DOI:
10.1039/D3SC06052G
(Edge Article)
Chem. Sci., 2024,
15, 4452-4457
Mechanochemistry enabling highly efficient Birch reduction using sodium lumps and D-(+)-glucose†
Received
12th November 2023
, Accepted 10th February 2024
First published on 12th February 2024
Abstract
In this study, a mechanochemical protocol for highly efficient and ammonia-free sodium-based Birch reduction was developed, leveraging the use of cheap and easy-to-handle sodium lumps. The key to achieving this transformation is the use of D-(+)-glucose as a proton source, which solidifies the reaction mixture in bulk state, enhancing the efficiency of the in situ mechanical activation of sodium lumps through the ball-milling process. Under the developed conditions, a diverse array of aromatic and heteroaromatic compounds were selectively reduced to produce the corresponding 1,4-cyclohexadiene derivatives in high yields within 30 min. Notably, all synthetic operations can be carried out without inert gases or the need for dry or bulk organic solvents. Furthermore, a scaled-up synthesis can be conducted without any yield losses. These results suggest that the present mechanochemical approach offers a more convenient, economically attractive, and sustainable alternative to previously established Birch reduction protocols.
Introduction
Birch reduction using alkali metals has been recognized as a powerful synthetic approach to convert arenes into 1,4-cyclohexadiene derivatives.1 Notable examples among several others are lithium-based Birch reduction protocols, which have garnered significant attention owing to the exceptional reduction ability of lithium metal.2 However, considering the limited availability of lithium resources, there is an increasing need to explore alternative options, such as replacing lithium metal with sodium metal in organic synthesis.3 In this context, sodium-based Birch reduction has attracted considerable attention as a more sustainable alternative to well-established lithium-based methodologies. Conventional sodium-based Birch reduction uses sodium lumps.1 However, this protocol necessitates the use of caustic and toxic liquid ammonia, which substantially reduces its practical utility in organic synthesis.1a To address this issue, several ammonia-free modifications have been devised. In 2005, Dye et al. reported an ammonia-free method using sodium nanocrystals absorbed in silica gel [Na–SG(I)] (Scheme 1a).4 Later, An et al. developed Birch reduction using sodium dispersion with 15-crown ether (Scheme 1a).5 More recently, Takai, Asako, and co-workers revealed that the use of 1,3-dimethyl-2-imidazolidinone (DMI) as a ligand facilitates Birch reduction with sodium dispersion (Scheme 1a).6 These activated sodium sources have a large surface area, enabling highly efficient reduction even in the absence of liquid ammonia. Although these achievements are remarkable, the requirement for activated sodium sources imposes substantial costs and renders them less appealing for large-scale synthesis. In the case of sodium dispersions, the inherent lack of shelf stability presents an additional drawback for practical synthetic applications.7 Therefore, the use of commercially available, cost-effective, and easy-to-handle sodium lumps remains significant from economic and practical perspectives.
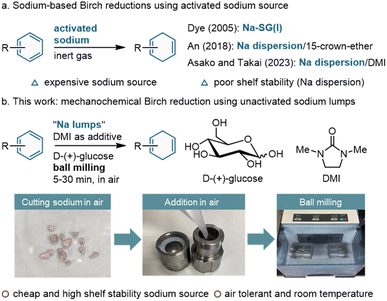 |
| Scheme 1 Sodium-based Birch reduction (a) state-of-the-art sodium-based Birch reductions using activated sodium source. (b) Air-tolerant sodium lump-based Birch reduction using ball milling technique (this work). | |
Over the past decades, ball milling has attracted attention as a new tool for organic synthesis.8,9 This protocol has the advantages of requiring few organic solvents for the reactions, a short reaction time, and simple experimental operations. Furthermore, recent findings have revealed that zero-valent metals can be efficiently activated by the mechanical impact provided by the ball-milling process, and metal–surface reactions with organic molecules are significantly accelerated under mechanochemical conditions.10,11 Recently, we reported an ammonia-free, extremely fast lithium-based Birch reduction using a ball-milling technique.12 The reduction of various aromatic compounds can be conducted without inert gases and achieved within a short duration of 1 min, without the need for a bulk organic solvent. The observed exceptional efficiency is likely attributed to the in situ mechanical activation of lithium metal, which serves to eliminate the inactive surface layer and increase the reactive surface area. Motivated by this success, we envisioned that a mechanochemical protocol could activate sodium lumps, which are much less reactive than sodium dispersions. This concept has the capacity to facilitate the realization of a highly efficient, sustainable, and economically viable sodium-based Birch reduction method.
Herein, we report the development of a highly efficient Birch reduction method using unactivated sodium lumps under mechanochemical conditions (Scheme 1b). Notably, this procedure can be performed without inert gases or the need for a bulk solvent. Under optimized ball-milling conditions, a diverse array of aromatic compounds exhibited significant chemoselectivity upon reduction. The successful realization of this conversion relies on the synergistic use of mechanical activation of sodium metal in conjunction with D-(+)-glucose as a solid proton source. Notably, D-(+)-glucose is a safe, sustainable, abundant, and inexpensive reagent. A scaled-up synthesis was also accomplished without decreasing the yield, emphasizing the synthetic utility of this protocol. These results suggest that mechanochemistry opens vast possibilities for the widespread implementation of a more sustainable and economically appealing sodium-Birch reduction method in organic synthesis.
Results and discussion
Our study commenced with the optimization of the reaction conditions using 1-phenyldecane 1a as the substrate (Table 1). All mechanochemical reactions were performed using a Retsch MM400 ball-mill. After removing the mineral oil by wiping with paper, the sodium lump was subjected to cutting, resulting in a diameter of approximately 4–5 mm. Subsequently, the sodium lump was weighed and introduced into a 10 mL stainless steel jar along with two 10 mm stainless steel balls in air. Through a series of extensive trials, it was determined that mechanochemical sodium-based Birch reduction proceeded efficiently to produce the corresponding reduction product 2a in 96% yield when employing a combination of sodium lump (6 equiv.), D-(+)-glucose (3 equiv.) as a proton source, and 1,3-dimethyl-2-imidazolidinone (DMI) (6 equiv.), which is an effective additive for sodium dispersion-based Birch reduction developed by Takai, Asako, and co-workers (entry 1).6 The requirement of an excess of sodium lumps is comparable to that in conventional sodium-based Birch reduction protocols using ammonia.1 Notably, D-(+)-glucose was found to be an optimal proton source under ball milling conditions. When the reactions were carried out using proton sources commonly used in solution-based Birch reduction, such as t-BuOH and i-PrOH, the desired product 2a was obtained in only 6% and 18% yield, respectively (entries 2 and 3). Under these conditions, the reaction mixture exhibited an oily state, and the sodium lumps were not crushed into smaller particles but just elongated because of their inherent softness (Fig. 1a). We expected that solidifying the reaction mixture in the bulk state would facilitate the effective transmission of mechanical force provided by ball milling to the sodium metal, promoting the Birch reduction process. Taking this into consideration, sea sand was added to the mixture as a grinding auxiliary. However, the reaction efficiency improved only slightly, even after a prolonged reaction time (13%, entry 4). We also attempted to use solid alcohols, such as 1-adamantanol (1-AdOH), instead of liquid alcohols to solidify the reaction mixture (entry 5). However, the reaction mixture retained its oily consistency after ball milling, which was probably due to the high solubility of 1-AdOH in DMI (Fig. 1b). As such, a suboptimal yield was obtained (18%), and the sodium lumps remained intact (entry 5 and Fig. 1b). Given this result, we decided to use D-(+)-glucose, which is hardly soluble in organic solvents, as the solidifying alcohol additive. Notably, the reaction mixture using D-(+)-glucose after ball milling exhibited a solid state, and the sodium lumps were fully consumed (Fig. 1c), providing the desired product 2a in 96% yield (entry 1). We also tested other commonly used additives, such as 15-crown-5 and hexamethylphosphoric triamide (HMPA), instead of DMI, which resulted in poor efficiency (entries 6 and 7, 19% and 23% yields, respectively).5,13 No reaction occurred in the absence of DMI (entry 8). When the number of balls or the frequency of ball milling was decreased, lower yields were obtained (entries 9 and 10, 85% and 72% yields, respectively), suggesting that a strong mechanical impact to activate the sodium metal is essential for efficient Birch reduction. Furthermore, reducing the sodium and DMI loadings to 4.0 equivalents led to a decreased yield (entry 11, 86%). Similarly, shortening the reaction time (5 min) also reduced the yield of 2a (entry 12, 61%).
Table 1 Optimization of the mechanochemical sodium-based Birch reduction of 1-phenyldecane (1a)a
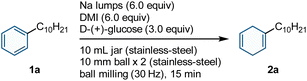
|
Entry |
Variation from standard conditions |
Yield (%) |
Unless otherwise noted, reactions were carried out in a 10 mL stainless-steel ball-milling jar with two 10 mm stainless-steel balls at 30 Hz. The yields were determined by 1H NMR spectroscopy using an internal standard.
|
1 |
None |
96 |
2 |
t-BuOH instead of D-(+)-glucose |
6 |
3 |
i-PrOH instead of D-(+)-glucose |
18 |
4 |
t-BuOH instead of D-(+)-glucose sea sand (100 mg), 30 min |
13 |
5 |
1-AdOH instead of D-(+)-glucose |
18 |
6 |
HMPA instead of DMI |
19 |
7 |
15-Crown-5 instead of DMI |
23 |
8 |
Without DMI |
<5 |
9 |
10 mm ball × 1 (stainless steel) |
85 |
10 |
Ball milling (25 Hz) |
72 |
11 |
Na lumps, DMI (4.0 equiv.) |
86 |
12 |
5 min |
61 |
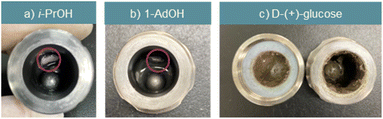 |
| Fig. 1 Reaction mixtures after grinding in a ball mill: (a) i-PrOH. (b) 1-AdOH. (c) D-(+)-glucose. | |
With the optimized conditions in hand, we explored the substrate scope of the mechanochemical Birch reduction using sodium lumps (Table 2). Overall, this method is amenable to a broad range of arenes and heteroarenes and is comparable to conventional solution-based Birch reduction protocols. The reduction of alkylbenzene-containing acetal (1b), alcohol (1c), and primary amine (1d) afforded the corresponding products (2b–2d) in moderate to high yields (86%, 76%, and 60% yields, respectively). Substrates bearing amines protected with acetyl groups (1e) and tert-butoxycarbonyl groups (2f) efficiently underwent Birch reduction. Unsubstituted amide (2g) and carboxylic acid (2h) were also selectively reduced at the aromatic ring in good to excellent yields (51% and 88% yields, respectively). The less-reactive electron-rich disubstituted alkylbenzenes (1i and 1j) also readily reacted with sodium lumps under mechanochemical conditions to afford the corresponding products (2i and 2j) in high yields (86% and 89%, respectively). In contrast, the reaction of meta-disubstituted alkylbenzene (1k) afforded the reduction product (2k) in moderate yield (44%). The reactions of conjugated aromatic compounds also provided the desired reduction products (2l–2o) in moderate to high yields (55–91%). While these arenes are often over reduced under conventional solution-based conditions to produce complex mixtures, only trace amounts of the overreduced products were observed under these mechanochemical conditions. Electron-rich aromatic ether (1p) was successfully reduced, but the yield was moderate (58%). 2-Methoxynaphthalene also reacted to yield the desired product 2q (34%); however, the demethylation side product (2q′) was the major product (43%).6,14 Furthermore, we conducted the reduction of N-heteroarenes. Acridine (1r) was reduced to an excellent yield (96%) without over-reduction. The reactions of N-alkylated indole (1s) and quinoline (1t) also afforded the corresponding N-heterocycles (2s and 2t) in moderate yields (50% and 49%, respectively). Although most of the products were isolated by column chromatography on silica gel, non-polar products such as 2i can be isolated by simple washing the crude mixture with water (for details, see the ESI†). This result highlights the practical utility of this mechanochemical protocol.
Table 2 Substrate scope of the mechanochemical sodium-based Birch reductiona
Unless otherwise noted, the following reaction conditions were used: 1.0 mmol arene; 10.0 mL stainless steel ball-milling jar with two 10 mm stainless steel balls; 30 Hz. See the ESI for detailed reaction conditions. Isolated yields are presented normally, and 1H NMR yields are shown in parentheses.
|
|
To demonstrate the practical utility of this reaction, we investigated the scaled-up synthesis of 2r (Scheme 2). A 3 mmol-scale reaction was conducted in 10 mL stainless steel jars with two 10 mm stainless steel balls. Using MM400, two simultaneous reactions were carried out to obtain 2r on the gram scale (Scheme 2). After ball milling, each 3 mmol-scale reaction was quenched with methanol. These reaction mixtures were then mixed, subjected to extraction, and purified by silica gel column chromatography to afford 2r in 95% yield (1.030 g), which was comparable to the yield obtained in the small-scale reaction. This result emphasizes the practical utility of the protocol.15
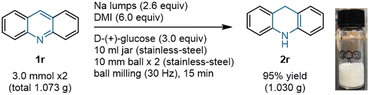 |
| Scheme 2 Scaled-up synthesis of 2r. | |
Control experiments were performed in solution to confirm the effectiveness of this mechanical activation approach using ball milling (Scheme 3). Initially, a commercially available sodium lump was used in a solution-based reaction with tetrahydrofuran (THF) as the solvent in the presence of D-(+)-glucose and DMI. Under these conditions, no reaction was observed, and a large amount of bulk sodium metal remained unaltered (Scheme 3a). Subsequently, we conducted an examination of the reactions in solvent using sodium lumps according to the experimental settings established by Takai and Asako (Scheme 3b), as well as the conditions devised by An (Scheme 3c), which were originally developed for sodium dispersions.5,6 Both reactions afforded poor results (<5% and 9% yields, respectively), and a large amount of bulk sodium metal remained unreacted. These results indicate that the strong mechanical impact of ball milling is necessary for efficient Birch reduction using unactivated sodium lumps without liquid ammonia. We assumed that the in situ mechanical activation of sodium metal by ball milling could form smaller metal particles with high reactivity comparable to that of sodium dispersion.
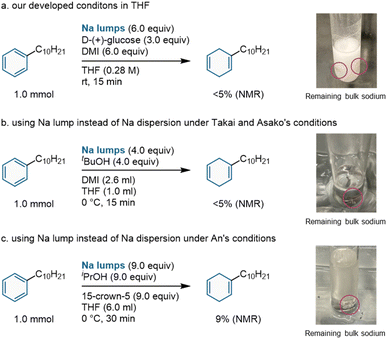 |
| Scheme 3 Reactivities of sodium lumps in solution (a) our developed conditions in THF. (b) Takai and Asako's conditions originally developed for the use of sodium dispersion. (c) An's conditions originally developed for the use of sodium dispersion. | |
Conclusion
In summary, we developed a mechanochemical protocol for highly efficient, economically attractive, and operationally simple Birch reduction using sodium lumps. The use of D-(+)-glucose as a proton source, which is a safe, sustainable, abundant, and inexpensive reagent,16 is the key to efficient transformations. Notably, this protocol can be performed without a complicated reaction setup involving inert gases or the pre-activation of sodium metal. These results demonstrate the practical utility of Birch reduction using sodium lumps as an alternative to established protocols that use lithium metal or other expensive and difficult-to-store activated sodium sources.
Data availability
All experimental data is available in the ESI.†
Author contributions
Koji Kubota and Hajime Ito conceived and designed the study. All authors co-wrote the paper. Keisuke Kondo performed the chemical experiments and analyzed the data. All authors discussed the results and commented on the manuscript.
Conflicts of interest
There are no conflicts to declare.
Acknowledgements
This work was supported by the Japan Society for the Promotion of Science (JSPS) via KAKENHI grants 22H00318 (H. I.), 21H01926 (K. K.), 22H05328 (K. K.), and 22K18333 (H. I.), as well as by the JST via CREST grant JPMJCR19R1 (H. I.) and FOREST grant JPMJFR201I (K. K.), as well as by the Institute for Chemical Reaction Design and Discovery (ICReDD), which was established by the World Premier International Research Initiative (WPI), MEXT, Japan. We thank Mr Sota Kawamura for his help in cross-checking the experiments.
Notes and references
-
(a) A. J. Birch and H. Smith, Q. Rev., Chem. Soc., 1958, 12, 17 RSC;
(b)
A. A. Akhrem, I. G. Reshetova and Y. A. Titov, Birch Reduction of Aromatic Compounds, Springer, US, 1972 CrossRef;
(c) P. W. Rabideau, Tetrahedron, 1989, 45, 1579 CrossRef CAS;
(d) P. W. Rabideau and Z. Marcinow, Org. React., 1992, 42, 1 CAS;
(e) A. J. Birch, Pure Appl. Chem., 1996, 68, 553 CrossRef CAS;
(f) A. G. Schultz, Chem. Commun., 1999, 1263 RSC;
(g) H. E. Zimmerman, Acc. Chem. Res., 2012, 45, 164 CrossRef CAS PubMed;
(h) M. J. O'Mahony, R. A. M. O'Ferrall, D. R. Boyd, C. M. Lam and A. C. O'Donoghue, J. Phys. Org. Chem., 2013, 26, 989 CrossRef;
(i) R. Stodt, S. Gencaslan, I. M. Müller and W. S. Sheldrick, Eur. J. Inorg. Chem., 2003, 1873 CrossRef CAS.
-
(a) A. L. Wilds and N. A. Nelson, J. Am. Chem. Soc., 1953, 75, 5360 CrossRef CAS;
(b) M. E. Garst, L. J. Dolby, S. Esfandiari, N. A. Fedoruk, N. C. Chamberlain and A. A. Avey, J. Org. Chem., 2000, 65, 7098 CrossRef CAS PubMed;
(c) T. J. Donohoe and D. House, J. Org. Chem., 2002, 67, 5015 CrossRef CAS PubMed;
(d) J. Burrows, S. Kamo and K. Koide, Science, 2021, 374, 741 CrossRef CAS PubMed.
- P. C. K. Vesborg and T. F. Jaramillo, RSC Adv., 2012, 2, 7933 RSC.
-
(a) J. L. Dye, K. D. Cram, S. A. Urbin, M. Y. Redko, J. E. Jackson and M. Lefenfeld, J. Am. Chem. Soc., 2005, 127, 9338 CrossRef CAS PubMed;
(b) M. J. Costanzo, M. N. Patel, K. A. Peterson and P. F. Vogt, Tetrahedron Lett., 2009, 50, 5463 CrossRef CAS;
(c) M. Carraro, N. Pisano and U. Azzena, Synthesis, 2017, 49, 1931 CrossRef CAS.
- P. Lei, Y. Ding, X. Zhang, A. Adijiang, H. Li, Y. Ling and J. An, Org. Lett., 2018, 20, 3439 CrossRef CAS PubMed.
- S. Asako, I. Takahashi, T. Kurogi, Y. Murakami, L. Llies and K. Takai, Chem. Lett., 2022, 51, 38 CrossRef CAS.
- Some reports pointed out poor shelf stability of sodium dispersion, see:
(a) S. Asako, H. Nakajima and K. Takai, Nat. Catal., 2019, 2, 297 CrossRef CAS;
(b) S. Asako, I. Takahashi, H. Nakajima, L. Ilies and K. Takai, Commun. Chem., 2021, 4, 76 CrossRef CAS PubMed.
- For selected reviews on the use of ball milling for organic synthesis, see:
(a) S. L. James, C. J. Adams, C. Bolm, D. Braga, P. Collier, T. Friščić, F. Grepioni, K. D. M. Harris, G. Hyett, W. Jones, A. Krebs, J. Mack, L. Maini, A. G. Orpen, I. P. Parkin, W. C. Shearouse, J. W. Steed and D. C. Waddell, Chem. Soc. Rev., 2012, 41, 413 RSC;
(b) G.-W. Wang, Chem. Soc. Rev., 2013, 42, 7668 RSC;
(c) J.-L. Do and T. Friščić, ACS Cent. Sci., 2017, 3, 13 CrossRef CAS PubMed;
(d) J. G. Hernández and C. Bolm, J. Org. Chem., 2017, 82, 4007 CrossRef PubMed;
(e) T.-X. Métro, J. Martinez and F. Lamaty, ACS Sustainable Chem. Eng., 2017, 5, 9599 CrossRef;
(f) T. K. Achar, A. Bose and P. Mal, Beilstein J. Org. Chem., 2017, 13, 1907 CrossRef CAS PubMed;
(g) O. Eguaogie, J. S. Vyle, P. F. Conlon, M. A. Gîlea and Y. Liang, Beilstein J. Org. Chem., 2018, 14, 955 CrossRef CAS PubMed;
(h) J. L. Howard, Q. Cao and D. L. Browne, Chem. Sci., 2018, 9, 3080 RSC;
(i) J. Andersen and J. Mack, Green Chem., 2018, 20, 1435 RSC;
(j) C. Bolm and J. G. Hernández, Angew. Chem., Int. Ed., 2019, 58, 3285 CrossRef CAS PubMed;
(k) T. Friščić, C. Mottillo and H. M. Titi, Angew. Chem., Int. Ed., 2020, 59, 1018 CrossRef PubMed;
(l) K. Kubota and H. Ito, Trends Chem., 2020, 2, 1066 CrossRef CAS;
(m) A. Porcheddu, E. Colacino, L. De Luca and F. Delogu, ACS Catal., 2020, 10, 8344 CrossRef CAS;
(n) J. A. Leitch and D. L. Browne, Chem.–Eur. J., 2021, 27, 9721–9726 CrossRef CAS PubMed;
(o) P. Ying, J. Yu and W. Su, Adv. Synth. Catal., 2021, 363, 1246 CrossRef CAS;
(p) K. J. Ardila-Fierro and J. G. Hernández, ChemSusChem, 2021, 14, 2145 CrossRef CAS PubMed;
(q) V. Martinez, T. Stolar, B. Karadeniz, I. Brekalo and K. Užarević, Nat. Rev. Chem, 2023, 7, 51 CrossRef CAS PubMed.
- For the selected mechanochemical synthesis using ball milling, see
(a) K. Kubota, T. Seo, K. Koide, S. Hasegawa and H. Ito, Nat. Commun., 2019, 10, 111 CrossRef PubMed;
(b) K. Kubota, Y. Pang, A. Miura and H. Ito, Science, 2019, 366, 1500 CrossRef CAS PubMed;
(c) T. Seo, K. Kubota and H. Ito, J. Am. Chem. Soc., 2020, 142, 9884 CrossRef CAS PubMed;
(d) Y. Pang, J. Lee, K. Kubota and H. Ito, Angew. Chem., Int. Ed., 2020, 59, 22570 CrossRef CAS PubMed;
(e) T. Seo, N. Toyoshima, K. Kubota and H. Ito, J. Am. Chem. Soc., 2021, 143, 6165 CrossRef CAS PubMed;
(f) K. Kubota, N. Toyoshima, D. Miura, J. Jiang, S. Maeda, M. Jin and H. Ito, Angew. Chem., Int. Ed., 2021, 60, 16003 CrossRef CAS PubMed;
(g) T. Seo, K. Kubota and H. Ito, J. Am. Chem. Soc., 2023, 145, 6823 CrossRef CAS PubMed.
- For a tutorial review on the mechanical activation of zero-valent metals, see: A. C. Jones, J. A. Leitch, S. E. Raby-Buck and D. L. Browne, Nat. Synth., 2022, 1, 763 CrossRef.
- For selected examples of mechanical activation of zero-valent metals, see
(a) Q. Cao, J. L. Howard, E. Wheatley and D. L. Browne, Angew. Chem., Int. Ed., 2018, 57, 11339 CrossRef CAS PubMed;
(b) W. Nicholson, J. Howard, G. Magri, A. Seastram, A. Khan, R. R. A. Bolt, L. Morrill, E. Richards and D. L. Browne, Angew. Chem., Int. Ed., 2021, 60, 23128 CrossRef CAS PubMed;
(c) R. Takahashi, A. Hu, P. Gao, Y. Gao, Y. Pang, T. Seo, S. Maeda, J. Jiang, H. Takaya, K. Kubota and H. Ito, Nat. Commun., 2021, 12, 6691 CrossRef CAS PubMed;
(d) V. S. Pfennig, R. C. Villella, J. Nikodemus and C. Bolm, Angew. Chem., Int. Ed., 2022, 61, e202116514 CrossRef CAS PubMed;
(e) P. Gao, J. Jiang, S. Maeda, K. Kubota and H. Ito, Angew. Chem., Int. Ed., 2022, 61, e20220711 Search PubMed;
(f) R. Takahashi, P. Gao, K. Kubota and H. Ito, Chem. Sci., 2023, 14, 49 Search PubMed;
(g) N. Davison, J. A. Quirk, F. Tuna, D. Collison, C. L. McMullin, H. Michaels, G. H. Morritt, P. G. Waddell, J. A. Gould, M. Freitag, J. A. Dawson and E. Lu, Chem, 2023, 9, 576 CrossRef CAS;
(h) K. Fujishiro, Y. Morinka, Y. Ono, T. Tanaka, L. T. Scott, H. Ito and K. Itami, J. Am. Chem. Soc., 2023, 145, 8163 CrossRef CAS PubMed.
- Y. Gao, K. Kubota and H. Ito, Angew. Chem., Int. Ed., 2023, 62, e202217723 CrossRef CAS PubMed.
- G. M. Whitesides and W. J. Ehmann, J. Am. Chem. Soc., 1969, 91, 3800 CrossRef CAS.
- R. L. Burwell Jr, Chem. Rev., 1954, 54, 615 CrossRef.
- Although we did not encounter any hazards in the gram-scale mechanochemical Birch reduction in air, anyone who wants to scale up should pay attention to safety issues. Organosodium compounds and sodium are commonly considered pyrophoric compounds. On the other hand, Birch reduction is an exothermic reaction that might release flammable vapors. Risk management must be performed to avoid fire and explosion hazards before attempting to scale up this reaction in the air.
- Retail price: ca. US $30 per kg (TCI chemicals) in Dec 2023.
|
This journal is © The Royal Society of Chemistry 2024 |
Click here to see how this site uses Cookies. View our privacy policy here.