Design of low temperature La2O3 oxidative coupling of methane catalysts using feature engineering and automated sampling†
Received
25th September 2024
, Accepted 8th November 2024
First published on 25th November 2024
Abstract
The design of efficient catalysts remains an challenge for complex systems such as the oxidative coupling of methane (OCM), where reaction mechanisms are still debated. Catalysts informatics workflows have proved useful in identifying high-performing material candidates and optimizing reaction conditions from underlying trends in experimental data. Herein, a data set composed La2O3-supported catalysts for the OCM reaction is used to construct a support-vector regression (SVR) model and extract four element combinations to support on La2O3 and test for low temperature catalytic activity, with the best result observed for (Y, Cs)/La2O3. This methodology presents an effective approach from building a regression model using engineered features with an automated sampling technique to the extraction and experimental validation of promising catalyst candidates, which can also be extended toward other catalytic reactions.
1 Introduction
Methane is an abundant resource that has been used for both the production of higher-value chemicals and in fuel applications. Although the direct synthesis of C2 hydrocarbons from methane was proposed more than forty years ago,1 the high stability of the C–H bond remains an obstacle to this day, since the conversion of a methane molecule to a methyl radical is the starting point of the reaction.2 The need for highly selective catalysts is widely understood, as the formation of deep oxidation products is more thermodynamically-favored at higher temperatures.3 Catalyst-assisted mechanism studies have also been carried out, as the reaction pathways depend directly on the catalyst surface's structure, chemistry and the process conditions.4–9 However, to this day, a definitive mechanism has not been elucidated, which leaves structure–activity relationships unclear.
Among the various metal oxides that have been studied as suitable OCM catalysts, lanthanum oxide (La2O3) has shown good activity and high selectivity for C2 products at relatively low temperatures10 that can be improved with the addition of promoter elements.11–18 These properties make it a good candidate as a support material for low temperature catalysts. In recent years, data-driven approaches have been adopted to propose and test new catalyst systems as an attempt to increase overall C2 yield. Starting from literature data,19–24 first-principle calculations25–27 to high-throughput experimentation approaches,28–34 data-driven approaches have proven successful in proposing and uncovering new active OCM catalysts and experimental conditions35 that improve C2 yield. Nevertheless, the complete optimization of this reaction remains unsolved, as it involves the reactions occurring gas phase,36 the surface reactions on the catalyst surface,8,37 the nature of the catalyst surface2,38,39 and the inclusion of additional elements through procedures such as impregnation that change the nature of the catalyst's surface.13–15
This work presents a machine learning-assisted approach to design descriptors (features) that represent catalyst composition to predict C2 yield as a function of reaction temperature and extract impregnated element combinations to enhance the C2 yield for the low temperature La2O3 OCM activity. For simplicity, the analyzed data set fixes the metallic oxide support, supported element amount and reaction gas flow conditions, leaving the identity of the supported elements and reaction temperature as the only variables to optimize towards low temperature-high C2 yield.
2 Methodology
Data handling, processing, analysis and visualization are done with Python (v. 3.10.12), and the Scikit-learn library (v. 0.23.2) is implemented for ML procedures.40
2.1 Data set
The data set employed for this study (from here on referred to as the training data) to develop first-order features has been reported by Nishimura et al.,41 with this work focusing only on the catalysts tested under the same gas flow conditions with a feed composed of CH4
:
O2
:
N2 at 66.7%, 22.6% and 9.7% vol., respectively. The data set is composed of 429 data points pertaining to 34 La2O3-supported oxidative coupling of methane (OCM) reaction activity and their observed C2 yield (%) across 500–850 °C. The catalysts correspond to equimolar binary and ternary combinations of impregnated metallic elements and expressed as M1⋯Mn/La2O3, where M1 to Mn correspond to elements selected from Ba, Ca, Ce, Eu, K, La, Li, Mg, Mo, Na, Sm, Sr, Ti and W.
2.2 Data analysis and method
OCM catalyst C2 yield (%) is predicted with a support-vector regression (SVR) model implemented with the radial basis function (RBF) kernel. To evaluate the performance of the regression models, a train–test split (80
:
20) is used to cross validate the predictions, with the evaluation metric being the average r2 score of the test data of data splits over random states 0–9. Hyperparameter values (C = 10, γ = 0.01) are optimized to avoid overfitting.
2.3 Reagents
Lanthanum(III) oxide (La2O3, >99%) purchased from Tokyo Chemical Industry, Co., Ltd. is used as support for the prepared catalysts. Potassium (KNO3, ≥99%) and yttrium (Y(NO3)3·6H2O, 99%) nitrates from Junsei Chemical Co. Ltd., lithium (LiNO3, 99%), cesium (CsNO3, 99%) and cerium(III) (Ce(NO3)3·6H2O, special grade) nitrates from Wako Pure Chemical Corporation and europium(III) nitrate (Eu(NO3)3·5H2O, 99.9%) from Sigma Aldrich are used as impregnation precursors for the tested catalysts. All reagents are used without further purification.
2.4 Experimental methodology
La2O3-supported catalysts are prepared based on a modified impregnation methodology previously reported by Nishimura et al.,41 The tested catalysts are prepared by impregnating La2O3 with water-soluble metallic nitrate precursors in the combinations presented on Table 1. In each instance, 2 g of La2O3 are dispersed in 100 mL of water and kept under continuous stirring. In parallel, 0.2 mmol of each metallic nitrate precursor are each separately dissolved in 50 mL of water and the solutions subsequently added to the La2O3 dispersion in increasing order of the precursors' metallic element atomic number, which is the same left-to-right order the elements are listed on Table 1. For example, in the case of Cat1, the order of addition is first Y(NO3)3, then CsNO3. The resulting mixture is then allowed to age for 14 h without stirring at room temperature. The stirring is restarted after this period and water is evaporated at 70 °C. The remaining powder is then collected and dried at 120 °C for 2 h. Lastly, the material is then ground in a mortar, calcined at 700 °C for 3 h and ground again before testing.
Table 1 Catalyst supported metal (M1, M2, M3)/La2O3 combinations tested for OCM performance
Label |
M1 |
M2 |
M3 |
Cat1 |
Y |
Cs |
None |
Cat2 |
Cs |
Ce |
None |
Cat3 |
Li |
K |
Eu |
Cat4 |
K |
Y |
Cs |
Catalyst performance is tested in a steel fixed-bet tubular reactor (L = 262 mm, ID = 7.05 mm, SUS316L) from MECAFARM CO., LTD. The catalyst powder (100 mg) is placed between two layers of quartz wool (5 mg each), with the catalyst layer located 97 mm from the top, and 165 mm from the bottom of the tube. The reactor temperature is monitored using a K-type thermocouple, with the tip placed near the outer reactor wall of the catalyst bed location. Prior to each measurement run, the system is purged at 300 °C for 30 min. Under N2 gas at a flow of 30 SCCM to flush out all environmental gases that may interfere with the measurement. The system is then cooled to room temperature under the same flow conditions to start the catalyst performance measurements. The performance is studied at 450–700 °C at 50 °C intervals under a CH4/O2/N2 flow at 18/9/3 SCCM, respectively. The reactor mixture is analyzed after an exposition time of 8 min for each temperature using a Shimadzu GC-2014 chromatograph equipped with a SHINCARBON ST 50/80 mesh column (3 mm × 2 m, He carrier). Gas conversion and product yield are estimated using N2 as an internal standard. Reagent R conversions for O2 and CH4 are calculated in accordance to eqn (1). Product P yield for CO, CO2, C2H4 and C2H6 is calculated in accordance to eqn (2), where n = 1 for CO and CO2, and n = 2 for C2H4 and C2H6. Lastly, C2 yield and selectivity are calculated according to eqn (3) and (4), respectively.
|  | (1) |
|  | (2) |
| C2yield = C2H4Yield + C2H6Yield | (3) |
|  | (4) |
3 Results and discussion
The data set is composed of 429 data points pertaining to 34 La2O3-supported OCM catalysts tested across 500–850 °C. The elements supported on La2O3 are presented on Fig. 1 and belong to groups 1, 2, 4 and 5 of the periodic table, along with four lanthanide group elements. Since the feed gas and the impregnated elements' composition are constant, the objective of the regression model is to predict C2 yield as a function of supported metals' combination (M1, M2, M3) and reaction temperature.
 |
| Fig. 1 Frequency count of the individual La2O3-supported metallic elements in the catalysts within the training data. | |
An SVR model is employed to predict C2 yield as a function of catalyst composition and reaction temperature. Catalyst composition-related base features are calculated in accordance to eqn (5), where the features D are the aritmethic mean of 58 reference values Di of each of the supported metallic elements i present in the La2O3 catalyst. Said reference values for the included elements are compiled in the XenonPy library42 and a brief description for them is included in the ESI† as Table S1. Arithmetic mean values are considered in this case due to all catalysts containing supported metals present in equimolar amounts respective to each other. For example, a calculated atomic radius feature of a catalyst impregnated with Sr and Ce would be represented as the average of the atomic radii of Sr and Ce. Lastly, multiple analogues of the compositional base features are engineered by calculating the square, cubic, square root, exponential, and natural logarithm values along with their reciprocals to incorporate different feature scales that may adjust better to predict C2 yield. After this step, the total number of feature increases from 59 to 639, as reaction temperature analogues are not engineered.
|  | (5) |
Feature selection is carried out through the MonteCat algorithm previously reported,43 where a regression model's cross validation r2 score is sought to be maximized through sequential randomized feature additions and removals across many iterations. In case a randomized feature inclusion or removal lowers the model's cross validation score, the implementation of this action is decided based on a computed probability P value as depicted in eqn (6) from a Boltzmann distribution that depends on the score's evolution Δr2 and a fixed MC temperature T parameter value that regulates the leniency of implementing score-reducing actions. The algorithm is implemented for 104 iterations using {5, 10, 20, 50, 100, 200, 500, 1000, 2000} values for the MC temperature parameter. As a final note, it is pointed out that this MonteCat temperature parameter has no relation to the experimental reaction temperature that takes part as one of the features in the regression model. A detailed workflow is included in the ESI† as Fig. S1 and S2.
|  | (6) |
The results of the feature selection procedure are presented on Fig. 2. Twenty five runs with different fixed random seed values are carried out for each depicted temperature value, and after the completion of each run, the highest observed score throughout the run is identified along with the feature subset at that point. A cross-validation score greater than 0.9 is consistently observed throughout all experiments (a), and a subset containing 15 features is extracted to be used in the prediction model (b), with the best test r2 score of 0.9403 (c).
 |
| Fig. 2 MonteCat process-extracted feature subsets' performance with a SVR (C = 10, γ = 0.01) model across various temperature parameter values (a), score-feature number behavior with the best-performing subset highlighted in red (b) and parity plot of the feature subset with the highest observed score (c). | |
From this point, this subset is used to carry out a sequential feature elimination (SFE) procedure to remove features that do not help increase the model's predictive accuracy. The results are presented on Fig. 3, where it can be observed that having only 5 features allows the SVR model to reach a test r2 score > 0.9. The features selected for the regression model are analogues of the atomic weight, covalent radius, number of valence electrons on the s shell, van der Waals radius and the reaction temperature.
 |
| Fig. 3 Backward feature elimination procedure results applied upon the MonteCat-extracted feature subset derived from the highest observed cross validation r2 score. The vertical guide line represents the spot where the features stopped being removed, leaving the final model with 5 only features. | |
An inverse prediction at 650 °C contemplating all binary and ternary combinations from Li, Na, Mg, K, Ca, Sc, Ti, V, Cr, Mn, Fe, Co, Ni, Cu, Zn, Rb, Sr, Y, Zr, Nb, Mo, Ru, Rh, Pd, Ag, Cd, Cs, Ba, La, Ce, Pr, Nd, Sm, Eu, Gd, Tb, Dy, Ho, Er, Tm, Yb, Lu, Hf, Ta, W, Re, Os, Ir, Pt, Au and Hg, which belong to blocks s, d and f of the periodic table is carried out. This results in 22
101 supported metal combinations whose C2 yield is predicted at 650 °C using the constructed SVR model. Table 2 presents the results for the five highest binary and ternary combinations from which the best two performing binary and ternary combinations are selected, prepared and tested experimentally. On an additional note, K/Ba is not tested due to that pair already being included in the training data.
Table 2 Extracted supported metal combinations with the highest predicted C2 yield at 650 °C
M1 |
M2 |
M3 |
Pred. C2y (%) |
Y |
Cs |
— |
15.90 |
K |
Ba |
— |
15.90 |
Cs |
Ce |
— |
15.77 |
Ba |
Th |
— |
15.68 |
Ba |
Pr |
— |
15.66 |
Li |
K |
Eu |
16.03 |
K |
Y |
Cs |
15.89 |
K |
Cs |
Ce |
15.86 |
Y |
Cs |
Ba |
15.84 |
K |
Cs |
Tm |
15.82 |
The average results for three measurements for Cat1–4 are presented on Fig. 4, where a Blank (the reaction carried out without catalyst inside) and La2O3 without supported metals are included as reference. The behavior observed without catalytic material is a steady increase in O2 and CH4 conversion, which could be attributable to CH4 oxidation taking place in gas phase and along the reactor walls.44,45 While the CH4 conversion increases steadily, there is an abrupt increase in O2 conversion between 650–700 °C also observed in CH4 and CO2 conversions. Starting at 650 °C, C2H6 is detected, which indicates that oxidative coupling starts around this temperature range with low C2 selectivity (<5%). When pure La2O3 is tested instead, O2 and CH4 conversions increase at lower temperatures due to La2O3 contributing to CH4 oxidation.10,11,46 In the same manner, CO2 yield is greater than the one observed in the absence of catalyst and C2H4 and C2H6 are both produced starting at 600 °C, although the highest observed C2 yield (at 650 °C) reached 1.5% with a C2 selectivity of 11%.
 |
| Fig. 4 Observed experimental reagent gas conversions (O2 and CH4), product gases' yields (CO, CO2, C2H4 and C2H6) and calculated C2 yields and selectivities at the bottom for each tested catalyst respective to the reaction temperatures. The depicted values represent an average across three runs, with error bars depicting the standard deviation of the measurements. | |
This behavior is enhanced with the presence of supported metals. Both Cat1 and Cat2 display similar O2 and CH4 conversion output, but Cat1 reaches a 100% O2 conversion at 600 °C, while Cat2 does so at 650 °C. Both catalysts reach their maximum C2 yield at 650 °C at values around 6% and 3.7% with selectivities of 31.8% and 20.5% for Cat1 and Cat2, respectively. The ternary catalysts Cat3 and Cat4 display different behavior from their binary counterparts. Cat3 displayed generally lower or equal O2 conversion compared to the Blank across the entire temperature range, while Cat4 behaved in a similar manner to the Blank, with the only noteworthy difference is a larger O2 conversion at 650 °C. For both ternary catalysts, the peak activity is observed at 700 °C, with Cat3 showing higher C2 yield and selectivity (4.9% and 23.4%, respectively) than Cat4 (2.6% and 13.6%, respectively). Interestingly, Cat3 is the only material that exhibited equal or lower reagent conversions compared to the results observed in the absence of catalyst. Measurements at temperatures higher than 700 °C are not included, as only COx products are detected possibly due to the SUS316 reactor becoming catalytically-active.
The catalytic activity of the tested materials can be better observed on Fig. 5 by comparing C2 selectivity versus CH4 conversion. At temperatures below 600 °C, no C2 products are detected even though there is CH4 conversion, resulting in a direct conversion into CO2. The binary catalysts indeed display both, a higher CH4 conversion with higher C2 selectivities at lower temperatures. Nevertheless, OCM activity decreases at 700 °C for La2O3 and Cat1–2, while Cat3–4 show higher activity at this temperature, with Cat3 achieving slightly lower C2 selectivity than Cat1 at roughly the same CH4 conversion.
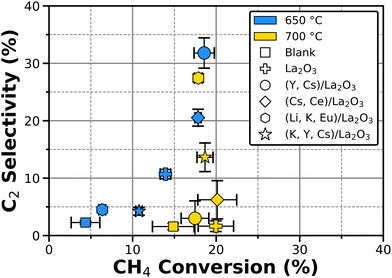 |
| Fig. 5 Observed OCM activity of the prepared catalysts at 650 and 700 °C. | |
4 Conclusion
This study presents a machine learning-assisted methodology to uncover low temperature OCM catalysts. Feature design and selection, catalyst prediction and experimental testing are all carried out, resulting in four impregnated metal combinations that boost La2O3 OCM activity in the 650–700 °C range. The best performance is observed on (Y, Cs)/La2O3 with a C2 selectivity at 32% with 18% CH4 conversion at 650 °C. This methodology presents an effective first approach at constructing regression models solely from catalyst composition and reaction conditions. New and efficient combinations of metals can then be characterized further to establish structure–property relationships that can then be used to elucidate reaction mechanisms.
Data availability
All data used in this work is provided in the ESI.†
Conflicts of interest
The authors declare no competing financial interest.
Acknowledgements
This work is funded by the Japan Science and Technology Agency (JST) CREST Grant Number (JPMJCR17P2), ERATO grant number (JPMJER1903), PRESTO grant number (JPMJPR24T5), JST Mirai Program Grant Number (JPMJMI22G4), JSPS KAKENHI Grant-in-Aid for Scientific Research (B) Grant Number (JP23H01762) and (24K01241). The authors would also like to acknowledge the technical support from Mr. Masato Ishii and Mr. Shigehiro Umegai from MECAFARM CO., LTD.
Notes and references
- G. Keller and M. Bhasin, Synthesis of ethylene via oxidative coupling of methane: I. Determination of active catalysts, J. Catal., 1982, 73, 9–19 CrossRef CAS
.
- D. Noon, A. Seubsai and S. Senkan, Oxidative Coupling of Methane by Nanofiber Catalysts, ChemCatChem, 2013, 5, 146–149 CrossRef CAS
.
- B. L. Farrell, V. O. Igenegbai and S. Linic, A Viewpoint on Direct Methane Conversion to Ethane and Ethylene Using Oxidative Coupling on Solid Catalysts, ACS Catal., 2016, 6, 4340–4346 CrossRef CAS
.
- K. Takanabe and E. Iglesia, Mechanistic Aspects and Reaction Pathways for Oxidative Coupling of Methane on Mn/Na2WO4/SiO2 Catalysts, J. Phys. Chem. C, 2009, 113, 10131–10145 CrossRef CAS
.
- C. Karakaya, H. Zhu, B. Zohour, S. Senkan and R. J. Kee, Detailed Reaction Mechanisms for the Oxidative Coupling of Methane over La2O3/CeO2 Nanofiber Fabric Catalysts, ChemCatChem, 2017, 9, 4538–4551 CrossRef CAS
.
- J. Si, G. Zhao, W. Sun, J. Liu, C. Guan, Y. Yang, X.-R. Shi and Y. Lu, Oxidative Coupling of Methane: Examining the Inactivity of the MnO-Na2WO4/SiO2 Catalyst at Low Temperature, Angew. Chem., 2022, 61, e202117201 CrossRef CAS
.
- S. Sourav, Y. Wang, D. Kiani, J. Baltrusaitis, R. R. Fushimi and I. E. Wachs, New Mechanistic and Reaction Pathway Insights for Oxidative Coupling of Methane (OCM) over Supported Na2WO4/SiO2 Catalysts, Angew. Chem., 2021, 60, 21502–21511 CrossRef CAS
.
- L. Hu, D. Pinto and A. Urakawa, Catalytic Oxidative Coupling of Methane: Heterogeneous or Homogeneous Reaction?, ACS Sustainable Chem. Eng., 2023, 11, 10835–10844 CrossRef CAS
.
- I. Miyazato, T. N. Nguyen, L. Takahashi, T. Taniike and K. Takahashi, Representing Catalytic and Processing Space in Methane Oxidation Reaction via Multioutput Machine Learning, J. Phys. Chem. Lett., 2021, 12, 808–814 CrossRef CAS
.
- K. D. Campbell, H. Zhang and J. H. Lunsford, Methane activation by the lanthanide oxides, J. Phys. Chem., 1988, 92, 750–753 CrossRef CAS
.
- J. M. DeBoy and R. F. Hicks, The oxidative coupling of methane over alkali, alkaline earth, and rare earth oxides, Ind. Eng. Chem. Res., 1988, 27, 1577–1582 CrossRef CAS
.
- V. R. Choudhary, B. S. Uphade and S. A. R. Mulla, Oxidative Coupling of Methane over a Sr-Promoted La2O3 Catalyst Supported on a Low Surface Area Porous Catalyst Carrier, Ind. Eng. Chem. Res., 1997, 36, 3594–3601 CrossRef CAS
.
- V. R. Choudhary, S. A. R. Mulla and V. H. Rane, Surface basicity and acidity of alkaline earth-promoted La2O3 catalysts and their performance in oxidative coupling of methane, J. Comb. Theory, B., 1998, 72, 125–130 CAS
.
- V. Choudhary, V. Rane and S. Chaudhari, Influence of various promoters on the basicity and catalytic activity of MgO catalysts in oxidative coupling of methane, Catal. Lett., 1990, 6, 95–98 CrossRef CAS
.
- K. Okabe, K. Sayama, H. Kusama and H. Arakawa, Effects of Additives on SrO-La2O3 Catalysts for Oxidative Coupling of Methane, J. Jpn. Pet. Inst., 1995, 38, 267–272 CrossRef CAS
.
- Y. Wang, X. Yang, F. Yin, K. Zhang, H. Guo, G. Wang, G. Jiang, C. Li and X. Zhu, Elucidating the effect of barium halide promoters on La2O3/CaO catalyst for oxidative coupling of methane, J. Energy Chem., 2022, 73, 49–59 CrossRef CAS
.
- J. Xiong, H. Yu, Y. Wei, C. Xie, K. Lai, Z. Zhao and J. Liu, Metal Ions (Li, Mg, Zn, Ce) Doped into La2O3 Nanorod for Boosting Catalytic Oxidative Coupling of Methane, Catalysts, 2022, 12(7), 713 CrossRef CAS
.
- V. J. Ferreira, P. Tavares, J. L. Figueiredo and J. L. Faria, Ce-Doped La2O3 based catalyst for the oxidative coupling of methane, Catal. Commun., 2013, 42, 50–53 CrossRef CAS
.
- U. Zavyalova, M. Holena, R. Schlögl and M. Baerns, Statistical Analysis of Past Catalytic Data on Oxidative Methane Coupling for New Insights into the Composition of High-Performance Catalysts, ChemCatChem, 2011, 3, 1935–1947 CrossRef CAS
.
- E. V. Kondratenko, M. Schlüter, M. Baerns, D. Linke and M. Holena, Developing catalytic materials for the oxidative coupling of methane through statistical analysis of literature data, Catal. Sci. Technol., 2015, 5, 1668–1677 RSC
.
- K. Suzuki, T. Toyao, Z. Maeno, S. Takakusagi, K.-I. Shimizu and I. Takigawa, Statistical Analysis and Discovery of Heterogeneous Catalysts Based on Machine Learning from Diverse Published Data, ChemCatChem, 2019, 11, 4537–4547 CrossRef CAS
.
- D. Zeng, Y. Song, M. Wang, Y. Lu, Z. Chen and R. Xiao, A machine learning approach for predicting the performance of oxygen carriers in chemical looping oxidative coupling of methane, Sustainable Energy Fuels, 2023, 7, 3464–3470 RSC
.
- R. Schmack, A. Friedrich, E. Kondratenko, J. Polte, A. Werwatz and R. Kraehnert, A meta-analysis of catalytic literature data reveals property-performance correlations for the OCM reaction, Nat. Commun., 2019, 10, 441 CrossRef CAS
.
- S. Mine, M. Takao, T. Yamaguchi, T. Toyao, Z. Maeno, S. M. A. Hakim Siddiki, S. Takakusagi, K.-I. Shimizu and I. Takigawa, Analysis of Updated Literature Data up to 2019 on the Oxidative Coupling of Methane Using an Extrapolative Machine-Learning Method to Identify Novel Catalysts, ChemCatChem, 2021, 13, 3636–3655 CrossRef CAS
.
- K. Takahashi, I. Miyazato, S. Nishimura and J. Ohyama, Unveiling Hidden Catalysts for the Oxidative Coupling of Methane based on Combining Machine Learning with Literature Data, ChemCatChem, 2018, 10, 3223–3228 CrossRef CAS
.
- K. Takahashi, L. Takahashi, S. D. Le, T. Kinoshita, S. Nishimura and J. Ohyama, Synthesis of Heterogeneous Catalysts in Catalyst Informatics to Bridge Experiment and High-Throughput Calculation, J. Am. Chem. Soc., 2022, 144, 15735–15744 CrossRef CAS
.
- L. Ugwu, Y. Morgan and H. Ibrahim, Enhancing Ethene Production through Low-Temperature Oxidative Coupling of Methane: Leveraging DFT and Data Analysis for Crafting Innovative and Efficient Catalyst Compositions, Ind. Eng. Chem. Res., 2023, 62, 19658–19673 CrossRef CAS
.
- J. Ohyama, S. Nishimura and K. Takahashi, Data Driven Determination of Reaction Conditions in Oxidative Coupling of Methane via Machine Learning, ChemCatChem, 2019, 11, 4307–4313 CrossRef CAS
.
- K. Chen, H. Tian, B. Li and S. Rangarajan, A chemistry-inspired neural network kinetic model for oxidative coupling of methane from high-throughput data, AIChE J., 2022, 68, e17584 CrossRef CAS
.
- T. N. Nguyen, S. Nakanowatari, T. P. Nhat Tran, A. Thakur, L. Takahashi, K. Takahashi and T. Taniike, Learning Catalyst Design Based on Bias-Free Data Set for Oxidative Coupling of Methane, ACS Catal., 2021, 11, 1797–1809 CrossRef CAS
.
- J. Ohyama, T. Kinoshita, E. Funada, H. Yoshida, M. Machida, S. Nishimura, T. Uno, J. Fujima, I. Miyazato, L. Takahashi and K. Takahashi, Direct design of active catalysts for low temperature oxidative coupling of methane via machine learning and data mining, Catal. Sci. Technol., 2021, 11, 524–530 RSC
.
- S. Nishimura, S. D. Le, I. Miyazato, J. Fujima, T. Taniike, J. Ohyama and K. Takahashi, High-throughput screening and literature data-driven machine learning-assisted investigation of multi-component La2O3-based catalysts for the oxidative coupling of methane, Catal. Sci. Technol., 2022, 12, 2766–2774 RSC
.
- S. Alturkistani, H. Wang, R. Gautam and S. M. Sarathy, Importance of Process Variables and Their Optimization for Oxidative Coupling of Methane (OCM), ACS Omega, 2023, 8, 21223–21236 CrossRef CAS PubMed
.
- C. L. M. von Meyenn and S. Palkovits, Prediction of suitable catalysts for the OCM reaction by combining an evolutionary approach and machine learning, Energy Adv., 2023, 2, 691–700 RSC
.
- C. Y. Thien, A. R. Mohamed and S. Bhatia, Process optimization of oxidative coupling of methane for ethylene production using response surface methodology, J. Comb. Theory, B., 2007, 82, 81–91 CAS
.
- H. Wang, C. Shao, J. Gascon, K. Takanabe and S. M. Sarathy, Noncatalytic Oxidative Coupling of Methane (OCM): Gas-Phase Reactions in a Jet Stirred Reactor (JSR), ACS Omega, 2021, 6, 33757–33768 CrossRef CAS PubMed
.
- B. Zohour, D. Noon and S. Senkan, New Insights into the Oxidative Coupling of Methane from Spatially Resolved Concentration and Temperature Profiles, ChemCatChem, 2013, 5, 2809–2812 CrossRef CAS
.
- S. Kuś, M. Otremba and M. Taniewski, The catalytic performance in oxidative coupling of methane and the surface basicity of La2O3, Nd2O3, ZrO2 and Nb2O5, Fuel, 2003, 82, 1331–1338 CrossRef
.
- V. R. Choudhary and V. H. Rane, Oxidative coupling of methane over La2O3. Influence of catalyst preparation on surface properties and steady and oscillating reaction behaviour, J. Chem. Soc., Faraday Trans., 1994, 90, 3357–3365 RSC
.
- F. Pedregosa,
et al. Scikit-learn: Machine Learning in Python, J. Mach. Learn. Res., 2011, 12, 2825–2830 Search PubMed
.
- S. Nishimura, X. Li, J. Ohyama and K. Takahashi, Leveraging machine learning engineering to uncover insights into heterogeneous catalyst design for oxidative coupling of methane, Catal. Sci. Technol., 2023, 13, 4646–4655 RSC
.
- XenonPy, https://xenonpy.readthedocs.io/en/latest/, Accessed: September 17, 2023.
- F. Garcia-Escobar, T. Taniike and K. Takahashi, MonteCat: A Basin-Hopping-Inspired Catalyst Descriptor Search Algorithm for Machine Learning Models, J. Chem. Inf. Model., 2024, 64, 1512–1521 CrossRef CAS
.
- O. Onsager, R. Lødeng, P. Søraker, A. Anundskaas and B. Helleborg, The homogeneous gas phase oxidation of methane and the retarding effect of basic/inert surfaces, Catal. Today, 1989, 4, 355–363 CrossRef CAS
.
- X.-Q. Qiu, Q.-M. Zhu, N.-B. Wong and K.-C. Tin, Catalytic contribution of reactor wall materials on oxidative coupling of methane, J. Comb. Theory, B., 1996, 65, 380–384 CAS
.
- S. Wang, S. Li and D. A. Dixon, Mechanism of selective and complete oxidation in La2O3-catalyzed oxidative coupling of methane, Catal. Sci. Technol., 2020, 10, 2602–2614 RSC
.
Footnote |
† Electronic supplementary information (ESI) available: Further details on the base features and the feature engineering and selection steps are included as supporting information. See DOI: https://doi.org/10.1039/d4cy01142b |
|
This journal is © The Royal Society of Chemistry 2025 |
Click here to see how this site uses Cookies. View our privacy policy here.