One step conversion of bio-based magnolol into low k materials at high frequency†
Received
3rd January 2024
, Accepted 27th April 2024
First published on 29th April 2024
Abstract
A facile one-pot conversion of a bio-based magnolol gave a functional monomer with curable benzocyclobutene groups, which was then thermally polymerized to form a cross-linked resin, displaying a very low dielectric loss of 1.0 × 10−3 at a frequency of 10 GHz and a dielectric constant of 2.78, as well as exhibiting good dimensional stability with a CTE of 46 ppm °C−1. These results indicate that the bio-based monomer has potential application as an encapsulation material used in the microelectronics industry.
Sustainability spotlight
In recent years, with the continuous reduction of traditional fossil energy reserves and the intensification of environmental pollution, clean biomass energy has entered the public's view. Increasing the commodity value added of biomass energy to replace non-renewable petroleum-based feedstocks can reduce greenhouse gas emissions and increase the share of renewable energy in the global energy mix. Aromatic biomass compounds always have apparent advantages when converted to functional materials because they have similar robust and rigid structures to the petrochemical aromatic monomers. Therefore, we use magnolol extracted from Magnolia officinalis as a raw material and convert it into a post-curable monomer through a one-step reaction, and the cured material has properties comparable to those of commercial products. Our work follows the principles of the UN sustainable development goals: affordable and clean energy (SDG 6), industry, innovation, and infrastructure (SDG 9), climate action (SDG 13).
|
Introduction
Among various natural products, magnolol is a very interesting compound. It contains two modified active groups including two allyl groups and two phenol units. Thus, this bio-based compound is an ideal starting material for the preparation of polymers, while most of the investigations focus on its pharmacological effects and its application as a fine chemical.1–5 There are a few reports regarding polymers based on magnolol.6–10 Therefore, investigation on the synthesis and properties of polymers based on magnolol is very desirable.
In recent years, much attention has been paid to organic materials with a low dielectric constant (Dk) and dielectric loss (Df) at high frequencies of more than 5 GHz because of their broad application as encapsulation resins in the microelectronics industry, especially as basis materials in the new generation of communication.11–17 From the perspective of application, a satisfactory low dielectric material should possess not only a low dielectric constant of less than 2.80 and low dielectric loss of lower than 5.0 × 10−3 at a frequency of higher than 5 GHz, but also display a low coefficient of thermal expansion (CTE)18 and good hydrophobicity.19 Thus, much effort has been made, and a lot of low dielectric materials have been explored and developed. Some examples include LCP,20–22 modified epoxies using active esters as curing agents23–27 and fluoro-containing polymers.28–31 However, there are a few species suitable for application in communication at high speed and high frequency. On the other hand, although commercial PTFE and its derivatives32 have been used in the electronics and microelectronics industries for many years, their processability and poor thermostability block their use. Hence, it is still necessary to develop suitable low dielectric materials.
It is noted that benzocyclobutene (BCB)-based polymers display good comprehensive properties including high thermostability,33 good dielectric properties,19 good film-forming ability and bonding strength on substrates.11,19,34 Therefore, study of organic materials containing BCB groups would be a convenient way for exploring new low dielectric materials with good properties.15,30,35 Based on the ease of conversion of magnolol into the functional precursors of polymers, we have designed and synthesized a magnolol-based monomer with benzocyclobutene groups. This monomer (M1) is easily prepared by a one-step reaction in a moderate yield. The cured resin based on this exhibits a Dk of 2.78 and a very low Df of 1.0 × 10−3 at a frequency of 10 GHz. In particular, the cured resin also exhibits good dimensional stability with a CTE of 46 ppm °C−1 and low water absorption of 0.5% even when immersed in boiling water for 96 h. These data imply that bio-based magnolol is an alternative resource for the preparation of electronic materials used in high technology fields. Here, we report the details.
Experimental section
Materials
Magnolol was purchased from Shanghai Defai Chemical Technology Co. Ltd. 4-Bromobenzocyclobutene was purchased from Chemtarget Technologies Co. Innocent (Beijing) Technology Co. Ligand L was purchased from Shanghai Haohong Biomedical Technology Co., Ltd. All solvents were used as received unless stated elsewhere.
Measurements
1H NMR, 13C NMR, and 19F NMR spectra were collected on an AVANCE 500 spectrometer with CDCl3 as the solvent. Elemental analysis (EA) was carried out using an Elementar VARIO ELIII apparatus. High-resolution mass spectrometry (HRMS) was performed using a Waters Premier GC-TOF MS instrument. Fourier transform-infrared (FT-IR) spectra were measured via a Thermo Scientific Nicolet spectrometer with KBr pellets in air. Differential scanning calorimetry (DSC) traces were obtained with a TA instrument (DSC Q200) at a heating rate of 10 °C min−1 under a nitrogen flow. Thermogravimetric analysis (TGA) curves were recorded on a TG 209F1 apparatus in nitrogen with a heating rate of 10 °C min−1. Dynamic mechanical analysis (DMA) was carried out on a DMA Q800 instrument in nitrogen with a heating rate of 5 °C min−1. Thermal mechanical analysis (TMA) was performed on a TA Q400 instrument in nitrogen with a heating rate of 5 °C min−1. The dielectric constant (Dk) and dielectric loss (Df) were determined on a Keysight n5227A vector network analyzer with a split post-dielectric resonator at a frequency of 10 GHz.
Synthesis of 1
A mixture of magnolol (5.33 g, 20 mmol), 4-bromobenzocyclobutene (10 mL, 60 mmol), cuprous iodide (400 mg, 2 mmol), ligand L (672 mg, 2.4 mmol), cesium carbonate (13.04 g, 40 mmol), sodium L-ascorbate (1.58 g, 8.0 mmol), and dioxane (20.0 mL) was stirred at a refluxing temperature under an atmosphere of N2 for 48 h, then cooled to room temperature and filtered. The filtrate was concentrated under reduced pressure. The obtained crude product was purified by column chromatography using n-hexane as the eluent. Pure M1 was obtained as a white solid in a yield of 65%. 1H NMR (500 MHz, CDCl3) δ 7.21 (s, 1H), 7.03 (d, J = 6.8 Hz, 1H), 6.87 (d, J = 7.9 Hz, 1H), 6.79 (d, J = 8.3 Hz, 1H), 6.70 (d, J = 7.6 Hz, 1H), 6.57 (s, 1H), 6.07 ∼ 5.82 (m, 1H), 5.16 ∼ 4.93 (m, 2H), 3.36 (d, J = 6.4 Hz, 2H), 3.14–2.94 (m, 4H). 13C NMR (126 MHz, CDCl3) δ 159.30, 156.92, 153.48, 146.04, 139.30, 137.36, 133.98, 131.84, 129.41, 128.52, 123.21, 118.24, 117.96, 115.59, 113.82, 77.16, 76.91, 76.65, 39.34, 28.81, 28.68. HRMS-EI (m/z): calcd for C34H30O2, 470.2240, found, 470.2237. Anal. calcd for C34H30O2: C, 86.78; H, 6.43. Found: C, 86.75; H, 6.47.
Preparation of the cured resin sheets for the measurement
A flat-bottomed glass tube with M1 (1.20 g) was put into a quartz tube furnace under an atmosphere of argon, and the furnace was allowed to heat to 80 °C and maintained at the temperature for about 1 h. The furnace was then heated to 180 °C, and maintained at 180 °C, 200 °C, 220 °C and 240 °C for 2 h, respectively. A fully cured M1 sheet was hence obtained.
Preparation of the cured polymer films
The solution of M1 (0.30 g) in mesitylene (3 mL) was heated under an atmosphere of N2 at 200 °C for 1 h to obtain a pre-polymer. After cooling to room temperature, the pre-polymer solution was spin-coated onto the surface of a silicon wafer. The wafer was then put into a quartz tube furnace, and treated at 220 °C and 240 °C for 2 h, respectively. Thus, a cured M1 film was obtained.
Results and discussion
Synthesis and characterization
Starting from magnolol, bio-based monomer M1 was successfully synthesized in a moderated yield of 65% through a facile one-step procedure, as shown in Scheme 1. Such a functionalized monomer with thermal cross-linkable BCB groups is easily soluble in common organic solvents such as toluene, chloroform, THF and acetone, implying its good processability.
 |
| Scheme 1 Procedure for the synthesis of M1. | |
The chemical structure of M1 was characterized by 1H NMR, 13C NMR, HRMS-EI and elemental analysis. The 1H NMR spectrum of M1 is shown in Fig. 1. As seen in Fig. 1, the peaks in the range of 6.57 ∼ 7.25 belong to the protons on the aromatic rings in the molecule. The characteristic peaks at 5.95, 5.06, and 3.36 ppm are assigned to the protons on the double-bond of propenyl groups. The peaks at 3.06 ppm are ascribed to the protons of the methylene group of BCB. The 13C NMR spectrum (see Fig. S1 in ESI†) further provides information to confirm the structure of M1. Moreover, the FT-IR spectrum, HRMS-EI and elemental analysis data of the monomer (see Experimental section) are also consistent with the proposed structure.
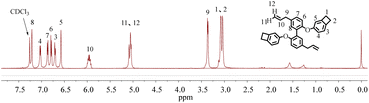 |
| Fig. 1
1H NMR spectrum of M1 in CDCl3 at 400 MHz. | |
Curing behavior of the monomer
After heating at high temperatures, monomer M1 can be converted into a cross-linked polymer (cured M1). The thermal crosslinking reaction of monomer M1 was monitored by DSC, and the results are exhibited in Fig. 2. As shown in Fig. 2, M1 displays a melting point of 78 °C and an onset curing temperature of 199 °C. The maximum exothermic peak temperature is observed at about 260 °C. At the second scan, no exothermic peak is observed, illustrating that monomer M1 has cured completely. The curing of M1 is related to the ring-open reaction of the BCB four-membered ring of the molecule. At high temperature, BCB groups have a tendency to form diradical or o-quinodimethane intermediates,36 which further convert to the homopolymer through a self-polymerization reaction or change to the copolymers by the Diels–Alder reaction with the double bond-containing molecules or groups. To well understand the curing process of M1, a schematic curing mechanism is depicted in Scheme 2.
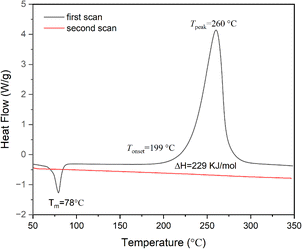 |
| Fig. 2 DSC traces of M1 at a heating rate of 10 °C min−1 in N2. | |
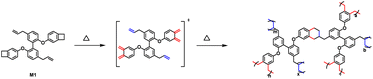 |
| Scheme 2 Schematic curing mechanism of monomer M1. | |
The curing reaction degree of M1 was studied by FT-IR spectroscopy, and the results are shown in Fig. 3. As can be seen from Fig. 3, the characteristic peaks of BCB at 1463 cm−1 and 989 cm−1 disappear after curing, and the characteristic peaks of allyl groups at 1639 cm−1 and 3078 cm−1 also disappear, suggesting that the curing reaction has completed and the allyl groups have participated in the curing reaction.
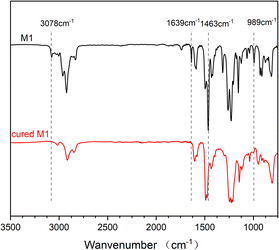 |
| Fig. 3 FT-IR spectra of M1 before and after curing. | |
Thermostability of cured M1
The thermostability of cured M1 was explored by TGA, and the results are shown in Fig. 4. Under a N2 atmosphere, cured M1 exhibited a 5% weight loss temperature (T5d) of 448 °C, such a T5d is superior to that of magnolol-based epoxy,8,9 as well as better than those of most of the bio-based polymers.37–39 The high thermostability may be ascribed to the rigid aromatic structure of the monomer.
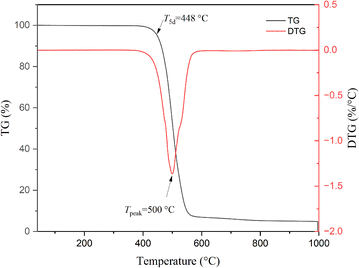 |
| Fig. 4 TGA curve of cured M1 at a heating rate of 10 °C min−1 in N2. | |
Dynamic mechanical properties of cured M1 were studied by DMA, and the results are depicted in Fig. 5. Estimating the peak of tan
δ gives a glass transition temperature (Tg) of 381 °C for cured M1. Such a high Tg implies the existence of a highly cross-linked network in cured M1. It can also be seen from Fig. 5 that cured M1 has a high E′ of 2.98 GPa at room temperature and a E′ of over 1.4 GPa even at a temperature of 300 °C. These data also suggest there is a highly cross-linked network in cured M1.
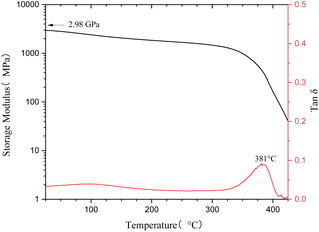 |
| Fig. 5 DMA curves of cured M1 at a heating rate of 5 °C min−1 in N2. | |
Thermal dimensional stability is an important parameter for materials used in the microelectronics industry. In our case, the thermal dimensional stability of cured M1 was evaluated by the coefficient of thermal expansion (CTE), which was measured by TMA. Fig. 6 depicts the CTE test results. As can be seen from Fig. 6, cured M1 exhibits a CTE of 46 ppm °C−1 in the temperature range of 50 to 250 °C. This CTE of cured M1 is lower than those of most of the low dielectric polymers, such as epoxy resins (72 ppm °C−1)40 and PPOs (56 ppm °C−1).41
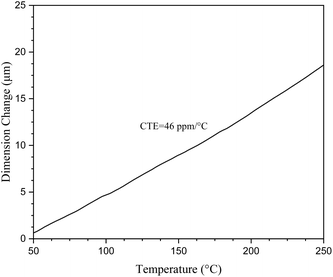 |
| Fig. 6 CTE curve of cured M1 at a heating rate of 5 °C min−1 in N2. | |
Hydrophobicity
High hydrophobicity is very important for polymers applied in the microelectronics field because it protects the devices from deterioration by moisture.42 In this contribution, the hydrophobicity of cured M1 was characterized by measuring the static water contact angle of water on the surface of the cured M1 film coated on a silicon wafer. As shown in Fig. 7, the contact angle of water on the surface of the cured M1 film is 95°. Further, water uptake of cured M1 was determined by immersing a cured resin sheet in boiling water for 96 h. The results indicate that cured M1 displays a water uptake of 0.5%. These results suggest that cured M1 possesses good hydrophobicity.
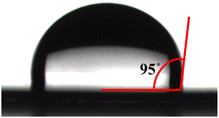 |
| Fig. 7 A photo image of the static contact angle of water on the surface of the cured M1 film. | |
Dielectric properties
One of the most important usages for low dielectric materials is as encapsulation resins used in the electronics and microelectronics industries.43 Thus, satisfactory low dielectric materials should possess a low dielectric constant (Dk) and low dielectric loss (Df). In particular, low Dk and Df are favorable for modern communication technology because they can solve the problems of signal delay and loss.34,44Dk and Df of cured M1 were measured using a split post dielectric resonator method at a frequency of 10 GHz, and the results are listed in Table 1. As summarized in Table 1, cured M1 displays a Dk of 2.78 with a Df of 1.0 × 10−3 at a frequency of 10 GHz. The Dk is lower than those of many commonly used dielectric materials,28,41 especially, the Df is lower than those of most commercial dielectric materials, such as polyimides (1.0 × 10−2),28 epoxy resins (2.0 × 10−2),40 and PPO (4.7 × 10−3).41 Dielectric materials with ultra low Df are necessary for the improvement of the signal transmission quality of high-frequency communication.45 The low Dk and Df can be attributed to the unique structure of M1. The rigidity and high torsional structure of M1 can enhance the free volume of the polymer and reduce the packing degree of the molecular chains, which are helpful to achieve low Dk of the cured resins. The multiple thermo-cross-linkable groups endow the cured polymer with high crosslinking density, which is beneficial to limit the movement of the dipoles in the polymers. As a result, cured M1 exhibits a low Df.
Table 1 Properties of cured M1
D
k
|
D
f
|
T
5d/°C |
T
g/°C |
CTE/ppm °C−1 |
Water uptakea |
Measured after immersing the samples in boiling water for 96 h.
|
2.78 |
1.0 × 10−3 |
448 |
381 |
46 |
0.50% |
Comprehensive properties of cured M1
A comparison of comprehensive properties of cured M1 with magnolol-based polymers and some reported bio-based BCB-containing resins is summarized in Table 2. As can be seen from Table 2, cured M1 exhibits good comprehensive properties, and it is also comparable to commercial products.46
Table 2 Comparison of the properties of cured M1
|
|
T
g
|
T
5d
|
D
k
|
D
f
|
Frequency |
References |
Magnolol-based polymers |
|
279 |
402 |
— |
— |
— |
9
|
|
— |
337 |
— |
— |
— |
8
|
|
151 |
329 |
— |
— |
— |
6
|
|
>500 |
527.6 |
— |
— |
— |
10
|
Bio-based BCB-containing resins |
|
— |
431 |
2.68 |
8.4 × 10−3 |
5 GHz |
39
|
|
334 |
483 |
2.60 |
1.4 × 10−3 |
10 GHz |
33
|
|
384 |
474 |
2.59 |
5.4 × 10−3 |
5 GHz |
19
|
|
132 |
473 |
2.56 |
1.2 × 10−3 |
5 GHz |
19
|
|
254 |
405 |
2.44 |
2.3 × 10−3 |
15 MHz |
37
|
|
261 |
406 |
2.51 |
5.0 × 10−3 |
0.1 ∼ 18 MHz |
38
|
A product from DOW chemicals |
Cyclotene™ |
293 |
446 |
2.70 |
8.0 × 10−3 |
1 MHz |
46
|
This work |
381 |
448 |
2.78 |
1.0 × 10−3 |
10 GHz |
|
Conclusion
In summary, we have successfully synthesized a functional monomer with thermally cross-linkable benzocyclobutene groups from bio-based magnolol through a one-step Ullman-Ma reaction. The thermally cross-linked product of the monomer displays good comprehensive properties including a low Dk of 2.78 and low Df of 1.0 × 10−3 at a frequency of 10 GHz, high T5d of 448 °C, high Tg of 381 °C and low CTE of 46 ppm °C−1 in the temperature range of 50 to 250 °C. Such properties are comparable to those of magnolol-based polymers and the reported benzocyclobutene-containing polymers, suggesting the bio-based monomer reported in this contribution is a suitable precursor for encapsulation resins for application in the microelectronics industry.
Author contributions
Zhuoyi Yang: synthesis, investigation, data-collection, writing – original draft. Jing Sun: supervision, writing – review & editing. Qiang Fang: supervision, conceptualization, writing – review & editing.
Conflicts of interest
There are no conflicts to declare.
Acknowledgements
Financial support from the Strategic Priority Research Program of the Chinese Academy of Sciences (Grant No. XDB 0590100) and Natural Science Foundation of China (NSFC, No. 21975278, 22075311, and 22175195) Technology Commission of Shanghai Municipality (23ZR1476200) is gratefully acknowledged.
References
- K. Bang, Y. Kim, B. Min, M. Na, Y. Rhee, J. Lee and K. Bae, Arch. Pharmacal Res., 2000, 23, 46–49 CrossRef CAS PubMed.
- Y. Lee, Y. Lee, C. Lee, J. Jung, S. Han and J. Hong, Pharmacol. Ther., 2011, 130, 157–176 CrossRef CAS PubMed.
- A. Sarrica, N. Kirika, M. Romeo, M. Salmona and L. Diomede, Planta Med., 2018, 84, 1151–1164 CrossRef CAS PubMed.
- J. Shen, K. Man, P. Huang, W. Chen, D. Chen, Y. Cheng, P. Liu, M. Chou and Y. Chen, Molecules, 2010, 15, 6452–6465 CrossRef CAS PubMed.
- K. Watanabe, H. Watanabe, Y. Goto, M. Yamaguchi, N. Yamamoto and K. Hagino, Planta Med., 1983, 49, 103–108 CrossRef CAS PubMed.
- M. Bu, X. Zhang, T. Zhou and C. Lei, Eur. Polym. J., 2022, 180, 111595 CrossRef CAS.
- W. Guo, F. Liang, S. Chen, D. Zhang, W. Li, K. Qian, Y. Xu and B. Fei, Polym. Degrad. Stab., 2022, 202, 110002 CrossRef CAS.
- C. Ma, L. Qian and J. Li, Polym. Degrad. Stab., 2021, 190, 109630 CrossRef CAS.
- Y. Qi, Z. Weng, K. Zhang, J. Wang, S. Zhang, C. Liu and X. Jian, Chem. Eng. J., 2020, 387, 124115 CrossRef CAS.
- Z. Weng, L. Song, Y. Qi, J. Li, Q. Cao, C. Liu, S. Zhang, J. Wang and X. Jian, Polymer, 2021, 226, 123814 CrossRef CAS.
- M. Dai, Y. Tao, L. Fang, C. Wang, J. Sun and Q. Fang, ACS Sustain. Chem. Eng., 2020, 8, 15013–15019 CrossRef CAS.
- S. Galli, A. Cimino, J. Ivy, C. Giacobbe, R. Arvapally, R. Vismara, S. Checchia, M. Rawshdeh, C. Cardenas, W. Yaseen, A. Maspero and M. Omary, Adv. Funct. Mater., 2019, 29, 1904707 CrossRef.
- G. Maier, Prog. Polym. Sci., 2001, 26, 3–65 CrossRef CAS.
- D. Shamiryan, T. Abell, F. Iacopi and K. Maex, Mater. Today, 2004, 7, 34–39 CrossRef CAS.
- M. Shi, G. Huang, J. Sun and Q. Fang, Polym. Chem., 2023, 14, 999–1006 RSC.
- S. Shi, X. Liao, W. Tang, P. Song, F. Zou, Z. Fan, F. Guo and G. Li, Adv. Eng. Mater., 2022, 24, 2100874 CrossRef CAS.
- L. Wang, X. Liu, C. Liu, X. Zhou, C. Liu, M. Cheng, R. Wei and X. Liu, Chem. Eng. J., 2020, 384, 123231 CrossRef CAS.
- Y. Wang, Y. Tao, J. Zhou, J. Sun and Q. Fang, ACS Sustain. Chem. Eng., 2018, 6, 9277–9282 CrossRef CAS.
- F. Liu, Q. Fang and J. Sun, ACS Appl. Polym. Mater., 2022, 4, 7173–7181 CrossRef CAS.
- P. Dutta, B. Saikia, P. Alapati and K. Borah, J. Electron. Mater., 2021, 50, 1434–1443 CrossRef CAS.
- Z. Feng, X. Liu, W. Zhang, J. Zeng, J. Liu, B. Chen, J. Lin, L. Tan and L. Liang, J. Mater. Sci., 2022, 57, 1156–1173 CrossRef CAS.
- S. Wang, S. Ma, N. Li, S. Jie, Y. Luo and X. Gao, Eur. Polym. J., 2023, 196, 112302 CrossRef CAS.
-
K. Li, China Pat., CN116240733A, 2022 Search PubMed.
-
W. Lin, T. Huang, J. You, Y. Xu, World Pat., WO2022088239A1, 2022 Search PubMed;
W. Lin, T. Huang, J. You, Y. Xu, China Pat., CN114478850A, 2022 Search PubMed.
-
L. Peng, H. Bu, L. Bu, China Pat., CN114958188A, 2022 Search PubMed;
L. Peng, H. Bu, L. Bu, China Pat., CN114958188B, 2023 Search PubMed.
-
R. Sun, P. Xu, J. Yu, S. Yu, S. Luo, China Pat., CN115565717A, 2023 Search PubMed;
R. Sun, P. Xu, J. Yu, S. Yu, S. Luo, World Pat., WO2024045159A1, 2024 Search PubMed.
-
Y. Zhou, China Pat., CN115583815A, 2022 Search PubMed.
- Y. Feng, J. Sun and Q. Fang, ACS Appl. Polym. Mater., 2023, 5, 4419–4426 CrossRef CAS.
- M. Huangfu, D. Shen, X. Zhi, Y. Zhang, Y. Jia, Y. An, X. Wei and J. Liu, Nanomaterials, 2021, 11, 537 CrossRef CAS PubMed.
- F. Liu, J. Sun and Q. Fang, ACS Appl. Polym. Mater., 2022, 4, 842–848 CrossRef CAS.
- J. Wang, J. Zhou, K. Jin, L. Wang, J. Sun and Q. Fang, Macromolecules, 2017, 50, 9394–9402 CrossRef CAS.
- P. Rae and D. Dattelbaum, Polymer, 2004, 45, 7615–7625 CrossRef CAS.
- H. Zhang, J. Sun and Q. Fang, Eur. Polym. J., 2022, 179, 111527 CrossRef CAS.
- W. Volksen, R. Miller and G. Dubois, Chem. Rev., 2010, 110, 56–110 CrossRef CAS PubMed.
- J. Hou, J. Sun and Q. Fang, Eur. Polym. J., 2022, 163, 110943 CrossRef CAS.
- M. Marks, J. Erskine and D. Mccrery, Macromolecules, 1994, 27, 4114–4126 CrossRef CAS.
- F. Fu, M. Shen, D. Wang, H. Liu, S. Shang, F. Hu, Z. Song and J. Song, Biomacromolecules, 2022, 23, 2856–2866 CrossRef CAS PubMed.
- F. Fu, D. Wang, M. Shen, S. Shang, Z. Song and J. Song, RSC Adv., 2019, 9, 29788–29795 RSC.
- G. Huang, L. Fang, C. Wang, M. Dai, J. Sun and Q. Fang, Polym. Chem., 2021, 12, 402–407 RSC.
- X. Chen, J. Hou, Q. Gu, Q. Wang, J. Gao, J. Sun and Q. Fang, Polymer, 2020, 195, 122443 CrossRef CAS.
- C. Chen, Z. Gu, Y. Tsai, R. Jeng and C. Lin, Polymer, 2018, 140, 225–232 CrossRef CAS.
- H. Yuan, J. Xu and L. Xie, Mater. Chem. Phys., 2011, 129, 1195–1200 CrossRef CAS.
- X. Zhao and H. Liu, Polym. Int., 2010, 59, 597–606 CrossRef CAS.
- M. Li, J. Sun and Q. Fang, Polym. Chem., 2021, 12, 4501–4507 RSC.
- Z. Hu, X. Liu, T. Ren, H. Saeed, Q. Wang, X. Cui, K. Huai, S. Huang, Y. Xia, K. Fu, J. Zhang and Y. Chen, Polym. Eng. Sci., 2022, 42, 677–687 CAS.
- D. Burdeaux, P. Townsend, J. Carr and P. Garrou, J. Electron. Mater., 1990, 19, 1357–1364 CrossRef CAS.
|
This journal is © The Royal Society of Chemistry 2024 |
Click here to see how this site uses Cookies. View our privacy policy here.