DOI:
10.1039/C4RA05763E
(Paper)
RSC Adv., 2014,
4, 48666-48670
Bi2S3 nanorods modified with Co(OH)2 ultrathin nanosheets to significantly improve its pseudocapacitance for high specific capacitance†
Received
15th June 2014
, Accepted 15th September 2014
First published on 15th September 2014
Abstract
Nanostructured Bi2S3 has been used in various energy conversion and storage systems, but it alone does not possess significant capacitance and this has never been investigated. A modification at the nanoscale is used to create a structure composed of Bi2S3 nanorods and α-Co(OH)2 nanosheets, which is controllably synthesized by a facile seed-layer assisted hydrothermal method to produce the former followed by electrochemical deposition of the latter. The Co(OH)2-modified Bi2S3 nanorods significantly boost the pseudocapacitance of Bi2S3 for high specific capacitance, while improving the cycle life stability. Results reveal that the controlled Co(OH)2 modification process promotes a networked, highly porous structure for a considerably larger surface allowing the electrolyte-access; thus, enhancing the pseudocapacitance and resulting in a high specific capacitance.
1. Introduction
Supercapacitors as energy conversion and storage systems have been extensively studied because of their high power density compared with lithium ion batteries/fuel cells and higher energy storage capacity than traditional capacitor.1–4 Supercapacitors are usually classified into pseudocapacitors and electrical double layer capacitors, of which the former have higher pseudocapacitance due to fast electrochemical redox reactions; thus, resulting in a considerably higher capacitance than electrical double layer capacitors.5–7 Because the performances of pseudocapacitors ultimately depend on the properties of the electrode materials, the development of innovative materials with high pseudocapacitance is essential. Nowadays, transition metal oxides are considered to be promising materials for pseudocapacitors because of their fast multi redox reactions. For example, RuO2 exhibits a high specific capacitance of 720–760 F g−1.8 Unfortunately, the high cost and low abundance of RuO2 limit its large-scale application.9 Thus, there is a great need to explore alternative material for pseudocapacitance-based supercapacitors.
Nanostructured metal sulphides are important materials used in various energy conversion/storage systems such as supercapacitors, hydrogen storages, Li-ion batteries, fuel cells and solar cells.10–14 CoS and ZnS have been explored as electrode materials in pseudocapacitors,10,15 which achieved a high specific capacitance of 508 F g−1 for CoS nanowires. Ni3S2 shows good hydrogen storage ability.16 Bi2S3 is a semiconductor, which has been also used in photovoltaic conversion,17 hydrogen storage12,18 and lithium-ion battery.19 Layer-structured Bi2S3 can be synthesized for various morphologies,20–23 among which Bi2S3 nanorods demonstrate a high surface area.24 However, it has not been investigated for its capacitive behaviours.
It has been reported that the modification of the metal sulphides with functional materials like carbons,25 noble metals,26 metal oxides/metal hydroxides27 and other metal sulphides28 can offer unique properties.7 Metal hydroxides/metal oxides have higher energy densities for supercapacitors than carbon materials, while offering better electrochemical stability than polymer materials. Electrodeposited Co(OH)2 is a material used in pseudocapacitance with high electrochemical activity, fast ion insertion/desertion rate and high redox reversibility.29,30
In this work, for the first time the Bi2S3 nanorods were grown on a Ti substrate to effectively avoid agglomeration for improved electron conductivity, followed further the modification of Co(OH)2 by electrodeposition for a networked, porous hybrid nanostructure. Thus, Bi2S3 could also be used as a good supercapacitor material. In this work, the inexpensive, highly pseudocapacitive Co(OH)2 could be combined with Bi2S3 nanorods to present a large surface area for a synergistically improved superior supercapacitive behaviour.
2. Experimental section
2.1 The preparation of Bi2S3 adhered on Ti
All the chemical reagents were of analytical grade and used as-received. To grow Bi2S3 nanorods on Ti substrate, Bi2S3 seeds were produced on Ti substrate first via pyrogenation followed by the synthesis of the Bi2S3 nanorods on Ti substrate via a hydrothermal process. For a typical preparation, 0.51 g Bi(NO3)2·5H2O and 0.21 g thiourea (Tu) were sequentially dissolved into 50 mL ethylene glycol. After stirring for 1 h, the solution was dropped onto a well-polished and cleaned Ti substrate and scraped with a flake for uniform distribution. Finally, Ti substrate was heated on a magnetic heater for 5 minutes at 140 °C. After the mobilization described above, the substrate was annealed at 350 °C for 2 h to firmly adhere Bi2S3 seeds onto the Ti surface. Then, the substrate was placed in a 50 mL Teflon-lined autoclave containing 40 mL of the mix ethylene glycol solution and heated at 140 °C for 10 h. After reaction, the autoclave was naturally cooled to room temperature; the substrates were then washed several times with deionized water and ethanol followed by drying at 60 °C for 4 h.
2.2 Electrodeposition of Co(OH)2
The electrodeposition process was performed in 1 M Co(NO3)2 with a conventional three-electrode cell, the Bi2S3 nanorods on Ti substrate (noted BNRs) are used as working electrodes, while platinum foil and Ag/AgCl electrode are used as counter and reference electrodes, respectively. A constant potential deposition of cobalt hydroxide was carried out at −1.0 V vs. Ag/AgCl for 50 s at 10 °C, 25 °C, 45 °C, 60 °C and 90 °C. The synthesized products are respectively named BCCs-10 °C, BCCs-25 °C, BCCs-45 °C, BCCs-60 °C and BCCs-90 °C. For comparison, Co(OH)2 on Ti substrate without Bi2S3 was also fabricated with the same constant potential deposition approach at 90 °C by using plain Ti as a working electrode (denoted as CNSs-90 °C).
2.3 Material characterization
The crystal structure of the products was characterized by X-ray diffraction (XRD-7000) operating at 40 kV, 2° min−1, 30 A and Cu Kα (λ = 0.15406) radiation. The morphology was examined by scanning electron microscopy (SEM, JSM-6510LV) operating at 20 kV and transmission electron microscopy (JEM-2100) operating at 200 kV. The element analysis is examined by EDS (INCA X-MAX 250).
2.4 Electrochemical measurements
Except specific description, all the electrochemical characterizations were carried out in 0.5 M Na2SO4 with a three-electrode cell using the products grown on Ti substrate (0.3 cm × 0.5 cm), platinum foil and saturated calomel electrode (SCE) as working, counter and reference electrodes, respectively, in which charge–discharge (CD) and cyclic voltammetry (CV) techniques were performed over −0.8 V to 0.1 V, while EIS measurement was conducted from 100 kHz to 0.01 Hz with a bias of 5 mV at the open circuit potential. All the electrochemical measurements were conducted with a CHI 660 electrochemical workstation (Shanghai Chenhua Co., China). Two expressions are used for specific capacitance: gravimetric and surface specific capacitance and both are widely used in literature. However, Gogotsi et al.31 have recently pointed out that the gravimetric performance is an unreliable method of comparison for supercapacitors. Here the specific area capacitance is used and calculated as follows: |
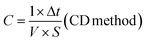 | (1) |
|
 | (2) |
where C (mF cm−2) is the specific capacitance, I (mA) is the discharge current, Δt (s) is the discharge time, V (V) is the potential window, and S (cm2) is the area of the work electrode, and ν (V s−1) is scan rate.
3. Results and discussion
The synthesized materials including Bi2S3 nanorods on Ti substrate, Co(OH)2 nanosheets electrodeposited at 90 °C on Ti substrate (named CNSs-90 °C) and the Bi2S3/Co(OH)2 composites electrodeposited at 90 °C on Ti substrate were examined by XRD as shown in Fig. 1a. Observations are well matched with the standard card (JCPDS card no. 17-0320) and confirm an orthorhombic-structured phase.17 The XRD curve of CNSs-90 corresponds to the well-known form of the layered α-Co(OH)2 (ref. 32) and the XRD curve for BCCs-90 °C hybrid displays the characteristic peaks of both Bi2S3 and α-Co(OH)2, clearly exposing its two components. No additional impurity peak is observed except that of Ti substrate, indicating a successful synthesis of the expected composite. The EDS image of BCCs-90 °C in Fig. 1b reveals that the composing elements are oxygen, cobalt, bismuth, sulphur and titanium; thus, proving the existence of Co(OH)2, Bi2S3 and Ti.
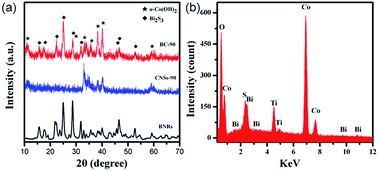 |
| Fig. 1 (a) XRD patterns of BNRs, CNSs-90 °C, and BCCs-90 °C. (b) EDS image of BCCs-90 °C. | |
The SEM and TEM morphologies of the products in Fig. 2 and 3 show that the obtained Bi2S3, which adhered on Ti substrate is composed of nanorods (Fig. 2a) with a diameters of 100–200 nm and lengths of 800–1000 nm. With different deposition temperatures the morphology of the produced Co(OH)2 significantly changes. When the deposition is made at 10 °C, Co(OH)2 slowly grows around the Bi2S3 nanorods displaying numerous pores. With increasing temperature, the Co(OH)2 grows faster, resulting in larger nanosheets as in Fig. 2c, which is very likely to connect together the nanorods because of fast growth. However, because the deposition area is limited, more Co(OH)2 nanosheets are deposited at higher temperatures, and have to be networked with each other to form a dense packed structure with smaller pores as shown in Fig. 2d–f; thus, producing a porous, networked structure. In addition, the low magnification SEM images of BCCs-90 °C in Fig. S4† show that the uniformity of BCCs is good.
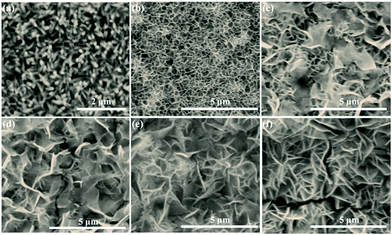 |
| Fig. 2 SEM images of the samples: (a) BNRs, (b) BCCs-10 °C, (c) BCCs-25 °C, (d) BCCs-45 °C, (e) BCCs-60 °C, and (f) BCCs-90 °C. | |
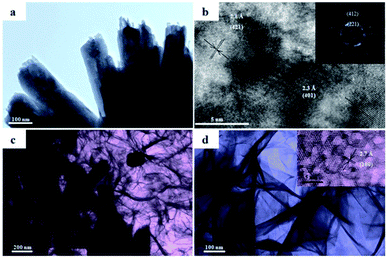 |
| Fig. 3 (a) The TEM image of BNRs. (b) The high magnification TEM image and corresponding SAED pattern of BNRs. (c) The TEM image of BCCs-90 °C. (d) The low magnification and high magnification TEM image of CNSs-90 °C. | |
The TEM image in Fig. 3a shows that the produced Bi2S3 has a diameter of about 125 nm. The lattice spacing values calculated from high resolution TEM (HRTEM) (Fig. 3b) are 2.1 Å and 2.3 Å, which correspond to (421) and (041) planes of the orthorhombic Bi2S3, respectively. The corresponding SAED pattern (inset of Fig. 3b) indicates that the product is multicrystaline and the diffractive ring correspond to (412) and (221) planes of the orthorhombic Bi2S3. The top-view image in Fig. 3c for the hybrid BCCs-90 shows that the nanorods are wrapped by Co(OH)2. The typical TEM and HRTEM images of the pure α-Co(OH)2 reveal that the product is highly thin and HRTEM (inset) further shows that a single piece of Co(OH)2 is made up of small nanoparticles with diameters of 2–5 nm and a lattice spacing value of 2.7 Å, corresponding to (100) plane of α-Co(OH)2, which further confirms the existence of α-Co(OH)2. The TEM images demonstrate that the modified nanocomposite comprises nanoscale particles with high porosity.
The CVs of BNRs, CNSs and BCCs-90 °C shown in Fig. 4a are obtained under the same conditions and possess two prominent redox peaks of Bi2S3 for large pseudocapacitance. However, the Co(OH)2 alone does not show any redox peak and also has no significant double-layer capacitance (Fig. 4a), indicating that the electrodeposited Co(OH)2 without Bi2S3 cannot deliver the capacitance. However, it is interesting to observe that the hybrid product, BCCs-90 °C greatly increases the pseudocapacitance. Fig. 4b presents the galvanostatic charge–discharge curves of BNRs, CNSs and BCCs-90 °C at the same current densities. All the discharge curves start with a sudden potential drop caused by the internal resistance, followed by various sections of slopes, indicating pseudocapacitive characteristics resulting from redox reactions of the products. Fig. 4b also reveals that neither pristine CNSs nor BNRs have any lasting discharge behaviour, demonstrating that the hybrid BCCs-90 °C with the modification of Co(OH)2 greatly improves the specific capacitance while increasing the cycle life.
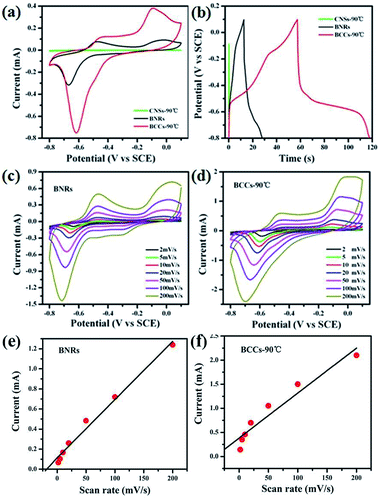 |
| Fig. 4 (a) The CV image of CNSs-90 °C, BNRs and BCCs-90 °C at a scan rate of 20 mV s−1. (b) Charge–discharge curve of CNSs-90 °C, BNRs and BCCs-90 °C at 1 mA cm−2 of current density. CV images of (c) BNRs (d) BCCs-90 °C at various scan rates. The relationships between peak current and scan rate for (e) BNRs, (f) BCCs-90 °C. | |
CV in a broader potential window from −1.05 V to 0.25 V was conducted to investigate the electrochemical behaviour of Bi2S3. As shown in Fig. S1,† there are two pairs of strong redox peaks and a pair of weak redox peaks for Bi2S3. Among them, the strong redox peak potentials (−0.6 V and 0.35 V) are very close to that of Bi2O3; thus, we suggest that these redox peaks are obtained from the change in the valence state bismuth.33 The other strong redox peaks and the weak ones probably are obtained from the two-step adsorption–desorption phenomenon of hydrogen in Bi2S3.34,35 The mechanism for the same is shown as following:
Bi2S3 + H2O + e− = (Hads + Bi2S3) + OH− |
for the as-prepared hybrid material, the increase in the electrodeposition temperature of Co(OH)
2 results in higher peak current at a same scan rate for higher specific capacitance in terms of
eqn (2) and a longer discharge time at a same current density for higher capacity (Fig. S2
†). When the temperature rises to 90 °C (the highest temperature of CoCl
2 electrolyte achieved at the atmospheric pressure in Chong Qing), it presents the highest discharge time. Thus, the optimal electrodeposition temperature is 90 °C.
Furthermore, measurements were conducted with BNRs and BCCs-90 °C. Fig. 4c and d illustrate that the peak current subsequently increases with increasing scan rates, while the CV shape still remains the same even at a high scan rate (200 mV s−1), which correspond to an ideal capacitive behaviour. Fig. 4e and f show the relationships between peak current (calculated from the peak at −0.7 V in Fig. 4c and d according the reported approach36) and scan rate. This relationship is linear for both catalysts, indicating that the redox reactions on both the catalysts are surface-limited, which is a good pseudocapacitive character.37
It is known that a larger potential window can offer higher energy density; however, the cycle stability of BCCs-90 °C is poor in a wider potential window of −1.05 V to 0.25 V, which can only maintain 20% of its initial specific capacitance after 1000 cycles. When the potential window is reduced to a range of −0.8 V to 0.1 V, the cycle stability improves to 94%. Thus, we choose the potential window from −0.8 V to 0.1 V to perform galvanostatic charge–discharge measurements of BNRs and BCCs-90 °C (Fig. 5a and b) for further studies. Both the charge and discharge curves have a slope, which is a reflection of the redox reaction of the product. However, the two as-prepared products show different discharge time at a same discharge current density, which infers different specific capacitance. For BCCs-90 °C, the specific capacitance value are 211 mF cm−2, 113.3 mF cm−2, 69.4 mF cm−2 and 66.7 mF cm−2 at current densities of 0.1 mA cm−2, 0.2 mA cm−2, 0.5 mA cm−2 and 1 mA cm−2, respectively. The capacitance of the pristine BNRs cannot be measured at too small charge current density, such as 0.1 mA cm−2, 0.2 mA cm−2 and 0.5 mA cm−2, and it only reaches 18 mF cm−2 at a discharge current density of 1 mA cm−2 (Fig. 5c), which is considerably smaller than BCCs-90 °C (66.7 mF cm−2 at 1 mA cm−2). In comparison to other reported pseudocapacitive materials such as Bi2O3, which can offer 22 mF cm−2 at 100 mV s−1 (ref. 38) the modified BCCs-90 °C produces a considerably higher capacitance of 28.4 mF cm−2. The electrochemical cycle stability of the synthesized product BNRs and BCCs-90 °C were examined at a scan rate of 100 mV s−1 in 0.5 M Na2SO4 over −0.8 V to 0.1 V by CV. Fig. 5d shows that the capacitance of BNRs gradually increases from 21.09 mF cm−2 to 30.86 mF cm−2 for the first 500 cycles, which is probably due to a material activation process,39 and then it gradually fades to 26.25 mF cm−2, which is about 85% of its highest capacitance. BCCs-90 °C exhibits a slight fading for the first 200 cycles, followed by a constant capacitance of approximately 33.5 mF cm−2 and achieves a retention rate of 94% after 1000 cycles (inset of Fig. 5d); thus, demonstrating the better cycle stability of BCCs compared to that of BNRs.
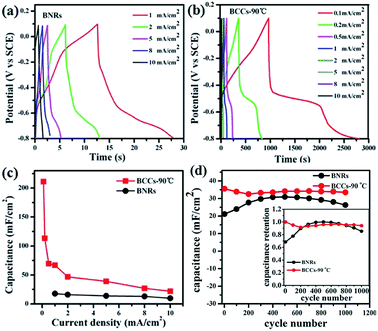 |
| Fig. 5 Charge–discharge curve (a) BNRs (b) BCCs-90 °C. (c) Capacitance of BCCs-90 °C and BNRs at various current densities. (d) CV cycling test at a scan rate of 100 mV s−1 for BNRs and BCCs-90 °C. The inset shows the capacitance retention ratio during the cycling test for BNRs and BCCs-90 °C. | |
The improved specific capacitance and cycle stability of the hybrid Bi2S3/Co(OH)2 nanocomposite can be obviously attributed to the modification of ultrathin Co(OH)2 nanosheets deposited at high temperature on Bi2S3 nanorods resulting in a porous and networked nanostructure as shown in Fig. 2. From the measured impedance spectra there is no significant improvement for the Faraday resistance because of their similar semi-circles (Fig. S3†). As discussed above, because the pseudocapacitance is the main contribution to the modification and because the peak current is proportional to the scan rate, the following equation can be used to calculate the surface reaction area:
|
Ip = (9.39 × 105)n2VAΓ*o
| (3) |
where
Ip (A) is the peak current,
n is the number of electrons transferred,
V (V s
−1) is the scan rate of CVs,
A (cm
2) is the electrode surface area, and
Γ*o (mol cm
−2) is the amount of absorbed reactant on the electrode surface. All the experiments for the four catalysts were conducted with the same amount of Bi
2S
3 and same scan rate, as well as
n,
V were also the same. Thus,
Ip is directly proportional to
A. According to CV curves in Fig. S1(a),
† the calculated ratios of the reaction surface areas for the four catalysts are
ABNRs![[thin space (1/6-em)]](https://www.rsc.org/images/entities/char_2009.gif)
:
ABCCs-10 °C![[thin space (1/6-em)]](https://www.rsc.org/images/entities/char_2009.gif)
:
ABCCs-25 °C![[thin space (1/6-em)]](https://www.rsc.org/images/entities/char_2009.gif)
:
A BCCs-90 °C = 1
![[thin space (1/6-em)]](https://www.rsc.org/images/entities/char_2009.gif)
:
![[thin space (1/6-em)]](https://www.rsc.org/images/entities/char_2009.gif)
1.4
![[thin space (1/6-em)]](https://www.rsc.org/images/entities/char_2009.gif)
:
![[thin space (1/6-em)]](https://www.rsc.org/images/entities/char_2009.gif)
2.4
![[thin space (1/6-em)]](https://www.rsc.org/images/entities/char_2009.gif)
:
![[thin space (1/6-em)]](https://www.rsc.org/images/entities/char_2009.gif)
4.6, indicating that BCCs-90 °C is 4.6 times larger than that of BNRs. Thus, it could be concluded that the Co(OH)
2 modification of Bi
2S
3 can produce a large surface reaction area for the larger pseudocapacitance, while the dense formed hybrid network is able to retain its intact structure during the cycle process for long cycle stability.
4. Conclusions
In summary, the capacitance behaviour of Bi2S3 is studied for the first time. The pure Bi2S3 alone does not show significant capacitive capacity; however, the modification of Bi2S3 nanorods with ultrathin Co(OH)2 nanosheets at high temperature significantly boosts the specific capacitance while improving the cycle stability, which is mainly because of the formed porous and networked nanostructure. CV results indicate that the modification mainly results in large surface reaction area for large pseudocapacitance, while the networked robust structure could remain intact during the cycle process for long cycle stability. This work demonstrates that the modification process is a facile approach to greatly change the physical nanostructure and reach excellent pseudocapacitive properties.
Acknowledgements
This work was supported by Institute for Clean Energy & Advanced Materials (Southwest University, Chongqing, China), Chongqing Key Laboratory for Advanced Materials and Technologies of Clean Energies, Chongqing Science and Technology Commission under cstc2012gjhz90002, and Chongqing development and reform commission and National Natural Scientific Fund (no. 21375108).
Notes and references
- Y. Luo, J. Jiang, W. Zhou, H. Yang, J. Luo, X. Qi, H. Zhang, Y. Denis, C. M. Li and T. Yu, J. Mater. Chem., 2012, 22, 8634–8640 RSC.
- Z. Cui, C. X. Guo, W. Yuan and C. M. Li, Phys. Chem. Chem. Phys., 2012, 14, 12823–12828 RSC.
- C. X. Guo and C. M. Li, Energy Environ. Sci., 2011, 4, 4504–4507 CAS.
- K. S. Tan and C. M. Li, Phys. Chem. Chem. Phys., 2011, 13, 14462–14465 RSC.
- P. Simon and Y. Gogotsi, Nat. Mater., 2008, 7, 845–854 CrossRef CAS PubMed.
- V. Subramanian, H. Zhu, R. Vajtai, P. Ajayan and B. Wei, J. Phys. Chem. B, 2005, 109, 20207–20214 CrossRef CAS PubMed.
- G. Wang, L. Zhang and J. Zhang, Chem. Soc. Rev., 2012, 41, 797–828 RSC.
- J. Zheng, P. Cygan and T. Jow, J. Electrochem. Soc., 1995, 142, 2699–2703 CrossRef CAS PubMed.
- X. Liu, B. Qu, F. Zhu, L. Gong, L. Su and L. Zhu, J. Alloys Compd., 2013, 560, 15–19 CrossRef CAS PubMed.
- S.-J. Bao, C. M. Li, C.-X. Guo and Y. Qiao, J. Power Sources, 2008, 180, 676–681 CrossRef CAS PubMed.
- T. Zhu, Z. Wang, S. Ding, J. S. Chen and X. W. D. Lou, RSC Adv., 2011, 1, 397–400 RSC.
- Q. Wang, X. Wang, W. Lou and J. Hao, New J. Chem., 2010, 34, 1930–1935 RSC.
- J.-S. Chung and H.-J. Sohn, J. Power Sources, 2002, 108, 226–231 CrossRef CAS.
- Y. Hu, Z. Zheng, H. Jia, Y. Tang and L. Zhang, J. Phys. Chem. C, 2008, 112, 13037–13042 CAS.
- M. Jayalakshmi and M. M. Rao, J. Power Sources, 2006, 157, 624–629 CrossRef CAS PubMed.
- B. Zhang, X. Ye, W. Dai, W. Hou and Y. Xie, Chem.–Eur. J., 2006, 12, 2337–2342 CrossRef CAS PubMed.
- H. Kim, C. Jin, S. Park, W. I. Lee, I.-J. Chin and C. Lee, Chem. Eng. J., 2013, 215, 151–156 CrossRef PubMed.
- P. Hu, Y. Cao and B. Lu, Mater. Lett., 2013, 106, 297–300 CrossRef CAS PubMed.
- Z. Zhang, C. Zhou, H. Lu, M. Jia, Y. Lai and J. Li, Mater. Lett., 2013, 91, 100–102 CrossRef CAS PubMed.
- R. Xing, D. Li, C. An, L. Zhang, Q. Li and S. Liu, J. Nanosci. Nanotechnol., 2012, 12, 8029–8033 CrossRef CAS PubMed.
- C. Tang, Y. Zhang, X. Dou and G. Li, J. Cryst. Growth, 2010, 312, 692–697 CrossRef CAS PubMed.
- H. Bao, C. M. Li, X. Cui, Q. Song, H. Yang and J. Guo, Nanotechnology, 2008, 19, 335302 CrossRef PubMed.
- M. B. Sigman and B. A. Korgel, Chem. Mater., 2005, 17, 1655–1660 CrossRef CAS.
- J. L. Xie, C. X. Guo and C. M. Li, Energy Environ. Sci., 2014, 7, 2559–2579 CAS.
- Y. Li, H. Wang, L. Xie, Y. Liang, G. Hong and H. Dai, J. Am. Chem. Soc., 2011, 133, 7296–7299 CrossRef CAS PubMed.
- J. Yang and J. Y. Ying, Angew. Chem., Int. Ed., 2011, 50, 4637–4643 CrossRef CAS PubMed.
- M.-R. Gao, S. Liu, J. Jiang, C.-H. Cui, W.-T. Yao and S.-H. Yu, J. Mater. Chem., 2010, 20, 9355–9361 RSC.
- W. Han, L. Yi, N. Zhao, A. Tang, M. Gao and Z. Tang, J. Am. Chem. Soc., 2008, 130, 13152–13161 CrossRef CAS PubMed.
- P. K. Nayak and N. Munichandraiah, J. Electrochem. Soc., 2008, 155, A855–A861 CrossRef CAS PubMed.
- H.-J. Ahn, W. B. Kim and T.-Y. Seong, Electrochem. Commun., 2008, 10, 1284–1287 CrossRef CAS PubMed.
- Y. Gogotsi and P. Simon, Science, 2011, 334, 917–918 CrossRef CAS PubMed.
- V. Gupta, T. Kusahara, H. Toyama, S. Gupta and N. Miura, Electrochem. Commun., 2007, 9, 2315–2319 CrossRef CAS PubMed.
- F. L. Zheng, G. R. Li, Y. N. Ou, Z. L. Wang, C. Y. Su and Y. X. Tong, Chem. Commun., 2010, 46, 5021–5023 RSC.
- P. Hu, Y. Cao and B. Lu, Mater. Lett., 2013, 106, 297–300 CrossRef CAS PubMed.
- A. J. Bard and L. R. Faulkner, Electrochemical methods: fundamentals and applications, Wiley, New York, 1980 Search PubMed.
- X. Li, T. Zhao, Q. Chen, P. Li, K. Wang, M. Zhong, J. Wei, D. Wu, B. Wei and H. Zhu, Phys. Chem. Chem. Phys., 2013, 15, 17752–17757 RSC.
- D. Pletcher, R. Greff, R. Peat, L. Peter and J. Robinson, Instrumental methods in electrochemistry, Elsevier, 2001 Search PubMed.
- T. P. Gujar, V. R. Shinde, C. D. Lokhande and S.-H. Han, J. Power Sources, 2006, 161, 1479–1485 CrossRef CAS PubMed.
- H. Wang, Q. Hao, X. Yang, L. Lu and X. Wang, Nanoscale, 2010, 2, 2164–2170 RSC.
Footnote |
† Electronic supplementary information (ESI) available. See DOI: 10.1039/c4ra05763e |
|
This journal is © The Royal Society of Chemistry 2014 |