DOI:
10.1039/D2NJ04884A
(Paper)
New J. Chem., 2023,
47, 297-306
Palladium nanoparticles immobilized on COF-modified honeycomb chitosan microcapsules as catalysts for the Suzuki reaction and p-nitrophenol reduction†
Received
4th October 2022
, Accepted 20th November 2022
First published on 21st November 2022
Abstract
Preparation of macroscopic objects using covalent organic frameworks (COFs) is challenging. However, it is imperative to fully utilize their customizable pore structure to synthesize nanomaterials with controlled size and dispersion. Here, CS/ZIF-8@COF microcapsules were successfully synthesized by growing COFs in situ within the pore channels of honeycomb chitosan microcapsules. COFs of different structures could grow uniformly and form fibrous or vesicle-like structures on the inner walls of chitosan microcapsules. COFs can significantly prevent chitosan from swelling in water and enhance the stability of CS/ZIF-8 microcapsules. The inherent porosity of COFs facilitates the immobilization and dispersion of palladium nanoparticles, and a large number of N atoms in their structure effectively prevent the aggregation and shedding of palladium. The prepared CS/ZIF-8@COFa-4@Pd showed excellent catalytic activity in the reduction of p-NP (Kapp = 1.1 min−1) and the Suzuki coupling (TOF = 7.1 × 104) reaction. The CS/ZIF-8@COFa-4@Pd catalyst exhibited no obvious loss of catalytic activity after five repeated uses.
1. Introduction
Covalent organic frameworks (COFs) are crystalline porous materials constructed by strong covalent bonds between organic compounds.1,2 They are characterized by improved chemical and thermal stabilities, permanent porosity, homogeneous pore sizes, high surface areas, chemically modifiable surfaces, and diverse structures.3 COFs, as an emerging highly porous crystalline polymer, have been widely used in organic catalysis, gas storage, photocatalytic water splitting, energy storage, drug delivery, proton conduction, and sensing.4–9 COFs have a larger surface area than most materials, such as porous polymers, molecular sieves, carbon materials, silica, and metal oxides. They also have better acid–base stability than most metal–organic framework materials.10 Therefore, COFs are a promising catalyst supporting material. Despite the many advantages of COFs mentioned above, the preparation process of COFs mostly requires organic solvents with high boiling points (such as mesitylene or 1,4-dioxane), high temperatures, and long reaction times.11 In addition, the COFs obtained are usually in the form of a powder (microcrystal), so it is difficult to separate the catalysts with COFs as carriers from the reaction system.12,13
To overcome the above difficulties, Xu and Zhao synthesized microporous, mesoporous, and porous COF materials using Fe3O4 and polystyrene microspheres as templates and applied them to electrocatalysis, synthetic reactions of p-aminophenol, and coupling reactions.14,15 In addition, the properties of covalent organic framework materials allow them to be prepared as macroscopically separable objects. Li et al. reported the successful growth of a covalent organic skeleton on the surface of a GO aerogel by a hydrothermal reaction and its application in organic solvent adsorption and capacitors.16 Zhu et al., through the in situ growth of COF-366-Fe on a three-dimensional graphene aerogel (GA), successfully prepared COF-366-Fe/GA aerogel composites and showed an ultra-sensitive response in the detection of NO.17 Yao et al., for the first time, designed and synthesized a novel covalently linked RGO-COF photocatalyst for enhanced hydrogen evolution.18
Chitosan is a natural polymer material and is cheap, readily available, endogenous, biodegradable, and green. Due to the abundant –NH2 and –OH functional groups in chitosan molecules, they can achieve strong compounding ability and electrostatic interaction with transition metals and have a broad range of applications in the areas of catalysis and adsorption. Chitosan aerogels/microcapsules are considered ideal carriers for the preparation of catalysts due to their hydrophilic surface (containing amino and hydroxyl groups) and large surface areas. Chitosan aerogels are extensively applied in the adsorption and catalysis fields and photocatalysis, as well as in the preparation of electrode materials, capacitor materials, and medical hydrogels. For example, a graphene/chitosan aerogel is prepared from GO and chitosan, and the chitosan aerogel supports a metal–organic framework as a high-performance capacitor material.19,20 MoS2 was grown in situ on the surface of the chitosan aerogel as a high-performance photocatalyst.21
The palladium-catalyzed Suzuki cross-coupling reaction is one of the most commonly used methods for the construction of carbon–carbon (C–C) bonds in organic synthesis.22,23 It has a wide range of promising applications in the synthesis of polymer materials, agrochemicals, pharmaceutical intermediates, etc., and can be synthesized with readily available reactants under mild conditions.24p-Nitrophenol (p-NP) is highly toxic and bioresistant, and it is difficult to remove it from the environment due to its recalcitrance and stability. In contrast, the corresponding reduction product, p-aminophenol (p-AP), is easily degraded25,26 or recycled as a widely used chemical material in organic synthesis, pharmaceutical development and materials science. Compared with traditional homogeneous catalysts, non-homogeneous catalysts have the advantages of easy separation, greenness and reusability, and therefore, the development of non-homogeneous catalysts has received increasing attention in recent decades.27–29 However, these non-homogeneous catalysts usually suffer from less exposure of metal active sites and limited reactant accessibility compared to homogeneous catalysts.30 Therefore, the development of high-performance catalysts that combine the advantages of high activity and selectivity of homogeneous catalysts with the high durability and the ease of separation of inhomogeneous catalysts is important for Suzuki coupling reactions and reduction of nitro compounds.
In this work, CS/ZIF-8@COF composites were successfully produced by growing covalent organic frameworks in situ on the surface of chitosan aerogel microspheres. A new catalyst CS/ZIF-8@COFa-4@Pd was prepared by loading nanoparticles of palladium in the CS/ZIF-8@COFa-4 composite. CS/ZIF-8@COFa-4@Pd showed excellent catalytic activity in the Suzuki coupling reaction and the reduction reaction of p-nitrophenol owing to the large specific surface area and the macroporous structure in the chitosan aerogel, which improved the mass transfer efficiency in the catalytic process. The inherent microporous structure of the COF shell layer effectively enhances the dispersion of Pd nanoparticles, which effectively increases the quantity of catalytically active sites. More notably, COFs can potentially prevent the swelling of chitosan in water or an acid medium and increase the stability of CS/ZIF-8 microcapsules. In addition, the CS/ZIF-8@COFa-4@Pd catalyst has no obvious loss of catalytic activity after repeated use five times. The universality study shows that the method can be applied to the growth of various COFs on the surface of the chitosan aerogel. This study provides a new idea for preparing novel multifunctional chitosan-covalent organic skeleton composites. Also, it gives a new possibility for preparing COF-loaded superfine metal nanoparticles with good dispersibility and stability.
2. Experimental section
2.1. Synthesis of spherical COFs
Several 10 mL centrifuge tubes with a screw cap were spiked with 1,3,5-tris(4-aminophenyl)benzene (TPB) (0.02 mmol) and 2,5-dihydroxy-p-benzaldehyde (0.03 mmol) and then 5 mL of acetonitrile was separately charged into each tube. The centrifuge tubes containing the mixture were sonicated for 1 min to dissolve the building blocks completely. Afterward, 0.4 mL of glacial acetic acid (12 M) was added in each tube, shaken thoroughly, and allowed to react at room temperature for 72 h. The yellow microspheres were collected by filtration and cleaned three times with acetonitrile and ethanol. The COFa-4 microspheres were then dried under a high vacuum for 24 h. In addition, COFa-1, COFa-2, COFa-3, COFb-1, COFb-2, COFb-3, and COFb-4 were synthesized using the same method (Fig. 1).
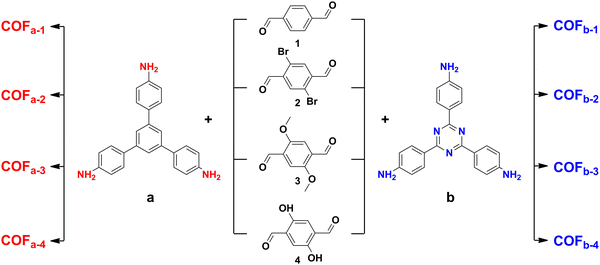 |
| Fig. 1 Molecular structures of building units for COFs. | |
2.2.
In situ growth of the COFs on the inner wall of CS/ZIF-8 (CS/ZIF-8@COF)
Several 50 mL centrifuge tubes with a screw cap were charged with CS/ZIF-8 (0.5 g), 1, 3, 5-tris(4-aminophenyl)benzene (TPB) (0.2 mmol) and 2,5-dihydroxy-p-benzaldehyde (0.3 mmol), and then 20 mL of acetonitrile was added to each test tube separately. Then 20 mL of acetonitrile was added to each tube and sonicated for 1 min to dissolve the building blocks completely. Afterward, glacial acetic acid (12 M) was added to each tube, mixed thoroughly, and allowed to react at room temperature for 72 h. The yellow microspheres were collected by filtration and repeatedly washed with acetonitrile and ethanol. Then, the CS/ZIF-8@COFa-4 microspheres were dried under a high vacuum for 24 h. In addition, CS/ZIF-8@COFa-1, CS/ZIF-8@COFa-2, CS/ZIF-8@COFa-3, CS/ZIF-8@COFb-1, CS/ZIF-8@COFb-2, CS/ZIF-8@COFb-3 and CS/ZIF-8@COFb-4 were synthesized using the same method (Fig. 2).
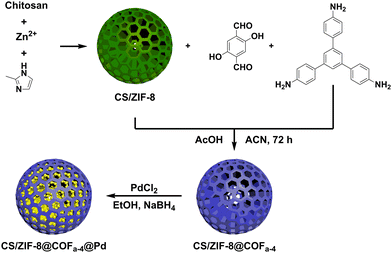 |
| Fig. 2 The preparation routes of the catalyst CS/ZIF-8@COFa-4@Pd. | |
2.3. Synthesis of the CS/ZIF-8@COFa-4@Pd aerogel microspheres
CS/ZIF-8@COFa-4 aerogel microspheres (1 g) were incorporated into 50 mL of ethanol containing 100 mg of palladium chloride (PdCl2) and were well mixed at room temperature for 24 h. Then, the newly prepared sodium borohydride solution was mixed into the system. Finally, the products obtained were filtered and repeatedly washed with ethanol to remove excess palladium.
2.4. The catalytic reaction of Suzuki coupling
A mixture of CS/ZIF-8@COFa-4@Pd (100 mg), Na2CO3 (2 mmol), phenylboronic acid (1.2 mmol), iodobenzene (1 mmol), and an appropriate solution of ethanol and water (1
:
1) was added to a pear-shaped flask. The reaction system was heated to 80 °C under magnetic stirring and reacted continuously for 4 h. After the completion of the reaction, the reaction system was extracted with ethyl acetate, and the organic phases were combined and dried overnight with anhydrous magnesium sulfate. The target product, biphenyl, was separated by column chromatography.
2.5. Catalytic reduction of p-nitrophenol
Under magnetic stirring, 1 mL of fresh NaBH4 solution (1 mg ml−1) was added to 5 mL of p-NP solution (1 mg mL−1) and stirred to mix thoroughly. CS/ZIF-8@COFa-4@Pd was then quickly added to the solution, and the extent to which the reaction proceeded was measured by inverse UV-Vis spectroscopy.
3. Results and discussion
3.1. Structural characterization of the CS/ZIF-8@COFs microspheres
The morphologies of the COFs and CS/ZIF-8@COFs were characterized by scanning electron microscopy (SEM). The COFs prepared at room temperature using different monomers mainly showed two structures, spherical and petal-shaped, as shown in Fig. 3(a1–a4 and c1–c4). The COFs prepared using TPB as the raw material were primarily spherical, with diameters between 200 nm and 500 nm. In contrast, the triazine-containing COFs designed with TAPT as the raw material showed petaloid (Fig. 3c1 and c3) and spherical structures (Fig. 3c2 and c4), and petal-shaped COFs have diameters of about 5 μm. As shown in Fig. 3(b1–b4 and d1–d4), the SEM images of CS/ZIF-8@COFs showed that the COF crystals were uniformly embedded on the inner walls of the CS/ZIF-8 channels and showed vesicular and linear morphologies, indicating the successful preparation of the CS/ZIF-8@COF composites. It is well known that the molecular structure of chitosan contains a large number of hydroxyl and amino groups, which have good hydrophilicity and are very easy to absorb water and swell in an aqueous solution, leading to a decrease in the mechanical properties of microspheres, which are difficult to be recycled when used as catalyst carriers. Therefore, the effect of the presence of the COF shell layer on the stability of the CS/ZIF-8@COFs was investigated. The CS/ZIF-8 and CS/ZIF-8@COFs microcapsules were immersed in an aqueous solution for 48 h, respectively. As shown in Fig. S1 (ESI†), CS/ZIF-8 exhibited significant swelling in aqueous solutions, increasing its volume to about twice than its original size and significantly reducing its mechanical properties. In contrast, the CS/ZIF-8@COF composites showed no swelling and maintained good morphology and excellent mechanical properties.
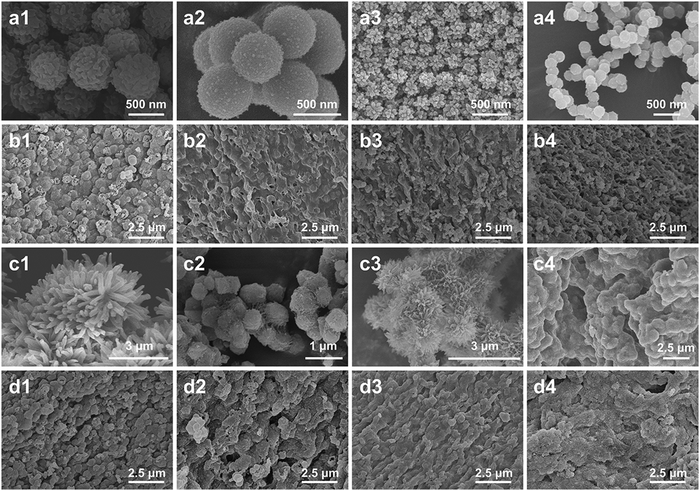 |
| Fig. 3 SEM images of COFa-1–COFa-4 (a1–a4), CS/ZIF-8@COFa-1-CS/ZIF-8@COFa-4 (b1–b4), COFb-1–COFb-4 (c1–c4) and CS/ZIF-8@COFb-1-CS/ZIF-8@COFb-4 (d1–d4). | |
3.2. Structure characterization of the CS/ZIF-8@COFa-4@Pd microspheres
The structure of the covalent organic framework grown in situ on the inner wall of honeycomb CS/ZIF-8 microspheres was observed by SEM. As shown in Fig. 4a1, the CS/ZIF-8 microcapsules are approximately 3 mm in diameter. The pores on the surface of the capsule are covered by chitosan and do not communicate with the outside world. The mechanical properties of the CS/ZIF-8 microcapsules were enhanced and hardened after cross-linking by glutaraldehyde. After intense agitation, the surface of the capsule was stripped of the overlying chitosan, revealing a honeycomb structure (Fig. 4a2). The pore size of the honeycomb structure is about 50 μm, and the thickness of the inner wall is 10 μm (Fig. S2, ESI†). COFa-4 is a spherical structure of approximately 400 nm in diameter, as shown in Fig. 4b1 and b2. COFa-4 grew mainly as spheres or vesicles in the pores of CS/ZIF-8 microcapsules and formed a shell layer, as shown in Fig. 4b3 and b4. More importantly, the introduction of COFa-4 improved the stability of the CS/ZIF-8 microcapsules in aqueous solutions, effectively avoiding their swelling in water (Fig. 4b3 and b4). Compared to ZIF-8, COFs have better stability in solvents. Therefore, the sustainability of the CS/ZIF-8 microcapsules in solvents can be effectively improved by introducing a COF shell layer.
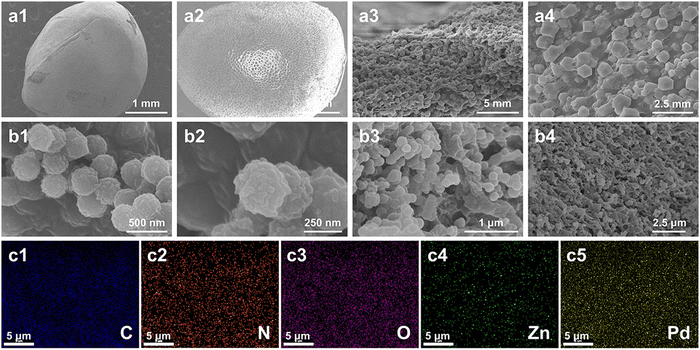 |
| Fig. 4 SEM images of CS/ZIF-8 (a1–a4), COFa-4 (b1 and b2), and CS/ZIF-8@COFa−4@Pd (b3 and b4) and EDS elemental mapping of CS/ZIF-8@COFa-4@Pd (c1–c5). | |
As shown in Fig. 4c1–c5, to clarify the elemental species and distribution state of CS/ZIF-8@COFa-4@Pd, an energy dispersive (EDS) mapping experiment was carried out. Elements C (Fig. 4c1), N (Fig. 4c2), O (Fig. 4c3), Zn (Fig. 4c4), and Pd (Fig. 4c5) were evenly distributed on the inner wall of the pore. No apparent agglomeration phenomenon was found for Pd NPs, indicating that the presence of COFa-4 could effectively improve the dispersion of Pd NPs, which would be conducive to enhancing the activity and selectivity of the catalyst.
The functional groups contained in the CS/ZIF-8@COFa-4@Pd composites were probed by FT-IR spectroscopy. As shown in Fig. 5, the absorption peak at 1307 cm−1 is attributed to the C–N stretching vibration of COFa-4, and the peak at 1590 cm−1 is the overlapping stretching vibration absorption peak of C
N and C
C (Fig. 5a).31,32 The peak at 3020 cm−1 belongs to the C–H bond stretching vibration of the benzene ring, and the methylene stretching vibration of the 2-methylimidazole ring causes the absorption peak at 2928 cm−1.
 |
| Fig. 5 FT-IR spectra of COFa-4 (a), CS/ZIF-8 (b), CS/ZIF-8@COFa-4 (c), and CS/ZIF-8@COFa-4@Pd (d). | |
N2 adsorption and desorption experiments of COFa-4, CS/ZIF-8, CS/ZIF-8@COFa-4, and CS/ZIF-8@COFa-4@Pd were carried out at 77 K, and the results showed that all of them showed type I isotherms (Fig. 6a). As shown in Fig. 6a, the N2 adsorption curves of CS/ZIF-8, CS/ZIF-8@COFa-4, and CS/ZIF-8@COFa-4@Pd, all four composites, increase rapidly at low pressures of 0–0.1, while, at pressures of 0.9–1.0, there is a clear hysteresis loop in the adsorption curves, indicating that the composite has a microporous structure. The pore size distribution of the CS/ZIF-8@COFa-4@Pd microcapsules is shown in Fig. 6b, and the pore size of CS/ZIF-8@COFa-4@Pd is mainly 1.4–1.7 nm in the microporous structure. Besides, it also contains a small number of mesopores with a pore size of 2.6 nm. The Brunauer–Emmett–Eller (BET) surface areas of COFa-4, CS/ZIF-8, CS/ZIF-8@COFa-4 and CS/ZIF-8@COFa-4@Pd are 95 m2 g−1, 713 m2 g−1, 621 m2 g−1, and 601 m2 g−1. The decrease of the BET surface area in CS/ZIF-8@COFa-4@Pd should be attributed to the introduction of COFa-4 and Pd NPs.
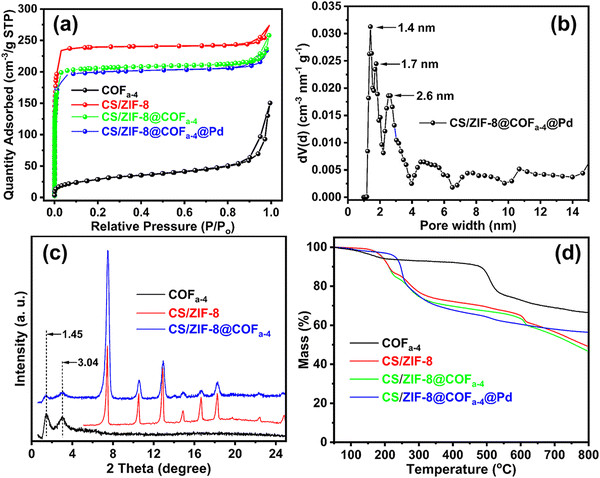 |
| Fig. 6 (a and b) Nitrogen sorption isotherms of COFa-4, CS/ZIF-8 and CS/ZIF-8@COFa-4. (c) XRD patterns and (d) TGA curves of COFa-4, CS/ZIF-8, CS/ZIF-8@COFa-4, and CS/ZIF-8@COFa-4@Pd. | |
The structure of the synthesized material was determined by powder X-ray diffraction (XRD). The XRD spectra of COFa-4 and CS/ZIF-8@COFa-4 show two peaks at 1.45° and 3.04°, respectively, as shown in Fig. 6c, which are considered reflections from the (100) plane. The relatively high intensity (100) peak reflects the high crystallinity of the spherical COFa-4.33 Furthermore, the XRD spectra of CS/ZIF-8@COFa-4 showed peaks of ZIF-8 (18.24°, 16.65°, 14.92°,12.93°, 10.59°, and 7.51°), suggesting that ZIF-8 was successfully attached to the interior of chitosan and had a good crystal structure. Fig. 6d shows that CS/ZIF-8 decomposes at 180 °C, while CS/ZIF-8@COFa-4 has good thermal stability within 250 °C. These phenomena suggest that the introduction of COFa-4 can effectively improve the thermal stability of honeycomb CS/ZIF-8 microcapsules.
The detailed chemical states of elements in the CS/ZIF-8@COFa-4@Pd microspheres were studied using X-ray photoelectron spectroscopy (XPS). As shown in Fig. 7a, the EDX spectra of the CS/ZIF-8@COFa-4@Pd microspheres show the characteristic absorption peaks for Pd, C, N, O, and Zn, indicating that Pd NPs have been successfully introduced into the pore space of the CS/ZIF-8@COFa-4 microspheres. As shown in Fig. 7b, bands of 343.78 eV and 335.58 eV in the 3d3/2 and 3d5/2 orbitals of Pd(II) appear on the XPS spectra of the 3d orbitals of Pd, and these phenomena indicate that metallic Pd is susceptible to oxidation (PdO) when exposed to air.34,35 The high-resolution peak value of C1s of the final mixed material is shown in Fig. 7c, showing the intense peak values of sp3 C–C at 284.18 eV, C–N at 285.58 eV, and C–O at 286.46 eV.36 In Fig. 7d, the spectra of N1s show two sharp peaks at 398.78 eV and at 399.78 eV belonging to N–C and N–Zn, respectively.37
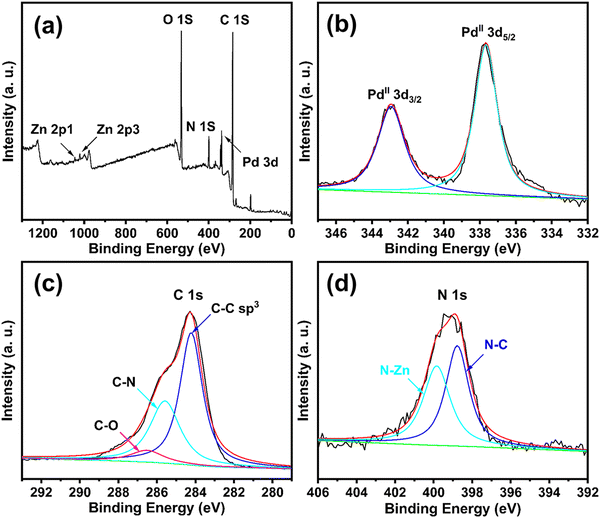 |
| Fig. 7 (a) Survey, (b) Pd 3d, (c) C 1s and (d) N 1s XPS spectra of CS/ZIF-8@COFa-4@Pd. | |
3.3. The catalytic performance studies of CS/ZIF-8@COFa-4@Pd
3.3.1. Catalytic Suzuki reaction.
The performance of the catalyst CS/ZIF-8@COFa−4@Pd and the optimum conditions required for the reaction were investigated using the Suzuki coupling reaction. The effects of different temperatures, times, solvents, bases, and catalyst amounts on the coupling reactions were discussed, as listed in Table 1. Studies have shown that metallic palladium was the catalytically active part of the catalyst. In addition, no products were formed from the reaction without the catalyst (Table 1, entry 1). The catalytic performance of the catalyst CS/ZIF-8@COFa-4@Pd was significantly higher than that of CS/ZIF-8@Pd under the same reaction conditions (Table 1, entries 2 and 4). The palladium content in CS/ZIF-8@Pd and CS/ZIF-8@COFa-4@Pd (Pd = 5.93%) was approximately twice as that of CS/ZIF-8@Pd (Pd = 2.88%) by ICP-MS analysis, indicating that CS/ZIF-8@COFa-4@Pd has more active sites compared to CS/ZIF-8@Pd. The yields of biphenyl improved from 82% to 99% when the reaction temperature was elevated from 60 to 80 °C. However, there was no improvement in the product biphenyl when the temperature was 100 °C, indicating that the optimum reaction temperature was 80 °C (Table 1, entries 3–5). The best results were observed when the reaction was carried out in water at 80 °C for 4 h, leading to a desired biphenyl yield of 99% (Table 1, entries 4, 6 and 7). Furthermore, when the reaction was carried out using a single solvent (H2O, EtOH, DMF and THF), the reaction proceeded smoothly, but the yield of biphenyl was low. Therefore, a mixture of H2O and EtOH was used as the solvent for this reaction (Table 1, entries 8–11). Finally, when the amount of the catalyst was increased to 100 mg, 99% yields were obtained in the presence of screened inexpensive bases (Na2CO3) under the given conditions (Table 1, entries 12–17).
Table 1 The optimal reaction conditions for the catalyst

|
Entry |
Catalyst/mg |
Solvent |
Base |
T/°C |
Time/h |
Yield/% |
1 |
— |
EtOH:H2O |
K2CO3 |
80 °C |
4 |
0 |
2 |
CS/ZIF-8@Pd/100 |
EtOH:H2O |
K2CO3 |
80 °C |
4 |
66 |
3 |
CS/ZIF-8@COFa-4@Pd/100 |
EtOH:H2O |
K2CO3 |
60 °C |
4 |
82 |
4 |
CS/ZIF-8@COFa-4@Pd/100 |
EtOH:H2O |
K2CO3 |
80 °C |
4 |
99 |
5 |
CS/ZIF-8@COFa-4@Pd/100 |
EtOH:H2O |
K2CO3 |
100 °C |
4 |
99 |
6 |
CS/ZIF-8@COFa-4@Pd/100 |
EtOH:H2O |
K2CO3 |
80 °C |
2 |
79 |
7 |
CS/ZIF-8@COFa-4@Pd/100 |
EtOH:H2O |
K2CO3 |
80 °C |
3 |
85 |
8 |
CS/ZIF-8@COFa-4@Pd/100 |
H2O |
K2CO3 |
80 °C |
4 |
74 |
9 |
CS/ZIF-8@COFa-4@Pd/100 |
EtOH |
K2CO3 |
80 °C |
4 |
96 |
10 |
CS/ZIF-8@COFa-4@Pd/100 |
DMF |
K2CO3 |
80 °C |
4 |
56 |
11 |
CS/ZIF-8@COFa-4@Pd/100 |
THF |
K2CO3 |
80 °C |
4 |
77 |
12 |
CS/ZIF-8@COFa-4@Pd/100 |
EtOH:H2O |
Et3N |
80 °C |
4 |
85 |
13 |
CS/ZIF-8@COFa-4@Pd/100 |
EtOH:H2O |
Cs2CO3 |
80 °C |
4 |
90 |
14 |
CS/ZIF-8@COFa-4@Pd/100 |
EtOH:H2O |
Na2CO3 |
80 °C |
4 |
99 |
15 |
CS/ZIF-8@COFa-4@Pd/25 |
EtOH:H2O |
Na2CO3 |
80 °C |
4 |
49 |
16 |
CS/ZIF-8@COFa-4@Pd/50 |
EtOH:H2O |
Na2CO3 |
80 °C |
4 |
74 |
17 |
CS/ZIF-8@COFa-4@Pd/75 |
EtOH:H2O |
Na2CO3 |
80 °C |
4 |
92 |
The range of the applicability of CS/ZIF-8@COFa-4@Pd was studied by the Suzuki–Miyaura coupling reaction of aryl halides and phenylboronic acids under optimal reaction conditions (Table 2). The catalyst CS/ZIF-8@COFa-4@Pd showed excellent catalytic activity in catalyzing the reactions involving aryl iodides and aryl bromides (Table 2, entries 1–12). However, CS/ZIF-8@COFa-4@Pd showed moderate catalytic activity in the reaction of chlorobenzene with phenylboronic acid and provided coupling yields of 44–57% (Table 2 entries 13–15). Finally, the coupling reactions of p-iodobenzene, bromobenzene, and chlorobenzene with phenylboronic acid containing –CH3 or –OCH3 substituents were investigated (Table 2 entries 16–21), and the synthesized CS/ZIF-8@COFa-4@Pd has good applicability in the Suzuki coupling reaction.
Table 2 General investigation of CS/ZIF-8@COFa-4@Pda
The performance of CS/ZIF-8@COFa-4@Pd was compared with previously reported catalysts through the Suzuki coupling reaction of iodobenzene and phenylboronic acid in Table 3. The comparison revealed the good catalytic activity of CS/ZIF-8@COFa-4@Pd, which gave the highest biphenyl yields with the shortest reaction times and lowest catalyst loadings. In addition, the CS/ZIF-8@COFa-4@Pd microcapsules were readily recovered and can be used multiple times compared to the already reported nanocatalysts.
Table 3 The catalytic activity comparison of CS/ZIF-8@COFa-4@Pd with some reported studies
Entry |
Catalysis |
Solvent |
T/°C |
Time |
Yield/% |
Ref. |
1 |
Pd NPs |
H2O |
100 |
12 h |
97 |
38
|
2 |
SiO2-pA-Cyan-Cys-Pd |
H2O |
100 |
5 h |
95 |
39
|
3 |
Pd@COF-QA |
H2O |
50 |
6 |
99 |
40
|
4 |
PdNPs@COF |
DMF:H2O |
50 |
3 |
99 |
41
|
5 |
Pd/NF300 |
NMP:H2O |
80 |
4 |
97 |
42
|
6 |
Pd/MIL-101 |
H2O |
80 |
20 |
99 |
43
|
7 |
Pd/TATAE |
H2O |
75 |
5 |
99 |
44
|
8 |
Pd/Y-MOF |
H2O |
80 |
8 |
98 |
45
|
9 |
CS/ZIF-8@COFa-4@Pd |
EtOH:H2O |
80 |
4 |
99 |
This work |
3.3.2. Catalytic reduction of p-nitrophenol.
The efficiency of CS/ZIF-8@COFa−4@Pd in the catalytic reduction of 4-NP was explored to extend the range of applications of the synthesized material. The residual content of 4-NP in solution during the reaction was measured in real-time by UV spectroscopy. After the start of the catalytic reaction, the absorbance of the reaction solution at 400 nm decreased rapidly to 0 within 9 min, and the solution rapidly lost its original bright yellow color. In comparison, the intensity of the absorption peak of the solution at 300 nm quickly increased over a period of 9 min. (Fig. 8a).
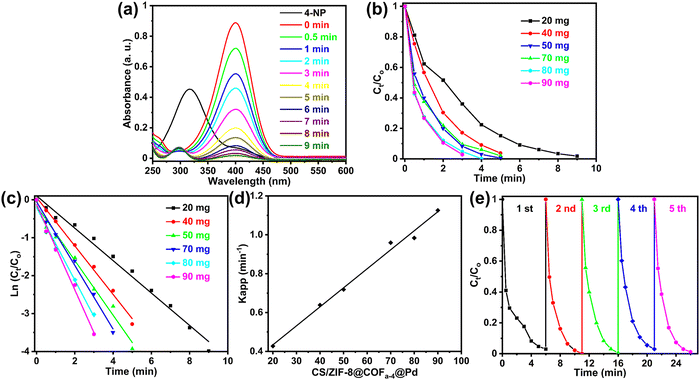 |
| Fig. 8 UV-vis spectrum. (a) The absorbance of 4-nitrophenol varies with time. (b) Ct/Co changes with time at different catalyst dosages. (c and d) The linear relationship between ln (Ct/Co) and Kapp. (e) The reusability of CS/@ZIF-8@COFa-4@Pd for the reduction reaction of p-NP. | |
To elucidate the catalytic kinetics of the catalyst CS/ZIF-8@COFa-4@Pd, the reduction efficiency of nitro phenols at different catalyst dosages was investigated in detail. As shown in Fig. 8b, when the catalyst concentration was low, an increase in the amount of the catalyst can lead to a more significant increase in the reaction efficiency, whereas when the catalyst concentration was high to a certain level, an increase in the amount of the catalyst does not lead to an increase in the reaction efficiency. Fig. 8c shows an excellent linear relationship between ln
(Co/Ct) and time, which indicates that the reaction of CS/ZIF-8@COFa−4@Pd catalyzed reduction of nitro phenols has quasi-first-order kinetic properties. Furthermore, an increase in the concentration of the catalyst CS/ZIF-8@COFa-4@Pd causes an increase in the value of the reaction rate constant Kapp over a specific test range (Fig. 8d). Research showed that the optimal Kapp value is 1.1 min−1 at room temperature with an appropriate amount of CS/ZIF-8@COFa-4@Pd.
3.4. Recyclability and structure stability of catalysts
After the catalytic reduction process was completed in each cycle, the catalysts were recovered by filtration and reused in the next cycle. There was no significant loss of catalyst activity after five cycles of use (Fig. 8e and Fig. 9). The mass loss of the separated catalysts was measured. The results showed that the catalyst mass remained essentially the same before and after the reaction. As shown in Fig. S19 and S21 (ESI†), the structure and morphology of the catalyst were not damaged after five cycles. The results of ICP-MS showed that the loss of palladium nanoparticles was only 0.08% after five cycles, which indicated that the presence of COFa-4 could effectively prevent the leaching of palladium nanoparticles during the reaction and further improve the stability of the catalyst. In contrast, the catalytic activity of CS/ZIF-8@Pd decreased significantly after five cycles due to the leaching of palladium nanoparticles caused by the wetting and swelling of CS/ZIF-8@Pd during the reaction. This phenomenon indicates that CS/ZIF-8@COFa-4@Pd has good stability.
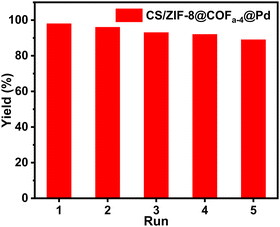 |
| Fig. 9 The reusability of CS/ZIF-8@COFa-4@Pd as the catalyst for ten cycles of reactions of the Suzuki coupling reaction. | |
4. Conclusions
In conclusion, we prepared and characterized new CS/ZIF-8@COF composites by growing COFs in situ on the inner wall of honeycomb CS/ZIF-8 microcapsules for the first time. The COF layer can effectively prevent the swelling of CS/ZIF-8@COFs in an aqueous solution and further improve the stability of the composite. The large number of N atoms in the structure of COFs and the inherent porous nature can effectively inhibit the agglomeration and leaching of Pd NPs during the reaction process, thus improving the catalytic activity and recycling performance of the catalyst. The CS/ZIF-8@COFa-4@Pd microcapsules exhibited excellent catalytic performance in the Suzuki–Miyaura reaction, and high reaction yields were obtained under mild reaction conditions. These microcapsules also showed perfect catalytic activity and stability in reducing p-NP to p-AP at room temperature. In addition, the catalytic reduction activity of CS/ZIF-8@COFa-4@Pd microcapsules remained essentially unchanged after being repeated 5 times. This study shows that the CS/ZIF-8@COFa-4@Pd microcapsules have apparent advantages over catalysts reported in the literature, such as the large size for easy recycling, high reusability, low cost, green, in-growth, biodegradable, and good thermal stability. Moreover, based on this method, the catalytic behavior of CS/ZIF-8@COFa-4@Pd microcapsules can be investigated under varying catalytic reaction conditions.
Conflicts of interest
The authors declare that they have no known competing financial interests or personal relationships that could have appeared to influence the work reported in this paper.
Acknowledgements
We gratefully acknowledge the financial support from Science and Technology Committee of Liaoning Province (2022JH1/10800068), the Scientific Research Fund Project of Ningde Normal University (2020Z02) and the Fujian Provincial Key Laboratory of Featured Biochemical and Chemical Materials, Ningde Normal University.
References
- K.-X. Cui, W.-F. Zhong, L.-Y. Li, Z.-Y. Zhuang, L.-Y. Li, J.-H. Bi and Y. Yu, Small, 2019, 15, 1804419 Search PubMed.
- C.-X. Tan, J.-Y. Li, W. Liu, Q.-W. Zhao, X.-D. Wang and Y.-Y. Li, Chem. Eng. J., 2020, 396, 125191 CrossRef CAS.
- D.-Y. Zhu, Y.-F. Zhu, Q.-Q. Yan, M. Barnes, F.-X. Liu, P.-F. Yu, C.-P. Tseng, N. Tjahjono, P.-C. Huang, M.-M. Rahman, E. Egap, P.-M. Ajayan and R. Verduzco, Chem. Mater., 2021, 33, 4216–4224 CrossRef CAS.
- S.-Y. Ding and W. Wang, Chem. Soc. Rev., 2013, 42, 548–568 RSC.
- S. Kandambeth, K. Dey and R. Banerjee, J. Am. Chem. Soc., 2019, 141, 1807–1822 CrossRef CAS.
- M.-S. Lohse and T. Bein, Adv. Funct. Mater., 2018, 28, 1705553 CrossRef.
- Y.-F. Zeng, Adv. Mater., 2016, 28, 2855–2873 CrossRef CAS.
- H. Xu, Nat. Chem., 2015, 7, 905–912 CrossRef CAS.
- H. Ding, Nat. Commun., 2018, 9, 5234 CrossRef CAS.
- C.-P. Guo, F.-H. Duan, S. Zhang, L.-H. He, M.-H. Wang, J.-L. Chen, J.-Q. Zhang, Q.-J. Jia, Z.-H. Zhang and M. Du, J. Mater. Chem. A, 2022, 10, 475–507 RSC.
- W.-T. Lia, W. Shi, Z.-J. Hu, T. Yang, M.-L. Chen, B. Zhao and J.-H. Wang, Appl. Surf. Sci., 2020, 530, 147254 CrossRef.
- M.-X. Wu, Y. Wang, G.-H. Zhou and X.-M. Liu, Coord. Chem. Rev., 2021, 430, 213735 CrossRef CAS.
- W. Li, H.-X. Jiang, Y. Geng, X.-H. Wang, R.-Z. Gao, A.-N. Tang and D.-M. Kong, ACS Appl. Mater. Interfaces, 2020, 12, 20922–20932 CrossRef CAS.
- Y.-L. Xu, X.-F. Shi, R. Hua, R. Zhang, Y.-J. Yao, B. Zhao, T. Liu, J.-Z. Zheng and G. Lu, Appl. Catal., B, 2020, 260, 118142 CrossRef CAS.
- X. Zhao, J. Am. Chem. Soc., 2019, 141, 6623–6630 CrossRef CAS PubMed.
- C.-X. Li, J. Yang, P. Pachfule, S. Li, M.-Y. Ye, J. Schmidt and A. Thomas, Nat. Commun., 2020, 11, 4712 CrossRef CAS.
- P.-H. Zhu, S.-S. Li, S. Zhou, N. Ren, S.-G. Ge, Y. Zhang, Y.-F. Wang and J.-H. Yu, Chem. Eng. J., 2021, 420, 127559 CrossRef CAS.
- Y.-H. Yao, J. Li, H. Zhang, H.-L. Tang, L. Fang, G.-D. Niu, X.-J. Sun and F.-M. Zhang, J. Mater. Chem. A, 2020, 8, 8949–8956 RSC.
- M.-X. Wang, J. Zhang, X.-B. Yi, X.-F. Zhao, B.-X. Liu and X.-C. Liu, Appl. Surf. Sci., 2020, 507, 145166 CrossRef CAS.
- Z.-H. Li, L. Yang, H.-B. Cao, Y. Chang, K. Tang, Z.-Q. Cao, J.-J. Chang, Y.-P. Cao, W.-B. Wang, M. Gao, C.-M. Liu, D.-G. Liu, H. Zhao, Y. Zhang and M.-J. Li, Carbohydr. Polym., 2017, 175, 223–230 CrossRef CAS.
- P. Chen, Y.-M. Liang, B.-Q. Yang, F.-F. Jia and S.-X. Song, ACS Sustainable Chem. Eng., 2020, 8, 3673–3680 CrossRef CAS.
- S.-Q. Ji, X.-W. Lu, M.-Y. Zhang, L.-P. Leng, H.-X. Liu, K.-B. Yin, C. Xu, C. He, J. Hugh Horton, J.-W. Zhang and Z.-J. Li, Chem. Eng. J., 2023, 452, 139205 CrossRef CAS.
- Z.-W. Lei, Y.-H. Deng and C. Y. Wang, J. Mater. Chem. A, 2018, 6, 3258 RSC.
- E. Fernandez, M.-A. Rivero-Crespo, I. Dominguez, P. Rubio-Marques, J. OliverMeseguer, L. Liu, M. Cabrero-Antonino, R. Gavara, J.-C. Hernandez-Garrido, M. Boronat, A. Leyva-Perez and A. Corma, J. Am. Chem. Soc., 2019, 141, 1928–1940 CrossRef CAS.
- Y. Fu, P. Xu, D. Huang, G. Zeng, C. Lai, L. Qin, B. Li, J. He, H. Yi and M. Cheng, Appl. Surf. Sci., 2019, 473, 578–588 CrossRef CAS.
- K. Layek, M.-L. Kantam, M. Shirai, D. Nishio-Hamane, T. Sasaki and H. Maheswaran, Green Chem., 2012, 14, 3164–3174 RSC.
- A. Fihri, M. Bouhrara, B. Nekoueishahraki, J. M. Basset and V. Polshettiwar, Chem. Soc. Rev., 2011, 40, 5181–5203 RSC.
- S.-Y. Ding, J. Gao, Q. Wang, Y. Zhang, W.-G. Song, C.-Y. Su and W. Wang, J. Am. Chem. Soc., 2011, 133, 19816–19822 CrossRef CAS PubMed.
- B.-Z. Zhang, M.-Y. Li, H.-J. Lei, J.-L. Chen, S.-H. Wang and C. Chen, Appl. Surf. Sci., 2022, 599, 153899 CrossRef CAS.
- W.-H. Li, J. Yang, D. Wang and Y. Li, Chem., 2022, 8, 119–140 CAS.
- R. Gomes, P. Bhanja and A. Bhaumik, Chem. Commun., 2015, 51, 10050 RSC.
- S. Royuela, J. Almarza, M. J. Mancheño, J. C. Pérez-Flores, E. G. Michel, M. M. Ramos, F. Zamora, P. Ocón and J. L. Segura, Chem. Eur. J., 2019, 25, 12394–12404 CrossRef CAS.
- W.-D. Ma, Q. Zheng, Y.-T. He, G.-R. Li, W.-J. Guo, Z. Lin and L. Zhang, J. Am. Chem. Soc., 2019, 141, 18271–18277 CrossRef CAS.
- T. Baran, İ. Sargın, M. Kaya, P. Mulerčikas, S. Kazlauskaitėc and A. Menteş, Chem. Eng. J., 2018, 331, 102–113 CrossRef CAS.
- X.-L. Ye, S.-J. Lin, J.-W. Zhang, H.-J. Jiang, L.-A. Cao, Y.-Y. Wen, M.-S. Yao, W.-H. Li, G.-E. Wang and G. Xu, ACS Sens., 2021, 6, 1103–1110 CrossRef CAS.
- Y.-H. Yao, J. Li, H. Zhang, H.-L. Tang, L. Fang, G.-D. Niu, X.-J. Sun and F.-M. Zhang, J. Mater. Chem. A, 2020, 8, 8949–8956 RSC.
- R. Zhao, T.-T. Ma, S. Zhao, H.-Z. Rong., Y.-Y. Tian and G.-S. Zhu, Chem. Eng. J., 2020, 382, 122893 CrossRef CAS.
- S. Bhattacharyya, S.-H. Pang, M.-R. Dutzer, R.-P. Lively, K.-S. Walton, D.-S. Sholl and S. Nair, J. Phys. Chem. C, 2016, 120, 27221–27229 CrossRef CAS.
- Q. Guo, C. Chen, L. Zhou, X. Li, Z. Li, D. Yuan, J. Ding, H. Wan and G. Guan, Microporous Mesoporous Mater., 2018, 261, 79–87 CrossRef CAS.
- J.-C. Wang, C.-X. Liu, X. Kan, X.-W. Wu, J.-L. Kan and Y.-B. Dong, Green Chem., 2020, 22, 1150 RSC.
- S.-L. Lu, Y.-M. Hu, S. Wan, R. McCaffrey, Y.-H. Jin, H.-W. Gu and W. Zhang, J. Am. Chem. Soc., 2017, 139, 17082–17088 CrossRef CAS PubMed.
- Z. Gao, Y.-J. Feng, F.-M. Cui, Z.-L. Hua, J. Zhou, Y. Zhu and J.-L. Shi, J. Mol. Catal. A: Chem., 2011, 336, 51–57 CrossRef CAS.
- B. Yuan, Y. Pan, Y. Li, B. Yin and H. Jiang, Angew. Chem., Int. Ed., 2010, 49, 4054–4058 CrossRef CAS PubMed.
- V. Sadhasivam, R. Balasaravanan, C. Chithiraikumar and A. Siva, ChemistrySelect, 2017, 2, 1063–1070 CrossRef CAS.
- J. Huang, W. Wang and H. Li, ACS Catal., 2013, 3, 1526–1536 CrossRef CAS.
|
This journal is © The Royal Society of Chemistry and the Centre National de la Recherche Scientifique 2023 |
Click here to see how this site uses Cookies. View our privacy policy here.