DOI:
10.1039/D3RA00595J
(Paper)
RSC Adv., 2023,
13, 10610-10620
Immobilization of heavy metals in tannery sludge by the formation of tobermorite in subcritical water treatment with rice husk silica†
Received
28th January 2023
, Accepted 29th March 2023
First published on 4th April 2023
Abstract
Tannery sludge, heavy metals (HMs) enriched hazardous solid waste, is produced extensively in many regions of the world. Even though the sludge is hazardous, it can be considered a material resource, if organic matter and HMs in the sludge can be stabilized to minimize its negative environmental impacts. This research aimed to evaluate the efficacy of using subcritical water (SCW) treatment for tannery sludge treatment through immobilization and thus reduction of HMs to mitigate their potential environmental risk and toxicity. HMs in the tannery sludge were analyzed by inductively coupled plasma mass spectrometry (ICP-MS) and the average concentration of HMs (mg kg−1) was found in the following decreasing order of Cr (12
950) > Fe (1265) > Cu (76) > Mn (44) > Zn (36) > Pb (14) with very high Cr concentration. The result of toxicity characteristics leaching procedure and sequential extraction procedure tests revealed that the raw tannery sludge leachate contained 11.24 mg L−1 Cr, which classified the raw tannery sludge into a very high-risk category. After SCW treatment, the concentration of Cr in leachate was reduced to 1.6 mg L−1 indicating risk reduction to a low-risk category. The eco-toxicity levels of other HMs also decreased considerably after SCW treatment. X-ray diffractometry (XRD) and scanning electron microscopy (SEM) analysis were employed to identify the effective immobilizing substances formed in the SCW treatment process. The favorable formation of immobilizing orthorhombic tobermorite (Ca5Si6O16(OH)2·4H2O) at 240 °C in the SCW treatment process was confirmed by XRD and SEM analysis. The results confirmed that the formation of 11 Å tobermorite is capable of strongly immobilizing HMs in the SCW treatment process. Further, both orthorhombic 11 Å tobermorite and 9 Å tobermorite were successfully synthesized by SCW treatment on a mixture of tannery sludge including rice husk silica and Ca(OH)2 with water under rather mild conditions. Hence, it can be concluded that SCW treatment of tannery sludge with supplementary silica from rice husk can effectively immobilize the HMs and significantly reduce their environmental risk through tobermorite formation.
1. Introduction
Tanning industries generate huge quantities of wastewater and solid wastes throughout the whole process. The treatment process of tanning effluents also produces a bulk quantity of solid materials called tannery sludge. This sludge is usually a by-product from wastewater treatment, typically generated through chemical precipitation with the addition of lime and inorganic coagulant, which contains approximately 500–5500 mg L−1 trivalent chromium (Cr).1,2 Most of the leather production industries around the world use Cr salts for leather tanning.3 Therefore, tannery sludge may contain high concentrations of Cr which is a potential contaminant of soil, surface water, and groundwater unless it is properly treated and disposed of.4 In addition to Cr, tannery sludge often contains elevated concentrations of other heavy metals (HMs) such as arsenic (As), nickel (Ni), cobalt (Co), copper (Cu), zink (Zn), iron (Fe), and cadmium (Cd) due to the use of Cr salt, syntans, dyes, pigments, and re-tanning agents that are used in tanning processes.5,6 Such HMs possess chronic adverse impacts on human health as well as the ecosystem because of their non-biodegradable nature, long biological half-lives, and potential for bioaccumulation.7 Therefore, the tannery sludge needs to be treated for removal or immobilization of HMs before being discharged into the environment. Moreover, the volume and mass of tannery sludge need to be reduced due to the scarcity of available landfill sites for its final disposal.
Various methods such as chemical extraction, bio-leaching, adsorption, and bioremediation have been applied for the removal of HMs from the tannery sludge and other waste such as tailing leachate.8–12 However, such methods are tedious and time-consuming and it has been observed that they are difficult to control for removal efficiency in the actual operation. Immobilization, in this regard, is a promising technique for treating heavy metal-contaminated sludge and soil and thus reducing the HMs toxicity in the environment.13 The technique is widely employed due to its high efficiency, simplicity, and cost-effectiveness.14 Subcritical water (SCW) treatment has recently gained widespread recognition as a potential technique for the pretreatment of organic sludge due to its simplicity and affordability.15 SCW may be effective in both immobilization of HMs in contaminated sludge and the reduction in its volume and mass. In contrast, a reduction in volume and/or mass means leads to an increase in the concentrations of HMs in the residual. Therefore, stable immobilization of HMs in the residue from tannery sludge is crucial. Several immobilizing agents, such as magnetite, biochar, sulfide, carbonate, silicate, and phosphate have been applied for the immobilization of HMs in sludge. The formation of tobermorite in the SCW process on tannery sludge can be an effective way to immobilize and stabilize HMs. Tobermorite is calcium silicate hydrated that is a carbonate–silicate-based mineral having the chemical formula of Ca5Si6O16(OH)2·4H2O or Ca5Si6(O, OH)18·5H2O. Tobermorite is a naturally occurring crystalline mineral and is known to immobilize a wide range of HMs with very high efficiency. It can also be synthesized under hydrothermal (subcritical water, SCW) conditions via the reaction of silica and calcium at moderately high temperatures as applied in Autoclaved Lightweight Aerated Concrete (ALAC) panel manufacturing process. ALAC is rich in tobermorite that provides strength behavior. Additional advantages of SCW treatment on sludge include stabilization of organic fraction and reduction in mass and volume of the final residue. Dewaterability is also improved which contributes to further mass and volume reduction in the final residue.
To develop a practical and feasible waste treatment system, the possibility of simultaneous treatment of multiple wastes should be incorporated. Since silica is needed for the formation of tobermorite, co-SCW treatment of tannery sludge with rice husk silica can be advantageous for both immobilization of HMs and the management of rice husk waste, which is one of the major agricultural solid wastes. Previously some researchers10,16,17 used tobermorite or tobermorite-based materials for the removal of HMs such as Pb, Cd, Cr, Cu, and other chemicals such as phosphate and ammonium from water. However, to the best of our knowledge, the immobilization and stabilization of HMs in tannery sludge using tobermorite have not been reported yet. The formation of tobermorite by facile SCW treatment of tannery sludge with rice husk-mediated amorphous silica, calcium oxide, and NaOH solution is expected to be able to provide means for tannery sludge stabilization before land application. Nevertheless, the risk of HMs in tannery sludge after SCW treatment with rice husk silica through tobermorite formation has not also been investigated yet. Therefore, the primary objective of the research is to evaluate and control the environmental risk of HMs in tannery sludge by SCW treatment with rice husk silica, and confirm that the sludge is safe before land application. Based on this consideration, the investigation on the immobilization of HMs in tannery sludge and the influential factor in SCW treatment is of great importance for risk control of HMs in the sludge to improve the risk reduction effects of SCW on HMs. The formation of tobermorite under SCW conditions is considered to be one of the causal factors for the immobilization of HMs in treated sludge. Therefore, investigating the formation of tobermorite under SCW conditions is necessary and urgent.
2. Materials and methods
2.1. Collection and preparation of tannery sludge
Tannery sludge samples were collected from Leather Industry, Merlimao industrial state, Merlimao Melaka, Malaysia. Samples were collected randomly from different sludge dumping sites. The sampling period represents normal process conditions for the leather industry. The wet weight of the individual sample was around 10 kg. After sampling, the sludge was crushed into small particles by a ball mill and stored at 4 °C in a sealed plastic bag for further experiments.
2.2. Preparation of amorphous silica from rice husk
About 10 kg of rice husk was collected from local farmers in Tsukuba, Japan for experimental purposes. The collected rice husk underwent a series of steps that included washing with a 5 M sodium dodecyl sulfate solution, air drying overnight, soaking in a 0.5 M sulfuric acid solution, and rinsing with tap water, distilled water, and Milli-Q water in that order. The cleaned rice husk samples were air-dried overnight and then dried in an oven at 105 °C for 24 h. 2 g per crucible of dry rice husk was kept in a muffle furnace, incinerated at 650 °C for 2 h to remove organic matters, and placed in a desiccator for cooling.18,19 The final product, amorphous silica from rice husk, was used in the experiments as the supplementary source of silicon as silica (SiO2) for tobermorite formation.
2.3. SCW treatment of tannery sludge
At first, amorphous silica and calcium oxide were mixed with 10 g of tannery sludge powder in a beaker at a ratio of 0.81. Then, 6 mL of 2 M NaOH solution was added to the mixture, and Milli-Q water was used to make the total volume to 100 mL. A bench-top SCW reactor system developed and manufactured by OM Labtech Company Limited (Model: MS200-C, OM Labtech, Tochigi, Japan) was used for SCW studies. The hot water inside the rector acts as a catalyst in a saturated pressure condition (ESI Fig. S1†). SCW experiments were conducted with 10 g of the mixture of tannery sludge powder and amorphous silica loaded into the reactor and treated under SCW conditions (200 to 280 °C) under the saturation steam pressure for 30 to 540 min. The predetermined SCW treatment conditions are summarized in ESI Tables 1 and 2.† The pressure range was between 1.5 MPa (200 °C) and 6.4 MPa (280 °C). The reactor was cooled below 100 °C after the SCW treatment for the removal of the treated sample. The raising temperature and the rapid cooling system follow a curve shown in ESI Fig. S2.† After solid–liquid separation by vacuum filtration with a 0.6-micron pore-size membrane filter, the collected solid residue was oven-dried at 105 °C for 24 h, crushed to powder, and stored in a sealed plastic bag at 4 °C until further experiments and analyses.
2.4. Physiochemical and elemental analysis of tannery sludge
The pH of the samples was determined by shaking 5 g of the sample in 100 mL of deionized water for 16–24 h followed by direct measurement with a pH meter (Sigma-Aldrich, USA). The calibration of the pH meter was carried out by standard buffer solutions of 5020 Reference Standard for pH 4 and Hanna HI 6010 for pH 10. To determine the water content of the sample, the mass of the wet sample was precisely measured before drying in an oven at 105 °C for 24 h. After drying, the sample was kept in a desiccator for about 30 min to cool and weighed. The water content was calculated by eqn (1). |
Water content = ((w − d)/w) × 100%
| (1) |
where, w = initial mass (g) of the sample as delivered and d is the mass (g) of the sample after drying. The volatile matter, which is indicative of organic matter in the sample, and ash content were determined after incinerating the dry sample in a muffle furnace at 600 to 650 °C for 3 h to decompose organic matter. The molybdenum blue and UV-visible spectrophotometer techniques were used to quantify the total amount of soluble phosphorus (P) and total soluble nitrogen (N) in the water fraction, respectively. To determine carbon (C), hydrogen (H), nitrogen (N), and oxygen (O) contents in the sample, an ultimate analysis was carried out using a CHNO analyzer (Flash 2000, Thermo scientific Fisher, USA).
For heavy metals (HMs) analysis, raw tannery sludge and treated sludge samples were prepared by the acid digestion method. About 1 g of dry solid was first incinerated in a muffle furnace at 550 °C for 4 h. Then, 25 mL of a 3
:
1 mixture of HNO3 and HClO4 was added to the resulting organic matter-free solid sample under cooled conditions and the mixture was gradually heated on a hot plate at 100–110 °C for ∼4 h. The resulting colorless solution was dried almost entirely by evaporation. After the digestion process was finished and the residue had cooled, 0.01 N HNO3 solution was added to make the final solution volume of 25 mL. HMs contents in the prepared samples were then determined by inductively coupled plasma mass spectrometry (ICP-MS) (ELAN DRC-e, PerkinElmer, USA). The raw sludge and treated sludge were sequentially extracted for HMs as per the procedure shown in Fig. 1 and analyzed accordingly. Sequential extraction using a similar method has been documented elsewhere.20 The concentration of HMs in the analyzed samples was calculated by the following eqn (2).
|
 | (2) |
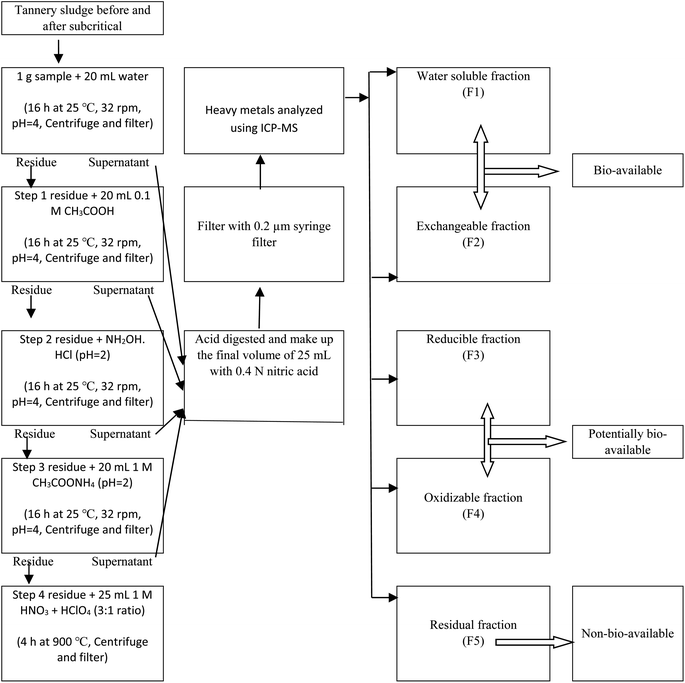 |
| Fig. 1 Sequential extraction procedure of heavy metals. | |
2.5. Risk assessment code (RAC) and ecotoxicity
A risk assessment code based on the metals in the first two fractions (F1 + F2), which are vulnerable to variations in salt content, pH of sludge, and the environment, was employed for a quantitative evaluation of the ecotoxicity of HMs in sludge.21 The risk index (RI), which is defined as the ratio of each metal in these two fractions (F1 + F2) to the overall concentration in the sludge [RI = ((Fl + F2)/total) × 100], was used to assess the ecotoxicity of HMs.22,23 Then, HMs in sludge may be categorized as having no risk, low risk, medium risk, high risk, and extremely high risk by using RAC (ESI Table S3†).
2.6. Analysis for tobermorite
The formation and presence of tobermorite were identified by X-ray diffraction (XRD) analysis, which produces characteristic patterns of the materials when an X-ray beam is diffracted by the material's surface. Using an agate mortar and pestle, the raw materials and tobermorite were crushed, pulverized to a fine powder <5 μm, and mounted on aluminum plate sample holders with a volume of 0.1 cm3. The samples were analyzed with a powder diffractometer (Smart Lab, Rigaku, Japan) operated in Bragg–Brentano geometry with Cu-kα radiation at 40 mA and 40 kV, and a secondary monochromator. The diffraction patterns were recorded in the 2θ angle range of 10–70° with a scanning step of 0.02°. The powder diffraction file database provided by the International Center for Diffraction Data (ICDD) was used to compare the diffraction patterns to the standard line pattern. The tannery sludge and synthetic product were also inspected by XRD analysis.
To determine how the surface morphology and porous structure of the samples change due to the conversion of sludge, a scanning electron microscope (SEM) (JSM.7800F Prime, JEOL, Japan) was used and the images were captured carefully at different magnifications.
3. Results and discussion
3.1. Elemental contents in tannery sludge, and chemical compositions of rice husk
The concentration of chemical elements in the tannery sludge collected from the tannery industry is presented in Table 1. Total carbon (19.7%), total hydrogen (3.65%), total nitrogen (2.63%), and silica (5300 mg kg−1) contents in the samples were determined on the dry sample. The average concentration of HMs was found in the following decreasing order of Cr > Fe > Cu > Mn > Zn > Pb. The highest concentration was observed for Cr (12
950 mg kg−1), which might be due to the effects of unplanned tanning activities and tannery waste dumping from the industries.24 The effluent discharged from tannery industries is the main source of Cr that is deposited in the sludge.25 It was also found that Ca content was high, while silica content was very low. These two elements are the basic components of tobermorite. High concentration of aluminum is due to the effects of coagulant (alum or poly-aluminum chloride) used in the wastewater treatment process. Other heavy metal concentrations spread over a very wide range, from 1 to more than 4500 mg kg−1. A similar wide variation in the concentration range of HMs was reported in the literature.26–28 The difference in the concentration of HMs in the industry is due to different raw materials and the operational processes applied.29
Table 1 Elemental contents in the tannery sludge samples
|
Elements |
Content |
Metals [mg kg−1 – dry matter] |
Al |
133 100 |
Ca |
30 300 |
Cr |
12 950 |
Si (as SiO2) |
5300 |
Fe |
1265 |
K |
400 |
Cu |
76 |
Mn |
44 |
Zn |
36 |
Pb |
14 |
Mg |
2500 |
Other elements [% dry matter] |
C |
19.7 |
H |
3.65 |
N |
2.63 |
O |
45.4 |
S |
1.55 |
P |
0.09 |
The chemical compositions of rice husks are presented in ESI Table S4.† The organic materials in rice husk consist of mainly cellulose (31.12%), hemicellulose (24.48%), and lignin (22.34%). The moisture and ash content were 7.86 and 13.87%, respectively. The rice husk ash contains several metal oxides (e.g., SiO2, K2O, MgO, Al2O3, CaO, Fe2O3) with the highest and lowest % of silica (93.19) and Fe2O3 (0.58), respectively (Table S4†).
3.2. Speciation, bioavailability, and eco-toxicity of HMs in the tannery sludge
The sequential extraction method provides useful information on the potential mobility and association of HMs with different phases of sludge.30,31 The fractional distribution of HMs in the tannery sludge is depicted in Fig. 2. The distribution of each HM, which is associated with different fractions in the tannery sludge, varies depending on the metals. In the case of Cr, the water-soluble fractions (F1) and the residual fraction (F5) were 14.3 and 22.7%, respectively. F1 of Pb was less than 5%, while 51% of it was found in the reducible fraction. Among the HMs studied, Mn was found with the highest water-soluble fraction.
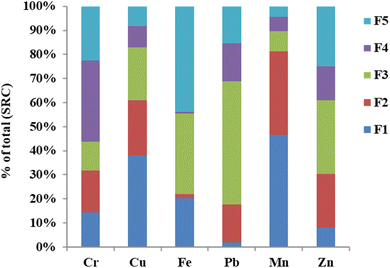 |
| Fig. 2 Fractional distribution of heavy metals in the tannery sludge, F1: water-soluble fraction, F2: exchangeable fraction, F3: reducible fraction, F4: oxidizable fraction, and F5: residual fraction. | |
The fraction distribution of HMs can be used to assess the bioavailability and toxicity of the HMs. Fig. 3 shows the distribution of availability of HMs. The criteria for their availability are summarized in ESI Table S5.† It was found that for HMs in raw tannery sludge before SCW treatment, the highest bioavailable fractions (Cbio) were observed with Mn (81.4%), Cu (61.1%), and Cr (31.7%) (Fig. 3). The potentially bioavailable fractions (Cp-bio) of Cr and Pb were 45.7 and 67.0%, respectively, which were the highest among the HMs studied. Considering the sum of bioavailable fraction and potentially bioavailable fraction, and the high concentration of Cr in the tannery sludge, the human health risk of Cr in the tannery sludge is high.
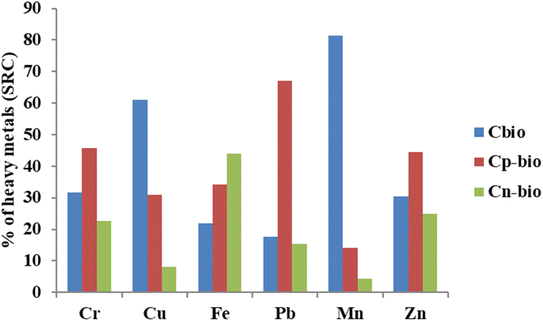 |
| Fig. 3 Distribution of heavy metals in bioavailability (Cbio: bioavailable fraction, Cp-bio: potentially bioavailable fraction, and Cn-bio: not bioavailable fraction). | |
The eco-toxicity results based on the RAC model are depicted in Fig. 4. As shown, Mn (81.0%), Cu (61.0%), Cr (31.7%), and Zn (30.5%) are regarded to be at high risk to the environment. Pb and Fe in the tannery sludge are considered to be at medium risk in this study. RI values also indicate their mobility, and hence toxicity in the environment. Based on the RAC results, the tannery sludge is judged not to be suitable for direct soil application. The risk and ecotoxicity of HMs must be reduced, especially for Cr because its original concentration is very high followed by high toxicity. The tannery sludge is very toxic, and its level of risk is very high if directly applied to the soil without treatment.
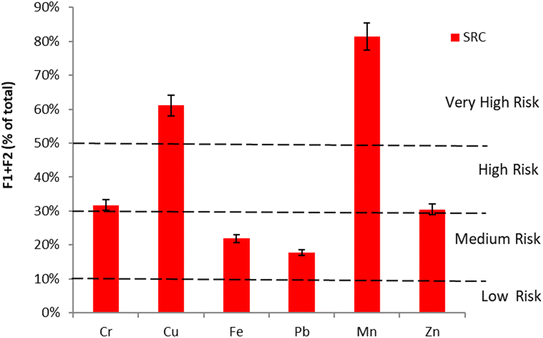 |
| Fig. 4 Eco-toxicity of heavy metals in tannery sludge by risk assessment code (RAC) model based on the scale of metals in (F1 + F2). | |
3.3. Effects of SCW on HMs immobilization
Even though the increase in the concentration of HMs in the collected residue of sludge after SCW due to the liquefaction of organic matter and improved dewaterability implies a possibility of increased potential risk, the evaluation must consider their fractionations and current forms. The current forms of HMs are often more significant because they control the HMs' bioavailability, mobility, and ecotoxicity. Different fractions of HMs in sludge and hydrochar made from sludge may be extracted, and these fractions may represent the HMs' current forms. The results are shown in ESI Fig. S3.† SCW process affected positively on immobilization of the HMs in the tannery sludge. The effects of immobility on HMs are somewhat related to the dehydration process. Some weakly bound HMs (in fractions Fl and F2) might have transferred with the migration of water, resulting in partial release or dissolution into liquid portions and partial fixation into sludge through precipitation and recombination. The suggested immobilization process is supported by the fractional transformation and redistribution of HMs.21
Stabilization and extraction occurred simultaneously during SCW treatment. Co-mixing of rice husk silica and tannery sludge treated at different SCW temperatures had a great influence on the redistribution of HMs in fractions and the reduction of ecotoxicity and bioavailability (ESI Fig. S3†). After a treatment within SCW, the existing forms of all HMs changed and accumulated in F5. The effects were more apparent at higher temperatures at 240 °C and 280 °C than at 200 °C. SCW treatment significantly transferred all heavy metal species to F4 and F5 fractions that have no risk to the environment which is consistent with the findings of some previous studies.25,32
Immobilization may have occurred simultaneously in two pathways, which are chemical stabilization and physical encapsulation. ESI Fig. S3(C)† shows that weakly bounded forms (F1 and F2) of HMs decreased in the sludge residue after SCW treatment. Importantly, the F5 fraction had changed significantly for all HMs after SCW treatment, especially at 240 °C and 280 °C, implying that added silica and Ca formed a C–S–H gel, or C–S–H layered structures, which were imperfect layered structures of tobermorite. According to a study reported by Vespa et al.,33 HMs may firmly occupy three positions of the layered structure of the tobermorite.
3.4. Bioavailability assessment of HMs in tannery sludge before and after SCW
Ecotoxicity and bioavailability were evaluated using the percentage of HMs in Cbio, Cp-bio, and Cn-bio; the findings are shown in ESI Fig. S4.† HMs in F1 and F2, which represent the weakly bounded fractions, can easily be released into the environment. These two fractions recorded higher contents with Mn (81%), Cu (61.7%), Cr (31%), and Zn (30%) than Fe (20%) and Pb (17%). A large fraction of each HM existed in a potentially bioavailable form in the raw tannery sludge. However, after SCW treatment, the bioavailable fraction (Cbio) of HMs decreased. A notable decrease was found with concerned Cr, which was reduced from 31 to 8.7%, while Cu decreased from 61 to 15%, Fe from 21 to 16%, Pb from 17 to 8%, Mn from 81 to 20%, and Zn from 30 to 9%. The potentially bioavailable fraction (Cp-bio) decreased slowly with increasing temperature except for Cr at 240 °C. The Cp-bio value of Cr decreased at 200 °C, then increased at 240 °C in contrast to the other metals. It was shown that the immobilization of Cr, Pb, and Mn was due to transformation from the Cbio fraction to the Cp-bio fraction in the treated tannery sludge. The Cn-bio fraction of HMs showed a significant increase after SCW treatment, which is crucial for the immobilization of HMs. The HMs content in the residual phase, Cn-bio, which is not likely to leach or degrade (as classified as non-toxic), increased sharply with SCW temperature, indicating that treatment temperature is a decisive factor for the immobilization of HMs in the tannery sludge.32
3.5. RAC analysis of HMs in tannery sludge before and after SCW
The RI value of each HM before and after the SCW is presented in Fig. 5. After SCW treatment at 200 °C with the addition of rice husk silica, the risk levels of Cr and Zn were reduced by one step down from high risk to medium risk. Cu was also reduced by one step down from very high risk to high risk. The effects of SCW treatment at 240 °C show that the high-risk level of Cr was reduced by one step down from the medium-risk zone to the low-risk zone, while Mn goes one step down from very high risk to high risk. Except for Fe, which risk level increased by 1% at the treatment of sludge at 240 °C. The risk level of Cr declined by 2% from the previous level at 280 °C. In the case of Pb, the risk level declined by 4%, which might be due to higher temperatures where Pb was immobilized in the residual fraction. The residual fraction of Pb increased with the increasing temperature leading to Pb immobilization,15,25 which indicated that the risk level of Pb was reduced. Mn also declined from the high-risk to a medium-risk zone.
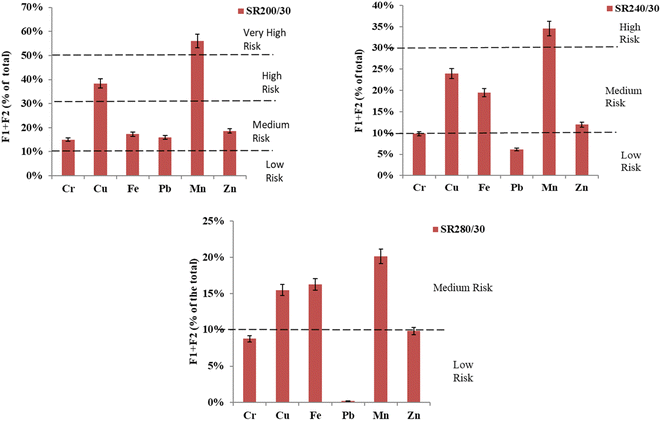 |
| Fig. 5 Eco-toxicity levels by risk assessment code (RAC) model SCW at 200, 240, and 280 °C, for 30 min. | |
3.6. XRD analysis
XRD pattern of raw tannery sludge showed that the major crystalline phase is quartz and calcium (ESI Fig. S5†). However, as shown in ESI Fig. S6,† a new phase of 9 Å tobermorite having a distinctive peak was observed by XRD, implying that tobermorite was formed in the SCW reaction with the presence of Ca and silica. Since the CaO/SiO2 molar ratio in the starting material was set at 0.8 and in excess quantities, it is expected that tobermorite-based porous material was first formed by the added silica serving as the starting material that was incorporated with NaOH solution. SCW treatment temperature, which was up to 240 °C, was apparently high enough to promote tobermorite formation in the presence of alkali such as NaOH.
After heating at 200 °C for 360 min, a crystal of orthorhombic tobermorite was formed, which is denoted as 11 Å tobermorite. Reflection data corresponding to the orthorhombic polytypes (lattice parameters: a = 11.27, b = 7.35, c = 22.7, α = 90°, β = 90°, γ = 90°) was detected. After heating at 240 °C for 180 min with 200% of silica, a crystal of orthorhombic tobermorite, 11 Å tobermorite, was formed. Reflection data corresponds to the orthorhombic polytypes, where a = 11.27, b = 7.42, c = 22.55, α = 90°, β = 90°, γ = 90° were obtained. Under different SCW conditions, triclinic tobermorite, one of the clino tobermorite types, was formed. It is known that there are two polytypes, i.e., monoclinic and triclinic. Triclinic polytypes were observed in the specimen after SEW treatment under the conditions SR200/540, SR240/180, SR240/360, SR200/360/D, and SR240/360/D %, which are all 9 Å tobermorite. However, in the case of treatment at SR240/180/D, a well-developed crystal of tobermorite, 11 Å tobermorite, was detected. The XRD pattern agrees closely with that found by Magaw and Kelsey.34
The XRD patterns of the treated sludge show that the main diffraction peaks are in good arrangement with 9 Å and 11 Å tobermorite (ESI Fig. S6†). In ESI Fig. S6(E),† the main diffraction peaks are in good arrangement with the JCPDS card no. 00-019-1364 for 11 Å tobermorite at the treatment temperature of 240 °C, reaction time 180 min, and double doses of calcium and silica. Minor peaks of calcite (CaCO3) were also presented during the formation of the tobermorite. The treated sludge with higher doses of calcium and silica may suggest an increased reaction rate of the tobermorite. Particularly narrow and sharp peaks indicate the tobermorite phase's strong crystallinity. The basal spacing of the 002-diffraction peak implies the high formation of the tobermorite phase, which is to be 11 Å. Tobermorite crystallization is known to be affected by the precursor of C–S–H gel, additional silica may enhance the formation of C–S–H gel to tobermorite.
3.7. Effects of temperature, reaction time, and Ca/SiO2 ratio on tobermorite formation
The effects of reaction temperature on tobermorite formation were investigated. Based on the XRD analysis data, there is no tobermorite in SRC. The quantity of tobermorite grows dramatically with time while the amount of quartz continues to decline.35 However, when SCW treatment was applied, it was observed that large quartz was present at 200 °C/30 min. However, at 280 °C/30 min, the tobermorite peak appeared. It is reported that the tobermorite is unstable at high temperatures and may be converted to walostine, which has a different crystal structure. In Fig. 6A and B, it is shown that among various peaks, the peaks of tobermorite at 2θ of 29.5 was relatively stable. The intensity of peaks increased to 7–8 and 28.5–29 when the curing temperature reached at 240 °C. As the temperature increased from 200 to 240 °C, the peak of SiO2 progressively reduced, suggesting that the curing temperature may speed up the interaction between Ca(OH)2 and SiO2. These phenomena proved that the temperature of 240 °C is favorable to form tobermorite.
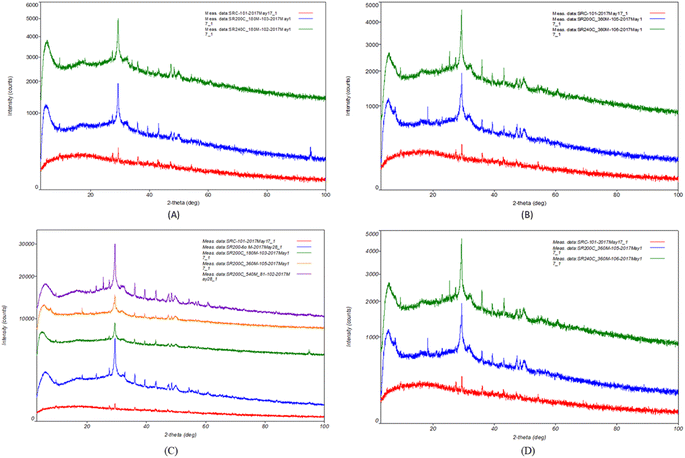 |
| Fig. 6 Effects of SCW temperature on XRD patterns. (A): 200 °C and 240 °C for 180 min; (B): 200 °C and 240 °C for 360 min. Effects of SCW reaction times on XRD patterns. (C): 200 °C, for 0, 60, 180, and 360 min; (D): 200 °C and 240 °C, for 360 min. | |
The effect of reaction time on the phase evolution was investigated at 200 °C and the results are presented in Fig. 6C and D. After 60 min, no sludge was found. The reflection peaks of the tobermorite become sharper as treatment time increases, indicating that longer durations result in greater crystallinity. After 540 minutes of treatment, the quartz reflection peaks entirely disappeared, indicating that the reaction had finished. The XRD patterns of the final samples show that as the reaction time increased, the amount of tobermorite formation increases sharply. A longer curing time is required for quartz to complete the reaction and produce pure tobermorite. The temperature of 200 °C and 540 min reaction time showed the best performance to form the tobermorite. Effects of the Ca/SiO2 ratio were examined. The result showed that adding more silica reduces the curing time to form the tobermorite. SR240C/180/D produced the best tobermorite according to XRD and SEM results.
3.8. SEM image observation on immobilization of HMs within tobermorite
The SEM photographs of tannery sludge before and after SCW treatment are shown in Fig. 7 and 8. Needle or sheet-like crystal, which is characteristic of tobermorite, was observed in the SEM images. Fig. 8A shows the distinctive morphology of tobermorite formed in SCW treatment at 240 °C and for 180 min added silica on double doses (SR240/180/D). The observed morphology of tobermorite 11 Å matches the research work of Nair et al.36 Whereas the SCW reaction at 240 °C and for 360 min with a double dose of silica, tobermorite 9 Å was also formed (Fig. 8C). It was observed that both orthorhombic 11 Å and 9 Å tobermorite were successfully synthesized by SCW treatment on the mixture of tannery sludge, rice husk silica, and Ca(OH)2 with water under rather mild conditions.
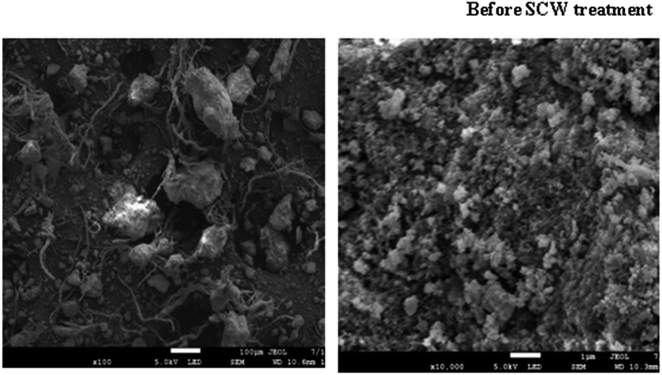 |
| Fig. 7 SEM photograph of a solid portion of raw tannery sludge. | |
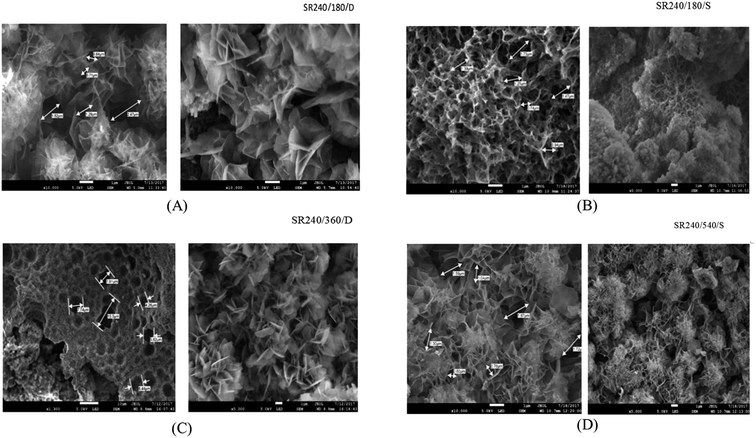 |
| Fig. 8 SEM photograph of the solid portion of tannery sludge SCW. (A): 240 °C for 180 min, D; (B): 240 °C for 180 min, S; (C): 240 °C for 360 min, D; (D): 240 °C for 540 min, S. | |
4. Conclusions
The present research demonstrates a comprehensive assessment of the immobilization of heavy metals (HMs) in tannery sludge by the formation of tobermorite (Ca5Si6O16(OH)2·4H2O) in subcritical water (SCW) treatment with rice husk silica. The results showed that most of the metals, especially Mn Cu, Cr, and Zn in tannery sludge remain in bioavailable form and also pose high environmental risks when evaluated by the risk assessment code and risk index. However, the cumulative of the bioavailable and potentially bioavailable fractions along with a high Cr concentration in the tannery sludge demonstrated its high human health risk. Pb and Fe showed to be a medium risk in sludge. However, the concentrations and risk of all the metals decreased after SCW treatment, especially when the sludge was treated at 240 and 280 °C. The results of SCW treatment effects revealed that 11 Å tobermorite was formed at 240 °C for 180 min treatment with a CaO/SiO2 ratio of 200%. In addition, 9 Å tobermorite was formed under SCW conditions of [SCW treatment (SR)/treatment temperature/reaction time/CaO & SiO2 ratio]: SR200C/360/200%, SR240C/360/200%, SR200C/540, SR240/360, and SR240/180. According to the XRD analysis confirmation, the favorable formation of 9 Å tobermorite was found in the SCW treatment process when the sludge was treated at 240 °C for 360 min with a double dose of silica (SR240/360/D) while 11 Å tobermorite was formed favorably in SCW treatment at 240 °C for 180 min with an added silica on double doses (SR240/180/D). Hence, it can be concluded that tannery sludge amendment with rice husk silica formed tobermorite successfully under SCW conditions which can effectively immobilize HMs reducing their environmental toxicity. This treated sludge could be used safely in land applications. However, it is recommended that future studies can focus on the formation of tobermorite within lower temperatures and the evaluation of the mechanism of trapping HMs within the crystal structure of tobermorite under SCW conditions.
Author contributions
Ayesha Akter: conceptualization, methodology, data curation, writing – original draft. Masafumi Goto and Megat Johari Megat Mohd Noor: investigation, supervision, resources, writing – reviewing and editing. Ahmed Parvez: data checking and validation, writing – reviewing and editing. Shamsunnahar Khanam: reviewing and editing. Md. Abu Bakar Siddique: writing – reviewing and editing. Md Faysal Hossain: reviewing and editing. Tapos Kormoker: conceptualization, investigation, validation, writing – original draft, reviewing and editing. All authors read and approved the final manuscript.
Conflicts of interest
The authors declare that they have no known competing financial interests or personal relationships that could have appeared to influence the work reported in this paper.
Acknowledgements
The authors are thankful to the authority of the University of Tsukuba, Japan, and Universiti Teknologi Malaysia, Malaysia for providing laboratory facilities to complete this study.
References
- P. P. Pathe, T. Nandy and S. N. Kaul, Properties of chromium sludge from chrome tan wastewater, in Wastewater Management with Special Reference to Tanneries, ed. S. N. Kaul, T. Nandy, L. Szpyrkowitz, A. Gautam and D. R. Khanna, Discovery Publishing House, New Delhi., 2005, pp. 342–346 Search PubMed.
- L. Mao, N. Deng, L. Liu, H. Cui and W. Zhang, Chem. Eng. J., 2016, 294, 1–8, DOI:10.1016/j.cej.2016.02.102.
- L. Alibardi and R. Cossu, Waste Manage., 2016, 52, 202–211, DOI:10.1016/j.wasman.2016.04.008.
- J. C. Thomson, J. Azariah and A. G. R. Viji, Environ. Monit. Assess., 1999, 18, 359–368 Search PubMed.
- Z. Houshyar, A. B. Khoshfetrat and E. Fatehifar, Chem. Eng. J., 2012, 191, 59–65, DOI:10.1016/j.cej.2012.02.053.
- E. Kiliç, R. Puig, G. Baquero, J. Font, S. Colak and D. J. Gürler, J. Hazard. Mater., 2011, 192(1), 393–401, DOI:10.1016/j.jhazmat.2011.05.040.
- B. Wilson and F. B. Pyatt, Ecotoxicol. Environ. Saf., 2007, 66, 224–231, DOI:10.1016/j.ecoenv.2006.02.015.
- A. Pathak, M. G. Dastidar and T. R. Sreekrishnan, J. Environ. Sci. Health, Part A, 2008, 43(4), 402–411, DOI:10.1080/10934520701795624.
- J. E. D. Silva, A. P. Paiva, D. Soares, A. Labrinchaa and F. J Castro, J. Hazard. Mater., 2005, 120(1), 113–118, DOI:10.1016/j.jhazmat.2004.12.008.
- Z. Wang, L. Xu, N. Su, S. Zhu and D. Wu, Environ. Sci. Pollut. Res., 2023 DOI:10.1007/s11356-023-26269-x.
- K. Z. Elwakeel, M. M. Ahmed, A. Akhdhar, M. G. Sulaiman and Z. A. Khan, Desalin. Water Treat., 2022, 272, 50–74, DOI:10.5004/dwt.2022.28834.
- A. Benettayeb, A. Morsli, K. Z. Elwakeel, M. F. Hamza and E. Guibal, Appl. Sci., 2021, 11(18), 8377, DOI:10.3390/app11188377.
- M. F. Hossain, M. S. Islam, M. A. Kashem, K. T. Osman and Y. Zhou, Chemosphere, 2021, 279, 130570, DOI:10.1016/j.chemosphere.2021.130570.
- P. Devi and A. K. Saroha, Bioresour. Technol., 2014, 162, 308–315, DOI:10.1016/j.biortech.2014.03.093.
- L. Li, Z. R. Xu, C. Zhang, J. Bao and X. Dai, Bioresour. Technol., 2012, 121, 169–175, DOI:10.1016/j.biortech.2012.06.084.
- Z. Wang, Z. Huang, B. Zheng, D. Wu and S. Zheng, J. Environ. Chem. Eng., 2022, 10(3), 107400, DOI:10.1016/j.jece.2022.107400.
- Z. Wang, Z. Huang, S. Zheng, D. Wu and W. Cai, Desalin. Water Treat., 2021, 235, 209–220, DOI:10.5004/dwt.2021.27639.
- R. A. Bakar, R. Yahya and S. N. Gan, Procedia Chem., 2016, 19, 189–195, DOI:10.1016/j.proche.2016.03.092.
- A. Ayesha, M. Goto, M. J. M. M. Noor, A. K. M. M. Islam, U. Motoo, Z. Z. Ya and A. Parvez, Chem. Eng. Trans., 2017, 56, 265–270, DOI:10.3303/CET1756045.
- R. Poykio, H. Nurmesniemi, T. Kuokkanen and P. Perämäki, Chemosphere, 2006, 65(11), 2122–2129, DOI:10.1016/j.chemosphere.2006.06.018.
- W. Shi, Behavior of heavy metals in sewage sludge during hydrothermal treatment, Doctoral thesis, University of Tsukuba, 2016 Search PubMed.
- H. Huang, X. Yuan, G. Zeng, H. Zhu, H. Li, Z. Liu, H. Jiang, L. Leng and W. Bi, Bioresour. Technol., 2011, 102, 10346–10351, DOI:10.1016/j.biortech.2011.08.117.
- K. P. Singh, D. Mohan, V. K. Singh and A. Malik, J. Hydrol., 2005, 312, 14–27, DOI:10.1016/j.jhydrol.2005.01.021.
- M. S. Islam, T. Kormoker, M. Mojumder, S. E. Anika, M. T. Islam, D. H. Hemy, U. S. Mimi, R. Proshad, M. H. Kabir and A. M. Idris, Toxin Rev., 2022, 41(3), 752–767, DOI:10.1080/15569543.2021.1925919.
- M. N. Islam, H. Y. Jung and J. H. Park, J. Environ. Manage., 2015, 163, 262–269, DOI:10.1016/j.jenvman.2015.08.007.
- E. Pantazopoulou, O. Zebiliadou, M. Mitrakas and A. Zouboulis, Waste Manage., 2017, 61, 327–336, DOI:10.1016/j.wasman.2017.01.009.
- M. T. Montañés, R. Sánchez-Tovar and M. S. Roux, J. Environ. Manage., 2014, 143, 71–79, DOI:10.1016/j.jenvman.2014.04.026.
- M. S. Islam, M. K. Ahmed, M. Raknuzzaman, M. Habibullah-Al-Mamun and G. K. Kundu, J. Geochem. Explor., 2017, 172, 41–49, DOI:10.1016/j.gexplo.2016.09.006.
- P. Venkateswaran, S. Vellaichamy and K. Palanivelu, Int. J. Environ. Sci. Technol., 2007, 4(4), 497–504, DOI:10.1007/BF03325986.
- H. Chen, Y. Wang, Q. Lyu, A. Ai, Y. Fu, H. Tian and Y. Kuang, Fertil. Steril., 2015, 103(5), 1194–1201, DOI:10.1016/j.fertnstert.2015.02.020.
- M. Vemic, F. Bordas, G. Guibaud, E. Joussein, J. Labanowski, P. N. Lens and E. D. Van Hullebusch, Waste Manage., 2015, 38, 303–311, DOI:10.1016/j.wasman.2014.12.021.
- W. Shi, C. Liu, D. Ding, Z. Lei, Y. Yang, C. Feng and Z. Zhang, Bioresour. Technol., 2013, 137, 18–24, DOI:10.1016/j.biortech.2013.03.106.
- M. Vespa, R. Dähn and E. Wieland, Phys. Chem. Earth, 2014, 70, 32–38, DOI:10.1016/j.pce.2014.01.001.
- H. D. Megaw and C. H. Kelsey, Nature, 1956, 177(4504), 390, DOI:10.1038/177390a0.
- L. Galvánková, J. Másilko, T. Solný and E. Štěpánková, Procedia Eng., 2016, 151, 100–107, DOI:10.1016/j.proeng.2016.07.394.
- A. Nair, A. A. Juwarkar and S. Devotta, J. Hazard. Mater., 2008, 152(2), 545–553, DOI:10.1016/j.jhazmat.2007.07.054.
|
This journal is © The Royal Society of Chemistry 2023 |
Click here to see how this site uses Cookies. View our privacy policy here.