DOI:
10.1039/D0NA00282H
(Communication)
Nanoscale Adv., 2020,
2, 2726-2730
Disulfide exchange assisted self-healing epoxy/PDMS/graphene oxide nanocomposites†
Received
8th April 2020
, Accepted 2nd June 2020
First published on 3rd June 2020
Abstract
Vitrimers, a class of polymeric networks that change their topology above a threshold temperature, have been investigated in recent years. In order to further extend their properties, in this research, we demonstrate disulfide exchange assisted polydimethylsiloxane (PDMS)- and graphene oxide (GO)-involved epoxy vitrimers, which exhibit a reduction in glass transition temperature and storage modulus with increase in flexural strain and low-temperature self-healing. Stress relaxation and Arrhenius study were carried out for the analysis of vitrimeric behavior, where the prepared epoxy material displays self-healing at 80 °C for 5 min, whereas a low-temperature self-healing (60 °C) was observed for epoxy/PDMS/GO nanocomposites.
Introduction
Thermoset materials with excellent mechanical,1–3 thermal4 and chemical resistance properties5 have been developed for many industrial,6 aircraft,7 wind turbine8 and composite applications.9 However, due to the lack of re-processability, recyclability, and reshaping ability, their applications have been restricted.10 In contrast, some thermoplastic materials have the ability to flow in certain temperature ranges and this prevailing temperature response is intriguing in reprocessing. However, their lower strength and structural ability do not match the required properties.11,12 Recyclable/reprocessable thermoset polymers have emerged over the past few years to acquire reliable reprocessing through simple and efficient mechanisms.13,14 In particular dynamic covalent exchange promoted thermoset materials were demonstrated with recycling and self-healing behavior,15–20 where during reprocessing promising associative exchange results in a concurrent exchange between chains, as introduced by Leibler and coworkers.21 The reported epoxy vitrimers execute associative exchanges through transesterification reactions, and the role of catalysts in exchange reactions was investigated thoroughly.22 Since then, many reports have discussed vitrimer materials with different chemistries such as transesterification,23–26 transalkylation,27 transamination,28 disulfide,29–31 transcarbamoylation32,33 and transcarbonation.34 Among these reactions, disulfide exchanges were prominently discussed in self-healing studies to realize effective properties.35,36
In the present study, catalyst-free disulfide exchange-promoted epoxy/PDMS/GO nanocomposite vitrimer materials with self-healing behavior are reported. The addition of catalyst not only causes toxicity but the mixing challenge also compromises the mechanical properties of the synthesized vitrimers. In addition, dynamic bond-exchange reactions often occur at elevated temperature, and thermal degradation could be hastened in the presence of a catalyst. Therefore, the absence of catalyst is advantageous owing to non-toxicity and non-degradability at high temperature.37,38 Furthermore, the addition of PDMS should not only be helpful for achieving low-temperature self-healing, but would also be helpful to overcome the brittleness of the epoxy matrix and improve its impact properties, including the resistance to crack propagation. As covalently crosslinked pristine epoxy demonstrates a brittle failure, the involvement of flexible epoxy-terminated PDMS has been effectuated to increase the toughness,39,40 and the incorporation of GO is helpful to enhance the material strength. The prepared composite vitrimer material exhibits a reduction in glass transition temperature (Tg) and storage modulus including an enhancement in flexural strain. The mechanical strength was increased by the addition of GO nanofillers, and fine dispersion of PDMS and GO was evaluated through SEM and contact angle measurements. Furthermore, vitrimer behavior was observed through stress relaxation characteristics and Arrhenius plots. The prepared pristine epoxy (EP-p) material displays self-healing at 80 °C for 5 min, whereas a low-temperature self-healing (60 °C) was observed for epoxy/PDMS/GO nanocomposites.
Experimental section
Materials and methods
Bisphenol A diglycidyl ether (BADGE) (340.41 g mol−1) resin, diglycidyl ether terminated PDMS (800 g mol−1), 2-aminophenyl disulfide (2-AFD) (248.37 g mol−1) hardener and graphite flakes were purchased from Sigma-Aldrich.
Preparation of epoxy composites
In a round-bottom flask, BADGE resin and epoxy terminated PDMS were stirred at 130 °C for 7 hours, and later 2-AFD was added and the reaction mixture was continuously stirred at the same temperature for 15 min (Fig. 1). Subsequently, the reaction mixture was poured into a mold and kept at 150 °C for 5 hours for curing. Finally, the attained specimen was used for further studies including those of mechanical and self-healing properties. To optimize the PDMS effect in epoxy, different percentages of PDMS were incorporated in the matrix and investigated effectively (shown in Table 1), and the samples were denoted as EP-x% (x = p (0), 1, 2, 3 and 5) (Table S1(a)†).
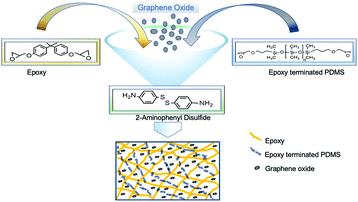 |
| Fig. 1 Synthesis route of epoxy-PDMS-GO nanocomposite. | |
Table 1 Glass transition temperature and contact angle values of different samples
Epoxy/PDMS (EP-x) |
Glass transition temperature (Tg) |
Contact angle (°) |
EP-p |
64 |
85 |
EP-1 |
62 |
88 |
EP-2 |
58 |
97 |
EP-3 |
62 |
94 |
EP-5 |
63 |
89 |
![[thin space (1/6-em)]](https://www.rsc.org/images/entities/char_2009.gif) |
Epoxy–PDMS–GO (EP-2-y)
|
EP-2-0.1 |
57 |
98 |
EP-2-0.2 |
56 |
99 |
EP-2-0.5 |
53 |
101 |
EP-2-1 |
55 |
97 |
EP-2-2 |
58 |
97 |
Preparation of epoxy nanocomposites
A similar procedure was followed for the preparation of nanocomposites, where ethanol-dispersed GO solution was added (Table S1(b)†) in the mixture (PDMS/epoxy) and stirring continued until ethanol evaporation. Finally, 2-AFD was added and stirred for another 15 min. The reaction mixture was poured in a mold and kept in an oven at 150 °C for 5 h.
Characterization techniques
GO was prepared through the Hummers method41,42 (SI) from graphite flakes. The obtained X-ray diffraction (D8 ADVANCE ECO, Bruker) peak shifting from 23° (graphite) to 12.3° confirmed the GO formation (Fig. S1†). FTIR (Frontier FT-IR/FIR, PerkinElmer) analysis was used for characterization. Rectangular specimens (15 mm × 5 mm × 0.5 mm) were investigated by TA-Q400em three-point bending test (40 °C to 120 °C) to determine the storage modulus and loss modulus (heat rate of 10 °C min−1; 50 mL min−1 nitrogen; 0.02 N). Stress relaxation and stress–strain experiments were performed at 40 °C, with 1 × 10−3 N preload (1% strain) and 0.02 N force respectively.
Results and discussion
The curing of epoxy was examined over regular time intervals (hourly basis) with the help of FTIR analysis (Fig. S2†); eventually after 5 hours no decrease (914 cm−1) was observed (Fig. 2(a)).36 Furthermore, THF swelling test was performed to identify the complete curing, as uncured epoxy-PDMS composite had unbonded covalent formations, which could not be retained under vigorous stirring (Fig. S3†). The dispersion of PDMS in epoxy was investigated through contact angle and SEM analysis. Initially, dispersion of the PDMS in epoxy was evaluated with hydrophobic changes, where enhancement in hydrophobicity was observed [sample EP-2], which could be due to a good dispersion of PDMS in epoxy matrix.40,43 However, with further addition of PDMS a gradual decrease in hydrophobicity was observed (Table 1), denoting PDMS dispersion failure in the matrix.40 A similar kind of behavior was observed for GO-based composites, where hydrophobicity was increased with incorporation of GO [EP-2-0.5], whereas further increasing GO incorporation decreases the hydrophobicity (Table 1). The temperature-dependent transition was noticed through DMA analysis and the obtained glass transition temperatures of the epoxy vitrimer samples are tabulated in Table 1. The resulting glass transition temperature effectively indicated that the incorporation of PDMS and GO is advantageous to reduce the Tg of the prepared composites. The observed change in Tg behavior could be owing to (i) low Tg of PDMS44 or (ii) fine dispersion of PDMS.43 However, after further addition of PDMS an increase in Tg was obtained.
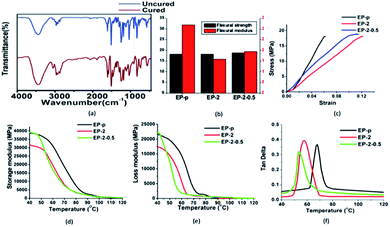 |
| Fig. 2 (a) FTIR spectra. (b) Bar diagram for flexural strength and modulus of different samples. (c) Stress–strain, (d) storage modulus, (e) loss modulus and (f) tan δ. | |
To find out the impact of nanofillers, different percentages of GO were included in EP-2 samples, and the obtained results demonstrate a further decrease in Tg, where GO-based nanofillers exhibit a free volume space between matrix and filler.45 However, a further addition of GO increases the Tg of the composites [EP-2-1; EP-2-2], which might be again due to agglomeration of GO, thus leading to poor interaction with the epoxy-PDMS matrix.
Based on these observations, further investigations were carried out for EP-p, EP-2 and EP-2-0.5 specimens. The determined storage modulus (E′), loss modulus (E′′) and tan
δ data exhibit a temperature-dependent viscoelastic behavior (Fig. 2(d–f)) for the prepared specimens and the obtained storage modulus of EP-p at 40 °C was much higher than that of EP-2. The reduction in storage modulus could be due to the presence of PDMS, which demonstrates a lower crosslinking density.43
Furthermore, incorporated GO restrains the covalent formation of epoxy and thus leads to the free volume space between filler and matrix. The storage modulus of specimen EP-2-0.5 was higher than that of EP-2, which could be due to the wavy topology of GO, enhancing intercalate interlocking between matrix and nanofiller at low temperature.46
Stress–strain curve shows that flexural strength (Fig. 2(b)) of Ep-p (18 MPa) was slightly lower than that of EP-2 and EP-2-0.5 (18.1 MPa and 18.7 MPa, respectively), though EP-2 strain at break point was higher than that of EP-p and EP-2-0.5 (Fig. 2(c)). The observed strain at break increase exemplified the flexural modulus decrease, and thus acquired due to the presence of PDMS which reduces the bending resistance/brittleness. Substantially, observed strain at break values of EP-2 and Ep-2-0.5 have increased two times (from 0.06 to 0.12) and 50% (0.06 to 0.09) compared to EP-p, respectively, whereas the obtained flexural moduli of EP-2 and EP-2-0.5 (15.7 GPa and 19.4 GPa, respectively) were less than the EP-p flexural modulus (32.1 GPa) (shown in Table 2).
Table 2 Different properties of EP-p, EP-2 and EP-2-0.5 samples
Sample |
Storage modulus (GPa) |
Flexural strength (MPa) |
Flexural strain at break (mm mm−1) |
Flexural modulus (GPa) |
Activation energy (Ea) (kJ mol−1) |
Topology transition temperature (Tv) (°C) |
Before healing (GPa) |
After healing (GPa) |
1st |
2nd |
EP-p |
39.7 |
18.0 |
0.06 |
32.1 |
59 |
19 |
32.1 |
23.4 |
19.5 |
EP-2 |
31.6 |
18.1 |
0.12 |
15.7 |
52 |
−1 |
15.7 |
13.5 |
12.1 |
EP-2-0.5 |
39.9 |
18.7 |
0.09 |
19.4 |
180 |
31 |
19.4 |
17.3 |
15.8 |
SEM analysis was carried out to study the effect of PDMS in the epoxy matrix. The fractured surfaces in Fig. 3(a and b) show that there is a homogeneous cured resin as no phase domains could be observed. The dispersibility of the GO nanosheets was analyzed using TEM imaging (Fig. 3(c)).
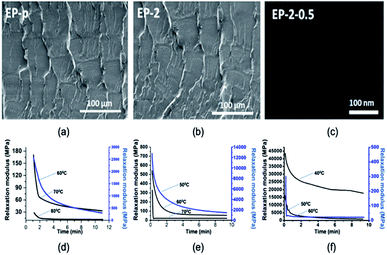 |
| Fig. 3 (a) SEM image of EP-p. (b) SEM image of epoxy/PDMS. (c) TEM image of epoxy/PDMS/GO nanocomposite. Stress relaxation analysis at different temperatures for (d) EP-p, (e) EP-2 and (f) EP-2-0.5. | |
The images show an excellent dispersion of GO nanosheets in epoxy vitrimer matrix (EP-2). For identifying the vitrimer behavior, stress relaxation behavior of the materials was studied.36 For instance, relaxation times of 112.8 s, 40.8 s and 34 s at 60 °C, 70 °C and 80 °C, respectively, were observed for EP-p specimen (Fig. 3(d)). However, in the case of EP-2, relaxation times of 42.6 s, 27.6 s and 13.8 s at 50 °C, 60 °C and 70 °C respectively were observed (Fig. 3(e)). However, due to the faster relaxation after Tg, specimen EP-2-0.5 demonstrates times of 89.6 s, 16.8 s and 3 s at 40 °C, 50 °C and 60 °C, respectively (Fig. 3(f)). Thus, obtained relaxation times were plotted on a graph to identify the Arrhenius equation, and from that equation activation energy (Ea) was calculated (Table 2). The material Tv has been generally considered once the viscosity reaches 1012 Pa s;21 hence this hypothesized Tv temperature range has been extrapolated based on the literature36 (see ESI†) for EP-p sample. Subsequently, investigated low-viscosity siloxanes containing PDMS involved in EP-2 resulted in a lower activation energy (Ea)47 and Tv than EP-p (Table 2).44,48
However, owing to the presence of GO, EP-2-0.5 exhibits a higher Tv and Ea than EP-2 (not EP-p), where GO nanofiller leads to an increase in viscosity and thus restricts the low-temperature chain mobility,49 whereas assimilated free volume has reduced the Tg.45 Self-healing behavior of EP-p was observed at 80 °C for 5 min, whereas the EP-2 and EP-2-0.5 samples demonstrate efficient healing at 60 °C for 5 min, which could be due to their lower Tg. The obtained self-healing of the material was acquired through disulfide exchanges, where sulfide radicals were accumulated at certain temperature (Fig. 4(a)). Such sulfide radical exchanges have been identified through electron paramagnetic resonance (EPR) analysis (80 °C) and the observed (g value = 2.003) peak confirms the radical formation in the material (Fig. 4(b)).
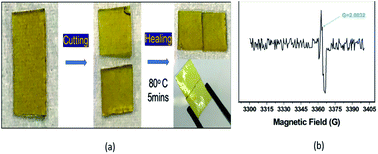 |
| Fig. 4 (a) Healing of sample EP-2. (b) EPR analysis graph. | |
Further, the self-healing efficiency was evaluated through the flexural modulus, where the strength of the material was found to be almost the same after consecutive healing (Table 2). The observed healing efficiency of the material was addressed through flexural modulus changes, where healing efficiencies of 72%, 85%, and 89% in the first cycle and 60%, 77%, and 82% in the second cycle were observed for EP-p, EP-2 and EP-2-0.5 specimens respectively (Fig. 5).
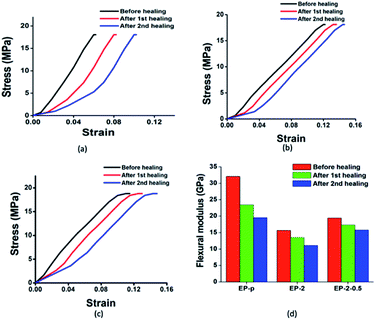 |
| Fig. 5 Stress–strain curves for (a) EP-p, (b) EP-2 and (c) EP-2-0.5 and (d) bar diagram for changes in flexural modulus after two healing cycles. | |
Conclusions
The synthesized epoxy-PDMS composite material exhibits a prominent reduction in glass transition temperature and effective decrease in bending resistance; however, the strength of the material does not show any change. After addition of PDMS and GO nanofiller in the epoxy vitrimer, certain mechanical properties were investigated through flexural studies and the obtained results indicated a difference in mechanical strength, strain at break and modulus. The pristine epoxy (EP-p) specimen demonstrates healing behavior at 80 °C for 5 min, whereas specimens EP-2 and EP-2-0.5 demonstrate healing at 60 °C for 5 min. Furthermore, the analyzed flexural modulus is helpful to quantify the mechanical properties and healing efficiency, where reduction in flexural modulus was observed after each healing cycle. However, the flexural strength of the material was not changed after two successive healing cycles. Overall, vitrimeric materials have enriched polymeric research via symbiosis of thermoset and thermoplastic properties. However, the demonstrated high glass transition temperature and activation energy restrict their performances. To overcome those snags, different mechanisms are involved. Herein, the synthesized multifunctional epoxy/PDMS/GO nanocomposite provides a new pathway to achieve a low glass transition temperature, required/designed to obtain a low-temperature self-healing, which is a current focus of interest.
Conflicts of interest
There is no conflict of interest.
Acknowledgements
We gratefully acknowledge the financial support from Science and Engineering Research Board (SERB-DST), Government of India (grant no. ECR/2016/001355) and Creative-Pioneering Researchers Program through Seoul National University (SNU) and Institute of Engineering Research at Seoul National University.
References
- A. Shiota and C. K. Ober, Prog. Polym. Sci., 1997, 22, 975–1000 CrossRef CAS.
- A. Tcharkhtchi, S. Faivre, L. E. Roy, J. P. Trotignon and J. Verdu, J. Mater. Sci., 1996, 31, 2687–2692 CrossRef CAS.
-
M. J. Mullins, D. Liu and H.-J. Sue, in Thermosets, ed. Q. Guo, Woodhead Publishing, 2012, pp. 28–61 Search PubMed.
-
D. Ratna, in Thermosets, ed. Q. Guo, Woodhead Publishing, 2012, pp. 62–91 Search PubMed.
-
Chemical Resistance of Thermosets, ed. E. Baur, K. Ruhrberg and W. Woishnis, William Andrew Publishing, 2018, pp. i–iii Search PubMed.
-
D. Song and R. K. Gupta, in Thermosets, ed. Q. Guo, Woodhead Publishing, 2012, pp. 165–188 Search PubMed.
- J. Baur and E. Silverman, MRS Bull., 2007, 32, 328–334 CrossRef CAS.
- L. Mishnaevsky, K. Branner, H. N. Petersen, J. Beauson, M. McGugan and B. F. Sørensen, Materials, 2017, 10, 1–24 CrossRef PubMed.
- C. T. Murray, R. L. Rudman, M. B. Sabade and A. V. Pocius, MRS Bull., 2003, 28, 449–454 CrossRef CAS.
-
A. Cervenka, in Mechanics of Composite Materials and Structures, ed. C. A. M. Soares, C. M. M. Soares and M. J. M. Freitas, Springer Netherlands, Dordrecht, 1999, pp. 289–298 Search PubMed.
- J. D. Muzzy and A. O. Kays, Polym. Compos., 1984, 5, 169–172 CrossRef CAS.
- G. Ken, Microelectron. Int., 1999, 16, 34–38 CrossRef.
- A. Li, J. Fan and G. Li, J. Mater. Chem. A, 2018, 6, 11479–11487 RSC.
- Y. Zhang, H. Ying, K. R. Hart, Y. Wu, A. J. Hsu, A. M. Coppola, T. A. Kim, K. Yang, N. R. Sottos, S. R. White and J. Cheng, Adv. Mater., 2016, 28, 7646–7651 CrossRef CAS PubMed.
- K. R. Hart, E. D. Wetzel, N. R. Sottos and S. R. White, Composites, Part B, 2019, 173, 106808 CrossRef.
- L. Guadagno, L. Vertuccio, C. Naddeo, E. Calabrese, G. Barra, M. Raimondo, A. Sorrentino, W. H. Binder, P. Michael and S. Rana, Polymers, 2019, 11, 903 CrossRef PubMed.
- M. Odarczenko, D. Thakare, W. Li, S. P. Venkateswaran, N. R. Sottos and S. R. White, Adv. Eng. Mater., 2020, 22, 1901223 CrossRef CAS.
- R. V. S. P. Sanka, B. Krishnakumar, Y. Leterrier, S. Pandey, S. Rana and V. Michaud, Front. Mater., 2019, 6, 137 CrossRef.
- S. Chen, N. Mahmood, M. Beiner and W. H. Binder, Angew. Chem., Int. Ed., 2015, 54, 10188–10192 CrossRef CAS PubMed.
- S. Y. Kim, N. R. Sottos and S. R. White, Compos. Sci. Technol., 2019, 175, 122–127 CrossRef CAS.
- D. Montarnal, M. Capelot, F. Tournilhac and L. Leibler, Science, 2011, 334, 965–968 CrossRef CAS PubMed.
- B. Krishnakumar, R. V. S. P. Sanka, W. H. Binder, V. Parthasarthy, S. Rana and N. Karak, Chem. Eng. J., 2019, 123820 Search PubMed.
- H. Han and X. Xu, J. Appl. Polym. Sci., 2018, 135, 46307 CrossRef.
- H. Zhang, C. Cai, W. Liu, D. Li, J. Zhang, N. Zhao and J. Xu, Sci. Rep., 2017, 7, 1–9 CrossRef PubMed.
- Z. Yang, Q. Wang and T. Wang, ACS Appl. Mater. Interfaces, 2016, 8, 21691–21699 CrossRef CAS PubMed.
- R. Long, H. J. Qi and M. L. Dunn, Soft Matter, 2013, 9, 4083–4096 RSC.
- B. Hendriks, J. Waelkens, J. M. Winne and F. E. Du Prez, ACS Macro Lett., 2017, 6, 930–934 CrossRef CAS.
- W. Denissen, G. Rivero, R. Nicolaÿ, L. Leibler, J. M. Winne and F. E. Du Prez, Adv. Funct. Mater., 2015, 25, 2451–2457 CrossRef CAS.
- Z. Ma, Y. Wang, J. Zhu, J. Yu and Z. Hu, J. Polym. Sci., Part A: Polym. Chem., 2017, 55, 1790–1799 CrossRef CAS.
- A. Ruiz de Luzuriaga, R. Martin, N. Markaide, A. Rekondo, G. Cabañero, J. Rodríguez and I. Odriozola, Mater. Horiz., 2016, 3, 241–247 RSC.
- A. Ruiz De Luzuriaga, J. M. Matxain, F. Ruipérez, R. Martin, J. M. Asua, G. Cabañero and I. Odriozola, J. Mater. Chem. C, 2016, 4, 6220–6223 RSC.
- D. J. Fortman, R. L. Snyder, D. T. Sheppard and W. R. Dichtel, ACS Macro Lett., 2018, 7, 1226–1231 CrossRef CAS.
- D. J. Fortman, J. P. Brutman, C. J. Cramer, M. A. Hillmyer and W. R. Dichtel, J. Am. Chem. Soc., 2015, 137, 14019–14022 CrossRef CAS PubMed.
- R. L. Snyder, D. J. Fortman, G. X. De Hoe, M. A. Hillmyer and W. R. Dichtel, Macromolecules, 2018, 51, 389–397 CrossRef CAS.
- A. Rekondo, R. Martin, A. Ruiz De Luzuriaga, G. Cabañero, H. J. Grande and I. Odriozola, Mater. Horiz., 2014, 1, 237–240 RSC.
- B. Krishnakumar, R. V. S. Prasanna Sanka, W. H. Binder, C. Park, J. Jung, V. Parthasarthy, S. Rana and G. J. Yun, Composites, Part B, 2019, 107647 Search PubMed.
- J. Han, T. Liu, C. Hao, S. Zhang, B. Guo and J. Zhang, Macromolecules, 2018, 51, 6789–6799 CrossRef CAS.
- J. J. Lessard, L. F. Garcia, C. P. Easterling, M. B. Sims, K. C. Bentz, S. Arencibia, D. A. Savin and B. S. Sumerlin, Macromolecules, 2019, 52, 2105–2111 CrossRef CAS.
- M. Raimondo, C. Naddeo, L. Vertuccio, L. Bonnaud, P. Dubois, W. H. Binder, A. Sorrentino and L. Guadagno, Nanotechnology, 2020, 31, 225708 CrossRef PubMed.
- A. Romo-Uribe, J. A. Arcos-Casarrubias, A. Reyes-Mayer and R. Guardian-Tapia, Polym.-Plast. Technol. Eng., 2017, 56, 96–107 CrossRef CAS.
- W. S. Hummers and R. E. Offeman, J. Am. Chem. Soc., 1958, 80, 1339 CrossRef CAS.
- A. S. Nia, S. Rana, D. Döhler, X. Noirfalise, A. Belfiore and W. H. Binder, Chem. Commun., 2014, 50, 15374–15377 RSC.
- N. M. Florea, A. Lungu, P. Badica, L. Craciun, M. Enculescu, D. G. Ghita, C. Ionescu, R. G. Zgirian and H. Iovu, Composites, Part B, 2015, 75, 226–234 CrossRef CAS.
- N. Bosq, N. Guigo, J. Persello and N. Sbirrazzuoli, Phys. Chem. Chem. Phys., 2014, 16, 7830–7840 RSC.
- C. Park, J. Jung and G. J. Yun, Composites, Part B, 2019, 161, 639–650 CrossRef CAS.
- S. Kopsidas, V. G. Rocha, A. C. Taylor, S. Eslava, E. S. Gutierrez, A. J. Kinloch, G. B. Olowojoba and C. Mattevi, J. Mater. Sci., 2017, 52, 7323–7344 CrossRef PubMed.
- F. E. Swallow, J. Appl. Polym. Sci., 2002, 84, 2533–2540 CrossRef CAS.
- C. Taplan, M. Guerre, J. M. Winne and F. E. Du Prez, Mater. Horiz., 2020, 7, 104–110 RSC.
- M. Castelaín, P. S. Shuttleworth, C. Marco, G. Ellis and H. J. Salavagione, Phys. Chem. Chem. Phys., 2013, 15, 16806–16811 RSC.
Footnote |
† Electronic supplementary information (ESI) available. See DOI: 10.1039/d0na00282h |
|
This journal is © The Royal Society of Chemistry 2020 |