DOI:
10.1039/D3RA07358K
(Paper)
RSC Adv., 2024,
14, 3085-3095
A photothermal MoS2 decorated biomass carbon-based aerogel with a directionally aligned porous structure for mitigating heavy metal stress under seawater acidification
Received
29th October 2023
, Accepted 4th January 2024
First published on 18th January 2024
Abstract
Marine animals and human are threatened by seawater acidification and metal contamination. Especially, the toxicity of copper (Cu) is expected to be boosted with seawater acidification. However, studies on the removal of Cu under seawater acidification are limited for practical applications, owing to obstacles such as instability, secondary contamination, and low adsorption efficiency. In this work, coconut shells were utilized for the synthesis of biomass carbon, which was then decorated with MoS2. A novel porous MoS2/carbon-based aerogel (MCA) with the synergistic effect of photothermal conversion and adsorption was constructed via directional freeze-drying technology. The adsorption properties of MCA were a precise match with Freundlich isotherm and pseudo-second-order kinetic models with a high correlation coefficient (R2) of more than 0.995. Under solar illumination, the surface temperature of MCA reached up to 36.3 °C and the adsorption capacity of MCA increased to 833.8 mg g−1, indicating that the remarkable thermal properties of MCA contributed to achieving high adsorption capacity. The adsorption mechanisms of MCA involved in the removal of Cu(II) ions were dominated by chemisorption rather than surface physical adsorption. Owing to its outstanding photothermal conversion performance and directionally aligned porous structure, MCA was able to remove Cu(II) species from seawater, and the adsorption ability of MCA reached 247.1 mg g−1 after ten adsorption cycles. MCA exhibited excellent stability to resist the complex natural environment and was easy to reuse. Overall, MCA with a series of merits, including high adsorption efficiency, excellent photothermal conversion property, and outstanding cycling stability, was confirmed to contribute to addressing heavy metal stress under seawater acidification.
1. Introduction
Seawater is composed of more than 15% global species, and it is one of the vast ecosystems on the earth.1,2 Owing to the anthropogenic emissions of CO2, the adsorption of atmospheric CO2 results in a decrease in the pH of seawater (a phenomenon termed as ocean acidification or seawater acidification).3,4 Seawater acidification is capable of seriously affecting biological and physiological properties, such as energy metabolism, nutrient digestion, and immune responses.5–7 More importantly, seawater acidification can lead to the speciation of metals and affect the toxicity of metals.8 For instance, seawater acidification alters the migration and retention of heavy metals and then promotes the accumulation of metals or aggravates the influence of metals on organisms.9 Several studies have indicated that seawater acidification can impact the physiological performance of aquatic species.10,11 Despite an increasing number of studies being reported on seawater acidification, an effective method to solve the problem of heavy metal stress under seawater acidification is still needed.
Of the common heavy metals, copper (Cu) is mainly dominated by carbonate species, including CuCO3 and Cu(CO3)22−, in seawater.12,13 However, a decreased pH originating from seawater acidification will greatly increase the speciation of dissolved Cu and subsequently improve the toxicity of Cu towards marine organisms.14 In addition, high Cu content in aquatic products will cause excessive Cu accumulation in the human body, which can contribute to methemoglobinemia, hemolytic anemia, or internal organ damage.15 Particularly, the World Health Organization (WHO) has set the maximum acceptable limit of Cu(II) ion concentration in drinking water at 1.5 mg L−1.16 Generally, ion exchange, adsorption, and electrochemical methods are applied for disposing heavy metal ions.17–19 In this view, as an eco-friendly and cost-efficient technology, adsorption technology has been widely utilized for the removal of Cu metal.20,21 As an illustration, Zhao et al. devised poly(butylene adipate-co-terephthalate) (PBAT) microplastics for the adsorption of Cu(II), and the maximum adsorption quantity was 140.547 μg g−1.22 Truong et al. prepared iron oxide particles doped with biochar (Fe-BAB) and employing Sargassum hemiphyllum as a carbon source. Fe-BAB demonstrated a superior adsorption performance of Cu(II) ions of 105.3 mg g−1, compared with other biochars.23 Most of these adsorbents suffer from plenty of shortcomings, involving low renewability, secondary pollution, and poor adsorption efficiency. More importantly, these adsorbents are only treated with heavy metal ions in a single solution. In contrast, aerogels possess a controlled pore structure and high surface area, which offers sufficient adsorption sites for metal ions.24 In addition, aerogels are easy to separate and recycle, which has the potential for practical applications in the complex marine environment.
Here, a novel photothermal-assisted aerogel with both a photothermal effect and excellent adsorption capacity was devised for the treatment of Cu heavy metal ions under seawater acidification. Specifically, the biomass carbon was decorated by MoS2, and the MoS2/C-based aerogel was constructed by directional freeze-drying technology. The MoS2/C-based aerogel was then investigated for the removal of Cu(II) ions from the marine environment together with the illustration of the interrelated removal mechanisms. Furthermore, the main points were the influence of the photothermal effect on the removal of Cu(II) ions. The kinetics and isotherms of the adsorption process of Cu(II) ions on MCA were studied, and the effects of pH on the adsorption of Cu(II) ions for MCA were also explored. Recyclability tests of the MCA in actual seawater were carried out to assess the feasibility of real-world applications. Structural changes on MCA during the adsorption process were demonstrated to propose the adsorption mechanisms of the Cu(II) ions by MCA (Fig. 1).
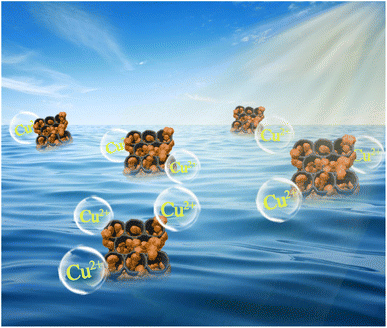 |
| Fig. 1 Fully developed MoS2/C-based aerogel for the application of Cu(II) heavy metal ion removal under seawater acidification. | |
2. Experimental section
2.1 Materials
Ammonium molybdate tetrahydrate ((NH4)6Mo7O24·4H2O), ethanol, thiourea (CS(NH2)2), chitosan, and acetic acid were purchased from Macklin Biochemical Co., Ltd (Shanghai, China). The coconut shell was purchased from a local market. All materials in this work were used directly without any purification.
2.2 Synthesis of coconut shell-based biomass carbon
The coconut shell-based biomass carbon was prepared using a facile inert calcination method according to the literature, and the typical process was as follows.25,26 Approximately, 1.000 g of coconut shell was soaked in 6 wt% NaOH solution, after stirring for 12 h at room temperature, it was repeatedly washed using distilled water to a pH of 7. The as-prepared coconut fiber was immersed in the NaOH/H2O2 mixture for bleaching, and heated to 80 °C for 30 min. After the completion of the reaction, the solution was cooled and the coconut fiber was washed repeatedly with distilled water. The products were then dried at 60 °C for 12 h. Finally, the coconut fiber was carbonized at 700 °C for 2 h in an Ar atmosphere, and the coconut fiber-based biomass carbon was obtained.
2.3 Synthesis of MoS2/C-based aerogel (MCA)
MoS2/C composites were fabricated using a one-step hydrothermal process.27,28 Specifically, 2.4718 g of ((NH4)6Mo7O24·4H2O), 2.1316 g of CS(NH2)2, and 0.0800 g of coconut fiber-based biomass carbon were dissolved in an 80 mL of deionized water and stirred for 30 min. The precursor solution was transferred into a 100 mL autoclave, and heated at 200 °C for 18 h. The resulting precipitate was centrifuged and washed three times using deionized water and ethanol. Then, the product was dried in an oven at 60 °C overnight. The MCA was obtained by directional freeze-drying technology. The chitosan was dissolved in an aqueous acetic acid solution, and heated at 80 °C to form a uniform solution. MCA were added into the above chitosan solution, and mechanically stirred for 1 h. Then, the aqueous dispersion was placed in a cylindrical mold, and liquid nitrogen was added for pre-cooling. The mold was transferred to a vacuum freeze dryer at −60 °C for 48 h, and then the directional MCA was obtained. For comparison, the biomass carbon-based aerogel (CA) was also prepared by the same methodology.
2.4 Characterization
X-ray diffraction (XRD) patterns obtained on a Bruker Advance D8 diffractometer by Cu Kα radiation at 40 kV and 200 mA were utilized to investigate the crystal structure. The microscopic morphology of samples was examined by field-emission scanning electron microscopy (FESEM, JSM7100F, Japan). The microstructure of the samples was studied using a field emission transmission electron microscope (FETEM, JEM-2100F, Japan), coupled with an energy dispersive X-ray spectrometer (EDX) to study the elemental distribution. X-ray photoelectron spectroscopy (XPS, ESCALAB 250Xi, ThermoFisher Scientific, America) was performed to validate the surface elements of samples. A universal testing machine (CLY2768TM-10, USA) was used to test the mechanical strength of the sample. The thermal conductivity (λ) of the sample was obtained using the following formula: |
 | (1) |
where q is the heat flux, dT is the temperature difference, and dx refers to the distance difference.
The thermal resistance (R) was calculated using the equation:
|
 | (2) |
where
λ is the thermal conductivity of the MCA, and
d is the thickness.
2.5 Adsorption experiment
A series of Cu(II) (Cu2+) solutions at different concentrations ranging from 5 to 200 mg L−1 were used to explore the adsorption effect of MCA and biomass carbon-based aerogel on Cu2+. The effects of pH (1, 2, 3, 4, 5, and 6) and time (10, 20, 30, 50, 60, 120, and 150 min) on the adsorption of Cu2+ by MCA and CA were also explored. All adsorption experiments were carried out in a constant temperature incubator shaker at 25 °C for 12 h. The supernatant was obtained using a needle-type water filter, and the Cu2+ concentrations were measured using a copper low-range portable photometer (HI96747, resolution of 0.001 mg L−1, Hanna Instruments). The adsorption isotherm experiments were conducted on MCA to further explore the adsorption mechanism.
The adsorption capacities (qe) of Cu2+ on MAC and CA were calculated using the following formula:29
|
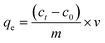 | (3) |
where
ct (mg L
−1) is the final concentration of Cu
2+,
c0 (mg L
−1) is the initial concentration of Cu
2+,
m (g) is the mass of the adsorbent, and
v (mL) is the volume of the solution.
2.6 Adsorption isotherms and kinetics
For the adsorption isotherm experiments, 0.0200 g MAC and CA were immersed in 100 mL of Cu(II) solution at different initial concentrations, and shaken at 180 rpm in the dark at 25 °C, 35 °C, and 45 °C for 12 h, respectively. The obtained data was assessed using the Langmuir and Freundlich isotherm models:30,31 |
 | (4) |
|
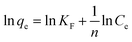 | (5) |
where qe (mg g−1) is the equilibrium adsorption ability; qm (mg g−1) represents the maximum adsorption capacity of the adsorbents at the monolayer; KF (L mg−1) and KL are the equilibrium constants of the Langmuir and Freundlich isotherm models, respectively; n (mg g−1) is an empirical coefficient for Freundlich isotherm models in connection with the adsorption capacity.
Adsorption kinetic experiments of MAC and CA at different adsorption times were conducted to give valuable evidence for the reaction pathways and the possible adsorption mechanisms. The adsorption experiments were performed at 25 °C with a pH of 6.0, and the data was described using the pseudo-first-order and pseudo-second-order models. The calculation formulas of the model are as follows:32,33
|
ln qe − ln qt = ln qe − k1t
| (6) |
|
 | (7) |
where
k1 (min
−1) and
k2 (g mg
−1 min
−1) are the rate constants of the pseudo-first-order and pseudo-second-order models, respectively;
qt (mg g
−1) is the adsorption capacity of the absorbents at different times.
2.7 Photothermal conversion properties
A solar simulator (CEL-S500, Zhongjiaojinyuan, Beijing) equipped with an optical filter for the standard AM 1.5G spectrum was used as a solar source. The samples were illuminated under one sun intensity (1 kW m−2). The temperature of the samples was tested using an IR camera (FLIR E4 Pro, America) and K-type thermocouples.
3. Results and discussion
The schematic of the fabrication of MoS2/C composites is presented in Fig. 2a. The coconut shell-based biomass carbon was employed as the substrate for the growth of MoS2, and the MoS2 nanoflower grew on the surface of the coconut shell-based fiber via a facile hydrothermal reaction. As depicted in Fig. 2b, the FESEM image for the coconut shell-based fiber presented a general view and indicated that the fiber exhibited a porous hollow-tube structure with smooth walls. The unique structure of the coconut shell-based fiber not only was beneficial to MoS2 nanosheets via in situ fabrication, but also could facilitate mass transfer and ion adsorption. Compared with the carbon fiber, the MoS2/C composites showed flower-like coating layers, which were generated by the self-assembly of MoS2 nanosheets (Fig. 2c and d). The elemental distribution of MoS2/C composites, shown in Fig. 2e, suggested the uniform distribution of Mo, S, and C elements. In addition, the high-resolution transmission electron microscopy (HRTEM) images of the MoS2/C composites, shown in Fig. 3a and b, illustrated that the MoS2 nanoflower was clearly observed on the surface. The interlayer spacing was 0.64 nm, corresponding to the (002) crystal plane of MoS2, which was larger than the standard lattice value of MoS2 (0.615 nm) reported in the previous literature.34,35
 |
| Fig. 2 (a) Schematic illustration for preparing MoS2/C composites for Cu(II) ion removal; SEM images of (b) coconut shell-based biomass carbon and (c) and (d) MoS2/C composites; (e) elemental mapping images of Mo, S, and C in MoS2/C composites. | |
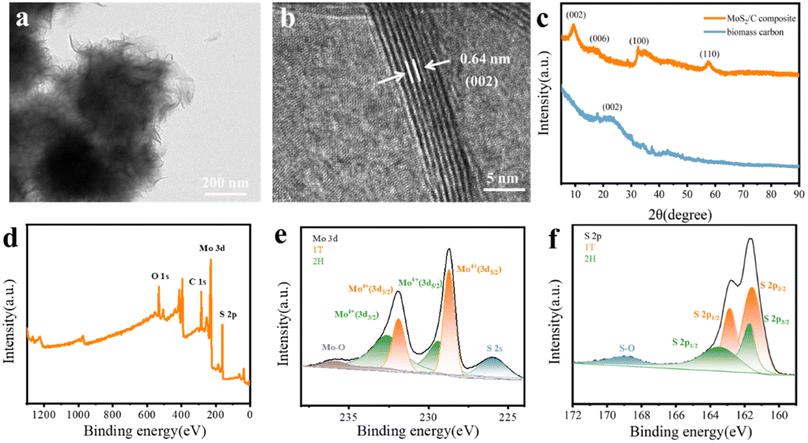 |
| Fig. 3 (a) and (b) TEM and HRTEM images of MoS2/C composites; (c) XRD patterns of the coconut shell-based biomass carbon and MoS2/C composites; (d) survey XPS spectrum of MoS2/C composites; (e) Mo 3d, and (f) S 2p XPS spectra of MoS2/C composites. | |
The crystal structure and phase composition of the coconut fiber-based biomass carbon and MoS2/C composites were characterized by X-ray diffraction (XRD), as depicted in Fig. 3c. The as-prepared coconut fiber-based biomass carbon possessed a distinct carbon-specific peak at 23.4°, manifesting the (002) plane of the graphite-like structure.36 The characteristic peaks of MoS2/C composites at 9.4°, 15.3°, 32.5°, and 57.5° were assigned to (002), (006), (100), and (110) planes, respectively.37 The diffraction peak of (002) of MoS2/C composites shifted to a lower scattering angle of 9.4°, which was ascribed to 1T-MoS2.38 The characteristic peak at (002) of the MoS2/C composites was very sharp, MoS2 possessed an excellent crystallinity, as previously proved by a similar result of HRTEM. The phase conversion was ascribed to the insertion of NH4+ and CO2. The insertion extended the interlayer distance, resulting in a distortion in the 2H phase structure.39 X-ray photoelectron spectroscopy (XPS) was conducted for the investigation of the chemical state of elements of MoS2/C composites. The survey XPS spectrum of MoS2/C composites showed Mo, S, C, N, and O elements, suggesting the existence of biomass and MoS2 (Fig. 3d). The high-resolution of XPS spectrum of Mo 3d demonstrated the existence of hybridized 1T/2H phases in the MoS2/C composites (Fig. 3e). The couple prevalent peaks at 228.7 and 231.9 eV were attributed to Mo 3d5/2 and Mo 3d3/2, respectively, of the 1T phase MoS2.40 While the other two doublets centered at 229.4 eV and 232.6 eV were assigned to the 2H phase.41 The concentration of the 1T phase was calculated to be approximately 60.1%. For the S 2p high-resolution spectrum, the pair of the strong peaks located at 161.5 and 162.8 eV corresponded to S 2p3/2 and S 2p1/2 of the 1T phase MoS2 in MoS2/C composites.42 Simultaneously, the two peaks at 161.7 and 163.4 eV are attributed to S 2p3/2 and S 2p1/2, respectively, of the 2H phase (Fig. 3f). In addition, the C 1s spectrum in Fig. 4a was deconvoluted into two peaks at 284.6, and 285.4 eV, indicating the existence of C–C bond, and C–O bond, respectively.43 The O 1s spectrum is presented in Fig. 4b; the peaks at 530.5, 531.7, and 533.5 eV belong to C
O, C–O–Mo and C–OH bonds, respectively.44 The XPS spectrum of N 1s displayed four peaks, as shown in Fig. 4c, and are assigned to the Mo–N bond, pyridinic N, pyrrolic N, and graphitic N, respectively.45
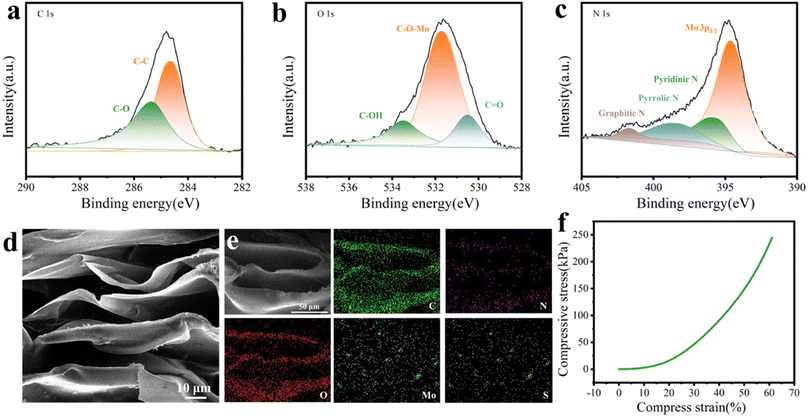 |
| Fig. 4 (a) C 1s, (b) O 1s, and (c) N 1s XPS spectra of MoS2/C composites; (d) SEM images of MCA showing a vertical channel structure; (e) EDS mappings images of Mo, S, C, N, and O elements in MCA; (f) strain–stress curve of the compressive test of MCA. | |
The porous structure of the aerogels has a direct impact on controlling the flow of water and the exposure of active sites, and the aerogel that MCA was conducted by MoS2/C composites and chitosan. The microstructure and morphologies of the MCA were studied by FESEM, as shown in Fig. 4d. MCA presented a three-dimensional and vertically aligned structure, which was similar to the CA without the addition of MoS2/C composites. The vertically aligned porous structure was likely to have more ice-ordered growth during the freezing process.46 Moreover, the average width of the vertically aligned pores was about 15 μm, and the average wall thickness was 2 μm. As shown in Fig. 4e, Mo, S, C, N, and O elements were evenly distributed on the entire MCA, demonstrating the co-existence of all components in the MCA aerogel network. The mechanical strength of the MCA was measured, and the stress test data of MCA from 0 to 60% strain is shown in Fig. 4f. The three deformation regions included a relative flat elastic deformation at the initial stage, fast deformation, and the final completely buckling stage. The compressive strength of MCA was as high as 244.5 MPa at 60% compressive strain, indicating that MCA exhibited excellent remarkable mechanical stability.
The different initial concentrations (5, 10, 20, 50, 100, 150, and 200 mg L−1) of Cu(II) solution were selected to explore the effect of temperature on the adsorption behavior. The isotherm curves are demonstrated in Fig. 5a–d, and the relevant isotherm parameters originating from the Langmuir and Freundlich isotherm models as well as determination coefficients (R2) are listed in Table 1. Compared with the Langmuir model, the Freundlich model was able to express the adsorption process of the MCA and CA for Cu(II) ions with relatively higher R2 values. Cu(II) ion adsorption on MCA and CA followed the form of a multilayer occurring on the surface of the MoS2/C composites and biomass carbon with active adsorption sites by chemical processes through the sharing or exchange of electrons.47 The maximum adsorption capacities of MCA and CA for Cu(II) ions from the Langmuir isotherm models were 947.5 and 937.3 mg g−1 at 45 °C, respectively. More importantly, the adsorption ability of MCA for Cu(II) ions was higher than that for other adsorbents reported in the literature, as displayed in Table 2.48–53
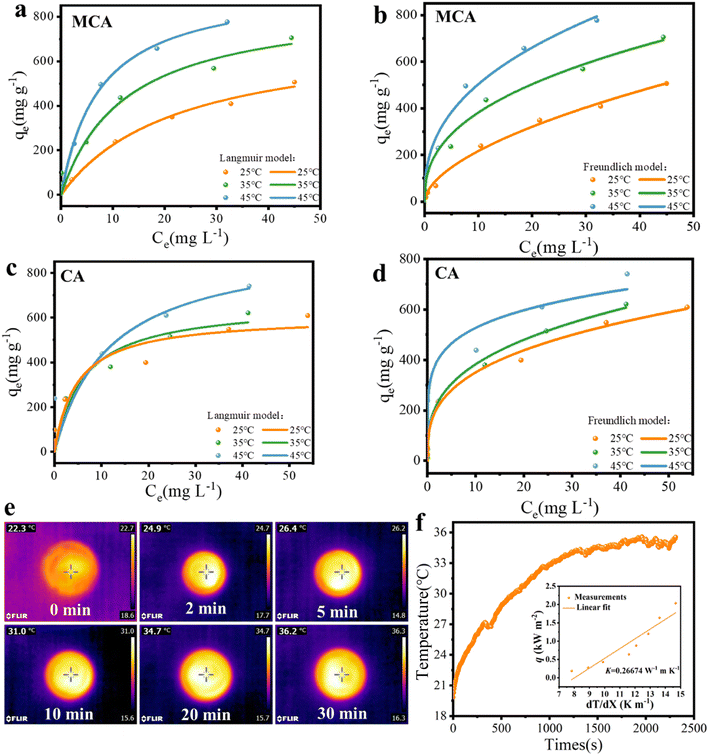 |
| Fig. 5 (a)–(d) Adsorption isotherms of MCA and CA for Cu(II) removal at different temperatures; (e) and (f) temporal changes in the surface temperature of MCA under solar illumination and the inset image showing the thermal conductivity of MCA. | |
Table 1 Isotherm parameters for the adsorption of Cu(II) ions by MCA and CA at different temperatures
Adsorbent |
Temperature (°C) |
Langmuir model |
Freundlich model |
qmax/(mg g−1) |
n |
R2 |
Kf/(L mg−1) |
n |
R2 |
MCA |
25 |
729.98048 |
0.04441 |
0.9928 |
59.11562 |
1.77057 |
0.9946 |
35 |
867.42244 |
0.08068 |
0.96715 |
152.32472 |
2.50563 |
0.98409 |
45 |
947.47883 |
0.13427 |
0.97898 |
204.39097 |
2.55382 |
0.98057 |
CA |
25 |
606.04337 |
0.21098 |
0.92925 |
166.82647 |
3.10254 |
0.95939 |
35 |
665.11685 |
0.16196 |
0.94467 |
180.7074 |
3.06755 |
0.99361 |
45 |
937.30764 |
0.08512 |
0.86124 |
348.41519 |
5.56313 |
0.94638 |
Table 2 The theoretical maximum adsorption capacity of various adsorbents for Cu(II) ions
Adsorbent |
qmax/(mg g−1) |
Temperature (°C) |
References |
Fe3O4@carbon@Z1F-8 |
226.24 |
25 |
48 |
MCs@Mg/Fe-LDHs |
338.98 |
60 |
49 |
E-CS aerogel |
108.14 |
25 |
50 |
Magnetic biosorbent |
90.00 |
— |
51 |
Enhanced nano-hydroxyapatite |
272.00 |
25 |
52 |
C-Phenylcalix[4]pyrogallolarene |
8.14 |
25 |
53 |
MCA |
730.1 |
25 |
This work |
Moreover, the adsorption capacities of MCA and CA were higher at higher temperatures, implying the increasing temperature of the adsorption process seemed to be beneficial for adsorptive abilities. One benefit of choosing MCA was its outstanding photothermal conversion ability, which was conducive to promoting the adsorption of Cu(II) ions. MCA was added to a Cu(II) ions solution with different concentrations to investigate the photothermal heating effect. The photothermal conversion performance was directly related to the local temperature, the surface temperature of a Cu(II) ion solution (50 mg L−1) under one sun illumination was tested. As presented in Fig. 5e and f, the temperature of the Cu(II) ion solution increased only slightly, and MCA was more responsive to temperature. The surface temperature of the MCA rose from 22.7 °C to 36.3 °C. The temperature change curve indicated that the MCA exhibited excellent photothermal effects, the MCA was able to convert the solar energy into thermal energy more quickly and efficiently. Furthermore, the thermal resistance (R) of the MCA was also explored. The thermal conductivity of MCA was operated at 0.26674 W m−1 K−1 as displayed in the inset image. MCA possessed a low thermal resistance of 299.9 cm2 K W−1, which was conducive to preventing the thermal energy from dissipating. Under solar illumination, the increased solution temperatures resulted in faster diffusion rates of Cu(II) ions and more Cu(II) ions were able to contact the MCA, which benefited the adsorption rates. The adsorption capacity of MCA increased to 833.8 mg g−1, while that of the CA was 731.6 mg g−1, under solar illumination (Fig. 6a and b). Therefore, the remarkable thermal properties of MCA were also very significant for achieving high adsorption capacity.
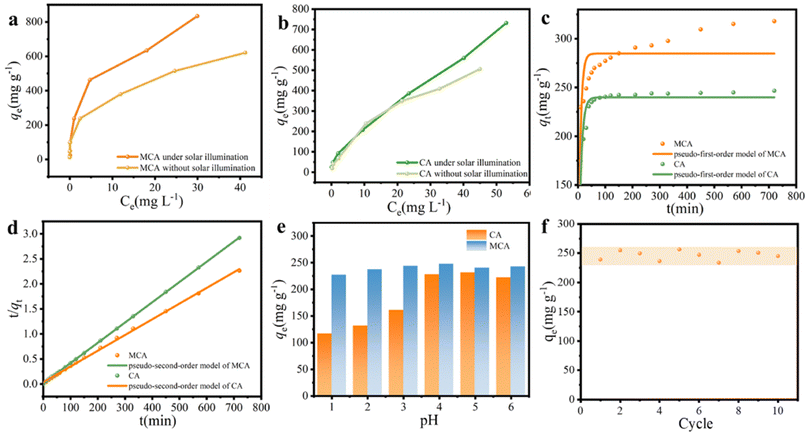 |
| Fig. 6 (a) and (b) The influence of the photothermal effect on the adsorption capacity of MCA and CA; (c) and (d) adsorption kinetic curves of MCA and CA; (e) the effect of pH at 1.0–6.0 on the adsorption capacity of MCA and CA; (f) reusability experiments of MCA for the adsorption of Cu(II) ions in seawater with an initial pH of 4. | |
The adsorption rate and the dominant factors of Cu(II) ions on MCA and CA were investigated using adsorption kinetics. In general, Cu(II) ions absorbed by MCA and CA were fast at the initial stage and subsequently became slow. As shown in Fig. 6c and d, the rapid uptake stage of an amount of Cu(II) ions was at the first 50 min, after which the adsorption rate showed a declining trend. With time, the adsorption capacity reached the equilibrium, owing to the decrease of available active adsorption sites. Thus, pseudo-first-order and pseudo-second-order kinetic models were adopted to further probe the adsorption mechanism of the MCA and CA for Cu(II) ions as well as the controlled step of the solid–liquid systems. The calculated kinetic parameters are summarized in Table 3. The R2 values of the pseudo-second-order model for MCA and CA were 0.999, and 0.999, respectively, all of which were slightly greater than the pseudo-first-order model. The pseudo-second-order kinetic model was well-matched with the adsorption behavior of MCA and CA for Cu(II) ions. From this, the rate-limiting step of Cu(II) ions adsorption on MCA and CA was chemical adsorption, which was attributed to complexation and ion exchange interaction.54
Table 3 Kinetic parameters for the adsorption of Cu(II) ions by MCA and CA at 25 °C
Adsorbent |
Pseudo-first-order kinetic model |
Pseudo-second-order kinetic model |
qe/(mg g−1) |
K1/(min−1) |
R2 |
qe/(mg g−1) |
K2/(g mg−1 min−1) |
R2 |
MCA |
284.74627 |
0.12745 |
0.92238 |
318.4713 |
0.00027 |
0.99912 |
CA |
239.8689 |
0.10515 |
0.97955 |
246.9136 |
0.00126 |
0.99995 |
The influence of pH level on the adsorption performance of MCA and CA toward Cu(II) ions was studied to verify the practical application of MCA under the circumstance of seawater acidification. As displayed in Fig. 6e, the adsorption capacity of Cu(II) ions was found to be inferior at pH = 2, which was ascribed to the existence of the high concentration of H+ for competing with the adsorption sites.55 As the pH value rose from 3.0 to 6.0, the Cu(II) adsorption capacity increased slightly, and the maximum Cu(II) adsorption capacity was 247.5 mg g−1 at 25 °C. With the increase of pH, the electrostatic repulsion between Cu(II) ions and the surface charge of MCA decreased, resulting in the few competitive H+ ions.56 Seawater was employed as the water source to investigate the reusability of MCA through consecutive adsorption cycles at pH = 4. As illustrated in Fig. 6f, the adsorption capability of MCA for Cu(II) ions remained at about 247.1 mg g−1 after ten adsorption cycles owing to the functional groups on the surface and the directionally aligned porous structure of MCA for the efficient function of Cu(II) ion adsorption. Overall, the excellent reusability of MCA is potentially attractive for mitigating heavy metal stress under seawater acidification.
To investigate the potential adsorption mechanism of Cu(II) ions by MCA, MCA after adsorption was analyzed by XPS. The survey spectra shown in Fig. 7a exhibited obvious peaks corresponding to C 1s, O 1s, Mo 3d, S 2p, and Cu 2p. The Cu 2p spectrum showed peaks at 932.6 and 952.4 eV, which are the satellite peaks of Cu 2p3/2 and Cu 2p1/2, respectively, confirming the successful adsorption of Cu(II) cations by MCA (Fig. 7b).57 The peaks of S 2p for 1T-MoS2 shifted to higher binding energies at 163.1 and 161.9 eV, suggesting that the S atom was the active adsorption site (Fig. 7c).58 As presented in Fig. 7d, with respect to Mo 3d peaks, two peaks at 228.7 and 231.9 eV belonged to the 1T-MoS2. Simultaneously, 1T-MoS2 possessed high stability under an ambient environment during the hydrothermal treatment, as observed from the XRD results of the MCA after its use for Cu(II) ions adsorption (Fig. 7e). In addition, the surface of MCA presented negative charges in the pH range from 2 to 6, as displayed in Fig. 7f. The enhanced adsorption capability was ascribed to the electrostatic interaction between MCA and Cu(II) ions. More importantly, owing to the metallic phase of 1T-MoS2, electrons were more easily transferred, and 1T-MoS2 had ultrafast adsorption kinetics compared with 2H-MoS2.59 Thus, the mechanism of adsorption toward Cu(II) ions by MCA was mainly attributed to chemisorption.
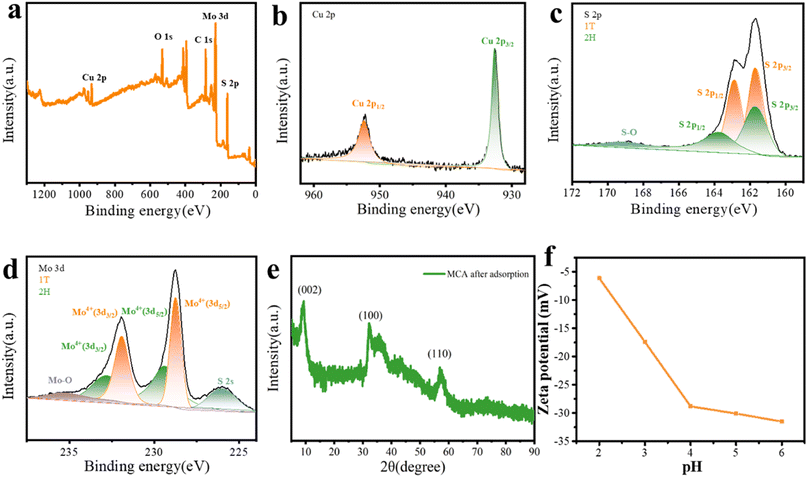 |
| Fig. 7 (a) XPS survey, (b)–(d) high-resolution spectra for Cu 2p, S 2p, and Mo 3d of MCA after the adsorption of Cu(II) ions; (e) XRD pattern of MCA after the adsorption of Cu(II) ions; (f) zeta potential of MCA. | |
4. Conclusions
In summary, the novel MoS2/carbon-based aerogel was synthesized via a directional freeze-drying technology, which was utilized for the removal of Cu(II) ions under seawater acidification. MoS2/carbon-based aerogel exhibited outstanding adsorption performance for Cu(II) ions with the maximum adsorption capacity of 947.5 mg g−1 at 45 °C, as obtained from the Langmuir model. The adsorption process of MoS2/carbon-based aerogel for Cu(II) ions was well described by the pseudo-second-order kinetic model and Freundlich isotherm model with a high correlation coefficient (R2) of more than 0.995. More importantly, the surface temperature of the MCA could reach 36.3 °C under one sun illumination. The best self-heating photothermal effect of MoS2/carbon-based aerogel was able to promote the adsorption performance, and the adsorption capacity of MCA increased to 833.8 mg g−1. The mechanism of sorption was explored, and the Cu(II) ion adsorption of MoS2/carbon-based aerogel was predominantly governed by chemisorption. The ultrafast electron transfer and electrostatic interaction between Cu(II) ions and MCA promoted the adsorption capacity of MCA. In addition, the adsorption performance of MCA was slightly affected by the acidity of the seawater. The adsorption capacity of Cu(II) ions for MoS2/carbon-based aerogel reached 247.1 mg g−1 after ten adsorption cycles under seawater acidification. Therefore, MoS2/carbon-based aerogel as a cost-effective and environmentally friendly adsorbent is expected to be applied for mitigating heavy metal stress under seawater acidification.
Author contributions
Fang Yu: writing-original draft, data curation, formal analysis, funding acquisition; Xiangyu Cheng: methodology, data curation, formal analysis; Juntian Xu: investigation; Qinfang Zhang: writing-review and editing, funding acquisition.
Conflicts of interest
There are no conflicts to declare.
Acknowledgements
The study was financially supported by the National Natural Science Foundation of China (No. 12274361), the Natural Science Foundation of Jiangsu Province (No. BK20211361), the College Natural Science Research Project of Jiangsu Province (No. 20KJA430004), the Natural Science Foundation of Jiangsu Province (No. BX2021054), and the Funding for school-level research projects of Yancheng Institute of Technology (No. xjr2021040 and No. xjr2021058).
References
- S. Sunagawa, S. G. Acinas, P. Bork, C. Bowler, D. Eveillard, G. Gorsky, L. Guidi, D. Iudicone, E. Karsenti, F. Lombard, H. Ogata, S. Pesant, M. B. Sullivan, P. Wincker and C. Vargas, Nat. Rev. Microbiol., 2020, 18, 428–445 CrossRef CAS PubMed.
- S. H. Thangal, M. Nivetha, C. Muttharasi, K. Anandhan and T. Muralisanka, Mar. Pollut. Bull., 2021, 169, 112476 CrossRef CAS PubMed.
- D. Qi, Z. X. Ouyang, L. Q. Chen, Y. X. Wu, R. B. Lei, B. S. Chen, R. A. Feely, L. G. Anderson, W. L. Zhong, H. M. Lin, A. Polukhin, Y. X. Zhang, Y. L. Zhang, H. B. Bi, X. Y. Lin, Y. M. Luo, Y. P. Zhuang, J. F. He, J. F. Chen and W. J. Ca, Science, 2022, 377, 1544–1550 CrossRef CAS PubMed.
- R. Freitasa, L. D. Marchia, M. Bastosa, A. Moreiraa, C. Veleza, S. Chiesaa, F. J. Wronab, E. Figueiraa and A. M. V. M. Soares, Ecol. Indic., 2017, 79, 54–62 CrossRef.
- R. Freitas, L. Marchi, A. Moreira, J. L. T. Pestana, F. J. Wrona, E. Figueira and A. M. V. M. Soares, Sci. Total Environ., 2017, 595, 691–701 CrossRef CAS PubMed.
- S. Nawaz, Y. Khan, S. Khalid, M. A. Malik and M. Siddiq, RSC Adv., 2023, 13, 28785–28797 RSC.
- W. T. Cui, L. Cao, J. H. Liu, Z. H. Ren, B. Zhao and S. Z. Dou, Sci. Total Environ., 2020, 718, 137234 CrossRef CAS PubMed.
- H. Wang, Q. Sui, J. Zhao, X. M. Sun, L. Zhu, B. J. Chen, K. M. Qu and B. Xia, J. Hazard. Mater., 2023, 453, 131361 CrossRef CAS PubMed.
- M. C. Passarelli, I. Riba, A. Cesar, F. Serrano-Bernando and T. A. DelValls, Sci. Total Environ., 2017, 595, 759–768 CrossRef CAS PubMed.
- S. J. Lin, Nat. Commun., 2023, 14, 2699 CrossRef CAS PubMed.
- A. Gallo, M. C. Esposito, A. Cuccaro, M. C. Buia, A. Tarallo, V. Monfrecola, E. Tosti and R. Boni, Environ. Pollut., 2020, 265, 115063 CrossRef CAS PubMed.
- T. Fujii, F. Moynier, M. Abe, K. Nemoto and F. Albarède, Geochim. Cosmochim. Acta, 2013, 110, 29–44 CrossRef CAS.
- K. J. Powell, P. L. Brown, R. H. Byrne, T. Gajda, G. Hefter, S. Sjöberg and H. Wanner, Pure Appl. Chem., 2007, 79, 895–950 CrossRef CAS.
- M. Yabanlı, İ. Şener, A. Yozukmaz, S. Öner and H. H. Yapıcı, Environ. Sci. Pollut. Res., 2021, 28, 53171–53180 CrossRef PubMed.
- J. Zheng, Q. Li and X. D. Zheng, Sci. Total Environ., 2023, 891, 164473 CrossRef CAS PubMed.
- N. Adimalla and H. K. Wang, Arabian J. Geosci., 2018, 11, 684 CrossRef.
- Y. X. Yang, Z. P. Zhong, Ji. F. Li, H. R. Du, Q. Li, X. Zheng, R. Z. Qi, S. Zhang, P. K. Ren and Z. Y. Li, Appl. Energy, 2023, 351, 121829 CrossRef CAS.
- N. A. A. Qasem, R. H. Mohammed and D. U. Lawal, npj Clean Water, 2021, 4, 36 CrossRef CAS.
- M. Zhai, B. Fu, Y. H. Zhai, W. J. Wang, A. Maroney, A. A. Keller, H. T. Wang and J. M. Chovelon, Water Res., 2023, 236, 119924 CrossRef CAS PubMed.
- M. Zheng, F. Ma, M. X. Liu, M. J. Li, Q. J. Yu, H. D. Zhu, H. L. Guo and H. M. Sun, J. Cleaner Prod., 2023, 395, 136387 CrossRef CAS.
- H. Awes, Z. Zaki, S. Abbas, H. Dessoukii, A. Zaher, S. A. A. Moaty, N. Shehata, A. Farghali and R. K. Mahmoud, Environ. Sci. Pollut. Res., 2021, 28, 47651–47667 CrossRef CAS PubMed.
- Y. Sun, B. Y. Peng, Y. Wang, X. J. Wang, S. Q. Xia and J. F. Zhao, Chem. Eng. J., 2023, 464, 142714 CrossRef CAS.
- Q. M. Truong, P. N. T. Ho, T. B. Nguyen, W. H. Chen, X. T. Bui, A. K. Patel, R. R. Singhania, C. W. Chen and C. D. Dong, Bioresour. Technol., 2022, 361, 127732 CrossRef CAS PubMed.
- N. J. Che, N. Liu, Y. H. Li, C. Li, Y. L. Liu and C. L. Li, Biochar, 2022, 4, 65 CrossRef CAS.
- S. C. Kishore, R. Atchudan, S. Perumal, T. N. J. I. Edison, Y. R. Lee, A. K. Sundramoorthy, R. Vinodh and M. Alagan, J. Nanostruct. Chem., 2023, 13, 545–561 CrossRef CAS.
- J. M. Liu, S. R. Zhao, C. B. Wang, Y. D. Ma, L. H. He, B. Z. Liu and Z. H. Zhang, J. Colloid Interface Sci., 2022, 608, 1627–1637 CrossRef CAS PubMed.
- Y. C. Pang, S. Y. Zhang, L. M. Liu, J. Liang, Z. J. Sun, Y. K. Wang, C. H. Xiao, D. W. Ding and S. J. Ding, J. Mater. Chem. A, 2017, 5, 17963–17972 RSC.
- H. Chen, H. C. Jiang, X. P. Cao, Y. T. Zhang, X. J. Zhang and S. L. Qiao, Mater. Chem. Phys., 2020, 252, 123244 CrossRef CAS.
- L. Z. Chen, K. Wu, M. H. Zhang, N. S. Liu, C. X. Li, Ji. Z. Qin, Q. L. Zhao and Z. F. Ye, Chem. Eng. J., 2023, 466, 143082 CrossRef CAS.
- S. Q. Wen, H. Q. Wang, Q. Xin, E. Hu, Z. W. Lei, F. Hu and Q. L. Wang, Carbohydr. Polym., 2023, 315, 120970 CrossRef CAS PubMed.
- K. C. Huang, S. Q. Yang, X. H. Liu, C. Zhu, F. L. Qi, K. Wang, J. Q. Wang, Q. S. Wang, T. Wang and P. Y. Ma, J. Cleaner Prod., 2023, 391, 136174 CrossRef CAS.
- F. Bu, W. Huang, M. Xian, X. L. Zhang, F. B. Liang, X. C. Liu, X. Y. Sun and D. X. Feng, J. Cleaner Prod., 2022, 336, 130485 CrossRef CAS.
- Z. Peng, S. Luo, D. D. Zhao and J. Zhang, J. Cleaner Prod., 2023, 385, 135655 CrossRef CAS.
- J. Q. Ma, N. Z. F. Jia, H. X. Jin, S. J. Yao, K. F. Zhang, Y. Kai, W. L. Wu and Y. Z. Wen, Sep. Purif. Technol., 2023, 317, 123880 CrossRef CAS.
- K. D. Rasamani, F. Alimohammadi and Y. G. Sun, Mater. Today, 2017, 20, 83–91 CrossRef CAS.
- C. Wang, H. W. Wang, C. X. Yang, B. K. Dang, C. C. Li and Q. F. Sun, Carbon, 2020, 168, 624–632 CrossRef CAS.
- C. Senthil, S. Amutha, R. Gnanamuthu, K. Vediappan and C. W. Lee, Appl. Surf. Sci., 2019, 491, 180–186 CrossRef CAS.
- U. Ghani, N. Iqbal, J. H. Li, A. A. Aboalhassan, B. Y. Sun, B. W. Liu, F. Ullah, J. Zeb, M. Imtiaz, J. J. Gu and Q. L. Liu, Electrochim. Acta, 2022, 432, 141130 CrossRef CAS.
- D. Z. Wang, X. Y. Zhang, S. Y. Bao, Z. T. Zhang, H. Fei and Z. Z. Wu, J. Mater. Chem. A, 2017, 5, 2681–2688 RSC.
- Q. M. Luo, L. Sun, Y. W. Zhao, C. Wang, H. Q. Xin, D. Y. Li and F. Ma, J. Mater. Sci. Technol., 2023, 145, 165–173 CrossRef CAS.
- J. F. Fang, W. B. You, C. Y. Xu, B. T. Yang, M. Wang, J. C. Zhang and R. C. Che, Small, 2023, 19, 2205407 CrossRef CAS PubMed.
- S. Q. Huang, B. Gong, Y. X. Jin, P. H. L. Sit and J. C. H. Lam, ACS Catal., 2022, 12, 11340–11354 CrossRef CAS.
- X. Zhang, T. Ma, T. Fang, Y. Z. Gao, S. Gao, W. W. Wang and L. X. Liao, J. Alloys Compd., 2020, 818, 152821 CrossRef CAS.
- X. H. Pi, X. X. Sun, R. Q. Wang, C. L. Chen, S. B. Wu, F. R. Zhan, J. B. Zhong, Q. Wang and K. K. Ostrikov, J. Colloid Interface Sci., 2023, 629, 227–237 CrossRef CAS PubMed.
- J. H. Li, Y. Q. Zhang, Y. Y. Mao, Y. Y. Zhao, D. X. Kan, K. Zhu, S. L. Chou, X. T. Zhang, C. L. Zhu, J. Ren and Y. J. Chen, Angew. Chem., Int. Ed., 2023, 34, 202303056 Search PubMed.
- M. G. Shang, X. Q. Peng, J. Zhang, X. C. Liu, Z. P. Yuan, X. F. Zhao, S. J. Liu, S. M. Yu, X. B. Yi and S. Filatov, ACS Appl. Mater. Interfaces, 2023, 15, 14634–14642 CAS.
- L. Z. Chen, K. Wu, M. H. Zhang, N. S. Liu, C. X. Li, J. Z. Qin, Q. L. Zhao and Z. F. Ye, Chem. Eng. J., 2023, 466, 143082 CrossRef CAS.
- Z. K. Xiong, H. L. Zheng, Y. D. Hu, X. B. Hu, W. Ding, J. Y. Ma and Y. S. Li, Sep. Purif. Technol., 2021, 277, 119053 CrossRef CAS.
- Y. Y. Xie, X. Z. Yuan, Z. B. Wu, G. M. Zeng, L. B. Jiang, X. Peng and H. Li, J. Colloid Interface Sci., 2019, 536, 440–455 CrossRef CAS PubMed.
- Z. Li, Y. P. Li, Z. Fu, L. B. Lu, J. R. Cheng and Y. S. Fei, J. Colloid Interface Sci., 2021, 594, 141–149 CrossRef PubMed.
- J. Liu, R. Y. Zhou, J. X. Yu, L. Guo, X. D. Li, C. Q. Xiao, H. B. Hou, R. Chi and G. Q. Feng, J. Environ. Manage., 2022, 322, 116157 CrossRef CAS PubMed.
- C. L. Zhou, X. Y. Wang, Y. W. Wang, X. Song, D. F. Fang and S. F. Ge, J. Environ. Chem. Eng., 2021, 9, 105240 CrossRef CAS.
- Y. Priastomo, H. R. Setiawan, Y. S. Kurniawan and K. Ohto, J. Environ. Chem. Eng., 2020, 8, 103971 CrossRef.
- Q. Y. Wang, L. P. Li, L. C. Kong, G. Y. Cai, P. Wang, J. Zhang, W. Zuo and Y. Tian, Sep. Purif. Technol., 2022, 293, 121146 CrossRef CAS.
- Z. H. Lin, R. K. Wang, S. T. Tan, K. Zhang, Q. Yin, Z. H. Zhao and P. Gao, J. Environ. Manage., 2023, 334, 117503 CrossRef CAS PubMed.
- Y. Y. Zhao, H. X. Hu, L. C. Zhan, Z. J. Xue, K. K. YusefF and M. J. Wu, J. Chem., 2020, 2020, 13 Search PubMed.
- M. J. Han, X. Wei, R. Wang, J. Li, W. Sun and C. Y. Zhang, Sep. Purif. Technol., 2024, 330, 125209 CrossRef CAS.
- T. Wu, X. W. Chen, H. G. Zhang, M. Zhao, L. Huang, J. Yan, M. H. Su and X. J. Liu, Sep. Purif. Technol., 2023, 304, 122284 CrossRef CAS.
- J. M. Luo, K. X. Fu, M. Sun, K. Yin, D. Wang, X. Liu and J. C. Crittenden, ACS Appl. Mater. Interfaces, 2019, 11, 38789–38797 CrossRef CAS PubMed.
|
This journal is © The Royal Society of Chemistry 2024 |
Click here to see how this site uses Cookies. View our privacy policy here.