could be the result of glucose remaining from the fermentation process. Glucose can undergo non-enzymatic browning reaction or Maillard reaction on the cotton fabric finished with itaconic acid as an anti-crease agent. Furthermore, curing temperatures at higher than 170 °C would result in a caramelization process18 of glucose which could be a reason to have a higher value of yellowness index than unfinished cotton fabric. A particular odor on the cotton fabric was also experienced when bio-synthesized itaconic acid was applied as an anti-crease agent.
Table 2 Characteristics of cotton fabrics treated by different anti-crease agents at various curing temperaturesa
Test methods |
Control |
8% w/v Maleic acid and 2% w/v SHP |
8% w/v Commercial itaconic acid and 8% w/v SHP |
8% w/v Bio-synthesized itaconic acid and 8% w/v SHP |
Curing temperature (°C) |
85 |
140 |
160 |
180 |
140 |
160 |
180 |
140 |
160 |
180 |
W = warp direction, F = filling direction, The different letters (a, b, c) in the same row mean that the results are significantly different at p ≤ 0.05 by the Duncan's multiple-range test. |
Wrinkle recovery angle (degree) |
W + F |
108.83 ± 6.11c |
135.67 ± 7.98b |
161.08 ± 4.28a |
192.75 ± 6.22a |
110.75 ± 2.58c |
123.62 ± 8.50b |
149.67 ± 9.40a |
143.67 ± 7.76b |
156.20 ± 4.09a |
158.20 ± 8.93a |
Breaking force (N) |
W |
296.21 ± 2.05a |
154.08 ± 7.65c |
174.66 ± 5.14b |
149.39 ± 7.06c |
246.16 ± 8.38b |
226.68 ± 5.57c |
207.08 ± 5.08d |
245.90 ± 5.87b |
246.78 ± 10.66b |
220.03 ± 3.78c |
F |
146.84 ± 5.12a |
86.73 ± 9.14b |
69.94 ± 7.12c |
67.55 ± 2.78c |
144.30 ± 6.70a |
127.38 ± 4.93b |
106.36 ± 5.31c |
119.58 ± 9.56b |
117.89 ± 9.23b |
112.66 ± 8.84b |
Tear force (N) |
W |
6.08 ± 0.21a |
3.06 ± 0.06b |
2.90 ± 0.12b |
2.43 ± 0.24c |
5.31 ± 0.40b |
4.34 ± 0.12bc |
4.09 ± 0.18c |
6.12 ± 0.37a |
5.66 ± 0.08b |
5.02 ± 0.18c |
F |
4.60 ± 0.55a |
2.32 ± 0.10b |
2.10 ± 0.09bc |
1.89 ± 0.12c |
3.81 ± 0.07b |
3.37 ± 0.12c |
2.62 ± 0.04d |
4.16 ± 0.17b |
4.10 ± 0.05b |
3.65 ± 0.07b |
Whiteness and yellowness index |
WIE |
123.84 ± 1.20a |
88.12 ± 2.27b |
79.24 ± 0.80c |
64.28 ± 2.35d |
122.24 ± 1.12b |
105.65 ± 0.26c |
96.40 ± 0.96d |
82.66 ± 5.17b |
75.81 ± 7.19b |
52.34 ± 4.67c |
YIE |
−16.44 ± 0.54a |
−2.46 ± 0.94b |
0.73 ± 0.16c |
5.91 ± 0.62d |
−15.97 ± 0.25a |
−9.40 ± 0.01b |
−5.64 ± 0.41c |
1.02 ± 3.57b |
6.23 ± 2.55c |
13.27 ± 1.77d |
3.4 Application of BTCA as a commercial anti-crease finish
BTCA which is a commercial anti-crease agent was applied on cotton fabrics to compare their characteristics with maleic and itaconic acids from the previous section. From the above-mentioned study, optimum conditions for the application of anti-crease agents can be identified which were 8% maleic acid with 2% SHP and 8% commercial and bio-synthesized itaconic acid with 8% SHP, using a curing temperature of 180 °C for 2 min. These characteristics of cotton fabrics were then compared with cotton fabrics finished with 6% BTCA and 6% SHP, using a curing temperature of 170 °C13 which is commonly used in the textile industry.
The cotton fabric treated with commercial BTCA and maleic acid had WRP values higher than that treated by commercial and bio-synthesized itaconic acids (Fig. 3). BTCA is a polycarboxylic acid that can arrange into the pentagon structure of anhydride when heating and form ester bonds between BTCA and cellulose. SHP acted as a catalyst for esterification reaction. Crosslinks between BTCA and cellulose fibers made cotton fabric to have better anti-crease properties (Fig. 4). However, BTCA is synthesized from chemicals while itaconic acid is from bio-synthesis.
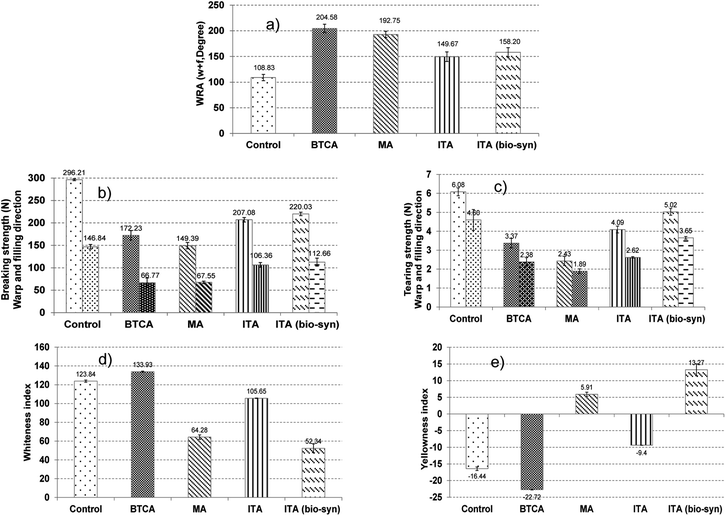 |
| Fig. 3 Mechanical properties and whiteness index of cotton fabrics after finishing with different crosslink agents: (a) wrinkle recovery (b) breaking strength (warp and filling direction) (c) tearing strength (warp and filling direction) (d) whiteness index (e) yellowness index (control: distilled water; BTCA: 6% w/v BTCA, 6% w/v SHP, curing at 170 °C; MA: 8% w/v commercial maleic acid, 2% w/v SHP, curing at 180 °C; ITA: 8% w/v commercial itaconic acid, 8% w/v SHP, curing at 180 °C; ITA (bio-synthesis): 8% w/v bio-synthesized itaconic acid, 8% w/v SHP, curing at 180 °C). | |
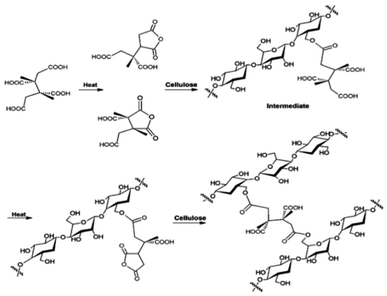 |
| Fig. 4 Crosslinking of cellulose by BTCA in the presence of H2PO2−. Source: reprinted (adapted) with permission from ref. 18. Copyright (2012) American Chemical Society. | |
Breaking strength and tearing strength of cotton fabrics finished with 8% bio-synthesized itaconic acid and 8% SHP at a curing temperature of 180 °C yielded a higher value than that of fabrics treated with commercial BTCA, maleic acid and itaconic acid. This is an advantage to utilize bio-synthesized itaconic acid which fermented from EPOFB waste for anti-creasing in a textile finishing process. However, the whiteness index of cotton fabric treated with bio-synthesized itaconic acid was lower than that treated with commercial anti-crease agents. Impurities from the fermentation process of itaconic acid should be controlled and removed to improve the whiteness index.
FTIR spectroscopy of control cotton fabric as shown in Fig. 5a presented the peaks at 2902 and 1371 cm−1 which were associated with vibration of C–H stretching and C–H bending of cellulose respectively. Also, the other peak at 1600–1700 cm−1 attributed to C–O asymmetric stretching vibration of cellulose. Concerning to crosslink bonds between anti-crease agents together with SHP and cellulose fibers as shown in Fig. 5b–e. The peak at wavenumber of 1640 cm−1 in FTIR spectra was assigned for C
C stretching of crosslinking agents. Peaks at wavenumbers of 1708 and 1720 cm−1 were identified as carbonyl ester formed between carboxylic groups of crosslinking agents with cellulose fibers (as shown above in Fig. 4). These peaks did not exist in the case of cotton fabric without anti-crease finishes (Fig. 5a). The SEM images of the cotton fabric before and after the anti-crease treatment of bio-synthesized itaconic acid were inserted in the Fig. 5. It shows the layer of anti-crease agent coated on cotton fibers (Fig. 5e SEM) compared to the control cotton fabric (Fig. 5a SEM). As this result, based on the average static water contact angle values shown in contact angle images inserted in Fig. 5, the cotton fabric finished by bio-synthetic itaconic acid (Fig. 5e contact angle image) cannot measure static water contact angle due to water drop absorb promptly within 5 second compared to cotton fabric with contact angle of 55°. It means that anti-creasing agent with carboxylic acid coated on cotton fabric showed hydrophilicity all time.
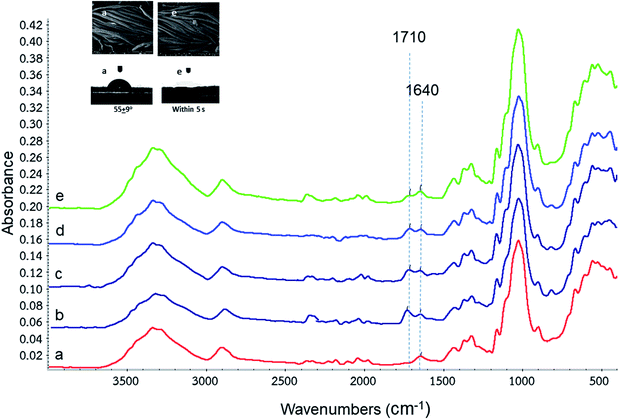 |
| Fig. 5 Infrared spectra of the cotton fabric treated with (a) control, (b) BTCA, (c) maleic, (d) itaconic, and (e) bio-synthesized itaconic acid with the SEM and contact angle images insertion showing the cotton fabric before and after the anti-crease treatment of bio-synthesized itaconic acid. | |
4. Conclusions
From this study, anti-creasing of cotton fabric treated with bio-synthesized itaconic acid from laboratory fermentation of EPOFB waste was compared to commercial anti-crease agents (BTCA, maleic and commercial itaconic acid) using SHP as a catalyst. The optimum concentration of SHP and curing temperature were investigated for each anti-crease finish. The characteristic results of finished cotton fabrics showed that application of bio-synthesized itaconic acid improved wrinkle resistance for cotton fabric and was not significantly different compared to commercial itaconic acid. Moreover, this treatment did not have adverse effect to cotton fibers, as can be seen from better mechanical characteristics than those fabrics treated by commercial anti-crease agents. However, bio-synthetic itaconic acid might not be the best choice for the application on white cotton fabrics due to the occurrence of Maillard reaction from leftover glucose. It should be interesting to conduct a study on itaconic acid that glucose was completely removed before applying as anti-crease finish. A study on the effects of curing temperatures at lower than 180 °C should also be conducted. In addition, alternative renewable resources, such as biomass, agricultural waste materials, could be used in fermentation process. This would provide a good alternative for anti-crease finishing for cotton fabrics that is friendly to the environment.
Author contributions
The project was conceived by Antika Boondaeng, Pilanee Vaithanomsat and Rungsima Chollakup. Experiments of bio-synthesis of itaconic acid were designed by Antika Boondaeng and Pilanee Vaithanomsat. Laboratory work by Chanaporn Trakunjae and Phornphimon Janchai. Application of anti-creasing agent on cotton fabric was carried out by Napassorn Chanka. Fabric characterization was carried out by Thanyachol Apipatpapha. Data analysis was performed by Waraporn Apiwatanapiwat, Antika Boondaeng, and Napassorn Chanka. Manuscript was written by Antika Boondaeng, and Rungsima Chollakup and English edited by Potjanart Suwanruji. All authors have read and agreed to the published version of the manuscript.
Conflicts of interest
There are no conflicts to declare.
Acknowledgements
Research team would like to express our appreciation to the Kasetsart University Research and Development Institute for its support of research funding throughout the research project in the fiscal year of 2018.
References
- T. Werpy and G. Petersen, Top value added chemicals from biomass; volume I-Results of screening for potential candidates from sugars and synthetic gas, National Renewable Energy Lab., Golden, CO, US, 2004 Search PubMed.
- T. Willke and K. D. Vorlop, Appl. Microbiol. Biotechnol., 2001, 56, 289–295 CrossRef CAS PubMed.
- M. Okabe, D. Lies, S. Kanamasa and E. Y. Park, Appl. Microbiol. Biotechnol., 2009, 84, 597–606 CrossRef CAS PubMed.
- A. Kuenz, Y. Gallenmüller, T. Willke and K. D. Vorlop, Appl. Biochem. Biotechnol., 2012, 96, 1209–1216 CAS.
- J. Dai, S. Ma, X. Liu, L. Han, Y. Wu, X. Dai and J. Zhu, Prog. Org. Coat., 2015, 78, 49–54 CrossRef CAS.
- M. Stanojević, M. K. Krušić, J. Filipović, J. Parojčić and M. Stupar, Drug Delivery, 2006, 13, 1–7 CrossRef PubMed.
- A. El-Halah, D. Machado, N. González, J. Contreras and F. López-Carrasquero, J. Appl. Polym. Sci., 2019, 136, 46999 CrossRef.
- Z. Mao and C. Q. Yang, J. Appl. Polym. Sci., 2001, 79, 319–326 CrossRef CAS.
- C. Q. Yang and Y. Lu, Text. Res. J., 1999, 69, 782–789 CrossRef CAS.
- R. Kaur, G. K. Goswami and A. N. Pathak, Int. J. Pure Appl. Biosci., 2015, 3, 242–250 Search PubMed.
- K. Chawong and P. Rattanaphanee, Int. J. Civ. Mech. Eng., 2011, 5, 733–736 Search PubMed.
- E. Hezavehi, S. Shahidi and P. Zolgharnein, Autex Res. J., 2015, 15, 104–111 CrossRef.
- V. A. Dehabadi, H. J. Buschmann and J. S. Gutmann, Text. Res. J., 2013, 83, 1974–1995 CrossRef.
- T. Al-Ameri, A. Najaf, A. Al-Khafaji, J. Zumberge and J. Pitman, Arabian J. Geosci., 2013, 7, 987–1000 CrossRef.
- C. Q. Yang, C. Hu and G. C. Lickfield, J. Appl. Polym. Sci., 2013, 87, 2023–2030 CrossRef.
- I. Kang, C. Q. Yang, W. Wei and G. C. Lickfield, Text. Res. J., 1998, 68, 865–870 CrossRef CAS.
- H. Ajandouz and E. Puigserver, J. Agric. Food Chem., 1999, 47, 1786–1793 CrossRef PubMed.
- H. Peng, C. Q. Yang, X. Wang and S. Wang, Ind. Eng. Chem. Res., 2012, 51, 11301–11311 CrossRef CAS.
|
This journal is © The Royal Society of Chemistry 2021 |
Click here to see how this site uses Cookies. View our privacy policy here.