DOI:
10.1039/D1RA02437J
(Paper)
RSC Adv., 2021,
11, 20541-20549
Methane production from wheat straw pretreated with CaO2/cellulase
Received
27th March 2021
, Accepted 25th May 2021
First published on 8th June 2021
Abstract
There are various lignocellulosic biomass pretreatments that act as attractive strategies to improve anaerobic digestion for methane (CH4) generation. This study proposes an effective technique to obtain more CH4 via the hydrothermal coupled calcium peroxide (CaO2) co-cellulase pretreatment of lignocellulosic biomass. The total organic carbon in the hydrolysate of samples treated with 6% CaO2 and 15 mg enzyme per g-cellulose was 7330 mg L−1, which represented an increase of 92.39% over the total organic carbon value of samples hydrolyzed with the enzyme alone. The promotion of the anaerobic digestion of wheat straw followed this order: hydrothermal coupled CaO2 co-cellulase pretreatment > hydrothermal coupled CaO2 pretreatment > enzymatic pretreatment alone > control group. The sample treated with 6% CaO2 and 15 mg enzyme per g-cellulose gave the highest CH4 production with a CH4 yield of 214 mL g−1 total solids, which represented an increase of 64.81% compared to the control group. The CH4 yield decreased slightly when the amount of added cellulase exceeded 15 mg enzyme per g-cellulose.
Introduction
With the increasing depletion of fossil fuels, there has been a gradual increase in environmental pollution problems caused by modern development. As the world's population grows, the demand for resources is increasing; biomass-based wastes have been studied worldwide in recent decades because they are a potential biomass resource.1 Wastes usually have the advantages of high abundance, low cost and carbon neutrality.2 However, direct incineration is the main technology used to treat biomass, and this treatment method not only generates large amounts of hazardous dust and gases that are harmful to human health and cause air pollution, but also has the potential to cause fires.3 Lignocellulose biomass is an agricultural biomass that provides an important source of energy for the sustainable production of biofuels.4 In the area of lignocellulose biomass, wheat straw is an attractive feedstock for large-scale biological production plants due to its low cost, high sugar content and abundance.5 Every year, a large amount of wheat straw is produced worldwide, and the annual output of wheat straw in China is about 80 million tons.6 Wheat straw is considered to be one of the most promising renewable raw materials for the sustainable production of biomethane (bioCH4) and biohydrogen (bioH2) from biomass.7,8
CH4 gas has a high calorific value, is easy to store, and the only products of its combustion are carbon dioxide and water, which do not cause haze because they do not contain ash. It also has the advantages of high efficiency, cleanliness, economy and safety, and is expected to become one of the most important future resources utilized for clean energy in China. Anaerobic digestion (AD) from waste biomass is an important method to produce CH4 because the process is cost-effective, efficient and reliable.9 Generally speaking, the AD process can be divided into the following four stages: (a) hydrolysis, (b) fermentation (or acidification), (c) acetic acid generation, and (d) CH4 production.10 In this process, hydrolysis is considered to be the rate-limiting step.11 Wheat straw is the part of wheat that remains after harvesting the seeds, and its main components include cellulose, hemicellulose, and lignin (about 85% to 95% of the total mass);12 these three polymers are embedded and cross-linked, and are often called lignocellulose. In addition, wheat straw contains small amounts of crude protein, pectin, fat, ash and moisture, which are linked with each other through various chemical bonds or binding forces.13,14 Therefore, wheat straw should be pretreated to destroy or remove the lignin to reduce its wrapping effect on cellulose and hemicellulose, to break the dense structure. This can reduce the degree of polymerization of the cellulose and increase its accessibility of enzymes to achieve effective utilization of the cellulose. This is also a key step to convert lignocellulose biomass into biofuel.10,15
There are a variety of current straw pretreatment technologies, which are categorized as physicochemical, thermal, thermochemical and biological pretreatments, in addition to combinations of these.15–18 However, all single pretreatment methods have some disadvantages that result in important additional costs to the process; these costs are often the main obstacle to the commercial pretreatment of lignocellulose waste. Thus, two or more pretreatment methods can be combined based on the characteristics of the different pretreatment techniques to give full play to their respective advantages in order to achieve cost savings, reduce the amount of chemicals used in the pretreatment process, lower the degree of equipment wear, improve pollution problems, and significantly increase the efficiency of straw hydrolysis and develop a low-energy, environmentally friendly and efficient pretreatment technology. Higher temperature can achieve a better pretreatment effect, but overly high temperatures (more than 150 °C) result in the conversion of lignin to phenolic compounds, which are toxic to the microbes in AD systems.19 Recent reports have revealed that the hydrolysis phase of AD can be accelerated at lower oxygen levels.20,21 The reason for this is that micro-aerobic conditions stimulate the secretion of extracellular hydrolytic enzymes such as cellulases and proteases,22 which ultimately improve the enzymatic efficiency of the enzymatic products.
Many investigations of hydrolysis using bases such as sodium hydroxide (NaOH) or calcium hydroxide (Ca(OH)2) have been carried out by scholars worldwide.23,24 The main advantage of alkali pretreatment is the breakdown of lignin, the presence of which greatly limits the role of enzymes in the AD process.25,26 Alkali conditions are efficient not only for breaking the ester bonds between polysaccharides and lignin,27 but also for dissolving some of the hemicellulose and cellulose.28 Calcium peroxide (CaO2) is one of the safest and most versatile solid inorganic peroxide compounds and is considered to be the solid form of H2O2.29 When CaO2 is dissolved in an aqueous solution, it can react with water and decompose at a controlled rate to slowly produce oxygen (O2), calcium hydroxide (Ca(OH)2) and hydrogen peroxide (H2O2), as shown in eqn (1) and (2).30–32 Due to these properties, CaO2 can be used as an alternative additive to supply oxygen to the AD process and create micro-oxygen demand conditions to facilitate the hydrolysis of the substrate. CaO2 can be used as a highly effective additive for pollutant removal due to the reactive oxygen species in it.30,33 CaO2 can enhance the hydrolytic acidification of activated sludge by increasing the activity of hydrolases and acid-producing enzymes.31 In addition, the reaction of CaO2 with water produces Ca(OH)2, which fixes CO2 (Ca(OH)2(l) + CO2(g) → CaCO3(s) + H2O(l)), thus increasing the CH4 content of the biogas. At the same time, the alkalinity of the AD system can be increased by the generation of Ca(OH)2 or CaCO3, which facilitates the production of volatile fatty acids (VFAs) and soluble chemical oxygen demand (SCOD).34 However, the OH− produced by CaO2 has a significant negative effect on CH4-producing bacteria.35 Therefore, when using CaO2 as an additive, the amount of CaO2 must be controlled to improve the efficiency of AD. The hydrolysis temperature of wheat straw is related to the biomass pretreatment performance.36 Based on this pretreatment, further enzymatic hydrolysis is considered in this work. Cellulase is a specific and highly efficient biotype catalyst for the hydrolysis of cellulose. It is a collective term for a number of enzymes that degrade the fibrous raw material dextran, and the different component enzymes act synergistically with each other.37 The purposes of this study of the pretreatment of wheat straw with CaO2 and cellulase were to (1) investigate the synergistic effects of CaO2, cellulase, and CaO2 reacted with cellulose; (2) evaluate the physicochemical properties of the pretreated straw hydrolysate and solid residues; (3) reveal the effects of the pretreatment conditions on the CH4 production performance of AD from lignocellulose materials; and (4) estimate the biodegradability and CH4 production potential of each substrate using the modified Gompertz kinetic model.
|
CaO2(s) + 2H2O(l) → Ca(OH)2(l) + H2O2(l)
| (1) |
|
2CaO2(s) + 2H2O(l) → 2Ca(OH)2(l) + O2(g)
| (2) |
Materials and methods
Feedstock and inoculum
The AD substrate used in this study was wheat straw from an agricultural processing plant in Shandong, China. Wheat straw must be pretreated prior to AD for CH4 production. After natural drying at 30–35 °C, the straw was chopped into small pieces of 2.5–3.5 cm, further homogenized using a plant disintegrator, crushed into straw powder of about 40 mesh (0.45 mm), and then placed in sample bags and sealed for later use. Its main elemental components were as follows: total N 0.45 ± 0.05%, total C 46.4 ± 0.4% and H 6.2 ± 0.02%.
Inoculated sludge was obtained from the laboratory of Qilu University of Technology (Shandong Academy of Science). The inoculated sludge was cultured with glucose (0.3 g L−1) for 20 d at 36 ± 1 °C until no gas was produced and then further concentrated by gravity separation, from which the AD inoculum was obtained. In addition, the cellulase used in this work was purchased from Novozymes (Denmark). The cellulase activity was 200
000 U mL−1, and its optimum temperature and pH value were 55–60 °C and 4.5–5.0, respectively. Moreover, the cellulase contained some metal ions such as Na+, Cu2+, Ca2+ and Zn2+, further promoting its activity. The main properties of the wheat straw and inoculum are shown in Table 1.
Table 1 The characteristics of the wheat straw and inoculum
Characteristic |
Wheat straw |
Inoculum |
pH |
6.69 |
7.2 |
Moisture content (%) |
7.63 |
90.06 |
Total solids (TS, %) |
92.37 |
9.94 |
Volatile solids (VS, % of TS) |
95.15 |
95.93 |
C (% of TS)/TOC (mg L−1) |
43.53 |
1950 |
N (% of TS)/NH4+–N (mg L−1) |
0.231 |
136.1 |
H (% of TS) |
6.182 |
— |
C/N ratio |
188.4 |
— |
Hydrothermal and enzymatic co-treatment for wheat straw
5 g straw samples were weighed out into seven 500 mL bioreactors numbered 1–7. To bioreactors no. 1–6, 6% CaO2 by mass was added, and bioreactor no. 7 was the control group without CaO2. The deionized water used this study was obtained by two-stage reverse osmosis, and was added to all the bioreactors to give a solid to liquid ratio (m straw/v deionized water) of 1
:
12. After the samples were thoroughly wetted, all the bioreactors with straw samples were placed in a 35 °C incubator at 150 rpm for 2 h. Bioreactors no. 1–6 were then taken out and placed into the reaction kettle, kept at a constant temperature at 121 °C for 60 min, and then removed and subsequently cooled to room temperature (20–25 °C) to obtain a mixture of hydrolytic liquids and solid residue. The pretreated samples of bioreactors no. 1–5 and 7 were adjusted to pH 4.5–5.0 with 1 mol L−1 HCl and placed in a constant temperature incubator set at 55 °C with shaking at 120 rpm. When the temperature was reached, the treatment was carried out by adding the appropriate amount of acidic cellulase, which was 0.1 mL, 0.2 mL, 0.3 mL, 0.4 mL, and 0.5 mL for reactors no. 1–5, and 0.3 mL for no. 7. The pretreated samples were further digested/hydrolyzed for 72 hours and then cooled to room temperature.38
AD design for methane production
Eight 500 mL serum bottles were numbered R1–R8 and the pretreated wheat straw mixtures numbered 1–7 were transferred into the serum bottles numbered R1–R7, respectively. The R6 group was pretreated with CaO2 alone, the R7 group was pretreated with cellulase alone, and in the R8 group, the wheat straw was directly fermented without additives to produce CH4 as a control experiment. Then, 150 mL of inoculated sludge was added to each bottle and distilled water was added to make up the volume to 400 mL. The top of each bioreactor was flushed with N2 for 1 min to remove O2 before the serum bottle was quickly sealed with a rubber stopper. Finally, all the bioreactors were placed in an electric-heated thermostatic water bath and digested at 36 ± 1 °C for 42 days. The above experiments were conducted in three parallel experiments. During the AD processes, each bioreactor was manually mixed by gently shaking it once a day and gas production data were recorded once a day. The extracted fermentation broth from each reactor was centrifuged at 5000 rpm for 5 minutes using a medical centrifuge, and the liquid parameters, such as the pH, volatile fatty acids (VFAs), total organic carbon (TOC), total carbon (TC), inorganic carbon (IC) and ammonium nitrogen (NH4+–N), were measured in the supernatant. The CH4 volume was converted to standard temperature and pressure (STP) through correction of the water vapor pressure at 25 °C, which was based on eqn (3).39 |
 | (3) |
where T = 25 °C (room temperature), W = 3167 Pa (water vapour pressure at 25 °C), and Vgas = volume of gas at STP (mL).
Analysis methods
Total solid (TS) and volatile solid (VS) were determined based on a previous work.40 Additionally, the ammonia nitrogen (NH4+–N), TOC and pH in the liquid samples were measured according to a previous study.41 The total carbon (C) and nitrogen (N) of wheat straw were also determined according to the method previously described by Zhang et al.41
In addition, the topography of the straw samples was measured using a scanning electronic microscope (SEM) (JEOL JSM-5600 LV, Japan) according to the method previously reported by Zhang et al.41 The changes in the functional groups in the wheat straw samples before and after treatment with CaO2 were evaluated using a Fourier transform infrared (FTIR) spectrophotometer (IR Prestige-21, Japan). The lignin, cellulose, and hemi-cellulose contents of the samples before and after treatment were measured based on a previous study.41 Additionally, an X-ray diffractometer (D8 Advance, Bruker AXS GmbH, Germany) was employed to obtain the X-ray diffractometry (XRD) curves of the cellulase- and CaO2-treated wheat straw samples.41 Moreover, the crystallinity index (CrI) of each sample was estimated based on the previous report.41 The bioCH4 yield was determined by the saturated NaOH drainage technique, and the CH4 content was measured using gas chromatography (GC-2014C/TCD, Shimadzu, Japan) with a thermal conductivity detector (TCD). The biogas volumes were further determined under STP conditions (273 K, 101.325 kPa).
Kinetic analysis of methane production
The CH4 production potential (MPP) was estimated by fitting a cumulative CH4 production (CMP) curve with the modified Gompertz model, which is described in eqn (4).42 The software Origin 9.0 was used to determine the Pm, Rm and λ values and evaluate the correlation coefficient (R2). |
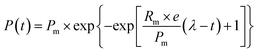 | (4) |
where P(t) is the CMP (mL) at time t (d), Pm is the MPP (mL), Rm is the maximum methane production rate (mL d−1), e is 2.72, λ is the lag period (d), and t is the fermentation time (d).
Results and discussion
Effects of CaO2/cellulase pretreatment on the hydrolysis products
The effect of hydrothermally coupled CaO2-coordinated cellulase pretreatment on the characteristics of the straw hydrolysis products was mainly evaluated in terms of the TOC of the pretreated hydrolysis products and the changes in the content of the three substances in the hydrolyzed straw residue.41 As shown in Tables 2 and 3, the addition of cellulase to the hydrothermally coupled CaO2 pretreatment technique for wheat straw increased the TOC of the hydrolysis products in all cases (Table 2). The TOC content of the hydrolysate from the control group was 1997 mg L−1. As the amount of cellulase used was increased from the 5 mg per g-cellulose to 25 mg per g-cellulose group, the TOC of the hydrolysis products increased, which indicated that the hydrolysis effect was enhanced by increasing the amount of cellulase added. However, the TOC value did not show a linear increase with the amount of cellulase added. As the amount of added cellulase was increased from 5 mg per g-cellulose to 15 mg per g-cellulose, the TOC value of the pretreated hydrolysis products increased significantly and rapidly. However, with further increasing the amount of cellulase, the increase in the TOC values became less pronounced, which was probably due to the inhibition of cellulase when the concentration of reducing sugars in solution was too high. The results showed that the samples without hydrothermally coupled calcium oxide pretreatment were the least hydrolysed, with an improvement of 90.79% over the control group. Due to the complex physical and chemical structure of wheat straw, it was difficult for cellulase to reach the cellulose surface directly for enzymatic hydrolysis. The TOC of the sample pretreated only with hydrothermally coupled CaO2 was 4865 mg L−1, which was 27.45% and 143.62% higher than those of the enzymatic-treatment and control groups, respectively. The TOC value of the hydrolysis product of the samples treated with 6% CaO2 plus 15 mg enzyme per g-cellulose was 7330 mg L−1, which was 92.39% and 267.05% higher than those from the enzymatic hydrolysis and control groups, respectively. The TOC from the sample treated with 6% CaO2 and 25 mg enzyme per g-cellulose was 7590 mg L−1, showing a 99.21% increase in the TOC value compared to enzymatic hydrolysis alone. In order to determine whether the effects of different pretreatment conditions on the hydrolysis process of straw were statistically significant, a one-way analysis of variance (ANOVA) and a post hoc test were carried out on the TOC values of the hydrolysis products of each group of samples using the analysis software SPSS, and a p-value of 0.00 (less than 0.05) was obtained, which indicated that different pre-treatment conditions had a significant effect on the TOCs of the hydrolysate samples. The co-pretreatment using 6% CaO2 and 15 mg enzyme per g-cellulose was optimal based on the combined effect of pre-hydrolysis and cost considerations.
Table 2 The indicators of straw hydrolysate after enzymatic pretreatment
Sample |
Enzyme (mg per g-cellulose) |
pH |
NH4+–N (mg L−1) |
TOC (mg L−1) |
1 |
6% CaO2 + 5 enzyme |
5.8 ± 0.2 |
36 ± 2.0 |
5180 ± 15 |
2 |
6% CaO2 + 10 enzyme |
5.7 ± 0.2 |
41 ± 2.5 |
6250 ± 15 |
3 |
6% CaO2 + 15 enzyme |
5.7 ± 0.2 |
79 ± 2.5 |
7330 ± 20 |
4 |
6% CaO2 + 20 enzyme |
5.6 ± 0.1 |
117 ± 3.0 |
7450 ± 15 |
5 |
6% CaO2 + 25 enzyme |
5.4 ± 0.2 |
110 ± 2.5 |
7590 ± 35 |
6 |
6% CaO2 + 0 enzyme |
8.9 ± 0.2 |
16 ± 2.5 |
4865 ± 15 |
7 |
0% CaO2 + 15 enzyme |
4.8 ± 0.1 |
67 ± 2.5 |
3810 ± 15 |
8 |
Control group |
6.7 ± 0.1 |
86.12 ± 2.0 |
1997 ± 15 |
Table 3 Lignin, cellulose, and hemicellulose content levels before and after pretreatment
Sample |
Cellulose (%) |
Hemicellulose (%) |
Lignin (%) |
Wheat straw |
38.8 ± 0.1 |
27.9 ± 0.1 |
20.1 ± 0.1 |
CaO2/cellulase |
30.2 ± 0.1 |
25.6 ± 0.3 |
18.6 ± 0.2 |
CaO2 |
45.1 ± 0.3 |
26.1 ± 0.3 |
18.8 ± 0.1 |
Cellulase |
36.8 ± 0.2 |
27.3 ± 0.3 |
20.0 ± 0.2 |
On the other hand, due to the different pretreatment conditions, the contents of cellulose, hemicellulose and lignin varied considerably after pretreatment hydrolysis. The most significant changes were observed in the samples pretreated with CaO2 co-cellulase; details are described in Table 3. The weight loss of the wheat straw was due to the dissolution of components such as cellulose, hemicellulose and lignin.42,43 The cellulose, hemicellulose and lignin contents of the raw wheat straw samples were 38.8%, 27.9% and 20.1%, respectively. The levels of the three substances in the samples subjected to direct enzymatic hydrolysis and in the samples pretreated with CaO2 did not change significantly, whereas the heat and CaO2 co-pretreatment was more effective in degrading hemicellulose to obtain soluble oligomers and monomeric sugars, and also in removing lignin, which was consistent with previous work.41 Consequently, the hemicellulose and lignin contents decreased, and the relative cellulose content increased. The contents of cellulose, hemicellulose and lignin in the sample under the conditions of 6% CaO2 and 25 mg enzyme per g-cellulose were 30.2%, 25.6% and 18.6%, respectively (Table 3). Additionally, hemicellulose and lignin were removed; the complex structure of the wheat straw was disrupted. Consequently, the straw sample was hydrated and swollen, exhibiting a loose and soft structure, which facilitated the accessibility of the cellulose and increased the adsorption sites for cellulase. The findings were in line with a previous report.41
Effects of CaO2-coordinated cellulase treatment on the wheat straw structure
The physical and chemical properties of the straw under different pretreatment conditions were analyzed and compared with those of the untreated wheat straw samples to investigate the differences in the surface structure, functional groups and crystal structure of the wheat straw before and after CaO2-coordinated cellulase treatment. The morphologies of the wheat straw samples under different pretreatment conditions were observed under a scanning electronic microscope (SEM). As shown in Fig. 1, the surface of unprepared wheat straw is smooth, dense, rigid and structurally intact (Fig. 1a); these properties do not facilitate access to the cellulose interior by cellulase during subsequent AD.32 After the pretreatment, the waxy surface coating of the wheat straw is removed, the surface roughness is significantly increased and the surface structure becomes porous and loose. Due to the alkalinity and strong oxidation of CaO2, part of the lignin was destroyed and part of the hemicellulose and cellulose was dissolved, allowing the surface structure of wheat straw to begin to separate and be converted into cellulose filaments (Fig. 1c), which was similar to the findings from Kang et al.42 and Solé-Bundó et al.44 The enzymatic hydrolysis of samples pretreated with enzyme alone resulted in a less damaged surface structure than for those pre-treated with hydrothermally coupled CaO2. This is mainly due to the complex structure of the straw, which prevents the effective utilization of cellulase due to its low accessibility (Fig. 1d). The SEM images of samples that were first pretreated with hydrothermally coupled CaO2 and then further hydrolyzed using cellulase showed that the surface structure of the wheat straw was greatly damaged under these conditions. Their morphologies revealed that the pre-treatment process allowed the wheat straw to hydrate and swell, and that the liquid penetrated into the wheat straw cells, effectively destroying the complex linkages between the various straw components. The combination treatment with CaO2 and cellulase was the most damaging to the surface structure of the wheat straw, followed by the hydrothermal coupled CaO2 pretreatment, and finally the cellulase hydrolysis alone.
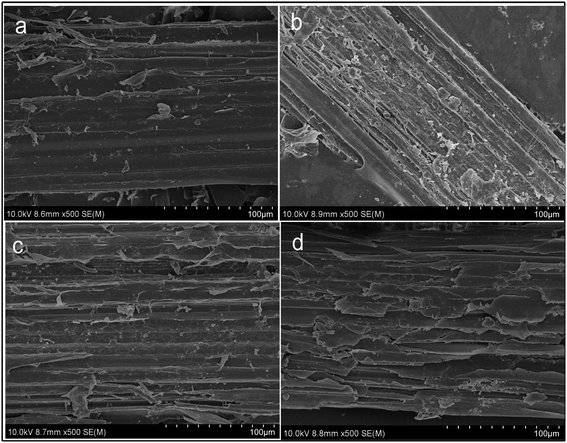 |
| Fig. 1 The morphologies of wheat straw under different pretreatment conditions: control group (a), CaO2 plus enzyme treatment (b), CaO2 treatment (c), and enzyme treatment (d). | |
The FTIR spectra of the raw straw samples, the CaO2-coordinated cellulase-pretreated samples, the CaO2-treated samples and the cellulose-treated samples are described in Fig. 2. The peaks of methyl (–CH3) or methylene (–CH2) groups occurred at 2920 cm−1 and the absorption peak at 3400 cm−1 was related to alcohol hydroxyl and phenolic hydroxyl (–OH) groups. In the pretreated samples, the absorption of this peak was weaker than in the original straw sample, indicating that the hydroxyl interactions decreased after the pretreatment. The hydrogen bonding was mainly present in the crystalline zone of cellulose, which indirectly indicated that the crystalline zone of cellulose was somewhat damaged and the degree of crystallinity decreased. The spectral bands at 1260 cm−1 (C–O bond, related to guaiac-based lignin) and 1635 cm−1 (related to the C
O vibration of the conjugate carbonyl group of lignin) were weakened by the removal or degradation of lignin.45,46 The degradation of hemicellulose was indicated by a decrease in the peak intensities at 1228 cm−1 and 1720 cm−1, which correspond to the C–O and ester/carboxylic acid bonds of the hemicellulose acetyl unit. In addition, the peak intensity at 898 cm−1 associated with the stretching vibration of the cellulose cyclic β-1,4-glycosidic bond was reduced and the absorption peak of the cellulose C–H bending vibration signature in the sample after CaO2 co-cellulase pretreatment was significantly lower than that of the raw material, which demonstrated the removal of cellulose from the samples after this co-pretreatment and further confirmed the degradation of amorphous cellulose.47 Similarly, the peak at 1736 cm−1 was related to the C
O stretching vibration, which reflected the variation in hemicellulose content. After the pretreatment process, the peaks were weakened, suggesting a decrease in hemicellulose content. In addition, the decrease in peak intensity at 1603 and 1511 cm−1 indicated the degradation of lignin.48 Co-cellulase pretreatment with CaO2 was more likely to give the maximum utilization of cellulose than heat and CaO2 co-treatment, resulting in improved straw biodegradability.
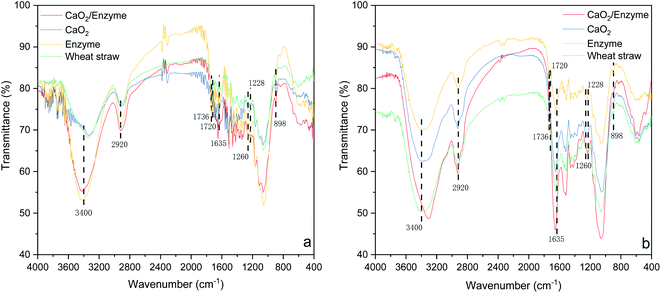 |
| Fig. 2 Changes in the surface functional groups before (a) and after (b) anaerobic digestion. | |
In addition, the XRD characterization of the wheat straw raw material and the samples treated under various treatment conditions is shown in Fig. 3, and their crystallinity is also presented in Table 4. The XRD profiles of the pre-treated samples and wheat straw were similar (Fig. 3). The presence of diffraction peaks indicated a relatively high degree of crystallinity in the structure of the fibers. After the alkali-treatment process, the cellulose chain segments were folded to form a new crystal structure.49 Natural cellulose consists of type I cellulose crystals, which undergo a structural change from type I to type II cellulose after alkali treatment.50 As revealed in Fig. 3, the XRD spectra of both the raw wheat straw and the pre-treated wheat straw samples had a clear and strong band at 2θ = 22.6°. There were two weak diffraction bands at 2θ = 14.7° and 16.4°, which indicated cellulose I.51 The XRD pattern of wheat straw before pretreatment had two strong diffraction bands at 2θ = 16° and 22°, but the intensities of the diffraction peaks were reduced by the pretreatment (Fig. 3). The crystallinity of the wheat straw was 33.12%. In the wheat straw sample treated with 6% CaO2, the band at 2θ = 29° shifted to a slightly higher angle and appeared as an intense and sharp diffraction peak. The half-width of the diffraction peak (002) became smaller and its intensity increased, and the crystallinity was 54.55%. The alkaline oxygen pretreatment under hydrothermal conditions effectively removed lignin and degraded part of the hemicellulose and amorphous cellulose, causing enrichment of the cellulose. Under the optimal conditions (6% CaO2 + 25 mg cellulase per g-cellulose), the crystallinity of the pretreated sample was 27.37%. SEM and FTIR spectroscopy of the samples demonstrated that the surface morphology and functional groups changed considerably after pretreatment with the different methods, which could be supported and corroborated by changes in the content of the three substances in the wheat straw and the composition of the hydrolysis product.
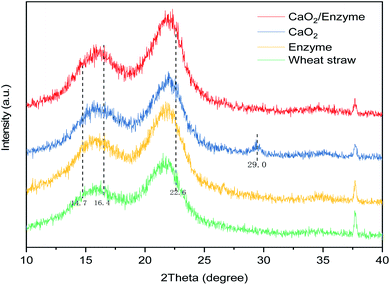 |
| Fig. 3 Changes in the crystallinity of the wheat straw before and after pretreatment. | |
Table 4 Crystallinity properties for different CaO2 and enzyme pretreatment conditions
Sample |
Crystallinity (%) |
Grain size (nm) |
Strain |
Wheat straw |
33.12 |
48.2 ± 2.5 |
0.678 ± 0.020 |
CaO2/enzyme |
27.37 |
7.5 ± 1.5 |
0.72 ± 0.018 |
CaO2 |
54.55 |
20.3 ± 1.4 |
0.196 ± 0.012 |
Enzyme |
31.41 |
28.5 ± 1.31 |
0.636 ± 0.101 |
Effects of CaO2-coordinated cellulase treatment on methane production
The CH4 production and yield are two important indexes to evaluate the AD process of wheat straw. Fig. 4 illustrates the relationship between the CMP and fermentation time under different pretreatment conditions, including the relationship between the CMP and AD time under different cellulase conditions (Fig. 4a), and methane production under the optimal conditions with different pretreatments compared to the control group (Fig. 4b). As demonstrated in Fig. 4a, the CMP curves coincided with the lag, log, stability and decay periods of the microbial growth curve. The possible mechanisms of the CaO2-coordinated cellulase treatment of wheat straw are shown in Fig. 5.52 The addition of cellulase increases the adhesion of cellulose to the enzyme, so that the TOC and NH4+–N contents of the hydrolysis product increase and the hydrolysis effect is enhanced. Bolado-Rodríguez et al.53 observed that alkali pretreatment promoted the hydrolysis process of wheat straw. Additionally, the addition of CaO2 released Ca2+, which is a trace element required by methanogens, into the liquid during the dissolution process. Additionally, cellulase addition further promoted the decomposition of hemicellulose, lignin and cellulose into small molecules that were readily attacked and used by different microorganisms. The hydrolytic and fermentative microbes with high anti-oxidative enzyme activity were capable of scavenging reactive oxygen species and protecting the methanogens. These properties all favored the growth and multiplication of methanogenic bacteria, which in turn increased the CH4 yield. In the AD system, when the cellulase addition was increased from 0 to 0.3 mL with the addition of 6% CaO2 pretreatment, the CMP increased progressively compared to that of the control group without pretreatment, from 22.29% to 57.06%. These results of the ANOVA showed a significant difference (p < 0.0001) between the total gas productions of straw treated with different amounts of cellulase, indicating that the enzymatic hydrolysis of wheat straw with various amounts of cellulase has a positive effect on the CH4 production from the wheat straw in the presence of CaO2 pretreatment. However, when the amount of cellulase added was continually increased, the CH4 yield revealed a decreasing trend; the addition of 0.4 and 0.5 mL cellulase lowered the CH4 yield by 10.40% and 13.10% compared to the highest yield, respectively. This was because excess cellulase inhibited the activity of the methanogenic bacteria, thereby lowering the CH4 production. In the group treated using enzymatic hydrolysis alone, the CH4 yield was only 12.33% higher than that of the control group (Table 5). After alkali treatment, the lignin was dissolved in the alkali solution, which was a potential toxicant to the microbes in AD system. Thus, a moderate amount of cellulase helped the anaerobes to produce more CH4 from wheat straw, while excess cellulase inhibited CH4 production.
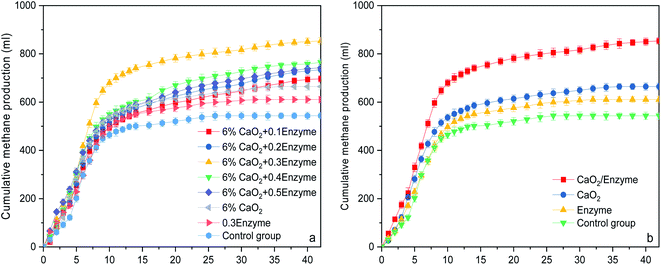 |
| Fig. 4 A comparison of CH4 production from the CaO2/cellulase co-treatment and control groups: (a) CMP under different enzyme conditions; and (b) CMP under the optimal conditions. | |
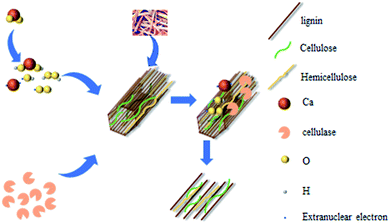 |
| Fig. 5 The possible mechanism involved in the CaO2/cellulase treatment of wheat straw (6% CaO2 coupled with 0.1–0.5 mL of enzyme). Adapted with permission.52 | |
Table 5 The kinetic parameters of synergistic CaO2/cellulase treated wheat straw in methane productiona
Reagent dosage |
Pm (mL) |
Rm (mL d−1) |
λ (d) |
R2 (%) |
CMP (mL) |
CH4 yield (mL g−1) |
Increase in CMP (%) |
“—” represents the difference between the cumulative methane production of the control group and itself (the difference is 0). |
6% CaO2/0.3 enzyme |
817.92 |
86.32 |
0.29 |
99.23 |
853.75 |
170.75 |
57.06 |
6% CaO2 |
641.54 |
72.62 |
1.15 |
99.22 |
664.72 |
132.94 |
22.29 |
0.3 enzyme |
600.74 |
64.92 |
1.32 |
99.69 |
610.58 |
122.12 |
12.33 |
Control group |
535.92 |
70.04 |
1.85 |
99.37 |
543.58 |
108.72 |
— |
Kinetic analysis of methane production
The length of the delay in the AD process depends on the concentration of substances that are easily digestible by microorganisms in the fermentation broth at the beginning of the reaction.54 The lag times of the pretreated samples were short due to the pretreatment, whereas the lag time of the control group without any pretreatment was long. It can be seen from Table 5 that the effect of cellulase addition on CH4 generation can be well fitted with the modified Gompertz model (eqn (4)), and that the correlation coefficient (R2) was greater than 98%, indicating that the fitting curve was significantly related to the experimental data. CaO2-coordinated cellulase treatment had significant effects on the Pm and Rm values. With the 6% CaO2 pretreatment and the addition of 0.3 mL of cellulase, the Pm value was 817.92 mL, which was 57.06% higher than that of the control group, and the maximum Rm value (86.59 mL d−1) was obtained under these conditions. The CH4 yield was proportional to the amount of cellulase when the amount of cellulase was below 0.3 mL. Further increasing the amount of cellulase caused a decrease in the Rm values. Therefore, the actual CH4 production is the result of a combination of factors such as solution pH, lignin, cellulose, AD time and temperature, as well as the inoculum. This further demonstrated that there was a difference between the theoretical and actual CH4 production potential.
Conclusions
Calcium peroxide (CaO2) and its combination with cellulase in the pretreatment of wheat straw for bioCH4 production were investigated in terms of the main characteristics of the wheat straw before and after the pretreatments and the subsequent bioCH4 generation. The results showed that the promotion of the anaerobic digestion of wheat straw followed the order hydrothermal and CaO2 co-cellulase pretreatment > hydrothermal and CaO2 pretreatment > cellulase hydrolysis alone > control group. The samples treated with 6% CaO2 and 15 mg cellulase per g-cellulose produced the highest CH4 yields, with a 64.81% increase compared to the control group. Pretreatment with a moderate amount of cellulase also promoted the hydrolysis of wheat straw and the subsequent anaerobic digestion process, while excess cellulase could limit CH4 production.
Author contributions
Zhenmin Li: data curation, writing – original draft. Jishi Zhang: supervision, conceptualization, writing – review and editing, funding acquisition. Chunduo Kong: methodology, data curation. Wenqing Li: writing – review and editing. Jinwei Wang: methodology. Lihua Zang: funding acquisition, supervision.
Conflicts of interest
There are no conflicts to declare.
Acknowledgements
This study was financially supported by the Natural Science Foundation of Shandong Province (ZR2016EEM33).
References
- C. Akobi, H. Yeo, H. Hafez and G. Nakhla, Appl. Energy, 2016, 184, 548–559 CrossRef CAS.
- Y. Wang, L. Dai, R. Wang, L. Fan, Y. Liu, Q. Xie and R. Ruan, J. Anal. Appl. Pyrolysis, 2016, 119, 251–258 CrossRef CAS.
- A. Kumar Sakhiya, A. Anand, I. Aier, P. Baghel, V. K. Vijay and P. Kaushal, Mater. Today: Proc., 2020 DOI:10.1016/j.matpr.2020.08.795.
- P. Ganguly, S. Sengupta, P. Das and A. Bhowal, Fuel, 2020, 280, 118581 CrossRef CAS.
- P. M. Bondesson and M. Galbe, Biotechnol. Biofuels, 2016, 222, 9159 Search PubMed.
- C. Huang, X. Wu, Y. Huang, C. Lai, X. Li and Q. Yong, Bioresour. Technol., 2016, 219, 583–588 CrossRef CAS PubMed.
- G. Kumar, P. Sivagurunathan, B. Sen, S. H. Kim and C. Y. Lin, Bioresour. Technol., 2017, 240, 137–143 CrossRef CAS PubMed.
- F. Talebnia, D. Karakashev and I. Angelidaki, Bioresour. Technol., 2010, 101, 4744–4753 CrossRef CAS PubMed.
- C. Huang, X. Wu, Y. Huang, C. Lai, X. Li and Q. Yong, Bioresour. Technol., 2016, 219, 583–588 CrossRef CAS PubMed.
- E. Rouches, I. Herpoël-Gimbert, J. P. Steyer and H. Carrere, Renewable Sustainable Energy Rev., 2016, 59, 179–198 CrossRef CAS.
- M. Hassan, W. Ding, J. Bi, E. Mehryar, Z. A. Talha and H. Huang, Bioresour. Technol., 2016, 200, 405–412 CrossRef CAS PubMed.
- S. Nadav, T. H. Yeats, S. Heidi, Y. Heather and S. Chris, BioScience, 2014, 64(3), 192–201 CrossRef.
- N. Sorek, T. H. Yeats, H. Szemenyei, H. Youngs and C. R. Somerville, BioScience, 2014, 64, 192–201 CrossRef.
- K. A. Underkofler, R. E. Teixeira, S. A. Pietsch, K. G. Knapp and R. T. Raines, ACS Sustainable Chem. Eng., 2015, 3, 606–613 CrossRef CAS PubMed.
- L. Janke, S. Weinrich, A. F. Leite, F. K. Terzariol, M. Nikolausz, M. Nelles and W. Stinner, Energy Convers. Manage., 2017, 141, 378–389 CrossRef CAS.
- E. Abdelsalam, M. Samer, Y. A. Attia, M. A. Abdel-Hadi, H. E. Hassan and Y. Badr, Energy Convers. Manage., 2017, 141, 108–119 CrossRef CAS.
- A. Cesaro and V. Belgiorno, Chem. Eng. J., 2014, 240, 24–37 CrossRef CAS.
- Y. Zheng, J. Zhao, F. Xu and Y. Li, Prog. Energy Combust. Sci., 2014, 42, 35–53 CrossRef.
- Z. Sapci, Bioresour. Technol., 2013, 128, 487–494 CrossRef CAS PubMed.
- W. Charles, L. Walker and R. Cord-Ruwisch, Bioresour. Technol., 2009, 100, 2329–2335 CrossRef CAS PubMed.
- J. E. Johansen and R. Bakke, Water Sci. Technol., 2006, 53, 43–50 CrossRef CAS PubMed.
- P. Tsapekos, P. G. Kougias, S. A. Vasileiou, G. Lyberatos and I. Angelidaki, Bioresour. Technol., 2017, 225, 246–253 CrossRef CAS PubMed.
- S. Kim and M. T. Holtzapple, Bioresour. Technol., 2005, 96, 1994–2006 CrossRef CAS PubMed.
- K. E. Kang, G. T. Jeong, C. Sunwoo and D. H. Park, Bioprocess Biosyst. Eng., 2012, 35, 77–84 CrossRef CAS PubMed.
- Z. Wang, D. R. Keshwani, A. P. Redding and J. J. Cheng, Bioresour. Technol., 2010, 101, 3583–3585 CrossRef CAS PubMed.
- L. Wu, M. Arakane, M. Ike, M. Wada, T. Takai, M. Gau and K. Tokuyasu, Bioresour. Technol., 2011, 102, 4793–4799 CrossRef CAS PubMed.
- J. Kainthola, A. Podder, M. Fechner and R. Goel, Bioresour. Technol., 2021, 321, 124397 CrossRef CAS PubMed.
- F. Monlau, A. Barakat, J. P. Steyer and H. Carrere, Bioresour. Technol., 2012, 120, 241–247 CrossRef CAS PubMed.
- Y. Qian, X. Zhou, Y. Zhang, W. Zhang and J. Chen, Chemosphere, 2013, 91, 717–723 CrossRef CAS PubMed.
- A. Zhang, J. Wang and Y. Li, Water Res., 2015, 71, 125–139 CrossRef CAS PubMed.
- Y. Li, J. Wang, A. Zhang and L. Wang, Water Res., 2015, 83, 84–93 CrossRef CAS PubMed.
- X. Huang, W. Dong, H. Wang, F. Sun and Y. Feng, J. Cleaner Prod., 2019, 228, 1526–1536 CrossRef CAS.
- A. Goi, M. Viisimaa, M. Trapido and R. Munter, Chemosphere, 2011, 82, 1196–1201 CrossRef CAS PubMed.
- H. Wu, J. Gao, D. Yang, Q. Zhou and W. Liu, Chem. Eng. J., 2010, 160, 1–7 CrossRef CAS.
- J. Wang and Y. Li, Appl. Energy, 2016, 183, 1123–1132 CrossRef CAS.
- W. Tian, Y. Chen, Y. Shen, C. Zhong, M. Gao, D. Shi, Q. He and L. Gu, Sci. Total Environ., 2020, 732, 139312 CrossRef CAS PubMed.
- T. Weide, C. D. Baquero, M. Schomaker, E. Brügging and C. Wetter, Biomass Bioenergy, 2020, 132, 105442 CrossRef CAS.
- D. Xu, Z. Ding, J. Bai, W. Ke, Y. Zhang, F. Li and X. Guo, Bioresour. Technol., 2020, 310, 123476 CrossRef CAS PubMed.
- Q. Feng and Y. C. Song, Energy Fuels, 2016, 30, 6467–6474 CrossRef.
- G. Kumar, B. Sen, P. Sivagurunathan and C.-Y. Lin, Fuel, 2016, 182, 131–140 CrossRef CAS.
- J. Zhang, C. Kong, M. Yang and L. Zang, ACS Omega, 2020, 5, 9151–9161 CrossRef CAS PubMed.
- X. Kang, Y. Sun, L. Li, X. Kong and Z. Yuan, Bioresour. Technol., 2018, 255, 205–212 CrossRef CAS PubMed.
- R. Narinthorn, W. Choorit and Y. Chisti, Biomass Bioenergy, 2019, 127, 105262 CrossRef CAS.
- M. Solé-Bundó, H. Carrère, M. Garfí and I. Ferrer, Algal Res., 2017, 24, 199–206 CrossRef.
- A. Hideno, Bioresour. Technol., 2017, 230, 140–142 CrossRef CAS PubMed.
- Y. Sheng, X. Tan, Y. Gu, X. Zhou, M. Tu and Y. Xu, Renewable Energy, 2021, 163, 732–739 CrossRef CAS.
- S. Gandolfi, G. Ottolina, R. Consonni, S. Riva and I. Patel, ChemSusChem, 2014, 7, 1991–1999 CrossRef CAS PubMed.
- A. M. Mustafa, H. Li, A. A. Radwan, K. Sheng and X. Chen, Bioresour. Technol., 2018, 259, 54–60 CrossRef CAS PubMed.
- C. C. Hernandez, F. F. Ferreira and D. S. Rosa, Carbohydr. Polym., 2018, 193, 39–44 CrossRef CAS PubMed.
- E. Jin, J. Guo, F. Yang, Y. Zhu, J. Song, Y. Jin and O. J. Rojas, Carbohydr. Polym., 2016, 143, 327–335 CrossRef CAS PubMed.
- A. D. French and M. Santiago Cintrón, Cellulose, 2013, 20, 583–588 CrossRef CAS.
- D. Kumari and R. Singh, Renewable Sustainable Energy Rev., 2018, 90, 877–891 CrossRef CAS.
- S. Bolado-Rodríguez, C. Toquero, J. Martín-Juárez, R. Travaini and P. A. García-Encina, Bioresour. Technol., 2016, 201, 182–190 CrossRef PubMed.
- D. Pečar, F. Pohleven and A. Goršek, Waste Manage., 2020, 102, 170–178 CrossRef PubMed.
|
This journal is © The Royal Society of Chemistry 2021 |
Click here to see how this site uses Cookies. View our privacy policy here.