DOI:
10.1039/D3RA04177H
(Review Article)
RSC Adv., 2023,
13, 25182-25208
Recent progress in high-performance environmental impacts of the removal of radionuclides from wastewater based on metal–organic frameworks: a review
Received
21st June 2023
, Accepted 1st August 2023
First published on 23rd August 2023
Abstract
The nuclear industry is rapidly developing and the effective management of nuclear waste and monitoring the nuclear fuel cycle are crucial. The presence of various radionuclides such as uranium (U), europium (Eu), technetium (Tc), iodine (I), thorium (Th), cesium (Cs), and strontium (Sr) in the environment is a major concern, and the development of materials with high adsorption capacity and selectivity is essential for their effective removal. Metal–organic frameworks (MOFs) have recently emerged as promising materials for removing radioactive elements from water resources due to their unique properties such as tunable pore size, high surface area, and chemical structure. This review provides an extensive analysis of the potential of MOFs as adsorbents for purifying various radionuclides rather than using different techniques such as precipitation, filtration, ion exchange, electrolysis, solvent extraction, and flotation. This review discusses various MOF fabrication methods, focusing on minimizing environmental impacts when using organic solvents and solvent-free methods, and covers the mechanism of MOF adsorption towards radionuclides, including macroscopic and microscopic views. It also examines the effectiveness of MOFs in removing radionuclides from wastewater, their behavior on exposure to high radiation, and their renewability and reusability. We conclude by emphasizing the need for further research to optimize the performance of MOFs and expand their use in real-world applications. Overall, this review provides valuable insights into the potential of MOFs as efficient and durable materials for removing radioactive elements from water resources, addressing a critical issue in the nuclear industry.
Introduction
Recently, with the lack of renewable energy sources, nuclear energy has become one of the world's vital sources of electrical power.1–4 The waste from these nuclear processes contains a high level of liquid, which contains many radioactive ions.5,6 The field of nuclear research, in addition to nuclear power plants, non-peaceful uses of nuclear energy as lethal weapons, and nuclear accidents, besides mining, is the most dangerous source of radioactive elements.7,8 Some of these radioactive elements exist naturally in the minerals of monazite and thorite.9,10
Radioactive waste is matter contaminated by some radioactive elements.11,12 Nuclear waste is divided into three groups as follows. (a) High-level waste (HLW) is comprised of radionuclides from fuel rods, moderators, and any radiation target in the reactor. (b) Transuranic waste (TRU) includes radionuclides in the cleaning waste, which emit alpha-particles (except for plutonium 238 and 241, which undergo fission). (c) Low-level waste (LLW) is waste that is contaminated by small amounts of radionuclides and is generated mainly by hospitals, research organizations, nuclear energy operations and nuclear reactors.13,14 Radionuclides such as strontium, cesium,15–19 rare earth elements, thorium, and uranium20,21 that result in waste are summarized in Table 1. All of these radioactive elements lead to nuclear waste and cause numerous health problems, such as kidney damage, cancer, and lung and liver cancers due to exposure to radiation from these radioactive elements.22,23 Due to their severity and toxicity, these radioactive elements must be separated from wastewater;15,24 therefore, it is important to remove these unpleasant dangerous sources and develop an easy treatment method.
Table 1 Common radionuclides
Nuclide |
T-half (year) |
Analog |
Forms |
3H |
12.3 |
H |
H2O, H+, OH−, H2 (g) |
14C |
5 × 103 |
C |
HCO3−, H2CO3, CO32−, CO2, CH4 |
36CI |
3.1 × 105 |
CI |
Cl−, HCI (g) |
63Ni |
100 |
Ni |
Ni2+, NiOH+, NiCI2, NiCO3, Ni(OH)2 |
90Sr |
29.0 |
Sr, Ca |
Sr2+, SrCO3 |
93Zr |
1.5 × 106 |
Zr |
Zr(OH)22+, Zr(OH)5−, ZrSiO4 |
94Nb |
2 × 104 |
Nb |
Nb(OH)5 |
107Pd |
7 × 106 |
Pd, Pt |
Pd2+, Pd(OH)2, PdCl42− |
129I |
2 × 107 |
I, CI, Br |
I−, 103− |
135Cs |
3 × 106 |
Cs, Rb |
Cs+ |
137Cs |
30.0 |
Cs, Rb |
Cs+ |
154Eu |
8.2 |
Eu, REE |
Eu3+, Eu(OH)2+, EuSO4+, Eu(OH)3 |
79Se |
6.5 × 104 |
Se, S |
Se2−, HSe−, Se(s), SeO42− SeO32− |
93Mo |
3.5 × 103 |
Mo |
Mo4+, MoO42−, MoS2 |
99Tc |
2 × l05 |
Re, Mn |
TcO4−, Tc4+, TCO2 TCS2, Tc(OH)4 |
106Ru |
1.0 |
Ru, Mo |
RuO42−, RUO2, RUS2 |
126Sn |
1 × l05 |
Sn |
SnH, Sn(OH)+, SnS, SnO2 |
147Sm |
1.3 × 1011 |
Sm, Nd |
Sm3+, Sm(OH)2+, Sm(OH)3 |
151Sm |
90.0 |
Sm, Nd |
Sm3+, Sm(OH)2+, Sm(OH)3 |
210Pb |
22.0 |
Pb |
Pb2+, Pb(OH)+, PbS, PbCl+ |
226Ra |
1.6 × 103 |
Ra, Ba, Sr, Ca |
Ra2+ |
227Ac |
22.0 |
REE |
Ac3+, Ac(OH)2+, Ac(OH)3 |
230Th |
8 × 104 |
Th |
Th4+, Th(OH)3+, ThO2, Th(OH)2 |
232Th |
1.4 × 1010 |
Th |
Th4+, Th(OH)3+, ThO2, Th(OH)4 |
231 Pa |
3 × 104 |
Pa |
Pa(OH)5 |
234U |
2.5 × 105 |
U |
U complexes |
235U |
7 × 108 |
U |
U complexes |
238U |
4.5 × 109 |
U |
U complexes |
237Np |
2 × 106 |
Np, U |
NpO2+, NpO2 |
238Pu |
88.0 |
Pu, Th |
Pu3+, PuO2+, PuO2 |
239Pu |
2.4 × 104 |
Pu, Th |
Pu3+, PuO2+, PuO2 |
241Am |
432.0 |
Nd |
Am(OH)3+, AmO2 |
243Am |
7 × 103 |
Nd |
Am(OH)3+, AmO2 |
243Cm |
28.0 |
Nd |
Cm(OH)3, Cm complexes |
Metal–organic frameworks are coordination polymers composed of organic ligands (linker) and inorganic metal or cluster-metal oxide as a metal node (Fig. 1a). The coordination complex that forms between the metal node and the ligand donor atom is called a secondary building unit (SBU). The connection between the ligand and the metal may form a dote structure or a chain structure arranged in one dimension, as well as a layer shape arranged in two dimensions and three dimensions, leading to a network structure25–27 (Fig. 1b).
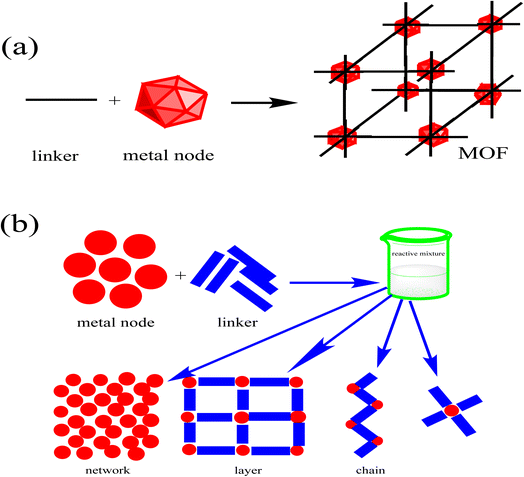 |
| Fig. 1 (a) A model of MOF fabrication. (b) Different MOF structures. | |
The shape of MOFs is affected by the molar ratio between the metal cluster or ion and the organic linker, for example, in general, a 1
:
2 molar ratio between the linker and the metal node leads to a two-dimensional structure such as in the case of the synthesis of cobalt MOFs in the presence of N-(3-pyridyl) nicotinamide ligand when four molecules of the linker are coordinated with the metal node. MOFs have potential voids and pores over their frameworks, and varying the organic linker and/or the metal node causes tuning of the pores. Also as the organic chain of the linker increases the pore size will increase.28,29 Based on the nature and the pore size of the MOFs, various potential uses have been applied such as gas separation, sensors, bio-medical applications, ion exchanger, adsorption, gas purification, and gas storage.30–35 One application of MOFs is as adsorbents due to their low density, chemical and thermal stability, and large pore size. Their insolubility in water and other aqueous media and extended surface areas, from 103 to 104 m2 g−1, enhance their applicability in the removal and separation of radionuclides and toxic metals.35,36 Consequently, these properties have allowed MOFs to surpass the traditional materials that are used for the same purpose, such as porous organic frameworks (POFs), zeolites, and carbons.
The impact of using organic solvents and solventless methods in the fabrication of MOFs on the environment, the mechanism of MOFs toward radionuclides, regeneration and reusability of MOFs toward radionuclides, behaviors against strong radiation conditions, applications such as catalysis and adsorption, and the separation of MOFs have been discussed in many reviews.37–40 Hot topics such as removing pollution, including dyes,41,42 emerging contaminants,43 and the removal of organic compounds,42,44 have also been overviewed. MOFs and their compounds have recently been shown to be remarkable solid porous materials that trap toxic and radioactive metal ions.45–48 This review aims to provide an overview of the most recent advances in the applications of MOFs as absorbents for water purification. To do this, we critically provide some focused examples and comparisons to evaluate the removal properties, conditions and mechanisms starting from precipitation methods and ending with MOFs including different synthetic methods, kinetic and thermodynamic stabilities, MOFs mechanism for removal of radionuclides, and metal ions, and the evaluation of the different MOF materials for the removal of various radionuclides.
Radioactive water decontamination removal techniques
The preconcentration of waste elements before the separation process is essential; these metal ion concentrations are deficient. Therefore, it is crucial to preconcentrate these ions to allow measurement and detection with high accuracy, a low detection limit, and sensitivity. Various separation methods are used for this target49 (Fig. 2), such as membrane filtration, electrolysis, ion exchange, co-precipitation, flotation, and some other methods50,51 that will be discussed in detail in the following sections.
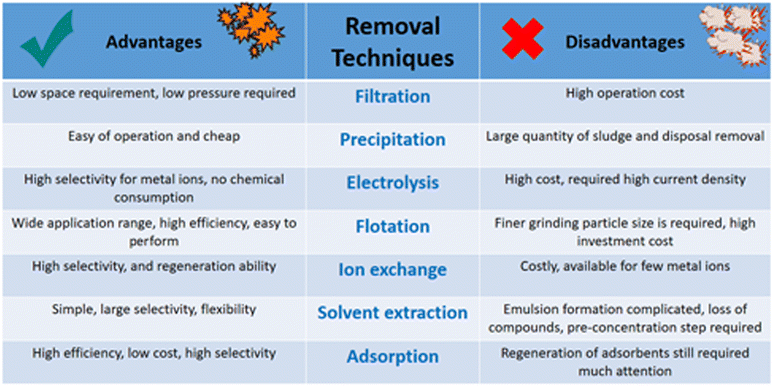 |
| Fig. 2 Techniques for the removal of toxic and radioactive elements. | |
Precipitation
Precipitation is the process of separating a specific ion from a solution based on the ionic equilibrium changes of the target ions in that solution; the soluble ion is converted into an insoluble form by nucleation and crystal growth and separated by separation techniques such as filtration. Precipitation usually separates heavy metal ions and hardness from water.52–54
Filtration
Wastewater treatment relies heavily on filtration to eliminate physical impurities from the water. This process involves passing the water through a bed of granular media, which removes suspended solids such as microorganisms, turbidity, particulates, and color. These impurities can be present in the water or produced during pre-treatment. The ultimate goal of filtration is to produce a clear and clean effluent that meets the necessary quality standards for safe discharge or reuse. Effective filtration is crucial to ensure the success of wastewater treatment and protect the environment from harmful contaminants.55 Several filtration techniques are commonly employed in wastewater treatment, including gravity filtration, vacuum filtration, centrifugal filtration, hot filtration, cold filtration, granular media filtration, and mechanical filtration. Each technique relies on different mechanisms to remove suspended solids from the water and produce a clear effluent. The choice of filtration technique depends on various factors, such as the nature of the wastewater, the required level of treatment, and the available resources. Understanding the advantages and limitations of each filtration technique is essential to select the most appropriate method for a particular application.56–60 Among these techniques, a filter membrane is used to remove soluble ions or molecules from solutions, based on the passing of these ions or molecules through a semi-permeable membrane under applied pressure. The filter membrane has a wide range of separation methods, such as reverse osmosis (RO), filtration, and ultra-filtration processes. It is used for the separation of some organic materials,61,62 and some heavy metals.63,64
Ion exchange
Ion exchange is a separation technique that can be used to separate anions and cations from solution using an anion exchanger with large porosity to allow the diffusion of ions to replace the exchanger ions, and these replaced ions will diffuse into the solution and be used for the removal of some organic molecules62 and some heavy metals.65–68
Electrolysis
The electrolysis separation technique depends on an applied electrical current to separate elements and components from each other and is considered highly efficient. It is used for the separation of gases from wastewater and isolating metals from their ores.69,70
Solvent extraction
Solvent extraction is considered the ideal separation technique for separating lower-concentration contaminants by distribution between two immiscible layers; it is a simple and fast separation technique. The substance is distributed from one layer to another in liquid–liquid extraction. Solvent extraction is utilized to separate radioactive materials, as well as liquid–solid extraction and other special techniques.71–73
Adsorption
In 1881, Kayser was the first to introduce the term adsorption to describe gas condensation on surfaces.74,75 Adsorption occurs on surfaces via the accumulation of substances called adsorbates on the surface of another substance called the adsorbent. This leads to an increased concentration of a specific substance at one interface as compared to another. The adsorption phenomenon is classified as either physical adsorption, called physisorption, or a chemical process called chemisorption. Chemisorption is a chemical interaction between the adsorbate on the surface of the adsorbent by electron sharing or exchanging. As a result, a new strong chemical bond is formed between the adsorbate and the adsorbent. Thus, chemisorption is a slow and irreversible adsorption phenomenon.76 Physisorption is a physical interaction between the adsorbate and adsorbent that involves a variety of interactions such as dipole–dipole forces, van der Waals forces, hydrogen bonds, and polarity. Physisorption is a fast and reversible adsorption phenomenon so the bonds are easily formed and broken.77
Flotation
Flotation is the process of separating and concentrating one type of particle from another through selective etching on liquid–liquid interfaces. Electrolytic flotation and dissolved air flotation are the best examples for water treatment.78 The flotation process has many advantages, such as removing heavy metals since it removes cadmium, copper, zinc, and chromium from wastewater using the ion flotation method. Ion flotation has many advantages such as low energy consumption, fast operation, availability for low concentrations, small space requirement, and low operating costs.79
Decontamination of radioactive elements from water resources using different adsorbents
Many types of adsorbents have been used for the removal of contaminants from waste, such as coal, wood-activated carbon, bone chars, resins, zeolites, and clays.80–89 Adsorption takes place when the adsorbate (solid) has a significant affinity for the adsorbent surface as compared to its solution. The chemical properties of the adsorbent and its compositional properties are essential in determining the nature of the interaction between the adsorbate and the adsorbent surface. Meanwhile, the presence of pores on the adsorbent surface causes the enhancement of the adsorption process.90,91
Organic adsorbents
Organic adsorbents are used for various applications such as purification, drying, separation, catalysis, and controlling pollutants. These organic sorbents, such as activated carbon, chitosan, and other organic adsorbents, consist of aromatic sheets condensed over each other, forming a hydrophobic character. Thus, when a nonpolar-organic material is exposed to its surface, it causes an interaction via van der Waals forces. In contrast, it is not suitable for an inorganic material except in the presence of some functional groups. Inorganic functional groups such as carbonyl, carboxyl, and hydroxyl enhance their interaction with the inorganic materials, which may be polar or charged materials like metal ions.91,92
Activated carbon
Activated carbon is a commonly used adsorbent in wastewater treatment.89,93–95 The popular common sources for obtaining activated carbons are coal, wood, and coke, in addition to nutshells.96,97 The activation of these materials is divided into two types: physical and chemical activation.86 The chemical activation process involves soaking the inactivated carbonized material in a strong dehydrating agent, usually phosphoric acid, then heating it at a high temperature of about 700–900 °C. After activation, the surface of the activated carbon requires some modifications to increase the chances for adsorption and the activated carbon adsorption properties;98–102 the modification processes increase the hydrophilic characteristics. The modification process may be a gas phase or liquid phase oxidation modification. In the case of gas modification, the surface of the activated carbon is exposed to hot oxygen gas at about 425 °C, which causes the formation of non-organic functional groups such as carbonyl and hydroxyl groups.98,99 In the case of liquid modification, it involves the oxidation of the activated carbon surface using inorganic acids like nitric and phosphoric acids at high temperatures so that carboxylic groups are formed.98–100 These modifications improve the hydrophobic characteristics, increasing the adsorption ability. Granular activated carbon, fibrous activated carbon, powdered activated carbon, and clothed activated carbon are the four types of activated carbon that vary in size and shape,103 such as mercury,104 copper,105 lead,106 chromium,103,107–111 cadmium,112,113 zinc,114 lithium,115 and uranium.116–118
Chitosan
Chitosan is an organic adsorbent produced from the N-deacetylation of chitin. Chitin exists in the exoskeleton of crustaceans and shellfish. It is a polysaccharide and the most naturally abundant biopolymer after cellulose.119 Chitosan contains a higher nitrogen content, so it is a suitable metal adsorbent and was used for the removal of cadmium,120 mercury,121 chromium,122 copper,123 vanadium,124 and platinum.103 Moreover, it is used for agricultural applications such as plant defense, increasing the yield of crops, and other different applications.125
Polyurethane foam
Polyurethane is an organic polymer composed of urethane monomers; it is widely used for producing soft car seats, mats, and toys and, additionally, in medicine for manufacturing prostheses. In 1970, polyurethane was first used for the removal of metal ions126,127 and then for the removal of organic materials.128,129 Polyurethane foam has two types; loaded and unloaded. Unloaded polyurethane foam has a low adsorption capacity for anions.127,130 It is used for the removal of metal ions; the adsorption of metal ions on unloaded polyurethane foam is carried out after the formation of a complex with organic or inorganic ligands, such as the thiocyanate ligand. Unloaded polyurethane is used for the removal of many metal ions such as zinc and molybdenum,131 cadmium,132 cobalt,133 iron,132 tungsten and technetium,134 osmium,135 lead,136 platinum,137 ruthenium,138 zirconium,139 and hafnium,139 in the presence of thiocyanate ligands. Whereas, the loaded polyurethane foam can contain and collect a large amount of organic and inorganic compounds-reagents, which causes modification and enhances the adsorption process. This can be achieved by using oxygenated or nitrogen-containing organic chelating reagents.126 These reagents and compounds are fixed on polyurethane foam by physical or chemical methods. During the synthesis of polyurethane foams, some compounds can be loaded; this is called chemical loading. The chemical immobilization of compounds on polyurethane foam is exhaustive so physical immobilization is most commonly used.126 Loaded polyurethane foam has a wider field of application than unloaded polyurethane foam. It is used for the removal of many heavy metals such as cadmium, copper, nickel, cobalt, zinc, manganese, lead,131 thorium,140 and uranium.141
Coal
Activated carbon, produced from coal, is a highly versatile material with several beneficial properties. It has a high specific surface area, a well-developed internal pore structure, and numerous functional groups on its surface. Additionally, activated carbon has a low density, good mechanical strength, and excellent chemical and thermal stability. These properties, along with its potential for large-scale production and the ability to change its properties using specific solvents, make activated carbon a desirable choice for a wide range of applications. Recently, activated carbon has garnered significant attention in water supply and sewage systems due to its favourable adsorption properties, economic efficiency, regenerative capacity, large quantity, and environmentally sustainable nature.142 Coal is well-known for its advantageous physical and chemical properties, which make it an effective adsorbent for removing dyes and heavy metals from polluted solutions; for example, it can effectively remove cadmium143 and mercury144 from such solutions.
Inorganic adsorbents
Inorganic adsorbents such as zeolites, metal oxides, activated alumina, bentonite, and silica gel have attracted great interest in separation methods due to their properties such as thermal stability, radiation stability, and difficulty to be reduced or oxidized. Among these inorganic adsorbents is activated alumina. Activated alumina is produced from the de-hydroxylation of aluminum hydroxide, which produces high porosity and a large surface area, making it available to be utilized as a catalyst, desiccant, filter, and adsorbent.145 Thus, activated alumina is used for the removal of some heavy metals such as chromium,145 arsenic,146 antimony,147 copper,148 cadmium, and lead.149
Another example is bentonite, which is an adsorbent consisting of montmorillonite-aluminum phyllosilicate clay and some other components such as calcium aluminosilicate and sodium aluminosilicate, which are called calcium and sodium feldspar.150 Bentonite can be divided into two types based on the exchangeable cations Ca and Na, which are known as sodium or calcium bentonite.151 The main structure of bentonite consists of three sheets: two of them are tetrahedral silica, and the other is alumina, which is octahedral and lies in the centre between the two silica tetrahedral sheets.152 Sodium bentonite has considerable swelling ability as compared to calcium bentonite, which has no capacity for swelling and is dispersed in water, forming colloidal solutions.150 Bentonite layers are attached through electrochemical forces and the surface acquires a negative charge, making its face an anion that is balanced by cations. The dominant cations are calcium and sodium, called calcium and sodium bentonite, where not only Ca and Na but also other alkaline earth metal cations can balance the negative charge of the surface.150 Bentonite has great commercial value due to its applicability in various industrial applications such as paper making, drilling fluid, paints, pharmaceutical products, dyes, water treatment,150 and the separation of different heavy metals such as lead, nickel, chrome, and copper.153
Organic and non-organic hybrid adsorbents
Metal–organic frameworks (MOFs) are hybrid materials combining organic linkers with metal ions or clusters. This results in materials that possess the advantageous properties of both inorganic and organic components, resulting in unique and desirable properties.154,155 MOFs, also called porous coordination polymers (PCPs),156–158 are a class of microporous crystalline materials.159–161 They are also new regulable and modifiable porous materials, combining coordination chemistry and material science.162,163 These properties allow MOFs to be promising materials for removing toxic and radioactive metal ions in nuclear waste.164–166 Recently, MOFs have been reported for the removal of toxic and radioactive elements from the environment to manage pollution.167–170
MOFs: an overview and fabrication methods
MOFs, part of the crystal porous materials family, are made up of metal assemblies – such as metal ions or groups – and linkers linked together by coordination bonds.167,168 It is well known that MOFs are among the most extensively researched materials in the twenty-first century due to their structure tailorability, high crystallinity and controlled porosity.26,169,170 Metal ions that are widely used to fabricate MOF include Fe3+, Cu2+, Ca2+, Al3+, Mg2+, Zn2+, Cd2+, Co2+, Zr2+, Ln3+ and Ti3+, which can have different coordination geometries such as diagonal, pyramidal, square, tetrahedral and octahedral.171–182 Metal ions such as Co2+ and Cd2+ or Eu3+ and Ag+ are known to be toxic or expensive but are still crucial for studying their participation in MOF fabrication and applications.183–187 Linkers such as melamine, carboxylates, 4,4′-biphenyldicarboxylic acids, 1,4-naphthalene dicarboxylic acids, and aliphatic polycarboxylates are regarded as the main components to synthesize MOFs.188–193 The reversibility of coordination bonds between metal nodes and organic linkers is critical for forming well-organized MOF structures. Because the metal nodes can easily adjust their coordination connections, highly ordered MOF architectures can be created.194,195 One of the commonly used techniques for the fabrication of MOF is the bottom-up method,196 which allows direct reaction between metal ions and organic linkers under specific reaction conditions to provide the targeted MOF.197 In general, MOFs can be synthesized using a variety of methods, including non-aqueous or aqueous direct synthesis and mixed non-aqueous or aqueous synthesis. Solvothermal growth, hydrothermal synthesis, chemical–mechanical synthesis, layer-by-layer assembly, ultrasonic synthesis, electrochemical synthesis, microwave-assisted synthesis, and high throughput synthesis are all standard synthesis techniques. The reversible nature of coordination bonds between metal nodes and organic linkers is critical in the formation of well-ordered MOF structures.194,197 A more detailed description of the linkers, metals, modulators and synthesis of MOFs is given below. Greater permanent porosity than any other class of porous materials is a beneficial property of MOFs with their ordered porous structures. This renders MOFs promising sorbent materials with remarkably high absorption efficiency for toxic and radioactive elements.187,198–206
Numerous organic linkers are used in MOFs, such as the following. (i) Melamine: Adekoya et al. synthesized a graphitic carbon nitride modified by copper and titanium nitrate, g-C3N4 through the calcination of melamine at 550 °C for 3 h, then copper and titanium were impregnated by wet impregnation. Cu–Ti-gC3N4 was used for the reduction of carbon dioxide into methanol and formic acid.188 Yang et al. constructed a melamine-based MOF called MIL-125/Ag/g-C3N4 (Fig. 3a), which was used as a photocatalyst for the oxidation of alcohols and the reduction of nitro compounds.207 Yu et al. prepared AgCl–Ag/g-C3N4 (Fig. 3b), which was used for the photo-degradation of methyl orange.208 Yao et al. synthesized Ag Pb-graphitic carbon nitride, which was used as a photocatalyst for the degradation of formic acid (Fig. 3c). Here, melamine was calcined at 823 K for 4 h and silver and lead were supported on the calcined carbon nitride via stirring for 24 h.209 Li et al. synthesized four new coordination polymers based on melamine as a linker and four lanthanide salts, Sm, Gd, Er, and Nd nitrates, using the hydrothermal method.210 Baraka et al. synthesized a silver melamine-based MOF in the presence of acetic acid via the hydrothermal method (Fig. 3d). The MOF synthesized by Baraka was used for the selective removal of methyl orange dye.211
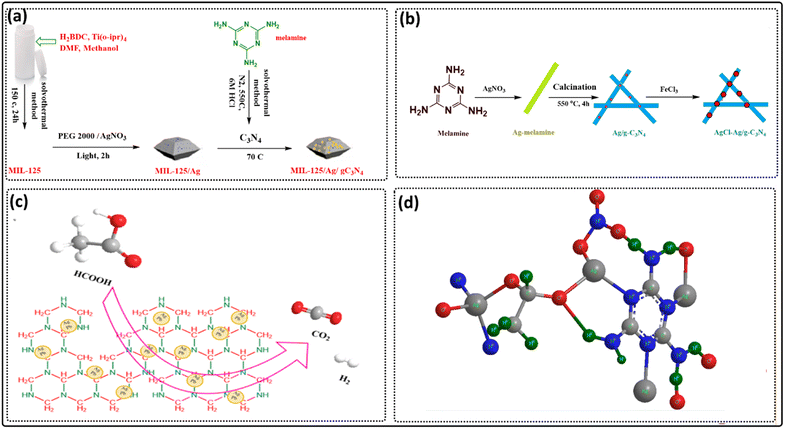 |
| Fig. 3 (a) An illustration of the preparation of MIL-125/Ag/g-C3N4 [adapted from ref. 207 with permission from Elsevier B.V., copyright 2016]. (b) Schematic illustration of the synthesis of AgCl–Ag/g-C3N4 [adapted from ref. 208 with permission from Elsevier B.V., copyright 2019]. (c) High efficient release of hydrogen from formic acid using AgPd/g-C3N4 [adapted from ref. 209 with permission from Elsevier B.V., copyright 2017]. (d) Silver melamine-based MOF structure in the presence of acetic acid [adapted from ref. 211 with permission from Elsevier Inc., copyright 2019]. | |
(ii) Terephthalic acid: Li et al. synthesized two coordination silver-based polymers using terephthalic acid as a linker and 1,6-(2-methylbenzimidazolyl)hexane via sonication and a hydrothermal method. The constructed compounds were used for the degradation of methylene blue with high efficiency.189 Ehrenmann et al. fabricated the MIL-101 MOF based on terephthalic acid as a linker, and used it for heat transformation applications due to its high stability.212 Scholz et al. prepared a strontium terephthalate MOF (Fig. 4a) using terephthalic acid by milling the powdered reactants for an hour.213
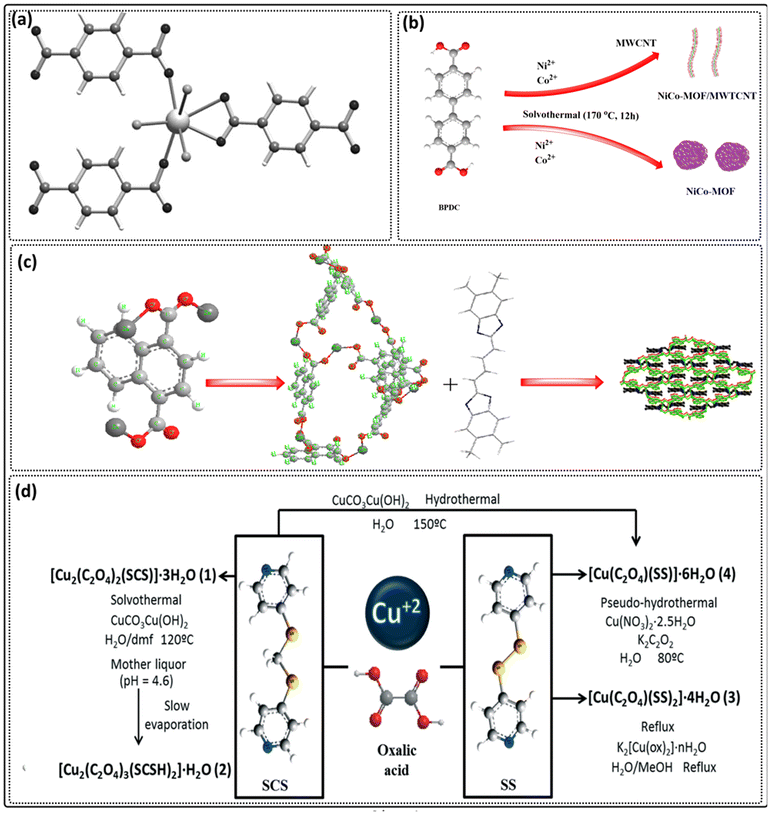 |
| Fig. 4 (a) A strontium terephthalate MOF structure [adapted from ref. 213 with permission from WILEY-VCH Verlag, copyright 2013]. (b) NiCo-MOF using 4,4′-biphenyldicarboxylic acid [adapted from ref. 190 with permission from Elsevier Inc, copyright 2019]. (c) Zn-MOFs based on 1,4-naphthalenedicarboxylic acid [adapted from ref. 191 with permission from Elsevier Inc, copyright 2019]. (d) Four MOFs using oxalic acid as a linker [adapted from ref. 214 with permission from Royal Society of Chemistry, copyright 2013]. | |
(iii) 4,4′-Biphenyldicarboxylic acid: Wang et al. synthesized NiCo-MOF using 4,4′-biphenyldicarboxylic acid as a ligand, via the solvothermal method, which was then used as an electrode material (Fig. 4b).190 (iv) 1,4-Naphthalenedicarboxylic acid: Yang et al. synthesized Zn-MOFs based on 1,4-naphthalenedicarboxylic acid via the hydrothermal method (Fig. 4c). These MOFs were used for the detection of dichromate ions and glyoxal.191 (v) Aliphatic polycarboxylates such as oxalic acid:192,193 Carballo et al. synthesized four MOFs (Fig. 4d) using oxalic acid as a linker using the hydrothermal method,214 with succinic acid215 and adipic acid (Fig. 5a)216,217 as ligands.
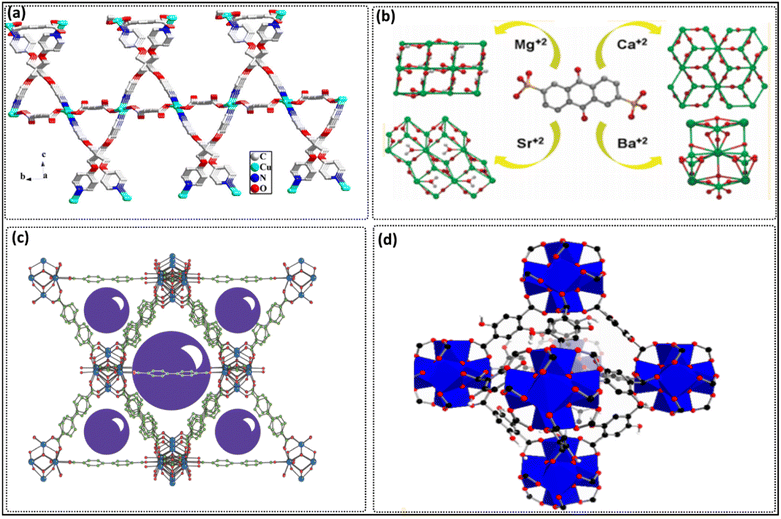 |
| Fig. 5 (a) Adipic acid-Cu MOF [adapted from ref. 216 with permission from Elsevier B.V., copyright 2012], (b) Ca, Sr, Mg and Ba ions MOFs with anthraquinone-2,6-disulfonate [adapted from ref. 225 with permission from American Chemical Society, copyright 2011], (c) structure of UiO-67 showing a single octahedral cage [adapted from ref. 229 with permission from The Royal Society of Chemistry, copyright 2013], (d) structure of UiO-66 [adapted from ref. 231 with permission from American Chemical Society, copyright 2017]. | |
To create MOFs, metal cations, including transition metals,218 rare earths,219,220 representative elements,221,222 and actinide metals223 can be utilized. Organic linkers can combine with metal cations, including alkaline earth metals such as Mg, Ca, Sr, and Ba, to form MOFs. Although MOFs based on these alkaline earth metals have been synthesized, they have not been as extensively studied as MOFs based on transition metals or lanthanides. MOFs containing alkaline earth metals, such as those prepared by Platero-Prats et al. who used Mg, Sr, Ba, and Ca as metal components (Fig. 5b)225 with anthraquinone-2,6-disulfonate ligands, showed thermal stability at high temperatures up to 500 °C.224–226 The unique properties of alkaline earth MOFs, such as their low toxicity, lightweight nature, air stability, and low cost, make them an appealing research subject.227 The presence of alkaline earth metals in MOFs can cause the formation of empty positions in the coordination sphere, resulting in the formation of Lewis acid sites.228
Moreover, modulating agents are usually added to the MOF reaction mixture and are required for controlling the properties of materials (e.g., morphological and porous features), such as HCl, acetic acid, and formic acid. Katz et al. synthesized UiO-67 (Fig. 5c) and UiO-66 MOFs (Fig. 5d) using hydrochloric acid as a modulator to condition the solvent used in synthesis (DMF), neutralizing the basic character of the solvent and/or enhancing the formation of the cluster structure of the required MOFs.229–231 HF was also used for modulating the crystal size and morphology of the prepared MOFs. Yang et al. used hydrofluoric acid as a modulator to study its effect on the crystallinity and morphology of the zirconium metal–organic framework UiO-66. They found a strong effect on the crystallinity and the crystal size of UiO-66 MOFs.232 Atzori et al. studied the effects of benzoic acid as a monocarboxylic organic acid modulator on the synthesis of UiO-66. They proved that benzoic acid used for modulation enhanced the reactivity of the MOFs toward their required application (adsorption, photocatalyst, and sensor). Meanwhile, it increased the MOFs' surface porosity because it allowed defects in the MOFs cluster structure.233 Schaate et al. used acetic and benzoic acids as modulators for increasing the crystal size and crystallinity of UiO-MOFs.234 The presence of modulators during fabrication causes decreases in the reaction rate, leading to proper crystal growth, which improves the crystalline property and repairs the lattice defects. On the other hand, adding an excess amount of modulator causes lattice defects due to the replacement of ligands by modulators in the lattice structure235 Bai et al. found that replacing terephthalates in UiO-66 by trifluoroacetate caused lattice defects and, therefore, the high catalytic activity of MOF.235
The methods used to create long afterglow materials significantly impact the microstructure features and defect distribution within the material.236 For the synthesis of MOFs, two directions can be taken related to solvent: one of these is solvent-based synthesis, and the second is a solvent-free synthesis, which is the conventional method.237 To achieve the desired compositions for long-lasting glow materials, high sintering temperatures are frequently used. However, this can result in agglomerated, irregularly shaped products. Chemical synthesis methods, such as the sol–gel method, which involves liquid phase reactions, can be used to overcome this challenge.238 On the other hand, solvothermal,239 hydrothermal,240 coprecipitation,241 combustion,242 sintering,243 solid phase,244 sonochemical,245,246 mechanochemical,247,248 microfluidic,249 and electrochemical methods,250 can lead to the formation of different morphologies and structures of MOFs.
Solvothermal and hydrothermal methods
These two synthesis methods involve dissolving specific amounts of metal salts and ligands in water or an organic solvent, and then the precursor is transferred to a stainless-steel Teflon reactor and heated at a specific temperature for a certain time. These two methods lasted from a few hours to days with a temperature range of 297–473 K. Within this time, high temperature and pressure in the reactor are generated and result in the formation and enhancement of MOFs with good morphology.251 Varying the synthesis time, temperature, molar concentration ratios of metal salts and ligands, and solvent volume help to control and/or modify the morphology and growth of the prepared MOF.
The solvothermal method is based on dissolving the ligand and salts in an organic solvent such as amines, alcohols, or basic organic solvents.252 Yaghi et al. fabricated ZIF-MOFs using (DMF) N,N-dimethylformamide and (DEF) N,N-diethylformamide.253 Alcohols are the alternative solvents for amides, and they are extensively used in MOFs synthesis due to their volatility and low price. Liu et al. synthesized Zn-MOF using methanol to dissolve the metal salt, Zn(NO3)2·6H2O, with 2-methylimidazole.254 Due to the high cost of treatment of organic solvents for pollution reduction, recent methods of synthesis using pure aqueous and mixed solutions have been reported. Pan et al. fabricated Zn-MOFs in a water and 2-methyl imidazole mixture.255 Also, the hydrothermal method is shorter than the solvothermal method in terms of fabrication time.256
Sonochemical method
The sonochemical method yields uniform nucleation and crystallization in a short time so it is more efficient and economical. The sonochemical method reduces the fabrication time from days to a few hours.257 In addition, smaller and more uniform particle sizes of MOFs are produced from sonochemical methods than from other traditional methods as reported by Seoane et al.258
Mechanochemical synthesis
The mechanochemical method is regarded as a green chemistry synthesis method, which shows quantitative output and large-scale production without using solvents and high temperatures. Adams et al.259 mechanochemically fabricated a Zn-imidazole-MOF using imidazole and ZnCl2 through two steps using KOH. The synthesis of ZIFs-MOFs at room temperature using NH4+ was also reported.260 Tanaka et al. synthesized Zn-imidazole-MOFs without using solvents or any reactants other than ZnO and 2-methylimidazole.261
Other fabrication methods
Microfluidic synthesis is synthesis using the microchannels of a micromixer for mixing reactants. It is favorable for controlling reaction parameters such as time, temperature, and pressure and avoiding variations between prepared batches.262 Faustini et al. fabricated ZIF-8 MOFs using the microfluidic method via a tubular reactor.262 Also, ZIF-8 was fabricated by Yamamoto et al. using a t-type micromixer.263 Dry-gel methods attract significant attention in MOFs synthesis.264 Lee et al. found that MOFs prepared by dry-gel produced an excellent MOF yield and smaller particle size than those produced by solvothermal, microwave, mechanochemical and microfluidic methods.265 Microwave heating has several advantages over traditional synthesis methods, including rapid heating, uniform heating, high efficiency, and ease of control,266 resulting in the most stable MOF.
The impact of using organic solvent and solventless fabrication of MOFs on the environment
MOF chemistry has several limitations that need to be addressed further, including issues with stability, toxicity, efficacy, safety, high energy consumption, and biodegradability.267,268 To address these challenges, incorporating the twelve principles of green chemistry recommended by Paul Anastas and John Warner, as outlined by the Environmental Protection Agency, can be an effective strategy for MOF synthesis.269 The focus on developing green MOFs gained traction in the latter part of the decade, and researchers such as Kumar et al. investigated their potential for creating sustainable materials with minimal environmental impact. To achieve this goal, various factors in the design of MOFs must be considered, such as the use of green solvents, energy-efficient processes, eco-friendly linkers, low-toxicity metal salts, less hazardous byproducts, biodegradable products, and green applications. These strategies are critical for the green chemistry of MOF design.269 To create a safer coordination framework, it is critical to carefully select raw materials that are compatible with biomass, use safer solvents, and employ energy-efficient processes that preserve the material's unique properties, structure, and crystallinity. Significant progress has been made in developing low-impact MOF synthesis, emphasizing the importance of continued progress in this field.270
Solvent-based synthesis
The solvents used in MOF synthesis are necessary because they influence the creation of controlled environments. Solvents can act as structural guides or metal ion coordinators, and thus play a vital role in the formation of MOFs.271 The MOF's final crystal lattice template is heavily influenced by the solvent used.271 Conventional studies on MOF manufacturing methods tend to adopt N,N-dimethylformamide (DEF), and dimethylformamide (DMF).272,273 These solvents are attractive for increasing acidity. The acidic and basic properties of the molecules of organic solvents have a profound effect on the interpretation of solute–solvent reactions.274 The slow evaporation rate and high boiling points of these solvents provide an extended period of reaction media availability. Nonetheless, the utilization of such solvents during heating or burning can produce a considerable quantity of hazardous amines.275
The toxicity of MOFs is attributed mainly to the use of solvents.276 To ensure process safety and minimize environmental impact, finding alternatives to traditional solvents is crucial. The use of green solvents can help to create a safer environment for chemicals, but the economic feasibility of such solvents must also be taken into account. The environmental impact of solvents can be evaluated based on factors such as their effect on human health, impact on natural resources, ecosystems, and potential for renewable resources. Disposing of solvents that can be recycled or reused can help reduce the risk and toxicity associated with their use.277,278
Alternatives such as methyl lactate or ethyl, dimethyl sulfoxide (DMSO), ionic liquids, and water can be used to avoid environmental and harmful solvent impacts.279,280 Glycerol products (such as triacetin),281 and lactone-based solvents, including c-butyrolactone and valerolactone, are additional alternatives to conventional solvents.282 We have summarized the most common solvents used for the fabrication of metal–organic frameworks in Table 2.
Table 2 Examples of the most common solvents used for the fabrication of metal–organic frameworks
No. |
MOF |
Solvent |
Temp. |
Time |
Application |
Ref. |
Water |
ZIF-93 |
H2O |
RT |
18 h |
CO2 adsorption |
283 |
MOF-74 (Ni) |
H2O |
160 °C |
1 h |
— |
284 |
MOF-303 (Al) |
H2O |
100 °C |
24 h |
Production of water from desert air |
285 |
Al-MIL-53 |
HTW |
250 °C |
10 min |
— |
286 |
MIL160(Al) |
H2O |
60 °C |
24 h |
Energy-reallocation systems |
287 |
Co-MOF |
H2O |
160 °C |
72 h |
Biodiesel |
288 |
Supercritical carbon dioxide |
Pt@MIL-101(Cr) |
scCO2 |
220 °C |
10 h |
Catalyst |
289 |
Cu-MOF (1D) |
scCO2 |
60 °C |
24 h |
— |
290 |
ZIF-8 |
CO2 |
35 °C |
10 h |
CO2 adsorption |
291 |
ZIF-8 |
scCO2 |
65 °C |
2 h |
— |
292 |
Cu3(BTC)2 |
scCO2 |
60 °C |
24 h |
Catalyst |
293 |
HKUST-1 |
scCO2 |
40 °C |
1 h |
— |
294 |
Ionic liquid |
UiO-66 (Zr-MOF) |
1-Octyl-3-methylimidazolium chloride |
RT |
1 h |
— |
295 |
HKUST-1 |
Cholinium ionic liquid |
RT |
30 min |
Adsorption kinetics |
296 |
Zn-MOF IL-1-propyl-3-methylimidazolium bromide |
Zn-MOF IL-1-propyl-3-methylimidazolium bromide |
160 °C |
120 h |
— |
297 |
Polyoxometalate MOF (Cu and Zn) |
([bmim]Br) |
170 °C |
120 h |
— |
297 |
La-MOFs |
1-Butyl-3-methylimidazolium hexafluorophosphate |
RT |
24 h |
— |
298 |
Zn, Cu and Fe MOF |
([emim]BF4) |
65 °C |
10 h |
— |
299 |
Water
Out of all the solvents, water is the most advantageous due to its abundance, affordability, and ability to facilitate the purification and recycling of artificial substances.270 Water is particularly well-suited for the development of scalable, sustainable, and water-based alternatives to MOFs.283,300 Organic solvents are not ideal for industrial-scale use as they require processing in a controlled and non-flammable environment. In contrast, water-based synthesis is a safer, more affordable, and more straightforward method of processing synthetic materials.284 Recent research on MOF synthesis, particularly for MILs and zeolite imidazolate (ZIF) frameworks, has emphasized the use of water at ambient temperatures and atmospheric pressure.301
The use of aqueous media for MOF synthesis has some limitations, including reduced final product stability, loss of crystallinity, and potential phase transitions. These limitations are often attributed to the interfacial interactions between water molecules and the hydrophilic parts of the MOF.302,303 Conveniently, the high specific heat and latent heat of the water will cause a high cost of evaporating energy. Due to their insolubility, the synthesis of coordination compounds in water is also difficult.304 Most organic salts and seals overcome these limitations and will require the following.
• The use of hydrophobic organic moieties (such as alkoxy acids and silicone polymers) and modifiers (such as polyvinylpyrrolidone (PVP) and formic acid).
• Understanding the detailed binding properties of MOFs, such as those associated with fluorination, N bonding, and chiral ligands, as well as the use of specific metal salts (e.g. oxides and sulfates), can aid in the synthesis of MOFs with desired properties.305–308
Water as a solvent has resulted in the development of novel MOF structural archetypes.309 Numerous novel MOFs have been manufactured since then, including MOF-74 (Zn) (Zn),304 CaU-22 (Zr),310 and MIL-91 (Ti).311 Water use is also perfect especially when making water-sensitive MOFs containing carboxylic acids, such as Cu3 (BTC)2 and Mg-MOF-74 (ref. 312). Due to the stability issue of MOFs in aqueous media, these MOFs can reduce crystallinity, phase transition, and structural decomposition.303 However, UiO66 (carboxylate containing MOF) has excellent water stability, which can be attributed to many chemical and steric factors.312 The small pore size of UiO-66 confirms that metal carboxylate sites can be used for a single water molecule. Preliminary research on MOF synthesis is based on a binary water/ethanol solvent to reduce the harmful effects of water.313 In these binary solvent systems, a wide range of reaction conditions lead to the formation of toxic by-products. Comprehensive research work focusing on sustainability focuses on limiting the formation of harmful pollutants. For example, it has been proven that the reagent Cu (OH)2 is completely converted to Cu3 (BTC)2 in an aqueous solution of ethanol at room temperature.314 Using a non-wasteful manufacturing method, it is possible to improve the performance of materials and prepare various other subcategories of zeolitic imidazolate frameworks (ZIFs). One example is the production of stable ZIF-93, which can be synthesized in ammonia based on the water route.283 ZIF-93 has been deemed an attractive alternative to various ecologically sound programmes, such as eliminating carbon dioxide from the environment. Jian et al.315 have reported a series of fine syntheses of ZIF-8 in water based on salts of metals (e.g., Zn (OAc)2 or ZnSO4) without the addition of regulators. Several parameters (such as water content, metal salt, and its ratio to ligand) were found to significantly impact the morphology of ZIF-8 in their study. Environmentally friendly X-MIL-53 (Al) materials have also been synthesized.304 MIL-53 has little or no unreacted connection salt in the pores, which can provide high-quality products. Zirconium-based frames (UiO type) are being reported for their new characteristics (such as stability and versatility). However, more sustainable synthetic methods are needed to increase the production of materials effectively. Chen et al.316 reported that the successful crystallization of Zr-based metal–organic frameworks (MOFs) such as UiO-66 and NU-901 was achieved at room temperature through the hydration process, facilitated by the addition of modulating agents such as trifluoroacetic acid and acetic acid.
This promising type of MOF has caught the attention of researchers as a potential replacement for high-quality hazardous solvents. The industry welcomes the use of solvents with less environmental impact. Additionally, eco-friendly MOFs could open up opportunities for effectively adsorbing toxic chemicals in both aqueous and gaseous systems. The hydrothermal synthesis of coordination scaffolds is expected to facilitate a transition to commercial production at high rates while simultaneously reducing the environmental impact and production costs.
Supercritical liquids
Supercritical liquids are another interesting option for environmental interaction media. Supercritical carbon (scCO2) provides high-potential carbon dioxide and green water solvents for MOF synthesis. Various MOFs can be produced by green synthesis technologies using supercritical liquids.317 Green solvents with adjustable properties, such as polarity, viscosity, surface tension, and phase, can be synthesized by controlling the conditions of the synthesis process. These adjustable properties make these solvents suitable for recycling, eliminating the need for distillation and reducing energy consumption.318,319 When the temperature and pressure exceed a critical point, water's polarity and hydrogen bonding properties undergo significant changes. High-temperature water (HTW) exhibits similar relative dielectric constant, ionization constant, and density as nonpolar solvents, which makes it capable of dissolving organic compounds (such as linkers) under normal conditions. However, the operating conditions required to achieve these properties are extremely high.
While it is true that the dissolution of compounds can be enhanced by increasing temperature and pressure, high-temperature water (HTW) and supercritical water solvents may not always be feasible in MOF synthesis due to certain limitations. To address these issues, researchers have studied the viability of water at 300 °C as a green solvent for the synthesis of de-solvated microporous Zn(II)-carboxylate MOFs.320 HTW may enhance MOF manufacturing for industrial uses by allowing reuse without cleaning, whereas organic solvents tend to degrade at high temperatures. Carbon dioxide is a non-flammable, low-impact, and virtually inexhaustible gas due to its low critical temperature (31.1 °C) and moderate pressure (73.83 bar). Liquid scCO2 and CO2 expanded liquid (CXL) are receiving much attention as solvents. Changing the operating temperature and pressure can change the consistency, density, and phase of scCO2. The various chemical properties of scCO2 aid in the simple dissolution of water-insoluble organic compounds.321,322 The above findings indicate that scCO2 holds excellent promise as a solvent for a wide range of applications, such as extraction, polymerization, biomedicine, catalytic reactions, and synthetic methods.323
Supercritical fluid was primarily used to clean pores after entrapped solvent synthesis. However, its utility in developing innovative and sustainable processes for extremely porous MOFs has recently been demonstrated.289 Reactive crystallization with scCO2 solvents has enabled the fabrication of more intricate one-dimensional (1D), two-dimensional (2D), and three-dimensional (3D) coordination structures. Utilizing scCO2 and two bipyridyl ligands, a copper coordination complex with a 1D structure was successfully developed.290 Portolés-Gil et al. reported the successful development of a copper coordination complex with a 1D structure using scCO2 and two bipyridyl ligands, and this green synthesis approach has been extended to construct a 2D MOF based on either Cu(II) or Zn(II), with the addition of a small amount of tert-butyl pyridine to improve the solubility of scCO2. Furthermore, scCO2 was employed for the active crystallization of a bio-MOF (Zn [curcumin]) composed entirely of bimolecular building blocks.324,325 The use of scCO2 in the one-pot synthesis of Zn(2-methylimidazole) (ZIF-8) has been shown to provide several advantageous properties for MOF structures, which include a highly active surface, and a reduced risk of pore collapse.291 Marret et al.292 investigated the ability of scCO2 solvents to convert the ionic precursor ZnO into ZIF-8 under mild conditions in the presence of imidazole-based linkers. This approach emphasizes gram scale availability for commercial scalability.
Ionic liquids
Ionic liquids (ILs) provide a new way to replace toxic solvents. These liquids are made up of organic or inorganic anions and cations and can withstand temperatures up to 100 °C. The IL's positively charged side chains can be ammonium/tetra phosphonium, pyridinium, or imidazolium, even though the anionic side chain could be tetrachloroaluminate, tertiary or hexafluorophosphate, or halogen.291,326 Compounds with a melting point below the boiling point of water can be classified as ionic liquid (IL) compounds, providing a promising option for sustainable and eco-friendly solvents. However, certain ILs, such as 1-butyl-3-methylimidazolium, perfluoroanions, and imidazole, are considered unsafe.327,328 Under ambient conditions, pure salts in liquid form can be held together solely by strong electrostatic discharge interactions, which can have a significant impact on the properties of ionic liquids (ILs) when used in the dissolution of charged solutes. Traditional solvents, on the other hand, are typically neutral. Because of their low vapor pressure, volatility, and flammability, ILs have recently received increased attention as green solvents.329 A vital factor to consider is the vast array of ionic combinations that can be achieved by modifying the ions, which provides a high degree of tunability. This feature makes ILs an ideal choice as “designer solvents” that can be utilized as modulators for porous structures and coordinating agents for MOF precursors.330
Many MOF structures have been synthesized and explored using ILs, such as polyoxometalate-based MOFs, and 3D ferroelectric MOFs.331 To date, in either room-temperature or isothermal conditions, MOF synthesis using IL-based compounds could be carried out. A mix between scCO2 and ILs has been submitted for the quick fabrication of MOFs at room temperature. In this combination, scCO2 can alter the viscosity of ionic liquids to be lower to enhance mass transfer at minimum temperatures and with shorter intervals.299 There have been limited studies on the use of IL/scCO2 combinations to fabricate MOFs. However, some recent research has explored the synthesis of microporous and mesoporous Co-MOFs using an IL/scCO2-based dual-functional system.332 Additionally, scCO2/imidazolium IL solvent mixtures have been utilized to synthesize various metal-based MOFs, such as those containing Zn, Cu, and Fe nodes.299
Bioderived solvents
Using biomass as a sustainable, renewable raw material for catalytic conversion into biochemicals and useable energy has gained significant attention. Biomass possesses several interesting properties, including its diversified nature, chirality, and oxygenation pattern, making it a highly favorable raw material for the production of high-value chemicals.333 Many downstream protocols have been scaled up from laboratory research to large-scale commercialization.334 In synthetic chemistry, it is currently not feasible to replace aprotic solvents like DMF and N-methyl-2-pyrrolidone (NMP) with alternative solvents.335
The use of bio-derived solvents as a potential alternative to aprotic solvents is discussed in this article, with a focus on 6,8-dioxabicyclo[3.2.1]octan-2-one (also known as Cyrene), an aprotic dipolar green solvent that can be obtained from various biomass sources such as larch trunks, bagasse, and poplar wood. The most productive biomass source for synthesizing levoglucosenone (OCT)/Cyrene (2H-OCT) is cellulose. The production of 2H-OCT involves two steps: first, the solid biomass is converted to LGO, and then LGO is reduced to 2H-LGO through a hydrogenation protocol. It is worth noting that the conversion of solid biomass into neutral energy only releases water into the environment.336,337 Pyrolysis is a common method for converting cellulose into LGO and then to Cyrene. However, a novel continuous approach to transforming cellulosic biomass directly into 2H-LGO without pretreatment has been developed.335 The conversion process involves using a Pd/Al2O3 catalyst and an IL on porous char, which yields 8.1% under a hydrogen gas atmosphere. Furthermore, in addition to its high potential in terms of reactivity profile when in the presence of acids, bases, nucleophiles, and peroxides, Cyrene has also been studied for its effectiveness as a solvent.338
In MOF synthesis, Cyrene is used to achieve crystallinity and a high surface area for MOF production, e.g., HKUST-1, Zn2 (BDC)2 (DABCO), UiO-66, MOF-74, and ZIF-8.339 Glycerol and its byproducts are polar compounds with a high boiling point, low toxicity, and low vapor pressure. Furthermore, glycerol can dissolve a wide range of inorganic/organic salts, including metal ion complexes. Glycerol production from organic waste is regarded as an economically viable product in the biodiesel industry. This approach to glycerol production is both robust and environmentally friendly.340 Several further solvents that possess comparable features, such as ethyl-lactate (ethyl 2-hydroxypropanoate), methyl lactate, c-butyrolactone, and 2-methyltetrahydrofuran (2-MeTHF), were also studied.340 In particular, 2-MeTHF, an aprotic renewable lignocellulosic biomass-derived ether solvent, possesses favorable base and acid stability, limited miscibility with water, and is commercially available.341 Those solvents generate less waste. In this account, 2-MeTHF has been applied to a variety of chemical processes, including the high-scale manufacturing of di-aryl and aryl ketones via Suzuki–Miyaura cross-coupling reactions,342,343 furan-functionalized polyesters,344 and quinazolinone synthesis.345 The exceptional sustainability of 2-MeTHF as a solvent has revolutionized synthetic chemistry as it can be easily used and scaled up. Additionally, the prospects for 2-MeTHF can be extended to the development of eco-friendly MOFs, further enhancing their potential as a green solvent.
Solventless fabrication methods
Although using a solvent enhances the synthesis kinetics of MOFs with a suitable crystalline nature, researchers have exerted tremendous effort to demonstrate a superior eco-friendly method via solventless fabrication. The free solvent fabrication of MOFs dissolves the difficulty in the selection of a suitable solvent that changes the method from environmental to green based on mechanochemical methods.346,347 Mechano-methods achieve a high production yield in a shorter time when compared to solvent-based methods.348
The adsorption mechanism of MOFs toward radionuclides
It is important to investigate the mechanism for the removal of radionuclides using MOFs. The mechanism was investigated through experimental studies and their corresponding observations, spectroscopic analysis techniques, and theoretical calculations. The performance of MOFs toward radionuclide removal is affected by intermolecular interactions between the radionuclides and MOF, as well as the intrinsic properties of MOF (e.g., pore size, surface charge, crystallinity, shape, electronic state, surface-to-mass ratio, and the surface functional groups),349 therefore numerous mechanisms may control the removal of radionuclides. The exact mechanisms for radionuclide removal could be investigated through macroscopic experiments and microscopic analysis.
The removal mechanism from the macroscopic experimental view
The removal mechanism could be investigated based on the reaction conditions, such as time, power of hydrogen (pH), and temperature. The reaction between MOFs and radionuclides was mainly affected by the solution pH.350,351 This is because the adsorbates may have more than one species and/or change the charge over the adsorbent and the functional groups.352,353 For example, U has more than one species. Thus, the removal is affected by the solution power of hydrogen.352 At a pH lower than three, uranium ions exist as UO22+ and at a pH higher than three, they exist as UO2(OH)+, (UO2)(OH)22+, and (UO2)3(OH)5+, while they precipitate at pH above eight.354 In addition, the charge over the framework depends on the solution pH, and as a result, the pH could control the adsorption capability of radionuclides based on the point of zero charge of MOF. When the MOF surface is protonated, it becomes cationic and is available for the removal of anionic radionuclides. The reverse is correct when the surface is deprotonated and the point of zero charges becomes lower than the solution pH; MOFs in this situation become ready for cationic radionuclides.355
Factors that affect adsorption time and speed, the adsorption control step, and the diffusion mechanism of radionuclides can be investigated via adsorption kinetics.349,353 For kinetic studies, some models must be applied and taken into consideration. The pseudo-first and second order models, the intraparticle diffusion model, and the Elovich model are commonly used for kinetic demonstration.354 Generally, the correlation coefficient, R2 is the value used for checking the best model352,356 but in general, the adsorption rate of radionuclide removal depends on intraparticle diffusion. Thus, the intraparticle diffusion model is suitable for explaining the diffusion mechanism over the framework.357 Also, the rate-controlling step is preferred for understanding the mechanism of radionuclide removal over MOFs. Related to the theory of Brownian movement, due to the variation in the Brownian motion, the removal of radionuclides by MOF is affected by temperature change.358,359
The removal mechanism from the microscopic analysis view
Numerous characterization techniques are used for the estimation of the surface properties of MOFs, the mechanism of removal, and the reaction pathway of MOFs with radionuclides through elementary analysis and functional group identification before and after the removal process.360–362 Microscopic analysis is the next important step, besides macroscopic analysis, for understanding the removal mechanism of radionuclides. XPS analysis estimates the type and composition of the MOF surface and the valence of the surface elements.360,362 FTIR analysis was used to estimate the functional groups over MOFs before and after radionuclide removal, which is clear evidence for the existence of the bonding between the MOF active sites and groups with the interested radionuclides.354 Other superior analysis techniques have become available and are more favorable for understanding the removal mechanism, such as Raman, XRD, and UV-visible analysis.363
MOFs usability for the decontamination of wastewater from radionuclides
Cesium
Very few MOFs are reported for the separation of Cs137 such UO2(NO3)2·6H2O with 3,5-di(4-carboxyl phenyl) benzoic acid, which showed a large capacity toward cesium.206 Noeimie et al. fabricated a novel ferric-benzene tricarboxylic acid MOF by the hydrothermal method. They modified it by impregnation with potassium nickel hexacyanoferrate and applied it in the removal of Cs ions from aqueous solutions with an adsorption capacity of 153 mg g−1. It showed high selectivity for sodium and potassium ions, and equilibrium was achieved after about 45 min.364 On the other hand, [(CH3)2NH2][UO2(L2)]0.5DMF·15H2O was reported for the removal of Cs with a large uptake percent of 94.51% after 20 minutes under acidic conditions (pH 3).365
Barium
Ba133 is one of the most toxic radionuclides, resulting in radioactive waste, so its removal from waste is a point of interest to protect humans and animals from a long-term threat. Zhong et al. reported that MOF-808-SO4 and MIL-101-SO3H were suitable materials with good removal performance toward barium due to the strong interactions between barium and sulfate ions. Both functionalized MOFs are suitable for the removal of barium with 90% uptake percent after five minutes and reached 99% after equilibrium. MOF-808-SO4 showed a removal capacity of 131.3 mg g−1 and 70.5 mg g−1 for MIL-101-SO3H.366 Also, Zr-BDC-NH2–SO4 was used by the same group for the removal of Ba at room temperature, showing a large removal capacity of about 181.8 mg g−1.367
Uranium
More than twenty MOFs have been reported for the removal of uranium, which exists in the form UO22+. Lin et al. fabricated the first MOF materials (UiO-68) that were applied in the removal of uranium ions from solutions, which showed excellent sorption capacity for uranium ions, about 217 mg g−1368 Wu et al. fabricated a ferric oxide-ZIF-8 composite (Fig. 6a) and used it for the removal of uranium(VI). The results showed a high uptake capacity (539 mg g−1) with a contact equilibrium time of 30 minutes.369 Also, MIL-101(Cr) has been reported for the removal of UO22+ from aqueous solutions with a high selective recovery and capacity of about 5.32 mg g−1 at pH 3 and 27.99 mg g−1 after an equilibrium contact time of 6.25 hours.370 The modifications of MIL-101 with amine, ethanediamine, and diethylenetriamine have been reported to show excellent and superior removal capacity: MIL-101-NH2, MIL-101-ED, and MIL-101-DETA showed 90, 200, and 350 mg g−1, respectively.371 Moreover, MIL-101 functionalized by the carboxyl group showed the suitable removal of uranium with a capacity of 314 mg g−1 after an equilibrium time of 2 h in a neutral pH medium.372 UiO-66-AO is the first amidoxime-based MOF fabricated by the post-modification method (Fig. 6b). It has been reported for the removal of uranium ions from seawater with high efficiency and a very fast removal time, and removed about 500 ppm of uranium ions in less than 10 minutes. UiO-66-AO showed an adsorption capacity equal to 2.68 mg g−1.373 Zhang et al. reported that Zn-MOF-74 modified with coumarin enhanced the opening of the pore sites of the MOFs and showed a high adsorption capacity for uranium ions of about 360 mg g−1.374 Another strategy for improving the adsorption capacity for the removal of uranium ions rather than modification is the addition of a ligand in the body of the MOFs framework, as reported by Zhang et al.374 Zn(HBTC)(L) (H2O)2 showed excellent ability for great performance in the removal of uranium ions with a capacity of 115 mg g−1 at lower pH. Meanwhile, MOF-76 (Fig. 6c) has been reported for the removal of uranium ions with an adsorption capacity of 298 mg g−1.375 On the other hand, MOF-5 was reported for the removal of uranium with a large removal capacity of 237 mg g−1 after a very short time (5 minutes) at pH 5.376
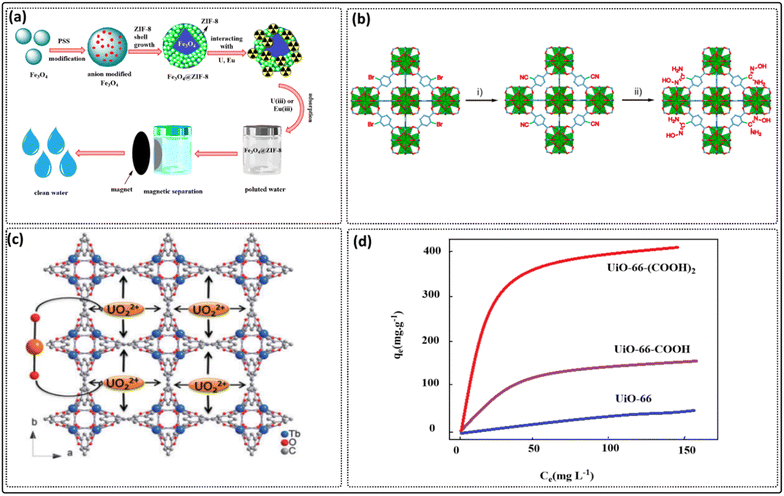 |
| Fig. 6 (a) Ferric oxide ZIF-8 composite synthesis and removal mechanism [adapted from ref. 369 with permission from Elsevier B.V., copyright 2019]. (b) The synthetic route for UiO-66-AO: (i) CuCN, N-methyl pyrrolidone, microwaved at 170 °C for 20 min; (ii) NH2OH·HCl, CH3CH2OH, refluxing for 24 h [adapted from ref. 373 with permission from American Chemical Society, copyright 2017]. (c) Schematic of the capture of UO22+ ions in the one-dimensional channels of MOF-76 [adapted from ref. 375 with permission from The Royal Society of Chemistry, copyright 2013]. (d) Schematic sorption properties of UiO-66, UiO-66-COOH, and UiO-66-(COOH)2 [adapted from ref. 368 with permission from Elsevier Inc, copyright 2019]. | |
Thorium
Thorium exists in nuclear waste in the oxidation state (IV). The first MOF applied in thorium removal was UiO-66, which showed a maximum sorption capacity of 47.5 mg g−1. Modification with carboxyl groups to give UiO-66-(COOH) resulted in maximum capacity (150 mg g−1). This is due to the uptake of thorium occurring as a result of the coordination bond between Th(IV) and carboxyl groups –COOH, while further modification gave UiO-66-(COOH)2, which showed adsorption capacity (350 mg g−1). Also, UiO-66-(COOH)2 showed a large uptake of thorium when compared with UiO-66-(COOH) and UiO-66 (Fig. 6d).368 Xiao et al. fabricated MnSO-MOF, which showed suitable removal ability toward thorium ions from rare earth elements with an adsorption capacity of 46.3 mg g−1, by making coordination bonds with N and O atoms present on the framework.368
Iodine
The I129 isotope is radioactive and harmful and should be removed from nuclear waste due to its long lifetime.377 Zeng et al. synthesized a Zn-lactate-pyridyl benzoate MOF that showed good adsorption toward iodine (Fig. 7a), where one gram of Zn3(DL-lac)2(pybz)2 is available for the removal of one gram of iodine.378 ZIF-8 has been reported by Sava et al. for iodine capture with high capacity379 (Fig. 7b).
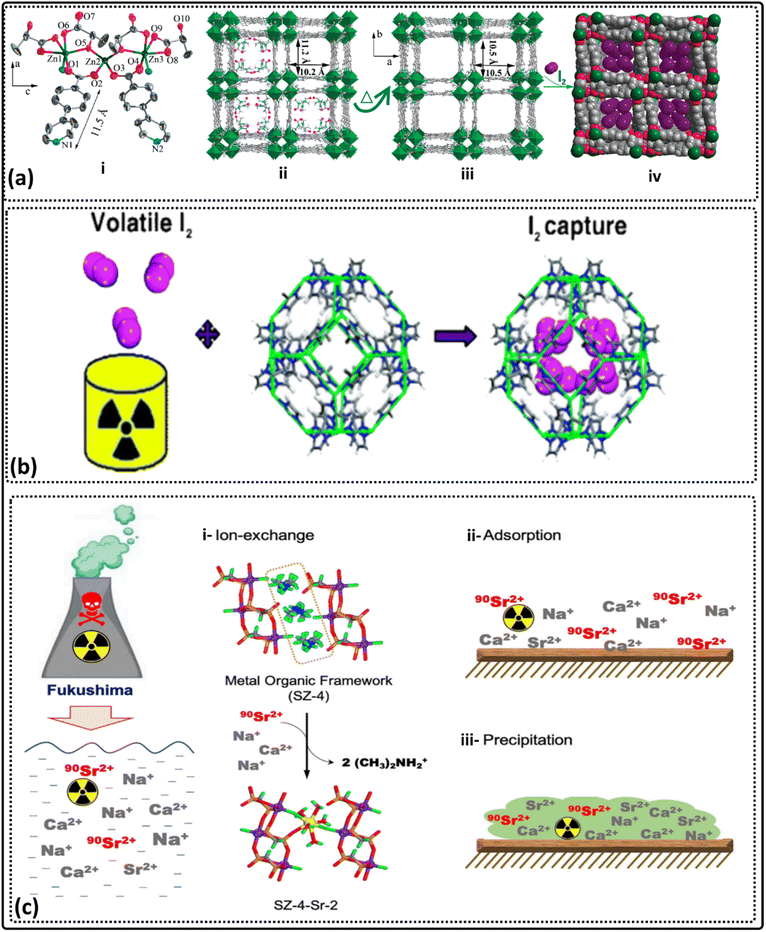 |
| Fig. 7 (a) Single-crystal to single-crystal, the controlled uptake and release of iodine, and electrical conductivity [adapted from ref. 378 with permission from American Chemical Society, copyright 2010]. (b) Zeolitic imidazolate framework-8 structure and its captured molecular iodine (I2) [adapted from ref. 379 with permission from the American Chemical Society, copyright 2011]. (c) The selective uptake of radioactive strontium-90 ions [adapted from ref. 380 with permission from Elsevier Inc, copyright 2019]. | |
Strontium
Strontium ions were removed using SZ-4 MOF through an ion exchange mechanism via two steps, which achieved an adsorption capacity of 121 mg g−1 at pH 2 within 20 minutes (Fig. 7c).380 MOF-808-C2O4 and MOF-808-SO4 have also been synthesized and used for Sr ions removal with high selectivity and the adsorption capacity of 167.56 mg g−1 for MOF-808-SO4 and 206.34 mg g−1 for MOF-808-C2O4.
Europium
Europium is a representative element for trivalent lanthanides, and its radioisotopes are listed among the hazardous species found in radioactive waste solutions. A little work has been done employing MOFs as sorbents for removing Eu(III) ions from aqueous solutions. Hua et al.381 fabricated a nanofibrous membrane MOF for the removal of Eu(III) ions, and its sorption capacity was about 191.9 mg g−1. Lin et al. fabricated a novel MIT-101-DGA MOF to remove Eu(III) with a maximum sorption capacity of 33 mg g−1 at pH 3.5.382 Hamouda et al. fabricated a novel bi-ligand strontium-based MOF (MTSr-MOF), which showed a lower removal percentage of approximately 13.59% for 152+154Eu radionuclides. To enhance its performance, MTSr-MOF was modified using various modifiers. The results showed that the MTSr-MOF modified with oxalic acid demonstrated a significantly higher removal efficiency for 152+154Eu radionuclides as compared to other modified MOFs, with a removal efficiency of approximately 96.42%. This finding suggests that MTSr-MOF modified with oxalic acid has the potential to be a promising candidate for the removal of 152+154Eu radionuclides from radioactive waste in the future, based on using bi-ligand MOFs.383
Organic frameworks-based materials behaviors against strong radiation conditions
For industrial applications, MOFs should possess high thermal and hydrothermal stabilities, while for radionuclide applications, they should acquire higher radioactive stability. The radioactive stability of MOFs could be tested via the study of the structure and crystallinity before and after radiation penetration, and also through the study of the surface area and the capacity of the investigated MOF toward a radioactive substrate of interest.
MOF stability has been examined for a few MOFs, such as a thorium-based MOF that showed superior radiation stability for up to 200 KGy of radiation.384 On the other hand, UiO-66, HKUST-1, and MIL-100 have been fabricated based on a transition metal node. They showed higher radiation stability; among them, MIL-101 was the most stable MOF, which retained its stability under high radiation levels equivalent to 2 MGy.385–387
The higher stability against radiation increased in ligands with extended π-systems due to the higher delocalization energy. Thus, the fabrication of promising radiation-stable MOFs required suitable ligand poses that extended π-systems.388 Gilson et al. fabricated a Th-based MOF using extended π-system ligands and showed higher stability to γ-rays with 4 MGy.388
Regeneration and reusability of MOFs toward radionuclides
The removal of radionuclides from the MOF's framework is an economic issue. MOFs can be regenerated after a series of removals of radionuclides or for another application. The most common and applicable method for the reusability of MOF is the elution of the adsorbed radionuclide substrate using a suitable eluting agent, which could be acid, salt, base, water, and others. The most common acids used are HCl and HNO3.371,389–395 Generally, NaOH is a suitable base used for regeneration.396,397 Salts such as sodium and potassium carbonates could also be used.206,375,398,399 Other eluting agents such as EDTA are used,400,401 and ion exchangers containing SO42−, NO31−, and Br1− (ref. 402–404) could also be used. The reusability of MOFs for radionuclide removal can be affected by several factors, including the stability and selectivity of the MOF, the concentration, and types of radionuclides in the sample, and the presence of competing ions or other contaminants. The stability of MOFs in the presence of radiation is a critical factor that can limit their reusability. MOFs can degrade or become structurally unstable when exposed to ionizing radiation, which can decrease their effectiveness and limit their reuse. To enhance the reusability of MOFs, several strategies have been proposed, including the modification of the MOF structure to increase its stability and selectivity, the use of multiple MOFs in combination to increase the range of target radionuclides, and the use of pre-treatment processes to remove interfering contaminants from the sample matrix before adsorption by the MOF.
Assessing MOFs versus conventional methods for radioactive waste cleanup
Effective methods for separating radionuclides from environmental samples are crucial for the safe and efficient removal of radioactive waste. Various conventional techniques, such as precipitation, membrane separation, ion exchange, extraction chromatography, solid-phase extraction, and liquid–liquid extraction (LLE), are available for this purpose, each with its pros and cons that must be considered when selecting the most suitable method for a particular application. While precipitation and coprecipitation are common methods that offer high recovery and repeatability, they are time-consuming and laborious. Membrane separation can achieve high decontamination factors but membrane fouling and structural instability are issues. Ion-exchange techniques offer high specificity and decontamination but are also time-consuming. Extraction chromatography combines the ease of use of ion exchange chromatography with the selectivity of LLE, making it useful for the separation of actinides and lanthanides. Solid-phase extraction techniques have several benefits, including the removal of non-target elements from the sample matrix, minimal waste production, and the ability to selectively separate target elements, among others. LLE is widely used due to its high selectivity, efficiency, scalability, and ability to selectively separate target radionuclides from other components in the waste stream, resulting in a significantly reduced waste volume for disposal. However, LLE has some drawbacks, including complex chemical reactions, the generation of secondary waste streams, and the handling of hazardous chemicals and radioactive materials.405 Compared to other techniques, MOFs have several advantages, such as high selectivity, capacity, and ease of synthesis. MOFs can be tailored to selectively capture specific radionuclides while ignoring interfering ions in the sample matrix, and they have high adsorption capacities due to their high surface area and porous nature. The synthesis of MOFs is relatively simple and can be easily scaled up for industrial applications. However, MOFs have some drawbacks, such as their stability in the presence of radiation, sensitivity to changes in pH and temperature, and large particle sizes.154–166 Overall, the effectiveness and practicality of MOFs as compared to conventional methods for removing radioactive waste require further research. While each method has its strengths and weaknesses, MOFs offer a promising new approach due to their high selectivity, capacity, and ease of synthesis. However, their stability in the presence of radiation must be addressed, and further studies are necessary to identify the most suitable method for practical applications in the field of radioactive waste removal.
Cost-effectiveness of MOF synthesis and application
It is crucial to consider the cost of preparing and using adsorbents when evaluating their suitability for wastewater treatment, especially given the availability of alternative technologies. There are several methods for determining the adsorbent cost, including the cost of raw materials, discounted cash flow, cost indices, and cost per gram of adsorbate removed. To evaluate the impact of process efficiency on process cost, a quantitative metric for comparing adsorbent costs known as “adsorbent cost performance” is used. This metric is represented in dollars per mole and shows the cost of producing and using 1.0 g of an adsorbent to remove 1 mole of a chemical species at the theoretical maximum uptake. Adsorbents with a cost performance of less than $1 per mol are considered inexpensive, while those above $200 per mol are considered expensive, with most adsorbents falling between these ranges.406 The cost of MOFs is evaluated over a range of annual production rates, ranging from 50
000 kg MOF per year to 2.5 million kg per year. The projected cost of MOFs is associated with a production facility that is optimized for the specific level of production.407 The cost of synthesizing MOFs is primarily determined by the cost of starting materials, the energy required for the process, and purification steps. To reduce the cost of starting materials, low-cost and readily available sources can be utilized. The energy requirements for MOF synthesis can be minimized by developing energy-efficient synthesis methods such as microwave-assisted or sonochemical synthesis. Furthermore, reducing the reactor volume and operation times can also lead to a reduction in the cost of MOF manufacturing, resulting in a lower overall manufacturing cost.406,407 The purification steps, which involve the removal of unwanted by-products or solvents, can also be optimized to reduce the cost of MOF synthesis.
The cost of MOF production per unit weight is influenced by the scale of production. Large-scale production can result in economies of scale, leading to a reduction in the cost per unit weight of the MOF. However, scaling up MOF production can also pose challenges in maintaining the consistent quality and reproducibility of the MOF. In addition, the reusability of MOFs is a critical factor to consider when evaluating their economic feasibility in various applications. The ability to reuse MOFs can significantly reduce the overall cost of MOF-based processes, eliminating the need for frequent replacement and disposal of the MOFs. This makes MOFs a cost-effective alternative to traditional materials.408,409
There have been limited studies that have investigated the cost analysis of synthesizing MOFs and their application in absorbing heavy metals and radioactive ions. Most studies have focused on the synthesis of MOFs and their application. Further research is, therefore, needed to optimize the synthesis process and evaluate the economic feasibility of using MOFs for the adsorption of heavy metals and radioactive ions.
Conclusion and perspectives
Metal–organic frameworks (MOFs) have emerged as promising new materials for removing and separating radionuclides and toxic metals from contaminated water sources. Herein, we have summarised the research progress of MOFs for the removal of radionuclides from wastewater. The properties of MOFs, such as low density, chemical and thermal stability, large pore size, and extended surface area, make them ideal candidates for this application. The choice of metal ions and organic linkers and the use of modulators during fabrication can impact the properties and morphology of the resulting MOF. The synthesis of MOFs using sustainable and eco-friendly alternatives such as water as a solvent has been explored, including the cost analysis of MOFs synthesis and application, which is dependent on various factors and requires a case-by-case analysis to determine the economic feasibility of MOFs. Researchers are working to overcome the limitations associated with this approach. MOFs have shown promising potential for the selective removal of radionuclides such as cesium, barium, uranium, thorium, iodine, and strontium from wastewater. MOFs are also stable under strong radiation conditions and can be regenerated and reused, making them a cost-effective solution for the removal of radionuclides from wastewater. However, further research is needed to investigate the use of MOFs for radionuclide removal and develop more efficient and eco-friendly methods for the synthesis and application of MOFs for this purpose.
MOFs are booming in the field of radionuclide removal, but several main challenges are still being overcome to achieve the highest selective adsorption in practical applications, which include the following.
(1) From a structural perspective, stability is an important consideration for MOFs, particularly in terms of their chemical stability under strong acid and radiation conditions. The stability of MOFs can limit their potential practical applications. However, more information can be obtained by conducting the synthesis of bi-metal, bi-ligand MOFs, as fewer MOFs with stable structures have been developed and are effective for removing ions from radioactive wastewater.
(2) To assess the performance of MOFs, it is necessary to analyze their adsorption behavior for radioactive ions. Additionally, more information can be obtained by studying various factors, such as biological contamination, high salinity, pH, competing ions, and long-term use.
(3) From an application perspective, the majority of MOFs utilized in wastewater treatment are in the form of powder, which can be challenging to manage and recover. This can result in possible secondary pollution, which restricts their practical use. To address this issue, certain improvements can be made to retain their exceptional adsorption capacity. For instance, modifying the shape of MOFs, combining them with magnetic materials, creating devices or films, or combining them in three-dimensional structures.
(4) Considering the economic aspects, the practical application of porous materials in wastewater treatment is hindered by obstacles, such as the synthetic processes of MOFs, a limited range of organic linkages, and low yields. Researchers have focused on using cost-effective organic monomers to reduce synthesis costs to overcome these limitations. Also, microwave-assisted or radiation-assisted synthesis is widely used in materials synthesis. Widespread and inexpensive methods are constantly being discovered.
(5) Future research should focus on developing more accurate and reliable models for predicting the cost of adsorbent synthesis and usage, taking into account factors such as energy requirements, scaling up production, regeneration, and the impact of different operating conditions on adsorption efficiency. A roadmap figure from the authors' viewpoint of the future of these materials is presented in (Fig. 8).
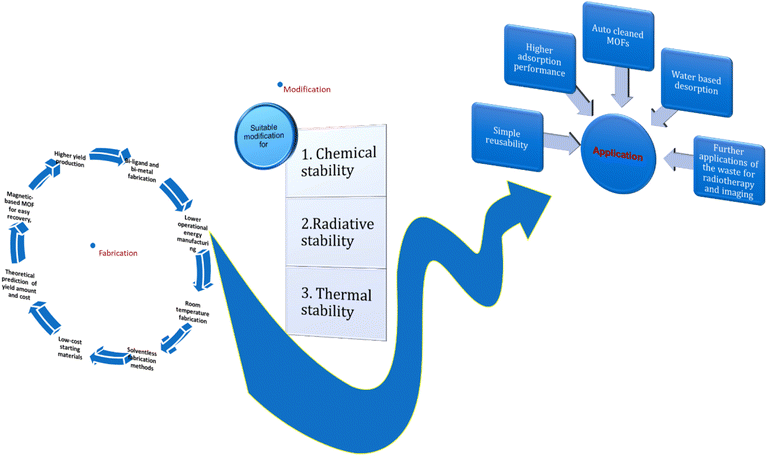 |
| Fig. 8 A roadmap figure from the authors' viewpoint of the future of MOFs materials for the adsorption, removal, and separation of radionuclides and toxic metals from contaminated water sources. | |
(6) The experimental study (synthesis and application) could be merged with a computational study to reduce the efforts used in that work and allow it to be a large-scale study to get more important results in industrial applications.
MOFs have shown tremendous promise as adsorbents for efficient radioactive removal in wastewater treatment. Even though their use in aquatic systems is still being developed, more investigation into their characteristics and mechanisms is needed. We anticipate that they will play a substantial role in eliminating radionuclides from wastewater in complicated systems due to their potential for further development.
Conflicts of interest
There are no conflicts to declare.
Acknowledgements
This work was supported by the financial support of the National Research Centre (NRC) Foundation of the internal project no. (13030201).
Notes and references
- Z. J. A. Belmonte, Y. T. Prasetyo, O. P. Benito, J.-H. Liao, K. C. Susanto, M. N. Young, S. F. Persada and R. Nadlifatin, Nucl. Eng. Technol., 2023, 23, 1738–5733 Search PubMed.
- G. Berndes, M. Hoogwijk and R. Van den Broek, Biomass Bioenergy, 2003, 25, 1–28 CrossRef.
- S. Bilgen, Renewable Sustainable Energy Rev., 2014, 38, 890–902 CrossRef CAS.
- C. Breyer, D. Bogdanov, A. Aghahosseini, A. Gulagi, M. Child, A. S. Oyewo, J. Farfan, K. Sadovskaia and P. Vainikka, Prog. Photovolt.: Res. Appl., 2018, 26, 505–523 CrossRef.
- I. Luhar, S. Luhar, M. M. A. B. Abdullah, A. V. Sandu, P. Vizureanu, R. A. Razak, D. D. Burduhos-Nergis and T. Imjai, Materials, 2023, 16, 954 CrossRef CAS.
- C. Cabaud, Y. Barré, L. De Windt, S. Gill, E. Dooryhée, M. P. Moloney, N. Massoni and A. Grandjean, Adsorption, 2019, 25, 765–771 CrossRef CAS.
- S. I. Y. Salameh, F. I. Khalili and A. H. Al-Dujaili, Int. J. Miner. Process., 2017, 168, 9–18 CrossRef CAS.
- Z. H. Saidin, 21st EGU Gen. Assem. EGU, Proc. Conf., Vienna, Austria, 2019, held 7-12 April Search PubMed.
- R. K. Jyothi, L. Gadelha, T. Costa, R. M. Santos and H. Yoon, Front. Energy Res., 2023, 11, 1–13 Search PubMed.
- M. E. Nasab, Fuel, 2014, 116, 595–600 CrossRef.
- M. Srebalová, T. Peráček and B. Mucha, in Developments in Information and Knowledge Management Systems for Business Applications, Studies in Systems, Decision and Control, Springer, Cham, 2023, vol. 462, pp. 271–292 Search PubMed.
- M. I. Ojovan, W. E. Lee and S. N. Kalmykov, An Introduction to Nuclear Waste Immobilisation, Elsevier, 3rd edn, 2019 Search PubMed.
- M. I. Atz and M. Fratoni, Nucl. Technol., 2023, 209, 677–695 CrossRef.
- J. P. Murray, J. J. Harrington and R. Wilson, Cato J., 1982, 2, 565 Search PubMed.
- D. Kadadou, E. A. Said, R. Ajaj and S. W. Hasan, J. Water Process Eng., 2023, 52, 103604 CrossRef.
- G. Atun, B. Bilgin and A. Kilislioglu, Appl. Radiat. Isot., 2002, 56, 797–803 CrossRef CAS PubMed.
- Y. Dai, R. Lv, J. Fan, X. Zhang and Q. Tao, J. Radioanal. Nucl. Chem., 2019, 321, 473–480 CrossRef CAS.
- J. Wang and S. Zhuang, Rev. Environ. Sci. Bio/Technol., 2019, 18, 231–269 CrossRef CAS.
- J.-G. K. Lalhmunsiama, S. S. Choi and S.-M. Lee, Appl. Chem. Eng., 2018, 29, 127–137 CAS.
- B. Özkan, Y. Altaş and S. İnan, J. Radioanal. Nucl. Chem., 2023 DOI:10.1007/s10967-023-08855-y.
- D. G. Brookins, Geochemical Aspects of Radioactive Waste Disposal, Springer Science & Business Media, 2012 Search PubMed.
- J. Xiao, Y. Chen, W. Zhao and J. Xu, J. Mol. Liq., 2013, 188, 178–185 CrossRef CAS.
- A. R. Keshtkar, M. Irani and M. A. Moosavian, J. Radioanal. Nucl. Chem., 2013, 295, 563–571 CrossRef CAS.
- D. Humelnicu, M. V. Dinu and E. S. Drăgan, J. Hazard. Mater., 2011, 185, 447–455 CrossRef CAS PubMed.
- J. Chen, H. Gao, Z. Tao, L. Wang, R. Li and G. Wang, Coord. Chem. Rev., 2023, 485, 215121 CrossRef CAS.
- D. J. Tranchemontagne, J. L. Tranchemontagne, M. O'Keeffe and O. M. Yaghi, Chem. Soc. Rev., 2009, 38, 1257–1283 RSC.
- H. Li, M. Eddaoudi, M. O'Keeffe and O. M. Yaghi, Nature, 1999, 402, 276–279 CrossRef CAS.
- S. F. Fatima, R. Sabouni, R. Garg and H. Gomaa, Colloids Surf., B, 2023, 225, 113266 CrossRef CAS PubMed.
- K. Uemura, S. Kitagawa, M. Kondo, K. Fukui, R. Kitaura, H. C. Chang and T. Mizutani, Chem. – Eur. J., 2002, 8, 3586–3600 CrossRef CAS.
- F. Valizadeh Harzand, S. N. Mousavi Nejad, A. Babapoor, S. M. Mousavi, S. A. Hashemi, A. Gholami, W.-H. Chiang, M. G. Buonomenna and C. W. Lai, Symmetry, 2023, 15, 403 CrossRef CAS.
- O. K. Farha and J. T. Hupp, Acc. Chem. Res., 2010, 43, 1166–1175 CrossRef CAS.
- J. M. Taylor, T. Komatsu, S. Dekura, K. Otsubo, M. Takata and H. Kitagawa, J. Am. Chem. Soc., 2015, 137, 11498–11506 CrossRef CAS PubMed.
- P. Kumar, A. Deep and K. H. Kim, TrAC, Trends Anal. Chem., 2015, 73, 39–53 CrossRef CAS.
- M. Khan, M. N. Tahir, S. F. Adil, H. U. Khan, M. R. H. Siddiqui, A. A. Al-warthan and W. Tremel, J. Mater. Chem. A, 2015, 3, 18753–18808 RSC.
- H. Furukawa, K. E. Cordova, M. O’Keeffe and O. M. Yaghi, Science, 2013, 341, 6149 CrossRef.
- J. Liu and Y. Wang, Molecules, 2023, 28, 2141 CrossRef CAS PubMed.
- S. P. Dubey, A. D. Dwivedi, I. C. Kim, M. Sillanpaa, Y. N. Kwon and C. Lee, Chem. Eng. J., 2014, 244, 160–167 CrossRef CAS.
- D. Fu, Z. He, S. Su, B. Xu, Y. Liu and Y. Zhao, J. Colloid Interface Sci., 2017, 505, 105–114 CrossRef CAS PubMed.
- S. Wu, K. Zhang, X. Wang, Y. Jia, B. Sun, T. Luo, F. Meng, Z. Jin, D. Lin, W. Shen, L. Kong and J. Liu, Enhanced Adsorption of Cadmium Ions by 3D Sulfonated Reduced Graphene Oxide, Elsevier B.V., 2015, vol. 262 Search PubMed.
- H. R. Pouretedal and M. Kazemi, Int. J. Ind. Chem., 2012, 3, 1–8 CrossRef.
- I. Saad, N. Ralha, M. R. Abukhadra, W. Al Zoubi and Y. G. Ko, J. Water Process Eng., 2023, 52, 103572 CrossRef.
- X. L. Wang, D. M. Guo, Q. Da An, Z. Y. Xiao and S. R. Zhai, Int. J. Biol. Macromol., 2019, 128, 268–278 CrossRef CAS.
- C. Lei, J. Gao, W. Ren, Y. Xie, S. Y. H. Abdalkarim, S. Wang, Q. Ni and J. Yao, Carbohydr. Polym., 2019, 205, 35–41 CrossRef CAS PubMed.
- R. Rao, S. Ma, B. Gao, F. Bi, Y. Chen, Y. Yang, N. Liu, M. Wu and X. Zhang, J. Colloid Interface Sci., 2023, 636, 55–72 CrossRef CAS.
- M. Hao, Y. Liu, W. Wu, S. Wang, X. Yang, Z. Chen, Z. Tang, Q. Huang, S. Wang, H. Yang and X. Wang, EnergyChem, 2023, 5, 100101 CrossRef CAS.
- M. Hasanpour and M. Hatami, Adv. Colloid Interface Sci., 2020, 284, 102247 CrossRef CAS PubMed.
- Q. Fang and B. Chen, J. Mater. Chem. A, 2014, 2, 8941–8951 RSC.
- M. Wang, Z. Wang, X. Zhou and S. Li, Appl. Sci., 2019, 9, 1–14 Search PubMed.
- S. Ferreira, J. Andrade, M. D. G. Korn, M. Pereira, V. Lemos, W. Santos, F. Rodrigues, A. Souza, H. Ferreira and E. da Silva, J. Hazard. Mater., 2007, 145, 358–367 CrossRef CAS.
- S. Shahida, A. Ali and M. H. Khan, J. Iran. Chem. Soc., 2014, 11, 1–8 CrossRef CAS.
- A. R. Türker, Sep. Purif. Rev., 2012, 41, 169–206 CrossRef.
- J. Poonoosamy, A. Kaspor, S. Rudin, G. L. Murphy, D. Bosbach and G. Deissmann, Minerals, 2023, 13, 636 CrossRef CAS.
- G. Sharma, A. Kumar, S. Sharma, M. Naushad, R. P. Dwivedi, Z. A. ALOthman and G. T. Mola, J. King Saud Univ., Sci., 2019, 31, 257–269 CrossRef.
- F. Fu, L. Xie, B. Tang, Q. Wang and S. Jiang, Chem. Eng. J., 2012, 189, 283–287 CrossRef.
- A. Cescon and J. Q. Jiang, Water, 2020, 12, 1–20 CrossRef.
- S. D. Muktiningsih and D. M. A. R. M. S. Putri, IOP Conf. Ser.: Earth Environ. Sci., 2021, 733, 012147 CrossRef.
- J. Wu, S. Xue, D. Bridges, Y. Yu, L. Zhang, J. Pooran, C. Hill, J. Wu and A. Hu, Chemosphere, 2019, 230, 527–535 CrossRef CAS PubMed.
- K. D. Lenz, S. Jakhar, J. W. Chen, A. S. Anderson, D. C. Purcell, M. O. Ishak, J. F. Harris, L. E. Akhadov, J. Z. Kubicek-Sutherland, P. Nath and H. Mukundan, Sci. Rep., 2021, 11, 1–8 CrossRef PubMed.
- M. Selvaraj, M. A. Assiri, S. L. Rokhum, C. Manjunatha, J. N. Appaturi, S. Murugesan, A. Bhaumik and C. Subrahmanyam, Dalton Trans., 2021, 50, 15118–15128 RSC.
- F. Seblany, E. Vincens and C. Picault, Int. J. Numer. Anal. Methods Geomech., 2021, 45, 1195–1211 CrossRef.
- M. A. Gulamhussein, B. Saini and A. Dey, Mater. Today: Proc., 2022, 77, 260–268 CrossRef.
- S. Dawood and T. Sen, J. Chem. Process Eng., 2014, 1, 1–11 Search PubMed.
- A. H. Behroozi, M. Al-Shaeli and V. Vatanpour, Desalination, 2023, 558, 116638 CrossRef CAS.
- J. Song, H. Oh, H. Kong and J. Jang, J. Hazard.
Mater., 2011, 187, 311–317 CrossRef CAS PubMed.
- A. S. Suneesh, A. Rout, T. Prathibha, B. R. Selvan, M. A. Suba, J. S. B. Rao, G. V. S. A. Kumar and N. Ramanathan, J. Radioanal. Nucl. Chem., 2023, 30, 1–13 Search PubMed.
- G. Sharma, A. Kumar, M. Naushad, D. Pathania and M. Sillanpää, J. Ind. Eng. Chem., 2016, 33, 201–208 CrossRef CAS.
- D. Pathania, G. Sharma, M. Naushad and V. Priya, Desalin. Water Treat., 2016, 57, 468–475 CAS.
- G. Sharma, B. Thakur, M. Naushad, H. Ala'a, A. Kumar, M. Sillanpaa and G. T. Mola, Mater. Chem. Phys., 2017, 193, 129–139 CrossRef CAS.
- P. Pradel, Nuclear Fuel Cycle, Springer Nature Singapore, Singapore, 2023, vol. 8 Search PubMed.
- D. G. Kim, W. Y. Kim, C. Y. Yun, D. Son, D. Chang, H. S. Bae, Y. H. Lee, Y. Sunwoo and K. H. Hong, Int. J. Electrochem. Sci., 2013, 8, 9835–9850 CrossRef CAS.
- T. Makanyire, S. Sanchez-Segado and A. Jha, Adv. Manuf., 2016, 4, 33–46 CrossRef CAS.
- J. Houzar, K. Čubová, M. Semelová and M. Němec, J. Radioanal. Nucl. Chem., 2023, 332, 1515–1519 CrossRef CAS.
- H. T. Truong, T. H. Nguyen and M. S. Lee, Hydrometallurgy, 2017, 171, 298–305 CrossRef CAS.
- E. Robens, Stud. Surf. Sci. Catal., 1994, 87, 109–118 CrossRef CAS.
- Y. Fang, D. Gu, Y. Zou, Z. Wu, F. Li, R. Che, Y. Deng, B. Tu and D. Zhao, Angew. Chem., Int. Ed., 2010, 49, 7987–7991 CrossRef CAS PubMed.
- S. J. Kulkarni, Int. J. Res. Rev., 2017, 4, 44–47 CAS.
- O. D. Agboola and N. U. Benson, Front. Environ. Sci., 2021, 9, 1–27 Search PubMed.
- A. V. Nguyen, in Reference Module in Chemistry, Molecular Sciences and Chemical Engineering, Elsevier, 2013, pp. 1–26 Search PubMed.
- K. Singh, N. A. Renu and M. Agarwal, Interdiscip. Environ. Rev., 2017, 18, 124 CrossRef.
- Y. Zhao, H. Luan, B. Yang, Z. Li, M. Song, B. Li and X. Tang, Water, 2023, 15, 767 CrossRef CAS.
- H. A. González-Ponce, D. I. Mendoza-Castillo, A. Bonilla-Petriciolet, H. E. Reynel-Ávila and K. I. Camacho-Aguilar, Int. J. Chem. Eng., 2023, 2023, 1–12 CrossRef.
- J. Fan, L. Duan, Y. Wang, P. Qiu, M. Fan, P. Shang, Y. He and T. Kang, Colloids Surf., A, 2023, 670, 131547 CrossRef CAS.
- M. Şenilă, E. Neag, C. Tănăselia and L. Şenilă, Materials, 2023, 16, 2965 CrossRef PubMed.
- B. K. Singh and W. Um, Minerals, 2023, 13, 1–21 Search PubMed.
- M. Ersoz and L. Barrott, Best Practice Guide on Metals Removal from Drinking Water by Treatment, IWA Publishing, 1st edn, 2012 Search PubMed.
- M. Polovina, B. Babić, B. Kaluderović and A. Dekanski, Carbon, 1997, 35, 1047–1052 CrossRef CAS.
- A. K. SenGupta, Ion Exchange Technology: Advances in Pollution Control, CRC Press, 1995 Search PubMed.
- Fe. W. John Thomas and B. Crittenden, Adsorption Technology and Design, Butterworth-Heinemann, 1998 Search PubMed.
- R. T. Yang, Adsorbents: Fundamentals and Applications, John Wiley & Sons, 2003 Search PubMed.
- B. Wang, J. Lan, C. Bo, B. Gong and J. Ou, RSC Adv., 2023, 13, 4275–4302 RSC.
- G. San Miguel, S. D. Lambert and N. J. D. Graham, J. Chem. Technol. Biotechnol., 2006, 81, 1685–1696 CrossRef CAS.
- S. Ruidas, A. Chowdhury, A. Ghosh, A. Ghosh, S. Mondal, A. D. D. Wonanke, M. Addicoat, A. K. Das, A. Modak and A. Bhaumik, Langmuir, 2023, 39, 4071–4081 CrossRef CAS PubMed.
- T. S. Saleh, A. K. Badawi, R. S. Salama and M. M. M. Mostafa, Materials, 2023, 16, 2170 CrossRef CAS PubMed.
- S. M. Miller, E. J. Fugate, V. O. Craver, J. A. Smith and J. B. Zimmerman, Environ. Sci. Technol., 2008, 42, 4274–4279 CrossRef CAS PubMed.
- G. Mckay, Use of Adsorbents for the Removal of Pollutants from Wastewater, CRC press, 1995 Search PubMed.
- S. J. T. Pollard, G. D. Fowler, C. J. Sollars and R. Perry, Sci. Total Environ., 1992, 116, 31–52 CrossRef CAS.
- G. San Miguel, G. D. Fowler and C. J. Sollars, Carbon, 2003, 41, 1009–1016 CrossRef CAS.
- S. A. C. Carabineiro, M. F. Pereira, J. J. M. Órfão and J. L. Figueiredo, Chem. Phys. Res. J., 2011, 4, 291 CAS.
- V. Strelko Jr, D. J. Malik and M. Streat, Sep. Sci. Technol., 2001, 36, 3367–3383 CrossRef.
- J. P. Chen and S. Wu, Langmuir, 2004, 20, 2233–2242 CrossRef CAS PubMed.
- P. Chingombe, B. Saha and R. J. Wakeman, Carbon, 2005, 43, 3132–3143 CrossRef CAS.
- N. Zhao, N. Wei, J. Li, Z. Qiao, J. Cui and F. He, Chem. Eng. J., 2005, 115, 133–138 CrossRef CAS.
- S. Babel and T. A. Kurniawan, J. Hazard. Mater., 2003, 97, 219–243 CrossRef CAS PubMed.
- C. P. Huang and D. W. Blankenship, Water Res., 1984, 18, 37–46 CrossRef CAS.
- A. Netzer and D. E. Hughes, Water Res., 1984, 18, 927–933 CrossRef CAS.
- B. E. Reed and S. Arunachalam, J. Environ. Eng., 1994, 120, 416–436 CrossRef CAS.
- C. F. Sharma, Water SA, 1996, 22, 153–160 Search PubMed.
- S. K. Ouki and R. D. Neufeld, J. Chem. Technol. Biotechnol., 1997, 70, 3–8 CrossRef CAS.
- I. Han, M. A. Schlautman and B. Batchelor, Water Environ. Res., 2000, 72, 29–39 CrossRef CAS.
- D. Aggarwal, M. Goyal and R. C. Bansal, Carbon, 1999, 37, 1989–1997 CrossRef CAS.
- S.-J. Park and W.-Y. Jung, Carbon Lett., 2001, 2, 15–21 Search PubMed.
- R. Leyva-Ramos, J. R. Rangel-Mendez, J. Mendoza-Barron, L. Fuentes-Rubio and R. M. Guerrero-Coronado, Water Sci. Technol., 1997, 35, 205–211 CrossRef CAS.
- J. R. Rangel-Mendez and M. Streat, Water Res., 2002, 36, 1244–1252 CrossRef CAS PubMed.
- B. M. Babić, S. K. Milonjić, M. J. Polovina, S. Čupić and B. V. Kaludjerović, Carbon, 2002, 40, 1109–1115 CrossRef.
- A. Seron, H. Benaddi, F. Beguin, E. Frackowiak, J. L. Bretelle, M. C. Thiry, T. J. Bandosz, J. Jagiello and J. A. Schwarz, Carbon, 1996, 34, 481–487 CrossRef CAS.
- P. Liu, Q. Yu, Y. Xue, J. Chen and F. Ma, J. Radioanal. Nucl. Chem., 2020, 324, 813–822 CrossRef CAS.
- W. A. Abbasi and M. Streat, Sep. Sci. Technol., 1994, 29, 1217–1230 CrossRef CAS.
- N. A. Salem and S. M. Ebrahim Yakoot, Desalin. Water Treat., 2016, 57, 28313–28322 CrossRef CAS.
- I. N. Jha, L. Iyengar and A. V. S. P. Rao, J. Environ. Eng., 1988, 114, 962–974 CrossRef CAS.
- S. Babel and T. A. Kurniawan, J. Hazard. Mater., 2003, B97, 219–243 CrossRef PubMed.
- C. Peniche-Covas, L. W. Alvarez and W. Argüelles-Monal, J. Appl. Polym. Sci., 1992, 46, 1147–1150 CrossRef CAS.
- P. Udaybhaskar, L. Iyengar and A. V. S. P. Rao, J. Appl. Polym. Sci., 1990, 39, 739–747 CrossRef CAS.
- W. S. W. Ngah and I. M. Isa, J. Appl. Polym. Sci., 1998, 67, 1067–1070 CrossRef.
- E. Guibal, I. Saucedo, M. Jansson-Charrier, B. Delanghe and P. Le Cloirec, Water Sci. Technol., 1994, 30, 183 CrossRef CAS.
- L. A. Hadwiger, Plant Sci., 2013, 208, 42–49 CrossRef CAS PubMed.
- S. G. Dmitrienko and Y. A. Zolotov, Russ. Chem. Rev., 2002, 71, 159–174 CrossRef CAS.
- H. J. M. Bowen, J. Chem. Soc. A, 1970, 1082–1085 RSC.
- T. Braun and A. B. Parag, Talanta, 1972, 19, 828–830 CrossRef CAS PubMed.
- T. Braun and A. B. Farag, Anal. Chim. Acta, 1972, 61, 265–276 CrossRef CAS.
- H. D. Gesser and G. A. Horsfall, J. Chim. Phys., 1977, 74, 1072–1076 CrossRef CAS.
- V. A. Lemos, M. S. Santos, E. S. Santos, M. J. S. Santos, W. N. L. Dos Santos, A. S. Souza, D. S. De Jesus, C. F. Das Virgens, M. S. Carvalho and N. Oleszczuk, Spectrochim. Acta, Part B, 2007, 62, 4–12 CrossRef.
- G. J. Moody, J. D. R. Thomas and M. A. Yarmo, Anal. Proc., 1983, 20, 132–135 CAS.
- R. F. Hamon, A. S. Khan and A. Chow, Talanta, 1982, 29, 313–326 CrossRef CAS PubMed.
- R. Caletka, R. Hausbeck and V. Krivan, Talanta, 1986, 33, 315–320 CrossRef CAS PubMed.
- S. J. Al-Bazi and A. Chow, Anal. Chim. Acta, 1984, 157, 83–89 CrossRef CAS.
- S. J. Al-Bazi and A. Chow, Talanta, 1983, 30, 487–492 CrossRef CAS PubMed.
- S. J. Al-Bazi and A. Chow, Anal. Chem., 1983, 55, 1094–1098 CrossRef CAS.
- S. J. Al-Bazi and A. Chow, Talanta, 1984, 31, 189–193 CrossRef CAS PubMed.
- L. Jin-Chun and A. Chow, Talanta, 1987, 34, 331–335 CrossRef CAS PubMed.
- M. M. Saeed, Sep. Sci. Technol., 2008, 43, 923–943 CrossRef CAS.
- S. Katragadda, H. D. Gesser and A. Chow, Talanta, 1997, 44, 1865–1871 CrossRef CAS PubMed.
- M. Elkady, H. Shokry and H. Hamad, Materials, 2020, 13, 2498 CrossRef CAS PubMed.
- A. K. Bhattacharya and C. Venkobachar, J. Environ. Eng., 1984, 110, 110–122 CrossRef CAS.
- J. Karthikeyan and M. Chaudhuri, Water Res., 1986, 20, 449–452 CrossRef CAS.
- S. Azarfar, F. Noorbakhsh, M. Salmani, S. Ansari, R. Soleymani and S. Sadighi, Proc. Iran Int. Alum. Conf., 2016, pp. 2–7 Search PubMed.
- P. Dhanasekaran, P. M. Satya Sai, C. Anand Babu, R. Krishna Prabhu and K. K. Rajan, Water Sci. Technol.: Water Supply, 2016, 16, 115–127 CAS.
- Y. Xu, A. Ohki and S. Maeda, Toxicol. Environ. Chem., 2001, 80, 133–144 CrossRef CAS.
- N. S. Sherwood and D. R. Steelman, US Pat., 10301192B2, 2019 Search PubMed.
- T. K. Naiya, A. K. Bhattacharya and S. K. Das, J. Colloid Interface Sci., 2009, 333, 14–26 CrossRef CAS PubMed.
- M. I. Magzoub, M. S. Nasser, I. A. Hussein, A. Benamor, S. A. Onaizi, A. S. Sultan and M. A. Mahmoud, Appl. Clay Sci., 2017, 147, 176–183 CrossRef CAS.
- H. Babaki, A. Salem and A. Jafarizad, Mater. Chem. Phys., 2008, 108, 263–268 CrossRef CAS.
- V. Vimonses, S. Lei, B. Jin, C. W. K. Chow and C. Saint, Chem. Eng. J., 2009, 148, 354–364 CrossRef CAS.
- P. P. Prabhu and B. Prabhu, MATEC Web Conf., 2018, 144, 1–13 CrossRef.
- M. B. Majewski, H. Noh, T. Islamoglu and O. K. Farha, J. Mater. Chem. A, 2018, 6, 7338–7350 RSC.
- L. Alaerts, C. E. A. Kirschhock, M. Maes, M. A. Van Der Veen, V. Finsy, A. Depla, J. A. Martens, G. V Baron, P. A. Jacobs and J. F. M. Denayer, Angew. Chem., Int. Ed., 2007, 46, 4293–4297 CrossRef CAS PubMed.
- Q. H. Hu, Y. G. Wang, X. Gao, Y. Z. Shi, S. Lin, R. P. Liang and J. D. Qiu, J. Hazard. Mater., 2023, 446, 1–8 Search PubMed.
- R. L. Yu, Q. F. Li, T. Zhang, Z. Le Li and L. Z. Xia, Process Saf. Environ. Prot., 2023, 174, 770–777 CrossRef CAS.
- D. J. Tranchemontagne, Chem. Soc. Rev., 2009, 38, 1257 RSC.
- Z. Ma, T. Yuan, Y. Fan, Y. Chen, Y. Bai and J. Xu, Nanomaterials, 2023, 13, 1743 CrossRef CAS PubMed.
- F. Xie, H. Wang and J. Li, J. Mater. Chem. A, 2023, 11, 12425–12433 RSC.
- S. Wang, Z. Ma, X. Du, S. Zhang and Z. Chen, Mater. Express, 2018, 8, 381–387 CrossRef CAS.
- N. Iqbal, X. Wang, J. Yu, N. Jabeen, H. Ullah and B. Ding, RSC Adv., 2016, 6, 4382–4386 RSC.
- N. Stock and S. Biswas, Chem. Rev., 2012, 112, 933–969 CrossRef CAS PubMed.
- F. Zadehahmadi, N. T. Eden, H. R. Mahdavi, K. Konstas, J. I. Mardel, M. Shaibani, P. C. Banerjee and M. R. Hill, Environ. Sci.: Water Res. Technol., 2023, 9, 1305–1330 RSC.
- S. Koppula, P. Jagasia and S. B. Manabolu Surya, Mater. Today Commun., 2023, 34, 105336 CrossRef CAS.
- Y. Fu, X. Wang, Y. Ju, Z. Zheng, J. Jian, Z.-J. Li, C. Jin, J.-Q. Wang and J. Lin, Dalton Trans., 2023, 52, 1177–1181 RSC.
- Y. Hua, D. Kukkar, R. J. C. Brown and K.-H. Kim, Crit. Rev. Environ. Sci. Technol., 2023, 53, 258–289 CrossRef CAS.
- H. Li, M. Eddaoudi, M. O'Keeffe and O. M. Yaghi, Nature, 1999, 402, 276–279 CrossRef CAS.
- A. Maleki and R. Taheri-Ledari, Physicochemical Aspects of Metal–Organic Frameworks, Springer Nature, Switzerland AG, 2023 Search PubMed.
- G. Maurin, C. Serre, A. Cooper and G. Férey, Chem. Soc. Rev., 2017, 46, 3104–3107 RSC.
- M. Gao, B. Li, J. Liu, Y. Hu and H. Cheng, J. Colloid Interface Sci., 2023, 629, 616–627 CrossRef CAS PubMed.
- X. Liu, J. Zhou, D. Liu and S. Liu, Sep. Purif. Technol., 2023, 306, 122526 CrossRef CAS.
- M. Guo, F. Li, Q. Ran, G. Zhu, Y. Liu, J. Han, G. Wang and H. Zhao, Microchem. J., 2023, 190, 108709 CrossRef CAS.
- M. Runowski, D. Marcinkowski, K. Soler-Carracedo, A. Gorczyński, E. Ewert, P. Woźny and I. R. Martín, ACS Appl. Mater. Interfaces, 2023, 15, 3244–3252 CrossRef CAS PubMed.
- B. Zeng, G. Lin, J. Li, W. Wang, Y. Li and Z. Ding, Mater. Sci. Eng. B, 2023, 290, 116337 CrossRef CAS.
- J. R. Long and O. M. Yaghi, Chem. Soc. Rev., 2009, 38, 1213–1214 RSC.
- L.-N. Ma, Z.-H. Wang, L. Zhang, L. Hou, Y.-Y. Wang and Z. Zhu, ACS Appl. Mater. Interfaces, 2023, 15, 2971–2978 CrossRef CAS PubMed.
- J. Hu, X. Zou, S. Ji, Q. Chen, D. Wang and Z. Gong, Anal. Chim. Acta, 2023, 1243, 340809 CrossRef CAS PubMed.
- S. A. Ali, S. N. Shah, M. U. H. Shah and M. Younas, Chemosphere, 2023, 311, 136913 CrossRef CAS PubMed.
- C. Wang, Z. Wang, J. Yu, K. Lu, W. Bao, G. Wang, B. Peng, W. Peng and F. Yu, Chem. Eng. J., 2023, 454, 140078 CrossRef CAS.
- R. Deka, R. Rajak, V. Kumar and S. M. Mobin, Inorg. Chem., 2023, 62, 3084–3094 CrossRef CAS PubMed.
- M. Ren, Y. Zhang, L. Yu, L. Qu, Z. Li and L. Zhang, Talanta, 2023, 255, 124219 CrossRef CAS PubMed.
- D. Akgün and M. Dükkancı, J. Water Process Eng., 2023, 51, 103469 CrossRef.
- D. Zhao, W. Li, R. Wen, N. Lei, W. Li, X. Liu, X. Zhang and L. Fan, Inorg. Chem., 2023, 62, 2715–2725 CrossRef CAS PubMed.
- G. M. Naja and B. Volesky, in Handbook of Advanced Industrial and Hazardous Wastes Management, CRC Press, Boca Raton, 1st edn, 2017, p. 46 Search PubMed.
- B. Sarkar, Heavy Metals In The Environment, CRC Press, 2002 Search PubMed.
- D. Sheng, L. Zhu, C. Xu, C. Xiao, Y. Wang, Y. Wang, L. Chen, J. Diwu, J. Chen, Z. Chai, T. E. Albrecht-Schmitt and S. Wang, Environ. Sci. Technol., 2017, 51, 3471–3479 CrossRef CAS PubMed.
- D. O. Adekoya, M. Tahir and N. A. S. Amin, J. CO2 Util., 2017, 18, 261–274 CrossRef CAS.
- J.-X. Li, Z. Qin, Y. Li and G. Cui, Ultrason. Sonochem., 2018, 48, 127–135 CrossRef CAS PubMed.
- X. Wang, N. Yang, Q. Li, F. He, Y. Yang, B. Wu, J. Chu, A. Zhou and S. Xiong, J. Solid State Chem., 2019, 277, 575–586 CrossRef CAS.
- Y. Yang, D. Liu, Y. Li and G. Cui, J. Solid State Chem., 2019, 278, 120891 CrossRef CAS.
- A. B. Lago, R. Carballo, O. Fabelo, N. Fernández-Hermida, F. Lloret and E. M. Vázquez-López, CrystEngComm, 2013, 15, 10550–10562 RSC.
- N. Sareen, S. Singh and S. Bhattacharya, Dalton Trans., 2014, 43, 4635–4638 RSC.
- H. L. I. B. Mohamed Eddaoudi, D. B. Moler, C. T. M. Reineke, M. O'keeffe and O. M. Yaghi, Acc. Chem. Res., 2001, 34, 319–330 CrossRef PubMed.
- H. Furukawa, N. Ko, Y. B. Go, N. Aratani, S. B. Choi, E. Choi, A. Ö. Yazaydin, R. Q. Snurr, M. O'Keeffe, J. Kim and O. M. Yaghi, Science, 2010, 329, 424–428 CrossRef CAS PubMed.
- B. Du, F. Yan, X. Lin, C. Liang, X. Guo, Y. Tan, H. Zhen, C. Zhao, Y. Shi, E. Kibet, Y. He and X. Yang, Sens. Actuators, B, 2023, 375, 132854 CrossRef CAS.
- J. Li, X. Wang, G. Zhao, C. Chen, Z. Chai, A. Alsaedi, T. Hayat and X. Wang, Chem. Soc. Rev., 2018, 47, 2322–2356 RSC.
- A. J. Howarth, M. J. Katz, T. C. Wang, A. E. Platero-Prats, K. W. Chapman, J. T. Hupp and O. K. Farha, J. Am. Chem. Soc., 2015, 137, 7488–7494 CrossRef CAS.
- K. K. Yee, N. Reimer, J. Liu, S. Y. Cheng, S. M. Yiu, J. Weber, N. Stock and Z. Xu, J. Am. Chem. Soc., 2013, 135, 7795–7798 CrossRef CAS PubMed.
- A. V. Desai, B. Manna, A. Karmakar, A. Sahu and S. K. Ghosh, Angew. Chem., 2016, 128, 7942–7946 CrossRef.
- M. Mon, F. Lloret, J. Ferrando-Soria, C. Martí-Gastaldo, D. Armentano and E. Pardo, Angew. Chem., 2016, 128, 11333–11338 CrossRef.
- M. Jian, H. Wang, R. Liu, J. Qu, H. Wang and X. Zhang, Environ. Sci.: Nano, 2016, 3, 1186–1194 RSC.
- S. Wang, E. V. Alekseev, J. Diwu, W. H. Casey, B. L. Phillips, W. Depmeier and T. E. Albrecht-Schmitt, Angew. Chem., 2010, 122, 1075–1078 CrossRef.
- J. Tian, L. V. Saraf, B. Schwenzer, S. M. Taylor, E. K. Brechin, J. Liu, S. J. Dalgarno and P. K. Thallapally, J. Am. Chem. Soc., 2012, 134, 9581–9584 CrossRef CAS PubMed.
- J. Li, Y. Liu, X. Wang, G. Zhao, Y. Ai, B. Han, T. Wen, T. Hayat, A. Alsaedi and X. Wang, Chem. Eng. J., 2017, 330, 1012–1021 CrossRef CAS.
- Y. Wang, Z. Liu, Y. Li, Z. Bai, W. Liu, Y. Wang, X. Xu, C. Xiao, D. Sheng and J. Diwu, J. Am. Chem. Soc., 2015, 137, 6144–6147 CrossRef CAS PubMed.
- Z. Yang, X. Xu, X. Liang, C. Lei, Y. Cui, W. Wu, Y. Yang, Z. Zhang and Z. Lei, Appl. Catal., B, 2017, 205, 42–54 CrossRef CAS.
- C. Yu, P. Wang, X. Wang, F. Chen and H. Yu, J. Alloys Compd., 2019, 806, 263–271 CrossRef CAS.
- F. Yao, X. Li, C. Wan, L. Xu, Y. An, M. Ye and Z. Lei, Appl. Surf. Sci., 2017, 426, 605–611 CrossRef CAS.
- X. Li, Y. Wu, H. Lun, H. Li, J. Yang and Y. Li, Synth. Met., 2017, 232, 103–110 CrossRef CAS.
- A. Baraka, H. Hatem, M. S. El-geundi, H. Tantawy, K. Karaghiosoff, M. Gobara, A. Elbeih, M. Shoaib, M. A. Elsayed and M. M. Kotb, J. Solid State Chem., 2019, 274, 168–175 CrossRef CAS.
- J. Ehrenmann, S. K. Henninger and C. Janiak, Eur. J. Inorg. Chem., 2011, 2011, 471–474 CrossRef.
- G. Scholz, F. Emmerling, M. Dreger and E. Kemnitz, Z. Anorg. Allg. Chem., 2013, 639, 689–693 CrossRef CAS.
- A. B. Lago, R. Carballo, O. Fabelo, N. Fernández-Hermida, F. Lloret and E. M. Vázquez-López, CrystEngComm, 2013, 15, 10550–10562 RSC.
- K. Banerjee and K. Biradha, Cryst. Growth Des., 2012, 12, 4264–4274 CrossRef CAS.
- D. Cao, L. Qin, X. Yao, J. Hu and H. Zheng, Inorg. Chem. Commun., 2013, 29, 27–29 CrossRef CAS.
- Z. Setifi, F. Setifi, M. Ghazzali, M. El-ghozzi, D. Avignant, O. Pérez and J. Reedijk, Polyhedron, 2014, 75, 68–72 CrossRef CAS.
- S. Zheng, X. Li, B. Yan, Q. Hu, Y. Xu, X. Xiao, H. Xue and H. Pang, Adv. Energy Mater., 2017, 7, 1602733 CrossRef.
- X. R. Wang, Z. Huang, J. Du, X. Z. Wang, N. Gu, X. Tian, Y. Li, Y. Y. Liu, J. Z. Huo and B. Ding, Inorg. Chem., 2018, 57, 12885–12899 CrossRef CAS PubMed.
- A. Karmakar, G. M. D. M. Rúbio, A. Paul, M. F. C. G. da Silva, K. T. Mahmudov, F. I. Guseinov, S. A. C. Carabineiro and A. J. L. Pombeiro, Dalton Trans., 2017, 46, 8649–8657 RSC.
- K. S. Asha, M. Makkitaya, A. Sirohi, L. Yadav, G. Sheet and S. Mandal, CrystEngComm, 2016, 18, 1046–1053 RSC.
- L. M. Aguirre-Díaz, D. Reinares-Fisac, M. Iglesias, E. Gutierrez-Puebla, F. Gandara, N. Snejko and M. Á. Monge, Coord. Chem. Rev., 2017, 335, 1–27 CrossRef.
- E. A. Dolgopolova, A. M. Rice and N. B. Shustova, Chem. Commun., 2018, 54, 6472–6483 RSC.
- C.-T. Yeh, W.-C. Lin, S.-H. Lo, C.-C. Kao, C.-H. Lin and C.-C. Yang, CrystEngComm, 2012, 14, 1219–1222 RSC.
- A. E. Platero-Prats, M. Iglesias, N. Snejko, Á. Monge and E. Gutiérrez-Puebla, Cryst. Growth Des., 2011, 11, 1750–1758 CrossRef CAS.
- Q. Zhou, F. Peng, Y. Ni, J. Kou, C. Lu and Z. Xu, J. Photochem. Photobiol., A, 2016, 328, 182–188 CrossRef CAS.
- N. Xu, Q. Zhang, B. Hou, Q. Cheng and G. Zhang, Inorg. Chem., 2018, 57, 13330–13340 CrossRef CAS PubMed.
- A. E. Platero-Prats, N. Snejko, M. Iglesias, Á. Monge and E. Gutiérrez-Puebla, Chem. – Eur. J., 2013, 19, 15572–15582 CrossRef CAS PubMed.
- M. J. Katz, Z. J. Brown, Y. J. Colón, P. W. Siu, K. A. Scheidt, R. Q. Snurr, J. T. Hupp and O. K. Farha, Chem. Commun., 2013, 49, 9449–9451 RSC.
- Z. Hu, M. Khurana, Y. H. Seah, M. Zhang, Z. Guo and D. Zhao, Chem. Eng. Sci., 2015, 124, 61–69 CrossRef CAS.
- Z. Hu, A. Nalaparaju, Y. Peng, J. Jiang and D. Zhao, Inorg. Chem., 2016, 55, 1134–1141 CrossRef CAS PubMed.
- Y. Han, M. Liu, K. Li, Y. Zuo, Y. Wei, S. Xu, G. Zhang, C. Song, Z. Zhang and X. Guo, CrystEngComm, 2015, 17, 6434–6440 RSC.
- C. Atzori, G. C. Shearer, L. Maschio, B. Civalleri, F. Bonino, C. Lamberti, S. Svelle, K. P. Lillerud and S. Bordiga, J. Phys. Chem. C, 2017, 121, 9312–9324 CrossRef CAS.
- A. Schaate, P. Roy, A. Godt, J. Lippke, F. Waltz, M. Wiebcke and P. Behrens, Chem. – Eur. J., 2011, 17, 6643–6651 CrossRef CAS PubMed.
- Y. Bai, Y. Dou, L. H. Xie, W. Rutledge, J. R. Li and H. C. Zhou, Chem. Soc. Rev., 2016, 45, 2327–2367 RSC.
- Y. Li, M. Gecevicius and J. Qiu, Chem. Soc. Rev., 2016, 45, 2090–2136 RSC.
- L. Jin, H. Zhang, R. Pan, P. Xu, J. Han, X. Zhang, Q. Yuan, Z. Zhang, X. Wang and Y. Wang, Nano Lett., 2015, 15, 6575–6581 CrossRef CAS PubMed.
- N. Basavaraju, K. R. Priolkar, D. Gourier, A. Bessière and B. Viana, Phys. Chem. Chem. Phys., 2015, 17, 10993–10999 RSC.
- R. Fazaeli and H. Aliyan, J. Iran. Chem. Soc., 2019, 16, 1–9 CrossRef CAS.
- G. Tan, L. Zhang, H. Ren, S. Wei, J. Huang and A. Xia, ACS Appl. Mater. Interfaces, 2013, 5, 5186–5193 CrossRef CAS PubMed.
- B. Cheng, H. Liu, M. Fang, Y. Xiao, S. Lei and L. Zhang, Chem. Commun., 2009, 944–946 RSC.
- Y. Teng, J. Zhou, S. N. Khisro, S. Zhou and J. Qiu, Mater. Chem. Phys., 2014, 147, 772–776 CrossRef CAS.
- J. Perelaer, B. De Gans and U. S. Schubert, Adv. Mater., 2006, 18, 2101–2104 CrossRef CAS.
- S. L. Pedersen, A. P. Tofteng, L. Malik and K. J. Jensen, Chem. Soc. Rev., 2012, 41, 1826–1844 RSC.
- M. Zhang, Q. Shang, Y. Wan, Q. Cheng, G. Liao and Z. Pan, Appl. Catal., B, 2019, 241, 149–158 CrossRef CAS.
- J. M. Lucero, T. J. Self and M. A. Carreon, New J. Chem., 2020, 44, 3562–3565 RSC.
- M. F. Thorne, M. L. R. Gómez, A. M. Bumstead, S. Li and T. D. Bennett, Green Chem., 2020, 22, 2505–2512 RSC.
- K. Imawaka, M. Sugita, T. Takewaki and S. Tanaka, Polyhedron, 2019, 158, 290–295 CrossRef CAS.
- O. Kolmykov, J. M. Commenge, H. Alem, E. Girot, K. Mozet, G. Medjahdi and R. Schneider, Mater. Des., 2017, 122, 31–41 CrossRef CAS.
- P. Wang, J. Liu, C. Liu, B. Zheng, X. Zou, M. Jia and G. Zhu, Chem. – Eur. J., 2016, 22, 16613–16620 CrossRef CAS PubMed.
- B. Ding, X. Wang, Y. Xu, S. Feng, Y. Ding, Y. Pan, W. Xu and H. Wang, J. Colloid Interface Sci., 2018, 519, 38–43 CrossRef CAS PubMed.
- Y. Chen and S. Tang, J. Solid State Chem., 2019, 276, 68–74 CrossRef CAS.
- O. M. Yaghi, Metal–Organic and Zeolite Imidazolate Frameworks (MOFs and ZIFs) for Highly Selective Separations, University of California-Los Angeles, 2012 Search PubMed.
- Y. Liu, H. Pang, X. Wang, S. Yu, Z. Chen, P. Zhang, L. Chen, G. Song, N. Saleh Alharbi, S. Omar Rabah and X. Wang, Chem. Eng. J., 2021, 406, 127139 CrossRef CAS.
- Y. Pan, Y. Liu, G. Zeng, L. Zhao and Z. Lai, Chem. Commun., 2011, 47, 2071–2073 RSC.
- A. F. Gross, E. Sherman and J. J. Vajo, Dalton Trans., 2012, 41, 5458–5460 RSC.
- H. Y. Cho, J. Kim, S. N. Kim and W. S. Ahn, Microporous Mesoporous Mater., 2013, 169, 180–184 CrossRef CAS.
- B. Seoane, J. M. Zamaro, C. Tellez and J. Coronas, CrystEngComm, 2012, 14, 3103–3107 RSC.
- C. J. Adams, M. A. Kurawa and A. G. Orpen, Dalton Trans., 2010, 39, 6974–6984 RSC.
- P. J. Beldon, L. Fábián, R. S. Stein, A. Thirumurugan, A. K. Cheetham and T. Friščić, Angew. Chem., 2010, 122, 9834–9837 CrossRef.
- S. Tanaka, K. Kida, T. Nagaoka, T. Ota and Y. Miyake, Chem. Commun., 2013, 49, 7884–7886 RSC.
- M. Faustini, J. Kim, G. Y. Jeong, J. Y. Kim, H. R. Moon, W. S. Ahn and D. P. Kim, J. Am. Chem. Soc., 2013, 135, 14619–14626 CrossRef CAS PubMed.
- D. Yamamoto, T. Maki, S. Watanabe, H. Tanaka, M. T. Miyahara and K. Mae, Chem. Eng. J., 2013, 227, 145–150 CrossRef CAS.
- I. Ahmed, J. Jeon, N. A. Khan and S. H. Jhung, Cryst. Growth Des., 2012, 12, 5878–5881 CrossRef CAS.
- Y. R. Lee, M. S. Jang, H. Y. Cho, H. J. Kwon, S. Kim and W. S. Ahn, Chem. Eng. J., 2015, 271, 276–280 CrossRef CAS.
- P. Lidström, J. Tierney, B. Watheyb and J. Westmana, Tetrahedron, 2001, 57, 9225–9283 CrossRef.
- M. Gaab, N. Trukhan, S. Maurer, R. Gummaraju and U. Müller, Microporous Mesoporous Mater., 2012, 157, 131–136 CrossRef CAS.
- S. Bahrani, S. A. Hashemi, S. M. Mousavi and R. Azhdari, Drug Metab. Rev., 2019, 51, 356–377 CrossRef CAS PubMed.
- S. Kumar, S. Jain, M. Nehra, N. Dilbaghi, G. Marrazza and K. H. Kim, Coord. Chem. Rev., 2020, 420, 213407 CrossRef CAS.
- J. Chen, K. Shen and Y. Li, ChemSusChem, 2017, 10, 3165–3187 CrossRef CAS PubMed.
- R. Seetharaj, P. V. Vandana, P. Arya and S. Mathew, Arabian J. Chem., 2019, 12, 295–315 CrossRef CAS.
- A. J. Howarth, Y. Liu, P. Li, Z. Li, T. C. Wang, J. T. Hupp and O. K. Farha, Nat. Rev. Mater., 2016, 1, 1–16 Search PubMed.
- D. Yang and B. C. Gates, ACS Catal., 2019, 9, 1779–1798 CrossRef CAS.
- A. Bagno and G. Scorrano, J. Am. Chem. Soc., 1988, 110, 4577–4582 CrossRef CAS.
- M. J. Raymond, C. S. Slater and M. J. Savelski, Green Chem., 2010, 12, 1826–1834 RSC.
- A. Babayigit, A. Ethirajan, M. Muller and B. Conings, Nat. Mater., 2016, 15, 247–251 CrossRef CAS PubMed.
- Y. Tao, G. Huang, H. Li and M. R. Hill, ACS Sustain. Chem. Eng., 2019, 7, 13627–13632 CrossRef CAS.
- L. Lomba, E. Zuriaga and B. Giner, Curr. Opin. Green Sustainable Chem., 2019, 18, 51–56 CrossRef.
- M. Tobiszewski, J. Namieśnik and F. Pena-Pereira, Green Chem., 2017, 19, 1034–1042 RSC.
- A. del P. Sánchez-Camargo, M. Bueno, F. Parada-Alfonso, A. Cifuentes and E. Ibáñez, TrAC, Trends Anal. Chem., 2019, 118, 227–237 CrossRef.
- Y. Gu and F. Jérôme, Green Chem., 2010, 12, 1127–1138 RSC.
- J. Bińczak, K. Dziuba and A. Chrobok, Materials, 2021, 14, 2881 CrossRef PubMed.
- E. V. Ramos-Fernandez, A. Grau-Atienza, D. Farrusseng and S. Aguado, J. Mater. Chem. A, 2018, 6, 5598–5602 RSC.
- S. Cadot, L. Veyre, D. Luneau, D. Farrusseng and E. Alessandra Quadrelli, J. Mater. Chem. A, 2014, 2, 17757–17763 RSC.
- F. Fathieh, M. J. Kalmutzki, E. A. Kapustin, P. J. Waller, J. Yang and O. M. Yaghi, Sci. Adv., 2018, 4, 1–10 Search PubMed.
- P. A. Bayliss, I. A. Ibarra, E. Pérez, S. Yang, C. C. Tang, M. Poliakoff and M. Schröder, Green Chem., 2014, 16, 3796–3802 RSC.
- A. Permyakova, O. Skrylnyk, E. Courbon, M. Affram, S. Wang, U. H. Lee, A. H. Valekar, F. Nouar, G. Mouchaham, T. Devic, G. De Weireld, J. S. Chang, N. Steunou, M. Frère and C. Serre, ChemSusChem, 2017, 10, 1419–1426 CrossRef CAS PubMed.
- R. Peña-Rodríguez, E. Márquez-López, A. Guerrero, L. E. Chiñas, D. F. Hernández-González and J. M. Rivera, Mater. Lett., 2018, 217, 117–119 CrossRef.
- K. Matsuyama, M. Motomura, T. Kato, T. Okuyama and H. Muto, Microporous Mesoporous Mater., 2016, 225, 26–32 CrossRef CAS.
- A. López-Periago, O. Vallcorba, C. Frontera, C. Domingo and J. A. Ayllón, Dalton Trans., 2015, 44, 7548–7553 RSC.
- P. López-Domínguez, A. M. López-Periago, F. J. Fernández-Porras, J. Fraile, G. Tobias and C. Domingo, J. CO2 Util., 2017, 18, 147–155 CrossRef.
- J. M. Marrett, C. Mottillo, S. Girard, C. W. Nickels, J. L. Do, G. Dayaker, L. S. Germann, R. E. Dinnebier, A. J. Howarth, O. K. Farha, T. Friščić and C. J. Li, Cryst. Growth Des., 2018, 18, 3222–3228 CrossRef CAS.
- L. Peng, J. Zhang, Z. Xue, B. Han, X. Sang, C. Liu and G. Yang, Nat. Commun., 2014, 5, 1–7 Search PubMed.
- H. V. Doan, Y. Fang, B. Yao, Z. Dong, T. J. White, A. Sartbaeva, U. Hintermair and V. P. Ting, ACS Sustain. Chem. Eng., 2017, 5, 7887–7893 CrossRef CAS.
- X. Sang, J. Zhang, J. Xiang, J. Cui, L. Zheng, J. Zhang, Z. Wu, Z. Li, G. Mo, Y. Xu, J. Song, C. Liu, X. Tan, T. Luo, B. Zhang and B. Han, Nat. Commun., 2017, 8, 1–7 CrossRef CAS PubMed.
- C. Fan, H. Dong, Y. Liang, J. Yang, G. Tang, W. Zhang and Y. Cao, J. Cleaner Prod., 2019, 208, 353–362 CrossRef CAS.
- X. Luo, Z. Mai and H. Lei, Inorg. Chem. Commun., 2019, 102, 215–220 CrossRef CAS.
- W. Shang, X. Kang, H. Ning, J. Zhang, X. Zhang, Z. Wu, G. Mo, X. Xing and B. Han, Langmuir, 2013, 29, 13168–13174 CrossRef CAS PubMed.
- A. López-Periago, P. López-Domínguez, J. Pérez Barrio, G. Tobias and C. Domingo, Microporous Mesoporous Mater., 2016, 234, 155–161 CrossRef.
- T. O. Abodunrin, M. Kloda, J. Demel and M. Taddei, Dalton Trans., 2023, 52, 5865–5869 RSC.
- Z. Hu, I. Castano, S. Wang, Y. Wang, Y. Peng, Y. Qian, C. Chi, X. Wang and D. Zhao, Cryst. Growth Des., 2016, 16, 2295–2301 CrossRef CAS.
- H. Chevreau, A. Permyakova, F. Nouar, P. Fabry, C. Livage, F. Ragon, A. Garcia-Marquez, T. Devic, N. Steunou, C. Serre and P. Horcajada, CrystEngComm, 2016, 18, 4094–4101 RSC.
- B. Zhang, J. Zhang, C. Liu, X. Sang, L. Peng, X. Ma, T. Wu, B. Han and G. Yang, RSC Adv., 2015, 5, 37691–37696 RSC.
- M. Sánchez-Sánchez, N. Getachew, K. Díaz, M. Díaz-García, Y. Chebude and I. Díaz, Green Chem., 2015, 17, 1500–1509 RSC.
- Z. Hu, I. Castano, S. Wang, Y. Wang, Y. Peng, Y. Qian, C. Chi, X. Wang and D. Zhao, Cryst. Growth Des., 2016, 16, 2295–2301 CrossRef CAS.
- H. Reinsch, S. Waitschat, S. M. Chavan, K. P. Lillerud and N. Stock, Eur. J. Inorg. Chem., 2016, 2016, 4490–4498 CrossRef CAS.
- X. Qian, F. Sun, J. Sun, H. Wu, F. Xiao, X. Wu and G. Zhu, Nanoscale, 2017, 9, 2003–2008 RSC.
- M. Joharian, A. Morsali, A. Azhdari Tehrani, L. Carlucci and D. M. Proserpio, Green Chem., 2018, 20, 5336–5345 RSC.
- J. Jacobsen, B. Achenbach, H. Reinsch, S. Smolders, F. D. Lange, G. Friedrichs, D. De Vos and N. Stock, Dalton Trans., 2019, 48, 8433–8441 RSC.
- S. Waitschat, H. Reinsch and N. Stock, Chem. Commun., 2016, 52, 12698–12701 RSC.
- V. Benoit, R. S. Pillai, A. Orsi, P. Normand, H. Jobic, F. Nouar, P. Billemont, E. Bloch, S. Bourrelly, T. Devic, P. A. Wright, G. De Weireld, C. Serre, G. Maurin and P. L. Llewellyn, J. Mater. Chem. A, 2016, 4, 1383–1389 RSC.
- J. B. Decoste, G. W. Peterson, B. J. Schindler, K. L. Killops, M. A. Browe and J. J. Mahle, J. Mater. Chem. A, 2013, 1, 11922–11932 RSC.
- S. S. Y. Chui, S. M. F. Lo, J. P. H. Charmant, A. G. Orpen and I. D. Williams, Science, 1999, 283, 1148–1150 CrossRef CAS PubMed.
- G. Majano and J. Pérez-Ramírez, Adv. Mater., 2013, 25, 1052–1057 CrossRef CAS PubMed.
- M. Jian, B. Liu, R. Liu, J. Qu, H. Wang and X. Zhang, RSC Adv., 2015, 5, 48433–48441 RSC.
- Z. Chen, X. Wang, T. Islamoglu and O. K. Farha, Inorganics, 2019, 7, 56 CrossRef CAS.
- H. Y. Guan, R. J. LeBlanc, S. Y. Xie and Y. Yue, Coord. Chem. Rev., 2018, 369, 76–90 CrossRef CAS.
- S. Abou-Shehada, J. H. Clark, G. Paggiola and J. Sherwood, Chem. Eng. Process.: Process Intensif., 2016, 99, 88–96 CrossRef CAS.
- A. Capuzzo, M. E. Maffei and A. Occhipinti, Molecules, 2013, 18, 7194–7238 CrossRef CAS PubMed.
- I. A. Ibarra, P. A. Bayliss, E. Pérez, S. Yang, A. J. Blake, H. Nowell, D. R. Allan, M. Poliakoff and M. Schröder, Green Chem., 2012, 14, 117–122 RSC.
- B. Li, W. Guo, W. Song and E. D. Ramsey, J. Chem. Eng. Data, 2016, 61, 2128–2134 CrossRef CAS.
- M. F. Dapaah and B. Liu, J. Inorg. Organomet. Polym. Mater., 2020, 30, 581–595 CrossRef CAS.
- C. Domingo and P. Subra-Paternault, Supercritical Fluid Nanotechnology: Advances and Applications in Composites and Hybrid Nanomaterials, CRC Press, 2016 Search PubMed.
- N. Portolés-Gil, S. Gowing, O. Vallcorba, C. Domingo, A. M. López-Periago and J. A. Ayllón, J. CO2 Util., 2018, 24, 444–453 CrossRef.
- N. Portolés-Gil, A. Lanza, N. Aliaga-Alcalde, J. A. Ayllón, M. Gemmi, E. Mugnaioli, A. M. López-Periago and C. Domingo, ACS Sustain. Chem. Eng., 2018, 6, 12309–12319 CrossRef.
- M. Dašić, I. Stanković and K. Gkagkas, Phys. Chem. Chem. Phys., 2019, 21, 4375–4386 RSC.
- A. Figoli, T. Marino, S. Simone, E. Di Nicolò, X. M. Li, T. He, S. Tornaghi and E. Drioli, Green Chem., 2014, 16, 4034–4059 RSC.
- P. Isosaari, V. Srivastava and M. Sillanpää, Sci. Total Environ., 2019, 690, 604–619 CrossRef CAS PubMed.
- T. Erdmenger, C. Guerrero-Sanchez, J. Vitz, R. Hoogenboom and U. S. Schubert, Chem. Soc. Rev., 2010, 39, 3317–3333 RSC.
- H.-C. Oh, S. Jung, I.-J. Ko and E.-Y. Choi, in Recent Advancements in the Metallurgical Engineering and Electrodeposition, IntechOpen, 2018 Search PubMed.
- B. Zhang, J. Zhang and B. Han, Chem. – Asian J., 2016, 11, 2610–2619 CrossRef CAS PubMed.
- H. Yu, D. Xu and Q. Xu, Chem. Commun., 2015, 51, 13197–13200 RSC.
- M. B. Comba, Y. H. Tsai, A. M. Sarotti, M. I. Mangione, A. G. Suárez and R. A. Spanevello, Eur. J. Org. Chem., 2018, 2018, 590–604 CrossRef CAS.
- F. Paquin, J. Rivnay, A. Salleo, N. Stingelin and C. Silva, J. Mater. Chem. C, 2015, 3, 10715–10722 RSC.
- J. E. Camp, ChemSusChem, 2018, 11, 3048–3055 CrossRef CAS PubMed.
- X. Huang, S. Kudo and J. ichiro Hayashi, Fuel Process. Technol., 2019, 191, 29–35 CrossRef CAS.
- T. W. Bousfield, K. P. R. Pearce, S. B. Nyamini, A. Angelis-Dimakis and J. E. Camp, Green Chem., 2019, 21, 3675–3681 RSC.
- J. Sherwood, M. De bruyn, A. Constantinou, L. Moity, C. R. McElroy, T. J. Farmer, T. Duncan, W. Raverty, A. J. Hunt and J. H. Clark, Chem. Commun., 2014, 50, 9650–9652 RSC.
- J. Zhang, G. B. White, M. D. Ryan, A. J. Hunt and M. J. Katz, ACS Sustain. Chem. Eng., 2016, 4, 7186–7192 CrossRef CAS.
- M. A. Rasool and I. F. J. Vankelecom, Green Chem., 2019, 21, 1054–1064 RSC.
- S. Santoro, F. Ferlin, L. Luciani, L. Ackermann and L. Vaccaro, Green Chem., 2017, 19, 1601–1612 RSC.
- M. Mondal and U. Bora, New J. Chem., 2016, 40, 3119–3123 RSC.
- C. T. Zhang, R. Zhu, Z. Wang, B. Ma, A. Zajac, M. Smiglak, C. N. Xia, S. L. Castle and W. L. Wang, RSC Adv., 2019, 9, 2199–2204 RSC.
- A. Pellis, F. P. Byrne, J. Sherwood, M. Vastano, J. W. Comerford and T. J. Farmer, Green Chem., 2019, 21, 1686–1694 RSC.
- A. V. Dubey and A. V. Kumar, ACS Sustain. Chem. Eng., 2018, 6, 14283–14291 CrossRef CAS.
- L. S. Germann, A. D. Katsenis, I. Huskić, P. A. Julien, K. Užarević, M. Etter, O. K. Farha, T. Friščić and R. E. Dinnebier, Cryst. Growth Des., 2020, 20, 49–54 CrossRef CAS.
- G. Ayoub, B. Karadeniz, A. J. Howarth, O. K. Farha, I. Lilović, L. S. Germann, R. E. Dinnebier, K. Užarević and T. Friščić, Chem. Mater., 2019, 31, 5494–5501 CrossRef CAS.
- T. Friščić, C. Mottillo and H. M. Titi, Angew. Chem., 2020, 132, 1030–1041 CrossRef.
- Y. Li, H. Zhang, Y. Chen, L. Huang, Z. Lin and Z. Cai, ACS Appl. Mater. Interfaces, 2019, 11, 22492–22500 CrossRef CAS PubMed.
- J. Huo, B. Luo and Y. Chen, ACS Omega, 2019, 4, 22504–22513 CrossRef CAS PubMed.
- S. Zhuang, Y. Liu and J. Wang, J. Hazard. Mater., 2020, 383, 121126 CrossRef CAS PubMed.
- Z. D. Li, H. Q. Zhang, X. H. Xiong and F. Luo, J. Solid State Chem., 2019, 277, 484–492 CrossRef CAS.
- X. Zhong, W. Liang, Z. Lu and B. Hu, Appl. Surf. Sci., 2020, 504, 144403 CrossRef CAS.
- Z. You, N. Zhang, Q. Guan, Y. Xing, F. Bai and L. Sun, J. Inorg. Organomet. Polym. Mater., 2020, 30, 1966–1979 CrossRef CAS.
- M. Afshari and M. Dinari, Synthesis of New Imine-Linked Covalent Organic Framework as High Efficient Absorbent and Monitoring the Removal of Direct Fast Scarlet 4BS Textile Dye Based on Mobile Phone Colorimetric Platform, Elsevier B.V., 2020, vol. 385 Search PubMed.
- M. Dinari and M. Hatami, Novel N-riched Crystalline covalent Organic Framework as a Highly Porous Adsorbent for Effective Cadmium Removal, Elsevier B.V., 2019, vol. 7 Search PubMed.
- W. Wang, S. Deng, L. Ren, D. Li, W. Wang, M. Vakili, B. Wang, J. Huang, Y. Wang and G. Yu, ACS Appl. Mater. Interfaces, 2018, 10, 30265–30272 CrossRef CAS PubMed.
- X. F. Lu, W. H. Ji, L. Yuan, S. Yu and D. S. Guo, Ind. Eng. Chem. Res., 2019, 58, 17660–17667 CrossRef CAS.
- Y. Li, C. Wang, S. Ma, H. Zhang, J. Ou, Y. Wei and M. Ye, ACS Appl. Mater. Interfaces, 2019, 11, 11706–11714 CrossRef CAS PubMed.
- L. Li, J. Hu, X. Shi, M. Fan, J. Luo and X. Wei, Environ. Sci. Pollut. Res., 2016, 23, 17880–17900 CrossRef CAS PubMed.
- S. Yu, X. Wang, H. Pang, R. Zhang, W. Song, D. Fu, T. Hayat and X. Wang, Chem. Eng. J., 2018, 333, 343–360 CrossRef CAS.
- S. Bae, R. N. Collins, T. D. Waite and K. Hanna, Environ. Sci. Technol., 2018, 52, 12010–12025 CrossRef CAS PubMed.
- X. Liu, H. Pang, X. Liu, Q. Li, N. Zhang, L. Mao, M. Qiu, B. Hu, H. Yang and X. Wang, Innov, 2021, 2, 100076 CAS.
- S. Naeimi and H. Faghihian, Sep. Purif. Technol., 2017, 175, 255–265 CrossRef CAS.
- Y. Wang, Z. Liu, Y. Li, Z. Bai, W. Liu, Y. Wang, X. Xu, C. Xiao, D. Sheng, J. Diwu, J. Su, Z. Chai, T. E. Albrecht-Schmitt and S. Wang, J. Am. Chem. Soc., 2015, 137, 6144–6147 CrossRef CAS PubMed.
- Y. Peng, H. Huang, D. Liu and C. Zhong, ACS Appl. Mater. Interfaces, 2016, 8, 8527–8535 CrossRef CAS PubMed.
- C. Kang, Y. Peng, Y. Tang, H. Huang and C. Zhong, Ind. Eng. Chem. Res., 2017, 56, 13866–13873 CrossRef CAS.
- C. Xiao and S. Wang, Radionuclide Sequestration by Metal–Organic Frameworks, Elsevier Inc., 2019. vol. 11 Search PubMed.
- Y. Wu, B. Li, X. Wang, S. Yu, H. Pang, Y. Liu and X. Liu, Chem. Eng. J., 2019, 378, 122105 CrossRef CAS.
- A. J. De Decker, K. Folens, J. De Clercq, M. Meledina, G. Van Tendeloo, G. Du Laing, V. Der Voort, D. D. Jeroen, F. Karel, D. C. Jeriffa, M. Meledina, G. Van Tendeloo, D. L. Gijs and V. Der Voort, J. Hazard. Mater., 2017, 335, 1–9 CrossRef PubMed.
- U. Vi, J. Mater. Chem. A, 2014, 3, 525–534 Search PubMed.
- L. Li, W. Ma, S. Shen, H. Huang, Y. Bai and H. Liu, ACS Appl. Mater. Interfaces, 2016, 8, 31032–31041 CrossRef CAS PubMed.
- L. Chen, Z. Bai, L. Zhu, L. Zhang, Y. Cai, Y. Li, W. Liu, Y. Wang, L. Chen, J. Diwu, J. Wang, Z. Chai and S. Wang, ACS Appl. Mater. Interfaces, 2017, 9, 32446–32451 CrossRef CAS PubMed.
- L. Zhang, L. L. Wang, L. Le Gong, X. F. Feng, M. B. Luo and F. Luo, J. Hazard. Mater., 2016, 311, 30–36 CrossRef CAS PubMed.
- W. Yang, Z. Q. Bai, W. Q. Shi, L. Y. Yuan, T. Tian, Z. F. Chai, H. Wang and Z. M. Sun, Chem. Commun., 2013, 49, 10415–10417 RSC.
- Y. Wu, H. Pang, W. Yao, X. Wang, S. Yu, Z. Yu and X. Wang, Sci. Bull., 2018, 63, 831–839 CrossRef CAS PubMed.
- B. J. Riley, J. D. Vienna, D. M. Strachan, J. S. McCloy and J. L. Jerden, J. Nucl. Mater., 2016, 470, 307–326 CrossRef CAS.
- M. H. Zeng, Q. X. Wang, Y. X. Tan, S. Hu, H. X. Zhao, L. S. Long and M. Kurmoo, J. Am. Chem. Soc., 2010, 132, 2561–2563 CrossRef CAS PubMed.
- D. F. Sava, M. A. Rodriguez, K. W. Chapman, P. J. Chupas, J. A. Greathouse, P. S. Crozier and T. M. Nenoff, J. Am. Chem. Soc., 2011, 133, 12398–12401 CrossRef CAS PubMed.
- M. Garai and C. T. Yavuz, Chem, 2019, 5, 750–752 CAS.
- W. Hua, T. Zhang, M. Wang, Y. Zhu and X. Wang, Chem. Eng. J., 2019, 370, 729–741 CrossRef CAS.
- W. Lin, Z. Zhao, F. Yang, Z. Liu, F. Tan, M. Xie, Y. Ma and L. Meng, Miner. Eng., 2021, 164, 106831 CrossRef CAS.
- M. A. Hamouda, S. M. Sheta, R. R. Sheha, A. T. Kandil, O. I. Ali and S. M. El-Sheikh, RSC Adv., 2022, 12, 13103–13110 RSC.
- Z. J. Li, Z. Yue, Y. Ju, X. Wu, Y. Ren, S. Wang, Y. Li, Z. H. Zhang, X. Guo, J. Lin and J. Q. Wang, Inorg. Chem., 2020, 59, 4435–4442 CrossRef CAS PubMed.
- A. A. Berseneva, C. R. Martin, V. A. Galitskiy, O. A. Ejegbavwo, G. A. Leith, R. T. Ly, A. M. Rice, E. A. Dolgopolova, M. D. Smith, H. C. Zur Loye, D. P. Diprete, J. W. Amoroso and N. B. Shustova, Inorg. Chem., 2020, 59, 179–183 CrossRef CAS PubMed.
- C. Volkringer, C. Falaise, P. Devaux, R. Giovine, V. Stevenson, F. Pourpoint, O. Lafon, M. Osmond, C. Jeanjacques, B. Marcillaud, J. C. Sabroux and T. Loiseau, Chem. Commun., 2016, 52, 12502–12505 RSC.
- S. J. Lee, T. U. Yoon, A. R. Kim, S. Y. Kim, K. H. Cho, Y. K. Hwang, J. W. Yeon and Y. S. Bae, J. Hazard. Mater., 2016, 320, 513–520 CrossRef CAS PubMed.
- S. E. Gilson, M. Fairley, P. Julien, A. G. Oliver, S. L. Hanna, G. Arntz, O. K. Farha, J. A. Laverne and P. C. Burns, J. Am. Chem. Soc., 2020, 142, 13299–13304 CrossRef CAS PubMed.
- L. L. Wang, F. Luo, L. L. Dang, J. Q. Li, X. L. Wu, S. J. Liua and M. B. Luoa, J. Mater. Chem. A, 2015, 3, 13724–13730 RSC.
- W. Liu, X. Dai, Z. Bai, Y. Wang, Z. Yang, L. Zhang, L. Xu, L. Chen, Y. Li, D. Gui, J. Diwu, J. Wang, R. Zhou, Z. Chai and S. Wang, Environ. Sci. Technol., 2017, 51, 3911–3921 CrossRef CAS PubMed.
- D. A. O'Sullivan and W. Lepkowski, Chem. Eng. News, 1990, 68, 42–61 CrossRef.
- N. Zhang, L. Y. Yuan, W. L. Guo, S. Z. Luo, Z. F. Chai and W. Q. Shi, ACS Appl. Mater. Interfaces, 2017, 9, 25216–25224 CrossRef CAS PubMed.
- M. Carboni, C. W. Abney, S. Liu and W. Lin, Chem. Sci., 2013, 4, 2396–2402 RSC.
- J. Cai, X. Wang, Y. Zhou, L. Jiang and C. Wang, Phys. Chem. Chem. Phys., 2016, 18, 10864–10867 RSC.
- M. Roushani, Z. Saedi and Y. M. Baghelani, Environ. Nanotechnol., Monit. Manage., 2017, 7, 89–96 Search PubMed.
- B. Liu, M. Jian, R. Liu, J. Yao and X. Zhang, Colloids Surf., A, 2015, 481, 358–366 CrossRef CAS.
- C. O. Audu, H. G. T. Nguyen, C. Y. Chang, M. J. Katz, L. Mao, O. K. Farha, J. T. Hupp and S. T. Nguyen, Chem. Sci., 2016, 7, 6492–6498 RSC.
- K. Li, S. Lin, Y. Li, Q. Zhuang and J. Gu, Angew. Chem., 2018, 130, 3497–3501 CrossRef.
- P. F. Shi, B. Zhao, G. Xiong, Y. L. Hou and P. Cheng, Chem. Commun., 2012, 48, 8231–8233 RSC.
- Y. Peng, H. Huang, Y. Zhang, C. Kang, S. Chen, L. Song, D. Liu and C. Zhong, Nat. Commun., 2018, 9, 187 CrossRef PubMed.
- X. Luo, L. Ding and J. Luo, J. Chem. Eng. Data, 2015, 60, 1732–1743 CrossRef CAS.
- Z. Q. Li, J. C. Yang, K. W. Sui and N. Yin, Mater. Lett., 2015, 160, 412–414 CrossRef CAS.
- H. R. Fu, Z. X. Xu and J. Zhang, Chem. Mater., 2015, 27, 205–210 CrossRef CAS.
- X. X. Lv, L. L. Shi, K. Li, B. L. Li and H. Y. Li, Chem. Commun., 2017, 53, 1860–1863 RSC.
- M. F. Alam, Z. A. Begum, Y. Furusho, H. Hasegawa and I. M. M. Rahman, Microchem. J., 2022, 181, 107637 CrossRef CAS.
- J. O. Ighalo, F. O. Omoarukhe, V. E. Ojukwu, K. O. Iwuozor and C. A. Igwegbe, Cleaner Chem. Eng., 2022, 3, 100042 CrossRef.
- D. DeSantis, J. A. Mason, B. D. James, C. Houchins, J. R. Long and M. Veenstra, Energy Fuels, 2017, 31, 2024–2032 CrossRef CAS.
- R. Schmalensee, in Barriers to New Competition, Harvard University Press, 1956, pp. 53–113 Search PubMed.
- A. Deacon, L. Briquet, M. Malankowska, F. Massingberd-Mundy, S. Rudić, T. l. Hyde, H. Cavaye, J. Coronas, S. Poulston and T. Johnson, Commun. Chem., 2022, 5, 1–10 CrossRef PubMed.
|
This journal is © The Royal Society of Chemistry 2023 |
Click here to see how this site uses Cookies. View our privacy policy here.