DOI:
10.1039/D3RA07366A
(Paper)
RSC Adv., 2023,
13, 35659-35671
Copper salt of a DABCO-based molten salt: a high-performance catalyst in the one-pot synthesis of 3,4-dihydropyrimidine and polyhydroquinoline derivatives†
Received
29th October 2023
, Accepted 27th November 2023
First published on 6th December 2023
Abstract
In this study, [DABCO](SO3H)2CuCl4 as a novel DABCO-based molten salt with dual acidic functionality (Brønsted and Lewis) has been synthesized, characterized and used as a high-performance catalyst in the one-pot synthesis of 3,4-dihydropyrimidine and polyhydroquinoline derivatives. The identification of this catalyst was accomplished by using techniques such as infrared spectroscopy (FT-IR), X-ray diffraction (XRD), thermo gravimetric analysis (TGA), field emission scanning electron microscopy (FESEM) and energy dispersive X-ray (EDS) spectroscopy. Excellent efficiency, short reaction times, a simple working method and also use of a recyclable catalyst are the considerable advantages of this process.
Introduction
One of the twelve principles of green chemistry is the usage of catalysts to design new synthetic processes.1 Catalysts have been used for the purpose of environmental protection, economic benefits, and eliminating or reducing waste and destructive materials in the petrochemical industry, and chemical and pharmaceutical processes.2 Among the various catalysts, ionic liquids have found a special place in green chemistry due to their unique properties as benign catalysts for the environment.3 Nowadays, ionic liquids have ended up as a fervent topic of research in several fields of the experimental sciences, including chemistry, physics, biology, and engineering.4 Ionic liquids are organic salts containing organic or inorganic cations and anions and their physical properties, polarity, and acidity/alkalinity can be adjusted by changing their cations and anions.5,6 DABCO, as a result of having features such as having the nitrogen atom pair in the main structure, being consistent with the environment, being easy to carry, being non-toxic and having high reactivity has been used as a source of a suitable cation in the synthesis of various ionic liquids.7,8 DABCO-based ionic liquids are not only used as catalysts in some organic transformations, but some of them can show biological activities such as antimicrobial and antibacterial ones.9
Metal-containing ionic liquids are a group of ionic liquids that combine the properties of ionic liquids with the magnetic, optical or catalytic properties of metal salts.10 One of the most important features of these compounds is their controllable acidity, which makes them suitable for use as catalysts. Their acidic nature can be Lewis or Brønsted–Lewis type.11 The performance of this type of ionic liquids as Lewis acids depends on the electrophilicity of the metal and the availability of its LUMO orbital.12 Also, Brønsted–Lewis acidic ionic liquids (BLAILs) can be obtained from the reaction of Lewis acid metal salts or oxides with Brønsted acid ionic liquids. BLAILs are useful catalysts with dual acidic performance in many organic transformations, especially in multi-component reactions, because some synthesis processes require both types of acidity in one or more stages of the reaction. Common metals such as Al, Zn and Fe have been used as Lewis acids in Brønsted–Lewis acidic ionic liquids. Recently, Cu-containing ionic liquids such as [(HSO3)3C3C1im][(1/2Cu2+)SO42−] and [(HSO3)3C3C1im]− [(1/2H+·1/4Cu2+)SO42−] are prepared by changing the molar ratio of Cu to Brønsted acidic ionic liquids.13
Over the past few years, chemists have focused on the development of new methods that pose a lower risk to human health and environment, and based on this many synthetic processes have been modified. Among these, multi-component reactions have become more important than multi-step reactions due to their economic nature, energy and time-saving factor, and convergence in the field of organic synthesis. The synthesis of dihydropyrimidinones and polyhydroquinolines are interesting examples of such reactions.14–17
Dihydropyrimidinones and polyhydroquinolines are known because of their wide range of biological responses. Dihydropyrimidinones show anti-tumor,18 anti-bacterial,19 anti-viral,20 anti-inflammatory,21 calcium channel blocker,22 antihypertensive,23 and other activities. Also, important drug functions such as anti-tumor,24 bronchodilators,25 anti-atherosclerotic,26 vasodilators, anti-inflammatory,27 modulate calcium channels28 and antidiabetic29 properties have been reported for polyhydroquinoline derivatives.
These types of compounds are usually prepared via Bigenilli reaction (the one-pot three-component condensation of aldehydes, β-diketones and urea)30–32 and Hantzsch condensation reaction (the one-pot four-component reaction of aldehydes, β-diketones, β-ketoesters and ammonium acetate), respectively.33,34 Different strategies and reagents have been used in this field, which of them use of microwave, ultrasound, solid reagents with supports, oxides of transition metals,35 Al2O3/MeSO3H,36 zirconia sulfuric acid,37 metal oxide-MWCNTs nanocomposites38 (in the synthesis of 3,4-dihydropyrimidinone), praseodymium(III) anchored on CoFe2O4MNPs,39 Yb(OTf)3,40 nickel nanoparticle,41 p-TSA,42 zinc oxide,43 Fe3O4@MCM-41@Cu-P2C,44 and Cu(II)-PAA/M-MCM-41NC45 (in the synthesis of polyhydroquinolines) are examples although these methods have undeniable advantages but most of them suffer from disadvantages such as the usage of expensive reagents, low efficiency, use of harmful heavy metal salts to the environment, tedious working methods, toxic solvents, being uneconomical, and problems in the preparation and non-recovery of catalysts. Therefore, the introduction of a high-performance catalytic system to synthesize these compounds and overcome all or some of the mentioned disadvantages is still required. In this article, [DABCO](SO3H)2CuCl4 is introduced as a new acidic catalyst which is efficiently able to promot the synthesis of 3,4-dihydropyrimidinone and polyhydroquinoline derivatives under mild conditions with considerable yields in short times.
Experimental
All required chemicals and solvents were purchased from Fluka, Merck, and Aldrich chemical companies. All yields refer to their isolated products. The products were stabilized by comparison of their physical constants, IR, and NMR spectra with reported samples in the resources. Thin layer chromatography (TLC) was used on polygram SILG/UV 254 plates, for the determination of the purity of the substrates and monitoring of the progress of the reaction.
Preparation of [DABCO](SO3H)2CuCl4
Diamino-bicyclo[2,2,2]octane (DABCO) (10 mmol, 1.12 g) was dissolved in 40 mL of the CH2Cl2. Then, ClSO3H (20 mmol, 1.330 mL) was added drop-wise in an ice bath (0 °C) to the prepared mixture during 5 min. The reaction was stirred for 2 hours at room temperature. After completion of the reaction, the obtained product was washed with diethyl ether and dried under vacuum. Finally, [DABCO](SO3H)2Cl2 was achieved as a white compound.46 In continue, CuCl2 (10 mmol, 1.345 g) was added to [DABCO](SO3H)2Cl2 (10 mmol, 3.45 g) in 40 mL of CH3CN. Then, the reaction mixture was stirred for 24 h under reflux conditions and after completion of the reaction, the obtained compound was washed with diethyl ether and dried under vacuum. Finally, [DABCO](SO3H)2CuCl4 was obtained as a green solid (4.79 g, 95% yield, Scheme 1).
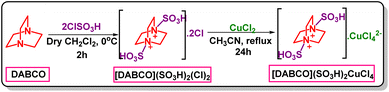 |
| Scheme 1 Preparation of [DABCO](SO3H)2CuCl4. | |
General procedure for the synthesis of 3,4-dihydropyrimidinone derivatives
20 mg of [DABCO](SO3H)2CuCl4 was added to a mixture of aldehyde (1 mmol), ethyl acetoacetate (1 mmol) and urea (1.5 mmol) in a 10 mL round bottom flask and the reaction mixture was stirred in an oil bath at 120 °C in the absence of solvent. The reaction progress was controlled by thin layer chromatography (TLC) [n-hexane
:
ethyl acetate (2
:
6)]. At the end of the reaction, water (10 mL) was added to the reaction mixture and the product was separated from the catalyst by filtration. Finally, recrystallization from ethanol was performed in order to purify the requested product with high efficiency.
General procedure for the synthesis of polyhydroquinoline derivatives
In a 10 mL round bottom flask, 40 mg of [DABCO](SO3H)2CuCl4 was added to a mixture of aldehyde (1 mmol), dimidone or 1,3-cyclohexanone (1 mmol), ammonium acetate (3 mmol), and ethyle or methyl acetoacetate (1 mmol). Then the reaction mixture was stirred under solvent-free conditions in an oil bath at 120 °C for an appropriate period of time. The progress of the reaction was followed by thin-layer chromatography (TLC) [n-hexane
:
ethyl acetate (2
:
6)]. After completion of the reaction, water (10 mL) was added to the reaction mixture and the product was separated from the catalyst by filtration. Finally, the product was purified by recrystallization from ethanol.
Results and discussion
Instrumentation
Melting points were measured by an electrothermal IA9100 melting point apparatus (United Kingdom) in capillary tubes. The Fourier-transform infrared spectros (FT-IR) were recorded with a VERTEX 70 (Brucker, Germany) instrument using KBr pellets for the obtained solid samples. X-ray diffraction (XRD) was performed on an X'Pert Pro instrument (Panalytical Company Netherlands). Field emission scanning electron microscopy (FESEM) was recorded using a TE-SCAN model Sigma VP (ZEISS Company in Germany). Thermogravimetric analysis (TGA) was performed on a TGA-DTA METTLER TGA/STTA 851 (Swiss).
Catalyst characterization
The FT-IR spectra of DABCO, [DABCO](SO3H)2Cl2 and [DABCO](SO3H)2CuCl4 are compared in Fig. 1. A large number of absorption bands are observed in DABCO's FT-IR spectrum which can be due to different types of stretching and bending vibrations in this compound. The appearance of new absorption bands in the FT-IR spectrum of [DABCO](SO3H)2Cl2 in the regions of 1179 cm−1 and 581 cm−1 can be attributed to the vibrations related to S
O and S–O, respectively.47 In addition, the absorption bands at 1852 cm−1 and 885 cm−1 are related to N–S bond vibrations.48 A number of absorption bands in the FT-IR spectrum of [DABCO](SO3H)2CuCl4 catalyst have been removed or reduced in intensity, which can be due to the presence of copper metal and the created limitations in the vibrations of the rings.
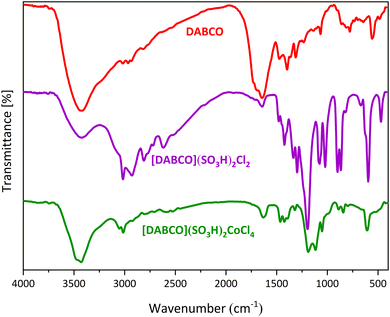 |
| Fig. 1 FT-IR spectra of DABCO, [DABCO](SO3H)2Cl2 and [DABCO](SO3H)2CuCl4. | |
The thermogravimetric analysis (TGA) was performed in order to compare the thermal stability of DABCO and [DABCO](SO3H)2CuCl4 (Fig. 2). As can be seen, DABCO completely degrades before 150 °C, while [DABCO](SO3H)2CuCl4 catalyst has higher thermal stability that can be due to hydrogen bonding and the presence of copper metal in the structure of the catalyst. In the TGA curve of the [DABCO](SO3H)2CuCl4, two weight losses are observed in the range of 150–250 °C and 250–450 °C, which can be the result of the thermal degradation of DABCO and sulfonic groups in its structure.
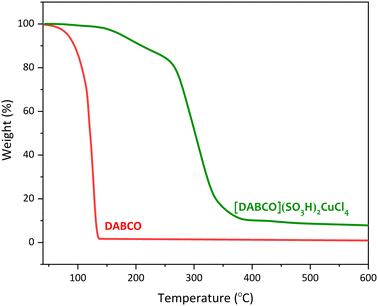 |
| Fig. 2 TGA curves of DABCO and [DABCO](SO3H)2CuCl4. | |
The X-ray diffraction patterns of DABCO and [DABCO](SO3H)2CuCl4 are shown in Fig. 3. In the diffraction pattern related to DABCO, ten peaks appeared around 2θ = 16.7, 17.2, 18.5, 19.4, 30.2, 30.9, 33.15, 35.46, 41.96 and 45.24 confirming DABCO.49 The intensity of these peaks has decreased in the diffraction pattern of the catalyst, which is due to decreasing its crystallinity. Furthermore, the increase in the number of peaks in this pattern can be a result of the presence of CuCl4 in the catalyst structure.
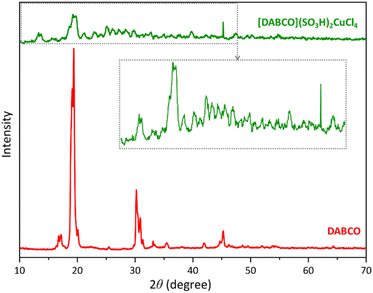 |
| Fig. 3 XRD patterns of DABCO and [DABCO](SO3H)2CuCl4. | |
The results of EDS analysis obtained from [DABCO](SO3H)2CuCl4 indicate the presence of all expected elements (C, O, N, S, Cl, Cu) in the structure of the sample (Fig. 4) showing its successful formation.
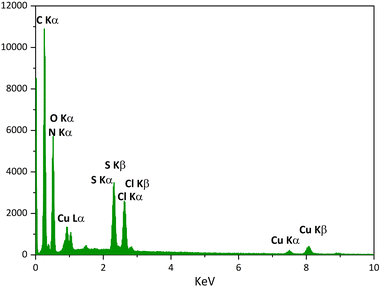 |
| Fig. 4 EDS analysis of [DABCO](SO3H)2CuCl4. | |
Fig. 5 shows the field emission scanning electron microscopy (FESEM) images of DABCO and [DABCO](SO3H)2CuCl4 which specifies the surface morphology, size distribution and particle shape of them. The pictures show that DABCO has a string structure with tiny holes. While the catalyst has continuous particles and a rough surface which can be due to the presence of intermolecular hydrogen bonds between and also dipole–dipole interaction between the catalyst particles.
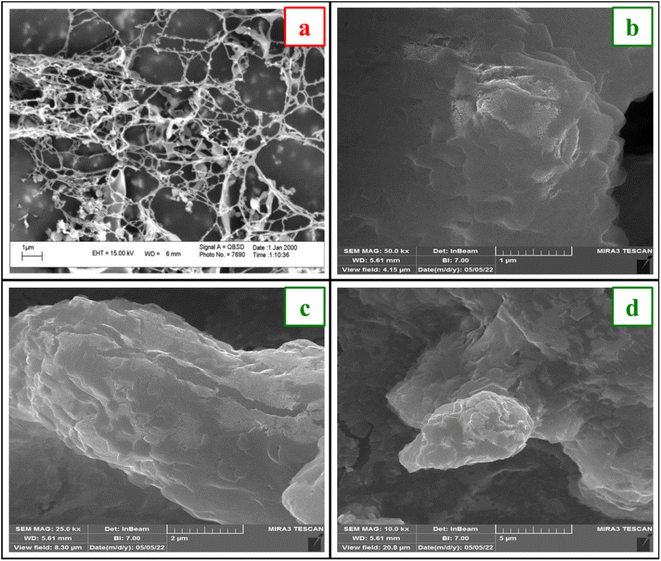 |
| Fig. 5 FESEM images of DABCO (a (1 μm)) and [DABCO](SO3H)2CuCl4 (b (1 μm), c (2 μm), d (5 μm)). | |
Catalytic activity
After successful identification of the prepared catalyst, it has been suggested that this reagent may be able to accelerate reactions that require an acidic catalyst. Therefore, we decided to study the performance of this catalyst in the synthesis of 3,4-dihydropyrimidinone derivatives. In this regard, the condensation of 4-chlorobenzaldehyde, ethyl acetate, and urea is selected as the model reaction and the effect of the amounts of the catalyst, solvent, and temperature was investigated on it (Table 1).
Table 1 Optimization of the reaction conditions for the synthesis of 3,4-dihydropyrimidinones catalyzed by [DABCO](SO3H)2CuCl4
Entry |
Catalyst (mg) |
Temperature (°C) |
Solvent |
Time (min) |
Conversion (%) |
1 |
20 |
80 °C |
Solvent free |
25 |
Mixed products |
2 |
20 |
100 °C |
Solvent free |
15 |
100 |
3 |
30 |
100 °C |
Solvent free |
14 |
100 |
4 |
40 |
100 °C |
Solvent free |
10 |
100 |
5 |
20 |
120 °C |
Solvent free |
10 |
100 |
6 |
30 |
120 °C |
Solvent free |
9 |
100 |
7 |
40 |
120 °C |
Solvent free |
8 |
100 |
8 |
20 |
Reflux |
H2O |
70 |
Not completed |
9 |
20 |
Reflux |
C2H5OH |
75 |
Not completed |
10 |
20 |
80 °C |
C2H5OH : H2O (1 : 1) |
80 |
Not completed |
It was found that the reaction can be performed in the absence of solvent. It should be mentioned that the reaction in solvents such as water and ethanol even under reflex conditions did not proceed considerably. Further investigations on the influence of the amounts of the catalyst and temperature clarified that 20 mg of the catalyst at 120 is enough to accomplish the reaction in shortest time with good efficiency (Table 1, entry 5) (Scheme 2).
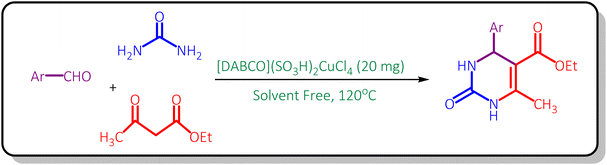 |
| Scheme 2 Synthesis of 3,4-dihydropyrimidinone derivatives catalyzed by [DABCO](SO3H)2CuCl4. | |
After determining optimal conditions, in order to generalize this method, a variety of aromatic aldehydes containing electron-donating or electron-withdrawing functional groups in ortho, meta, and para positions of the aromatic ring were used to synthesize a variety of 3,4-dihydropyrimidinone derivatives under these conditions. The results show that all derivatives are synthesized in short reaction time with high yields (Table 2).
Table 2 Synthesis of 3,4-dihydropyrimidinone derivatives in the presence of [DABCO](SO3H)2CuCl4a
Entry |
Aldehyde |
Product |
Time (min) |
Yielda (%) |
Melting point (°C) |
Found |
Reported |
Isolated yields. |
1 |
 |
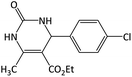 |
10 |
92 |
195–197 |
198–202 (ref. 50) |
2 |
 |
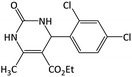 |
25 |
94 |
231–233 |
228–230 (ref. 51) |
3 |
 |
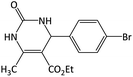 |
30 |
94 |
228–230 |
232–234 (ref. 52) |
4 |
 |
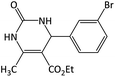 |
28 |
93 |
197–199 |
185–187 (ref. 53) |
5 |
 |
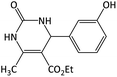 |
9 |
95 |
159–160 |
165–167 (ref. 54) |
6 |
 |
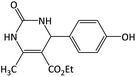 |
15 |
92 |
194–196 |
197–199 (ref. 55) |
7 |
 |
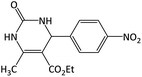 |
14 |
95 |
204–206 |
205–207 (ref. 56) |
8 |
 |
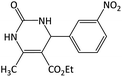 |
10 |
93 |
217–218 |
224–226 (ref. 57) |
9 |
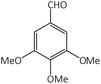 |
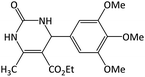 |
9 |
97 |
213–215 |
213–215 (ref. 58) |
10 |
 |
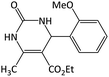 |
22 |
96 |
245–247 |
252–254 (ref. 59) |
11 |
 |
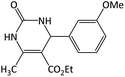 |
14 |
95 |
210–212 |
207–209 (ref. 60) |
12 |
 |
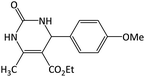 |
45 |
80 |
200–202 |
205–207 (ref. 61) |
13 |
 |
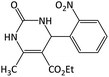 |
16 |
98 |
235–237 |
233–235 (ref. 62) |
14 |
 |
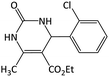 |
30 |
94 |
220–222 |
219–221 (ref. 61) |
15 |
 |
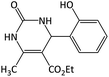 |
22 |
90 |
190–192 |
200–202 (ref. 63) |
16 |
 |
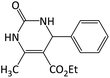 |
32 |
88 |
195–197 |
201–203 (ref. 64) |
17 |
 |
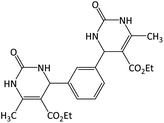 |
8 |
94 |
211–213 |
212–214 (ref. 65) |
After the successful application of [DABCO](SO3H)2CuCl4 as a catalyst in the synthesis of 3,4-dihydropyrimidinones, we decided to study the ability and efficiency of this reagent in the synthesis of polyhydroquinoline derivatives via Hantzsch condensation. In the first step, to find the optimum conditions, a model reaction was performed with a mixture of 4-hydroxybenzaldehyde, ethyl acetoacetate, dimedone, and ammonium acetate in the presence of different amounts of the catalyst in the presence and absence of solvent at a variety of temperatures (Table 3).
Table 3 Optimization of the reaction conditions for the synthesis of polyhydroquinoline catalyzed by [DABCO](SO3H)2CuCl4
Entry |
Catalyst (mg) |
Temperature (°C) |
Solvent |
Time (min) |
Conversion (%) |
1 |
10 |
100 °C |
Solvent free |
20 |
Not completed |
2 |
20 |
100 °C |
Solvent free |
11 |
100 |
3 |
30 |
100 °C |
Solvent free |
10 |
100 |
4 |
40 |
100 °C |
Solvent free |
10 |
100 |
5 |
10 |
120 °C |
Solvent free |
15 |
Not completed |
6 |
20 |
120 °C |
Solvent free |
10 |
100 |
7 |
30 |
120 °C |
Solvent free |
9 |
100 |
8 |
40 |
120 °C |
Solvent free |
6 |
100 |
9 |
40 |
Reflux |
C2H5OH |
58 |
Not completed |
10 |
40 |
Reflux |
H2O |
65 |
Not completed |
11 |
40 |
80 °C |
C2H5OH : H2O (1 : 1) |
70 |
Not completed |
The results obtained show that the reaction of aldehyde (1 mmol) with ethyl acetoacetate (1 mmol), dimedon (1 mmol) and ammonium acetate (2 mmol) was performed in the presence of 40 mg of the catalyst at 120 °C under solvent-free conditions in less times with higher yields (Table 3, entry 8) (Scheme 3).
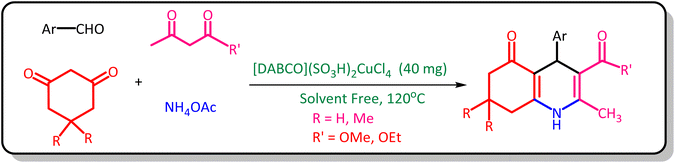 |
| Scheme 3 Synthesis of polyhydroquinoline derivatives catalyzed by [DABCO](SO3H)2CuCl4. | |
In continue and in order to generalize the optimized reaction conditions, a wide range of aldehydes and different β-diketones were used in this four-component condensation. It was found that this method is very efficient for the conversion of aromatic aldehydes containing electron-donor and electron-acceptor substituents, to their corresponding polyhydroquinoline derivatives with good yields in short times (Table 4).
Table 4 Synthesis of polyhydroquinolines derivatives in the presence of [DABCO](SO3H)2CuCl4a
Entry |
Aldehyde |
R |
R′ |
Time (min) |
Yielda (%) |
Melting point (°C) |
Found |
Literature |
Isolated yields. |
1 |
 |
CH3 |
OEt |
6 |
98 |
230–232 |
232–234 (ref. 29) |
2 |
 |
CH3 |
OEt |
10 |
93 |
214–216 |
217–219 (ref. 66) |
3 |
 |
CH3 |
OEt |
27 |
90 |
222–224 |
228–232 (ref. 9) |
4 |
 |
CH3 |
OEt |
21 |
93 |
191–193 |
198–200 (ref. 67) |
5 |
 |
CH3 |
OEt |
11 |
93 |
204–206 |
199–200 (ref. 68) |
6 |
 |
CH3 |
OEt |
15 |
96 |
244–246 |
248–250 (ref. 49) |
7 |
 |
CH3 |
OEt |
18 |
90 |
195–197 |
198–200 (ref. 49) |
8 |
 |
CH3 |
OEt |
35 |
90 |
240–242 |
246–248 (ref. 69) |
9 |
 |
CH3 |
OEt |
8 |
90 |
226–228 |
231–233 (ref. 49) |
10 |
 |
CH3 |
OEt |
6 |
98 |
215–217 |
211–213 (ref. 29) |
11 |
 |
CH3 |
OEt |
8 |
88 |
309–311 |
305–307 (ref. 49) |
12 |
 |
CH3 |
OEt |
10 |
88 |
288–290 |
281–282 (ref. 49) |
13 |
 |
H |
OEt |
2 |
98 |
245–247 |
244–246 (ref. 49) |
14 |
 |
H |
OEt |
2 |
92 |
223–225 |
228–230 (ref. 9) |
15 |
 |
H |
OEt |
11 |
94 |
160–162 |
157–160 (ref. 70) |
16 |
 |
H |
OEt |
3 |
92 |
211–213 |
204–206 (ref. 49) |
17 |
 |
CH3 |
OMe |
8 |
85 |
240–242 |
232–234 (ref. 71) |
18 |
 |
CH3 |
OMe |
4 |
94 |
256–258 |
252–256 (ref. 67) |
19 |
 |
CH3 |
OMe |
10 |
90 |
258–260 |
260–262 (ref. 72) |
20 |
 |
CH3 |
OMe |
8 |
90 |
252–254 |
258–259 (ref. 49) |
A suggested mechanism for the studied reactions in the presence of [DABCO](SO3H)2CuCl4 as the catalyst is shown in Scheme 4. Path (a) is related to the synthesis of 3,4-dihydropyrimidinones. At the first step of this path, the carbonyl group of the aldehyde is activated by the acidic catalyst producing the intermediate (I) through nucleophilic attak of urea. Then, the reaction of the intermediate (I) and the activated ethyl acetate by the catalyst produces the intermediate (II). Finally, intermolecular cyclization of this intermediate and removal of a molecule of water provides the desired product. Path (b) shows the mechanism of the synthesis of polyhydroquinoline derivatives. Firstly, aldehyde and β-diketone (dimedone or 1,3-cyclohexanedione) be converted to their active form by the catalyst and then the Knoevenagel condensation of them lead to the intermediate I′. On the other hand, activated β-ketoester (ethyl acetoacetate and methyl acetoacetate) reacted with the ammonia obtained from ammonium acetate and converted to enamine (intermediate II′) by removing a molecule of water. Then, enamine reacts with intermediate (I′) via Michael addition. Finally, poly-hydroquinoline derivatives are produced by nucleophilic attack of nitrogen on the carbonyl group, intermolecular cyclization and removal of a water molecule.
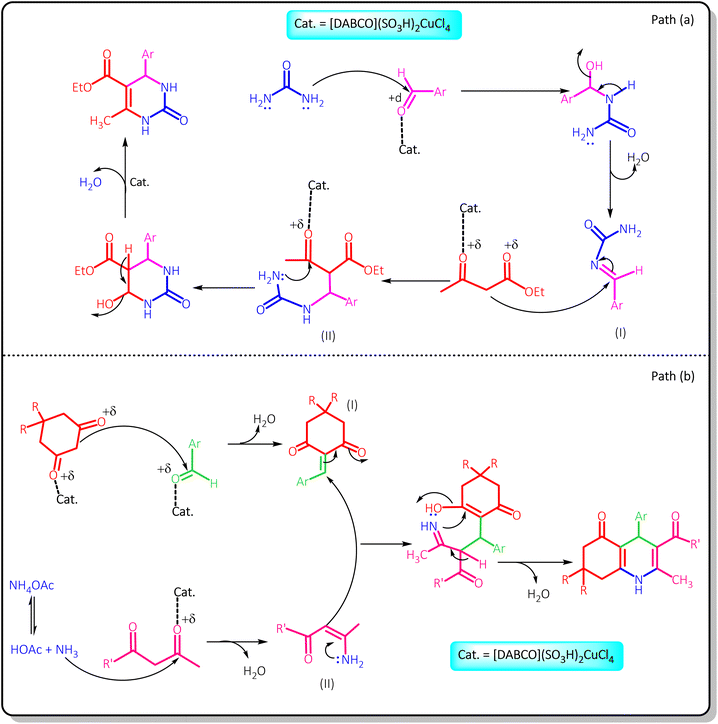 |
| Scheme 4 The proposed mechanism for the synthesis 3,4-dihydropyrimidinones and polyhydroquinolines in the presence of [DABCO](SO3H)2CuCl4. | |
Table 5 compares the performance of [DABCO](SO3H)2CuCl4 in the synthesis of one of the 3,4-dihydropyrimidine and polyhydroquinoline derivatives with some of the previous reported catalysts. The results of this comparison clearly show the superiority of this catalyst in the reduction of the amounts of the catalyst, and reaction times, and increasement of the yields over the other catalytic systems reported in the sources.
Table 5 Comparison of the results obtained from the synthesis of ethyl 4-(4-chlorophenyl)-6-methyl-2-oxo-1,2,3,4-tetrahydropyrimidine-5-carboxylate and ethyl 4-(4-hydroxyphenyl)-2,7,7-trimethyl-5-oxo-1,4,5,6,7,8-hexahydroquinoline-3-carboxylate in the presence of [DABCO](SO3H)2CuCl4 with some of the best results reported in the references
Entry |
Catalyst (mg) [ref.] |
Reaction conditions |
Time (min) |
Yield (%) |
Product |
1 |
Fe3O4@SiO2/TES Mo+HSO4 (60)73 |
C2H5OH/78 °C |
60 |
87 |
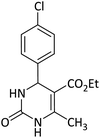 |
2 |
Nafion-Ga (200)74 |
Solvent free/110 °C |
60 |
94 |
3 |
NH4H2PO4/MCM-41 (40)75 |
Solvent free/100 °C |
219 |
72 |
4 |
Al2O3–SO3H (31)76 |
Solvent free/120 °C |
96 |
94 |
5 |
Al(HSO4)3 (27)76 |
Solvent free/100 °C |
55 |
90 |
6 |
Phytic acid (66)77 |
Solvent free/100 °C |
180 |
88 |
7 |
[DABCO](SO3H)2CuCl4 (20) [this work] |
Solvent free/120 °C |
6 |
96 |
8 |
[TBA]2[W6O19] (132)78 |
Solvent free/110 °C |
20 |
91 |
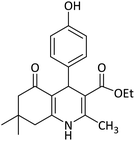 |
9 |
CAN (55)79 |
C2H5OH/reflux |
120 |
89 |
10 |
[(DABCO)2C3H5OH]·2Cl (30)9 |
Solvent free/120 °C |
15 |
90 |
11 |
Aluminized polyborate (75)80 |
Solvent free/100 °C |
25 |
89 |
12 |
Cell-Pr-NHSO3H (50)81 |
C2H5OH/reflux |
50 |
85 |
13 |
MCM-41@Serine@Cu(II) (50)82 |
C2H5OH/reflux |
130 |
91 |
14 |
VDDAP (100)83 |
C2H5OH : H2O/r.t |
90 |
73 |
15 |
[DABCO](SO3H)2CuCl4 (40) [this work] |
Solvent free/120 °C |
6 |
96 |
To evaluate the recyclability of the catalyst, the reaction of 4-hydroxybenzaldehyde with daimedone, ethyl acetoacetate, and ammonium acetate under optimized reaction conditions was investigated. After the completion of the reaction, water was added and the catalyst was separated from the product by filtration. After drying, the recycled catalyst was reused for the same reaction. This process was repeated six times. In all reactions, there was no significant change in the time and yield of the products, which clearly demonstrates the practical recyclability of this catalyst (Fig. 6). Comparison of the FT-IR of the recycled and freshly prepared catalyst shows it stability during the course of the reaction.
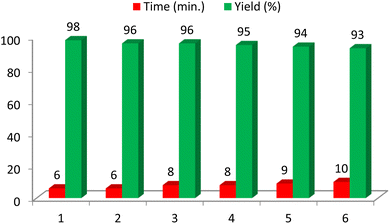 |
| Fig. 6 Reusability of the [DABCO](SO3H)2CuCl4. | |
Conclusions
In conclusion, in this study, the preparation of [DABCO](SO3H)2CuCl4 was described in detail. After identification, it was used as an adequate and cost-effective catalyst in the synthesis of 3,4-dihydropyrimidinone and polyhydroquinoline derivatives. This method shows advantages such as high reaction rates, high efficiency, no use of hazardous organic solvents, ease of the catalyst preparation, and use of a reusable catalyst.
Conflicts of interest
There are no conflicts to declare.
Acknowledgements
We are thankful to the Research Council of the University of Guilan for the partial support of this work.
References
- K. J. Ardila-Fierro and J. G. Hernández, ChemSusChem, 2021, 14, 2145–2162 CrossRef CAS PubMed.
- P. Sarma, A. K. Dutta and R. Borah, Catal. Surv. Asia, 2017, 21, 70–93 CrossRef CAS.
- C. Dai, J. Zhang, C. Huang and Z. Lei, Chem. Rev., 2017, 117, 6929–6983 CrossRef CAS PubMed.
- B. Wang, L. Qin, T. Mu, Z. Xue and G. Gao, Chem. Rev., 2017, 117, 7113–7131 CrossRef CAS PubMed.
- C. G. Yoo, Y. Pu and A. J. Ragauskas, Curr. Opin. Green Sustainable Chem., 2017, 5, 5–11 CrossRef.
- C. Verma, E. E. Ebenso and M. Quraishi, J. Mol. Liq., 2019, 276, 826–849 CrossRef CAS.
- N. Jamasbi, M. Irankhah-Khanghah, F. Shirini, H. Tajik and M. S. N. Langarudi, New J. Chem., 2018, 42, 9016–9027 RSC.
- R. Gupta, M. Yadav, R. Gaur, G. Arora, P. Rana, P. Yadav, A. Adholeya and R. K. Sharma, ACS Omega, 2019, 4, 21529–21539 CrossRef CAS PubMed.
- M. Zabihzadeh, A. Omidi, F. Shirini, H. Tajik and M. S. N. Langarudi, J. Mol. Struct., 2020, 1206, 127730–127740 CrossRef CAS.
- C. Chiappe, C. S. Pomelli, U. Bardi and S. Caporali, Phys. Chem. Chem. Phys., 2012, 14, 5045–5051 RSC.
- K. Li, H. Choudhary and R. D. Rogers, Curr. Opin. Green Sustainable Chem., 2018, 11, 15–21 CrossRef.
- J. Estager, J. Holbrey and M. Swadźba-Kwaśny, Chem. Soc. Rev., 2014, 43, 847–886 RSC.
- A. S. Amarasekara, Chem. Rev., 2016, 116, 6133–6183 CrossRef CAS PubMed.
- M.-N. Chen, L.-P. Mo, Z.-S. Cui and Z.-H. Zhang, Curr. Opin. Green Sustainable Chem., 2019, 15, 27–37 CrossRef.
- R. Afshari and A. Shaabani, ACS Comb. Sci., 2018, 20, 499–528 CrossRef CAS PubMed.
- Z. Zhang, Y. You and C. Hong, Macromol. Rapid Commun., 2018, 39, 1800362–1800374 CrossRef PubMed.
- C. Lamberth, Bioorg. Med. Chem., 2020, 28, 115471–115483 CrossRef CAS PubMed.
- R. V. Patil, J. U. Chavan, D. S. Dalal, V. S. Shinde and A. G. Beldar, ACS Comb. Sci., 2019, 21, 105–148 CrossRef CAS PubMed.
- M. Khodamorady, S. Sohrabnezhad and K. Bahrami, Polyhedron, 2020, 178, 114340–114353 CrossRef CAS.
- N. Khaldi-Khellafi, M. Makhloufi-Chebli, D. Oukacha-Hikem, S. T. Bouaziz, K. O. Lamara, T. Idir, A. Benazzouz-Touami and F. Dumas, J. Mol. Struct., 2019, 1181, 261–269 CrossRef CAS.
- E. Vessally, A. Hassanpour, R. Hosseinzadeh-Khanmiri, M. Babazadeh and J. Abolhasani, Monatsh. Chem., 2017, 148, 321–326 CrossRef CAS.
- Y. Liu, Y. Dang, D. Yin, X. Yang, L. Yang and Q. Zou, Res. Chem. Intermed., 2020, 46, 547–555 CrossRef CAS.
- A. R. Kiasat and J. Davarpanah, Res. Chem. Intermed., 2015, 41, 2991–3001 CrossRef CAS.
- M. Hajjami and B. Tahmasbi, RSC Adv., 2015, 5, 59194–59203 RSC.
- A. Ghorbani-Choghamarani, B. Tahmasbi, P. Moradi and N. Havasi, Appl. Organomet. Chem., 2016, 30, 619–625 CrossRef CAS.
- A. Ghorbani-Choghamarani, M. Mohammadi, T. Tamoradi and M. Ghadermazi, Polyhedron, 2019, 158, 25–35 CrossRef CAS.
- J. Davarpanah, M. Ghahremani and O. Najafi, J. Mol. Struct., 2019, 1177, 525–535 CrossRef CAS.
- A. Maleki, F. Hassanzadeh-Afruzi, Z. Varzi and M. S. Esmaeili, Mater. Sci. Eng. C, 2020, 109, 110502–110536 CrossRef CAS PubMed.
- R. R. Harale, P. V. Shitre, B. R. Sathe and M. S. Shingare, Res. Chem. Intermed., 2017, 43, 3237–3249 CrossRef CAS.
- K. Selvakumar, T. Shanmugaprabha, M. Kumaresan and P. Sami, Synth. Commun., 2018, 48, 223–232 CrossRef CAS.
- L. Moradi and M. Tadayon, J. Saudi Chem. Soc., 2018, 22, 66–75 CrossRef CAS.
- K. A. Dilmaghani, B. Zeynizadeh and H. Parasajam, Phosphorus, Phosphorus, Sulfur Relat. Elem., 2012, 187, 544–553 CrossRef CAS.
- S. Mondal, B. C. Patra and A. Bhaumik, ChemCatChem, 2017, 9, 1469–1475 CrossRef CAS.
- S. K. Das, S. Mondal, S. Chatterjee and A. Bhaumik, ChemCatChem, 2018, 10, 2488–2495 CrossRef CAS.
- P. Gogoi, A. K. Dutta and R. Borah, Catal. Lett., 2017, 147, 674–685 CrossRef CAS.
- H. Sharghi and M. Jokar, Synth. Commun., 2009, 39, 958–979 CrossRef CAS.
- M. M. Hosseini, E. Kolvari, N. Koukabi, M. Ziyaei and M. A. Zolfigol, Catal. Lett., 2016, 146, 1040–1049 CrossRef CAS.
- J. Safari and S. Gandomi-Ravandi, J. Mol. Struct., 2014, 1074, 71–78 CrossRef CAS.
- T. Tamoradi, S. M. Mousavi and M. Mohammadi, New J. Chem., 2020, 44, 3012–3020 RSC.
- L.-M. Wang, J. Sheng, L. Zhang, J.-W. Han, Z.-Y. Fan, H. Tian and C.-T. Qian, Tetrahedron, 2005, 61, 1539–1543 CrossRef CAS.
- S. B. Sapkal, K. F. Shelke, B. B. Shingate and M. S. Shingare, Tetrahedron Lett., 2009, 50, 1754–1756 CrossRef CAS.
- S. R. Cherkupally and R. Mekala, Chem. Pharm. Bull., 2008, 56, 1002–1004 CrossRef CAS PubMed.
- F. M. Moghaddam, H. Saeidian, Z. Mirjafary and A. Sadeghi, J. Iran. Chem. Soc., 2009, 6, 317–324 CrossRef CAS.
- M. Nikoorazm and Z. Erfani, Chem. Phys. Lett., 2019, 737, 136784–136794 CrossRef CAS.
- S. Vaysipour, Z. Rafiee and M. Nasr-Esfahani, Polyhedron, 2020, 176, 114294–114333 CrossRef CAS.
- N. Seyyedi, F. Shirini and M. S. N. Langarudi, RSC Adv., 2016, 6, 44630–44640 RSC.
- M. Abedini, F. Shirini, J. Mohammad-Alinejad Omran, M. Seddighi and O. Goli-Jolodar, J. Iran. Chem. Soc., 2016, 42, 4443–4458 CAS.
- O. Goli-Jolodar, F. Shirini and M. Seddighi, J. Nanosci. Nanotechnol., 2018, 18, 591–603 CrossRef CAS PubMed.
- O. Goli-Jolodar, F. Shirini and M. Seddighi, RSC Adv., 2016, 6, 26026–26037 RSC.
- D. Azarifar, Y. Abbasi and O. Badalkhani, J. Iran. Chem. Soc., 2016, 13, 2029–2038 CrossRef CAS.
- S. Rezayati, F. Kalantari, A. Ramazani, S. Sajjadifar, H. Aghahosseini and A. Rezaei, Inorg. Chem., 2021, 61, 992–1010 CrossRef PubMed.
- Y. T. Wang, G. M. Tang and Y. S. Wu, Appl. Organomet. Chem., 2020, 34, 1–19 Search PubMed.
- S. Kargar, D. Elhamifar and A. Zarnegaryan, J. Phys. Chem. Solids, 2020, 146, 109601–109640 CrossRef CAS.
- Z. Ghadamyari, A. Shiri, A. Khojastehnezhad and S. M. Seyedi, Appl. Organomet. Chem., 2019, 33, 1–10 CrossRef.
- K. A. Dilmaghani, B. Zeynizadeh and M. Amirpoor, Phosphorus Sulfur Silicon Relat. Elem., 2013, 188, 1634–1642 CrossRef CAS.
- Z.-B. Xie, L.-H. Fu, J. Meng, J. Lan, Z.-Y. Hu and Z.-G. Le, Bioorg. Chem., 2020, 101, 103949–103956 CrossRef CAS PubMed.
- R. Esmaeili, L. Kafi-Ahmadi and S. Khademinia, J. Mol. Struct., 2020, 1216, 128124–128134 CrossRef CAS.
- H. Sachdeva, R. Saroj, S. Khaturia and H. L. Singh, J. Chil. Chem. Soc., 2012, 57, 1012–1016 CrossRef CAS.
- M. Nasr-Esfahani and T. Abdizadeh, Phosphorus, Sulfur Relat. Elem., 2013, 188, 596–608 CrossRef CAS.
- A. Khorshidi, K. Tabatabaeian, H. Azizi, M. Aghaei-Hashjin and E. Abbaspour-Gilandeh, RSC Adv., 2017, 7, 17732–17740 RSC.
- E. Abbaspour-Gilandeh, A. Yahyazadeh and M. Aghaei-Hashjin, RSC Adv., 2018, 8, 40243–40251 RSC.
- M. G. Dekamin, F. Mehdipoor and A. Yaghoubi, New J. Chem., 2017, 41, 6893–6901 RSC.
- K. Godugu, V. D. S. Yadala, M. K. M. Pinjari, T. R. Gundala, L. R. Sanapareddy and C. G. R. Nallagondu, Beilstein J. Org. Chem., 2020, 16, 1881–1900 CrossRef CAS PubMed.
- R. Tayebee, M. Fattahi Abdizadeh, N. Erfaninia, A. Amiri, M. Baghayeri, R. M. Kakhki, B. Maleki and E. Esmaili, Appl. Organomet. Chem., 2019, 33, 1–10 CrossRef.
- K. Niknam, A. Hasaninejad and M. Arman, Chin. Chem. Lett., 2010, 21, 399–402 CrossRef CAS.
- L. Shiri, A. Ghorbani-Choghamarani and M. Kazemi, Monatsh. Chem., 2017, 148, 1131–1139 CrossRef CAS.
- M. Roozifar, N. Hazeri and H. Faroughi Niya, J. Heterocycl. Chem., 2021, 58, 1117–1129 CrossRef CAS.
- G. D. Rao, S. Nagakalyan and G. Prasad, RSC Adv., 2017, 7, 3611–3616 RSC.
- A. Ghorbani-Choghamarani, Z. Heidarnezhad, B. Tahmasbi and G. Azadi, J. Iran. Chem. Soc., 2018, 15, 2281–2293 CrossRef CAS.
- B. Das, M. Srilatha, B. Veeranjaneyulu and B. Shashi Kanth, Helv. Chim. Acta, 2011, 94, 885–891 CrossRef CAS.
- A. R. Moosavi-Zare, M. A. Zolfigol, M. Zarei, A. Zare and J. Afsar, Appl. Catal., A, 2015, 505, 224–234 CrossRef CAS.
- X.-H. Yang, P.-H. Zhang, Y.-H. Zhou, C.-G. Liu, X.-Y. Lin and J.-F. Cui, Arkivoc, 2011, 10, 327–337 Search PubMed.
- H. S. Oboudatian, H. Naeimi and M. Moradian, RSC Adv., 2021, 11, 7271–7279 RSC.
- G. S. Prakash, H. Lau, C. Panja, I. Bychinskaya, S. K. Ganesh, B. Zaro, T. Mathew and G. A. Olah, Catal. Lett., 2014, 144, 2012–2020 CrossRef CAS.
- R. Tayebee and M. Ghadamgahi, Arab. J. Chem., 2017, 10, S757–S764 CrossRef CAS.
- H. R. Shaterian, A. Hosseinian, M. Ghashang, F. Khorami and N. Karimpoor, Phosphorus Sulfur Silicon Relat. Elem., 2009, 184, 2333–2338 CrossRef CAS.
- Q. Zhang, X. Wang, Z. Li, W. Wu, J. Liu, H. Wu, S. Cui and K. Guo, RSC Adv., 2014, 4, 19710–19715 RSC.
- A. Davoodnia, M. Khashi and N. Tavakoli-Hoseini, Chin. J. Catal., 2013, 34, 1173–1178 CrossRef CAS.
- C. S. Reddy and M. Raghu, Chin. Chem. Lett., 2008, 19, 775–779 CrossRef CAS.
- D. Aute, A. Kshirsagar, B. Uphade and A. Gadhave, Res. Chem. Intermed., 2020, 46, 3491–3508 CrossRef CAS.
- S. Karhale, C. Bhenki, G. Rashinkar and V. Helavi, New J. Chem., 2017, 41, 5133–5141 RSC.
- T. Tamoradi, M. Ghadermazi and A. Ghorbani-Choghamarani, Catal. Lett., 2018, 148, 857–872 CrossRef CAS.
- A. Rajini, M. Nookaraju, I. Reddy and V. Narayanan, Chem. Pap., 2014, 68, 170–179 CAS.
|
This journal is © The Royal Society of Chemistry 2023 |
Click here to see how this site uses Cookies. View our privacy policy here.