DOI:
10.1039/D4SU00163J
(Paper)
RSC Sustain., 2024,
2, 1985-1993
Biodegradable and wood adhesive polyesters based on lignin-derived 2-pyrone-4,6-dicarboxylic acid†
Received
4th April 2024
, Accepted 22nd May 2024
First published on 23rd May 2024
Abstract
2-Pyrone-4,6-dicarboxylic acid (PDC) is a chemically stable metabolic intermediate of lignin, and its condensation polymers can be synthesized by utilizing the functionality of two carboxylic acids. In this study, biodegradable PDC-based polyesters, namely, P(PDC2) and P(PDC3), with strong adhesive properties toward wood were developed by polycondensation with diols. The adhesive properties of P(PDC2) and P(PDC3) were fully characterized by tensile lap shear strength measurements, X-ray photoelectron spectroscopy, and cross-sectional computed tomography. The biodegradability of P(PDC2) and P(PDC3) in natural pond water was also measured. Both P(PDC2) and P(PDC3) showed strong adhesive strengths to wood with the highest average adhesion of 5.55 MPa, which usually causes wood failure. In order to quantitatively investigate the adhesive strengths of P(PDC2) and P(PDC3), decomposition acceleration experiments were performed. The average adhesive strength of 2.57 MPa remained even after immersion in hot water at 60 °C for 4 h, which demonstrated the excellent adhesive strength and water resistivity of the PDC-based polyesters. P(PDC2) and P(PDC3) remained almost uniformly biodegraded after 60 days of incubation in a simulated natural environment and reached a biodegradation rate of about 54% and 52%, respectively. The excellent adhesive properties and biodegradability of the PDC-based polyesters provide a new strategy for preparing safe and environmentally-friendly bio-based adhesives.
Sustainability spotlight
Manufacturing polymeric materials from petroleum increases carbon dioxide emissions, which in turn causes climate change. It also causes ocean pollution from microplastics because they usually do not biodegrade. To solve these problems, it is desirable to develop biomass-based biodegradable polymers. Biodegradable polymers using lactic acid and succinic acid have already been established, but excellent functionality has not been achieved. In this study, a new biomass component derived from lignin was used to develop a biodegradable polymer that exhibits excellent wood adhesion properties. This study contributes to SDGs 13 “Climate action” and 14 “Life below water”.
|
Introduction
As a sustainable alternative to petrochemicals, bio-based and environmentally-friendly renewable materials have attracted much attention.1–6 Lignin, one of the carbon resources abundant in nature, has a complex three-dimensional reticular structure containing aromatic rings and thus has the potential to be utilized for the preparation of (pseudo-)aromatic functional biodegradable small molecules.7–9 In a previous study, lignin-derived aromatic compounds were successfully converted into 2-pyrone-4,6-dicarboxylic acid (PDC) on a large scale using engineered Pseudomonas putida strains.10 PDC consists of a polar pseudo-aromatic pyrone ring with two carboxyl groups, which can be directly dehydrated and condensed with diols to synthesize a variety of PDC-based polyesters with good mechanical and biodegradable properties.11–14 In addition, various studies have shown that PDC-based polymers have strong adhesive properties to various metallic or non-metallic materials, making it essential to further develop their future as adhesives.15–18
Adhesives have an extensive range of applications in furniture, packaging, electronics and construction, and a high number of wood adhesives are inevitably used in the production of wood composites, such as plywood, particle board, and fibre board.19–23 However, most of the wood adhesives used in the production of wood composites are aldehyde-based, such as urea-formaldehyde, phenol-formaldehyde, and melamine-formaldehyde resins,24–26 which inevitably release formaldehyde, a carcinogen that has a severe impact on human health during production and use. This problem poses a serious challenge to applying traditional adhesives, thus developing non-toxic, environmentally-friendly, and biodegradable bio-based adhesives is of far-reaching significance. Researchers have invested a great deal of effort into the development of green adhesives, and more and more bio-based, non-toxic, and sustainable adhesives have been developed.27–33
In our past studies, we successfully prepared functional PDC-based polyesters, P(PDC2) and P(PDC3) (Scheme 1), by the direct polycondensation of PDC with 1,2-ethylene glycol or 1,3-propylene glycol at high temperature.11 Although P(PDC2) and P(PDC3) have a strong adhesion to various metals, such as stainless steel, iron, aluminium, and copper, their adhesive properties to wood have never been investigated. Since PDC is prepared from lignin, which is environmentally friendly, and PDC-based polymers are biodegradable, it is of great significance to study their adhesive properties to wood. In this study, we synthesized the PDC-based polyesters, P(PDC2) and P(PDC3), and fully characterized their adhesive properties to wood in various environments. By cross-sectional computed tomography, we analysed the PDC-based polyesters between wood plates and speculated on the reasons for the differences in the adhesive properties between the different PDC-based polyesters. The structural changes in the PDC-based polyesters before and after hot-pressing were also analysed by X-ray photoelectron spectroscopy. In addition, since the PDC-based polyesters are degradable, the biodegradability of P(PDC2) and P(PDC3) in a simulated natural environment according to ISO 14851:1999 was also tested.
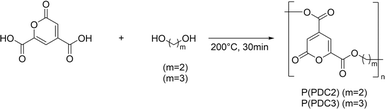 |
| Scheme 1 Synthetic route of P(PDC2) and P(PDC3). | |
Experimental
Materials
2-Pyrone-4,6-dicarboxylic acid (PDC) was prepared from vanillic acid by microbial fermentation in a sodium ion-free medium, as previously reported.10 The culture medium containing PDC was centrifuged to remove the bacteria. The resultant supernatant was adjusted the pH to less than 1 with hydrochloric acid, and then extracted with ethyl acetate. The extracted liquid was dried with magnesium sulfate, evaporated, and recrystallized to give pure PDC. Ethylene glycol was purchased from Kanto Chemical Co., Inc. (Tokyo, Japan). Antimony(III) oxide was purchased from the Fujifilm Wako, Co. (Osaka, Japan). 1,3-Propanediol was purchased from Tokyo Kasei Kogyo Co., Ltd (Tokyo, Japan). The cypress wood plate pieces were kindly supplied by the Sumitomo Forestry Co. (Tokyo, Japan). A woodworking bond was purchased from Konishi, Co., Ltd (Tokyo, Japan). Bis(2-hydroxyethyl)-2-pyrone-4,6-dicarboxylate (BHPDC) was prepared according to a literature method.15 All reagents were used without further purification.
The pond water and soil from the bottom of the pond were collected from the Senzokuike Park in Ota City (Tokyo, Japan). It was used on the day of sampling. For preparation of the standard test medium according to ISO 14851:1999, ammonium chloride (NH4Cl), anhydrous potassium dihydrogen phosphate (KH2PO4), anhydrous dipotassium hydrogen phosphate (K2HPO4), magnesium sulfate heptahydrate (MgSO4·7H2O), calcium chloride dihydrate (CaCl2·2H2O) and iron(III) chloride hexahydrate (FeCl3·6H2O) were purchased from Kanto Chemical Co., Inc. (Tokyo, Japan). Disodium hydrogen phosphate dihydrate (Na2HPO4·2H2O) was purchased from Tokyo Kasei Kogyo Co., Ltd (Tokyo, Japan). The PET pellets produced by the Toray Co. (Tokyo, Japan) were used as a control sample. The cellulose (microcrystalline) was purchased from Kanto Chemical Co., Inc. (Tokyo, Japan). All reagents were used without further purification.
The synthetic route of P(PDC2) and P(PDC3) is the same as previously reported literature.11 Their molecular weights estimated from GPC (eluent: THF) were 2000–4000 and the weight loss temperatures were about 250 °C. These values were similar to those previously reported.11
P(PDC2): PDC (18.41 g, 0.1000 mol), antimony trioxide (1 mol%, 292 mg, 1.00 mmol) and ethylene glycol (5.578 mL, 0.1000 mol) were placed in a round-bottom flask. After stirring at 140 °C for 0.5 h to completely dissolve the PDC in ethylene glycol, the temperature was increased to 200 °C and stirred for another 0.5 h. The reacted liquid was cooled to room temperature to obtain P(PDC2) (20.84 g, 99.2%) as a yellow solid.
P(PDC3): PDC (18.41 g, 0.1000 mol), antimony trioxide (1 mol%, 292 mg, 1.00 mmol) and 1,3-propanediol (7.248 mL, 0.1000 mol) were placed in a round-bottom flask. After stirring at 140 °C for 0.5 h to completely dissolve the PDC in 1,3-propanediol, the temperature was increased to 200 °C and stirred for another 0.5 h. The reacted liquid was cooled to room temperature to obtain P(PDC3) (21.48 g, 95.8%) as a yellow solid.
Adhesive measurements
Tensile lap shear strength measurements were obtained according to JIS K 6850-1994 using a Shimadzu Co. (Tokyo, Japan) autograph AGS-10kNX STD. The size of the wood plate pieces (cypress wood) used for the adhesion measurements was 25.0 mm × 100.0 mm × 3.5 mm. Approximately 60 mg of the PDC-based polyester (P(PDC2) or P(PDC3)) solid or woodworking bond was placed on the wood plate surface. A set of two plates was placed in contact with each other by (hot-)pressing at 1.25 MPa. To control the reliability of the adhesive conditions in each test environment, a 0.20 mm thick Teflon spacer was used between the wood plates. This was used to keep the thickness of the adhesive layer at 0.20 ± 0.02 mm. To eliminate residual stresses within the adhesive itself during each measurement, the wood plates and the adhesive were slowly cooled to room temperature after hot-pressing. The failure force was measured at room temperature at the rate of 1 mm min−1. In order to balance the forces, an additional set of wood plates was used when measuring the tensile lap shear strengths. In addition to the two original wood plates adhered by the adhesive, a pair of other wood plates with the same size and thickness was placed on each side to fill the shortfall and balance the force on the measured wood plates. The adhesive strengths were calculated as the failure force divided by the adhesive area (25.00 ± 1.00 mm × 10.00 ± 1.00 mm).
Accelerated deterioration treatment
The mechanical strength of wood is not as strong as that of metal, which means that the adhesive strength of the adhesives may exceed the mechanical strength of the wood itself, and the wood, not the adhesive, is likely to be damaged (Fig. S1†). Therefore, accelerated deterioration treatment of the adhesives is necessary to measure their adhesive abilities to wood in harsh environments. In this study, the adhesive properties of P(PDC2) and P(PDC3) were measured under the following five treatments after hot-pressing.
(1) No accelerated deterioration treatment.
(2) Soak in DI water at 30 °C for 3 h → soak in DI water at 20 °C for 10 min.
(3) Soak in DI water at 60 °C for 3 h → soak in DI water at 20 °C for 10 min.
(4) Soak in boiling DI water for 4 h → soak in DI water at 60 °C for 20 h → soak in boiling DI water for 4 h → soak in DI water at 20 °C for 10 min.
(5) Soak in boiling DI water for 72 h.
After the accelerated deterioration treatment, the samples were immediately used for adhesive measurements.
Cross-sectional computed tomography
Cross-sectional computed tomography was recorded using a Rigaku (Tokyo, Japan) nano3DX X-ray Microscope. After hot-pressing, the wood plates and P(PDC2) or P(PDC3) were cut into 1 mm strips, and a cross-sectional computed tomography analysis was performed on the adhesive layer between the wood plates.
X-ray photoelectron spectroscopy
X-ray photoelectron spectroscopy (XPS) was recorded by a ULVAC-PHI (Kanagawa, Japan) PHI 5000 VersaProbe III. The P(PDC2) and P(PDC3) powders without hot-pressing were cast on copper tape for the XPS analysis. For P(PDC2) and P(PDC3) after hot-pressing, the adhesive layer between the wood plates was analysed. For reference, wood plates without any treatment were also analysed.
Biodegradation test
Biochemical oxygen demand (BOD) tests were performed to evaluate the biodegradability of P(PDC2), P(PDC3), PET, PDC, and BHPDC in the simulated natural environment by an OxiTop IS-6 (WTW GmbH, Weilheim in Oberbayern, Germany) referring to the ISO 14851:1999 standard. The following buffer solutions were prepared: solution A; KH2PO4, 8.5 g L−1; K2HPO4, 21.75 g L−1; Na2HPO4, 33.4 g L−1; NH4Cl, 0.5 g L−1, solution B; MgSO4·7H2O, 22.5 g L−1, solution C; CaCl2·2H2O, 36.4 g L−1, solution D, FeCl3·6H2O, 0.25 g L−1. To prepare 1 L standard test medium, 10 mL of solution A and 1 mL of each of solutions B, C, and D were added to 500 mL of water and the solution was made up to 1 L. To prepare the soil inoculum for the BOD test, the soil from the bottom of the pond (10.0 g) was dispersed in a standard test medium and stirred for at least 10 min. After standing for 2 h, the supernatant was filtered and used as soil inoculum.
Briefly, the biodegradation tests were performed in the dark, in closed 250 mL vessels, and incubated at 25 °C. To each of the vessels, about 100 mL of standard test medium was added in all the experiments. Subsequently, about 10 mg of the test materials and a volume fraction of 2% of soil inoculum were added to the corresponding vessels, and some vessels without test materials were retained as blanks. Each group has at least three vessels. CO2 evolved from the test materials was trapped by sodium hydroxide (350 mg) inside the vessels. The oxygen consumption in the vessels was calculated by the pressure change of the gas in the closed vessels. The biodegradability was estimated using the following equation:
where BOD
sample (mg L
−1) represents the amount of oxygen consumption from a vessel and test material at time
t, BOD
blank (mg L
−1) is the average amount of oxygen consumption of the blank at time
t, and ThOD (mg L
−1) is the maximum amount of oxygen consumption that could be theoretically consumed by the test material based on the amount of added carbon.
For the biodegradation tests, P(PDC2) and P(PDC3) were ground into powder and screened through a sieve to control particle size less than 250 μm.
Results and discussion
Adhesive properties
Before the adhesive measurements, since the water content of the wood itself affects the mechanical strength of the wood to a certain extent and possibly also affects the adhesive properties of the adhesives, it is necessary to first evaluate the water content of the wood. The weight of the wood dried in a vacuum oven at 100 °C for 72 hours was compared to the weight before drying, and the water content was calculated by the following equation:
where Mbefore (g) represents the mass of wood before drying, and Mafter (g) represents the mass of wood after drying. The water content of the cypress test plates was 5.97%. At this water content, the tensile lap shear strength of the cypress wood used in this study was about 7 MPa.
Since PDC is derived from lignin, it is interesting to study the adhesion properties of PDC polyesters to wood. The adhesive properties of P(PDC2) and P(PDC3) to cypress wood were evaluated under different hot-press conditions, and the retention of the adhesive properties of the PDC polyester to wood by accelerated deterioration treatment was investigated (Fig. 1).
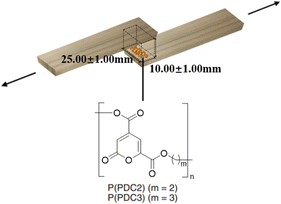 |
| Fig. 1 The tensile lap-shear strengths measurements of P(PDC2) and P(PDC3). | |
However, since the strength of the PDC's adhesive ability on wood is unknown, it is necessary to first know the approximate adhesive strength. In this context, P(PDC3), which has excellent mechanical strength and film-forming properties, was first selected as a sample and its adhesion to wood was measured under the same conditions as metal. On a wood plate, 60 mg of P(PDC3) was placed, and the paired plates were then hot-pressed under vacuum at the pressure of 1.25 MPa and 200 °C for one hour.
The results showed that P(PDC3) retained its adhesive properties to wood even after alternating boiling and warm water treatments. P(PDC3) without accelerated deterioration treatment caused the wood failure, and the tensile lap shear strength (3.86 MPa) was only about half of the average tensile lap shear strength of cypress (7 MPa), which indicated that the strength of the wood was significantly affected by the vacuum treatment at 200 °C (Fig. 2(a) and Table 1). In addition, the water content of the wood in all the treatment groups was below 0%, which indicated that not only did the wood lose water after the 200 °C vacuum hot-pressing, but it may have lost its own mass, resulting in a significant decrease in its mechanical strength. Observation of the cross sections revealed that the untreated P(PDC3) caused the wood to fracture, while the warm water-treated P(PDC3) lost some of its adhesive and separated from the wood, leaving a thin layer of adhesive on the wood (Fig. S2†). P(PDC3) treated alternately with boiling water and warm water showed a change in its properties. It adhered to both sides of the wood in a liquid form and still retained some adhesive strength, indicating that P(PDC3) also has a strong adhesive strength to the wood plates as does the metal plates. After a prolonged boiling water treatment, P(PDC3) lost its adhesive properties. This result indicated that extreme temperatures and humid environments have a significant impact on the adhesive properties of P(PDC3).
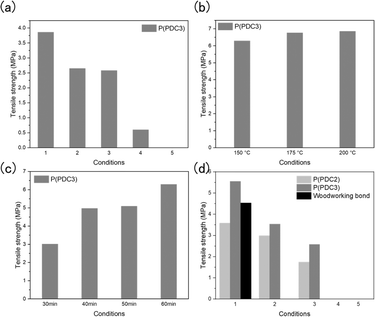 |
| Fig. 2 Adhesive properties of P(PDC2) and P(PDC3) at different treatment conditions between wood plates under different accelerated deterioration treatments. (a) Adhesive properties of P(PDC3) hot pressed at 200 °C for one hour under different accelerated deterioration treatment conditions. (b) Adhesive properties of P(PDC3) hot pressed at 150/175/200 °C for one hour. (c) Adhesive properties of P(PDC3) hot pressed at 150 °C for 30/40/50/60 min. (d) Adhesive properties of P(PDC2) and P(PDC3) hot pressed at 175 °C for 30 min and adhesive properties of woodworking bond pressed at 25 °C for 30 min under different accelerated deterioration treatments. | |
Table 1 Tensile lap shear strengths (MPa) of P(PDC3) hot pressed at 200 °C for one hour under different accelerated deterioration treatment conditions according to JIS K 6850-1994
|
Tensile lap-shear strength [MPa] |
(1) No accelerated deterioration treatment; (2) soak in DI water at 30 °C for 3 h → soak in DI water at 20 °C for 10 min; (3) soak in DI water at 60 °C for 3 h → soak in DI water at 20 °C for 10 min; (4) soak in boiling DI water for 4 h → soak in DI water at 60 °C for 20 h → soak in boiling DI water for 4 h → soak in DI water at 20 °C for 10 min; (5) soak in boiling DI water for 72 h.
Wood failure.
Time to lose adhesive ability.
|
Conditionsa |
1 |
2 |
3 |
4 |
5 |
P(PDC3) |
3.86b |
2.65 |
2.58 |
0.60 |
-(∼18 h)c |
The vacuum treatment during hot-pressing was removed because of the significant water loss in the wood, resulting in a considerable reduction in the mechanical strength. Since prolonged treatment of the wood in an aerobic environment at high temperatures can cause wood fires, it was necessary to measure the adhesive properties at lower temperatures or shorter hot-press times. Based on the same measurement method, 60 mg of P(PDC3) was cast on the wood plate surface, then the paired plates were hot-pressed at 1.25 MPa at different temperatures for different times.
First, the adhesive properties of P(PDC3) to wood were measured by hot-pressing for 1 h at different temperatures. It can be seen that the adhesive strength of P(PDC3) to wood gradually increased with the increasing temperature from 150 to 200 °C (Fig. 2(b) and Table 2). This may be due to the possibility that the adhesion mechanism of the PDC polymers to wood is similar to that of metals, and at higher temperatures, the pyrone ring of PDC is most likely to open and interact with the material surface to cause adhesion. In addition, it can be seen that the tensile lap shear strengths that caused wood failure were all close to 7 MPa. This indicated that the vacuum treatment had a significant effect on the mechanical strength of the wood, and P(PDC3) exhibited a higher adhesive strength than the tensile lap shear strength of the wood.
Table 2 Tensile lap shear strengths (MPa) of P(PDC3) hot pressed at 150/175/200 °C for one hour according to JIS K 6850-1994
|
Tensile lap-shear strength (MPa) |
Wood failure.
|
Conditions |
150 °C |
175 °C |
200 °C |
P(PDC3) |
6.29 |
6.76a |
6.85a |
For the adhesive properties of P(PDC3) to wood at the different hot-press times, the reference temperature was 150 °C, where differences are easily observed (Fig. 2(c) and Table 3). It can be seen that the adhesive strength gradually increased with the increase in the hot-press time, and the difference in the adhesive strength of P(PDC3) at 40/50/60 min was slight, but the adhesive strength of P(PDC3) at 30 min was significantly lower than that for the other measured times. This may be due not only to the insufficient hot-press time, but also to the fact that the thermal conductivity of the wood took time to reach the specified temperature.
Table 3 Tensile lap shear strengths (MPa) of P(PDC3) hot pressed at 150 °C for 30/40/50/60 min according to JIS K 6850-1994
|
Tensile lap-shear strength (MPa) |
Conditions |
150 °C – 30 min |
150 °C – 40 min |
150 °C – 50 min |
150 °C – 60 min |
P(PDC3) |
3.01 |
4.97 |
5.09 |
6.29 |
Based on the previous experimental results, the adhesion of P(PDC3) and P(PDC2) to wood under different accelerated deterioration treatments was measured by hot-pressing at 175 °C for 30 min as the experimental conditions (Fig. 2(d) and Table 4). As a comparison, the adhesion of woodworking bond was also measured by pressing at 25 °C for 30 min. To accelerate the drying of woodworking bond, a vacuum was applied during the pressing. P(PDC3) showed a decrease in the adhesive strength and loss of its resistance in boiling water, possibly due to the insufficient hot-press temperature and time. However, the adhesive properties of P(PDC3) under the warm water treatment conditions were better than those of the adhesive hot-pressed at 200 °C for 60 min, and P(PDC3) without the accelerated deterioration treatment maintained the high adhesive strength to wood, indicating the high adhesive ability of P(PDC3) to wood. A comparison of P(PDC2) and P(PDC3) showed that although the adhesion of P(PDC2) to wood was overall lower than that of P(PDC3) under the same accelerated deterioration treatment, P(PDC2) showed strong adhesive properties, which were only slightly lower than the commercial woodworking bond without accelerated deterioration treatment. This may be due to the possibility that the mechanical properties and film-forming properties of P(PDC2) are weaker than those of P(PDC3).
Table 4 Tensile lap shear strengths (MPa) of P(PDC2) and P(PDC3) hot pressed at 175 °C for 30 min and woodworking bond pressed at 25 °C for 30 min under different accelerated deterioration treatments according to JIS K 6850-1994a
Conditionsb |
Tensile lap-shear strength [MPa] |
1 |
2 |
3 |
4 |
5 |
The tensile lap shear strengths are average values of 5 measurements.
(1) No accelerated deterioration treatment; (2) soak in DI water at 30 °C for 3 h → soak in DI water at 20 °C for 10 min; (3) soak in DI water at 60 °C for 3 h → soak in DI water at 20 °C for 10 min; (4) soak in boiling DI water for 4 h → soak in DI water at 60 °C for 20 h → soak in boiling DI water for 4 h → soak in DI water at 20 °C for 10 min; (5) soak in boiling DI water for 72 h.
Wood failure.
Time to lose adhesive ability.
|
Ave. |
Wood-working bond |
4.53 |
−(∼3 h)d |
−(∼2.5 h)d |
−(∼20 min)d |
— |
P(PDC3) |
5.55c |
3.54 |
2.57 |
−(3 h)d |
— |
P(PDC2) |
3.58 |
2.99 |
1.75 |
−(2 h)d |
— |
Standard deviation |
Wood-working bond |
3.01 |
— |
— |
— |
— |
P(PDC3) |
0.54 |
0.64 |
0.65 |
— |
— |
P(PDC2) |
0.64 |
0.71 |
0.79 |
— |
— |
Cross-sectional computed tomography
To verify the idea that the adhesive properties may be influenced by the mechanical properties and film-forming properties, P(PDC2) and P(PDC3) were observed by cross-sectional computed tomography (Fig. 3). Although voids are present in the adhesive layers of both P(PDC2) and P(PDC3) (Fig. 3a(2) and b(2)), it was clearly observed that P(PDC2) has larger voids than P(PDC3) and their distribution was more non-uniform. This could significantly affect the mechanical strength of P(PDC2) and thus the adhesion strength of P(PDC2). Comparing Fig. 3a(1) and b(1), it can be seen that the P(PDC3) adhesive layer is more homogeneous and denser, which leads to better mechanical properties of the P(PDC3) adhesive layer. This feature affected the adhesive strength.
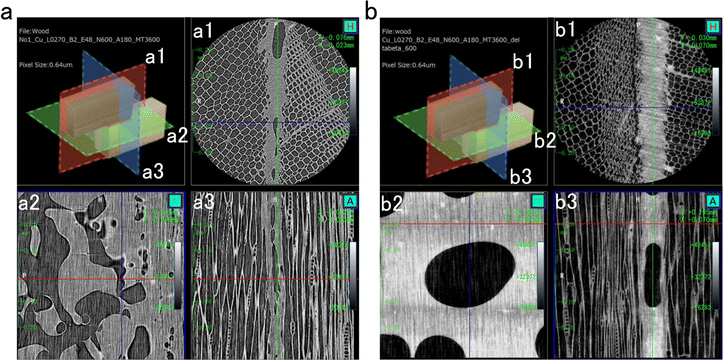 |
| Fig. 3 Computed tomography images of wood paired sites with (a) P(PDC2) and (b) P(PDC3) as adhesives. The cut planes of each figure are shown in the upper left inset. | |
X-ray photoelectron spectroscopy
To further confirm the structural changes of P(PDC2) and P(PDC3) after hot-pressing between the wood plates, an X-ray photoelectron spectroscopy analysis was performed. In the C 1s core level scan spectra of P(PDC2) and P(PDC3) without hot-pressing, there were three characteristic peaks at 284.4, 285.9, and 288.4 eV (Fig. 4), which were assigned to the C–C, C–O, and C
O bonds, respectively. After the hot-pressing treatment, it is evident from the C1s core level scan spectra that the peak ratios of the C–C and C–O bonds are substantially increased compared to the C
O bonds. In this case, the ratio of the P(PDC2) peaks is significantly different from that of P(PDC3), which may be caused by the fact that the P(PDC2) on the wood plates does not entirely cover the substrate (wood surface) and the XPS analysis is affected by the substrate peaks. Due to the relatively poor film formation and fluidity of P(PDC2), the adhesive layer formed during hot-pressing had abundant voids. P(PDC2) was thus in a granular form and could not completely cover the wood plates. This also explains why the adhesive strength of P(PDC2) to wood was not as good as that of P(PDC3).
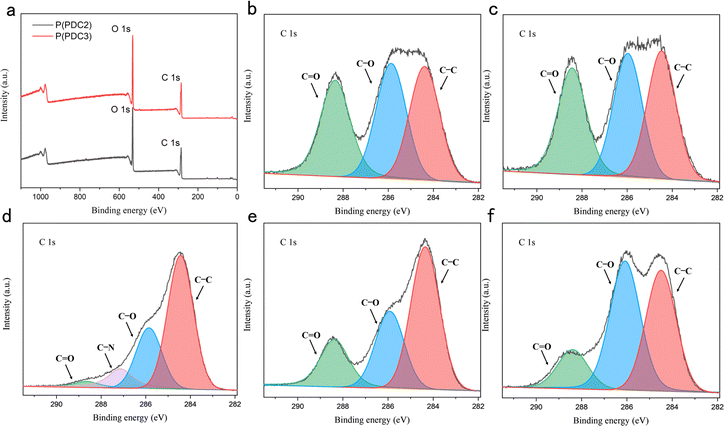 |
| Fig. 4 (a) XPS survey spectra of P(PDC2) and P(PDC3), (b) C 1s core-level spectrum of P(PDC2), (c) C 1s core-level spectrum of P(PDC3), (d) C 1s core-level spectrum of cypress wood plate, (e) C 1s core-level spectrum of P(PDC2) after hot-pressing, (f) C 1s core-level spectrum of P(PDC3) after hot-pressing. | |
The change in the ratio of the peaks before and after hot-pressing in the XPS analysis confirmed that the structures of P(PDC2) and P(PDC3) changed after the hot-pressing and cross-links with the wood and created adhesion. It has been previously reported that when used as a metal adhesive, the pyrone ring of the PDC-based polymer opens under heated conditions and forms covalent bonds with oxides on the metal surface, resulting in adhesion.34 Similar to this, due to the high number of hydroxyl groups in wood, as represented by cellulose, the PDC polymers are expected to react under heating conditions, resulting in a higher ratio of C–O and C–C bonds as shown in the XPS analysis. Similar to this result, O 1s core level scan spectra also showed a higher ratio of C–O bonds (Fig. S3(f)†). These demonstrated that PDC polymers can be used not only for metal adhesives but also for wood.
Biodegradation test
The biodegradability of P(PDC2) and P(PDC3) and their lower molecular weight component units, PDC and BHPDC, was measured at 25 °C according to ISO 14851:1999 standard (Fig. 5). It should be noted that the previously reported biodegradability of PDC polymers was assessed in compost.12 Under the same conditions, we tested PET as a non-biodegradable comparison but a structurally similar polymer to P(PDC2), and also tested cellulose to verify the activity of the soil inoculum.
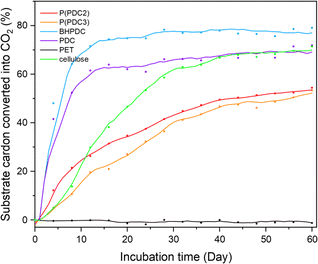 |
| Fig. 5 Biodegradation rates of P(PDC2), P(PDC3), BHPDC, PDC, PET and cellulose for 60 days according to ISO 14851:2019. Average plots of three test samples. | |
Time-dependent biodegradation plots of P(PDC2), P(PDC3), BHPDC, PDC, PET and cellulose are shown in Fig. 5. In 60 days biodegradation test, the biodegradation rate of cellulose exceeded 60% after the 27th day, proving the activity of the soil inoculum used in this biodegradation test meets the ISO 14851:1999 standard. For the small molecular units of PDC and BHPDC, the biodegradation rate rapidly reached over 60% within two weeks of the start of the biodegradation test and entered plateau phase, which indicated that lignin-derived PDC and PDC derivatives can be biodegraded and used as a source of nutrients for microorganisms. It can be seen that although both PDC and BHPDC achieved high biodegradation rates of 69% and 77%, respectively, BHPDC was slightly higher than PDC. In a previous report, the pKa1 and pKa2 of PDC were 1.13 and 2.52, respectively, suggesting that PDC is highly acidic.35 It may have caused adverse effects on the microorganisms in the environment. Compared to PDC, BHPDC does not have carboxyl groups and is not as acidic as PDC, which may be more favourable for the survival of microorganisms and biodegradation.
After 60 days of biodegradation, P(PDC2) and P(PDC3) gradually biodegrade with time, entering a plateau phase with the final biodegradation rate of approximately 54% and 52%, respectively. The biodegradation rate of P(PDC3) was not as high as that of P(PDC2) during the first 30 days, but the biodegradation rate of P(PDC3) gradually approached that of P(PDC2) as the biodegradation experiment progressed. This result indicated that P(PDC2) and P(PDC3) do possess a high biodegradability. In contrast, no biodegradation was observed for PET, which is a representative non-biodegradable synthetic polymer.
In addition to using the soil inoculum and standard test medium based on ISO 14851:1999 standard, the biodegradability of P(PDC2) was also tested in water directly collected from the pond (Fig. S4†). Despite the slow biodegradation rate, about 15% of P(PDC2) was found to be biodegraded within 180 days. This indicated that P(PDC2) is biodegradable in the natural environment.
Conclusions
In summary, this study reported the adhesive properties of PDC-based polyesters, P(PDC2) and P(PDC3), to wood plates and their biodegradability in natural pond water. The tensile lap shear strength measurements indicated that both P(PDC2) and P(PDC3) showed a strong adhesive strength to wood, with the highest average adhesion of 5.55 MPa that caused wood failure. The average adhesive strength of 2.57 MPa remained even after immersion in hot water at 60 °C for 4 h, demonstrating the excellent adhesive strength and water resistance of the PDC-based polyesters. Despite the water resistance, it was demonstrated that the PDC-based polyesters are also biodegradable. After 180 days of biodegradation in natural pond water, P(PDC2) and P(PDC3) exhibited a biodegradation rate of 54% and 52%, respectively. This is in sharp contrast to the biodegradation behaviour of the similar structural synthetic polymer PET. The excellent adhesive properties and biodegradability of the PDC-based polyesters provide a new strategy for the preparation of safe and environmentally-friendly bio-based adhesives.
Author contributions
Conceptualization, T. M.; investigation, Y. J.; resources, T. A., N. K., E. M., and M. N.; writing—original draft preparation, Y. J.; writing—review and editing, T. M.; funding acquisition, T. M. All authors have read and agreed to the published version of the manuscript.
Conflicts of interest
There are no conflicts to declare.
Acknowledgements
This research was partially supported by JST CREST, grant number JPMJCR23L4, JST the establishment of university fellowships towards the creation of science technology innovation, grant number JPMJFS2112, NEDO, grant number 23200050-0, and the Amano Institute of Technology. We thank the Open Facility Center of Tokyo Institute of Technology for XPS measurements and Kazuya Tamura, Rigaku Corporation, for CT image measurements using a nano3DX.
References
- T. Iwata, Biodegradable and bio-based polymers: future prospects of eco-friendly plastics, Angew. Chem., Int. Ed., 2015, 54(11), 3210–3215, DOI:10.1002/anie.201410770.
- Y. Sun and J. Cheng, Hydrolysis of lignocellulosic materials for ethanol production: A review, Bioresour. Technol., 2002, 83(1), 1–11, DOI:10.1016/S0960-8524(01)00212-7.
- E. T. Vink, K. R. Rábago, D. A. Glassner and P. R. Gruber, Applications of life cycle assessment to NatureWorks™ polylactide (PLA) production, Polym. Degrad. Stab., 2003, 80(3), 403–419, DOI:10.1016/S0141-3910(02)00372-5.
- S. Hirota, T. Sato, Y. Tominaga, S. Asai and M. Sumita, The effect of high-pressure carbon dioxide treatment on the crystallization behavior and mechanical properties of poly(L-lactic acid)/poly(methyl methacrylate) blends, Polymer, 2006, 47(11), 3954–3960, DOI:10.1016/j.polymer.2006.03.069.
- A. J. Ragauskas, G. T. Beckham, M. J. Biddy, R. Chandra, F. Chen, M. F. Davis, B. H. Davison, R. A. Dixon, P. Gilna and M. Keller,
et al., Lignin valorization: Improving lignin processing in the biorefinery, Science, 2014, 344(6185), 1246843, DOI:10.1126/science.1246843.
- J. N. Chheda, G. W. Huber and J. A. Dumesic, Liquid-phase catalytic processing of biomass-derived oxygenated hydrocarbons to fuels and chemicals, Angew. Chem., Int. Ed., 2007, 46(38), 7164–7183, DOI:10.1002/anie.200604274.
- L. Changzhi, Z. Xiaochen, W. Aiqin, W. H. George and Z. Tao, Catalytic Transformation of Lignin for the Production of Chemicals and Fuels, Chem. Rev., 2015, 115(21), 11559–11624, DOI:10.1021/acs.chemrev.5b00155.
- R. Rinaldi, R. Jastrzebski, M. T. Clough, J. Ralph, M. Kennema, P. C. A. Bruijnincx and B. M. Weckhuysen, Paving the Way for Lignin Valorisation: Recent Advances in Bioengineering, Biorefining and Catalysis, Angew. Chem., Int. Ed., 2016, 55(29), 8164, DOI:10.1002/anie.201510351.
- Q. Mei, X. Shen, H. Liu and B. Han, Selectively transform lignin into value-added chemicals, Chin. Chem. Lett., 2018, 30(1), 15–24, DOI:10.1016/j.cclet.2018.04.032.
- Y. Otsuka, T. Araki, Y. Suzuki, M. Nakamura, N. Kamimura and E. Masai, High-Level Production of 2-Pyrone-4,6-dicarboxylic Acid from a Lignin-Derived Aromatic Compound by Metabolically Engineered Fermentation to Realize Industrial Valori-zation Processes of Lignin, Bioresour. Technol., 2023, 377, 128956, DOI:10.1016/j.biortech.2023.128956.
- T. Michinobu, M. Hishida, M. Sato, Y. Katayama, E. Masai, M. Nakamura, Y. Otsuka, S. Ohara and K. Shigehara, Polyesters of 2-pyrone-4,6-dicarboxylic acid (PDC) obtained from a metabolic intermediate of lignin, Polym. J., 2008, 40(1), 68–75, DOI:10.1295/polymj.PJ2007158.
- T. Michinobu, M. Bito, Y. Yamada, M. Tanimura, Y. Katayama, E. Masai, M. Nakamura, Y. Otsuka, S. Ohara and K. Shigehara, Fusible, elastic, and biodegradable polyesters of 2-pyrone-4,6-dicarboxylic acid (PDC), Polym. J., 2009, 41(12), 1111–1116, DOI:10.1295/polymj.PJ2009045R.
- T. Michinobu, M. Bito, M. Tanimura, Y. Katayama, E. Masai, M. Nakamura, Y. Otsuka, S. Ohara and K. Shigehara, Synthesis and characterization of hybrid biopolymers of L-lactic acid and 2-pyrone-4,6-dicarboxylic acid, J. Macromol. Sci., Part A: Pure Appl.Chem., 2010, 47(6), 564–570, DOI:10.1080/10601321003742121.
- K. Shikinaka, Y. Hashimoto, S. Kajita, E. Masai, Y. Katayama, M. Nakamura, Y. Otsuka, S. Ohara and K. Shigehara, Ther-moplastic polyesters of 2-pyrone-4,6-dicarboxylic acid (PDC) obtained from a metabolic intermediate of lignin, Sen'i Gakkaishi, 2013, 69(2), 39–47, DOI:10.2115/fiber.69.39.
- M. Hishida, K. Shikinaka, Y. Katayama, S. Kajita, E. Masai, M. Nakamura, Y. Otsuka, S. Ohara and K. Shigehara, Polyesters of 2-pyrone-4,6-dicarboxylic acid (PDC) as bio-based plastics exhibiting strong adhering properties, Polym. J., 2009, 41(4), 297–302, DOI:10.1295/polymj.PJ2008291.
- Y. Cheng, K. Kuboyama, S. Akasaka, T. Araki, E. Masai, M. Nakamura and T. Michinobu, Polyurethanes based on lig-nin-derived metabolic intermediate with strong adhesion to metals, Polym. Chem., 2022, 13(48), 6589–6598, 10.1039/D2PY01128J.
- T. Michinobu, K. Hiraki, Y. Inazawa, Y. Katayama, E. Masai, M. Nakamura, S. Ohara and K. Shigehara, Click synthesis and adhesive properties of novel biomass-based polymers from lignin-derived stable metabolic intermediate, Polym. J., 2011, 43(7), 648–653, DOI:10.1038/pj.2011.40.
- Y. Jin, M. Joshi, T. Araki, N. Kamimura, E. Masai, M. Nakamura and T. Michinobu, Click Synthesis of Triazole Polymers Based on Lignin-Derived Metabolic Intermediate and Their Strong Adhesive Properties to Cu Plate, Polymers, 2023, 15(6), 1349, DOI:10.3390/polym15061349.
- P. Antov, V. Savov, N. Trichkov, Ľ. Krišťák, R. Réh, A. N. Papadopoulos, H. R. Taghiyari, A. Pizzi, D. Kunecová and M. Pachikova, Properties of High-Density Fiberboard Bonded with Urea–Formaldehyde Resin and Ammonium Lignosulfonate as a Bio-Based Additive, Polymers, 2021, 13(16), 2775, DOI:10.3390/polym13162775.
- H. Lei, G. Du, Z. Wu, X. Xi and Z. Dong, Cross-linked soy-based wood adhesives for plywood, Int. J. Adhes. Adhes., 2014, 50, 199–203, DOI:10.1016/j.ijadhadh.2014.01.026.
- J. Li, S. Pradyawong, Z. He, X. S. Sun, D. Wang, H. N. Cheng and J. Zhong, Assessment and application of phosphorus/calcium-cottonseed protein adhesive for plywood production, J. Cleaner Prod., 2019, 229, 454–462, DOI:10.1016/j.jclepro.2019.05.038.
- S. Khosravi, F. Khabbaz, P. Nordqvist and M. Johansson, Protein-based adhesives for particleboards, Ind. Crops Prod., 2010, 32(3), 275–283, DOI:10.1016/j.indcrop.2010.05.001.
- J. Domínguez-Robles, Q. Tarrés, M. Delgado-Aguilar, A. Rodríguez, F. X. Espinach and P. Mutjé, Approaching a new generation of fiberboards taking advantage of self lignin as green adhesive, Int. J. Biol. Macromol., 2018, 108, 927–935, DOI:10.1016/j.ijbiomac.2017.11.005.
- F. Song, T. Liu, Q. Fan, D. Li, R. Ou, Z. Liu and Q. Wang, Sustainable, high-performance, flame-retardant waterborne wood coatings via phytic acid based green curing agent for melamine-urea-formaldehyde resin, Prog. Org. Coat., 2021, 162, 106597, DOI:10.1016/j.porgcoat.2021.106597.
- W. Zhang, Y. Ma, Y. Xu, C. Wang and F. Chu, Lignocellulosic ethanol residue-based lignin–phenol–formaldehyde resin adhesive, Int. J. Adhes. Adhes., 2012, 40, 11–18, DOI:10.1016/j.ijadhadh.2012.08.004.
- W. Gindl, F. Zargar-Yaghubi and R. Wimmer, Impregnation of softwood cell walls with melamine-formaldehyde resin, Bioresour. Technol., 2003, 87(3), 325–330, DOI:10.1016/S0960-8524(02)00233-X.
- Y. Zhang, M. Chen, J. Zhang, J. Li, S. Q. Shi and Q. Gao, A High-Performance Bio-Adhesive Using Hyperbranched Aminated Soybean Polysaccharide and Bio-Based Epoxide, Adv. Mater. Interfaces, 2020, 7(9), 2000148, DOI:10.1002/admi.202000148.
- T. Jin, H. Zeng, Y. Huang, L. Liu, W. Yao, H. Lei, S. Shi, G. Du and L. Zhang, Bio-hyperbranched polyesters synthesized from citric acid and bio-polyols and applications on wood adhesives, Polym. Test., 2023, 120, 107974, DOI:10.1016/j.polymertesting.2023.107974.
- J. Sutiawan, D. Hermawan, M. Y. Massijaya, S. S. Kusumah, M. A. R. Lubis, R. Marlina, D. Purnomo and I. M. Sulastiningsih, Influence of different hot-pressing conditions on the performance of eco-friendly jabon plywood bonded with citric acid adhesive, Wood Mater. Sci. Eng., 2021, 17(6), 400–409, DOI:10.1080/17480272.2021.1884898.
- K. Umemura, T. Ueda, S. S. Munawar and S. Kawai, Application of citric acid as natural adhesive for wood, J. Appl. Polym. Sci., 2012, 123(4), 1991–1996, DOI:10.1002/app.34708.
- T. Fujita, E. Nishi, D. Koma and M. Naito, Hydroxytyrosol: Bioinspired Nature-Based Adhesive Motif with Excellent Chemical Modifiability and Stability, ACS Appl. Polym. Mater., 2023, 5(5), 3230–3234, DOI:10.1021/acsapm.3c00365.
- C. R. Westerman, B. C. McGill and J. J. Wilker, Sustainably sourced components to generate high-strength adhesives, Nature, 2023, 621, 306–311, DOI:10.1038/s41586-023-06335-7.
- G. Yang, Z. Gong, X. Luo, L. Chen and L. Shuai, Bonding wood with uncondensed lignins as adhesives, Nature, 2023, 621, 511–515, DOI:10.1038/s41586-023-06507-5.
- Y. Hasegawa, K. Shikinaka, S. Kajita, E. Masai, Y. Katayama, A. Nakao, Y. Otsuka, M. Nakamura, S. Ohara and K. Shigehara, Curing Kinetics of Lignin-based Epoxy Resins, Sen'i Gakkaishi, 2012, 68(4), 73–78, DOI:10.2115/fiber.68.73.
- T. Michinobu, M. Bito, Y. Yamada, Y. Katayama, K. Noguchi, E. Masai, M. Nakamura, S. Ohara and K. Shigehara, Molecular properties of 2-pyrone-4,6-dicarboxylic acid (PDC) as a stable metabolic intermediate of lignin isolated by fractional precipitation with Na+ ion, Bull. Chem. Soc. Jpn., 2007, 80(12), 2436–2442, DOI:10.1246/bcsj.80.2436.
Footnote |
† Electronic supplementary information (ESI) available: Pictures of cypress and P(PDC3) adhesives under different accelerated deterioration treatments, adhesive properties of P(PDC3), and XPS of O 1s core-level spectra after hot-pressing (PDF). See DOI: https://doi.org/10.1039/d4su00163j |
|
This journal is © The Royal Society of Chemistry 2024 |