DOI:
10.1039/D1MA00841B
(Review Article)
Mater. Adv., 2022,
3, 3365-3388
Tannin as a renewable raw material for adhesive applications: a review
Received
12th September 2021
, Accepted 14th March 2022
First published on 6th April 2022
Abstract
Considering the limits of petrochemical availability and their toxicity, there has been rapid development and innovation in the field of alternatives for petrochemical adhesives. The carcinogenicity of formaldehyde has reduced the demand for formaldehyde-based wood adhesives, which has resulted in the development of adhesives based on renewable resources. This review article summarizes various works published on bio-derived adhesives focusing on tannin. Increasingly acknowledged renewability, sustainability, lower cost, and chemical modification opportunities make tannin a credible precursor for developing competent bio-based adhesives. Henceforth, the chemistry of tannin, its usefulness, possible chemical modification, and compatibility in an attempt to synthesize bio-based adhesives is also being highlighted and compared with its hydrocarbon-derived counterparts. In addition to this, categories of tannin, and techniques available for their extraction along with their pluses and misuses, have also been explained. Moreover, this review includes a detailed discussion on tannin as a raw material for preparing epoxy, polyurethane, polyethylenimine, and furfuryl-based adhesives. It is expected that by exploring further possibilities of chemical modification, tannin can be a potential candidate that can compete with the petrochemical-based adhesives, thereby paving the way for the advancement of bio-adhesives.
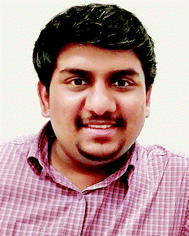
Pritam V. Dhawale
| Pritam V. Dhawale is currently working as a Research Associate in the Coatings and Polymer division of CRODA India Company Pvt. Ltd, Mumbai. He received his master's degree (MTech) in Surface Coating Technology from the Institute of Chemical Technology (ICT), Mumbai, after completing his BS degree (BTech) in Chemical Engineering from Laxminarayan Institute of Technology, Nagpur, India. Before joining as a Research Associate, he was a Research Intern at CRODA for one year, where he worked on developing thermoregulating coatings, modifying acrylic-based latexes, and optimization of TiO2 in decorative coatings. Since 2019, he has been a visiting student at Prasanth's research group, Materials Science and NanoEngneering Lab, at the Department of Polymer Science and Rubber Technology, Cochin University of Science and Technology (CUSAT), Cochin. He has published a couple of research articles and reviews on adhesives and coatings in international peer reviewed journal publications. He has presented his research findings at International/national symposiums and workshops as well as participated in industry defined problem solving competitions. His area of interest includes green chemistry, passive thermal energy storage materials, wood adhesives, biopolymers, microencapsulation, and self-healing coatings. |
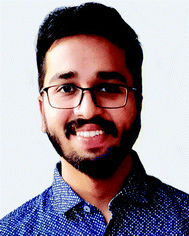
S. K. Vineeth
| Vineeth S. K. is currently a co-tutelle PhD student at Queensland University, Australia and Indian Institute of Technology (IIT-D), New Delhi. He completed his MS degree (MTech) in Polymer Engineering and Technology from the Department of Polymer and Surface Engineering, Institute of Chemical Technology (ICT), Mumbai, India after completing his BS degree (BTech) in Polymer Science and Engineering from, Department of Polymer Science and Rubber Technology, Cochin University of Science and Technology (CUSAT), Cochin. He has done research internships in polymer and rubber based industries including at the Rubber research institute of India, Kerala, Pidilite Industries, Mumbai etc. From 2019, he was the visiting student at Prasanth's research group, Materials Science and NanoEngneering Lab, at Department of Polymer Science and Rubber Technology, Cochin University of Science and Technology (CUSAT), Cochin. He has expertise in developing organic solvent free water-based and bio-based adhesives. He developed tannin blended polyvinyl alcohol (PVA) adhesives and polyvinyl acetate (PVAc) emulsion based adhesives and has a couple of full length research/review articles on adhesives in peer reviewed international journals and publishers. Also he has a bunch of book chapters with international publishers to his credit. His areas of interest include organo-electronics, polymer electrolytes for energy storage devices, polymer blends and alloys, adhesives, coatings, nanotechnology, and modification of polymers. Apart from this he is a passionate traveller, loves cooking and is a cinephile. |
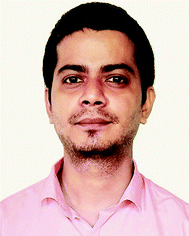
Ravindra V. Gadhave
| Dr Ravindra V. Gadhave, is currently working as R&D Manager in the Consume product Maintenance Department (CP-MNT) of Pidilite Industries Limited, Mumbai, India. He completed his bachelor's degree in technology (BTech) in Surface Coating Technology from the Institute of Chemical Technology (ICT), Mumbai. After receiving his B.Tech degree, he joined as a direct PhD scholar at ICT, Mumbai and received his Doctoral degree in technology in the field of Adhesives and Surface Coating Technology in 2020. During his PhD, he worked on chemical modification of biopolymer like starch, lignin, cellulose, and tannin for adhesive application. He joined Pidilite Industries Limited in 2011 as a Graduate Engineer (GE) and worked on alkyd-based wood finishes, unsaturated polyester putty for automotive applications, polyvinyl acetate-based wood adhesives, moisture curing polyurethane adhesives, silane terminated pre-polymer based adhesives, sealants, and coatings. He is the recipient of many talent awards including Promising Young Talent Award-2012 and Innovation Award-2017 for Pidilite R&D. He has presented his research findings at many International/national level Symposiums and workshops. In 2018, he received the ‘PU Tech Innovation Award’ for his poster at the IPUA Exhibition. He has several full length research publications and review articles in peer reviewed international journals to his credit. His areas of interest include structural adhesives, sealants, coatings, nanomaterials, biopolymers, tannin and lignin based adhesives. |
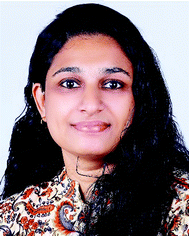
Jabeen Fatima M. J.
| Dr Jabeen Fatima M. J. is a senior research scientist at the Materials Science and NanoEngineering Lab (MSNE Lab), Department of Polymer Science and Rubber Technology (PSRT), Cochin University of Science and Technology (CUSAT), Kerala, India. Before joining the MSNE Lab, she worked as an Assistant Professor at the Department of Nanoscience and Technology, University of Calicut, India. Dr Fatima received her PhD in Nanoscience and Technology from University of Calicut, India, in 2016, with the support of a prestigious National Fellowship CSIR JRF/SRF from the Council of Scientific and Industrial Research (CSIR), under the Ministry of Science and Technology, Government of India. Her research area was focused on the synthesis of nanostructures for photoelectrodes for photovoltaic applications, energy storage devices, photoelectrochemical water splitting, catalysis etc. She received her MS degree in Applied Chemistry (University First Rank) from Mahatma Gandhi University (MGU), Kottayam, India after receiving her BS degree in Chemistry from the University of Calicut, Kerala, India. Dr Fatima has received many prestigious fellowships, including Junior/Senior Research fellowships (JRF/SRF) from the Council for Scientific and Industrial Research, Department of Science and Technology, Ministry of India, a post-doctoral/research scientist fellowship from Kerala State Council for Science, Technology and Environment (KSCSTE), an InSc Research Excellence award, Kairali Research Excellence award from Government of Kerala etc. Dr Fatima has published many full-length research articles in peer-reviewed international journals, books as well as chapters in books with international publishers. Dr Fatima is the book editor for Springer Nature, Elsevier, Taylor and Francis, CRC Press etc. She acts as a reviewer for many STM journals published by Wiley International, Elsevier, Springer Nature etc. She is editor of 8 books and has contributed about 50 book chapters to different renowned international publishers like Elsevier, Springer, Taylor and Francis, CRC Press, etc. Dr Fatima's current research areas of interest include the development of flexible and free-standing electrodes for printable and stretchable energy storage solutions and the development of novel nanostructured materials, ternary composite electrodes and electrolytes for sustainable energy applications, such as supercapacitors, fuel cells and lithium-ion batteries. |
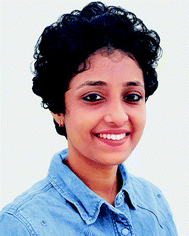
Mrudul Vijay Supekar
| Mrudul V. Supekar graduated with First Rank in her MS degree (MSc) in Applied Chemistry from Mahatma Gandhi University, Kerala, 2015, and was the recipient of an Aspire fellowship (2014–15), Ministry of Higher Education, Govt. of Kerala. Currently Mrudul Supekar is a joint full-time research scholar at Department of Polymer Science and Rubber Technology and Department of Applied Chemistry, Cochin University of Science and Technology (CUSAT), India. After her MS degree, she moved to CSIR-National Chemical Laboratory (NCL), Pune and worked as a researcher for three years. Her research was focused on target oriented synthesis of designed molecules with potential biomedical applications. After three years of stint appointment in NCL, she moved to Kerala in 2019 and joined as Senior Quality Control Chemist in a renowned Ltd. Company in Kerala. The strong will to continue with research was triggered in her and she joined to Prasanth's research group Materials science and NanoEngineering Lab as a full time research scholar in fall 2019. Her general research interests lie in lab scale design, synthesis and characterization of organic compounds, methodology development, medicinal Chemistry especially in CNS activity and its modification study to minimize its side effects. She is the recipient of many prestigious awards including the Outstanding Student Achiever Award, University First rank for her MS Degree (2015) and Department Admission Test (DAT-2020) in CUSAT etc. Supekar have a couple of peer reviewed full length research articles in the international SCI journals and book chapters with international academic publishers to her credit. Her research is presently focused on polymer synthesis, their hybrid composites in the micro to nanoscale, and thermally insulating elastomeric materials for high temperature applications. Her area of interest is on polymer nanocomposites, the chemistry and technology of elastomeric materials, and environment friendly polymer composites and their applications. Apart from science and technology, Supekar is a fashion designer and doing modelling. |
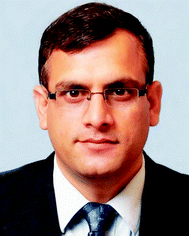
Vijay Kumar Thakur
| Vijay Kumar Thakur is currently a Professor and Head of the Biorefining and Advanced Materials Research Centre at SRUC, Edinburgh, UK. He also holds an Adjunct Professor position in the Research School of Polymeric Materials, Jiangsu University, China, Visiting Professor at Shiv Nadar University, India, and a Visitor at Cranfield University, the UK. Prior to commencing in the SRUC, Edinburgh, he has held faculty positions at the School of Aerospace, Transport and Manufacturing at Cranfield University, in the School of Mechanical and Materials Engineering at Washington State University, USA and in Temasek Laboratories at Nanyang Technological University, Singapore. Prof. Thakur did his post-doctoral study in Materials Science & Engineering at Iowa State University, USA. His research activities span the disciplines of Biorefining, Chemistry, Chemical Engineering, Manufacturing, Materials Science, and Nanotechnology, as well as all aspects of Sustainable and Advanced Materials. He has been a PI/Co-PI on several projects sponsored by BAE Systems, EPSRC, Royal Academy of Engineering, UKIERI, Innovate the UK etc. He has published over 350 SCI journal articles, 2 patents, 52 books, and 40 book chapters in areas concerning polymers, nanotechnology, and materials science (Hi-82, citations > 21,000). He sits on the editorial board of 20+ SCI journals as EiC/Associate Editor/ Editorial Advisory Board member. |
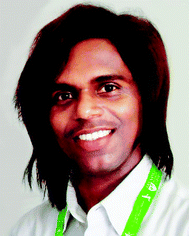
Prasanth Raghavan
| Prof. (Dr) Prasanth Raghavan is a Professor at the Department of Polymer Science and Rubber Technology, Cochin University of Science and Technology (CUSAT), Kerala, India, and Visiting Professor at the Department of Materials Engineering and Convergence Technology, Gyeongsang National University, Republic of Korea. Prof. Prasanth is also holding the Associate/Adjunct Faculty position at the Inter-University Centre for Nanomaterials and Devices (IUCND), CUSAT. He received his PhD in Engineering under the guidance of Prof. Jou-Hyeon Ahn, from the Department of Chemical and Biological Engineering, Geyongsang National University, Republic of Korea, in 2009, supported by a prestigious Brain Korea (BK21) Fellowship. Prof. Prasanth completed his B. Tech and M. Tech from CUSAT. After a couple of years of attachment as a Project Scientist at the Indian Institute of Technology (IIT-D), New Delhi, he moved to the Republic of Korea for his PhD studies in 2007. His PhD research was focused on the fabrication and investigation of nanoscale fibrous electrolytes for high-performance energy storage devices. He completed his Engineering doctoral degree in less than three years, still a record in the Republic of Korea. After his PhD, Prof. Prasanth joined at the Nanyang Technological University (NTU), Singapore, as a Research Scientist, in collaboration with the Energy Research Institute at NTU (ERI@N) and TUM CREATE, a joint electromobility research centre between Germany's Technische Universität München (TUM) and NTU, where he was working with Prof. (Dr) Rachid Yazami, who successfully introduced graphitic carbon as an anode for commercial lithium-ion batteries, and received the Draper Prize, along with the Nobel laureates, Prof. (Dr) John B. Goodenough and Prof. (Dr) Akira Yoshino. After four years in Singapore, Prof. Prasanth moved to Rice University, USA as Research Scientist, where he worked with Prof. (Dr) Pulickal M Ajayan, the co-inventor of carbon nanotubes, and was fortunate to work with 2019 Chemistry Nobel Prize laureate, Prof. (Dr) John B. Goodenough. Prof. Prasanth was selected for a Brain Korea Fellowship (2007), SAGE Research Foundation Fellowship, Brazil (2009), Estonian Science Foundation Fellowship, European Science Foundation Fellowship (2010), Faculty Recharge, University Grants Commission (UGC), Ministry of Higher Education, India (2015), etc. Prof. Prasanth has received many international awards, including Young Scientist award, Korean Electrochemical Society (2009), and was selected for the Bharat Vikas Yuva Ratna Award (2016) and recently awarded with Education Excellence Award (2021), Dr S Radha krishnan Bharat Shiksha National Award (2021) etc. He has developed many products such as a high-performance breaking parachute, flex wheels for space shuttles, high-performance lithium-ion batteries for leading companies for portable electronic device and electric automobiles etc. Prof. Prasanth has a general research interest in polymer synthesis and processing, nanomaterials, green/nanocomposites, and electrospinning. His current research focuses on nanoscale materials and polymer composites for printed and lightweight charge storage solutions, including high-temperature supercapacitors and batteries. Prof. Prasanth has published many research papers in high-impact factor journals, and a number of books/book chapters, and has more than 7000 citation and h-index of 50 plus. He sits on the editorial board of SCI journals as an Editor or Editorial Advisory Board member of SCI international journals including Journal of Materials Research, Nanofabrication, Biomaterials and Polymers Horizon and Frontiers of Materials etc. Prof. Prasanth is a book series editor for Springer Nature, Elsevier, Taylor and Francis, CRC Press etc. Apart from science and technology, Prof. Prasanth is a poet, activist and a columnist in online portals and printed media. |
Introduction
The proliferation of the human population has led to developments in the infrastructure sector resulting in demand for wood-based products such as fiberboards, particleboards, wood panels, oriented strand boards, plywood, laminates, etc. The usage of wood products is inevitable in the construction sector. A variety of wood products are being used in both indoor and outdoor applications. Furthermore, the furniture manufacturing industries are also massive consumers of wood products. To ensure the strength and better performance of various wood products, the joining of wood samples plays a significant role. Wood adhesives provide durable and strong bonds between different wooden parts and offer thermal and moisture resistance.1 Conventional wood adhesives are formaldehyde-based systems functioning as binders. Major adhesives based on formaldehyde include phenol–formaldehyde (PF), urea–formaldehyde (UF), and melamine–formaldehyde (MF).1 Formaldehyde-based adhesives were mostly available separately as resins and hardeners in a powder form.2 In addition, the durability, robust bond formation, moisture resistance, low cost, and gap-filling property of formaldehyde-based adhesives revolutionized the wood adhesive industries. However, health hazards associated with formaldehyde and its identification as a potential carcinogen with negative environmental impacts led to the exploration of environment-friendly alternative wood adhesives.3,4 Among different alternatives, water-based adhesives are used to consolidate wood (or wood panels or wood veneers),5–7 where water acts as a solvent, thereby reducing the dependency on harmful and toxic organic solvents. To further mitigate the usage of petrochemical-based adhesives, bio-materials incorporating wood adhesives have gained significant attention in recent years. The world's most prevalent biopolymers have been explored for their use in wood adhesives, including cellulose8,9 derived as a residue or in several other forms such as carboxymethyl cellulose (CMC),10,11 microfibrilated cellulose,12 chemically modified nanocellulose,13 cellulose nanofibrils,14 or microcrystalline cellulose;15 starch16–18 or blends prepared in various ratios using starch and co-ingredients such as polyvinyl alcohol,19,20 silica nanoparticles,21 silane coupling agent,22 or sodium dodecyl sulphate;23 lignin24,25 or tailor-made resins like lignin-epoxy from biomass26 and lignin–polyurethane27 in an attempt to give an alternative to formaldehyde; similarly, soy proteins28 or their chemical modifications29 for enhanced end properties and thus performance. With increasingly acknowledged credibility of these naturally available polymers in terms of abundant supply, cost, and ease of functionalization,30,31 lately the research focus has shifted from finding suitable raw-materials to developing competent bio-derived adhesives compared to their hydrocarbon-based counterparts.32,33 Therefore, with the objective of developing next-generation sustainable adhesives, while hunting for similar suitable materials, which are capable of meeting today's (environmental and health) regulations and exceeding (or meeting) the performance bar set by their hydrocarbon-derived counterparts is critical. With that in mind, tannin is one such material with similar potential and has been thoroughly investigated34,35 especially to develop sustainable and competent bio-based wood adhesives.
Tannin
As its generic name, tannin is a highly water-soluble substance, astringent in its aqueous solution, and has the feature of tanning leather. Chemically, tannin is a conjunction of complex organic compounds, with a phenolic structure.36 Primarily tannin can be classified into hydrolyzable and condensed tannin. Fig. 1 shows the basic classification of tannins. Hydrolyzable tannin results in a mixture of gallic acid, ellagic acid, and digallic acid on heating with dilute acid. These consist of ester linkages formed between benzoic acid and sugars. Also, they possess lower nucleophilicity with lower phenolic content.
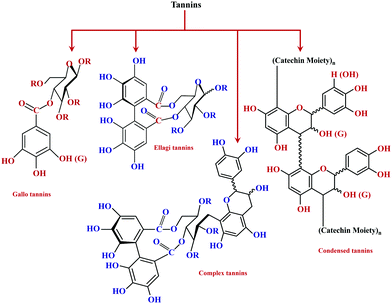 |
| Fig. 1 Types of tannin (hydrolyzable and condensed tannin) and their chemical structure. | |
Whereas the condensed tannin upon polymerization results in water-insoluble phlobaphene,37 extracts of chestnut, myrobolans (Terminalia and Phyllantus), and dividivi (Caesalpinacoraria) contain hydrolyzable tannin. On the other side, condensed tannin is present in decent concentrations in the bark and wood of various trees.38 The presence of free hydroxyl groups enables the ease of accessibility as well as the feasibility for modification, hence facilitating chemical modification on tannin.39 Chemical modifications engineer tannin as a potential candidate for the functional adhesive category.40
The introduction of tannin as a renewable material has opened up new avenues in various applications published in several reviews and book chapters from the early 1980s.41–44 Tannin is widely reported as a precursor for wood adhesives and waste-water treatment, bio-sorbent, and green raw material for the food and pharmaceutical industries. In addition its antioxidant and antimicrobial properties were also revealed in various reports.45–48 Furthermore, bio-foams derived from tannin have also gained much interest.49 Koopmann and colleagues50 reviewed the interaction of tannin with ceramic and polymeric materials, extending their applications. Considering the adhesion properties, major developments were reported from the second half of 2010.51–57 The most recent detailed review on tannin was published in 2021, which was focused on the developments of tannin and lignin-based polyurethane resins and their applications.54 This study summarized various classes of polyurethanes and the importance of non-isocyanate polyurethane resins in multiple applications with a detailed synthesis mechanism.54 Although multiple reviews41–49 are available on tannin as an adhesive, comprehensive reviews discussing the structure–property relationship, benefits that tannin-derived adhesives are capable of offering beyond its renewability, or molecular structures, in particular, having the potential to provide new functionalities with a view on physico-chemical analysis remain scant.
Moreover, recent advancements in tannin extraction and purification protocols, which are catalyzing tannin's industrial viability, have not been reviewed yet. Also, an exclusive review on tannin with detailed discussion on various chemical modifications of tannin and tannin blended adhesives still remains lacking. As tannin-based adhesives are free from formaldehyde emission, and also tannin forms are employed as a precursor for isocyanate-free polyurethanes and bio-derived epoxy resins, and as a source of natural phenolics, updating such a material to industrial level applications is unequivocally important. Being an updated exclusive review on tannin for adhesive applications, this manuscript is addressing the aforementioned gaps. In particular, as the advancement in environmentally benign and bio-derived adhesives has been booming in the past few decades, the same is being reflected in tannin-based adhesives as well.
Hence with this aim, this review paper is an overview of various works reported on tannin as a potential candidate for developing bio-derived wood adhesives. The article sheds light on multiple related topics, including the methodologies reported for extracting tannin and its classification, followed by a detailed discussion of their pluses and minuses. Increasingly acknowledged renewability, sustainability, lower cost, and chemical modification opportunities make tannin a credible precursor for developing competent bio-based adhesives. Henceforth, the chemistry of tannin, its usefulness, possible chemical modification, and compatibility in an attempt to synthesize bio-based adhesive is also being highlighted and compared with their hydrocarbon-derived counterparts. Moreover, the paper includes detailed studies on the binding properties of tannin and its function as a reactive polymer with other binders such as epoxy, polyurethane, polyethylenimine, and furfuryl-alcohol, in an effort to develop bio-derived adhesive systems. This work, therefore, aims to provide a complete database on tannin, showcasing the potential applications as a reactive bio-derived material for adhesive applications.
Chemistry of tannin
Among hydrolyzable and condensing units, condensed tannin shows reduction in the formaldehyde emission level, due to its higher reactivity with formaldehyde and the presence of catechol groups. Hence, condensed tannin serves as one of the most explored wood adhesive precursors in the global community with an increased market value, compared to hydrolysable tannin.55 Furthermore, the presence of flavonoid units in the condensed tannin helps in catalysing the polymerization reaction. The flavonoid groups are affiliated with their precursors, for example, flavanes-3,4-diols, and flavanes-3-ol.58,59 Every flavonoid unit consists of two categories of phenolic nuclei, namely, the 'I' ring and 'II' ring, as shown in Fig. 2. The ‘I’ ring of condensed tannin comprises phloroglucinol and resorcinol, whereas the 'II' ring incorporates catechol and pyrogallol. As tannin is a conjunction of complex organic compounds, the 'I' rings of different tannins hold different chemical structures, with those extracted from sources like wattle/mimosa, douglas-fir, quebracho, and spruce incorporating resorcinol, while that from pine contains phloroglucinol.60
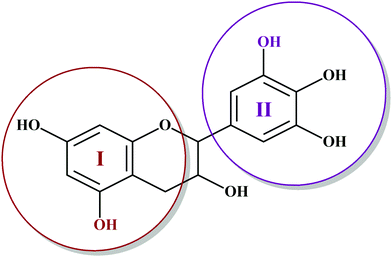 |
| Fig. 2 Condensed tannin structure comprising the I-ring (includes resorcinol and phloroglucinol) and II-ring (includes pyrogallol and catechol). | |
According to the resorcinol ‘I’ ring and pyrogallol II-ring, the main polyphenolic pattern is portrayed through flavonoid analogues (Unit-A from Fig. 3). The structure of this entity accounts for about 70% of tannin. The B-unit in condensed tannin accounts for 25%, with a resorcinol ‘I’ ring and catechol ‘II’ ring (Unit-B from Fig. 3). The remaining 5% is a combination of phloroglucinol–pyrogallol, and phloroglucinol–catechol flavonoids represented in the ‘C’ and ‘D’ units of Fig. 3.61 These four units/models constitute an average of 65 to 80% of mimosa bark extract. The rest of the constituents are non-tannins, hydrocolloid gums, simple carbohydrates, and nitrogen-based compounds like amino acids and imino acids. Simultaneously, pectin and gums are the crucial constituents of tannin and have a notable effect on the extract's viscosity. They are found to be effective even with concentrations of as low as 4 to 6%.62 These non-tannin constituents are found to be responsible for weakening wood products and may also lead to decreased moisture resistance.63 Pine-based tannin primarily confers two models: the first is unit-E, i.e., phloroglucinol ‘I’ ring and catechol ‘II’ ring structures, and the other one is unit ‘F’, i.e., phloroglucinol I-ring and phenol II-ring, represented in Fig. 3.
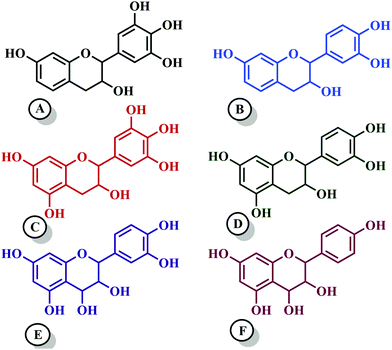 |
| Fig. 3 The condensed tannin units, where the ‘A’ unit contains 70% tannin and comprises a resorcinol ‘I’ ring and pyrogallol ‘II’ ring; the ‘B’ unit includes 25% tannin with a resorcinol ‘I’ ring and catechol ‘II’ ring; the remaining 5% is a mixture of phloroglucinol–pyrogallol (shown by ‘C’ unit) and phloroglucinol–catechol flavonoids (indicated by ‘D’ unit), and units ‘E’ and ‘F’ are non-tannin compounds. | |
Extraction of tannin
Tannins are phenolic compounds with a substantial and natural abundance with complex aromatic and heterocyclic ring structures.51 A wide variety of tannins (approximately 8000 variants) have been explored so far. The majority of these are found in plant cells in bound or free forms. It is possible to distinguish terrestrial plant tannins into four types, namely ellagitannins, gallotannins, complex tannin, and proanthocyanidins (condensed tannin).51 Plant-derived tannins include oligomers or phloroglucinol polymers, which have been identified as 'phlorotannins.' The percentage of tannin extracted principally relies on the plant species, its habitat, harvest time, and extraction techniques.64 Owing to their eco-friendliness and vast applications, tannins have recently gained considerable interest. In the current scenario, tannins are widely explored in various sectors like food, ink, adhesives, beverages, medicine processing, pigments, tanning industries, water purification, plastic resins, and surface coatings.51 These compounds have also been widely explored as precipitating agents or complexing agents where the performance of the same is governed based on its concentration.65 However, owing to its heterogeneous nature, the extraction is still the principal bottleneck for their recovery. Therefore, effective utilization and recovery of tannin are important for exploring the uniqueness of the material for various applications. Hence, considering the importance of tannin extraction and processing techniques, a detailed discussion based on work carried out over the last 20 years is summarized. An overview of various extraction methods of tannin is shown in Fig. 4.
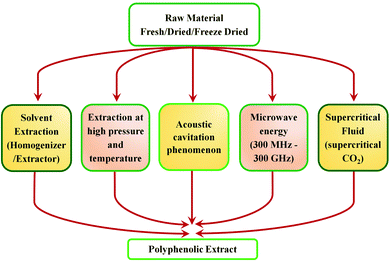 |
| Fig. 4 Schematic illustration of the different extraction methods. The raw material is subjected to various extraction methods to obtain a polyphenolic extract as the product: solvent extraction (solid–liquid extraction-SLE), extraction at high temperature and pressure (pressurized liquid extraction-PLE), acoustic cavitation phenomenon (ultrasonic-assisted extraction-UAE), microwave energy (microwave assisted extraction-MAE), and supercritical fluid (super critical extraction-SCE). | |
Advanced extraction methods of tannin
Conventionally, tannins are extracted from various sources using mechanical processes such as milling and grinding. Tannin sources such as barks, wood chips, saw dust, leaves, shoots, etc., are typically ground to a particle size ranging from 0.5 μm to 0.5–5 mm.37 Extraction proceeds faster with smaller particles of the source material. The yield of tannin varies from 6–43%, depending on the source, method of extraction, type of solvent used, time and temperature of the extraction process.51 Water or aqueous solutions of sodium salts, such as sodium carbonate/bicarbonate, sodium sulphite/bisulphite or aqueous NaOH solution are the widely reported solvents for the extraction.51 Moreover, various solvent mixtures are also used for the extraction and purification of tannin. Solvent mixtures such as acetone/water, acetone/ethanol, methanol/water, or organic solvents such as N,N-dimethylammonium, N′,N′-dimethylcarbamate etc., under stirring and refluxing have been reported from early times.37 Advancement in technology has reflected its impact on the extraction process as well, hence newer extraction methods were explored. This section aims to explain the evolution of the current methods for tannin extraction. A comprehensive analysis has been carried out between various techniques. Each method's key strengths and drawbacks are discussed in detail. This provides a cleaner and more productive development of tannins.
Solid–liquid extraction (SLE)
In the solid–liquid extraction (SLE) method, tannin extraction is solely based on the interaction between the raw material and a solvent. The solvent penetrates the feedstock's cell wall, leading to the dissolution of the tannin, followed by separation.66 SLE is one of the most straightforward and traditional techniques used to isolate tannins. Several forms of solvents, such as aqueous solutions, organic solvents, and ionic liquids, are widely explored. Extraction processes utilizing aqueous and organic solvents, and Soxhlet apparatus are widely used.67,68 However, other methods, such as infusion or maceration, are also used and documented in the literature.68 Water-based extraction can be carried out under refluxing or by simple maceration. It is typically performed on wood bark on an industrial scale by percolation or open diffusion.69 Sepperer and colleagues performed a purification of industrial tannin, employing the SLE method.69 Investigators used black wattle tannin extract purification followed by vacuum filtration, recovery of the extract, drying in a rotary evaporator, and pulverization. Mass spectroscopy analysis and gel permeation chromatography (GPC) showed that the extract is a complex polyphenolic compound with high molecular weight, insoluble compounds. It contains flavonoids, proteins, phenolic substituents, and aliphatic chains. Analysis showed the existence of chemical bonds between polyphenolic molecules and carbohydrates. Moreover, the sample contains constituents which are insoluble in acetone, which have antioxidant properties. Extraction involving ionic liquids is another option focused on substituting these modern liquids for conventional solvents, which are considered to have exceptional properties such as high thermal stability, negligible vapor pressure, and dissolution of a wide variety of plant compounds.70
To conclude, it can be observed that simplicity, productivity, and reduced cost are the key benefits of this system. In hot water extraction, it is also necessary to highlight the method that is capable of commercialization at the industrial level, particularly wood bark extraction.71,72 Major disadvantages of this process are longer extraction time ranging from hours to days, as well as the surplus usage of solvents. Utilizing ionic liquids (ILs), which exhibit unique properties favorable for the extraction, could mitigate these disadvantages.73 Nonetheless, the higher cost of these solvents coupled with the difficulty of recovering the ILs continues to impede their use.
Supercritical fluid extraction (SCE)
Supercritical fluid extraction (SCE) is based on a critical point, described by a maximum pressure and temperature at which the pristine material may exist in a liquid–vapor equilibrium.74 Above this point, the properties of the fluid are exchanged between the liquid as well as the gaseous state, such as the standard weight of liquids including the gas-penetration power.75 Carbon dioxide (CO2) is the most employed solvent in the majority of SCE because of its favorable characteristics such as lower critical point (temperature of 31 °C and a pressure of 7.28 MPa), non-corrosive nature, non-flammability, non-toxicity, and ease of availability.76,77 For the favorable extraction of tannins, the addition of polar co-solvents (e.g., ethanol, methanol, or aqueous mixtures) enhances CO2 solvation to tannins and thereby augments the extraction rates.78,79
A major advantage of the SCE extraction method includes the utilization of non-toxic solvents like CO2 that can be easily removed by generating an oxygen-free environment and preventing further oxidation reactions. On the other hand, the method requires high pressure for extraction (the major drawback), creating a huge investment cost.80 Another major hitch of this method is the non-polar nature of CO2, which considerably reduces tannin extraction owing to the polar nature of the components; hence the efficient extraction of tannin using SCE requires the incorporation of co-solvents like methanol, ethanol, acetone, or water.
Pressurized water extraction (PLE)
The pressurized water extraction (PLE) method requires the usage of aqueous solvents at elevated temperatures and pressure, typically under subcritical conditions. The temperature, as well as pressure, ranges between its ambient boiling point (100 °C, 0.1 MPa) and its critical point (374 °C, 22.1 MPa).37 At the subcritical point, water retains its liquid state but significantly decreases the polarity, surface tension, viscosity, decoupling constant, etc.81 Reduction of these properties increases the transfer of mass from the feedstock matrix of the tannins.82 Moreover, the ability to remove multiple compounds from the feedstock is enhanced under these conditions.83 The key difference of PLE with conventional hot-water solid–liquid extraction is the usage of pressurised water at higher temperature.
Principal benefits of PLE include the decreased extraction time with lower consumption of solvents, and the absence of harmful organic solvents. Another benefit is that tannins of varying polarities can be selectively isolated by adjusting the pressure, co-solvent, or temperature. Apart from these advantages, the key drawbacks are the requirement of elevated temperatures and pressures (reduced selectivity of separation and probable analytes degradation). Moreover, the PLE set up includes the usage of costly equipment (pressure vessel, system controller, solvent transporting pump, and a collection device for the extract are required).
Microwave-assisted extraction (MAE)
The microwave-assisted extraction (MAE) approach is based on the combination of the standard tannin extraction using solvents and accelerated microwave heating method.84 In some instances, extraction is enhanced by the direct contact between the solvent and sample with electromagnetic radiation, which can quickly heat the material (depending on their dielectric characteristics). Another approach is to heat one of the constituents, which expands the pores in the feedstock, thereby facilitating the penetration of the solvent and accelerating the solubility of tannin.84 Hence, in both the cases, isolation of tannins from the feedstock cell wall proceeds faster. The principal benefits of the MAE technique include the reduced extraction duration, and lower consumption of solvent, compared to conventional solid–liquid separation. Irradiating microwaves provides a further benefit, which reduces the phenomena of mass transfer.85 The key drawbacks are the high cost of equipment (particularly at a larger scale) and the risk of feedstock and/or tannin degradation, as it has a large number of thermally sensitive hydroxyl groups.86
Ultrasound-assisted extraction (UAE)
The ultrasound-assisted extraction technique is utilized for the extraction of tannins based on the creation, development, and disintegration of the micro-bubbles within the liquid process as a result of ultrasonic vibration.87 The blisters are pumped into the plant matrix by ultrasonic vibrations above a frequency of 20 kHz. These vibrations induce a crack in the cell wall of tissues, thereby increasing the solvent penetration into the matrix, hence tannin is isolated from the cell walls.88 The key advantages of this technique include the fast extraction time, easiness of execution as well as low cost.87,88 On the other hand, the major disadvantages are focused on the reduced uniformity in the power of ultrasound throughout the medium (the maximum intensity peak is observed in the region of direct irradiation whereas a decrease intensity is evident on the edges of the container as the distance from the source increases).85 The power of the sonication also decreases with time, which also affects the product concentration.85
Microwave-assisted and ultrasound-assisted extraction methods of tannin are safer and greener with better efficiency, hence further developments in such techniques can accelerate the efficient extraction of tannin. Coupling of these two powerful radiation techniques (ultrasonic and microwave) offers an efficient approach to extract bioactive compounds. The newer method called ultrasound/microwave-assisted extraction (UMAE) further reduces the extraction time and solvent consumption, and offers higher extraction yields than conventional methods51 or MAE84 or UAE.86Fig. 5 depicts the schematic illustration of the UMAE extraction setup. Xiao and colleagues compared the yields of flavonoids from Spatholobus suberectus obtained by UMAE with MAE, UAE, Soxhlet and heated reflux extraction methods under optimized conditions and showed the highest yield obtained for UMAE.89 The extraction time was short at 7.5 min and the solvent to solid ratio was 20 mL g−1 for UMAE, while for other extractions, the optimum yields depended on a higher solvent-sample ratio (40–120 mL g−1) and longer extraction time (30–3600 min) (Fig. 6).89
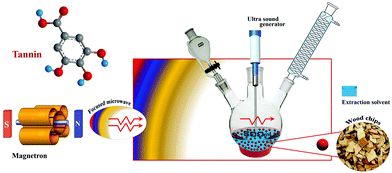 |
| Fig. 5 Schematic illustration of the experimental setup for ultrasound/microwave-assisted extraction (UMAE) of tannin. | |
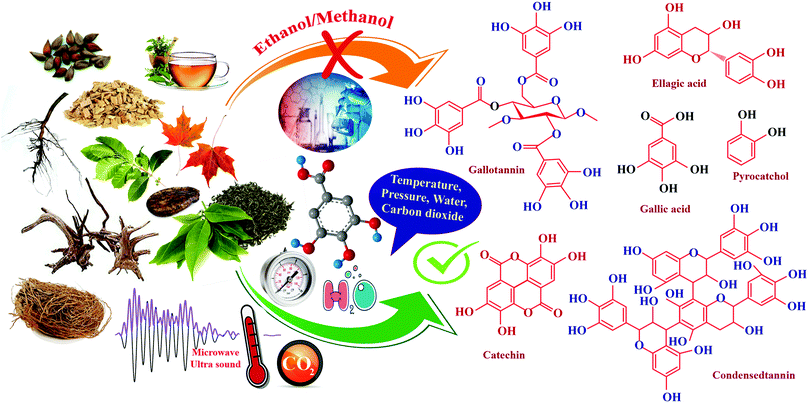 |
| Fig. 6 Schematic illustration of the extraction of tannin from various renewable resources by different methods leading to the extraction of the major chemical components of tannin such as ellagic acid, gallic acid, pyrocatechol, catechin, etc. | |
Tannin as a renewable raw material for wood adhesive
In the wood adhesive sector, formaldehyde-based resins such as urea–formaldehyde, phenol–formaldehyde, melamine–formaldehyde, and the resins from co-polycondensation, which include phenol–urea–formaldehyde and melamine–urea–formaldehyde, are some of the most explored systems. Although the above-mentioned synthetic resins offer excellent weatherability and mechanical strength, their raw materials are petroleum-derived, thereby raising concerns regarding the environment and economy. Moreover, products from these raw materials emit formaldehyde, a volatile and carcinogenic material.90 Equating the growing concerns over volatile organic solvents and the limited availability of fossil fuels, approaches to develop alternatives have received much appreciation.91
As tannin is unique in its composition and abundantly available, the development of value-added products offers a sustainable alternative. It is emerging as a green substitute for the wood adhesives, produced from petroleum-based resources, specifically phenol and resorcinol.92,93 There have been a number of works reported on tannin-based adhesives for particleboard, plywood, and laminated products from the group of Pizzi.35,94–96 Tannin can be classified as hydrolyzable tannin, and condensed tannin.
Hydrolyzable tannin has limited applications in the wood industry because of its low reactivity with formaldehyde, which can be ascribed to its simple phenolic structure, as shown in Fig. 1. Apart from the phenolic structures of tannin, commercial extracts consist of sugars and gums hence making the tannin extract impure.51
Sugars and gums are unitedly known as non-tannin components, usually 20–30% in black wattle and hardwood-based tannin, whereas pine obtained tannin has non-tannin components as high as 40–50%.97 As non-tannin components do not take part in the synthesis of the resin adhesive, they reduce the actual solid content, therefore hampering the final properties of the resin.98 Non-tannin constituents are responsible for the weaker strength of the resin and accountable for the poor moisture resistance of the adhesives. In addition to that, an un-modified tannin-based adhesive is unfit for wood products having high requirements. Table 1 summarises the limitations and respective causes of tannin as an adhesive material. In the current scenario, these disadvantages are the most significant obstacle limiting the productive and global development of tannin as a bio-derived alternative. Hence to unveil the limitations and to reveal the ease of resin formation, a better insight into structure–property relations of tannin needs utmost interest. As tannin has complex phenolic groups, exhibiting excellent physico-chemical properties, with easiness-to-use compared to conventional phenolic resin, it can function as a potential candidate for greener adhesives.99 Furthermore, the chemical composition of tannin allows possibilities for further chemical modification.100
Table 1 Limitations of tannin-adhesive resin and their respective causes
Limitations of tannin-adhesive resin |
Causes |
Poor strength of resin and poor water resistance |
Presence of non-tannin components (like sugars and gums). |
Highly viscous |
High molecular weight of tannin extract. |
|
Presence of hydrogen bonding and electrostatic interaction between gum–gum, tannin–gum, and tannin–tannin |
Low-grade strength |
Phenolic substituents in tannin with hydroxyl groups makes tannins highly reactive. |
Bad adhesion |
Short pot life with lower crosslinking, due to the tannin/formaldehyde condensate. |
Brittleness |
|
Unserviceable shelf and pot lives |
|
Large pressing time |
|
Short assembly time |
|
Uneconomic conditions of application |
|
Chemical modification of tannin
The resemblance of tannin and similarity in the reactivity with formaldehyde-based systems, such as conventional phenol resorcinol formaldehyde, makes tannin a potential substituent for petrochemical based resins.90 Although tannins have limitations as listed in Table 1, wood adhesives based on condensed tannin have been extensively studied. Moreover, hydrolysable tannin has limited reaction with formaldehyde.54 In addition, linking units between hydrolysable tannin groups are highly susceptible to moisture, whereas condensed tannin is found to be highly immune to moisture.101 Several attempts have been made to improve the properties of tannin, blending tannin with polymers or copolymerizing or used as additives to the main resin etc.35,95,96 The polyphenolic structure of tannin can be engineered through various chemical modifications, such as acylation, esterification, methylolation, etherification etc.36 Two primary approaches through which condensed tannin can be used to manufacture adhesives are auto-condensation and polycondensation reactions.
Co-polymerization of tannin with synthetic adhesives is also possible and the reason behind this is often,
• to suppress the emission of formaldehyde from synthetic resin (when a small percentage of tannin is added) or.
• to make the tannin-based adhesive immune to moisture (when a small percentage of synthetic resins are added). A simple addition of a small percentage (∼10 to 30%) of polymeric 4,4'-diphenylmethane diisocyanate (pMDI) into mimosa tannin-based adhesive resulted in enhancing the Young's modulus values to the positive side.102,103Table 2 shows an overview of tannin-based adhesives with its remarkable outcome.
Table 2 Applications of tannin-based adhesives for consolidation of various wood products with significant outcomes
No. |
Resin + hardener |
Application |
Outcomes |
Ref. |
1 |
Wattle tannin + HCHO (modified by different bridging agent) |
Exterior plywood |
A marketable adhesive in South Africa (SA) |
98
|
2 |
Wattle tannin + resorcinol–HCHO |
Glulam and finger joints |
A marketable adhesive in SA (South Africa) |
104
|
3 |
Mimosa tannin + methylol–urea |
Particleboard (for exterior and semi exterior application) |
Inexpensive Tannin adhesives. methylol–ureas can be effectively used as hardeners. |
105
|
4 |
Larix tannin (60%) + phenol–formaldehyde |
Plywood (for general and construction application) |
The obtained resin had much better properties than pure phenol–formaldehyde |
106
|
5 |
Quebracho tannin + furfuryl alcohol |
Hardboard |
Results were similar to that of phenol–formaldehyde |
107
|
6 |
Phenol–formaldehyde + pinus oocarpa tannin (10%) |
Plywood |
Modulus of rupture and modulus of elasticity remains constant, except for similar modulus of elasticity. |
108
|
7 |
Wattle tannin + polyvinyl acetate (20%) |
Bonding fancy veneers to plywood |
The bonding strength of tannin-based adhesives is improved using 20% polyvinyl acetate |
109
|
8 |
Phenol–formaldehyde (80%) + corn starch (15%) + quebracho tannin (5%) |
Plywood (for exterior use) |
Improved mechanical properties than plywood panels made out of commercial phenol–formaldehyde |
110
|
9 |
Corn-starch + wattle tannin + formaldehyde |
Plywood (for interior use) |
Outstanding mechanical properties, similar to phenol–formaldehyde |
111
|
10 |
Phenol–formaldehyde + Eucalyptus tannin (10–15%) |
Cellulose fibre composite sheets |
Improved mechanical properties against the panel using pure phenol–formaldehyde. |
112
|
11 |
Mimosa tannin (50%) + lignin (50%) |
Particleboard (for interior use) |
Exterior grade panels can be made out of tannin alone. |
113
|
12 |
Grape tannin (60%) + lignin (40%) |
Particleboard (for interior use) |
Tannin molecules, responsible for a higher density, crosslinking, and increased strength |
114
|
13 |
Mimosa tannin/formaldehyde (60%) + lignin (40%) |
Particleboard |
Meet all the requirements for internal bonding specified by European standards. |
115
|
14 |
Pine tannin
|
Particleboard and medium density fibreboard |
It has the potential to become an industrial adhesive. |
95
|
15 |
Furfuryl alcohol (54%) + Quebracho tannin (45%) + para-toluene sulfonic acid (0.9%) |
Composite with vegetal fibers reinforcement |
Outstanding mechanical properties and fast curing |
116
|
16 |
Melamine–formaldehyde/phenol–formaldehyde + tannin (20%) |
Plywood |
The reaction between Tannin and formaldehyde leads to crosslinking of the adhesive system and resulted in the reinforced melamine–formaldehyde and Phenol–formaldehyde |
117
|
17 |
Mimosa/Pine tannin – Furfuryl Alcohol (50%) |
Particleboard |
Capable of meeting European standards at pH = 10 |
118
|
18 |
Pine tannin + Phenol–Formaldehyde /urea formaldehyde/polymeric iso-cyanate |
Interior and exterior plywood |
Adding 20 to 35% of synthetic adhesive encouraged tannin adhesive. |
94
|
19 |
Lignin polyol–tannin + polyethylenimine (PEI) |
plywood |
PEI brings greater tensile strength, heat and moisture-resistance |
119
|
20 |
Tannin + PVA + boric acid |
Hardwood and softwood |
Free hydroxyl groups of PVA and tannin serve as cross-linking sites that enhance thermal, mechanical, and performance properties. An improved hydrophobicity was noticed. |
120
|
Polycondensation reaction of tannin with aldehydes or non-aldehyde hardeners
Tannin, on reaction with aldehydes or various non-aldehyde-based hardeners (such as furfuryl alcohol, glyoxal, and hexamine) results in polycondensation reaction. For several years, tannin–formaldehyde based wood adhesives have been commercially used for the production of wood-based composites.95,121 Exterior grade wood-composites bonded with tannin-based adhesives are manufactured through polycondensation of tannin with aldehyde-type hardeners, which showed excellent weatherability with negligible emission of formaldehyde.54 Furthermore, tannin-based adhesives prepared by non-aldehyde hardener, hexamine (hexamethylenetetramine), under basic-conditions are more environmentally friendly, as it showed no emission of formaldehyde and ammonia, as the breakdown products.122,123
Hence, the formaldehyde emission from such adhesives will be negligible, when the bonded substrates undergo thermal treatment during production or processing. Based on the conditions under which they are produced, wood panels prepared with tannin–hexamine adhesives are capable of equally meeting the interiors along with exterior grade standard specification requirements.99 Tannins derived from mimosa, quebracho, etc. are slow reacting and can be used with hexamine to produce interior-grade particleboard.65,99
Chen and colleagues developed a wood adhesive from commercial mimosa tannin and glycerol diglycidyl ether (GDE), where GDE acted as a crosslinker.35 The study evaluated the effect of varying the ratios of tannin and GDE on physical, chemical, and thermal stability along with adhesive performance. Simple preparation of the adhesive included mixing of tannin in water, followed by the addition of GDE. Free hydroxyl groups of tannin react with the epoxy groups of GDE, and form network-like structures by the elimination of water molecules as depicted in Fig. 7. The viscosity of the adhesive significantly depends on the weight ratio of tannin: GDE at constant pH. At a specific curing temperature, samples of 1:1 ratio (tannin:GDE) showed superior Young's modulus compared to the samples having a higher amount of tannin content (example 2:1 and 3:1). Moreover, from thermogravimetric analysis (TGA) and the first derivative of TGA, derivative thermogravimetry (DTG), the 1:1 sample showed the maximum enhancement in thermal stability. In addition to thermal stability, the same sample showed enhancement in shear strength tested after immersion in hot and cold water for 3 h, according to the Chinese National Standard (GB/T 17657–2013). Fourier Transform-Infrared spectroscopy (FT-IR), Matrix-assisted laser desorption ionization time-of-flight (MALDI-ToF) and Nuclear magnetic resonance spectroscopy (NMR) analysis confirmed the formation of a non-hydrolysable ether, which benefitted water resistance along with enhancement in adhesive properties. Furthermore, from analysing the peaks obtained from the MALDI-ToF of tannin/GDE adhesive, the four oligomeric structures of tannin were proposed, namely fisetinidin, robinetinidin, catechin and delphinidin (Fig. 8).35
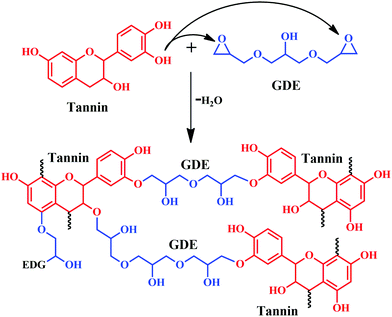 |
| Fig. 7 Possible reaction mechanism between Mimosa tannin and glycerol diglycidyl ether (GDE) leading to the formation of a crosslinked network structure. | |
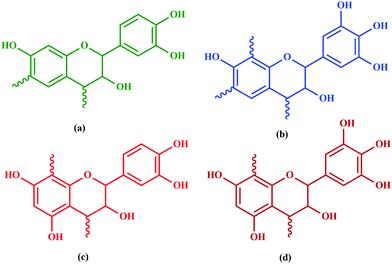 |
| Fig. 8 Basic chemical structures of Mimosa tannin: (a) Fisetinidin structure (molecular weight − 272.3 g mol−1); (b) Robinetinidin (molecular weight − 288.3 g mol−1); (c) Catechin (molecular weight − 288.3 g mol−1); (d) Delphinidin (molecular weight − 304.3 g mol−1). | |
Tannins under different pressing conditions give exterior-grade particleboard.124 In a recent study, using a sole bio-hardener, procured from the extract of African trees, ‘Senegalia Senegal’ and ‘Vachellianilotica,’ were employed as a hardener for maritime pine tannin resin, without addition of aldehyde.125 The extracts successfully functioned as a green hardener, and a complete bio-adhesive, applicable for interior particleboards.125Fig. 9 shows the chemical reaction involving the bio-hardener hydrolysis and crosslinking of tannin by reacting with 2-hydroxy-5-hydroxymethyl furan, resulting in 2,5-dihydroxymethyl furan. The particle board bonded using the adhesive exhibited enhanced mechanical properties and met the criteria of European norms.
 |
| Fig. 9 Reaction of bio-hardener hydrolysis and the crosslinking of tannins with 2-hydroxy-5-hydroxymethyl furan, resulting in 2,5-dihydroxymethyl furan. | |
Omura and colleagues developed a novel adhesive by the reaction of tannin with ε-poly-L-lysine (EPL), without any chemical additives.126 The as-prepared adhesive showed non-toxic behaviour, as it consisted of natural renewable ingredients; in the combination, about 30% of the tannin is mixed with 13% of the EPL. Among the tested samples, about 44 out of 100 samples passed the criteria of EN 314 class-1,126 confirming the pertinence for indoor bonding applications. Fig. 10 represents the reaction involved, where the adhesive showed excellent water resistance and bonding strength. The reaction follows a Michael addition-type plausible mechanism, where gallic acid oxidises to a diketone molecule.126
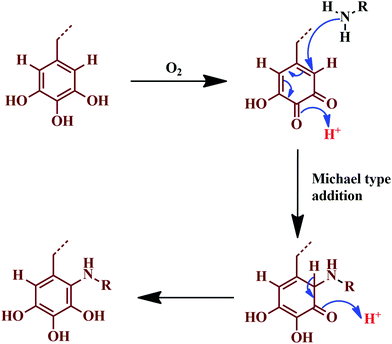 |
| Fig. 10 Michael addition-type plausible reaction mechanism, where gallic acid is oxidised to a diketone. | |
Auto-condensation reaction without hardeners
‘Auto-condensation’ terminology applies to the opening of the pyran rings under acidic as well as alkaline conditions without using an external hardener.127 This is a unique chemical property of tannin, as it induces self-polymerization to obtain a crosslinked polyphenolic network.65 The rates of auto-condensation reaction of tannins depend on the source of extraction and its chemical composition. 'Quebracho' and 'mimosa' tannins are slower-natured, whereas 'pecan nut' and 'pine' are comparatively faster, considering the auto-condensation.128 For faster-natured tannins, rapid self-polymerization is just a contact away with the lignocellulose surface.127 Contrarily, the slower-nature took more time, resulting in poor internal strength of the bonded wood panel due to its sluggish rate of hardening.129 The polyflavonoid tannin adhesives undergo auto-condensation, which can be physically observed by the increase in viscosity without aldehydes or dialdehydes.65,127 Under acidic or alkaline conditions, the chain opening of the flavonoid units occurs on the O1–C2 bonds followed by condensation at C2 with the free sites of flavonoid at C6/C8 with different tannin molecules.130 The chemical reaction of auto-condensation is shown in Fig. 11.
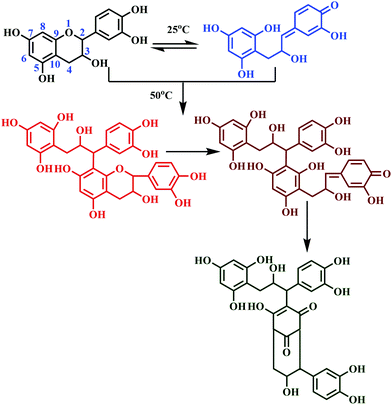 |
| Fig. 11 Mechanism of auto-condensation of tannin molecules. | |
It is reported that the auto-condensation of different tannins can be swayed by weak Lewis acids, like boric acid, silicates, aluminium chloride, and silica.131 Lewis-acid catalyses auto-condensation of tannin, thus rectifying the problems associated with the slower reaction of tannins. Moreover, the Lewis-acid based auto-condensation system demonstrates a reduction in pressing time and pressing temperature and offers stronger internal bonds.127,132 A recent study reported the usage of quebracho tannin adhesive (of 50% water solution), and (2 to 4%) boric acid, for the preparation of a poplar plywood (populous deltoids) panel.133 The prepared plywood panels met the bonding requirements of the relevant standard; also, the panel showed enhanced biological resistance due to the biocide nature of boric acid.133 The tannins, which are hardened by the auto-condensation technique, induced either by Lewis-acid or lingo-cellulosic substrate, solely resulted in bonds of interior grade quality.54
Tannin epoxy-based adhesives
Epoxy resin is the most popular and highly demanding commercial thermosetting polymer, which has been extensively used in various fields such as coatings,134–138 adhesives,139–142 and advanced composites143–148 due to its unique chemical resistance, excellent adhesion, and mechanical properties.149,150 However, petrochemical based epoxy resins are not environmentally benign. Based on recent European directives, especially the EU's 2015 Circular Economy Strategy, the industrial approach and research directions are now focused on reducing waste and lowering pollutant volume.151 Moreover, realising the toxicity of petrochemical compounds to both humans and the environment, many petrochemical-based substances are identified as carcinogens.
Conventionally, many of these compounds were widely used by plastic industries. Among them, bisphenol-A (BPA) is classified as CMR R3, which is one of the main components of epoxy resins.149,150 However, BPA, a primary raw material for the production of commercial epoxy resin, is a petroleum-derived product. Economic, health, and environmental consequences of these materials have inhibited their extensive use industry, which is being converted to a green-labelled industry. The substitution of petroleum-derived chemicals with newer and eco-friendly (preferably bio-derived) polymers has come in first place as far as the most attractive development projects are concerned.152,153 Coupled with environmental awareness and primarily food safety and packaging considerations, developments in the exploration of green materials have boomed. As a result, low toxic precursor materials which can synthesize epoxy resin have been extensively explored in the past few years. Bio-derived materials also function as a raw material or as a substitute for the non-biodegradable petroleum-derived product.154–156 As green technology has received huge investment, extensive research, regarding chemically modified bio-derived epoxy resin from lignin, tannin, clay material, plant-seed oils, eugenol, vanillin, plant waste filler, cellulosic materials etc., has been reported.154–160 Moreover, incorporating natural materials, containing natural-phenolic compounds, in epoxy technology offers comparable properties to synthetic materials. However, the lower value of modulus, mechanical strength, and curing is still a significant challenge with natural-phenolic materials. Tannin is one of the naturally occurring phenolic materials, consisting of amorphous and complex-natured compounds.92 As mentioned earlier, the extraction of tannins can be possible from natural products, such as tree barks, plant cell walls, and plant-based by-products.161 For the production of adhesives, partial substitution of phenol with tannins can be a potential step in the manufacturing of epoxy-based adhesive.65,99,100 Partial substitution is possible, because of the numerous hydroxyl and phenolic groups present in tannin.158–160 Previous studies reported that approximately 90% of phenol could be substituted by tannin in the phenolic resin technologies, particularly by condensed tannin.162,163 Among different bio-resources, polyphenolic natured tannins, which are derived from woods, ought to be a multi-functional epoxy hardener.149,164 Condensed tannins include recurring flavonoid units; on the other hand, hydrolyzable tannins are saccharides partially or wholly replaced by ellagic or gallic acid. The presence of hydroxyl groups as well as aromatic rings in its structure enables covalent and non-covalent interactions at the cost of the mechanical properties of the epoxy resin. With the tuneful effect these tannin properties bring, one might expect an enhanced flame retardancy and improved mechanical properties of polymeric materials.165
Towards preparing flame-retardant epoxy resin, the most remarkable renewable hardener is tannic acid (TA), which has applications as an oxygen radical quencher, and charring agent.165–167 It reacts with commercial-grade diglycidyl ether of bisphenol-A (DGEBA) to form TA-DGEBA, which acts an effective flame retardant thermoset compound, possessing a limiting oxygen index (LOI) value of 46% more than that of the control sample.166 Hence, confirming the potential role of TA-based epoxy resins as a flame-retardant polymer. The chemical reaction of TA with epoxy monomer is considered to be the most promising method to synthesize flame-retardant epoxy, which finds application in various fields like aerospace, automobile, construction, etc.166 Eucalyptus tannin can also be considered a promising route for the partial replacement of BPA from commercial-grade epoxy. Bio-derived epoxy resin can also be synthesized by the reaction of condensed tannin with epichlorohydrin, through glycidylation reaction, as shown in Fig. 12.
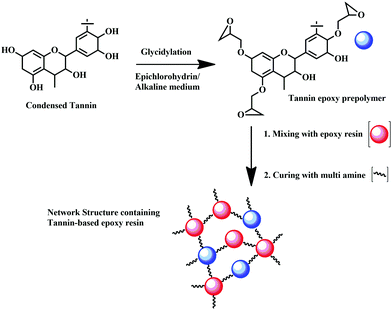 |
| Fig. 12 Preparation of tannin-based epoxy resin by glycidylation reaction of condensed tannin with epichlorohydrin in alkaline medium. | |
Tannin also acts as a precursor for bio-derived epoxy resin and possesses the role of a curing accelerator for epoxy resin.164 The subunits of tannin, namely, catechin, epicatechin, and 2 flavon-3-ol epimers are widely spread across the plant kingdom. In catechin, the molecular structure has two phenolic rings which differ by the hydroxylation pattern: the hydroxyl groups (two OH groups) of the I-ring are in the meta position, whereas in the II-ring they are in the ortho position, as shown in Fig. 2.
Another study reported the preparation of epoxy acrylate resin, using glycidyl ether tannin (GET) and acrylic acid.168 Towards the effort of completely replacing BPA, the said reaction was successful, on heating at 95 °C, in the presence of a catalyst and hydroquinone. The optimum time was reported as 12 h, for synthesizing tannin-based epoxy acrylate.134,168 The resulting wood joint bonded with tannin-based epoxy acrylate displayed enhanced block shear strength. Overall, unique structural features of tannin make it a potential candidate for the preparation of bio-derived epoxy resin for adhesive applications. Recently, Zhang and colleagues prepared bio-derived epoxy from tannin extract.36 Investigators utilized myrica tannin extract (MTE) as a precursor for epoxy resin. The preparation of epoxidized MTE involved liquefaction through the alkoxylation method. The prepared sample was then employed to improve the properties of commercial DGEBA. It is reported that, by introducing 5 wt.% epoxy resin (synthesized from MTE) to DGEBA, 35.8% enhancement in tensile strength was achieved. In addition, the impact strength improved by 243.8%, with a significant shift in the elongation at break and flexural strength. Crosslinks formed by introducing MTE based epoxy and DGEBA contributed to enhancing the mechanical properties with a notable improvement in solvent resistance.
Tannin-based polyurethane adhesives
The strong research trend on resins, adhesives, and plastics derived for renewable, bio-derived materials has gained momentum as interest in such materials continues to grow. In the case of polyurethanes (PUs), considerable literature is now available on the usage of bio-derived polyols. About 50% of PUs are now synthesized by using bio-derived polyols.169–174 Synthesizing isocyanates using fatty acids from vegetable oils and furan derivatives has been reported from the early 1960s.175–179 These chemicals, however, were still isocyanates, and thus potentially toxic and are not extracted from bio-derived materials. Later, an alternative approach to the preparation of PUs without isocyanates was reported.180–182 Investigators reported PUs from polyols from several renewable materials like tannin171,173,183,184 and lignin185–188 for a wide range of applications. Oxypropylated flavonoid tannins are one such example of a nature-derived polyol, which when reacted with polymeric isocyanate results in PU.189 Different chemical methods have already been established to develop non-isocyanate polyurethane (NIPU) and hydroxy-PU.180 For example, polyaddition of diamines over cyclic polycarbonates,190 like derivatives of polyethylene glycol decarbonate and glycerol carbonate.191,192
Pizzi prepared wattle tannin-based PU adhesive, where wattle tannin functioned as the source for polyol.184 Wattle tannin was partially benzoylated through the Schotten–Baumann method, by reacting with benzoyl chloride. The reactive hydroxyl group was thus partially substituted forming benzoylated tannin, which reacted with di-isocyanate leads to the formation of tannin-based PU. The tannin-based PU offered excellent weathering resistance and was reported for surface coatings.184 Tannin has hydroxyl group-rich flavonoid constituents, making them a precursor for bio-derived PUs.193 Tannin-based cold setting PU adhesives enhance the moisture resistance and mechanical properties, which can partially replace the commercial PUs.169–171,173,174,184 In the latter instance, it should be highlighted that the tannin has a significant contribution in reducing the curing time of PU adhesive. It was reported that the synthesis of the tannin–PU copolymer follows an exothermic reaction; however, the extent of formation remains uncertain.184
Moubarik and colleagues reported the formation of a resinous product through the reaction between tannin and formaldehyde.111 The prepared resin exhibited adhesion properties and facilitated consolidation of particleboard, upon reaction with pMDI.111 Crosslinked structures established by methylene bridges resulted in urethane linkages, which enhances the adhesion properties.111 The detailed reaction is shown in Fig. 13.
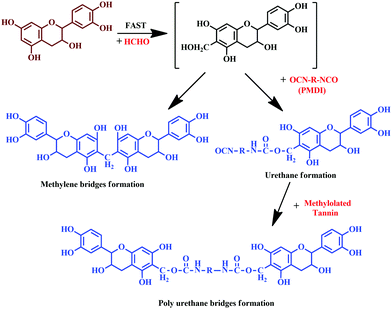 |
| Fig. 13 Chemical reaction of tannin with formaldehyde and polymeric 4,4'-diphenylmethane diisocyanate (pMDI), and the formation of urethane linkages. | |
Thébault and colleagues reported the preparation of a bio-derived NIPU from mimosa tannin.194 Synthesis involved reaction of aminated and commercial mimosa tannin extract, pre-reacted with dimethyl carbonate, at ambient temperature. The resultant PU exhibited higher curing temperature (greater than 100 °C). NIPU from tannin can be synthesized by the reaction of flavonoid tannin's hydroxyl groups with dimethyl carbonate followed by hexamethylene diamine.171 The reaction is represented in Fig. 14. Esmaeili and colleagues synthesized NIPU using TA as the raw material by a three step method.195 As represented in Fig. 15, the synthesis of NIPU from TA involves the preparation of epoxidized tannic acid by a glycidylation and conversion to carbonated tannic acid (CTA) by a chemical CO2 fixation method. In addition to the cure kinetics, TA based NIPU was evaluated for antioxidant and cytotoxic properties, and the sample exhibited better biocompatibility with antioxidant and non-toxic properties. Cure kinetics studies showed the interaction between amino groups and TA molecules by a Michael addition reaction. It was found that the interaction between polyphenolic resin and aromatic rings of curing agents are by π–π stacking, offering it as a potential bio-derived precursor for NIPU.
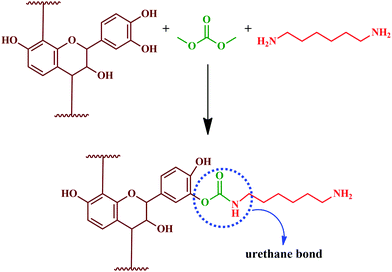 |
| Fig. 14 Preparation of novel bio-derived tannin-based non-isocyanate polyurethane (NIPU) by the chemical reaction between free hydroxyl groups of flavonoid tannin with dimethyl carbonate followed by hexamethylene diamine. | |
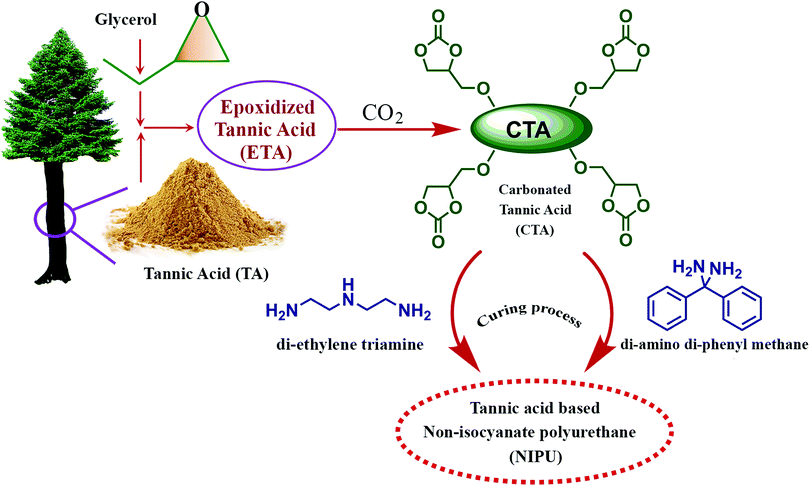 |
| Fig. 15 Schematic illustration of the synthesis of non-isocyanate polyurethane (NIPU) by a three step preparation method from tannic acid (TA). | |
Likewise, the carbohydrate fraction of the tannin extract also seemed to be carbonated, and their reaction leads to the formation of isocyanate-free urethane linkages with aminated tannin. Thus, it can be inferred that the polyphenolic fraction of the tannin extract and other components also has a significant role in the PU synthesis. Hence, it is possible for the preparation of bio-derived NIPU for adhesives and surface finishes, which can be obtained through the reaction of carbonated condensed flavonoid tannin. The carbohydrate fraction of the tannin extract can also be carbonated and reacted to generate isocyanate-free urethane linkages with aminated tannins. Carbohydrates in tannin extracts are either monomers or oligomers, resulting from the hydrolysis of hemicellulose during tannin extraction.61–64
These findings showed that the entire tannin extract, including polyphenolic components, can be used to prepare PUs.194 Hydrolysable chestnut tannin possesses a small amount of hydroxyl group; after reacting with dimethyl carbonate, it reacts with hexamethylene di-amine later. Hence, it can be noted that in PU synthesis, isocyanate is not involved as a reactant; instead, it is carried out using renewable materials, like hydrolysable chestnut tannin. Thébault and colleagues reported the preparation of NIPU using hydrolysable chestnut tannin.196 Preparation of NIPU involved carbonation of hydrolysable chestnut tannin with dimethyl carbonate followed by reacting with hexamethylenediamine. In another study, Thébault and colleagues prepared NIPU from condensed flavonoid tannin and tested it for their applicability in surface coatings.197 The study involved evaluation of condensed flavonoid tannin from different sources such as maritime pine, radiate pine barks and quebracho wood. Urethane linkages were engineered by the reaction of condensed flavonoid tannin with dimethyl carbonate and hexamethylene diamine (Fig. 16). Urethane linkages were evidenced from FT-IR analysis for all the tannin reaction products. The oligomeric distribution of the prepared sample was analysed by the MALDI-ToF technique. GPC analysis identified high molecular species, and showed that varying the condition alters the molecular weight of PU formed. Most of the samples showed difficulty in dissolution for the GPC analysis, which indicated the formation of a crosslinked 3D network structure. Furthermore, the GPC analysis showed a molecular weight of > 3500 Da, when the reaction was at a temperature of 103 °C. TGA analysis showed that the prepared PU degrades between a temperature of 180 and 200 °C. The sample showed suitability for wood coating applications as it displayed hydrophobic properties and a minimum filming temperature of 170 °C.
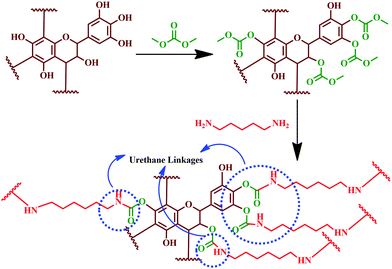 |
| Fig. 16 Reaction mechanism showing the formation of urethane linkages by the chemical reaction between condensed flavonoid tannin, dimethyl carbonate and hexamethylene diamine. | |
Characteristic peaks at 1690, 1265, and 1537 cm−1 in the FT-IR spectra confirmed the reaction and the formation of urethane linkages. Contact angle measurement showed that the coated surface has superior hydrophobic nature compared to the substrate. Thermal degradation of PU was observed between 180 and 200 °C (from the TGA analysis), which unveiled the suitability as a thermally stable wood coating. This study was the first approach to exhibit that tannin can be a better substitute for polyols after reacting with dimethyl carbonate and a diamine.197
Tannin-based polyethylenimine adhesives
Coupled with the health hazards of petrochemicals and formaldehyde emission, chemically modified bio-derived materials have gained significant interest.187–189 Marine adhesive protein (MAP), is one such bio-derived material that is formaldehyde free, and a potential material for adhesives. The main components of the attachment plaques consist of a decapeptide (Ala–Lys–Pro–Ser–(Tyr/DOPA)–Hyp–HypThr–DOPA–Lys).190–192,198 Recent studies have reported that DOPA, present on MAPs, has a major role in adhesion properties.193,194,196 Soy proteins and poly(N-acryloyl dopamine), which contain phenolic substituents, are widely reported as water-resistant wood adhesives.197,199 It is noteworthy to highlight that these compounds also contain phenolic groups, hence it can be implied that adjacent phenolic groups play an important role in adhesion. As tannin is a polyphenolic compound, researchers have explored the possibility of using chemically modified tannin to produce a high performance adhesive. Engineering the tannin through physico-chemical modification is a greener protocol for the development of eco-friendly adhesives.51
Condensed tannins, also known as polymeric proanthocyanidins, are used extensively in the wood adhesive industry due to their abundance, low cost, and structural advantages. As their structure varies on the basis of the sources, it can be further sub-classified based on the hydroxylation pattern of the repeating flavonoid monomer units.177 The most abundant form is a procyanidin polymer isolated from Douglas-fir inner bark and purified over Sephadex LH-20.200,201 The adhesive prepared from a procyanidin-type tannin, isolated from the inner barks of Douglas-fir inner bark, and polyethylenimine (PEI) showed good adhesion properties with its advantage as a formaldehyde-free system.202 The samples exhibited high shear strengths and possessed excellent water-resistance. As tannin and PEI, represented in Fig. 17, are water-soluble, an aqueous solution of both was mixed to obtain the tannin PEI adhesive.192
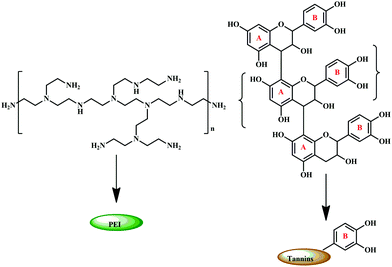 |
| Fig. 17 Structure of polyethylenimine (PEI) and condensed tannin with their respective schematic representation. | |
Preparation of the tannin–PEI adhesive (possible reaction is shown in Fig. 18) involved water as a solvent, making the process free from organic solvents. The work showed a detailed study on the effect of parameters like effect of mixing time, total solid content, tannin to PEI weight ratio, temperature and cure time of the adhesive.202 At a total solid content of 12–24%, the adhesive showed good spreadability on wood veneer. From the experiments, the optimum weight ratio of tannin:PEI was found to be 2:1, for adhesives with high shear strength and water-resistance. At a hot press temperature of 100 °C, and for 2 minutes of thermal application, fully cured two-plywood composites were produced. Also, long term storage of the adhesive decreased the bonding ability, with a decline in shear strength of bonded wood specimens.
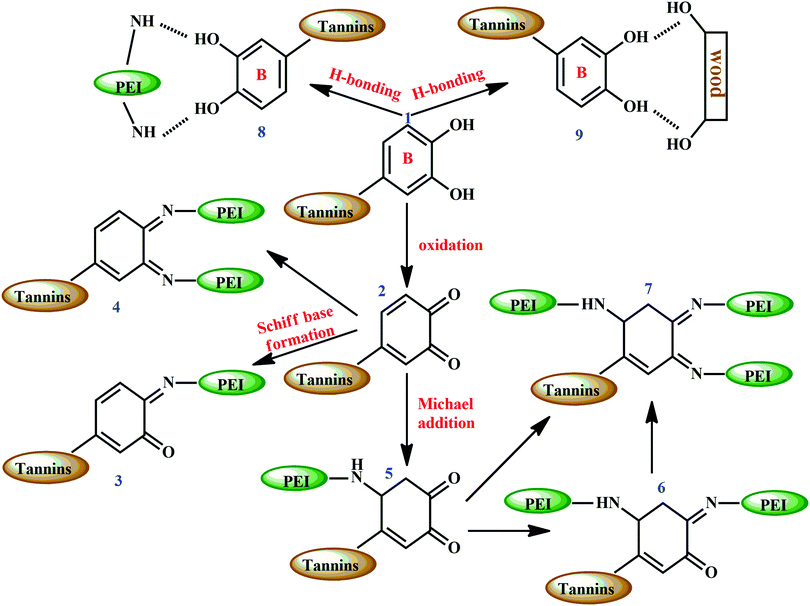 |
| Fig. 18 Schematic illustration of the possible chemical reactions between condensed tannin and polyethylenimine (PEI). Interaction of hydrogen bonds between amine groups of PEI and free hydroxyls of tannin (represented as 8) and hydrogen bonding between the wood specimen and tannin (represented as 9). | |
Catechol groups (represented as 1 in Fig. 18) present in the B-ring of tannin undergo oxidation at high temperatures (hot press temperatures) and form ortho-quinone (represented as 2 in Fig. 18) which further reacts with amino groups in PEI. This produces Schiff bases (represented as 3 and 4 in Fig. 18). ortho-Quinone also reacts following a Michael addition mechanism, and forms Schiff bases (represented as 6 and 7 in Fig. 18), with 3D network structures. Moreover, there can be hydrogen bonds between amine groups of PEI and tannin (represented as 8 in Fig. 18), with the free hydroxyl groups of wood specimens and tannin (represented as 9 in Fig. 18). The hydrogen bonding between the wood specimen and adhesive sample contributed to enhancing the adhesive bonds.
Faris and colleagues reported water-resistant adhesives from a mixture of PEI, tannin and lignin.119 The prepared adhesive when bonded to the plywood sample showed enhanced thermal stability of 360 °C and a tensile strength value of 63.04 MPa. The solid content of the adhesive increases upon incorporation of PEI and at 56.92%, the sample showed enhancement in the tensile strength on the plywood specimen. Crosslinks created by the reaction between the amino groups of PEI and catechol groups present tannin and lignin resulting in an enhancement in the properties.
Tannin-based furfuryl alcohol adhesives
Another potential and green adhesive system prepared using tannin as a main component is the furfuryl alcohol adhesives. Tannin furfuryl resins react with tannin rather than undergoing self-condensation reactions in the presence of an alkaline medium, as shown in Fig. 19. The reaction can be possible in three ways, namely chain condensation reaction, reaction between hydroxyl groups and rearrangement of a furanic cycle.203,204 The rearrangements result in crosslinking reaction, opening new avenues to develop wood adhesives, which are free from formaldehyde.
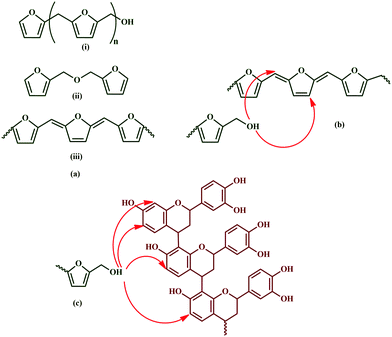 |
| Fig. 19 (a) Self-condensation of furfuryl alcohol: (i) chain condensation reaction, (ii) reaction between hydroxyl groups and (iii) rearrangement of furanic cycle; (b) crosslinking sites for furfuryl alcohol; (c) possible reaction sites between flavonoid units and polyfurfuryl alcohol's hydroxyl group. | |
The gel time of furfuryl alcohols with either mimosa tannin extract or pine tannin extract at 100 °C at different proportions and pH was determined and studied extensively. At a particular gel time and thermo-mechanical analysis, the reaction led to the co-condensation of tannin extract with furfuryl alcohol, thus leading to a bonded joint.203 The acidic conditions are avoided since the furfuryl alcohols undergo self-condensation reactions.203,204 Therefore, since crosslinking occurs between tannin and furfuryl alcohol, gelling and hardening occurs under alkaline conditions. Studies showed that the best results were demonstrated with 50% furfuryl alcohol and mimosa-tannin extract at pH 10. The gelation time was reduced gradually with decrease in pH and an increase in furfuryl alcohol percentage. Gelling ceases when the pH is in the range of 3–8.
Pine tannin extract shows better gel times, and from thermo-mechanical analysis (TMA) the hardened adhesive showed enhanced strength. Moreover, the eco-friendly and non-toxic tannin adhesive showed satisfactory values for bonding wood particleboards based on European standards.203
Investigation by Shirmohammadli and colleagues reported that the moisture resistance of tannin adhesives can be improved by incorporating PEI and furfuryl alcohol.205 Condensation reactions between amine groups in PEI and hydroxyl groups of furfuryl alcohol were evident from the FT-IR analysis. The thermal stability of the adhesives increased on addition of PEI and furfuryl alcohol. Moreover, a decrease in heat absorption peak was recorded on introducing PEI and furfuryl alcohol into the adhesive formulation. The adhesive met the moisture requirements as per the British standard 1204-2 (BS 1204-2), when the formulation had a mixing proportion of tannin:furfuryl alcohol of 1:0.75, containing 20% PEI.
Tannin-based glyoxal adhesives
Glyoxal, a non-volatile reactive aldehyde, was considered a befitting candidate to be used as an exterior grade tannin-based adhesive. Investigations have been performed on tannin–glyoxal adhesives, and the properties evaluated based on the proportion of each constituent.204,206 It was observed that the gel time of the samples has direct relation with the pH. At a pH from 8 to 9.5, the tannin–glyoxal showed a similar gel time to a tannin–formaldehyde system at a range of pH 6 to 7. The study demonstrated that, analogous to the tannin–formaldehyde system, a bio-derived formulation of tannin with glyoxal at optimum concentration can serve the purpose.204,206
Conclusion
As a circular economy and green protocols have been fuelled by developing sustainable materials for various applications, the requirement of potential raw materials has also been given focus. This holds true in the case of adhesives, where the focus is on unveiling sustainable material-based adhesives. Moreover, identification of formaldehyde as a carcinogen has further reduced the demand for formaldehyde-based adhesives, which catalysed a rapid increase in the growth and research of bio-derived wood adhesives. Among various renewable materials, tannin has been a material of interest in the wood adhesive sector; renewability, sustainability, and lower cost are the advantages that tannin provide compared to petrochemical-based materials. It can be underlined from the various works that tannin, due to its multi-phenolic structure, has the possibility to function as an alternative for commercial petrochemical-based resins for wood bonding. As tannin adhesives developed by the reaction of tannin and formaldehyde show brittleness, various strategies have been postulated. Enhancement in adhesion can be achieved by adding phenol and resorcinol molecules. Such additives generate bond formation between tannin molecules through methylene linkages, and reduce the inherent high viscosity of tannin. Thus, the multi-phenolic structure of tannin with certain additives can be used to improve the physical as well as mechanical properties.
Despite the excellent adhesion properties that formaldehyde offers, the corresponding volatile organic compounds show some malignant issues. An adequate investigation has been carried out on some of the recent adhesives, initiating from propionaldehyde, acetaldehyde, furfural, or n-butyraldehyde. Combining these aldehydes with mimosa tannin to produce an adhesive for wood panel applications showed retarded adhesion. In contrast, partial substitution of formaldehyde by n-butyraldehyde or furfural gave satisfactory adhesion results; also, the non-polarity of the carbon-chain of n-butyraldehyde brings hydrophobic nature resulting in superior water-resistance. In addition to the above formulation with urea, compounds such as mono-methylol or di-methylol play a significant role, to enhance the adhesion properties. Thus, the multi-phenolic structure of tannin with the opportunity for further modification and solubility in water are the key reasons for the growing interest in tannins for the wood adhesive sector.
This review paper highlighted the developments done on tannin-based adhesives for wood bonding. Different sources of tannin and its structures have been well studied. This structural analysis helps to better understand potential sites for modification. Chemical modifications have played a vital role in expanding the applications of tannin. Chemical modifications such as acylation, where chemical bonds are formed between tannin molecules using adipoyl dichloride inter-chains, bring better flexibility. Apart from this, blending with other polymers, preparing copolymers with tannin, crosslinking, and using tannin as a precursor for other polymers are the most reported modifications.
Similarly, the usage of tannin as a precursor for epoxy resin and PU has attracted interest among researchers for further innovation and development. Condensed tannin has tremendous potential to produce a harmless industrial substitute for rigid epoxy resin obtained from woods. To name a few, its reaction with di-epoxy or pine tannin with di- or polyglycidyl ether under alkaline conditions results in epoxy resin. Hydrolysable tannin works as a crosslinking agent for epoxy resin. The high crosslinking density of tannin-based epoxy resin offers excellent mechanical and thermal properties. Other similar resins also have superb resistance properties despite being quickly broken-down for recycling.
The synthesis of bio-derived PU is fascinating and promising, due to the utilization of hydrolysable tannin, which mitigates the usage of iso-cyanates. The preparation of more than 70% bio-derived NIPU for adhesives and surface finishes obtained by the reaction of carbonated condensed flavonoid tannin extracts by reaction with aminated tannin extracts of the same nature seems to be possible. The formation of urethane linkages is evidenced from various analytical methods, and has proved their industrial viability to replace the conventional isocyanate-based systems. Moreover, recent developments in tannin–PEI, tannin-blended polymers, tannin-based furfuryl alcohol adhesives, tannin–glyoxal systems etc., have emerged as a potential substituent for conventional adhesives (formaldehyde, isocyanate etc.). Researchers are exploring the structural and chemical modifications on the polyphenolic structure of tannin, which can update the tannin as a precursor for various bio-derived materials.
In a nutshell, the recent developments highlight tannin's immense potential for developing novel and high-performance materials in accordance with the new concept of sustainable development. In order to establish bio-derived wood adhesives, tannin, a green aromatic building block, revealed a new path and a new area for research. Hence, calculating the developments in tannin, it can be unambiguously stated that with such transformations, tannin can be a promising and exciting sustainable resource for a greener world.
Future perspectives
As tannin shows promising properties compared to petrochemicals, there are comprehensive reviews on the application of tannin in the wood adhesive sector.163,199 However, the present work includes a complete database with highlights from an industrial viewpoint. Although there are many limitations associated with tannin usage, promising developments have been reported in the last few decades. Efficient and green extraction methods need to be emphasized to meet industrial mass production of tannin-based materials. Development of in situ techniques for the structural analysis of tannin should be a main focus, as the chemical composition of tannin varies based on its sources. Accelerated performance tests and developing possible approaches for the effective utilization of tannin and non-tannin constituents should be given equal importance. Unveiling the limitations of tannin can probably shed light on gaining interest for tannin as a precursor for replacing petrochemical-based resins.
To start with, the quantity of tannin naturally available, compared with the capacity of synthetic adhesives used in the wood industry, has resulted in a great deal of research on expanding tannin. Several companies have started building new extraction plants, as they realized the capability of the substance for tannin extraction, where this material can be extracted in millions of tons each globally. However, this movement is still at its infancy, comparatively small and underway.
Moreover, other approaches such as copolymerizing with sustainable and renewable materials including tannin and lignin, soy flour or soy protein and tannin, synthesis of furfuryl alcohol and tannin adhesive formulation, etc., can be environmentally benign processes.207,208 Free hydroxyl groups of wattle tannin can be modified chemically by blending with PVA and crosslinking with boric acid.120 Selection of similar crosslinkers and blending with a compatible commercial binder (PVA) can partially reduce the dependency of petrochemical derived binders. Recent inclusion of a circular economy and green protocol limits the usage of toxic substances,151 which has made researchers and industries working on wood adhesives promote bio-derived adhesives. As formaldehyde emission has an adverse impact on human health and the environment, approaches to mitigate emission have been given primary priority. Based on this search, several attempts have been proposed, of which major works on tannin are as follows:
1. Eliminating the toxic formaldehyde and replacing it with other aldehydes, which are relatively non-toxic and non-volatile,119,206 such as vanillin, glutaraldehyde or glyoxal. In addition, aldehydes prepared by reacting sodium periodate with carbohydrates/sucrose/glucose.
2. Utilizing hardeners which are non-aldehyde including tris-hydroxymethyl nitromethane,203 tris-hydroxymethyl amino-methane or any compounds which can act as a copolymer and hardener, such as furfuryl alcohol-based copolymer.107,118 Moreover, exploring the uniqueness of the polyphenolic structure of tannin and tailoring it through chemical modifications such as acylation, esterification, methylolation and etherification, could further engineer tannin for its suitability as a precursor for bio-derived materials.
3. Using hexamine as a hardener leads to the formation of –CH2–NH–CH2– a bridge between tannin units. However, the secondary amine is apt to mop-up any release of formaldehyde at the time of release itself or any other release of formaldehyde in order to develop a true no-formaldehyde emission panel.123,208–211
4. Tannin can be cured by the process of auto-condensation (without the addition of hardener).127,131,210–212 This approach utilizes the wood substrate itself acting as a responsible candidate for proceeding auto-condensation. In the case of faster-reacting tannin, like procyanidin tannins, or pine bark tannin, as well as slower-reacting tannin, auto-condensation is carried out by adding silicate or silica or other promoters,127,131,210–213 allowing the formulation of wood particleboard of indoor quality.
5. Approaches to prepare tannin blended adhesive systems, with PEI, furfuryl alcohol, glyoxal as an alternative to formaldehyde, GDE as crosslinker shows comparable properties, meeting standards including BS 1204-2, Chinese National Standard (GB/T 17657–2013) etc. Hence further investigation of potential green crosslinkers, polymers which can be blended with tannin can open up chemically modified value-added products from tannin. Although tannin–PEI adhesives have been reported, the applicability of PEI as a crosslinker for tannin has not been explored. Studies using PEI as a crosslinker for natural polyphenolic compounds have been reported,214 which can be established for tannin as well. Hence, investigators can explore similar works for tannin-based systems as well.
Although tannin has been commercialized for leather manufacturing industries, in the recent past, tannin has emerged as a promising natural phenolic polymer and has significant applications in various sectors, including adhesives, coatings, bio-foams, automotive and building sectors etc.215,216 Tannin as a raw material, however, for adhesive applications still poses certain issues, like short pot life, high viscosity, reactivity, and poor weather resistance. Comprehensive investigation and introduction of newer concepts like copolymerization, chemical modifications etc., can catalyse the development of tannin as a sustainable raw material for adhesive applications. Furthermore, investigation on tannin resin adhesives should be taken further to other advanced wooden composites instead of limiting it to only wood panels. Besides, the industrial development of tannin-based adhesives in the domain of wood fabrication is obligatory.
Author contributions
Pritam V. Dhawale and S. K. Vineeth contributed equally.
Conflicts of interest
There are no conflicts of interest to declare from any of the contributors or institutes.
Acknowledgements
The authors, Dr Jabeen Fatima M. J. and Prof. Prasanth Raghavan, gratefully acknowledge the Kerala State Higher Education Council (KSHEC) and Kerala State Council for Science, Technology and Environment (KSCSTE), Government of Kerala. The authors also greatly acknowledge the Cochin University of Science and Technology (CUSAT), Institute of Chemical Technology (ICT), Mumbai and Biorefining and Advanced Materials Research Centre, SRUC, UK for the technical support.
References
- M. N. Islam, F. Rahman, A. K. Das and S. Hiziroglu, Int. J. Adhes. Adhes., 2022, 112, 102992 CrossRef CAS.
- M. Dunky, Macromol. Symp., 2004, 217, 417–430 CrossRef CAS.
- M. Böhm, M. Z. M. Salem and J. Srba, J. Hazard. Mater., 2012, 221–222, 68–79 CrossRef PubMed.
- J. H. E. Arts, M. A. J. Rennen and C. de Heer, Regul. Toxicol. Pharmacol., 2006, 44, 144–160 CrossRef CAS PubMed.
- C. R. Frihart, For. Prod. J., 2015, 65, 4–8 Search PubMed.
- L. Zhao, Y. Liu, Z. Xu, Y. Zhang, F. Zhao and S. Zhang, For. Stud. China, 2011, 13, 321–326 CrossRef CAS.
- A. Salvini, L. M. Saija, S. Finocchiaro, G. Gianni, C. Giannelli and G. Tondi, J. Appl. Polym. Sci., 2009, 114, 3841–3854 CrossRef CAS.
- S. Liu, G. Du, H. Yang, H. Su, X. Ran, J. Li, L. Zhang, W. Gao and L. Yang, ACS Sustainable Chem. Eng., 2021, 9, 16849–16861 CrossRef CAS.
- P. J. Weimer, A. H. Conner and L. F. Lorenz, Appl. Microbiol. Biotechnol., 2003, 63, 29–34 CrossRef CAS PubMed.
- Z. Qiao, J. Gu, Y. Zuo, H. Tan and Y. Zhang, BioResources, 2014, 9, 6117–6129 CrossRef.
-
X. Zhang, X. Liu, S. Yang, K. Long and Y. Wu, in Proceedings of 2012 International Conference on Biobase Material Science and Engineering, IEEE, 2012, pp. 230–233.
- N. Ayrilmis, J.-H. Kwon, S.-H. Lee, T.-H. Han and C.-W. Park, J. Adhes. Sci. Technol., 2016, 30, 2032–2043 CrossRef CAS.
- S. K. Vineeth, R. V. Gadhave and P. T. Gadekar, Open J. Polym. Chem., 2019, 09, 86–99 CrossRef.
- S. Veigel, U. Müller, J. Keckes, M. Obersriebnig and W. Gindl-Altmutter, Cellulose, 2011, 18, 1227 CrossRef CAS PubMed.
- R. V. Gadhave, S. K. Vineeth, P. A. Mahanwar and P. T. Gadekar, J. Adhes. Sci. Technol., 2021, 35, 1072–1086 CrossRef CAS.
- R. V. Gadhave, P. A. Mahanwar and P. T. Gadekar, Open J. Polym. Chem., 2017, 07, 19–32 CrossRef CAS.
- Z. Wang, Z. Li, Z. Gu, Y. Hong and L. Cheng, Carbohydr. Polym., 2012, 88, 699–706 CrossRef CAS.
- Y. Gu, L. Cheng, Z. Gu, Y. Hong, Z. Li and C. Li, Int. J. Biol. Macromol., 2019, 134, 247–254 CrossRef CAS PubMed.
- S. K. Vineeth, R. V. Gadhave and P. T. Gadekar, Indian Chem. Eng., 2021, 1–11 Search PubMed.
- W. Sridach, S. Jonjankiat and T. Wittaya, J. Adhes. Sci. Technol., 2013, 27, 1727–1738 CrossRef CAS.
- Z. Wang, Z. Gu, Y. Hong, L. Cheng and Z. Li, Carbohydr. Polym., 2011, 86, 72–76 CrossRef CAS.
- L. Chen, Y. Wang, Zia-ud-Din, P. Fei, W. Jin, H. Xiong and Z. Wang, Int. J. Biol. Macromol., 2017, 104, 137–144 CrossRef CAS PubMed.
- Z. Li, J. Wang, L. Cheng, Z. Gu, Y. Hong and A. Kowalczyk, Carbohydr. Polym., 2014, 99, 579–583 CrossRef CAS PubMed.
- A. F. Ang, Z. Ashaari, S. H. Lee, P. Md Tahir and R. Halis, Int. J. Adhes. Adhes., 2019, 95, 102408 CrossRef.
- X. Gong, T. Liu, S. Yu, Y. Meng, J. Lu, Y. Cheng and H. Wang, Ind. Crops Prod., 2020, 153, 112593 CrossRef CAS.
- R. J. Li, J. Gutierrez, Y.-L. Chung, C. W. Frank, S. L. Billington and E. S. Sattely, Green Chem., 2018, 20, 1459–1466 RSC.
- R. V. Gadhave, P. S. Kasbe, P. A. Mahanwar and P. T. Gadekar, Int. J. Adhes. Adhes., 2019, 95, 102427 CrossRef CAS.
-
B. B. Adhikari, P. Appadu, M. Chae and D. C. Bressler, in Bio-based Wood Adhesives, CRC Press, 2017, pp. 1–58 Search PubMed.
- Y. Liu and K. Li, Macromol. Rapid Commun., 2002, 23, 739–742 CrossRef CAS.
-
A. M. Alrefai, R. Alrefai, K. Y. Benyounis and J. Stokes, in Reference Module in Materials Science and Materials Engineering, Elsevier, 2020 Search PubMed.
- J. Liu, L. Zhang, W. Shun, J. Dai, Y. Peng and X. Liu, J. Polym. Sci., 2021, 59, 1474–1490 CrossRef CAS.
- H. M. Siebert and J. J. Wilker, ACS Sustainable Chem. Eng., 2019, 7, 13315–13323 CrossRef CAS.
- S. Ma, Y. Wu and F. Zhou, Curr. Opin. Colloid Interface Sci., 2020, 47, 84–98 CrossRef CAS.
- A. Arias, S. González-García, G. Feijoo and M. T. Moreira, J. Ind. Ecol., 2021 DOI:10.1111/jiec.13210.
- X. Chen, A. Pizzi, E. Fredon, C. Gerardin, J. Li, X. Zhou and G. Du, J. Adhes., 2020, 1–18 Search PubMed.
- T. Zhang, C. Yu, M. Yu, Y. Huang, J. Tan, M. Zhang and X. Zhu, Ind. Crops Prod., 2022, 176, 114255 CrossRef CAS.
-
H. L. Hergert, Condensed tannins in adhesives: introduction and historical perspectives, ACS Publications, 1989, pp. 155-171 Search PubMed.
-
R. W. Hemingway and J. J. Karchesy, Chemistry and significance of condensed tannins, Springer Science & Business Media, 2012 Search PubMed.
- J.-P. Salminen, M. Karonen and J. Sinkkonen, Chem. – Eur. J., 2011, 17, 2806–2816 CrossRef CAS PubMed.
- N. Sahiner, S. Sagbas, M. Sahiner, C. Silan, N. Aktas and M. Turk, Int. J. Biol. Macromol., 2016, 82, 150–159 CrossRef CAS PubMed.
- A. Pizzi, J. Macromol. Sci., Part C: Polym. Rev., 1980, 18, 247–315 CrossRef.
- A. Pizzi, Ind. Eng. Chem. Prod. Res. Dev., 1982, 21, 359–369 CrossRef CAS.
- T. Okuda, Q. Rev. Biol., 1991, 66, 210–211 CrossRef.
- C. N. Aguilar and G. Gutierrez-Sanchez, Food Sci. Technol. Int., 2001, 7, 373–382 CrossRef CAS.
- H. A. M. Bacelo, S. C. R. Santos and C. M. S. Botelho, Chem. Eng. J., 2016, 303, 575–587 CrossRef CAS.
-
C. A. Combs, Tannins: Biochemistry, Food Sources and Nutritional Properties, Nova Science Publishers, Incorporated, 2016 Search PubMed.
- S. Dhiman, G. Mukherjee and A. K. Singh, Int. Microbiol., 2018, 21, 175–195 CrossRef CAS PubMed.
- K. Sharma, V. Kumar, J. Kaur, B. Tanwar, A. Goyal, R. Sharma, Y. Gat and A. Kumar, Toxin Rev., 2021, 40, 432–444 CrossRef CAS.
- A. Pizzi, J. Renewable Mater., 2019, 7, 477–492 Search PubMed.
- A.-K. Koopmann, C. Schuster, J. Torres-Rodríguez, S. Kain, H. Pertl-Obermeyer, A. Petutschnigg and N. Hüsing, Molecules, 2020, 25, 4910 CrossRef CAS PubMed.
- Y. Shirmohammadli, D. Efhamisisi and A. Pizzi, Ind. Crops Prod., 2018, 126, 316–332 CrossRef CAS.
- V. Hemmilä, S. Adamopoulos, O. Karlsson and A. Kumar, RSC Adv., 2017, 7, 38604–38630 RSC.
-
M. Dunky, in Progress in Adhesion and Adhesives, Wiley, 2021, pp. 383–529 Search PubMed.
- M. A. Aristri, M. A. R. Lubis, S. M. Yadav, P. Antov, A. N. Papadopoulos, A. Pizzi, W. Fatriasari, M. Ismayati and A. H. Iswanto, Appl. Sci., 2021, 11, 4242 CrossRef CAS.
-
X. Zhou and G. Du, in Tannins - Structural Properties, Biological Properties and Current Knowledge, IntechOpen, 2020 Search PubMed.
-
P. M. Tahir, J. A. Halip and S. Hua Lee, in Lignocellulose for Future Bioeconomy, Elsevier, 2019, pp. 109–133 Search PubMed.
- A. K. Das, M. N. Islam, M. O. Faruk, M. Ashaduzzaman and R. Dungani, S. Afr. J. Bot., 2020, 135, 58–70 CrossRef CAS.
- S. Drewes and D. Roux, Biochem. J., 1963, 87, 167–172 CrossRef CAS PubMed.
-
D. W. Griffiths, in Toxic Substances in Crop Plants, Elsevier, 1991, pp. 180–201 Search PubMed.
- T. P. Clausen, F. D. Provenza, E. A. Burritt, P. B. Reichardt and J. P. Bryant, J. Chem. Ecol., 1990, 16, 2381–2392 CrossRef CAS PubMed.
- Z. Chang, Q. Zhang, W. Liang, K. Zhou, P. Jian, G. She and L. Zhang, Evidence-Based Complementary Altern. Med., 2019, 2019, 1–26 Search PubMed.
- N. Mahato, M. Sinha, K. Sharma, R. Koteswararao and M. H. Cho, Foods, 2019, 8, 523 CrossRef CAS PubMed.
- U. L. Zidanes, M. C. Dias, M. S. Lorenço, E. da Silva Araujo, M. J. Ferreira e Silva, T. B. Sousa, S. R. Ferreira, J. C. Ugucioni, G. H. Denzin Tonoli, M. L. Bianchi and F. A. Mori, Holzforschung, 2021, 75, 159–167 CrossRef CAS.
- M. A. Dettlaff, V. Marshall, N. Erbilgin and J. F. Cahill, AoB Plants, 2018, 10, ply044 CrossRef PubMed.
-
A. Pizzi, in Monomers, Polymers and Composites from Renewable Resources, Elsevier, 2008, pp. 179–199 Search PubMed.
- T. E. C. Kraus, R. A. Dahlgren and R. J. Zasoski, Plant Soil, 2003, 256, 41–66 CrossRef CAS.
- W. B. Jensen, J. Chem. Educ., 2007, 84, 1913 CrossRef CAS.
- M. D. Luque de Castro and F. Priego-Capote, J. Chromatogr. A, 2010, 1217, 2383–2389 CrossRef CAS PubMed.
- T. Sepperer, F. Hernandez-Ramos, J. Labidi, G. J. Oostingh, B. Bogner, A. Petutschnigg and G. Tondi, Ind. Crops Prod., 2019, 139, 111502 CrossRef.
- H. Olivier-Bourbigou, L. Magna and D. Morvan, Appl. Catal., A, 2010, 373, 1–56 CrossRef CAS.
- G. Amaral-Labat, L. I. Grishechko, V. Fierro, B. N. Kuznetsov, A. Pizzi and A. Celzard, Biomass Bioenergy, 2013, 56, 437–445 CrossRef CAS.
- K. Kemppainen, M. Siika-aho, S. Pattathil, S. Giovando and K. Kruus, Ind. Crops Prod., 2014, 52, 158–168 CrossRef CAS.
- F. J. Hernández-Fernández, J. Bayo, A. Pérez de los Ríos, M. A. Vicente, F. J. Bernal and J. Quesada-Medina, Ecotoxicol. Environ. Saf., 2015, 116, 29–33 CrossRef PubMed.
- C. M. Ajila, S. K. Brar, M. Verma, R. D. Tyagi, S. Godbout and J. R. Valéro, Crit. Rev. Biotechnol., 2011, 31, 227–249 CrossRef CAS PubMed.
- J. Azmir, I. S. M. Zaidul, M. M. Rahman, K. M. Sharif, A. Mohamed, F. Sahena, M. H. A. Jahurul, K. Ghafoor, N. A. N. Norulaini and A. K. M. Omar, J. Food Eng., 2013, 117, 426–436 CrossRef CAS.
- M. V. Palmer and S. S. T. Ting, Food Chem., 1995, 52, 345–352 CrossRef CAS.
- A. I. Talmaciu, M. Ravber, I. Volf, Ž. Knez and V. I. Popa, J. Supercrit. Fluids, 2016, 117, 243–251 CrossRef CAS.
- R. N. Cavalcanti, H. J. Navarro-Díaz, D. T. Santos, M. A. Rostagno and M. A. A. Meireles, J. Food Res., 2012, 1, 282 CrossRef CAS.
- E. Conde, J. Hemming, A. Smeds, B. D. Reinoso, A. Moure, S. Willför, H. Domínguez and J. C. Parajó, J. Supercrit. Fluids, 2013, 81, 193–199 CrossRef CAS.
- M. Perrut, Ind. Eng. Chem. Res., 2000, 39, 4531–4535 CrossRef CAS.
- X. Liang and Q. Fan, J. Mater. Sci. Chem. Eng., 2013, 01, 1–6 CAS.
- J. R. Vergara-Salinas, P. Bulnes, M. C. Zúñiga, J. Pérez-Jiménez, J. L. Torres, M. L. Mateos-Martín, E. Agosin and J. R. Pérez-Correa, J. Agric. Food Chem., 2013, 61, 6929–6936 CrossRef CAS PubMed.
- P. Rangsriwong, N. Rangkadilok, J. Satayavivad, M. Goto and A. Shotipruk, Sep. Purif. Technol., 2009, 66, 51–56 CrossRef CAS.
- W. Routray and V. Orsat, Food Bioprocess Technol., 2012, 5, 409–424 CrossRef CAS.
- P. L. de Hoyos-Martínez, J. Merle, J. Labidi and F. Charrier-El Bouhtoury, J. Cleaner Prod., 2019, 206, 1138–1155 CrossRef.
- C.-C. Xu, B. Wang, Y.-Q. Pu, J.-S. Tao and T. Zhang, Chin. J. Nat. Med., 2017, 15, 721–731 CAS.
- F. Chemat, Zill-e-Huma and M. K. Khan, Ultrason. Sonochem., 2011, 18, 813–835 CrossRef CAS PubMed.
- A. Ali, X. Y. Lim, C. H. Chong, S. H. Mah and B. L. Chua, LWT, 2018, 89, 681–688 CrossRef CAS.
- X.-L. Cheng, J.-Y. Wan, P. Li and L.-W. Qi, Journal of Chromatography A, 2011, 1218 DOI:10.1016/j.chroma.2011.06.091.
- L. A. Heinrich, Green Chem., 2019, 21, 1866–1888 RSC.
- S. Magalhães, L. Alves, B. Medronho, A. C. Fonseca, A. Romano, J. F. J. Coelho and M. Norgren, Polymers, 2019, 11, 1685 CrossRef PubMed.
- J. Shi, M. Wen, X. Li, W. Xu and Z. Li, J. For. Eng., 2018, 3, 1–10 CrossRef.
-
K. L. Mittal, Progress in adhesion and adhesives, John Wiley & Sons, 2015 Search PubMed.
- X. Zhou and A. Pizzi, Int. Wood Prod. J., 2014, 5, 27–32 CrossRef.
- J. Valenzuela, E. von Leyser, A. Pizzi, C. Westermeyer and B. Gorrini, Eur. J. Wood Wood Prod., 2012, 70, 735–740 CrossRef CAS.
- S. Ghahri and A. Pizzi, Wood Sci. Technol., 2018, 52, 261–279 CrossRef CAS.
- H. Pasch, A. Pizzi and K. Rode, Polymer, 2001, 42, 7531–7539 CrossRef CAS.
- A. Pizzi and H. O. Scharfetter, J. Appl. Polym. Sci., 1978, 22, 1745–1761 CrossRef CAS.
- A. Pizzi, Wood Sci. Technol., 2000, 34, 277–316 CrossRef CAS.
- A. Pizzi, R. Kueny, F. Lecoanet, B. Massetau, D. Carpentier, A. Krebs, F. Loiseau, S. Molina and M. Ragoubi, Ind. Crops Prod., 2009, 30, 235–240 CrossRef CAS.
- M. Zanetti, E. Cesprini, M. Marangon, A. Szczurek and G. Tondi, Fuel, 2021, 289, 119907 CrossRef CAS.
- Z. Osman, J. Therm. Anal. Calorim., 2012, 107, 709–716 CrossRef CAS.
- A. Pizzi, E. P. von Leyser, J. Valenzuela and J. G. Clark, Holzforschung, 1993, 47, 168–174 CrossRef CAS.
- A. Pizzi and D. G. Roux, J. Appl. Polym. Sci., 1978, 22, 1945–1954 CrossRef CAS.
- A. Pizzi and M. Merlin, Int. J. Adhes. Adhes., 1981, 1, 261–264 CrossRef CAS.
- L. Yuebin, S. Qiang, C. Jun and G. Zhenzhong, J. Northeast For. Univ., 1994, 5, 65–68 CrossRef.
- A. Trosa and A. Pizzi, Holz Roh- Werkst., 1998, 56, 213–214 CrossRef CAS.
-
É. S. Ferreira and R. C. C. Lelis, in Proceedings of the 51st International Convention of Society of Wood Science and Technology, 2008, pp. 1–11.
- S. Kim, Bioresour. Technol., 2009, 100, 744–748 CrossRef CAS PubMed.
- A. Moubarik, A. Pizzi, A. Allal, F. Charrier and B. Charrier, Ind. Crops Prod., 2009, 30, 188–193 CrossRef CAS.
- A. Moubarik, A. Allal, A. Pizzi, F. Charrier and B. Charrier, Eur. J. Wood Wood Prod., 2010, 68, 427–433 CrossRef CAS.
- A. S. Hussein, K. I. Ibrahim and K. M. Abdulla, Nat. Resour., 2011, 02, 98–101 CAS.
- P. Navarrete, A. Pizzi, S. Tapin-Lingua, B. Benjelloun-Mlayah, H. Pasch, K. Rode, L. Delmotte and S. Rigolet, J. Adhes. Sci. Technol., 2012, 26, 1667–1684 CrossRef CAS.
- L. Ping, F. Gambier, A. P. Pizzi, Z. Guo and N. Brosse, Cellul. Chem. Technol., 2012, 46, 457–462 CAS.
- M. Petit-Conil, F. Bertaud, S. Tapin-Lingua, A. P. Pizzi and P. Navarette, ATIP J., 2011, 65, 6–12 Search PubMed.
- A. Nicollin, X. Li, P. Girods, A. Pizzi and Y. Rogaume, J. Renewable Mater., 2013, 1, 311–316 CrossRef.
- M. Gangi, T. Tabarsa, S. Sepahvand and J. Asghari, J. Adhes. Sci. Technol., 2013, 27, 1407–1417 CrossRef CAS.
- U. H. B. Abdullah and A. Pizzi, Eur. J. Wood Wood Prod., 2013, 71, 131–132 CrossRef CAS.
- A. H. Faris, A. A. Rahim, M. N. M. Ibrahim, A. M. Alkurdi and I. Shah, J. Appl. Polym. Sci., 2016, 133, 2–7 CrossRef.
- R. V. Gadhave, S. K. Vineeth, P. V. Dhawale and P. T. Gadekar, Des. Monomers Polym., 2020, 23, 188–196 CrossRef CAS PubMed.
- A. Pizzi, Ann. For. Sci., 2016, 73, 185–203 CrossRef.
- A. Pizzi and P. Tekely, Holzforschung, 1996, 50, 277–281 CrossRef CAS.
- C. Kamoun, A. Pizzi and M. Zanetti, J. Appl. Polym. Sci., 2003, 90, 203–214 CrossRef CAS.
- A. Pizzi, P. Stracke and A. Trosa, Holz Roh- Werkst., 1997, 55, 168 CrossRef CAS.
- B. Ndiwe, A. Pizzi, R. Danwe, B. Tibi, N. Konai and S. Amirou, Eur. J. Wood Wood Prod., 2019, 77, 1221–1223 CrossRef CAS.
- S. Omura, Y. Kawazoe and D. Uemura, Int. J. Adhes. Adhes., 2017, 74, 35–39 CrossRef CAS.
- A. Pizzi, N. Meikleham, B. Dombo and W. Roll, Holz Roh- Werkst., 1995, 53, 201–204 CrossRef CAS.
- A. Pizzi and A. Stephanou, Holz Roh- Werkst., 1994, 52, 218–222 CrossRef CAS.
- A. Pizzi, J. Adhes., 2009, 85, 57–68 CrossRef CAS.
-
K. L. Mittal and A. Pizzi, Wood Adhesives, VSP, 2010 Search PubMed.
- N. Meikleham, A. Pizzi and A. Stephanou, J. Appl. Polym. Sci., 1994, 54, 1827–1845 CrossRef CAS.
- R. Garcia and A. Pizzi, J. Appl. Polym. Sci., 1998, 70, 1093–1109 CrossRef CAS.
- D. Efhamisisi, M.-F. Thevenon, Y. Hamzeh, A.-N. Karimi, A. Pizzi and K. Pourtahmasi, ACS Sustainable Chem. Eng., 2016, 4, 2734–2740 CrossRef CAS.
- C. Decker, Macromol. Rapid Commun., 2002, 23, 1067–1093 CrossRef CAS.
- J. Gu, G. Zhang, S. Dong, Q. Zhang and J. Kong, Surf. Coat. Technol., 2007, 201, 7835–7841 CrossRef CAS.
- X. Shi, T. A. Nguyen, Z. Suo, Y. Liu and R. Avci, Surf. Coat. Technol., 2009, 204, 237–245 CrossRef CAS.
- M. Nonahal, H. Rastin, M. R. Saeb, M. G. Sari, M. H. Moghadam, P. Zarrintaj and B. Ramezanzadeh, Prog. Org. Coat., 2018, 114, 233–243 CrossRef CAS.
- R. David, V. S. Raja, S. K. Singh and P. Gore, Prog. Org. Coat., 2018, 120, 58–70 CrossRef CAS.
- D. Ratna and A. K. Banthia, Polym. Int., 2000, 49, 281–287 CrossRef CAS.
- F. Lapique and K. Redford, Int. J. Adhes. Adhes., 2002, 22, 337–346 CrossRef CAS.
- S. Popineau, C. Rondeau-Mouro, C. Sulpice-Gaillet and M. E. R. Shanahan, Polymer, 2005, 46, 10733–10740 CrossRef CAS.
- L. Guadagno, M. Sarno, U. Vietri, M. Raimondo, C. Cirillo and P. Ciambelli, RSC Adv., 2015, 5, 27874–27886 RSC.
- T. Lan and T. J. Pinnavaia, Chem. Mater., 1994, 6, 2216–2219 CrossRef CAS.
- P. B. Messersmith and E. P. Giannelis, Chem. Mater., 1994, 6, 1719–1725 CrossRef CAS.
- J. Zhu, H. Peng, F. Rodriguez-Macias, J. L. Margrave, V. N. Khabashesku, A. M. Imam, K. Lozano and E. V. Barrera, Adv. Funct. Mater., 2004, 14, 643–648 CrossRef CAS.
- S. Ganguli, A. K. Roy and D. P. Anderson, Carbon, 2008, 46, 806–817 CrossRef CAS.
- Z. Spitalsky, D. Tasis, K. Papagelis and C. Galiotis, Prog. Polym. Sci., 2010, 35, 357–401 CrossRef CAS.
- O. Zabihi, M. Ahmadi, H. Khayyam and M. Naebe, Sci. Rep., 2016, 6, 38194 CrossRef CAS PubMed.
- M. Vera and B. F. Urbano, Polym. Chem., 2021, 12, 4272–4290 RSC.
- F.-L. Jin, X. Li and S.-J. Park, J. Ind. Eng. Chem., 2015, 29, 1–11 CrossRef CAS.
- M. Geissdoerfer, P. Savaget, N. M. P. Bocken and E. J. Hultink, J. Cleaner Prod., 2017, 143, 757–768 CrossRef.
- S. N. Khot, J. J. Lascala, E. Can, S. S. Morye, G. I. Williams, G. R. Palmese, S. H. Kusefoglu and R. P. Wool, J. Appl. Polym. Sci., 2001, 82, 703–723 CrossRef CAS.
- D. Ratna and A. K. Banthia, J. Adhes. Sci. Technol., 2000, 14, 15–25 CrossRef CAS.
- K. Wang, L. Chen, J. Wu, M. L. Toh, C. He and A. F. Yee, Macromolecules, 2005, 38, 788–800 CrossRef CAS.
- W. Liu, R. Zhou, H. L. S. Goh, S. Huang and X. Lu, ACS Appl. Mater. Interfaces, 2014, 6, 5810–5817 CrossRef CAS PubMed.
- A. Fankhauser-Noti, K. Fiselier, S. Biedermann-Brem and K. Grob, Food Chem. Toxicol., 2006, 44, 1279–1286 CrossRef CAS PubMed.
- J. Qin, H. Liu, P. Zhang, M. Wolcott and J. Zhang, Polym. Int., 2014, 63, 760–765 CrossRef CAS.
- S. Nikafshar, O. Zabihi, S. Hamidi, Y. Moradi, S. Barzegar, M. Ahmadi and M. Naebe, RSC Adv., 2017, 7, 8694–8701 RSC.
- K. Salasinska, M. Barczewski, M. Borucka, R. L. Górny, P. Kozikowski, M. Celiński and A. Gajek, Polymers, 2019, 11, 1234 CrossRef CAS PubMed.
- S. Nair, C. Dartiailh, D. Levin and N. Yan, Polymers, 2019, 11, 612 CrossRef PubMed.
- A. Formagio, C. Volobuff, M. Santiago, C. Cardoso, M. Vieira and Z. Valdevina Pereira, Antioxidants, 2014, 3, 745–757 CrossRef PubMed.
- Y. Lu and Q. Shi, Holz Roh- Werkst., 1995, 53, 17–19 CrossRef CAS.
-
A. Pizzi and K. L. Mittal, Handbook of adhesive technology, CRC press, 2017 Search PubMed.
- H. A. Shnawa, Polym. Bull., 2021, 78, 1925–1940 CrossRef CAS.
- M. Korey, A. Johnson, W. Webb, M. Dietenberger, J. Youngblood and J. Howarter, Green Mater., 2020, 8, 150–161 CrossRef.
- Y.-O. Kim, J. Cho, H. Yeo, B. W. Lee, B. J. Moon, Y.-M. Ha, Y. R. Jo and Y. C. Jung, ACS Sustainable Chem. Eng., 2019, 7, 3858–3865 CrossRef CAS.
- N. Z. Tomić, M. Saeedifar, M. N. Saleh, A. Marinković, D. Zarouchas and S. Teixeira de Freitas, Polym. Test., 2022, 106, 107444 CrossRef.
- S. Jahanshahi, A. Pizzi, A. Abdulkhani and A. Shakeri, Polymers, 2016, 8, 143 CrossRef PubMed.
- Y. Peng, Z. Zheng, P. Sun, X. Wang and T. Zhang, New J. Chem., 2013, 37, 729 RSC.
- J. Ge, X. Shi, M. Cai, R. Wu and M. Wang, J. Appl. Polym. Sci., 2003, 90, 2756–2763 CrossRef CAS.
- A. Gnassiri Wedaina, A. Pizzi, W. Nzie, R. Danwe, N. Konai Siham Amirou, C. Segovia and R. Kueny, J. Renewable Mater., 2021, 9, 477–493 Search PubMed.
- M. Basso, A. Pizzi, C. Lacoste, L. Delmotte, F. Al-Marzouki, S. Abdalla and A. Celzard, Polymers, 2014, 6, 2985–3004 CrossRef.
- M. C. Basso, S. Giovando, A. Pizzi, H. Pasch, N. Pretorius, L. Delmotte and A. Celzard, J. Appl. Polym. Sci., 2014, 131, 40499 CrossRef.
- J.-J. Ge and K. Sakai, J. Wood Sci., 1998, 44, 103–105 CrossRef CAS.
- L. Hojabri, X. Kong and S. S. Narine, Biomacromolecules, 2009, 10, 884–891 CrossRef CAS PubMed.
- S. S. Washburne and W. R. Peterson, J. Am. Oil Chem. Soc., 1972, 49, 694–695 CrossRef CAS.
- J. Nowakowski, J. Prakt. Chem./Chem.-Ztg., 1992, 334, 187–189 CrossRef CAS.
- J. D. O. Rodrigues, C. K. Z. Andrade, R. L. Quirino and M. J. A. Sales, Prog. Org. Coat., 2022, 162, 106557 CrossRef CAS.
- S. Boufi, M. N. Belgacem, J. Quillerou and A. Gandini, Macromolecules, 1993, 26, 6706–6717 CrossRef CAS.
- G. Rokicki and A. Piotrowska, Polymer, 2002, 43, 2927–2935 CrossRef CAS.
- B. Nohra, L. Candy, J.-F. Blanco, C. Guerin, Y. Raoul and Z. Mouloungui, Macromolecules, 2013, 46, 3771–3792 CrossRef CAS.
- H. Blattmann, M. Fleischer, M. Bähr and R. Mülhaupt, Macromol. Rapid Commun., 2014, 35, 1238–1254 CrossRef CAS PubMed.
- J. Ge, X. Shi, M. Cai, R. Wu and M. Wang, J. Appl. Polym. Sci., 2003, 90, 2756–2763, DOI:10.1002/app.12928.
- X. Chen, A. Pizzi, E. Fredon, C. Gerardin, X. Zhou, B. Zhang and G. Du, Int. J. Adhes. Adhes., 2022, 112, 103001 CrossRef CAS.
- O. Faruk and M. Sain, J. Biobased Mater. Bioenergy, 2013, 7, 309–314 CrossRef CAS.
- H. Hatakeyama and T. Hatakeyama, J. Renewable Mater., 2013, 1, 113–123 CrossRef.
- J. Liu, H.-F. Liu, L. Deng, B. Liao and Q.-X. Guo, J. Appl. Polym. Sci., 2013, 130, 1736–1742 CrossRef CAS.
- Z. Wang, S. Xu, W. Hu and Y. Xie, BioEnergy Res., 2013, 6, 896–902 CrossRef CAS.
- D. E. García, W. G. Glasser, A. Pizzi, A. Osorio-Madrazo and M.-P. Laborie, Ind. Crops Prod., 2013, 49, 730–739 CrossRef.
- V. Besse, F. Camara, C. Voirin, R. Auvergne, S. Caillol and B. Boutevin, Polym. Chem., 2013, 4, 4545 RSC.
- L. Annunziata, A. K. Diallo, S. Fouquay, G. Michaud, F. Simon, J.-M. Brusson, J.-F. Carpentier and S. M. Guillaume, Green Chem., 2014, 16, 1947–1956 RSC.
- F. Camara, S. Benyahya, V. Besse, G. Boutevin, R. Auvergne, B. Boutevin and S. Caillol, Eur. Polym. J., 2014, 55, 17–26 CrossRef CAS.
- D. E. García, W. G. Glasser, A. Pizzi, S. Paczkowski and M.-P. Laborie, Eur. Polym. J., 2015, 67, 152–165 CrossRef.
- M. Thébault, A. Pizzi, F. J. Santiago-Medina, F. M. Al-Marzouki and S. Abdalla, J. Renewable Mater., 2017, 5, 21–29 CrossRef.
- N. Esmaeili, M. J. Zohuriaan-Mehr, A. Salimi, M. Vafayan and W. Meyer, Thermochim. Acta, 2018, 664, 64–72 CrossRef CAS.
- M. Thébault, A. Pizzi, S. Dumarçay, P. Gerardin, E. Fredon and L. Delmotte, Ind. Crops Prod., 2014, 59, 329–336 CrossRef.
- M. Thébault, A. Pizzi, H. A. Essawy, A. Barhoum and G. Van Assche, Eur. Polym. J., 2015, 67, 513–526 CrossRef.
- S. Ogawa and Y. Yazaki, Molecules, 2018, 23, 837 CrossRef PubMed.
-
R. E. Kreibich, in Chemistry and Significance of Condensed Tannins, Springer US, Boston, MA, 1989, pp. 457–478 Search PubMed.
- L. Y. Foo and J. J. Karchesy, Phytochemistry, 1989, 28, 3185–3190 CrossRef CAS.
- ed. R. W. Hemingway, J. J. Karchesy and S. J. Branham, Chemistry and Significance of Condensed Tannins, Springer US, Boston, MA, 1989 Search PubMed.
- K. Li, X. Geng, J. Simonsen and J. Karchesy, Int. J. Adhes. Adhes., 2004, 24, 327–333 CrossRef CAS.
- F. Santiago-Medina, G. Foyer, A. Pizzi, S. Caillol and L. Delmotte, Int. J. Adhes. Adhes., 2016, 70, 239–248 CrossRef CAS.
- A. Trosa and A. Pizzi, Holz Roh- Werkst., 2001, 59, 266–271 CrossRef CAS.
- Y. Shirmohammadli, P. Moradpour, A. Abdulkhani, D. Efhamisisi and A. Pizzi, Int. Wood Prod. J., 2019, 10, 16–21 CrossRef.
- A. Ballerini, A. Despres and A. Pizzi, Holz Roh- Werkst., 2005, 63, 477–478 CrossRef CAS.
- H. R. Mansouri, P. Navarrete, A. Pizzi, S. Tapin-Lingua, B. Benjelloun-Mlayah, H. Pasch and S. Rigolet, Eur. J. Wood Wood Prod., 2011, 69, 221–229 CrossRef CAS.
- S. Ghahri, A. Pizzi, B. Mohebby, A. Mirshokraie and H. R. Mansouri, J. Adhes., 2018, 94, 218–237 CrossRef CAS.
- F. Pichelin, M. Nakatani, A. Pizzi, S. Wieland, A. Despres and S. B. T.-F. P. J. Rigolet, For. Prod. J., 2006, 56, 31 CAS.
- C. Kamoun and A. Pizzi, Holzforsch. Holzverwert., 2000, 52, 16–19 CAS.
- A. Pizzi, N. Meikleham and A. Stephanou, J. Appl. Polym. Sci., 1995, 55, 929–933 CrossRef CAS.
- R. Garcia, A. Pizzi and A. Merlin, J. Appl. Polym. Sci., 1997, 65, 2623–2633 CrossRef CAS.
- R. Garcia and A. Pizzi, J. Appl. Polym. Sci., 1998, 70, 1111–1119 CrossRef CAS.
- Z. Wang, S. Zhao, R. Song, W. Zhang, S. Zhang and J. Li, Sci. Rep., 2017, 7, 9664 CrossRef PubMed.
- O. Ajao, M. Benali, A. Faye, H. Li, D. Maillard and M. T. Ton-That, Ind. Crops Prod., 2021, 167, 113435 CrossRef CAS.
- P. L. de Hoyos-Martínez, H. Issaoui, R. Herrera, J. Labidi and F. Charrier-El Bouhtoury, ACS Sustainable Chem. Eng., 2021, 9, 1729–1740 CrossRef.
|
This journal is © The Royal Society of Chemistry 2022 |
Click here to see how this site uses Cookies. View our privacy policy here.