DOI:
10.1039/C4RA00583J
(Paper)
RSC Adv., 2014,
4, 21277-21283
Directly hydrothermal growth of ultrathin MoS2 nanostructured films as high performance counter electrodes for dye-sensitised solar cells†
Received
20th January 2014
, Accepted 30th April 2014
First published on 30th April 2014
Abstract
Ultrathin MoS2 nanostructured films with a surface exposed layered nanosheet structure were successfully grown onto fluorine-doped tin oxide (FTO) conducting substrates by a facile one-pot hydrothermal method. After calcination at 400 °C in argon, the resulting MoS2 films were directly used as counter electrodes (CEs) for dye-sensitised solar cells (DSSCs), exhibiting excellent DSSC performance. The hydrothermal reaction temperature and molar ratio of reaction precursors were found to have significant influence on the resulting structure of MoS2, and thus the DSSCs performance. It was found that ultrathin MoS2 nanostructured film with surface exposed layered nanosheet structures can be obtained by hydrothermal treatment of a reaction solution including (NH4)6Mo7O24·4H2O and NH2CSNH2 with a molar ratio of 1
:
28 at 150 °C for 24 h. The obtained MoS2 films as CEs for DSSCs showed the best light conversion efficiency of 7.41%, which was superior to Pt-based DSSCs (7.13%). The excellent DSSC performance could be due to high stability, good electrical conductivity, rich electrocatalytically active sites, and good electrolyte transport properties of the fabricated MoS2 film with a surface layered nanosheet structure. This study demonstrated the applicability of a facile hydrothermal approach for direct growth of highly electrocatalytically active metal chalcogenide films as high performance CEs for DSSCs.
Introduction
Development of low cost, resource abundant and highly catalytically active electrocatalysts as counter electrode (CE) materials for dye-sensitised solar cells (DSSCs) has attracted great research attention because of the high cost and the scarcity of Pt-based electrocatalysts in conventional DSSCs.1,2 For DSSCs, a promising electrocatalyst as a CE material should have the following advantages: low cost, abundance, good electrical conductivity, superior electrocatalytic activity and high stability.3,4 Low cost and resource abundance can ensure the large-scale production and application of the developed electrocatalyst for DSSCs.5 Good electrical conductivity and high electrocatalytic activity of the electrocatalyst can provide superior electron transfer property and high redox efficiency of iodide/triiodide couple, thus high performance DSSCs.6 Also, high stability of an excellent electrocatalyst is critically important to develop high efficiency solar cells for long-term use.7 Based on the foregoing discussion, searching more electrocatalysts as CE materials with the advantages of the foregoing clarification is highly desired to develop high performance DSSCs.
To date, tremendous efforts have been executed to explore low-cost and resource abundant alternative materials to achieve comparable electrocatalytic activities to Pt-based electrocatalysts, such as carbonaceous materials,8–10 conducting polymers,11 metal chalcogenides,12–14 nitrides,15 carbides3 and phosphides.16 Many investigated materials as electrocatalysts have shown great potential to replace Pt-based electrocatalysts for DSSCs.17 Recently, molybdenum chalcogenide such as MoS2 has exhibited excellent performance as CE material for DSSCs.18 As a layered 2-dimensional material, MoS2 is traditionally used as solid state lubricant and catalyst for hydrodesulfurisation and hydrogen evolution reaction.19–21 Due to the analogue structure to graphene and potential electrocatalytic activity, MoS2 has been investigated to be a promising CE material for DSSCs.13 In some reports, very thick MoS2 films with opaque property (ca. 3.0–20 μm in thickness) were fabricated to achieve desired electrocatalytic activities and high solar cell efficiencies.13,14,22–25 Recently, varieties of MoS2-based composites such as MoS2/graphene,14,22 MWCNT/MoS2,23 and MoS2/C25 have become popular CE materials for DSSCs. Compared to pure MoS2 electrocatalyst, the composites exhibited significantly improved DSSCs performance.23,25 Amongst all investigated MoS2-based DSSCs (see Table S1, ESI†), the highest light conversion efficiency of 7.69% has been reported using an opaque MoS2/C film with 12 μm in thickness as CE material, which is superior to Pt-based DSSCs (6.74%).25 To date, the highest DSSCs efficiency of 7.59% can be reached using a pure MoS2 as CE material with a thickness of ca. 20 μm, however, this performance is still lower than that of Pt-based DSSCs (7.64%).13 Very recently, few reports claimed to achieve MoS2 films with several hundred nanometres in thickness and good optical transmittance,18,26 but the light conversion efficiencies of DSSCs made of these MoS2 film CEs are still lower than that of Pt-based DSSCs. To avoid complex preparation process and achieve high solar cell efficiency, development of pure MoS2 nanostructured film directly grown onto conductive substrate is deserved to be further investigated.
Herein, we report a hydrazine assisted hydrothermal method to directly grow ultrathin MoS2 nanostructured film onto FTO conductive substrate with surface exposed layered nanosheet structure. After calcination at 400 °C in argon, the resulting MoS2 film as CE material for DSSCs exhibits an overall light conversion efficiency of 7.41%, which is higher than that of Pt-based DSSCs (7.13%). The superior DSSCs performance has been investigated and explained by the measurements of cyclic voltammetry (CV), electrochemical impedance spectroscopic (EIS) technique and Tafel polarisation. Also, the effect of some experimental parameters such as reaction temperature and the molar ratio of reaction precursors on the MoS2 structure and resulting solar cell performance has been investigated and discussed in detail based on the experimental results.
Experimental section
Preparation of MoS2 nanostructured films
The MoS2 nanostructured films were directly grown onto fluorine-doped tin oxide (FTO) conductive substrates via a low-temperature hydrothermal method. In a typical preparation, different amount (2.84 mmol, 5.67 mmol, 11.34 mmol or 17.01 mmol) of NH2CSNH2 (ACS reagent, ≥99.0%) was firstly added to 24 mL of deionised water and then stirred for 1 h. The resulting solution was clear with a pH of ca. 5.5. Subsequently, 0.405 mmol (NH4)6Mo7O24·4H2O (Reagent grade, Ajax Chemicals) was added to the above solutions containing different amount of NH2CSNH2, respectively, and further stirred for another 30 min. The resulting solutions were clear with a pH of ca. 5.0. Finally, 6.0 mL of N2H4·H2O (35 wt% solution in water, ACROS Organics) was added to the above solutions with vigorous stirring for another 10 min. The pH of the final solution was ca. 10.0. The mixture was then transferred into a 100 mL of Teflon lined autoclave and kept at different temperatures (120, 150, 180 and 210 °C) for 24 h. Prior to hydrothermal reaction, a piece of pre-cleaned FTO conducting glass (15 Ω square−1, Nippon Sheet Glass, Japan) with the conduction side facing up was placed into the Teflon lined autoclave. After hydrothermal reaction, the autoclaves were allowed to cool down at room temperature and the obtained products were rinsed with adequate amount of deionised water and CS2, and then dried at room temperature. The resulting products were further annealed in a tube furnace at 400 °C for 1 h under continuous flow of argon gas prior to solar cell fabrication. The prepared MoS2 counter electrodes were denoted as MS–X–Y, where X is reaction temperature and Y stands for molar ratio of reaction precursors of (NH4)6Mo7O24·4H2O and NH2CSNH2.
Characterisation
Scanning electron microscope (SEM, JSM-7001F), transmission electron microscopy (TEM, Philips F20), and X-ray diffraction (XRD, Shimadzu XRD-6000 diffractometer) were used to characterise the sample structure. Chemical compositions of the samples were analysed by X-ray photoelectron spectroscopy (XPS, Kratos Axis ULTRA incorporating a 165 mm hemispherical electron energy analyser).
Measurements
For a meaningful comparison, commercially available TiO2 nanoparticle films (Dyesol, Australia) were used and pre-calcinated at 500 °C for 30 min in air before dye (N719, Dyesol, Australia) adsorption for another 24 h. The dye-sensitised TiO2 photoanodes having an active area of 0.25 cm2 were further assembled with the predrilled commercial platinum counter electrodes (Dyesol, Australia) into a sandwich-type cell and then sealed with a hot-melt gasket of the ionomer Surlyn® 1702 (Deysol, Australia). The DSSCs made of MoS2 counter electrodes were also assembled as above. A 500 W Xe lamp (Trusttech Co., Beijing) with an AM 1.5G filter (Sciencetech, Canada) was used as the light source. The Light intensity was measured by a radiant power meter (Newport, 70260) coupled with a broadband probe (Newport, 70268). The photovoltaic measurements of DSSCs were recorded by a scanning potentiostat (Model 362, Princeton Applied Research, US). Cyclic voltammograms (CVs) were recorded using CHI 760D (CH Instruments, Inc.) in the voltage range of −0.40–1.2 V (vs. Ag/AgCl reference electrode) at a scan rate of 100 mV s−1. The electrolyte for CV measurements consisted of 10 mM LiI, 1 mM I2 and 0.1 M LiClO4 in acetonitrile.13,27 A platinum mesh was used as counter electrode. A symmetrical dummy cell, consisting of two identical MoS2 films (or Pt electrodes), was prepared. These dummy cells containing the same operating electrolyte used for DSSCs were utilised for measuring electrochemical impedance spectroscopic (EIS) and Tafel polarisation curves. The EIS experiments were conducted with an impedance analyser (CHI 760D, CH Instruments, Inc.). The frequency range was 105 to 10−1 Hz where the perturbation amplitude was 10 mV. All measurements were carried out at room temperature in dark condition. Tafel polarisation curves were recorded by electrochemical workstation (CHI 760D, CH Instruments, Inc.) in two electrode system with a scan rate of 10 mV s−1.
Results and discussion
Structure characteristics
The MoS2 films with different structure were directly grown onto FTO conductive substrates by a facile one-pot hydrothermal method. In the process of hydrothermal reaction, hydrazine is believed to initially act as a ligand to form hexavalent molybdenum complex, which can effectively inhibit the quick hydrolysis of (NH4)6Mo7O24·4H2O in reaction solution, beneficial for the formation of MoS2 structure.28 Furthermore, hydrazine can act as a mild reducing agent to reduce Mo6+ to Mo4+ (eqn (1)), and then Mo4+ ions react with S2− originated from the decomposition of thiourea under hydrothermal condition to form molybdenum disulphide in the reaction solution (eqn (2)–(4)).29 The molar ratios of reaction precursors and reaction temperature have important influence on the morphology and composition of the resulting products, which deserves a further investigation. |
Mo6+ +2NH2–NH2 + 2OH− → Mo4+ + 2H2O + 2N2↑
| (1) |
|
CH4N2S + OH− → SH− + CH2N2 + H2O
| (2) |
|
SH− + OH− → S2− + H2O
| (3) |
Fig. 1 shows the XRD patterns of as-synthesised sample fabricated at 150 °C for 24 h (MS-150-28) and calcined samples with different molar ratios of reaction precursors of (NH4)6Mo7O24·4H2O and NH2CSNH2. As shown, all calcined samples (curves b–e) exhibit a hexagonal MoS2 crystal structure (JCPDS 75-1539).13 Moreover, all calcined samples display a strong (002) diffraction peak at 2θ = 13.5°, indicating a well-stacked layered nanosheet structure.30 Obviously, the crystallinity of the fabricated samples is significantly improved after calcination (take unsintered MS-150-28 as a comparison, curve a in Fig. 1), which may be favourable to improve the electron transfer property of the sample, thus DSSCs performance.
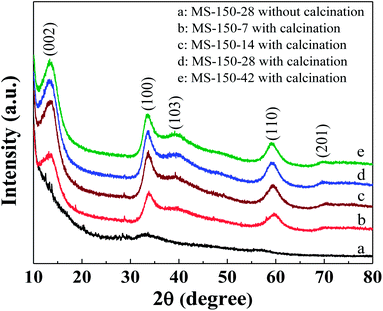 |
| Fig. 1 XRD patterns of as-synthesised sample fabricated at 150 °C for 24 h (a, MS-150-28) and calcined samples with different molar ratios of reaction precursors fabricated at 150 °C for 24 h (curves b–e). The calcination temperature was 400 °C. | |
Fig. 2A–D shows the surface and cross-sectional SEM images of the calcined samples (MS-150-7, MS-150-14, MS-150-28 and MS-150-42). As shown, the MS-150-7 exhibits uniform film surface with nanoparticle structure (Fig. 2A). With increasing the molar ratio of (NH4)6Mo7O24·4H2O and NH2CSNH2, the film surface starts to appear strip-like structure (MS-150-14, Fig. 2B). When the molar ratio of (NH4)6Mo7O24·4H2O and NH2CSNH2 is set at 1
:
28, more compact and short strip-like structure can be observed, as shown in Fig. 2C. Further increasing the molar ratio, strip-like surface structure disappears and compact nanoparticle surface can be observed again (MS-150-42). The above results indicate that the molar ratio of reaction precursors in reaction solution is critically important on the morphology of the sample. TEM characterisation reveals that the surface strip-like structure is actually layered nanosheet structure for MS-150-28 (Fig. 2E). Similar result can be also obtained for MS-150-14. High-resolution TEM image displays a well layered crystal structure with an interlayer distance of the (002) plane of 0.62 nm (Fig. 2E), which is consistent with the hexagonal lattice of the 2H–MoS2 phase.31 This layered crystal structure may be beneficial for improving the electrolyte transport property in solar cell application.32 As shown in Fig. 2E, the top exposed nanosheet structure film has a thickness of ca. 18 nm and the bottom structure is compact MoS2 particle structure for MS-150-28. For all investigated samples, it is found that the whole film thickness is about 0.4–0.5 μm, which is less than that of most reported results.13,14,22,23,25 The thinner MoS2 films in all fabricated samples exhibited semi-transparent optical property.
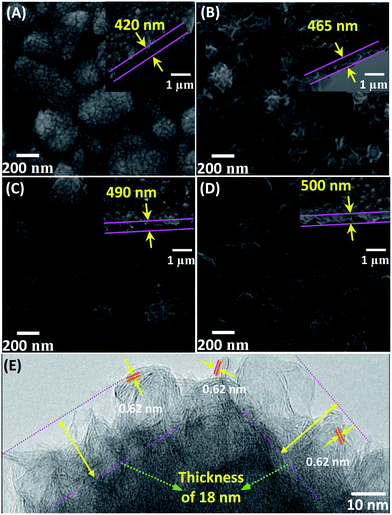 |
| Fig. 2 SEM and TEM images of the calcined samples with different molar ratios of reaction precursors fabricated at 150 °C for 24 h. (A) MS-150-7; (B) MS-150-14; (C) MS-150-28; (D) MS-150-42; (E) HRTEM image of MS-150-28. The calcined temperature was 400 °C. | |
When the molar ratio of (NH4)6Mo7O24·4H2O and NH2CSNH2 was fixed at 1
:
28, the effect of the hydrothermal temperature on the morphology of the sample was also investigated. Fig. S1 (ESI†) shows the surface SEM images of MS-120-28, MS-180-28 and MS-210-28 after calcination. As shown, MS-120-28 exhibits a uniform surface structure composed of nanoparticles. With increasing reaction temperature, compact strip-like surface structure can be observed at hydrothermal temperature of 150 °C (MS-150-28, Fig. 2C), which has been confirmed as nanosheet structure. Further increasing reaction temperature to 180 °C and 210 °C, relatively loose film with strip-like structure can be observed, especially for MS-210-28. The film with relatively loose nanosheet structure may not be beneficial for providing more catalytic active sites in comparison with the compact nanosheet surface structure as CE material for DSSCs.
In this work, X-ray photoelectron spectroscopy (XPS) was applied to investigate the elemental surface composition of the samples fabricated at 150 °C with different precursor molar ratios. The surface survey spectra demonstrate that all investigated samples are composed of C, Mo, S and a small amount of O (Fig. S2 in ESI†). The O element is possibly ascribed to the incomplete reduction of the samples during thermal treatment.33 Fig. 3 shows the high resolution XPS spectra of Mo and S of the calcined samples including MS-150-7, MS-150-14, MS-150-28 and MS-150-42. As shown, two peaks at around 229.5 and 232.7 eV can be attributed to the presence of the doublet of Mo 3d5/2 and Mo 3d3/2,34 revealing that Mo4+ state is dominant in the calcined samples and meaning the formation of MoS2. It is worthwhile to mention that a small number of Mo6+ state is still present for the calcined samples, which is possibly due to the incomplete reduction during hydrothermal reaction, similar with the reported results.35 The high resolution XPS spectra of S for all calcined samples display the binding energy at around 226.8, 162.4 and 163.6 eV, which are assigned as S 2s, S 2p3/2 and S 2p1/2, respectively.36 It should be noted that an energy peak at around ∼169 eV was observed only for MS-150-42, which is probably due to the presence of oxidised sulphur originated from excess precursor containing S.37 Nevertheless, there are no distinguishable peaks for other samples at the same peak position, indicating an apt amount of reaction precursor is important to form completely MoS2. The element compositions of the calcined samples with different precursor molar ratio are shown in Table 1. It can be seen that the atomic ratio of S and Mo is in the range of 1.90 to 1.96, which approaches the theoretical value of MoS2, meaning the samples to be stoichiometric MoS2.
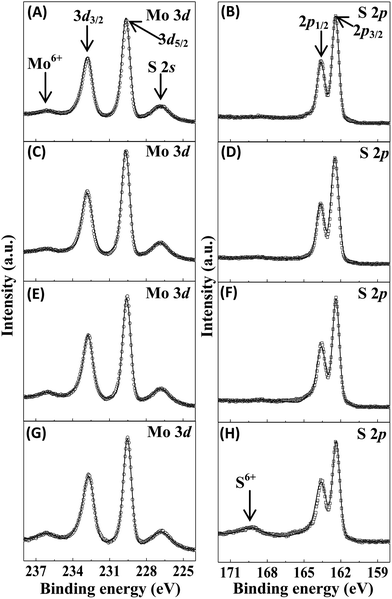 |
| Fig. 3 High resolution Mo and S XPS spectra of MoS2 samples with different molar ratios of reaction precursors fabricated at 150 °C for 24 h followed by calcination at 400 °C. (A and B) MS-150-7, (C and D) MS-150-14, (E and F) MS-150-28 and (G and H) MS-150-42. | |
Table 1 Composition of MoS2 samples prepared at different precursor molar ratios
Samples |
Elements (At.%) |
S/Mo |
O |
C |
Mo |
S |
MS-150-7 |
16.34 |
36.32 |
16.33 |
31.01 |
1.90 |
MS-150-14 |
14.79 |
33.89 |
17.60 |
33.71 |
1.92 |
MS-150-28 |
17.71 |
42.35 |
13.58 |
26.35 |
1.94 |
MS-150-42 |
20.33 |
55.13 |
8.28 |
16.26 |
1.96 |
DSSCs performance
As a promising electrocatalyst, MoS2-based material has been widely investigated as CE material for dye-sensitised solar cells (DSSCs).13,18 In this work, the fabricated MoS2 products were also evaluated as CE materials for DSSCs. Fig. 4 shows the photocurrent (Jsc)–photovoltage (Voc) curves of DSSCs assembled with the calcined MoS2 CEs fabricated at 150 °C with different precursor molar ratios. The obtained photovoltaic performance characteristics are summarised in Tables 2 and S2 (ESI†). In this work, each experimental condition was investigated concurrently with three parallel electrode samples for DSSCs measurements. The chosen data in Table 2 are all close to the average values of DSSCs under each experimental condition. When the hydrothermal temperature was fixed at 150 °C, it was found that the Voc has no obvious change for MS-150-7, MS-150-14, MS-150-28 and MS-150-42 (Fig. 4 and Table 2). However, the Jsc and FF values initially increase with precursor molar ratio, and then decrease with further increasing precursor molar ratio (MS-150-42). It was found that the DSSCs based on the MS-150-28 CE achieves a short-circuit current density (Jsc) of 18.37 mA cm−2, an open-circuit voltage (Voc) of 698 mV, a fill factor (FF) of 57.8% and an overall light conversion efficiency (η) of 7.41%, the highest efficiency amongst all investigated MoS2 based DSSCs in this work. These superiorly photovoltaic parameters achieved by DSSCs made of MS-150-28 CE can possibly be attributed to the high electrocatalytic activity and good electrical conductivity of the MS-150-28, which deserves a further investigation. The above results also reveal that an apt precursor ratio is critically important to obtain MoS2 catalyst with high electrocatalytic activity, thus high performance DSSCs. When the molar ratio of the reaction precursors was fixed at 1
:
28, the Jsc–Voc characteristic curves of the DSSCs prepared with MS-120-28, MS-180-28 and MS-210-28 are shown in Fig. S3 (ESI†), and the corresponding photovoltaic parameters are also summarised in Table 2. Similarly, the Voc values have no obvious change for all investigated samples compared to MS-150-28. However, the FF value of the MoS2 sample synthesised at higher hydrothermal temperature is apparently better than that of the MoS2 sample synthesised at lower hydrothermal temperature, which may be due to better electrical conductivity and improved contact between the conducting substrate and MoS2 catalyst at high hydrothermal temperature. The best light to electrical conversion efficiency obtained by DSSCs assembled with MS-150-28 indicates that the hydrothermal temperature is also significant to obtain high efficiency MoS2 electrocatalyst, thus high performance DSSCs. In this work, commercially available Pt electrode was also measured in DSSCs for a comparison. An overall light conversion efficiency of 7.13% can be achieved using DSSCs made of Pt-based CEs. Obviously, the solar cell made of MS-150-28 counter electrode possesses higher efficiency than that of solar cell assembled with commercial Pt electrode, indicating a great potential of pure MoS2-based electrocatalyst for photovoltaic application. The high solar cell performance can be further investigated and explained by the measurements of electrocatalytic activity of MoS2-based CEs.
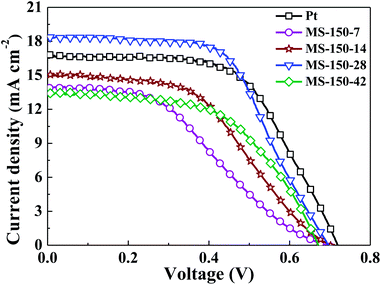 |
| Fig. 4 Photovoltaic characteristics of the DSSCs with different MoS2 counter electrodes prepared under different molar ratios of reaction precursors at 150 °C. | |
Table 2 Photovoltaic parameters, charge transfer resistance and exchange current density of various MoS2-based counter electrodes
Counter electrodes |
Voc (mV) |
Jsc (mA cm−2) |
η (%) |
FF (%) |
Rct (Ω cm2) |
Jo (mA cm−2) |
MS-150-7 |
691 |
13.92 |
3.70 |
38.5 |
1.72 |
1.71 |
MS-150-14 |
702 |
15.17 |
4.97 |
46.7 |
1.34 |
6.19 |
MS-150-28 |
698 |
18.37 |
7.41 |
57.8 |
0.619 |
6.47 |
MS-150-42 |
673 |
13.44 |
4.96 |
54.9 |
1.45 |
4.20 |
MS-120-28 |
708 |
14.25 |
5.52 |
54.8 |
0.948 |
5.78 |
MS-180-28 |
709 |
16.33 |
7.15 |
61.7 |
0.776 |
5.79 |
MS-210-28 |
709 |
12.76 |
5.47 |
60.5 |
0.861 |
5.52 |
Pt |
722 |
16.78 |
7.13 |
58.8 |
3.78 |
1.94 |
Electrocatalytic properties
Cyclic voltammetry (CV) is considered to be one of the powerful electrochemical tools to investigate the electrocatalytic activity of electrocatalysts as reported in many literatures.38 Fig. 5 shows the cyclic voltammetry (CV) curves of the MoS2 samples synthesised at 150 °C with different precursor molar ratios. For comparison, commercially available Pt electrode was also measured. As shown, for all investigated counter electrodes (CEs), two redox pairs are visible in the CV curves, where the left pair is associated with the redox reaction of I3−/I−, and the right pair is related to the redox reaction of I2/I3−.39 It is well known that the electrocatalytic activity of an electrocatalyst for redox reaction of I3−/I− in a solar cell can be evaluated in terms of its cathodic peak potential (Epc), cathodic peak current (Ipc) and peak to peak voltage separation (Epp).8 Higher Ipc, more positive Epc and lower Epp values mean better electrocatalytic activity of a CE for the reduction of I3− ions in the corresponding DSSCs.40 As shown in Fig. 5, the Ipc values of the investigated CEs with different molar ratios (Fig. 5) and different hydrothermal temperatures (Fig. S4, ESI†) are better than that of Pt CE. For all investigated CEs, MS-150-28 exhibits the highest Ipc value, and more positive cathodic peak potential (Epc) position. Although MS-150-14 and MS-180-28 show slightly narrower Epp values than that of MS-150-28, it is believed that the higher Ipc of MS-150-28 contributes higher electrocatalytic activity (Fig. 5 and S4 in ESI†). Overall, MS-150-28 CE shows the highest cathodic peak current density, more positive Epc and narrowed Epp, indicating the MS-150-28 CE has better electrocatalytic activity compared with other CEs. The superior electrocatalytic activity of MS-150-28 could be due to the surface exposed nanosheet crystal structure possessing rich catalytic active sites and layered structure favourable for electrolyte transport.41 After scanning 100 times (Fig. S5, ESI†), the CVs results show that the electrocatalytic performance of MS-150-28 has no obvious loss, indicating good catalytic stability of the electrocatalyst.
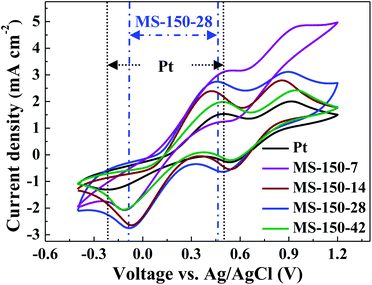 |
| Fig. 5 CVs of the MoS2 counter electrodes prepared with different molar ratios of reaction precursors at 150 °C. | |
Tafel polarisation measurements were conducted to correlate the cathodic peak current density with the resistance variation of the MoS2-based counter electrodes with different molar ratios and different hydrothermal temperatures, as shown in Fig. 6 and S6 (ESI†). For comparison, commercial Pt electrode was also measured. The exchange current densities (Jo) of the different counter electrodes were calculated from the tangent slopes of the corresponding Tafel curves and listed in Table 2. The variation of Jo is closely associated with the charge transfer resistance (Rct) according to the eqn (5) and (6).38 Apparently, MS-150-28 displayed the exchange current density of 6.47 mA cm−2, which is the highest among all investigated CEs in this work, and is almost 3.34 times of commercial Pt CE.
|
 | (5) |
|
 | (6) |
where
D is the diffusion coefficient of the triiodide,
l is the spacer thickness;
R,
F and
n represent their usual meaning.
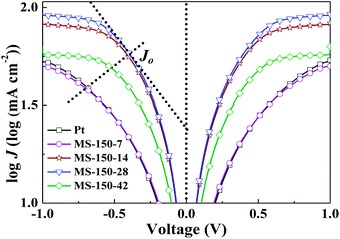 |
| Fig. 6 Tafel polarisation curves of the MoS2 counter electrodes prepared with different molar ratios of reaction precursors at 150 °C. | |
The electrochemical properties of the MoS2-based CEs with different molar ratios and different hydrothermal temperatures were further studied by using electrochemical impedance spectroscopic (EIS) technique (Fig. 7 and S7 in ESI†). The EIS measurements were conducted using symmetric cells fabricated with two identical MoS2 electrodes.42 For all investigated CEs, the Nyquist curves show two semicircles (left-higher frequency region and right-lower frequency region). The high frequency intercept on the real axis represents the ohmic series resistance (Rs).38 The semicircle in the high frequency region corresponds to the charge-transfer process (Rct) of electrolyte/electrode interface, while the semicircle in the low-frequency region is due to the Nernst diffusion process of triiodide ions.43 As shown in Fig. 7 and S7 (ESI†), MS-150-28 exhibits the smallest Rs value amongst all investigated electrodes, meaning superior electrical conductivity, which is critically important for improving DSSCs performance. Further, the charge-transfer resistance Rct values in the MS-150-7, MS-150-14, MS-150-28, MS-150-42, MS-120-28, MS-180-28, MS-210-28 and commercial Pt are calculated to be 1.72, 1.34, 0.619, 1.45, 0.948, 0.776, 0.861 and 3.78 Ω cm2, respectively (see Table 2). The smallest Rct (0.619 Ω cm2) value indicates that the MS-150-28 has a superior electrocatalytic activity compared to other investigated CEs including commercial Pt electrode.13,32 The above results are in agreement with Tafel curves and CV measurements.
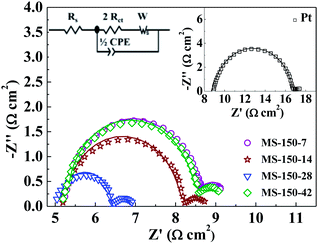 |
| Fig. 7 Nyquist plots of the dummy cells fabricated with two identical electrodes prepared at 150 °C with different molar ratios in I3−/I− electrolyte. Inset is the equivalent circuit model and Nyquist plot of Pt. | |
Conclusions
In this work, an ultrathin MoS2 film with exposed layered nanosheet structure was successfully prepared by low temperature hydrothermal method using fluorine-doped tin oxide (FTO) conducting glass as substrate. After calcination, the resulting MoS2 film was directly used as counter electrode material for dye-sensitised solar cells (DSSCs), exhibiting an overall light conversion efficiency of 7.41%, which was superior to that of Pt-based DSSCs (7.13%). The high solar cell performance could be ascribed to the good electrical conductivity and rich catalytic active sites providing by the MoS2 nanosheet crystal structure. The layered nanosheet structure was favourable for electrolyte transport, also contributing high solar cell efficiency. Our findings demonstrated the feasibility of developing low-cost and abundant metal chalcogenide electrocatalysts with high catalytic activity and stability by a facile hydrothermal method to replace Pt-based electrocatalysts for photovoltaic application.
Acknowledgements
This work was financially supported by Australian Research Council (ARC) Discovery Project and the Natural Science Foundation of China (Grant no. 51372248).
Notes and references
- B. O'regan and M. Grätzel, Nature, 1991, 353, 737 CrossRef CAS.
- M. Grätzel, Nature, 2001, 414, 338 CrossRef PubMed.
- M. Wu, X. Lin, A. Hagfeldt and T. Ma, Angew. Chem., Int. Ed., 2011, 50, 3520 CrossRef CAS PubMed.
- A. Hauch and A. Georg, Electrochim. Acta, 2001, 46, 3457 CrossRef CAS.
- L. Kavan, J. H. Yum and M. Graetzel, Phys. Status Solidi B, 2013, 250, 2643 CrossRef CAS.
- F. Gong, H. Wang, X. Xu, G. Zhou and Z. S. Wang, J. Am. Chem. Soc., 2012, 134, 10953 CrossRef CAS PubMed.
- M. Wang, A. M. Anghel, B. Marsan, N. L. Cevey Ha, N. Pootrakulchote, S. M. Zakeeruddin and M. Grätzel, J. Am. Chem. Soc., 2009, 131, 15976 CrossRef CAS PubMed.
- J. D. Roy-Mayhew, D. J. Bozym, C. Punckt and I. A. Aksay, ACS Nano, 2010, 4, 6203 CrossRef CAS PubMed.
- J. Chen, K. Li, Y. Luo, X. Guo, D. Li, M. Deng, S. Huang and Q. Meng, Carbon, 2009, 47, 2704 CrossRef CAS PubMed.
- Z. Yang, T. Chen, R. He, G. Guan, H. Li, L. Qiu and H. Peng, Adv. Mater., 2011, 23, 5436 CrossRef CAS PubMed.
- K. S. Lee, H. K. Lee, D. H. Wang, N. G. Park, J. Y. Lee, O. O. Park and J. H. Park, Chem. Commun., 2010, 46, 4505 RSC.
- C. T. Li, C. P. Lee, Y. Y. Li, M. H. Yeh and K. C. Ho, J. Mater. Chem. A, 2013, 1, 14888 CAS.
- M. Wu, Y. Wang, X. Lin, N. Yu, L. Wang, L. Wang, A. Hagfeldt and T. Ma, Phys. Chem. Chem. Phys., 2011, 13, 19298 RSC.
- C. J. Liu, S. Y. Tai, S. W. Chou, Y. C. Yu, K. D. Chang, S. Wang, F. S. S. Chien, J. Y. Lin and T. W. Lin, J. Mater. Chem., 2012, 22, 21057 RSC.
- G. R. Li, F. Wang, Q. W. Jiang, X. P. Gao and P. W. Shen, Angew. Chem., Int. Ed., 2010, 49, 3653 CrossRef CAS PubMed.
- M. Wu, J. Bai, Y. Wang, A. Wang, X. Lin, L. Wang, Y. Shen, Z. Wang, A. Hagfeldt and T. Ma, J. Mater. Chem., 2012, 22, 11121 RSC.
- H. Bi, W. Zhao, S. Sun, H. Cui, T. Lin, F. Huang, X. Xie and M. Jiang, Carbon, 2013, 61, 116 CrossRef CAS PubMed.
- S. A. Patil, P. Y. Kalode, R. S. Mane, M. M. M. Sung, S. B. Ambade and S. H. Han, Dalton Trans., 2014, 43, 5256 RSC.
- E. Benavente, M. Santa Ana, F. Mendizábal and G. González, Coord. Chem. Rev., 2002, 224, 87 CrossRef CAS.
- A. B. Laursen, S. Kegnæs, S. Dahl and I. Chorkendorff, Energy Environ. Sci., 2012, 5, 5577 CAS.
- Y. Li, H. Wang, L. Xie, Y. Liang, G. Hong and H. Dai, J. Am. Chem. Soc., 2011, 133, 7296 CrossRef CAS PubMed.
- G. Yue, J. Y. Lin, S. Y. Tai, Y. Xiao and J. Wua, Electrochim. Acta, 2012, 85, 162 CrossRef CAS PubMed.
- S. Y. Tai, C. J. Liu, S. W. Chou, F. S. S. Chien, J. Y. Lin and T. W. Lin, J. Mater. Chem., 2012, 22, 24753 RSC.
- J. Y. Lin, C. Y. Chan and S. W. Chou, Chem. Commun., 2013, 49, 1440 RSC.
- G. Yue, J. Wu, Y. Xiao, M. Huang, J. Lin and J. Y. Lin, J. Mater. Chem. A, 2013, 1, 1495 CAS.
- G. Li, B. Lei and X. Gao, J. Mater. Chem. A, 2014, 2, 3919 Search PubMed.
- H. Sun, D. Qin, S. Huang, X. Guo, D. Li, Y. Luo and Q. Meng, Energy Environ. Sci., 2011, 4, 2630 CAS.
- L. Zhang, J. C. Yu, M. Mo, L. Wu, Q. Li and K. W. Kwong, J. Am. Chem. Soc., 2004, 126, 8116 CrossRef CAS PubMed.
- K. M. Garadkar, A. A. Patil, P. P. Hankare, P. A. Chate, D. J. Sathe and S. D. Delekar, J. Alloys Compd., 2009, 487, 786 CrossRef CAS PubMed.
- K. Chang and W. Chen, Chem. Commun., 2011, 47, 4252 RSC.
- X. Feng, Q. Tang, J. Zhou, J. Fang, P. Ding, L. Sun and L. Shi, Cryst. Res. Technol., 2013, 48, 363 CrossRef CAS.
- J. Y. Lin, G. Yue, S. Y. Tai, Y. Xiao, H. M. Cheng, F. M. Wang and J. Wu, Mater. Chem. Phys., 2013, 143, 53 CrossRef CAS PubMed.
- K. Chang, W. Chen, L. Ma, H. Li, H. Li, F. Huang, Z. Xu, Q. Zhang and J. Y. Lee, J. Mater. Chem., 2011, 21, 6251 RSC.
- Y. Shi, J. K. Huang, L. Jin, Y. T. Hsu, S. F. Yu, L. J. Li and H. Y. Yang, Sci. Rep., 2013, 3, 1839 Search PubMed.
- J. M. Yun, Y. J. Noh, J. S. Yeo, Y. J. Go, S. I. Na, H. G. Jeong, J. Kim, S. Lee, S. S. Kim and H. Y. Koo, J. Mater. Chem. C, 2013, 1, 3777 RSC.
- M. Baker, R. Gilmore, C. Lenardi and W. Gissler, Appl. Surf. Sci., 1999, 150, 255 CrossRef CAS.
- C. M. Whelan, M. R. Smyth, C. J. Barnes, N. Brown and C. A. Anderson, Appl. Surf. Sci., 1998, 134, 144 CrossRef CAS.
- M. Wu, X. Lin, Y. Wang, L. Wang, W. Guo, D. Qi, X. Peng, A. Hagfeldt, M. Grätzel and T. Ma, J. Am. Chem. Soc., 2012, 134, 3419 CrossRef CAS PubMed.
- N. Q. Fu, Y. Y. Fang, Y. D. Duan, X. W. Zhou, X. R. Xiao and Y. Lin, ACS Nano, 2012, 6, 9596 CrossRef CAS PubMed.
- K. C. Huang, Y. C. Wang, R. X. Dong, W. C. Tsai, K. W. Tsai, C. C. Wang, Y. H. Chen, R. Vittal, J. J. Lin and K. C. Ho, J. Mater. Chem., 2010, 20, 4067 RSC.
- Y. Hou, D. Wang, X. H. Yang, W. Q. Fang, B. Zhang, H. F. Wang, G. Z. Lu, P. Hu, H. J. Zhao and H. G. Yang, Nat. Commun., 2013, 4, 1583 CrossRef PubMed.
- S. Sakurai, H. Q. Jiang, M. Takahashi and K. Kobayashi, Electrochim. Acta, 2009, 54, 5463 CrossRef CAS PubMed.
- R. Cruz, D. A. Pacheco Tanaka and A. Mendes, Sol. Energy, 2012, 86, 716 CrossRef CAS PubMed.
Footnote |
† Electronic supplementary information (ESI) available: SEM images, solar cell performance and electrochemical characterisation results. See DOI: 10.1039/c4ra00583j |
|
This journal is © The Royal Society of Chemistry 2014 |
Click here to see how this site uses Cookies. View our privacy policy here.