DOI:
10.1039/C7RA02788E
(Paper)
RSC Adv., 2017,
7, 23041-23045
Reusable ionic liquid-catalyzed oxidative esterification of carboxylic acids with benzylic hydrocarbons via benzylic Csp3–H bond activation under metal-free conditions†
Received
7th March 2017
, Accepted 19th April 2017
First published on 26th April 2017
Abstract
A metal-free protocol for the direct oxidative esterification of the Csp3–H bond in benzylic hydrocarbons with carboxylic acids using heterocyclic ionic liquid as catalyst has been reported. The catalyst 1-butylpyridinium iodide could be easily recycled and reused for at least four cycles without obvious loss of catalytic activity.
Introduction
It is well known that benzyl esters are prevalent functional groups in medicinal agents and natural products.1 The traditional methods of preparing benzyl esters by utilizing benzyl alcohols/bromides/chlorides with carboxylic acids as coupling partners have been reported over the decades (Scheme 1a).2 Furthermore, Khan's group proposed benzyl esters can also be obtained by the reaction of aromatic carboxylic acids with substituted toluenes in the presence of NaBrO3/NaHSO3 in early 2003.3 However, some approaches have disadvantages of long reaction time or sensitivity to the environment. With increasing interest in transition metal-catalyzed C–H bonds activation to construct C–O bonds, several types of transition metals, including Cu, Pd, Pt and Rh have been recently revealed admirable catalytic activity in esterification.4 Among them, the approach of Pd-catalyzed benzylation of toluene with carboxylic acids under 1 atm of oxygen has been disclosed by Zhang's group (Scheme 1b).4j It did not need to be pre-functionalized and provided a more facile, atom-economic method to prepare benzyl esters. Despite their obvious potential application, these transition metal-catalyzed C–H bond activation methods suffered from a few drawbacks such as expense and toxicity of transition metals, which limit their practicability. Hence, the development of a facile and practical approach for constructing benzyl esters under metal-free conditions is extremely desirable.
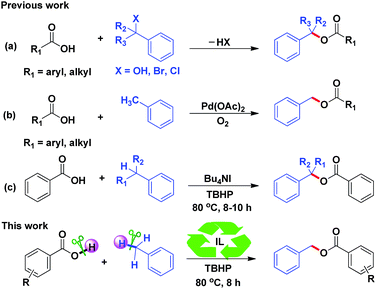 |
| Scheme 1 A variety of methods for the synthesis of benzyl esters. | |
In 2012, Yu and co-workers established Bu4NI-catalyzed esterification of benzylic Csp3–H bonds (Scheme 1c).5 Subsequently, Singh's group applied carboxylic acids with alkyl benzenes to synthesis of benzyl esters catalyzed by NBS with TBHP as an oxidant under alkaline conditions.6 Moreover, Patel's group presented a strategy for the efficient preparation of benzylic esters through Bu4NI-catalyzed cross dehydrogenative coupling of alkylbenzenes as the only precursor.7 The main advantage of these methodologies is their environmentally friendliness.
In recent years, ionic liquids (ILs) are widely used as an environmentally eco-friendly and recyclable reaction medium or catalyst in green synthesis,8 which have attracted great attention of chemists all around the world. Compared with other organic agents, ILs have unique advantages such as low toxicity, easy recyclability, excellent chemical and thermal stability, negligible vapor pressure, as well as good solubility with organic and inorganic compounds.9 Latterly, transition metal-catalyzed C–H activation reactions with ionic liquids as solvents have already been developed.10 Up to now, ionic liquids promoted C–C bond and catalyzed C–N bond formation reactions have been published by our group.11 However, as far as we know, classical heterocyclic ILs-catalyzed benzylic Csp3–H activation for C–O bond formation to prepare benzyl esters have been rarely reported. With this background in mind, we herein report a heterocyclic IL-catalyzed the direct oxidative esterification between Csp3–H bond of benzylic hydrocarbons and carboxylic acids for the synthesis of benzyl esters under metal-free conditions.
Results and discussion
We commenced our study using benzoic acid (1a) and toluene (2a) as a model system (Table 1). Firstly, the reaction of 1a and 2a was carried out at 80 °C for 8 h to give the desired benzyl ester product 3a in 70% yield in the presence of 1.4 equiv. of TBHP and 20 mol% [BPy]I (Table 1, entry 1). Encouraged by this result, further optimization of conditions for the oxidative esterification was explored. Unfortunately, other ionic liquids such as 1-butylpyridinium bromide ([BPy]Br) and 1-butylpyridinium chloride ([BPy]Cl) were proved to be poor activity for this esterification (Table 1, entries 2–3). Meanwhile, it was found that essentially no reaction occurred in the catalyst-free system (Table 1, entry 4). The yield of product 3a was not improved obviously by increasing the amount of TBHP to 2 equiv. (Table 1, entry 5). Subsequently, when the dosage of [BPy]I was increased from 20 mol% to 25 mol%, there was no significant improvement in yield (Table 1, entry 6). In contrast, decreasing the amount of [BPy]I resulted in dramatically reducing the yield of 3a (Table 1, entries 7–8). After a brief screening of oxidants such as 3-chloroperbenzoic acid, hydrogen peroxide, di-tert-butyl peroxide and iodobenzene diacetate, TBHP remained the optimal choice (Table 1, entries 1, 9–12). Finally, the effects of reaction temperature and reaction time were also screened (Table 1, entries 13–17), the results suggested that the optimized reaction temperature and time were 80 °C and 8 h, respectively. Therefore, the reaction was carried out with [BPy]I (20 mol%) as the catalyst and TBHP (1.4 mmol, 70% aqueous solution) as the oxidant at 80 °C for 8 h.
Table 1 Optimizing the reaction conditionsa
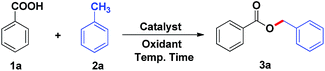
|
Entry |
Catalyst (mol%) |
Oxidantb (1.4 mmol) |
Temp. (°C) |
Time (h) |
Yieldc (%) |
Reaction conditions: 1a (1 mmol), 2a (20 mmol), oxidant (1.4 mmol). TBHP: tert-butyl hydroperoxide 70% in water; m-CPBA: m-chloroperoxybenzoic acid; DTBP: di-tert-butyl peroxide; H2O2: 30% in water. Isolated yield. Not reaction. TBHP: 2.0 mmol. |
1 |
[BPy]I (20) |
TBHP |
80 |
8 |
70 |
2 |
[BPy]Br (20) |
TBHP |
80 |
8 |
Trace |
3 |
[BPy]Cl (20) |
TBHP |
80 |
8 |
N.R.d |
4 |
— |
TBHP |
80 |
8 |
N.R. |
5 |
[BPy]I (20) |
TBHP |
80 |
8 |
72e |
6 |
[BPy]I (25) |
TBHP |
80 |
8 |
71 |
7 |
[BPy]I (15) |
TBHP |
80 |
8 |
57 |
8 |
[BPy]I (10) |
TBHP |
80 |
8 |
Trace |
9 |
[BPy]I (20) |
m-CPBA |
80 |
8 |
N.R. |
10 |
[BPy]I (20) |
H2O2 |
80 |
8 |
N.R. |
11 |
[BPy]I (20) |
DTBP |
80 |
8 |
N.R. |
12 |
[BPy]I (20)) |
PhI(OAc)2 |
80 |
8 |
N.R. |
13 |
[BPy]I (20) |
TBHP |
100 |
8 |
72 |
14 |
[BPy]I (20) |
TBHP |
60 |
8 |
26 |
15 |
[BPy]I (20) |
TBHP |
80 |
10 |
70 |
16 |
[BPy]I (20) |
TBHP |
80 |
6 |
60 |
Under the optimized reaction conditions, the scope of carboxylic acids was explored. As shown in Table 2, a wide variety of benzoic acid derivatives with electron-donating substitutes and electron-withdrawing substitutes underwent this esterification smoothly and afforded the corresponding benzyl esters (3b–3t) in good to excellent yields. It is important to note that the methyl or nitro group substituted at ortho-, meta- or para-position of benzene ring were all compatible (3b–3d, 3q–3s). In particular, the multisubstituted substrates such as 2,3,4,5,6-pentafluorobenzoic acid, 3,5-dinitrobenzoic acid could be transformed well with 73% and 93% yield, respectively (3k, 3t). All of the above results indicated that the electronic and steric effects had no significant influence on the yield of products. To our delight, cinnamic acid and terephthalic acid were also amenable substrates (3u, 3v). In order to better expand substrates scope, aromatic heterocyclic carboxylic acid such as 2-phenyl-2H-1,2,3-triazole-4-carboxylic acid and 2-furoic acid were explored and the corresponding products (3w, 3x) were obtained in 85% and 55% yields, respectively.
Table 2 Esterification of toluene with various carboxylic acidsa
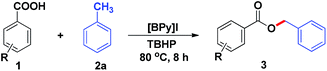
|
Reaction conditions: 1 (1 mmol), 2a (20 mmol), [BPy]I (20 mol%), TBHP (1.4 mmol) at 80 °C for 8 h unless otherwise noted. TBHP: 2.0 mmol. |
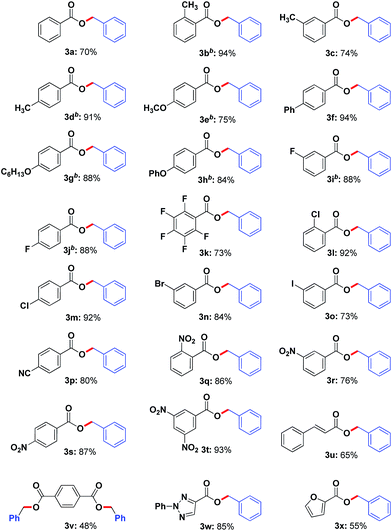 |
Subsequently, we investigated the scope of benzylic hydrocarbons. As shown in Table 3, a wide range of toluene derivatives with electron-donating groups and electron-withdrawing groups were well tolerated and obtained the desired products (4a–4g) in moderate to good yields. It is worth noting that p-xylene and mesitylene only gave monoesterification products (4a, 4b) in 78% and 82% yields, respectively. When the substrate with p-OCH3 was used, the target product (4c) was afforded in yield of 71%. In particular, the chloro group substituted at ortho-, meta- or para-position of benzene ring were all amenable substrates (4e–4g). Additionally, both ethylbenzene and cumene were suitable reactants, affording the corresponding products (4h, 4i) in moderate yields.
Table 3 Esterification of benzoic acid with benzylic hydrocarbonsa
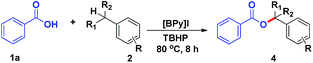
|
Reaction conditions: 1a (1 mmol), 2 (20 mmol), [BPy]I (20 mol%), TBHP (1.4 mmol) at 80 °C for 8 h unless otherwise noted. TBHP: 2.0 mmol. |
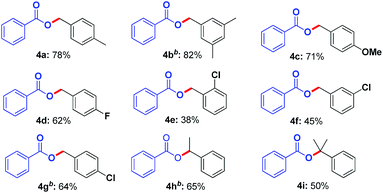 |
To further demonstrate the potential application of the esterification method in industry, an IL-catalyzed gram-scale esterification between 2-nitrobenzoic acid and toluene was investigated (Scheme 2). The result showed that the reaction was easily performed under the optimized reaction conditions to give the desired benzyl ester in 80% isolated yield.
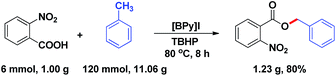 |
| Scheme 2 Gram-scale oxidative esterification. | |
In order to validate the reaction mechanism, control experiments were carried out (see the ESI†). In the presence of 2 equiv. of TEMPO (2,2,6,6-tetramethylpiperidine-N-oxyl) as a free radical scavenger, the esterification was almost inhibited under the optimal conditions. When the amount of TEMPO was increased to 3 equiv., benzyl benzoate as the target could not be obtained at all. The results showed that the esterification may involve a radical pathway.
Based on the results of control experiments and previous studies,5,11b,12 a possible radical mechanism is proposed (Scheme 3). Initially, [BPy]I is oxidized by TBHP to generate {[BPy]+[IO]−} A or {[BPy]+[IO2]−} B species. Subsequently, the benzyl radical C is obtained from the hemolytic cleavage of a benzylic C–H bond in the presence of A or B, followed by combination with benzoic acid to give the benzyl ester radical anion F. Finally, the desired product benzyl ester is produced by losing an electron from F with the assistance of hydroxyl radical (Scheme 3, path A). Furthermore, the benzyl radical is easily oxidized by active iodine species A or B to give the benzyl cation D and the hydroxide ion simultaneously. Subsequently, benzoic acid is deprotonated by the hydroxide ion to form the benzoate anion E. At last, the electrostatic attraction between the benzoate anion with specie E to yield corresponding product 3a (Scheme 3, path B).
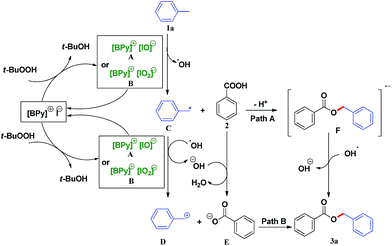 |
| Scheme 3 The proposed mechanism. | |
It's worth noting that ionic liquid could be easily recycled. 2-Chlorobenzoic acid and methylbenzene were chosen as model substrates to study the reusability of the catalyst [BPy]I under standard reaction conditions. After completion of the reaction, ethyl acetate and water were added, and then the ionic liquid [BPy]I was recovered from the aqueous phase and reused without the significant loss of its activity (Fig. 1).
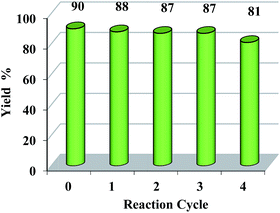 |
| Fig. 1 Recycling reactions. | |
Conclusions
In summary, we have developed classic heterocyclic ionic liquid-catalyzed oxidative esterification of carboxylic acid derivatives with benzylic hydrocarbons. Most importantly, a inexpensive and recyclable ionic liquid [BPy]I is reused for at least four cycles with similar catalytic activity. Ionic liquid catalyzed C–H bond activation reactions are ongoing in our laboratory.
Acknowledgements
This work is supported by Grants from Key Laboratory of Xinjiang Uyghur Autonomous Region (2015KL014) and the National Natural Science Foundation of China (21572195 and 21262035).
Notes and references
-
(a) V. Vindigni, R. Cortivo, L. Iacobellis, G. Abatangelo and B. Zavan, Int. J. Mol. Sci., 2009, 10, 2972 CrossRef CAS PubMed;
(b) A. Aliboni, A. D'Andrea and P. Massanisso, J. Agric. Food Chem., 2011, 59, 282 CrossRef CAS PubMed;
(c) C. S. Pappas, A. Malovikova, Z. Hromadkova, P. A. Tarantilis, A. Ebringerova and M. G. Polissiou, Carbohydr. Polym., 2004, 56, 465 CrossRef CAS;
(d) A. Isidro-Llobet, M. Álvarez and F. Albericio, Chem. Rev., 2009, 109, 2455 CrossRef CAS PubMed.
- Selected traditional esterification methods:
(a) J. C. Lee, Y. S. Oh, S. H. Cho and J. D. Lee, Org. Prep. Proced. Int., 1996, 28, 480 CrossRef CAS;
(b) C.-T. Chen and Y. S. Munot, J. Org. Chem., 2005, 70, 8625 CrossRef CAS PubMed;
(c) F. Cardellini, L. Brinchi, R. Germani and M. Tiecco, Synth. Commun., 2014, 44, 3248 CrossRef CAS;
(d) R. Kore and R. Srivastava, Catal. Commun., 2011, 12, 1420 CrossRef CAS;
(e) N. Iranpoor, H. Firouzabadi and D. Khalili, Org. Biomol. Chem., 2010, 8, 4436 RSC;
(f) X. Wu, X. Han, L. Zhou and A. Li, Indian J. Chem., Sect. A: Inorg., Bio-inorg., Phys., Theor. Anal. Chem., 2012, 51, 791 Search PubMed;
(g) X. Li, W. Eli and G. Li, Catal. Commun., 2008, 9, 2264 CrossRef CAS;
(h) K. Kankanala, V. R. Reddy, K. Mukkanti and S. Pal, J. Fluorine Chem., 2009, 130, 505 CrossRef CAS.
- K. M. Khan, G. M. Maharvi, S. Hayat, Z. Ullah, M. I. Choudhary and A.-u. Rahman, Tetrahedron, 2003, 59, 5549 CrossRef CAS.
- Selected esterification protocols through C–H activation:
(a) X. Chen, X.-S. Hao, C. E. Goodhue and J.-Q. Yu, J. Am. Chem. Soc., 2006, 128, 6790 CrossRef CAS PubMed;
(b) A. R. Dick, K. L. Hull and M. S. Sanford, J. Am. Chem. Soc., 2004, 126, 2300 CrossRef CAS PubMed;
(c) M. S. Chen, N. Prabagaran, N. A. Labenz and M. C. White, J. Am. Chem. Soc., 2005, 127, 6970 CrossRef CAS PubMed;
(d) J. H. Delcamp and M. C. White, J. Am. Chem. Soc., 2006, 128, 15076 CrossRef CAS PubMed;
(e) D. J. Covell and M. C. White, Angew. Chem., Int. Ed., 2008, 47, 6448 CrossRef CAS PubMed;
(f) T. Yoneyama and R. H. Crabtree, J. Mol. Catal. A: Chem., 1996, 108, 35 CrossRef CAS;
(g) L. V. Desai, K. L. Hull and M. S. Sanford, J. Am. Chem. Soc., 2004, 126, 9542 CrossRef CAS PubMed;
(h) R. Giri, J. Liang, J.-G. Lei, J.-J. Li, D.-H. Wang, X. Chen, I. C. Naggar, C. Guo, B. M. Foxman and J.-Q. Yu, Angew. Chem., Int. Ed., 2005, 44, 7420 CrossRef CAS PubMed;
(i) D. Li, M. Yu, J. Zhang, Z. Liu and Y. Zhang, Org. Lett., 2015, 17, 5300 CrossRef CAS PubMed;
(j) H. Liu, G. Shi, S. Pan, Y. Jiang and Y. Zhang, Org. Lett., 2013, 15, 4098 CrossRef CAS PubMed;
(k) J. M. Lee and S. Chang, Tetrahedron Lett., 2006, 47, 1375 CrossRef CAS;
(l) Z. Ye, W. Wang, F. Luo, S. Zhang and J. Cheng, Org. Lett., 2009, 11, 3974 CrossRef CAS PubMed.
- J. Feng, S. Liang, S.-Y. Chen, J. Zhang, S.-S. Fu and X.-Q. Yu, Adv. Synth. Catal., 2012, 354, 1287 CrossRef CAS.
- T. Guntreddi, R. Vanjari and K. N. Singh, Tetrahedron, 2014, 70, 3887 CrossRef CAS.
- G. Majji, S. Guin, A. Gogoi, S. K. Rout and B. K. Patel, Chem. Commun., 2013, 49, 3031 RSC.
-
(a) P. Wasserscheid and W. Keim, Angew. Chem., Int. Ed., 2000, 39, 3772 CrossRef CAS;
(b) J. Dupont, R. F. Souza and P. A. Z. Suarez, Chem. Rev., 2002, 102, 3667 CrossRef CAS PubMed;
(c) V. I. Pârvulescu and C. Hardacre, Chem. Rev., 2007, 107, 2615 CrossRef PubMed;
(d) B. Xin and J. Hao, Chem. Soc. Rev., 2014, 43, 7171 RSC;
(e) J. R. Harjani, R. D. Singer, M. T. Garcia and P. J. Scammells, Green Chem., 2009, 11, 83 RSC.
-
(a) M. Petkovic, K. R. Seddon, L. P. N. Rebelo and C. S. Pereira, Chem. Soc. Rev., 2011, 40, 1383 RSC;
(b) C. D. Hubbard, P. Illner and R. Eldik, Chem. Soc. Rev., 2011, 40, 272 RSC;
(c) J. P. Hallett and T. Welton, Chem. Rev., 2011, 111, 3508 CrossRef CAS PubMed;
(d) M. E. Zakrzewska, E. Bogel-Łukasik and R. Bogel-Łukasik, Chem. Rev., 2011, 111, 397 CrossRef CAS PubMed;
(e) Q. Zhang and J. M. Shreeve, Chem. Rev., 2014, 114, 10527 CrossRef CAS PubMed;
(f) M. V. Fedorov and A. A. Kornyshev, Chem. Rev., 2014, 114, 2978 CrossRef CAS PubMed.
-
(a) J. Li, W. Yang, S. Yang, L. Huang, W. Wu, Y. Sun and H. Jiang, Angew. Chem., Int. Ed., 2014, 53, 7219 CrossRef CAS PubMed;
(b) J. Li, S. Yang, H. Jiang, W. Wu and J. Zhao, J. Org. Chem., 2013, 78, 12477 CrossRef CAS PubMed;
(c) O. Baslé, N. Borduas, P. Dubois, J. M. Chapuzet, T. H. Chan, J. Lessard and C. J. Li, Chem.–Eur. J., 2010, 16, 8162 CrossRef PubMed;
(d) S. B. Park and H. Alper, Chem. Commun., 2005, 1315 RSC;
(e) P. Ehlers, A. Petrosyan, J. Baumgard, S. Jopp, N. Steinfeld, T. V. Ghochikyan, A. S. Saghyan, C. Fischer and P. Langer, ChemCatChem, 2013, 5, 2504 CrossRef CAS;
(f) A. Biffis, L. Gazzola, C. Tubaro and M. Basato, ChemSusChem, 2010, 3, 834 CrossRef CAS PubMed.
-
(a) H. Li, C. Liu, Y. Zhang, Y. Sun, B. Wang and W. Liu, Org. Lett., 2015, 17, 932 CrossRef CAS PubMed;
(b) W. Liu, C. Liu, Y. Zhang, Y. Sun, A. Abdukader, B. Wang, H. Li, X. Ma and Z. Zhang, Org. Biomol. Chem., 2015, 13, 7154 RSC;
(c) D. Cao, Y. Zhang, C. Liu, B. Wang, Y. Sun, A. Abdukader, H. Hu and Q. Liu, Org. Lett., 2016, 18, 2000 CrossRef CAS PubMed.
-
(a) Q. Xue, J. Xie, H. Li, Y. Cheng and C. Zhu, Chem. Commun., 2013, 49, 3700 RSC;
(b) L. Wang, K. Zhu, Q. Chen and M. He, J. Org. Chem., 2014, 79, 11780 CrossRef CAS PubMed.
Footnote |
† Electronic supplementary information (ESI) available. See DOI: 10.1039/c7ra02788e |
|
This journal is © The Royal Society of Chemistry 2017 |
Click here to see how this site uses Cookies. View our privacy policy here.