Biodegradable biopolymers for active packaging: demand, development and directions
Received
24th August 2022
, Accepted 30th October 2022
First published on 29th November 2022
Abstract
The food packaging industry is a major contributor to plastic waste. The end-of-life scenario of fossil-fuel derived plastics often has a detrimental effect on the natural environment, including the formation of microplastic pollution and increased GHG emissions. Therefore, alternative food packaging materials are required to overcome these effects and reduce the unsustainable use of plastics. The sustainability of biopolymers is related to the valorisation of waste, the abundance of the source, and the biodegradability of the material. Conventional fossil-fuel based plastics often have the ideal properties to protect food from environmental conditions which enhance food degradation. Therefore, bioplastics require equal or superior mechanical and barrier properties to outcompete traditional plastics. Here we review the use of biodegradable biopolymers for active food packaging, discussing bioplastics at the forefront of active packaging research. Particular attention is paid to the source of the biopolymer, the film properties, and different scale-up technologies used to produce active packaging materials. The variation in bioplastic properties upon incorporation of active agents is also explored. Moreover, the controversies relating to biodegradable certifications are discussed. This review builds upon current literature by providing a specific overview of biopolymers in the context of their use as active packaging materials. Overall, it is evident that active packaging prospects will rely on; (i) bio-based and biodegradable bioplastics (ii) optimising the properties of bioplastics containing active agents, (iii) adhering to strict safety regulations of food contact.
1 Introduction
1.1 The environmental concerns of petroleum-based plastic packaging
Plastic packaging accounts for more than 30% of global plastic production and the food packaging industry has the largest revenue share of plastic packaging worldwide.1 Traditional fossil-fuel based plastic packaging materials last for over 1000 years in landfill. Indeed, most of the plastic ever produced still exists, polluting various environments. The UN Environment Programme (UNEP) plastic waste report in 2018 detailed that, since 2015, only 9% of all plastic waste had been recycled.2 The remaining plastic waste was incinerated (12%) or accumulated in landfill and the natural environment (79%).2 Furthermore, the US Environmental Protection Agency (EPA) reported that in 2018, plastic production amounted to 35.7 million tonnes, making up 12.2% of municipal solid waste.3 The report calculated that the overall recycling rate was 8.7%, however for specific plastics such as polyethylene terephthalate (PET) and high-density polyethylene (HDPE), the recycling rate was 29.1% and 29.3% respectively.3 Furthermore, the UK began to export a vast proportion of its plastic waste to countries including Malaysia and Indonesia after China banned plastic waste imports in 2018.4 Often, these countries do not have the correct waste-infrastructure to deal with vast quantities of plastic waste, and so the plastic is often discarded into landfill or waterways. Indeed, a UK government report from 2019 detailed that around 8 million tonnes of plastic waste entered the ocean each year.4 Between 55 and 60% of this marine plastic was said to originate from countries which had received imported plastic waste.4 This end-of life scenario of plastics may lead to the formation of microplastics, polluting waterways and causing detrimental effects on marine life.5 The long term health effects of microplastic exposure is not yet well-researched, and microplastics have recently been detected for the first time in human placenta.6 More recently, microplastics were detected in human blood samples for the first time, raising health concerns.7
Whilst the US, UK and EU have many regulations in place surrounding recycling of plastics, the replacement of plastics with degradable alternatives would undoubtably reduce plastic waste further. Moreover, conventional recycling methods are limited by public participation, and sorting the waste is often complicated by contamination, colour and size variations.4 Recycling also produces products with lower-value applications than the original plastics.2 However, it is not currently feasible to remove food packaging altogether in most circumstances. Food packaging serves to prolong food freshness and shelf-life. In turn, this reduces food wastage due to spoilage during storage or transportation. Food degradation occurs primarily by lipid oxidation, which is prevented or reduced by barrier packaging.8 Strikingly, the FAO reported that food waste emitted greenhouse gas (GHG) emissions were greater than all countries except from China and the USA in 2011.9 Furthermore, successful packaging reduces the occurrence of foodborne diseases. Foodborne diseases due to microbial outbreaks in the food we consume are a global public health concern, with 420
000 annual fatalities recorded as an average in 2015.10
1.2 Bioplastics as a tool to reduce plastic waste
Food packaging holds a large proportion of the applications of bioplastics.1 Successful food packaging protects food from oxygen, water vapour, UV light and microbial contamination.11 Traditional food packaging based on petroleum-based plastics such as polyvinyl chloride (PVC), polyethylene terephthalate (PET) and polyethylene (PE) often has the ideal properties to protect food from these environmental conditions. However, the detrimental effect that fossil-fuel based, non-biodegradable plastics have on the environment is well-documented and is now, arguably, common knowledge. A potential solution to this is to develop bio-based and biodegradable materials as alternatives. A bioplastic may be bio-based, biodegradable, or have both attributes.1 Bio-based materials are derived from living material and often renewable resources, in contrast to fossil fuels. Ideally, biopolymeric active food packaging would be able to degrade under natural composting conditions.
Fig. 1 categorises several plastics based on their biodegradability and source. Some examples of commonly used bioplastics in active packaging research and development include chitosan, poly lactic acid (PLA), bacterial cellulose, starch, cellulose, pectin, gums, agar, alginate, dextran, gelatin, casein and whey protein.12–14 Overall, the considerations for active packaging raw materials include the abundance of the source material, the amount of water used to extract or material, the energy usage, the solvents and chemicals used in extraction or film-synthesis, and the scalability of the material. Furthermore, the implementation of waste valorisation would improve the sustainability profile of the packaging material. This review will provide an overview of promising bioplastic materials and discuss their viability in the context of mechanical properties, biodegradability and scale-up potential.
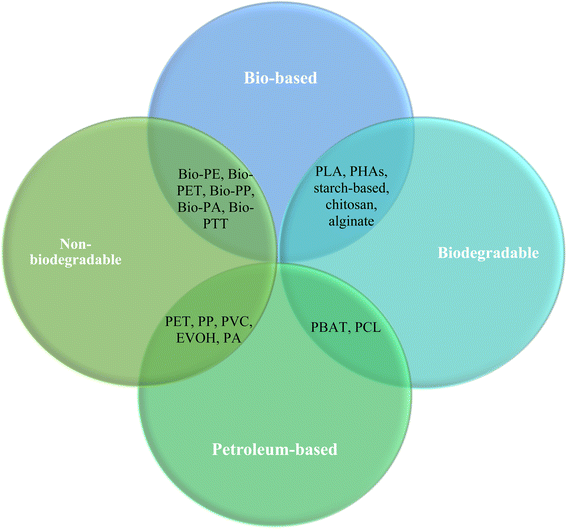 |
| Fig. 1 Examples of plastics based on their source and biodegradation capabilities. | |
1.3 The environmental benefits of biodegradable active packaging
Active food packaging materials contain active ingredients that act to prevent contamination or degradation of food to extend shelf-life. Active packaging (AP) enables antimicrobial or antioxidant activity, and the objectives of this technology are to reduce both food waste and the occurrence of foodborne diseases. This invention may also reduce the energetic costs associated with refrigeration of loose fruit and vegetables.4 The techniques used in active packaging include antioxidant release, antimicrobial release and the sequestration of certain degradation-enhancing gases such as oxygen and ethene. Active packaging incorporating natural antimicrobial or antioxidant substances is becoming the most researched form of active packaging, implying high developmental potential. The use of inherently antimicrobial polymers is also well-researched, for example the biopolymers chitosan and alginate have antimicrobial activities.15 Combining bioplastics with active packaging methodology would produce a food packaging material which meets consumer demands of (i) a reduced environmental footprint and (ii) an extended shelf-life of fresh produce. The active component is either released onto the surface of the food (direct contact) or into the headspace between the packaging and the food (indirect contact).16 Overall, the active agent should be non-toxic, abundant, renewable, and simple to obtain or extract. Specific examples of active agents for active packaging are discussed in several reviews.17–19
Biodegradable active packaging technology has the capacity to reduce fossil fuel based plastic usage and related greenhouse gas (GHG) emissions. The benefits of bioplastic use in place of traditional synthetic polymers include reduction in the carbon footprint of packaging, the reduction in plastic waste and of the maintenance of fresh produce. To achieve a circular process, bioplastics should be obtained from renewable or recycled resources and use renewable energy. Edible packaging is an important bioplastic-based invention that has been utilised for over 100 years, with the traditional use of wax-coatings on fruit. Edible packaging has recently gained attraction in the literature, in synergy with the search for materials to replace conventional fossil-fuel based plastics. Currently, materials such as potato starch and seaweed-based polymers are used for edible packaging.4 Other inventions in this field include ‘smart’ or ‘intelligent’ packaging. Intelligent packaging monitors the conditions of packaging to elucidate the freshness of a product. For example, the packaging may monitor pH or temperature which are often proportional to the degree of food degradation.20 There is an interesting area of research at the intersection of the inventions of active packaging, edible packaging and intelligent packaging. Edible packaging is likely to be based on biopolymers, and these may have an inherent preservation effect on the food. Moreover, monitoring the conditions of the food within packaging can enable the determination of the success of active packaging.
1.4 Commercial development prospects
The successful replacement of conventional plastics with bioplastics requires stringent testing of the bio-based materials to determine their barrier properties, physical properties, optical properties and mechanical properties such as tensile strength. Furthermore, to pose a measurable environmental advantage, bioplastics must have good biodegradability profiles. However, there is a general lack of clarity concerning biodegradability since the definition may allow microplastic-forming materials to be termed as biodegradable. Furthermore, many studies on bio-based active packaging materials do not determine the biodegradability of the packaging material. Biodegradability values of different combinations of materials and active agents are therefore difficult to obtain from the literature. It is important to consider the end-of-life scenario for bioplastics in the development of more environmentally friendly active packaging. Furthermore, the solubility of the material and its compostability are key factors to determine before commercialisation and determination of suitable waste management facilities.4,21
Despite high implementation costs, some bioplastics are already used on a large scale. The projections for 2026 depict that polybutylene adipate terephthalate (PBAT), polybutylene succinate (PBS), poly-lactic acid (PLA), polyhydroxyalkanoates (PHAs), starch blends and cellulose films will have the greatest production capacity.22 The land usage for many of these bio-derived biopolymers is expected to reach 0.06% of the total agricultural area worldwide, suggesting that the production of these materials will not compete for space for food or feedstock.22 Additionally, VTT have developed a recrystallised cellulose pilot plant for cellulose film production.23 Similarly, Lei et al. (2022) have recently detailed a large scale manufacturing method to make durable and recyclable cellulose films using a roll-to-roll fabrication line.24 Flexible packaging holds the largest market segment amongst all uses of plastics, therefore this is undoubtably an important area of research for improving the overall sustainability profile of plastic-usage.22
It is important for bioplastics to have similar mechanical, barrier and physical properties to traditional packaging materials. The blending of biopolymers with other biopolymers, or with synthetic polymers has been used to regulate these material properties.1,21 For example, chitosan has been blended with carboxymethylcellulose (CMC), sodium alginate and antimicrobial microcrystalline cellulose (AMCC) to form an active packaging material capable of extending the shelf-life of cheese.25 Similarly, coatings or emulsion layers are commonly used. For example, cutin has been used on chitosan biopolymers in order to reduce the water sensitivity of the bioplastic material.14 Furthermore, polyhydroxyalkanoates (PHA) films have been used on thermoplastic starch (TPS) as moisture barriers, reducing water uptake and improving other gas barrier properties.26 This technique is useful for moisture-sensitive foods and is often required with biopolymers due to high water-sensitivity. However, it is important to consider the changes to the organoleptic properties or unfavourable changes to other properties such as oxygen permeability that may arise after coating or blending.14 Furthermore, whilst blending with conventional polymers may improve properties of the material and therefore the scalability, this method reduces the environmental benefits of using completely bio-based materials.
1.5 Outcompeting conventional plastics
Bioplastics must compete with conventional plastics in cost and performance for packing applications. They must mimic the feel and properties of these petroleum-based plastics, as previously discussed.21 To provide a significant advantage over conventional plastics, a bioplastic requires good biodegradability. Moreover, the invention of edible films overcame many of the issues associated with BP development. Edible films, necessarily, are considered safe and satisfy FDA regulations for safe food ingredients. Since they may be eaten with food, their end-of-life scenario and biodegradability will thus also be satisfactory.8 However, in all cases, it is essential that the correct disposal method of any packaging is made clear to the consumer.4 Furthermore, biopolymeric waste may be more suited to dedicated collections, which require development and investment.4
The high complexity of many synthetic procedures for active packaging may reduce the scalability of the material due to associated costs. The scale up of the fabrication and processing of bioplastic materials is currently limited in comparison to conventional plastics. For example, many large plastic packaging manufacturing plants utilise extrusion or injection moulding. For active packaging, it is important to ensure that the active agent is stable at the high temperatures often required by these methods. Furthermore, many research papers on active packaging report film casting as the film-formation method. Whilst this technique is ideal for lab-scale material preparation, the parameters have high variability which reduces the scalability of the process. Typical scalable film-formation methods include extrusion, injection moulding, film blowing, thermoforming, electrospinning and vacuum forming.
Moreover, bioplastic materials may have issues with water solubility and sensitivity. Specifically, the water sensitivity of HPMC and chitosan films has been researched by ref. 27. Water solubility improves the ease of disposal of a material. However, for food packaging applications, the plastic material requires a good water vapour barrier and low solubility. The water sensitivity may be reduced by cross-linking, polymer lamination, polymer blending, or hydrophobic plasma treatment.28 The commercial viability of bioplastics for AP technology will undoubtably rely on new and substantial investments into research, production and waste management facilities.21 The plastic packaging tax introduced in April 2022 in the UK, alongside the recent £30 million boost of funding directed towards the Smart Sustainable Plastic Packaging (SSPP) challenge should facilitate this transition.22,29,30
1.6 Marketed examples of bioplastic food packaging
In 2018, the UK Plastics Pact was launched by WRAP and the Ellen MacArthur Foundation.4 Members of the collaboration are working towards 2025 targets including eliminating the majority of single-use packaging and moving towards the exclusive use of reusable, recyclable or compostable plastics.4 To this end, there is a growing market for commercial biodegradable active packaging materials. There are several start-up companies and larger companies working to produce bioplastic packaging which may outcompete traditional plastics. Currently, many of these commercialised materials do not contain active components for active packaging. However, the antimicrobial films Zeomic™ and Microgarde™ are examples of commercialised active packaging materials.31 The company TIPA® makes compostable films for the food packaging and fashion industries.32 These films are made using existing machinery and are between 20 and 80% bio-based, but 100% compostable. Interestingly, these films are suitable for freezing, but not for heating nor for high liquid-content foods due to the degradation mechanisms of the material.32 Furthermore, the start-up company Notpla has recently gained attention for the invention of sustainable, edible seaweed packaging.33
1.7 Outlook
The bio-based active packaging must have good mechanical properties, good stability and good barrier properties to pose a viable alternative to fossil-fuel based plastics.34 Additionally, the product description and label should include all added substances including the active component to adhere to food contact safety regulations.35 Therefore, the prospects of bioplastics for active packaging rely on (i) the properties of the packaging in its final form and (ii) the safety of the components used in the packaging.34,35
Ghosh and Jones (2021) and Zhao et al. (2020) recently produced in-depth reviews on bioplastics, with the latter specific to use in food packaging.1,36 Additionally, there have been several recent reviews on bio-based biopolymeric materials including the valorisation of waste materials.37–39 In contrast, this review provides a more specific overview of biopolymers in the context of their use as active packaging materials. We review the topic of bio-based, biodegradable polymers for active packaging with specific discussions of (i) the substrate, (ii) biodegradability classifications and related controversies, (iii) bioplastic properties and modulations thereof and (iv) film-formation techniques. These areas of active packaging research are vital for the successful commercialisation of the material. This review will focus on bio-based, biodegradable polymers for Active Packaging (AP) technology. For a more in-depth of discussion of the active agent for biodegradable active packaging, including encapsulation and controlled release methods, a review was recently published by our group.17
2 The bio-polymeric substrate for active packaging
2.1 Outlook on biopolymers for active packaging
Physical and mechanical properties of biopolymers (BPs) may be regulated and optimised by a multitude of techniques such as blending with other polymers. The development of water-soluble BPs is becoming more important to overcome issues with the persistence of conventional polymers in marine environments. Water-soluble BPs may include carboxymethylcellulose (CMC), hydroxyethyl cellulose (HEC), xanthan, pullulan and polyvinyl alcohol (PVA).21 In particular, pullulan has been used to form edible films with good moisture exchange properties and low oxygen permeability, which are both important parameters for food packaging.40 The limiting factor to developing research on this material beyond lab scale is the cost of the biopolymer.40 Therefore, research is still required on the performance of these materials, their safety, and lowering the cost of their manufacture. Zhao et al. (2020) recently reviewed the types of bioplastics, comparing their properties.1 Importantly, they reported the average price for conventional plastics (HDPE, LDPE, PET, PP, PVC and PS) as USD$ 1.17–1.56/kg, whereas the average for bioplastics (PLA, TPS, CA) was higher in price at USD$ 2.74–3.92/kg.1 This represents a key hindrance to bioplastic development. However, the cost of implementing these new materials should become a secondary factor to their capability of mimicking conventional plastics and providing a real sustainability advantage. In fact, the bioplastics market is forecast to grow significantly in the next decade, which should provide an incentive for further industrial development.8 Due to the environmental benefits and current demand for radical change, this review will focus on biodegradable polymers, specifically those derived from natural compounds, for use in active packaging materials.
2.2 Polymers commonly used for active packaging
In this section, the major polymers used in active packaging (AP) research and development will be discussed and categorised based on their source (petroleum based or bio-based), and their biodegradation capacity. The review highlights bio-based, biodegradable polymers as the most promising materials for real environmental advantages over conventional plastics and discusses specific biopolymers within this category with high potential for further development. Fig. 2 shows a schematic representation of bio-based biodegradable active packaging materials.
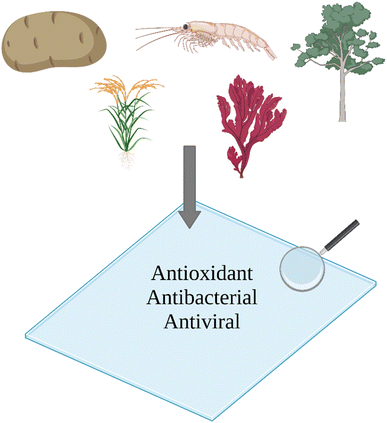 |
| Fig. 2 Schematic representation of biodegradable active packaging derived from bio-based materials including starch, chitosan, cellulose, rice husks and seaweed. | |
2.2.1 Petroleum-based, biodegradable polymers.
Polycaprolactone (PCL) is a thermoplastic biopolymer synthesised from crude oil. PCL is often blended with starch to reduce costs and the usage of non-renewable feedstock.21 The production of PCL is scalable and water-resistant sheets of PCL may be formed by melt-extrusion.21 PCL degrades in bioactive environments, so may be termed as biodegradable. However, there is controversy on the definition of biodegradability relating to the formation of microplastics for both petroleum-based and bio-based polymers.21 PCL is hydrophobic and has a slow degradation rate, but it is highly researched in pharmacology for drug delivery owing to its long term stability and controlled release properties.41 Phenolic compounds have been loaded into PCL films by melt-blending to form materials capable of achieving good antibacterial inhibition of common food bacteria.42
Poly butyrate adipate terephthalate (PBAT) is another polymer in this category, made from the copolymerisation of adipic acid, 1,4-butanediol and dimethyl terephthalate.43 PBAT degrades with the use of lipases, and it is suitable for forming flexible packaging, with similar properties to conventional LDPE.1,43
2.2.2 Bio-based, non-biodegradable polymers.
The major non-biodegradable bio-based plastics include bio-polyethylene (bio-PE), bio-polypropylene (bio-PP), bio-polyamide (bio-PA), bio-poly-trimethylene terephthalate (bio-PTT) and bio-polyethylene terephthalate (bio-PET).44 Bio-PE may be formed from bioethanol via dehydration and polymerisation. Bio-PP and bio-PET may be derived from bioethanol via synthetic methods including dehydration, dimerisation, isomerisation, metathesis oxidation, hydration, polycondensation, and polymerisation.44 The chemical structures of these compounds are similar to conventional petroleum-based plastics and therefore, they have similar properties and uses. These materials do not utilise fossil-fuels and so are an inherently more sustainable option. However, these materials do not address the issue of plastic waste. Furthermore, many of these materials are derived from crops which could be otherwise used for food resources.
2.2.3 Bio-based, biodegradable polymers.
Poly(3-hydroxybutyrate) (PHB) and poly(lactic-co-glycolide) (PLGA) have been described as promising bio-based polymers for packaging applications.21,45 The biopolymers polylactic acid (PLA) and polyglycolide (PGA) have also been reported extensively for AP applications.14
2.2.3.1 Polyhydroxyalkanoates (PHAs).
PHAs may be obtained from bacterial fermentation, produced from sludge or produced from municipal wastewater treatment.1,46 Therefore, it is possible to valorise agro-industrial waste to obtain these polymers. The properties of PHAs are similar to conventional PVC (polyvinyl chloride), and PHAs are insoluble in water which is important for many food packaging applications. However, PHAs are thermally unstable.1 Processability may be an issue for PHAs such as poly(3-hydroxybutyrate-co-3-hydroxyvalerate) (PHBV) because the melting temperature of the polymer exceeds the decomposition temperature and therefore the molecular weight of the polymer decreases at high processing temperatures (180 °C).47 PHA-degrading hydrolytic enzymes may be used for degradation purposes and importantly, PHAs may be composted and thermally processed with minimal changes to machinery and techniques.21 Polyhydroxy butyrate (PHB) is a promising microbially bioprocessed polymer from the PHA family.48 PHB is biocompatible, non-toxic and biodegradable in bioactive environments.48 It may be biosynthesised from bacteria, which is beneficial due to the controversy of using food crops for material applications.
2.2.3.2 Poly lactic acid (PLA).
PLA is produced by (i) the condensation polymerisation of lactic acid or (ii) the ring-opening polymerisation of lactides. The monomer of lactic acid is usually derived from the fermentation of starch from plants. However, PLA may also be produced from food waste.38 PLA is widely used on a large scale in industry as it can be processed using existing technology and it is generally recognised as safe (GRAS) by the FDA. PLA has high tensile strength, but it has low flexibility, high hydrophobicity, poor barrier properties, low stability and a low heat deformation temperature.1,14 PLA can form single-layer films or laminated packaging films.49 Importantly, the technology to produce conventional plastics is applicable to PLA.1 The biodegradation of PLA is often slow.50 However, enzymatic degradation can improve the rate of biodegradation.50 Additionally, PLA has been used extensively to encapsulate active agents in active packaging with a simple method for nanoparticle formation.51 However, during the synthesis of PLA nanoparticles, dissolving commercial PLA pellets may require harsh solvents such as CHCl3. Furthermore, PGLA is a biodegradable copolymer of PLA and PGA. PGLA has good barrier properties and has been approved by the FDA as a food contact material, which is highly beneficial in terms of commercial development.45
2.2.4 Bio-based, biodegradable and food-compatible polymers.
Food compatible film-forming biopolymers include alginate, cellulose, chitosan, pectin, chitosan, starch, agar, dextran, casein, whey protein and carrageenan.12,13 These biopolymers, amongst others, may be used for the manufacture of edible films and composite films.12
2.2.4.1 Starch.
Starch biopolymers are largely used for packaging applications and are available in abundance, with annually renewable crops. Examples of source of starch include waste organic material and the biorefinery of microalgae.52 Starch polymers are brittle with low moisture barriers and low tensile strength values. However, plasticisation can improve mechanical properties and processability of starch polymers.21 Thermoplastic starch (TPS) is plasticised starch or de-structuralised, nanocrystalline starch formed by the application of heat and work.21 TPS may be blended with other polymers, such as PLA, to modulate properties and overcome humidity and temperature dependant mechanical properties.1,21 Loose-fill TPS foams with more than 85% starch content have the potential to mimic polystyrene, although these foams are generally water sensitive which reduces their capacity to replace polystyrene directly but could allow for solubilisation in water as a possible end-of-life scenario.21 A promising film based on corn starch and porous starch encapsulating tea polyphenols was recently reported, with sustained release of the active component.53
2.2.4.2 Cellulose.
Cellulose is a highly abundant biopolymer derived from biomass and is GRAS by the FDA. However, the extraction and refinery of cellulose is often energy intensive, using large volumes of solvents and other chemicals. Furthermore, cellulose production waste has environmental concerns due the potential presence of heavy metals.54 Chemical derivatives of cellulose include biopolymers such as cellulose acetate, carboxymethylcellulose and hydroxypropyl methylcellulose. Cellulose acetate is already used on a large scale for cigarette butts and is popular in the textile industry.55 Cellulose acetates with degrees of substitution up to 2.5 are considered to be biodegradable.21 However, as with many semi-synthetic plastics, cellulose acetate may form water-polluting microplastics and 300
000 tonnes of microplastic waste from cigarette butts enters the aquatic environment each year.56 Surface modifications of cellulose may improve properties which hinder the development of cellulose-based materials, such as sensitivity to water and humidity.57 Cellulose nanocrystals (CNCs) and nanoparticles are also commonly used in active packaging. CNCs can be derived from organic waste and are used to improve tensile strength, water resistance, thermal resistance and barrier properties when incorporated into bioplastic films.58 For example, cellulose nanoparticles have been used within a PVA film as a reinforcement and acted as an active component to elongate the shelf life of prawns.59
Furthermore, bacterial cellulose (BC), synthesised by bacteria, has been researched for biomedical applications. BC has a milder purification method than plant cellulose and does not utilise biomass.60 However, currently its production is limited by cost and low capacity. The high production costs can be attributed to the nutrients required as substrates for the bacteria or algae.52 BC films, fibres and nanocrystals are all promising materials for biodegradable food packaging.61 Bacterial cellulose is usually added to a composite film as a suspension or used as the film itself since BC required ionic liquids or harsh chemicals for dissolution.61 Bacterial cellulose has been combined with curcumin and chitosan to form a composite active film using a simple mixing method followed by solution casting.62 BC is highly fibrous and could act as a substrate on which other biopolymers are added to in order form composite films. Moreover, BC has been reported to be self-healing in the context of wound covers, which may have potential applications in the field of active packaging.63 BC nanofibrils, formed by H2SO4 treatment, have been utilised as reinforcement agents for bio-nanocomposite films to modulate mechanical and barrier properties.64
Hydroxypropyl methylcellulose (HPMC) is a hydrophilic matrix material with promising applications in AP technology. HPMC is made by the alkaline, acidic and etherification treatment of cellulose. The film-formation method described by Wrona et al. (2017), originally used by Dow Chemical company (2002) is simple and reproducible.51 However, HPMC is water-soluble and therefore not suitable for high water-content foods. Cross-linking HPMC with citric acid has been reported to reduce the water solubility of the bioplastic.65 HPMC is scalable, but due to solubility issues it is often used in fibres and incorporated into composites rather than as the film material. Furthermore, the scale-up of HPMC often requires mixing with polyethylene oxide (PEO), especially for extrusion methods.66,67 Another derivative of cellulose is carboxymethylcellulose (CMC), CMC has been used in a composite with curcumin and ZnO to form an active film with good antimicrobial activity and improved water-vapour barrier properties.68 Overall, cellulose has good thermal resistance, but in many cases, it has a high hydrophilicity which limits its stability and use as a packaging material.52
2.2.4.3 Chitosan.
Chitosan is obtained by the treatment of chitin with NaOH or by enzymatic methods using chitin deacetylase. Chitin is obtained from the demineralisation, deproteinization and decolouration treatment of shellfish waste. Chitosan is a fully compostable, non-toxic bioplastic with good potential to replace conventional plastics, and it has been approved as a food ingredient by the FDA. It is the second most abundant organic compound after cellulose, and may be produced on a large scale.69 Importantly, chitosan is an example of a biopolymer for which the production does not require the use of land which could also be used for subsistence crops. Using a waste product is highly beneficial for production, however, there remains a high cost of implementation in comparison to conventional plastics. It is expected that, whilst this is currently a limiting factor, the cost should decrease with increasing demand. Chitosan can also be obtained from fungi, which may overcome any perceived issues with legislation on selling products derived from animal waste or public concerns regarding seafood allergens.69 Furthermore, this reduces the need for NaOH which, at high concentrations can be toxic to plants.
Importantly, Chen et al. (1998) reported the inherent antimicrobial activity of deacylated chitosan against Gram-positive and Gram-negative bacteria.70 Furthermore, natural active compounds have been incorporated into the chitosan matrix to improve this effect.71–73 Chitosan has good film-forming properties; however, literature studies have reported poor mechanical properties and high water sensitivity.14,31,74 For this reason, composites of chitosan are typically used, composite films are also commonly investigated to improve bioplastic properties relative to the natural polymer. For example, composite films of chitosan-HPMC were cross-linked with citric acid to reduce water solubility and the resulting film successfully inhibited the growth of Listeria monocytogenes.28 Chitosan may also be used to encapsulate active agents within nanoparticles for active packaging.75,76 Florez et al. (2022) recently reviewed chitosan uses in the context of active an intelligent packaging.77
For the scale-up of biopolymeric films and structures, chitosan is suitable for injection moulding and film casting to form thin films and acidic aqueous solutions are typically used to form chitosan solutions.69 In a report by Fernandez and Ingber (2014) detailing the successful scale-up of chitosan by injection moulding, 80% of the solvent of the chitosan solution was removed before moulding at 80 °C, and CaCO3 was added as a filler to prevent shrinkage and reduce costs.69 The scalability of methods including electrospinning and melt-extrusion for chitosan may require additives such as polyacrylic acid polyethylene oxide (PEO).78 Moreover, chitosan is a natural biopolymer, with good a biodegradation capacity that may be increased with the use of hydrolase and chitinolytic enzymes.79
2.2.4.4 Alginate.
The polysaccharides alginate and agar are extracted from seaweed. These biopolymers have good mechanical properties including high tensile strength and elongation at break values.80 Natural films of alginate are also inherently antimicrobial and hydrophobic. The mechanical, barrier and thermal properties of alginate films may be improved by adding nanofillers or by blending with other polymers such as PLA.81 For example, Huq et al. (2012) added nanocrystalline cellulose to alginate in order to improve film-properties.82 An edible packaging material was recently reported incorporating alginate, aloe vera and garlic oil.83 Importantly, good barrier properties and antimicrobial properties were reported for the active coating, eluding to promising implementation in the food packaging industry.83 Moreover, seaweed polysaccharide films can be water-soluble, compostable within a suitable timeframe, and renewable.4 However, one drawback of the use of alginate for bioplastic packaging is the possible accumulation of toxic metals in seaweed taken from industrial coastlines.80
2.2.4.5 Pectin.
Pectin is a low-cost, non-toxic polymer which is largely used in active packaging research due to these attributes. Moreover, pectin can be obtained from food waste as a valorisation technique. Indeed, the main source of pectin is citrus peel waste. Hydrophilicity and thermal instability have been highlighted as issues hindering the commercialisation of pectin-based materials. However, a recent review by Huang et al. (2021) discusses the modification of pectin based packaging to overcome these shortcomings and highlights pectin as a promising material for active packaging, with a discussion of possible film-formation methods.84
2.2.4.6 Zein.
Zein is extracted from maize and makes up almost 80% of the plant protein within corn.85 Zein is an abundant biopolymer which is applicable to bioplastic film-formation methods. For example, zein has been combined with the active agent thymol to produce an edible active film, and electrospun fibres of zein have also been used for encapsulation in active packaging technology.86,87
2.2.4.7 Rice husks.
Rice husks are derived from agricultural waste material. This valorisation of waste avoids open-air burning or landfill end-of-life scenarios and so improves the sustainability of the material. Recently, the encapsulation of eugenol within rice husk tar microparticles has been reported.88 The group described bio-composite films based on alginate containing the rice-husk microparticles with suitable properties for food-packaging applications. Recently, rice husk tar was obtained by the pyrolysis of rice husk biomass using a pilot scale reactor, displaying the capability of scaling up this technology.88 However, the scale-up capacity of the rice husk based active packaging could be limited by the use of dichloromethane to dissolve the tar for microparticle synthesis and energy-intensive pyrolysis extraction methods.
2.3 Promising biopolymers for active packaging development
Considerations to be made for biopolymeric active packaging include the use and valorisation of waste materials, the biodegradability of the material, and the availability and cost of the source for the biopolymer materials. Another consideration is the potential ethical concern of utilising commodity crops such as corn for these packaging materials instead of food. Two particularly valuable biopolymers identified in this review are alginate and chitosan, with pectin, rice husks and bacterial cellulose also defining important areas of development. Chitosan is a naturally occurring biopolymer derived from shellfish waste. Alginate is derived from seaweed, which is also sequesters carbon during its growth. Interestingly, these biopolymers may both be considered as inherently antimicrobial, improving the shelf-life of food before the addition of antimicrobials or antioxidants for active packaging purposes. Both biopolymers have good biodegradation capabilities, a discussion of these values will follow in section 3.3 of this review.
Encapsulation technology may be considered revolutionary in active packaging development to control the release of active agents such as antimicrobials to optimise the shelf-life extension of food. To this end, the biopolymers mentioned in this section are also used in active packaging to encapsulate active compounds and allow for controlled release. Furthermore, the biodegradability is related to the release capacity of these materials. For example, persisting plastics may have poor release profiles, whereas chitosan nanoparticles have been reported extensively with good release profiles for both drug delivery and active packaging.89,90 For a more in-depth of discussion of encapsulation and controlled release methods, a review was recently published by our group.17
2.4 Sustainable development considerations for active packaging materials
Currently, competition from inexpensive synthetic plastics with proven performance has led to a low incentive for manufacturers to utilise bioplastics (BPs). The expense associated with BPs may be attributed to the smaller production capacity and increased cost of raw materials. Indeed, the market share of commercialised bioplastics in 2017 was less than 1%.1 However, this value has been predicted to increase to 40% by 2030.1 Poor water solubility of certain bioplastics is concerning due to the difficulty of disposal using the current waste infrastructure.
The sustainability of biopolymeric alternatives for food packaging materials should also consider the synthetic route. To minimize environmental impacts of the extraction and modulation of biopolymers, it is important to adhere to green chemistry principles. Dupe and Salehpour (2014) highlighted the importance of this, and detailed specific examples including the use of different types of catalysis.91 Sustainability metrics should always be considered for the complete synthetic route of an active biopolymeric film. Some relevant principles to adhere to in this instance include reducing solvent usage, optimising atom efficiency, and minimizing the use of hazardous chemicals during synthesis. Furthermore, a low environmental (E)-factor describes a process with minimal waste and is often indicative of a more sustainable chemical process. For example, biodegradable plasticisers should be utilised to improve the overall sustainability of the bioplastic material.92 Importantly, a focus on biodegradable bioplastics for active packaging will satisfy the principle of design for degradation, which is vital a vital metric relating to a reduction in plastic waste.
3 Environmental impacts of biopolymers: defining biodegradability
3.1 Recognised standards and definitions for biodegradability
There is a lack of clarity in the literature when defining biodegradability. Biodegradability does not have one recognised definition, and many plastics that may be termed biodegradable take years to fully degrade, or even disintegrate into microplastic pollution.4 Biodegradability defines a process and not a specific timeframe nor conditions. Biodegradation tests do have recognised standards; however, these are relatively general such as minimum and maximum incubation periods. A substance may be termed as ‘inherently degradable’ if it degrades by at least 70% within 14 days.93 A bioplastic could be termed as ‘ultimately degradable’ if it degrades by at least 90% within 6 months in aqueous environments, or 24 months in soil.93 Thus, there is an opportunity for microplastic-forming plastics to be defined as ‘biodegradable’ within these definitions. Harrison et al. (2018) provided an important review on biodegradability standards of plastic bags in aquatic environments, highlighting that new standards should be put in place to address issues of toxicity and microplastic formation.94
A life cycle analysis (LCA) is an assessment of the environmental impact of a process or material throughout its lifetime. The biopolymer should be derived from renewable substances by cyclic processes and the raw materials should be annually renewable in order to provide a viable sustainable alternative to conventional plastics.69 There have been many literature examples of LCA of bioplastics in recent years, including reviews on LCA methods.95–97 An LCA for PLA reported a 40% reduction in GHG emissions in comparison to traditional plastics such as polyethylene (PE) and polyethylene terephthalate (PET).98 A life cycle analysis can typically be described in terms of a ‘cradle to grave’ lifetime of a material. For example, to satisfy a cyclic process, the source of a biopolymer must not compete with food production (cradle) for its raw material and the end-of-life options (grave) must recover value for feedstock. Therefore, the production of biopolymers must not compete for resources for basic human needs and the biopolymer must be rapidly broken down.69
3.2 Biodegradability versus compostability
The biodegradability of polymers depends on; (a) the chain length or molecular weight of the polymer, (b) the complexity of the chemical formula and (c) the crystallinity of the polymer.1,99 The highest degradation rate generally occurs for low molecular weight amorphous polymers with low levels of complexity. On the other hand, compostability relates to a type of enhanced biodegradation under managed environmental conditions optimal for degradation including high temperature, high humidity, aerobic conditions and the presence of microorganisms.1 Test methods for industry to determine the compostability of a material include biodegradation tests (ISO 14855), disintegration tests (ISO 16929), ecotoxicity tests and heavy metal tests.36 The maximum testing period for composting is 180 days, within a specified temperature range.100 Composting provides nutrient rich material, whereas landfill releases CO2 and methane, therefore it is highly beneficial to replace conventional single-use plastics with compostable alternatives. Importantly, compostable plastics made from plant matter remain compostable when contaminated with food, unlike conventional plastics which would be rendered non-recyclable and sent to landfill.4 Importantly, the environment for degradation will have a large effect on the compostability or biodegradability of a biopolymer, including the presence or absence of microorganisms to aid degradation.36 Managed (industrial facilities) and unmanaged (natural environments; soil, water, landfill, compost) degradation methods often have distinct results due to varied environmental conditions, such as UV light exposure and the presence or absence of oxygen.36
3.3 Quantifying biodegradability values
Quantification of biodegradability is difficult as it depends on many factors, but clarification may be enabled by mechanistic studies of the degradation of bioplastics.99 Ideally, bioplastics would degrade under natural composting conditions. Furthermore, the products of biodegradation may be used as feedstock materials. For example, starch and cellulose biodegrade into products which may be used as feedstock including CO2, water, humic matter, CH4 and biomass.21 However, some BPs require bioactive environments or bioconversion facilities to completely degrade. These environments utilise enzymes, bacteria, fungi or algae to break down the material, although chemical hydrolysis is also possible.
There is discrepancy between the results of laboratory and field testing of compostability. Laboratory condition are reproducible with optimal temperatures and humidity levels, whereas field tests encounter fluctuation and variation over time.36 Overall, field tests are much more complex and are more likely to study disintegration of the bioplastic rather than focusing on one variable such as CO2 evolution therefore a bioplastic may perform well in the laboratory, but not degrade well in the environment.36,101 Interestingly, Kijchavengkul et al. (2006) built, calibrated and tested an automatic respirometric system used to elucidate biodegradation from the amount of CO2 produced, reporting values for PLA, PET and corn starch.102 Furthermore, Raman spectroscopy may be used to detect modification of chemical bonds and relate this to biodegradation rates.103 It is worth noting that weight loss of the material may be considered a secondary parameter, and CO2 evolution is preferable to determine biodegradation rates.36 Importantly, the tests must be carried out on the final form of the material, including any active agents or other additives. Table 1 shows biodegradation values for several biopolymers, these values are ranked subjectively as low, medium or high biodegradability.
Table 1 Ease of biodegradation of certain bio-based or petroleum-based biopolymers and experimental conditions used to determine these values
Category |
Biopolymer |
Biodegradability (%) |
Bio-degradation ranka |
Method used |
Test environment |
Conditions |
Time period (days) |
Ref. |
Rank created subjectively, where low biodegradability is 0–10%, medium biodegradability is 10–70% and high biodegradability is >70%.
|
Bio-based |
Chitosan (medium MW) |
100 |
High |
Weight loss |
Aqueous medium |
30 °C |
35 |
136
|
Alginate |
90 |
High |
Weight loss |
Compost |
32 °C, 35% relative humidity (RH) |
35 |
137
|
PLA |
84 |
High |
CO2 produced |
Compost |
58 °C, pH 8.5, 63% RH |
58 |
138
|
PLA |
10 |
Low |
Weight loss |
Soil |
30% moisture content (MC) |
98 |
139
|
PLA |
13 ± 3 |
Low |
CO2 produced |
Compost |
58 °C |
60 |
140
|
PHB |
79.9 |
High |
CO2 produced |
Compost |
58 ± 2 °C |
110 |
141
|
PHB |
64.3 |
Medium |
Weight loss |
Soil |
Not reported (laboratory conditions) |
180 |
142
|
Starch-based |
14.2 |
Low |
CO2 produced |
Soil |
60% MC, 20 °C |
110 |
143
|
Cellulose acetate |
100 |
High |
CO2 produced |
Compost |
53 °C |
18 |
144
|
PHA |
48.5 |
Medium |
CO2 produced |
Soil |
60% MC, 20 °C |
280 |
143
|
PHA |
5.7 |
Low |
Weight loss |
Compost |
39–43 °C |
56 |
106
|
Petroleum-based |
PBAT |
34–67 |
Medium |
CO2 produced |
Compost |
58 °C |
45 |
145
|
PBS |
1 |
Low |
Weight loss |
Soil |
25 °C, 60% RH |
28 |
146
|
PBS |
90 |
High |
CO2 produced |
Compost |
Aerobic, pH 7–8, 58–65 °C, 50–55% MC |
160 |
147
|
PCL |
11.7 |
Low |
Weight loss |
Compost |
39–43 °C |
28 |
106
|
PLA is often described as biodegradable, but it only degrades within a suitable timescale using industrial composting facilities with high temperatures (60 °C).1 A study by Narancic et al. (2018) determined the biodegradation of 7 different biopolymers and composites formed by blending biopolymers.100 The study investigated managed composting scenarios including home composting, industrial composting and anaerobic digestion.100 Additionally, the study measured unmanaged soil, anaerobic conditions, marine and freshwater conditions.100 The experiments concluded that only TPS and PHB degraded in all of these environments, with the other 13 biopolymers or composites failing in at least one category.100
Another analytical method which may be used to study biodegradation of polymers is neutron scattering. Neutron scattering studies on the dynamics of polymers and biopolymers are becoming more prevalent in literature relating to active packaging technology. Interestingly, previous small-angle neutron scattering (SANS) studies using cellulose as the biopolymer of interest have shown that the pore size and distribution of this material determined the enzymatic digestion rate.104 The group determined that small pores were not accessible to cellulase, and larger pores were only accessible with mild agitation.104 In this case, the enzyme was able to degrade the cellulose from within the pores and open up the internal structure by digestion to initiate the biodegradation process.104 This was observed using SANS by using a D2O buffer for the enzyme and exploiting the contrast between hydrogen and deuterium with this technique due to the large difference in their scattering cross-sections.104
3.4 Factors affecting the rate of biodegradation of biopolymers
Biodegradation may occur by aerobic or anaerobic digestion, with or without oxygen, respectively. Alternatively, mechanical and chemical recycling are useful technologies being researched currently for bioplastics with long degradation times and other plastics that are usually poorly degradable. Payne and Jones (2021) recently reviewed the topic of the chemical recycling, highlighting the benefits of obtaining valuable platform chemicals as a result of this process.105 Moreover, enzymes, catalysts and microbes are able to selectively degrade polymers.1 The biodegradation rate is related to the chemical structure of a compound. High complexity retards degradation as different microorganisms may be required to attack the increased number of different chemical bonds.99 Enzymes can increase the rate of biodegradation for biopolymers. For example, the biodegradability of PCL, measured by the weight loss, increased from 11.7% to 27.7% with the addition of Streptomyces sp. BV315.106 Furthermore, chitosan can be degraded by specific bond-cleaving enzymes, which aid biodegradation.107 Interestingly, chitosan has been explored for use in drug-encapsulation technology for medicines because it is thought to degrade by the action of lysozyme and enzymes in the colon.107 This biodegradation or enzymatic degradation technology enables value to be recovered to make feedstock, which provides obvious benefits over thermal pyrolysis methods which use high temperatures to achieve plastic degradation.4 Furthermore, bioconversion facilities have the potential to yield valuable chemical compounds from bioplastic waste, on a large scale.21
3.5 Water-soluble bioplastics
The end-of-life scenario of the bioplastic is an important consideration. There are issues with conventional water-soluble plastics. Whilst these plastic materials may degrade with additives and thus may be termed ‘biodegradable’ under the current definition; they may also lead to microplastic formation. On the other hand, non-water-soluble bioplastics pose issues due to poor waste infrastructure, leading to the eventual disposal of these materials in landfill. There is not yet suitable infrastructure to deal with these end-of-life options and the large-scale disposal of bioplastics. Landfill conditions are dry and reduce biodegradation rates, which leads to a loss of biowaste. This biowaste could otherwise be valorised into compost, chemicals or energy.21 Thus, water soluble bioplastics such as HEC and CMC have the most promising end-of-life scenarios at present. These particularly bioplastics may enter water treatment facilities, of which the infrastructure is already widely available.21
3.6 Outlook
Strikingly, a recent study determined that plastic bags which had been labelled as biodegradable did not degrade substantially in soil or marine environments over a 3 year period.108 Therefore, it is vital that the behaviour of active packaging materials is tested in different end-of-life scenarios to determine the optimal route of disposal. Furthermore, the microplastic formation tendency of bioplastics should also be investigated. Many bioplastics require controlled composting conditions with high temperatures. However, industrial composting facilities such as these are rare. Options for recycling may include chemical and mechanical methods. However, the lifetime of polymers is reduced during recycling due to the reduction in chain lengths.4 Recycling and home-compost schemes rely on public participation to be effective. Furthermore, if the compostable or recyclable bioplastics end up in landfill, it is likely that the low oxygen conditions will hinder degradation and these polymers may then persist. Therefore, it is important that the disposal routes are clearly marked on commercialised packaging to optimise the benefits over conventional fossil-fuel based plastics. Taking this into account, the primary certification required for development of a biodegradable active packaging material is compostability. Following this, soil- and marine-degradable certifications may be required for specific materials. Third-party certifications such as these are vital in the development from laboratory research to producing a marketable material.
4 Packaging properties for commercialisation
4.1 Outcompeting conventional plastics
Plastics make up a large proportion of global waste including marine litter, which can develop into microplastics and form a microbial biofilm termed a “plastisphere”.14 The toxicity of microplastics has been raised as a human health concern.14 Indeed, polyfluorinated plastics, often used as moisture barrier materials, are highly complex to remove from the environment and are often considered to be carcinogenic.14 On the other hand, bioplastics (BPs) are synthesised from plant matter containing CO2. During biodegradation, BPs are converted to CO2, CH4, water, biomass and humic matter.21 Naturally sourced BPs are the primary choice for sustainable packaging due to their biocompatibility, biodegradability and lack of toxicity providing potential for industrial application.14 For the specific application in active packaging for food, different types of packaging have different metrics of success. For example, hard plastics for meat trays will have different requirements than plastic wrapping used to cover fruit and vegetables. The eventual use of the active packaging material relates to the metrics possible. For example, flexible films are commonly made from cellulose due to its inherent film-forming properties.
Properties of considerable importance for the biopolymeric substrate include mechanical properties such as tensile strength (MPa), Young's modulus (MPa) and elongation at break (%). Physical properties to consider include gas permeability, water-vapour permeability, optical properties, thermal properties, morphological properties, moisture content and water solubility. Moisture content and solubility values may be determined through mass-balance calculations.109 Good barrier properties are especially important for bioplastics because gases such as oxygen speed up food degradation rates, and poor barrier properties may allow pathogens to enter the packaging material.5 Protection from UV light is also important to reduce food spoilage. Therefore, the evaluation of optical properties such as opacity and transmittance is vital. For example, spectrophotometry may be used to determine the transparency of a film.110 Moreover, the thermal stability of a polymer blend is related to the molecular weight of the polymer, the functional groups present, the cross-linking degree, the crystallinity and the degree of polymer branching. Table 2 provides a comparison of several popular bioplastic materials in terms of their thermal stability, general properties, cost and availability. The table includes the values for PET as a comparison to fossil-fuel based plastic properties (Table 2). For biopolymers to pose real advantages over conventional plastics, they must not only meet the requirements for these properties, but also biodegrade within a suitable timeframe.
Table 2 A comparison of selected characteristics relating to scalability of biodegradable biopolymers for active packaging
Biopolymer |
Thermal stability/melting temperature (Tm) (°C) |
Tensile strength (MPa) |
General properties and availability |
Cost (USD kg−1) |
Ref. |
Chitosan |
T
m: 111.15 |
21.07 |
Abundant valorisation of crustacean shell waste |
30 |
52, 70, 148 and 149 |
Non-toxic |
Inherently antimicrobial |
Stability: 200–220 |
Not water-soluble (pH 7), forms hydrogels |
Mild synthetic conditions (1% acetic acid) |
High biodegradability |
Rice husks |
Stability: pyrolysis temperatures > 400 |
106–136 |
Valorised agricultural waste |
3.58–3.77 (production cost) |
88 and 150–153 |
Scalable synthesis of rice husk tar microcapsules |
Extracted by pyrolysis |
Alginate |
T
g: 80.6 |
33.6 |
Inherent antimicrobial effect |
100 |
154–156
|
Suitable for edible packaging |
Cellulose (HPMC/BC/CA) |
T
g: 160 (HPMC) |
17–46 |
Transparent films, water soluble (HPMC) |
3–10 |
1, 52, 157 and 158 |
Higher cost of production (BC) |
T
m: 164 (CA) |
Limited scale of production (BC) |
2.49–3.40 (CA) |
Milder purification than plant cellulose (BC) |
High tensile strength (H-bonding) |
Starch |
Stability: 150 (TPS) |
9.7 (TPS) |
High abundance |
2.43–4.85 (starch blends) |
52, 159 and 160 |
Low-cost |
Non-toxic |
Often brittle |
High biodegradability |
Zein |
T
g: 90 |
3.1–4.2 |
Derived from food crops |
200 |
161–164
|
Stability: 120 |
Pectin |
T
m: 233 |
9.65 |
Derived from food waste |
25–35 |
165–167
|
PLA |
T
m: 151.10 |
58.2 |
GRAS by the FDA |
3.31–3.5 |
1 and 168 |
Used on large scale |
T
g: 67.9 |
Relatively slow degradation |
PHAs |
Stability: 175 (PHB) |
20–40 (PHBV) |
Obtain from wastewater or bacteria |
6–30 (PHB) |
1, 47, 52, 169 and 170 |
Stability: 136–162 (PHBV) |
Composted with enzymes |
6.86–20.26 (PHBV) |
Some thermal instability issues |
High tensile strength |
PET |
Stability: 212–265 |
55–79 |
Derived from fossil fuels |
1.51–2.12 |
1 and 52 |
4.2 Overcoming issues with biopolymer properties
Unfortunately, few biopolymers are suitable for thermal and mechanical processing by either extrusion, injection moulding or thermoforming.16 The poor processability of biopolymers is a major hindrance to AP development. One method of overcoming this is to modify the structure to increase thermoplasticity.16 Adding plasticisers such as glycerol and polyethylene glycol (PEG) can increase the plasticity and flexibility of a material, improving the elongation at break values. Many plasticisers are derived from crude oil. The most popular plasticisers within this category including phthalates and adipates are used on an industrial scale. However, natural alternatives include soybean oil and rapeseed oil are becoming increasingly popular.92 Moreover, glycerol is ubiquitously used in research as a plasticiser. Interestingly, Jakubowska et al. (2022) recently utilised a choline chloride/citric acid deep eutectic solvent as a plasticiser for chitosan, reporting improved elongation at break of the biopolymer.111 Furthermore, many biopolymers including PLA and PHAs are highly crystalline and have poor thermal stability. Therefore, only small temperature ranges are available for these materials and consequently, they have poor processability.1 Chain grafting, branching or cross-linking may be used improve the thermal stability and tensile strength of a polymeric material.1
Water-solubility and water vapour permeability are important metrics relating to the eventual use of the food packaging material. Many biopolymers are water-sensitive, however the sensitivity may be reduced by cross-linking (chemically, photochemically or thermally), lamination with other polymers, heat-sealing methods, blending with other polymers or hydrophobic plasma treatment.28 For moisture control, polyacrylate salt polymers and graft copolymers of starch have also been recorded to absorb water.112 Interestingly, Inthamat et al. (2021) improved the moisture barrier of a film based on chitosan and astaxanthin by heat curing.113 Furthermore, brittleness and rigidity are common issues faced by bioplastics, which may be overcome with mechanical reinforcements.1 For example, modified silica nanoparticles improved the mechanical and barrier properties of a chitosan film.114 Additionally, most BPs have lower ductility, tensile strength and flexibility than conventional plastics.1
4.3 Barrier properties to gases and moisture
Barrier properties are also of concern for bioplastic use in active packaging, specifically oxygen permeability and water vapour permeability. Good barrier properties reduce the lipid oxidation rate in food and the humidity within the packaging, leading to a reduction in microbial contamination. Lamination, blending or coating with barrier plastics such as petroleum based PP and PE can improve the barrier properties of packaging materials.1 The blending of polymers is a well-known technique used to modulate properties to a more desirable level for their application.100 To this end, bioplastics are often combined with high barrier materials to decrease permeability values.115 Furthermore, dispersion coating may be used to provide barrier coatings to materials with inherently high permeability to gases and water vapour, this technique may also be used on materials such as cardboard to improve these properties.
The use of nanofillers can be used to modulate the mechanical and barrier properties of biopolymers.16,116 For barrier properties, cellulose nanocrystals (CNCs) are often be used, other fillers include xanthan gum and rice husk flour. CNCs can be derived from organic waste and are used to improve tensile strength, water resistance, thermal resistance and barrier properties when incorporated into bioplastic films.58 Harris and Lee (2008) reported that increasing the degree of crystallinity of PLA films using fillers such as nanocellulose improved mechanical properties of the film.117 Similarly, the addition of nanofillers such as clays has also been reported to improve oxygen and other gas-barrier properties.118,119 This method functions by increasing the diffusion path within the material.1 Moreover, the uniform dispersion of nanofillers in a composite film may be achieved by using ultrasonication.52 Biopolymer–nano-clay composite materials have good sustainability and low toxicity profiles. Nano-clays are used extensively to fabricate nanocomposite films with improved barrier properties. Furthermore, Bertolino et al. (2020) recently reviewed smart bio-nanocomposite materials and discussed the drug-delivery capacity of these materials.120 Moreover, the sustained release of active agents from active packaging can be achieved using these nanocomposite materials.
Importantly, the active agent used in active packaging can influence the properties of the biopolymer substrate. It is vital to note that the degree of change will largely depend on the percentage of the active agent in the film. Fig. 3 and Table 3 show a visualisation of the percentage change in certain bioplastic properties upon the addition of an active agent to the material. As seen in Fig. 3, the addition of banana peel extract to a chitosan film reduced the tensile strength, elongation at break, and Young's modulus values of the BP film.72 The individual effects are variable; however, the active agent evidently modulates important material properties of bioplastics (Fig. 3). Furthermore, a recent study determined that the addition of garlic extract and TiO2 nanoparticles enhanced the water vapour transmission rate, oxygen transmission rate, mechanical properties and antimicrobial properties of a CMC/arabic gum/gelatin composite film.121 Therefore, studies on bioplastic active packaging materials should compare the bare film and active film for optimisation of physical properties.
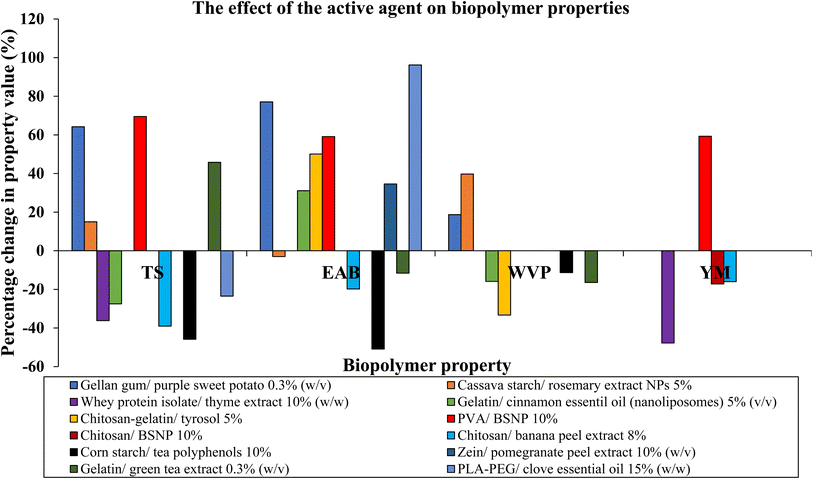 |
| Fig. 3 Schematic bar chart showing the percentage change in certain biopolymer properties upon adding an active agent. The properties included are tensile strength (TS), elongation at break (EAB), water vapour pressure (WVP) and Young's modulus (YM). The references were chosen as a range of composites formed by film casting, with between 0.3% and 15% content of the active agent. It may be deduced that from this selection of references (Table 3), there is no clear pattern in the change in properties upon adding active agents and the effect is property specific. Instead, this highlights the variation between different biopolymers and different active agents and the values of these properties. However, it may be deduced that TS and EAB are mostly sensitive to the addition of an active agent. Where there is no bar for a property, either the paper whether did not report the value, or the change was not statistically significant. | |
Table 3 Data utilized and extracted for Fig. 3
Example |
Ref. |
Gellan gum/purple sweet potato 0.3% (w/v) |
171
|
Cassava starch/rosemary extract nanoparticles 5% |
110
|
Whey protein isolate/thyme extract (10% w/w) |
172
|
Gelatin/cinnamon essential oil (nanoliposomes) 5% (v/v) |
173
|
Chitosan–gelatin/tyrosol 5% |
174
|
PVA/biosorbed-silver nanoparticles (BSNP)10% |
175
|
Chitosan/BSNP 10% |
175
|
Chitosan/banana peel extract 8% |
72
|
Corn starch/tea polyphenols 10% |
53
|
Zein/pomegranate peel extract 10% (w/v) |
176
|
Gelatin/green tea extract 0.3% (w/v) |
177
|
PLA–PEG/clove essential oil 15% (w/w) |
178
|
4.4 Outlook on improving bioplastic properties for commercialisation
As previously mentioned, the mechanical and barrier properties of bioplastics are often a hindrance to bioplastic development beyond the lab-scale. Interestingly, quantitative water vapour permeation changes are widely reported in the literature, unlike the determination of gas-barrier properties.16 As shown by Fig. 3, the important mechanical and barrier properties of bioplastics are altered by the incorporation of active agents. Therefore, studies on bioplastic active packaging materials should compare the bare film and active film for optimisation of physical properties. Moreover, investigations on active packaging film properties should determine the barrier properties of the material and include values of the bare polymeric films without the active component for comparison. Importantly, any added substance must be taken into account when considering end-of-life processing, as biodegradation rates may be altered.122 Moreover, research on this topic often focuses on packaging properties, and less so on the effect when applied to the eventual use to package real food material.31 Further research into the final application of the material, for example by applying the bioplastic film to food products, would improve the commercialisation success of active packaging.
5 Film-forming techniques for bioplastic production
5.1 Scale-up of bioplastics
Films for research studies are commonly made using the solvent casting technique. Other film-formation methods include extrusion, injection moulding, thermoforming, blow-moulding, electro spraying and electrospinning.1,8,123 Extrusion and injection moulding are commonly used for conventional plastic production. This discrepancy between laboratory scale research methods and large-scale production methods may hinder the commercial development of active packaging. This section will discuss several different film-forming technologies and their advantages and disadvantages, relating to their industrial feasibility for active packaging materials.
Certain bioplastics are not suitable for commonly used scale-up methods. For example, HPMC has a high glass transition temperature (Tg) and a low degradation temperature, therefore it is challenging to achieve scale-up using extrusion methods.124 However, Ma et al. (2013) utilised the plasticiser propylene glycol (PEG) to achieve hot melt extrusion of the biopolymer.124 Chitosan is not thermoplastic, therefore it also has similar barriers to the use of extrusion methods for scale-up operations.125 However, mild heating of concentrated chitosan bioplastic solutions can allow for casting into moulds or injection moulding techniques.69 On the other hand, alginate may be suitable for extrusion techniques.126
5.2 Film-forming technologies
The polymer-processing and film formation technique is reliant on the type of material required for the active packaging application. For example, hard bioplastics made by injection moulding are used for robust food trays, whereas thin flexible films made by film casting are more suitable for wrapping materials. The following section is a discussion of commonly used film-forming techniques. However, the eventual film-forming technology used will rely on both the inherent properties of the biopolymer and the eventual application of the material.
5.2.1 Film casting.
Film casting, or solvent casting, is the most common technique utilised in the literature to prepare biopolymeric films for small-scale research. The polymer is dissolved in solvent, a thin layer of polymer solution is formed on a substrate and then evaporation of the solvent under ambient conditions affords a polymeric film.8 Despite the popularity of this technique, experimental conditions such as temperature and solvent choice affect the mechanical properties, controlled release properties and morphology of the film.8
5.2.2 Injection moulding.
Injection moulding is a scalable technology used to make hard plastics from conventional polymers. The molten polymer is injected into a mould and allowed to cool to form a 3D structure. Chitosan been used to make 3D structures using injection moulding.69 Chitosan was heated to 80 °C to decrease the velocity before injection moulding, the heat also ensured that the bioplastic adhered to the walls of the mould.69 Other bioplastics with properties similar to petroleum-based polymers are applicable to this technique, including PLA.
5.2.3 Electrospinning.
Electrospinning uses a high voltage electric field to form nanofibers by stretching a polymer. The resulting fibres have a high surface area to mass ratio and may be functionalised further. Electrospun fibres show promise as an encapsulation technology for use in active packaging.127,128 Bangar et al. (2021) reported good control over film structure, low costs and high surface area to volume ratios achieved using this technique.12Fig. 4 shows a schematic representation of electrospinning and film-casting techniques. Electrospinning may pose as a promising technology to bridge the gap between small scale research and conventional scale-up methods where the active packaging components are not suitable for high temperature processing methods. Biopolymers may be hard to electro-spin as the pure material, therefore many studies have combined bioplastics with polymers such as PEO in order to form spinnable solutions.129
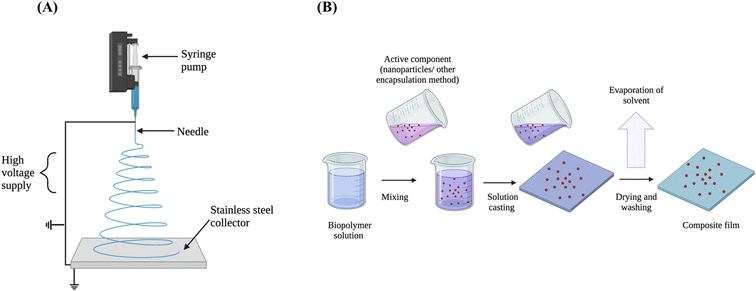 |
| Fig. 4 Schematic representations of film forming technologies; (A) electrospinning, (B) solution casting, created with https://BioRender.com. | |
5.2.4 Extrusion.
Extrusion is used for traditional plastic formation, and is a preferential technique for manufacturers.8 Extrusion may include melt-blending a biopolymer with an active component using a mixing chamber to form an active film.130 This material may then be heated and cooled to form sheets. Small pieces may be cut and added into a temperature-controlled rotating extruder to form the desired film.130 Similarly, injection moulding involves the injection of polymeric pellets in this manner for melt-processing.131 Biopolymers are often mixed with other polymers to achieve the properties required for this technique. For example, polyurethane–chitosan composites, with a chitosan content of 30% were melt-compounded to form composite films.132 Extrusion uses high processing temperatures, so the decomposition of temperature-sensitive active components is the primary concern for active packaging applications. Liu et al. (2009) detailed the reduction of nisin antimicrobial activity as a result of the high processing temperature (160 °C) of PLA during extrusion.133
5.2.5 Melt-spinning.
Melt-spinning involves melting and extruding a polymer, then spinning the resultant strands to reduce their thickness and induce orientation.127 However, the application of this technique to biopolymers is limited as high polymer decomposition temperatures and low melt viscosities are required.134
5.2.6 Solution blowing.
Solution blowing involves thermoplastic formation on a large scale by melt-extrusion, then pumping to form a single layer of polymer.127 This technique not yet commonly used for biopolymers, but has been utilised on conventional polymers.135
5.3 Outlook
Melt-spinning, solution blowing and electrospinning can be considered as promising technologies for the improvement of stability and controlled-release properties of active compound-containing films.127 Recently, 3D printing has also gained attention as a possible method to scale-up bioplastics using layer-by-layer deposition methods.52 Overall, the film formation method is determined by the choice of active agent, the biopolymer, the heat lability of the components and the compatibility between these components. Table 3 shows a critical comparison of film-forming techniques applicable to bioplastics, highlighting electrospinning as a technique with high potential for bioplastic film formation. Although film casting is the most used method of film formation in the literature, the scale-up capacity is not comparable to methods such as extrusion for conventional plastics (Table 4).
Table 4 Advantages and disadvantages of different film-forming technologies
Ranka |
Film-forming technique |
Advantages |
Disadvantages |
Active packaging example |
Subjective rank based on perceived industrial feasibility.
|
1 |
Extrusion (or co-extrusion, melt-extrusion, melt-processing) |
Provides good mechanical properties8 |
Not applicable to heat-resistant biopolymers |
PHBV based nano-composites with clay and oregano essential oil109 |
Industrial applicability |
Not applicable to non-thermoplastic biopolymers125 |
Scalable, production not limited by production scalable69 |
High shear forces and pressure may destroy active agent |
Relative abundance of facilities |
High temperatures may destroy active agent131 |
2 |
Electrospinning |
Thermally sensitive components may be used |
The processing conditions may influence the results obtained in terms of film properties127 |
Carvacrol encapsulated in electrospun zein and PLA fibers128 |
Simple, efficient, low cost, flexible and scalable |
Fibers may be used for encapsulation179 |
Low production rate on small-scale could limit scale-up potential181 |
Fibres can be spun into ‘mats’ with uniform thickness180 |
3 |
Film-blowing |
Large scale formation8 |
Not applicable to natural film-forming materials (lack of tenacity) |
Starch/PBAT films containing alpha tocopherol182 |
Simple continuous and low cost |
4 |
Injection-moulding |
Scalable technology commonly used for conventional plastics |
Equipment alterations may be needed to achieve thin films (thin wall injection moulding) |
PLA-thermoplastic cassava starch filled with duckweed biomass183 |
Quick production |
Common for hard-plastic items |
Applicable to biopolymers with properties similar to conventional plastics |
High temperatures may de-stabilise active agent |
3D materials can be made69 |
5 |
Film casting (or solvent casting) |
Common, simple technique |
High variability of the technique reduces viability of scale-up in industry |
Corn starch films containing tea polyphenols and porous starch53 |
Thermally sensitive components may be used |
Biopolymers and natural active compounds have favorable solubility characteristics for this method8 |
Tape-casting and continuous casting have been reported as a scalable versions of this technique184 |
Chitosan–nanoclay bio-nanocomposite films containing milk-thistle extract185 |
6 |
Melt-spinning |
May be able to encapsulate active compounds within fibres127 |
Only applicable to viscoelastic materials due to high stress during the ‘drawing process’ |
PCL, rosemary extract (melt-electrospinning)187 |
Commonly used to make textile fibres on a large scale186 |
High temperatures may lead to loss of active agent |
Limited to formation of fibres |
6 Concluding remarks on the potential of biodegradable bioplastics for active packaging
6.1 Hindrances
Limiting factors to bioplastic based active packaging development include manufacturing expenses, long degradation times, lack of processing facilities and issues with the supply of raw materials. To outcompete petroleum-based plastics, the bioplastic must utilise sustainable raw materials, have similar properties to conventional plastics and degrade within a suitable timeframe. Bio-based polymers have tuneable properties, high biocompatibility and are amenable to controlled release mechanisms. However, moving forward, standardised testing methods to determine the biodegradability of bioplastic-based active packaging composites are needed to prove the advantages over conventional plastics. Furthermore, the barrier properties of bioplastics are a hindrance to development. Gas barrier properties are vital due to the correlation between gases such as oxygen, and food degradation. Similarly, mechanical properties must be optimised to compete with conventional plastics. There are several techniques available to do this including polymer blending, cross-linking and the use of additives such as nanofillers.
Poor processability is a major hindrance to development. Current methods used to overcome this are based on increasing the thermoplasticity of the bioplastics through structural modifications. Relating to this, film casting is the most common technique used to form bioplastic films during research and development stages. However, this technique is highly variable, and the reproducibility is comparatively low. Other film-formation methods such as extrusion are more suitable for scale-up. However, often these other film-formation techniques are less suited to bioplastics. Electrospinning, melt-spinning and solution blowing have been highlighted as promising techniques for bioplastic film-formation. The cost of bioplastics is another developmental hindrance. The average price of bioplastics is currently greater than the average cost of conventional plastics. This may be due to small production capacity and larger cost of raw materials. However, the market share of commercialised bioplastics is expected to increase, with environmentally influenced investments. Another hurdle to commercialisation is the end-of-life option for the bioplastic active packaging. Dedicated collections are not yet available for this biopolymeric waste, and the implementation of these will incur a large cost.
6.2 Wider applications of active packaging materials
Other applications of active packaging based on biodegradable biopolymers include water filtration membranes and films for medical use, such as wound covers. In all cases, the active component of the packaging is vital to optimise the desired function of the material. For purification membranes, an antimicrobial bioplastic film would prevent the attachment of bacteria and microorganisms, reducing biofouling. Hence, replacements would be less frequent and therefore less waste would be produced. In contrast to some applications of active packaging, for the application of water-filtration, a water-soluble bioplastic would not be desirable. Medical wound-covers could also utilise this technology to prevent infections. This field of research, when applied to wound covers and other medical materials, provides the benefit of preventing infection whilst reducing waste with the use of biodegradable and biopolymeric materials.
6.3 Future trends and further developments required
Naturally sourced biopolymers are the primary choice in the development of bio-polymeric active packaging, and this is a ripe area of research. The biocompatibility and biodegradability common with these polymers are promising metrics for developing a compostable packaging material. This is seen with the development of edible films based on natural biopolymers. Examples of these polymers at the forefront of current research include seaweed biopolymers (carrageenan, alginate, agar), food waste biopolymers (pectin), pullulan, chitosan and starch. Bacterial cellulose also has high potential to be used for applications in biodegradable packaging. Water solubility is a key metric currently with the development of bioplastics due to a lack of suitable waste management infrastructure for non-water-soluble bioplastics. The current focus may then be directed to either (i) water-soluble bioplastics or (ii) bioplastics with well-defined biodegradation profiles which can be disposed of with food waste or composted. The former water-soluble bioplastics are unlikely to be successful for many food-packaging applications due to the high moisture content of foods and storage in fridge or freezer environments.
To move this field forward, there must be more research into the toxicity profile of bioplastics and active packaging composites. Stringent safety regulations on added substances are heightened in the case of food packaging. The active ingredients may be food-contact materials depending on the type of active packaging utilised. For example, release based active packaging would involve a determination of the concentration released into the headspace of the food packaging. Therefore, successful commercialisation will rely on good quality safety measurements of the material. Additionally, biodegradation studies are vital to evidence the benefit over cheaper fossil-fuel based plastics. These studies should be carried out on the final form of the bioplastic including active ingredients or additives. Commercialisation will undoubtably rely on the end-of-life scenario of the material. Importantly, the bioplastic should avoid landfill and break down in a controlled manner, without the formation of microplastic pollution. Future studies should also determine the properties of the bare polymeric film and the active film to form a comparison and determine possible optimisation strategies. Furthermore, a focus on the eventual application of packaging real food materials will enhance commercialisation success. In this sense, the packaging effect should be tested on real food. The material properties should also be tested under conditions mimicking those of storage and transport of packaging, over an extended period.
6.4 Concluding statement on biodegradable biopolymers for active packaging
Substantial investments into research, production and waste management are undoubtably required to ensure commercial viability of this technology. However, the biopolymer must meet the material property requirements and biodegrade within a suitable timeframe to successfully outcompete conventional plastics. The biodegradability should be rigorously tested to avoid the formation of micro- or nano-plastics that persist in the environment. The sustainability of the bioplastic will also rely on the use of a renewable supply of raw material, and the use of safe additives and active ingredients throughout its lifecycle. Nonetheless, it is evident that a major reduction in the unsustainable use of plastics is required on a global scale. This will drive an effort to develop the research and investments for the commercialisation of biodegradable and biopolymer-based, active packaging for food.
Furthermore, researchers and industry-partners should work collaboratively to advance the most promising biodegradable packaging materials from the current literature to commercialisation due to an environmentally pressured timescale. These materials should have a low-complexity synthetic route, low-cost component materials, abundant starting biopolymers and a viable translation to large-scale production. The current focus of the field of active packaging should be the scale-up and commercialisation of a biodegradable material which has similar properties to conventional plastics but acts to successfully increase the shelf-life of food and reduce wastage. Novel, more sophisticated inventions should be developed once we have achieved a method to reduce the vast amounts of plastic waste from the food packaging industry. Overall, this review has built upon the current literature by providing an outlook on bioplastics specifically for active packaging materials and detailing key considerations in their development.
Conflicts of interest
The authors declare no competing financial interest.
Acknowledgements
J. R. W. would like to thank the EPSRC for a PhD studentship. M. X. and X. Y. Z. acknowledge the funding support by National Natural Science Foundation of China (22008162), China Postdoctoral Science Foundation (2021M702016), and City-school Integration Development Strategy Project in 2021 (JNSX2021048).
References
- X. Y. Zhao, K. Cornish and Y. Vodovotz, Narrowing the Gap for Bioplastic Use in Food Packaging: An Update, Environ. Sci. Technol., 2020, 54(8), 4712–4732 CrossRef CAS PubMed.
-
UNEP, Single-Use Plastics: A Roadmap for Sustainability, 2018 Search PubMed.
-
EPA, Advancing Sustainable Materials Management: 2018 Tables and Figures, in Assessing Trends in Materials Generation and Management in the United States, 2020 Search PubMed.
-
C. Wood and P. Border, Plastic Food Packaging Waste, POST, 2019, POSTnote Search PubMed.
- A. Chamas,
et al., Degradation Rates of Plastics in the Environment, ACS Sustainable Chem. Eng., 2020, 8(9), 3494–3511 CrossRef CAS.
- A. Ragusa,
et al., Plasticenta: First evidence of microplastics in human placenta, Environ. Int., 2021, 146, 106274 CrossRef CAS PubMed.
- H. A. Leslie,
et al., Discovery and quantification of plastic particle pollution in human blood, Environ. Int., 2022, 163, 107199 CrossRef CAS PubMed.
- L. Y. Kuai,
et al., Controlled release of antioxidants from active food packaging: A review, Food Hydrocolloids, 2021, 120, 106992 CrossRef CAS.
-
FAO, Food wastage footprint: impacts on natural resources: summary report, 2013 Search PubMed.
-
WHO, Who Estimates of the Global Burden of Foodborne Diseases, 2015 Search PubMed.
- P. Prasad and A. Kochhar, Active Packaging in Food Industry: A Review, IOSR J. Environ. Sci., Toxicol. Food Technol., 2014, 8(5), 01–07 CrossRef.
- S. P. Bangar,
et al., Natural Antimicrobials as Additives for Edible Food Packaging Applications: A Review, Foods, 2021, 10(10), 2282 CrossRef PubMed.
- D. H. Lin,
et al., Bacterial cellulose in food industry: Current research and future prospects, Int. J. Biol. Macromol., 2020, 158, 1007–1019 CrossRef CAS PubMed.
- N. Omerovic,
et al., Antimicrobial nanoparticles and biodegradable polymer composites for active food packaging applications, Compr. Rev. Food Sci. Food Saf., 2021, 20(3), 2428–2454 CrossRef CAS PubMed.
- P. Appendini and J. H. Hotchkiss, Review of Antimicrobial Food Packaging, Innovative Food Sci. Emerging Technol., 2002, 3(2), 113–126 CrossRef CAS.
- A. M. Khaneghah, S. M. B. Hashemi and S. Limbo, Antimicrobial agents and packaging systems in antimicrobial active food packaging: An overview of approaches and interactions, Food Bioprod. Process., 2018, 111, 1–19 CrossRef.
-
J. R. Westlake, et al., Biodegradable Active Packaging with Controlled Release: Principles, Progress, and Prospects.ACS Food Science & Technology, 2022 Search PubMed.
- C. Vilela,
et al., A concise guide to active agents for active food packaging, Trends Food Sci. Technol., 2018, 80, 212–222 CrossRef CAS.
- C. E. Realini and B. Marcos, Active and intelligent packaging systems for a modern society, Meat Sci., 2014, 98(3), 404–419 CrossRef PubMed.
- L. T. Wu,
et al., Active and intelligent gellan gum-based packaging films for controlling anthocyanins release and monitoring food freshness, Carbohydr. Polym., 2021, 254, 117410 CrossRef CAS PubMed.
- R. A. Gross and B. Kalra, Biodegradable polymers for the environment, Science, 2002, 297(5582), 803–807 CrossRef CAS PubMed.
-
EUBP, Bioplastics facts and figures, E. Bioplastics, 2022 Search PubMed.
-
VTT, VTT develops transparent cellulose film to replace traditional plastic in food packaging, 2022, https://vttresearch.com Search PubMed.
- C. Lei,
et al., Large-Scale Manufacture of Recyclable Bioplastics from Renewable Cellulosic Biomass Derived from Softwood Kraft Pulp, ACS Appl. Polym. Mater., 2022, 4(2), 1334–1343 CrossRef CAS.
- H. S. El-Sayed,
et al., Development of Eco-friendly Probiotic Edible Coatings Based on Chitosan, Alginate and Carboxymethyl Cellulose for Improving the Shelf Life of UF Soft Cheese, J. Polym. Environ., 2021, 29(6), 1941–1953 CrossRef CAS.
- L. S. Dilkes-Hoffman,
et al., Environmental impact of biodegradable food packaging when considering food waste, J. Cleaner Prod., 2018, 180, 325–334 CrossRef CAS.
- I. Sebti,
et al., Water Sensitivity, Antimicrobial, and Physicochemical Analyses of Edible Films Based on HPMC and/or Chitosan, J. Agric. Food Chem., 2007, 55(3), 693–699 CrossRef CAS PubMed.
- H. Möller,
et al., Antimicrobial and Physicochemical Properties of Chitosan–HPMC-Based Films, J. Agric. Food Chem., 2004, 52(21), 6585–6591 CrossRef PubMed.
-
H. R. Customs, Introduction of Plastic Packaging Tax from April 2022, H. R. Customs, 2021 Search PubMed.
-
UKRI, Plastic packaging innovations receive £30 million boost from UKRI, 2022 Search PubMed.
- M. S. Firouz, K. Mohi-Alden and M. Omid, A critical review on intelligent and active packaging in the food industry: Research and development, Food Res. Int., 2021, 141, 110113 CrossRef PubMed.
-
TIPA®, Packaging that acts like plastic, with the same disposal as organic material, cited 2021 6th January, Available from: https://tipa-corp.com/bio_plastic_technology/ Search PubMed.
- P. Patel, Can you really have your cake and eat the wrapper, too?, ACS Cent. Sci., 2019, 5, 1907–1910, DOI:10.1021/acscentsci.9b01251.
- J. W. Han,
et al., Food Packaging: A Comprehensive Review and Future Trends, Compr. Rev. Food Sci. Food Saf., 2018, 17(4), 860–877 CrossRef PubMed.
- EFSA, Opinion of the Panel on food contact materials, enzymes, flavourings and processing aids (CEF) Guidelines on submission of a dossier for safety evaluation by the EFSA of active or intelligent substances present in active and intelligent materials and articles intended to come into contact with food, EFSA J., 2009, 7(8), 1208 Search PubMed.
- K. Ghosh and B. H. Jones, Roadmap to Biodegradable Plastics-Current State and Research Needs, ACS Sustainable Chem. Eng., 2021, 9(18), 6170–6187 CrossRef CAS.
- M. Asgher,
et al., Bio-based active food packaging materials: Sustainable alternative to conventional petrochemical-based packaging materials, Food Res. Int., 2020, 137, 109625 CrossRef CAS PubMed.
- Y. F. Tsang,
et al., Production of bioplastic through food waste valorization, Environ. Int., 2019, 127, 625–644 CrossRef CAS PubMed.
- A. Moeini,
et al., Formulation of secondary compounds as additives of biopolymer-based food packaging: A review, Trends Food Sci. Technol., 2021, 114, 342–354 CrossRef CAS.
- S. Farris,
et al., Pullulan- Based Films and Coatings for Food Packaging: Present Applications, Emerging Opportunities, and Future Challenges, J. Appl. Polym. Sci., 2014, 131(13), 40539 CrossRef.
- E. Archer, M. Torretti and S. Madbouly, Biodegradable polycaprolactone (PCL) based polymer and composites, Phys. Sci. Rev., 2021, 255–278 Search PubMed.
- M. E. Diken,
et al., Antibacterial and antioxidant phenolic compounds loaded PCL biocomposites for active food packaging application, J. Appl. Polym. Sci., 2022, e52423 CAS.
- G. Li,
et al., Effects of preparation method on properties of poly(butylene adipate-co-terephthalate) films, Food Sci. Biotechnol., 2015, 24(5), 1679–1685 CrossRef CAS.
- M. H. Rahman and P. R. Bhoi, An overview of non-biodegradable bioplastics, J. Cleaner Prod., 2021, 294, 126218 CrossRef CAS.
- N. Mlalila,
et al., Antimicrobial packaging based on starch, poly(3-hydroxybutyrate) and poly(lactic-co-glycolide) materials and application challenges, Trends Food Sci. Technol., 2018, 74, 1–11 CrossRef CAS.
- F. Morgan-Sagastume,
et al., Polyhydroxyalkanoate (PHA) production from sludge and municipal wastewater treatment, Water Sci. Technol., 2014, 69(1), 177–184 CrossRef CAS PubMed.
-
M. Niaounakis, Chapter 2 – Properties, Biopolymers: Processing and Products, William Andrew Publishing, 2015 Search PubMed.
- B. McAdam,
et al., Production of Polyhydroxybutyrate (PHB) and Factors Impacting Its Chemical and Mechanical Characteristics, Polymers, 2020, 12(12), 2908 CrossRef CAS PubMed.
- W. Q. de Oliveira,
et al., Food packaging wastes amid the COVID-19 pandemic: Trends and challenges, Trends Food Sci. Technol., 2021, 116, 1195–1199 CrossRef PubMed.
- X. Qi, Y. Ren and X. Wang, New advances in the biodegradation of poly(lactic) acid, Int. Biodeterior. Biodegrad., 2017, 117, 215–223 CrossRef CAS.
- M. Wrona,
et al., Development and characterisation of HPMC films containing PLA nanoparticles loaded with green tea extract for food packaging applications, Carbohydr. Polym., 2017, 156, 108–117 CrossRef CAS PubMed.
- S. V. G. Kumari, K. Pakshirajan and G. Pugazhenthi, Recent advances and future prospects of cellulose, starch, chitosan, polylactic acid and polyhydroxyalkanoates for sustainable food packaging applications, Int. J. Biol. Macromol., 2022, 221, 163–182 CrossRef CAS PubMed.
- Z. K. Miao, Y. F. Zhang and P. F. Lu, Novel active starch films incorporating tea polyphenols-loaded porous starch as food packaging materials, Int. J. Biol. Macromol., 2021, 192, 1123–1133 CrossRef CAS PubMed.
- J. Antonkiewicz,
et al., The effect of cellulose production waste and municipal sewage sludge on biomass and heavy metal uptake
by a plant mixture, Environ. Sci. Pollut. Res., 2018, 25(31), 31101–31112 CrossRef CAS PubMed.
- J. H. Chen,
et al., Cellulose acetate fibers prepared from different raw materials with rapid synthesis method, Carbohydr. Polym., 2016, 137, 685–692 CrossRef CAS PubMed.
- M. C. Shen,
et al., Smoked cigarette butts: Unignorable source for environmental microplastic fibers, Sci. Total Environ., 2021, 791, 148384 CrossRef CAS PubMed.
- N. Asim, M. Badiei and M. Mohammad, Recent advances in cellulose-based hydrophobic food packaging, Emergent Mater., 2021, 5, 703–718 CrossRef.
- M. H. Salim,
et al., Exploration of multifunctional properties of garlic skin derived cellulose nanocrystals and extracts incorporated chitosan biocomposite films for active packaging application, Int. J. Biol. Macromol., 2022, 210, 639–653 CrossRef PubMed.
- R. Shruthy, S. Jancy and R. Preetha, Cellulose nanoparticles synthesised from potato peel for the development of active packaging film for enhancement of shelf life of raw prawns (Penaeus monodon) during frozen storage, Int. J. Food Sci. Technol., 2021, 56(8), 3991–3999 CrossRef CAS.
- Z. J. Shi,
et al., Utilization of bacterial cellulose in food, Food Hydrocolloids, 2014, 35, 539–545 CrossRef CAS.
- P. Cazon and M. Vazquez, Bacterial cellulose as a biodegradable food packaging material: A review, Food Hydrocolloids, 2021, 113, 106530 CrossRef CAS.
- Y. X. Xu,
et al., Development and properties of bacterial cellulose, curcumin, and chitosan composite biodegradable films for active packaging materials, Carbohydr. Polym., 2021, 260, 117778 CrossRef CAS PubMed.
- M. Khamrai, S. L. Banerjee and P. P. Kundu, Modified bacterial cellulose based self-healable polyelectrolyte film for wound dressing application, Carbohydr. Polym., 2017, 174, 580–590 CrossRef CAS PubMed.
- M. A. Woehl,
et al., Bionanocomposites of thermoplastic starch reinforced with bacterial cellulose nanofibres: Effect of enzymatic treatment on mechanical properties, Carbohydr. Polym., 2010, 80(3), 866–873 CrossRef CAS.
- I. Sebti, J. Delves-Broughton and V. Coma, Physicochemical properties and bioactivity of nisin-containing cross-linked hydroxypropylmethylcellulose films, J. Agric. Food Chem., 2003, 51(22), 6468–6474 CrossRef CAS PubMed.
- H. Wu,
et al., Application of HPMC HME polymer as hot melt extrusion carrier in carbamazepine solid dispersion, Drug Dev. Ind. Pharm., 2020, 46(12), 1911–1918 CrossRef CAS PubMed.
- A. Hu,
et al., The Properties of HPMC:PEO Extended Release Hydrophilic Matrices and their Response to Ionic Environments, Pharm. Res., 2017, 34(5), 941–956 CrossRef CAS PubMed.
- S. Roy and J.-W. Rhim, Carboxymethyl cellulose-based antioxidant and antimicrobial active packaging film incorporated with curcumin and zinc oxide, Int. J. Biol. Macromol., 2020, 148, 666–676 CrossRef CAS PubMed.
- J. G. Fernandez and D. E. Ingber, Manufacturing of Large-Scale Functional Objects Using Biodegradable Chitosan Bioplastic, Macromol. Mater. Eng., 2014, 299(8), 932–938 CrossRef CAS.
- C. S. Chen, W. Y. Liau and G. J. Tsai, Antibacterial effects of N-sulfonated and N-sulfobenzoyl chitosan and application to oyster preservation, J. Food Prot., 1998, 61(9), 1124–1128 CrossRef CAS PubMed.
- M. Kurek,
et al., Effect of relative humidity on carvacrol release and permeation properties of chitosan based films and coatings, Food Chem., 2014, 144, 9–17 CrossRef CAS PubMed.
- W. L. Zhang, X. X. Li and W. B. Jiang, Development of antioxidant chitosan film with banana peels extract and its application as coating in maintaining the storage quality of apple, Int. J. Biol. Macromol., 2020, 154, 1205–1214 CrossRef CAS PubMed.
- J. L. Liu,
et al., Chitosan-based films with antioxidant of bamboo leaves and ZnO nanoparticles for application in active food packaging, Int. J. Biol. Macromol., 2021, 189, 363–369 CrossRef CAS PubMed.
- K. B. Biji,
et al., Smart packaging systems for food applications: a review, J. Food Sci. Technol., 2015, 52(10), 6125–6135 CrossRef CAS PubMed.
- M. Yanat and K. Schroën, Preparation methods and applications of chitosan nanoparticles; with an outlook toward reinforcement of biodegradable packaging, React. Funct. Polym., 2021, 161, 104849 CrossRef CAS.
- P. Kongkaoroptham, T. Piroonpan and W. Pasanphan, Chitosan nanoparticles based on their derivatives as antioxidant and antibacterial additives for active bioplastic packaging, Carbohydr. Polym., 2021, 257, 117610 CrossRef CAS PubMed.
- M. Florez,
et al., Chitosan for food packaging: Recent advances
in active and intelligent films, Food Hydrocolloids, 2022, 124, 107328 CrossRef CAS.
- S. Jeung and M. K. Mishra, Hot Melt Reactive Extrusion of Chitosan with Poly(acrylic acid), Int. J. Polym. Mater. Polym. Biomater., 2010, 60(1), 102–113 CrossRef.
- R. Priyadarshi and J.-W. Rhim, Chitosan-based biodegradable functional films for food packaging applications, Innovative Food Sci. Emerging Technol., 2020, 62, 102346 CrossRef CAS.
- D. Carina,
et al., Seaweeds polysaccharides in active food packaging: A review of recent progress, Trends Food Sci. Technol., 2021, 110, 559–572 CrossRef CAS.
- D. Kostic,
et al., Multifunctional ternary composite films based on PLA and Ag/alginate microbeads: Physical characterization and silver release kinetics, Mater. Sci. Eng., C, 2019, 98, 1159–1168 CrossRef CAS PubMed.
- T. Huq,
et al., Nanocrystalline cellulose (NCC) reinforced alginate based biodegradable nanocomposite film, Carbohydr. Polym., 2012, 90(4), 1757–1763 CrossRef CAS PubMed.
- M. S. A. Aziz and H. E. Salama, Developing multifunctional edible coatings based on alginate for active food packaging, Int. J. Biol. Macromol., 2021, 190, 837–844 CrossRef PubMed.
- J. Huang,
et al., Pectin-based active packaging: A critical review on preparation, physical properties and novel application in food preservation, Trends Food Sci. Technol., 2021, 118, 167–178 CrossRef CAS.
- E. Corradini,
et al., Recent Advances in Food-Packing, Pharmaceutical and Biomedical Applications of Zein and Zein-Based Materials, Int. J. Mol. Sci., 2014, 15(12), 22438–22470 CrossRef CAS PubMed.
- M. Mastromatteo,
et al., Controlled release of thymol from zein based film, Innovative Food Sci. Emerging Technol., 2009, 10(2), 222–227 CrossRef CAS.
- M. Ghasemi,
et al., Encapsulation of cumin essential oil in zein electrospun fibers: characterization and antibacterial effect, J. Food Meas. Char., 2022, 16(2), 1613–1624 CrossRef.
- M. E. Taverna,
et al., Bio-composite Films Based on Alginate and Rice Husk Tar Microparticles Loaded with Eugenol for Active Packaging, Waste Biomass Valorization, 2022, 13, 3061–3070 CrossRef CAS.
- A. Chaudhury and S. Das, Recent Advancement of Chitosan-Based Nanoparticles for Oral Controlled Delivery of Insulin and Other Therapeutic Agents, AAPS PharmSciTech, 2011, 12(1), 10–20 CrossRef CAS PubMed.
- M. Gulfam and B. G. Chung, Development of pH-Responsive Chitosan-Coated Mesoporous Silica Nanoparticles, Macromol. Res., 2014, 22(4), 412–417 CrossRef CAS.
- M. A. Dube and S. Salehpour, Applying the Principles of Green Chemistry to Polymer Production Technology, Macromol. React. Eng., 2014, 8(1), 7–28 CrossRef CAS.
- M. G. A. Vieira,
et al., Natural-based plasticizers and biopolymer films: A review, Eur. Polym. J., 2011, 47(3), 254–263 CrossRef CAS.
- L. Filiciotto and G. Rothenberg, Biodegradable Plastics: Standards, Policies, and Impacts, ChemSusChem, 2021, 14(1), 56–72 CrossRef CAS PubMed.
- J. P. Harrison,
et al., Biodegradability standards for carrier bags and plastic films in aquatic environments: a critical review, R. Soc. Open Sci., 2018, 5(5), 171792 CrossRef PubMed.
- C. Moretti,
et al., Cradle-to-grave life cycle assessment of single-use cups made from PLA, PP and PET, Resour., Conserv. Recycl., 2021, 169, 105508 CrossRef CAS.
- G. Bishop, D. Styles and P. N. L. Lens, Environmental performance comparison of bioplastics and petrochemical plastics: A review of life cycle assessment (LCA) methodological decisions, Resour., Conserv. Recycl., 2021, 168, 105451 CrossRef CAS.
- S. R. Hobbs,
et al., Life Cycle Assessment of Bioplastics and Food Waste Disposal Methods, Sustainability, 2021, 13(12), 6894 CrossRef CAS.
- Y. Q. Zhu, C. Romain and C. K. Williams, Sustainable polymers from renewable resources, Nature, 2016, 540(7633), 354–362 CrossRef CAS PubMed.
- V. G. L. Souza and A. L. Fernando, Nanoparticles in food packaging: Biodegradability and potential migration to food-A review, Food Packag. Shelf Life, 2016, 8, 63–70 CrossRef.
- T. Narancic,
et al., Biodegradable Plastic Blends Create New Possibilities for End-of-Life Management of Plastics but They Are Not a Panacea for Plastic Pollution, Environ. Sci. Technol., 2018, 52, 10441–10452 CrossRef CAS PubMed.
-
C. Lilley, E. Guzniczak, and I. Arhcer, A Review of Standards for Biodegradable Plastics, The Industrial Biotechnology Innovation Centre, 2019 Search PubMed.
- T. Kijchavengkul,
et al., Development of an automatic laboratory-scale respirometric system to measure polymer biodegradability, Polym. Test., 2006, 25(8), 1006–1016 CrossRef CAS.
- G. Ambrosio,
et al., Study of the Degradation of Biobased Plastic after Stress Tests in Water, Coatings, 2021, 11(11), 1330 CrossRef CAS.
- M. S. Kent,
et al., Study of Enzymatic Digestion of Cellulose by Small Angle Neutron Scattering, Biomacromolecules, 2010, 11(2), 357–368 CrossRef CAS PubMed.
- J. Payne and M. D. Jones, The Chemical Recycling of Polyesters for a Circular Plastics Economy: Challenges and Emerging Opportunities, Chemsuschem, 2021, 14(19), 4041–4070 CrossRef CAS PubMed.
- M. Mandic,
et al., Biodegradation of poly(E-caprolactone) (PCL) and medium chain length polyhydroxyalkanoate (mcl-PHA) using whole cells and cell free protein preparations of Pseudomonas and Streptomyces strains growth on waste cooking oil, Polym. Degrad. Stab., 2019, 162, 160–168 CrossRef CAS.
- T. Kean and M. Thanou, Biodegradation, biodistribution and toxicity of chitosan, Adv. Drug Delivery Rev., 2010, 62(1), 3–11 CrossRef CAS PubMed.
- I. E. Napper and R. C. Thompson, Environmental Deterioration of Biodegradable, Oxo-biodegradable, Compostable, and Conventional Plastic Carrier Bags in the Sea, Soil, and Open-Air Over a 3-Year Period, Environ. Sci. Technol., 2019, 53(9), 4775–4783 CrossRef CAS PubMed.
- R. C. da Costa,
et al., Poly(hydroxybutyrate-co-hydroxyvalerate)-based nanocomposites for antimicrobial active food packaging containing oregano essential oil, Food Packag. Shelf Life, 2020, 26, 100602 CrossRef.
- A. Lopez-Cordoba,
et al., Cassava starch films containing rosemary nanoparticles produced by solvent displacement method, Food Hydrocolloids, 2017, 71, 26–34 CrossRef CAS.
- E. Jakubowska,
et al., Development and characterization of active packaging films based on chitosan, plasticizer, and quercetin for repassed oil storage, Food Chem., 2023, 399, 133934 CrossRef CAS PubMed.
- L. Vermeiren,
et al., Developments in the active packaging of foods, Trends Food Sci. Technol., 1999, 10(3), 77–86 CrossRef CAS.
- P. Inthamat,
et al., Improving moisture barrier and functional properties of active film from genipin-crosslinked chitosan/astaxanthin film by heat curing, Int. J. Food Sci. Technol., 2021, 57, 137–144 CrossRef.
- W. X. Dong,
et al., Characterization and antioxidant properties of chitosan film incorporated with modified silica nanoparticles as an active food packaging, Food Chem., 2022, 373, 131414 CrossRef CAS PubMed.
- A. L. Brody,
et al., Innovative food packaging solutions, J. Food Sci., 2008, 73(8), R107–R116 CrossRef CAS PubMed.
- Y. Zhang, Q. Liu and C. Rempel, Processing and characteristics of canola protein-based biodegradable packaging: A review, Crit. Rev. Food Sci. Nutr., 2018, 58(3), 475–485 CAS.
- A. M. Harris and E. C. Lee, Improving mechanical performance of injection molded PLA by controlling crystallinity, J. Appl. Polym. Sci., 2008, 107(4), 2246–2255 CrossRef CAS.
- A. Lacoste,
et al., Advancing controlled release packaging through smart blending, Packag. Technol. Sci., 2005, 18(2), 77–87 CrossRef CAS.
- M. A. Priolo,
et al., Recent Advances in Gas Barrier Thin Films via Layer-by-Layer Assembly of Polymers and Platelets, Macromol. Rapid Commun., 2015, 36(10), 866–879 CrossRef CAS PubMed.
- V. Bertolino,
et al., Polysaccharides/Halloysite nanotubes for smart bionanocomposite materials, Carbohydr. Polym., 2020, 245, 116502 CrossRef CAS PubMed.
- A. M. Youssef,
et al., Preparation and characterization of novel bionanocomposites based on garlic extract for preserving fresh Nile tilapia fish fillets, RSC Adv., 2021, 11(37), 22571–22584 RSC.
-
L. Higueras, et al., Measurement of Antioxidant Concentration in Active Food Packaging – Impact on Activity in the Stored Food, in Handbook of Antioxidant Methodology: Approaches to Activity Determination, ed. P. D. Prenzler, D. Ryan, and K. Robards, Royal Society of Chemistry, 2021, pp. 279–302 Search PubMed.
- J. A. Tapia-Hernández,
et al., Micro- and Nanoparticles by Electrospray: Advances and Applications in Foods, J. Agric. Food Chem., 2015, 63(19), 4699–4707 CrossRef PubMed.
- D. C. Ma,
et al., Development of a HPMC-based controlled release formulation with hot melt extrusion (HME), Drug Dev. Ind. Pharm., 2013, 39(7), 1070–1083 CrossRef CAS PubMed.
- P. Cazon and M. Vazquez, Mechanical and barrier properties of chitosan combined with other components as food packaging film, Environ. Chem. Lett., 2020, 18(2), 257–267 CrossRef CAS.
- T. Senturk Parreidt, K. Muller and M. Schmid, Alginate-Based Edible Films and Coatings for Food Packaging Applications, Foods, 2018, 7(10), 170 CrossRef PubMed.
- N. Maftoonazad and H. Ramaswamy, Novel techniques in food processing: bionanocomposites, Curr. Opin. Food Sci., 2018, 23, 49–56 CrossRef.
- A. Altan, Z. Aytac and T. Uyar, Carvacrol loaded electrospun fibrous films from zein and poly(lactic acid) for active food packaging, Food Hydrocolloids, 2018, 81, 48–59 CrossRef CAS.
- M. Pakravan, M.-C. Heuzey and A. Ajji, A fundamental study of chitosan/PEO electrospinning, Polymer, 2011, 52(21), 4813–4824 CrossRef CAS.
- M. A. Del Nobile,
et al., Active packaging by extrusion processing of recyclable and biodegradable polymers, J. Food Eng., 2009, 93(1), 1–6 CrossRef CAS.
- F. Velazquez-Contreras,
et al., Effect of PLA Active Packaging Containing Monoterpene-Cyclodextrin Complexes on Berries Preservation, Polymers, 2021, 13(9), 1399 CrossRef CAS PubMed.
- H. Moustafa, N. A. Darwish and A. M. Youssef, Rational formulations of sustainable polyurethane/chitin/rosin composites reinforced with ZnO-doped-SiO2 nanoparticles for green packaging applications, Food Chem., 2022, 371, 131193 CrossRef CAS PubMed.
- L. S. Liu,
et al., Preparation of Antimicrobial Membranes: Coextrusion of Poly(lactic acid) and Nisaplin in the Presence of Plasticizers, J. Agric. Food Chem., 2009, 57(18), 8392–8398 CrossRef CAS PubMed.
-
R. Bruenler, et al., Fiber-based hybrid structures as scaffolds and implants for regenerative medicine, Smart Textiles and Their Applications, 2016, vol. 178, pp. 241–256 Search PubMed.
- S. Temesgen,
et al., Review on Spinning of Biopolymer Fibers from Starch, Polymers, 2021, 13(7), 1121 CrossRef CAS PubMed.
- M. Ratajska,
et al., Studies on the biodegradation of chitosan in an aqueous medium, Fibres Text. East. Eur., 2003, 11(3), 75–79 CAS.
- B. Deepa,
et al., Biodegradable Nanocomposite Films Based on Sodium Alginate and Cellulose Nanofibrils, Materials, 2016, 9(1), 50 CrossRef PubMed.
- G. Kale,
et al., Biodegradability of polylactide bottles in real and simulated composting conditions, Polym. Test., 2007, 26(8), 1049–1061 CrossRef CAS.
- C. S. Wu, Preparation, Characterization, and Biodegradability of Renewable Resource-Based Composites from Recycled Polylactide Bioplastic and Sisal Fibers, J. Appl. Polym. Sci., 2012, 123(1), 347–355 CrossRef CAS.
- H. K. Ahn,
et al., Biodegradability of injection molded bioplastic pots containing polylactic acid and poultry feather fiber, Bioresour. Technol., 2011, 102(7), 4930–4933 CrossRef CAS PubMed.
- Y. X. Weng, X. L. Wang and Y. Z. Wang, Biodegradation behavior of PHAs with different chemical structures under controlled composting conditions, Polym. Test., 2011, 30(4), 372–380 CrossRef CAS.
- R. Jain and A. Tiwari, Biosynthesis of planet friendly bioplastics using renewable carbon source, J. Environ. Health Sci. Eng., 2015, 13, 11 CrossRef PubMed.
- E. F. Gomez and F. C. Michel, Biodegradability of conventional and bio-based plastics and natural fiber composites during composting, anaerobic digestion and long-term soil incubation, Polym. Degrad. Stab., 2013, 98(12), 2583–2591 CrossRef CAS.
- J. Puls, S. A. Wilson and D. Holter, Degradation of Cellulose Acetate-Based Materials: A Review, J. Polym. Environ., 2011, 19(1), 152–165 CrossRef CAS.
- T. Kijchavengkul,
et al., Biodegradation and hydrolysis rate of aliphatic aromatic polyester, Polym. Degrad. Stab., 2010, 95(12), 2641–2647 CrossRef CAS.
- S. M. Emadian, T. T. Onay and B. Demirel, Biodegradation of bioplastics in natural environments, Waste Manage., 2017, 59, 526–536 CrossRef CAS PubMed.
- A. Anstey,
et al., Processability and Biodegradability Evaluation of Composites from Poly(butylene succinate) (PBS) Bioplastic and Biofuel Co-products from Ontario, J. Polym. Environ., 2014, 22(2), 209–218 CrossRef CAS.
- M. Salari,
et al., Development and evaluation of chitosan based active nanocomposite films containing bacterial cellulose nanocrystals and silver nanoparticles, Food Hydrocolloids, 2018, 84, 414–423 CrossRef CAS.
- M. A. Diab, A. Z. El-Sonbati and D. M. D. Bader, Thermal
stability and degradation of chitosan modified by benzophenone, Spectrochim. Acta, Part A, 2011, 79(5), 1057–1062 CrossRef CAS PubMed.
- H. Rong,
et al., Combustion Characteristics and Slagging during Co-Combustion of Rice Husk and Sewage Sludge Blends, Energies, 2017, 10(4), 438 CrossRef.
- E. Menya,
et al., Production and performance of activated carbon from rice husks for removal of natural organic matter from water: A review, Chem. Eng. Res. Des., 2018, 129, 271–296 CrossRef CAS.
- M. Choudhary,
et al., Thermal kinetics and morphological investigation of alkaline treated rice husk biomass, J. Indian Chem. Soc., 2022, 99(5), 100444 CrossRef CAS.
- Z. Chen, Y. Xu and S. Shivkumar, Microstructure and tensile properties of various varieties of rice husk, J. Sci. Food Agric., 2018, 98(3), 1061–1070 CrossRef CAS PubMed.
- J.-W. Rhim, Physical and mechanical properties of water resistant sodium alginate films, LWT–Food Sci. Technol., 2004, 37(3), 323–330 CrossRef CAS.
- E. D. Freitas,
et al., Thermal characterization and stability investigation of sericin and alginate blend loaded with diclofenac sodium or ibuprofen, Eur. Polym. J., 2021, 142, 110125 CrossRef CAS.
-
Sigma-Aldrich, Sodium alginate, 4th October 2022, Available from: https://www.sigmaaldrich.com/GB/en/product/aldrich/w201502 Search PubMed.
- H. McPhillips,
et al., Characterisation of the glass transition of HPMC using modulated temperature differential scanning calorimetry, Int. J. Pharm., 1999, 180(1), 83–90 CrossRef CAS PubMed.
- N. Dairi,
et al., Cellulose acetate/AgNPs-organoclay and/or thymol nano-biocomposite films with combined antimicrobial/antioxidant properties for active food packaging use, Int. J. Biol. Macromol., 2019, 121, 508–523 CrossRef CAS PubMed.
- A. L. Da Róz,
et al., Thermoplastic starch modified during melt processing with organic acids: The effect of molar mass on thermal and mechanical properties, Ind. Crops Prod., 2011, 33(1), 152–157 CrossRef.
- S. C. Clarizio and R. A. Tatara, Tensile Strength, Elongation, Hardness, and Tensile and Flexural Moduli of Injection-Molded TPS Filled with Glycerol-Plasticized DDGS, J. Polym. Environ., 2013, 21(3), 623–630 CrossRef CAS.
-
Sigma-Aldrich, Zein, 4th October 2022, Available from: https://www.sigmaaldrich.com/GB/en/product/sigma/z3625 Search PubMed.
- G. W. Selling, The effect of extrusion processing on Zein, Polym. Degrad. Stab., 2010, 95(12), 2241–2249 CrossRef CAS.
- Y. Wang and G. W. Padua, Tensile Properties of Extruded Zein Sheets and Extrusion Blown Films, Macromol. Mater. Eng., 2003, 288(11), 886–893 CrossRef CAS.
- J. Bouman,
et al., The Development of Direct Extrusion-Injection Moulded Zein Matrices as Novel Oral Controlled Drug Delivery Systems, Pharm. Res., 2015, 32(8), 2775–2786 CAS.
- C. Sun,
et al., Preparation and characterization of pectin-based edible coating agent encapsulating carvacrol/HPβCD inclusion complex for inhibiting fungi, Food Hydrocolloids, 2022, 125, 107374 CrossRef CAS.
- A. Sood and C. S. Saini, Red pomelo peel pectin based edible composite films: Effect of pectin incorporation on mechanical, structural, morphological and thermal properties of composite films, Food Hydrocolloids, 2022, 123, 107135 CrossRef CAS.
-
PULVIT, Pectin market analysis, 4th October 2022, Available from: https://pulvit.com/pectin-market/ Search PubMed.
- V. S. G. Silverajah,
et al., Mechanical, Thermal and Morphological Properties of Poly(lactic acid)/Epoxidized Palm Olein Blend, Molecules, 2012, 17, 11729–11747 CrossRef CAS PubMed.
-
D. Plackett and I. Siró, 18 – Polyhydroxyalkanoates (PHAs) for food packaging, in Multifunctional and Nanoreinforced Polymers for Food Packaging, ed. J.-M. Lagarón, Woodhead Publishing, 2011, pp. 498–526 Search PubMed.
- L.-J. Vandi,
et al., Wood-PHA Composites: Mapping Opportunities, Polymers, 2018, 10(7), 751 CrossRef PubMed.
- Y.-C. Wei,
et al., Active gellan gum/purple sweet potato composite films capable of monitoring pH variations, Food Hydrocolloids, 2017, 69, 491–502 CrossRef CAS.
- S. G. G. Aziz and H. Almasi, Physical Characteristics, Release Properties, and Antioxidant and Antimicrobial Activities of Whey Protein Isolate Films Incorporated with Thyme (Thymus vulgaris L.) Extract-Loaded Nanoliposomes, Food Bioprocess Technol., 2018, 11(8), 1552–1565 CrossRef CAS.
- J. L. Wu,
et al., The preparation, characterization, antimicrobial stability and in vitro release evaluation of fish gelatin films incorporated with cinnamon essential oil nanoliposomes, Food Hydrocolloids, 2015, 43, 427–435 CrossRef CAS.
- N. Benbettaieb,
et al., Impact of functional properties and release kinetics on antioxidant activity of biopolymer active films and coatings, Food Chem., 2018, 242, 369–377 CrossRef CAS PubMed.
- L. Wang,
et al., The antimicrobial activity of silver nanoparticles biocomposite films depends on the silver ions release behaviour, Food Chem., 2021, 359, 129859 CrossRef CAS PubMed.
- H. Y. Cui,
et al., Biodegradable zein active film containing chitosan nanoparticle encapsulated with pomegranate peel extract for food packaging, Food Packag. Shelf Life, 2020, 24, 100511 CrossRef.
- J. L. Wu,
et al., Preparation, properties and antioxidant activity of an active film from silver carp (Hypophthalmichthys molitrix) skin gelatin incorporated with green tea extract, Food Hydrocolloids, 2013, 32(1), 42–51 CrossRef CAS.
- Y. A. Arfat,
et al., Polylactide/graphene oxide nanosheets/clove essential oil composite films for potential food packaging applications, Int. J. Biol. Macromol., 2018, 107, 194–203 CrossRef CAS PubMed.
- S. Estevez-Areco,
et al., Active bilayer films based on cassava starch incorporating ZnO nanorods and PVA electrospun mats containing rosemary extract, Food Hydrocolloids, 2020, 108, 106054 CrossRef CAS.
- H. I. Ryu,
et al., Uniform-thickness electrospun nanofiber mat production system based on real-time thickness measurement, Sci. Rep., 2020, 10(1), 20847 CrossRef CAS PubMed.
- P. Vass,
et al., Scale-up of electrospinning technology: Applications in the pharmaceutical industry, Wiley Interdiscip. Rev.: Nanomed. Nanobiotechnol., 2020, 12(4), e1611 Search PubMed.
- A. C. Lopes,
et al., Eco-friendly materials produced by blown-film extrusion as potential active food packaging, Polym. Adv. Technol., 2021, 32(2), 779–788 CrossRef CAS.
- R. Yoksan,
et al., Poly(lactic acid)/thermoplastic cassava starch blends filled with duckweed biomass, Int. J. Biol. Macromol., 2022, 203, 369–378 CrossRef CAS PubMed.
- J. O. de Moraes,
et al., Scale-up of the production of cassava starch based films using tape-casting, J. Food Eng., 2013, 119(4), 800–808 CrossRef.
- S. Beigzadeh Ghelejlu, M. Esmaiili and H. Almasi, Characterization of chitosan–nanoclay bionanocomposite active films containing milk thistle extract, Int. J. Biol. Macromol., 2016, 86, 613–621 CrossRef CAS PubMed.
- R. Hufenus,
et al., Melt-Spun Fibers for Textile Applications, Materials, 2020, 13(19), 4298 CrossRef CAS PubMed.
- S. K. Bhullar, B. Kaya and M. B. G. Jun, Development of Bioactive Packaging Structure Using Melt Electrospinning, J. Polym. Environ., 2015, 23(3), 416–423 CrossRef CAS.
|
This journal is © The Royal Society of Chemistry 2023 |
Click here to see how this site uses Cookies. View our privacy policy here.