DOI:
10.1039/D0RA08535A
(Paper)
RSC Adv., 2021,
11, 71-77
Application of electroactive Au/aniline tetramer–graphene oxide composites as a highly efficient reusable catalyst
Received
7th October 2020
, Accepted 13th November 2020
First published on 22nd December 2020
Abstract
This study proposes a cost-effective, energy-saving, and green process that uses π–π interactions to modify graphene oxide (GO), and the conjugate structure of aniline tetramer (AT) to enhance the dispersion of GO. Au/aniline tetramer–graphene oxide (Au/ATGO) composites were synthesized and applied as a catalyst in this study. The adsorption of AT on GO, via π–π interaction, formed ATGO composites. Subsequently, the amine group on ATGO was stably anchored on Au nanoparticles (Au NPs) to form Au/ATGO composites. The Au/ATGO composites were characterized and the electroactive properties determined by Fourier-transform infrared spectroscopy, X-ray photoelectron spectroscopy, transmission electron microscopy, and cyclic voltammetry. The Au/ATGO composites showed excellent performance and stability as catalysts when applied for the reduction of nitrophenol to aminophenol within 225 s and the rate constant was 0.02 s−1. The activation energy for the reduction of 4-NP and 2-NP was 48.10 and 68.71 kJ mol−1, respectively. Following a recycling test repeated 20 times, the Au/ATGO composites maintained a conversion rate higher than 94%.
Introduction
Conducting polymers such as polyaniline (PANI), polypyrrole, and polythiophene are interesting materials that have been studied and applied in various areas of technology. Owing to its facile synthesis process, unique redox properties, excellent environmental stability, good electrical conductivity, and simple acid–base doping/dedoping chemistry,1–3 PANI is one of the most promising types of polymer types used for the production of anticorrosion coatings,4 chemical sensors,5 catalysis,6 and supercapacitors.7 However, the application of PANI has some drawbacks such as low solubility in the most common solvents, infusibility, and difficulty in processing.8 Also, its electrical conductivity decreases over a long cycle time.9 To solve these problems, an aniline oligomer can be used in place of PANI because it not only retains the advantageous properties of PANI, but it also exhibits much better processability.10,11 Kaner et al. mentioned that aniline tetramer (AT) is the shortest oligomer with a structure similar to that of PANI.12 It is easy to control the morphology and size via the doping. Various crystalline nanostructures such as fibers, sheets, porous structure, and hollow spheres can be obtained by controlling the nucleation of the crystals and the non-covalent interactions between the doped oligomers.13 Yan et al. synthesized aniline oligomer/graphene oxide (GO) to enhance the electrochemical cycling stability of a supercapacitor from 84.2% to above 95.1%, after 2000 cycles. They mentioned that AT is a polymer with a short-chain, and the bonding itself may be weak. GO is a material with a 2D micrometer-sized structure, and it can support AT to prevent dissolution.9 Li et al. used the tetraphenylethylene group to fabricate soluble reduced graphene oxide (rGO) composites through efficient π–π stacking interactions; stable dispersions of graphene sheets in organic solvents could also be prepared. These findings provide new opportunities for the development of graphene-based materials that may have applications in optoelectronic devices, chemical sensors, and biomedical areas.14 Han et al. combined various aniline oligomers (dimer, trimer, and tetramer) with graphene to enhance the electrical and electrochemical performance of asymmetric supercapacitors. They observed that the AT exhibited higher areal capacitance, volumetric capacitance, and energy density than the samples fabricated from the dimer and trimer electrodes. Significant improvements in the performance of the tetramer sample were highly related to the improved electrical conductivity and structural stability when compared with the samples containing the trimer and dimer electrodes.15
Recently, chemical amino functional groups have been used as agents to anchor nanoparticles on substrates such as carbon nanotube (CNT),16 graphene,17,18 SiO2,19 and zirconium phosphate (ZrP)20 have been studied. Ou et al. used 1-pyrenemethylamine as the inter-linker to synthesize CNT–Au composites. The alkylamine substituent of 1-pyrenemethylamine binds to an Au nanoparticle (Au NP), while the pyrene chromophore was non-covalently attached to the sidewall of a carbon nanotube via π–π interaction. Using this strategy, Au NPs within the size range of 2–4 nm can be closely assembled on multiwalled carbon nanotubes.21 Yao et al. modified the surface GO using N1-(3-trimethoxysilylpropyl)diethylene triamine. The amine groups of the functionalized GO could effectively template the Au NPs assembly on the graphene surface with a high density and good dispersity. The TEM images of the modified GO show that the Au NPs maintained their original size, and they were well-anchored on the graphene surfaces with an average size of 15 nm.22 Furthermore, Yao et al. also used a variety of amine end group silane coupling agents that modified GO lead to GO/Au composites by controlling the grafting density of Au NPs. These different functional groups enabled the alteration of the grafting density of Au NPs which tailored the Au NPs for different catalytic applications. All GO/Au composites showed high efficiency in catalyzing a hydrogenation reaction, completing the reaction within 16 min. After 7 catalytic cycles of testing, no signs of detachment or aggregation were observed.23 These methods demonstrated the efficient inhabitation of Au NPs aggregation and the improvement of its catalytic activities.
In previous literature, graphene or GO were modified using silane agents, polymers, and so on following several complicated steps that require high cost, energy consumption, and the process is time-consuming. Herein, we used π–π interactions to modify GO. This method is cost-effective, saves energy, and requires the use of environmentally friendly solvents. To the best of our knowledge, the use of aniline tetramer–graphene oxide (ATGO) composites containing Au NPs as a catalyst have seldomly been studied. In this study, the conjugate structure of AT enhanced the dispersion of GO in the solvent through π–π interactions. Subsequently, a multi-amino functional group on ATGO was used to stably anchor Au NPs to form Au/ATGO composites. The Au/ATGO composites were characterized by field-emission transmission electron microscopy (TEM), Fourier-transform infrared (FTIR) spectroscopy, UV-visible (UV-Vis) spectroscopy, X-ray photoelectron (XPS) spectroscopy, and cyclic voltammetry (CV). The Au/ATGO composites showed good stability against agglomeration and excellent catalytic activity in a model reduction reaction of 4-NP into 4-AP, and 2-nitrophenol (2-NP) to 2-aminophenol (2-AP). The catalytic activity of the Au/ATGO composites was over 94% after 20 cycles.
Experimental
Materials
Graphite and N-phenyl-p-phenylenediamine were purchased from Alfa Aesar. Iron(III) chloride, hydrochloric acid (HCl), sulfuric acid (H2SO4), hydrogen peroxide (H2O2), and alcohol were obtained from ECHO chemical company. Potassium permanganate (KMnO4) was obtained from TCI. Tetrachloroauric(III) acid trihydrate (HAuCl4), sodium citrate, sodium borohydride (NaBH4), 4-nitrophenol, and 2-aminophenol were procured for Sigma-Aldrich.
Synthesis of ATGO composites
GO was prepared from graphite by the modified Hummers method.24,25 3 g of graphite was mixed with 360 mL H2SO4 and 40 mL H3PO4 in a flask, and the temperature was raised to 50 °C followed by the addition of 18 g of KMnO4. The mixture was continuously stirred overnight, and then 10 mL of H2O2 was added into the mixture. The fully oxidized suspension was poured into a large amount of deionized (DI) water, it was then centrifuged and washed to obtain the GO powder. AT was synthesized using a method we had previously developed.26 N-Phenyl-p-phenylenediamine (0.01 mol) was dissolved in 200 mL of 1 M HCl. Subsequently, a solution containing iron(III) chloride (0.01 mol) was added to the HCl containing N-phenyl-p-phenylenediamine while it was stirred in an ice bath. The resulting solution was allowed to react for another 4 h. The precipitate was filtered and washed with distilled water several times. The obtained AT was freeze-dried overnight. ATGO was prepared by simultaneous dispersion of 10 mg AT and 100 mg GO in 250 mL of alcohol and stirred for 24 h. The ATGO was washed three times with alcohol by centrifugation and resuspension, it was then dried at 70 °C in an oven for 24 h, and subsequently ground into a fine powder with a mortar and pestle.
Fabrication of Au/ATGO composites
100 mL of HAuCl4 (1 mM) aqueous solution was refluxed and stirred. 10 mL of sodium citrate (38.8 mM) aqueous solution was rapidly added to the boiling solution, and this resulted in a color change from yellow to wine red. The resulting solution was stirred for 10 min, then the heat source was removed. The solution was continuously stirred until the solution cold down to room temperature to obtain the Au NPs solution.20 To prepare the Au/ATGO composites, Au NPs solution (50 mL) was mixed with ATGO (10 mg) at room temperature and stirred overnight. The final Au/ATGO composites were collected by centrifugation and washed with DI water. The schematic representation of the synthesis process is shown in Scheme 1.
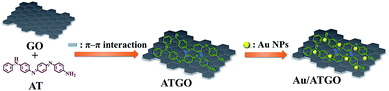 |
| Scheme 1 Synthesis of Au/ATGO composites. | |
Characterization
The FTIR spectra were recorded with a FTIR-4600 spectrometer (Jasco, Japan), the resolution used in the measurements and the number of scans were 4 cm−1 and 64 scans, respectively. The mass spectra were obtained on a triple quadrupole mass spectrometer with an ESI source (Thermo Scientific, United States). The UV-Vis absorption spectra were measured using a V-750 spectrometer (Jasco, Japan). The XPS analysis was performed using a PHI 5000 VersaProbe (ULVAC-PHI, Japan). The morphology and crystal structures of the samples were observed by TEM operated at 200 kV. Energy dispersive X-ray (EDX) mapping analysis was carried out on the TEM measurement (JEOL JEM-2100F, Japan). Thermogravimetric analysis (TGA) was conducted in air and nitrogen atmosphere at a heating rate of 20 °C min−1 over a temperature range of 30–800 °C using a TA Q500 (TA Instrument, United States). Electrochemical experiments were performed using a CHI 6273E electrochemical analyzer with a conventional three-electrode system (CH Instruments, United States).
Catalytic activity
To study the catalytic performance of the Au/ATGO composites, the composite was applied in the reduction reaction of 4-NP and 2-NP. NaBH4 was used as a hydrogen generation source in water. 1 mg of Au/ATGO composites was dispersed in 3 mL of 4-NP or 2-NP solution (0.1 mM). Then a freshly prepared 0.15 mL solution of NaBH4 (100 mM) was added. The molar ratio of 4-NP (2-NP)/NaBH4 is 0.02. The mixture was immediately into a quartz cuvette and the UV-Vis absorption spectra were recorded to monitor changes in the reaction mixture.
Results and discussion
Characterization of AT, GO, ATGO, and Au/ATGO composites
The mass spectra of AT are shown in Fig. 1(a). The characterizations of AT were conducted as follows: ion trap-MS m/z: [M + H]+ calculated for C24H20N4 = 364.3. Found 365.3. The FTIR spectra of GO, AT, and ATGO are shown in Fig. 1(b). From the FTIR spectrum of GO, the peak at 1041 cm−1 was ascribed to C–O–C bonding, and the peaks at 3373, 1725, and 1620 cm−1 signified the presence of –OH, C
O, and C
C functional groups, respectively, which indicates that abundant oxygen-containing groups existed on the surface of GO.24,27 The peak between 3314 and 3209 cm−1 can be attributed to the N–H stretching vibration, while those at 3032 cm−1 can be attributed to the C–H stretching vibration.28 The AT showed N
Q
N (quinoid ring) and N
B
N (benzenoid ring) bands at 1594 and 1504 cm−1, respectively.29,30 The peak at 1309 cm−1 can be attributed to C–N stretching vibration.31,32 The other peaks at 1165, 834, and 748 cm−1 are due to C–H bending vibrations.33 The FTIR spectrum of the ATGO contains the characteristic peaks of AT and GO.
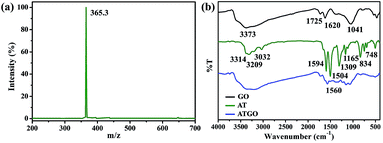 |
| Fig. 1 (a) Mass spectra of AT. (b) FTIR spectra of GO, AT, and ATGO. | |
The UV-Vis spectra of AT and ATGO supernatants are shown in Fig. 2(a). The two absorption peaks at 312 and 598 nm in the UV-Vis spectrum of AT are attributed to the π–π* transition of the benzene unit and the πB–πQ transition of benzenoid to quinoid, respectively.34,35 For ATGO, an absorption peak at 304 nm similar to that in the UV-Vis spectrum of AT was observed. A new absorption peak at 415 nm was observed, and the peak was attributed to the polaron → π* band transitions, and the peak at 785 nm was ascribed to the π → polaron transitions, which demonstrated that GO was doped on the AT.36,37 Pristine Au NPs with a particle size of 15 nm show a surface plasmon resonance peak at approximately 525 nm in the visible spectrum.38 The surface plasmon resonance peaks of the assembled Au/ATGO composites become much broader owing to the strong inter-particle coupling of closely packed particles (Fig. 2(b)).
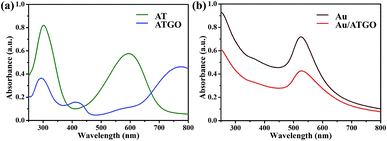 |
| Fig. 2 UV-Vis spectra of (a) AT and ATGO, and (b) Au and Au/ATGO composites. | |
XPS was also used to detect the compositions of the samples. The XPS profiles of GO, ATGO, and Au/ATGO composites are shown in Fig. 3. The characteristic peaks of C 1s and O 1s were observed in the profile of the three samples at 286.0 and 533.0 eV, respectively.39 A different peak assigned to N 1s was observed in the XPS profile of ATGO. The N 1s peak at 398.0 eV indicates the presence of AT.40,41 The existence of Au was confirmed by the Au 4f peak at approximate 87.0 eV, which is enlarged in Fig. 3(b). The diffused peaks with binding energies of 84.0 and 87.8 eV correspond well with Au 4f7/2 and Au 4f5/2 in the metallic state, respectively.42
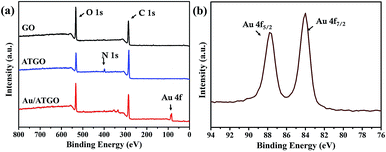 |
| Fig. 3 XPS profiles of (a) GO, ATGO, and Au/ATGO; Au 4f spectra of (b) Au/ATGO composites. | |
The morphologies of the GO, Au, Au/ATGO composites were characterized by TEM. As shown in Fig. 4(a), a typical 2D GO nanosheet by itself contains wrinkled structures, and the TEM image of pure Au NPs with a diameter of 15 nm is shown in Fig. 4(b). After the growth of Au NPs on the surface of the ATGO, the morphology of the ATGO remained unaltered. The TEM images of the Au/ATGO composites (Fig. 4(c and d)) clearly indicate that spherical Au NPs were anchored and well-distributed on the surface of the ATGO. The elemental mappings of the Au/ATGO composites shown in Fig. 4(e–h) indicates that the nanoparticles were caused by the Au NPs anchored on the ATGO.
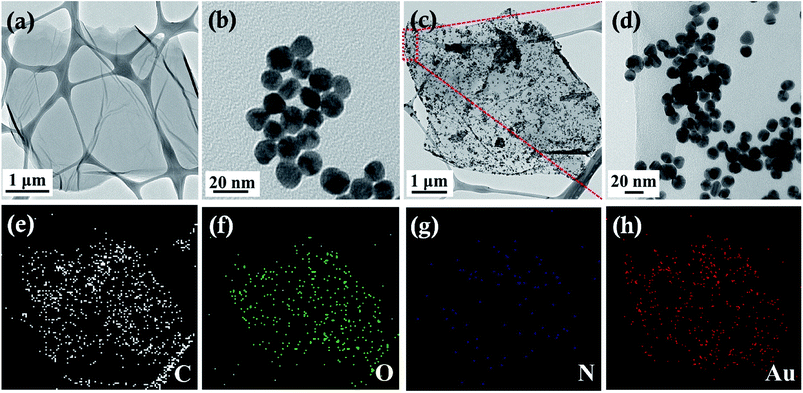 |
| Fig. 4 TEM images of (a) GO, (b) Au, (c) Au/ATGO composites, (d) high magnification of Au/ATGO composites shown in the area in (c), and (e–h) elemental mapping images. | |
The thermogravimetry analysis curves of GO, ATGO, and Au/ATGO composites showed an notable weight loss between 150 and 250 °C, which is attributed to the pyrolysis of the labile oxygen-containing functional groups that yielded CO, CO2, and steam.43 The TGA curves of GO and ATGO show a complete decomposition of carbon at approximately 525 °C. In contrast, carbon was completely decomposed in the Au/ATGO composites at a lower temperature of approximately 448 °C. A residual mass of approximately 33.4% indicates the loading of Au NPs in the Au/ATGO composites (Fig. 5).44
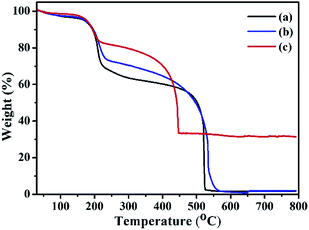 |
| Fig. 5 TGA curves of (a) GO, (b) ATGO, and (c) Au/ATGO composites. | |
Electrical properties of ATGO and Au/ATGO composite
To study the redox behavior of ATGO and Au/ATGO composites, two samples were systematically examined by CV in 40 mL of 1.0 M H2SO4 and a potential ranging from −0.2 to 1.0 V at a scan rate of 50 mV s−1. Fig. 6(a) shows the CV curves of the ATGO and Au/ATGO composites. Both the ATGO and Au/ATGO composites show two distinct pairs of redox peaks. This observation could be attributed to the change in the molecular structure of AT. The first oxidation peak corresponded to the transition from the leucoemeraldine base to the emeraldine base (EB), the second peak corresponded to the transition from EB to the pernigraniline base, as shown in Fig. 6(b).45,46 Furthermore, with the Au NPs acting as electrically conductive bridges inside the Au/ATGO composites, the diffusion length of the electrolyte ions was significantly reduced, resulting in an enhanced current when compared with that of the ATGO.47
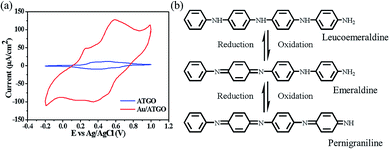 |
| Fig. 6 Representative CV curves of the (a) ATGO and Au/ATGO composites in H2SO4 solution. Scan rate: 50 mV s−1. (b) Molecular structures of ATGO at various oxidation states. | |
Catalytic characterization of Au/ATGO composites
Currently, water pollution and scarcity of consumable water resources have led to damaging consequences around the world, and this posed a threat to human life. Among the harmful toxins and compounds in polluted water, nitrophenol is one of the 126 priority pollutants listed by the United States Environmental Protection Agency.48,49 It is commonly found in wastewaters of industries that manufacture pesticide, dye, pharmaceutical, and petrochemical products.50 Aminophenol is an important intermediate in the preparation of several analgesics and antipyretic drugs.51,52 It is a strong reducing agent, and it is used as a corrosion inhibitor in paints as well as photographic development.53,54 Due to the aforementioned reasons, it is important to convert nitrophenol to aminophenol. Compared to other conversion routes, the method where NaBH4 is used as a reducing agent in an aqueous medium under mild conditions is relatively simple and quick.55
To evaluate the catalytic activity of the synthesized nanocatalyst samples, reduction of 4-NP and 2-NP by NaBH4 was first selected as the model reaction, which can be monitored by time-dependent UV-Vis spectroscopy. The aqueous solution of 4-NP is light yellow and it shows a strong absorption peak at 316 nm. After the addition of NaBH4, a color change from light yellow to deep yellow was observed, and a strong absorption peak at 400 nm appeared owing to the formation of 4-nitrophenolate ions (Fig. 7(a)).56,57 Furthermore, in the blank test, no change in the absorption intensity was observed for a long period with NaBH4, which indicates that the reduction reaction did not occur without the addition of the catalyst. After the addition of the Au/ATGO composites, the absorption peak at 400 nm owing to 4-nitrophenolate ions gradually decreased; at the same time, a new peak was observed at 296 nm indicating the formation of 4-AP.58 The Au/ATGO composites showed high activity and completed the reaction in 225 s (Fig. 7(b)).
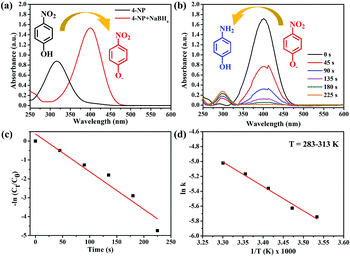 |
| Fig. 7 UV-Vis spectra of (a) 4-NP before and after addition of NaBH4, (b) time-dependent reduction process after the addition of Au/ATGO composites in the reaction. 4-NP reduction catalyzed by Au/ATGO composites in the presence of NaBH4. (c) The plot of −ln(Ct/C0) versus time, and (d) the plot of ln k versus 1/T based at different temperatures. | |
For a comparative study, the apparent rate constants were calculated for all the catalyst samples. Since NaBH4 (100 mM) was used in excess and remained approximately constant throughout the progression of the reaction, pseudo-first-order kinetics was applied for evaluating the apparent rate constants (kapp). The kapp values were calculated from linear plots of ln(Ct/C0) vs. reduction time t (Fig. 7(c)). Here, Ct and C0 represent the absorbance of 4-NP after time t = t and t = 0, which can be considered equivalent to the concentration at time t = t (Ct) and t = 0 (C0), respectively.59,60 The linear relationship between ln(Ct/C0) and t indicates the pseudo-first-order reduction of 4-NP by the Au/ATGO composites, and the calculated value of kapp was 0.021 s−1. A comparative study of 4-NP reduction with other catalysts is given in Table 1. Compare to other catalyst materials containing Au nanoparticles, Au/ATGO showed high catalytic performance. In this study, we also carried out a series of reactions for the reduction of 4-NP in the presence of Au/ATGO composites to obtain thermodynamic parameters that reveal how the reaction temperature can affect the kinetics of such a reaction. Apparently, the reaction rate is quite sensitive to temperature and the value of the rate constant, k, increases with temperature. In addition, according to the Arrhenius equation: ln
k = ln
A − Ea/RT, the activation energy (Ea) can be obtained from the slope based on the linear fitting of ln
k versus 1/T.61 The activation energy of the reaction catalyzed by Au/ATGO composites was determined from the Arrhenius plot to be 48.10 kJ mol−1.
Table 1 Comparative characteristics and catalytic performance of catalyzers in the reported literature
Catalyzer |
mg |
Degradation time (s) |
Rate constant (min−1) |
Ref. |
CB: carbon black. |
Au/GO |
0.02 |
720 |
0.15 |
23 |
Au/ZrP–SH |
7 |
420 |
0.19 |
64 |
Au/EPA |
0.5 |
270 |
0.42 |
65 |
Au/carbon black |
10 |
300 |
0.83 |
42 |
Au/ZrP–NH2 |
1 |
180 |
1.08 |
20 |
Ni–Au/HNO3–CBa |
5 |
180 |
1.96 |
56 |
Au/ATGO |
1 |
225 |
1.26 |
This work |
Based on the above results, we also used the Au/ATGO composites to perform the catalytic reduction of 2-NP, as shown in Fig. 8. The yellow solution of 2-NP exhibited two distinct absorption peaks at 278 and 350 nm. Following the addition of NaBH4, a color change from light yellow to deep yellow was observed, and the absorption peaks shifted to 282 and 416 nm owing to the formation of 2-nitrophenolate ions (Fig. 8(a)).62 However, adding Au/ATGO composites to a 2-NP and NaBH4 mixed solution caused a reduction in the intensity of the peak at 416 nm over time, indicating the formation of 2-AP.63 As shown in Fig. 8(b), it took 180 s for the complete reduction of 2-NP. As shown in Fig. 8(c), the kapp value was 0.02 s−1 and the Ea was 68.71 kJ mol−1. The results indicate that Au/ATGO composites exhibited significant activity during the reduction of nitrophenols with NaBH4 as the hydrogen donor.
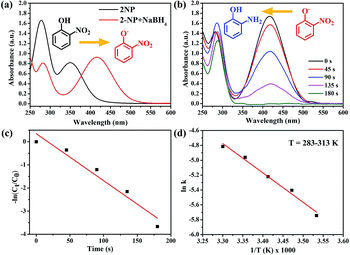 |
| Fig. 8 UV-Vis spectra of (a) 2-NP before and after addition of NaBH4, (b) time-dependent reduction process after the addition of Au/ATGO composites in the reaction. 2-NP reduction catalyzed by Au/ATGO composites in the presence of NaBH4 (c) the plot of −ln(Ct/C0) versus time, and (d) the plot of ln k versus 1/T based on different temperature. | |
Recycling tests
As shown in Fig. 9, the Au/ATGO composites can be easily separated by sedimentation and reused under the same reaction conditions. The reduction rate of 4-NP to 4-AP, and 2-NP to 2-AP was maintained above 94% and 96%, respectively, after 20 cycles; this indicates the high stability and reusability of the resulting Au/ATGO composites system.
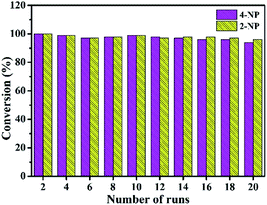 |
| Fig. 9 Recycling stability of the Au/ATGO composites system for catalytic reduction of nitrophenol to aminophenol. | |
Conclusions
In this study, stable, and reusable Au/ATGO composites were prepared and used as catalysts for the degradation reaction of nitrophenol. The synthesis of ATGO was based on the π–π interaction of GO and AT. Subsequently, the amine group on ATGO stably anchored Au nanoparticles (Au NPs) to form Au/ATGO composites. Furthermore, because of the growth of the Au NPs based on Au seeds, the catalyst was reused for more than 20 cycles and stored for over 2 months, while maintaining approximately the same catalytic performance (conversion rate above 94%). The Au/ATGO composites showed many advantages including high catalytic activity and excellent recyclability that makes them attractive for several other applications.
Conflicts of interest
There are no conflicts to declare.
Acknowledgements
We would like to thank the Ministry of Science and Technology, Taiwan under grant numbers MOST 108-2917-I-167-001, MOST 108-2221-E-167-020, MOST 108-2731-M-005-001, and MOST 109-2637-E-241-004 for their financial support. This material is based on work supported by the Research Center for Circular Economy at Chung-Yuan Christian University, Taiwan. We thank the Instrument Center of National Chung Hsing University for the help with the SEM, TEM, and XPS measurements.
References
- T. Hou, P. Gai, M. Song, S. Zhang and F. Li, J. Mater. Chem. B, 2016, 4, 2314–2321 RSC
. - T. S. Radoman, J. V. Džunuzović, B. N. Grgur, M. M. Gvozdenović, B. Z. Jugović, D. S. Miličević and E. S. Džunuzović, Prog. Org. Coat., 2016, 99, 346–355 CrossRef CAS
. - T. C. Huang, J. M. Yeh and C. Y. Lai, in Advances in Polymer Nanocomposites, ed. F. Gao, Woodhead Publishing, 2012, pp. 605–638 Search PubMed
. - C.-H. Chang, T.-C. Huang, C.-W. Peng, T.-C. Yeh, H.-I. Lu, W.-I. Hung, C.-J. Weng, T.-I. Yang and J.-M. Yeh, Carbon, 2012, 50, 5044–5051 CrossRef CAS
. - I. Fratoddi, I. Venditti, C. Cametti and M. V. Russo, Sens. Actuators, B, 2015, 220, 534–548 CrossRef CAS
. - L. Sun, S. Peng, L. Jiang, Y. Zheng, X. Sun, H. Su and C. Qi, Colloid Polym. Sci., 2019, 297, 651–659 CrossRef CAS
. - C.-M. Chang, C.-J. Weng, C.-M. Chien, T.-L. Chuang, T.-Y. Lee, J.-M. Yeh and Y. Wei, J. Mater. Chem. A, 2013, 1, 14719–14728 RSC
. - M. Chi, S. Wang, Y. Liang, D. Chao and C. Wang, J. Colloid Interface Sci., 2014, 423, 7–12 CrossRef CAS
. - J. Yan, L. Yang, M. Cui, X. Wang, K. J. Chee, V. C. Nguyen, V. Kumar, A. Sumboja, M. Wang and P. S. Lee, Adv. Energy Mater., 2014, 4, 1400781 CrossRef
. - Y. Zhou, E. B. Berda, Q. Ma, X. Liu, C. Wang and D. Chao, ChemElectroChem, 2019, 6, 5293–5300 CrossRef CAS
. - T.-C. Huang, T.-C. Yeh, H.-Y. Huang, W.-F. Ji, Y.-C. Chou, W.-I. Hung, J.-M. Yeh and M.-H. Tsai, Electrochim. Acta, 2011, 56, 10151–10158 CrossRef CAS
. - Y. Wang, H. D. Tran, L. Liao, X. Duan and R. B. Kaner, J. Am. Chem. Soc., 2010, 132, 10365–10373 CrossRef CAS
. - Y. Wang, J. Liu, H. D. Tran, M. Mecklenburg, X. N. Guan, A. Z. Stieg, B. C. Regan, D. C. Martin and R. B. Kaner, J. Am. Chem. Soc., 2012, 134, 9251–9262 CrossRef CAS
. - P. Li, Z. Qu, X. Chen, X. Huo, X. Zheng, D. Wang, W. Yang, L. Ji, P. Liu and X. Xu, J. Mater. Chem. C, 2017, 5, 6216–6223 RSC
. - H. Han, S. W. Lee, K. H. Moon and S. Cho, ACS Omega, 2019, 4, 1244–1253 CrossRef CAS
. - J.-M. Yeh, K.-Y. Huang, S.-Y. Lin, Y.-Y. Wu, C.-C. Huang and S.-J. Liou, J. Nanotechnol., 2009, 2009, 217469 Search PubMed
. - X.-k. Kong, Z.-y. Sun, M. Chen, C.-l. Chen and Q.-w. Chen, Energy Environ. Sci., 2013, 6, 3260–3266 RSC
. - X.-F. Zhang, X.-Y. Zhu, J.-J. Feng and A.-J. Wang, Appl. Surf. Sci., 2018, 428, 798–808 CrossRef CAS
. - Y. Li, J. Y. Lan, J. Liu, J. Yu, Z. Luo, W. Wang and L. Sun, Ind. Eng. Chem. Res., 2015, 54, 5656–5663 CrossRef CAS
. - G.-H. Lai, T.-C. Huang, Y.-H. Pai, B.-S. Huang, M.-H. Tsai, T.-I. Yang and Y.-H. Chung, J. Taiwan Inst. Chem. Eng., 2019, 95, 525–531 CrossRef CAS
. - Y.-Y. Ou and M. H. Huang, J. Phys. Chem. B, 2006, 110, 2031–2036 CrossRef CAS
. - H. Yao, L. Jin, H.-J. Sue, Y. Sumi and R. Nishimura, J. Mater. Chem. A, 2013, 1, 10783–10789 RSC
. - H. Yao, T.-C. Huang and H.-J. Sue, RSC Adv., 2014, 4, 61823–61830 RSC
. - G. H. Lai, T. C. Huang, I. H. Tseng, B. S. Huang, T. I. Yang and M. H. Tsai, eXPRESS Polym. Lett., 2019, 13, 772–784 CrossRef CAS
. - P. Li, T.-C. Huang, K. L. White, S. Hawkins, M. Kotaki, R. Nishimura and H.-J. Sue, RSC Adv., 2015, 5, 102633–102642 RSC
. - B.-S. Huang, G.-H. Lai, T.-I. Yang, M.-H. Tsai and Y.-C. Chou, Polymers, 2020, 12, 91 CrossRef CAS
. - H.-L. Guo, X.-F. Wang, Q.-Y. Qian, F.-B. Wang and X.-H. Xia, ACS Nano, 2009, 3, 2653–2659 CrossRef CAS
. - Y.-H. Yu, Y.-Y. Lin, C.-H. Lin, C.-C. Chan and Y.-C. Huang, Polym. Chem., 2014, 5, 535–550 RSC
. - L.-C. Yeh, T.-C. Huang, Y.-J. Lin, G.-H. Lai, T.-I. Yang, A.-Y. Lo and J.-M. Yeh, Int. J. Green Energy, 2016, 13, 1334–1341 CrossRef CAS
. - H.-Y. Huang, J.-W. Jian, Y.-T. Lee, Y.-T. Li, T.-C. Huang, J.-H. Chang, L.-C. Yeh and J.-M. Yeh, Polymer, 2012, 53, 4967–4976 CrossRef CAS
. - L.-C. Yeh, T.-C. Huang, F.-Y. Lai, G.-H. Lai, A.-Y. Lo, S.-C. Hsu, T.-I. Yang and J.-M. Yeh, Surf. Coat. Technol., 2016, 303, 154–161 CrossRef CAS
. - T.-C. Huang, L.-C. Yeh, G.-H. Lai, B.-S. Huang, T.-I. Yang, S.-C. Hsu, A.-Y. Lo and J.-M. Yeh, Int. J. Green Energy, 2017, 14, 113–120 CrossRef CAS
. - Y. Ding, J. Liang, G. Liu, W. Ni and L. Shen, Coatings, 2019, 9, 399 CrossRef CAS
. - S. Wang, D. Chao, E. B. Berda, X. Jia, R. Yang, X. Wang, T. Jiang and C. Wang, RSC Adv., 2013, 3, 4059–4065 RSC
. - H.-Y. Huang, T.-C. Huang, J.-C. Lin, J.-H. Chang, Y.-T. Lee and J.-M. Yeh, Mater. Chem. Phys., 2013, 137, 772–780 CrossRef CAS
. - T. Liu, J. Li, X. Li, S. Qiu, Y. Ye, F. Yang and H. Zhao, Prog. Org.
Coat., 2019, 128, 137–147 CrossRef CAS
. - A. A. Salem and B. N. Grgur, Prog. Org. Coat., 2018, 119, 138–144 CrossRef CAS
. - J. Zhu, H.-f. Du, Q. Zhang, J. Zhao, G.-j. Weng, J.-j. Li and J.-w. Zhao, J. Mater. Chem. C, 2019, 7, 3322–3334 RSC
. - J. Chen, B. Yao, C. Li and G. Shi, Carbon, 2013, 64, 225–229 CrossRef CAS
. - T.-C. Huang, L.-C. Yeh, H.-Y. Huang, Z.-Y. Nian, Y.-C. Yeh, Y.-C. Chou, J.-M. Yeh and M.-H. Tsai, Polym. Chem., 2014, 5, 630–637 RSC
. - T. C. Huang, L. C. Yeh, G. H. Lai, F. Y. Lai, T. I. Yang, Y. J. Huang, A. Y. Lo and J. M. Yeh, eXPRESS Polym. Lett., 2016, 10, 450–461 CrossRef CAS
. - L. Qin, H. Yi, G. Zeng, C. Lai, D. Huang, P. Xu, Y. Fu, J. He, B. Li, C. Zhang, M. Cheng, H. Wang and X. Liu, J. Hazard. Mater., 2019, 380, 120864 CrossRef CAS
. - M.-H. Tsai, I. H. Tseng, J.-C. Chiang and J.-J. Li, ACS Appl. Mater. Interfaces, 2014, 6, 8639–8645 CrossRef CAS
. - P. Kar, S. Sardar, B. Liu, M. Sreemany, P. Lemmens, S. Ghosh and S. K. Pal, Sci. Technol. Adv. Mater., 2016, 17, 375–386 CrossRef CAS
. - L.-C. Yeh, T.-C. Huang, Y.-P. Huang, H.-Y. Huang, H.-H. Chen, T.-I. Yang and J.-M. Yeh, Electrochim. Acta, 2013, 94, 300–306 CrossRef CAS
. - H.-Y. Huang, Y.-T. Lee, L.-C. Yeh, J.-W. Jian, T.-C. Huang, H.-T. Liang, J.-M. Yeh and Y.-C. Chou, Polym. Chem., 2013, 4, 343–350 RSC
. - M. H. Tsai, S. H. Lu, Y. H. Lai, G. H. Lai, G. V. Dizon, T. I. Yang, Y. J. Lin and Y. C. Chou, eXPRESS Polym. Lett., 2018, 12, 71–81 CrossRef CAS
. - P. Deng, Z. Xu, Y. Feng and J. Li, Sens. Actuators, B, 2012, 168, 381–389 CrossRef CAS
. - A. Verma, S. Kumar, W.-K. Chang and Y.-P. Fu, Dalton Trans., 2020, 49, 625–637 RSC
. - H. G. Soğukömeroğulları, Y. Karataş, M. Celebi, M. Gülcan, M. Sönmez and M. Zahmakiran, J. Hazard. Mater., 2019, 369, 96–107 CrossRef
. - T. Wi-Afedzi, F.-Y. Yeoh, M.-T. Yang, A. C. K. Yip and K.-Y. A. Lin, Sep. Purif. Technol., 2019, 218, 138–145 CrossRef CAS
. - H. Koga and T. Kitaoka, Chem. Eng. J., 2011, 168, 420–425 CrossRef CAS
. - D. Xu, P. Diao, T. Jin, Q. Wu, X. Liu, X. Guo, H. Gong, F. Li, M. Xiang and Y. Ronghai, ACS Appl. Mater. Interfaces, 2015, 7, 16738–16749 CrossRef CAS
. - Z.-S. Lv, X.-Y. Zhu, H.-B. Meng, J.-J. Feng and A.-J. Wang, J. Colloid Interface Sci., 2019, 538, 349–356 CrossRef CAS
. - Y. Ma, X. Wu and G. Zhang, Appl. Catal., B, 2017, 205, 262–270 CrossRef CAS
. - L. Qin, Z. Zeng, G. Zeng, C. Lai, A. Duan, R. Xiao, D. Huang, Y. Fu, H. Yi, B. Li, X. Liu, S. Liu, M. Zhang and D. Jiang, Appl. Catal., B, 2019, 259, 118035 CrossRef CAS
. - Y. Xu, F. Zhou, M. Chen, H. Hu, L. Lin, J. Wu and M. Zhang, New J. Chem., 2020, 44, 9793–9801 RSC
. - W.-J. Liu, K. Tian, H. Jiang and H.-Q. Yu, Green Chem., 2014, 16, 4198–4205 RSC
. - X.-Y. Zhu, Z.-S. Lv, J.-J. Feng, P.-X. Yuan, L. Zhang, J.-R. Chen and A.-J. Wang, J. Colloid Interface Sci., 2018, 516, 355–363 CrossRef CAS
. - M. Liu, H. Yang, Z. Xu, W. Ma, F. Cui, G. Lu, L. Xu and T. Cui, New J. Chem., 2020, 44, 7035–7041 RSC
. - S. R. Thawarkar, B. Thombare, B. S. Munde and N. D. Khupse, RSC Adv., 2018, 8, 38384–38390 RSC
. - H. Liu and Q. Yang, J. Mater. Chem., 2011, 21, 11961–11967 RSC
. - E. Abroushan, S. Farhadi and A. Zabardasti, RSC Adv., 2017, 7, 18293–18304 RSC
. - Y. Zhou, H. Ding, J. Liu, A. M. LaChance, M. Xiao, Y. Meng and L. Sun, Adv. Compos. Hybrid Mater., 2019, 2, 520–529 CrossRef CAS
. - G.-H. Lai, B.-S. Huang, T.-I. Yang, M.-H. Tsai and Y.-C. Chou, Polymer, 2020, 123200, DOI:10.1016/j.polymer.2020.123200
.
|
This journal is © The Royal Society of Chemistry 2021 |
Click here to see how this site uses Cookies. View our privacy policy here.