DOI:
10.1039/D0RA02266G
(Paper)
RSC Adv., 2020,
10, 17713-17723
Dip-coating decoration of Ag2O nanoparticles on SnO2 nanowires for high-performance H2S gas sensors
Received
11th March 2020
, Accepted 30th April 2020
First published on 6th May 2020
Abstract
SnO2 nanowires (NWs) are used in gas sensors, but their response to highly toxic gas H2S is low. Thus, their performance toward the effective detection of low-level H2S in air should be improved for environmental-pollution control and monitoring. Herein, Ag2O nanoparticle decorated SnO2 NWs were prepared by a simple on-chip growth and subsequent dip-coating method. The amount of decorated Ag2O nanoparticles on the surface of SnO2 NWs was modified by changing the concentration of AgNO3 solution and/or dipping times. Gas-sensing measurements were conducted at various working temperatures (200–400 °C) toward different H2S concentrations ranging within 0.1–1 ppm. The selectivity of Ag2O-decorated SnO2 NW sensors for ammonia and hydrogen gases was tested. Results confirmed that the Ag2O-decorated SnO2 NW sensors had excellent response, selectivity, and reproducibility. The gas-sensing mechanism was interpreted under the light of energy-band bending by sulfurization, which converted the p–n junction into n–n, thereby significantly enhancing the sensing performance.
1. Introduction
Air pollution caused by H2S gas is extremely dangerous even at low concentrations (sub-ppm level) because this gas is colorless, flammable, and highly toxic.1 The sources of H2S are very diverse2 because it can be produced naturally from crude petroleum, oil drilling, and volcano eruption or from the bacterial decomposition of organic matter in anaerobic environments.3 H2S is also produced as a by-product in biogas plants during waste treatment.4 The effects of H2S on the human body are summarized in Table 1.5 The threshold odor concentration of H2S is about 10 ppb, but its toxic concentration range is very broad (i.e., from ppb to ppm). The threshold limit of H2S is reportedly 0.003 ppm for 8 h of exposure.5 However, the permissible concentration of H2S recommended by the Scientific Advisory Board on Toxic Air Pollutants (USA) ranges within 20–100 ppb.6 Thus, effective gas sensors for detecting low levels of H2S under field conditions are urgent to develop.2
Table 1 Effects of exposure to H2S.5
Concentration (ppm) |
Effects |
0.003–0.02 |
Approximate threshold for odor |
3–10 |
Obvious offensive odor |
50–100 |
Serious eye irritation and respiratory tract irritation |
100–200 |
Loss of smell |
250–500 |
Fluid buildup in lungs and imminent threat to life |
500 |
Anxiety, headache, dizziness, excessively rapid respiration, amnesia, and unconsciousness |
500–1000 |
Immediate collapse, irregular heartbeat, neural paralysis, and respiratory paralysis leading to death |
Many techniques for H2S detection have been developed, but metal oxide-based resistive-type gas sensors are advantageous because of their low cost, high sensitivity, real-time detection, portability, and low power consumption.7–10 SnO2 (ref. 11) is one of the most popular materials for such sensors because of its relatively high sensitivity to various gases, as well as its feasibility in functionalization to improve sensing performance.12,13 However, SnO2 has the main drawback of low response to low concentration of H2S14 and poor selectivity over air-polluting gases such as NH3, H2S, and CO.15,16 This problem can be solved by using heterojunctions between two dissimilar semiconducting materials, which utilizes the unique effects and leads to enhanced sensor performance.15 Nano-heterostructures are often utilized owing to their small size and high surface-to-volume ratio,17,18 and many efforts have been devoted to the fabrication of p–n heterojunctions for increasing H2S-sensing performance.19–24 The most common p–type metal oxides used to form heterojunctions with n-type SnO2 semiconductor are CuO,18,25 NiO,26,27 and Co3O4 (ref. 24) because of their easy sulfidation into CuS, NiS, and CoS, respectively. However, sensors with these oxides can detect H2S gas only at high concentrations of >10 ppm28 because the sulfidation of transition-metal oxides requires a high supply of sulfur source.29 Meanwhile, Ag2O has unique characteristics that enable it to functionalize SnO2 nanomaterials to enhance gas-sensing performance to different gases such as H2,30 ethanol,31 and CO.32 The decoration of p-type Ag2O on the surface of n-type SnO2 is advantage over the use of metallic Ag because it forms the p–n heterojunction, thus enhances the gas sensing performance.33–35 Ag2O is also reported easily converted into Ag2S in the presence of H2S36 because of its low free Gibbs energy for the reaction. The free Gibbs energy for conversion of Ag2O, CuO, and NiO into Ag2S, CuS, and NiS in the present of H2S gas is −224.7, −119.1, and −62.5 kJ mol−1, respectively. Therefore, decoration of Ag2O nanoparticles on the surface of SnO2 is expected to show better sensing performance such as low detection limit of H2S with higher sensitivity than others. However, few studies have focused on improving of H2S-sensing properties using Ag2O/SnO2 thin film.33–35 It is hard to find the related work reported on the decoration of Ag2O on the surface of SnO2 NWs for enhanced H2S gas despite the significantly higher stability of NWs than their thin-film counterparts.37 Doped thick films have shown good sensitivity to low concentrations of H2S but are not feasible to miniaturize.33 Decorated thin films present poor response to high concentrations of H2S.34 A previous work35 has reported extremely low response (99%) to the high H2S concentration of 50 ppm at 74 °C. Our group has recently reported the H2S-sensing characteristics of self-heated Ag-coated SnO2 NWs, where the decoration of Ag is realized by sputtering method.38 However, this method requires vacuum conditions and expensive equipment for Ag decoration, and the content of Ag2O nanoparticles on the surface of SnO2 NWs are difficult to control. Thus, a low-cost, suitable, and effective method for functionalizing p-type Ag2O nanoparticles with low activation energy for reversible sulfidation and oxidation, as well as enhanced H2S-sensing performance of SnO2 NWs, must be developed.
Herein, we reported the dip-coating decoration of Ag2O nanoparticles on the surface of on-chip-grown SnO2 NWs to enhance their H2S gas-sensing performance. Decoration was realized by dipping the sensor in AgNO3 solution, followed by oxidation to form Ag2O nanocrystals on the surface of SnO2 NWs. The effects of Ag2O content on the H2S gas-sensing performance of the SnO2 NWs were studied to maximize sensor response to H2S. Results demonstrated that the sensors processed excellent performance for monitoring extremely low H2S concentrations. The H2S gas-sensing mechanism of the SnO2 NWs functionalized with Ag2O nanoparticles was also discussed through the perspective of band-structure and sulfurization process.
2. Experimental
The preparation of SnO2 NWs-based sensors has been described in our previous publication.14 The NW sensors were directly grown on thermally oxidized silicon substrate using a chemical vapor deposition system, as shown in Scheme 1(A).39 In a typical procedure, SnO2 NWs were grown on seeded Pt electrodes at 750 °C from a starting material of Sn powder through thermal evaporation. Growth proceeded at 750 °C for 20 min with an oxygen gas flow of 0.5 sccm and pressure of 1.8 × 10−1 torr. For one batch of fabrication, up to 8 sensors were obtained, as shown in Scheme 1(B). The SnO2 NWs were homogenously grown on the Pt electrode fingers, as shown in Scheme 1(C). The bare SnO2 NWs sensors were decorated with Ag2O nanoparticles by dip coating in AgNO3 solutions and subsequent annealing at 500 °C for 3 h in air. This decoration method had the advantage over the sputtering method of not requiring vacuum conditions.38 The density of Ag2O nanoparticles decorated on the surface of SnO2 NWs was controlled by varying the concentration of AgNO3 solution (0.05, 0.2, and 1 mM) and the dipping times (1, 5, and 20 times). The samples were denoted as S0, S1, S2, S3, S4, and S5 (Table 2). The morphology, chemical composition and structural characteristics of pristine and Ag2O-decorated SnO2 NWs were investigated by scanning electron microscopy (SEM; JEOL 7600F), energy-dispersive X-ray spectroscopy (EDS), high-resolution transmission electron microscopy (HRTEM; JEOL 2100F), and X-ray diffraction (XRD; D8 Advance).3
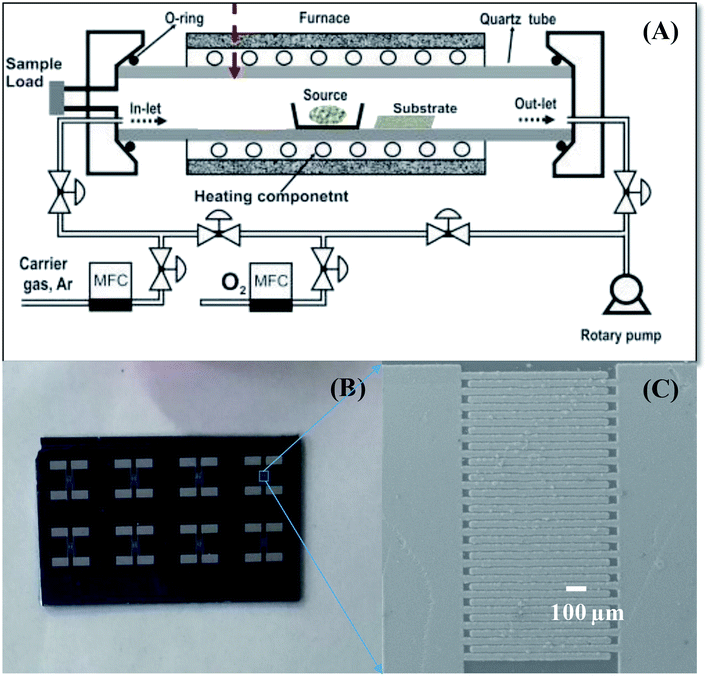 |
| Scheme 1 . Sensor fabrication process: (A) CVD system used to grow SnO2 NWs, (B) photo of sensor chips; (C) SnO2 NW sensor after fabrication. | |
Table 2 Samples at different AgNO3 concentrations and dipping times
Sample |
AgNO3 concentration (mM) |
Dipping times |
S0 |
0 |
0 |
S1 |
0.05 |
1 |
S2 |
0.2 |
1 |
S3 |
1 |
1 |
S4 |
1 |
5 |
S5 |
1 |
20 |
Gas-sensing properties were measured using a SourceMeter® Keithley 2602B. Details about the gas-sensing measurement system are described elsewhere.40 Dry air was used as reference and diluting gas. Sensor response to different H2S concentrations (0.1–1 ppm) at various working temperatures (200, 250, 300, 350, and 400 °C) were investigated. The selectivity among reducing gases (including ammonia and hydrogen) and the reproducibility of the sensors were also tested. During gas-sensing measurements, sensor resistance was continuously recorded, and the target gas and dry air were alternatively switched on/off. Gas response was defined as S = Ra/Rg for the reducing gas H2S, where Ra and Rg are the sensor resistances in air and in target gas, respectively.3
3. Results and discussion
3.1. Material characterization
We did not characterize all samples and instead selected sensors S1, S2, and S5 for SEM, EDS, and TEM analysis. Fig. 1(A) illustrates a SEM image of SnO2 NWs (S1) grown on patterned Pt electrodes. Notably, the electrode finger was 20 μm wide [inset of Fig. 1(A)]. Although the gap between two electrode fingers was 20 μm, the grown SnO2 NWs can still efficiently cover the gaps, as shown in the inset of Fig. 1(A). SnO2 NWs grew primarily on the surface of Pt electrode fingers, but their lengths were controlled sufficiently to connect between the fingers and thus act as conducting channels in the gas-sensing measurement. The average diameter of SnO2 NWs was approximately 70 nm. The surface of pristine SnO2 NWs was as smooth as that of the single crystal. This result was consistent with the growth of SnO2 NWs by vapor–liquid–solid mechanism.41 Herein, we did not use Au as catalyst during the growth of SnO2 NWs, so belt-like NWs were obtained at the initial state. A SnO2 NW comprises a single crystal, as reported in our previous article.14 Composition analysis of the SnO2 NW by EDS [Fig. 1(B)] revealed the existance of O, Sn, and Pt elements. Pt was originally from the electrode, whereas O and Sn were from the SnO2 NWs.
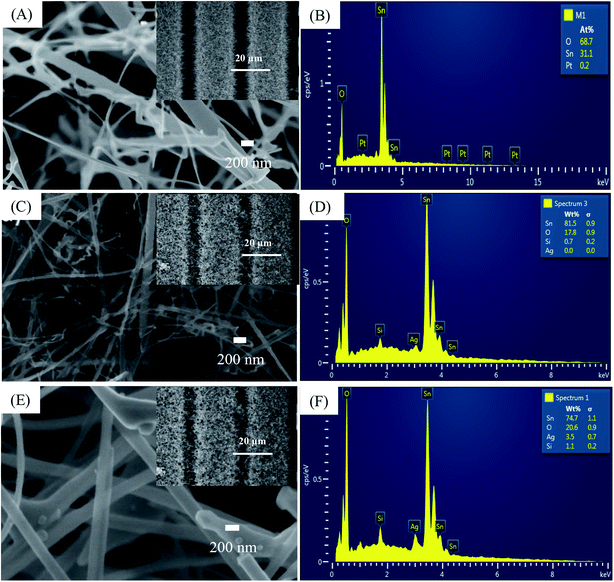 |
| Fig. 1 SEM images and EDS analysis of: (A and B) sensor S1 (0.05 mM); (C and D) sensor S2 (0.2 mM), (E and F) sensor S5 (1 mM). Insets are correspondent sensors' fringes. | |
The SEM image of SnO2 NWs after decoration with Ag2O nanoparticles (S2) is presented in Fig. 1(C), whose inset is a low-magnification SEM image. The electrode fingers were covered by the SnO2 NWs. Ag2O decoration by dip coating maintained the morphology of the SnO2 NWs, but their surface was not as smooth as that of the pristine sample and tiny particles can be seen in the SEM images. The high-magnification SEM image revealed the presence of Ag2O nanoparticles on the surface of SnO2 NWs. EDS composition analysis of S2 [Fig. 1(D)] confirmed the presence of Ag at an energy of 2.98 eV despite the quantitative evaluation displaying a value of zero.
The SEM image of S5 is shown in Fig. 1(E), whose inset is a low-magnification SEM image of S5. With increased AgNO3 amount in dipping solution and dipping times, the morphology of the SnO2 NWs slightly changed. More tiny particles can be seen in the SEM image of S5, but the sample maintained its entangled NW morphology. Whether the Ag2O nanoparticles continuously or discontinuously decorated the surface of SnO2 NWs was difficult to observe simply by SEM observation. However, the surface of the samples was found to have increased roughness with increased Ag2O decoration. EDS composition analysis of S5 [Fig. 1(F)] showed that the content of Ag was very high (about 3.5 wt%). This result demonstrated that increasing the concentration of AgNO3 solution and the dipping times can increase the content of Ag2O nanoparticles decorated on the surface of SnO2 NWs for effective H2S detection.
To further study the decoration of Ag2O on the surface of SnO2 NWs, we selected S1, S2, and S5 for TEM characterizations. The grown SnO2 NWs had a very smooth and clean surface [Fig. 2(A)]. The average diameter of a SnO2 NW was approximately 70 nm, consistently with the observation by SEM images. No Ag2O nanoparticle was observed in this sample possibly because the AgNO3 concentration of the dipping solution was too low. The HRTEM images of S2 and S5 are shown in Fig. 2(B), and (C), respectively. The black dots decorated on the SnO2 NWs surface were Ag2O nanoparticles. Given that S2 was decorated by a low concentration of AgNO3 (0.2 mM) solution, the density of Ag2O nanoparticles on the surface of SnO2 NWs was very low [Fig. 2(B)] and the particle sizes were about 7 nm. The size and density of Ag2O increased with increased AgNO3 concentration (1 mM, 20 times of dipping), as observed in S5 [Fig. 2(C)]. The diameter of Ag2O nanoparticles decorated on the surface of SnO2 NWs ranged within 5–20 nm. However, they were still smaller than the diameter of SnO2 NWs. The wettability of AgNO3 solution on the SnO2 NW surface is very important for the decoration of Ag2O nanoparticles performed by dipping method. Wettability ensures the homogenous decoration of Ag2O nanoparticles on the total surface of SnO2 NWs. At a high density, Ag2O particles may agglomerate and form a large cluster. A high-magnification HRTEM image of about 5 nm Ag2O nanoparticle is shown in Fig. 2(D). The interspacing of ∼0.23 nm, which corresponded to the (200) lattice plane of cubic structured Ag2O,42 was observed. This result was consistent with a previous one on the thermal decomposition of AgNO3 at 250–440 °C (ref. 43) into Ag. Then, Ag was oxidized into Ag2O at an oxidation temperature of about 350–500 °C.44 In the process of e-beam decoration, Ag nanoparticles are anisotropically decorated on one side of NWs but not homogenously.31 Herein, the wet chemical method was used to ensure that nanoparticles were homogenously decorated on the surface of the NWs. Notably, S5 had larger Ag2O nanoparticles than S2, but decoration was not continuous because overdecoration of Ag2O nanoparticles can reduce sensor response.45
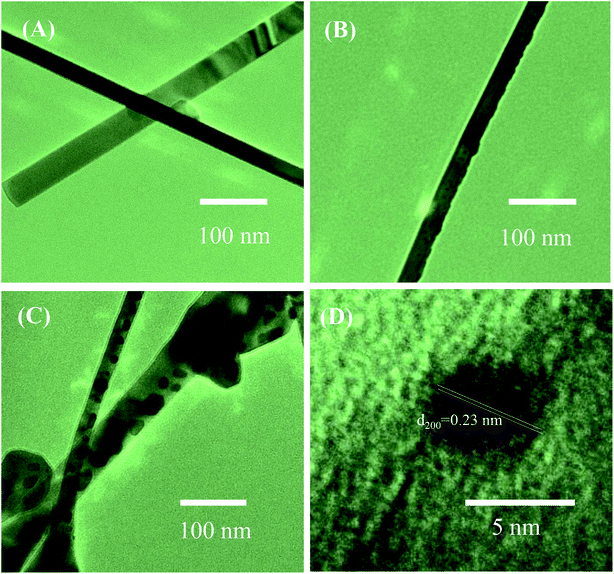 |
| Fig. 2 TEM images of SnO2 nanowires and SnO2 nanowires decorated with Ag2O nanoparticles: (A) sensor S1; (B) sensor S2, (C) sensor S5; (D) HRTEM image of Ag2O nanoparticle on the surface of nanowire. | |
3.2. Gas-sensing characteristics
Fig. 3(A)–(F) show the changes in transient resistance with time of S0–S5, respectively, upon exposure to various H2S concentrations (0.1, 0.25, 0.5, and 1 ppm) measured at different working temperatures (200, 250, 300, 350, and 400 °C). S0 showed significant response to H2S at all measured temperatures, but the response and recovery times were very long at low working temperature [Fig. 3(A)]. At a working temperature of 200 °C, S0 required almost 1.5 h to finish one measurement at four concentrations of H2S. Thus, stair-type tests were conducted for H2S gas sensing because of the slow recovery characteristics [Fig. 3(B)–(F)]. This finding indicated that measurements were conducted through a stepwise increase in H2S concentration from 0.1 ppm to 1 ppm before finally being refreshed by dry air. The obtained plots illustrated that the resistance of pristine and decorated SnO2 NW sensors steeply increased when H2S gas was injected into the test chamber [Fig. 3(B)–(F)]. The resistance then recovered to the initial values when H2S was replaced by dry air. All these sensors presented the typical n-type gas-sensing behavior of SnO2 NW semiconductor, where resistance decreased with increased H2S gas exposure. The base resistance in air of pristine SnO2 NWs (S0) was much smaller than that of Ag2O-decorated SnO2 sensors from S1 to S5. S5, with the largest amount of Ag2O decoration, had the highest resistance values in air of about 7 MΩ at 200 °C. Notably, Ag2O is also a good conductor, so the high base resistance value of S5 confirmed that the nanoparticles decorated on the surface of SnO2 NW formed the p–n heterojunction. Based on the plot of transient resistance versus time of the sensors, we roughly estimated that the response values increased but the recovery rate of the sensors decreased with increased Ag2O decoration.
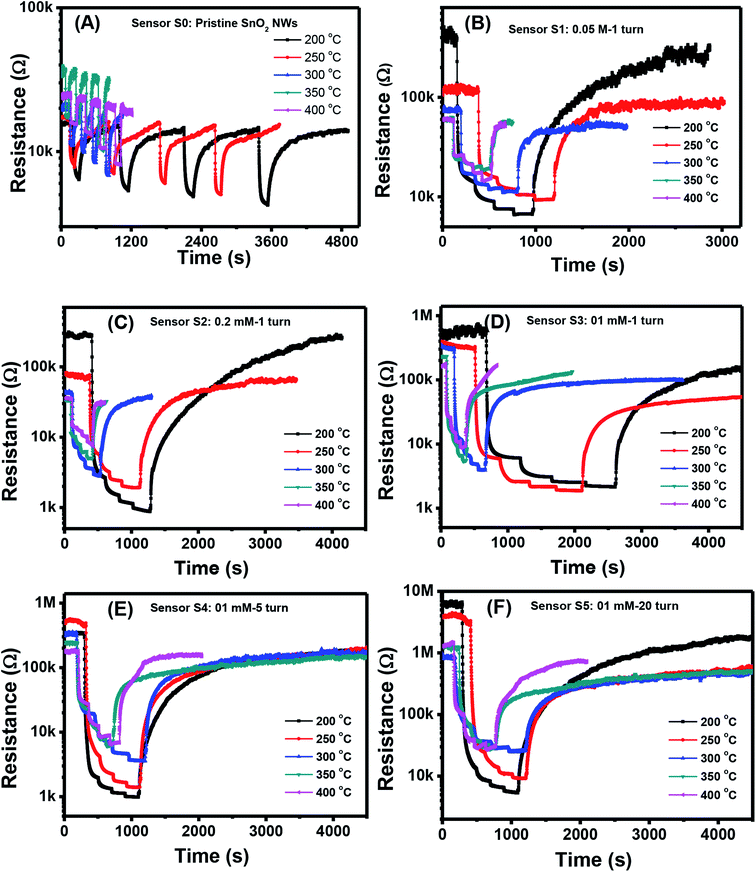 |
| Fig. 3 Transient response to different H2S concentrations various working temperature of the sample: S0 (A), S1 (B), S2 (C), S3 (D), S4 (E), S5 (F). | |
The quantitative response values of different sensors are shown in Fig. 4(A)–(F). The response values of all sensors decreased with increased working temperature within the measured range. This result was similar to that of other metal-oxide-based H2S gas sensors.46 The pristine SnO2 NW sensor (S0) had the highest response value of less than 4 over all the range of working temperatures and gas concentrations [Fig. 4(A)]. The response values for 1 ppm H2S decreased almost linearly from 3.6 to 2.9 with increased working temperature from 200 °C to 400 °C. These values were very low compared with the response of Ag2O-decorated SnO2 NW sensors [Fig. 4(B)–(F)]. The responses of Ag2O-decorated SnO2 NW sensors from S1 to S5 were much higher than that of pristine SnO2 NWs, S0. The responses of Ag2O-decorated SnO2 NW sensors increased with increased amount of decorated Ag2O nanoparticles. All sensors showed better response at lower operating temperatures, reaching the highest values at 200 °C within the measured range. The response values to 1 ppm H2S at 200 °C of S1–S5 were approximately 61, 358, 392, 690 and 1155, respectively. The response to 1 ppm H2S at 200 °C of S5 was about 320-fold higher than that of S0 under the same measurement condition. Notably, the maximum response to 1 ppm H2S gas of rGO-loaded Fe2O3 nanofibers is only 9.2.46 Herein, all sensors had decreased response values with increased working temperature from 200 °C to 400 °C. The response to 0.1 ppm H2S at 400 °C of S1 was 2.5, whereas that of S5 was much higher at about 16. Clearly, within the studied H2S concentration range (0.1–1 ppm), S5 had the best sensing performance because of its high sensitivity. This finding can be attributed to the p–n heterojunctions between Ag2O nanoparticles on the surface and SnO2 NWs,31,47 similar to the p–n heterojunctions between CuO and SnO2 (ref. 19) or NiO and SnO2.21 Details about the gas-sensing mechanism are discussed in subsequent sections.
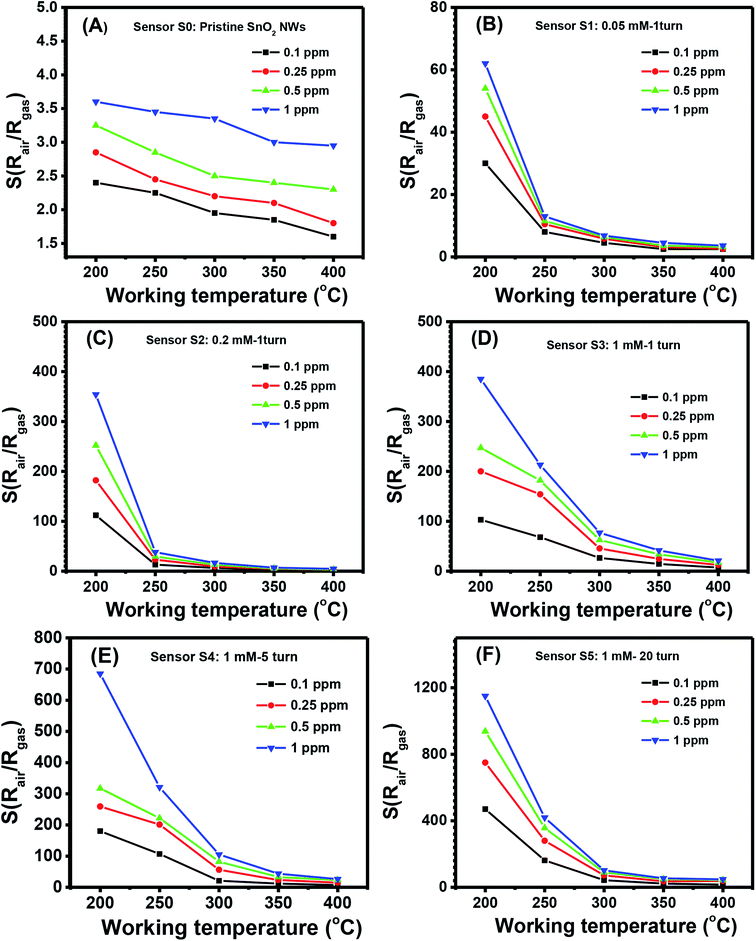 |
| Fig. 4 Response to different H2S concentrations various working temperature of the sample: S0 (A), S1 (B), S2 (C), S3 (D), S4 (E), S5 (F). | |
The response values of different sensors measured at 200 °C as a function of H2S concentration are shown in Fig. 5(A). With a low content of Ag2O decoration (S0 to S4), the response values increased almost linearly with H2S concentration in the measured range, but their values were low. The highest response value of the sensor S0 at 200 °C for 1 ppm H2S is about 3.7. S5 had the highest response values, and the response values increased nonlinearly with H2S concentration. Along with the gas response, the recovery time of the sensor is very important in practical applications because it determines sensor reusability. The effects of working temperature on the recovery time of Ag2O-decorated SnO2 NW sensor are shown in Fig. 5(B). Obviously, the sensor had very poor recovery characteristics at low working temperatures of 200, 250, and 300 °C, i.e., resistance did not recover to the initial value after refreshing for 1000 s. However, the sensor presented 100% recovery characteristics at working temperatures of 350 and 400 °C, with a recovery time of approximately 70 s. In practical application, balance should be achieved between sensor sensitivity and recovery depending on the objective of the application. For instance, the sensors based on 2D materials have poor recovery characteristics, but they could operate at room temperature, thus suitable for low power consumption devices.48,49 Herein, the long recovery time is possible due to the formation enthalpy of Ag2S (−32.6 kJ mol−1) is lower than that of Ag2O (−31 kJ mol−1), thus it requires higher energy to break the bonding of Ag2S than that of Ag2O compound. As a result, the sensor has longer recovery time than the response time. The selectivity of S5 toward three reducing gases H2S, NH3, and H2 was tested, and the results are shown in Fig. 5(C). At a low working temperature of 200 °C, the sensor did not show good recovery to H2S, so we tested the selectivity at 250, 300, 350, and 400 °C. Results demonstrated that S5 had the highest response toward 0.5 ppm H2S despite the 1000-fold concentration in all working temperatures. At a working temperature of 400 °C, S5 still had a high response value of 44–0.5 ppm H2S, whereas the corresponding values for 500 ppm NH3 and 500 ppm H2 were 1.16 and 11, respectively. Reproducibility and repeatability are also important properties of a gas sensor; thus, we tested the short-term stability of the sensor by switching on/off the ambient from air to 0.25 ppm H2S gas and back to air at a working temperature of 250 °C. As shown in Fig. 5(D), excepted for the first cycle, the sensor exhibited good recovery characteristics for 10 pulses of measurement, where the base resistance recovered to the initial value after refreshing the chamber with air. The relative standard deviation (RSD) was calculated by the equation 100 × S/|
|, where S is the sample standard deviation,
is sample mean. The RSD value of the sensor for ten pulses measurement is 92.4%, indicating the good reproducibility of the device. However, for real application, long term stability of the sensor should be studied. This work will be characterized in next step, and the data will be reported elsewhere.
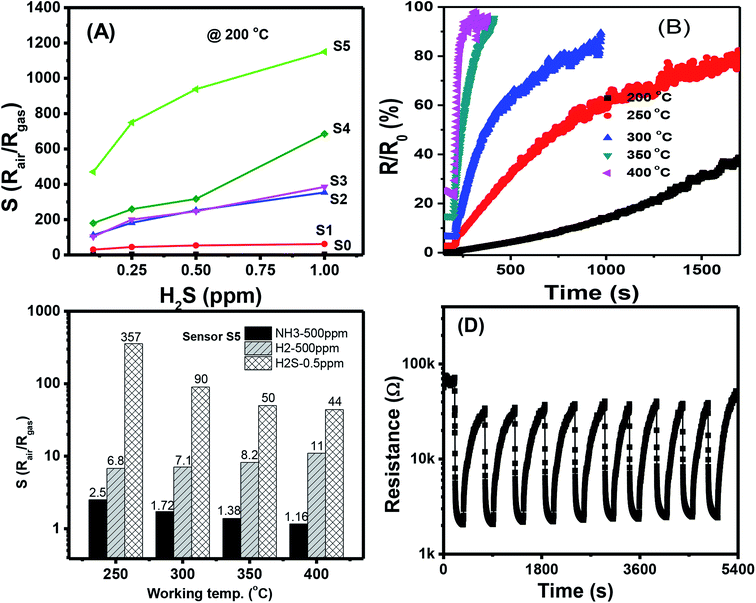 |
| Fig. 5 (A) Comparative response of different sensors at 200 °C; (B) response time of sensor S5 measured at different temperatures; (C) response of the sensor S5 at different working temperatures to various gases; (D) stability of the sensor S5 for 10 cycles measured at 250 °C. | |
For a better vision, the H2S sensing performances of the sensors based on functionalized-SnO2 nanomaterials are summarized in Table 3. Compared to other results in the references, our sensor showed comparable working temperature whereas was superior in response toward much lower concentration. This means that the Ag2O decoration on the surface of SnO2 NWs is suitable for development of high performance H2S gas sensor.
Table 3 A comparative result on the functionalized-SnO2 gas sensors for H2S detection
Material |
Conc. (ppm) |
Working temp (°C) |
Response (Ra/Rg) |
Response/recovery times (s) |
Ref. |
S = (Rair − Rgas)/Rair. |
Ag2O–SnO2 thin film |
50 |
74 |
99a |
>600/4500 |
35 |
CuO–SnO2 NWs |
80 |
300 |
1280 |
1/828 |
23 |
NiO–SnO2 NWs |
10 |
300 |
1372 |
11/102 |
21 |
CuO–SnO2 NWs |
10 |
250 |
26.3 |
180/600 |
19 |
CuO–SnO2 nanofibers |
10 |
150 |
3000 |
2/3000 |
25 |
CuO–SnO2 thin film |
100 |
180 |
25.3 |
10/42 |
22 |
CuO–SnO2 hollow spheres |
1 |
300 |
22.4 |
500/1000 |
50 |
Ag2O–SnO2 mesoporous |
1 |
100 |
71.5 |
390/1600 |
33 |
NiO–SnO2 nanoweb |
100 |
300 |
∼6 |
N/A |
26 |
NiO–SnO2 thin film |
10 |
Room |
440 |
2000/30 000 |
27 |
Ag2O–SnO2 NWs |
0.5 |
— |
21 |
12/1000 |
51 |
SnO2 NWs |
1 |
— |
∼3.5 |
50/200 |
14 |
Ag2O–SnO2 NWs |
1 |
200 |
1150 (S5) |
350/4000 |
This work |
60 (S1) |
200/1500 |
3.3. Gas-sensing mechanism
The gas-sensing mechanism of a metal oxide-based sensor is determined by the surface reaction of the analyzed gas molecule and pre-adsorbed oxygen species.9 When SnO2 was exposed to air, atmospheric oxygen molecules were adsorbed on the surface of SnO2 NWs to form oxygen ions (O2−, O−, and O2−) by withdrawing electrons from the conduction band of SnO2, as shown in the following eqn (1)–(3): |
O2(gas) + e− ↔ O2−(ads)
| (1) |
As shown in the above equations, the resistance of SnO2 in air increased because of the formation of a thick conduction-depletion region. When air was replaced by H2S, the oxygen ions reacted with H2S to form SO2 and H2O and then released electrons back to the conduction band, resulting in decreased SnO2 resistance, as presented in eqn (4)–(6):
|
2H2S + 3O2− ↔ 2SO2 + 2H2O + 6e−
| (4) |
|
H2S + 3O− ↔ SO2 + H2O + 3e−
| (5) |
|
H2S + 3O2− ↔ SO2 + H2O + 6e−
| (6) |
However, the chemophysical processes of decoration with silver and silver oxide involved in the gas-sensing properties of metal oxides can be explained in various ways.30,52–54 The mechanisms are primarily electronic and/or chemical sensitization. The electronic mechanism is related to the extension of the electron-depleted space charge region at the interface between two materials, and the latter is related to the dominance of the dissociation of gas molecules on the surface of decorated materials by spillover effect.53,54
Herein, we believed that the dissociation of gas molecules at Ag-based sites on the surface of Ag-decorated SnO2 facilitated the charge-transfer reaction between sensor surface and H2S molecule. The gas-sensing mechanism of Ag2O-decorated SnO2 NWs may involve the variation in band structure caused by the conversion of Ag2O into Ag2S and back to Ag2O when the test ambient switched from air to H2S and back to air, as shown in Fig. 6(A) and (B), respectively. Ag2O is a p-type narrow band-gap semiconductor (1.3 eV)47 with a work function of 5.0 eV,55,56 whereas SnO2 is a n-type wide direct-band-gap (3.7 eV) semiconductor with a higher work function of 4.6 eV.57 Given the extension of the electron-depleted region underneath Ag2O nanoparticles on the surface of SnO2 NWs, the barrier at the interface between these two materials developed much more than usual.31 Furthermore, the formation of a continuous series of n–p–n junctions by decorating Ag2O nanoparticles on the network of SnO2 NWs, which prevented the electron current in SnO2 NWs, aggravated the decrease in SnO2 conductivity.21 Upon exposure to H2S, Ag2O was converted into Ag2S58 according to eqn (7).
|
Ag2O + H2S ↔ Ag2S + H2O
| (7) |
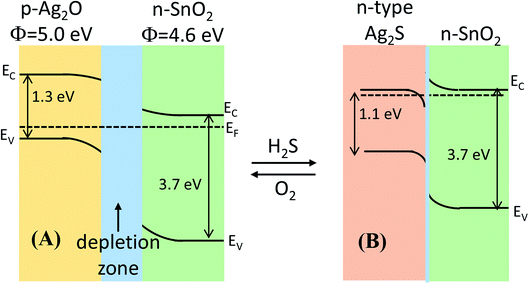 |
| Fig. 6 Energy band diagram of the formation of the p-Ag2O/n-SnO2 junction in air and n-Ag2S/n-SnO2 in H2S atmosphere. | |
The conversion of Ag2O into AgS2 occurred spontaneously because of the negative free Gibbs energy of the reaction (−224.7 kJ mol−1) at room temperature. Therefore, the conversion Ag2O into Ag2S requires less H2S gas, thus the sensor has a lower detection limit. In addition, Ag2S can be an n- or p-type semiconductor depending on its surrounding environment and the pressure.59,60 The monoclinic α-Ag2S is a n-type semiconductor with a band gap of ∼1.1 eV and a work function of 4.42 eV. Upon exposure to H2S, the conversion of p-type Ag2O58 into n-type Ag2S destroyed the p–n junctions of Ag2O–SnO2 and formed the n–n of Ag2S–SnO2, resulting in largely decreased resistance [Fig. 6(B)]. Ag2S was then re-oxidized when the sensor was in air and the p–n junctions were re-established, and the sensor resistance thus recovered to its initial value. Hence, the functionalization of silver on the surface of SnO2 NWs improved their H2S-sensing properties.
4. Conclusion
We introduced a dip-coating method of decorating Ag2O nanoparticles on the surface of on-chip-grown SnO2 NW sensors toward H2S gas monitoring. The effect of Ag2O nanoparticles decorated on the surface of SnO2 NWs on H2S gas-sensing performance was investigated. SnO2 NW sensor decorated with Ag2O nanoparticles illustrated the highest response of 1150 to 1 ppm H2S at a working temperature of 200 °C with reasonable response and recovery time. Selectivity tests over high concentrations of NH3 (500 ppm) and H2 (500 ppm) at various working temperatures presented excellent response, selectivity, and reproducibility, demonstrating the sensor's potential application in the selective monitoring of low-level H2S gas. The high performance of the sensor was also confirmed under the light of sulfurization, which turned the band structure from p–n of Ag2O–SnO2 into n–n of Ag2S–SnO2.
Conflicts of interest
The authors hereby declare that they have no conflict of interests regarding the publication of this paper.
Acknowledgements
This work was supported by the Vietnam National Foundation for Science and Technology Development (NAFOSTED) under grant number 103.02-2017.25.
References
- S. K. Pandey, K. H. Kim and K. T. Tang, TrAC, Trends Anal. Chem., 2012, 32, 87–99 CrossRef CAS.
- OSHA, OSHA standards or regulations of Hydrogen Sulfide (H2S), 2005 Search PubMed.
- P. Van Tong, N. D. Hoa, H. T. Nha, N. Van Duy, C. M. Hung and N. Van Hieu, J. Electron. Mater., 2018, 47, 7170–7178 CrossRef CAS.
- E. Ashori, F. Nazari and F. Illas, Int. J. Hydrogen Energy, 2014, 39, 6610–6619 CrossRef CAS.
- B. R. Doyle, Hazardous Gases Underground: Applications to Tunnel Engineering, Marcel Dekker, Inc., USA, 2001 Search PubMed.
- T.-T. Xu, Y.-M. Xu, X.-F. Zhang, Z.-P. Deng, L.-H. Huo and S. Gao, Front. Chem., 2018, 6, 165 CrossRef PubMed.
- A. Mirzaei, S. S. Kim and H. W. Kim, J. Hazard. Mater., 2018, 357, 314–331 CrossRef CAS PubMed.
- L. Sui, T. Yu, D. Zhao, X. Cheng, X. Zhang, P. Wang, Y. Xu, S. Gao, H. Zhao, Y. Gao and L. Huo, J. Hazard. Mater., 2020, 385, 121570 CrossRef PubMed.
- T. Seiyama, A. Kato, K. Fujiishi and M. Nagatani, Anal. Chem., 1962, 34, 1502–1503 CrossRef CAS.
- A. Natkaeo, D. Phokharatkul, J. H. Hodak, A. Wisitsoraat and S. K. Hodak, Sens. Actuators, B, 2018, 260, 571–580 CrossRef CAS.
- P. H. Phuoc, C. M. Hung, N. Van Toan, N. Van Duy, N. D. Hoa and N. Van Hieu, Sens. Actuators, A, 2020, 303, 111722 CrossRef CAS.
- L. V. Thong, L. T. N. Loan and N. Van Hieu, Sens. Actuators, B, 2010, 150, 112–119 CrossRef.
- M. Batzill and U. Diebold, Prog. Surf. Sci., 2005, 79, 47–154 CrossRef CAS.
- N. X. Thai, N. Van Duy, C. M. Hung, H. Nguyen, T. M. Hung, N. Van Hieu and N. D. Hoa, J. Sci. Adv. Mater. Devices, 2020, 5, 40–47 CrossRef.
- S. R. Morrison, Sens. Actuators, 1987, 12, 425–440 CrossRef CAS.
- Z. Chen, D. Pan, Z. Li, Z. Jiao, M. Wu, C.-H. Shek, C. M. L. Wu and J. K. L. Lai, Chem. Rev., 2014, 114, 7442–7486 CrossRef CAS PubMed.
- D. Zappa, V. Galstyan, N. Kaur, H. M. M. Munasinghe Arachchige, O. Sisman and E. Comini, Anal. Chim. Acta, 2018, 1039, 1–23 CrossRef CAS PubMed.
- T. Maekawa, J. Tamaki, N. Miura and N. Yamazoe, Chem. Lett., 1991, 20, 575–578 CrossRef.
- F. Shao, M. W. G. Hoffmann, J. D. Prades, R. Zamani, J. Arbiol, J. R. Morante, E. Varechkina, M. Rumyantseva, A. Gaskov, I. Giebelhaus, T. Fischer, S. Mathur and F. Hernández-Ramírez, Sens. Actuators, B, 2013, 181, 130–135 CrossRef CAS.
- N. Van Toan, N. V. Chien, N. Van Duy, D. D. Vuong, N. H. Lam, N. D. Hoa, N. Van Hieu and N. D. Chien, Appl. Surf. Sci., 2015, 324, 280–285 CrossRef CAS.
- N. Van Hieu, P. Thi Hong
Van, L. Tien Nhan, N. Van Duy and N. Duc Hoa, Appl. Phys. Lett., 2012, 101, 253106 CrossRef.
- S. Zhang, P. Zhang, Y. Wang, Y. Ma, J. Zhong and X. Sun, ACS Appl. Mater. Interfaces, 2014, 6, 14975–14980 CrossRef CAS PubMed.
- I.-S. Hwang, J.-K. Choi, S.-J. Kim, K.-Y. Dong, J.-H. Kwon, B.-K. Ju and J.-H. Lee, Sens. Actuators, B, 2009, 142, 105–110 CrossRef CAS.
- M. N. Rumyantseva, S. A. Vladimirova, N. A. Vorobyeva, I. Giebelhaus, S. Mathur, A. S. Chizhov, N. O. Khmelevsky, A. Y. Aksenenko, V. F. Kozlovsky, O. M. Karakulina, J. Hadermann, A. M. Abakumov and A. M. Gaskov, Sens. Actuators, B, 2018, 255, 564–571 CrossRef CAS.
- S.-W. Choi, A. Katoch, J. Zhang and S. S. Kim, Sens. Actuators, B, 2013, 176, 585–591 CrossRef CAS.
- Y. Wang, H. Zhang and X. Sun, Appl. Surf. Sci., 2016, 389, 514–520 CrossRef CAS.
- M. Kaur, B. K. Dadhich, R. Singh, K. Ganapathi, T. Bagwaiya, S. Bhattacharya, A. K. Debnath, K. P. Muthe and S. C. Gadkari, Sens. Actuators, B, 2017, 242, 389–403 CrossRef CAS.
- A. Khanna, R. Kumar and S. S. Bhatti, Appl. Phys. Lett., 2003, 82, 4388–4390 CrossRef CAS.
- C.-J. Chen and R.-K. Chiang, Dalton Trans., 2011, 40, 880–885 RSC.
- N. Cattabiani, C. Baratto, D. Zappa, E. Comini, M. Donarelli, M. Ferroni, A. Ponzoni and G. Faglia, J. Phys. Chem. C, 2018, 122, 5026–5031 CrossRef CAS.
- I.-S. Hwang, J.-K. Choi, H.-S. Woo, S.-J. Kim, S.-Y. Jung, T.-Y. Seong, I.-D. Kim and J.-H. Lee, ACS Appl. Mater. Interfaces, 2011, 3, 3140–3145 CrossRef CAS PubMed.
- N. Bhardwaj and S. Mohapatra, Ceram. Int., 2016, 42, 17237–17242 CrossRef CAS.
- T. Yang, Q. Yang, Y. Xiao, P. Sun, Z. Wang, Y. Gao, J. Ma, Y. Sun and G. Lu, Sens. Actuators, B, 2016, 228, 529–538 CrossRef CAS.
- P. S. Kolhe, P. M. Koinkar, N. Maiti and K. M. Sonawane, Phys. B, 2017, 524, 90–96 CrossRef CAS.
- J. Gong, Q. Chen, M.-R. Lian, N.-C. Liu, R. G. Stevenson and F. Adami, Sens. Actuators, B, 2006, 114, 32–39 CrossRef CAS.
- X. Wen, S. Wang, Y. Xie, X.-Y. Li and S. Yang, J. Phys. Chem. B, 2005, 109, 10100–10106 CrossRef CAS PubMed.
- V. V. Sysoev, T. Schneider, J. Goschnick, I. Kiselev, W. Habicht, H. Hahn, E. Strelcov and A. Kolmakov, Sens. Actuators, B, 2009, 139, 699–703 CrossRef CAS.
- T. M. Ngoc, N. Van Duy, C. M. Hung, N. D. Hoa, H. Nguyen, M. Tonezzer and N. Van Hieu, Anal. Chim. Acta, 2019, 1069, 108–116 CrossRef CAS PubMed.
- N. Van Hieu, L. T. N. Loan, N. D. Khoang, N. T. Minh, D. T. Viet, D. C. Minh, T. Trung and N. D. Chien, Curr. Appl. Phys., 2010, 10, 636–641 CrossRef.
- M. Tonezzer, D. T. T. Le, S. Iannotta and N. Van Hieu, Sens. Actuators, B, 2018, 277, 121–128 CrossRef CAS.
- D. D. Trung, N. Van Toan, P. Van Tong, N. Van Duy, N. D. Hoa and N. Van Hieu, Ceram. Int., 2012, 38, 6557–6563 CrossRef CAS.
- N. Liang, M. Wang, L. Jin, S. Huang, W. Chen, M. Xu, Q. He, J. Zai, N. Fang and X. Qian, ACS Appl. Mater. Interfaces, 2014, 6, 11698–11705 CrossRef CAS PubMed.
- K. H. Stern, J. Phys. Chem. Ref. Data, 1972, 1, 747–772 CrossRef.
- M. A. M. Hassan, I. R. Agool and L. M. Raoof, Appl. Nanosci., 2014, 4, 429–447 CrossRef CAS.
- I.-S. Hwang, J.-K. Choi, H.-S. Woo, S.-J. Kim, S.-Y. Jung, T.-Y. Seong, I.-D. Kim and J.-H. Lee, ACS Appl. Mater. Interfaces, 2011, 3, 3140–3145 CrossRef CAS PubMed.
- N. Van Hoang, C. M. Hung, N. D. Hoa, N. Van Duy, N. Van Toan, H. S. Hong, P. T. Hong Van, N. T. Sơn, S.-G. Yoon and N. Van Hieu, J. Alloys Compd., 2020, 826, 154169 CrossRef.
- Y. Zhao, C. Tao, G. Xiao and H. Su, RSC Adv., 2017, 11211–11221 RSC.
- D. J. Late, Y.-K. Huang, B. Liu, J. Acharya, S. N. Shirodkar, J. Luo, A. Yan, D. Charles, U. V. Waghmare, V. P. Dravid and C. N. R. Rao, ACS Nano, 2013, 7, 4879–4891 CrossRef CAS PubMed.
- P. K. Kannan, D. J. Late, H. Morgan and C. S. Rout, Nanoscale, 2015, 7, 13293–13312 RSC.
- K.-I. Choi, H.-J. Kim, Y. C. Kang and J.-H. Lee, Sens. Actuators, B, 2014, 194, 371–376 CrossRef CAS.
- A. Stanoiu, S. Somacescu, C. E. Simion, J. M. Calderon-Moreno and O. G. Florea, in 2017 International Semiconductor Conference (CAS), IEEE, 2017, pp. 93–96 Search PubMed.
- X. Chen, Z. Guo, W.-H. Xu, H.-B. Yao, M.-Q. Li, J.-H. Liu, X.-J. Huang and S.-H. Yu, Adv. Funct. Mater., 2011, 21, 2049–2056 CrossRef CAS.
- S. Matsushima, Y. Teraoka, N. Miura and N. Yamazoe, Jpn. J. Appl. Phys., 1988, 27, 1798–1802 CrossRef CAS.
- N. Yamazoe, Y. Kurokawa and T. Seiyama, Sens. Actuators, 1983, 4, 283–289 CrossRef CAS.
- D. Sarkar, C. K. Ghosh, S. Mukherjee and K. K. Chattopadhyay, ACS Appl. Mater. Interfaces, 2013, 5, 331–337 CrossRef CAS PubMed.
- H. Won Choi, S. Young Kim, K.-B. Kim, Y.-H. Tak and J.-L. Lee, Appl. Phys. Lett., 2005, 86, 12104 CrossRef.
- V. Van Quang, N. Van Dung, N. Sy Trong, N. Duc Hoa, N. Van Duy and N. Van Hieu, Appl. Phys. Lett., 2014, 105, 13107 CrossRef.
- L.-M. Lyu and M. H. Huang, Chem.–Asian J., 2013, 8, 1847–1853 CrossRef CAS PubMed.
- J. Zhang, C. Liu, X. Zhang, F. Ke, Y. Han, G. Peng, Y. Ma and C. Gao, Appl. Phys. Lett., 2013, 103, 82116 CrossRef.
- J. Jang, K. Cho, S. H. Lee and S. Kim, Mater. Lett., 2008, 62, 1438–1440 CrossRef CAS.
|
This journal is © The Royal Society of Chemistry 2020 |
Click here to see how this site uses Cookies. View our privacy policy here.