DOI:
10.1039/D2SC04324F
(Edge Article)
Chem. Sci., 2022,
13, 12876-12882
Spatial disposition of square-planar mononuclear nodes in metal–organic frameworks for C2H2/CO2 separation†
Received
3rd August 2022
, Accepted 16th October 2022
First published on 17th October 2022
Abstract
The efficient separation of acetylene (C2H2) from its mixture with carbon dioxide (CO2) remains a challenging industrial process due to their close molecular sizes/shapes and similar physical properties. Herein, we report a microporous metal–organic framework (JNU-4) with square-planar mononuclear copper(II) centers as nodes and tetrahedral organic linkers as spacers, allowing for two accessible binding sites per metal center for C2H2 molecules. Consequently, JNU-4 exhibits excellent C2H2 adsorption capacity, particularly at 298 K and 0.5 bar (200 cm3 g−1). Detailed computational studies confirm that C2H2 molecules are indeed predominantly located in close proximity to the square-planar copper centers on both sides. Breakthrough experiments demonstrate that JNU-4 is capable of efficiently separating C2H2 from a 50
:
50 C2H2/CO2 mixture over a broad range of flow rates, affording by far the largest C2H2 capture capacity (160 cm3 g−1) and fuel-grade C2H2 production (105 cm3 g−1, ≥98% purity) upon desorption. Simply by maximizing accessible open metal sites on mononuclear metal centers, this work presents a promising strategy to improve the C2H2 adsorption capacity and address the challenging C2H2/CO2 separation.
1. Introduction
Acetylene (C2H2) is one of the most essential feedstocks in petrochemical industries with a global market of 5.6 billion US$ in 2018 and projected to reach 11.42 billion US$ in 2023.1 It is manufactured by hydrocarbon cracking or partial nature gas combustion, in which carbon dioxide (CO2) is an inevitable byproduct.2 Thus, the removal of CO2 is a must-do step before further production of value-added chemicals. Yet, the C2H2/CO2 separation is a challenging task owing to their very close molecular sizes/shapes (C2H2, 3.34 Å × 3.32 Å × 5.70 Å; CO2, 3.33 Å × 3.18 Å × 5.36 Å, Fig. S1†) and similar physical properties (boiling points: C2H2, 189.3 K; CO2, 194.7 K).3 The industrial purification of C2H2 from CO2 is carried out by cryogenic distillation and liquid absorption,4–7 both of which are highly energy-intensive and often associated with potential safety hazards.
Adsorptive separation enables efficient gas purification and is deemed an energy-saving alternative technology. Porous materials that can selectively adsorb one type of molecule over others have recently aroused great interest and are deemed promising to replace traditional industrial practices. For instance, metal–organic frameworks (MOFs), a.k.a. porous coordination polymers (PCPs), are porous crystalline solids constructed from the self-assembly of organic linkers and metal ions/clusters.8–20 Although recently emerged, MOFs stand out in gas separation studies and the reticular chemistry enables exquisite control over pore size and surface chemistry to realize preferential binding or even molecular sieving effects.21–28 With regard to C2H2/CO2 separation, however, the trade-off between adsorption capacity and selectivity still poses a daunting challenge for materials scientists.
Surface engineering with electronegative elements (e.g., N, O, and F) usually facilitates the binding of C2H2 over CO2 due to their difference in the quadrupole moments (−13.4 × 10−40 and +20.5 × 10−40 C m2 for CO2 and C2H2, respectively) and electrostatic potentials (Fig. S1†).29–48 For example, a highly fluorinated MOF material SIFSIX-Cu-TPA exhibits a very large C2H2 adsorption of 185 cm3 g−1 at 298 K and 1 bar with a moderate C2H2/CO2 selectivity of 5.4.31 This approach, however, may not necessarily favor C2H2 adsorption as the overall mismatch of electrostatic potentials between the framework surface and C2H2 molecule could disrupt and even reverse the selectivity.49
On the other hand, a more reliable approach is surface engineering with open metal sites (OMSs) to preferentially bind C2H2 molecules via π-complexation.50–56 Most of the reported clusters in MOFs offer one accessible OMS per metal, such as mononuclear square-pyramidal,57 dinuclear paddle-wheel,58 and trinuclear μ3-oxo clusters.59 It is interesting to point out that a simple square-planar mononuclear center may be able to provide as many as two binding sites for C2H2 molecules. The material UTSA-74a is constructed with both square-planar and tetrahedral mononuclear zinc centers. Although the square-planar zinc center can provide two accessible binding sites, the tetrahedral one has no accessible binding sites due to the rigid coordination geometry.51 The material NKMOF-1-Ni is a rare MOF example constructed with square-planar mononuclear centers.60 As strong as it may seem in the binding of C2H2 over CO2 (C2H2/CO2 selectivity = 249.3), its C2H2 adsorption capacity (85.7 cm3 g−1) is relatively low, likely due to the short Ni⋯Ni distance (5.75 Å) allowing only one C2H2 molecule in between. Intuitively, by employing organic linkers of right size and geometry as spacers, it is plausible to realize the maximum utilization of binding sites of square-planar metal centers, and therefore, achieve not only high C2H2/CO2 selectivity but also large C2H2 adsorption capacity (Scheme 1).
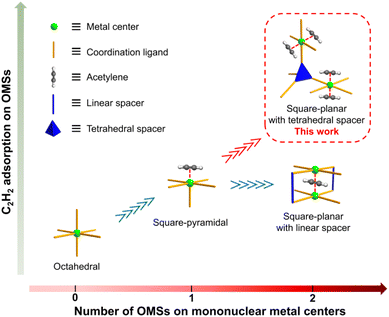 |
| Scheme 1 A simple concept to enhance C2H2 adsorption via spatial disposition of square-planar mononuclear metal centers with tetrahedral spacers. | |
Herein we report a microporous MOF (termed JNU-4, JNU = Jinan University) featuring a 4,4-connected pts topology with square-planar mononuclear copper(II) centers spaced by tetrahedral organic linkers. Structural analysis shows that every copper center has both OMSs orientated toward the channels, and thus, spatially accessible for C2H2 molecules. As a result, the activated JNU-4 (JNU-4a) exhibits excellent C2H2 adsorption capacity, particularly at 298 K and 0.5 bar (200 cm3 g−1). Computational studies confirm that C2H2 molecules indeed preferentially occupy both OMSs of the square-planar copper centers, and the simulated adsorption data are consistent with the experimental results. Breakthrough measurements demonstrate that JNU-4a is capable of efficiently separating C2H2 from C2H2/CO2 mixtures over a broad range of flow rates, realizing by far the largest C2H2 capture capacity and fuel-grade C2H2 production even under humid conditions.
2. Results and discussion
2.1. Structure and porosity analysis
JNU-4 was synthesized according to a modified procedure previously reported by Krautscheid.61 The solvothermal reaction of 5-(3-methyl-5-(pyridin-4-yl)-4H-1,2,4-triazol-4-yl)-1,3-benzenedicarboxylic acid (H2MPTBDC) and Cu(NO3)2·3H2O in a mixture of acetonitrile, water, and nitric acid yielded dark blue crystals of JNU-4. Single crystal X-ray diffraction (SCXRD) data reveal that the as-synthesized JNU-4 crystallized in the monoclinic P21/c space group. There are two crystallographically independent Cu(II) atoms in the asymmetric unit, both of which are in four-coordination with the oxygen/nitrogen atoms of MPTBDC linkers, affording Cu(COO)2(N-pyridine)2 and Cu(COO)2(N-triazole)2 of similar square planar geometry. One Cu atom coordinates with two O atoms from carboxylate groups and two N atoms from pyridine groups, while the other coordinates with two O atoms from carboxylate groups and two N atoms from triazole groups. The tetrahedral MPTBDC linkers and the square planar copper centers are further linked to generating a three-dimensional (3D) MOF with a 4,4-connected pts topology network. The copper centers are sufficiently spaced by the organic linkers and the two binding sites are potentially accessible for C2H2 molecules (Fig. 1 and S2†). The phase purity of the bulk JNU-4 was verified by comparison of the simulated and experimental powder X-ray diffraction (PXRD) patterns (Fig. S3†). The N2 adsorption/desorption measurements of JNU-4a (see the ESI† for the detailed activation method) at 77 K display a reversible type I adsorption isotherm with a saturated adsorption of 400 cm3 g−1, characteristic of a microporous material (Fig. 2a). The pore size distribution (PSD) calculated using Non-Localized Density Functional Theory (NL-DFT) methods shows two main peaks centered at 4.8 and 9.3 Å (Fig. 2a inset), which are arguably in the right range for realizing both high C2H2 adsorption and C2H2/CO2 selectivity.62 The Brunauer–Emmett–Teller surface area of JNU-4a was calculated to be 1533 m2 g−1 and the pore volume to be 0.62 cm3 g−1 at P/P0 = 0.9 (Fig. S4†), which matches well with the crystal structure (0.60 cm3 g−1), indicating that the sample can be fully desolvated while maintaining the structural integrity. The high surface area, suitable pore size, and square planar mononuclear centers of JNU-4a encouraged us to further investigate its C2H2 adsorption and C2H2/CO2 separation. The OMS density of JNU-4a is about 4.8 mmol cm−3 (Table S5†), which is mediocre compared to other MOFs, likely due to its high specific surface area (1533 m2 g−1) and large pore volume (0.62 cm3 g−1).
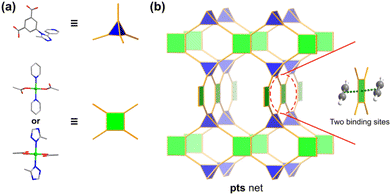 |
| Fig. 1 (a) MPTBDC organic linker as a tetrahedral building unit, Cu(COO)2(N-pyridine)2 and Cu(COO)2(N-triazole)2 complexes as square-planar 4-connected building units, respectively. (b) Simplified pts topology of JNU-4, highlighting that every copper center has both OMSs orientated toward the channels accessible for C2H2 interaction. Color code: green, Cu; red, O; blue, N; gray, C. C2H2 molecules are shown in a ball-and-stick model depicted in gray. | |
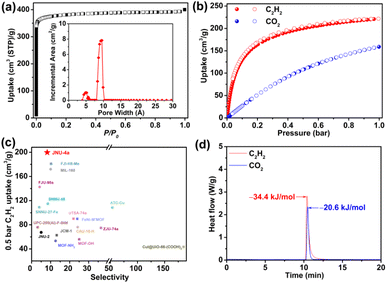 |
| Fig. 2 (a) N2 adsorption/desorption isotherms of JNU-4a at 77 K. Filled/empty squares represent adsorption/desorption. (Inset) Calculated pore-size distribution using the Non-Localized Density Functional Theory (NL-DFT) method. (b) C2H2 and CO2 single-component adsorption/desorption isotherms of JNU-4a at 298 K up to 1 bar. (c) Comparison of C2H2 gravimetric uptake in JNU-4a and some representative MOF materials at room temperature (0.5 bar and 1 bar). (d) Differential scanning calorimetry of JNU-4a upon introducing C2H2 or CO2 at a flow rate of 20 mL min−1 under ambient conditions (298 K and 1 bar). | |
2.2. Gas adsorption
Hence, we collected single-component C2H2 and CO2 adsorption isotherms at different temperatures. As expected, JNU-4a manifests a steep adsorption curve with an adsorption capacity of 222 cm3 g−1 at 298 K and 1 bar (Fig. 2b and S5†), which is superior to most of the top-performing materials, such as SIFSIX-Cu-TPA (185 cm3 g−1),31 FJU-90a (180 cm3 g−1),32 SIFSIX-3-Ni (73.9 cm3 g−1),33 ZJU-74a (85.7 cm3 g−1),50 UTSA-74a (108 cm3 g−1),51 UPC-200(Al)-F-BIM (144.5 cm3 g−1),34 FeNi-M′MOF (96 cm3 g−1),52 SNNU-27-Fe (182.4 cm3 g−1),62 JCM-1 (75 cm3 g−1),35 and JNU-1 (64 cm3 g−1),63 and slightly lower than that for FJI-H8-Me (229 cm3 g−1).64 For an equimolar C2H2/CO2 separation, the C2H2 uptake value at a partial pressure of 0.5 bar is considered an essential indicator of its separation potential. JNU-4a exhibits a gravimetric C2H2 adsorption capacity of 200 cm3 g−1. To the best of our knowledge, this value is higher than those of reported top-performance porous materials for C2H2/CO2 separation (Fig. 2c), including MIL-160 (172 cm3 g−1),65 Co-MOF-74 (174 cm3 g−1),55 SIFSIX-Cu-TPA (168.8 cm3 g−1),31 and FJI-H8-Me (180 cm3 g−1).64 By contrast, the CO2 adsorption capacity of JNU-4a at 0.5 bar is 109 cm3 g−1, which is almost half of that for C2H2 under similar conditions. We further employed ideal adsorption solution theory (IAST)66 to simulate the adsorption behavior for a 50
:
50 C2H2/CO2 gas mixture. As shown in Fig. S6–S8,† JNU-4a shows a moderate IAST selectivity of C2H2 over CO2, reaching up to 8.2 at 298 K and 1 bar, which is higher than that of many benchmark materials studied for C2H2/CO2 separation, such as FJU-90a (4.3),32 MUF-17 (6.0),36 SIFSIX-21-Ni (7.8),38 UPC-200(Al)-F-BIM (3.15),34 and SNNU-27-Fe (3.6).62
2.3. Adsorption enthalpy
To quantitatively depict the large adsorption difference between C2H2 and CO2 on JNU-4a, their isosteric heat of adsorption (Qst) values were calculated from the fitting of single-component gas adsorption isotherms collected at different temperatures. As shown in Fig. S9–S11,† the Qst for C2H2 at zero coverage was calculated to be 26.8 kJ mol−1, significantly higher than that for CO2 (19.7 kJ mol−1). To further experimentally quantify the Qst for C2H2 and CO2 on JNU-4a, we performed differential scanning calorimetry measurements of heat flow upon introducing C2H2 or CO2 at a flow rate of 20 mL min−1, respectively, at 298 K and 1 bar (Fig. 2d). The obtained experimental Qst for C2H2 and CO2 is 34.4 kJ mol−1 and 20.6 kJ mol−1, respectively, indicative of a significantly stronger binding affinity for C2H2 than CO2. It is worth mentioning that the Qst for C2H2 on JNU-4a is lower than those on UTSA-300 (57.6 kJ mol−1),67 SIFSIX-3-Ni (36.7 kJ mol−1),33 and most of the benchmark MOFs with high-density OMSs, such as ATC-Cu (79.1 kJ mol−1),56 NKMOF-1-Ni (60.3 kJ mol−1),60 ZJU-74a (45 kJ mol−1),50 and CuI@UiO-66-(COOH)2 (74.5 kJ mol−1)54 (Fig. S12†). Such a low Qst value implies that JNU-4a could be regenerated under mild conditions, which would be highly beneficial for energy-efficient C2H2/CO2 separation. To prove the easy regeneration and recyclability of JNU-4a, we carried out twenty continuous gas adsorption/desorption measurements for C2H2 and CO2 without applying heat at the degassing stage. As expected, no obvious loss of C2H2 and CO2 adsorption capacity was observed (Fig. S13 and S14†).
2.4. Computational studies
To corroborate the adsorption capacity and the preferred C2H2 binding sites in JNU-4a, grand canonical Monte Carlo (GCMC) simulations were first carried out at 298 K.68,69 The experimental and simulated isotherms are in reasonably good agreement, particularly for C2H2 at low pressures and for CO2 over the entire pressure range (Fig. 3a). The density distribution and radial distribution functions of C2H2 and CO2 at 298 K and 1 bar further reveal that C2H2 molecules are indeed predominantly located on both sides of Cu(COO)2(N-triazole)2 (site I) and Cu(COO)2(N-pyridine)2 (site II), whereas CO2 molecules were observed only at site I (Fig. 3b, c and S15†). To describe the detailed interactions of gas molecules at both sites, dispersion-corrected density functional theory (DFT-D) calculations were then carried out. As shown in Fig. 3d–f, two C2H2 molecules at site I interact with Cu2+ through π-complexation with distances of 3.02 and 3.05 Å, respectively, which are comparable to the sum of the van der Waals radii of carbon (1.70 Å) and copper (1.40 Å) atoms. Additionally, one of the H atoms of C2H2 molecules is bound by uncoordinated carboxylate O atoms through C–H⋯O interaction with a distance of 1.95 Å (Fig. 3d). At site II, two C2H2 molecules interact with Cu2+ with distances of 3.31 and 3.96 Å, respectively, and both C2H2 molecules have an H atom bound by uncoordinated carboxylate O atoms through C–H⋯O interaction with distances of 1.72 and 1.95 Å (Fig. 3e). By contrast, both CO2 molecules at site I interact side-on with Cu2+ through Cu⋯O
C
O interaction with distances of 3.80 and 3.81 Å, respectively, and the same interacting O atoms are also bound by H atoms of methyl groups through C
O⋯H interaction with distances of 2.70 and 3.14 Å, respectively (Fig. 3f). The static binding energies (ΔE) for C2H2 were calculated to be 41.7 and 33.2 kJ mol−1 at site I and site II, respectively, which is much higher than that for CO2 at site I (29.87 kJ mol−1). The overall large difference between C2H2 and CO2 in their static binding energies on JNU-4a is in good agreement with their respective experimental Qst values. Thus, not only was the square planar copper center successfully integrated into the framework but also the two OMSs of copper clusters were proved accessible for C2H2 binding due to the right-sized organic linker as a spacing unit. The unprecedented maximum utilization of OMSs of the square planar metal center in JNU-4a enables both strong binding of C2H2 molecules and large C2H2 adsorption capacity, which prompted us to further investigate its C2H2/CO2 separation performance.
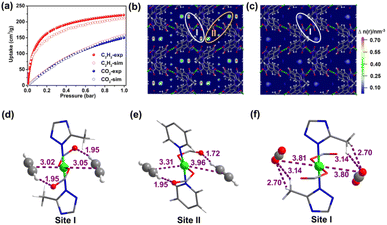 |
| Fig. 3 (a) Experimental and simulated adsorption isotherms of C2H2 (red) and CO2 (blue) at 298 K and up to 1 bar. (b) GCMC simulated adsorption density distributions of C2H2 in JNU-4a at 298 K and 1 bar. (c) GCMC simulated adsorption density distributions of CO2 in JNU-4a at 298 K and 1 bar. (d) DFT-D-calculated binding configurations of C2H2 at site I. (e) DFT-D-calculated binding configurations of C2H2 at site II. (f) DFT-D-calculated binding configurations of CO2 at site I (green, Cu; dark gray, C; blue, N; red, O; white, H. C2H2 and CO2 are represented in ball-and-stick models in (d)–(f), and the distance unit is Å). | |
2.5. Breakthrough experiments
Column breakthrough experiments were first performed on JNU-4a for a 50
:
50 C2H2/CO2 mixture at a flow rate of 4 mL min−1 at 298 K. As shown in Fig. 4a, a clean separation of C2H2/CO2 was observed with a large separation window; CO2 quickly broke through the column after 42 min g−1, whereas the retention time of C2H2 on the column was 79 min g−1, almost doubled that of CO2. Moreover, the breakthrough curve for CO2 exhibited a typical but very strong rolling-up at 42 min g−1, with a C/C0 value rising to 2.0, indicating that a great deal of the adsorbed CO2 was displaced by C2H2 until breakthrough equilibrium, which can be rationalized by their large binding energy difference. Based on the breakthrough curves, the amount of C2H2 and CO2 captured on the breakthrough column was estimated to be 160 cm3 g−1 and 12.5 cm3 g−1, respectively. Notably, such a captured amount of C2H2 is by far the highest among all reported porous materials (Fig. 4b and S17†), including MIL-160 (152 cm3 g−1 or 142 cm3 g−1 in a different report),65,70 FeNi-M′MOF (66.7 cm3 g−1),52 CuI@UiO-66-(COOH)2 (64.7 cm3 g−1),54 and ZJU-74 (81.5 cm3 g−1).50 With the captured amount of C2H2 and CO2, the separation factor was estimated to be 12.8, which is consistent with the IAST selectivity, and higher than that of most of the top-performing porous materials, such as CuI@UiO-66-(COOH)2 (3.4),54 FeNi-M′MOF (1.7),52 FJU-90a (2.1),32 NKMOF-1-Ni (2.6),60 and SNNU-45 (2.9)37 (Fig. S17 and S18†).
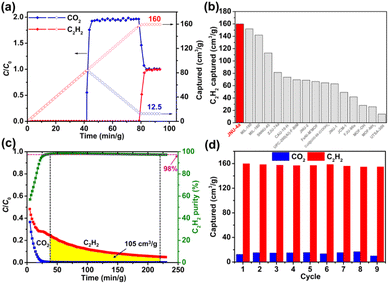 |
| Fig. 4 (a) Breakthrough curves (left y-axis) of C2H2 and CO2 on JNU-4a for an equimolar mixture of C2H2/CO2 (4.0 mL min−1) at 298 K. Empty squares depict the estimated amount of C2H2 and CO2 captured on the breakthrough column (right y-axis). (b) Comparison of the estimated amount of C2H2 captured on the breakthrough column for an equimolar mixture of C2H2/CO2 (JNU-4a and other top-performing materials). (c) Desorption curves of C2H2 and CO2 after breakthrough equilibrium with helium gas (10.0 mL min−1) sweeping at 298 K. Solid green squares represent the ratios of C2H2/CO2 in the desorbed gas mixture. The yellow area highlights C2H2 with over 98% purity (105 cm3 g−1) collectible during the desorption. (d) Continuous breakthrough experiments on JNU-4a for an equimolar mixture of C2H2/CO2 at 298 K and the estimated amount of C2H2 and CO2 captured on the breakthrough column of nine cycles. In situ regeneration was carried out with helium gas (10.0 mL min−1) sweeping at 298 K. | |
Although many MOF materials have been studied for C2H2/CO2 separation, only a few of them reported C2H2 purity and productivity. The high separation factor of JNU-4a prompted us to conduct desorption experiments. Indeed, fuel-grade C2H2 (98% purity) can be achieved upon desorption and the productivity was estimated to be 105 cm3 g−1 (Fig. 4c and S19†), which is sustainably higher than those of reported porous materials.33,44,49,71,72 To further evaluate the recyclability of JNU-4a, continuous breakthrough experiments were carried with helium sweeping at room temperature as the regeneration method (Fig. 4d and S20–S22†). Benefitting from its low Qst, JNU-4a maintained the high C2H2 capture capacity after nine cycles, highlighting the easy regeneration and good recyclability of JNU-4a for C2H2/CO2 separation. A high diffusion rate is crucial for industrial applications, which will drastically reduce the operation time.73 Volumetric adsorption kinetics was first studied on a BEL MAX II sorption analyzer; both C2H2 and CO2 exhibit a relatively high diffusion rate with diffusion constants (D/r2) calculated to be 3.00 × 10−3 and 2.59 × 10−3, respectively (Fig. S29a and b†). The data were consistent with the time-dependent gravimetric adsorption performed on a thermogravimetric analyzer; both C2H2 and CO2 can reach adsorption saturation in a short time period (Fig. S29c†). To investigate the influence of the flow rate on the separation performance, column breakthrough experiments were carried out for a 50
:
50 C2H2/CO2 mixture at different flow rates (up to 10.0 mL min−1) (Fig. S23–S25†). The breakthrough times of C2H2 and CO2 were reduced with the increase of flow rates, while the amount of the captured C2H2 was estimated to be 158.0 cm3 g−1, 162.4 cm3 g−1, and 168.3 cm3 g−1 at flow rates of 6.0 mL min−1, 8.0 mL min−1, and 10.0 mL min−1, respectively. The results suggest that the higher flow rate may increase the amount of C2H2 captured on the breakthrough column owing to the buildup of pressures.
In industrial C2H2/CO2 separation, the feed gases may contain water vapor, which will likely affect the separation performance of MOF materials with OMSs. Continuous single-component adsorption/desorption experiments were carried out on JNU-4a with moisturized C2H2 (10% relative humidity, RH). As shown in Fig. S26 and S27,† no obvious loss of adsorption capacity was observed after ten cycles of adsorption/desorption. Furthermore, we conducted eight cycles of continuous breakthrough experiments for an equimolar C2H2/CO2 mixture with a flow rate of 6.0 mL min−1 under humid conditions (10% RH) (Fig. 5a), and also no obvious loss of capture capacity was observed. The amount of C2H2 captured on the breakthrough column was estimated to be 145 cm3 g−1 (Fig. 5b). Based on desorption curves, about 85 cm3 of fuel-grade C2H2 can be retrieved for 1 g of JNU-4a (Fig. 5c). Although lower than the productivity under dry conditions, it is still much higher than those of reported porous materials, including SIFSIX-3-Ni (56 cm3 g−1, 99.9%),33 SIFSIX-dps-Cu (55.6 cm3 g−1, 99.9%),71 ZNU-1 (53.8 cm3 g−1, 99.5%),44 JXNU-11(Fe2Ni) (44.3 cm3 g−1, 95%),72 and Cd-NP (27.8 cm3 g−1, 99.99%)49 (Fig. 5d). Many MOFs with OMSs have been reported to be poisoned by water vapor, and it is worth pointing out that JNU-4a may be capable of efficiently separating C2H2/CO2 even under humid conditions.
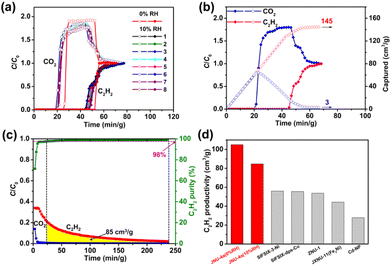 |
| Fig. 5 (a) Continuous breakthrough curves of C2H2 and CO2 on JNU-4a for an equimolar C2H2/CO2 mixture (6.0 mL min−1) under dry (0% RH) and humid conditions (10% RH). In situ regeneration was carried out with helium gas (10.0 mL min−1) sweeping at 298 K. (b) One set of breakthrough curves (left y-axis) of C2H2 and CO2 on JNU-4a for an equimolar C2H2/CO2 mixture (6.0 mL min−1) under humid conditions (10% RH). Empty squares depict the estimated amount of C2H2 and CO2 captured on the breakthrough column (right y-axis). (c) Desorption curves of C2H2 and CO2 after breakthrough equilibrium with helium gas (10.0 mL min−1) sweeping at 298 K. Solid green squares represent the ratios of C2H2/CO2 in the desorbed gas mixture. The yellow area represents C2H2 with over 98% purity (85 cm3 g−1) collectible during the desorption. (d) Comparison of the C2H2 productivity estimated from desorption curves for an equimolar C2H2/CO2 mixture. | |
3. Conclusion
We have implemented a simple concept of two accessible OMSs per metal in MOFs by employing square-planar mononuclear centers as nodes and tetrahedral organic linkers as spacers. The 4,4-connected pts topology network (JNU-4) exhibits excellent C2H2 adsorption capacity, particularly at 298 K and 0.5 bar (200 cm3 g−1). Computational modeling studies reveal that C2H2 molecules indeed preferentially occupy both OMSs of the square-planar centers. Breakthrough experiments demonstrate by far the largest C2H2 capture capacity (160 cm3 g−1) from a 50
:
50 C2H2/CO2 mixture and fuel-grade C2H2 production (105 cm3 g−1, ≥98%) upon desorption. This work illustrates a straightforward design strategy to maximize the accessible OMSs in MOFs for C2H2 adsorption. Further optimization of the spacing linkers with the assistance of computational simulations would be key to advancing in this direction to address the challenging C2H2/CO2 separation.
Data availability
The data that support the plots within this paper and other finding of this study are available from the corresponding authors upon reasonable request.
Author contributions
W. L. and D. L. conceived and designed the research. H. Z., W. L., and D. L. co-wrote the manuscript. H. Z. and X.-J. X. planned and executed the synthesis, characterization, and gas separation studies. Y. W. performed the theoretical simulations. D. L. and R.-J. W. carried out the structural analyses. All authors participated in and contributed to the preparation of the manuscript.
Conflicts of interest
There are no conflicts to declare.
Acknowledgements
This work was financially supported by the National Natural Science Foundation of China (No. 21731002, 21975104, 21901085, 22271120, 22201101, and 22150004), Guangdong Major Project of Basic and Applied Research (No. 2019B030302009), Guangdong Basic and Applied Basic Research Foundation (No. 2020A1515011005), Innovation Team Project in Guangdong Colleges and Universities (No. 2021KCXTD009), National Postdoctoral Program for Innovative Talent (No. BX20220132 and 2022M711327), and Outstanding Innovative Talents Cultivation Funded Programs for Doctoral Students of Jinan University (No. 2021CXB003).
Notes and references
-
Acetylene Gas Market Review 2021 and Strategic Plan for 2022 - Insights, Trends, Competition, Growth Opportunities, Market Size, Market Share Data and Analysis Outlook to 2028, 2022, https://www.researchandmarkets.com/reports/5460706/acetylene-gas-market-review-2021-and-strategic#tag-pos-1 Search PubMed.
- A. Granada, S. B. Karra and S. M. Senkan, Ind. Eng. Chem. Res., 1987, 26, 1901–1905 CrossRef CAS.
- C. R. Reid and K. M. Thomas, J. Phys. Chem. B, 2001, 105, 10619–10629 CrossRef CAS.
- S. Chu, Y. Cui and N. Liu, Nat. Mater., 2017, 16, 16–22 CrossRef PubMed.
- S. Sircar, Ind. Eng. Chem. Res., 2002, 41, 1389–1392 CrossRef CAS.
- Q. Qian, P. A. Asinger, M. J. Lee, G. Han, K. MizrahiRodriguez, S. Lin, F. M. Benedetti, A. X. Wu, W. S. Chi and Z. P. Smith, Chem. Rev., 2020, 120, 8161–8266 CrossRef CAS PubMed.
- D. S. Sholl and R. P. Lively, Nature, 2016, 532, 435–437 CrossRef PubMed.
- H. C. Zhou, J. R. Long and O. M. Yaghi, Chem. Rev., 2012, 112, 673–674 CrossRef CAS PubMed.
- H. Lyu, O. I.-F. Chen, N. Hanikel, M. I. Hossain, R. W. Flaig, X. Pei, A. Amin, M. D. Doherty, R. K. Impastato, T. G. Glover, D. R. Moore and O. M. Yaghi, J. Am. Chem. Soc., 2022, 144, 2387–2396 CrossRef CAS PubMed.
- H. Li, L. Li, R.-B. Lin, W. Zhou, Z. Zhang, S. Xiang and B. Chen, EnergyChem, 2019, 1, 100006 CrossRef.
- N. Hanikel, M. S. Prévot and O. M. Yaghi, Nat. Nanotechnol., 2020, 15, 348–355 CrossRef CAS PubMed.
- X. Zhao, Y. Wang, D. S. Li, X. Bu and P. Feng, Adv. Mater., 2018, 30, 1705189 CrossRef.
- M. Ding, R. W. Flaig, H. L. Jiang and O. M. Yaghi, Chem. Soc. Rev., 2019, 48, 2783–2828 RSC.
-
O. M. Yaghi, M. J. Kalmutzki and C. S. Diercks, Introduction to reticular chemistry: Metal-organic frameworks and covalent organic frameworks, Wiley-VCH, Weinheim, 2019 Search PubMed.
- K. Adil, Y. Belmabkhout, R. S. Pillai, A. Cadiau, P. M. Bhatt, A. H. Assen, G. Maurin and M. Eddaoudi, Chem. Soc. Rev., 2017, 46, 3402–3430 RSC.
- H. Wang, X. Pei, M. J. Kalmutzki, J. Yang and O. M. Yaghi, Acc. Chem. Res., 2022, 55, 707–721 CrossRef CAS PubMed.
- Z. Ji, T. Li and O. M. Yaghi, Science, 2020, 369, 674–680 CrossRef CAS PubMed.
- H. Wang, Y. Liu and J. Li, Adv. Mater., 2020, 32, 2002603 CrossRef CAS PubMed.
- Y. Wang, Q. Liu, Q. Zhang, B. Peng and H. Deng, Angew. Chem., Int. Ed., 2021, 130, 7238–7243 CrossRef.
- W. Yan, S. Li, T. Yang, Y. Xia, X. Zhang, C. Wang, Z. Yan, F. Deng, Q. Zhou and H. Deng, J. Am. Chem. Soc., 2020, 142, 16182–16187 CrossRef CAS PubMed.
- B. Chen, S. Xiang and G. Qian, Acc. Chem. Res., 2010, 43, 1115–1124 CrossRef CAS PubMed.
- J.-R. Li, R. J. Kuppler and H.-C. Zhou, Chem. Soc. Rev., 2009, 38, 1477–1504 RSC.
- H. Zeng, M. Xie, T. Wang, R.-J. Wei, X.-J. Xie, Y. Zhao, W. Lu and D. Li, Nature, 2021, 595, 542–548 CrossRef CAS PubMed.
- R. B. Lin, Z. Zhang and B. Chen, Acc. Chem. Res., 2021, 54, 3362–3376 CrossRef CAS PubMed.
- Z.-Q. Zhang, S.-B. Peh, Y.-X. Wang, C.-J. Kang, W.-D. Fan and D. Zhao, Angew. Chem., Int. Ed., 2020, 59, 18927–18932 CrossRef CAS PubMed.
- R. Matsuda, R. Kitaura, S. Kitagawa, Y. Kubota, R. V. Belosludov, T. C. Kobayashi, H. Sakamoto, T. Chiba, M. Takata, Y. Kawazoe and Y. Mita, Nature, 2005, 436, 238–241 CrossRef CAS PubMed.
- K. J. Chen, D. G. Madden, S. Mukherjee, T. Pham, K. A. Forrest, A. Kumar, B. Space, J. Kong, Q. Y. Zhang and M. J. Zaworotko, Science, 2019, 366, 241–246 CrossRef CAS PubMed.
- C. Gu, N. Hosono, J. J. Zheng, Y. Sato, S. Kusaka, S. Sakaki and S. Kitagawa, Science, 2019, 363, 387–391 CrossRef CAS PubMed.
- C. Graham, J. Pierrus and R. E. Raab, Mol. Phys. Sci., 1989, 67, 939–955 CrossRef CAS.
- A. Halkier and S. Coriani, Chem. Phys. Lett. Sci., 1999, 303, 408–412 CrossRef CAS.
- H. Li, C. Liu, C. Chen, Z. Di, D. Yuan, J. Pang, W. Wei, M. Wu and M. Hong, Angew. Chem., Int. Ed., 2021, 60, 7547–7552 CrossRef CAS PubMed.
- Y. Ye, Z. Ma, R.-B. Lin, R. Krishna, W. Zhou, Q. Lin, Z. Zhang, S. Xiang and B. Chen, J. Am. Chem. Soc., 2019, 141, 4130–4136 CrossRef CAS PubMed.
- K. J. Chen, H. S. Scott, D. G. Madden, T. Pham, A. Kumar, A. Bajpai, M. Lusi, K. A. Forrest, B. Space, J. J. Perry and M. J. Zaworotko, Chem, 2016, 1, 753–765 CAS.
- W. Fan, S. Yuan, W. Wang, L. Feng, X. Liu, X. Zhang, X. Wang, Z. Kang, F. Dai, D. Yuan, D. Sun and H.-C. Zhou, J. Am. Chem. Soc., 2020, 142, 8728–8737 CrossRef PubMed.
- J. Lee, C.-Y. Chuah, J. Kim, Y. Kim, N. Ko, Y. Seo, K. Kim, T.-H. Bae and E. Lee, Angew. Chem., Int. Ed., 2018, 57, 7869–7873 CrossRef CAS.
- O.-T. Qazvini, R. Babarao and S.-G. Telfer, Chem. Mater., 2019, 31, 4919–4926 CrossRef CAS.
- Y. P. Li, Y. Wang, Y. Y. Xue, H. P. Li, Q. G. Zhai, S. N. Li, Y. C. Jiang, M. C. Hu and X. Bu, Angew. Chem., Int. Ed., 2019, 58, 13590–13595 CrossRef CAS PubMed.
- N. Kumar, S. Mukherjee, N. C. Harvey-Reid, A. A. Bezrukov, K. Tan, V. Martins, M. Vandichel, T. Pham, L. M. van Wyk, K. Oyekan, A. Kumar, K. A. Forrest, K. M. Patil, L. J. Barbour, B. Space, Y. Huang, P. E. Kruger and M. J. Zaworotko, Chem, 2021, 7, 3085–3098 CAS.
- S. Dutta, S. Mukherjee, O. Qazvini, A. Gupta, S. Sharma, D. Mahato, R. Babarao and S. Ghosh, Angew. Chem., Int. Ed., 2022, 61, e202114132 CAS.
- Y. Wang, X. Jia, H. Yang, Y. Wang, X. Chen, A. N. Hong, J. Li, X. Bu and P. Feng, Angew. Chem., Int. Ed., 2020, 59, 19027–19030 CrossRef CAS.
- J. Pang, F. Jiang, M. Wu, C. Liu, K. Su, W. Lu, D. Yuan and M. Hong, Nat. Commun., 2015, 6, 7575 CrossRef.
- M. L. Foo, R. Matsuda, Y. Hijikata, R. Krishna, H. Sato, S. Horike, A. Hori, J. Duan, Y. Sato, Y. Kubota, M. Takata and S. Kitagawa, J. Am. Chem. Soc., 2016, 138, 3022–3030 CrossRef CAS.
- L. Yang, L. Yan, Y. Wang, Z. Liu, J. He, Q. Fu, D. Liu, X. Gu, P. Dai, L. Li and X. Zhao, Angew. Chem., Int. Ed., 2021, 60, 4570–4574 CrossRef CAS PubMed.
- L. Wang, W. Sun, Y. Zhang, N. Xu, R. Krishna, J. Hu, Y. Jiang, Y. He and H. Xing, Angew. Chem., Int. Ed., 2021, 60, 22865–22870 CrossRef CAS PubMed.
- Y. Zhang, J. Hu, R. Krishna, L. Wang, L. Yang, X. Cui, S. Duttwyler and H. Xing, Angew. Chem., Int. Ed., 2020, 59, 17664–17669 CrossRef CAS PubMed.
- W. Gong, H. Cui, Y. Xie, Y. Li, X. Tang, Y. Liu, Y. Cui and B. Chen, J. Am. Chem. Soc., 2021, 143, 14869–14876 CrossRef CAS PubMed.
- J. Pei, H. M. Wen, X. W. Gu, Q. L. Qian, Y. Yang, Y. Cui, B. Li, B. Chen and G. Qian, Angew. Chem., Int. Ed., 2021, 133, 2–9 CrossRef.
- F. Moreau, I. da Silva, N. H. Al Smail, T. L. Easun, M. Savage, H. G. Godfrey, S. F. Parker, P. Manuel, S. Yang and M. Schroder, Nat. Commun., 2017, 8, 14085 CrossRef CAS PubMed.
- Y. Xie, H. Cui, H. Wu, R.-B. Lin, W. Zhou and B. Chen, Angew. Chem., Int. Ed., 2021, 60, 9604–9609 CrossRef CAS PubMed.
- J. Pei, K. Shao, J. X. Wang, H. M. Wen, Y. Yang, Y. Cui, R. Krishna, B. Li and G. Qian, Adv. Mater., 2020, 32, 1908275 CrossRef CAS PubMed.
- F. Luo, C. Yan, L. Dang, R. Krishna, W. Zhou, H. Wu, X. Dong, Y. Han, T.-L. Hu, M. O'Keeffe, L. Wang, M. Luo, R.-B. Lin and B. Chen, J. Am. Chem. Soc., 2016, 138, 5678–5684 CrossRef CAS PubMed.
- J. Gao, X. Qian, R.-B. Lin, R. Krishna, H. Wu, W. Zhou and B. Chen, Angew. Chem., Int. Ed., 2020, 59, 4396–4400 CrossRef CAS PubMed.
- S. Liu, X. Han, Y. Chai, G. Wu, W. Li, J. Li, I. da Silva, P. Manuel, Y. Cheng, L. L. Daemen, A. J. Ramirez-Cuesta, W. Shi, N. Guan, S. Yang and L. Li, Angew. Chem., Int. Ed., 2021, 60, 6526–6532 CrossRef CAS PubMed.
- L. Zhang, K. Jiang, L. Yang, L. Li, E. Hu, L. Yang, K. Shao, H. Xing, Y. Cui, Y. Yang, B. Li, B. Chen and G. Qian, Angew. Chem., Int. Ed., 2021, 60, 15995–16002 CrossRef CAS PubMed.
- S. Xiang, W. Zhou, Z. Zhang, M. A. Green, Y. Liu and B. Chen, Angew. Chem., Int. Ed., 2010, 49, 4615–4618 CrossRef CAS PubMed.
- Z. Niu, X. Cui, T. Pham, G. Verma, P. C. Lan, C. Shan, H. Xing, K. A. Forrest, S. Suepaul, B. Space, A. Nafady, A. M. Al-Enizi and S. Ma, Angew. Chem., Int. Ed., 2021, 60, 5283–5288 CrossRef CAS PubMed.
- E. D. Bloch, W. L. Queen, R. Krishna, J. M. Zadrozny, C. M. Brown and J. R. Long, Science, 2012, 335, 1606–1610 CrossRef CAS PubMed.
- S. S. Y. Chui, S. M. F. Lo, J. P. H. Charmant, A. G. Orpen and I. D. Williams, Science, 1999, 283, 1148–1150 CrossRef CAS PubMed.
- T. Loiseau, L. Lecroq, C. Volkringer, J. Marrot, G. Férey, M. Haouas, F. Taulelle, S. Bourrelly, P. L. Llewellyn and M. Latroche, J. Am. Chem. Soc., 2006, 128, 10223–10230 CrossRef CAS PubMed.
- Y.-L. Peng, T. Pham, P. Li, T. Wang, Y. Chen, K.-J. Chen, K. A. Forrest, B. Space, P. Cheng, M. J. Zaworotko and Z. Zhang, Angew. Chem., Int. Ed., 2018, 57, 10971–10975 CrossRef CAS PubMed.
- D. Lässig, J. Lincke, J. Moellmer, C. Reichenbach, A. Moeller, R. Gläser, G. Kalies, K. A. Cychosz, M. Thommes, R. Staudt and H. Krautscheid, Angew. Chem., Int. Ed., 2011, 50, 10344–10348 CrossRef PubMed.
- Y.-Y. Xue, X.-Y. Bai, J. Zhang, Y. Wang, S.-N. Li, Y.-C. Jiang, M.-C. Hu and Q.-G. Zhai, Angew. Chem., Int. Ed., 2021, 60, 10122–10128 CrossRef CAS PubMed.
- H. Zeng, M. Xie, Y.-L. Huang, Y. Zhao, X.-J. Xie, J.-P. Bai, M.-Y. Wan, R. Krishna, W. Lu and D. Li, Angew. Chem., Int. Ed., 2019, 58, 8515–8519 CrossRef CAS PubMed.
- Z. Di, C. Liu, J. Pang, C. Chen, F. Hu, D. Yuan, M. Wu and M. Hong, Angew. Chem., Int. Ed., 2021, 60, 10828–10832 CrossRef CAS PubMed.
- Y. Ye, S. Xian, H. Cui, K. Tan, L. Gong, B. Liang, T. Pham, H. Pandey, R. Krishna, P. C. Lan, K. A. Forrest, B. Space, T. Thonhauser, J. Li and S. Ma, J. Am. Chem. Soc., 2022, 144, 1681–1689 CrossRef CAS PubMed.
- A. L. Myers and J. M. Prausnitz, AIChE J., 1965, 11, 121–127 CrossRef CAS.
- R. B. Lin, L. Li, H. Wu, H. Arman, B. Li, R. G. Lin, W. Zhou and B. Chen, J. Am. Chem. Soc., 2017, 139, 8022–8028 CrossRef CAS.
- D. Dubbeldam, A. Torres-Knoop and K. S. Walton, Mol. Simul., 2013, 39, 1253–1292 CrossRef CAS.
- D. Dubbeldam, S. Calero, D. E. Ellis and R. Q. Snurr, Mol. Simul., 2016, 42, 81–101 CrossRef CAS.
- Y.-M. Gu, H.-F. Qi, T.-T. Sun, Xi-W. Liu, S. Qadir, T.-J. Sun, D.-F. Li, S.-S. Zhao, D. Fairen-Jimenez and S.-D. Wang, Chem. Mater., 2022, 34, 2708–2716 CrossRef CAS.
- J. Wang, Y. Zhang, Y. Su, X. Liu, P. Zhang, R.-B. Lin, S. Chen, Q. Deng, Z. Zeng, S. Deng and B. Chen, Nat. Commun., 2022, 13, 200–206 CrossRef CAS PubMed.
- X.-P. Fu, Y.-L. Wang, X.-F. Zhang, Z. Zhang, C.-T. He and Q.-Y. Liu, CCS Chem., 2022, 4, 3416–3425 CrossRef.
- D. M. Polyukhov, A. S. Poryvaev, A. S. Sukhikh, S. A. Gromilov and M. V. Fedin, ACS Appl. Mater. Interfaces, 2021, 13, 40830–40836 CrossRef PubMed.
Footnotes |
† Electronic supplementary information (ESI) available. CCDC 2160960. For ESI and crystallographic data in CIF or other electronic format see DOI: https://doi.org/10.1039/d2sc04324f |
‡ These authors contributed equally. |
|
This journal is © The Royal Society of Chemistry 2022 |
Click here to see how this site uses Cookies. View our privacy policy here.