DOI:
10.1039/D3RA08198B
(Paper)
RSC Adv., 2024,
14, 2678-2686
The distribution and enrichment characteristics of rare earth elements between coals and coal ashes from four coal-fired power plants
Received
30th November 2023
, Accepted 9th January 2024
First published on 16th January 2024
Abstract
Coal and coal ash (slag and fly ash) have emerged as important potential sources for rare earth elements (REY). The distribution and enrichment of REY during coal combustion from coal-fired power plants are of great significance for the recovery of REY. In this study, the concentration of REY in coal and coal ash from four coal-fired power plants in China was determined using microwave digestion-inductively coupled plasma mass spectrometry. The distribution and enrichment characteristics of REY in coal and coal ash were studied. The coal ash contains 310–683 μg g−1 of REY, and the proportion of critical REY was greater than 30%, which is higher than the extraction concentration (300 μg g−1) recommended by the United States Department of Energy, indicating significant REY recovery potential. The concentration of REY in coal was positively correlated with ash yield, which could be explained by the fact that REY are mainly distributed in minerals. Coal and coal ash show similar REY distribution patterns, indicating that REY were not fractionated during the coal combustion. In addition, the enrichment coefficient of REY in fly ash was greater than that in slag, which revealed that REY were mainly enriched in fly ash. Therefore, the REY in fly ash has more recycling potential.
1. Introduction
Rare earth elements (REY) are a group of metals consisting of 15 lanthanides along with yttrium.1 REY have been included in the list of critical metals by the European Union, and the United States due to their important strategic significance.2 From 2002 to 2012, China has been the primary supplier of over 90% of the world's rare earth supply.3 However, due to excessive exploitation and increased prospecting efforts in other countries, the reserves of rare earth resources in China have declined rapidly. According to the latest global rare earth reserves released by the US Geological Service in 2022, China's rare earth resources have dropped from 70% to 33.8%.4 Due to the increasing demand for traditional rare earth resources, it is expected that China would need to import rare earth resources from abroad to meet domestic production needs by 2040.5 Therefore, it is of great theoretical and practical significance to find new rare earth metal resources for the stable supply of national mineral resources.
Research has indicated that coal and coal ash contain enriched levels of REY and are considered potential resources for their extraction.6,7 Based on the geochemical properties of REY in coal, REY can be divided into light (LREY-La, Ce, Pr, Nd, and Sm), medium (MREY-Eu, Gd, Tb, Dy, and Y), and heavy (HREY-Ho, Er, Tm, Yb, and Lu).6 In the meantime, REY can be further classified into critical (critical-Nd, Eu, Tb, Dy, Y and, Er), uncritical (uncritical-La, Pr, Sm, and Gd) and excessive (excessive-Ce, Ho, Tm, Yb, and Lu) according to the supply and demand relationship.8 Coal-based materials with the proportion of critical REY greater than 30% and the prospect coefficient (Cout1, ratio of critical to excessive) greater than 0.7 are deemed to have potential for REY recovery.8 In addition, the U.S. Department of Energy recommends that coal-based materials with a concentration higher than 300 μg g−1 can be used as raw materials for REY recovery.9 Coal mines that have exhibited abnormal enrichment of REY at domestic and abroad have the potential for REY recovery, such as the Russian Far East coalfield (300–1000 μg g−1);10 coal seams (500–4000 μg g−1) in eastern Kentucky, the United States;11,12 and the Daqingshan (721 μg g−1), Heidaigou (1031 μg g−1), Haerwusu (1347 μg g−1), Zhanghe (K8, 1401 μg g−1 and K9, 804 μg g−1), Songzao (K12, 1968 μg g−1), Yishan, Huayingshan, Guiding, Kaili (874 μg g−1), Huaqiu (K9, 239 μg g−1 and K16, 630 μg g−1) in China.13–20 Moreover, REY in coal is not easy to volatilize during the coal combustion,21,22 so REY are further enriched in coal ash, and even reaches the level of industrial extraction.10,11 Therefore, coal and coal ash are considered to be new types of mineral resources rich in REY,6,7,23 and have attracted the attention of various countries. Since 2014, the United States has made significant investments in various departments to quickly initiate the project of recovering REY from coal and coal ash.24–26 Meantime, coal-producing countries such as Europe,27–29 Russia,30,31 Canada,32 India,33–35 South Africa,36 and China37–41 have also done extensive studies on the distribution and occurrence of REY in coal. Our team has also studied the occurrence of REY in coal and coal ash, revealing that REY in coal mainly exist in minerals, while most of the very fine minerals containing REY are wrapped in the glass phase of coal ash.42 In addition, domestic and foreign scholars have done many researches on the distribution and enrichment of REY during the coal combustion process in power plant.39–49 However, the research results are inconsistent, including three main enrichment modes: the first is mainly enriched in slag;43 the second is mainly enriched in fly ash;40,44 the third is enriched in both slag and fly ash.39,46
Based on the above research, the concentration of REY in coal and coal ash is determined by microwave digestion-inductively coupled plasma mass spectrometry for four coal-fired power plants in China. This study aims to deepen the understanding of the distribution and enrichment characteristics of REY in coal and coal ash, as well as to analyze their recovery potential. This analysis provides theoretical guidance for the recovery and utilization of REY from coal-based materials.
2. Materials and methods
2.1 Materials
The coal and coal ash (slag and fly ash) samples used in this study were obtained from four coal-fired power plants in China, including P1-600 MW, P2-600 MW, P3-1000 MW, and P4-1000 MW pulverized coal power plants. All power plants use Shenhua coal. The coal was collected from the feed coal of the power plant, while the slag was collected from the boiler slag outlet, and the fly ash was collected from the first row hoppers of the electrostatic precipitator.
Nitric acid (HNO3, 65–68%, GR grade) and hydrofluoric acid (HF, 40%, GR grade) were purchased from Beijing Chemical Inc. Boric acid (H3BO3, ≥99.8%, GR grade) was purchased from Sinopharm Chemical Reagent Co., Ltd. The experiment utilized deionized water with a resistance of 18.2 MΩ cm.
2.2 Elements analysis
The analysis of Rare Earth Elements (REY) was performed using inductively coupled plasma-mass spectrometry (ICP-MS, NexION 2000C ICP-MS, PerkinElmer, USA) in accordance with HJ766-201. Blank and certified reference materials, i.e., NIST 1632d (coal), and GSR-3 (rock), were also included in each experimental batch for quality control and assurance purposes. The recovery of REY in the reference materials ranged between 90% and 110%.
2.3 Experimental
To analyze the REY in coal and coal ash, the coal and coal ash were first dissolved by microwave digestion, followed by the concentration of the REY in the solution using ICP-MS. The specific steps of microwave digestion were follows: in the first step, 0.1 g of sample (coal or coal ash) was weighed with a precision balance, and then 5 mL of nitric acid and 2 mL of hydrofluoric acid were measured with a measuring cylinder. Finally, the sample, nitric acid and hydrofluoric acid were added to the PTFE digestion tank in turn and allowed to stand for two hours. During the standing process, the tank mouth was sealed with a fresh-keeping film to prevent debris from falling into the contaminated sample. In the second step, the digestion tank was placed in the microwave digestion instrument and the heating program was set as follows: firstly, the temperature was raised to 150 °C at a rate of 50 °C min−1 and maintained at this temperature for 5 minutes. Then the temperature was raised to 180 °C at a rate of 15 °C min−1 and maintained for 10 minutes. Finally, the temperature was raised to 210 °C at a rate of 6 °C min−1 and maintained for 15 minutes. In the third step, to prevent the formation of fluoride precipitation in the digestion process and the corrosion of analytical instruments by excessive hydrofluoric acid in the determination process, 20 mL of saturated boric acid solution was added to the digestion tank. Then, according to the second step of the heating program, the digestion was continued to decompose the fluoride precipitate and complex the excess hydrofluoric acid.50 After microwave digestion, the solution in the digestion tank was poured into a centrifuge bottle, and the digestion tank was rinsed with 3% dilute nitric acid for three times. The rinse solution was also poured into a centrifuge bottle and diluted to 50 mL for determination. Each sample was digested three times simultaneously.
3. Results and discussion
3.1 Physicochemical characteristics of coal
The results of industrial analysis and elemental analysis of the coal are shown in Table 1. According to MT/T 849-2000, the coal of P4 power plant is identified as mid-high volatile coal (>28.00–37.00%), whereas the coal of the other three power plants is identified as high volatile coal (>37.00–50.00%). Based on GB/15224.1-2018, the coal in three power plants (P1, P2, and P3) is low ash coal (>10.00–20.00%), but the coal of P4 power plant belongs to medium ash coal (>20.00–30.00%). According to MT/T 561-2008, the coal of the four power plants is low fixed carbon coal (≤55.00%). According to GB/15224.2-2010, the coal used in P1 and P2 power plants is ultra-low sulfur coal (≤0.50%), the coal of P3 power plant is low sulfur coal (0.51–1.00%), and the coal of P4 power plant is middle sulfur coal (1.01–2.00%).
Table 1 Proximate and ultimate analysis results of coal samples (wt%)a
Sample |
Proximate analysis |
Ultimate analysis |
Mad |
Vdaf |
Ad |
FCd |
Cdaf |
Hdaf |
Ndaf |
Sd |
Odaf |
M moisture, V volatile matter, A ash yield, FC fixed carbon, C carbon, H hydrogen, N nitrogen, S sulfur, O oxygen, ad air-dry basis, d dry basis, daf dry and ash-free basis. |
P1-coal |
6.36 |
37.79 |
15.65 |
52.48 |
72.34 |
5.62 |
1.24 |
0.40 |
26.90 |
P2-coal |
5.83 |
37.48 |
18.06 |
51.23 |
89.54 |
5.59 |
1.53 |
0.48 |
11.91 |
P3-coal |
4.98 |
37.76 |
15.28 |
52.74 |
84.65 |
5.15 |
0.97 |
0.71 |
14.16 |
P4-coal |
4.05 |
35.30 |
20.60 |
51.37 |
84.97 |
16.46 |
2.58 |
1.12 |
11.72 |
3.2 Geochemical characteristics of REY in coal and coal ash
The concentration and characteristic parameters of REY in coal and coal ash (slag and fly ash) are shown in Table 2. The total REY concentrations in P2 and P4 power plant coals were higher than the world average value (68.5 μg g−1).51 In contrast, the concentrations of REY in coal from P1 and P3 power plants were below the world average. Additionally, the concentration of REY in coal ash of each power plant was higher than that in the corresponding feed coal. The concentration of REY in slag was lower than the world average value (403.5 μg g−1),51 while the concentration of REY in fly ash exceeded the world average value. Moreover, the concentration of critical REY (critical) and the prospect coefficient8 (Cout1, as shown in eqn (1)) in coal and coal ash, except for the coal and slag of P2 power plant and the coal of P4 power plant, the concentration of critical REY and the prospect coefficient in the coal and coal ash of P1 and P3 power plants, the fly ash of P2 power plant, and the coal ash of P4 power plant were all above 30% and 0.7. |
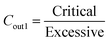 | (1) |
where Cout1 is the prospect coefficient, Critical represents the total concentration of critical REY (Nd, Eu, Tb, Dy, Y, and Er) and Excessive represents the total concentration of excessive REY (Ce, Ho, Tm, Yb, and Lu). Based on the market supply and demand relationship, Seredin and Dai6 proposed that coal ash with REY oxides concentration greater than 1000 μg g−1 and prospect coefficient (Cout1) greater than 0.7 have the potential for REY recovery. In addition, the U.S. Department of Energy (DOE) has recommended that coal ash with a total REY concentration of more than 300 μg g−1 has REY recovery potential.9 Therefore, according to the evaluation method proposed by Dai et al.,17 the coal ash of four power plants cannot be used as the raw material for the recovery of REY, but according to the recommended extraction value of DOE,9 the coal ash of four coal-fired power plants has the potential for REY recovery.
Table 2 Concentrations and characteristics of REY in coal and coal ash (μg g−1)
Element |
P1 |
P2 |
P3 |
P4 |
Coal |
Slag |
Fly ash |
Coal |
Slag |
Fly ash |
Coal |
Slag |
Fly ash |
Coal |
Slag |
Fly ash |
La |
9.3 |
76.1 |
122.9 |
24.4 |
79.2 |
123.7 |
9.7 |
58.8 |
85.3 |
32.6 |
79.0 |
136.0 |
Ce |
20.4 |
148.6 |
238.6 |
46.1 |
156.6 |
235.5 |
21.3 |
116.3 |
165.6 |
60.6 |
151.7 |
263.5 |
Pr |
2.3 |
17.1 |
27.1 |
4.9 |
17.4 |
26.1 |
2.4 |
13.7 |
18.6 |
6.4 |
17.3 |
28.8 |
Nd |
7.9 |
60.6 |
98.9 |
15.3 |
58.3 |
90.8 |
8.0 |
46.5 |
66.3 |
20.7 |
58.8 |
99.9 |
Sm |
1.4 |
10.9 |
17.2 |
2.9 |
10.6 |
15.9 |
1.5 |
8.8 |
11.9 |
3.8 |
10.5 |
17.3 |
Eu |
0.3 |
2.0 |
3.2 |
0.5 |
2.1 |
3.0 |
0.3 |
1.7 |
2.4 |
0.7 |
2.0 |
3.2 |
Gd |
1.4 |
10.4 |
16.0 |
2.7 |
10.0 |
14.2 |
1.4 |
8.3 |
11.2 |
3.6 |
10.0 |
16.0 |
Tb |
0.2 |
1.6 |
2.5 |
0.4 |
1.5 |
2.3 |
0.2 |
1.3 |
1.7 |
0.6 |
1.6 |
2.5 |
Dy |
1.3 |
9.3 |
14.4 |
2.3 |
8.6 |
13.2 |
1.2 |
7.0 |
9.7 |
3.2 |
8.6 |
14.2 |
Y |
7.7 |
46.8 |
86.8 |
11.9 |
43.7 |
77.5 |
6.4 |
37.7 |
62.6 |
16.8 |
43.7 |
80.5 |
Ho |
0.3 |
1.8 |
2.9 |
0.4 |
1.7 |
2.6 |
0.2 |
1.4 |
2.0 |
0.6 |
1.7 |
2.8 |
Er |
0.8 |
5.2 |
8.5 |
1.3 |
4.7 |
7.7 |
0.7 |
4.1 |
5.8 |
1.8 |
4.9 |
8.2 |
Tm |
0.1 |
0.7 |
1.2 |
0.2 |
0.6 |
1.1 |
0.1 |
0.6 |
0.8 |
0.2 |
0.7 |
1.1 |
Yb |
0.7 |
4.4 |
7.4 |
1.1 |
4.0 |
6.9 |
0.6 |
3.5 |
5.2 |
1.5 |
4.1 |
7.3 |
Lu |
0.1 |
0.7 |
1.1 |
0.2 |
0.6 |
1.0 |
0.1 |
0.5 |
0.8 |
0.2 |
0.6 |
1.1 |
LREY |
41.3 |
313.3 |
504.6 |
93.7 |
322.2 |
492.0 |
43.0 |
244.1 |
347.8 |
124.1 |
317.3 |
545.6 |
MREY |
11.0 |
70.1 |
122.8 |
17.9 |
65.9 |
110.1 |
9.5 |
56.1 |
87.5 |
24.8 |
66.0 |
116.4 |
HREY |
2.0 |
12.8 |
21.1 |
3.2 |
11.7 |
19.3 |
1.7 |
10.0 |
14.6 |
4.4 |
11.9 |
20.7 |
REY |
54.3 |
396.2 |
648.5 |
114.7 |
399.7 |
621.4 |
54.2 |
310.2 |
449.9 |
153.3 |
395.2 |
682.6 |
LREY (%) |
76.2 |
79.1 |
77.8 |
81.6 |
80.6 |
79.2 |
79.3 |
78.7 |
77.3 |
80.9 |
80.3 |
79.9 |
MREY (%) |
20.2 |
17.7 |
18.9 |
15.6 |
16.5 |
17.7 |
17.5 |
18.1 |
19.5 |
16.2 |
16.7 |
17.0 |
HREE (%) |
3.6 |
3.2 |
3.2 |
2.8 |
2.9 |
3.1 |
3.2 |
3.2 |
3.2 |
2.9 |
3.0 |
3.0 |
Critical |
18.3 |
125.5 |
214.2 |
31.7 |
119.0 |
194.5 |
16.8 |
98.3 |
148.5 |
43.7 |
119.5 |
208.6 |
Uncritical |
14.4 |
114.5 |
183.1 |
35.0 |
117.2 |
179.9 |
15.1 |
89.5 |
127.0 |
46.4 |
116.9 |
198.1 |
Excessive |
21.6 |
156.2 |
251.2 |
48.1 |
163.6 |
247.1 |
22.3 |
122.3 |
174.4 |
63.3 |
158.8 |
276.0 |
Critical (%) |
33.6 |
31.7 |
33.0 |
27.6 |
29.8 |
31.3 |
31.0 |
31.7 |
33.0 |
28.5 |
30.2 |
30.6 |
Cout1 |
0.8 |
0.8 |
0.9 |
0.7 |
0.7 |
0.8 |
0.8 |
0.8 |
0.9 |
0.7 |
0.8 |
0.8 |
3.3 Distribution and enrichment characteristics of REY in coal and coal ash
3.3.1 Modes of occurrence of REY in coal. According to the ash yield and the concentration of REY in coal from four different power plants, the correlation between ash and REY was analyzed, as shown in Fig. 1 and 2. The ash yield in the coal of P3 and P1 power plants was similar, and the concentration of REY in corresponding coal was also approximately equal. However, from P2 to P4 power plants, as the ash yield in the coal increases significantly, and the concentration of each REY also increases substantially (Fig. 1). In addition, with the increase of the volatile matter content in the coal, the change in the concentration of each REY was not regular (Fig. 2). This indicates a positive correlation between the concentration of REY in coal and ash yield. This was consistent with the existing research results, indicating that REY were mainly distributed in REY minerals (monazite, phosphates, sulfates, carbonates, and fluorocarbonates, etc.), accessory minerals (zircon, apatite, etc.), and clay minerals in coal.6,52,53
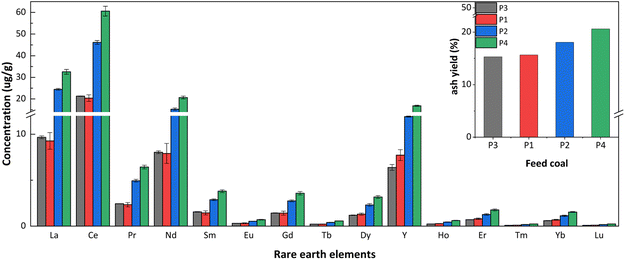 |
| Fig. 1 Effect of ash yield in coal on the distribution of REY. | |
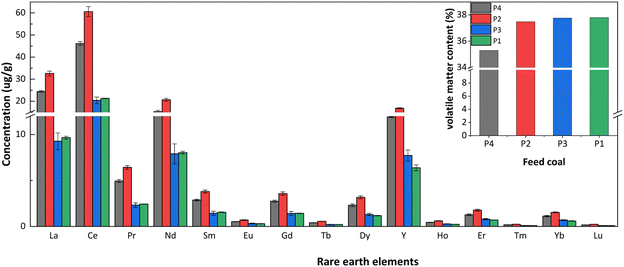 |
| Fig. 2 Effect of volatile matter content in coal on the distribution of REY. | |
3.3.2 Distribution characteristic of REY in coal and coal ash. The concentration of each REY in coal and coal ash from four coal-fired power plants was normalized to the Upper Continental Crust (UCC),54 respectively. The normalized REY pattern is shown in Fig. 3. The coal and coal ash showed a relatively flat REY distribution pattern, and the distribution patterns of REY in the coal, slag, and fly ash of each power plant were consistent, indicating that REY have no obvious fractionation under different coal types and combustion conditions.37,39 In addition, due to the volatilization and combustion of organic matter in coal, the concentrations of REY in all ashes were higher than that in the corresponding coals, indicating that each REY was enriched in different degrees during the combustion process of different coals. Moreover, the minerals containing REY in coal were formed very fine particles during coal combustion, which may be mainly distributed in fly ash.55–59 Meantime, REY combined with organic matter may partially volatilize and condense into fly ash during combustion.57 Studies have shown that REY exist in amorphous and graphite carbons surrounding Al–Si glass and magnetite in fly ash.46,60 Therefore, fly ash may be more enriched in REY than slag.
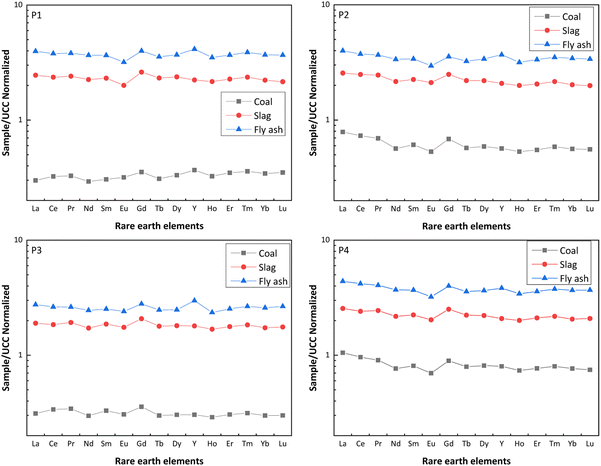 |
| Fig. 3 UCC-normalized REY patterns of coal and coal ash sample. | |
3.3.3 Enrichment characteristic of REY in coal and coal ash. The enrichment coefficient18 was used to illustrate the enrichment behavior of REY in coal and coal ash, that is, the concentration ratio of elements in one sample to corresponding elements in another sample was analyzed, as shown in Table 3. In the enrichment coefficient (CC1) of coal relative to world coal, the total REY enrichment coefficients in P1 and P3 power plants were both equal or less than 1. The enrichment coefficients of total REY in P2 and P4 power plants increased in turn and were all greater than 1. Compared with P1 and P3 power plants, the REY in the coal of P4 power plant are obviously enriched. In the enrichment coefficients of coal ash (slag and fly ash) relative to world ash, the enrichment coefficient of slag relative to world ash (CC2) in each power plant was less than 1, while the enrichment coefficient of fly ash relative to world ash (CC3) was greater than 1, indicating that REY are more likely to be enriched into fly ash during coal combustion. In addition, in the enrichment coefficients (CC4 and CC5) of coal ash (slag and fly ash) relative to the feed coal, the enrichment coefficient of coal ash relative to the coal in each power plant was all greater than 1, and the enrichment coefficients (CC6) of fly ash relative to slag were all greater than 1. This further indicates that REY were mainly present in fine minerals and glass particles, and the amorphous and graphite carbon surrounding Al–Si glass and magnetite in fly ash may be beneficial to the enrichment of REY. Moreover, the yield of fly ash was far greater than that of slag. Therefore, REY in fly ash have more potential for recovery. In addition, with the increase of enrichment coefficient (CC5), the ash yield decreased, while the volatile matter content increased (Fig. 4). This indicates that the lower the ash yield and the higher the volatile matter content in coal, the greater the enrichment coefficient of REY in fly ash.
Table 3 Enrichment coefficient of REY in coal and coal asha
Element |
P1 |
P2 |
P3 |
P4 |
CC1 |
CC2 |
CC3 |
CC4 |
CC5 |
CC6 |
CC1 |
CC2 |
CC3 |
CC4 |
CC5 |
CC6 |
CC1 |
CC2 |
CC3 |
CC4 |
CC5 |
CC6 |
CC1 |
CC2 |
CC3 |
CC4 |
CC5 |
CC6 |
CC1 represents the enrichment coefficient of coal to world coal, CC2 represents the enrichment coefficient of slag to world ash, CC3 represents the enrichment coefficient of fly ash to world ash, CC4 represents the enrichment coefficient of slag to coal, CC5 represents the enrichment coefficient of fly ash to coal, CC6 represents the enrichment coefficient of fly ash to slag, the data of REY in world coal and ash came from Ketris and Yudovich51. |
La |
0.84 |
1.10 |
1.78 |
8.21 |
13.26 |
1.61 |
2.22 |
1.15 |
1.79 |
3.24 |
5.06 |
1.56 |
0.88 |
0.85 |
1.24 |
6.09 |
8.84 |
1.45 |
2.96 |
1.14 |
1.97 |
2.43 |
4.18 |
1.72 |
Ce |
0.89 |
1.14 |
1.84 |
7.29 |
11.70 |
1.61 |
2.01 |
1.20 |
1.81 |
3.39 |
5.10 |
1.50 |
0.93 |
0.89 |
1.27 |
5.46 |
7.78 |
1.42 |
2.64 |
1.17 |
2.03 |
2.50 |
4.35 |
1.74 |
Pr |
0.66 |
0.85 |
1.35 |
7.34 |
11.63 |
1.59 |
1.41 |
0.87 |
1.30 |
3.53 |
5.28 |
1.50 |
0.70 |
0.68 |
0.93 |
5.62 |
7.66 |
1.36 |
1.84 |
0.87 |
1.44 |
2.70 |
4.48 |
1.66 |
Nd |
0.66 |
0.90 |
1.48 |
7.67 |
12.52 |
1.63 |
1.27 |
0.87 |
1.36 |
3.82 |
5.94 |
1.56 |
0.67 |
0.69 |
0.99 |
5.79 |
8.25 |
1.43 |
1.72 |
0.88 |
1.49 |
2.84 |
4.83 |
1.70 |
Sm |
0.72 |
0.84 |
1.32 |
7.57 |
11.96 |
1.58 |
1.43 |
0.81 |
1.23 |
3.69 |
5.55 |
1.51 |
0.77 |
0.67 |
0.91 |
5.66 |
7.65 |
1.35 |
1.90 |
0.81 |
1.33 |
2.77 |
4.55 |
1.64 |
Eu |
0.68 |
0.80 |
1.27 |
6.31 |
10.03 |
1.59 |
1.13 |
0.85 |
1.18 |
3.97 |
5.55 |
1.40 |
0.65 |
0.70 |
0.96 |
5.70 |
7.85 |
1.38 |
1.49 |
0.81 |
1.29 |
2.91 |
4.61 |
1.58 |
Gd |
0.52 |
0.65 |
1.00 |
7.38 |
11.29 |
1.53 |
1.02 |
0.62 |
0.89 |
3.63 |
5.18 |
1.43 |
0.53 |
0.52 |
0.70 |
5.82 |
7.84 |
1.35 |
1.32 |
0.63 |
1.00 |
2.81 |
4.47 |
1.59 |
Tb |
0.68 |
0.77 |
1.18 |
7.51 |
11.48 |
1.53 |
1.25 |
0.73 |
1.08 |
3.84 |
5.65 |
1.47 |
0.65 |
0.60 |
0.82 |
5.98 |
8.28 |
1.38 |
1.74 |
0.74 |
1.19 |
2.80 |
4.50 |
1.60 |
Dy |
0.62 |
0.66 |
1.03 |
7.15 |
11.12 |
1.56 |
1.10 |
0.61 |
0.94 |
3.72 |
5.74 |
1.54 |
0.56 |
0.50 |
0.69 |
5.95 |
8.17 |
1.37 |
1.51 |
0.62 |
1.01 |
2.72 |
4.48 |
1.65 |
Y |
0.92 |
0.92 |
1.70 |
6.06 |
11.24 |
1.85 |
1.42 |
0.86 |
1.52 |
3.67 |
6.51 |
1.77 |
0.76 |
0.74 |
1.23 |
5.91 |
9.81 |
1.66 |
2.00 |
0.86 |
1.58 |
2.60 |
4.78 |
1.84 |
Ho |
0.50 |
0.45 |
0.73 |
6.65 |
10.76 |
1.62 |
0.82 |
0.41 |
0.66 |
3.74 |
5.94 |
1.59 |
0.44 |
0.35 |
0.49 |
5.82 |
8.13 |
1.40 |
1.13 |
0.42 |
0.71 |
2.72 |
4.64 |
1.71 |
Er |
0.86 |
0.95 |
1.54 |
6.52 |
10.56 |
1.62 |
1.36 |
0.86 |
1.40 |
3.72 |
6.07 |
1.63 |
0.75 |
0.74 |
1.06 |
5.80 |
8.29 |
1.43 |
1.90 |
0.88 |
1.50 |
2.75 |
4.66 |
1.70 |
Tm |
0.35 |
0.35 |
0.58 |
6.58 |
10.82 |
1.65 |
0.57 |
0.32 |
0.53 |
3.68 |
5.97 |
1.62 |
0.30 |
0.28 |
0.40 |
5.84 |
8.46 |
1.45 |
0.78 |
0.33 |
0.56 |
2.72 |
4.69 |
1.73 |
Yb |
0.69 |
0.72 |
1.19 |
6.47 |
10.76 |
1.66 |
1.12 |
0.65 |
1.11 |
3.60 |
6.12 |
1.70 |
0.60 |
0.56 |
0.83 |
5.79 |
8.62 |
1.49 |
1.53 |
0.66 |
1.18 |
2.69 |
4.79 |
1.78 |
Lu |
0.54 |
0.56 |
0.95 |
6.15 |
10.50 |
1.71 |
0.86 |
0.51 |
0.87 |
3.56 |
6.06 |
1.70 |
0.46 |
0.45 |
0.69 |
5.87 |
8.87 |
1.51 |
1.16 |
0.54 |
0.95 |
2.79 |
4.93 |
1.77 |
REY |
0.79 |
0.98 |
1.61 |
7.30 |
11.95 |
1.64 |
1.68 |
0.99 |
1.54 |
3.48 |
5.42 |
1.55 |
0.79 |
0.77 |
1.11 |
5.72 |
8.30 |
1.45 |
2.24 |
0.98 |
1.69 |
2.58 |
4.45 |
1.73 |
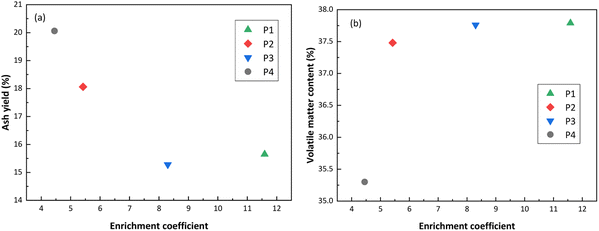 |
| Fig. 4 Effect of the major components in coal on the enrichment coefficient of REY. (a) Represents the effect of the ash yield in coal on the enrichment coefficient (CC5) of REY. (b) Represents the effect of the volatile matter content in coal on the enrichment coefficient (CC5) of REY. | |
4. Conclusions
In this paper, the distribution and enrichment characteristics of REY in coal and coal ash from four different coal-fired power plants in China were studied. The concentrations of REY in the fly ash of the four coal-fired power plants were higher than the extraction values recommended by the US Department of Energy. Meantime, the proportion of critical REY and the prospect coefficient (Cout1) were both greater than 30% and 0.7, respectively, suggesting potential for these resources to be utilized as secondary resources of REY. In addition, with the increase of ash yield in coal, the concentration of REY increases. However, with the increase of volatile matter content in coal, the concentration of REY did not increase. This indicates that REY mainly exist in the minerals of coal. The coal and coal ash of each coal-fired power plant have similar REY distribution patterns, which revealed that the REY in the combustion process of the coal in each power plant do not have obvious fractionation. When the ash yield in coal was lower and the volatile matter content was higher, the enrichment coefficient of REY in coal ash was larger. The content of REY in fly ash was greater than that in slag, and it has the potential of REY recovery. These results provide a theoretical basis for the recovery of REY from coal and coal ash.
Author contributions
Guoqiang Wu: conceptualization, formal analysis, resources, funding acquisition, data analysis and writing – original draft, supervision. Zhanlong Ma: methodology, investigation, criticism, writing – review & editing. Guosheng Li: writing – review & editing. Chunmiao Bo: criticism.
Conflicts of interest
There are no conflicts to declare.
Acknowledgements
This research was supported by the Natural Science Foundation of Ningxia Province (2022AAC03247).
References
- S.-S. Chai, W.-B. Zhang, J.-L. Yang, L. Zhang, M. M. Theint, X.-L. Zhang, S.-B. Guo, X. Zhou and X.-J. Ma, Sustainability applications of rare earths from metallurgy, magnetism, catalysis, luminescence to future electrochemical pseudocapacitance energy storage, RSC Sustainability, 2023, 1(1), 38–71 RSC.
- R. Lin, B. H. Howard, E. A. Roth, T. L. Bank, E. J. Granite and Y. Soong, Enrichment of rare earth elements from coal and coal by-products by physical separations, Fuel, 2017, 200, 506–520 CrossRef CAS.
- Information Office of the State Council of the People 's Republic of China, China 's rare earth situation and policy, China Met. bull., 2012, 24, 20–24 Search PubMed.
- U.S. Geological Survey. Mineral Commodity Summaries 2023, U.S. Geological Survey, United States, 2023, DOI:10.3133/mcs2023.
- Z. H. Weng, S. M. Jowitt, G. M. Mudd and N. Haque, Assessing rare earth element mineral deposit types and links to environmental impacts, Appl. Earth Sci., 2013, 122(2), 83–96 CrossRef CAS.
- V. V. Seredin and S. Dai, Coal deposits as potential alternative sources for lanthanides and yttrium, Int. J. Coal Geol., 2012, 94, 67–93 CrossRef CAS.
- S. Dai and R. B. Finkelman, Coal as a promising source of critical elements: Progress and future prospects, Int. J. Coal Geol., 2018, 186, 155–164 CrossRef CAS.
- V. V. Seredin, A new method for primary evaluation of the outlook for rare earth element ores, Geol. Ore Deposits, 2010, 52(5), 428–433 CrossRef.
- U.S. Department of Energy NETL, Rare Earth Elements from Coal and Coal By-Products, 2017, https://www.netl.doe.gov/research/coal/rare-earth-elements Search PubMed.
- V. V. Seredin, Rare earth element-bearing coals from the Russian Far East deposits, Int. J. Coal Geol., 1996, 30(1), 101–129 CrossRef CAS.
- S. M. Mardon and J. C. Hower, Impact of coal properties on coal combustion by-product quality: examples from a Kentucky power plant, Int. J. Coal Geol., 2004, 59(3), 153–169 CrossRef CAS.
- J. C. Hower, L. F. Ruppert and C. F. Eble, Lanthanide, yttrium, and zirconium anomalies in the Fire Clay coal bed, Eastern Kentucky, Int. J. Coal Geol., 1999, 39(1), 141–153 CrossRef CAS.
- W. H. Huang, B. Jiu and Y. Li, Distribution characteristics of rare earth elements in coal and its prospects on development and exploitation, J. China Coal Soc., 2019, 44(1), 287–294 Search PubMed.
- S. F. Dai, Y. P. Zhou, D. Y. Ren, X. B. Wang, D. Li and L. Zhao, Geochemistry and mineralogy of the Late Permian coals from the Songzao Coalfield, Choongqing, Southwestern China, Sci. China, Ser. D: Earth Sci., 2007, 37(3), 353–362 Search PubMed.
- S. Dai, Y. Jiang, C. R. Ward, L. Gu, V. V. Seredin, H. Liu, D. Zhou, X. Wang, Y. Sun, J. Zou and D. Ren, Mineralogical and geochemical compositions of the coal in the Guanbanwusu Mine, Inner Mongolia, China: Further evidence for the existence of an Al (Ga and REE) ore deposit in the Jungar Coalfield, Int. J. Coal Geol., 2012, 98, 10–40 CrossRef CAS.
- S. Dai, Y. Luo, V. V. Seredin, C. R. Ward, J. C. Hower, Z. Lei, S. Liu, C. Zhao, H. Tian and J. Zou, Revisiting the late Permian coal from the Huayingshan, Sichuan, southwestern China: Enrichment and occurrence modes of minerals and trace elements, Int. J. Coal Geol., 2014, 122(1), 110–128 CrossRef CAS.
- S. Dai, P. Xie, C. R. Ward, X. Yan, W. Guo, D. French and I. T. Graham, Anomalies of rare metals in Lopingian super-high-organic-sulfur coals from the Yishan Coalfield, Guangxi, China, Ore Geol. Rev., 2017, 88, 235–250 CrossRef.
- S. Dai, V. V. Seredin, C. R. Ward, J. C. Hower, Y. Xing, W. Zhang, W. Song and P. Wang, Enrichment of U–Se–Mo–Re–V in coals preserved within marine carbonate successions: geochemical and mineralogical data from the Late Permian Guiding Coalfield, Guizhou, China, Miner. Deposita, 2015, 50(2), 159–186 CrossRef CAS.
- Y. Y. Wu, Y. Qin and T. S. Yi, Enrichment of rare earth elements in high sulfur coal of Liangshan Formation from Kaili, Guizhou, China and geological origin, Acta Geol. Sin., 2010, 84(2), 280–285 CrossRef CAS.
- Z. D. Cao, Geochemical characteristics of lanthanide in the 9Th and 16Th coal seams in the Huaqiu exploration area in Northern Guizhou coalfield, Acta Mineral. Sin., 2007, 27(3/4), 499–504 CAS.
- J. C. Hower, B. Fu and S. Dai, Geochemical partitioning from pulverized coal to fly ash and bottom ash, Fuel, 2020, 279, 118542 CrossRef CAS.
- L. B. Clarke, The fate of trace elements during coal combustion and gasification: an overview, Fuel, 1993, 72(6), 731–736 CrossRef CAS.
- S. J. Qin, F. Xu, L. Cui, J. X. Wang, S. Y. Li, Z. S. Zhao, L. Xiao, Y. X. Guo and C. L. Zhao, Geochemistry characteristics and resource utilization of strategically critical trace elements from coal-related resources, Coal Sci. Technol., 2022, 50(3), 1–38 CAS.
- J. C. Hower, J. G. Groppo, H. Hsu-Kim and R. K. Taggart, Signatures of rare earth element distributions in fly ash derived from the combustion of Central Appalachian, Illinois, and Powder River basin coals, Fuel, 2021, 301, 121048 CrossRef CAS.
- S. F. Dai, L. Zhao, Q. Wei, X. L. Song, W. F. Wang, J. J. Liu and P. P. Duan, Resources of critical metals in coal-bearing sequences in China:Enrichment types and distribution, Chin. Sci. Bull., 2020, 65(33), 3715–3729 CrossRef.
- B. Fu, J. C. Hower, W. Zhang, G. Luo, H. Hu and H. Yao, A review of rare earth elements and yttrium in coal ash: Content, modes of occurrences, combustion behavior, and extraction methods, Prog. Energy Combust. Sci., 2022, 88, 100954 CrossRef.
- B. Valentim, A. T. Abagiu, L. Anghelescu, D. Flores, D. French, P. Gonçalves, A. Guedes, L. G. Popescu, G. Predeanu, J. Ribeiro, A. C. Santos, V. Slăvescu and C. R. Ward, Assessment of bottom ash landfilled at Ceplea Valley (Romania) as a source of rare earth elements, Int. J. Coal Geol., 2019, 201, 109–126 CrossRef CAS.
- Z. Adamczyk, J. Komorek, B. Białecka, J. Nowak and A. Klupa, Assessment of the potential of polish fly ashes as a source of rare earth elements, Ore Geol. Rev., 2020, 124, 103638 CrossRef.
- I. C. Okeme, R. A. Crane, W. M. Nash, T. I. Ojonimi and T. B. Scott, Characterisation of rare earth elements and toxic heavy metals in coal and coal fly ash, RSC Adv., 2022, 12(30), 19284–19296 RSC.
- S. I. Arbuzov, I. Y. Chekryzhov, R. B. Finkelman, Y. Z. Sun, C. L. Zhao, S. S. Il'enok, M. G. Blokhin and N. V. Zarubina, Comments on the geochemistry of rare-earth elements (La, Ce, Sm, Eu, Tb, Yb, Lu) with examples from coals of north Asia (Siberia, Russian far East, North China, Mongolia, and Kazakhstan), Int. J. Coal Geol., 2019, 206, 106–120 CrossRef CAS.
- T. Skripkina, M. Belokozenko, S. Shatskaya, V. Tikhova and I. Lomovskiy, Concentrating rare earth elements in brown coal humic acids by mechanochemical treatment, RSC Adv., 2021, 11(57), 36016–36022 RSC.
- B. A. Bishop, K. R. Shivakumar, D. S. Alessi and L. J. Robbins, Insights into the rare earth element potential of coal combustion by-products from western Canada, Environ. Sci.: Adv., 2023, 2(3), 529–542 CAS.
- S. Mondal, A. Ghar, A. K. Satpati, P. Sinharoy, D. K. Singh, J. N. Sharma, T. Sreenivas and V. Kain, Recovery of rare earth elements from coal fly ash using TEHDGA impregnated resin, Hydrometallurgy, 2019, 185, 93–101 CrossRef CAS.
- A. Kumari, R. Parween, S. Chakravarty, K. Parmar, D. D. Pathak, J.-c. Lee and M. K. Jha, Novel approach to recover rare earth metals (REMs) from Indian coal bottom ash, Hydrometallurgy, 2019, 187, 1–7 CrossRef CAS.
- K. K. Karan, R. E. Masto, H. Agarwalla, S. Bari, M. Kumar, P. Gopinathan, B. Hazra, S. Saha and S. Maity, Separation of coal combustion residue for critical element extraction and other bulk uses, Environ. Sci.: Adv., 2023, 3, 109–118 Search PubMed.
- N. J. Wagner and A. Matiane, Rare earth elements in select Main Karoo Basin (South Africa) coal and coal ash samples, Int. J. Coal Geol., 2018, 196, 82–92 CrossRef CAS.
- S. Dai, L. Zhao, J. C. Hower, M. N. Johnston, W. Song, P. Wang and S. Zhang, Petrology, Mineralogy, and Chemistry of Size-Fractioned Fly Ash from the Jungar Power Plant, Inner Mongolia, China, with Emphasis on the Distribution of Rare Earth Elements, Energy Fuels, 2014, 28(2), 1502–1514 CrossRef CAS.
- J. Pan, C.-C. Zhou, C. Liu, M. Tang, S. Cao, T. Hu, W. Ji, Y. Luo, M. Wen and N. Zhang, Modes of Occurrence of Rare Earth Elements in Coal Fly Ash: A Case Study, Energy Fuels, 2018, 32, 9738–9743 CrossRef CAS.
- Z. Wang, S. Dai, J. Zou, D. French and I. T. Graham, Rare earth elements and yttrium in coal ash from the Luzhou power plant in Sichuan, Southwest China: Concentration, characterization and optimized extraction, Int. J. Coal Geol., 2019, 203, 1–14 CrossRef CAS.
- Z. Li, X. Li, L. Zhang, S. Li, J. Chen, X. Feng, D. Zhao, Q. Wang, Z. Gao and B. Xiong, Partitioning of rare earth elements and yttrium (REY) in five coal-fired power plants in Guizhou, Southwest China, J. Rare Earths, 2020, 38(11), 1257–1264 CrossRef CAS.
- L. Zhao, S. Dai, V. P. Nechaev, E. V. Nechaeva, I. T. Graham, D. French and J. Sun, Enrichment of critical elements (Nb-Ta-Zr-Hf-REE) within coal and host rocks from the Datanhao mine, Daqingshan Coalfield, northern China, Ore Geol. Rev., 2019, 111, 102951 CrossRef.
- G. Wu, N. Shi, T. Wang, C.-M. Cheng, J. Wang, C. Tian and W.-P. Pan, Enrichment and occurrence form of rare earth elements during coal and coal gangue combustion, Environ. Sci. Pollut. Res., 2022, 29, 44709–44722 CrossRef CAS.
- Z. Li, A. H. Clemens and T. A. Moore, Partitioning behaviour of trace elements in a stoker-fired combustion unit: An example using bituminous coals from the Greymouth coalfield (Cretaceous), New Zealand, Int. J. Coal Geol., 2005, 63(1/2), 98–116 CrossRef CAS.
- Z. Ma, X. Shan and F. Cheng, Distribution Characteristics of Valuable Elements, Al, Li, and Ga, and Rare Earth Elements in Feed Coal, Fly Ash, and Bottom Ash from a 300 MW Circulating Fluidized Bed Boiler, ACS Omega, 2019, 4(4), 6854–6863 CrossRef CAS PubMed.
- J. C. Hower, C. F. Eble, S. Dai and H. E. Belkin, Distribution of rare earth elements in eastern Kentucky coals: Indicators of multiple modes of enrichment, Int. J. Coal Geol., 2016, 160–161, 73–81 CrossRef CAS.
- M. M. Hood, R. K. Taggart, R. C. Smith, H. Hsu-Kim, K. R. Henke, U. Graham, J. G. Groppo, J. M. Unrine and J. C. Hower, Rare Earth Element Distribution in Fly Ash Derived from the Fire Clay Coal, Kentucky, Coal Combust. Gasif. Prod., 2017, 9, 22–33 Search PubMed.
- J. Liu, S. Dai, H. Xin, J. C. Hower and T. Sakulpitakphon, Size-dependent variations in fly ash trace-element chemistry:
Examples from a Kentucky power plant and with emphasis on rare earth elements, Energy Fuels, 2017, 31(1), 438–447 CrossRef CAS.
- J. C. Hower, E. Cantando, C. F. Eble and G. C. Copley, Characterization of stoker ash from the combustion of high-lanthanide coal at a Kentucky bourbon distillery, Int. J. Coal Geol., 2019, 213, 103260 CrossRef CAS.
- J. C. Hower, J. G. Groppo, P. Joshi, D. V. Preda, D. P. Gamliel, D. T. Mohler, J. D. Wiseman, S. D. Hopps, T. D. Morgan, T. Beers and M. Schrock, Distribution of Lanthanides, Yttrium, and Scandium in the Pilot-Scale Beneficiation of Fly Ashes Derived from Eastern Kentucky Coals, Minerals-Basel, 2020, 10(2), 1–17 Search PubMed.
- A. Iwashita, T. Nakajima, H. Takanashi, A. Ohki, Y. Fujita and T. Yamashita, Effect of pretreatment conditions on the determination of major and trace elements in coal fly ash using ICP-AES, Fuel, 2006, 85(2), 257–263 CrossRef CAS.
- M. P. Ketris and Y. E. Yudovich, Estimations of Clarkes for Carbonaceous biolithes: World averages for trace element contents in black shales and coals, Int. J. Coal Geol., 2009, 78(2), 135–148 CrossRef CAS.
- S. F. Dai, D. Y. Ren, Y. P. Zhou, V. V. Seredin, D. H. Li, M. Q. Zhang, J. C. Hower, C. R. Ward, X. B. Wang, L. Zhao and X. L. Son, Coal-hosted rare metal deposits: Genetic types, modes of occurrence, and utilization evaluation, J. China Coal Soc., 2014, 39(8), 1707–1715 CAS.
- R. Lin, T. L. Bank, E. A. Roth, E. J. Granite and Y. Soong, Organic and inorganic associations of rare earth elements in central Appalachian coal, Int. J. Coal Geol., 2017, 179, 295–301 CrossRef.
- S. Dai, I. Graham and C. Ward, A review of anomalous rare earth elements and yttrium in coal, Int. J. Coal Geol., 2016, 159, 82–95 CrossRef CAS.
- S. Dai, Z. Lei, J. C. Hower, M. N. Johnston, W. Song, P. Wang and S. Zhang, Petrology, Mineralogy, and Chemistry of Size-Fractioned Fly Ash from the Jungar Power Plant, Inner Mongolia, China, with Emphasis on the Distribution of Rare Earth Elements, Energy Fuels, 2014, 28(2), 1502–1514 CrossRef CAS.
- J. C. Hower, S. Dai, V. V. Seredin, L. Zhao, I. J. Kostova, L. F. O. Silva, S. M. Mardon and G. Gurdal, A Note on the Occurrence of Yttrium and Rare Earth Elements in Coal Combustion Products, Coal Combust. and Gasif. Prod., 2013, 5, 39–47 Search PubMed.
- S. Dai, L. Zhao, S. Peng, C.-L. Chou, X. Wang, Y. Zhang, D. Li and Y. Sun, Abundances and distribution of minerals and elements in high-alumina coal fly ash from the Jungar Power Plant, Inner Mongolia, China, Int. J. Coal Geol., 2010, 81(4), 320–332 CrossRef CAS.
- J. Pan, C. Zhou, M. Tang, S. Cao, C. Liu, N. Zhang, M. Wen, Y. Luo, T. Hu and W. Ji, Study on the modes of occurrence of rare earth elements in coal fly ash by statistics and a sequential chemical extraction procedure, Fuel, 2019, 237(1), 555–565 CrossRef CAS.
- R. S. Blissett, N. Smalley and N. A. Rowson, An investigation into six coal fly ashes from the United Kingdom and Poland to evaluate rare earth element content, Fuel, 2014, 119(1), 236–239 CrossRef CAS.
- J. C. Hower and J. G. Groppo, Rare Earth-bearing particles in fly ash carbons: Examples from the combustion of eastern Kentucky coals, Energy Geosci., 2021, 2(2), 90–98 CrossRef.
|
This journal is © The Royal Society of Chemistry 2024 |
Click here to see how this site uses Cookies. View our privacy policy here.