DOI:
10.1039/D3RA08660G
(Paper)
RSC Adv., 2024,
14, 2673-2677
Efficient construction of a β-naphthol library under continuous flow conditions†
Received
19th December 2023
, Accepted 4th January 2024
First published on 15th January 2024
Abstract
A β-naphthol library has been efficiently constructed utilizing a mild continuous flow procedure, relying on a tandem Friedel–Crafts reaction and starting from readily available arylacetyl chloride and alkynes. Multiple functionalized β-naphthols can be acquired within 160 s in generally high yields (up to 83%). Using an electron-rich phenylacetyl chloride derivative (4-OH- or 4-MeO-) provides spirofused triene dione as the primary product. A scale-up preparation affords a throughput of 4.70 g h−1, indicating potential large-scale application. Herein, we present a rapid, reliable, and scalable method to obtain various β-naphthols in the compound library.
Introduction
β-Naphthols are essential structural elements ubiquitous in a diverse range of natural products1 and pharmaceutical agents2 (Fig. 1). Furthermore, they serve as the critical synthetic precursor for the preparation of chiral binaphthyl compounds, especially BINOL,3 BINAP,4 and BNDHP,5 which play a significant role in asymmetric synthesis. β-Naphthols are also versatile synthetic intermediates that can be transformed into valuable molecules.6 Due to their wide application in pharmaceutical and agrochemical fields, investigating methodologies for the efficient synthesis of β-naphthols has attracted intensive interest in organic chemistry.
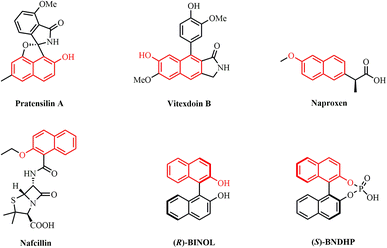 |
| Fig. 1 Bioactive and functional compounds containing β-naphthol moieties. | |
Over the past few decades, several synthetic methods have been developed for the construction of mono- or polysubstituted β-naphthols, generally relying on intramolecular cyclization reactions such as electrocyclization,7 Dieckmann8 and Aldol9 condensation, Pd-catalyzed annulation,10 oxidative cyclization.11 However, the known synthetic strategies typically suffer from some drawbacks, such as long synthetic sequences, modest regioselectivity, limited substrate scope, and not readily available starting materials. It is worth noting that the tandem Friedel–Crafts reaction of easily available arylacetyl chloride with alkynes provided selectively 3,4-disubstituted β-naphthols, affording a unique strategy for obtaining β-naphthols (Scheme 1).12
 |
| Scheme 1 The synthesis of β-naphthols from arylacetyl chloride with alkynes. | |
As an emerging and prospective technique, continuous flow considerably improves chemical synthesis productivity13 and provides a powerful tool to address long-standing challenges in academia and industry.14 The flow process is enabled by utilizing the micro-reactor, which has a high surface/volume ratio that permits rapid heat and mass transfer.15 Furthermore, the precise control of reaction parameters (time, temperature, and mixing) in continuous flow gives fast condition screening and efficient synthesis, and a reliable and straightforward scale-up was also readily achieved by raising the flow rate, processing time, or micro-reactor volume.16 It was found that Friedel–Crafts reaction was particularly suitable to conduct under continuous flow conditions and typically showcased improved performance than the batch process.17 Out of our keen interest in asymmetric catalysis, various β-naphthols were in demand as building blocks to prepare chiral binaphthyl ligands. Herein, we disclose an efficient continuous flow procedure to rapidly establish a β-naphthol library that relies on tandem Friedel–Crafts reaction starting from arylacetyl chloride and alkynes, to satisfy the demand for multiple β-naphthols.
Results and discussion
In preliminary experiments, our investigation focused on the reaction between phenylacetyl chloride (1a) and diphenylacetylene (2a) in a simple continuous flow system, which comprised two HPLC pumps, a T-shaped mixer (Mixer, PEEK, 1/16′′ I.D.), and a coil reactor (Reactor, PFA, 1/16′′ O.D., 5.9 mL internal volume). As shown in Fig. 2, 1a and AlCl3 were mixed in CH2Cl2 and sonicated for 1 min to provide a clear complex solution. 1a-AlCl3 solution (0.1 M in CH2Cl2) was driven by an HPLC pump at a given flow rate (A mL min−1) into Mixer, where it was mixed with 2a solution (0.1 M in CH2Cl2) and delivered by the other HPLC pump at a flow rate of B mL min−1. The reaction was performed as the combined stream was passed through Reactor with a residence time of tR s. After quenching with H2O and the usual workup, the target product β-naphthol 3a was obtained.
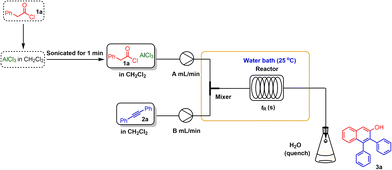 |
| Fig. 2 The flow system for the synthesis of β-naphthol 3a. | |
Various reaction parameters (reagent dosage, residence time, temperature, and concentration) were screened; the results were summarized in Table 1. Considering the critical role of AlCl3 in the Friedel–Crafts reaction, the amount of AlCl3 was first investigated. Keeping the flow rate of two solutions at 1.0 mL min−1, using 1.1 equiv. of AlCl3, and with a residence time of 176 s, the β-Naphthol 3a was only obtained in a low yield of 49% (entry 1). The elevated AlCl3 to 1.3 equiv. resulted in an increased formation of 3a and still with a surplus of 2a, while the higher amount (1.5 equiv.) provided similar results (entries 2 and 3). Thus, the use of 1.3 equiv. of AlCl3 was most advantageous. Our further attempts to improve the yield focus on enhancing the amount of 1a-AlCl3. After increasing the flow rate of 1a-AlCl3 solution from 1.1 to 1.5 mL min−1, the best result (83% yield) was achieved at a flow rate of 1.2 mL min−1 and with a residence time of 160 s (entry 5). It had a detrimental impact on the formation of 3a when the flow rate elevated further, probably due to reduced reaction time (entries 6 and 7). In addition, there was no measurable yield improvement on extending the reaction time to 320 s by lowering the flow rate (entry 8), and decreased yields were observed when shortening the residence time to 107 s and 80 s (entries 9 and 10). The influence of temperature was also examined; performing the reaction at 0 °C led to a lower yield of 3a (entry 11), but increasing the reaction to 40 °C could be well tolerated (entry 12). Furthermore, the screen results for the concentration revealed that the low concentration at 0.05 M was detrimental to the generation of 3a (entry 13); however, the higher concentration (0.2 M) gave a satisfactory outcome (entry 14). We also evaluated BF3·Et2O as the Lewis acid instead of AlCl3, but only trace amounts of the desired product were obtained.
Table 1 Condition screen results of the reaction between phenylacetyl chloride and diphenylacetylene
Entry |
A (mL min−1) |
B (mL min−1) |
AlCl3a (equiv.) |
tR (s) |
Yieldb (%) |
Relative to phenylacetyl chloride. Isolated yield based on the starting diphenylacetylene. The coil reactor was dipped in a cooling bath at 0 °C. The coil reactor was dipped in a water bath at 40 °C. The concentration of 1a and 2a in CH2Cl2 were 0.05 M. The concentration of 1a and 2a in CH2Cl2 were 0.2 M. BF3·Et2O was used in this case. |
1 |
1.0 |
1.0 |
1.1 |
176 |
49 |
2 |
1.0 |
1.0 |
1.3 |
176 |
63 |
3 |
1.0 |
1.0 |
1.5 |
176 |
65 |
4 |
1.1 |
1.0 |
1.3 |
168 |
78 |
5 |
1.2 |
1.0 |
1.3 |
160 |
83 |
6 |
1.3 |
1.0 |
1.3 |
153 |
79 |
7 |
1.5 |
1.0 |
1.3 |
141 |
72 |
8 |
0.6 |
0.5 |
1.3 |
320 |
84 |
9 |
1.8 |
1.5 |
1.3 |
107 |
64 |
10 |
2.4 |
2.0 |
1.3 |
80 |
60 |
11c |
1.2 |
1.0 |
1.3 |
160 |
56 |
12d |
1.2 |
1.0 |
1.3 |
160 |
81 |
13e |
1.2 |
1.0 |
1.3 |
160 |
66 |
14f |
1.2 |
1.0 |
1.3 |
160 |
80 |
15g |
1.2 |
1.0 |
1.3 |
160 |
Trace |
Thus, the optimized flow conditions for the preparation of β-naphthol were obtained as follows. A solution of 1a-AlCl3 (0.1 M in CH2Cl2, 1.3 equiv. AlCl3 relative to 1a, 1.2 mL min−1) and a solution of 2a (0.1 M in CH2Cl2, 1.0 mL min−1) were introduced to Mixer with HPLC pumps. The combined stream was passed through Reactor with a residence time of 160 s at 25 °C, furnishing β-naphthol 3a with 83% yield after quenching with H2O.
With the efficient continuous flow protocol, we next explored the rapid development of a β-naphthol library under continuous flow conditions. Firstly, the substrate scope for phenylacetyl chloride with various alkynes was evaluated in the flow system (Table 2). The alkyl disubstituted internal alkyne (2b) could be smoothly converted into 3,4-disubstituted β-naphthol with moderate yield (entry 1, 70%). While the asymmetric disubstituted alkyne (2c) with aryl and alkyl substituents led to the regioselective generation of 3,4-disubstituted product, providing a high yield of β-naphthol (entry 2, 81%). The terminal alkynes bearing aryl or alkyl substituents (2d–2g) were also well-tolerated, affording the 4-substituted β-naphthol with good yields ranging from 74 to 78% (entries 3–6). Interestingly, subjecting trimethylsilylacetylene (2h) to the flow system, 2-naphthol (3h) could be selectively obtained in superior yield (82%) and with the removal of the TMS group (entry 7); the result was different from the mixture obtained in batch previously reported in the literature.12 Furthermore, the presence of electron-withdrawing functional group (Cl, OAc) in the alkyl terminal alkynes (2i and 2j) was also compatible furnished the corresponding products with lower yields (entries 8 and 9); these groups could be used for further functionalization.
Table 2 Reaction of phenylacetyl chloride with various alkynes under continuous flow conditions
In order to enlarge the substrate scope in the β-naphthol library, the flow synthesis was carried out by modifying the arylacetyl chlorides and alkynes (Table 3). 4-Methylphenylacetyl chloride (1b) was examined in the reaction of diphenylacetylene and 1-decyne, provided the β-naphthols in moderate yields (entries 1 and 2, 73% and 68%). The 2-methylphenylacetyl chloride (1c) and 4-tert-butyl phenylacetyl chloride (1d) were also well-tolerated in the reaction of 1-decyne; the corresponding products were obtained with good yields (entries 3 and 4, 74% and 78%). Interestingly, the reaction of electron-rich 4-hydroxyphenylacetyl chloride (1e) with diphenylacetylene and 1-decyne both resulted in the formation of spiro adducts instead of β-naphthol (entries 5 and 6). Similarly, 4-methoxyphenylacetyl chloride (1f) was reacted with diphenylacetylene and 1-decyne, affording spirofused triene dione (4e and 4f) as the primary product (63% and 75%); however, a small amount of β-naphthol (4g and 4h) were still generated (entries 7 and 8). In addition, 3-methoxyphenylacetyl chloride (1g) was smoothly transformed into β-naphthols through the reaction with diphenylacetylene, phenylacetylene, and 1-decyne; the yields ranged from 64–72% (entries 9–11). The evaluation of the electron-deficient phenylacetyl chloride derivative demonstrated that it has lower reactivity; the reaction of 4-chlorophenylacetyl chloride (1h) with diphenylacetylene and 1-decyne led to moderate yields of products (entries 12 and 13) while worse results were observed with 3,4-dichlorophenylacetyl chloride (1i), furnished the desired products in poor yields (entries 14 and 15). Finally, using 1-naphthalacetyl chloride (1j) resulted in the formation of cyclobutanaphthalenone with 91% yield (entry 16), which was presumably due to poor electrophilicity of 1j, the β-chlorovinyl ketone intermediate could not be obtained, the own Friedel–Crafts acylation reaction was performed instead.
Table 3 Reaction of various arylacetyl chlorides with alkynes under continuous flow conditions
To evaluate the scalability of the continuous flow procedure we developed in the synthesis of β-naphthol, a scale-up preparation of 3g was performed in a coil reactor with an enlarged internal volume of 11.8 mL (Scheme 2). Thus, utilizing 1a-AlCl3 (0.2 M in CH2Cl2, 1.3 equiv. AlCl3 relative to 1a, 2.4 mL min−1) and 2g (0.2 M in CH2Cl2, 2.0 mL min−1), with a residence time of 160 s at 25 °C, 7.05 g of 4-octylnaphthalen-2-ol (3g, 76% yield) was straightforwardly produced after 1.5 h processing time, corresponding to a throughput of 4.70 g h−1. The yield was similar to the previous small reaction, suggesting that the reaction conditions used to synthesize small-scale products could be transferred to a larger scale without further optimization. Additionally, the synthetically important chiral BINOL derivatives could be obtained using the method reported in the literature.3e
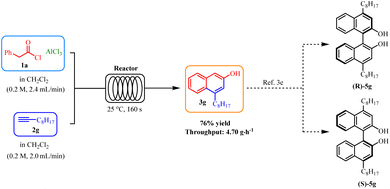 |
| Scheme 2 Scale-up preparation of β-naphthol under continuous flow conditions and the synthesis approach to BINOL derivatives. | |
Conclusions
In summary, a β-naphthol library has been prepared through a continuous flow protocol based on tandem Friedel–Crafts reaction and using readily available arylacetyl chloride and alkynes. A broad range of functionalized β-naphthols could be obtained within 160 s in generally high yields (up to 83%). Interestingly, using electron-rich (4-OH- or 4-MeO-) substituted phenylacetyl chloride afforded spirofused triene dione as the primary product. Furthermore, a scale-up preparation of 3g proceeded stably with a throughput of 4.70 g h−1, demonstrating reliable and efficient scale-up performance. Featuring mild reaction conditions, short reaction time, and broad substrate scope, the flow procedure furnished a rapid and scalable approach to acquire β-naphthols, the essential synthetic precursor preparing chiral binaphthyl ligands. The following work about asymmetric catalysis will be reported in due course.
Conflicts of interest
There are no conflicts to declare.
Acknowledgements
This work was partially supported by the Scientific Research Foundation of Heze University (XY23BS46) and Natural Science Foundation of Shandong Province (ZR2020QB180).
Notes and references
-
(a) S. Zhang, Q. Yang, L. Guo, Y. Zhang, L. Feng, L. Zhou, S. Yang, Q. Yao, G. Pescitelli and Z. Xie, Chem. Commun., 2017, 53, 10066–10069 RSC;
(b) L. Guo, L. Zhang, Q. Yang, B. Xu, X. Fu, M. Liu, Z. Li, S. Zhang and Z. Xie, Front. Chem., 2020, 8, 586 CrossRef CAS PubMed;
(c) C.-J. Zheng, B.-K. Huang, T. Han, Q.-Y. Zhang, H. Zhang, K. Rahman and L.-P. Qin, J. Nat. Prod., 2009, 72, 1627–1630 CrossRef CAS PubMed;
(d) Z.-H. Lou, H.-M. Li, L.-H. Gao and R.-T. Li, J. Asian Nat. Prod. Res., 2014, 16, 963–969 CrossRef CAS PubMed.
-
(a) İ. M. Han and G. Ş. Küçükgüzel, Mini-Rev. Med. Chem., 2020, 20, 1300–1310 CrossRef PubMed;
(b) M.-W. Ha and S.-M. Paek, Molecules, 2021, 26, 4792 CrossRef CAS PubMed;
(c) G. Sakoulas, C. Y. Okumura, W. Thienphrapa, J. Olson, P. Nonejuie, Q. Dam, A. Dhand, J. Pogliano, M. R. Yeaman, M. E. Hensler, A. S. Bayer and V. Nizet, J. Mol. Med., 2014, 92, 139–149 CrossRef CAS PubMed;
(d) C. A. King, K. M. Babcock, R. J. Godios and B. S. King, Ther. Adv. Drug Saf., 2018, 9, 667–671 CrossRef CAS PubMed.
-
(a) J. M. Brunel, Chem. Rev., 2005, 105, 857–898 CrossRef CAS PubMed;
(b) H. Egami and T. Katsuki, J. Am. Chem. Soc., 2009, 131, 6082–6083 CrossRef CAS PubMed;
(c) J. Wencel-Delord, A. Panossian, F. R. Leroux and F. Colobert, Chem. Soc. Rev., 2015, 44, 3418–3430 RSC;
(d) J.-D. Chen, L. Fang and C.-F. Chen, Mini-Rev. Org. Chem., 2015, 12, 310–327 CrossRef CAS;
(e) H. Y. Kim, S. Takizawa, H. Sasai and K. Oh, Org. Lett., 2017, 19, 3867–3870 CrossRef CAS PubMed.
-
(a) M. Berthod, G. Mignani, G. Woodward and M. Lemaire, Chem. Rev., 2005, 105, 1801–1836 CrossRef CAS PubMed;
(b) M. M. Pereira, M. J. F. Calvete, R. M. B. Carrilho and A. R. Abreu, Chem. Soc. Rev., 2013, 42, 6990–7027 RSC;
(c) A. L. Clevenger, R. M. Stolley, J. Aderibigbe and J. Louie, Chem. Rev., 2020, 120, 6124–6196 CrossRef CAS PubMed.
-
(a) D. Parmar, E. Sugiono, S. Raja and M. Rueping, Chem. Rev., 2014, 114, 9047–9153 CrossRef CAS PubMed;
(b) Y.-B. Wang and B. Tan, Acc. Chem. Res., 2018, 51, 534–547 CrossRef CAS PubMed;
(c) Á. M. Pálvölgyi, F. Scharinger, M. Schnürch and K. Bica-Schröder, Eur. J. Org Chem., 2021, 2021, 5367–5381 CrossRef PubMed.
-
(a) M. C. Kozlowski, B. J. Morgan and E. C. Linton, Chem. Soc. Rev., 2009, 38, 3193–3207 RSC;
(b) N. Battini, S. Battula, R. R. Kumar and Q. N. Ahmed, Org. Lett., 2015, 17, 2992–2995 CrossRef CAS PubMed;
(c) A. Jacob, T. Roy, T. Kaicharla and A. T. Biju, J. Org. Chem., 2017, 82, 11269–11274 CrossRef CAS PubMed;
(d) J. Sim, H. Jo, M. Viji, M. Choi, J.-A. Jung, H. Lee and J.-K. Jung, Adv. Synth. Catal., 2018, 360, 852–858 CrossRef CAS;
(e) F. Bartoccini, M. Mari, M. Retini, S. Bartolucci and G. Piersanti, J. Org. Chem., 2018, 83, 12275–12283 CrossRef CAS PubMed;
(f) A. Chaudhary, Mol. Diversity, 2021, 25, 1211–1245 CrossRef CAS PubMed.
-
(a) C. A. Mulrooney, X. Li, E. S. DiVirgilio and M. C. Kozlowski, J. Am. Chem. Soc., 2003, 125, 6856–6857 CrossRef CAS PubMed;
(b) H. Juteau, Y. Gareau and H. Lachance, Tetrahedron Lett., 2005, 46, 4547–4549 CrossRef CAS;
(c) X. Zhang, S. Sarkar and R. C. Larock, J. Org. Chem., 2006, 71, 236–243 CrossRef CAS PubMed.
-
(a) M. Shindo, Y. Sato and K. Shishido, J. Org. Chem., 2001, 66, 7818–7824 CrossRef CAS PubMed;
(b) J. P. Deville and V. Behar, Org. Lett., 2002, 4, 1403–1405 CrossRef CAS PubMed;
(c) A. D. Martinez, J. P. Deville, J. L. Stevens and V. Behar, J. Org. Chem., 2004, 69, 991–992 CrossRef CAS PubMed.
-
(a) A. Martínez, M. Fernández, J. C. Estévez, R. J. Estévez and L. Castedo, Tetrahedron, 2005, 61, 485–492 CrossRef;
(b) M. Fernández, Synthesis, 2009, 2009, 3051–3060 CrossRef;
(c) K. Okuma, R. Itoyama, A. Sou, N. Nagahora and K. Shioj, Chem. Commun., 2012, 48, 11145–11147 RSC;
(d) K. Okuma, K. Horigami, N. Nagahora and K. Shioji, Synthesis, 2015, 47, 2937–2944 CrossRef CAS;
(e) J. Santhi and B. Baire, ChemistrySelect, 2017, 2, 4338–4342 CrossRef CAS;
(f) P. Nimnual, K. Norseeda, B. Akkachairin, J. Tummatorn, P. Laohapaisan, N. Supantanapong, P. Chuangsoongnern, C. Thongsornkleeb, S. Sittihan, S. Ruchirawat and W. Rodphon, Asian J. Org. Chem., 2018, 7, 932–945 CrossRef CAS.
-
(a) Y. Terao, T. Satoh, M. Miura and M. Nomura, Tetrahedron, 2000, 56, 1315–1320 CrossRef CAS;
(b) Y. Dai, X. Feng, H. Liu, H. Jiang and M. Bao, J. Org. Chem., 2011, 76, 10068–10077 CrossRef CAS PubMed;
(c) S. Aiken, B. Armitage, C. D. Gabbutt and B. M. Heron, Tetrahedron Lett., 2015, 56, 4840–4842 CrossRef CAS.
-
(a) N. Ji, B. M. Rosen and A. G. Myers, Org. Lett., 2004, 6, 4551–4553 CrossRef CAS PubMed;
(b) H. A. Cooke, J. Zhang, M. A. Griffin, K. Nonaka, S. G. Van Lanen, B. Shen and S. D. Bruner, J. Am. Chem. Soc., 2007, 129, 7728–7729 CrossRef CAS PubMed.
- H. Y. Kim and K. Oh, Org. Lett., 2014, 16, 5934–5936 CrossRef CAS PubMed.
-
(a) D. Dallinger, B. Gutmann and C. O. Kappe, Acc. Chem. Res., 2020, 53, 1330–1341 CrossRef CAS PubMed;
(b) A. Gioiello, A. Piccinno, A. M. Lozza and B. Cerra, J. Med. Chem., 2020, 63, 6624–6647 CrossRef CAS PubMed;
(c) J. Jiao, W. Nie, T. Yu, F. Yang, Q. Zhang, F. Aihemaiti, T. Yang, X. Liu, J. Wang and P. Li, Chem. - Eur. J., 2021, 27, 4817–4838 CrossRef CAS PubMed;
(d) A. Domokos, B. Nagy, B. Szilágyi, G. Marosi and Z. K. Nagy, Org. Process Res. Dev., 2021, 25, 721–739 CrossRef CAS;
(e) X. Xie, S. Xie, H. Yao, X. Ye, Z. Yu and W. Su, React. Chem. Eng., 2019, 4, 927–931 RSC;
(f) C. Schotten, L. G. T. Leist, A. L. Semrau and D. L. Browne, React. Chem. Eng., 2018, 3, 210–215 RSC.
-
(a) M. Baumann, T. S. Moody, M. Smyth and S. Wharry, Eur. J. Org Chem., 2020, 2020, 7398–7406 CrossRef CAS;
(b) M. Baumann, Org. Biomol. Chem., 2018, 16, 5946–5954 RSC;
(c) W. C. Fu, P. M. MacQueen and T. F. Jamison, Chem. Soc. Rev., 2021, 50, 7378–7394 RSC;
(d) F. M. Akwi and P. Watts, Chem. Commun., 2018, 54, 13894–13928 RSC;
(e) J. Chen, X. Xie, J. Liu, Z. Yu and W. Su, React. Chem. Eng., 2022, 7, 1247–1275 RSC;
(f) C. R. Sagandira, S. Nqeketo, K. Mhlana, T. Sonti, S. Gaqa and P. Watts, React. Chem. Eng., 2022, 7, 214–244 RSC.
-
(a) B. Gutmann, D. Cantillo and C. O. Kappe, Angew. Chem., Int. Ed., 2015, 54, 6688–6728 CrossRef CAS PubMed;
(b) M. Movsisyan, E. I. P. Delbeke, J. K. E. T. Berton, C. Battilocchio, S. V. Ley and C. V. Stevens, Chem. Soc. Rev., 2016, 45, 4892–4928 RSC;
(c) M. Guidi, P. H. Seeberger and K. Gilmore, Chem. Soc. Rev., 2020, 49, 8910–8932 RSC;
(d) A. Bonner, A. Loftus, A. C. Padgham and M. Baumann, Org. Biomol. Chem., 2021, 19, 7737–7753 RSC.
-
(a) M. B. Plutschack, B. Pieber, K. Gilmore and P. H. Seeberger, Chem. Rev., 2017, 117, 11796–11893 CrossRef CAS PubMed;
(b) M. Berton, J. M. de Souza, I. Abdiaj, D. T. McQuade and D. R. Snead, J. Flow Chem., 2020, 10, 73–92 CrossRef;
(c) R. Galaverna, T. McBride, J. C. Pastre and D. L. Browne, React. Chem. Eng., 2019, 4, 1559–1564 RSC;
(d) M. Guidi, S. Moon, L. Anghileri, D. Cambié, P. H. Seeberger and K. Gilmore, React. Chem. Eng., 2021, 6, 220–224 RSC.
-
(a) W. Li, S. Yang, X. Guo, G. He and H. Jin, Chin. J. Chem. Eng., 2018, 26, 1307–1311 CrossRef CAS;
(b) H. Koo, H. Y. Kim and K. Oh, Org. Lett., 2019, 21, 10063–10068 CrossRef CAS PubMed;
(c) H. Koo, H. Y. Kim and K. Oh, Org. Chem. Front., 2019, 6, 1868–1872 RSC;
(d) J. Szeto, V.-A. Vu, J. P. Malerich and N. Collins, J. Flow Chem., 2019, 9, 35–42 CrossRef CAS;
(e) X. Rao, H. Ishitani, W.-J. Yoo and S. Kobayashi, Asian J. Org. Chem., 2019, 8, 316–319 CrossRef CAS;
(f) V. R. L. J. Bloemendal, B. Spierenburg, T. J. Boltje, J. C. M. van Hest and F. P. J. T. Rutjes, J. Flow Chem., 2021, 11, 99–105 CrossRef CAS;
(g) R. Mougeot, P. Jubault, J. Legros and T. Poisson, Molecules, 2021, 26, 7183 CrossRef CAS PubMed;
(h) D. R. Snead and T. F. Jamison, Angew. Chem., Int. Ed., 2015, 54, 983–987 CrossRef CAS PubMed.
|
This journal is © The Royal Society of Chemistry 2024 |
Click here to see how this site uses Cookies. View our privacy policy here.