DOI:
10.1039/D2TC04363G
(Paper)
J. Mater. Chem. C, 2023,
11, 2505-2513
Enhanced field emission stability of vertically aligned carbon nanotubes through anchoring for X-ray imaging applications†
Received
13th October 2022
, Accepted 25th December 2022
First published on 28th December 2022
Abstract
It remains difficult to obtain a carbon nanotube (CNT) emitter that simultaneously exhibits high current density, low fluctuation, and long service time because CNTs are easily detached from the substrate in a strong electric field due to the weak adhesion between direct-growth CNTs and heterogeneous substrates. Herein, a mold-aligned transfer anchoring method is employed to anchor vertically aligned CNT film and CNT arrays on a metallic substrate using silver conductive paint via an annealing process. After 100 h of continuous testing with an initial current of ∼2 mA and a current density of ∼900 mA cm−2, the decay rate of the emission current of the anchored CNT emitter decreased by ∼88%, and the current fluctuation was ∼57% lower than that of the unanchored CNT emitter. Furthermore, a metal wire with a width of ∼90 μm could be clearly distinguished by a CNT cold cathode X-ray imaging system. These results testify that the proposed anchoring method can significantly improve the stability and lifetime of CNT field emitters with a high current density, which provides a new route for developing the cold cathode of X-ray sources and other industrial applications in the vacuum electronics field.
1. Introduction
Electron sources are the core components of various vacuum electron devices, and as such, they are widely used in displays,1 electron microscopy,2 traveling-wave tubes,3 medical diagnosis,4 free-electron lasers,5,6 X-ray sources,7 and other fields. Conventional electron sources predominantly consist of thermionic cathodes with metal filaments, which have continually dominated this field for nearly a century despite their numerous drawbacks, including a relatively poor electron beam quality, a slow response, and high energy consumption.8 However, with the emergence of new materials and theories, cold cathode electron sources based on the quantum tunneling effect have become the research focus over the past decades. The advantages of cold cathodes include a narrow electron energy dispersion, a high current density, a fast response, a low energy consumption, and the possibility of being miniaturized,9–11 which are necessary aspects for fabricating equipment with high spatial and temporal resolution.
To select appropriate cold cathode electron sources, various materials containing SiC,12–14 carbon nanotubes (CNTs),15–21 LaB6,22 graphene,23–25 WO3,26 Si tips,27 and ZnO28,29 have been developed as field emitters. Particularly, CNTs exhibit excellent performance, such as a high aspect ratio, superior conductivity, good chemical stability, good toughness, and high mechanical strength. Furthermore, they can be realized using controllable growth methods. These characteristics make CNTs appealing for achieving the high emission current density and low current fluctuation required in electron sources. Numerous studies of CNT-based cold cathode X-ray sources have been reported in the fields of micrometer-scale resolution, fast pulsed exposure, and distributed X-ray sources.30–33
Normally, the emitters of the CNT film or array are directly fabricated on the heterostructure substrate; thus, when a high-density current passes through the junction under a strong electric field, the CNTs are easily detached from the substrate due to the weak adhesion force between the emitters and the substrates. To enhance the adhesion force, various methods have been used, including adding aluminium as the morphological control layer,34 adding a Cu/Al/W/Ti metal layer,35 using microwave treatment,36 filling with reactive nanometer-scale SiC,37 adding glass frits as a binder,38 anchoring via the melting of an indium layer,39 chemical postdeposition treatment,40 combining electrophoresis and successive electroplating,41 tying the CNT yarn to a conductive substrate,42 modifying the substrate with alkali,43 using a 3D nickel foam substrate,44 modifying CNTs by radio-frequency plasma,45 employing screen printing,46 adding an adhesive layer,47 and using a flexible substrate.48 However, these methods are affected by several issues, which have not yet been solved; for example, the CNTs become disorganized, the substrate cannot tolerate a high temperature, the adhesive layer is in the nanometer range, and CNTs have low density and lie flat on the substrate. Hence, simultaneously achieving a large emission current, high current stability, and a long lifetime remains challenging for CNT field emitters. This seriously hinders the practical application of CNT emitters in X-ray sources and other applications.
In this work, vertically aligned CNT films and arrays were successfully synthesized on a polished metal substrate using a thermal chemical vapor deposition (CVD) method. Based on a mold-aligned transfer anchoring method developed in this work, the vertically aligned CNTs were firmly anchored on the substrates via silver conductive paint (SCP) under an annealing treatment. During anchoring, the CNTs can maintain the integrity of their overall morphology. After 100 h of testing, it was found that the anchored CNT film could generate a 2 mA emission current (∼900 mA cm−2) with a fluctuation of ∼2.84% and a decay of ∼2%, which is considerably better than the 6.62% fluctuation and 50% decay of the unanchored emitters. To verify the advantages of the proposed anchoring method, the anchored CNT emitter was assembled into a homemade X-ray source, and clear X-ray images were obtained, in which a ∼90 μm-width wire could be distinguished. Furthermore, the fluctuation of the X-ray radiation dose was reduced by ∼48% after anchoring. These results confirm that the proposed mold-aligned anchoring method is effective in improving the field emission performance of CNT emitters, especially regarding the emission stability with a high current density, and it is envisaged that this method can be successfully used in the realization of cold cathode X-ray sources.
2. Experimental section
2.1 Growth of vertically aligned CNTs
The vertically aligned CNT films were grown on a polished stainless-steel substrate (304 type; thickness of 0.5 mm and diameter of 10 mm) using the thermal CVD method. Before growth, to remove impurities and organics from the surfaces, the substrates were ultrasonically cleaned using deionized (DI) water, acetone, and isopropyl alcohol for 15 min at 50 °C, and then dried with nitrogen gas. Then, a metal mask with an oval hole in the center (with major and minor axes of 1136 and 250 μm, respectively), was placed on the surface of the substrate. The substrate and the mask were then placed in an e-beam evaporation system to deposit 10 nm of aluminium and 2 nm of iron as the double-layer catalyst. Next, the substrates were loaded into the CVD system and heated to 620 °C at a pressure of 90 mbar. When the growth temperature was reached, acetylene gas was introduced into the chamber at a flow rate of 40 sccm as the carbon feedstock. After 10 min of growth, the system was allowed to cool to room temperature naturally, and the CNT films were successfully prepared. The CNT array had a pitch of 120 μm and a diameter of 60 μm, and its overall shape was the same as that of the CNT film except for the fact that the catalyst pattern was prepared using electron beam lithography (EBL).
2.2 Preparation of the anchored vertically aligned CNTs
The anchoring preparation process of the CNT emitter is shown in Fig. 1. Firstly, the CNT nanostructures with a height of ∼500 μm were grown in the center of the polished stainless-steel substrate (yellow color in Fig. 1a) using the thermal CVD method, and another similar substrate (pink color in Fig. 1a) coated with SCP (SPI # 05001-AB) in the center was chosen as the cathode substrate. Secondly, a size-matched stainless-steel mold with a central hole with a thickness of 500 μm and a diameter of 3000 μm was placed on the surface of the CNT-growing substrate (Fig. 1b), and the SCP-coated substrate was then placed on the surface of the mold, as shown in Fig. 1c. This stainless-steel mold can keep the two substrates coaxial and also keep the SCP in contact with the top of the CNTs. After being heated to 150 °C and maintaining this temperature for 20 min, the CNTs were successfully peeled off from the primary-growing substrate and fixed in the center of the SCP-coated substrate after removing the cathode substrate from the mold (Fig. 1d). Finally, the substrate with the CNTs and SCP was annealed in a tube furnace at 900 °C for 10 min to remove the organics substances contained in the SCP using argon as the protective gas. After annealing, many melted and aggregated Ag lumps adhered to the bottom of the CNTs film, which could enhance the adhesion between the CNTs and the substrate, as shown in Fig. S1 (ESI†). The results obtained for other annealing temperatures were also compared, as shown in Fig. S2 (ESI†). After the annealing process of the silver nanoparticles in the SCP, the CNTs were firmly anchored on the target substrate. Similarly, the CNT array was also transferred and anchored successfully. Thus, three types of emitters, namely the CNT film, anchored CNT film and anchored CNT array, were investigated and compared.
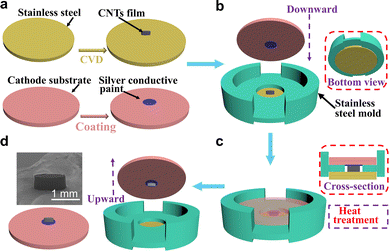 |
| Fig. 1 Schematic diagram of the proposed mold-aligned transfer anchoring method. (a) Preparation of the CNTs and coating of SCP on a substrate. (b) Placement of the mold and the substrate coated with SCP. (c) Heat treatment of the entire transfer tools. (d) The substrate was extracted upward, and the CNTs were anchored on the substrate coated with SCP. | |
2.3 Morphology and electrical conductivity characterization
The surface morphology and the structure of the CNT emitters were observed via field emission scanning electron microscopy (FESEM, Hitachi-SU8220) and high-resolution transmission electron microscopy (HRTEM, Tecnai G2 F20 U-TWIN, FEI), respectively. The lattice vibration and defects of the CNTs were characterized via Raman spectroscopy (Renishaw inVia plus) using a laser with a central excitation wavelength of 514 nm. The surface work function (WF) of the CNTs was measured via ultraviolet photoelectron spectroscopy (UPS, ESCALAB250Xi) using a HeI discharge lamp (with a resolution of 0.45 eV and hν = 21.2 eV). As for the resistance test between the CNTs and the substrate, a current source meter (Keithley 2600s) was used for repeated measurements of the I–V curves. During the measurements, the substrate with the vertically aligned CNT film was fixed on an insulated flat table, and a tungsten probe was installed in an insulated position controller that can move in three directions. Additionally, the substrate and the probe were connected to the negative and positive terminals of the current source meter through low-resistance wires. After the tungsten probe was moved right above the CNT film using the x–y-direction controller, the probe was moved slowly down along the z-direction until its tip was in contact with the surface of the CNT emitters; then, multiple I–V curves were recorded.
2.4 Field emission measurements and X-ray imaging
The field emission properties of the emitters were measured using a parallel-plate diode configuration in a homemade vacuum chamber with a pressure of ∼5 × 10−6 Pa at room temperature. A pure copper plate (70 × 30 × 5 mm3) was used as the anode, the ceramic spacers were placed between the anode and the cathode substrate, and a 500 kΩ protective resistor was connected to the cathode substrate. The distance between the anode and the top of the CNT emitter was ∼300 μm, and the height of the CNT emitter was ∼500 μm. An adjustable high-voltage source (0–10 kV) and an ampere meter with an accuracy of 1 μA were used to provide the anode voltage and to record the field emission current, respectively. The lifetime of the emitters was tested in a continuous emission mode.
For the X-ray imaging experiment, the CNT film emitter before and after anchoring was used as the cold cathode of a triode-type electron gun built in a dynamic vacuum X-ray source system at a pressure of 5 × 10−6 Pa. In addition to the emitter, the electron gun also included a molybdenum grid electrode with a width of 30 μm and a pitch of 300 μm, as well as a circular-hole-shaped focusing electrode with a diameter of 10 mm. A tungsten anode target was placed 8 mm away from the electron gun used for the X-ray generation. A metal grid was used for the X-ray imaging sample and was placed 10 cm away from the X-ray output window. A digital X-ray imaging flat-panel detector (PaxScan 1313DX, Varian Medical Systems, Inc.) with 1024 × 1024 pixels was placed 100 cm away from the sample to acquire the X-ray images.
3. Results and discussion
3.1 Characterization of the CNTs before anchoring
The SEM image of the vertically aligned CNT film grown on a mirror-polished stainless-steel substrate is shown in Fig. 2a (45° viewing angle). The CNT film has a thickness of ∼500 μm and an elliptical shape (around 1136 × 250 μm2); it is regular, uniform, and dense, and the growth direction is generally perpendicular to the substrate due to the van der Waals interactions between neighboring CNTs.49 It should be noted that on viewing from the sidewall of the film (Fig. 2b), although the as-grown CNT film contains many nanotubes, they exist independently along the z-axis direction, and their diameters are almost the same from the bottom to the top. However, in Fig. 2c, the CNTs on the top surface of the film are intertwined and disordered, which is related to the dramatic changes occurring at the end of the growth process, such as the reduction of feed gas and the reduction of pressure in the chamber. It was observed that the catalyst nanoparticles exist on the top of the individual CNTs, which will either change the WF of the CNTs or create an interfacial barrier between the CNTs and the catalyst nanoparticles, thereby affecting the electron transfer rate along the nanotube axis and the emission ratio.50,51Fig. 2d shows a typical low-resolution TEM image of the CNTs. Most CNTs have a diameter in the range of 4–8 nm, except for a few individual CNTs. This unique structure of the nanoscale tip and the high aspect ratio can result in a high field enhancement factor (β) around the tips of the CNTs during field emission, which can lead to a high current density at a relatively low macroscopic electric field intensity. Fig. 2e is a typical HRTEM image of a single CNT, which indicates that the as-grown CNTs are highly crystalline and consist of four-layer carbon atom walls, and their diameter is ∼7 nm. For the whole CNT film, we estimate that the tube walls are approximately composed of 1–8 layers. Furthermore, the image shows that the surface of the as-grown CNTs is not completely smooth because of the deposition of amorphous carbon during the growth process. This amorphous carbon can be removed by the annealing treatment, as is discussed below.
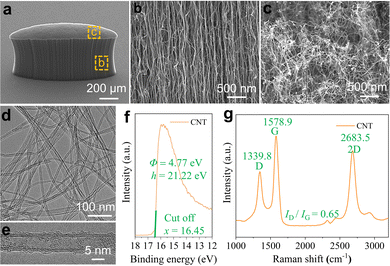 |
| Fig. 2 Basic characterization of the CNTs before anchoring. (a) Low-resolution SEM image of the vertically aligned CNT film. (b) and (c) High-resolution SEM images of the regions surrounded by the dashed yellow lines shown in (a). (d) Low-resolution TEM image and (e) HRTEM image of the CNTs. (f) UPS of the CNTs. (g) Raman spectrum of the CNTs. | |
The WF of the CNTs was measured to be 4.77 eV via UPS as shown in Fig. 2f, which is close to the value reported by a previous study.52 To better understand the quality of the obtained CNTs, the Raman spectrum is shown in Fig. 2g, in which the G-band (1578 cm−1) indicates the sp2 hybridization of the carbon atoms, while the D-band (1339 cm−1) is related to the lattice defects. The intensity ratio of the D-band to the G-band (ID/IG) reflects the density of the lattice defects; for our CNTs, ID/IG = 0.65, which indicates that the as-grown CNTs have few lattice defects. The presence of defects in nanomaterials can enhance field emission, as demonstrated by Chen's work.26
3.2 Morphology and contact resistance of the CNTs after anchoring
The SEM image of the CNT film anchored at 900 °C is shown in Fig. 3a. The elliptical cylindrical morphology was completely maintained after anchoring because the central hole and the CNT film have almost the same thickness. Compared with the CNTs before anchoring, the anchored CNT film mainly exhibited the following three advantages: Firstly, it is uniformly flat to a considerable extent, which can provide a more uniform electric field in the field emission process. Secondly, as shown in the inset of Fig. 3a, the CNTs on the top exist independently along the z-direction, which is significantly different from the intertwined disorder before anchoring shown in Fig. 2c. These arranged CNT tips can provide more field emission excitation sites. Thirdly, at the tip of the CNTs, the catalyst particle density is considerably lower than in the pristine films. It is well known that these characteristics are favorable for the field emission of the cold cathode. Additionally, below and beside the CNT film, as shown in Fig. 3b, there are thick layers of Ag nanoparticles, which could firmly anchor the CNT film to the substrate through annealing processes and significantly enhance the adhesive force.
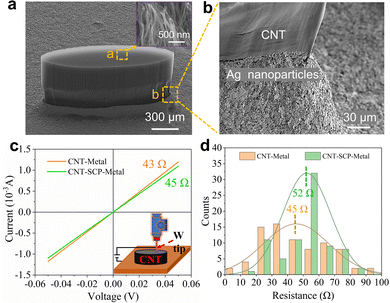 |
| Fig. 3 Characterization of the morphology and contact resistance of the CNTs after anchoring. (a) Low-resolution SEM image of the anchored CNT film. Inset: High-resolution SEM image of the region surrounded by the dashed yellow line. (b) Magnified SEM image of the region surrounded by the dashed yellow line in (a). (c) I–V curves of the unanchored (CNT–Metal) and anchored (CNT–SCP–Metal) CNT film in the voltage range from −0.05 to 0.05 V. Inset: Schematic diagram of the resistance test. (d) Statistical histogram of the resistance of the anchored and unanchored CNT films, and five random points were tested for each sample, therefore, a total of 100 data points were collected both before and after anchoring. | |
The contact resistance between the CNTs and the substrate is an important parameter that needs to be considered because a high resistance would result in a voltage division under a high field emission current, causing the voltage applied between the cathode and the anode to increase.53,54 Furthermore, the large resistance would generate considerable Joule heating during long-term field emission testing, which would affect the mechanical contact force between the CNTs and the substrate, resulting in the detachment of the CNTs from the substrate. Hence, we measured and compared the changes in the contact resistance between the CNTs and the substrate before and after anchoring, and the corresponding I–V measurement results are shown in Fig. 3c.
The two I–V curves show a clear linear relationship, suggesting that the contact between the CNTs, metal substrate, and Ag nanoparticles is a typical ohmic contact, which facilitates the direct injection of electrons from the substrate (or silver film) into the CNTs. For the unanchored CNTs (CNT–Metal), the resistance was ∼43 Ω, while the resistance of the anchored CNTs (CNT–SCP–Metal) was ∼45 Ω, almost the same as that obtained in Liu's work.55 To improve the accuracy of the experiment, we measured five random points for each sample, and a total of 100 data points were collected both before and after anchoring; the corresponding statistical histogram is shown in Fig. 3d. The resistance before and after anchoring is mainly distributed in the range of 20–80 Ω and the statistically calculated average resistance was 45 Ω and 52 Ω before and after anchoring, respectively. The results show that the low resistance did not change significantly after anchoring, which is beneficial for field emission.
3.3 Field emission measurements
The field emission measurements of the CNT emitters were carried out in a homemade vacuum chamber using a high-voltage power supply, and the measurement scheme is shown in Fig. 4a. Fig. 4b shows the emission current (I) as a function of the applied electric field (Ea) of different CNT emitters. An emission current of 2 mA (which corresponds to a current density of nearly 900 mA cm−2 for the ellipse emission area) can be achieved for all CNT emitters. According to the accuracy of the testing instruments, we define the electric field corresponding to an emission current of 1 μA (current density of 450 μA cm−2) as the turn-on field (Eon) and that corresponding to an emission current of 100 μA as the threshold electric field (Ethr). Thus, the calculated Eon and Ethr were 3.7 and 4.2 V μm−1 for the CNT film, 3.5 and 4.5 V μm−1 for the anchored CNT film, and 3.3 and 4.1 V μm−1 for the anchored CNT array, respectively. The anchored CNT array had the smallest Eon and Ethr due to the reduced shielding effect, as shown in the inset of Fig. 4b. The Fowler–Nordheim (FN) plots derived from the above I–V curves are shown in Fig. 4c. In the high-field range, the bent FN curve is related to the space charge and the resistance between the CNTs and the substrate.56 In the low-field range, the FN curve shows a typical linear behavior, which proves that the emission current exhibits a field-driven behavior given by the FN equation | J = A (β2E2/Φ)exp(−BΦ3/2/βE) | (1) |
where J is the emission current, A = 1.56 × 10−6 A V−2 eV and B = 6.83 × 109 V eV−3/2 V m−1 are constants, β is a field enhancement factor, Φ is the WF, and E is the applied electric field. β can be calculated from the slope (S) of the linearized FN data according to the following equation: | ln(J/E2) = ln(Aβ2/Φ) − (BΦ3/2/βE) | (2) |
and thus
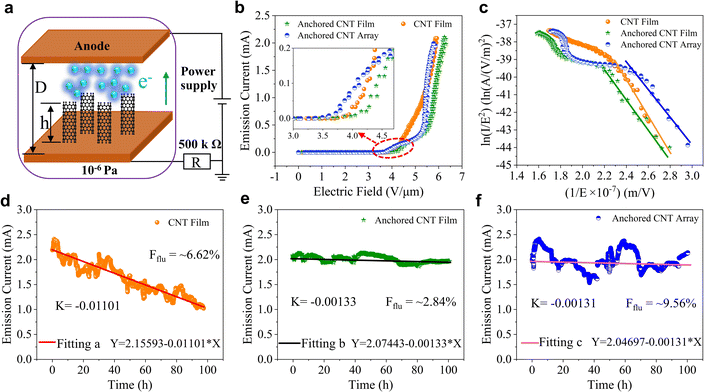 |
| Fig. 4 Field emission characterization of the CNTs. (a) Schematic diagram of the field emission measurements. (b) I–V curves of the different CNT emitters (unanchored CNTs film, anchored CNT film and anchored CNT array); inset: locally magnified field emission I–V curves of the region surrounded by a red dotted line. (c) FN plots corresponding to (b). (d)–(f) Field emission stability of different CNT emitters measured over 100 h. | |
The calculated β values for the CNT film, anchored CNT film and anchored CNT array are 720, 887, and 924, respectively.
Emission stability is an important indicator for measuring the lifetime of an electron source. We conducted stability measurements with a high initial emission current of ∼2 mA and a total continuous time of ∼100 h for the CNT emitters, as shown in Fig. 4d–f. For the unanchored CNT film, the current decreased gradually with time, and after 100 h, the current was only half the initial current (i.e., a decrease of 50%). In contrast, the current of the anchored CNT film and array did not decrease significantly, and the final current values were 1.96 mA (i.e., a decrease of 2%) and 2.1 mA, respectively. The fluctuation is usually calculated according to Tang's work57 using the equation
| 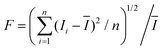 | (4) |
where
Ī is the average emission current over 100 h,
n is the number of total data recorded and
Ii is the emission current at a specific time. However, the emission current of the CNT film showed not only a wide beating range but also a typical rapid decrease; thus, it is not appropriate to use the average emission current as a reference. We fitted the recorded current-
versus-time curve and obtained the revised equation as follows:
| 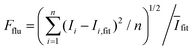 | (5) |
where
Ii,fit is the current obtained from the fitting of
Ii (at the same time), and
Īfit is the average of
Ifit over 100 h. Therefore, the calculated current fluctuations of the CNT film, anchored CNT film, and anchored CNT array were ∼6.62%, 2.84%, and 9.56%, respectively. Before anchoring, the CNTs showed not only a high current decay rate of 50% but also a high current fluctuation of ∼6.62% during the emission current stabilization process, which seriously affected their practical application. After anchoring, the current decay rate of the CNT emitters, which is defined by the slope
K of the fitting line, was reduced by ∼88% for both the anchored CNT film and the array. Although the CNT array showed a good final emission current, the current fluctuation was high (∼9.56%). However, the anchored CNT film exhibited the best field emission current stability combined with the minimum current fluctuation (∼2.84%), which is 57% lower than that obtained before anchoring, and the current decay rate was only ∼2%, which is ideal for X-ray applications.
58 Because the unanchored CNT emitter detached from the substrate during the field emission, the emission current showed a large fluctuation. Compared with the anchored CNT film, when the electron emission site was destroyed due to the sparking phenomenon,
59 the anchored CNT array exhibited a more complex geometric structure. Therefore, the CNTs participating in the emission had more randomness, which resulted in a larger current fluctuation under a high electric field. Furthermore, the array had an emission current density of nearly 2000 mA cm
−2, which is much larger than that of 900 mA cm
−2 for the film under the same current, so the array is more easily damaged and shows a large current fluctuation.
To better understand the decay and fluctuation of the emission current, we compared the morphology of the CNT emitters before and after the stability tests via SEM, as shown in Fig. 5. From the images of the unanchored CNT film before (Fig. 5a) and after (Fig. 5d) testing, it can be seen that a large number of CNTs were detached from the substrate due to the weak adhesion between the CNTs and the substrate. Thus, with increased testing time, the number of CNTs participating in the field emission process gradually decreased, resulting in a clear fluctuation and decline in the field emission current. However, as shown in Fig. 5e and f, after 100 h of testing, the bottom of the anchored CNT film and array emitters were well preserved, and no CNTs detached from the substrate because of the strong anchoring effect of the Ag nanoparticles, thus, the lifetime of the field emission current could significantly increase; however, many scattered CNTs were observed around all the CNT emitters. Besides the detachment of the CNTs from the substrate, the following factors also need to be considered. Firstly, a higher vacuum level is preferred in the chamber. The residual air molecules in the chamber can collide with the emission electrons under a low vacuum, and the CNT are damaged by the bombardment of the high-speed electrons and molecules caused by the collision.60 Secondly, the surface of the CNT emitters can also adsorb a large number of gas molecules, which will be continuously released during the field emission, causing an increase in the vacuum level.61 Thirdly, the emission electrons are accelerated by the electric field and hit the metal anode, causing the metal particles in the anode to be sputtered out and hit the CNT.62 This damage mechanism has not been fully understood yet and requires in-depth exploration. We compared the Raman spectra of the CNT before and after a 100 h long test, and the Raman spectra are shown in Fig. 5g. After testing, the intensity ratios of the D-band to the G-band (ID/IG) for the unanchored, anchored film and anchored array were 1.01, 1.08 and 1.17 respectively, which are much larger than that of 0.65 before testing. This indicates that the lattice structure of CNTs changed due to the impact of gas molecules and electrons, the sputtering of anode metal particles and the local sparking phenomenon during the process of field emission.
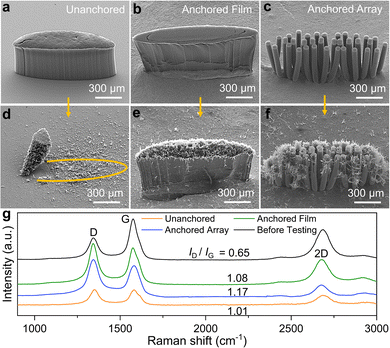 |
| Fig. 5 SEM images and Raman spectra of the CNT emitters before and after the stability tests. (a)–(c) SEM images of the CNT film, anchored CNT film, and anchored CNT array before the stability tests, respectively. (d)–(f) SEM images of the CNT film, anchored CNT film, and anchored CNT array after 100 h-long stability tests, respectively. (g) Raman spectra of the CNT emitter before and after the stability tests. | |
To prove that the anchoring method is feasible, we tested and compared a large number of CNT film emitters before and after anchoring, and some of the results are shown in Fig. S3 (ESI†). For the unanchored CNTs, the emission current fell from 2 to 0.2 mA within 20 h or even 5 h; however, for the anchored CNTs film, it took over 40 h or even 100 h for the emission current to drop from 2 to 1.8 mA. This result demonstrates that the mold-aligned transfer anchoring method proposed in this work can enhance the field emission stability of CNTs.
3.4 X-ray imaging
The CNT film and anchored CNT film were used as the cold cathode in an X-ray source and imaging experiment. Fig. 6a shows the schematic diagram of our homemade X-ray source equipment with a triode-type electron gun and the X-ray imaging system. Fig. 6b shows the changes in the X-ray radiation dose over ∼2 min measured using a photomultiplier tube (PMT) with a CsI scintillator. The cathode materials were either the CNT film or the anchored CNT film. The anchored CNT film had an X-ray radiation dose fluctuation of ∼9.83%, which is significantly smaller than that of the unanchored CNT film (∼18.92%). Fig. 6c and d show the low- and high-resolution SEM images of a metal grid that has a line width of 90 μm, a horizontal period of 390 μm, and a vertical period of 340 μm. The metal grid was imaged using the X-ray system employing either the CNT film or the anchored CNT film as the cold cathode, and the results are shown in Fig. 6e and g, respectively. The anode accelerating voltage was 45 kV, the anode current was 35 μA, and the exposure time was 1s. Fig. 6f and h display the magnified images of the regions surrounded by the dashed yellow line in Fig. 6e and g, respectively. A ∼90 μm-width wire can be distinguished by both the CNT film and anchored CNT film used as cathode emitters. This result demonstrates that the mold-aligned transfer anchoring method developed in this work can not only improve the stability of CNTs but can also enable them to act as emission sources for X-ray imaging equipment, and this provides a novel idea for improving the performance of the existing electron sources.
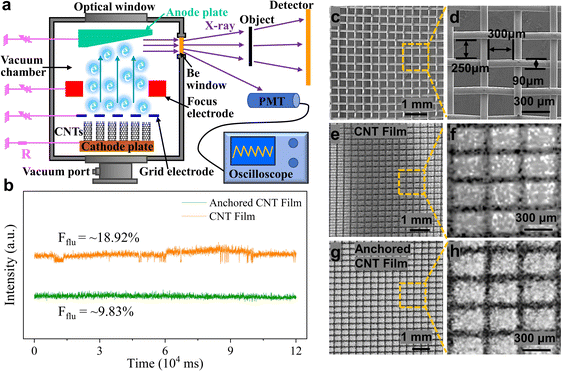 |
| Fig. 6 X-ray imaging conducted using the CNT film and the anchored CNT film as cathode emitters. (a) Schematic diagram of our homemade X-ray source equipment and imaging system. (b) Changes in the X-ray radiation dose over ∼2 min measured using a PMT with a CsI scintillator. The cathode materials are the CNT film and the anchored CNT film. (c) Low-resolution SEM image of a metal grid with a line width of 90 μm, a horizontal period of 390 μm, and a vertical period of 340 μm. (d) Magnified SEM image of the region surrounded by the dashed yellow line in (c). (e) and (g) Low-resolution X-ray images of the metal grid imaged by either the CNT film or the anchored CNT film as the cathode emitter, respectively. (f) and (h) Magnified X-ray images of the regions surrounded by the dashed yellow line in (e) and (g), respectively. | |
4. Conclusion
In summary, we have proposed a mold-aligned transfer anchoring method, through which the vertically aligned CNTs can be firmly anchored on the cathode substrate by employing SCP under annealing treatment. The CNT samples can maintain the integrity of their overall morphology and the contact resistance of the samples was almost unchanged before and after the anchoring treatment. The decay rate of the anchored CNT emitter decreased by ∼88% over 100 h of continuous emission with an initial current of 2 mA with a current density of 900 mA cm−2. Furthermore, the anchored CNT film had a limited current fluctuation (∼2.84%), which is smaller than that of the unanchored CNT film (6.62%). The anchored CNT film emitter was assembled into a homemade X-ray source and imaging system as the cold cathode, and a clear X-ray image of a metal grid was obtained, in which a ∼90 μm-width wire could be easily distinguished. Additionally, the X-ray current fluctuation of the anchored CNT film was ∼9.83%, which is ∼48% smaller than that of the unanchored CNT film. These results show that the proposed mold-aligned transfer anchoring method can considerably improve the stability of CNT-based field emission cathodes, and it is envisaged that these cathodes could be adopted for use in cold cathode X-ray sources and other industrial applications in the vacuum electronics field.
Author contributions
Xinchuan Liu: conceptualization, formal analysis, data curation, writing – original draft. Yuanxun Li: methodology. Jianfeng Xiao: validation. Jiuzhou Zhao: resources. Chi Li: supervision, visualization. Zhenjun Li: writing – review & editing, project administration, funding acquisition.
Conflicts of interest
There are no conflicts to declare.
Acknowledgements
This work is supported by the National Key R&D Program of China (Grant No. 2021YFC2802000, 2016YFA0202000), the Key Area Research and Development Program of Guangdong Province, China (Grant No. 2020B0101020002), the Strategic Priority Research Program of Chinese Academy of Sciences (Grant No. XDB36000000), the National Natural Science Foundation of China (Grant No. 51972072, 52072084, 51925203), CAS Interdisciplinary Innovation Team (Grant No. JCTD-2018-03), and the GBA National Institute for Nanotechnology Innovation (Grant No. 2020GN0106).
References
- A. A. Kuznetzov, S. B. Lee, M. Zhang, R. H. Baughman and A. A. Zakhidov, Carbon, 2010, 48, 41–46 CrossRef CAS.
- H. Zhang, Y. Jimbo, A. Niwata, A. Ikeda, A. Yasuhara, C. Ovidiu, K. Kimoto, T. Kasaya, H. T. Miyazaki and N. Tsujii, Nat. Nanotechnol., 2022, 17, 21–26 CrossRef CAS PubMed.
- X. Li, B. Chen, Y. Feng, Y. Zhang, S. Deng and J. Feng, IEEE Trans. Electron Devices, 2019, 66, 2382–2388 CAS.
- M. Kumakhov, A. Gamaliy, V. Vasiliev, M. Y. Zaytsev, K. Zaytseva, A. Markelov and Y. V. Ozerov, Proc. SPIE, 2006, 5943, 210–218 Search PubMed.
- J. Duris, D. Kennedy, A. Hanuka, J. Shtalenkova, A. Edelen, P. Baxevanis, A. Egger, T. Cope, M. McIntire and S. Ermon, Phys. Rev. Lett., 2020, 124, 124801 CrossRef CAS PubMed.
- J. Rossbach, J. R. Schneider and W. Wurth, Phys. Rep., 2019, 808, 1–74 CrossRef CAS.
- K. Tsuji, T. Matsuno, Y. Takimoto, M. Yamanashi, N. Kometani, Y. C. Sasaki, T. Hasegawa, S. Kato, T. Yamada and T. Shoji, Spectrochim. Acta, Part B, 2015, 113, 43–53 CrossRef CAS.
- J. Y. Gao, Y. F. Yang, X. K. Zhang, S. L. Li, P. Hu and J. S. Wang, Tungsten, 2020, 2, 289–300 CrossRef.
- E. D. Eidelman and A. V. Arkhipov, Phys.-Usp., 2020, 63, 648 CrossRef CAS.
- M. T. Cole, K. B. Teo, O. Groening, L. Gangloff, P. Legagneux and W. I. Milne, Sci. Rep., 2014, 4, 1–5 Search PubMed.
- H. Gan, L. Peng, X. Yang, Y. Tian, N. Xu, J. Chen, F. Liu and S. Deng, RSC Adv., 2017, 7, 24848–24855 RSC.
- J. Xiao, J. Zhao, G. Liu, M. T. Cole, S. Zhou, K. Chen, X. Liu, Z. Li, C. Li and Q. Dai, Nanomaterials, 2021, 11, 3025 CrossRef CAS PubMed.
- Q. Chen, S. Chen, F. Gao, L. Wang, Z. Xie and W. Yang, J. Mater. Chem. C, 2016, 4, 1363–1368 RSC.
- L. Wang, L. Jiang, T. Zhang, F. Gao, S. Chen and W. Yang, J. Mater. Chem. C, 2019, 7, 13748–13753 RSC.
- C. Li, K. Chen, M. Guan, X. Wang, X. Zhou, F. Zhai, J. Dai, Z. Li, Z. Sun and S. Meng, Nat. Commun., 2019, 10, 1–9 CrossRef PubMed.
- C. Li, X. Zhou, F. Zhai, Z. Li, F. Yao, R. Qiao, K. Chen, M. T. Cole, D. Yu and Z. Sun, Adv. Mater., 2017, 29, 1701580 CrossRef PubMed.
- Z. Li, X. Yang, F. He, B. Bai, H. Zhou, C. Li and Q. Dai, Carbon, 2015, 89, 1–7 CrossRef CAS.
- X. Yang, Z. Li, F. He, M. Liu, B. Bai, W. Liu, X. Qiu, H. Zhou, C. Li and Q. Dai, Small, 2015, 11, 3710–3716 CrossRef CAS PubMed.
- J. Zhao, Z. Li, M. T. Cole, A. Wang, X. Guo, X. Liu, W. Lyu, H. Teng, Y. Qv and G. Liu, Nanomaterials, 2021, 11, 3244 CrossRef CAS PubMed.
- N. Liu, G. Fang, W. Zeng, H. Zhou, H. Long and X. Zhao, J. Mater. Chem., 2012, 22, 3478–3484 RSC.
- P. Tripathi, B. K. Gupta, A. Bhatnagar, C. Patel, P. K. Banker, D. J. Late, M. A. More, N. Lalla, D. Phase and R. Choudhary, J. Mater. Chem. C, 2018, 6, 6584–6590 RSC.
- S. Tang, J. Tang, J. Uzuhashi, T. Ohkubo, W. Hayami, J. Yuan, M. Takeguchi, M. Mitome and L. C. Qin, Nanoscale Adv., 2021, 3, 2787–2792 RSC.
- J. Liu, R. Jiang, K. Yang, X. Chai, Y. Fang, J. Deng, X. Liu and B. Zeng, Mater. Lett., 2018, 229, 232–235 CrossRef CAS.
- K. Murakami, T. Igari, K. Mitsuishi, M. Nagao, M. Sasaki and Y. Yamada, ACS Appl. Mater. Interfaces, 2019, 12, 4061–4067 CrossRef PubMed.
- X. Shao, A. Srinivasan, W. K. Ang and A. Khursheed, Nat. Commun., 2018, 9, 1–8 CrossRef CAS PubMed.
- Z. Lin, P. Xie, R. Zhan, D. Chen, J. She, S. Deng, N. Xu and J. Chen, ACS Appl. Nano Mater., 2019, 2, 5206–5213 CrossRef CAS.
- N. Djuzhev, M. Makhiboroda, R. Y. Preobrazhensky, G. Demin, E. Gusev and A. Dedkova, J. Surf. Invest.: X-Ray, Synchrotron Neutron Tech., 2017, 11, 443–448 CrossRef CAS.
- L. Zhao, Y. Chen, Z. Zhang, X. Cao, G. Zhang, J. She, S. Deng, N. Xu and J. Chen, Sci. Rep., 2018, 8, 1–10 Search PubMed.
- M. Li, H. Luo, W. Qian, W. Huang, L. Wan and C. Dong, J. Mater. Chem. C, 2019, 7, 8730–8736 RSC.
- X. Hong, W. Shi, H. Zheng and D. Liang, Vacuum, 2019, 169, 108917 CrossRef CAS.
- W. Lei, Z. Zhu, C. Liu, X. Zhang, B. Wang and A. Nathan, Carbon, 2015, 94, 687–693 CrossRef CAS.
- S. Park, A. P. Gupta, S. J. Yeo, J. Jung, S. H. Paik, M. Mativenga, S. H. Kim, J. H. Shin, J. S. Ahn and J. Ryu, Nanomaterials, 2018, 8, 378 CrossRef PubMed.
- B. J. Walker, J. Radtke, G. H. Chen, K. W. Eliceiri and T. R. Mackie, Nucl.
Instrum. Methods Phys. Res., Sect. A, 2017, 868, 1–9 CrossRef CAS.
- K. Zhang, W. Gong, Z. Li, W. Xu and Y. Yao, Carbon, 2021, 176, 540–547 CrossRef CAS.
- I. Lahiri and W. Choi, Acta Mater., 2011, 59, 5411–5421 CrossRef CAS.
- H. C. Su, C. H. Chen, Y. C. Chen, D. J. Yao, H. Chen, Y. C. Chang and T. R. Yew, Carbon, 2010, 48, 805–812 CrossRef CAS.
- J. W. Kim, J. W. Jeong, J. T. Kang, S. Choi, S. Park, M. S. Shin, S. Ahn and Y. H. Song, Carbon, 2015, 82, 245–253 CrossRef CAS.
- X. Calderón-Colón, H. Geng, B. Gao, L. An, G. Cao and O. Zhou, Nanotechnology, 2009, 20, 325707 CrossRef PubMed.
- Y. I. Song, G. Y. Kim, H. K. Choi, H. J. Jeong, K. K. Kim, C. M. Yang, S. C. Lim, K. H. An, K. T. Jung and Y. H. Lee, Chem. Vap. Deposition, 2006, 12, 375–379 CrossRef CAS.
- A. Santidrián, O. Sanahuja, B. n Villacampa, J. L. Diez, A. M. Benito, W. K. Maser, E. Muñoz and A. Ansón-Casaos, ACS omega, 2019, 4, 2804–2811 CrossRef PubMed.
- W. Y. Sung, S. M. Lee, W. J. Kim, J. G. Ok, H. Y. Lee and Y. H. Kim, Diamond Relat. Mater., 2008, 17, 1003–1007 CrossRef CAS.
- J. Lee, Y. Jung, J. Song, J. S. Kim, G. W. Lee, H. J. Jeong and Y. Jeong, Carbon, 2012, 50, 3889–3896 CrossRef CAS.
- S. He, X. Hong, H. Zheng and D. Liang, Vacuum, 2021, 190, 110286 CrossRef CAS.
- Y. Wu, J. Li, J. Ye, Y. Song, X. Chen, S. Huang, Z. Sun and W. Ou-Yang, J. Alloys Compd., 2017, 726, 675–679 CrossRef CAS.
- M. Lu, Q. He, Y. Li, F. Guo and Z. Dai, Carbon, 2019, 142, 592–598 CrossRef CAS.
- S. J. Kim, S. A. Park, Y. C. Kim and B. K. Ju, J. Vac. Sci. Technol., B: Nanotechnol. Microelectron.: Mater., Process., Meas., Phenom., 2017, 35, 011802 Search PubMed.
- S. C. Lim, H. K. Choi, H. J. Jeong, Y. I. Song, G. Y. Kim, K. T. Jung and Y. H. Lee, Carbon, 2006, 44, 2809–2815 CrossRef CAS.
- T. Tsai, C. Lee, N. Tai and W. Tuan, Appl. Phys. Lett., 2009, 95, 013107 CrossRef.
- S. Fan, M. G. Chapline, N. R. Franklin, T. W. Tombler, A. M. Cassell and H. Dai, Science, 1999, 283, 512–514 CrossRef CAS PubMed.
- J. H. Deng, G. A. Cheng, R. T. Zheng, B. Yu, G. Z. Li, X. G. Hou, M. L. Zhao and D. J. Li, Carbon, 2014, 67, 525–533 CrossRef CAS.
- L. Dong, J. Jiao, C. Pan and D. Tuggle, Appl. Phys. A, 2004, 78, 9–14 CrossRef CAS.
- K. Jiang, J. Wang, Q. Li, L. Liu, C. Liu and S. Fan, Adv. Mater., 2011, 23, 1154–1161 CrossRef CAS PubMed.
- J. She, Z. Xiao, Y. Yang, S. Deng, J. Chen, G. Yang and N. Xu, ACS Nano, 2008, 2, 2015–2022 CrossRef CAS PubMed.
- P. Zhang, S. Fairchild, T. Back and Y. Luo, AIP Adv., 2017, 7, 125203 CrossRef.
- Y. Fu, Y. Qin, T. Wang, S. Chen and J. Liu, Adv. Mater., 2010, 22, 5039–5042 CrossRef CAS PubMed.
- C. Li, Y. Zhang, M. Mann, P. Hiralal, H. Unalan, W. Lei, B. Wang, D. Chu, D. Pribat and G. Amaratunga, Appl. Phys. Lett., 2010, 96, 143114 CrossRef.
- S. Tang, J. Tang, Y. Wu, Y. H. Chen, J. Uzuhashi, T. Ohkubo and L. C. Qin, Nanoscale, 2021, 13, 17156–17161 RSC.
- J. W. Jeong, J. W. Kim, J. T. Kang, S. Choi, S. Ahn and Y. H. Song, Nanotechnology, 2013, 24, 085201 CrossRef PubMed.
- M. Kildemo, S. Calatroni and M. Taborelli, Phys. Rev. Spec. Top.–Accel. Beams, 2004, 7, 092003 CrossRef.
- Y. N. Yang, C. Ding, Y. Fan, B. R. Huang and X. Y. Wang, Ferroelectrics, 2022, 593, 76–85 CrossRef CAS.
- H. Zhang, D. Li, P. Wurz, Y. Cheng, Y. Wang, C. Wang, J. Sun, G. Li and R. G. Fausch, Materials, 2019, 12, 2937 CrossRef CAS PubMed.
- H. M. Manohara, R. Toda, R. H. Lin, A. Liao, M. J. Bronikowski and P. H. Siegel, J. Infrared, Millimeter, Terahertz Waves, 2009, 30, 1338–1350 CAS.
|
This journal is © The Royal Society of Chemistry 2023 |
Click here to see how this site uses Cookies. View our privacy policy here.