DOI:
10.1039/D2TC04784E
(Paper)
J. Mater. Chem. C, 2023,
11, 2494-2504
Optical temperature sensing with an Er3+, Yb3+ co-doped LaBMoO6 single crystal†
Received
10th November 2022
, Accepted 19th January 2023
First published on 19th January 2023
Abstract
Optical temperature sensing technology, especially the fluorescence intensity ratio (FIR) type sensor based on Er3+, Yb3+ co-doped up-conversion (UC) luminescent materials, presents numerous opportunities in the field of temperature detection. Various Er3+, Yb3+ co-doped fluorides and oxides have been explored for the application of temperature sensing. Most of these Er3+, Yb3+ co-doped sensing materials are phosphors, for which the high temperature phase and chemical stability is still challenging. The Er3+, Yb3+ co-doped oxide single crystal is a promising solution to explore temperature sensing materials with practical application ability. In this work, an Er3+, Yb3+ co-doped LaBMoO6 single crystal (LBMO-SC: Er3+, Yb3+) is grown through flux assisted spontaneous crystal growth technology. Compared with the Er3+, Yb3+ co-doped LaBMoO6 polycrystalline samples (LBMO-PC: Er3+, Yb3+), the LBMO-SC: Er3+, Yb3+ shows improved UC performance with enhanced light emission and prolonged luminescence lifetime. The UC performance improvement results from the more efficient energy transfer between Yb3+ and Er3+. The energy transfer efficiency from Yb3+ to Er3+ in the LBMO-PC: Er3+, Yb3+ powders sintered at 1000 °C for 15 h is 7.3%, while it is 29.7% in the LBMO-SC: Er3+, Yb3+. The strong UC luminescence of LBMO-SC: Er3+, Yb3+ extends the temperature detection range; the luminescence of 4S3/2 → 4I15/2 in LBMO-SC: Er3+, Yb3+ is still measurable even when the temperature reaches 570 K. The LBMO-SC: Er3+, Yb3+ has a maximum value of relative temperature sensitivity of 1.16% K−1 at 300 K. Finally, an optical fiber type temperature sensor with practical application capability is successfully fabricated by using LBMO-SC: Er3+, Yb3+ as the luminescence sensing medium.
1. Introduction
Since the traditional temperature detection technology has limited application in harsh environments, such as high temperature and strong electromagnetic environments, there is a growing demand for the temperature sensor based on optical probing technology.1–3 Among various optical probing technologies,4–7 the ratiometric fluorescence temperature probe based on the fluorescence intensity ratio (FIR) method has attracted much attention because of its advantages of self-reference and not being affected by the excitation source power fluctuation or other external factors.8–11 In general, the FIR method is based on the temperature dependent luminescence of a pair of thermally coupled energy levels (TCELs, energy gap: 200 cm−1 ≤ ΔE ≤ 2000 cm−1) in rare earth ions such as Nd3+, Eu3+ and Er3+.12–17 With a typical TCELs of 2H11/2 and 4S3/2 (ΔE ≈ 800 cm−1), Er3+-activated up-conversion (UC) materials are considered promising sensing media for temperature detection.14,15 Because of the large absorption cross section in the near-infrared band, the Yb3+ ion is often used as a sensitizer to transfer energy to the Er3+ ion, which can significantly improve the UC luminescence efficiency of Er3+ doped UC phosphors.18 The temperature sensing properties of many Er3+, Yb3+ co-doped materials such as fluorides and oxides have been studied. The Er3+, Yb3+ co-doped fluorides such as NaYF4 and CaF2 usually have a large temperature sensing range because of their high UC efficiency.19–22 Moreover, the Er3+, Yb3+ co-doped oxides such as CaWO4 and CaMoO4 are low cost and easy to prepare.23,24 Most of the above mentioned temperature sensing materials are phosphors, for which the phase and chemical stabilities at high temperature are challenging. Because of the advantages of mechanical and thermal stability, Er3+ doped single crystals with excellent optical properties are widely used in the field of laser and non-linear optics.25,26 These Er3+ doped large size single crystals such as borates and molybdates are excellent multi-wavelength laser gain media and self-frequency-doubling laser gain media.27,28 However, the application of single crystal materials in the field of optical temperature sensing has rarely been reported.
LaBMoO6 (LBMO) is a member of the molybdenum borate family with the formula of LnBMoO6 (Ln = La − Nd). The LBMO single crystal and phosphors have great potential for application in the optoelectronic field.29–33 Benefitted from its congruent melting habit, large size LBMO single crystals with high crystallinity could be rapidly grown from the melt. Zhao and Yu reported the growth of LBMO and Nd3+ doped LBMO single crystals through the Czochralski method and flux-assisted Czochralski method, respectively.31,32 The large size LBMO single crystal has excellent non-linear optical performance with a large value of second harmonic generation (SHG) coefficient.32 When doped with Nd3+, the LBMO crystal could be used as the gain medium for self-frequency-doubling lasers and self-Raman lasers.31,33 On the other hand, the LBMO polycrystalline phosphors doped with Er3+, Eu3+, Pr3+, Dy3+, Tb3+ and other rare earth ions are also widely studied. The asymmetric coordination environment of La3+ in LBMO facilitates the 4f–4f transition of rare earth ions.34 The phosphors synthesized by the traditional solid state reaction method display excellent luminescence; especially, the Er3+ doped LBMO (LBMO: Er3+) polycrystalline phosphor was considered to be a potential candidate for luminescence temperature detection.35 Although the study result of Hua reveals that the LBMO: Er3+ phosphor has a limited UC luminescence and temperature sensing ability, it can be concluded that the LBMO has good dopability for Er3+ and other rare earth ions. In summary, the LBMO has the superiority of single crystal growth and rare earth ion doping. However, the temperature sensing property of Er3+, Yb3+ co-doped LBMO single crystals has yet to be studied.
In this work, an Er3+ and Yb3+ co-doped LBMO single crystal (LBMO-SC: Er3+, Yb3+) was grown by using the flux method with B2O3 and Li2Mo2O7 as solvents. The doping concentration of Er3+ and Yb3+ in the LBMO-SC was optimized before the optical spectroscopy study. Under excitation with 980 nm light, the LBMO-SC: Er3+, Yb3+ shows intense green light emission with a luminescence lifetime of 142 μs. The UC luminescence performance of the LBMO-SC: Er3+, Yb3+ is better than that of the Er3+ and Yb3+ co-doped LBMO polycrystalline phosphors (LBMO-PC: Er3+, Yb3+), because of the more efficient energy transfer from Yb3+ to Er3+ in the single crystal. The energy transfer efficiency from Yb3+ to Er3+ in the LBMO-PC: Er3+, Yb3+ powders sintered at 1000 °C for 15 h is 7.3%, while it is 29.7% in the LBMO-SC: Er3+, Yb3+ sample. Benefiting from the higher energy transfer efficiency and better UC performance, the LBMO-SC: Er3+, Yb3+ samples have more advanced performance in temperature detection. The luminescence of 4S3/2 → 4I15/2 in LBMO-SC: Er3+, Yb3+ is still measurable even when the temperature reaches 570 K, making the LBMO-SC: Er3+, Yb3+ temperature detector theoretically work at 570 K. However, the light emission belonging to 4S3/2 → 4I15/2 transition of LBMO-PC: Er3+, Yb3+ completely quenches at 500 K. On the other hand, the maximum value of Sr of LBMO-SC: Er3+, Yb3+ is 1.16% K−1 at 300 K, which is slightly larger than that of the LBMO-PC: Er3+, Yb3+ sample (1.11% K−1). Finally, an optical fiber temperature sensor was fabricated with LBMO-SC: Er3+, Yb3+ as the luminescence sensing medium, which achieved accurate temperature sensing within 417 K. Our work demonstrates that LBMO-SC: Er3+, Yb3+ is a candidate material for optical temperature sensing.
2. Experimental
2.1 Materials
The raw materials of MoO3 (99.99%) and Li2CO3 (99.99%) were purchased from Sinopharm Chemical Reagent Co., Ltd (Shanghai China). Yb2O3 (99.999%), Er2O3 (99.999%) and H3BO3 (99.99%) were purchased from Aladdin Reagent Co., Ltd (Shanghai China). All raw materials were used without any further processing.
2.2 Growth of LBMO-SC: Er3+, Yb3+
Flux exploration.
We employed Li2Mo2O7 and B2O3 as the flux to grow LBMO single crystals. Li2Mo2O7 is commonly used as the flux to lower the melting point of rare earth molybdates. As a component of LBMO, B2O3 can not only decrease the melting point of the LBMO–Li2W2O7–B2O3 flux system, but also can adjust the viscosity and suppress the volatilization of the melt. To make the flux composition exploration more efficient, we adopted the mixture design technology to guide the flux exploration experiment. The mixture design is a useful tool for handling complex systems with three or more components, and hence it is widely used in the field of food processing and composite materials.36–38 Recently, the mixture design method was firstly developed for crystal growth in our lab.39,40 The mixture is characterized by the sum of the proportions of all components being 100%. This means that the only constrain in the mixture design experiment is x1 + x2 + x3 = 1, where x1, x2, and x3 are the mol contents of LBMO, B2O3 and Li2Mo2O7, respectively.41 In this work, a round of flux exploration experiment was conducted, and a regular region was used to design the composition distribution of test points. As seen in Fig. S1 (ESI†), there are 19 test points in the design diagram, and the composition of each test point is listed in Table S1 (ESI†). The distribution of test points in Fig. S1 (ESI†) is determined by the simplex lattice mixture method, the details of which are described in ref. 39. At the same time, the experimental response value (Result, y) was determined by observing the melting degree of the flux system at 1050 °C and the amount of the grown crystal after cooling. If the starting materials do not melt, the value of Result is set to zero. As the melting situation improves and the amount of grown crystals increases, the value of Result increases, but does not exceed 10.
The flux exploration experiment for crystal growth was carried out in a vertical furnace. To make the flux exploration result reliable, the total amount of the starting materials for each test experiment was set to be 10 g after all the volatile matter disappeared, which could be described by eqn (1)–(3):
|  | (1) |
|  | (2) |
|  | (3) |
After being weighed, the starting chemicals were mixed and fully ground in an agate mortar and then loaded into a platinum crucible. High temperature melting was performed in a homemade vertical furnace with an observation window. It was slowly heated to 1050 °C, and kept at this temperature for more than 10 h to make the chemicals react thoroughly. Then, it was cooled to 850 °C at a rate of 10 °C h
−1. During this procedure, it could be observed if the crystal growth takes place. When the temperature decreased to 850 °C, the flux was then rapidly dropped to room temperature.
Crystal growth.
After the flux exploration experiment, the optimal composition was chosen to grow LBMO single crystals (LBMO-SC) and Er3+, Yb3+ co-doped LBMO single crystals. The basic procedure of crystal growth is similar to that of the flux exploration test experiment. The total amount of the starting materials was set to 30 g after all the volatile matter disappeared. During the cooling process from 1050 °C to 850 °C, single crystals were grown out spontaneously from the melt. Typically, the crystal growth could be completed in 3 days. After the crucible was moved out from the vertical furnace, the transparent crystals with a size of centimeter level were collected and treated in aqueous solution with an ultrasonic machine to completely remove the attached flux.
2.3 Preparation of LBMO-PC: Er3+, Yb3+ powders
The polycrystalline powder of pure and Er3+, Yb3+ co-doped LBMO was prepared by the traditional solid state reaction method shown in Fig. S2 (ESI†). The starting raw material was weighed according to the stoichiometry in eqn (4) and then fully ground in an agate mortar. The obtained mixture was pressed into a tablet under a pressure of 10 MPa and transferred to an alumina crucible for sintering. Two rounds of sintering in a muffle furnace were performed. The mixture was firstly pre-sintered at 600 °C for 6 h, then re-ground and pressed to perform the second round of sintering. The products after two rounds of sintering were ground to powders and marked as LBMO-PC: Er3+, Yb3+ for further characterization. |  | (4) |
2.4 Phase and elemental analysis
The powder X-ray diffraction (PXRD) patterns were obtained on a RIGAKU-Miniflex II type X-ray diffractometer with Cu Kα radiation for phase identification. The morphology was characterized using a field emission scanning electron microscope (SEM SUPRA 55) equipped with an energy-dispersive X-ray spectrometer (EDS). The elemental concentration was measured by ICP-AES (Aglient 5110).
2.5 Optical spectroscopy measurement
The diffuse reflectance spectra (DRS) were measured in the wavelength range of 200–1100 nm using a UV-Visible-NIR spectrophotometer (PerkinElmer Lambda 950). The UC luminescence spectra and UC luminescence decay curves were measured on a FluoroMax-4 type fluorescence spectrophotometer (HORIBA Jobin Yvon Co.) equipped with a continuous xenon lamp (350 mW) and a pulsed 980 nm laser diode (LD) as pumping sources. The near infrared emission spectra and luminescence decay curves were measured on an FLS980 type spectrometer (Edinburgh) equipped with both continuous (450 W) and pulsed xenon lamps. For temperature-dependent UC luminescence measurements, the samples were placed on the thermal stage (THMS 600, Linkam Scientific Instruments) and excited with a continuous-wave (CW) 980 nm laser diode. Temperature-dependent spectra in the 298–578 K range were measured.
2.6 Computational details
The geometry optimization and electronic structures were performed using the Vienna Ab initio Simulation Package (VASP) according to density functional theory (DFT). We adopted the hybrid functional (HSE03) as exchange–correlations functional in the calculations to obtain the energy band and density of states information of the LBMO. The total potential energies of the doped and un-doped LBMO were calculated by using the PBE functional. The number of plane waves included in the basis sets was determined by a cutoff energy of 500 eV. For the Brillouin zone integration, a K-point sampling scheme of 2 × 6 × 2 Gamma scheme was used.
3. Results and discussion
3.1 Crystal growth and basic characterization of the LBMO-SC: Er3+, Yb3+ crystal
Flux exploration result and growth of LBMO-SC and LBMO-SC: Er3+, Yb3+ crystals.
The LBMO-SC crystal could be grown by using Li2Mo2O7 and B2O3 as the flux, as shown in Fig. 1a and b. The melting effect of the LBMO–Li2Mo2O7–B2O3 flux system can be displayed by a two-dimensional (2D) contour map, which is drawn based on the response surface method. The corresponding 3D contour map is shown in Fig. S3 (ESI†). The flux system melts thoroughly at 1050 °C when y exceeds 6. As shown in the contour maps, the flux system has a wide composition range, which is suitable for growing LBMO-SC and LBMO-SC: Er3+, Yb3+ crystals. Considering that there would be more LBMO-SC crystals grown out if there is more solute (LBMO) in the LBMO–Li2Mo2O7–B2O3 flux system, point A with the composition of LBMO
:
Li2Mo2O7
:
B2O3 = 0.667
:
0.167
:
0.167 (mol) is considered the optimal one to grow LBMO-SC and LBMO-SC: Er3+, Yb3+ crystals. This also reveals that the flux composition exploration could be accomplished by only one round of mixture design test. Fig. 1c shows the grown LBMO-SC: Er3+, Yb3+ crystals with a size of centimeter level. Excited by the 980 nm LD, the grown LBMO-SC: Er3+, Yb3+ crystals emit bright green light. The PXRD pattern of the obtained single crystals matches well with the standard one, as displayed in Fig. 1d.
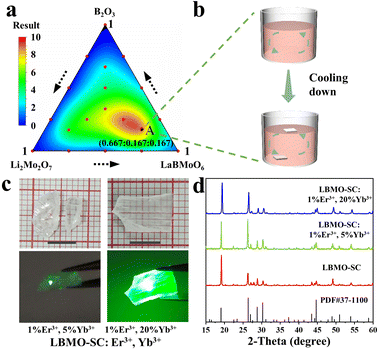 |
| Fig. 1 Two-dimensional contour map of the flux exploration result (a). Spontaneous growth of the LBMO-SC: Er3+, Yb3+ single crystal (b). Photos of the as-grown LBMO-SC: Er3+, Yb3+ single crystals (c). PXRD patterns of LBMO-SC and Er3+, Yb3+ doped LBMO-SC crystals (d). | |
Elemental and electronic properties of the LBMO-SC: Er3+, Yb3+ crystals.
Fig. 2a shows the SEM image of a piece of single crystal cut from the grown LBMO-SC: Er3+, Yb3+. The crystallinity of the samples is very high, and the growth stripes of the layered growth process are clearly visible. Fig. 2b exhibits the EDS mapping images of the LBMO-SC: Er3+, Yb3+ (Fig. S4, ESI† for LBMO-PC: Er3+, Yb3+). It can be clearly seen that each element is distributed uniformly in the particle, indicating that Er3+ and Yb3+ are successfully doped into the LBMO-SC. The DRS spectra of LBMO-SC and LBMO-SC: Er3+, Yb3+ are shown in Fig. 2c (Fig. S5, ESI† for the -PC sample). Both samples have a similar profile with the same absorption edge located at about 288 nm, revealing that the doping of Er3+ and Yb3+ does not change the band gap of LBMO. According to the Kubelka–Munk theory,42 it can be deduced that the optical band gap of LBMO is 4.3 eV. Meanwhile, the typical absorption peaks of the dopants appear in the DSR spectra of LBMO-SC: Er3+, Yb3+. Among them, the broad peak around 980 nm belongs to the 2F7/2 → 2F5/2 transition of Yb3+ and 4I15/2 → 4I11/2 transition of Er3+, and the sharp peaks at 510 nm and 620 nm are attributed to the transitions from the 4I15/2 state to the lower 2H11/2 and 4F9/2 states of Er3+.43 The DRS patterns shown in this figure confirm the successful doping of Er3+ and Yb3+ in the single crystal. The LBMO has a smooth bottom of conduction band and a smooth top of valence band, as shown in Fig. 2d. The calculated energy gap of LBMO is 4.79 eV,40 which is slightly larger than the measured optical band gap based on DRS. Considering the calculation error,44 we believe that the HSE03 functional can more accurately describe the band structure of LBMO. As can be seen from the density of states (DOS) diagram, the main contributors to the conduction band bottom and valence band top are Mo and O atoms, respectively. In addition, the change of the total potential energy of the LBMO system caused by the doping of Er3+ and Yb3+ is also calculated by the DFT method to analyze the site occupancy of dopants. Since Er3+, Yb3+ and La3+ have the same valence state and similar ionic radii, we believe that Er3+ and Yb3+ ions tend to preferentially occupy La sites. As shown in Fig. S6 (ESI†), La3+ occupies three lattice sites in the LBMO crystal, meaning that there are three different coordination environments for La3+. As seen from Table 1 and Table S2 (ESI†), the energy changes are 0.83eV, 0.94 eV, and 0.83 eV when Er3+ occupies three different La sites. The energy changes are 6.93 eV, 6.95 eV and 6.94 eV when Yb3+ substitutes for La3+ ions in three different sites. Since the doping of Er3+ and Yb3+ will increase the system energy, the segregation coefficients of these ions should be less than 1 in LBMO-SC. As seen in Table S3 (ESI†), the real contents of Er3+ and Yb3+ in the LBMO-SC: 1% Er3+, 20% Yb3+crystal are 0.16% and 0.89% in mol, respectively.
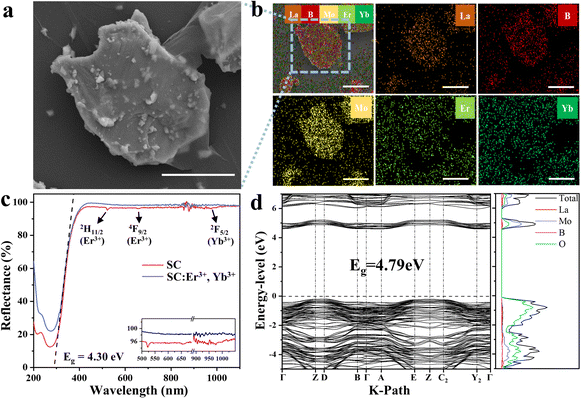 |
| Fig. 2 SEM image (a) and EDS element mapping images (b) of LBMO-SC: Er3+, Yb3+. The scale bar length is 5 μm. Diffuse reflectance spectra of LBMO-SC and LBMO-SC: Er3+, Yb3+ samples (c). Band and density of states diagram of LBMO calculated by VASP (d). | |
Table 1 Energy changes caused by the doping of Er3+ and Yb3+ occupying different cationic sites in the LBMO lattice
Dopants |
La1 site |
La2 site |
La3 site |
Er3+ |
0.83 eV |
0.94 eV |
0.83 eV |
Yb3+ |
6.93 eV |
6.95 eV |
6.94 eV |
3.2 UC spectra and luminescence dynamics of LBMO-SC: Er3+, Yb3+
Influence of doping concentration on the UC emission.
All the UC luminescence spectra of LBMO-SC: Er3+, Yb3+ samples shown in Fig. 3 display a typical profile of Er3+ emission, which consists of two intense green emission bands and one weak red emission band. The emission bands are assigned to the transitions from upper 2H11/2, 4S3/2 and 4I9/2 manifold states to the 4I15/2 ground state.45,46 All the green emission bands split into three peaks due to the influence of local crystal field.47,48 Since the green emission intensity far exceeds the red one, all samples exhibit bright green emission under excitation with a 980 nm laser (Fig. 1c).
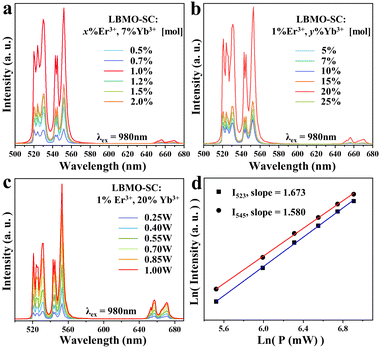 |
| Fig. 3 UC luminescence spectra of LBMO-SC: x% Er3+, 7% Yb3+ samples (a) and LBMO-SC: 1% Er3+, y% Yb3+ samples (b). Pumping power dependent UC luminescence spectra (c) and plot of log(I) vs. log(P) (d) of LBMO-SC: 1% Er3+, 20% Yb3+, where I is the UC emission intensity, and P is the pumping power. | |
To avoid the self-energy transfer induced luminescence quenching,49,50 the doping concentrations of Er3+ and Yb3+ in LBMO-SC have been optimized. As seen in Fig. 3a, the UC luminescence emission intensity of LBMO-SC: x% Er3+, 7% Yb3+ samples increases first with the increase of Er3+ concentration, reaching the maximum at x = 1. Then, it decreases when the content of Er3+ goes upwards 1 percent. This may be due to the enhancement of the non-radiative energy transfer process and the cross-relaxation between Er3+ ions.51Fig. 3b shows the UC luminescence spectra of LBMO-SC: 1% Er3+, y% Yb3+ samples. Similarly, the UC luminescence intensity of LBMO-SC: 1% Er3+, y% Yb3+ samples increases with the rise of Yb3+ content until the maximum intensity is reached when y = 20. Therefore, the optimal doping concentration of the LBMO single crystal is 1% for Er3+ and 20% for Yb3+, respectively. The phase of all single crystal samples mentioned above is consistent with the standard pattern, as shown in Fig. S7 (ESI†). Furthermore, the influence of Yb3+ on the luminescence of Er3+ has also been studied by recording the luminescence decay curves from the 2H11/2 state of Er3+. As displayed by Fig. S8 (ESI†), all the luminescence decay curves of LBMO-SC: 1% Er3+, y% Yb3+ samples could be fitted by a first-order exponential function. The lifetime of Er3+ amplifies from 96 μs to 142 μs as the content of Yb3+ increases from 5% to 20%, indicating that the UC luminescence quantum efficiency of the Er3+, Yb3+ co-doped LBMO-SC reaches the maximum when Yb3+ ions are at the optimal content.
UC luminescence dynamics in the Er3+, Yb3+ doped LBMO-SC.
In order to illustrate the UC emission mechanism of Er3+, the pumping power-dependent UC emission spectra were studied. As shown in Fig. 3c and d, the UC emission intensities of LBMO-SC: 1% Er3+, 20% Yb3+ increase with the rise of pumping power. Generally, the emission intensity of the UC system is proportional to the n-th power of the pumping power, which can be expressed as follows:43,52where n is the number of the pumping photons absorbed by each emitted photon in the UC process, I is the emission intensity and P is the power of pumping light. Fig. 3d shows the natural logarithmic plots of the emission intensity as a function of the pumping power corresponding to the 2H11/2 and 4S3/2 energy levels of the LBMO-SC: 1% Er3+, 20% Yb3+ sample. Both the plots exhibit a good linearity with the value of n equal to 1.673 (2H11/2), and 1.580 (4S3/2), respectively. Similar results were obtained for LBMO-PC: 0.7% Er3+, 10% Yb3+, as shown in Fig. S9 (ESI†). The results reveal that the UC emission in Er3+, Yb3+ co-doped LBMO-SC and LBMO-PC samples involves a two-photon process.52,53 Usually, the synergistic effect when the sensitizer transfers energy to the activator makes the value of n less than 2.54 Fig. S10 (ESI†) illustrates the possible electronic transition dynamics between Er3+ and Yb3+ in the UC luminescence process. When the Er3+, Yb3+ co-doped LBMO is excited with a 980 nm laser, Yb3+ will be excited from the ground state 2F7/2 to the upper 2F5/2 state. Meanwhile, Er3+ is excited to the 4F7/2 state after two consecutive energy absorptions due to the energy transfer from Yb3+ to Er3+. Afterwards, Er3+ will relax to the lower 2H11/2, 4S3/2 and 4F9/2 energy levels through a series of non-radiative transitions and relax to the ground state through a radiative transition pathway, resulting in the emission of green and red light. This is the typical two-photon UC luminescence of Er3+.43,52,53
3.3 Mechanism of UC emission enhancement from the polycrystalline sample to the single crystal
Serial Er3+, Yb3+ co-doped LBMO-PC samples were synthesized to study the difference of UC luminescence between the LBMO-PC and LBMO-SC. Based on the optimization of sintering time, sintering temperature and doping concentration (Fig. S11–S15, ESI†), the LBMO-PC: 0.7% Er3+, 10% Yb3+ sample sintered at 1000 °C for 15 h has the most intense UC emission. Meanwhile, the UC emission intensity has a positive dependence on the sintering time when it prolongs from 5 h to 15 h. But, the UC emission intensity of Er3+, Yb3+ co-doped LBMO-PC samples is weaker than that of the LBMO-SC: 1%Er3+, 20% Yb3+ crystal, as shown in Fig. 4a. The luminescence decay curves have a similar evolution trend, as shown in Fig. S16 (ESI†). Among these samples, the LBMO-SC: 1%Er3+, 20% Yb3+ has the longest luminescence lifetime of 141 μs, which is about 7.7% larger than that of the polycrystalline sample sintered at 1000 °C for 15 h. This means that the LBMO-SC: 1%Er3+, 20% Yb3+ has the highest UC luminescence quantum efficiency among these samples displayed in this figure.
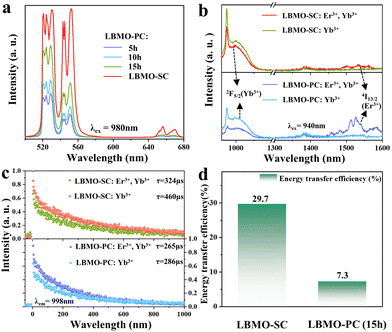 |
| Fig. 4 UC luminescence spectra of LBMO-SC: 1% Er3+, 20% Yb3+ and LBMO-PC: 0.7% Er3+, 10% Yb3+ samples sintered at 1000 °C for different times (a). Luminescence (b) and luminescence decay curves (c) of LBMO-SC: 1% Er3+, 20% Yb3+, LBMO-SC: 20% Yb3+, LBMO-PC: 0.7% Er3+, 10% Yb3+ and LBMO-PC: 10% Yb3+. Histogram of the energy transfer efficiency between Er3+ and Yb3+ in LBMO-SC: 1% Er3+, 20% Yb3+ and LBMO-PC: 0.7%Er3+, 10% Yb3+ (d). | |
The UC emission improvement from the Er3+, Yb3+ co-doped LBMO-PC sample to the Er3+, Yb3+ co-doped LBMO-SC crystal results from the enhanced energy transfer efficiency between Yb3+ and Er3+. Fig. 4b shows the luminescence spectra of LBMO-SC: 20% Yb3+ and LBMO-SC: 1% Er3+, 20% Yb3+ crystals. When excited with 940 nm light, the LBMO-SC: 20%Yb3+ sample displays a broadband emission with a peak at about 998 nm, which is attributed to the transition from the 2F5/2 manifold state to the ground state 2F7/2 of Yb3+.45,55 The light emission of 2F5/2 → 2F7/2 transition decreases in the presence of Er3+, while the emission with a wavelength ranging from 1450 nm to 1600 nm caused by the transition 4I13/2 → 4I15/2 of Er3+ appears.56 The decrease of 2F5/2 → 2F7/2 transition of Yb3+ and appearance of 4I13/2 → 4I15/2 of Er3+ reveal that energy transfer between Er3+ and Yb3+ takes place in the LBMO-SC: 1%Er3+, 20%Yb3+ sample. The energy transfer between Er3+ and Yb3+ is confirmed by the change of Yb3+ luminescence lifetime, as shown in Fig. 4c. Since the luminescence from the 2F5/2 manifold state of Yb3+ decays in a non-single exponential way, the average luminescence lifetime (τavg) of the 2F5/2 manifold state of Yb3+ in LBMO-SC: 20%Yb3+ and LBMO-SC: 1%Er3+, 20%Yb3+ samples was calculated according to the following formula:7,43,57
|  | (6) |
where
t is the time and
I(
t) is the emission intensity at time
t. The luminescence lifetime is fitted to be 460 μs for the LBMO-SC: 20%Yb
3+ sample, while it turns to be 324 μs for the LBMO-SC: 1%Er
3+, 20%Yb
3+. The shrinkage of lifetime of the
2F
5/2 manifold state of Yb
3+ is caused by the energy transfer mentioned above. Furthermore, the energy transfer efficiency (
η) from the sensitizer Yb
3+ to the activator Er
3+ could be calculated by the following formula:
58 |  | (7) |
where
τ1 and
τ2 are the lifetimes of the sensitizer in the absence and presence of the activator, respectively. The calculated
η value is 29.7% for the LBMO-SC: 1%Er
3+, 20%Yb
3+ sample. The energy transfer between Er
3+ and Yb
3+ also takes place in the LBMO-PC sample, which is demonstrated by
Fig. 4b and c. The typical light emission of Er
3+ at 1450–1600 nm appears in the LBMO-PC: 0.7% Er
3+, 10% Yb
3+ sample. Meanwhile, the co-doping of Er
3+ makes the Yb
3+ relax faster from the
2F
5/2 manifold state, with the lifetime reduced from 286 μs to 265 μs. Hence, the energy transfer efficiency from Yb
3+ to Er
3+ in LBMO-PC: 0.7%Er
3+, 10%Yb
3+ samples sintered at 1000 °C for 15 h is 7.3%. As displayed in
Fig. 4d, the energy transfer efficiency from Yb
3+ to Er
3+ ions in the LBMO-SC sample is more than four times that of the LBMO-PC sample sintered at 1000 °C for 15 h. It can be concluded that the single crystal sample exhibits the best UC luminescence performance due to its more efficient energy transfer between Er
3+ and Yb
3+.
Both of UC emissions of the Er3+, Yb3+ co-doped LBMO-PC and LBMO-SC involve a two-photon UC luminescence process. In the pumping procedure of a typical two-photon UC luminescence shown in Fig. S10 (ESI†), Yb3+ ions at the excited 2F5/2 state transfer energy to the Er3+ ion at the 4I11/2 state, making Er3+ ions further excited to the upper 4F7/2 state. As seen from the figure, the energy difference between 2F5/2 and 2F7/2 of Yb3+, energy difference between 4I11/2 and 4I15/2 of Er3+ and energy difference between 4F7/2 and 4I15/2 of Er3+ are similar to each other. This is the basis for the energy transfer between them. In fact, the slight mismatch between the energy levels of 2F5/2 of Yb3+ and 4I11/2 of Er3+ indicates that the UC luminescence of Yb3+, Er3+ co-doped materials is a phonon-assisted process, even if the amount of required phonons is small. Compared with the single crystal, the polycrystalline samples have grain boundaries in them. From the perspective of materials science, the grain boundary is a typical kind of planar defect that destroys the uniform orientation of grains. Meanwhile, atoms in the grain boundaries are arranged in an intermediate state between amorphous and crystalline. Normally, the dopants segregated from the crystal grains will aggregate in the boundaries, making the atoms in the grain boundary in a higher energy state. Therefore, the phonons in polycrystalline samples will be scattered by the grain boundaries, leading to the possible distortion of the lattice vibration dispersion mode. On the other hand, the energy transfer between Yb3+ and Er3+ usually happens under the driving force of quadrupole–quadrupole and exchange interactions.59–61 Although the interaction has nothing to do with the charge transfer or photon propagation, the transitions between electric quadrupoles are modulated by the distance between rare earth ions.62 Because of the existence of grain boundaries, the interaction between Er3+ and Yb3+ in polycrystalline samples may also be affected. Hence, the different condensed state of single crystal and polycrystalline powders results in the difference of energy transfer efficiency between Er3+ and Yb3+.
3.4 Luminescence temperature sensing performance of LBMO-SC: 1%Er3+, 20%Yb3+
The enhancement of UC emission in LBMO-SC: 1%Er3+, 20%Yb3+ expands the temperature sensing range. Fig. 5a and b shows the temperature dependent UC luminescence spectra of LBMO-SC: 1%Er3+, 20%Yb3+ and LBMO-PC: 0.7%Er3+, 10%Yb3+ samples sintered at 1000 °C for 15 h. All the luminescence intensities in these figures are normalized. A competition between thermal occupying and thermal quenching of the TCELs system is observed in these flame diagrams. As the temperature rises, the optical emission during 519–535 nm that belongs to the 2H11/2 → 4I15/2 transition of Er3+ of both samples increases gradually, while the optical emission of 4S3/2 → 4I15/2 transition ranging from 542 nm to 556 nm decreases. This result indicates that the rise of temperature promotes the population from the 4S3/2 energy level to the higher 2H11/2 energy level in Er3+, which is a typical procedure in the TCELs systems. As the temperature continues to rise, all emission intensities gradually decrease because of the thermal quenching of the whole TCELs system. Generally, the UC emission intensity of LBMO-SC:1% Er3+, 20% Yb3+ (Fig. 5a) is higher than that of the LBMO-PC:0.7% Er3+, 10% Yb3+ samples sintered at 1000 °C for 15 h (Fig. 5b) throughout the measured temperature range. What's more, the UC emission intensity of 4S3/2 → 4I15/2 transition in the single crystal sample drops slower as the temperature rises. Fig. 5c shows the integrated emission intensities of the 4S3/2 → 4I15/2 transition displayed in Fig. 5a and b. It can be seen that at room temperature, the emission intensity of the single crystal sample is much larger than that of the polycrystalline sample. With the increase of temperature, the emission intensity decreases gradually. However, in the range of 300–500 K, the emission intensity of the single crystal sample is always larger than that of the polycrystalline samples. As shown in Fig. 5a, the luminescence in the 542–556 nm range (4S3/2 → 4I15/2) of the single crystal sample is still measurable when the temperature reaches 570 K, while the luminescence of the three polycrystalline sample is completely quenched at about 500 K (Fig. 5b and Fig. S17, ESI†). This undoubtedly demonstrates that the Er3+, Yb3+ co-doped LBMO-SC sample has a broader theoretical working range of temperature sensing.
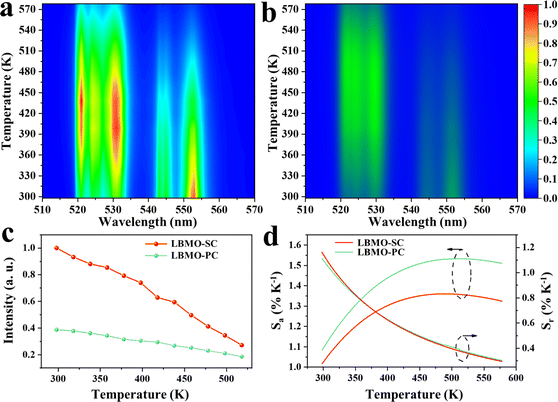 |
| Fig. 5 Flame diagram of the UC luminescence of LBMO-SC: 1% Er3+, 20% Yb3+ (a) and LBMO-PC: 0.7% Er3+, 10% Yb3+ samples (b). Evolution of the integrated luminescence intensity of the 4S3/2 → 4I15/2 transition versus temperature (c) and temperature dependent Sa and Sr (d) of LBMO-SC: 1% Er3+, 20% Yb3+ and LBMO-PC: 0.7% Er3+, 10% Yb3+. | |
Since the particle population of 2H11/2 and 4S3/2 of Er3+ follows the Boltzmann distribution law,43,63 the FIR of 2H11/2 and 4S3/2 states of Er3+ can be described as follows:11
| 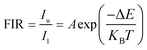 | (8) |
where
Iu and
Il are the UC emission intensities of the upper (
2H
11/2) and lower (
4S
3/2) energy levels, respectively; Δ
E is the energy gap between the TCELs;
KB and
T denote the Boltzmann constant and absolute temperature, respectively;
A is a pre-exponential coefficient affected by factors such as the intensity of such as spontaneous emission transition rate and fluorescence branch ratio, which can be expressed as
|  | (9) |
where
vi is the frequency of the radiation,
βij is the luminescence branching ratio,
Aij is the spontaneous radiation transition rate and
gi is the level degeneracy. The parameter
A is generally regarded as a constant.
64 Fig. S18 (ESI
†) shows the temperature-dependent FIR values for the LBMO-SC: 1% Er
3+, 20% Yb
3+ and LBMO-PC: 0.7% Er
3+, 10% Yb
3+ samples, both of which are well fitted by
eqn (8). Besides the temperature sensing range, the temperature sensitivity coefficients such as absolute temperature sensitivity coefficient
Sa and relative temperature sensitivity
Sr are crucial parameters to estimate the temperature sensing performance of optical thermometry. The values of
Sa and
Sr are calculated according to the following equations:
63,65 | 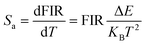 | (10) |
| 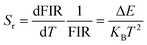 | (11) |
Fig. 5d displays the temperature dependent Sa and Sr values of LBMO-SC: 1% Er3+, 20% Yb3+ and LBMO-PC: 0.7% Er3+, 10% Yb3+ sintered at 1000 °C for 15 h. The maximum value of Sr for LBMO-PC:0.7% Er3+, 10% Yb3+ sintered at 1000 °C for 15 h is 1.11% K−1 at 300 K. Although the LBMO-SC: 1% Er3+, 20% Yb3+ has a slightly less value of Sa than the polycrystalline sample, the value of Sr of the single crystal is similar to that of the polycrystalline sample. As shown in the figure, the LBMO-SC: 1% Er3+, 20% Yb3+ has a maximum Sr of 1.16% K−1 at 300 K.
It can be concluded that using the LBMO-SC sample instead of the -PC sample as a temperature sensing material rarely influences the relative sensitivity of their luminescence temperature sensing, but it has a positive impact on expanding the operating temperature range.
3.5 Establishment of the temperature sensing device based on the LBMO-SC: 1% Er3+, 20% Yb3+ crystal
Because of the more intense UC luminescence, the LBMO-SC: 1% Er3+, 20% Yb3+ shows the optimal comprehensive performance in temperature sensing. Hence, a luminescence temperature sensing device was designed and assembled by using the LBMO-SC:1% Er3+, 20% Yb3+ as the temperature sensing medium. As shown in Fig. 6a, the device consists of three main parts: a detector with LBMO-SC: 1% Er3+, 20% Yb3+ as the sensing medium, a pumping source of 980 nm laser and a light collector based on a smart spectrometer. The detector, pumping source and light collector are connected by a relay station composed of three connecters and a beam splitter through high temperature resistant optical fibers. The detector consists of a ceramic sleeve encapsulating a piece of LBMO-SC: 1% Er3+, 20% Yb3+ crystal. After encapsulation, the optical fiber was inserted into the sleeve and then firmly bonded by using an inorganic type high temperature resistant glue. In order to simplify the equipment and reduce the cost, only one optical fiber is used to set up the optical path. The 980 nm pumping light can get through the beam splitter directly and go forwards to the detector. Once the detector is excited with a 980 nm laser, the emitted green light returns to the light collector across the relay station. Because of the use of the beam splitter, the emitted green light can only go to the optical collector along the connector 3. The spectral data were processed using the spectrometer (Ocean Optics). The practical working performance of the sensing device was tested in a homemade semi-closed vertical furnace and on the open surface of a heating plate, as shown in Fig. 6b and c. The luminescence changes are visualized with the increase of temperature. The spectral data tested in a vertical furnace are shown in Fig. 6d. Since the accuracy of the spectrometer used in practical applications is lower than that of the laboratory spectrometer, when the temperature is higher than 453 K, the luminescence data from the 4S3/2 level can hardly be detected. This result suggests that the real operating temperature range of the detector is smaller than the theoretical operating temperature range of the LBMO-SC: 1% Er3+, 20% Yb3+ crystal, since the attenuation of optical signal is inevitable in the real operation of the detector.
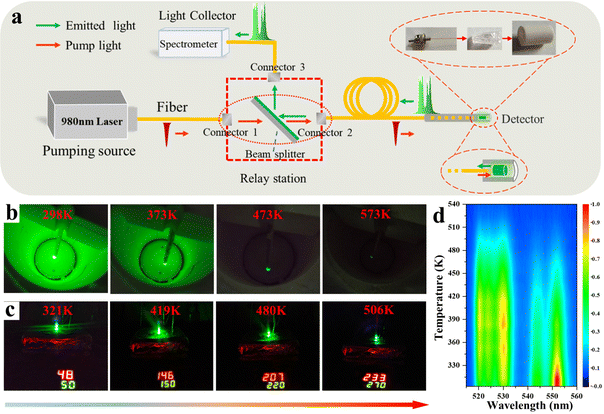 |
| Fig. 6 (a) Simple schematic diagram of the device structure. Photo of actual operation (b) in a vertical heater in the temperature range 298–578 K and (c) on an open heating table in the temperature range of 321–506 K; (d) spectrogram of actual operation. | |
What's more, the sensitivity of the luminescent temperature detector was studied to estimate its real performance. Fig. S19a (ESI†) shows the FIR value obtained by fitting the spectral data in Fig. 6d. The data can be well fitted according to eqn (8) when the temperature is lower than 453 K, meaning that the sensing device can accurately detect the ambient temperature, while the FIR data become dispersed when it is higher than 453 K, which is mainly caused by the signal attenuation in the optical fiber. Although the actual working temperature range is not as wide as the theoretical one, the sensitivity of the temperature sensing device remains at a high level. Fig. S19b (ESI†) shows the temperature dependent Sa and Sr calculated according to eqn (10) and (11). The sensing device has a maximum Sr of 1.6% K−1 at 303 K. The results show that the temperature measurement accuracy of the optical temperature detector does not decrease compared with the theoretical data. In conclusion, the precision of the prepared temperature sensing device is basically consistent with the theoretical data measured in the laboratory. However, problems such as light collection accuracy decrease and signal loss in the light path narrow down the sensing range of temperature. This indicates that it is very important to improve the light emission intensity as much as possible in order to achieve the large-scale application of optical temperature sensing devices. And when using the ratiometric temperature measurement principle, it is especially necessary to increase the luminescence intensity of the lower thermal couple energy level to prevent data dispersion and extend the temperature sensing range.
4. Conclusions
In summary, the Er3+, Yb3+ co-doped LBMO single crystal was grown and studied as a luminescent temperature sensing material. The LBMO-SC: Er3+, Yb3+ crystal was grown by using the flux method with B2O3 and Li2Mo2O7 as solvents. Compared with the Er3+, Yb3+ co-doped LaBMoO6 polycrystalline samples (LBMO-PC: Er3+, Yb3+), the LBMO-SC: Er3+, Yb3+ shows improved UC performance with enhanced light emission and prolonged luminescence lifetime. The UC performance improvement from polycrystalline samples to the single crystal results from the more efficient energy transfer between Yb3+ and Er3+ when the crystallinity increases. The energy transfer efficiency from Yb3+ to Er3+ in the LBMO-PC: Er3+, Yb3+ powders sintered at 1000 °C for 15 h is 7.3%, while it is 29.7% in the LBMO-SC: Er3+, Yb3+. The strong UC luminescence of LBMO-SC: Er3+, Yb3+ enlarges the temperature detection range. The light emission belonging to the 4S3/2 → 4I15/2 transition of Er3+ in LBMO-PC: Er3+, Yb3+ completely quenches at 500 K, but the luminescence of 4S3/2 → 4I15/2 in LBMO-SC: Er3+, Yb3+ is still measurable even when the temperature reaches 570 K. Meanwhile, the update from the polycrystalline sample to the single crystal rarely influences the relative sensitivity of temperature sensing. The maximum values of Sr of LBMO-SC: Er3+, Yb3+ and LBMO-PC: Er3+, Yb3+ samples sintered at 1000 °C for 15 h are 1.16% K−1 and 1.11% K−1, respectively. The improvement of UC luminescence and temperature sensing performance by using single crystals as sensing media provides guidance to explore more efficient FIR type luminescence temperature sensors. Finally, an optical fiber temperature sensor with practical application capability was fabricated by using LBMO-SC: Er3+, Yb3+ as the luminescence sensing medium.
Author contributions
XL: investigation, data curation, writing – original draft. BB: data curation. JY: resources, formal analysis. GW: validation. YH: resources. LL: resources, supervision, writing – review & editing. YY: resources, supervision.
Conflicts of interest
There are no conflicts to declare.
Acknowledgements
The authors greatly acknowledge the support from the National Natural Science Foundation of China (No. 51972061, U1905215), the National Key Research and Development Program/Key Scientific Issues of Transformative Technology (2020YFA0710303) and the Natural Science Foundation of Fujian Province, China (2022J01088).
Notes and references
- C. D. Brites, P. P. Lima, N. J. Silva, A. Millan, V. S. Amaral, F. Palacio and L. D. Carlos, Nanoscale, 2012, 4, 4799–4829 RSC.
- C. D. S. Brites, S. Balabhadra and L. D. Carlos, Adv. Optical Mater., 2018, 7, 1801239 CrossRef.
- X. Wang, Q. Liu, Y. Bu, C.-S. Liu, T. Liu and X. Yan, RSC Adv., 2015, 5, 86219–86236 RSC.
- Y. Chen, J. He, X. Zhang, M. Rong, Z. Xia, J. Wang and Z. Q. Liu, Inorg. Chem., 2020, 59, 1383–1392 CrossRef CAS PubMed.
- Z. Cai, S. Kang, X. Huang, X. Song, X. Xiao, J. Qiu and G. Dong, J. Mater. Chem. C, 2018, 6, 9932–9940 RSC.
- L. Li, F. Qin, L. Li, H. Gao and Z. Zhang, J. Mater. Chem. C, 2019, 7, 7378–7385 RSC.
- M. Wu, D. Deng, F. Ruan, B. Chen and S. Xu, Chem. Eng. J., 2020, 396, 125178 CrossRef CAS.
- L. Marciniak, K. Elzbieciak-Piecka, K. Kniec and A. Bednarkiewicz, Chem. Eng. J., 2020, 388, 124347 CrossRef CAS.
- M. Runowski, S. Goderski, D. Przybylska, T. Grzyb, S. Lis and I. R. Martín, ACS Appl. Nano Mater., 2020, 3, 6406–6415 CrossRef CAS.
- Ł. Marciniak, A. Bednarkiewicz, D. Hreniak and W. Strek, J. Mater. Chem. C, 2016, 4, 11284–11290 RSC.
- H. Suo, X. Zhao, Z. Zhang, Y. Wang, J. Sun, M. Jin and C. Guo, Laser Photonics Rev., 2020, 15, 2000319 CrossRef.
- S. Senapati and K. K. Nanda, J. Mater. Chem. C, 2017, 5, 1074–1082 RSC.
- A. A. Kalinichev, M. A. Kurochkin, E. V. Golyeva, A. V. Kurochkin, E. Lähderanta, M. D. Mikhailov and I. E. Kolesnikov, J. Lumin., 2018, 195, 61–66 CrossRef CAS.
- G. Xiang, Q. Xia, X. Liu and X. Wang, Dalton Trans., 2020, 49, 17115–17120 RSC.
- M. Jia, Z. Sun, F. Lin, B. Hou, X. Li, M. Zhang, H. Wang, Y. Xu and Z. Fu, J. Phys. Chem. Lett., 2019, 10, 5786–5790 CrossRef CAS PubMed.
- G. Xue, X. Chen, C. Zheng, G. Wang and L. Li, Chin. J. Struct. Chem., 2020, 39, 301–309 CAS.
- F. Huang, X. Li, Z. Zhang, Z. Jiang, G. Wang, L. Li and Y. Yu, Chin. J. Struct. Chem., 2022, 41, 2204068–2204074 CAS.
- F. Auzel, Chem. Rev., 2004, 104, 139–173 CrossRef CAS PubMed.
- D. T. Klier and M. U. Kumke, RSC Adv., 2015, 5, 67149–67156 RSC.
- J. Cai, X. Wei, F. Hu, Z. Cao, L. Zhao, Y. Chen, C. Duan and M. Yin, Ceram. Int., 2016, 42, 13990–13995 CrossRef CAS.
- Y. Huang, S. Peng, J. Liu, Z. Feng, W. Huang and T. Liao, Appl. Opt., 2022, 61, 202–207 CrossRef CAS PubMed.
- M. Jin, J. Xiang, Y. Chen, C. Chen, H. Suo, Z. Zhang, J. Sun, X. Zhao and C. Guo, J. Lumin., 2022, 244, 118692 CrossRef CAS.
- W. Xu, Y. Hu, L. Zheng, Z. Zhang, W. Cao, H. Liu and X. Wu, J. Lumin., 2019, 208, 415–423 CrossRef CAS.
- F. Huang, Y. Gao, J. Zhou, J. Xu and Y. Wang, J. Alloys Compd., 2015, 639, 325–329 CrossRef CAS.
- Y. Chen, Y. He, Q. Zhang, J. Xu, Z. Fang, S. Ding, R. Dou, W. Liu and S. Yin, J. Alloys Compd., 2020, 814, 152267 CrossRef CAS.
- W. Ma, X. Qian, J. Wang, J. Liu, X. Fan, J. Liu, L. Su and J. Xu, Sci. Rep., 2016, 6, 36635 CrossRef CAS PubMed.
- Y. Chen, Y. Huang, Z. Lin and Y. Huang, OSA Continuum, 2019, 2, 3598–3603 CrossRef CAS.
- Y. Yu, K. Shao, X. Zhu, X. Zhang, H. Qiu, S. Wu and G. Wang, J. Lumin., 2021, 237, 118194 CrossRef CAS.
- D. Zhao, W. D. Cheng, H. Zhang, S. P. Hang and M. Fang, Dalton Trans., 2008, 3709–3714 RSC.
- P. Becker, L. Bohatý, H. Rhee, H. J. Eichler, J. Hanuza and A. A. Kaminskii, Laser Phys. Lett., 2008, 5, 114–121 CrossRef.
- W. Zhao, L. Zhang, G. Wang, M. Song, Y. Huang and G. Wang, Opt. Mater., 2009, 31, 849–853 CrossRef CAS.
- Y. Yu, L. Li, Z. Lin and G. Wang, CrystEngComm, 2013, 15, 5245–5249 RSC.
- P. Becker, B. van der Wolf, L. Bohatý, J. Dong and A. A. Kaminskii, Laser Phys. Lett., 2008, 5, 737–745 CrossRef CAS.
- E. Kaewnum, N. Wantana and J. Kaewkhao, Mater. Today: Proc., 2018, 5, 13940–13947 CAS.
- Y. Hua, P. Du and J. Su Yu, Mater. Res. Bull., 2018, 107, 314–320 CrossRef CAS.
- S. Saoudi, N. Chammem, I. Sifaoui, I. A. Jimenez, J. Lorenzo-Morales, J. E. Pinero, M. Bouassida-Beji, M. Hamdi and L. Bazzocchi I, J. Sci. Food Agric., 2017, 97, 3300–3311 CrossRef CAS PubMed.
- X.-Y. Hu, K. Zhou, B.-Y. Chen and C.-T. Chang, Appl. Surf. Sci., 2016, 362, 329–334 CrossRef CAS.
- T. Skopak, P. Hee, Y. Ledemi, M. Dussauze, S. Kroeker, T. Cardinal, E. Fargin and Y. Messaddeq, J. Non-Cryst. Solids, 2017, 455, 83–89 CrossRef CAS.
- L. Li, Y. Lin, L. Zhang, Q. Cai and Y. Yu, Cryst. Growth Des., 2017, 17, 6541–6549 CrossRef CAS.
- L. Li, F. Huang, Y. Shi, Z.-Z. Luo, G.-Q. Wang, X.-X. Li, B. Li, L. Zhang, Y. Yu, Y.-N. Feng, C. Yang, Y. Yu and K. R. Poeppelmeier, J. Am. Chem. Soc., 2022, 144, 11822–11830 CrossRef CAS PubMed.
- N. D. Austin, N. V. Sahinidis and D. W. Trahan, Chem. Eng. Sci., 2017, 159, 93–105 CrossRef CAS.
- X. Zhang, L. Zhang, Y. Xu, X. Wu, S. Yin, C. Zhong and H. You, Inorg. Chem., 2022, 61, 7597–7607 CrossRef CAS PubMed.
- Y. Jiang, Y. Tong, S. Chen, W. Zhang, F. Hu, R. Wei and H. Guo, Chem. Eng. J., 2021, 413, 127470 CrossRef CAS.
- J. Hafner, J. Comput. Chem., 2008, 29, 2044–2078 CrossRef CAS PubMed.
- G. Bai, M.-K. Tsang and J. Hao, Adv. Funct. Mater., 2016, 26, 6330–6350 CrossRef CAS.
- B. Cao, Y. Bao, Y. Liu, J. Shang, Z. Zhang, Y. He, Z. Feng and B. Dong, Chem. Eng. J., 2020, 385, 123906 CrossRef CAS.
- B. P. Kore, A. Kumar, L. Erasmus, R. E. Kroon, J. J. Terblans, S. J. Dhoble and H. C. Swart, Inorg. Chem., 2018, 57, 288–299 CrossRef CAS PubMed.
- Q. Xiao, Y. Zhang, H. Zhang, G. Dong, J. Han and J. Qiu, Sci. Rep., 2016, 6, 31327 CrossRef CAS PubMed.
- N. J. Johnson, S. He, S. Diao, E. M. Chan, H. Dai and A. Almutairi, J. Am. Chem. Soc., 2017, 139, 3275–3282 CrossRef CAS PubMed.
- W. Wei, G. Chen, A. Baev, G. S. He, W. Shao, J. Damasco and P. N. Prasad, J. Am. Chem. Soc., 2016, 138, 15130–15133 CrossRef CAS PubMed.
- D. He, C. Guo, S. Jiang, N. Zhang, C. Duan, M. Yin and T. Li, RSC Adv., 2015, 5, 1385–1390 RSC.
- M. Lin, L. Xie, Z. Wang, B. S. Richards, G. Gao and J. Zhong, J. Mater. Chem. C, 2019, 7, 2971–2977 RSC.
- A. Pandey, S. Som, V. Kumar, V. Kumar, K. Kumar, V. K. Rai and H. C. Swart, Sens. Actuators, B, 2014, 202, 1305–1312 CrossRef CAS.
- Y. Zhang, B. Wang, Y. Liu, G. Bai, Z. Fu and H. Liu, Dalton Trans., 2021, 50, 1239–1245 RSC.
- L. Yao, Q. Shao, S. Han, C. Liang, J. He and J. Jiang, Chem. Mater., 2020, 32, 2430–2439 CrossRef CAS.
- H. J. Ma, W. K. Jung, Y. Park and D. K. Kim, J. Mater. Chem. C, 2018, 6, 11096–11103 RSC.
- P. Cai, L. Qin, C. Chen, J. Wang, S. Bi, S. I. Kim, Y. Huang and H. J. Seo, Inorg. Chem., 2018, 57, 3073–3081 CrossRef CAS PubMed.
- X. Zhang, Z. Zhu, Z. Guo, Z. Sun and Y. Chen, Chem. Eng. J., 2019, 356, 413–422 CrossRef CAS.
- X. Qin, A. N. Carneiro Neto, R. L. Longo, Y. Wu, O. L. Malta and X. Liu, J. Phys. Chem. Lett., 2021, 12, 1520–1541 CrossRef CAS PubMed.
- O. L. Malta, J. Non-Cryst. Solids, 2008, 354, 4770–4776 CrossRef CAS.
- A. N. Carneiro Neto, R. T. Moura and O. L. Malta, J. Lumin., 2019, 210, 342–347 CrossRef CAS.
- W. Zhang, W. Zheng, L. Li, P. Huang, Z. Gong, Z. Zhou, J. Sun, Y. Yu and X. Chen, Angew. Chem., Int. Ed., 2022, 61, e202116085 CAS.
- G. Gao, D. Busko, N. Katumo, R. Joseph, E. Madirov, A. Turshatov, I. A. Howard and B. S. Richards, Adv. Opt. Mater., 2020, 9, 2001901 CrossRef.
- L. Li, Z. Zhou, F. Huang, S. Peng, Y. Huang, G. Wang, X. Li, F.-F. Chen, C. Yang, X.-X. Li and Y. Yu, J. Rare Earths, 2023, 41, 42–50 CrossRef CAS.
- E. Casagrande, M. Back, D. Cristofori, J. Ueda, S. Tanabe, S. Palazzolo, F. Rizzolio, V. Canzonieri, E. Trave and P. Riello, J. Mater. Chem. C, 2020, 8, 7828–7836 RSC.
|
This journal is © The Royal Society of Chemistry 2023 |
Click here to see how this site uses Cookies. View our privacy policy here.