DOI:
10.1039/C6RA00372A
(Paper)
RSC Adv., 2016,
6, 31181-31190
The performance and mechanism for the catalytic oxidation of dibromomethane (CH2Br2) over Co3O4/TiO2 catalysts†
Received
6th January 2016
, Accepted 15th March 2016
First published on 17th March 2016
Abstract
Brominated hydrocarbons are a typical pollutant in exhaust gas from the synthesis process of Purified Terephthalic Acid (PTA), and may cause various environmental problems once emitted into the atmosphere. Dibromomethane (DBM) was employed as the model compound in this study, and a series of Co3O4/TiO2 catalysts with various Co contents were prepared for the catalytic oxidation of DBM. The prepared catalysts were characterized by XRD, BET, SEM, TEM, XPS, H2-TPR and NH3-TPD. Among the prepared catalysts, CoTi-5 (5 wt% Co/TiO2) showed the highest catalytic activity, with T90 at about 346 °C, which was mainly attributed to the enrichment of well-dispersed Co3O4 and the high surface Co3+/Co2+ ratio, as it could provide more surface active sites and active oxygen species. The kinetic study showed that the reaction order of DBM was pseudo first-order and the reaction order of oxygen was approximately zero-order. A plausible DBM reaction mechanism over Co3O4/TiO2 catalysts was also proposed based on the results of in situ FTIR and the analysis of gas products by GC-MS. The reaction process started with the adsorption on surface oxygen vacancies, breakage of C–Br bonds and partial dissociation of C–H bonds with the formation of intermediate species, and then the intermediate species were further oxidized to form CO and CO2.
1. Introduction
In recent years, China has become the largest producer and consumer of Purified Terephthalic Acid (PTA) in the world. With the expansion of the PTA production scale, concerns have been raised about atmospheric emission from PTA exhaust gas,1 and protests against such projects by several large groups have taken place in China in the past years. Typically, the untreated PTA exhaust gas is a mixture of various organic components, including carbon monoxide, acetic acid methyl ester, p-xylene (PX) and brominated hydrocarbon, which can cause great threats to the environment and human health once emitted.2 Up to now, the treatment methods of PTA exhaust gas mainly include activated carbon adsorption, the thermal oxidation method and catalytic oxidation. Catalytic oxidation is considered to be the most promising technology for removal of PTA exhaust gas due to its low consumption of energy, high efficiency and its excellent selectivity towards the formation of the less harmless products.3 However, the presence of brominated hydrocarbon easily causes the catalysts bromine poisoning, and then the catalysts become deactivation. Thus, the key issue of this technology is the available of high activity and high stability catalysts on the removal of brominated hydrocarbon.
At present, various catalytic materials have been used as catalysts for the catalytic oxidation of brominated hydrocarbon, including noble metal and transition metal oxide catalysts.4,5 Although noble mental catalysts exhibit excellent activities, the high cost and low thermal stability restrain their wide applications on industries. Hence, further efforts are demanded to develop the cheap catalysts with high activity and high stability. As a typical transition metal oxide, cobalt oxides have been widely studied for low temperature catalytic oxidation. For example, Rivas et al.6 studied the different synthesis routes of nanocrystalline Co3O4, and found that the nanocrystalline Co3O4 prepared by precipitation method decomposed 1,2-dichloroethane at the lowest temperature, no appreciable deactivation with time on stream. As a halogenated hydrocarbon, brominated hydrocarbon may be similar to chlorinated hydrocarbon in the certain properties. Therefore, Co3O4 may be a good candidate for the catalytic oxidation of brominated hydrocarbon.
In this study, dibromomethane (DBM) chosen as a model brominated hydrocarbon was evaluated in a fixed-bed flow reactor. A series of Co3O4/TiO2 catalysts with various Co contents were prepared by a conventional impregnation method. The physical and chemical properties of the catalysts, as well as DBM conversion, were investigated. The product distribution and catalyst stability were studied, and kinetic parameters of DBM oxidation reaction were also calculated. Furthermore, based on the results of in situ FTIR and the analysis of gas products by GC-MS, a plausible DBM reaction mechanism over Co3O4/TiO2 catalysts was proposed.
2. Experimental section
2.1 Catalyst preparation
A series of Co3O4/TiO2 catalysts with various Co contents (1, 2.5, 5, 10 and 25 wt%, calculated by the weight percentage of Co/TiO2) were prepared by a conventional impregnation method. Commercial P25 TiO2 (Degussa; 80% anatase and 20% rutile phases) was used as a support. In a typical preparation, Co(NO3)3·6H2O used as the Co3O4 precursor was dissolved in ultrapure water, then P25 TiO2 was added into Co(NO3)3·6H2O solution and stirred for 4 h. All the water was evaporated using a rotary evaporation apparatus. The obtained powers were dried at 60 °C overnight and calcined in air at 500 °C for 3 h. The samples were marked for CoTi-1, CoTi-2.5, CoTi-5, CoTi-10 and CoTi-25, respectively.
2.2 Catalyst characterization
The X-ray diffraction (XRD) measurements were recorded on a Shimadzu XRD-6100, and the data were collected in the 2θ range 10–80 °with a scanning velocity of 10° min−1. The BET (Brunauer–Emmett–Teller) surface areas of the samples were determined using N2 adsorption at −196 °C and using a quartz tube (Quantachrome 2200e). The morphology and microstructure of the samples were analyzed by scanning electron microscope (SEM) (JSM-7800F) and transmission electron microscopy (TEM) (JEOL-2100F). The samples were dispersed in ethanol with strong sonication before analysis. The H2-TPR experiments were investigated on the chemisorption analyzer (2920, AutoChem II, Micromeritics). Prior to the measurement, the samples were pretreated in Ar stream at 300 °C for 2 h. After cooling down to 50 °C, the samples were heated to 1000 °C with temperature ramp of 10 °C min−1 in 10% H2/Ar. The NH3-TPD experiments were also investigated on the chemisorption analyzer (2920, AutoChem II, Micromeritics). Prior to the measurement, the 200 mg samples were pretreated in He stream at 400 °C for 2 h. Then NH3 adsorption was performed at 50 °C with 10% NH3/He for 1 h. Next, the samples were purged in He stream for 30 min to remove physically adsorbed NH3, and then heated to 600 °C with temperature ramp of 10 °C min−1 with a 50 mL min−1 He flow. The X-ray photoelectron spectroscopy (XPS) results were recorded with an AXIS UItra DLD (Shimadzu-Kratos) spectrometer with Al Kα as the excitation source, and the C 1s line at 284.8 eV was used as a reference for the binding energy calibration.
2.3 Catalytic activity evaluation
The performances of the catalysts for DBM oxidation were tested in a fixed-bed quartz tube reactor (i.d 6 mm) containing 130 mg catalyst. The typical reactant gas stream was composed of 500 ppm DBM, 10% O2 and N2 as the balance gas in 150 mL min−1, corresponding to a gas hourly space velocity (GHSV) of 60
000 h−1. The reaction was run from 150 to 450 °C in a step mode with a 20 min plateau at each temperature investigated. The inlet and outlet gases were analyzed by a gas chromatograph equipped with a flame ionization detector. The removal efficiency of DBM was defined as: |
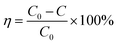 | (1) |
where C0 and C were the inlet and outlet DBM concentrations, respectively. The gas products were detected by gas chromatography and mass spectrometry (GCMS-QP2010, Shimadzu). The final products CO and CO2 were measured using a gas chromatograph (GC-14B, Shimadzu) equipped with a FID detector with methane conversion oven. Br2 and HBr were absorbed in a KI solution firstly. Then, Br2 concentration was determined by the titration with sodium thiosulfate using starch solution as an indicator. The concentration of bromide ions in the bubbled solution was determined by using an ion chromatography. The selectivity of CO, CO2, Br2 and HBr was defined as, respectively: |
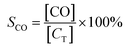 | (2) |
|
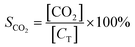 | (3) |
|
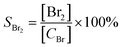 | (4) |
|
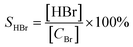 | (5) |
where [CO] and [CO2] were the amount of CO and CO2 (ppm) after the reaction, [CT] was the amount of carbon atom (ppm) in oxidized DBM during the reaction, which could be calculated by eqn (6): |
[CT] = ([CH2Br2]0 − [CH2Br2])
| (6) |
where [CH2Br2]0 and [CH2Br2] were the amount of DBM (ppm) in the gas stream before and after the reaction, respectively. [Br2] and [HBr] were the amount of Br2 and HBr (ppm) after the reaction, [CBr] was the amount of bromine atom (ppm) in oxidized DBM during the reaction, which could be calculated by eqn (7): |
[CBr] = ([CH2Br2]0 − [CH2Br2]) × 2
| (7) |
2.4 Kinetic study
The external diffusion effect was investigated by varying the speed of feed gas while keeping a constant GHSV (60
000 h−1). Similarly, the internal diffusion effect was checked by changing the particle size of the catalysts (as shown in Fig. S2†). The results showed that the catalytic reaction was operated without diffusional limitation below 10% conversion of DBM. The kinetic experiments were carried out under differential condition (the maximum conversion was controlled below 10%). And the reaction rate was calculated as follows: |
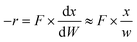 | (8) |
where −r (mol g−1 s−1) was the reaction rate, F (mol s−1) was the inlet flow rate, x (%) was the conversion of DBM, and W was the catalyst weight (g).
2.5 In situ FTIR experiments
In situ FTIR spectra were recorded on a Fourier transform infrared spectrometer (FTIR, Nicolet 6700) equipped with a smart collector and an MCT detector cooled by liquid N2. The diffuse reflectance FTIR measurements were carried out in a high-temperature cell with ZnSe windows. Mass flow controllers and a sample temperature controller were used to simulate the real reaction conditions. In situ FTIR spectra were recorded by accumulating 100 scans at a resolution of 4 cm−1. Prior to each experiment, all the samples were pretreated with 10% O2/N2 at 400 °C for 2 h. Spectra of the clean catalyst surface were collected and used as the background at different temperature. Then, a 500 ppm DBM/10% O2/N2 stream was introduced into the IR cell at 50 °C for 1 h. Subsequently, the catalyst was treated in flowing 10% O2/N2 at different temperature. In situ FTIR spectra were collected at different temperature where a steady was reached.
3. Results and discussion
3.1 Catalytic performance for DBM oxidation
Fig. 1 shows the activity of Co3O4/TiO2 catalysts for DBM oxidation as a function of temperature. It is convenient to compare the catalytic activities of these catalysts by using the reaction temperatures T50 and T90 (corresponding to the DBM conversion = 50 and 90%). The results indicated that the conversion of DBM decreased in the following order, CoTi-5 > CoTi-2.5 > CoTi-10 > CoTi-25 > CoTi-1 > TiO2. Pure TiO2 exhibited the lowest activity with T50 > 450 °C. However, with the presence of Co3O4 species on TiO2, the activities of catalysts were remarkably improved and the conversion curves shifted into lower temperature. Moreover, it was found that Co3O4/TiO2 catalysts exhibited a rising conversion with the increase of Co content from 0% to 5%. CoTi-5 showed the highest activity, and the T90 value was about 346 °C. However, further increasing the Co content to 25%, Co3O4/TiO2 catalysts showed a declined catalytic activity. This result revealed that there were not enough active sites on the surface of the catalyst when the Co content was below 5%, and the catalytic activity dropped. Nevertheless, when the Co content was above 5%, the Co3O4 particles dispersed on the surface began to agglomerate, and the Co3O4 particles on the surface overlapped and the number of active sites was reduced, which decreased the catalytic activity.
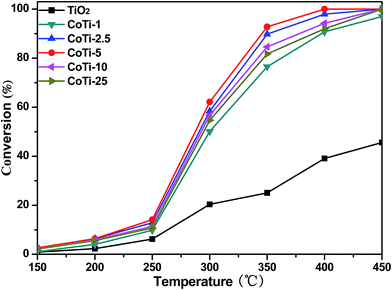 |
| Fig. 1 DBM conversion over Co3O4/TiO2 catalysts with various Co contents; gas composition: 500 ppm DBM, 10% O2 and N2 balance; GHSV = 60 000 h−1. | |
3.2 Catalyst characterization
Fig. 2 shows the XRD patterns of Co3O4/TiO2 catalysts. For all the catalysts, the pure Co phase identified was spinel-structured Co3O4 (PDF#43-1003). The other observed diffraction peaks were attributed to TiO2, which were in the form of anatase and rutile. No representative diffraction peaks of Co3O4 were observed when Co content was less than 5%. The Co3O4 crystalline might be formed in CoTi-5 and some small characteristic peaks were observed, which might be due to its small size or well dispersed state.7 Only when the Co content exceeded 10%, the remarkable XRD peaks representing Co3O4 could be observed in the patterns and increasing Co content enhanced the intensity of the diffraction peaks of the spinel-structured Co3O4.
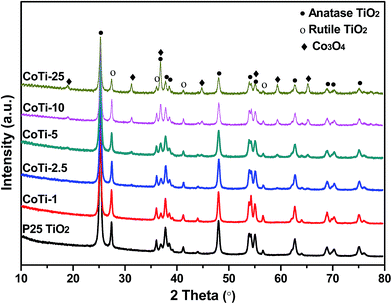 |
| Fig. 2 XRD patterns of Co3O4/TiO2 catalysts with various Co contents. | |
Table 1 displays the specific surface area, pore volume and pore diameter of Co3O4/TiO2 catalysts. After the loading of Co into TiO2, the specific surface area began to decrease, owing to a clogging or covering of the TiO2 support. Moreover, when the Co content increased from 1 to 5%, the specific surface area gradually increased. However, with further increasing the Co content to 25%, the specific surface area began to decrease. CoTi-5 had the biggest specific surface area among all the Co3O4/TiO2 catalysts, and it might have more active sites for catalytic reaction.
Table 1 Specific surface area, pore volume and pore diameter of Co3O4/TiO2 catalysts
Samples |
Specific surface area (m2 g−1) |
Pore volume (cm3 g−1) |
Pore diameter (nm) |
TiO2 |
53.233 |
0.13 |
23.277 |
CoTi-1 |
34.635 |
0.304 |
25.34 |
CoTi-2.5 |
36.999 |
0.314 |
24.516 |
CoTi-5 |
40.32 |
0.362 |
24.785 |
CoTi-10 |
32.433 |
0.275 |
24.871 |
CoTi-25 |
29.473 |
0.202 |
23.277 |
To obtain the microscopic morphology information of the catalysts, transmission electron microscope (TEM) analysis of Co3O4/TiO2 catalysts was performed. As shown in Fig. 3, the TEM images in Fig. 3(a–e) exhibited evenly distributed Co3O4/TiO2 nanoparticles with diameters of 30–40 nm. The high-resolution transmission electron microscopy (HRTEM) image of CoTi-25 (Fig. 3(f)) further confirmed the crystalline structure of Co3O4/TiO2. As seen from the figure, the interplanar spacing of 0.28 nm and 0.35 nm corresponded to Co3O4 (220) and TiO2 (101),8,9 respectively, indicating that cobalt was loaded on the surface of TiO2 and existed in the form of Co3O4, consistent with the XRD results.
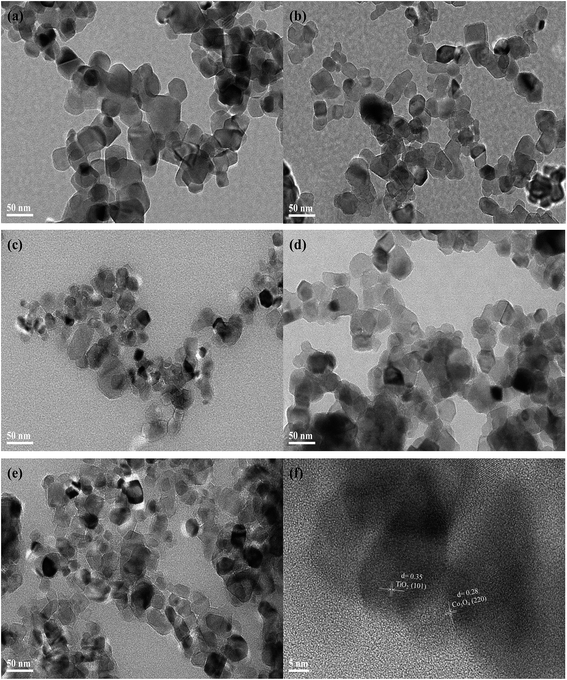 |
| Fig. 3 TEM images of (a) CoTi-1, (b) CoTi-2.5, (c) CoTi-5, (d) CoTi-10 and (e) CoTi-25 and HRTEM image of (f) CoTi-25. | |
XPS is a good tool to investigate the surface element composition, element oxidation sate, and adsorbed species of a material.10 Fig. 4 shows the Co 2p and O 1s spectra of Co3O4/TiO2 catalysts. As shown in Fig. 4(a), for all the Co3O4/TiO2 catalysts with various Co contents, there were two main peaks corresponding to Co 2p3/2 and Co 2p1/2 at 779.9–781.3 and 795.1–797.2 eV, respectively, with satellite peaks. By performing peak-fitting deconvolution, the main Co 2p3/2 peak could be separated into two peaks, the lower binding energy was belong to Co3+, while the higher binding energy could be ascribed to Co2+.11 A spectral feature that could distinguish between Co2+ and Co3+ was a satellite for Co2+ peak, because photoemitted electrons interacted with core vacancies and valence electrons of Co2+ but not with those of Co3+.12 As shown in Table 2, the surface Co3+/Co2+ ratio increased from 0.23 to 1.23 as Co content from 1 to 5%, indicating an increase of Co3+ percentage on the catalyst surface. However, the surface Co3+/Co2+ ratio decreased as further increasing Co content, which illustrated that excessive Co3O4 loading decreased the surface Co3+/Co2+ ratio. The cation distribution of the spinel-structured Co3O4 had been demonstrated to be Co2+[Co3+]2O4, and the more surface Co3+/Co2+ ratio could lead to more anionic defects. This had been shown to bring excess surface oxygen and promote gas molecular adsorption.13
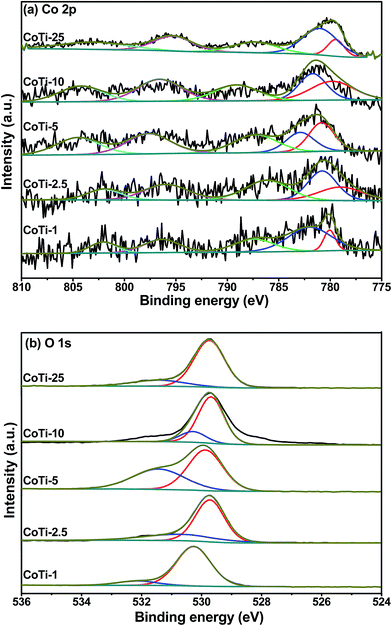 |
| Fig. 4 XPS spectra of (a) Co 2p and (b) O 1s for Co3O4/TiO2 catalysts with various Co contents. | |
Table 2 XPS parameters of Co3O4/TiO2 catalysts
Samples |
Co3+/Co2+ |
Oads/Olat |
CoTi-1 |
0.23 |
0.13 |
CoTi-2.5 |
0.69 |
0.38 |
CoTi-5 |
1.32 |
0.76 |
CoTi-10 |
1.11 |
0.23 |
CoTi-25 |
0.30 |
0.22 |
As shown in Fig. 4(b), one can see an asymmetrical O 1s XPS peak of the catalysts that could be resolved into two components at BE = 529.7–530.3 and 530.4–532.1 eV. The former was due to the surface lattice oxygen (Olat), whereas the latter was due to the surface adsorbed oxygen (Oads).14–16 It was also found from Table 2 that the surface Oads/Olat ratio decreased in the order of CoTi-5 > CoTi-2.5 > CoTi-10 > CoTi-25 > CoTi-1. The formation of oxygen adsorbed species was due to the presence of surface oxygen vacancies on Co3O4/TiO2 catalysts, which implied that there might be the coexistence of Co3+ and Co2+ ions on Co3O4/TiO2 catalysts. Such a deduction was supported by the Co 2p3/2 XPS results of the catalysts. In general, surface adsorbed oxygen is more active than lattice oxygen due to its high mobility, and it plays an important role in catalytic oxidation reaction.11 Hence, more surface adsorbed oxygen will lead to the stronger oxidization ability, which is consistent with our DBM oxidation results.
Fig. 5 shows the H2-TPR profiles of Co3O4/TiO2 catalysts. As shown in the figure, the H2-TPR profiles of CoTi-1, CoTi-10 and CoTi-25 exhibited two reduction peaks, which were related to the reduction of Co3+ to Co2+ at lower temperature and Co2+ to Co0 at higher temperature, respectively.7 Whereas the H2-TPR profiles of CoTi-2.5 and CoTi-5 exhibited three reduction peaks between 300 °C and 500 °C, the first peak was attributed to the reduction process of some surface oxygen, and the second and third peaks were attributed to the reduction of Co3+ to Co2+ and Co2+ to Co0, respectively.17 It could also be observed that these reduction peaks shifted to lower temperature with an increase in the Co content. The peak at 434 °C in CoTi-1 could be related to the reduction peak of isolated Co, and the peak at 640 °C could be attributed to the strong interaction between Co and Ti.18 When Co content was higher than 2.5%, two reduction peaks appeared at about 419 °C and 491 °C were observed, which could be assigned to Co3O4 crystalline. As further increasing the Co content, these reduction peaks slightly shifted to higher temperature, which might be due to the sintering.19 CoTi-5 showed the best reducibility, which probably resulted in its high catalytic performance for DBM oxidation.
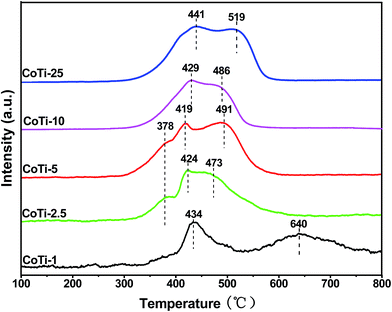 |
| Fig. 5 H2-TPR profiles of Co3O4/TiO2 catalysts with various Co contents. | |
Surface acidities of the catalysts are found to have significantly influence on VOCs oxidation as they provide sites for the chemisorption of VOCs molecules.20 Therefore, surface acidities of the catalysts are measured by NH3-TPD, and the results are shown in Fig. 6. For all the Co3O4/TiO2 catalysts, a broad shoulder peak appeared in the range of 120 °C and 150 °C, which could be the weak acid sites. Moreover, the amount of the acid sites decreased in order of CoTi-5 > CoTi-2.5 > CoTi-10 > CoTi-25 > CoTi-1. CoTi-5 had the most acid sites, which could be beneficial for the catalytic oxidation of DBM.
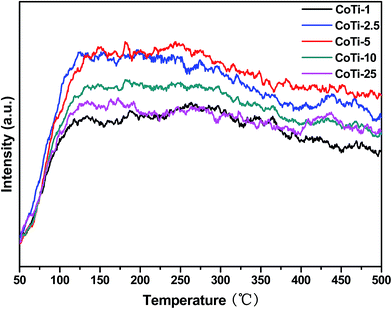 |
| Fig. 6 NH3-TPD profiles of Co3O4/TiO2 catalysts with various Co contents. | |
3.3 Analysis of products
It should be noticed that for brominated hydrocarbon oxidation, high conversion is not the only criterion for good catalysts, and selectivity of the products is more important. The ideal decomposition products of brominated hydrocarbon are CO2 and HBr or Br2. Thus, the products in outlet at each evaluated temperature over CoTi-5 were analyzed by GC-MS and the results were listed in Table 3. As seen in Table 3, the byproduct CH3Br was emerged at low temperature (below 200 °C) and it was disappeared with the increase of temperature. CO, HBr and H2O were always existed at each evaluated temperature, CO2 was generated above 200 °C and Br2 was generated above 350 °C. Up to 400 °C, CH2Br2 was completely disappeared.
Table 3 Products in outlet at each evaluated temperature over CoTi-5
Temperature (°C) |
Detected substances |
150 |
CH2Br2, CH3Br, CO, HBr, H2O |
200 |
CH2Br2, CH3Br, CO, CO2, HBr, H2O |
250 |
CH2Br2, CO, CO2, HBr, H2O |
300 |
CH2Br2, CO, CO2, HBr, H2O |
350 |
CH2Br2, CO, CO2, HBr, Br2, H2O |
400 |
CO, CO2, HBr, Br2, H2O |
450 |
CO, CO2, HBr, Br2, H2O |
Fig. 7 shows the DBM conversion and selectivity for CO, CO2, Br2 and HBr as a function of temperature over CoTi-5. As can be seen, the main products of DBM conversion were CO, CO2 and HBr at a low temperature range (below 300 °C). However, with the increase of temperature, the amount of CO2 was gradually improved and its selectivity was exceeded 50% at 335 °C due to the further oxidation of CO. When the temperature was above 350 °C, Br2 was generated, which might be attributed to the Deacon reaction (4HBr + O2 = 2Br2 + 2H2O).21 With the further increase of temperature, the selectivity for Br2 was also further improved, and its selectivity got to 31% at 450 °C. Therefore, the main products of DBM conversion were CO, CO2, HBr and Br2 at a high temperature range (above 350 °C). However, the deep oxidation (the oxidation of CO to CO2) still needed to be further improved.
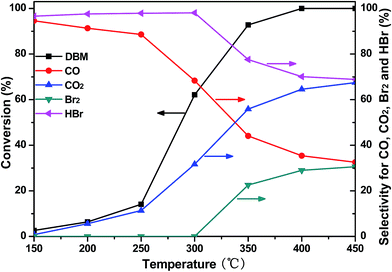 |
| Fig. 7 DBM conversion and selectivity for CO, CO2, Br2 and HBr as a function of temperature over CoTi-5. | |
3.4 Catalyst stability
For commercial application, the stability of the catalyst is an important factor. The stability of the catalyst in the reaction was tested by reusing the catalyst in consecutive oxidation recycles and by performing long catalytic runs at constant oxidation temperature. As shown in Fig. 8, CoTi-5 was submitted to successive oxidation cycles. In this case, CoTi-5 also maintained its catalytic activity well after five oxidation cycles. The evolution of DBM conversion with time on stream at 300 °C over CoTi-5 is presented in Fig. S3.† CoTi-5 could maintain its catalytic activity well after 600 min of reaction. These results showed that CoTi-5 had a good stability for DBM oxidation.
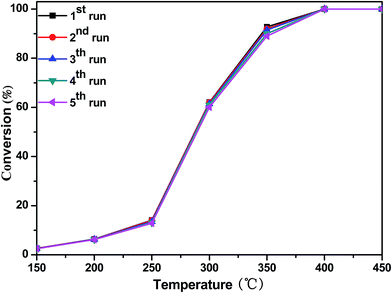 |
| Fig. 8 DBM conversion as a function of temperature over CoTi-5 for first to fifth run (GHSV = 60 000 h−1). | |
3.5 Kinetic study
Fig. 9 shows DBM conversion as a function of temperature over CoTi-5 under various oxygen and inlet DBM concentrations. As shown in Fig. 9(a), the conversion of DBM increased with the increase of oxygen concentration, and the observed T50 changed from 313 °C to 278 °C (corresponding to the oxygen concentrations of 2% and 20%, respectively). In Fig. 9(b), it was found that the conversion of DBM decreased with the increase of DBM concentration. Observed T50 changed from 287 °C to 314 °C (corresponding to the DBM concentrations of 500 ppm and 3000 ppm, respectively). These data illustrated that both the oxygen and the DBM concentrations might be not very sensitive parameters. To gain further insight in this question, kinetic studies were carried out by investigating the effect of oxygen and inlet DBM concentrations on the reaction rate (−r) as shown in Fig. 10. The conversions were controlled below 10% to obtain initial reaction rate for all conditions. It was found that all the data could be explained by the power law equation as follows: |
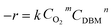 | (9) |
where k was the kinetic constant, CO2 (mol N m−3) was the O2 concentration, CDBM (mol N m−3) was the inlet DBM concentration, m and n were the apparent reaction orders of oxygen and DBM, respectively. The values of m and n were obtained from the slope of each line in Fig. 10(b) and (d).
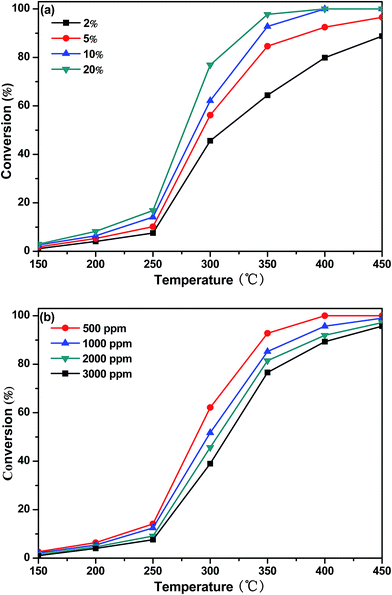 |
| Fig. 9 DBM conversion as a function of temperature over CoTi-5 in various (a) O2 and (b) DBM concentrations (GHSV = 60 000 h−1). | |
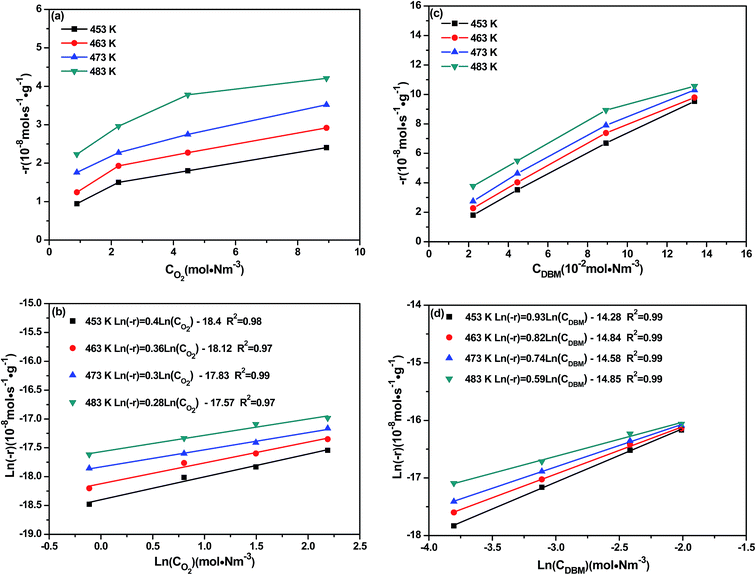 |
| Fig. 10 Dependence of the DBM reaction rate on the (a and b) oxygen partial pressure and (c and d) DBM partial pressure over CoTi-5. | |
As shown in Fig. 10(a), the reaction rate grew nonlinearly with the increase of oxygen concentration in the studied temperature range. In Fig. 10(c), a similar tendency could also be seen, but the growth of the reaction rate seemed to be more rapidly with the increase of DBM concentration. Really, compared with the values of n, the values of m were lower (shown in Table 4). Particularly, the reaction order of DBM was pseudo first-order, which indicated that the adsorption of DBM on the catalyst surface was difficult. However, strong adsorption caused apparent zero-order for reaction, because all the active sites on the catalyst surface were occupied. For oxygen as a reactant, the reaction order was closed to zero-order. It could be supposed that if the intermediates could directly react with gas-phase oxygen, the reaction order of oxygen would be approximate first-order, thus indicating that DBM molecular might not directly react with gas-phase oxygen. Moreover, on the basis of Arrhenius equation, the apparent activation energy (Ea) was also obtained.
Table 4 Kinetic parameters for DBM oxidation over CoTi-5
Kinetic parameter |
453 K |
463 K |
473 K |
483 K |
m |
0.4 |
0.36 |
0.3 |
0.28 |
n |
0.93 |
0.82 |
0.74 |
0.59 |
Ea (kJ mol−1) |
23.4 |
3.6 In situ FTIR experiments
The kinetic results showed an important feature of the catalytic reaction, which was the apparent reaction order of oxygen or DBM was between zero- and first-order. However, kinetic method tended to be a general method, which still could not explain the reaction mechanism directly. For example, the understanding in regard to intermediate products of the catalytic reaction needed more direct tools. Hence, the in situ FTIR method was used to study the mechanism on the interaction between DBM molecule and Co3O4/TiO2 catalysts.
In situ FTIR spectra collected at different temperature over CoTi-5 are shown in Fig. 11(a) and (b). After exposed to the mixture of 500 ppm DBM, 10% O2 and N2 balance, the bands at 3072, 2992, 1600 and 1201 cm−1 were observed. The bands at 3072, 2992 and 1201 cm−1 were attributed to antisymmetric stretching, symmetric stretching and wagging of methylene, respectively, which were the approximated mode of DBM molecule on the surface of CoTi-5 at 50 °C.22,23 With the increase of temperature, the intensity of these bands decreased and disappeared above 100 °C, suggesting either desorption or consumption of the DBM molecules. The band at 1600 cm−1 was assigned to H2O absorbed on the catalyst surface,24 which gradually disappeared with the increase of temperature. Meanwhile, the disappearance of DBM was accompanied by appearance of the new bands of 2960, 2935, 2873, 2835, 1560, 1380, 1365 and 1215 cm−1. Among them, the bands at 2960, 2873, 1560, 1380 and 1365 cm−1 (including 2881 cm−1 developed at 150 °C) were assigned to adsorbed formate species.25,26 While the other bands at 2935 and 2835 cm−1 were assigned to methyl antisymmetric stretching and symmetric stretching of absorbed methoxy groups.27,28 The band at 1215 cm−1 was developed at 250 °C, which was assigned to bicarbonate.29 All these bands developed with the oxidation of the absorbed DBM, which meant that the formate groups and methoxy groups were the main intermediate species generated on the surface of CoTi-5. With the further increase of temperature, the intensity of the bands decreased distinctly at 300 °C and disappeared at 350 °C. It indicated that CoTi-5 could degrade intermediate products to CO and CO2 at high temperature. Then the adsorbed formate species and methoxy species were hard to be observed above 300 °C. Moreover, the desorption of CO, CO2 and HBr as final products was supposed to be very quick, which was evident that no bands assigned to these species could be observed.
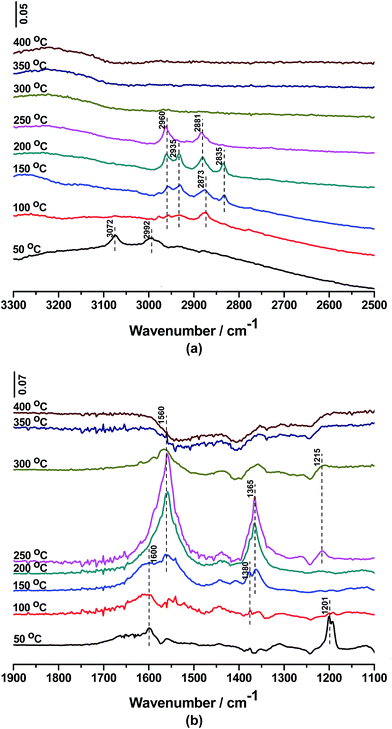 |
| Fig. 11 In situ FTIR spectra of DBM oxidation over CoTi-5 (a, b) as a function of temperature. | |
Based on the results of in situ FTIR and reported mechanisms of CH2Cl2 oxidation over various catalysts,24,30,31 a plausible reaction mechanism could be proposed for catalytic oxidation of DBM over Co3O4/TiO2 catalysts, as shown in Fig. 12. The reaction pathways mainly consist of two sequential cycles: formation of formate species and oxidation of formate species to CO and CO2. The reaction steps were described as follows: (1) the adsorption of DBM molecule on surface oxygen vacancies of the catalyst. (2) The adsorbed DBM were attacked by the surface adjacent nucleophilic oxygen species. (3) The two bromine atoms were substituted by oxygen atoms, generating absorbed formaldehyde (hemiacetal species).30 (4) The adsorption of gas-phase oxygen on the surface oxygen vacancies to replenish the consumed oxygen. (5) The Cannizzaro reaction between absorbed formaldehyde and hemiacetal species formed the adsorbed formate species and methoxy species. (6) The adsorbed formate species and methoxy species were further attacked by surface active oxygen species to form CO and CO2. The Br species adsorbed active sites could be removed in the form of HBr via the reaction of surface of hydroxyl groups and the dissociatively adsorbed Br, or in the form of Br2 at high temperature via the Deacon reaction (4HBr + O2 = 2Br2 + 2H2O).
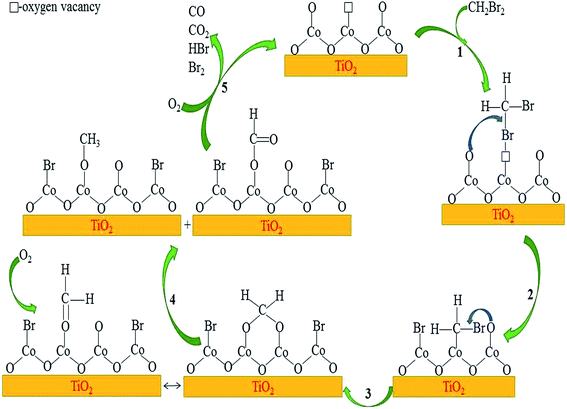 |
| Fig. 12 A plausible reaction mechanism for DBM oxidation over Co3O4/TiO2 catalysts. | |
4. Conclusions
A series of Co3O4/TiO2 catalysts with various Co contents prepared by a conventional impregnation method were characterized by XRD, BET, SEM, TEM, XPS, H2-TPR and NH3-TPD, and used in catalytic oxidation of DBM, some new information was obtained in this study. Firstly, Co3O4/TiO2 catalysts were found to be very active for DBM oxidation, which had not been reported before. The highest catalytic activity with T90 at about 346 °C was obtained over CoTi-5, which might be attributed to the enrichment of well dispread Co3O4 and high surface Co3+/Co2+ ratio, as it could provide more surface active sites and active oxygen species. Secondly, the kinetic study showed that the reaction order of DBM was pseudo first-order and the reaction order of oxygen was approximate zero-order over CoTi-5, respectively. Thirdly, some reaction intermediates such as formate species and methoxy species were detected by in situ FTIR, based on which a plausible DBM reaction mechanism over Co3O4/TiO2 catalysts was proposed. The reaction process started with the adsorption on surface oxygen vacancies, breakage of C–Br bonds and partial dissociation of C–H bonds with the formation of intermediate species, and then the further dissociation of C–H bonds and the oxidation of CO to CO2 were started, and finally the reaction recycle was finished.
Acknowledgements
This work was supported by the Major State Basic Research Development Program of China (973 Program, No. 2013CB430005).
References
- B. Chen, J. Carson, J. Gibson, R. Renneke, T. Tacke, M. Reisinger, R. Hausmann, A. Geisselmann, G. Stochniol and P. Panster, Chemical Industries, Marcel Dekker, New York, 2003, pp. 179–190 Search PubMed.
- M. Moreton, Int. J. Hydrocarbon Eng., 1998, 3, 57–58 CAS.
- T. Cai, H. Huang, W. Deng, Q. Dai, W. Liu and X. Wang, Appl. Catal., B, 2015, 166–167, 393–405 CrossRef CAS.
- K. Ding, A. R. Derk, A. Zhang, Z. Hu, P. Stoimenov, G. D. Stucky, H. Metiu and E. W. McFarland, ACS Catal., 2012, 2, 479–486 CrossRef CAS.
- G. R. Lester, Catal. Today, 1999, 53, 407–418 CrossRef CAS.
- B. de Rivas, R. López-Fonseca, C. Jiménez-González and J. I. Gutiérrez-Ortiz, J. Catal., 2011, 281, 88–97 CrossRef CAS.
- Y. Liu, Y. Wang, H. Wang and Z. Wu, Catal. Commun., 2011, 12, 1291–1294 CrossRef CAS.
- L. Hu, Q. Peng and Y. Li, J. Am. Chem. Soc., 2008, 130, 16136–16137 CrossRef CAS PubMed.
- S. Zhao, Z. Li, Z. Qu, N. Yan, W. Huang, W. Chen and H. Xu, Fuel, 2015, 158, 891–897 CrossRef CAS.
- F. Wang, H. Dai, J. Deng, G. Bai, K. Ji and Y. Liu, Environ. Sci. Technol., 2012, 46, 4034–4041 CrossRef CAS PubMed.
- H. Hu, S. Cai, H. Li, L. Huang, L. Shi and D. Zhang, ACS Catal., 2015, 5, 6069–6077 CrossRef CAS.
- T. Chuang, C. Brundle and D. Rice, Surf. Sci., 1976, 59, 413–429 CrossRef CAS.
- B. Meng, Z. Zhao, X. Wang, J. Liang and J. Qiu, Appl. Catal., B, 2013, 129, 491–500 CrossRef CAS.
- A. Carley, M. Roberts and A. Santra, J. Phys. Chem. B, 1997, 101, 9978–9983 CrossRef CAS.
- N. Yamazoe, Y. Teraoka and T. Seiyama, Chem. Lett., 1981, 1767–1770 CrossRef CAS.
- J. Fierro and L. G. Tejuca, Appl. Surf. Sci., 1987, 27, 453–457 CrossRef CAS.
- Q. Wang, Y. Peng, J. Fu, G. Z. Kyzas, S. M. R. Billah and S. An, Appl. Catal., B, 2015, 168–169, 42–50 CrossRef CAS.
- M. M. Yung, E. M. Holmgreen and U. S. Ozkan, J. Catal., 2007, 247, 356–367 CrossRef CAS.
- C. Resini, T. Montanari, L. Nappi, G. Bagnasco, M. Turco, G. Busca, F. Bregani, M. Notaro and G. Rocchini, J. Catal., 2003, 214, 179–190 CrossRef CAS.
- Q.-Y. Chen, N. Li, M.-F. Luo and J.-Q. Lu, Appl. Catal., B, 2012, 127, 159–166 CrossRef CAS.
- C.-Y. Chen and J. J. Pignatello, Appl. Catal., B, 2013, 142–143, 785–794 CrossRef CAS.
- M.-T. Chen, C.-F. Lien, L.-F. Liao and J.-L. Lin, J. Phys. Chem. B, 2003, 107, 3837–3843 CrossRef CAS.
- F. Solymosi and J. Rasko, J. Catal., 1995, 155, 74–81 CrossRef CAS.
- Y. Wang, A.-P. Jia, M.-F. Luo and J.-Q. Lu, Appl. Catal., B, 2015, 165, 477–486 CrossRef CAS.
- C.-C. Chuang, W.-C. Wu, M.-C. Huang, I.-C. Huang and J.-L. Lin, J. Catal., 1999, 185, 423–434 CrossRef CAS.
- C. Ma, D. Wang, W. Xue, B. Dou, H. Wang and Z. Hao, Environ. Sci. Technol., 2011, 45, 3628–3634 CrossRef CAS PubMed.
- W.-C. Wu, C.-C. Chuang and J.-L. Lin, J. Phys. Chem. B, 2000, 104, 8719–8724 CrossRef CAS.
- C. Su, J.-C. Yeh, C.-C. Chen, J.-C. Lin and J.-L. Lin, J. Catal., 2000, 194, 45–54 CrossRef CAS.
- C.-W. Tang, L.-C. Hsu, S.-W. Yu, C.-B. Wang and S.-H. Chien, Vib. Spectrosc., 2013, 65, 110–115 CrossRef CAS.
- I. Maupin, L. Pinard, J. Mijoin and P. Magnoux, J. Catal., 2012, 291, 104–109 CrossRef CAS.
- S. Cao, H. Wang, F. Yu, M. Shi, S. Chen, X. Weng, Y. Liu and Z. Wu, J. Colloid Interface Sci., 2016, 463, 233–241 CrossRef CAS PubMed.
Footnote |
† Electronic supplementary information (ESI) available. See DOI: 10.1039/c6ra00372a |
|
This journal is © The Royal Society of Chemistry 2016 |
Click here to see how this site uses Cookies. View our privacy policy here.