DOI:
10.1039/D2RA05196F
(Paper)
RSC Adv., 2022,
12, 29554-29561
Highly selective electrochemical sensing based on electropolymerized ion imprinted polyaniline (IIPANI) on a bismuth modified carbon paste electrode (CPE-Bi) for monitoring Nickel(II) in river water†
Received
19th August 2022
, Accepted 19th September 2022
First published on 17th October 2022
Abstract
Electrochemical sensors based on ion-imprinting polymers have emerged as an effective analytical tool for heavy metal tracking. This study describes a simple and facile technique for manufacturing a highly selective and sensitive electrode using an ion imprinting polymer on a bismuth-modified carbon paste electrode. The developed sensor applied aniline as a functional monomer and was used for tracking Ni(II) ions. The proposed sensor was thoroughly characterized by scanning electron microscopy, cyclic voltammetry, and differential pulse striping anodic voltammetry. The analytical evaluation showed that the proposed sensor has a linear dynamic range (R2 = 0.999) for the Ni(II) concentration range of 0.01 to 1 μM and a limit of detection value of 0.00482 μM. The proposed sensor showed excellent performance when tested for tracking Ni(II) ions in the presence of interfering ions (Cd(II), Co(II), Cu(II), and Zn(II) ions) at a 1000-fold higher concentration. When the proposed sensor was tested for tracking Ni(II) concentration in an actual river sample, our modified sensor showed similar results compared to the atomic absorption spectroscopy evaluation (p > 0.05, n = 3). In summary, our proposed sensor is promising for monitoring Ni(II) ions in the aquatic environment.
Introduction
Heavy metals, such as nickel, chromium, lead, copper, and zinc, are often detected in wastewater around electronics, textiles, and metal industries. Nickel, Ni(II), is one of the dangerous heavy metals in aquatic environments. The International Agency for Research on Cancer (IARC) classified Ni(II) as a human carcinogen, as suggested by its potential to trigger lung cancer. More importantly, as reported, Ni(II) exposures at 0.07 to 1 mg m−3 resulted in visual and tubular dysfunction.1,2 Zhang et al. (2015) reported that Ni(II) exhibits toxic effects on THP-1 cell growth.3 The government of the Republic of Indonesia has released a regulation that the maximum Ni(II) level in the environment should be below 75 g L−1.6 Therefore, water monitoring for heavy metal ions, including Ni(II), is essential.4,5
It is not easy to trace heavy metals in low quantities. The current advanced analytical methods such as atomic fluorescence spectroscopy (AFS), inductive coupled plasma mass spectroscopy (ICP-MS), and atomic absorption spectroscopy (AAS)7–11 have shown satisfactory results. However, those methods are fraught with difficulties, including multi-step, time-consuming, and expensive procedures. The electrochemical method has shown its potency in detecting metal ions at low concentrations and small sample quantities. Electrochemical techniques offer portability, inexpensive, simple preparation, and rapid measurement.12,13
A mercury-based electrode is generally applied for measuring heavy metal ions using a voltammetry technique. Following environmental issues, a mercury-free electrode is preferred. As an alternative, a carbon-based electrode is generally used.14–17 It is imperative to note that a bare electrode, such as carbon, platina, or gold electrode, usually exhibits a relative low electrochemical response to an analyte. Therefore, the modulation of the electronic structure on the electrode surface is required to improve the current response.14,18–23,55 Studies have shown that a bismuth-modified carbon paste electrode exhibits excellent performance in tracking heavy metal ions at a low concentration, as suggested by a greater current response in comparison to a bare carbon paste electrode.18,20,21
A polymer containing an ion template and a functional monomer is called as an ion-imprinted polymer (IIP). IIP have exceptional recognition capabilities, which are characterized by their high affinity and selectivity for target ions. Thus, the influence of competing ions is minimized.24–31
The synthesis mechanism of IIP can be classified into four groups: (1) crosslinking of linear chain polymers carrying metal-binding groups; (2) chemical immobilization; (3) surface imprinting; and (4) trapping. Surface imprinting creates binding sites on the surface or near the imprinted polymers.24,25,27,32–35 It is, therefore, possible to improve the current response and selectively bind the target ions. In this work, we are interested in developing a surface imprinting by electropolymerization, giving ion imprinted polymer for Ni(II) ions.
Polyaniline (PANI), a polymer, is a versatile conducting polymer that has several unique advantages, including being easy to prepare and good environmental stability.36–38 It is also reported that PANI can be protonated, changing the conductivity, and improving the electrochemical response.39–41 In addition, PANI has shown excellent performance as a composite with various types of binders. PANI can be produced by oxidative polymerization as well as electropolymerization. By utilizing electropolymerization, it provides a faster and easier process.42,43 Mohammad and Atassi (2021) reported that polyaniline enhanced the removal efficiency of metal ions. PANI deposition onto a polyacrylonitrile membrane's surface provides a high adsorption capacity, as suggested by a higher direct current conductivity.45 It seems through the covalent bond and electrostatic interaction, the pair of electrons free of aniline plays an essential role in specific binding with the target molecule. Therefore, we hypothesized that the pair of free electrons of aniline might interact with Ni(II) to create Ni(II) ion-imprinted polyaniline.
To our knowledge, the application of electropolymerized PANI for Ni(II) detection has not been reported. With the aim of selective monitoring Ni(II) ions in water samples, an imprinted electro-synthesized layer has been developed on the surface of bismuth modified carbon paste electrode (see Fig. 1). The optimal electropolymerization conditions were observed by optimizing the cycles of electro-polymerization and aniline concentration. We evaluated the modified sensor by scanning electron microscopy (SEM), cyclic voltammetry (CV), and differential pulse anodic stripping voltammetry (DPASV). The analytical application of the proposed sensor for tracking Ni(II) in a river water sample is also presented.
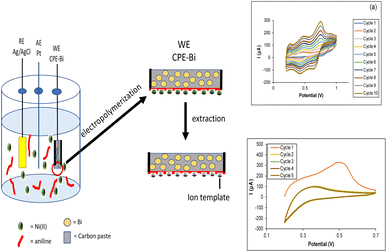 |
| Fig. 1 Schematic representation of the preparation of the Ni-IPANI/CPE-Bi electrode. | |
Results and discussion
Surface characterization of bismuth-modified carbon paste electrode (CPE-Bi)
The surface morphology of the bismuth-modified carbon paste electrode (CPE-Bi) is presented in Fig. 2. As depicted in Fig. 2a, the SEM image of the bare carbon paste showed a rough surface at 500× magnification. When the carbon paste was further modified with Bi, it clearly showed that the Bi powders were attached onto the carbon paste, as suggested by smaller particles spread on the carbon (see Fig. 2b). Next, we performed the energy dispersive X-ray spectroscopy (EDS) evaluation to confirm the presence of Bi. As shown in Fig. 2c, the EDS image of CPE-Bi shows the presence of carbon (C), oxygen (O), and bismuth (Bi) elements. Undoubtedly, the C and Bi elements came from graphite and bismuth powder. At the same time, the O element may come from water and moisture during storage before EDS evaluation. The EDS image confirms that Bi has successfully modified the CPE.
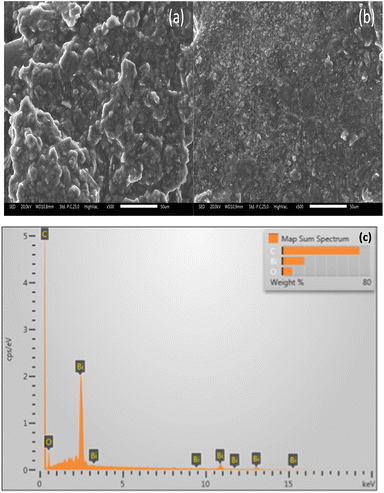 |
| Fig. 2 (a) The surface morphology of the bare carbon paste electrode (CPE) and (b) the bismuth-modified carbon paste electrode (CPE-Bi) at 500× magnification. (c) The EDS image of CPE-Bi. | |
Electropolymerization of Ni-IPANI on CPE-Bi
The CPE-Bi was further modified using aniline by electropolymerization. Ni(II) ion imprinted polyaniline modified CPE-Bi (Ni-IPANI/CPE-Bi) was prepared in a solution of 0.5 M H2SO4 using potential cycling between 0.2 and 1.0 V vs. Ag/AgCl (3 M KCl) with a scan rate of 100 mV s−1. Fig. 3a depicts a ten-cycle cyclic voltammogram (CV) recorded during the electropolymerization of the Ni-IPANI. The peak current gradually increases, indicating the proliferation of the conducting polymer matrix. The CV displays some basic information associated with PANI reduction and oxidation characteristics. The three sets of redox potentials present in the CV are associated with leucoemeraldine (LEB), emeraldine (EM) and pernigraniline (PMG).44 The continuous cycling of the peaks with increasing redox current implies that the surface of CPE-BI generated the Ni-IPANI layer. Next, we extracted the trapped Ni(II) ions from the Ni-IPANI matrices to create a Ni(II) ions template. As shown in Fig. 3b, a reduction in the oxidation peak at a working potential of 0.5 V was observed on the second cycle (yellow line), indicating a rapid extraction of Ni(II) ions from the polymer matrix. The disappearance of oxidation peaks after the fifth extraction cycle highlights Ni(II) ions removal.12
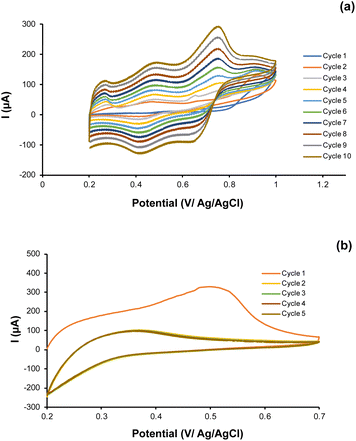 |
| Fig. 3 (a) The CV voltammogram of aniline (ANI) electropolymerization and (b) extraction process of Ni(II) from the PANI matrix. | |
The electrochemical response of Ni(II) ions on modified Ni-IPANI/CPE-Bi
The electrochemical response of Ni(II) ions in a 0.5 M H2SO4 solution was evaluated using the DPASV technique at a potential range of 0.2 to 0.8 V and a scan rate of 50 mV s−1. The DPASV voltammogram for 1 μM Ni(II) ions at the unmodified CPE, CPE-Bi, Ni-IPANI/CPE-Bi, and NIPANI/CPE-Bi are shown in Fig. 4a. We revealed that the greatest anodic peak current response was observed on the Ni-IPANI/CPE-Bi (31.2 μA) surface in comparison with bare CPE (4.33 μA), CPE-Bi (14.4 μA), and NIPANI/CPE-Bi (20.8 μA) (see Fig. 4b), suggesting an elevation in peak current through the inclusion of both Ni-IPANI and CPE-Bi. CPE-Bi has multiple benefits, including being more environmentally friendly, not requiring the removal of dissolved oxygen during stripping analysis, and has vast negative potential.20 Whereas PANI has been reported to have excellent electrical conductivity and adsorption capacity of metal ions.37 When Ni-IPANI further modified the CPE-Bi, the presence of Ni(II) ions template selectively trapped Ni(II) from the analyte, and the interaction between Ni(II) ions with Ni-IPANI/CPE-Bi improved the current response. Remarkably, resulting in the highest current response.
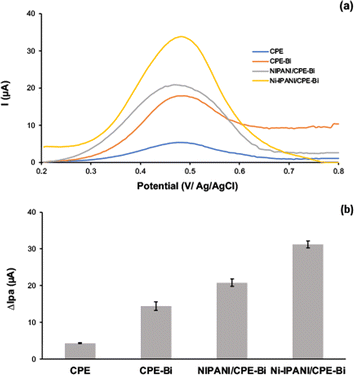 |
| Fig. 4 (a) The DPASV voltammogram and (b) histogram of 1 μM Ni(II) peak current response on bare CPE, CPE-Bi, NIPANI/CPE-Bi, and Ni-IPANI/CPE-Bi. | |
Electropolymerization optimization of Ni-IPANI
The fundamental advantage of electropolymerization is its controllability via changes in electrochemical parameters like as current, voltage, cycles, and so on. The thickness of the sensing layer is an essential thing in sensor construction since it affects the sensor's sensitivity. The imprinted sites in the electropolymerized polymer are insufficient when the imprinted layer is too thin, resulting in diminished sensitivity. In reverse, if the imprinted layer is too thick, the imprinted sites may be implanted too firmly in the polymer, making extraction of the template and attachment of the target ions to the imprinted sites more complicated.45 Therefore, optimizing the electropolymerization cycles is essential to attain the optimum thickness of the imprinted Ni-IPANI layer on CPE-Bi. For electro polymerization of Ni-IPANI on CPE-Bi, various scanning cycles were recorded. The DPASV responses of the developed Ni-IPANI/CPE-Bi modified electrode were evaluated using 1 μM Ni(II). Fig. 5a shows the peak current peak response of 1 μM Ni(II) at various CV scanning cycles and the DPASV voltammogram is presented in ESI 1.† It was revealed that the peak current response elevated with the number of scanning cycles and reached a maximum when the number of scanning cycles was 10. In reverse, a reduction in peak current response was observed when the scanning cycle was increased from 10 to 20. By this result, 10 scanning cycles were selected as the optimum number of CV scanning cycles for electropolymerization of the Ni-IPANI on CPE-Bi.
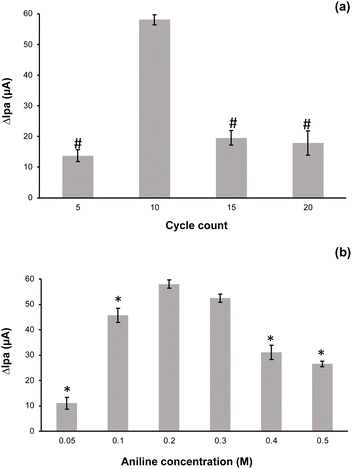 |
| Fig. 5 The histogram of 1 μM Ni(II) at (a) different scanning cycles and (b) various aniline concentration during electropolymerization. # means significantly different at p ≤ 0.05 vs. 10 cycle count (n = 3); * means significantly different at p ≤ 0.05 vs. 0.2 M aniline concentration (n = 3). | |
Next, we also optimized the aniline concentration required for electropolymerization because the variation of aniline concentration also affects the modified sensor's current response. The DPASV voltammogram of 1 μM Ni(II) on the Ni-IPANI modified CPE-Bi at various aniline concentration are shown in ESI 2.† It was revealed that the current responses tended to increase as the aniline concentration was elevated (see Fig. 5b). However, the current response starting to decrease when the aniline concentration was raised over 0.2 M. It seems that the thickness of polymer was also accountable for this phenomenon.46 The ANOVA evaluation shows that by applying aniline at 0.2 M and 0.3 M, no significant difference (p > 0.05, n = 3) was observed. Therefore, for effectiveness, aniline at 0.2 M was selected as the optimum concentration for electropolymerization of aniline on CPE-Bi.
Optimization of pH for analytical evaluation
The occurrence of an acidic or basic functional group at the imprinted sites of ion imprinted polymer leads the adsorption and acquisition of the target ions to be highly influenced by the pH of the environment. In this work, various pH values from 3 to 8 were assessed respectively to determine an optimum pH of experimental test. As presented in Fig. 6a. The DPASV voltammogram of Ni(II) standard solutions at pH ranging from 3 to 8 were recorded. It revealed that the peak current responses increased with the increment of pH from 3 to 5 and then decreased when the pH of the solution raised (see Fig. 6b). At low pH (pH < 5), the functional group of PANI can be easily protonated, thereby decreasing the interaction between Ni(II) and Ni-IPANI/CPE-Bi. When the pH is more alkaline (pH > 5), Ni(II) may react with OH− to generate precipitation, then resulting in a reduction of electrode responsiveness.47
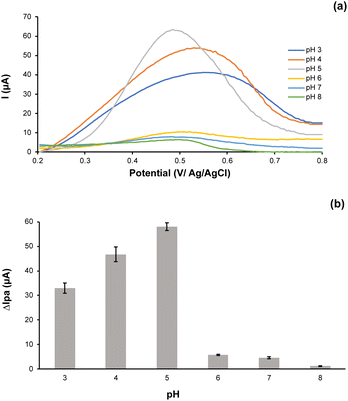 |
| Fig. 6 (a) The DPASV voltammogram and (b) histogram of Ni(II) peak current response on the Ni-IPANI/CPE-Bi at pH 3 to 8. | |
Reproducibility, repeatability, and selectivity of Ni-IPANI/CPE-Bi
In this work, the reproducibility of Ni-IPANI/CPE-Bi was evaluated using five different sensors that were produced in the same condition by DPSAV (see ESI 3†). The calculation of the percentage (%) relative standard deviation (RSD) value for Ni(II) was found to be 2.2%. This % RSD value reveals that Ni-IPANI/CPE-Bi showed excellent reproducibility.
Next, we evaluated the repeatability of the proposed sensor. A simple chemical regenerating protocol of an electrode is critical for possible mass manufacture and practical applications. It should prevent time-consuming techniques for cleaning and regenerating electrodes. In this present investigation, the electrochemical sensor based on Ni-IPANI/CPE-Bi could be regenerated by CV technique and PBS solution pH 5 for 5 cycles. The regenerated Ni-IPANI/CPE-Bi demonstrated impressive consistency for tracking Ni(II) ion as suggested by similar peak current response (see ESI 4†). The calculation of relative standard deviation for tracking 1 μM Ni(II) was 3%, indicating adequate repeatability of our modified sensor.
We further assess the selectivity of the modified sensor using various interfering ions that are Cd(II), Cu(II), Co(II) and Zn(II). The interfering ions were tested individually as a control to validate the selectivity of the modified sensor towards Ni(II) ions as well as to prevent any possibility of overlapping signals. We revealed that no peak was recorded in the potential range of 0.2 to 0.8 V when the interfering ions were tested individually. In reverse, the peak of Ni(II) ion was obviously detected (see Fig. 7a), confirming the selectivity of the as-prepared sensor. Next, we also observed the interference study under the optimized working conditions by adding the interfering ions at a ratio of 1
:
1, 1
:
10, 1
:
100, 1
:
500, and 1
:
1000 into the standard solution containing 1 μM Ni(II). The DPASV voltammogram of Ni(II) in the presence of interfering compounds at a ratio of 1
:
1 can be seen in Fig. 7a. Whereas the comparative findings of the peak current response are summarized in Fig. 7b. Notably, no considerable current changes were recorded. More importantly, the presence of interfering ions such as Cd(II), Cu(II), Co(II), and Zn(II) at a 1000-fold concentration does not interfere with the determination of 1 μM of Ni(II), as suggested by the error value of less than 5%, which makes the Ni-IPANI/CPE-Bi electrode suitable as a highly selective sensor.54 It seems that the unique templates in the polymeric matrix that fit with the Ni(II) ion accounted for this selectivity.28
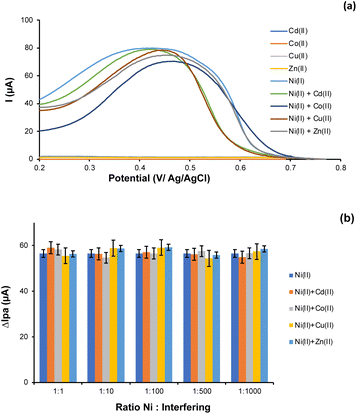 |
| Fig. 7 (a) The DPASV voltammogram of 1 μM each interfering ions, 1 μM Ni(II), and 1 μM Ni(II) in the presence of interfering ions at 1 : 1. (b) The histogram of peak current response of 1 μM Ni(II) and 1 μM Ni(II) in the presence of interfering ions at ratio of 1 : 1, 1 : 10, 1 : 100, 1 : 500, and 1 : 1000 (b). | |
Calibration plot and limit of detection
DPASV was applied to determine the Ni(II) current response at various concentration gradients at pH 5.0. Fig. 8a shows the DPASV voltammogram of Ni(II) response at various concentration. Whereas Fig. 8b shows the calibration plot of peak current response vs. Ni(II) ion concentration. As presented, the higher Ni(II) concentration, the higher current response. According to Fig. 8b, the association of Ni(II) peak current with its concentration is linear in the range of 0.01 to 1.0 μM. The linear equation is as follows: y = 48.502x + 7.5954, with correlation coefficient of 0.999.
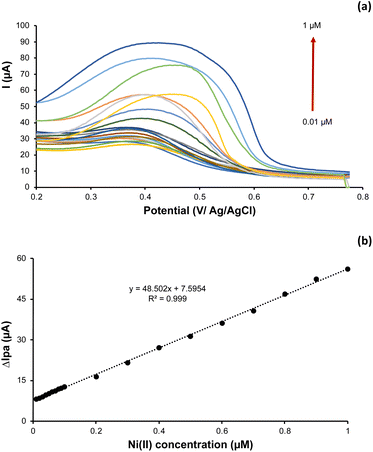 |
| Fig. 8 (a) The DPASV voltammogram and (b) plot of Ni(II) concentration (0.01 to 1 μM) vs. anodic peak current. | |
The limit of detection (LOD), Cm, of Ni(II) was then calculated using the following formula:
where
m denotes the slope of the calibration plot (48.502 μA μM
−1) and 3
ò is the standard deviation of the blank response, which is recorded from 20 replicate measurements of the blank solution. The calculated LOD is 0.00482 μM.
Table 1 compares the reports of the Ni(
II) evaluation with various modified electrode. It is demonstrated that the performance of our proposed modified sensor Bi-CPE/Ni-IPANI is similar to the proposed sensor of
eZIF-8@DMG/β-CD/RGO.
48 However, since our proposed method offers a simple, inexpensive, and facile preparation, therefore, more promising.
Table 1 Comparison of the proposed sensor with other previous sensor for tracking Ni(II)
Method |
Sensor type |
Linear dynamic range (μM) |
LOD (μM) |
Ref. |
Dimethylglyoxime modified carbon paste electrode. Dimethylglyoxime-nafion modified screen printed carbon electrode. Bismuth modified screen printed carbon electrode. Ni(II) imprinted polidopamine modified glassy carbon electrode. Zeolitic imidazolate framework-8@dimethylglyoxime/β-cyclodextrin/reduced graphene oxide. |
DPAdSV |
Mercury film electrode |
0.02–0.75 |
0.006 |
49 |
SWAdCSV |
Solid bismuth vibrating electrode |
0–0.17 |
0.01 |
50 |
DPV |
DMG/CPEa |
1.35–10 |
0.46 |
51 |
DPV |
DMG-N/SPCEb |
1–8.5 |
0.5 |
52 |
AdSV |
Bi-SPCEc |
0.17–3.85 |
0.049 |
53 |
DPASV |
Ni-PDA/GCEd |
1–25 |
0.39 |
56 |
AdSV |
DMG/SPCE |
0.13–3.4 |
0.039 |
57 |
DPAdSV |
ZIF-8@DMG/β-CD/RGOe |
0.01–1 |
0.005 |
48 |
DPASV |
Ni-IPANI/CPE-Bi |
0.01–1 |
0.00482 |
This work |
Determination of Ni(II) in actual water samples
The proposed sensor was applied to trace Ni(II) in actual water sample collected from a river near Bandung city to assess the feasibility. As a comparison, we also test the river sample using the AAS technique. Ni(II) ions were detected in the river water using the AAS and the proposed sensor. As presented in Table 2, The Ni(II) concentrations were found to be 7.4 ± 0.51 and 7.4 ± 1.06 μM when tested using the proposed sensor and AAS technique respectively. More importantly, the Texp is smaller than Ttable (0.02 vs. 4.30), suggesting that the proposed method is acceptable without any significant difference (p > 0.05, n = 3). Next, to test the accuracy of the proposed method, the recovery test was performed using a standard technique by spiking the known Ni(II) concentration at 0.5 μM to sample. The % recovery was around 97.9%, indicating that the developed Ni-IPANI/CPE-Bi sensor has excellent accuracy for practical application.
Table 2 Determination of Ni(II) in river water
Sample |
Ni(II) (μM) |
texp |
ttablea |
Recovery (%) |
Proposed method |
AAS |
Confidence level of 95% (p > 0.05, n = 3). |
River water |
7.4 ± 0.51 |
7.4 ± 1.06 |
0.021 |
4.303 |
97.9 |
Experimental
Materials
NaCl, K3[Fe(CN)6], K4[Fe(CN)6], NaOH, H3PO4 (≧85%), KH2PO4, K2HPO4, H2SO4 (≧99%), NiSO4, CdCl2, CoCl2, CuCl2, ZnCl2, aniline, paraffin oil, and graphite powder are from Merck (Darmstadt, Germany) with pro analytical grade. The bismuth powder was supplied from Sigma-Aldrich and the Whatman 42 filter paper was obtained from Cytiva. Ultrapure water was prepared by a Module E-pure D4642-33 instrument (Barnstead) with a resistivity ≥18 MΩ.
Apparatus
A computerized hand-held eDAQ potentiostat was employed for the voltametric measurement. The analytical procedure was controlled by 2.1.5 EChem software. A conventional three-electrode systems (Ag/AgCl electrode as reference electrode, platinum wire as auxiliary electrode, and carbon paste electrode (CPE) modified with the Bi and Ni-IPANI (Ni-IPANI/CPE-Bi) as the modified working electrode) were used for the electrochemical evaluation.
Preparation of bismuth-modified carbon paste electrode (CPE-Bi)
Carbon paste was prepared by mixing graphite powder with paraffin oil at a ratio of 3.5
:
1.5 (w/w). At the same time the bismuth paste was prepared by mixing bismuth powder with paraffin oil at a ratio of 4
:
1 (w/w). The bismuth-modified carbon paste electrode (CPE-Bi) was prepared by homogenizing bismuth paste and carbon paste at a ratio of 1.5
:
2 (w/w). The mixture was then homogenized for 15 min then firmly packed into a plastic tube with a copper wire for electrical contact. The surface of the modified bismuth carbon paste electrode (CPE-Bi) was smoothed by rubbing it with a piece of weighing paper.
Preparation of ion imprinted polymer (Ni-IPANI/CPE-Bi) and non imprinted polymer (NIPANI/CPE-Bi)
The schematic presentation for the fabrication of Ni-IPANI/CPE-Bi is presented in Fig. 1. The Ni-IPANI was fabricated by electropolymerization using aniline as the functional monomer and NiSO4 as the source of Ni(II) ions. The electro-polymerization of aniline was carried out using the cyclic voltammetry (CV) technique at the potential ranging from 0.2 V to 1.0 V. After completed electropolymerization, the as prepared Ni-IPANI/CPE-Bi was rinsed by 0.1 M phosphate buffer solution (PBS) pH 5 using the CV technique at the potential range from 0.2 V to 0.7 V and a scan rate of 100 mV s−1 for 5 cycles to create Ni(II) templates. The non-imprinted polymer polyaniline (NIPANI) was also synthesized to compare the performance of modified sensing. The NIPANI/CPE-Bi was prepared using the same procedure as Ni-IPANI/CPE-Bi protocol without NiSO4.
Surface characterization
For evaluation of the surface morphology of carbon paste electrode (CPE) and bismuth modified CPE, scanning electron microscopy (SEM) attached with Energy Dispersive X-ray Spectroscopy (EDS) (JEOL JSM IT300, Japan) was applied.
Actual sample analysis
According to this research, we used river water from Bandung city as the actual water sample. The river water was centrifuged for 10 min and filtered with filter paper (Whatman 42) before the evaluation. The sample pH was adjusted to pH 5 and preconcentrated by CV at −0.8 V for 100 s. The Ni(II) concentration was evaluated using the DPASV technique.
Statistical analysis
Results were expressed as mean values ± standard deviation (SD) (n = 3). Experimental data were analyzed using Microsoft excel 2016 and SPSS 26. Statistical significance was determined by One-way analysis of variance (ANOVA) followed by Tukey's test and p values ≤ 0.05 were considered statistically significant.
Conclusions
In this present investigation, an electrochemical sensing-based ion imprinted PANI on CPE-Bi was developed to trace Ni(II) in water. Two steps of the preparation were carried out to modify the carbon paste electrode, including direct mixing of the Bi powder with carbon paste and electropolymerization of imprinted PANI for specific recognition of target Ni(II). The developed Ni-IPANI/CPE-Bi exhibits excellent selectivity and sensitivity, which can be attributed to the high-affinity binding site and the plentiful templates present in the Ni-IPANI on CPE-Bi toward target Ni(II) ions. Good repeatability and reproducibility were also observed. More importantly, when the proposed sensor was applied to trace Ni(II) ions in a river water sample, excellent accuracy with good recovery was recorded. In conclusion, our findings show that the developed sensor can be used to monitor Ni(II) pollutants in rivers or aquatic environments.
Author contributions
HS and VS: design, project administration, manuscript writing and finalization, data collection, data interpretation, discussion. DRP: data collection, data interpretation, and draft manuscript writing. NM and MAZ: discussion, data analysis, and interpretation.
Conflicts of interest
There are no conflicts to declare.
Acknowledgements
This research was partially funded by PDUPT (Grant contract No. 263/IT1.B07.1/SPP-LPPM/V/2022) for fiscal year 2022 under HS and Indonesia Endowment Fund for Education (LPDP) assisted by Analytical Chemistry Research Group, Faculty of Mathematics and Natural Sciences, Institut Teknologi Bandung. Author also thanks to the BASICS advances laboratories, Research and Innovation Agency Republic of Indonesia (BRIN) for supporting the research analysis.
References
- K. H. Vardhan, P. S. Kumar and R. C. Panda, J. Mol. Liq., 2019, 290 Search PubMed.
- I. K. Herath, S. Wu, M. Ma and H. Ping, Environ. Sci. Pollut. Res., 2022, 32929, DOI:10.1007/s11356-022-18525-3.
- Y. Zhang, Z. W. Zhang, Y. M. Xie, S. S. Wang, Q. H. Qiu, Y. L. Zhou and G. H. Zeng, Mol. Med. Rep., 2015, 3273, DOI:10.3892/mmr.2015.3878.
- D. Schrenk, M. Bignami, L. Bodin, J. K. Chipman, J. del Mazo, B. Grasl-Kraupp, C. Hogstrand, L. Hoogenboom, J. C. Leblanc, C. S. Nebbia, E. Ntzani, A. Petersen, S. Sand, T. Schwerdtle, C. Vleminckx, H. Wallace, T. Guérin, P. Massanyi, H. van Loveren, K. Baert, P. Gergelova and E. Nielsen, EFSA J., 2020, e06268, DOI:10.2903/j.efsa.2020.6268.
- C. M. G. Van Den Berg and M. Nimmo, Sci. Total Environ., 1987, 60, 185–195, DOI:10.1016/0048-9697(87)90415-3.
- H. Bubala, T. A. Cahyadi and R. Ernawati, Rekayasa Teknologi Industri dan Informasi, 2019, pp. 113–122 Search PubMed.
- Q. Hu, G. Yang, Y. Zhao and J. Yin, Anal. Bioanal. Chem., 2003, 375, 831, DOI:10.1007/s00216-003-1828-y.
- H. F. Lubis and G. H. Simamora, in IOP Conference Series: Earth and Environmental Science, 2021, vol. 912 Search PubMed.
- T. Deriaty, I. Nasution and M. Yusuf, Dent. J., 2018, 51(1), 5, DOI:10.20473/j.djmkg.v51.i1.p5-9.
- A. Lari, N. Esmaeili and H. Ghafari, Anal. Methods Environ. Chem. J., 2021, 4(2), 72, DOI:10.24200/amecj.v4.i02.144.
- G. Ma, X. Duan and J. Sun, Spectrochim. Acta, Part B, 2018, 149, 57, DOI:10.1016/j.sab.2018.07.009.
- H.-L. Zhou, X.-D. Wu, D. Lin and L.-Q. Zhang, IOP Conf. Ser.: Mater. Sci. Eng., 2021, 1117, 012013, DOI:10.1088/1757-899x/1117/1/012013.
- P. Faradilla, H. Setiyanto, R. V. Manurung and V. Saraswaty, RSC Adv., 2022, 12, 743, 10.1039/d1ra06862h.
- A. E. Kartika, H. Setiyanto, R. V. Manurung, S. N. A. Jenie and V. Saraswaty, ACS Omega, 2021, 6(47), 31477, DOI:10.1021/acsomega.1c03414.
- V. Vatanpour, S. S. Madaeni, S. Zinadini and H. R. Rajabi, J. Membr. Sci., 2011, 373(1–2), 36, DOI:10.1016/j.memsci.2011.02.030.
- P. K. Q. Nguyen and S. K. Lunsford, Talanta, 2012, 101, 110, DOI:10.1016/j.talanta.2012.09.004.
- A. Mourya, B. Mazumdar and S. K. Sinha, Indian J. Chem. Technol., 2019, 26(6), 562, DOI:10.56042/ijct.v26i6.21941.
- A. M. Ashrafi, S. Cerovac, S. Mudrić, V. Guzsvány, L. Husáková, I. Urbanová and K. Vytřas, Sens. Actuators, B, 2014, 191, 320, DOI:10.1016/j.snb.2013.08.087.
- H. Devnani and S. P. Satsangee, Int. J. Environ. Sci. Technol., 2015, 12, 1269, DOI:10.1007/s13762-014-0497-z.
- J. Sochr, M. Machková, Ľ. Machyňák, F. Čacho and Ľ. Švorc, Acta Chim. Slovaca, 2016, 9, 28, DOI:10.1515/acs-2016-0006.
- I. Švancara, L. Baldrianová, E. Tesařová, S. B. Hočevar, S. A. A. Elsuccary, A. Economou, S. Sotiropoulos, B. Ogorevc and K. Vytřas, Electroanalysis, 2006, 18(2), 177, DOI:10.1002/elan.200503391.
- S. B. Hočevar, I. Švancara, K. Vytřas and B. Ogorevc, Electrochim. Acta, 2005, 51(4), 706, DOI:10.1016/j.electacta.2005.05.023.
- H. Tian, D. Wu, J. Li, J. Luo, C. Jia, Z. Liu, W. Huang, Q. Chen, C. M. Shim, P. Deng, Y. Shen and X. Tian, J. Energy Chem., 2022, 70, 230, DOI:10.1016/j.jechem.2022.02.021.
- J. F. Ping, J. Wu and Y. bin Ying, Chin. Sci. Bull., 2012, 57, 1781, DOI:10.1007/s11434-012-5115-1.
- Q. Yang, C. Yang, J. Yi, G. Fan, H. Yang and Z. Ge, ECS J. Solid State Sci. Technol., 2020, 9, 101012, DOI:10.1149/2162-8777/abb8ba.
- A. Aravind and B. Mathew, J. Macromol. Sci., Part A: Pure Appl. Chem., 2019, 256 DOI:10.1080/10601325.2019.1691451.
- A. B. Abdallah, M. R. El-Kholany, A. F. S. Molouk, T. A. Ali, A. A. El-Shafei and M. E. Khalifa, RSC Adv., 2021, 11, 30771, 10.1039/d1ra05489a.
- P. Wei, Z. Zhu, R. Song, Z. Li and C. Chen, Electrochim. Acta, 2019, 317, 93, DOI:10.1016/j.electacta.2019.05.136.
- W. Huang, Y. Liu, N. Wang, G. Song, X. Yin, L. Zhang, X. Ni and W. Xu, J. Inorg. Organomet. Polym. Mater., 2021, 31, 2043, DOI:10.1007/s10904-021-01892-8.
- J. Fu, X. Wang, J. Li and L. Chen, Prog. Chem., 2016, 28, 83, DOI:10.7536/PC150742.
- Y. Hua, S. Zhang, H. Min, J. Y. Li, X. H. Wu, D. Sheng, X. B. Cui, Y. J. Chen, C. Li, H. Z. Lian and S. Liu, At. Spectrosc., 2021, 42(4), 217, DOI:10.46770/AS.2021.027.
- J. Zhou, B. Li, A. Qi, Y. Shi, J. Qi, H. Xu and L. Chen, Sens. Actuators, B, 2020, 305, 127462, DOI:10.1016/j.snb.2019.127462.
- J. Fu, L. Chen, J. Li and Z. Zhang, J. Mater. Chem. A, 2015, 3, 13598, 10.1039/c5ta02421h.
- J. Fu, X. Wang, J. Li, Y. Ding and L. Chen, RSC Adv., 2016, 6, 44087, 10.1039/c6ra07785d.
- C. X. Li, J. M. Pan, J. Gao, Y. S. Yan and G. Q. Zhao, Chin. Chem. Lett., 2009, 20(8), 985, DOI:10.1016/j.cclet.2009.03.020.
- W. Li, J. Guo, H. Du, D. Wang, J. Cao and Z. Wang, Sep. Purif. Technol., 2022, 286, 120486, DOI:10.1016/j.seppur.2022.120486.
- A. E. Bodoki, B. C. Iacob, L. E. Gliga, S. L. Oprean, D. A. Spivak, N. A. Gariano and E. Bodoki, Molecules, 2018, 23(8), 1875, DOI:10.3390/molecules23081875.
- I. Karbownik, O. Rac-Rumijowska, M. Fiedot-Toboła, T. Rybicki and H. Teterycz, Materials, 2019, 12(4), 664, DOI:10.3390/ma12040664.
- M. Beygisangchin, S. A. Rashid, S. Shafie, A. R. Sadrolhosseini and H. N. Lim, Polymers (Basel), 2021, 13(12), 2003, DOI:10.3390/polym13122003.
- X. Wang, D. Wu, X. Song, W. Du, X. Zhao and D. Zhang, Molecules, 2019, 24 Search PubMed.
- R. Pauliukaite, C. M. A. Brett and A. P. Monkman, Electrochim. Acta, 2004, 50(1), 159, DOI:10.1016/j.electacta.2004.07.034.
- S. Feng, J. Luo, J. Li, Y. Yu, Z. Kang, W. Huang, Q. Chen, P. Deng, Y. Shen and X. Tian, Mater. Today Phys., 2022, 23, 1000646, DOI:10.1016/j.mtphys.2022.100646.
- P. Walde, K. Kashima and G. Ćirić-Marjanović, Front. Bioeng. Biotechnol., 2019, 7(165) DOI:10.3389/fbioe.2019.00165.
- J. Scotto, M. I. Florit and D. Posadas, J. Electroanal. Chem., 2016, 774, 42, DOI:10.1016/j.jelechem.2016.04.052.
- N. Mohammad and Y. Atassi, Water Sci. Eng., 2021, 14(2), 129, DOI:10.1016/j.wse.2021.06.004.
- A. Korent, K. Žagar Soderžnik, S. Šturm and K. Žužek Rožman, J. Electrochem. Soc., 2020, 167, 106504, DOI:10.1149/1945-7111/ab9929.
- G. Ziyatdinova, E. Guss and E. Yakupova, Sensors, 2021, 21 Search PubMed.
- E. Muñoz, M. A. Heras, Á. Colina, V. Ruiz and J. López-Palacios, Electrochim. Acta, 2007, 52(14), 4778, DOI:10.1016/j.electacta.2007.01.016.
- T. Lindfors and A. Ivaska, J. Electroanal. Chem., 2002, 531(1), 43, DOI:10.1016/S0022-0728(02)01005-7.
- X. Cui, B. Yang, S. Zhao, X. Li, M. Qiao, R. Mao, Y. Wang and X. Zhao, Sens. Actuators, B, 2020, 315, 128091, DOI:10.1016/j.snb.2020.128091.
- O. A. Farghaly, Microchem. J., 2003, 75(2), 119, DOI:10.1016/S0026-265X(03)00090-0.
- G. M. S. Alves, J. M. C. S. Magalhães and H. M. V. M. Soares, Electroanalysis, 2013, 25(5), 1247, DOI:10.1002/elan.201200643.
- A. Ferancová, M. K. Hattuniemi, A. M. Sesay, J. P. Räty and V. T. Virtanen, Mine Water Environ., 2016, 35, 547, DOI:10.1007/s10230-015-0357-1.
- A. Ferancová, M. K. Hattuniemi, A. M. Sesay, J. P. Räty and V. T. Virtanen, J. Hazard. Mater., 2016, 306, 50, DOI:10.1016/j.jhazmat.2015.11.057.
- C. Barceló, N. Serrano, C. Ariño, J. M. Díaz-Cruz and M. Esteban, Electroanalysis, 2015, 28(3), 640, DOI:10.1002/elan.201500511.
- H. Razmi and M. Dehghanzade, Electroanalysis, 2019, 32(1), 198, DOI:10.1002/elan.201900097.
- M. Rosal, X. Cetó, N. Serrano, C. Ariño, M. Esteban and J. M. Díaz-Cruz, J. Electroanal. Chem., 2019, 839, 83, DOI:10.1016/j.jelechem.2019.03.025.
|
This journal is © The Royal Society of Chemistry 2022 |
Click here to see how this site uses Cookies. View our privacy policy here.