DOI:
10.1039/D2YA00134A
(Perspective)
Energy Adv., 2023,
2, 268-279
Towards an accelerated decarbonization of the chemical industry by electrolysis
Received
7th June 2022
, Accepted 12th November 2022
First published on 25th November 2022
Abstract
The transition towards carbon-neutral chemical production is challenging due to the fundamental reliance of the chemical sector on petrochemical feedstocks. Electrolysis-based manufacturing, powered with renewables, is a rapidly evolving technology that might be capable of drastically reducing CO2 emissions from the chemical sector. However, will it be possible to scale up electrolysis systems to the extent necessary to entirely decarbonize all chemical plants? Applying a forward-looking scenario, this perspective estimates how much electrical energy will be needed to power full-scale electrolysis-based chemical manufacturing by 2050. A significant gap is identified between the currently planned renewable energy grid expansion and the energy input necessary to electrify the chemical production: at minimum, the energy required for production of hydrogen and electrolysis of CO2 corresponds to 24–54% of all renewable power that is planned to be available. To cover this gap, strategies enabling a drastic reduction of the energy input to electrolysis are being discussed from the perspectives of both a single electrolysis system and an integrated electro-plant. Several scale-up oriented research priorities are formulated to underpin the timely development and commercial availability of described technologies, as well as to explore synergies and support further growth of the renewable energy sector, essential to realize described paradigm shift in chemical manufacturing.
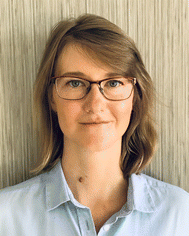
Magda H. Barecka
| Dr Magda H. Barecka is an Assistant Professor at Northeastern University in Boston, Department of Chemical Engineering and Chemistry and Chemical Biology. Her group focuses on the discovery and scale-up of electrochemical CO2 utilization methods. Dr Barecka completed postdoctoral training at the University of Cambridge, Research Centre for Research and Education in Singapore (CARES). She developed a new approach for CO2 utilization (Carbon Capture On-Site Recycling), as well as co-authored three patents. She holds a PhD degree from TU Dortmund (Germany) and, as a part of her PhD thesis, developed a methodology supporting implementation of intensified technologies in chemical manufacturing. |
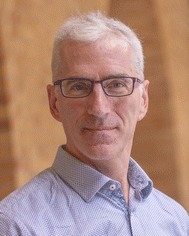
Joel W. Ager
| Joel W. Ager III is a Senior Staff Scientist in the Materials Sciences Division of Lawrence Berkeley National Laboratory and an Adjunct Full Professor in the Materials Science and Engineering Department, UC Berkeley. He graduated from Harvard College in 1982 with an A.B. in chemistry and from the University of Colorado in 1986 with a PhD in Chemical Physics. His research interests include the discovery of new photoelectrochemical and electrochemical catalysts for solar to chemical energy conversion, fundamental electronic and transport properties of semiconducting materials, and the development of new types of transparent conductors. |
Introduction
Transition to carbon neutrality requires drastic changes to happen in an unprecedently short period of time.1 Decarbonization of chemical manufacturing is crucial for achieving Net Zero 2050, as this sector is responsible for over 15% of all industrial CO2 emissions.2 It is particularly challenging to decarbonize the chemical industry due to its fundamental reliance on the inputs of petrochemical feedstocks, used in two dominant ways. First, petrochemical resources (e.g., natural gas) are used as fuels for combustion, which is necessary to produce thermal energy to drive the chemical transformations. Secondly, feedstocks such as crude oil are being used as starting materials for the production of bulk chemicals, and the petrochemical-derived carbon becomes embodied in the structures of the final products. If bulk chemicals are used to produce fuels, this carbon load will soon result in CO2 emissions;3 the same holds true for products with short life-cycles such as plastics which are incinerated instead of being buried in the landfills. While these emissions do not necessarily happen within the physical boundary of the plant, they are a direct consequence of manufacturing strategies deployed at the production site (Fig. 1a).
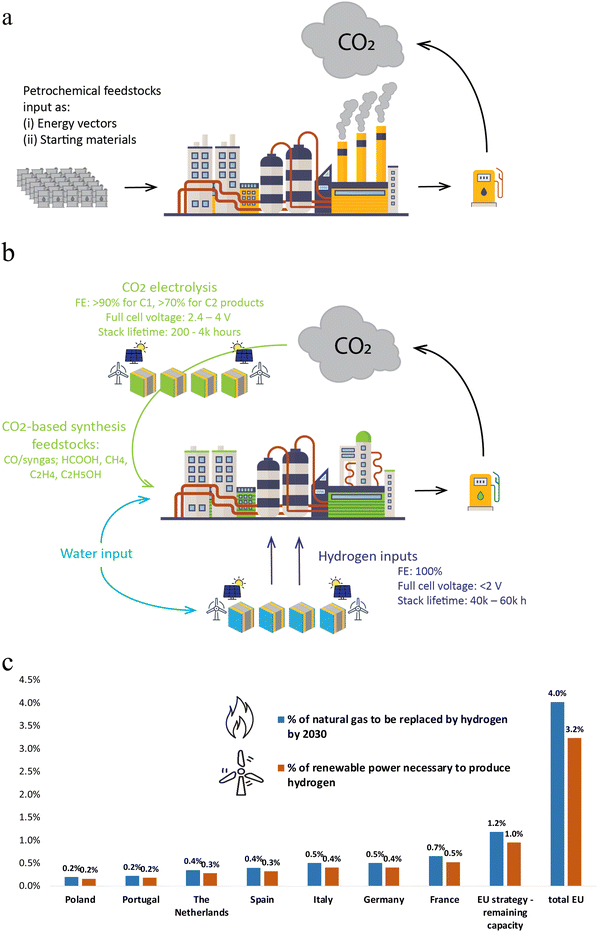 |
| Fig. 1 CO2 emissions from the chemical sector and pathways to their mitigation by electrolysis technologies: (a) scheme of a typical chemical manufacturing plant, where petrochemical feedstocks are used to supply energy and starting materials, and (b) concept of a decarbonized manufacturing by means of electrolysis; hydrogen from water electrolysis is supplied as an energy vector, and feedstocks for chemical conversion processes are obtained by electrolysis of CO2. To reduce life-cycle CO2 emissions, all electrolyzers need to be powered by low-carbon electricity. Performance benchmarks22,37–41 are cited here for the most investigated, scalable low-temperature electrolysis systems, based on gas diffusion electrode assemblies for CO2 electrolysis and PEM electrolyzers for hydrogen production. (c) Overview of current plans for adoption of hydrogen production by water electrolysis across the European Union. Blue bars (left) depict the percentage of the EU natural gas demand that will be replaced with green hydrogen, while orange bars (right) show the share of EU renewable energy that will be consumed to produce the hydrogen. Based on the current growth of the renewables sector, it will not be feasible to scale up electrolysis to entirely replace e.g. natural gas inputs, as this would consume all renewable energy planned to be available. Data sources.48–50 | |
To deeply decarbonize the chemical sector, we need to find a sustainable replacement for petrochemical resources, which at the same time delivers energy (through its chemical bonds), as well as carbon and hydrogen necessary to build complex products. In this context, emerging electrolysis technology is particularly promising, as it uses electrical energy to drive chemical transformations; this energy can be sourced in a renewable manner. It also uses dilute, though naturally abundant materials such as CO2 and water as feedstocks to produce chemicals (e.g. ethylene); hence it is capable of being a sustainable replacement of petrochemical inputs to chemical manufacturing4 (Fig. 1b). In contrast to biomass-based methods used to produce chemicals, electrolysis does not require to sacrifice arable land, which is particularly scarce in some regions.5
Given this great promise and the significant R&D interest in electrolysis,6 this perspective scrutinizes the potential of this technology to operate on scales necessary for the decarbonization of the chemical industry, focusing on the necessary energy inputs for producing hydrogen and powering CO2 electrolysis. The analysis presented in this paper highlights the extremely high, and so far likely underestimated, requirement for renewable power to drive scaled-up electrolysis. In response to this challenge, diverse strategies allowing for up to two orders of magnitude reduction of the required renewable power input are briefly introduced. The authors discuss as well how to maximize the reduction of CO2 emissions across the entire chemical sector, operate electrolysis in synergy with renewable energy production, and identify the features of electrolysis technology which need to be developed to facilitate further growth of the renewables sector. To the best of the authors’ knowledge, this is the first contribution that not only discusses the challenges related to the scale-up of electrolysis systems, but also highlights specific methods and pathways to address these challenges, providing the community with a concise research guide.
Electrolysis types in chemical manufacturing
Electrolysis technology is not completely unknown to chemical manufacturing as it has been used since the 19th century for production of chlorine and sodium hydroxide (chloralkali process) and is widely deployed in the electrometallurgy of, e.g., aluminium and lithium.7–9 However, electrolysis-based methods did not successfully penetrate other manufactures.10,11 Electrolysis technologies, which are currently investigated in the context of carbon neutrality, focus mostly on hydrogen production and CO2 electroconversion to hydrocarbons. Hydrogen electro-production is a relatively mature and scalable approach, available at a Technology Readiness Level (TRL) of 9 (operational system) in alkaline-type12 or rapidly developing Polymer Electrolyte Membrane (PEM) electrolyzers.13–19 Hydrogen generated by electrocatalytic methods can replace natural gas used as the thermal energy vector and can eliminate the emissions arising from combustion of petrochemical sources, as long as the electricity used for electrolysis is generated from renewable resources. Importantly, the use of hydrogen as an alternative fuel is reported to require only minor retrofits to the existing furnaces, especially if hydrogen will be blended with some amount of natural gas. This holds promise for reducing the carbon footprint of chemical manufactures with a limited retrofit cost and shut-down time.20 Furthermore, renewably sourced hydrogen can be subsequently used as a co-feedstock in the catalytic production of hydrocarbons from CO2, with methanol synthesis being a well-understood and scalable example of such an approach.21
Instead of deploying a two-step synthesis, renewably sourced hydrocarbons can be produced in a single step by a direct electrolysis of CO2 to carbon monoxide, ethylene, methane, ethanol or propanol.4,22–25 This technology allows for a simplified deployment of modular units that can yield bulk chemicals. Among different CO2 electrolysis products, carbon monoxide/syngas26 can be obtained from commercially available units (TRL 9) which use high-temperature solid oxide cells;27 there are also several start-ups working towards the scale up of CO2 to syngas in low-temperature stacks.28,29 Production of ethylene,22,23,30 methane31 and liquid fuels has been reported only on a laboratory-scale so far, with significant interest in scale-up.6 From a commercial perspective, ethylene is a particularly promising electrolysis product due its high price in certain markets (Asia, European Union).32 It has been demonstrated that there exist a large number of applications where ethylene production by electrolysis could yield a remarkable economic benefit,33,34 assuming electricity prices below $0.045 per kWh and performance metrics currently demonstrated in laboratory environments. In addition to that, there is an increasing demand for green ethylene as a starting material for synthesis of polymers, further used to manufacture carbon neutral products (e.g. apparel, fashion accessories), gaining popularity among climate-aware customers.35,36
Renewable power required for large-scale electrolysis
Taking into consideration how the chemical industry operates, both hydrogen and CO2 electrolysis products will be necessary on large scales to provide carbon-neutral energy sources and feedstock materials. With significant progress in the development of all electrolysis processes described above, it is timely to question if we are planning for a sufficient expansion of renewable electricity grids to power these processes on the scales necessary by 2050. Deploying a simple assessment and assuming that all natural gas input to chemical manufactures42 shall be replaced with hydrogen, we quantified the required hydrogen input (as it has different energy density than natural gas), and consequently the necessary electrical energy to generate this amount of hydrogen (based on the forward-looking electrolyzer efficiency of 85%). We compared the resulting energy requirement (∼5 × 1019 J per year) to the most ambitious scenarios of renewables capacity expansion. Full-scale hydrogen production would consume, at a minimum, 22–44% of the total electricity generated from renewable resources projected to be available by 2050 by the International Energy Agency (“NZE scenario”)43 and the International Renewable Energy Agency (IRENA; “Remap case”).44 Recently, IRENA published an update highlighting the need for even faster expansion of renewables,45 up to ∼2.6 × 1020 J per year of renewably-sourced electricity generated in 2050. In the light of the most forward looking analysis published so far, the electrical energy requirement for hydrogen production would account for ∼20% of total electricity generation from renewables, and 110% of electricity consumption allocated to all manufacturing industries.
A similar analysis was deployed to assess the power required for electrocatalytic production of ethylene, on the scale necessary to replace all petrochemically-derived ethylene used as a starting material for chemical synthesis (185 Mt per year46). With a hypothetical electrolyzer efficiency of 85%, ∼1 × 1019 J per year of electrical energy would be needed, being 4–10% of the planned electricity generation from renewable sources in 2050 (based on reports cited above43–45), and 22% of electricity consumption in industry.45 Importantly, this assessment is done based on current ethylene (and natural gas) consumption; with growing population and needs across the food, health and personal care sectors, the demand for raw materials will also increase. We also did not include the energy requirement towards CO2 capture and product separations, which are crucial to the CO2-based value chain47 and must be driven using renewably sourced energy to ensure carbon neutrality across the entire life-cycle of chemicals and fuels.
In total, a minimum power consumption for production of hydrogen and electrolysis of CO2 would be >24–54% of all renewably sourced electricity that is planned to be available, leaving less than 46–76% capacity to power electrified transportation, commercial/public services, residential buildings, food production, data centres and other manufacturing sectors beyond bulk chemical production. Therefore, even the most ambitious plans on renewable power generation (at the global level) might be not sufficient to allow for deep decarbonization of the chemical industry by means of electrolysis and will consequently be a rate-limiting factor in decarbonization efforts.
We sought to understand this challenge also on a regional scale and used European Union green hydrogen production plans as a case study. Based on the agreed national plans for the adoption water electrolysis by 2030,48 we estimated how much of the total natural gas demand in the EU49 will be replaced with the hydrogen obtained by electrolysis. Subsequently, we compared it with how much of the total EU renewable energy produced50 will be consumed by electrolysis (again, assuming the best case scenario of high electrolyzer efficiency, Fig. 1c). In total, only 4% of the EU natural gas demand will be replaced with hydrogen obtained from electrolysis by 2030, at an expense of the consumption of 3.2% of the available renewable energy, with France, Germany and Italy being the main contributors to the EU electrolysis capacities. Looking at a regional level, it becomes even more apparent that at the current rate of the growth of the renewables sector it will not be possible to fully scale electrolysis technologies as production of hydrogen would consume almost all available renewable electricity. Hence, we need to plan the expansion of the renewable electricity production much more boldly or (and) drastic reductions in terms of the energy input to the electrolysis units. This perspective proposes multiple emerging research areas which can yield scalable technologies that respond to this challenge and allow for production of chemicals and fuels with a minimized input of renewable power. Given the scale of the problem, we focused on technologies that have potential for drastic reduction of the energy input (min. an order of magnitude) as these bold improvements are necessary to pursue full-scale decarbonization of the chemical manufacturing with a limited renewable power budget.
Pathways to energy input reduction: hydrogen
Drastic reduction of the energy input to hydrogen production requires looking beyond the currently deployed chemistry. One of the ways to reduce this input is to study other reactions than water splitting, which is thermodynamically bound to min. 1.23 V energy input at standard temperature and pressure. The energy-intensive anodic oxygen evolution reaction can be replaced with electro-oxidation, which instead of pure water uses liquid biomass derivatives, alcohols or amines51 (Fig. 2a). As a result, the thermodynamic cell voltage requirement can be drastically reduced52,53 (e.g. to 0.3 V). This drastic reduction of energy requirement for hydrogen production can be a paradigm shift in the large scale deployment of electrocatalytic systems and at the same time allows generation of value-added chemicals on the anode side (instead of the oxygen stream, or CO2 which would be the case if the biomass feedstock was completely oxidized).
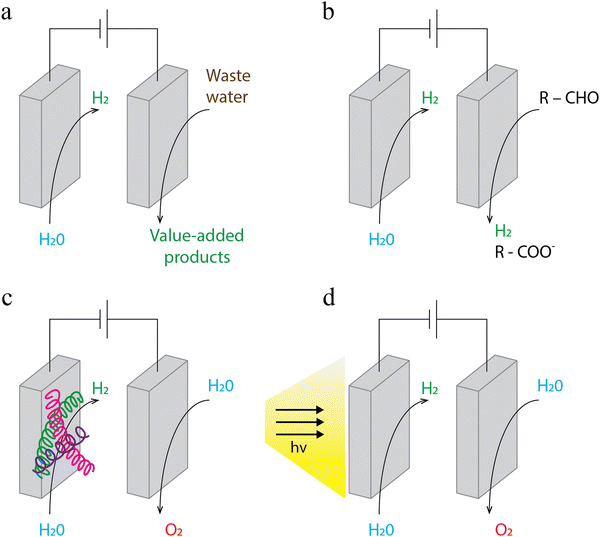 |
| Fig. 2 Conceptual representation of exemplary strategies allowing for a drastic reduction of energy input to electrolysis processes, exemplified for hydrogen production by means of: (a) combination with anodic oxidation, (b) co-production of hydrogen on the anode side, (c) incorporation of enzymes, and (d) inclusion of solar radiation energy inputs. | |
Consequently, it is important to understand how to sustainably source large quantities of the molecules which could be a convenient anodic feedstock. Coupling hydrogen production with industrial wastewater treatment is promising in this regard. This concept was proposed by Qiu et al.54 for the case of the pulping industry, which yields a wide range of carbohydrate alkaline degradation products (CHADs), and such a simulated waste stream was demonstrated to be a functional feed for hydrogen production. Sustainably sourced alcohols are also a feasible anodic input;55 this pathway can be particularly promising if ethanol could be sourced from waste streams from biomanufacturing, as these industries are likely to scale up in the upcoming decades. Wang et al.56 further explored this concept by proposing anodic oxidation reactions that also yield hydrogen products; hence, the overall energy requirement is decreased not only by a more thermodynamically favourable anodic transformation, but also because of the increased hydrogen output from the same unit (Fig. 2b). The limitations in the scaling of the approach that involves the use of alternative feedstocks on the anode side are described in the “Limitations of the study” section.
An interesting example of manipulating the anode-side environment was reported by Dotan et al.57 Their proposed hydrogen production technology – electrochemically–thermally activated chemical cycle (E-TAC) – separates electrolysis into two steps. First, water is reduced on the cathode side to hydrogen, and simultaneously water participates in the reaction of oxidizing the anode (from Ni(OH)2 to NiOOH). Subsequently, the anode is placed in hot water to allow for its reduction and the release of oxygen. This arrangement allows production of hydrogen at 1.44–1.6 V and deployment of reactors without membrane separators, as the risk of creating an explosive mixture of oxygen and hydrogen is mitigated by producing these gases in separate steps. Though an order of magnitude reduction of energy requirement for electrolysis cannot be achieved with this approach, it does provide excellent advantages in terms of scalability and the technology is currently commercially available (H2Pro58), with a 600 MW production facility being currently commissioned in Israel. The decoupling scheme could in principle be deployed across other systems discussed in this perspective.
Another possibility for reduction of the electrical energy input is related to the inclusion of enzymes and the development of combined electrochemistry–enzyme systems (Fig. 2c). Enzymes have been extensively studied for their excellent catalytic properties and as a sustainable replacement for catalysts that would need to be otherwise mined, like e.g. noble metals.59 In the field of hydrogen production, numerous enzyme–electroreduction systems were investigated for their potential to deliver improvement in energy efficiency.60–62 Hardt et al.63 reported an example of such enzymatic systems (hydrogenase embedded in a hydrogel), allowing production of hydrogen with only 12 mV overpotential.
Furthermore, system energy requirements can be reduced by inclusion of additional energy sources beyond the externally sourced electricity. This approach includes the use of bacteria, which could produce electricity used to drive the electrochemical reaction (like in microbial electrolysis cells); however, bacteria emit CO2 that will need to be captured and stored.64 Alternatively, bacteria could be deployed for a direct hydrogen production, which could be further intensified by combination with electrocatalytic methods. Vasiliadou et al.65 described such an approach, which combines the capacity of purple phototrophic bacteria to produce hydrogen with electrochemical reaction on a working electrode of graphite.
Another pathway to reduce external inputs of electricity to electrocatalytic systems uses energy from sunlight by means of photocatalytic systems, which has been demonstrated on a scale of up to 100 m2 of the electrode surface66 (Fig. 2d). However, these devices at present are much less productive in terms of hydrogen output per surface area as compared to solely electrical-energy powered electrolyzers (e.g. PEM); hence extremely large reactors will be required to deliver the same hydrogen throughout. Resulting high investment costs, along with extended requirements for space and materials necessary to build electrodes, highlight the need to focus on increasing the productivity and to seek for widely available, or easily recyclable electrode materials.67
Pathways to energy input reduction: CO2 electrolysis
All pathways towards the reduction of energy input described above are applicable not only to hydrogen production, but also to CO2 electrolysis.68 Na et al. scrutinized the possibility of replacement of water feed on the anode side with different organic waste streams leading to co-production of useful chemicals on the anode side, and, most importantly, to a drastic reduction in the energy input. Their analysis discusses the opportunities to produce 13 different chemicals on the cathode side and 20 on the anode side. Remarkably, combination of CO2 electrolysis to ethylene on the cathode side with glycerol oxidation to formic acid on the anode side leads to reduction of the full cell voltage from 1.15 V to 0.06 V69 (under hypothetical 100% efficiency). This two-orders of magnitude reduction in energy requirement opens the pathway to electrolysis deployment at unprecedented levels.
Inclusion of enzymes,70 bacteria,71 and additional energy sources72 has also been proposed for CO2 electrolysis application. Interestingly, there are also insights into combination of some or all of these functionalities into one device, inspired by the photosynthesis process. Possibilities of enzymatic electroreduction were studied to deliver carbon monoxide, formic acid and methanol;73 promising findings in terms of energy input reduction and excellent selectivity and stability were reported for carbon monoxide production by carbon monoxide dehydrogenase from Moorella thermoacetica.74 The energy barrier could be further reduced by including the direct energy input from solar radiation in photo-bio-electrocatalytic devices.75
Eliminating several sources of emissions with the same energy input
Another approach to support the deployment of electrolysis is to focus on mitigating several sources of CO2 emissions with one electrocatalytic device, increasing the amount of avoided CO2 emissions per unit of energy input to the processes. This could be achieved by a direct, one-step CO2 electrolysis to complex molecules, with these being the final output of the chemical manufacture (e.g. ethylene glycol). As a result, the electrolysis enables bypassing the entire chemical plant, avoiding CO2 emissions from the use of petrochemical resources as energy vectors and production feedstocks. Hence, there is no need to separately invest energy to produce hydrogen and sustainably-sourced hydrocarbon feedstocks; instead, a single power input, along with CO2 and water, will suffice for the operation of the entire electro-plant. So far, this approach has been explored for laboratory scale production of ethylene oxide, propylene oxide76 and ethylene glycol.77 More research is necessary to extend this portfolio, and, importantly, these insights should be incorporated in devices applicable for large-scale electrolysis (gas diffusion electrode assembly) instead of H-cell type electrolyzers preferred for the convenience of laboratory studies.78 Ideally, the development of electrocatalytic routes towards more complex chemicals should be combined with any approach that reduces energy requirements: use of enzymes or alternative anode-side reactions.
Synergistic support for renewables expansion
Direct production of complex chemicals from CO2 can also support further investment in new renewable electricity projects by providing a strategy to address the current limitations towards the expansion of renewables: the high cost of power transmission and battery storage.79 First, being able to produce chemical products directly next to the power plant eliminates the energy transmission cost; however, targeted products should either be used locally, or be easily and safely transported. Secondly, the ability to operate electrochemical processes in an intermittent manner can also remove the need for costly and material-intense battery storage, as the produced electricity can be directly consumed on site only when it is generated. Low-temperature electrolysis, itself, is perfectly suited to operate only upon the availability of renewable energy, with start-up and shut-down times in the range of seconds to minutes. However, to deploy this concept, it is necessary also to run intermittently further transformations of the electrolysis product. This is particularly challenging to achieve if one envisions e.g. further conversion of hydrogen or syngas by means of high-temperature catalytic methods which are associated with extended start-up and shut-down times. Thus, the ability to directly produce complex chemicals solves this problem, as no further chemical transformations are necessary. The availability of such modular electro-plants could foster the investment in new renewable energy projects, well beyond what is currently planned to be executed by 2050.
Emerging research priorities
Notably, all of the approaches described here have been verified only on the laboratory scale, and their further development needs to happen in a very short period of time. Therefore, it is timely to review the research goals and formulate strategies that will support an accelerated scale-up.
First, despite the fact that the most mature electrolysis technologies (water splitting and CO2 electrolysis with water feed on the anode side) are much more energy intensive than the alternatives discussed in this perspective, we should not refrain from scaling up these higher TRL options and deploying for commercial production of bulk chemicals. It has been demonstrated that if well connected to the existing value chain, these technologies can be economically viable with current renewable electricity prices, even with no CO2 taxation in place.33 Use of the electrolysis on a large scale will yield unique knowledge and experience, necessary to develop other systems. Most importantly, scaling up these technologies now means that by the time that alternative electrolysis approaches will gain better understanding, large electrolyzers will be already commissioned and integrated within chemical plants. Therefore, at that point in the future, it will be simpler and faster to retrofit existing “classical” electrodes by the more energy efficient next generation of materials, or to deploy alternative anodic feeds and energy co-sources (Fig. 3). This parallel electrolysis scale-up, along with the expansion of the renewable electricity, could allow meeting the goal of carbon neutral production by 2050.
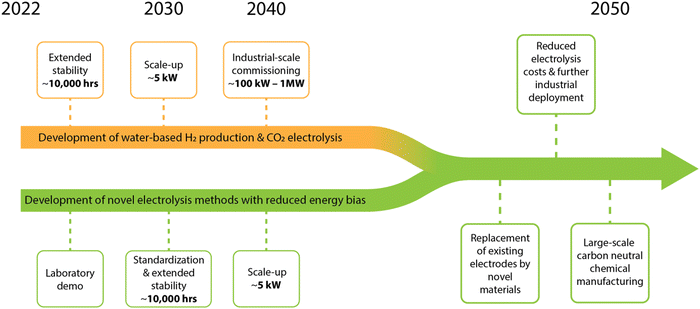 |
| Fig. 3 Proposed phases for the scale-up of electrolysis systems: in parallel, we need to scale and commission the most mature systems based on water electrolysis and perform further research on energy-efficient alternatives described in this perspective. This will allow in the future for adopting already deployed electrolyzers once better alternatives are developed and save time as opposed to a classical, consecutive scale-up approach. Proposed targets related to the stability and scale-up were inspired by the reports for commercially available, small-scale hydrogen electrolyzers,80 and techno-economic analysis for hydrogen production published by the National Renewable Energy Laboratory.41 | |
Equally important, we need a coordinated development of the described technologies. Building up a common understanding of the experimental procedures for electrolysis characterization will help to quantify the status of the development of each electrolysis variant. To this end, standards and protocols that detail the testing environment (e.g. reactor architecture, conditioning, operating conditions such as current density and feed composition) are required. While protocols for standardized testing of commercial water electrolyzers have been proposed recently by the Joint Research Centre of the EU81 and the National Renewable Energy Laboratory in the US,82 further discussion is necessary to understand how to make these protocols deployable for the assessment of less mature technologies, available on a laboratory scale. There is also an ongoing discussion in the CO2 electrolysis field regarding how to ensure a precise product quantification through the test rig design,83 how to test catalysts under the conditions relevant for industrial application,78 and how much the performance of the catalyst can be hindered by the use of suboptimal testing environments.84 These examples highlight the importance of standardization in the electrolysis field, and it will be crucial to define the structure of a protocol covering all these aspects in one testing procedure. Deploying such a protocol for every new material will consequently facilitate transparent comparison between electrolysis variants and understanding of related limitations. So far, rigorous protocols have been proposed in the CO2 electrolysis field only for techno-economic analysis,85 and their availability is likely to support the acquisition of funding for further development.
We also need to anticipate scale-up challenges already within the early laboratory tests and focus the research on solving the critical problems towards the development of functional systems. As such, we should test the operation of devices with industrial streams, which might include some minor, particularly challenging impurities. Running early-development tests with e.g. waste water feeds for hydrogen production or CO2 from industrial source points for CO2 electrolysis would help to verify potential catalyst poisoning effects. While sourcing CO2 from an industrial emitter is feasible to be done by using bottled gas, direct use of waste water is more restricted in research facilities. Therefore, developing test units that could be distributed to e.g. waste water treatment plants for testing with “real” streams should become part of an early development procedure. Detailed insights into the durability of electrodes as well as sourcing and recycling of materials for their construction will be also pivotal to achieving ambitious scale-up goals. So far, the stability of electrodes has usually been verified on the time scale of hours to days, what needs to be increased by a factor of 100–1000 to open commercially viable applications. Frequently, stability studies are hindered by the lack of the infrastructure suited for long-term testing, which will allow for a safe, unsupervised execution of experiments involving production gases such as hydrogen and carbon monoxide. Thus, the development of well-sealed, thoroughly monitored and automatized set-ups for electrolysis tests could support scrutinizing electrodes’ durability, which is particularly challenging in the CO2 electroreduction field.
While developing new electrolysis systems, it is also crucial to balance the academic pursuit towards excellence with a practical, hands-on approach. Though an idealistic 100% faradaic efficiency (FE) towards a single product of electroreduction is an exciting research goal, it might be more insightful to appreciate what is the minimum FE necessary for a commercially attractive process and prioritize the work towards functional though less selective processes.
To further understand what is the minimum selectivity or conversion of an electrolysis process that will yield a commercially attractive application, we need to question how electrolysis will operate as a part of the established value chain. Especially while thinking of electrolysis coupled with anodic oxidation, a connection to specific waste stream will be required, and electrolysis will deliver at least two different products. It is crucial to consider the availability of these waste streams, which varies locally, and will change with any transformation of the chemical industry, as well the possibilities of the use of anodic products. Therefore, it is reasoned to work towards a wide portfolio of reactions that can be deployed to produce hydrogen, and will allow to uptake various, locally available waste sources and to deliver anodic side by-products which will be easily separable and useful in the given environment. Overall, from the perspective of large-scale electrolysis adoption, it might be more impactful to have access to less optimized, but a wide range of electrochemical reactions functional for e.g. hydrogen production, rather than having sole access to thoroughly optimized water electrolyzers, which will in any case require vast energy input.
Readiness for the industrial integration of electrolyzers requires also more research in the area of separation technologies. Products which are accumulated in the catholyte (e.g. ethanol obtained from CO2 electrolysis) or different products of the anodic oxidation are typically highly dilute, as their high accumulation would otherwise change the properties of the catholyte/anolyte. The separations of these products might have high energy footprints if performed by means of classical approaches such as distillation.47 Therefore, there is a need to investigate technologies less frequently adopted in the industry, such as membrane separations, separation using ionic liquids, or separation using new energy forces (for details, see e.g. the database of intensified technologies86), in order to unveil new pathways to energy-efficient separations.
Last, we need to support the exchange of ideas and learnings between the hydrogen production and CO2 electrolysis fields. There are fundamental similarities between these two systems; however, the research frequently happens separately. The deployment of unified testing protocols and standards might also help to intensify this collaboration. It is important to appreciate that, ultimately, we will likely need a portfolio of water and CO2 electrolysis options, rather than rely on one well developed technology. The unavailability of these diverse and scalable options that can suit production needs at a particular manufacture increases the long-term risk of not meeting the carbon neutrality goal.
Limitations of the study
The present analysis focuses only on the necessary power inputs to electrolyzers and does not consider other energy needs across the life cycle, such as the cost of CO2 capture and transport, inevitable for the electrolysis reactors that operate with concentrated CO2 streams.87 The large-scale deployment of this technology would thus require a capacity to pre-concentrate biogenic CO2, which, though abundant, has a much lower concentration than industrial source points (with an exception of some fermentation-based processes88). Consequently, the total energy requirement of future electro-manufactures will be even higher, which further emphasises the need to focus on the energy efficiency aspects. We anticipate that though significant improvements have been reported in terms of the cost and scalability of direct air/biogenic sources capture,89 ensuring the availability of concentrated CO2 will be another challenge that the electrolysis community needs to address; a country-wide analysis of biogenic CO2 sourcing, related challenges and research priorities has been recently published by Badgett et al.90 The analysis provides a basis for future planning of chemical manufacturing mainly based on CO2 inputs from direct air capture and scrutinizes the connection of these systems to the value chain and renewable electricity sources.
Responding to the growing renewable power needs will also come at a significant capital cost, which is not quantified in our analysis. The investment in the manufacturing of solar panels (or wind mills), construction and maintenance of the new infrastructure for power distribution will strongly influence the feasibility of deployment of large scale electro-manufacturing envisioned here.
Pursuing some of the described strategies for the minimized energy input to hydrogen production will also require re-inventing the way we optimize production processes on scale. Instead of working with a single set of feeds and products, electro-manufactures envisioned here will need to flexibly take up waste streams with varying availabilities, as well as to be able to adjust their production strategies to the fluctuating market demand for the anode side by-products. Thus, in parallel to increasing the TRL of electrolysis technologies, we also need to develop new process design methods that will respond to the increasing complexity of the supply chain. Such methods need to be capable of optimizing production routes through various feedstocks, in terms of both the cost and the sustainability of the overall process. The availability of such planning tools on regional or even larger scales could substantially contribute to the use of electrolysis as a tool for circular, decarbonized manufacturing.
Author contributions
M. H. B. developed the scale-up methodology, visualized the data, and wrote the original manuscript; M. H. B. and J. W. A. conceptualized the paper; J. W. A. acquired funding for the project, administered the project, supervised the project, and reviewed and edited the manuscript.
Conflicts of interest
The authors co-filed patent applications US62/987369, US63/036477 and US63/213936 for novel electroreduction-base processes, e.g. for CO2 recycling in ethylene-based plants. There are no other conflicts of interest to declare.
Acknowledgements
The authors acknowledge the support of the National Research Foundation (NRF), the Prime Minister's Office, Singapore, under its Campus for Research Excellence and Technological Enterprise (CREATE) Programme through the eCO2EP project, operated by the Cambridge Centre for Advanced Research and Education in Singapore (CARES) and the Berkeley Education Alliance for Research in Singapore (BEARS). The contribution of Andres J. Sanz Guillen to discussions, proofreading and the enrichment of the visual content is gratefully acknowledged.
References
- J. H. Wesseling, S. Lechtenböhmer, M. Åhman, L. J. Nilsson, E. Worrell and L. Coenen, The transition of energy intensive processing industries towards deep decarbonization: Characteristics and implications for future research, Renewable Sustainable Energy Rev., 2017, 79, 1303–1313 CrossRef CAS.
-
P. Levi, Technology Roadmap The global iron and steel sector, International Energy Agency, 2019 Search PubMed.
- P. Bains, P. Psarras and J. Wilcox, CO2 capture from the industry sector, Prog. Energy Combust. Sci., 2017, 63, 146–172 CrossRef.
- J. W. Ager and A. A. Lapkin, Chemical storage of renewable energy, Science, 2018, 360, 707–708 CrossRef CAS PubMed.
- V. Piemonte and F. Gironi, Land-use change emissions: How green are the bioplastics?, Environ. Prog. Sustainable Energy, 2011, 30, 685–691 CrossRef CAS.
- S. Garg, M. Li, A. Z. Weber, L. Ge, L. Li, V. Rudolph, G. Wang and T. E. Rufford, Advances and challenges in electrochemical CO2 reduction processes: an engineering and design perspective looking beyond new catalyst materials, J. Mater. Chem. A, 2020, 8, 1511–1544 RSC.
- G. Botte, Electrochemical Manufacturing in the Chemical Industry, Interface Mag., 2014, 23, 49–55 CrossRef.
-
D. Pletcher, Industrial electrochemistry, Chapman and Hall, London, New York, 1984, 1982 Search PubMed.
- I. Moussallem, J. Jörissen, U. Kunz, S. Pinnow and T. Turek, Chlor-alkali electrolysis with oxygen depolarized cathodes: history, present status and future prospects, J. Appl. Electrochem., 2008, 38, 1177–1194 CrossRef CAS.
- B. A. Frontana-Uribe, R. D. Little, J. G. Ibanez, A. Palma and R. Vasquez-Medrano, Organic electrosynthesis: a promising green methodology in organic chemistry, Green Chem., 2010, 12, 2099 RSC.
- H. Lund, A Century of Organic Electrochemistry, J. Appl. Electrochem., 2002, 149, S21 CrossRef CAS.
-
J. O. Jensen, V. Bandur, N. J. Bjerrum, S. H. Jensen, S. Ebbesen, M. Mogensen, N. Tophøj and L. Yde, Pre-investigation of water electrolysis, Report, PSO-F&U 2006-1-6287, 2006.
- S. Shiva Kumar and V. Himabindu, Hydrogen production by PEM water electrolysis – A review, Mater. Sci. Energy Technol., 2019, 2, 442–454 Search PubMed.
- A. Ursua, L. M. Gandia and P. Sanchis, Hydrogen Production From Water Electrolysis: Current Status and Future Trends, Proc. IEEE, 2012, 100, 410–426 CAS.
- K. Zeng and D. Zhang, Recent progress in alkaline water electrolysis for hydrogen production and applications, Prog. Energy Combust. Sci., 2010, 36, 307–326 CrossRef CAS.
- W. Kreuter, Electrolysis: The important energy transformer in a world of sustainable energy, Int. J. Hydrogen Energy, 1998, 23, 661–666 CrossRef CAS.
-
T. Smolinka, Water Electrolysis, in Encyclopedia of electrochemical power sources, ed. J. Garche, Elsevier, Amsterdam, 2009 Search PubMed.
- R. Leroy, Industrial water electrolysis: Present and future, Int. J. Hydrogen Energy, 1983, 8, 401–417 CrossRef CAS.
- M. Paidar, V. Fateev and K. Bouzek, Membrane electrolysis—History, current status and perspective, Electrochim. Acta, 2016, 209, 737–756 CrossRef CAS.
- M. Mayrhofer, M. Koller, P. Seemann, R. Prieler and C. Hochenauer, Assessment of natural gas/hydrogen blends as an alternative fuel for industrial heat treatment furnaces, Int. J. Hydrogen Energy, 2021, 46, 21672–21686 CrossRef CAS.
- R. Guil-López, N. Mota, J. Llorente, E. Millán, B. Pawelec, J. L. G. Fierro and R. M. Navarro, Methanol Synthesis from CO2: A Review of the Latest Developments in Heterogeneous Catalysis, Materials, 2019, 12, 1–24 CrossRef.
- F. P. García de Arquer, C.-T. Dinh, A. Ozden, J. Wicks, C. McCallum, A. R. Kirmani, D.-H. Nam, C. Gabardo, A. Seifitokaldani, X. Wang, Y. C. Li, F. Li, J. Edwards, L. J. Richter, S. J. Thorpe, D. Sinton and E. H. Sargent, CO2 electrolysis to multicarbon products at activities greater than 1 A cm-2, Science, 2020, 367, 661–666 CrossRef.
- C.-T. Dinh, T. Burdyny, M. G. Kibria, A. Seifitokaldani, C. M. Gabardo, F. P. García de Arquer, A. Kiani, J. P. Edwards, P. de Luna, O. S. Bushuyev, C. Zou, R. Quintero-Bermudez, Y. Pang, D. Sinton and E. H. Sargent, CO2 electroreduction to ethylene via hydroxide-mediated copper catalysis at an abrupt interface, Science, 2018, 360, 783–787 CrossRef CAS PubMed.
- J. E. Huang, F. Li, A. Ozden, A. Sedighian Rasouli, F. P. García de Arquer, S. Liu, S. Zhang, M. Luo, X. Wang, Y. Lum, Y. Xu, K. Bertens, R. K. Miao, C.-T. Dinh, D. Sinton and E. H. Sargent, CO2 electrolysis to multicarbon products in strong acid, Science, 2021, 372, 1074–1078 CrossRef CAS.
- M. Li, M. N. Idros, Y. Wu, T. Burdyny, S. Garg, X. S. Zhao, G. Wang and T. E. Rufford, The role of electrode wettability in electrochemical reduction of carbon dioxide, J. Mater. Chem. A, 2021, 9, 19369–19409 RSC.
- W. Guo, J. Bi, Q. Zhu, J. Ma, G. Yang, H. Wu, X. Sun and B. Han, Highly Selective CO 2 Electroreduction to CO on Cu–Co Bimetallic Catalysts, ACS Sustainable Chem. Eng., 2020, 8, 12561–12567 CrossRef CAS.
- C. Mittal, C. Hadsbjerg and P. Blennow, Small-scale CO from CO2 using electrolysis, Chem. Eng. World, 2017, 44–46 Search PubMed.
- Dioxycle, Company website, https://dioxycle.com, 2022.
- Twelve, Company website, https://www.twelve.co/, 2022.
- L. Zaza, K. Rossi and R. Buonsanti, Well-Defined Copper-Based Nanocatalysts for Selective Electrochemical Reduction of CO2 to C2 Products, ACS Energy Lett., 2022, 7, 1284–1291 CrossRef CAS.
- A. Sedighian Rasouli, X. Wang, J. Wicks, G. Lee, T. Peng, F. Li, C. McCallum, C.-T. Dinh, A. H. Ip, D. Sinton and E. H. Sargent, CO2 Electroreduction to Methane at Production Rates Exceeding 100 mA/cm2, ACS Sustainable Chem. Eng., 2020, 8, 14668–14673 CrossRef CAS.
- ICIS, 2021 Global Market Outlook – Chemicals, Independent Commodity Intelligence Services report., 2020.
- M. H. Barecka, J. W. Ager and A. A. Lapkin, Carbon neutral manufacturing via on-site CO2 recycling, iScience, 2021, 24, 102514 CrossRef CAS PubMed.
- M. H. Barecka, J. W. Ager and A. A. Lapkin, Economically viable CO2 electroreduction embedded within ethylene oxide manufacturing, Energy Environ. Sci., 2021, 14, 1530–1543 RSC.
- S. J. Davis, N. S. Lewis, M. Shaner, S. Aggarwal, D. Arent, I. L. Azevedo, S. M. Benson, T. Bradley, J. Brouwer, Y.-M. Chiang, C. T. M. Clack, A. Cohen, S. Doig, J. Edmonds, P. Fennell, C. B. Field, B. Hannegan, B.-M. Hodge, M. I. Hoffert, E. Ingersoll, P. Jaramillo, K. S. Lackner, K. J. Mach, M. Mastrandrea, J. Ogden, P. F. Peterson, D. L. Sanchez, D. Sperling, J. Stagner, J. E. Trancik, C.-J. Yang and K. Caldeira, Net-zero emissions energy systems, Science, 2018, 360, 1–9 CrossRef.
-
A. Peters, The lenses in these sunglasses are made from captured CO2, https://www.fastcompany.com/90678020/the-lenses-in-these-sunglasses-are-made-from-captured-co2, Fastcompany, 2021.
- R. B. Kutz, Q. Chen, H. Yang, S. D. Sajjad, Z. Liu and I. R. Masel, Sustainion Imidazolium-Functionalized Polymers for Carbon Dioxide Electrolysis, Energy Technol., 2017, 5, 929–936 CrossRef CAS.
- H. Yang, J. J. Kaczur, S. D. Sajjad and R. I. Masel, Electrochemical conversion of CO2 to formic acid utilizing Sustainion™ membranes, J. CO2 Util., 2017, 20, 208–217 CrossRef CAS.
- W. Ma, S. Xie, T. Liu, Q. Fan, J. Ye, F. Sun, Z. Jiang, Q. Zhang, J. Cheng and Y. Wang, Electrocatalytic reduction of CO2 to ethylene and ethanol through hydrogen-assisted C–C coupling over fluorine-modified copper, Nat. Catal., 2020, 3, 478–487 CrossRef CAS.
- K. Bareiß, C. de La Rua, M. Möckl and T. Hamacher, Life cycle assessment of hydrogen from proton exchange membrane water electrolysis in future energy systems, Appl. Energy, 2019, 237, 862–872 CrossRef.
-
A. Mayyas, M. Ruth, B. Pivovar, G. Bender and K. Wipke, NREL is a national laboratory of the U.S. Department of Energy Office of Energy Efficiency & Renewable Energy Operated by the Alliance for Sustainable Energy, LLC. This report is available at no cost from the National Renewable Energy Laboratory (NREL) at http://www.nrel.gov/publications. Contract No. DE-AC36-08GO28308 Technical Report NREL/TP-6A20-72740 August 2019 Manufacturing Cost Analysis for Proton Exchange Membrane Water Electrolyzers. Technical Report NREL/TP-6A20-72740, 2019.
- IEA, Gas, Report by the International Energy Agency, https://www.iea.org/fuels-and-technologies/gas, 2022.
-
L. Cozzi, T. Güll, S. Bouckaert, A. Fernandez Pales, C. McGlade, U. Remme, B. Wanner, L. Varro, D. D’Ambrosio and T. Spencer, Net Zero by 2050, A Roadmap for the Global Energy Sector, International Energy Agency, 2021 Search PubMed.
-
IRENA, Global energy transformation. Roadmap to 2050, International Renewable Energy Agency, 2018 Search PubMed.
- International Renewable Energy Agency, World energy transitions outlook. 1.5 °C Pathway, 2021.
-
L. Fernandez, Global demand of ethylene 2017-2022, http://Statista.com, 2021.
- J. B. Greenblatt, D. J. Miller, J. W. Ager, F. A. Houle and I. D. Sharp, The Technical and Energetic Challenges of Separating (Photo)Electrochemical Carbon Dioxide Reduction Products, Joule, 2018, 2, 381–420 CrossRef CAS.
- International Renewable Energy Agency, Green hydrogen supply, IRENA Report, 2021.
- Bp, BP corporate review, Statistical review 2021, http://www.bp.com/content/dam/bp/business-sites/en/global/corporate/pdfs/energy-economics/statistical-review/bp-stats-review-2021-full-report.pdf, 2021.
- European Commission, REPpowerEU: affordable, secure and sustainble energy for Europe. http://www.ec.europa.eu, 2022.
- M. Xiang, N. Wang, Z. Xu, H. Zhang and Z. Yan, Accelerating Hydrogen Evolution by Anodic Electrosynthesis of Value-Added Chemicals in Water over Non-Precious Metal Electrocatalysts, ChemPlusChem, 2021, 86, 1307–1315 CrossRef CAS.
- Y. Xu and B. Zhang, Recent Advances in Electrochemical Hydrogen Production from Water Assisted by Alternative Oxidation Reactions, ChemElectroChem, 2019, 6, 3214–3226 CrossRef CAS.
- Y. X. Chen, A. Lavacchi, H. A. Miller, M. Bevilacqua, J. Filippi, M. Innocenti, A. Marchionni, W. Oberhauser, L. Wang and F. Vizza, Nanotechnology makes biomass electrolysis more energy efficient than water electrolysis, Nat. Commun., 2014, 5, 4036 CrossRef CAS PubMed.
- Z. Qiu, D. Martín-Yerga, P. A. Lindén, G. Henriksson and A. Cornell, Green hydrogen production via electrochemical conversion of components from alkaline carbohydrate degradation, Int. J. Hydrogen Energy, 2021, 22, 4115 Search PubMed.
- H. Ju, S. Giddey, S. P. S. Badwal and R. J. Mulder, Electro-catalytic conversion of ethanol in solid electrolyte cells for distributed hydrogen generation, Electrochim. Acta, 2016, 212, 744–757 CrossRef CAS.
- T. Wang, L. Tao, X. Zhu, C. Chen, W. Chen, S. Du, Y. Zhou, B. Zhou, D. Wang, C. Xie, P. Long, W. Li, Y. Wang, R. Chen, Y. Zou, X.-Z. Fu, Y. Li, X. Duan and S. Wang, Combined anodic and cathodic hydrogen production from aldehyde oxidation and hydrogen evolution reaction, Nat. Catal., 2021, 488, 294 Search PubMed.
- H. Dotan, A. Landman, S. W. Sheehan, K. D. Malviya, G. E. Shter, D. A. Grave, Z. Arzi, N. Yehudai, M. Halabi, N. Gal, N. Hadari, C. Cohen, A. Rothschild and G. S. Grader, Decoupled hydrogen and oxygen evolution by a two-step electrochemical–chemical cycle for efficient overall water splitting, Nat. Energy, 2019, 4, 786–795 CrossRef CAS.
- H2Pro, H2Pro company website. http://www.h2pro.co, 2022.
- N. Adam, S. Schlicht, Y. Han, M. Bechelany, J. Bachmann and M. Perner, Metagenomics Meets Electrochemistry: Utilizing the Huge Catalytic Potential From the Uncultured Microbial Majority for Energy-Storage, Front. Bioeng. Biotechnol., 2020, 8, 567 CrossRef PubMed.
-
P. A. Ash and K. A. Vincent, Encyclopedia of Interfacial Chemistry, Elsevier, 2018, pp. 590–595 Search PubMed.
- M. H. G. Prechtl and U.-P. Apfel, Toward electrocatalytic chemoenzymatic hydrogen evolution and beyond, Cell Rep. Phys. Sci., 2021, 2, 100626 CrossRef CAS.
- J. C. Ruth, F. M. Schwarz, V. Müller and A. M. Spormann, Enzymatic Hydrogen Electrosynthesis at Enhanced Current Density Using a Redox Polymer, Catalysts, 2021, 11, 1197 CrossRef CAS.
- S. Hardt, S. Stapf, D. T. Filmon, J. A. Birrell, O. Rüdiger, V. Fourmond, C. Léger and N. Plumeré, Reversible H2 Oxidation and Evolution by Hydrogenase Embedded in a Redox Polymer Film, Nat. Catal., 2021, 4, 251–258 CrossRef CAS.
- B. E. Logan and J. M. Regan, Microbial Fuel Cells—Challenges and Applications, Environ. Sci. Technol., 2006, 40, 5172–5180 CrossRef CAS.
- I. A. Vasiliadou, A. Berná, C. Manchon, J. A. Melero, F. Martinez, A. Esteve-Nuñez and D. Puyol, Biological and Bioelectrochemical Systems for Hydrogen Production and Carbon Fixation Using Purple Phototrophic Bacteria, Front. Energy Res., 2018, 6, 8818 Search PubMed.
- H. Nishiyama, T. Yamada, M. Nakabayashi, Y. Maehara, M. Yamaguchi, Y. Kuromiya, Y. Nagatsuma, H. Tokudome, S. Akiyama, T. Watanabe, R. Narushima, S. Okunaka, N. Shibata, T. Takata, T. Hisatomi and K. Domen, Photocatalytic solar hydrogen production from water on a 100-m2 scale, Nature, 2021, 598, 304–307 CrossRef CAS.
- K. Villa, J. R. Galán-Mascarós, N. López and E. Palomares, Photocatalytic water splitting: advantages and challenges, Sustainable Energy Fuels, 2021, 5, 4560–4569 RSC.
- J. Na, B. Seo, J. Kim, C. W. Lee, H. Lee, Y. J. Hwang, B. K. Min, D. K. Lee, H.-S. Oh and U. Lee, General technoeconomic analysis
for electrochemical coproduction coupling carbon dioxide reduction with organic oxidation, Nat. Commun., 2019, 10, 5193 CrossRef PubMed.
- S. Verma, S. Lu and P. J. A. Kenis, Co-electrolysis of CO2 and glycerol as a pathway to carbon chemicals with improved technoeconomics due to low electricity consumption, Nat. Energy, 2019, 4, 466–474 CrossRef CAS.
- A. R. Oliveira, C. Mota, C. Mourato, R. M. Domingos, M. F. A. Santos, D. Gesto, B. Guigliarelli, T. Santos-Silva, M. J. Romão and I. A. Cardoso Pereira, Toward the Mechanistic Understanding of Enzymatic CO2 Reduction, ACS Catal., 2020, 10, 3844–3856 CrossRef CAS.
- K. P. Nevin, T. L. Woodard, A. E. Franks, Z. M. Summers and D. R. Lovley, Microbial electrosynthesis: feeding microbes electricity to convert carbon dioxide and water to multicarbon extracellular organic compounds, mBio, 2010, 1, 1–4 CrossRef.
- G. Liu, F. Zheng, J. Li, G. Zeng, Y. Ye, D. M. Larson, J. Yano, E. J. Crumlin, J. W. Ager, L.-W. Wang and F. M. Toma, Investigation and mitigation of degradation mechanisms in Cu2O photoelectrodes for CO2 reduction to ethylene, Nat. Energy, 2021, 6, 1124–1132 CrossRef CAS.
-
P. Majumdar, M. K. Bera, D. Pant and S. Patra, Encyclopedia of Interfacial Chemistry, Elsevier, 2018, pp. 577–589 Search PubMed.
- W. Shin, S. H. Lee, J. W. Shin, S. P. Lee and Y. Kim, Highly selective electrocatalytic conversion of CO2 to CO at −0.57 V (NHE) by carbon monoxide dehydrogenase from Moorella thermoacetica, J. Am. Chem. Soc., 2003, 125, 14688–14689 CrossRef CAS.
- N. S. Weliwatte and S. D. Minteer, Photo-bioelectrocatalytic CO2 reduction for a circular energy landscape, Joule, 2021, 5, 2564–2592 CrossRef CAS.
- W. R. Leow, Y. Lum, A. Ozden, Y. Wang, D.-H. Nam, B. Chen, J. Wicks, T.-T. Zhuang, F. Li, D. Sinton and E. H. Sargent, Chloride-mediated selective electrosynthesis of ethylene and propylene oxides at high current density, Science, 2020, 368, 1228–1233 CrossRef CAS.
- Y. Lum, J. E. Huang, Z. Wang, M. Luo, D.-H. Nam, W. R. Leow, B. Chen, J. Wicks, Y. C. Li, Y. Wang, C.-T. Dinh, J. Li, T.-T. Zhuang, F. Li, T.-K. Sham, D. Sinton and E. H. Sargent, Tuning OH binding energy enables selective electrochemical oxidation of ethylene to ethylene glycol, Nat. Catal., 2020, 3, 14–22 CrossRef CAS.
- T. Burdyny and W. A. Smith, CO2 reduction on gas-diffusion electrodes and why catalytic performance must be assessed at commercially-relevant conditions, Energy Environ. Sci., 2019, 12, 1442–1453 RSC.
- D. DeSantis, B. D. James, C. Houchins, G. Saur and M. Lyubovsky, Cost of long-distance energy transmission by different carriers, iScience, 2021, 24, 103495 CrossRef.
- Fuel Cell Store, Water electrolysis system 5 kW, https://www.fuelcellstore.com/water-electrolysis-system-5kw, 2022.
-
G. Tsotridis and A. Pilenga, EU harmonised protocols for testing of low temperature water electrolysers. JRC122565 Report., Publications Office of the European Unio, 2021.
-
C. H. Rivkin, R. M. Burgess and W. J. Buttner, Regulations, Codes, and Standards (RCS) for Large-Scale Hydrogen Systems. NREL/CP-5400-70929, International Conference on Hydrogen Safety (ICHS 2017), 11–13 September 2017, Hamburg, Germany, 2017.
- Z.-Z. Niu, L.-P. Chi, R. Liu, Z. Chen and M.-R. Gao, Rigorous assessment of CO2 electroreduction products in a flow cell, Energy Environ. Sci., 2021, 14, 4169–4176 RSC.
- B. Chen, B. Li, Z. Tian, W. Liu, W. Liu, W. Sun, K. Wang, L. Chen and J. Jiang, Enhancement of Mass Transfer for Facilitating Industrial-Level CO2 Electroreduction on Atomic NiN4 Sites, Adv. Energy Mater., 2021, 11, 2102152 CrossRef CAS.
- M. H. Barecka, J. W. Ager and A. A. Lapkin, Techno-economic assessment of emerging CO2 electrolysis technologies, STAR Protoc., 2021, 2, 100889 CrossRef CAS.
- M. H. Barecka, M. Skiborowski and A. Górak, A novel approach for process retrofitting through process intensification: Ethylene oxide case study, Chem. Eng. Res. Des., 2017, 123, 295–316 CrossRef CAS.
- Y. C. Tan, K. B. Lee, H. Song and J. Oh, Modulating Local CO2 Concentration as a General Strategy for Enhancing C−C Coupling in CO2 Electroreduction, Joule, 2020, 4, 1104–1120 CrossRef CAS.
- V. Rodin, J. Lindorfer, H. Böhm and L. Vieira, Assessing the potential of carbon dioxide valorisation in Europe with focus on biogenic CO2, J. CO2 Util., 2020, 41, 101219 CrossRef CAS.
- F. Sabatino, A. Grimm, F. Gallucci, M. van Sint Annaland, G. J. Kramer and M. Gazzani, A comparative energy and costs assessment and optimization for direct air capture technologies, Joule, 2021, 5, 2047–2076 CrossRef CAS.
- A. Badgett, A. Feise and A. Star, Optimizing utilization of point source and atmospheric carbon dioxide as a feedstock in electrochemical CO2 reduction, iScience, 2022, 25, 104270 CrossRef CAS PubMed.
|
This journal is © The Royal Society of Chemistry 2023 |
Click here to see how this site uses Cookies. View our privacy policy here.