DOI:
10.1039/C9RA10723A
(Paper)
RSC Adv., 2020,
10, 3487-3492
Study on the wetting interface of Zr–Cu alloys on the SiC ceramic surface
Received
19th December 2019
, Accepted 2nd January 2020
First published on 21st January 2020
Abstract
A Zr–Cu alloy, as a new type of filler metal, is proposed for brazing SiC ceramic under special working conditions. The wetting angle of Zr–Cu alloy/SiC ceramic at different temperatures and holding times was investigated by a high-temperature wetting tester. The composition of the wetting interface was tested by XRD, and the interfacial reaction layer was analyzed with SEM and EDS. The results show that the wetting angle decreases sharply with the change in temperature from 1100 °C to 1175 °C and remains unchanged when the temperature is higher than 1175 °C, about 34 ± 1°. The dynamic wetting angle of Zr–Cu/SiC at 1200 °C with the increase in holding time conforms to the law of exponential decay, and the equilibrium wetting angle is 5°. The transition layer with a certain thickness is formed during the spreading process of the Zr–Cu alloy at a high temperature, and the microstructure of the interfacial reaction layer mainly consists of ZrC and Zr2Si.
1 Introduction
Silicon carbide (SiC), as a structural ceramic material, has a series of excellent properties such as ultra-high hardness, wear resistance, high-temperature resistance and corrosion resistance. It has been widely used in rocket engines and space mirrors. In addition, it also has wide application potential in nuclear industries, high-speed brakes, high-temperature gas filters and so on.1–3 In view of the problems exposed by the Fukushima nuclear power plant explosion in 2011, Prof. Kazimi of the MIT and his team pointed out that SiC ceramic with great potential for applications is likely to become the cladding material of the 4th-generation nuclear reactor.4,5 However, it is very difficult to fabricate SiC ceramic with complex and large parts mainly because of its intrinsic brittleness and poor processing performance. Therefore, the research on the joining technology of the SiC ceramic is the key to expand its application range. At present, the joining methods of the SiC ceramic mainly include brazing, diffusion bonding, reaction bonding and ceramic precursor bonding.6–13 Among them, brazing can produce ideal joints at a low temperature and short time, and it is most likely to realize the mass production of joints. The main filler metals used for brazing the SiC ceramic are Ag-based, Cu-based, Ti-based, Ni-based and Co-based filler metals.6,7,14–16 However, the SiC ceramic brazed joints with the above filler metals cannot simultaneously meet the requirements of good high-temperature performance and small thermal neutron absorption cross-sections. Based on the mature application of the Zr alloy as a nuclear fuel cladding material and the high activity of the element Zr making it easy to react with SiC ceramic, a new type of Zr-based filler metal for brazing nuclear SiC ceramic was proposed by our research group.17,18 The excellent brazing performance is related to the wettability of the Zr–Cu alloy on the SiC ceramic surface. The wetting angle of Cu and Si on the SiC ceramic decreases with the increase in temperature, but the interface hardly reacts, according to Rado.19,20 The wetting behavior of the SiC ceramic with Ti as the active element was investigated.21 It is found that the interfacial reaction between element Ti and SiC ceramic occurs, and the wetting angle is about 86–36° in the temperature range of 1350–1500 °C. At the same time, Al–Si, Ag–Cu–Ti, Pd–Co–V, and Zr–Ti–Ni–Cu–Be were used as the active filler metal to study the wetting behavior on the SiC ceramic surface at a certain temperature.22–25 It is found that there are active elements in the filler metal that react with the interface of SiC ceramic, and the wetting behavior is mainly controlled by the interface reaction. Zr–Cu alloy, as a new type of filler metal, has laid a theoretical foundation for the development and design of the Zr-based filler metal and the formulation of the joining process by the study of the flow wettability on the SiC ceramic surface. Herein, the wetting interface between Zr–Cu alloy and SiC ceramic at different temperatures and holding times was investigated.
2 Materials and methods
Reactive sintered silicon carbide (RBSiC) as the ceramic material was used in the wetting experiment; the related properties of the SiC ceramic with 20 wt% free silicon are shown in Table 1. SiC ceramic was processed in the shape of 10 × 10 × 10 mm3, and Zr–Cu alloy (80Zr20Cu (wt%)), as the Zr-based filler metal, was machined into 3 × 3 × 3 mm3. SiC ceramic and Zr–Cu alloys were prepared with a surface roughness of not less than 100 nm and not less than 50 nm, respectively, using a 2000# diamond grinding disc, and then cleaned with ultrasonic wave in acetone for 30 min. The wetting experiment between Zr–Cu alloy and SiC ceramic at high temperature was carried out in a high-temperature wetting tester by drop method. The Zr–Cu alloy and SiC ceramic substrate were heated to the specified temperature at a certain rate of holding time, and the wetting angle was measured at a vacuum of no less than 10−3 Pa during the wetting process. The phase of the interface between the Zr–Cu alloy and SiC ceramic at high temperature was measured by XRD (Empyrean, Netherlands). The microstructure of the wetting interface was observed by a metallographic microscope (GX71, OLYMPUS, Japan) and scanning electron microscope (S-4800, SEM, HITACHI) with EDS analysis.
Table 1 Properties of RBSiC ceramic
Properties |
Maximum temperature of application |
Density |
Open porosity |
Bending strength |
Modulus of elasticity |
Thermal conductivity |
Coefficient of thermal expansion |
RBSiC |
1380 °C |
>3.02 g cm−3 |
<0.1% |
280 MPa |
300 GPa |
74 W m−1 K−1 |
4.5 × 10−6 K−1 |
3 Results and discussion
3.1 Temperature effect on wetting behavior of the Zr–Cu alloy/SiC ceramic
The variation in the wetting angle between Zr–Cu alloy and SiC ceramic with temperature is shown in Fig. 1. The wetting angle of Zr–Cu alloy on SiC ceramic is no-wetting when the temperature is lower than 1100 °C, decreases rapidly from 1100 °C to 1175 °C, and remains unchanged when the temperature is higher than 1175 °C, about 34 ± 1°. According to Fig. 1, the wettability of Zr–Cu alloy/SiC ceramic at different temperatures can be obtained as shown in Table 2. It can be seen that the wetting angle of Zr–Cu alloy on the SiC ceramic surface is 34° when the temperature is higher than 1175 °C. The wettability of Zr–Cu alloy on SiC ceramic is from non-wettability to partial wettability until good wettability. This is mainly due to the increased activation and fluidity of Zr–Cu alloy on the SiC ceramic surface with the increase in temperature. The activation of the Zr–Cu alloy is not obvious when the temperature is higher than 1175 °C, but the fluidity of the alloy on the SiC ceramic surface tends to be stable.
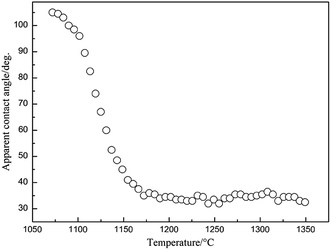 |
| Fig. 1 The wetting angle of Zr–Cu alloy/SiC ceramic changes with temperature. | |
Table 2 Wettability of Zr–Cu alloy and SiC ceramic at different temperatures
Temperatures (°C) |
Wetting angle (°) |
Wettability |
1056–1100 |
>90 |
No-wetting |
1100–1175 |
90–34 |
Preferable |
1175–1350 |
34 ± 1 |
Perfect |
The wetting and interfacial microstructures of Zr–Cu alloy and SiC ceramic at different temperatures are shown in Fig. 2. It can be seen from Fig. 2(a) that the wetting angle is higher than 90° and the alloy cannot wet the SiC ceramic surface at 1100 °C. The shape of the alloy gradually changes from cube to ellipsoid, and the melted alloy slowly spreads on the SiC ceramic surface. The microstructure of the interface at 1100 °C is shown in Fig. 2(b). It can be seen that the Zr–Cu alloy can spread on the SiC ceramic surface and form a certain bond with the interface of SiC ceramic. Since the Zr–Cu alloy contains a large number of active elements, Zr and SiC ceramic undergo complex physical and chemical changes, resulting in the formation of an interfacial reaction layer. The wetting angle decreases with the increase in temperature, and tends to be stable at 1200 °C, and remains basically unchanged with further increase in temperature, as shown in Fig. 2(c) and (e), respectively. It can be found that the interface between Zr–Cu alloy and SiC ceramic forms an interface reaction layer with a certain thickness. It is more obvious at high temperature, as shown in Fig. 2(d) and (f). Therefore, molten Zr–Cu alloy can fill the SiC ceramic surface at high temperature, and an interfacial reaction occurs to form an interfacial reaction layer of a certain thickness, thus realizing the bonding between Zr–Cu alloy and SiC ceramic.
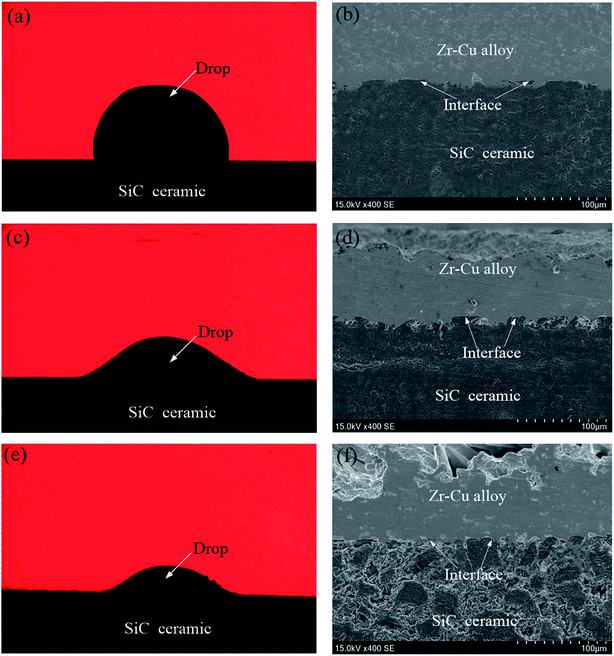 |
| Fig. 2 Wetting and microstructure of the Zr–Cu alloy/SiC ceramic at different temperatures: (a) wetting at 1100 °C, (b) interfacial microstructure at 1100 °C, (c) wetting at 1200 °C, (d) interfacial microstructure at 1200 °C, (e) wetting at 1300 °C, and (f) interfacial microstructure at 1300 °C. | |
3.2 Holding time effect on wetting behavior of the Zr–Cu alloy/SiC ceramic
The wetting angle of Zr–Cu alloy on the SiC ceramic surface remains basically unchanged when the temperature is higher than 1175 °C. Therefore, the wetting behavior change of the Zr–Cu alloy/SiC ceramic at 1200 °C with holding time was mainly investigated. As shown in Fig. 3, the wetting angle decreases rapidly with the increase in the holding time at the beginning of spreading, drops rapidly from 90° to 30° in about 40 s, and then decreases slowly with the increase in the holding time until it is maintained at about 5°. The dynamic wetting angle of Zr–Cu alloy/SiC ceramic at 1200 °C with holding time conforms to the law of exponential decay, and its expression is as follows:26
In the formula, t represents the holding time, θd, θ0, and θe are the dynamic wetting angle, initial wetting angle and equilibrium wetting angle, respectively, n is a constant, and τ is the characteristic time. The fitting curve of the wetting angle is shown in Fig. 3, where n is 0.37, and τ is 39.5 ± 0.7 s.
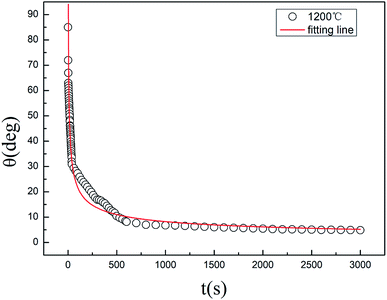 |
| Fig. 3 The apparent contact angle of Zr–Cu alloy/SiC ceramic system changes with heat preservation time during wetting at 1200 °C. | |
As shown in Fig. 4, the spreading precursor effect exists with the increase of holding time. Due to the effect of containing active element Zr in the alloy, an irregular “halo” is formed at the spreading front of the alloy on the SiC ceramic surface at high temperature, which flows outward in a vertical “halo” at the spreading front; a thin precursor film is formed as shown in the arrow direction in Fig. 4. The precursor film is bonded together with SiC ceramic and does not fall off when the temperature is cooled to room temperature, and no cracks are formed on the Zr–Cu alloy surface. The precursor film was analyzed by EDS. The results show that a transition layer with a thickness of about 25 μm is formed at the interface between the precursor film and SiC ceramic, which mainly consists of Si, Zr and Cu elements. From SiC ceramics to the transition layer and then to the alloys, the content distribution of Si element decreases gradually, but there is with no Si element in the alloy layer, Zr and Cu elements mainly appear in the transition layer and alloy layer. Therefore, it can be inferred that element diffusion and chemical reaction exist in the precursor film between Zr–Cu alloy and SiC ceramic, which leads to the phenomenon that Zr–Cu alloy does not fall off from the SiC ceramic surface.
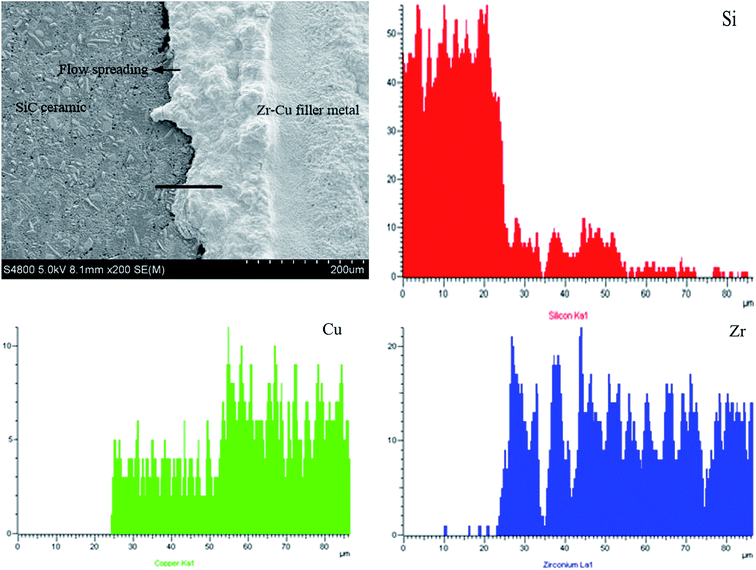 |
| Fig. 4 Precursor film effect and EDS analysis of Zr–Cu/SiC after wetting at 1200 °C for 1200 s. | |
Zr–Cu alloy can flow and spread on the surface of SiC ceramics at high temperature and form an interfacial reaction layer of a certain thickness as shown in Fig. 5(a). It can be seen that a chemical metallurgical bonding is formed between the alloy and SiC ceramic. The interfacial reaction layer products of the wetted samples were analyzed by XRD, as shown in Fig. 6. The results show that the products are mainly composed of ZrC and Zr2Si, which are consistent with the results of thermodynamic calculation.18 At the same time, ZrC and Zr2Si, which have excellent nuclear performance and nuclear compatibility, are also often used as nuclear fuel element materials.27,28 An interfacial reaction layer of a certain thickness is formed with the increase in the reactive products, which lays a foundation for the brazing of Zr–Cu filler metal and SiC ceramic. Based on thermodynamics, the formation mechanism of the reactive products at the interface was analyzed.
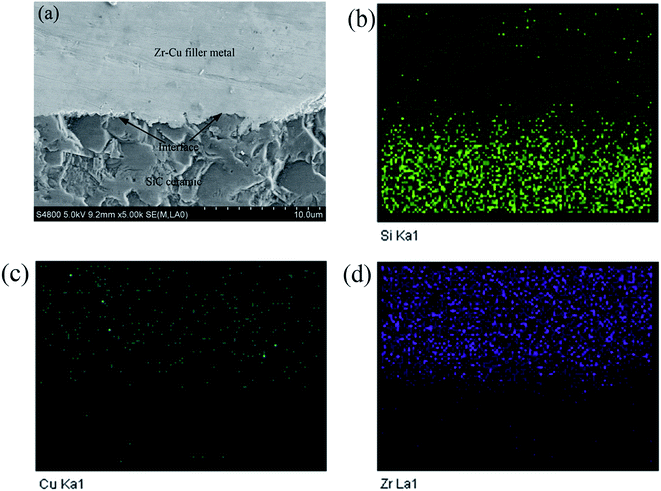 |
| Fig. 5 Interfacial microstructure of Zr–Cu alloy/SiC ceramic after wetting at 1200 °C for 1200 s; (a) XRD of the reaction interface; (b) the distribution of Si element; (c) the distribution of Cu element; (d) the distribution of Zr element. | |
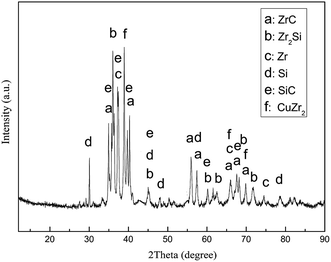 |
| Fig. 6 XRD patterns of the interface of the Zr–Cu alloy/SiC ceramic. | |
Through calculating and comparing the formation Gibbs free energy (ΔG) of SiC, ZrC and Zr2Si within the wetting temperature range of 1100–1350 °C, the standard molar free energy of formation (ΔGm) of ZrC and Zr2Si is found to be lower than that of SiC, which shows that ZrC and Zr2Si are more stable than SiC in the temperature range of 1100–1350 °C. In addition, ΔGm (SiC) is negative, which indicates that SiC ceramic is stable in this temperature range and cannot decompose spontaneously. However, when the heating temperature reaches the melting point of the Zr–Cu alloy, the active element Zr in the liquid alloy concentrates on the surface of SiC ceramic under the action of chemical potential driving force, so that SiC ceramic can be decomposed into Si atoms and C atoms (SiC = Si + C). At this time, the reactions with the active element Zr are as follows: C + Zr = ZrC and Si + 2Zr = Zr2Si. In conclusion, the reaction between SiC ceramic and active element Zr is as follows: SiC + 3Zr = ZrC + Zr2Si. The Gibbs free energy of the reaction (ΔGr) is negative in the temperature range of 1100–1350 °C, and (ΔGr)1200 °C = −327.53 kJ mol−1, indicating that the reaction can be spontaneous.
To sum up, certain interface reaction products are formed when Zr–Cu alloy is wetted on the surface of SiC ceramic, which lays a foundation for later research on the brazing performance between Zr–Cu filler metal and SiC ceramic. In order to further determine the reaction products at the interface, EDS analysis was carried out at the interface. The distribution of Si, Cu and Zr elements in the interfacial reaction layer is shown in Fig. 5(c), (d) and (e) respectively. There is a transition region between Si and Zr in the interfacial reaction layer, which indicates that the diffusion and reaction between C and Zr and Si and Zr elements in the interface reaction layer during the wetting spreading process, and from new phases ZrC and Zr2Si, thus realizing the combination of Zr–Cu alloy and SiC ceramic.
4 Conclusion
(1) The wetting angle of the Zr–Cu/SiC decreases rapidly from 1100 °C to 1175 °C, remains unchanged when the temperature is higher than 1175 °C, about 34 ± 1°, and the alloy has excellent wettability on the SiC ceramic surface.
(2) The wetting angle between Zr–Cu alloy and SiC ceramic decreases quickly at 1200 °C with the increase in holding time at the beginning of spreading, drops rapidly from 90° to 30° in about 40 s, and then decreases slowly with the increase in holding time until it is maintained at about 5°. Thus, the dynamic wetting angle of Zr–Cu/SiC with holding time conforms to the law of exponential decay.
(3) The transition layer with a certain thickness is formed during the spreading process of the alloy at high temperature. The interface reaction occurs between the Zr–Cu alloy and SiC ceramic, and the composition is mainly ZrC and Zr2Si.
Conflicts of interest
There are no conflicts to declare.
Acknowledgements
This research is financially supported by the Doctoral Research Initiation Fund (No. BK201902) of Hubei University of Automotive Technology, Sichuan Science and Technology Program (No. 2019YFG0225) of Sichuan Province in China.
References
- Y. H. Huang, D. L. Jiang and X. F. Zhang, et al. Enhancing toughness and strength of SiC ceramics with reduced graphene oxide by HP sintering, J. Eur. Ceram. Soc., 2018, 38, 4329–4337 CrossRef CAS.
- K. Kollins, C. Przybyla and M. S. Amer, Residual stress measurements in melt infiltrated SiC/SiC ceramic matrix composites using Raman spectroscopy, J. Eur. Ceram. Soc., 2018, 38(7), 2784–2791 CrossRef CAS.
- T. Koyanagia, Y. Katoh and J. O. Kiggans, et al. Irradiation resistance of silicon carbide joint at light water reactor-relevant temperature, J. Nucl. Mater., 2017, 488, 150–159 CrossRef.
- R. Parekh, M. Kazimia and S. Skorupskib, Intestine transplantation across a positive crossmatch with preformed donor-specific antibodies, Transplant. Proc., 2016, 48(2), 489–491 CrossRef CAS.
- Y. Lee, T. J. McKrell and C. Yue, et al. Safety assessment of SiC cladding oxidation under loss-of-coolant accident conditions in light water reactors, Nucl. Technol., 2013, 183(2), 210–227 CrossRef CAS.
- F. Moszner, G. Mata-Osoro and M. Chiodi, et al. Mechanical behavior of SiC joints brazed using an active Ag-Cu-In-Ti braze at elevated temperatures, Int. J. Appl. Ceram. Technol., 2017, 14, 703–711 CrossRef CAS.
- H. T. Zhao, J. H. Huang and H. Zhang, et al. Vacuum brazing of Si/SiC ceramic and low expansion titanium alloy by using Cu-Ti fillers, Rare Met. Mater. Eng., 2007, 36, 2184–2188 CAS.
- Q. Wang, Q. H. Li and D. L. Sun, et al. Microstructure and mechanical properties of SiC/Ti diffusion bonding joints under electric field, Rare Met. Mater. Eng., 2016, 45, 1749–1754 Search PubMed.
- J. H. Kim, D. S. Kim and S. T. Lim, et al. Interfacial microstructure of diffusion-bonded SiC and Re with Ti Interlayer, J. Alloys Compd., 2017, 701, 316–320 CrossRef CAS.
- M. Singh, A reaction forming method for joining of silicon carbide based ceramic, Scr. Mater., 1997, 37, 1151–1154 CrossRef CAS.
- H. Y. Dong, S. J. Li and Y. Y. Teng, et al. Joining of SiC ceramic-based material with ternary carbide Ti3SiC2, Mater. Sci. Eng., B, 2011, 176, 60–64 CrossRef CAS.
- X. K. Yuan and H. Chen, Residual thermal stress analysis of SiC joint by polysiloxane silicon resin YR3187, J. Adhes. Adhes., 2014, 27, 1525–1534 Search PubMed.
- M. Singh, A reaction forming method for joining of silicon carbide based ceramic, Scr. Mater., 1997, 37, 1151–1154 CrossRef CAS.
- J. Li, L. Liu and Y. Wu, et al. Microstructure of high temperature Ti-based brazing alloys and wettability on SiC ceramic, Mater. Des., 2009, 30(2), 275–279 CrossRef.
- W. B. Tian, Z. M. Sun and P. Zhang, et al. Brazing of silicon carbide ceramics with Ni-Si-Ti powder mixtures, J. Aust. Ceram. Soc., 2017, 53, 511–516 CrossRef CAS.
- H. P. Xiong, W. Mao and Y. H. Xie, et al. Control of interfacial reactions and strength of the SiC/SiC joints brazed with newly-developed Co-based brazing alloy, J. Mater. Res., 2007, 22(10), 2727–2736 CrossRef CAS.
- B. F. Zhou, Z. C. Zeng and Y. C. Cai, et al. FEM simulation and verification of brazing SiC ceramic with novel Zr-Cu filler metal, Materials, 2019, 12(20), 3380–3388 CrossRef.
- B. F. Zhou and K. Q. Feng, Zr-Cu alloy filler metal for brazing SiC ceramic, RSC Adv., 2018, 8(46), 26251–26254 RSC.
- C. Rado, B. Drevet and N. Eustahopoul, The role of compound formation in reactive wetting: the Cu/SiC system, Acta Mater., 2000, 48(18), 4483–4491 CrossRef CAS.
- C. Rado, S. Kalogeropoulou and N. Eustathopoulos, Bonding and wetting in non-reactive metal: SiC systems: weak or strong interfaces, Mater. Sci. Eng. A, 2000, 276(1), 195–202 CrossRef.
- S. J. Li, Y. Zhou and H. P. Duan, Wettability and interfacial reaction in SiC/Ni plus Ti system, J. Mater. Sci., 2002, 37(12), 2575–2579 CrossRef CAS.
- Y. B. Ren, R. S. Zhou and D. Y. Zhu, et al. The reactive wetting kinetics of interfacial tension: a reaction-limited model, RSC Adv., 2017, 7(21), 13003–13009 RSC.
- W. Tillmann, J. Pfeiffer and L. Wojarski, Influencing factors on the reactive wetting of Cu-Sn-Ti and Ag-Cu-Ti alloys on silicon carbide-microstructural observations, effects and multivariate modeling, Adv. Sci. Technol., 2014, 88, 172–177 Search PubMed.
- H. P. Xiong, B. Chen and W. Mao, et al. Joining of Cf/SiC composite with Pd-Co-V brazing filler, Weld. World, 2012, 56, 76–80 CrossRef CAS.
- B. Zhang, W. Li and H. Li, Spontaneous infiltration and wetting behaviors of a Zr-based alloy melt on a porous SiC substrate, Int. J. Miner., Metall. Mater., 2018, 25(7), 817–823 CrossRef CAS.
- X. H. Zheng, P. Shen and X. H. Han, et al. Wettability and reactivity between B4C and molten Zr55Cu30Al10Ni5 metallic glass alloy, Mater. Chem. Phys., 2009, 117, 377–383 CrossRef CAS.
- L. Xu, C. Z. Huang, H. I. Liu, B. Zou, H. T. Zhu and G. L. Zhao, Int. J. Refract. Met. Hard Mater., 2014, 42, 116–119 CrossRef CAS.
- H. Yeom, C. Lockhart, R. Mariani, P. Xu, M. Corradini and I. Sridharan, J. Nucl. Mater., 2018, 499, 256–267 CrossRef CAS.
|
This journal is © The Royal Society of Chemistry 2020 |
Click here to see how this site uses Cookies. View our privacy policy here.