Effects of static mixers on continuous methyl ester production: comparing four types of 3D-printed mixing elements
Received
27th August 2022
, Accepted 17th October 2022
First published on 17th October 2022
Abstract
Four types of 3D-printed mixing elements for static mixer reactors, namely, a twisted plate static mixer (TPSM), cross semi-elliptical static mixer (CSSM), X-grid static mixer (XGSM), and corrugated plate static mixer (CPSM), were evaluated for continuous biodiesel production from refined palm oil in terms of the methyl ester purity and the pressure drop across the reactor. The methanol content, potassium hydroxide loading, and static mixer length were optimized for each mixing element with respect to the methyl ester purity using the response surface methodology. The methyl ester conversion for the CPSM, with a short residence time of 132 s, surpassed those for the other three types of static mixers. The CPSM, XGSM, and CSSM reactors afforded methyl ester purities exceeding 99 wt% at reactor positions of 4, 6, and 10 m, respectively. The XGSM reactor was determined to be the preferred option among the four types of static mixers owing to its high reaction rate and low pressure drop during continuous biodiesel production. The CPSM reactor also displayed certain advantages, such as a small space requirement and short reaction time, although it required more pumping power than the XGSM reactor.
Introduction
The COVID-19 pandemic has had enormous global effects. Following the implementation by governments worldwide of social distancing and lockdown measures aimed at slowing down or stopping disease spread,1 the resulting supply chain and logistical issues have led to high volatility in crude oil prices and petroleum utilization.2 Biodiesel is an alternative fuel that has attracted considerable attention owing to its environmentally friendly nature and potential to reduce the consumption of petroleum diesel.3 The main advantages of utilizing biodiesel as a fuel are that it emits less pollution (e.g., CO2, CO, and SO2), has a greater combustion efficiency, produces less visible smoke, and has a higher lubricating ability than petroleum diesel.4 Furthermore, the physical properties and combustion characteristics of biodiesel are similar to those of other diesel fuels.5 Thus, biodiesel can be directly blended with petroleum diesel and used in a diesel engine without major modifications.6 When a base-catalyzed transesterification process is used to produce biodiesel from vegetable oils and animal fats, the free fatty acid (FFA) levels in the oils and fats should not exceed 1 wt%.7 In such a process, as shown in Scheme 1, triglycerides (TGs), diglycerides (DGs), and monoglycerides (MGs) are converted to their methyl esters (MEs).8
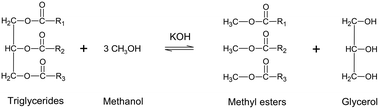 |
| Scheme 1 Transesterification reaction for biodiesel production. | |
In the transesterification process, the mixing intensity is an important parameter that drives the forward reaction to achieve high ME purity.9 Therefore, the mixing equipment plays a crucial role in the reaction by enhancing the ME content. The conventional mixing technology of continuous stirred tank reactors can be used to mix the two immiscible phases during biodiesel production.10 However, other mixing technologies more suited to biodiesel production, such as plug flow reactors (PFRs),8 ultrasonic cavitation reactors,10 and hydrodynamic cavitation reactors,11 have mostly been applied. In addition, compared with other reactors, static mixers are characterized by less space requirements, no moving components, cheaper operating and maintenance costs, shorter residence times, greater mixing distribution, and reduced energy consumption.12 Furthermore, static mixers enhance heat transfer and chemical reactions in both laminar and turbulent flow patterns by increasing the interphase dispersion in liquid–liquid, liquid–gas, and solid–liquid systems.13 The application of static mixers for mixing two or more immiscible substances within a short residence time has been extensively utilized in the polymer, chemical, food, paint, pharmaceutical, and wastewater treatment industries.14 In addition, static mixers have been widely used as reactors for mixing substances for both circulation and continuous biodiesel production. For instance, Alamsyah et al. studied the production of MEs from palm oil using the circulation process through a twisted plate static mixer (TPSM) with a length of 0.3 m.15 Furthermore, the kinetics of the blade agitator in a batch process were investigated and compared with those of static mixers. The results revealed that the reaction time was significantly shorter for the static mixer than for the blade agitator and the former afforded an ME purity of 96.5 wt%. Thus, the authors concluded that the mixing achieved using the static mixer was superior to that using the agitator. Sungwornpatansakul et al. examined the reaction rate and methanol droplet size during biodiesel production using a mechanical agitator and a static mixer.16 The measured conversion indicated that the static mixer afforded greater mixing intensity compared with the mechanical stirrer. Furthermore, it produced smaller and more uniform methanol droplets in the soybean oil, resulting in a faster reaction rate and shorter reaction time than the mechanical stirrer. Somnuk et al. studied the optimization of ME and ethyl ester production from refined palm oil (RPO) using response surface methodology (RSM) with helical static mixers as continuous reactors.17 The ME and ethyl ester purities both exceeded 96.5 wt%. For methanolysis, the optimized conditions included a static mixer length of 4.8 m, a potassium hydroxide (KOH) concentration of 11.2 g L−1, and a methanol concentration of 44.7 vol%. For ethanolysis, the optimized conditions included a static mixer length of 5.1 m, a KOH concentration of 12.5 g L−1, and an ethanol concentration of 45.3 vol%.
In another study, Nguyen et al. employed a static mixer with a capacity of 700 L h−1 for the large-scale production of MEs from waste cooking oil (WCO) in Vietnam.18 RSM was used to optimize the effects of three factors, namely, the methanol-to-oil molar ratio, NaOH concentration, and reaction temperature, on ME production. An ME content of 97.8 wt% was achieved using 12 mixing elements with 10 wt% NaOH, a methanol-to-oil molar ratio of 6
:
1, and a reaction temperature of 60 °C. Somnuk et al. optimized a three-step process for preparing biodiesel from high-FFA oil, wherein MEs were generated from palm fatty acid distillate (PFAD) using a helical static mixer as the reactor.19 Sulfuric acid was used as an acid catalyst in the first and second esterification steps. In the third step, KOH was used as a base catalyst to mediate the transesterification reaction. Consequently, an ME purity of 99.96 wt% was obtained within a total residence time of 147 s for the helical static mixer containing three elements. Hence, the static mixer exhibited significant potential for improving mass transfer during biodiesel synthesis, wherein high-viscosity oils are blended with alcohol. The results obtained for various types of static mixers are summarized in Table 1.
Table 1 Summary of the results obtained for various types of static mixers during biodiesel production
Authors |
Static mixer type |
Raw material |
Alcohol |
Catalyst |
Static mixer length |
Residence time (flow rate) |
Temperature |
Results |
Abbreviations: SM, static mixer; MEs, methyl esters; EEs, ethyl esters; MeOH, methanol; EtOH, ethanol; KOH, potassium hydroxide; SMD, Sauter mean diameter; AV, acid value; FFAs, free fatty acids; RPO, refined palm oil; WCO, waste cooking oil; PFAD, palm fatty acid distillate; TPSM, twisted plate static mixer; CSSM, cross semi-elliptical static mixer; XGSM, X-grid static mixer; CPSM, corrugated plate static mixer. |
Alamsyah et al.15 |
TPSM |
RPO |
10.5 : 1 MeOH to oil |
1 wt% KOH |
0.3 m |
300 s |
65 °C |
96.5 wt% MEs |
(8836 L h−1) |
Sungwornpatansakul et al.16 |
TPSM |
Corn oil |
4.3 : 1 and 6 : 1 MeOH to oil |
0.6, 1.2, and 1.8 wt% KOH |
0.26 m |
600 s |
26–30 °C |
>90 wt% MEs |
(432 L h−1) |
SMD = 6.49 μm |
Somnuk et al.17 |
TPSM |
RPO |
44.7 vol% MeOH |
11.2 g L−1 KOH |
4.8 m |
48 s |
60 °C |
96.5 wt% MEs |
(20 L h−1) |
RPO |
45.3 vol% EtOH |
12.5 g L−1 KOH |
5.1 m |
51 s |
60 °C |
96.5 wt% EEs |
(20 L h−1) |
Nguyen et al.18 |
TPSM |
WCO |
6 : 1 MeOH to oil |
1 wt% H2SO4 |
3 m |
2 s |
60 °C |
2.54 mg KOH per g AV |
(700 L h−1) |
Pretreated WCO |
6 : 1 MeOH to oil |
1 wt% KOH |
3 m |
2 s |
60 °C |
97.8 wt% MEs |
(700 L h−1) |
Somnuk et al.19 |
TPSM |
PFAD |
45.1 vol% MeOH |
5.7 vol% H2SO4 |
5 m |
58 s |
50 °C |
26.43 wt% FFAs |
(25 L h−1) |
Pretreated PFAD |
57.0 vol% MeOH |
7.8 vol% H2SO4 |
7 m |
81 s |
60 °C |
0.95 wt% FFAs |
(25 L h−1) |
Pretreated PFAD |
13.0 vol% MeOH |
5.0 g L−1 KOH |
0.7 m |
8 s |
60 °C |
99.96 wt% MEs |
(25 L h−1) |
Meng et al.20 |
TPSM, CSSM |
High-viscosity fluid |
— |
— |
0.48–0.96 m |
0.46–921 s |
— |
— |
(5.70–5704 L h−1) |
Muruganandam et al.21 |
XGSM |
Vegetable oil-in-water emulsion |
— |
— |
0.714 m |
30–240 s |
Room temperature |
<8 μm mean droplet size |
(750–1250 L h−1) |
El-Jaby et al.22 |
XGSM |
Mini-emulsion systems |
— |
— |
0.042–0.126 m |
5.5–8.5 s |
70 °C |
170 nm mean droplet size |
(848–1304 L h−1) |
Frascari et al.23 |
CPSM |
Sunflower oil |
6 : 1 MeOH to oil |
0.8 wt% KOH |
0.075 m |
40–270 s |
60 °C |
90 wt% MEs |
254–827 L h−1 |
This study |
TPSM, CSSM, XGSM, CPSM |
RPO |
10–40 vol% MeOH |
5–15 g L−1 KOH |
1–10 m |
26–533 s |
60 °C |
99.77 wt% MEs for CPSM |
(32.7 L h−1) |
Various static mixer types, such as the cross semi-elliptical static mixer (CSSM), X-grid static mixer (XGSM), and corrugated plate static mixer (CPSM), have been examined for various processes both experimentally and through simulations. For example, Meng et al. studied the mixing characteristics of a CSSM and a TPSM under Reynolds numbers (Re) of 0.1–100 in the laminar flow regime using a Lagrangian particle method based on a particle tracking technique.20 They also compared the mixing performances of different mixer aspect ratios (1.0, 1.5, and 2.0 for the CSSM and 1.0 for the TPSM) when a high-viscosity fluid (1200 kg m−3 density, 0.5 Pa s viscosity) was employed. The authors concluded that the mixing performance factor increased with increasing Re and decreasing mixer aspect ratio. According to the evaluated mixing performance profiles, the mixing ability of the CSSM was superior to that of the TPSM. Muruganandam et al. studied the droplet size and distribution of oil-in-water (O/W) emulsions through nine horizontal XGSM mixing elements under Re values of 1500–2500.21 The dispersed phase of vegetable oil in the water varied from 1 to 4 vol% and was blended via XGSM under room-temperature conditions. The results showed that the Sauter mean diameter (SMD) of the oil droplets decreased with decreasing concentration of the dispersed phase and increasing flow rate; the SMD decreased from 4.7 to 4.1 μm when the dispersed phase concentration was reduced from 4 to 1 vol%. The emulsion obtained via XGSM was stable for up to 4 h without the addition of any emulsifier. Furthermore, El-Jaby et al. investigated the homogenization of O/W mini-emulsion systems employing 21 XGSM mixing elements in comparison with a bladed agitator operating at 3000 rpm.22 A mini-emulsion droplet size of 170 nm was obtained through XGSM in a short mixing time of 19.5 min while using 185 kJ kg−1 less energy than a conventional mixing approach. Frascari et al. compared the conversion of sunflower oil to MEs for biodiesel production using a CPSM with that obtained by mechanical agitation.23 The 90 wt% ME conversion obtained by five CPSM mixing components was equivalent to that produced with an agitator operating at 700 rpm. Furthermore, the CPSM required less energy than the mechanically agitated system, reducing the energy consumption from 35 to 17 J per kilogram of biodiesel.
In recent years, three-dimensional (3D) printing has become one of the most common advanced manufacturing methods for creating complex structures.24 This fabrication technique has been exploited to create prototype models in various disciplines, including the aerospace, automotive, construction, manufacturing, medical equipment, and robotics fields.25 Regarding the application of 3D printing technology to biodiesel production, Oo et al. measured the reduction in the FFA values of mixed crude palm oil (MCPO) during a continuous esterification process using a 3D-printed rotor.11 During the preliminary investigation, a rotor printed from acrylonitrile butadiene styrene (ABS) filament was used. To study the material erosion, filament segments were submerged in a mixture of methanol and sulfuric acid for almost six months. No changes were observed in the weight or surface appearance of the rotor, indicating the ability of ABS to resist corrosion due to the chemical reactants used for the methyl esterification of the FFAs in oils. Moreover, the 3D-printed rotor–stator hydrodynamic cavitation reactor reduced the FFA content in MCPO from 11.5 to 1.0 wt%, and a maximum esterified oil yield of approximately 91.27 vol% was achieved after purification.
The primary goal of the present investigation was to implement a cost-effective 3D-printed static mixer in a continuous biodiesel production process. Another purpose of this study was to examine the performance of four different mixing elements for biodiesel production. In our previous paper, the main purpose of only 15 static mixer mixing elements for the transesterification reactions was to preliminarily study the pressure drop and ME conversions under the fixed conditions of 23.81 vol% methanol and 11.8 wt% KOH at 50 °C,26 which forms the basis of this study. To the best of our knowledge, few researchers have compared various types of 3D-printed mixing elements for continuous biodiesel production. Therefore, the results of this study are expected to fill critical knowledge gaps in biodiesel production using various types of 3D-printed static mixer reactors (TPSM, CSSM, XGSM, and CPSM), which was optimized in terms of the effects of the methanol content (10–40 vol%), KOH loading (5–15 g L−1), and static mixer length (1–5 m) on the ME purity (wt%) using 45–450 mixing elements in a continuous transesterification process. Furthermore, we also consider the production cost of the 3D-printed mixing element, pressure drop, friction factor (f), required pumping power, and product yield.
Materials and methods
Materials
RPO was employed as the feedstock for continuous ME production using a 3D-printed motionless mixer. The RPO was composed of 97.55 wt% TGs, 0.23 wt% FFAs, 1.87 wt% DGs, and 0.35 wt% MGs, with a specific gravity of 0.89 at 60 °C and a mean molecular weight of 833.5 g mol−1. The potassium methoxide (CH3KO) solution for the transesterification process was prepared using commercial-grade methanol (99.7%) and KOH (95%). The components of the purified biodiesel were evaluated by thin-layer chromatography with flame ionization detection (TLC/FID; Iatroscan MK-65, Mitsubishi Kagaku Latron Inc., Tokyo, Japan) and a stationary phase (Chromarod, type S-III quartz rod). Various mobile phases, including analytical-grade hexane, diethyl ether, formic acid, and benzene, were employed to evaluate the compositions of the RPO and biodiesel, including the percentages of MEs, TGs, FFAs, DGs, and MGs.
Forming and preparation of static mixers
Various mixing elements for the static mixer reactor were printed using a high-performance 3D printer (Creator 3, FlashForge, China), as shown in Fig. 1. Three-dimensional computer-aided design was used to create 3D models of the mixing elements, which were sliced into numerous horizontal layers using FlashPrint software version 4.5.1 to obtain the highest quality of the printed mixing elements. ABS filament of 1.75 mm diameter was used to create four different types of mixing elements: TPSM, CSSM, XGSM, and CPSM. The dimensions of all mixing elements were specified as follows: length-to-diameter (L/D) ratio of 1.0, length (L) of 22 mm, width (D) of 22 mm, and thickness (t) of 2 mm. These values were used for calculating the ME conversions. ABS printing was performed with a constant nozzle temperature of 230 °C and a constant platform temperature of 100 °C to prevent differential thermal contraction and disengagement of the 3D-printed layers from the build platform.27 A relatively large number of mixing elements was required to create a mixer length of 1 m. Therefore, batch 3D printing was used to minimize the printing time, reduce the cost of setting up the printer, and eliminate the need to swap tools or filaments. Accordingly, 45 mixing elements, which were required for a mixer length of 1 m per batch printing time, were printed for each mixer. The required printing times were approximately 4.5, 7.5, 20.5, and 24.5 h for the TPSM, CSSM, XGSM, and CPSM, respectively, which were dependent on the geometric complexity of the mixing parts and the printing accuracy used. The printing position and orientation were set by the FlashPrint software to achieve the desired printing results. The workpieces were placed perpendicular to the printing bed, while the 3D printer performed layer-by-layer horizontal printing until the part was complete. The best printing profile option available employed a filling density of 100%, a layer height of 0.15 mm, and a base printing speed of 50 mm s−1. A hexagonal design was chosen for the printed products because it provided a substantial model for the filling filament. Using 100% filler filaments for technical printing ensures that the ABS filaments are used to achieve a high density of the mixing element material. Therefore, when creating a prototype mixing element for a chemical process, using a 100% filling filament is recommended.11 After each experiment, the corrosion of the mixing element surface was examined and the mixing element weight was measured. No change in either the mixing element weight or exterior appearance was observed for any of the mixing elements.
 |
| Fig. 1 Various types of mixing elements (L = 22 mm, D = 22 mm). Three-dimensional models of the (a) TPSM, (b) CSSM, (c) XGSM, and (d) CPSM; photographs of the 3D-printed (e) TPSM, (f) CSSM, (g) XGSM, and (h) CPSM. | |
Four static mixers (TPSM, CSSM, XGSM, and CPSM) were utilized in this study because of their high pumping power capability to limit the pressure loss and increase the mixing performance during the transesterification reaction. The mixing elements were inserted into the empty tube of the static mixer reactor. Fig. 1a shows the TPSM-type mixing element. The mixing element of the TPSM was connected to the assembly of a long mixing element with a 180° twist and an L/D ratio of 1.0.16 For the CSSM-type mixing element shown in Fig. 1b, each element was formed by two semi-elliptical plates connected together through two triangular plates. The mixing elements were arranged at angles of 45° and 135° in the direction of the flow.28 The XGSM was composed of five crossed bars alternately positioned perpendicular to one another in an “X” shape. All of the crossed bars had a thickness of 2 mm and were arranged at an angle of 45° to the axial flow direction to maximize the flow efficiency,29 as shown in Fig. 1c. For the CPSM, five corrugated plates were placed across the diameter of the element at 45° to the flow direction, giving the element a “V” shape from the side view,30 as shown in Fig. 1d. The detailed geometrical parameters of the TPSM, CSSM, XGSM, and CPSM, such as L, D, L/D ratio, t, porosity (ε), and hydraulic diameter (Dh), are listed in Table 2. To evaluate the mixing in the continuous static mixers, Re and f were calculated by considering water with a density of 995.7 kg m−3 and a viscosity of 0.7975 mPa s. For each design, the pressure drop was measured for a reactor length of 1 m. The calculations and measurements of the pressure drop across the static mixers are described in the subsections entitled “pressure drop correlations” and “pressure drop acquisition”. The overall cost of mixing the components was estimated considering the required weight of ABS filament and the electricity consumption measured by a digital power analyzer (C.A 8220, Chauvin-Arnoux, France). As shown in Table 2, the overall cost of the 3D-printed mixing parts was approximately US$0.04–0.18 per element, depending on the ABS plastic weight and printing time. By contrast, the cost of stainless steel mixing components may range between US$2.5 and US$100 per element.31 Therefore, the reported 3D-printed static mixers were inexpensive and were studied on a laboratory scale for application to biodiesel production.
Table 2 Geometric dimensions, pumping powers, and printing costs of the 3D-printed static mixers
Description |
Static mixer type |
TPSM |
CSSM |
XGSM |
CPSM |
Abbreviations: TPSM, twisted plate static mixer; CSSM, cross-semi-elliptical static mixer; XGSM, X-grid static mixer; CPSM, corrugated plate static mixer. The pumping power per unit meter for the continuous static mixer reactor was calculated from the water flow rate (48 L h−1) according to eqn (3). The residence time of the mixture flowing through the continuous static mixer reactor was calculated from the RPO flow rate (25 L h−1). The hydraulic Reynolds number (Reh) was calculated from the properties of RPO at 60 °C and a flow rate of 25 L h−1. |
Element length, L (mm) |
22.0 |
22.0 |
22.0 |
22.0 |
Diameter, D (mm) |
22.0 |
22.0 |
22.0 |
22.0 |
Length-to-diameter ratio, L/D |
1.0 |
1.0 |
1.0 |
1.0 |
Thickness, t (mm) |
2.0 |
2.0 |
2.0 |
2.0 |
Porosity, ε |
0.90 |
0.81 |
0.76 |
0.40 |
Hydraulic diameter, Dh (mm) |
21.8 |
17.9 |
9.0 |
2.9 |
Pumping power per unit meter (mW m−1)a |
7.7 |
10.4 |
10.7 |
74.5 |
Residence time in reactor (s m−1)b |
67 |
62 |
57 |
37 |
Weight of mixing element (g per element) |
1.40 |
2.25 |
3.88 |
6.30 |
Printing time of mixing element (min per element) |
14 |
20 |
49 |
61 |
Material cost of mixing element (US$ per element) |
0.03 |
0.05 |
0.08 |
0.13 |
Electricity cost of mixing element (US$ per element) |
0.01 |
0.02 |
0.04 |
0.05 |
Overall cost of mixing element (US$ per element) |
0.04 |
0.07 |
0.12 |
0.18 |
Hydraulic Reynolds number for RPO flow rate in reactorc |
21.43 |
19.65 |
10.52 |
6.34 |
Pressure drop correlations
The mixing intensity of a flowing fluid increases with increasing Re. In general, Re is the most commonly used parameter for describing smooth or unsteady streamlines of the overall flow at its beginning. This parameter is primarily influenced by the inertial-to-viscous force ratio of the fluid. According to Chuan et al., increasing Re may promote a smaller and more uniform methanol droplet size in continuous biodiesel production when a TPSM is used.32 Therefore, using different types of static mixers may increase the solubility of the oil and methanol phases because the porosity (ε) of each mixing element in the mixer is different. The mixer porosity is defined as the ratio of the fluid volume in the mixing segment (Vf) to the total volume (Vt). Therefore, ε can be applied to estimate the ratio of the superficial velocity (vs) in an empty pipe to the interstitial velocity (vi) of the fluid flowing through the mixer.33 This is one of the most critical parameters, with values of 0.90, 0.81, 0.76, and 0.40 for the TPSM, CSSM, XGSM, and CPSM, respectively, as shown in Table 2. This parameter represents the reactor flow volume based on the geometry of the static mixer. As a result, a fluid can flow more easily through a high-porosity mixer (e.g., TPSM or CSSM) than through a low-porosity mixer (e.g., CPSM). In this study, the pressure drop across the static mixers was determined in terms of the hydraulic Reynolds number (Reh) and hydraulic friction factor (fh),30 as expressed in eqn (1) and (2), respectively. When the fluid passes through the static mixer reactor, the flow energy gradually decreases throughout the total length of the pipe.34 Therefore, the pumping power (Wpump) of the flow system was evaluated to estimate the energy demand required to overcome the pressure drop for the various types of mixing elements. The pumping power requirement can be defined using eqn (3):35 |  | (1) |
| 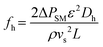 | (2) |
where ρ is the density, vs is the velocity, Dh is the hydraulic diameter, ε is the porosity of the mixing element, μ is the dynamic viscosity, ΔPSM is the pressure drop, L is the reactor length, fh is the friction factor, Wpump is the pumping power requirement, and Q is the volumetric flow rate.
Pressure drop acquisition
The schematic diagram presented in Fig. 2 shows the pressure drop measurements in the static mixer reactor. The static mixing elements were placed inside stainless steel pipes of various lengths. A total of 45 mixing elements were combined in the reactor to achieve a length of 1 m. The experimental pressure drop in the static mixer reactor was measured using pressure sensors attached to a differential pressure drop device. The pressure drop measurements for the various types of static mixers, including the TPSM, CSSM, XGSM, CPSM, and PFR, were performed at water flow rates ranging from 6 to 48 L h−1. A flow rate sensor, temperature sensor, differential pressure transducer, and manometer were used to evaluate the pressure drop in the continuous reactor containing the 45 mixing elements. For the preparation step, a dosing pump (DMX 50-10, Grundfos Alldos, Germany) recirculated the water from the tank into the static mixer reactor, and the temperature was measured using a temperature sensor (MAX6675, Maxim, China) coupled with a K-type thermocouple. At the start of the experiment, the dosing pump supplied the required water flow rate to the static mixer reactor. The water flow rate was measured using a Hall effect sensor (IM-J650, IMARI, Japan). Piezoelectric pressure transducer taps (SS302+, Sendo Sensor, China) were used to analyze the pressure differential across the static mixer for the pressure drop measurements. Finally, all of the data from the sensors were computed using a microcontroller (Mega 2560 R3, Arduino, Italy), and the real-time data were recorded on a computer through Bluetooth using Telemetry Viewer version 0.6 software. The overall experimental uncertainty was determined as ±6.03% by the principle of propagation of errors,36 as shown in Table 3.
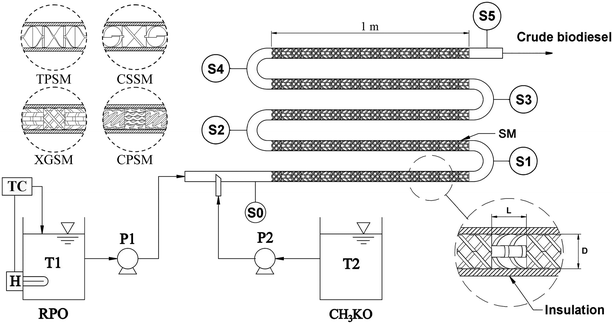 |
| Fig. 2 Schematic diagram of continuous biodiesel production using a 3D-printed static mixer. Abbreviations: T1, RPO tank; H, submerged heater; TC, temperature controller; P1, RPO dosing pump; T2, CH3KO tank; P2, CH3KO dosing pump; S0–S5, sampling ports at 0–5 m; SM, static mixer; L, length; D, diameter of mixing element. | |
Table 3 Measurement ranges, accuracies, and percentage uncertainties
No. |
Measurement |
Device |
Measurement range |
Accuracy |
% uncertainty |
The overall experimental uncertainty was calculated as .
|
1 |
Flow rate |
Flow rate sensor |
0.3–2.4 L min−1 |
±3% |
6 |
2 |
Temperature |
Temperature sensor |
0–600 °C |
±1.5% |
0.1 |
3 |
Pressure |
Pressure sensor |
0–10 kPa |
±0.5% |
0.57 |
Overall experimental uncertaintya |
6.03 |
Experimental setup for biodiesel production using 3D-printed mixing elements
The experimental setup used for continuous biodiesel production using the 3D-printed static mixer reactor is depicted in Fig. 2. This continuous system comprised a stainless steel (SUS304) tube with a length of 5 m, an inner diameter of 22.5 mm, and a wall thickness of 2.11 mm. The SUS304 tube was insulated with thermal insulation rubber foam to prevent heat loss from the exothermic reactions in the reactor. The 3D-printed static mixers (TPSM, CSSM, XGSM, and CPSM) were installed and inserted into the pipe. The space between the mixers and tube wall was narrow to prevent fluid shortcuts during flow through the mixing element. The primary focus of our research was evaluating the mixing of the RPO and CH3KO solutions by the 3D-printed mixing elements. The RPO (T1) and CH3KO (T2) tanks contained the raw material and chemical reactant, respectively, required for the transesterification process. Furthermore, the key component of the static mixer does not involve moving parts, thus facilitating operation and maintenance.
Continuous transesterification reaction using the static mixer
To prepare for the experiment, the RPO in tank T1 was heated to 60 °C using a 1000 W immersion heater combined with an electrical thermocouple. To maintain the temperature, 15 L of RPO was heated to 60 °C and continuously circulated through the pipe using the RPO circulating pump. The RPO in tank T1 and CH3KO solution in tank T2 were both continuously pumped into the continuous static mixer reactor at a flow rate of 25 L h−1 using dosing pumps P1 (DME 60-10, Grundfos Alldos, France) and P2 (DMS 12-3, Grundfos Alldos, France), respectively. To evaluate the flow regime in the continuous static mixer reactor, the Reh was calculated by considering RPO at 60 °C with a density of 891 kg m−3 and a viscosity of 18.4 mPa s, as expressed in eqn (1). As listed in Table 2, the Reh values were 6.34, 10.52, 19.65, and 21.43 for the CPSM, XGSM, CSSM, and TPSM, respectively, which were calculated based on the properties of RPO at a flow rate of 25 L h−1. Thus, the flow of RPO corresponded to the laminar flow regime in all cases. This dimensionless number of Reh values in each reactor can be used to perform the relevant scale-up condition. To investigate the ME conversion, three independent variables were considered, namely, the methanol content (10–40 vol%), KOH loading (5–15 g L−1), and static mixer length (1–5 m), which were coded into three levels as summarized in Table 4. To start the test, both of the digital dosing pumps were initiated, thus constantly feeding RPO and CH3KO into the static mixer. Before collecting the samples, the continuous reactor was operated for approximately 10 min to ensure that each set of conditions had reached equilibrium conversion. To better understand the conversion of glycerides to MEs along the reactor length, crude biodiesel samples (30 mL) were collected at the sampling ports, as shown in Fig. 2. Each sample was immediately cooled to 0 °C in a water bath to stop the reaction and then purified with warm water to remove the glycerol, excess catalyst, and methanol. All of the washed samples were analyzed using TLC/FID to determine the contents of MEs, TGs, FFAs, DGs, and MGs in the biodiesel. RSM was used to optimize the ME purity from the investigated parameters.
Table 4 Coding of independent variables
Independent variable |
Units |
Coding level |
−1 |
0 |
+1 |
Methanol content (M) |
vol% |
10 |
25 |
40 |
KOH loading (K) |
g L−1 |
5 |
10 |
15 |
Static mixer length (L) |
m |
1 |
3 |
5 |
Experimental design
Eighteen experimental runs and four repeated central points were investigated using RSM, three coding levels, and a three-factor face-centered central composite design for the continuous transesterification process. The effects of the methanol content (10–40 vol%), KOH loading (5–15 g L−1), and static mixer length (1–5 m) on the ME purity were investigated for the various types of static mixers (Table 4). Table 5 lists the independent variables tested and corresponding experimental results. As presented in eqn (4), a second-order response surface model was used to predict the ME purity after continuous transesterification. Analysis of variance (ANOVA) with a 95% confidence level was used to evaluate the fit of the model to the experimental data. In addition, contour plots were prepared to demonstrate the interactive effects of the independent variables on the ME purity. |  | (4) |
where y is the response, β0 is a constant value, βixi is the main effect term, βijxixj is the interaction term, βiixixi is the quadratic term, k is the number of independent variables, and ε is the error term.
Table 5 Experimental design and methyl ester (ME) purities for the various types of static mixers
Run |
Independent variable |
ME purity (wt%) |
M (vol%) |
K (g L−1) |
L (m) |
TPSM |
CSSM |
XGSM |
CPSM |
Abbreviations: M, methanol content; K, potassium hydroxide loading; L, static mixer length; TPSM, twisted plate static mixer; CSSM, cross semi-elliptical static mixer; XGSM, X-grid static mixer; CPSM, corrugated plate static mixer. |
1 |
10 |
5 |
1 |
2.57 |
3.48 |
35.02 |
59.85 |
2 |
10 |
5 |
5 |
11.10 |
19.31 |
42.70 |
78.23 |
3 |
10 |
10 |
3 |
27.70 |
35.53 |
54.91 |
79.60 |
4 |
10 |
15 |
1 |
23.35 |
30.91 |
39.17 |
83.59 |
5 |
10 |
15 |
5 |
53.82 |
55.5 |
56.55 |
80.46 |
6 |
25 |
5 |
3 |
12.83 |
23.92 |
77.95 |
84.01 |
7 |
25 |
10 |
1 |
5.49 |
7.41 |
65.48 |
83.59 |
8 |
25 |
10 |
3 |
17.02 |
24.72 |
90.31 |
97.16 |
9 |
25 |
10 |
3 |
18.39 |
23.59 |
89.94 |
97.49 |
10 |
25 |
10 |
3 |
17.53 |
24.21 |
88.52 |
97.27 |
11 |
25 |
10 |
3 |
17.98 |
23.69 |
91.01 |
97.58 |
12 |
25 |
10 |
5 |
34.99 |
48.8 |
96.21 |
97.77 |
13 |
25 |
15 |
3 |
39.88 |
48.64 |
93.12 |
98.22 |
14 |
40 |
5 |
1 |
6.43 |
13.49 |
47.05 |
73.81 |
15 |
40 |
5 |
5 |
37.49 |
54.31 |
77.52 |
88.64 |
16 |
40 |
10 |
3 |
13.75 |
34.17 |
82.49 |
95.52 |
17 |
40 |
15 |
1 |
10.90 |
10.47 |
57.81 |
90.61 |
18 |
40 |
15 |
5 |
74.06 |
87.28 |
91.47 |
91.75 |
Results and discussion
Pressure drop, friction factor, and pumping power of the static mixers
The pressure drop is one of the variables that should be considered when determining the efficiency of a mixer. The degree of pressure loss in inline mixers depends on the mixer type. A greater pressure drop in the pipe increases the pumping power requirements and thus the energy cost.37 To achieve the necessary mixing performance while maintaining a minimal pressure drop, a compromise must be made between two main objectives: the pressure drop and the ME purity. In this section, the flow through the various static mixers (TPSM, CSSM, XGSM, and CPSM) is described in terms of the Reh values based on the pressure drops generated from single-phase water flow. The experiments clearly demonstrated that increasing the water flow rate increased the pressure drop. Fig. 3a shows the comparison of pressure drop generated by various types of SM. Three geometric parameters: the porosity, hydraulic diameter of each mixing element, and measured pressure drop, are entered in eqn (1) and (2). In this study, as the number of mixing elements increased, the individual pressure drop became insignificant compared with the pressure drop produced by the mixers. From these calculations, the fh = f(Reh) plots for the four static mixer types per unit meter are shown in Fig. 3b. Furthermore, the laminar flow regime was observed for Reh values were 1054, 917, 520, and 315, respectively, which corresponds to Re of 963 for the PFR under a flow rate of 48 L h−1. Moreover, a similar trend in the fh = f(Reh) plots was reported by Theron and Sauze, who investigated an emulsification process using a CPSM and an XGSM.30 They concluded that the pressure drop generated by the mixed flows was also demonstrated in terms of fh or as a function of Reh for all geometric and flow parameters. The generated fh of the XGSM was approximately two times higher than that of the CPSM. They also mentioned that the representation in terms of “hydraulic” values enables predicting the generated pressure drops, particularly the porosity and the hydraulic diameter of different types of SM.
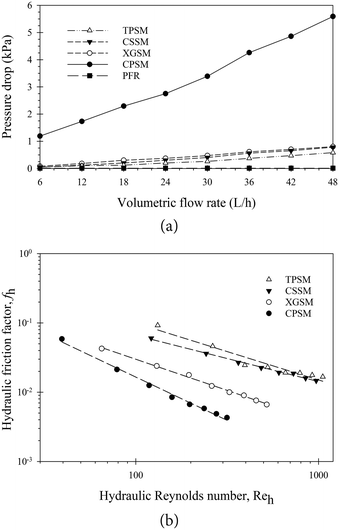 |
| Fig. 3 Pressure drop across the static mixers and hydraulic friction factors. (a) Pressure drop variations across the various types of static mixers for a static mixer length of 1 m. (b) Hydraulic friction factor as a function of hydraulic Reynolds number. | |
Response surface model results for biodiesel production
Table 5 presents the actual results for 18 biodiesel production runs performed under various reaction conditions to demonstrate the relationships and interactions between the different parameters. The ME purities obtained for the TPSM, CSSM, XGSM, and CPSM were in the ranges of 2.57–74.06, 3.48–87.28, 35.02–96.21, and 59.85–98.22 wt%, respectively. Multiple regression analysis was performed using RSM to fit a second-order polynomial equation to the measured ME purities (Table 5). Therefore, quadratic regression models were used to determine the correlation between the independent and response variables and obtain the optimal conditions for biodiesel production, as described by eqn (5) for the TPSM, eqn (6) for the CSSM, eqn (7) for the XGSM, and eqn (8) for the CPSM. The coefficients, p values, coefficients of determination (R2), and adjusted coefficients of determination (Radjusted2) for the fitted response surface models are given in Table 6. The Radjusted2 values were obtained by eliminating the insignificant coefficients. This validity of this approach was confirmed by the high Radjusted2 values of 0.942, 0.936, 0.990, and 0.970 for the TPSM, CSSM, XGSM, and CPSM, respectively. Therefore, the predicted and actual outcomes were in reasonable agreement. The Radjusted2 values of the four models approached the predicted R2 values, confirming that the quadratic model for the prediction of biodiesel production was adequate in terms of statistical accuracy. | ME1 = β0 + β2K + β5K2 + β7MK + β8ML + β9KL | (5) |
| ME2 = β0 + β5K2 + β7MK + β8ML + β9KL | (6) |
| ME3 = β0 + β1M + β2K + β3L + β4M2 + β5K2 + β6L2 + β8ML | (7) |
| ME4 = β0 + β1M + β2K + β3L + β4M2 + β5K2 + β6L2 + β9KL | (8) |
Here, ME1, ME2, ME3, and ME4 are the ME purities for the TPSM, CSSM, XGSM, and CPSM, respectively, β0 is a constant, and β1 to β9 are the coefficients of each independent variable.
Table 6 Coefficients and p values of the fitted response surface models
Coefficient |
TPSM |
CSSM |
XGSM |
CPSM |
Value |
p value |
Value |
p value |
Value |
p value |
Value |
p value |
Abbreviations: TPSM, twisted plate static mixer; CSSM, cross semi-elliptical static mixer; XGSM, X-grid static mixer; CPSM, corrugated plate static mixer. |
β
0
|
12.67 |
0.22676 |
−2.357 |
0.4801337 |
−43.53 |
0.000019459 |
8.558 |
0.1356851 |
β
1
|
— |
— |
— |
— |
5.025 |
0.000000130 |
2.042 |
0.0000983 |
β
2
|
−4.318 |
0.06693 |
— |
— |
4.466 |
0.007414737 |
5.621 |
0.0008816 |
β
3
|
— |
— |
— |
— |
15.16 |
0.000188568 |
13.13 |
0.0002527 |
β
4
|
— |
— |
— |
— |
−0.09320 |
0.000000174 |
−0.03302 |
0.0004681 |
β
5
|
0.325 |
0.00723 |
0.144 |
0.0025954 |
−0.165 |
0.031468867 |
−0.155 |
0.0240455 |
β
6
|
— |
— |
— |
— |
−2.206 |
0.000330823 |
−1.077 |
0.0144180 |
β
7
|
−0.03506 |
0.03728 |
−0.05385 |
0.0057987 |
— |
— |
— |
— |
β
8
|
0.169 |
0.00228 |
0.293 |
0.0000366 |
0.163 |
0.000483172 |
— |
— |
β
9
|
0.439 |
0.00312 |
0.302 |
0.0374325 |
— |
— |
−0.440 |
0.0004108 |
R
2
|
0.942 |
|
0.936 |
|
0.990 |
|
0.970 |
|
R
adjusted
2
|
0.917 |
0.917 |
0.983 |
0.948 |
Before examining the p values, it should be noted that nine terms exist in the completed forms of the predictive equations (eqn (5)–(8)). The p value is an essential parameter for assessing the statistical significance of each regression coefficient in models when determining the importance of each independent variable.38 Statistical significance at the 95% confidence level is achieved if the p values are less than 0.05. Otherwise, the insignificant term is eliminated from the regression model.11Table 6 shows the coefficients of each term for the TPSM, CSSM, XGSM, and CPSM after considering the p values. The lowest p values of 0.0000983 and 0.000000130 were found for the β1M term for both CPSM and XGSM, respectively. Therefore, β1M affects methanol, which significantly affects the conversion of RPO to MEs using the various 3D-printed static mixers. The smallest p values of methanol are essential for producing the required ester level in a continuous transesterification process using the CPSM and XGSM mixing elements. Methanol demonstrates the most significant effect on both types of reactors because glycerides shift the transesterification equilibrium to high-purity MEs.39 Similar results were reported by Keera et al., who produced alkyl esters from soybean and cottonseed oils using sodium hydroxide (NaOH) as the catalyst.40 The effects of methanol-to-oil molar ratios in the range from 3
:
1 to 12
:
1 were investigated with 1 wt% NaOH, a temperature of 60 °C, a reaction time of 1 h, and a stirring speed of 400 rpm. The authors reported insufficient conversion for molar ratios lower than 6
:
1. Furthermore, when the molar ratio was increased from 3
:
1 to 6
:
1, the ME yields for soybean and cottonseed oils were 90% and 98.5%, respectively. They concluded that the methanol-to-oil molar ratio was the most significant factor in the conversion to biodiesel. The terms β3L and β4M2 ranked second while the terms β4M2 and β3L ranked third for the CPSM and XGSM, respectively.
The experimental results for the CSSM and TPSM reactors are particularly notable because the order of p values was the same for both reactors. In the interaction term β8ML, which substantially influenced the ME formation, the lowest p values of 0.0000366 and 0.0022760 were observed for the CSSM and TPSM mixing elements, respectively. Therefore, higher methanol consumption was required for producing biodiesel when the CSSM and TPSM were used; the same trend was observed for both the CPSM and XGSM in this experiment. However, for the CSSM and TPSM mixing elements it was necessary to extend the static mixer length because extended residence times were required inside the inline reactor. Similar results were reported by Rauline et al., who compared the mixing performance of two commercial static mixers, namely, a TPSM and an XGSM, in the laminar flow regime.41 Several criteria, such as the pressure drop, mean shear rate, and segregation intensity, were compared using a 3D numerical simulation technique. Although the TPSM had a pressure drop that was 3.7 times lower than that of the XGSM, 2.5 mixing elements were required to achieve a similar mixing distribution. Therefore, the mixing efficiency of the XGSM surpassed that of the TPSM in achieving complex mixing when the installation area was restricted. Fourcade et al. investigated the development of striation behavior in a TPSM and an XGSM in a laminar flow field.42 Computational fluid dynamics results, which were validated by laser-induced fluorescence measurements, were employed to estimate the mean value of striation thinning across the mixer. With only one mixing element, the XGSM had a striation thinning parameter that was six times greater than that of the TPSM; hence, the XGSM afforded more vigorous mixing than the TPSM. Meng et al. reported a similar tendency for a CSSM and a TPSM and numerically analyzed the mixing performance of the two systems in the laminar flow regime.20 The CSSM exhibited more chaotic mixing characteristics than the TPSM. The curvatures of the walls of the two mixers may have been responsible for the small difference in their mixing performances.
When considering the role of the catalyst in the reaction, the quadratic term of the CSSM (β5K2) for KOH was ranked second, and the interaction term of the TPSM reactor (β9KL) was similarly ranked. Consequently, a greater amount of the base catalyst must be employed for synthesizing biodiesel using low-efficiency static mixers such as the CSSM and TPSM. The geometry of the static mixer had the greatest influence on the generated pressure drop and mixing intensity. To compare the mixer characteristics, two parameters, namely, ε and Dh, were evaluated. ε (Table 2) can be applied to estimate the ratio of the mean velocity (vs) to the interstitial velocity (vi) through the mixer of the fluid flowing.33 Different porosities and hydraulic diameters will occur owing to the different cross-sectional areas of the mixing elements. The flow velocity increases with increasing flow area, which depends on the cross-sectional area and increases the flow mixing efficiency.43 In this study, the CPSM had the lowest porosity of 0.40, indicating that the maximum velocity of the liquid occurred in this system, resulting in higher mixing intensity and pressure drop increase in the flowing fluid. The ME purity was found to increase with decreasing mixer porosity; under the same experimental conditions, the CPSM afforded the highest ME purity, followed by the XGSM, CSSM, and TPSM. As a result, the CPSM exhibited the highest mixing intensity among the static mixer types examined, enabling higher mixing efficiency and allowing a shorter reactor length. Using a laser-induced fluorescence approach, Wadley and Dawson investigated the mixing performance of three types of static mixers: a TPSM, a Chemineer high-efficiency vortex static mixer, and a CPSM.44 The results revealed that the minimum number of mixer elements needed for the CPSM to achieve complete mixing was four, whereas the other two types required at least six. Finally, the CPSM mixer displayed the highest mixing intensity, as demonstrated by the good mixing of a fluorescent dye solution in the water-based flow system. Nonetheless, an unanticipated pressure drop was found when employing the low-porosity CPSM mixer. Similar results were reported by Cheng et al., who used computational fluid dynamics to investigate the mixing characteristics of a static mixer in a tubular photobioreactor.45 To obtain acceptable configurations, the effects of the two-blade cross-angle, horizontal spacing, open porosity, and hole radius were evaluated. The authors concluded that the static mixer provided better fluid mixing and whirling flow. They also reported that increasing the mixer porosity from 12% to 20% decreased the pressure loss and average shear stress.
ANOVA was used to evaluate the statistical significance of the models (Table 7). The statistical data were verified using ANOVA while also examining the relative relevance of the multiple variables for each model.46 The predictive model significance was determined by the F-test statistic (F0), which must be higher than the critical value (Fcrit) when employing the F-test to establish model significance. The critical value is denoted by Fα,n−1−i, where α is the axial point for ratability, n is the number of experiments, and i is the number of coefficients in the experiment.11,46 The F0 and Fcrit values were derived by ANOVA for each response surface model; the determined F0 values were 38.69 (TPSM), 47.73 (CSSM), 144.2 (XGSM), and 45.58 (CPSM), all of which were greater than the Fcrit values. Thus, all of the response surface models accurately predicted that the 3D-printed static mixers provided good mixing between oil and methanol for biodiesel production.
Table 7 ANOVA results for each response surface model
Type |
Source |
SS |
MS |
F
0
|
F
crit
|
DOF |
Abbreviations: SS, sum of squares; MS, mean square; DOF, degrees of freedom; TPSM, twisted plate static mixer; CSSM, cross semi-elliptical static mixer; XGSM, X-grid static mixer; CPSM, corrugated plate static mixer. |
TPSM |
Regression |
5459.8 |
1092.0 |
38.69 |
3.11 (F0.05,5,12) |
5 |
Residual (error) |
338.66 |
28.22 |
12 |
Lack-of-fit error |
337.62 |
37.51 |
9 |
Pure error |
1.042 |
0.347 |
3 |
Total |
5798.5 |
|
17 |
CSSM |
Regression |
6914.2 |
1728.5 |
47.73 |
3.18 (F0.05,4,13) |
4 |
Residual (error) |
470.80 |
36.22 |
13 |
Lack-of-fit error |
469.98 |
47.00 |
10 |
Pure error |
0.816 |
0.272 |
3 |
Total |
7385.0 |
|
17 |
XGSM |
Regression |
7485.8 |
1069.4 |
144.2 |
3.14 (F0.05,7,10) |
7 |
Residual (error) |
74.16 |
7.416 |
10 |
Lack-of-fit error |
70.86 |
10.12 |
7 |
Pure error |
3.298 |
1.099 |
3 |
Total |
7559.9 |
|
17 |
CPSM |
Regression |
1838.9 |
262.70 |
45.58 |
3.14 (F0.05,7,10) |
7 |
Residual (error) |
57.64 |
5.764 |
10 |
Lack-of-fit error |
57.52 |
8.218 |
7 |
Pure error |
0.113 |
0.03750 |
3 |
Total |
1896.5 |
|
17 |
Contour plots and effects of influential parameters on biodiesel purity
The effects of the independent variables of methanol content (10–40 vol%), KOH loading (5–15 g L−1), and static mixer length (1–5 m) on the ME conversion during continuous biodiesel production using the 3D-printed static mixers are presented in Fig. 4. These contour plots show the results obtained for the TPSM (Fig. 4a, e, and i), CSSM (Fig. 4b, f, and j), XGSM (Fig. 4c, g, and k), and CPSM reactors (Fig. 4d, h, and l). As described in the previous subsection, the methanol content had the most pronounced effect on the ME purity for all static mixer types, followed by the KOH loading and static mixer length, all of which were assessed statistically with the p values. The CPSM and XGSM mixing elements were more efficient than the CSSM and TPSM in affording ME conversions over 99 wt% in short reactors. Therefore, the CPSM and XGSM were selected to describe the relationships between the high ME purity and the three independent variables from the contour plots. The effects of the KOH loading and static mixer length on the ME purity for the CPSM reactor are shown in Fig. 4d. ME purities exceeding 98 wt% were observed for KOH loadings between 11 and 15 g L−1 and static mixer lengths between 2.5 and 4.2 m. For the XGSM, ME purities of greater than 92 wt% were achieved for KOH loadings and static mixer lengths in the ranges of 11–15 g L−1 and 3.6–5.0 m, respectively, as shown in Fig. 4c. Therefore, the CPSM reactor outperformed the XGSM reactor in terms of the catalyst requirement and static mixer length, efficiently converting RPO to MEs at lower catalyst concentrations and reaction times. The dependence of the ME purity on the methanol content and static mixer length was also evaluated for the XGSM and CPSM reactors, as plotted in Fig. 4g and h, respectively. For the CPSM reactor, ME purities exceeding 97.5 wt% were attained for methanol contents in the range of 26–36 vol% and static mixer lengths in the range of 3.0–5.0 m (Fig. 4h). In the case of the XGSM reactor, the highest ME content of 93 wt% was obtained for static mixer lengths greater than 4.0 m and methanol contents in the range of 26–38 vol% (Fig. 4g).
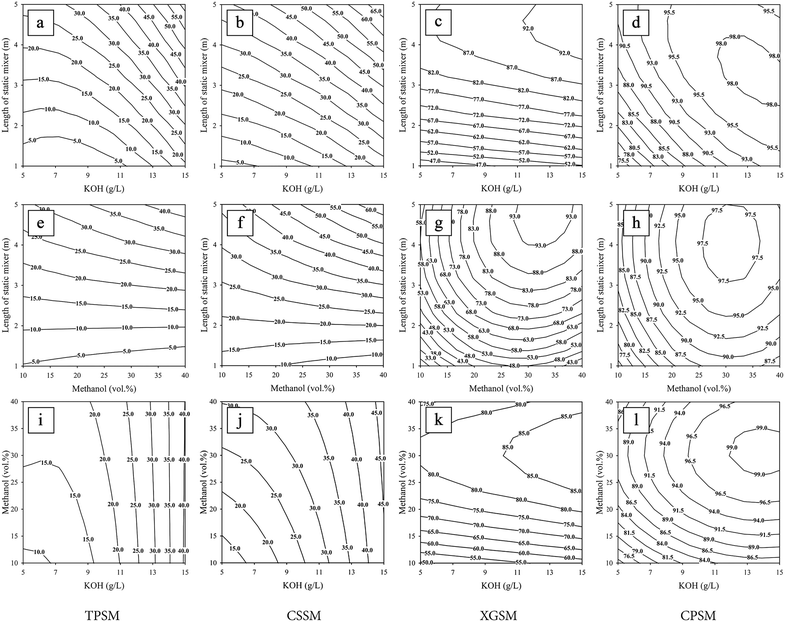 |
| Fig. 4 Contour plots used to determine the optimal conditions for continuous biodiesel production, showing the effects of (a–d) KOH loading and static mixer length, (e–h) methanol content and static mixer length, and (i–l) KOH loading and methanol content on the ME purities for the TPSM, CSSM, XGSM, and CPSM, respectively. | |
The CPSM displayed superior ME conversion to the other three types of static mixers, with a short residence time of 132 s (for a mixer length of 5 m). The effects of the KOH loading and methanol content on the ME purity for the CPSM reactor are shown in Fig. 4l. ME purities of greater than 99 wt% were observed for KOH loadings in the range of 12–15 g L−1 and methanol contents in the range of 26–35 vol%. For the XGSM reactor, KOH loadings between 11 and 15 g L−1 and methanol contents between 23 and 38 vol% afforded ME purities in excess of 85 wt%, as shown in Fig. 4k. When the methanol content was increased for the CPSM, the ME purities decreased when methanol is used at 31 vol%, as illustrated in Fig. 4h and l. Therefore, values outside the selected range of methanol are considered for the CPSM because a high methanol concentration is required to enhance mass transfer and drive the transesterification equilibrium forward to obtain high biodiesel yields. However, an excessive amount of methanol in the reaction could potentially dilute the base catalyst, resulting in reduced biodiesel yield. Similar results were reported by Khoobbakht et al., who investigated the effects of experimental parameters such as the methanol-to-oil molar ratio, KOH concentration, and reaction temperature on the transesterification of waste canola cooking oil.39 Excess methanol was required to drive the conversion of TGs to MEs, which resulted in an increased biodiesel yield. However, excessive amounts of methanol reduced the biodiesel yield.
When comparing ME conversions between the CPSM and XGSM for a short reactor length of 5 m using the RSM analysis, the CPSM was superior to the XGSM in terms of increasing KOH, methanol, and reaction time. However, when the length of the static mixer was increased to 10 m, the XGSM was significantly superior to the CPSM in terms of both high ME purity and pumping power requirements. These details are presented in the subsection entitled “comparison of ME conversions using static mixers”.
Process optimization of biodiesel production using 3D-printed static mixers
The optimization of ME purity in biodiesel was analyzed using RSM with three-factor CCD. Biodiesel production using the 3D-printed static mixers was studied at an RPO flow rate of 25 L h−1 and a reaction temperature of 60 °C. The independent variables, namely, methanol content (10–40 vol%), KOH loading (5–15 g L−1), and static mixer length (1–5 m), were optimized to obtain the highest ME purity, which was analyzed by TLC/FID (Table 5). In the experimental design, these ranges of independent variables resulted in ME purities of 2.57–74.06 wt% for TPSM, 3.48–87.28 wt% for CSSM, 35.02–96.21 wt% for XGSM, and 59.85–98.22 wt% for CPSM, as shown in Table 5. Thus, when the CSSM and TPSM mixers were employed, the ME purity did not exceed 87.28 and 74.06 wt%, respectively, for a mixer length of 5 m. The ME purity results for XGSM and CPSM were solved using the “Solver” add-in for Microsoft Excel to determine the optimized conditions from eqn (7) and (8). For the XGSM, the prediction model delivered an ME purity of 99.11 wt% according to eqn (7) for a methanol content of 31.0 vol%, a KOH loading of 13.5 g L−1, and a static mixer length of 4.6 m. In the actual experiment, the XGSM delivered an ME purity of 98.31 wt%. Therefore, the percentage error between the predicted and actual ME purity for the XGSM was 0.81%. When considering the optimal conditions for the CPSM by solving eqn (8), the predicted ME purity was 99.77 wt% for a methanol content of 30.9 vol%, a KOH concentration of 13.3 g L−1, and a static mixer length of 3.4 m. In the actual experiment, the CPSM afforded an ME purity of 99.81 wt%, corresponding to an error of 0.04%. Therefore, these predictive models can be considered to provide accurate and acceptable estimates of ME production. The corresponding biodiesel yields after purification were 98.3 and 98.5 vol% for the CPSM and XGSM, respectively. Table 8 summarizes the optimal conditions, biodiesel compositions, and yields for the different types of 3D-printed static mixers in the continuous transesterification process.
Table 8 Optimal conditions, compositions, and yields for continuous biodiesel production using various types of static mixers
Result |
Static mixer type |
TPSM |
CSSM |
XGSM |
CPSM |
The pumping power of the static mixers was calculated based on an RPO flow rate of 25 L h−1 under optimal conditions.
|
Optimal conditions |
|
|
|
|
Methanol content (vol%) |
40.0 |
40.0 |
31.0 |
30.9 |
Potassium hydroxide loading (g L−1) |
15.0 |
15.0 |
13.5 |
13.3 |
Static mixer length (m) |
5.0 |
5.0 |
4.6 |
3.4 |
Methyl ester purity from predictive model (wt%) |
66.78 |
79.03 |
99.11 |
99.77 |
Experimental compositions |
|
|
|
|
Methyl esters (wt%) |
|
|
98.31 |
99.81 |
Triglycerides (wt%) |
|
|
0.00 |
0.00 |
Diglycerides (wt%) |
|
|
1.35 |
0.08 |
Monoglycerides (wt%) |
|
|
0.21 |
0.09 |
Free fatty acids (wt%) |
|
|
0.13 |
0.02 |
Pumping power (W)a |
|
|
0.23 |
0.43 |
Yields |
|
|
|
|
Crude biodiesel (vol%) |
|
|
110.0 |
109.6 |
Purified biodiesel (vol%) |
|
|
98.5 |
98.3 |
Comparison of ME conversions using static mixers
As described in the previous subsection, the CPSM reactor was superior to the XGSM reactor for a static mixer length of 5 m. For the results described in this subsection, the static mixer length was increased to 10 m and the ME conversion using the CPSM was compared with those using the other types of static mixers (XGSM, CSSM, TPSM, and PFR) under optimal conditions for continuous ME production. The influence of the mixing length on the ME purity was investigated under the optimal CPSM conditions of 30.9 vol% methanol and 13.3 g L−1 KOH along a 10 m reactor with a 25 L h−1 RPO flow rate at 60 °C. As shown in Fig. 5, the ME purity sharply increased with increasing mixing length for the CPSM and XGSM reactors, and an equilibrium ME purity of 99 wt% was achieved after mixing lengths of 4 and 6 m, respectively. For the CSSM reactor, the ME purity slowly increased to >99 wt% over the entire mixing length. By contrast, the ME purities for the TPSM and PFR reactors did not exceed 81.91 and 21.08 wt%, respectively, even at a mixing length of 10 m. Therefore, the ME purity and pumping power requirements for the other three reactor types (CSSM, XGSM, and CPSM) were examined in more detail. The CSSM, XGSM, and CPSM reactors produced biodiesel with ME purities exceeding 99 wt% ME at mixing lengths of 10, 6, and 4 m, respectively. Thus, the CSSM reactor exhibited poor mixing performance and was unable to successfully blend the oil and methanol phases within a short residence time. Considering the pumping power requirements relative to the static mixer length, the CPSM required greater pumping power than the CSSM and the XGSM owing to its higher pressure drop. To achieve an ME purity of 99 wt%, pumping powers of 0.31, 0.30, and 0.51 W were required at static mixer lengths of 10, 6, and 4 m for the CSSM, XGSM, and CPSM reactors, respectively. Overall, the XGSM reactor was preferable because it converted the oil to high-purity esters faster than the CSSM and required less pumping power than either the CSSM or the CPSM. The XGSM reactor reduced the pumping power by 4% and 70% compared with the CSSM and CPSM reactors, respectively. A similar result was reported by Theron and Sauze, who studied an emulsification process using static mixers.30 They observed that an XGSM and a CPSM were associated with higher energy costs and a lower emulsion droplet size than the other designs (CSSM and TPSM). Moreover, the mean droplet size of the emulsion obtained using the XGSM was lower than that obtained using the CPSM. On the basis of the obtained experimental results, the XGSM was the most suitable among the four types of static mixers tested when considering the correlation between the high reaction rate and low pressure drop during continuous biodiesel production. In addition, the CPSM reactor displayed some particular advantages, such as a small installation space, the highest mixing intensity, lower chemical consumption, and a short reaction time. The CPSM mixer is also suitable for other mixing applications requiring intensive mixing within a short mixing time, although it requires more pumping power than other types of static mixers.
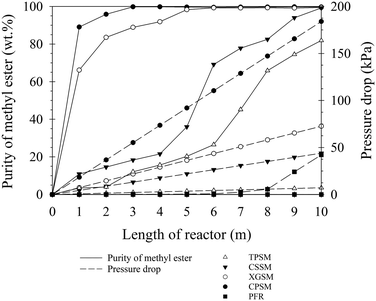 |
| Fig. 5 ME purities and calculated pressure drops for various reactor types under the optimal conditions for the CPSM (30.9 vol% methanol and 13.3 g L−1 KOH). | |
Conclusions
In this study, various 3D-printed static mixer reactors (TPSM, CSSM, XGSM, and CPSM) were evaluated in a continuous ME production process from RPO. In terms of ME conversion, the CPSM reactor was clearly superior to the other reactor types. An ME purity exceeding 99 wt% was achieved with the CPSM under the optimal conditions of a methanol content of 30.9 vol%, a KOH loading of 13.3 g L−1, and a static mixer length of 3.4 m in a short residence time of 132 s. Thus, the CPSM was more effective than the TPSM, CSSM, and XGSM. Nevertheless, a high pressure drop was observed in the CPSM reactor, necessitating a high pumping power. A fast reaction rate and low pressure drop are required to reduce the chemical and energy consumption during continuous biodiesel production. Consequently, the XGSM reactor was found to be more suitable than the CSSM reactor because it rapidly converted oil into high-purity esters with less pumping power than the CSSM and CPSM reactors. Further studies should focus on the feasibility of 3D-printed XGSM and CPSM combinations to produce high-purity esters with low pumping power requirements.
Author contributions
This project was led by Krit Somnuk. Kritsakon Pongraktham and Krit Somnuk conceived, designed, data curation, and validated the research. The experimental works, including reactor setup, calibration, and experiments, were performed by Kritsakon Pongraktham and supervised by Krit Somnuk. Funding acquisition was carried out by Krit Somnuk. Both authors contributed to writing and revising the manuscript and have approved the submitted version.
Conflicts of interest
There are no conflicts to declare.
Acknowledgements
This research project was supported by the National Research Council of Thailand (NRCT) (Contract no. N41A650121) and Prince of Songkla University (Grant No. ENG6201064S).
References
- J. Du, H. A. Rakha, F. Filali and H. Eldardiry, Int. J. Transp. Sci. Technol., 2021, 10, 184–196 CrossRef
.
- L. V. Smith, N. Tarui and T. Yamagata, Energy Econ., 2021, 97, 105170 CrossRef
.
- S. Zivkovic and M. Veljkovic, Environ. Sci. Pollut. Res., 2018, 25, 191–199 CrossRef
.
- H. M. Mahmudul, F. Y. Hagos, R. Mamat, A. A. Adam, W. F. W. Ishak and R. Alenezi, Renewable Sustainable Energy Rev., 2017, 72, 497–509 CrossRef CAS
.
- F. Jaliliantabar, B. Ghobadian, A. P. Carlucci, G. Najafi, A. Ficarella, L. Strafella, A. Santino and S. D. Domenico, Fuel, 2018, 222, 156–174 CrossRef CAS
.
- P. Tamilsevan, N. Nallusamy and S. Rajkumar, Renewable Sustainable Energy Rev., 2017, 79, 1134–1159 CrossRef
.
- A. S. Elgharbawy, W. A. Sadik, O. M. Sadek and M. A. Kasaby, Biomass Bioenergy, 2021, 146, 105997 CrossRef CAS
.
- K. Somnuk, T. Prasit and G. Prateepchaikul, Energy Convers. Manage., 2017, 140, 91–97 CrossRef CAS
.
- M. A. Rahman, M. A. Aziz, R. A. Al-khulaidi, N. Sakib and M. Islam, J. Radiat. Res. Appl. Sci., 2017, 10, 140–147 CrossRef CAS
.
- M. Tabatabaei, M. Aghbashlo, M. Dehhaghi, H. K. S. Panahi, A. Mollahosseini, M. Hosseini and M. M. Soufiyan, Prog. Energy Combust. Sci., 2019, 74, 239–303 CrossRef
.
- Y. M. Oo, G. Prateepchaikul and K. Somnuk, Ultrason. Sonochem., 2021, 73, 105529 CrossRef CAS PubMed
.
- A. Ghanem, T. Lemenand, D. D. Valle and H. Peerhossaini, Chem. Eng. Res. Des., 2014, 92, 205–228 CrossRef CAS
.
- C. F. Joaquim Jr., A. Reynol, E. Cekinski, M. M. Seckler and J. R. Nunkez, Can. J. Chem. Eng., 2011, 89, 734–744 CrossRef
.
- S. M. Hosseini, K. Razzaghi and F. Shahraki, AIChE J., 2018, 65, 1126–1133 CrossRef
.
- R. Alamsyah, A. H. Tambunan, Y. A. Purwanto and D. Kusdiana, Agric. Eng. Int.: CIGR J., 2010, 12, 99–106 Search PubMed
.
- P. Sungwornpatansakul, J. Hiroi, Y. Nigahara, T. K. Jayasinghe and K. Yoshikawa, Fuel Process. Technol., 2013, 116, 1–8 CrossRef CAS
.
- K. Somnuk, K. Wijitsopa and G. Prateepchaikul, Biofuels, 2018, 9, 331–339 CrossRef CAS
.
- V. P. Nguyen, H. H. M. Nguyen, D. T. Nguyen, H. L. Nguyen and T. M. Huynh, Biofuels, 2018, 9, 1–8 Search PubMed
.
- K. Somnuk, N. Soysuwan and G. Prateepchaikul, Renewable Energy, 2019, 131, 100–110 CrossRef CAS
.
- H. B. Meng, M. Y. Song, Y. F. Yu, X. H. Jiang, Z. Y. Wang and J. H. Wu, Int. J. Chem. React. Eng., 2016, 15, 1–21 Search PubMed
.
- L. Muruganandam, D. Kunal and G. O. Melwyn, J. Appl. Fluid Mech., 2018, 11, 107–114 CrossRef
.
- U. El-Jaby, M. Cunningham and T. F. L. McKenna, AIChE J., 2011, 57, 1585–1594 CrossRef CAS
.
- D. Frascari, M. Zuccaro, D. Pinelli and A. Paglianti, Energy Fuels, 2008, 22, 1493–1501 CrossRef CAS
.
- S. Wickramasinghe, T. Do and P. Tran, Polymer, 2020, 12, 1529 CAS
.
- L. Zhao, M. Zhang, B. Chitrakar and B. Adhikari, Crit. Rev. Food Sci. Nutr., 2021, 61, 3489–3503 CrossRef CAS
.
- K. Pongraktham and K. Somnuk, Mater. Sci. Forum, 2020, 998, 134–139 Search PubMed
.
- M. Domingo-Espin, J. A. Travieso-Rodriguez, R. Jerez-Mesa and J. Lluma-Fuentes, Materials, 2018, 11, 2521 CrossRef
.
- H. Meng, M. Han, Y. Yu, Z. Wang and J. Wu, Int. J. Heat Mass Transfer, 2020, 156, 119788 CrossRef
.
- S. Hirschberg, R. Koubek, F. Moser and J. Schock, Chem. Eng. Res. Des., 2009, 87, 524–532 CrossRef CAS
.
- F. Theron and N. L. Sauze, Int. J. Multiphase Flow, 2011, 37, 488–500 CrossRef CAS
.
-
Nantong Langgao Petrochemical Equipment, LG type static mixer, https://www.langgao.com/products_show.asp?product_ID=238, (accessed 30 May 2022).
-
J. L. Y. Chuan, Experimental and numerical investigation of a static mixer for the production of biodiesel, Doctor of Philosophy thesis, School of Engineering, Monash University Sunway Campus, Malaysia, 2012, pp. 1–191 Search PubMed
.
- N. Kiss, G. Brenn, H. Purcher, J. Wieser, S. Scheler, H. Jennewein, D. Suzzi and J. Khinast, Chem. Eng. Sci., 2011, 66, 5084–5094 CrossRef CAS
.
- M. Stec and P. M. Synowiec, Can. J. Chem. Eng., 2017, 95, 2156–2167 CrossRef CAS
.
- D. Revathi and K. Saravanan, Chem. Ind. Chem. Eng. Q., 2020, 26, 329–335 CrossRef CAS
.
- H. G. How, Y. H. Teoh, H. H. Masjuki, H. T. Nguyen, M. A. Kalam, H. G. Chuah and A. Alabdulkarem, Renewable Energy, 2019, 139, 515–529 CrossRef CAS
.
-
Y. A. Cengel and J. M. Cimbala, Fluid mechanics: fundamental and applications, McGraw-Hill Education, New York, 4th edn, 2017, pp. 352–424 Search PubMed
.
- C. B. Ezekannagha, C. N. Ude and O. D. Onukwuli, Egypt. J. Pet., 2017, 26, 1001–1011 CrossRef
.
- G. Khoobbakht, K. Kwheiralipour, H. Rasouli, M. Rafiee, M. Hadipour and M. Karimi, Energy, 2020, 196, 117092 CrossRef CAS
.
- S. T. Keera, S. M. E. Sabagh and A. R. Taman, Fuel, 2011, 90, 42–47 CrossRef CAS
.
- D. Rauline, J. M. L. Blevec, J. Bousquet and P. A. Tanguy, Chem. Eng. Res. Des., 2000, 78, 389–396 CrossRef CAS
.
- E. Fourcade, R. Wadley, H. C. J. Hoefsloot, A. Green and P. D. Iedema, Chem. Eng. Sci., 2001, 56, 6729–6741 CrossRef CAS
.
- A. Ismail, A. Khalid and T. Y. Kiong, Journal of Complex Flow, 2020, 1, 16–22 Search PubMed
.
- R. Wadley and M. K. Dawson, Chem. Eng. Sci., 2005, 60, 2469–2478 CrossRef CAS
.
- W. Cheng, J. Huang and J. Chen, J. Chem. Technol. Biotechnol., 2016, 91, 327–335 CrossRef CAS
.
- M. Mohamad, N. Ngadi, S. L. Wong, M. Jusoh and N. Y. Yahya, Fuel, 2017, 190, 104–112 CrossRef CAS
.
|
This journal is © The Royal Society of Chemistry 2023 |
Click here to see how this site uses Cookies. View our privacy policy here.