DOI:
10.1039/D3RA05158G
(Review Article)
RSC Adv., 2023,
13, 28262-28287
The current status of hydrogen energy: an overview
Received
30th July 2023
, Accepted 18th September 2023
First published on 25th September 2023
Abstract
Hydrogen is the most environmentally friendly and cleanest fuel that has the potential to supply most of the world's energy in the future, replacing the present fossil fuel-based energy infrastructure. Hydrogen is expected to solve the problem of energy shortages in the near future, especially in complex geographical areas (hills, arid plateaus, etc.) and harsh climates (desert, ice, etc.). Thus, in this report, we present a current status of achievable hydrogen fuel based on various scopes, including production methods, storage and transportation techniques, the global market, and the future outlook. Its objectives include analyzing the effectiveness of various hydrogen generation processes and their effects on the economy, society, and environment. These techniques are contrasted in terms of their effects on the environment, manufacturing costs, energy use, and energy efficiency. In addition, hydrogen energy market trends over the next decade are also discussed. According to numerous encouraging recent advancements in the field, this review offers an overview of hydrogen as the ideal renewable energy for the future society, its production methods, the most recent storage technologies, and transportation strategies, which suggest a potential breakthrough towards a hydrogen economy. All these changes show that this is really a profound revolution in the development process of human society and has been assessed as having the same significance as the previous industrial revolution.
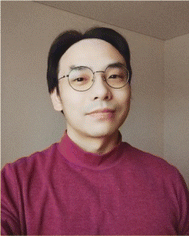 Phuoc-Anh Le | Phuoc-Anh Le currently works at the Center for Environmental Intelligence and College of Engineering & Computer Science, Vin University, Vietnam. He received his PhD from the National Yang Ming Chiao Tung University, Taiwan, in 2021. His research focuses on the development of novel materials for energy storage and conversion applications. |
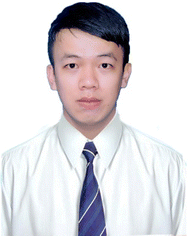 Vuong Dinh Trung | Vuong Dinh Trung is currently a PhD student at the Interdisciplinary Graduate School of Science and Technology, Shinshu University in Natsuki's group. He received his Master degree from the Department of Mechanical Engineering and Robotics, Shinshu University in 2022. His research interests focus on nanomaterials for energy harvesting and storage. |
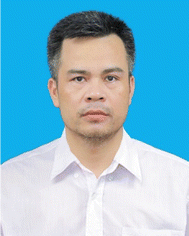 Phi Long Nguyen | Dr Phi Long Nguyen is currently working as a senior researcher at the Viettel Aerospace Institute and Vin University in Vietnam. He earned a PhD in Computer Science and Engineering in 2013 at Kanazawa University, Japan. He has extensive research experience in the fields of heat transfer, thermal plasma, laser technology, and their application techniques. |
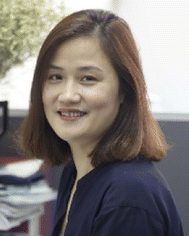 Thi Viet Bac Phung | Dr Viet Bac Thi Phung received her PhD from Kanazawa University, Japan. Her research is mainly directed towards computational and simulation materials science. From 2010 to 2013, she was a postdoctoral researcher at the National Advanced Institute of Industrial Science and Technology (AIST) and the Japan Advanced Institute of Science and Technology (JAIST). She also spent four years as a specially appointed assistant professor at Fukui University, Japan, before taking on the role of senior researcher at Vin University, Vietnam. |
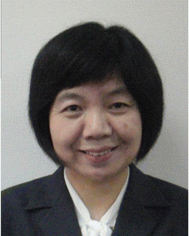 Jun Natsuki | Dr Jun Natsuki received her PhD degree from Kyoto University, Kyoto, Japan, in 1994. She has worked as a research scientist at R&D sections of some companies and the National Institute of Advanced Industrial Science and Technology (AIST), Tsukuba, Japan, since 1994. Currently, she is working as a researcher at the Institute for Fiber Engineering (IFES) and the Interdisciplinary Cluster for Cutting Edge Research (ICCER) of Shinshu University. |
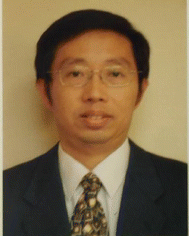 Toshiaki Natsuki | Toshiaki Natsuki received his PhD from Kyoto Institute of Technology, Kyoto, Japan, in 1994. He has been a research scientist at the R&D sections of Hitachi Chemical Company, Ltd., Tsukuba, Japan, and the National Institute of Advanced Industrial Science and Technology (AIST), Japan, since 1994. He joined Shinshu University, Japan, as an associate professor in 2006. His current research interests include the design, fabrication, structural analysis, and evaluation of novel materials for supercapacitors and hydrogen production. |
1 Introduction
Over the past ten years, there has been a noticeable and significant shift in the global fuel supply. Traditional fossil fuels like coal, gas, and oil will progressively be phased out; this is also an unavoidable tendency of civilization, with negative implications and effects on the climate, water resources, land resources, and people. Renewable energy sources, including the sun, wind, ocean waves, hydrogen, and others, have emerged as the most promising and likely prospects for the future of energy supply.1,2 In which hydrogen energy is anticipated to become widely used in the future, exerting significant influence on a variety of societal developments. Hydrogen energy could be created on an industrial scale without relying on the environment, in contrast to renewable energy sources like sun, wind, and tide energy that are dependent on weather conditions.3,4 This is another key benefit of this fuel type. Moreover, hydrogen fuel can be produced using various techniques based on the specific industrial infrastructure conditions of each country, making it a very flexible energy fuel type.
There is a trend for the usage of fossil fuels to progressively decline dramatically as the adoption of new, more ecologically friendly energy solutions and renewable energy sources rises. A big role is anticipated for hydrogen-based energy processes in our upcoming generations as they appear to be one of the best ways to create improved environmental and sustainability circumstances.5,6 In an ever-increasing number of studies, hydrogen is being viewed as a critical component of a global sustainable energy plan that significantly lessens the menace of climate change, air pollution, and global warming.7–9 As an inevitable development trend of human civilization, the world has started to convert energy from one to one another. Here, the prediction of transition from solids to liquids and gas fuels has been illustrated in Fig. 1.
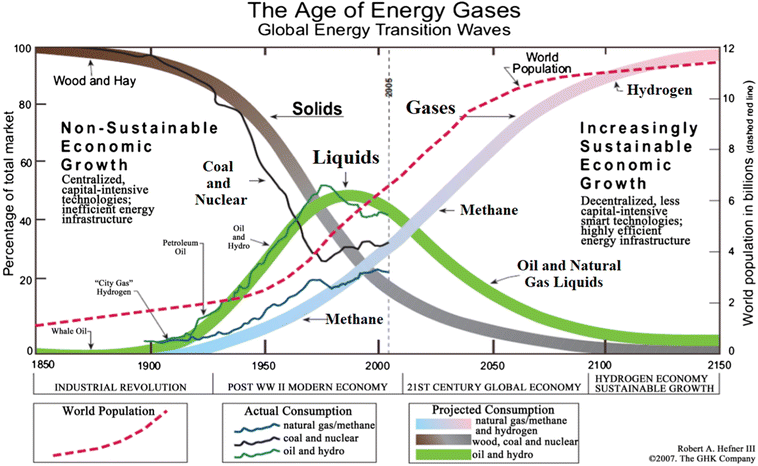 |
| Fig. 1 The energy form transitioned from solid to liquid from 1850 to 2150.7 Reproduced from ref. 7 with permission from [Scientific Research], copyright [2019]. | |
It is possible to manufacture hydrogen fuel from environmentally benign sources (solar, wind, tide, etc.), which is regarded as a renewable energy fuel. However, most of the hydrogen is being produced from fossil fuels, and the actual output of hydrogen being created using water electrolysis and renewable resources like biomass, sewage sludge is still too small due to the limitations of technology and the high cost in comparison with the other traditional fossil precursors.10–15 Almost all of the hydrogen utilized today is generated from fossil fuels, with a few rare exceptions. Fig. 2a clearly shows that the majority of the hydrogen generated worldwide (about 48%) comes from natural gas, 18% of hydrogen is produced from coal, and 30% of dedicated hydrogen is produced from oil. Electrolysis of water and electricity is used to create the remaining 4%.16
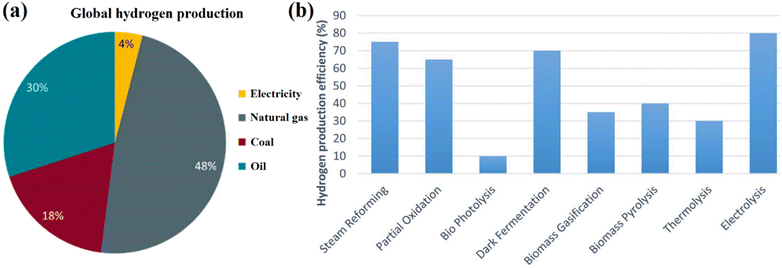 |
| Fig. 2 (a) Global hydrogen production,16 reproduced from ref. 16 with permission from [MDPI], copyright [2022] and (b) hydrogen production efficiency from various different process.17 Reproduced from ref. 17 with permission from [Royal Society of Chemistry], copyright [2023]. | |
Fig. 2b shows hydrogen production efficiency from various different processes, with electrolysis demonstrating the highest efficiency at around 80%, but this technology is still expensive and difficult to use on a large scale.17 Currently, the steam reforming is the most popular strategy to produce hydrogen.
In the long run, hydrogen fuel will replace hydrocarbon fuels because of its benefits and adaptability. In recent years, the water splitting method has been heavily researched to produce clean hydrogen gas, which means that no harmful gases (CO, and CO2) are generated during the production process. Thus, water is only produced as a byproduct of the creation of hydrogen fuel if we use the electrocatalyst method, which is thought to be the most effective and clean energy source.18–20 The use of hydrogen fuel as an independent, clean energy source with a higher energy content than fossil fuels is acknowledged on a global scale. A great choice as an energy source for heat and power, among many other uses, hydrogen has many beneficial characteristics, including a large storage capacity, renewability, purity, massive transportation, high transformation, low emission sources, versatility, and rapid recovery.21–23 It is therefore recognized as the most promising and ecologically beneficial energy source of the twenty-first century. Hydrogen fuel will soon play a key role in industrial applications, spurring the growth of business, electronic technology, transportation, and air technology (Fig. 3).
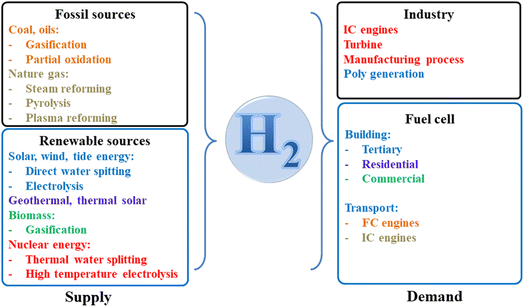 |
| Fig. 3 The relationship between supply and demand of hydrogen fuel. | |
Over the next decade, the race to produce green hydrogen in Asia will intensify as many of the world's leading energy companies join hands with regional partners to implement a range of energy projects. Green hydrogen is created by separating water into hydrogen and oxygen using renewable energy from sources like solar and wind power. This hydrogen fuel can be used for heavy industries such as steel production, concrete, and the transportation industry. Demand for green hydrogen is growing strongly globally, especially in Europe, which is accelerating the development of renewable energy to reduce dependence on fossil energy supplies, especially in the winter season. However, this investment trend is forecast to explode in Asia in the near future. Moreover, hydrogen storage and transportation techniques also require stronger research and investment resources in the context of increasing demand. This has led to a strong investment in research into new materials for liquid hydrogen containers and gaseous hydrogen storage. In summary, the hydrogen industry will lead the rapid development of various supporting industries that help to raise the economy and provide a great opportunity for a future society based on clean renewable energy.
There have been numerous reviews about hydrogen fuel, production methods, storage and transport facilities, and economic value. Each review brings certain knowledge and perspectives to this future fuel. This review is presented with the ambition of being able to synthesize, distill key points, and timely update important information about hydrogen energy.
2 Hydrogen productions
Hydrogen fuels current can be generally categorized by various types based on the color, such as green type can be produced from renewable sources, blue type can be made from fossil sources with CO and CO2 capture, grey type can be created from fossil sources without harmful gases capture, red type can be produced from nuclear energy (Fig. 4).24–26 Even though most hydrogen fuels now are of the blue and grey types, which can be generated via the steam hydrocarbon reforming technique with CO and CO2 release, green hydrogen may also be produced from renewable energy sources. A common technique is electrolysis, which splits water into oxygen and hydrogen under applied electrical current and produces green hydrogen with no outright emissions of carbon dioxide. The required electricity might be generated using renewable energy sources. Fig. 5 shows the various methods to produce hydrogen fuels including three types of blue, red, and green from two main sources: (i) fossil fuels, and (ii) renewable resources.27–30 Each of these methods has advantages and disadvantages, which will be discussed below.
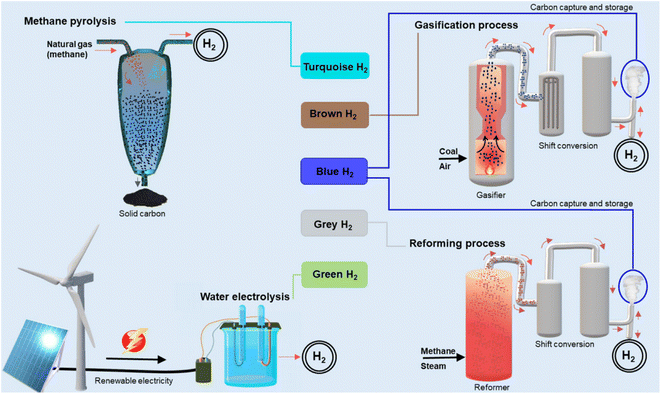 |
| Fig. 4 The hydrogen color is based on various production techniques.30 Reproduced from ref. 30 with permission from [Springer], copyright [2022]. | |
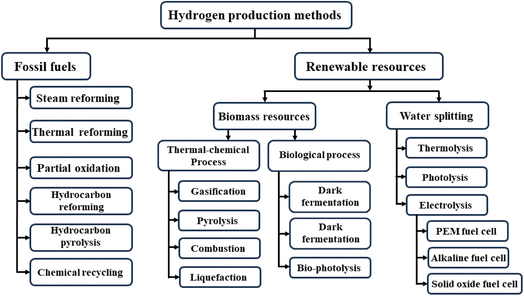 |
| Fig. 5 Commonly hydrogen production strategies. | |
2.1 Hydrogen from fossil sources
At present, global hydrogen production is mainly produced from fossil fuel inputs by two main methods: reforming and pyrolysis on an industrial scale. Up until now, hydrogen fuel circulating on the market has been blue and grey, with the advantages of low cost, being able to be supplied in large quantities, and being produced in many different countries spanning four continents.
2.1.1 Steam reforming. The majority of the hydrogen used in the worldwide market is produced by reforming hydrocarbon fuels. The creation of hydrogen is thought to mostly be produced by the steam reforming of hydrocarbons, particularly in refineries. In the steam reforming reaction, a combination of steam and hydrocarbons reacts at a high temperature to create carbon dioxide and hydrogen (Fig. 6). Natural gas such as liquefied petroleum gas and naphtha are both used in the steam reforming process to obtain hydrogen. Here, steam methane reforming from natural gas or light hydrocarbons is the hydrocarbon reformation technique that is most frequently utilized. The general process of methane steam reforming can be described by following equations:31–33
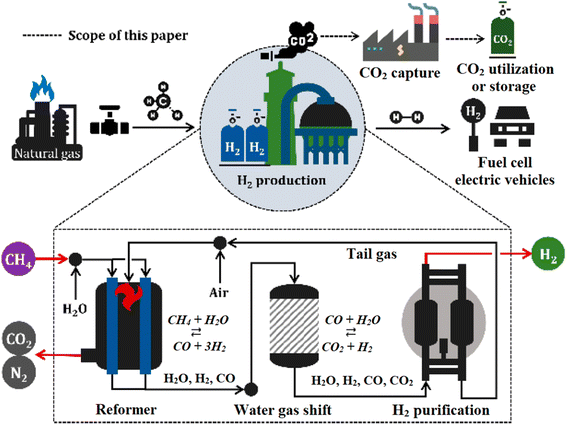 |
| Fig. 6 Diagram of steam methane reforming for industrial hydrogen production.31 Reproduced from ref. 31 with permission from [MDPI], copyright [2021]. | |
- Steam reforming reaction:
|
CH4 + H2O (heat) → CO + 3H2
| (1) |
- Water gas shift:
- CO2 reforming:
|
CH4 + CO2 → 2CO + H2O
| (3) |
- Higher hydrocarbons steam reforming:
|
CmHn + mH2O (g) → mCO + (m + 0.5n) H2
| (4) |
For example, methanol and oxygenated hydrocarbons need to be heated to 180 °C, but most traditional hydrocarbons need to be heated to more than 500 °C in order to undergo steam reforming.34–37 Additionally, the use of catalyst reforming techniques with extra metal has been researched to overcome the restrictions of mass and heat transfer to permit the kinetics of steam reforming.38,39 Both nonprecious metals, like nickel, and precious metals from group VIII elements, such platinum or rhodium, are utilized as catalysts.40–43 Conventional steam reformers are constrained by the efficacy factor of pelletized catalysts due to significant mass and heat transmission restrictions.44 Therefore, with traditional steam reformer reactors, kinetics is seldom the limiting factor, and as a result, less costly nickel catalysts are utilized in industry.45,46 In general, steam reforming will continue to be the dominant source of hydrogen fuel in the coming decade because it has an established industrial production system, an assured supply of input fuel, and an optimized manufacturing method that yields the highest quality product. Of course, the hydrogen fuel industry's long-term objective is to substitute other, more environmentally friendly production techniques for the steam reforming process that uses natural gas fuel sources and emits CO or CO2 during operation.
2.1.2 Partial oxidation. An alternate strategy to steam reforming processes is partial oxidation which focus on methane, heavy fuel oil, coal, and other feed stocks might all be used in this process.47,48 The best method for producing hydrogen from coal and heavy fuel oil is partial oxidation.48,49 Hydrocarbon fuels are transformed into a mixture of hydrogen, CO, CO2, and other partially oxidized compounds by the exothermic process of partial oxidation. One benefit of this method is the strong exothermic nature of oxygen processes, which negates the need for an external energy source. Frequently, heavy oil fractions and low-grade coal, which are challenging to further process and use, are gasified source materials.50 Biogas and methane are also possibilities.51,52 In a non-catalytic process called partial oxidation, the raw material is gasified in the presence of oxygen and possibly steam at pressures between 3 and 8 MPa and temperatures between 1300 and 1500 °C, which generate more CO than steam reforming, so the partial oxidation process needs to be completed by the steam-based conversion of CO into H2 and CO2. The partial oxidation process is an exothermic reaction, and the equation for the reaction is given by the following equation:51,52 |
CmHn + 0.5mO2 → mCO + 0.5nH2
| (5) |
Moreover, in order to increase the hydrogen conversion rates and decrease the reaction temperature compared to non-catalyzed partial oxidation techniques, hydrogen generation from the partial oxidation of hydrocarbons employing catalysts has been used in commercial settings (Fig. 7).53–55
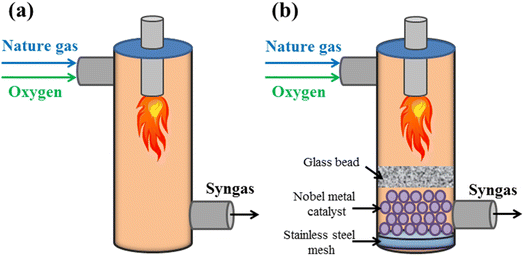 |
| Fig. 7 (a) Traditional partial oxidation reactor, and (b) catalytic partial oxidation reactor. | |
2.1.3 Autothermal reforming. The method for producing hydrogen by combining the catalytic partial oxidation process is known as autothermal reforming. Steam reforming (endothermic) and partial oxidation (exothermic) processes are both components of autothermal reforming.56,57 Compared to steam reforming of methane, autothermal reforming has the advantages of not requiring external heat and being easier and low-cost. In short, the reformer is filled with both steam and oxygen, which causes the reforming and oxidation events to occur concurrently and produce a thermodynamically neutral reaction.58 Compared to the partial oxidation reforming method, the autothermal reforming technique can be carried out at low pressure. Fig. 8 shows the general autothermal reforming reactor following chemical equations:
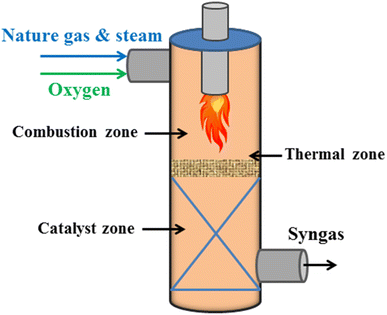 |
| Fig. 8 Schematic of an autothermic reactor. | |
- Combustion zone:
|
CmHn + 0.5mO2 → mCO + 0.5nH2
| (6) |
- In thermal and catalyst zone:
|
CmHn + mH2O (g) → mCO + (m + 0.5n) H2
| (9) |
The choice of catalyst, much like in partial oxidation or steam reforming, is critical to the outcome, with the most widely used catalysts being nickel-based because of their efficiency and affordability. Due to this method's exceptional thermal efficiency, less energy is used compared to partial oxidation or steam reforming.59 Moreover, an important benefit of the auto-thermal reaction method over partial oxidation is that it may create a lot of hydrogen gas while beginning and ending quickly. The steam to carbon ratio and the oxygen to fuel ratio were both thought to be essential for controlling the temperature and avoiding coke formation during the autothermal reaction process.60–62
2.1.4 Pyrolysis. Pyrolysis is a thermal decomposition technique happening in non-oxygen or anaerobic condition in order to covert different light liquid hydrocarbons into hydrogen and other carbon element.63 The degradation of hydrocarbons by heat is referred to as pyrolysis, which depends on the characteristics of the coal, and these decomposition processes have been conducted at 300 to 400 °C.64,65 The thermal breakdown of other hydrocarbons has been place at high temperatures; for example, methane requires a high temperature of 1400 °C to thermally decompose.66 In addition, the use of a transition metal catalyst like Ni, Fe, or Co can lower the temperature of the pyrolysis procedure.68,69 The pyrolysis of hydrocarbon can be described by following equations:64–69 |
CmHn + (2m − 0.5n) H2 → mCH4
| (12) |
When heavy residual fractions with a boiling point greater than 300 °C are the source of thermal breakdown, it makes sense to produce hydrogen using a two-step process that includes (i) hydrogasification (eqn (12)) and (ii) methane cracking gasification (eqn (13)). Despite producing less hydrogen than the other methods, this method enables the simultaneous creation of useful byproducts, such as carbon nanotubes, carbon nanofibers and carbon spheres.70–72
2.1.5 Fossil gasification. The fossil gasification technique is described as a series of thermochemical reactions between the gasifying agent, such as oxygen, steam, air, or carbon dioxide, and the fossil fuel, such as coal, that occur at high temperatures.73,74 For instance, the thermochemical conversion process known as coal gasification transforms coal into gaseous products like hydrogen and carbon monoxide (Fig. 9).75,76 This procedure tries to substitute coal burning in order to lessen hazardous emissions and boost the fuel's energy density. The key benefit of this strategy is the cheaper fuel than natural gas reforming. However, given the high carbon content, the major issue with producing hydrogen via coal gasification as opposed to alternative methods that employ various feedstocks is connected to greater CO2 emissions.77 Due to these benefits, coal gasification and carbon capture-based technologies are being combined.78 The gasification of coal is the earliest way of producing hydrogen, which is created in outdated gas plants and comprises a significant quantity of CO and approximately 60% hydrogen.79 Coal, for example, has pyrolysis process following equations:75–79 |
3C (coal, patch, etc.) + O2 + H2O → H2 + 3CO
| (14) |
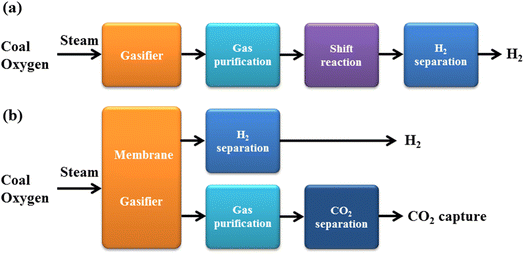 |
| Fig. 9 General schematic for hydrogen production from: (a) traditional process of coal gasification, (b) modified process of coal membrane gasification with CO2 capture. | |
2.2 Hydrogen from renewable sources
2.2.1 Hydrogen production from biomass resources. Biomass is considered a great energy resource for hydrogen production due to its abundant sources and environmental friendliness, which aim to replace fossil fuels.80 Currently, there are several techniques to produce energy from biomass, including physical, thermal, chemical, and biological conversion.81 Biomass might be transformed into heat, power, solid fuels (coal), liquid fuels (bio-oil, methanol, etc.), and gas fuels (hydrogen, syngas, etc.) via the gasification and pyrolysis processes, water splitting, respectively.82The oldest and most well-known method for utilizing biomass as a source of hydrogen generation is gasification, which employs a carefully regulated process involving heat, steam, and oxygen to transform biomass into hydrogen and other products without burning.83,84 Because carbon dioxide is removed from the atmosphere during the development of biomass, this method may have negligible net carbon emissions, especially if carbon capture, use, and storage are employed. The construction and operation of biofuel gasification facilities can provide high-quality hydrogen fuels at a reasonable cost. Typically, in the process of gasification, carbon monoxide, hydrogen, and carbon dioxide are produced from organic or fossil-based carbonaceous materials at temperatures above 500 °C without burning (Fig. 10). After that, the carbon monoxide reacts with water in a water–gas shift reaction to create carbon dioxide and more hydrogen. This gas stream can have the hydrogen removed using adsorbers or certain membranes. The biomass gasification process can be described by following reactions:83,85,86
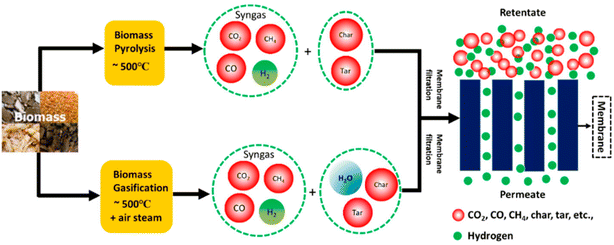 |
| Fig. 10 Pyrolysis and gasification technologies for hydrogen production using biomass resources.83 Reproduced from ref. 83 with permission from [MDPI], copyright [2020]. | |
First simplified gasification
|
CxHyOzNmSl (biomass resources) + O2 + N2 + H2O → CO + CO2 + H2 + other species
| (16) |
Water–gas shift reaction
One another strategy to produce hydrogen from biomass is pyrolysis technology. In fact, pyrolysis is modified-gasification technology in the absence of oxygen.87 Compared to coal, biomass is more difficult to gasify, and when no oxygen is utilized, it also creates additional hydrocarbon compounds in the gas mixture that leaves the gasifier. Consequently, a further step is often required to reform these hydrocarbons using a catalyst to produce a clean syngas combination of hydrogen, carbon monoxide, and carbon dioxide. The carbon monoxide is then transformed into carbon dioxide using steam in a subsequent step known as a shift reaction, just like in the gasification process used to create hydrogen (Fig. 11).88,89 The generated hydrogen is then sorted and cleaned after separation and purification.
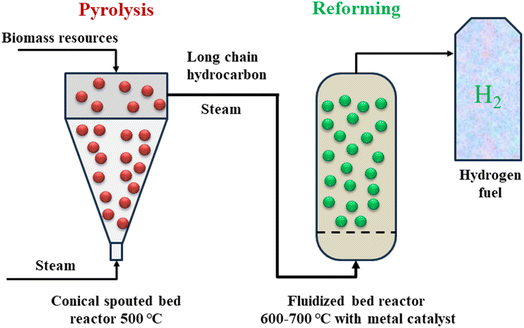 |
| Fig. 11 Schematic flow diagram of pyrolysis-reforming biomass to produce hydrogen. | |
2.2.2 Hydrogen production from plastic wastes. Because plastics are employed in so many different aspects of daily life, their production, consumption, and resulting plastic waste have all increased steadily since the industrialization of plastic production.90,91 Significant negative effects on the environment, particularly for terrestrial and marine ecosystems, are caused by the proliferation and misuse of plastic packaging, improper management of residues, unlawful dumping, and unregulated landfilling. Since plastic pollution has been documented for a long time, it has raised economic and societal concerns. In fact, plastics can break into micro- and nano-plastics through erosion and degradation, which is an issue that is difficult to manage due to its ability to contaminate water supplies, interact with chemical species in the environment, and even enter human bodies.92,93The problem of recycling plastic waste has been proposed for decades with many experimental technologies. One of the ideas that is considered groundbreaking is to decompose plastic waste as an input precursor to synthesize hydrogen through several classic methods such as gasification, gasification–pyrolysis, and electrolysis.94–96 Among them, hydrogen production from plastic gasification is the most popular technology with the most synchronized infrastructure and has been put into production on an industrial scale. Hydrogen production by gasification can at the same time obtain methane (CH4) as a major product and segregated capture, as shown in Fig. 12.94 This technology has been the main method of making hydrogen fuel from plastic waste with high efficiency, stability, and low cost.
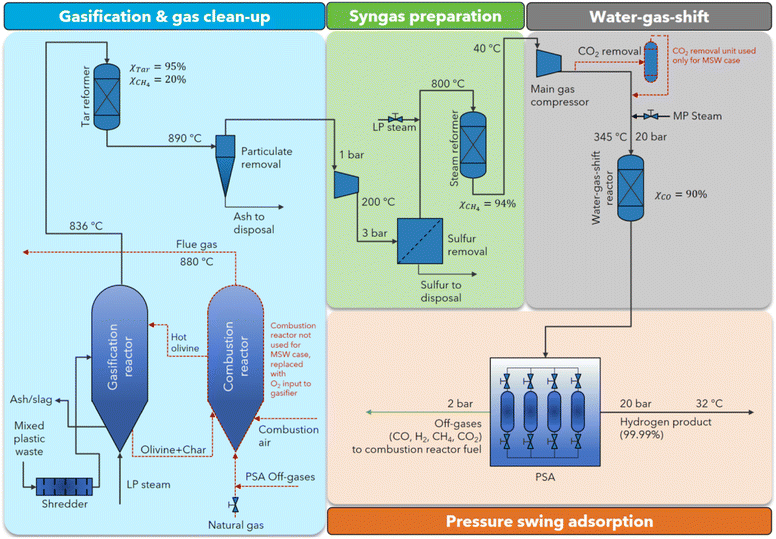 |
| Fig. 12 Schematic of flow diagram of gasification process using mixed plastic waste precursor to produce hydrogen and other species.94 Reproduced from ref. 94 with permission from [Royal Society of Chemistry], copyright [2023]. | |
With the goal of increasing the efficiency of hydrogen gas production, pyrolysis has been developed with the advantage of being able to gasify large volumes of plastic waste such as tires, plastic containers, etc. Plastic pyrolysis is a technology that involves the rapid usage of trash and results in significant issues (Fig. 13). The quickest approach to prevent adding significant volumes of plastic waste such as plastic bag, plastic container, tires to municipal solid waste is to use this technique.97–99 Pyrolysis also has the advantage of blocking the channel via which micro- and nano-polymers can exist in water sources and enter the human body. However, the plastic pyrolysis technology also has some limitations of carbon dioxide and waste oil product during pyrolysis process. Currently, to increase the hydrogen fuels, various modified-techniques have been used such as pyrolysis-steam reforming,100 pyrolysis-CO2 dry reforming,101 pyrolysis-plasma catalytic processing.102,103
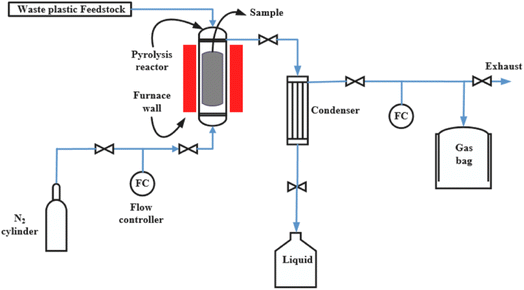 |
| Fig. 13 A scheme of pyrolysis process to produce hydrogen from waste plastic resources.99 Reproduced from ref. 99 with permission from [Elsevier], copyright [2023]. | |
In addition to gasification and pyrolysis–gasification methods that are widely used in industry, electrocatalyst methods are also being developed. Electrocatalysis is an appealing and sustainable method to produce clean H2 from electrolyte containing organic materials at the cathode and value-added oxygenates at the anode under moderate circumstances, which can be powered by renewable energy.104,105 Typically, there are two different ways to convert polymers through electrocatalytic oxidation: direct oxidation and indirect oxidation. Indirect oxidation employing potent oxidizing intermediates predominates in the conversion of plastics, whereas direct oxidation corresponds to the electrophilic assault on a polymer by OH created by water discharge on the anode surface.106 For example, Fig. 14a shows electrocatalyst reforming process of for direct oxidation polyethylene terephthalate (PET) by using palladium modified nickel foam (Pd/NF) anode and pure NF cathode. After 20 h of electrolysis at 0.7 V vs. RHE at a current density of 400 mA cm−2, the conversion efficiency of PET increased up to 100%.107 Fig. 14(b)–(d) illustrates the electrocatalyst reforming PET by KOH and the final product including potassium diformate, terephthalic acid electrolyte and hydrogen fuel.108
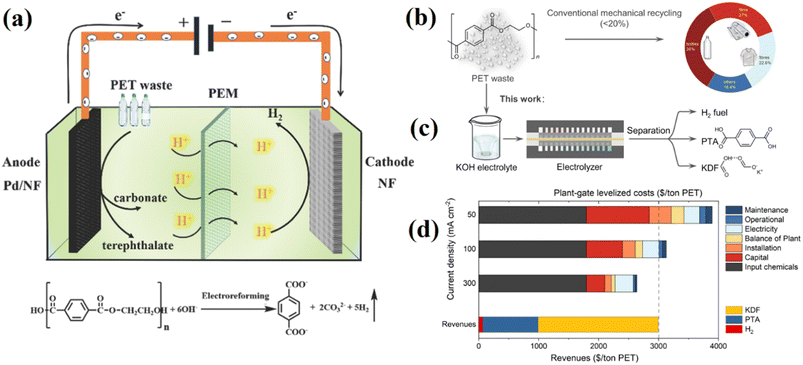 |
| Fig. 14 (a) The electrocatalyst reforming process of PET into high value-added chemicals and H2 fuel,107 reproduced from ref. 107 with permission from [Royal Society of Chemistry], copyright [2021], (b) conventional route for PET recycling, (c) electrocatalytic PET upcycling to commodity chemicals and H2 fuel, (d) technoeconomic analysis (TEA) of route I at different current density.108 Reproduced from ref. 108 with permission from [Springer], copyright [2021]. | |
In general, the purpose of recycling plastic waste still has a long way to go. However, it must be affirmed that the advent of disruptive methods such as gasification, pyrolysis, and electrochemical reforming will give hope for a future where plastic waste can be completely used as abundant input resource into hydrogen fuel production.
2.2.3 Hydrogen production from water splitting using renewable energy. At the present time, the production of hydrogen fuel by the water splitting method is a topic of great interest for research and improving technology to reduce costs. Why is water splitting so fascinating? Because the ultimate objective of this technique is to develop an electrolytic system that generates hydrogen and oxygen using seawater as an electrolyte. One of the best advantages of this technique is that it can obtain up to 95% purity hydrogen product. In general, water splitting methods can be classified by three techniques: (i) low temperature water electrolysis, (ii) high temperature water electrolysis, and (iii) photonic.Low temperature water electrolysis is the process by which electrical energy is used to separate water into hydrogen and oxygen at ambient temperature. With this method, the total energy required for electrolyzing water slightly rises with temperature. The water electrolysis process is described by the generic equation below:109,110
|
H2O + electricity → H2 + 0.5O2
| (18) |
For acid electrolyte:
|
At anode: 2H2O → O2 + 4H+ + 4e−; E° = 0 V
| (19) |
|
At cathode: 4H+ + 4e− → 2H2; E° = +1.23 V
| (20) |
For base electrolyte:
|
At anode: 4OH− → O2 + 2H2O + 4e−; E° = +0.401 V
| (21) |
|
At cathode: 4H2O + 4e− → 2H2 + 4OH−; E° = −0.828 V
| (22) |
For neutral electrolyte:
|
At anode: 2H2O → O2 + 4H+ + 4e−; E° = +0.817 V
| (23) |
|
At cathode: 4H2O + 4e− → 2H2 + 4OH−; E° = +0.413 V
| (24) |
Here, the process of breaking the hydrogen and oxygen bonds within water depends on the passage of a current of electricity through an anode and cathode placed in the electrolyte. Although the principle is the same, several electrolysis techniques, such as alkaline-, anion exchange-, solid oxide-, and proton exchange membrane-electrolysers, can be used to produce hydrogen [
Fig. 15(a)–(c)].
111–113 Fig. 15a shows the general working principle of one water splitting system while
Fig. 15b and c are the developed system of anion exchange membrane (AEM) electrolysis and proton exchange membrane (PEM) electrolysis, respectively. These approaches differ mostly in terms of the electrolyte type used or the ion transport technique used. Currently, water electrolysis can obtain a high transition efficiency of up to 80%, which is higher than gasification and pyrolysis, but this technique needs to be evaluated for its price to be viable for large-scale production in industry.
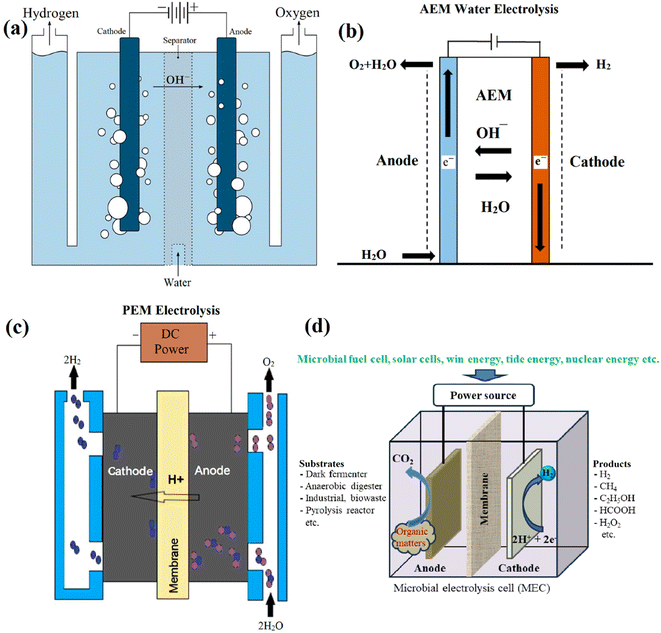 |
| Fig. 15 Scheme of low temperature water electrolysis: (a) alkaline electrolyzers, (b) anion exchange electrolyzers, and (c) proton exchange membrane electrolysers113 Fig. 15(a)–(c) reproduced from ref. 113 with permission from [MDPI], copyright [2023] and (d) microbial electrolysis cell system. | |
A microbial electrolysis cell (MEC) is a bioelectrochemical hydrogen generation method that is ecologically benign. Fig. 15d shows the construction of one standard MEC system based on three main parts: (i) cathode, (ii) membrane, and (iii) anode, where anodic bio-catalytic oxidation and cathodic reduction processes are used in the technique.114 An external renewable energy source, such as solar or wind energy, can serve as a power source for a MEC system and become a promising strategy to produce hydrogen. Currently, MEC is focused on wastewater treatment and also bioenergy hydrogen production because the hydrogen production efficiency of the MEC system provides greater yields than water electrolysis. However, the MEC system still has some disadvantages that need improvement, such as the instability of the bioanode at high temperatures, the high substrate concentration, the fact that bioanodes are quite sensitive to high acid concentrations, and the fact that the bioanode can assume hydrogen. Additionally, MEC is an interesting technique that was developed based on microbial fuel cells (MFC). MFC has a long history, beginning with a simple half-fuel cell in 1931 by Barnett Cohen and progressing through various completed systems to the present. In general, MFCs are electrochemical devices that can produce electricity by converting chemical energy into electrical energy from the biochemical reactions of bacteria.
High-temperature electrolysis is the process of dissociating H2O into H2 and O2 under steam conditions at very high temperatures from 500 to 1000 °C, and system efficiencies rise with rising operating temperatures (Fig. 16). In the high temperature water electrolysis system, the needed power supply is lower than low temperature water electrolysis because the required power supply decreases with the increasing temperature. It is recognized that high-temperature electrolysis is more effective than standard electrolysis that takes place at normal temperature and provides higher efficiency. Therefore, the high-temperature electrolysis process is being completed and will be applied on an industrial scale in the near future. Currently, the solid oxide electrolyser is preferred for use in high-temperature systems due to its chemical stability at high temperatures and cost-effectiveness. Since non-rare-earth elements are more often utilized as catalysts, solid oxide electrolysis is a growing technique that gains from its high efficiency. The most popular electrode material is a composite of yttria-stabilized zirconia or Ni-based ceramics, with ceramics serving as the electrolyte in most cases.115
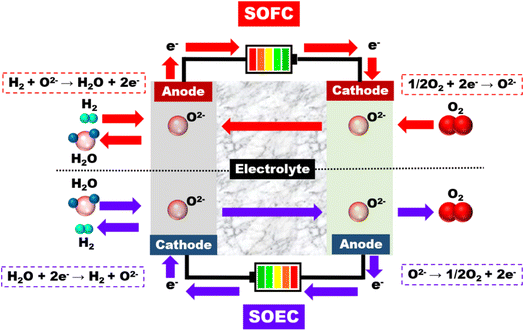 |
| Fig. 16 A comparison between solid oxide fuel cell (SOFC) and solid oxide electrolysis cell (SOEC).115 Reproduced from ref. 115 with permission from [Wiley], copyright [2020]. | |
In summary, low-temperature and high-temperature water electrolysis are promising technologies for addressing the global energy crisis. In the hydrogen economy, they also play a significant role in manufacturing the hydrogen gas that powers the industrial and transportation sectors. A wide range of research interests have been expanded to include additional industrial uses as well as the development of high-performing materials in order to optimize their potential usage. These research interests go beyond just electrolyzing water to produce hydrogen.
Hydrogen from photocatalyst technique is the water splitting separates into hydrogen and oxygen via photocatalysis. Since this is what normally occurs in the creation of photosynthetic oxygen, light energy (photons), water, and catalyst materials are required. Currently, semiconductors and their composites are commonly used as photocatalysts. The working principle of water splitting can be described in Fig. 17, when absorbing photons from light with energy equal to or higher than the band gap energy of the catalyst materials, it will promote electrons in the valence band (VB) to the conduction band (CB), leaving holes in the valence band and creating electron and hole pairs. Here, electrons and holes will cause a redox reaction similar to electrolysis to produce hydrogen and oxygen (Fig. 17a and b).116,117 For the water reduction process, the valence band must be at a potential higher than 1.23 V and the conduction band lower than 0 V compared to a typical hydrogen electrode (NHE) (H+/H2).118 Currently, there are various type of materials have been studying for photocatalyst hydrogen production including metal oxide (TiO2, ZnO, SnO2, Cu2O, Fe2O3),119 metal chalcogenide (MoS2, WS2, NiS2),120 carbon-based materials (carbon dots, carbon nanotube, graphene),121 metal–organic framework (MOF-5, UiO-66, MIL-125, MIL-101),122 etc. However, there are still limits due to the low photocatalytic effectiveness and unstable catalyst materials, which can be overcome by preventing photoelectron-hole recombination, reducing secondary pollution from byproducts, and preventing toxic deactivation.
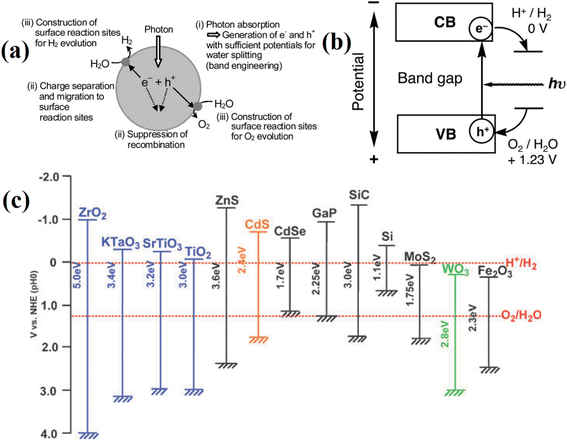 |
| Fig. 17 Photocatalyst water splitting of (a) main process, (b) working principle when using semiconductor as catalyst materials, and (c) band structure of semiconductors and redox potentials of water splitting.116 Reproduced from ref. 116 with permission from [Royal Society of Chemistry], copyright [2009]. | |
3 Hydrogen storage and transportation techniques
Hydrogen storage is just as important as hydrogen production. After being synthesized and prepared by various methods, hydrogen is stored in two main forms: gas and liquid.123 In addition, depending on the infrastructure and equipment of each area, hydrogen storage can be divided into two types: stationary storage and mobile storage.124,125 The major applications of stationary storage techniques are stationary energy generation and on-site storage at the place of production or usage. Applications for mobile devices are either used to move hydrogen that has been stored to a location for usage or storage, or to utilise hydrogen in a vehicle. This article categorizes hydrogen storage into two primary categories based on actual needs: physical storage and material-based storage (Fig. 18).126–128
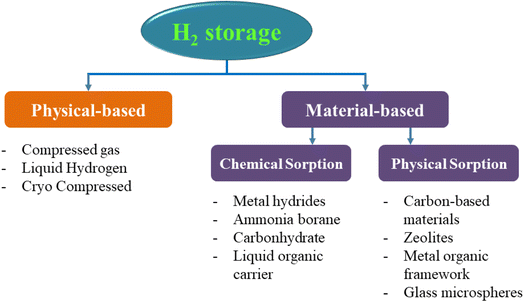 |
| Fig. 18 Hydrogen storage methods. | |
3.1 Compressed gaseous hydrogen storage
At present, hydrogen fuel is stored as gas in many different techniques. For transportation purposes, compressed gas is used in special tanks. Steel with a carbon cover or lightweight composites might be used to create the storage tank. The most popular technique of storing hydrogen involves compressing it to pressures more than 300 bars. Cryo compressed gas is an alternative to compressed gas technology, utilizing both temperature and pressure to increase the volumetric energy density in a storage system. Moreover, with the great development of technology, hydrogen gas is also stored underground in deep geological formations, including salt mines, caves of solid rock, and even depleted oil and gas fields (Fig. 19).30,129 The advantage of this technology is that it preserves the equilibrium of the hydrogen source despite weather changes and climatic fluctuations, which is crucial for storing large quantities of hydrogen fuel.130,131 The predicted demand for hydrogen in the future will exceed the storage capacity of the currently installed surface infrastructure, such as pipelines or tanks. Hydrogen may be produced outside of times of peak demand and safely stored underground until needed, ensuring long-term energy security and supply stability.
 |
| Fig. 19 Diagrammatic representation of the many processes involved in the generation of hydrogen by electrolysis, its seasonal storage in salt caverns or geological formations, its use in the manufacturing of ammonia, and its re-electrification through fuel cells.30 Reproduced from ref. 30 with permission from [Springer], copyright [2022]. | |
3.2 Liquefied hydrogen storage
Hydrogen gas can be liquefied at extremely low temperatures (−253 °C at 1 bar) so that it can be stored in special containers for transportation purposes over long distances, such as from one continent to another.132 However, the liquefaction of hydrogen gas requires a large amount of energy for liquefaction at temperatures below −253 °C and pre-cooling in the liquefaction process. Therefore, liquid hydrogen tanks are also specially designed with complex systems for the storage and transport of liquid hydrogen (Fig. 20).133
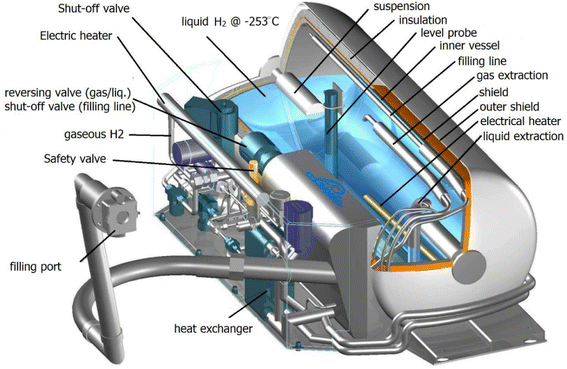 |
| Fig. 20 Schematic of a cryogenic hydrogen tank.133 Reproduced from ref. 133 with permission from [MDPI], copyright [2020]. | |
The liquid hydrogen storage also faces a big problem of liquid evaporation due to the increase in temperature in the tank following the outside temperature. This evaporation phenomenon is addressed as the hydrogen lost per day, also known as the boil rate.134 To reduce the thermal impact of the external environment, liquid hydrogen fixed storage facilities prefer to use spherical tanks with very large volumes, up to thousands of cubic meters. When transporting liquid hydrogen by road, horizontal tubular tanks are used to balance the displacement of liquid inside, while spherical tanks will be prioritized for water transportation on giant ships carrying liquefied petroleum gas. Fig. 20 depicts a conventional liquid hydrogen storage tank, together with all its numerous parts, including vacuum super insulation. Tanks for storing hydrogen have two walls, with insulation between them. Due to the significant temperature difference between outside ambient temperature and liquid hydrogen, the inner vessel is insulated with multilayer insulation, also referred to as vacuum super insulation. This insulation is made of alternating layers of metal foil and padding material. In summary, due to the power required for liquefaction, liquid hydrogen has a high operational cost, but depending on the volume of hydrogen and the delivery distance, it also has cheaper capital expenses.
3.3 Hydrogen transportation
Hydrogen may be transferred from the production site to the final customer in a variety of methods, depending on hydrogen amounts, transportation distances, and terrain. Based on currently in use and developed gas transportation methods, there are now three primary categories: shipping, pipeline transportation, and road transportation.135 The easiest method for solving a small hydrogen need is to transport pressure tanks by trucks that are filled with compressed hydrogen. This is the optimal transportation solution over short distances, especially within one territory. However, the low volume density of hydrogen gas makes large-scale transportation of hydrogen a technological problem. This suggests that when being changed into a higher-density form, hydrogen is carried oversea distances more effectively.136 Transporting hydrogen fuel in liquid form is considered an excellent solution to the problems of geographical distance and large volume.
Liquid hydrogen, liquid organic hydrogen carriers, and ammonia are the most common forms of hydrogen export that are thought to be practical. These hydrogen storage strategies use a variety of energy-intensive conversion processes, such as cooling, pressure, chemical conversion, and release. The transportation of hydrogen fuel in large volumes and over long distances can only be done by sea. Fig. 21 depicts the process of transporting hydrogen fuel by various strategies, where hydrogen fuel is compressed gas being transported by heavy trucks, and large-tonnage ships within the country or to neighboring countries.135 For long-term and intercontinental transportation requirements, hydrogen is usually converted to liquid form in three main ways: liquid hydrogen, ammonia, and liquid-organic hydrogen carriers. The transportation of liquid hydrogen fuel is difficult due to the boiling and evaporation of liquid hydrogen when the temperature in the container increases and the complex control system to keep the liquefied temperature during transportation. Therefore, other more controllable and cheaper methods in use today are ammonia and liquid hydrogen carriers.
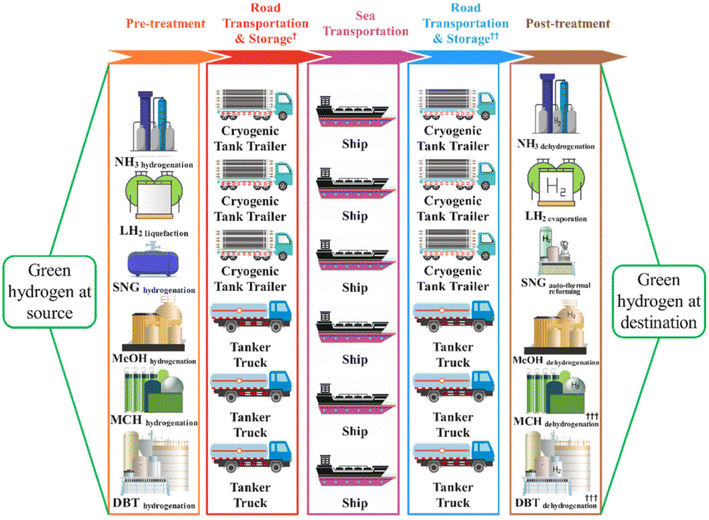 |
| Fig. 21 A schematic of the hydrogen delivery pathways.135 Reproduced from ref. 135 with permission from [Royal Society of Chemistry], copyright [2022]. | |
Ammonia offers several benefits over alternative hydrogen storage materials, including a high hydrogen density, well-developed manufacturing and distribution technologies, and simple catalytic breakdown.137 Currently, the Haber–Bosch method is commonly used to produce ammonia on an industrial scale:
|
3H2 (g) + N2 (g) ↔ 2NH3 (g), ΔH° = 92 kJ mol−1
| (25) |
It has the benefit that there is no CO2 emission at the end user in comparison to hydrocarbons and alcohols. The advantages of using hydrogen carriers like ammonia (NH3) in liquid form at comparatively low pressures are that they have a higher energy density than 1.5 times liquefied hydrogen and 3 times compressed hydrogen. However, the disadvantages mostly relate to the toxicity of liquid ammonia and issues with minute quantities of ammonia remaining in the hydrogen after breakdown.137,138 Currently, various countries world-wide have been developing green ammonia synthesis aiming to replace fossil fuels and provides alternative strategy for hydrogen production. Fig. 22a shows the green ammonia can be produced from renewable sources (solar, wind, hydroelectricity power, etc.) for various use targets.139,140 The goal is to provide green ammonia on a worldwide scale and have it break down into hydrogen at the point of use to provide hydrogen refueling stations. Direct ammonia fuel cells and other complementary technologies to extract the energy contained in green ammonia are required by the growing green ammonia sector. In order to build green hydrogen as an energy source and a sustainable hydrogen economy, green ammonia is progressively assuming a crucial role.
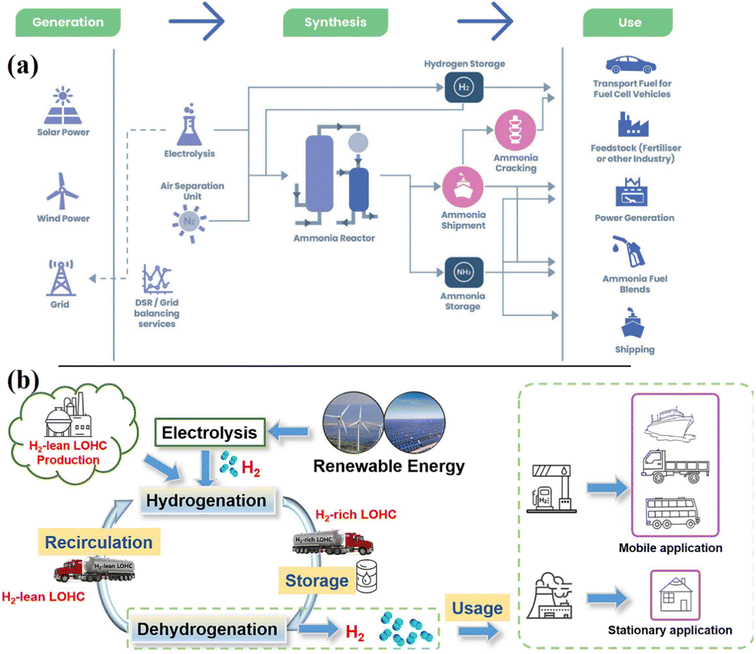 |
| Fig. 22 Process to synthesize and distribute hydrogen carrier for (a) ammonia,140 reproduced from ref. 140 with permission from [Royal Society of Chemistry], copyright [2021] and (b) liquid-organic hydrogen carries.141 Reproduced from ref. 141 with permission from [Elsevier], copyright [2023]. | |
Liquid-organic hydrogen carrier is another alternative technology of hydrogen transportation which focuses on using unsaturated liquid organics such as naphthalene, toluene, decalin, methylcyclohexane, etc.140 In this method, unsaturated liquid organics that may collect and release hydrogen through chemical reactions are known as liquid organic hydrogen carriers. In theory, Fig. 22b shows the hydrogenation process, which may add hydrogen to any organic unsaturated molecule, and then, following endothermal dehydrogenation, hydrogen is purified before being transported to end customers.141 Systems for carrying liquid organic hydrogen outperform traditional energy systems in terms of sustainability, recycling, and emissions. Additionally, it may be used in fixed and mobile applications globally and is safer and simpler to handle than other hydrogen-based systems.141 Hydrogen fuel will undoubtedly be employed in the near future and be present in various industries, from heavy industrial to transportation vehicles like fuel automobiles and ships.142 This is due to the current rising energy need. With the movement of fuel across continents, the logistics industry for hydrogen transportation is certain to see a huge acceleration. There is no doubt that in the upcoming decades, methods for storing and moving hydrogen fuel in both gaseous and liquid forms will advance significantly.
4 Global markets and future prospects for hydrogen-based energy
Energy consumers will become more and more numerous as global population growth and urbanization trends continue, and it is anticipated that by 2030, when the world population is expected to quadruple, there will be a significant rise in global energy demand. Research and development have heavily concentrated on developing new alternative sources and researching the effective use of the present fossil fuels due to the limited availability and depletion of fossil fuels.
A hydrogen economy will arise, forcing the infrastructure of the fossil economy and human activities to undergo significant transformation, just like an oil–gas economy did. It will be necessary to design and construct new infrastructure for the way of storing, transporting, and providing hydrogen for consumption demands since the new energy source production mode is no longer search, exploration, and exploitation. Naturally, it will be different from gasoline and diesel engines since the engine will be constructed using a novel concept appropriate for hydrogen energy. It will be necessary to rebuild technical standards, safety norms, and legal requirements while employing new energy sources. In contrast to the existing fossil economy, education, training, and scientific research for the hydrogen economy will need new facilities and new content. In a brief period of time, significant adjustments must be made in order to reach carbon neutrality. Chemical industry must be decarbonized in order to reach Net Zero by 2050 since it accounts for more than 15% of all industrial CO2 emissions (Fig. 23).143 All these developments demonstrate that this revolution is as profound and significant as past industrial revolutions in the history of human society. For example, Fig. 23b shows the future potential electrolyzer systems must be powered by low-carbon electricity in order to decrease life-cycle CO2 emissions. Performance benchmarks are concentrated on the most researched, scalable low-temperature electrolysis systems based on PEM electrolyzers for hydrogen generation and gas diffusion electrode assemblies for CO2 electrolysis.
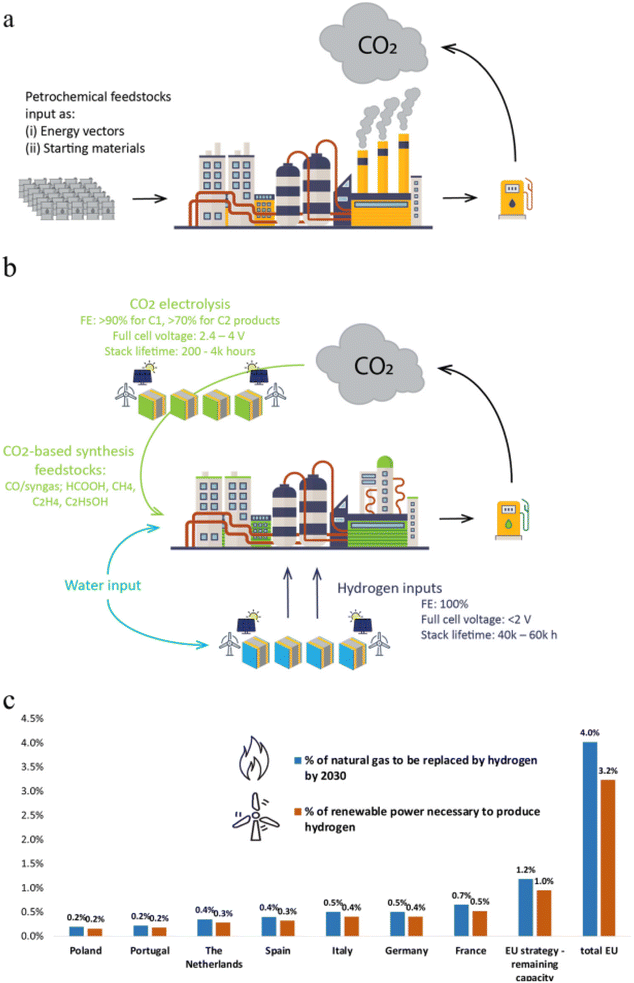 |
| Fig. 23 Emissions of CO2 from the chemical industry and methods for reducing them using electrolysis technologies: (a) schema of a typical chemical production facility, where energy and raw materials are provided by petrochemical feedstocks, (b) the idea of a decarbonized manufacturing process using electrolysis; hydrogen is produced from water electrolysis as an energy source, and CO2 is electrolyzed to produce feedstocks for chemical conversion processes, and (c) a description of the present plans for the implementation of water electrolysis for the generation of hydrogen throughout the European Union.143 Reproduced from ref. 143 with permission from [Royal Society of Chemistry], copyright [2023]. | |
It can be seen that hydrogen fuel sources are and will be used widely in industries, especially heavy industries such as metallurgy and machine manufacturing. These industries require huge amounts of hydrogen fuel and a continuous, uninterrupted supply. This puts great pressure on the hydrogen fuel production industry and requires the complete development of infrastructure for a new type of fuel that is completely different from traditional fossil fuels. In addition, light industries such as food and medicine also need a clean supply of hydrogen fuel for storage, preservation, and manufacturing applications. In order to create a chemical reaction involving organic molecules, hydrogen is added during the hydrogenation process. In the food industry, for instance, H2 molecules are incorporated into unsaturated vegetable oils and fats. Moreover, hydrogen presents a fascinating option for producing fertilizers that are more durable. Hydrogen is also used a lot in medicine, with typical applications such as using clean, high-purity hydrogen to treat diseases. H2 gas inhalation using a ventilator circuit, facemask, or nasal cannula is an easy therapeutic approach. Inhalation is thought to be the most effective way to treat stress since inhaled H2 gas defuses quickly and is absorbed into the entire body. The application of hydrogen in medicine is very widespread and truly necessary. Therefore, in this medical field, a clean, high-purity, and stable source of hydrogen gas is required.
Most of the commercial hydrogen currently generated comes from fossil fuels, such as gasification of coal or reforming of natural gas. Hydrogen may be produced from biomass feedstocks using similar procedures. For a few decades, certain industrial applications have employed water electrolysis to make hydrogen, but in recent years, interest in this process has grown as a result of rapidly developing technology and the accessibility of inexpensive power.143–145 Many predictions for the future of hydrogen generation rely heavily on electrolysis, but other developing technologies, such thermolysis and photolysis, may allow for a more effective use of thermal or solar energy.
The future trend is to produce green hydrogen from the water electrolysis by environmentally friendly renewable energy (Fig. 24). This production method is forecasted to be cheaper than industrial production because the main input cost is electricity from renewable energy (solar, wind, hydroelectric, tidal). The technology of hydrogen production from biomass, algae and biotransformation processes is still in the process of research and testing of the national hydrogen strategy and budget for implementation.
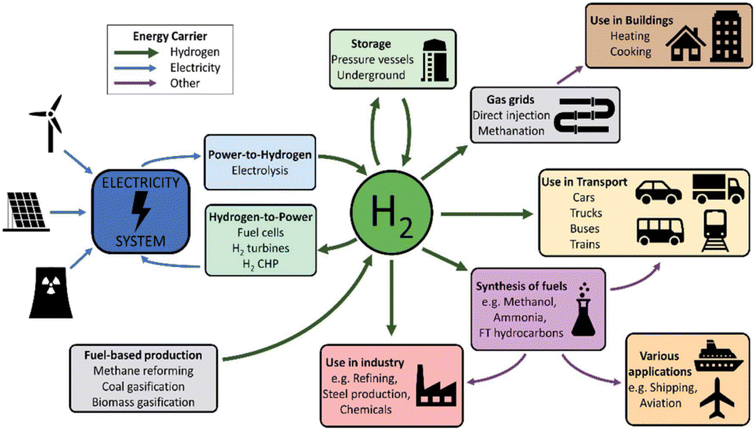 |
| Fig. 24 Future overview of hydrogen fuel and usage pathways. Hydrogen has a wide range of uses and production choices, which makes it useful for giving energy systems flexibility and sector coupling.144 Reproduced from ref. 144 with permission from [Royal Society of Chemistry], copyright [2020]. | |
With greenhouse gas emissions rising and the frequency of extreme weather events increasing, it is not difficult to see why countries are looking towards a future where energy plays a central role clean quantity. However, current efforts to move beyond fossil fuels are extremely difficult. Moreover, the geopolitical influence of oil and gas is present and dwarfs all other fuel sources. The world is facing a comprehensive energy crisis that directly affects the economy and stock market. The ambition to transition from an oil economy to a renewable energy economy is great and worth pursuing, but there are still too many economic and geopolitical hurdles that need to be overcome. The transition to renewable energy takes time because the world will inevitably face severe shocks due to the need to redistribute the entire energy system that powers the world economy and is the foundation of the geopolitical order.
5 Conclusions
Hydrogen fuel, which is created from renewable energy, is still in its infancy but has great potential for development. Many countries have announced green hydrogen strategies with huge investments. Green hydrogen production from renewable sources is competitive these days, especially as the price of solar has plummeted in recent years. Currently, electrolysis technology is improving, allowing the development of large-scale production factories. On the other hand, the decreasing cost of electricity production from renewable energy sources, especially wind and solar power, is also an important factor promoting the development of the green hydrogen industry. Moreover, climate change pressures fuel the need to phase out fossil fuels, fueling green hydrogen strategies. Governments, energy corporations, and car companies promote the use of clean fuels, and hydrogen plays a key role in helping to reduce greenhouse gas emissions enough to prevent the consequences of climate change. That prospect has sparked a global race to gain share in a market worth hundreds of billions of dollars.
Due to the significance of green hydrogen toward achieving a net-zero emission economy, it is considered essential that global hydrogen strategies and decadal plans be created based on the results of exhaustive research studies that present the key findings and provide guidelines for future policy implications. A viable route for meeting the world's large-scale hydrogen requirement is the transportation of liquid hydrogen. However, there is still a need for technological solutions to reduce shipping costs, protect hydrogen in liquid form during transportation, and keep the boil-off efficiency at an acceptable level. The necessity to construct home, industrial, and transportation infrastructure that is compatible with hydrogen fuel sources is another crucial issue. Converting our present fossil fuel infrastructure to alternative fuels will undoubtedly take some time. Additionally, this presents enormous difficulties for all nations in the world. In conclusion, hydrogen is now undergoing extensive study in an effort to create a high-tech, ecologically friendly, and secure society. Hydrogen will undoubtedly be a main energy source in the future.
Conflicts of interest
The authors declare that they have no known competing financial interests.
Acknowledgements
The authors wish to acknowledge the support given by the VinUniversity, Vietnam and Shinshu University, Japan. This work was also supported by JSPS KAKENHI (Grant Number JP23H01299), and in part by the program of the Fujian Minjiang Chair Professor Program (CN) [No2022(4)].
References
- P. A. Owusu and S. A. Sarkodie, A review of renewable energy sources, sustainability issues and climate change mitigation, Cogent Eng., 2016, 3, 1167990, DOI:10.1080/23311916.2016.1167990.
- M. Erdiwansyah, H. Husin Nasaruddin and M. Z. Muhibbuddin, A critical review of the integration of renewable energy sources with various technologies, Prot. Control Mod. Power Syst., 2021, 6, 3, DOI:10.1186/s41601-021-00181-3.
- C. Li, G. Liao and B. Fang, Magnetic-field-promotedphotocatalytic overall water-splitting systems, Chem Catal., 2022, 2(2), 238–241, DOI:10.1016/j.checat.2022.01.007.
- P. J. Megía, A. J. Vizcaíno, J. A. Calles and A. Carrero, Hydrogen Production Technologies: From Fossil Fuels toward Renewable Sources, Energy Fuels, 2021, 35(20), 16403–16415, DOI:10.1021/acs.energyfuels.1c02501.
- M. Yue, H. Lambert, E. Pahon, R. Roche, S. Jemei and D. Hissel, Hydrogen energy systems: a critical review of technologies, applications, trends and challenges, Renewable Sustainable Energy Rev., 2021, 146, 111180, DOI:10.1016/j.rser.2021.111180.
- M. Spek, C. Banet, C. Bauer, P. Gabrielli, W. Goldthorpe, M. Mazzotti, S. T. Munkejord, N. A. Røkke, N. Shah, N. Sunny, D. Sutter, J. M. Truslerh and M. Gazzani, Perspective on the hydrogen economy as a pathway to reach net-zero CO2 emissions in Europe, Energy Environ. Sci., 2022, 15, 1034–1077, 10.1039/D1EE02118D.
- M. E. Shafie, S. Kambara and Y. Hayakawa, Hydrogen Production Technologies Overview, J. Power Energy Eng., 2019, 7, 107–154, DOI:10.4236/jpee.2019.71007.
- G. Liao, X. Tao and B. Fang, An innovative synthesis strategy for high-efficiency and defectsswitchable-hydrogenated TiO2 photocatalysts, Matter, 2023, 5(2), 377–389, DOI:10.1016/j.matt.2022.01.006.
- M. S. Macedo, M. A. Soria and L. M. Madeira, Process intensification for hydrogen production through glycerol steam reforming, Renewable Sustainable Energy Rev., 2021, 146, 111151, DOI:10.1016/j.rser.2021.111151.
- D. R. Palo, R. A. Dagle and J. D. Holladay, Methanol Steam Reforming for Hydrogen Production, Chem. Rev., 2007, 107(10), 3992–4021, DOI:10.1021/cr050198b.
- P. Sun, B. Young, A. Elgowainy, Z. Lu, M. Wang, B. Morelli and T. Hawkins, Criteria Air Pollutants and Greenhouse Gas Emissions from Hydrogen Production in U.S. Steam Methane Reforming Facilities, Environ. Sci. Technol., 2019, 53, 7103–7113, DOI:10.1021/acs.est.8b06197.
- A. Posada and V. Manousiouthakis, Heat and Power Integration of Methane Reforming Based Hydrogen Production, Ind. Eng. Chem. Res., 2005, 44(24), 9113–9119, DOI:10.1021/ie049041k.
- M. N. Uddin and W. M. A. Wan Daud, Technological Diversity and Economics: Coupling Effects on Hydrogen Production from Biomass, Energy Fuels, 2014, 28(7), 4300–4320, DOI:10.1021/ef5007808.
- G. Yang and J. Wang, Enhanced Hydrogen Production from Sewage Sludge by Cofermentation with Forestry Wastes, Energy Fuels, 2017, 31, 9633–9641, DOI:10.1021/acs.energyfuels.7b02135.
- M. Axelsson, C. F. N. Marchiori, P. Huang, C. M. Araujo and H. Tian, Small Organic Molecule Based on Benzothiadiazole for Electrocatalytic Hydrogen Production, J. Am. Chem. Soc., 2021, 143(50), 21229–21233, DOI:10.1021/jacs.1c10600.
- M. Jaradat, O. Alsotary, A. Juaidi, A. Albatayneh, A. Alzoubi and S. Gorjian, Potential of Producing Green Hydrogen in Jordan, Energies, 2022, 15, 9039, DOI:10.3390/en15239039.
- M. K. Sarmah, T. P. Singh, P. Kalita and A. Dewan, Sustainable hydrogen generation and storage–a review, RSC Adv., 2023, 13, 25253, 10.1039/D3RA04148D.
- G. Liao, B. Fang and C. Li, A high-pressure-tolerant vapor-fed photocatalytic system for efficient water splitting, Chem Catal., 2023, 3, 100671, DOI:10.1016/j.checat.2023.100671.
- P. A. Le, V. Q. Le, T. L. Tran, N. T. Nguyen and T. V. B. Phung, A computation and investigation of two-dimensional WO3·H2O nanoflowers for electrochemical studies of energy conversion and storage applications, ACS Omega, 2022, 7(12), 10115–10126, DOI:10.1021/acsomega.1c06150.
- P. A. Le, V. Q. Le, N. T. Nguyen, T. L. Tran, V. A. Dinh and T. V. B. Phung, Two-dimensional NH4V3O8 Nanoflakes as Efficient Energy Conversion and Storage for the Hydrogen Evolution Reaction and Supercapacitors, ACS Omega, 2022, 7(29), 25433–25442, DOI:10.1021/acsomega.2c02375.
- G. Liu, F. Hou, Y. Wang, X. Wang and B. Fang, Engineering Ir and Ni3N heterogeneous interfaces for promoted overall water splitting, Appl. Surf. Sci., 2023, 637, 157896, DOI:10.1016/j.apsusc.2023.157896.
- M. A. Rosen and S. K. Fayegh, The prospects for hydrogen as an energy carrier: an overview of hydrogen energy and hydrogen energy systems, Energy, Ecol. Environ., 2016, 1, 10–29, DOI:10.1007/s40974-016-0005-z.
- U. Y. Qazi, Future of Hydrogen as an Alternative Fuel for Next-Generation Industrial Applications; Challenges and Expected Opportunities, Energies, 2022, 15, 4741, DOI:10.3390/en15134741.
- C. Bauer, K. Treyer, C. Antonini, J. Bergerson, M. Gazzani, E. Gencer, J. Gibbins, M. Mazzotti, S. T. McCoy, R. McKenna, R. Pietzcker, A. P. Ravikumar, M. C. Romano, F. Ueckerdt, J. Ventek and M. Spek, On the climate impacts of blue hydrogen production, Sustainable Energy Fuels, 2022, 6, 66–75, 10.1039/D1SE01508G.
- H. Singh, C. Li, P. Cheng, X. Wang and Q. Liu, A critical review of technologies, costs, and projects for production of carbon-neutral liquid e-fuels from hydrogen and captured CO2, Energy Adv., 2022, 1, 580–605, 10.1039/D2YA00173J.
- J. Guo, Y. Zhang, A. Zavabeti, K. Chen, Y. Guo, G. Hu, X. Fan and G. K. Li, Hydrogen production from the air, Nat. Commun., 2022, 13, 5046, DOI:10.1038/s41467-022-32652-y.
- F. Osselin, C. Soulaine, C. Fauguerolles, E. C. Gaucher, B. Scaillet and M. Pichavant, Orange hydrogen is the new green, Nat. Geosci., 2022, 15, 765–769, DOI:10.1038/s41561-022-01043-9.
- R. W. Howarth and M. Z. Jacobson, How green is blue hydrogen?, Energy Sci. Eng., 2021, 9, 1676–1687, DOI:10.1002/ese3.956.
- A. Hodges, A. L. Hoang, G. Tsekouras, K. Wagner, C. Y. Lee, G. F. Swiegers and G. G. Wallace, A high-performance capillary-fed electrolysis cell promises more cost-competitive renewable hydrogen, Nat. Commun., 2022, 13, 1304, DOI:10.1038/s41467-022-28953-x.
- A. I. Osman, N. Mehta, A. M. Elgarahy, M. Hefny, A. Al-Hinai, A. H. Al-Muhtaseb and D. W. Rooney, Hydrogen production, storage, utilisation and environmental impacts: a review, Environ. Chem. Lett., 2022, 20, 153–188, DOI:10.1007/s10311-021-01322-8.
- S. Lee, H. S. Kim, J. Park, B. M. Kang, C. H. Cho, H. Lim and W. Won, Scenario-Based Techno-Economic Analysis of Steam Methane Reforming Process for Hydrogen Production, Appl. Sci., 2021, 11, 6021, DOI:10.3390/app11136021.
- E. Shagdar, B. G. Lougou, Y. Shuai, E. Ganbold, O. P. Chinonso and H. Tan, Process analysis of solar steam reforming of methane for producing low-carbon hydrogen, RSC Adv., 2020, 10, 12582–12597, 10.1039/C9RA09835F.
- A. Boretti and B. K. Banik, Advances in Hydrogen Production from Natural Gas Reforming, Adv. Energy Sustainability Res., 2021, 2100097, DOI:10.1002/aesr.202100097.
- M. Katebah, M. A. Rawashdeh and P. Linke, Analysis of hydrogen production costs in Steam-Methane Reforming considering integration with electrolysis and CO2 capture, Clean. Eng. Technol., 2022, 10, 100552, DOI:10.1016/j.clet.2022.100552.
- C. S. Song, Fuel Processing for Low-Temperature and High-Temperature Fuel Cells: Challenges, and Opportunities for Sustainable Development in the 21st Century, Catal. Today, 2002, 77, 17–49, DOI:10.1016/S0920-5861(02)00231-6.
- R. Farrauto, S. Hwang, L. Shore, W. Ruettinger, J. Lampert, T. Giroux, Y. Liu and O. Ilinich, New Material Needs for Hydrocarbon Fuel Processing: Generating Hydrogen for the PEM Fuel Cell, Annu. Rev. Mater. Res., 2003, 33, 1–27, DOI:10.1146/annurev.matsci.33.022802.091348.
- Y. C. Sharma, A. Kumar, R. Prasad and S. N. Upadhyay, Ethanol steam reforming for hydrogen production: latest and effective catalyst modification strategies to minimize carbonaceous deactivation, Renewable Sustainable Energy Rev., 2017, 74, 89–103, DOI:10.1016/j.rser.2017.02.049.
- F. M. B. Kontchouo, Z. Gao, X. Xianglin, Y. Wang, Y. Sun, S. Zhang and X. Hu, Steam reforming of n-hexane and toluene: understanding impacts of structural difference of aliphatic and aromatic hydrocarbons on their coking behaviours, J. Environ. Chem. Eng., 2021, 9(6), 106383, DOI:10.1016/j.jece.2021.106383.
- M. T. Azizan, A. Aqsha, M. Ameen, A. Syuhada, H. Klaus, S. Z. Abidin and F. Sher, Catalytic reforming of oxygenated hydrocarbons for the hydrogen production: an outlook, Biomass Convers. Biorefin., 2020, 13, 8441–8464 CrossRef PubMed.
- A. M. Ranjekar and G. D. Yadav, Steam Reforming of Methanol for Hydrogen Production: A Critical Analysis of Catalysis, Processes, and Scope, Ind. Eng. Chem. Res., 2021, 60(1), 89–113, DOI:10.1021/acs.iecr.0c05041.
- K. Murata, L. Wang, M. Saito, M. Inaba, I. Takahara and N. Mimura, Hydrogen Production from Steam Reforming of Hydrocarbons over Alkaline-Earth Metal-Modified Fe- or Ni-Based Catalysts, Energy Fuels, 2004, 18(1), 122–126, DOI:10.1021/ef0301295.
- Z. R. Ismagilov, E. V. Matus, I. Z. Ismagilov, O. B. Sukhova, S. A. Yashnik, V. A. Ushakov and M. A. Kerzhentsev, Hydrogen production through hydrocarbon fuel reforming processes over Ni based catalysts, Catal. Today, 2019, 323, 166–182, DOI:10.1016/j.cattod.2018.06.035.
- C. A. Chagas, R. L. Manfro and F. S. Toniolo, Production of Hydrogen by Steam Reforming of Ethanol over Pd-Promoted Ni/SiO2 Catalyst, Catal. Lett., 2020, 150, 3424–3436, DOI:10.1007/s10562-020-03257-1.
- O. Shtyka, Z. Dimitrova, R. Ciesielski, A. Kedziora, G. Mitukiewicz, J. Leyko, W. Maniukewicz, A. Czylkowska and T. Maniecki, Steam reforming of ethanol for hydrogen production: influence of catalyst composition (Ni/Al2O3, Ni/Al2O3–CeO2, Ni/Al2O3–ZnO) and process conditions, React. Kinet., Mech. Catal., 2021, 132, 907–919, DOI:10.1007/s11144-021-01945-6.
- Y. S. Noh, K. Y. Lee and D. J. Moon, Hydrogen production by steam reforming of methane over nickel based structured catalysts supported on calcium aluminate modified SiC, Int. J. Hydrogen Energy, 2019, 44(38), 21010–21019, DOI:10.1016/j.ijhydene.2019.04.287.
- M. Musso, A. Cardozo, M. Romero, R. Faccio, D. Segobia, C. Apesteguía and J. J. Bussi, High performance Ni-catalysts supported on rare-earth zirconates (La and Y) for hydrogen production through ethanol steam reforming. Characterization and assay, Catal. Today, 2022, 394, 524–538, DOI:10.1016/j.cattod.2021.07.001.
- S. Ogo and Y. Sekine, Recent progress in ethanol steam reforming using non-noble transition metal catalysts: a review, Fuel Process. Technol., 2020, 199, 106238, DOI:10.1016/j.fuproc.2019.106238.
- C. Hognon, Y. Simon and P. M. Marquaire, Hydrogen Production by Homogeneous Partial Oxidation of Propane, Energy Fuels, 2012, 26(3), 1496–1508, DOI:10.1021/ef201938t.
- A. E. Lutz, R. W. Bradshaw, L. Bromberg and A. Rabinovich, Thermodynamic analysis of hydrogen production by partial oxidation reforming, Int. J. Hydrogen Energy, 2004, 29, 809–816, DOI:10.1016/j.ijhydene.2003.09.015.
- A. I. Osman, Catalytic Hydrogen Production from Methane Partial Oxidation: Mechanism and Kinetic Study, Chem. Eng. Technol., 2020, 43(4), 641–648, DOI:10.1002/ceat.201900339.
- J. J. Krummenacher, K. N. West and L. D. Schmidt, Catalytic partial oxidation of higher hydrocarbons at millisecond contact times: decane, hexadecane, and diesel fuel, J. Catal., 2003, 215, 332–343, DOI:10.1016/S0021-9517(03)00011-3.
- A. Holmen, Direct conversion of methane to fuels and chemicals, Catal. Today, 2009, 142, 2–8, DOI:10.1016/j.cattod.2009.01.004.
- K. A. Petersen, J. H. B. Hansen, T. S. Christensen, I. Dybkjaer, P. S. Christensen, C. S. Nielsen, S. E. L. W. Madsen and J. R. R. Nielsen, Technologies for large-scale gas conversion, Appl. Catal., A, 2001, 221, 379–387, DOI:10.1016/S0926-860X(01)00811-0.
- Y. J. O. Asencios, P. A. P. Nascente and E. M. Assaf, Partial oxidation of methane on NiO–MgO–ZrO2 catalysts, Fuel, 2012, 97, 630–637, DOI:10.1016/j.fuel.2012.02.067.
- A. Scarabello, D. D. Nogare, P. Canu and R. Lanza, Partial oxidation of methane on Rh/ZrO2 and Rh/Ce–ZrO2 on monoliths: catalyst restructuring at reaction conditions, Appl. Catal., B, 2015, 174, 308–322, DOI:10.1016/j.apcatb.2015.03.012.
- W. H. Chen, Y. Q. Su, B. J. Lin, J. K. Kuo and P. C. Kuo, Hydrogen production from partial oxidation and autothermal reforming of methanol from a cold start in sprays, Fuel, 2021, 287, 119638, DOI:10.1016/j.fuel.2020.119638.
- M. Luneau, E. Gianotti, F. C. Meunier, C. Mirodatos, E. Puzenat, Y. Schuurman and N. Guilhaume, Deactivation Mechanism of Ni Supported on Mg–Al Spinel during Autothermal Reforming of Model Biogas, Appl. Catal., B, 2017, 203, 289–299, DOI:10.1016/j.apcatb.2016.10.023.
- R. Baruah, M. Dixit, P. Basarkar, D. Parikh and A. Bhargav, Advances in Ethanol Autothermal Reforming, Renewable Sustainable Energy Rev., 2015, 51, 1345–1353, DOI:10.1016/j.rser.2015.07.060.
- R. Tariq, F. Maqbool and S. Z. Abbas, Small-Scale Production of Hydrogen via Auto-Thermal Reforming in an Adiabatic Packed Bed Reactor: Parametric Study and Reactor's Optimization through Response Surface Methodology, Comput. Chem. Eng., 2021, 145, 107192, DOI:10.1016/j.compchemeng.2020.107192.
- K. Geissler, E. Newson, F. Vogel, T. B. Truong, P. Hottingera and A. Wokaun, Autothermal methanolreforming for hydrogen production in fuel cell applications, Phys. Chem. Chem. Phys., 2001, 3, 289–293, 10.1039/B004881J.
- M. Krumpelt, T. R. Krause, J. D. Carter, J. D. Kopasz and S. Ahmed, Fuel Processing for Fuel Cell Systems in Transportation and Portable Power Applications, Catal. Today, 2002, 77, 3–16, DOI:10.1016/S0920-5861(02)00230-4.
- T. Liu, H. Temur and G. Veser, Autothermal Reforming of Methane in a Reverse-Flow Reactor, Chem. Eng. Technol., 2009, 32(9), 1358–1366, DOI:10.1002/ceat.200900203.
- S. Wang, G. Dai, H. Yang and Z. Luo, Lignocellulosic Biomass Pyrolysis Mechanism: A State-of-the-Art Review, Prog. Energy Combust. Sci., 2017, 62, 33–86, DOI:10.1016/j.pecs.2017.05.004.
- N. Z. Muradov, How to Produce Hydrogen from Fossil Fuels without CO2 Emission, Int. J. Hydrogen Energy, 1993, 18(3), 211–215, DOI:10.1016/0360-3199(93)90021-2.
- A. Bakhtyari, M. A. Makarem and M. R. Rahimpour, Hydrogen production through pyrolysis, in Encyclopedia of Sustainability Science and Technology, ed. R. Meyers, Springer, New York, NY, 2018, DOI: DOI:10.1007/978-1-4939-2493-6_956-1.
- C. Palmer, M. Tarazkar, M. J. Gordon, H. Metiu and E. W. McFarland, Methane pyrolysis in low-cost, alkali-halide molten salts at high temperatures, Sustainable Energy Fuels, 2021, 5, 6107–6123, 10.1039/D1SE01408K.
- N. S. Bastardo, R. Schlogl and H. Ruland, Methane Pyrolysis for CO2 -Free H2 Production: A Green Process to Overcome Renewable Energies Unsteadiness, Chem. Ing. Tech., 2020, 92(10), 1596–1609, DOI:10.1002/cite.202000029.
- C. Palmer, E. Bunyan, J. Gelinas, M. J. Gordon, H. Metiu and E. W. McFarland, CO2-Free Hydrogen Production by Catalytic Pyrolysis of Hydrocarbon Feedstocks in Molten Ni–Bi, Energy Fuels, 2020, 34(12), 16073–16080, DOI:10.1021/acs.energyfuels.0c03080.
- F. Angikath, G. Pezzella and S. M. Sarathy, Bubble-Size Distribution and Hydrogen Evolution from Pyrolysis of Hydrocarbon Fuels in a Simulated Ni0.27Bi0.73 Column Reactor, Ind. Eng. Chem. Res., 2022, 61(34), 12369–12382, DOI:10.1021/acs.iecr.2c01148.
- J. X. Qian, D. B. Liu, J. M. Basset and L. Zhou, Methane decomposition to produce hydrogen and carbon nanomaterials over costless, iron-containing catalysts, J. Cleaner Prod., 2021, 320, 128879, DOI:10.1016/j.jclepro.2021.128879.
- A. A. Volodin, P. V. Fursikov, Y. A. Kasumov, I. I. Khodos and B. P. Tarasov, Synthesis of carbon nanofibers by catalytic pyrolysis of ethylene and methane on hydrides of intermetallic compounds of lanthanum with nickel, Russ. Chem. Bull., 2005, 54, 2281–2285, DOI:10.1007/s11172-006-0110-9.
- M. Keller, A. Matsumura and A. Sharma, Spray-dried Fe/Al2O3 as a carbon carrier for COx-free hydrogen production via methane cracking in a fluidized bed process, J. Chem. Eng., 2020, 398, 125612, DOI:10.1016/j.cej.2020.125612.
- N. V. Gnanapragasam, B. V. Reddy and M. A. Rosen, Hydrogen production from coal gasification for effective downstream CO2 capture, Int. J. Hydrogen Energy, 2010, 35(10), 4933–4943, DOI:10.1016/j.ijhydene.2009.07.114.
- K. Stańczyk, K. Kapusta, M. Wiatowski, J. Świądrowski, A. Smoliński, J. Rogut and A. Kotyrba, Experimental Simulation of Hard Coal Underground Gasification for Hydrogen Production, Fuel, 2012, 91(1), 40–50, DOI:10.1016/j.fuel.2011.08.024.
- G. J. Stiegel and M. Ramezan, Hydrogen from coal gasification: an economical pathway to a sustainable energy future, Int. J. Coal Geol., 2006, 65, 173–190, DOI:10.1016/j.coal.2005.05.002.
- S. Mukherjee, P. Kumar, A. Hosseini, A. Yang and P. Fennell, Comparative Assessment of Gasification Based Coal Power Plants with Various CO2 Capture Technologies Producing Electricity and Hydrogen, Energy Fuels, 2014, 28(2), 1028–1040, DOI:10.1021/ef4024299.
- M. Liszka, T. Malik and G. Manfrida, Energy and exergy analysis of hydrogen-oriented coal gasification with CO2 capture, Energy, 2012, 45, 142–150, DOI:10.1016/j.energy.2012.03.054.
- H. A. Alibrahim, S. S. Khalafalla, U. Ahmed, S. Park, C. J. Lee and U. Zahid, Conceptual design of syngas production by the integration of gasification and dry-reforming technologies with CO2 capture and utilization, Energy Convers. Manage., 2021, 244, 114485, DOI:10.1016/j.enconman.2021.114485.
- M. Kayfeci, A. Keçebaş and M. Bayat, Chapter 3 – Hydrogen Production – Solar Hydrogen Production, Processes, Systems and Technologies, 2019, pp. 45–83, DOI: DOI:10.1016/B978-0-12-814853-2.00003-5.
- H. Song, G. Yang, P. Xue, Y. Li, J. Zou, S. Wang, H. Yang and H. Chen, Recent development of biomass gasification for H2 rich gas production, Applications in Energy and Combustion, Science, 2022, 10, 100059, DOI:10.1016/j.jaecs.2022.100059.
- S. I. M. Hurtado, P. Puello and A. Cabarcas, Process Analysis of Hydrogen Production via Biomass Gasification under Computer-Aided Safety and Environmental Assessments, ACS Omega, 2020, 5, 19667–19681, DOI:10.1021/acsomega.0c02344.
- A. C. C. Chang, H. F. Chang, F. J. Lin, K. H. Lin and C. H. Chen, Biomass gasification for hydrogen production, Int. J. Hydrogen Energy, 2011, 36, 14252–14260, DOI:10.1016/j.ijhydene.2011.05.105.
- A. T. Besha, M. T. Tsehaye, G. A. Tiruye, A. Y. Gebreyohannes, A. Awoke and R. A. Tufa, Deployable Membrane-Based Energy Technologies: the Ethiopian Prospect, Sustainability, 2020, 12(21), 8792, DOI:10.3390/su12218792.
- S. I. M. Hurtado, P. Puello and A. Cabarcas, Process Analysis of Hydrogen Production via Biomass Gasification under Computer-Aided Safety and Environmental Assessments, ACS Omega, 2020, 5(31), 19667–19681, DOI:10.1021/acsomega.0c02344.
- G. Sołowski, M. S. Shalaby, H. Abdallah, A. M. Shaband and A. Cenian, Production of hydrogen from biomass and its separation using membrane technology, Renewable Sustainable Energy Rev., 2018, 82, 3152–3167, DOI:10.1016/j.rser.2017.10.027.
- T. Lepage, M. Kammoun, Q. Schmetz and A. Richel, Biomass-to-hydrogen: a review of main routes production, processes evaluation and techno-economical assessment, Biomass Bioenergy, 2021, 144, 105920, DOI:10.1016/j.biombioe.2020.105920.
- A. Arregi, G. Lopez, M. Amutio, I. Barbarias, J. Bilbao and M. Olazar, Hydrogen production from biomass by continuous fast pyrolysis and in-line steam reforming, RSC Adv., 2016, 6, 25975–25985, 10.1039/C6RA01657J.
- Z. Gao, D. Zeng, S. Wu, S. Ren, F. Zhou, M. Gao, F. Song, Y. Zhai and R. Xiao, High-purity hydrogen production from real biomass pyrolysis vapors via a chemical looping process, Sustainable Energy Fuels, 2023, 7, 2200–2208, 10.1039/D2SE01635D.
- P. Lang, A. Lu, P. Liu, Y. Li, X. Li, T. Sun, Y. Yang and T. Lei, Pyrolysis of wood waste to enhance hydrogen production on iron-based aluminum dross, Fuel, 2023, 334, 126781, DOI:10.1016/j.fuel.2022.126781.
- S. M. Al-Salem, P. Lettieri and J. Baeyens, Recycling and recovery routes of plastic solid waste (PSW): a review, Waste Manage., 2009, 29, 2625–2643, DOI:10.1016/j.wasman.2009.06.004.
- M. Kedzierski, D. Frere, G. L. Maguer and S. Bruzaud, Why is there plastic packaging in the natural environment? Understanding the roots of our individual plastic waste management behaviours, Sci. Total Environ., 2020, 740, 139985, DOI:10.1016/j.scitotenv.2020.139985.
- W. C. Li, H. F. Tse and L. Fok, Plastic waste in the marine environment: a review of sources, occurrence and effects, Sci. Total Environ., 2016, 566–567, 333–349, DOI:10.1016/j.scitotenv.2016.05.084.
- A. Bianco, F. Sordello, M. Ehn, D. Vione and M. Passananti, Degradation of nanoplastics in the environment: reactivity and impact on atmospheric and surface waters, Sci. Total Environ., 2020, 742, 140413, DOI:10.1016/j.scitotenv.2020.140413.
- S. Afzal, A. Singh, S. R. Nicholson, T. Uekert, J. S. DesVeaux, E. C. D. Tan, A. Dutta, A. C. Carpenter, R. M. Baldwin and G. T. Beckham, Techno-economic analysis and life cycle assessment of mixed plastic waste gasification for production of methanol and hydrogen, Green Chem., 2023, 25, 5068–5085, 10.1039/D3GC00679D.
- A. S. Al-Fatesh, N. Y. A. AL-Garadi, A. I. Osman, F. S. Al-Mubaddel, A. A. Ibrahim, W. U. Khan, Y. M. Alanazi, M. M. Alrashed and O. Y. Alothman, Fuel, 2023, 344, 128107, DOI:10.1016/j.fuel.2023.128107.
- Y. Wang, K. Liu, F. Liu, C. Liu, R. Shi and Y. Chen, Selective electro-reforming of waste polyethylene terephthalate-derived ethylene glycol into C2 chemicals with long-term stability, Green Chem., 2023, 25, 5872–5877, 10.1039/D3GC01486J.
- E. Yazdani, S. H. Hashemabadi and A. Taghizadeh, Study of waste tire pyrolysis in a rotary kiln reactor in a wide range of pyrolysis temperature, Waste Manage., 2019, 85, 195–201, DOI:10.1016/j.wasman.2018.12.020.
- N. Nkosi, E. Muzenda, J. Gorimbo and M. Belaid, Developments in waste tyre thermochemical conversion processes: gasification, pyrolysis and liquefaction, RSC Adv., 2021, 11, 11844–11871, 10.1039/D0RA08966D.
- A. S. Al-Fatesh, N. Y. A. Al-Garadi, A. I. Osman, F. S. Al-Mubaddel, A. A. Ibrahim, W. U. Khan, Y. M. Alanazi, M. M. Alrashed and O. Y. Alothman, From plastic waste pyrolysis to Fuel: impact of process parameters and material selection on hydrogen production, Fuel, 2023, 344, 128107, DOI:10.1016/j.fuel.2023.128107.
- S. Wang, R. Shan, J. Gu, T. Huhe, X. Ling, H. Yuan and Y. Chen, High-yield H2 production from polypropylene through pyrolysis-catalytic reforming over activated carbon based nickel catalyst, J. Cleaner Prod., 2022, 352, 131566, DOI:10.1016/j.jclepro.2022.131566.
- J. M. Saad and P. T. Williams, Pyrolysis-Catalytic-Dry Reforming of Waste Plastics and Mixed Waste Plastics for Syngas Production, Energy Fuels, 2016, 30(4), 3198–3204, DOI:10.1021/acs.energyfuels.5b02508.
- H. Xiao, J. Harding, S. Lei, W. Chen, S. Xia, N. Cai, X. Chen, J. Hu, Y. Chen, X. Wang, X. Tu, H. Yang and H. Chen, Hydrogen and aromatics recovery through plasma-catalytic pyrolysis of waste polypropylene, J. Cleaner Prod., 2022, 350, 131467, DOI:10.1016/j.jclepro.2022.131467.
- I. Aminu, M. A. Nahil and P. T. Williams, Pyrolysis-plasma/catalytic reforming of post-consumer waste plastics for hydrogen production, Catal. Today, 2023, 420, 114084, DOI:10.1016/j.cattod.2023.114084.
- R. S. Sherbo, R. S. Delima, V. A. Chiykowski, B. P. MacLeod and C. P. Berlinguette, Complete electron economy by pairing electrolysis with hydrogenation, Nat. Catal., 2018, 1, 501–507, DOI:10.1038/s41929-018-0083-8.
- W. J. Liu, Z. Xu, D. Zhao, X. Q. Pan, H. C. Li, X. Hu, Z. Y. Fan, W. K. Wang, G. H. Zhao, S. Jin, G. W. Huber and H. Q. Yu, Efficient electrochemical production of glucaric acid and H2 via glucose electrolysis, Nat. Commun., 2020, 11, 265, DOI:10.1038/s41467-019-14157-3.
- A. Rafey, K. Pal, A. Bohre, A. Modak and K. K. Pant, A State-of-the-Art Review on the Technological Advancements for the Sustainable Management of Plastic Waste in Consort with the Generation of Energy and Value-Added Chemicals, Catalysts, 2023, 13, 420, DOI:10.3390/catal13020420.
- R. Shi, K. S. Liu, F. Liu, X. Yang, C. C. Hou and Y. Chen, Electrocatalytic reforming of waste plastics into high value-added chemicals and hydrogen fuel, Chem. Commun., 2021, 57, 12595–12598, 10.1039/D1CC05032J.
- H. Zhou, Y. Ren, Z. Li, M. Xu, Y. Wang, R. Ge, X. Kong, L. Zheng and H. Duan, Electrocatalytic upcycling of polyethylene terephthalate to commodity chemicals and H2 fuel, Nat. Commun., 2021, 12, 4679, DOI:10.1038/s41467-021-25048-x.
- M. Yu, E. Budiyanto and H. Tgysgz, Principles of Water Electrolysis and Recent Progress in Cobalt-, Nickel-, and Iron-Based Oxides for the Oxygen Evolution Reaction, Angew. Chem., Int. Ed., 2022, 61, e202103824, DOI:10.1002/anie.202103824.
- A. Raveendran, M. Chandran and R. Dhanusuraman, A comprehensive review on the electrochemical parameters and recent material development of electrochemical water splitting electrocatalysts, RSC Adv., 2023, 13, 3843–3876, 10.1039/D2RA07642J.
- Y. Kim, S. M. Jung, K. S. Kim, H. Y. Kim, J. Kwon, J. Lee, H. S. Cho and Y. T. Kim, Cathodic Protection System against a Reverse-Current after Shut-Down in Zero-Gap Alkaline Water Electrolysis, JACS Au, 2022, 2(11), 2491–2500, DOI:10.1021/jacsau.2c00314.
- G. Liu, D. Shan, B. Fang and X. Wang, Novel hybrid coating of TiN and carbon with improved corrosion resistance for bipolar plates of PEM water electrolysis, Int. J. Hydrogen Energy, 2023, 48, 18996–19007, DOI:10.1016/j.ijhydene.2023.02.015.
- M. F. Vostakola, H. Ozcan, R. S. El-Emam and B. A. Horri, Recent Advances in High-Temperature Steam Electrolysis with Solid Oxide Electrolysers for Green Hydrogen Production, Energies, 2023, 16, 3327, DOI:10.3390/en16083327.
- A. Bora, K. Mohanrasu, T. A. Swetha, V. Ananthi, R. Sindhu, N. T. L. Chi, A. Pugazhendhi, A. Arun and T. Mathimani, Microbial electrolysis cell (MEC): reactor configurations, recent advances and strategies in biohydrogen production, Fuel, 2022, 328, 125269, DOI:10.1016/j.fuel.2022.125269.
- K. Kamlungsua, P. C. Su and S. H. Chan, Hydrogen Generation Using Solid Oxide Electrolysis Cells, Fuel Cells, 2020, 20, 644–649, DOI:10.1002/fuce.202070602.
- A. Kudo and Y. Miseki, Heterogeneous photocatalyst materials for water splitting, Chem. Soc. Rev., 2009, 38, 253–278, 10.1039/B800489G.
- G. L. Chiarello and E. Selli, Advances in Hydrogen Production, Storage and Distribution, ed. A. Basile and A. Iulianelli, Elsevier, Amsterdam, 2014, 8 – Photocatalytic Production of Hydrogen, ch. 8, vol. 1, pp. 216–247, DOI: DOI:10.1533/9780857097736.2.216.
- K. C. Christoforidis and P. Fornasiero, Photocatalytic Hydrogen Production: A Rift into the Future Energy Supply, ChemCatChem, 2017, 9, 1523–1544, DOI:10.1002/cctc.201601659.
- F. T. Geldasa, M. A. Kebede, M. W. Shura and F. G. Hone, Experimental and computational study of metal oxide nanoparticles for the photocatalytic degradation of organic pollutants: a review, RSC Adv., 2023, 13, 18404–18442, 10.1039/D3RA01505J.
- W. Peng, Y. Li, F. Zhang, G. Zhang and X. Fan, Roles of Two-Dimensional Transition Metal Dichalcogenides as Cocatalysts in Photocatalytic Hydrogen Evolution and Environmental Remediation, Ind. Eng. Chem. Res., 2017, 56(16), 4611–4626, DOI:10.1021/acs.iecr.7b00371.
- S. Sahani, K. M. Tripathi, T. I. Lee, D. P. Dubal, C. P. Wong, Y. C. Sharma and T. Y. Kim, Recent advances in photocatalytic carbon-based materials for enhanced water splitting under visible-light irradiation, Energy Convers. Manage., 2022, 252, 115133, DOI:10.1016/j.enconman.2021.115133.
- Y. Li, H. Xu, S. Ouyang and J. Ye, Metal–organic frameworks for photocatalysis, Phys. Chem. Chem. Phys., 2016, 18, 7563–7572, 10.1039/C5CP05885F.
- E. Rivard, M. Trudeau and K. Zaghib, Hydrogen Storage for Mobility: A Review, Materials, 2019, 12, 1973, DOI:10.3390/ma12121973.
- R. Moradi and K. M. Growth, Hydrogen storage and delivery: review of the state of the art technologies and risk and reliability analysis, Int. J. Hydrogen Energy, 2019, 44(23), 12254–12269, DOI:10.1016/j.ijhydene.2019.03.041.
- J. O. Abe, A. P. I. Popoola, E. Ajenifuja and O. M. Popoola, Hydrogen energy, economy and storage: review and recommendation, Int. J. Hydrogen Energy, 2019, 44(29), 15072–15086, DOI:10.1016/j.ijhydene.2019.04.068.
- H. T. Hwang and A. Varma, Hydrogen storage for fuel cell vehicles, Curr. Opin. Chem. Eng., 2014, 5, 42–48, DOI:10.1016/j.coche.2014.04.004.
- M. Reuß, T. Grube, M. Robinius, P. Preuster, P. Wasserscheid and D. Stolten, Seasonal storage and alternative carriers: a flexible hydrogen supply chain model, Applied Energy, 2017, 200, 290–302, DOI:10.1016/j.apenergy.2017.05.050.
- A. Lys, J. O. Fadonougbo, M. Faisal, J. Y. Suh, Y. S. Lee, J. H. Shim, J. Park and Y. W. Cho, Enhancing the Hydrogen Storage Properties of AxBy Intermetallic Compounds by Partial Substitution: A Short Review, Hydrogen, 2020, 1, 38–63, DOI:10.3390/hydrogen1010004.
- N. S. Muhammed, B. Haq, D. A. Shehri, A. Al-Ahmed, M. M. Rahman and E. Zaman, A review on underground hydrogen storage: insight into geological sites, influencing factors and future outlook, Energy Rep., 2022, 8, 461–499, DOI:10.1016/j.egyr.2021.12.002.
- M. Bai, K. Song, Y. Sun, M. He, Y. Li and J. Sun, An overview of hydrogen underground storage technology and prospects in China, J. Pet. Sci. Eng., 2014, 124, 132–136, DOI:10.1016/j.petrol.2014.09.037.
- S. Iglauer, Optimum geological storage depths for structural H2 geo-storage, J. Pet. Sci. Eng., 2022, 212, 109498, DOI:10.1016/j.petrol.2021.109498.
- J. Andersson and S. Gronkvist, Large-scale storage of hydrogen, Int. J. Hydrogen Energy, 2019, 44(29), 11901–11919, DOI:10.1016/j.ijhydene.2019.03.063.
- A. G. Rao, F. Yin and H. G. C. Werij, Energy Transition in Aviation: The Role of Cryogenic Fuels, Aerospace, 2020, 7, 181, DOI:10.3390/aerospace7120181.
- D. E. Demirocak, Hydrogen storage technologies, in Nanostructured Materials for Next-Generation Energy Storage and Conversion, ed. Y. P. Chen, S. Bashir and J. L. Liu, Springer, Berlin, Heidelberg, 2017, DOI: DOI:10.1007/978-3-662-53514-1_4.
- R. Dickson, M. S. Akhtar, A. Abbas, E. D. Park and J. Liu, Global transportation of green hydrogen via liquid carriers: economic and environmental sustainability analysis, policy implications, and future directions, Green Chem., 2022, 24, 8484–8493, 10.1039/D2GC02079C.
- P. Balcombe, P. E. Dodds, P. Ekins, N. Shahd and K. R. Ward, The role of hydrogen and fuel cells in the global energy system, Energy Environ. Sci., 2019, 12, 463–491, 10.1039/C8EE01157E.
- A. Ibrahim, M. Paskevicius and C. E. Buckley, Chemical compression and transport of hydrogen using sodium borohydride, Sustainable Energy Fuels, 2023, 7, 1196–1203, 10.1039/D2SE01334G.
- L. Lin, Y. Tian, W. Su, Y. Luo, C. Chen and L. Jiang, Techno-economic analysis and comprehensive optimization of an on-site hydrogen refuelling station system using ammonia: hybrid hydrogen purification with both high H2 purity and high recovery, Sustainable Energy Fuels, 2020, 4, 3006–3017, 10.1039/C9SE01111K.
- L. Zhai, S. Liu and Z. Xiang, Ammonia as a carbon-free hydrogen carrier for fuel cells: a perspective, Ind. Chem. Mater., 2023, 1, 332–342, 10.1039/D3IM00036B.
- G. Jeerh, M. Zhang and S. Tao, Recent progress in ammonia fuel cells and their potential applications, J. Mater. Chem. A, 2021, 9, 727–752, 10.1039/D0TA08810B.
- C. Chu, K. Wu, B. Luo, Q. Cao and H. Zhang, Hydrogen storage by liquid organic
hydrogen carriers: catalyst, renewable carrier, and technology – a review, Carbon Resour. Convers., 2023, 6, 334–351, DOI:10.1016/j.crcon.2023.03.007.
- M. Niermann, S. Drunert, M. Kaltschmitt and K. Bonhoff, Liquid organic hydrogen carriers (LOHCs) – techno-economic analysis of LOHCs in a defined process chain, Energy Environ. Sci., 2019, 12, 290–307, 10.1039/C8EE02700E.
- M. H. Barecka and J. W. Ager, Towards an accelerated decarbonization of the chemical industry by electrolysis, Energy Adv., 2023, 2, 268, 10.1039/D2YA00134A.
- C. J. Quarton, O. Tlili, L. Welder, C. Mansilla, H. Blanco, H. Heinrichs, J. Leaver, N. J. Samsatli, P. Lucchese, M. Robinius and S. Samsatli, The curious case of the conflicting roles of hydrogen in global energy scenarios, Sustainable Energy Fuels, 2020, 4, 80–95, 10.1039/C9SE00833K.
- M. Nasser, T. F. Megahed and S. O. H. Hassan, A review of water electrolysis-based systems for hydrogen production using hybrid/solar/wind energy systems, Environ. Sci. Pollut. Res., 2022, 29, 86994–87018, DOI:10.1007/s11356-022-23323-y.
|
This journal is © The Royal Society of Chemistry 2023 |
Click here to see how this site uses Cookies. View our privacy policy here.