DOI:
10.1039/D2RA02922G
(Paper)
RSC Adv., 2022,
12, 29562-29568
Influencing the froth flotation of LiAlO2 and melilite solid solution with ionic liquids†
Received
9th May 2022
, Accepted 8th October 2022
First published on 17th October 2022
Abstract
In the present work experiments for single mineral flotation against LiAlO2 and melilite s.s. were carried out for seven ionic liquids (ILs). From these, IL-1 with an imidazolium cation and a bromide anion and IL-7 with a pyridinium cation and a bromide anion were selected for further flotation experiments (dosage, pH). Flotation experiments were also conducted using naphthenic acid, a conventional flotation fatty acid-based collector, and FS-2, a commercial collector in order to compare the results with ILs. Moreover, the effects of different anions in the ILs on the flotation were evaluated and a significant influence on the hardness of anions was found on the flotation process. Finally, a pre-functionalization was also explored with modified cholesterol derivatives, comparing the effect of cholesterylsulfate and cholesterylphosphate on the flotation of LiAlO2 and melilite s.s. This study is vital for the further optimization of lithium recovery from the pyrometallurgical recycling path of lithium-ion batteries and the flotation of primary minerals such as aluminosilicates.
1. Introduction
Ionic liquids (ILs) are salts with a melting point below 100 °C and are usually composed of organic cations and inorganic or organic anions.1–4 Common cations in ILs include imidazolium, pyrrolidinium, ammonium, and so forth. The unique physical and chemical properties of ILs,5,6 such as wide solubility range, low melting point, and thermal stability, have led to their increased utilization in separation, electrochemistry, and catalysts.3,5,7–10 In addition, the properties of ILs can be changed by selecting different groups of cations and anions, which is why ILs are also called “designer solvents”.11
ILs are gradually being used more often in flotation processes due to their excellent solubility and non-volatility. Sahoo et al. reported the use of tricaprylmethyl ammonium salicylate (TOMAS),12 Aliquat-336 (C25H54ClN),13 Cetyl pyridinium bromide (CPA)6 in the flotation of quartz. Azizi et al. employed tetrabutylammonium bis(2-ethylhexyl)-phosphate ([N4444][DEHP]) for the flotation of monazite and bastnäsite, two minerals that are typical rare earth minerals.14 Li et al. employed tetraethylammonium mono-(2-ethylhexyl)2-ethylhexyl phosphonate ([N2222][EHEHP]) for the flotation of bastnäsite and its two common gangue minerals, quartz and hematite.5 However, the current application of ILs as collectors in froth flotation is still rare, especially for aluminate minerals or aluminosilicate minerals.
The demand for lithium resources is booming, with the rapid production of lithium-ion batteries for electric vehicles. At the same time, a large number of lithium-ion batteries go retired. As a critical raw material categorized by the European Commission,15,16 lithium in spent lithium-ion batteries needs to be effectively recycled from an economic and environmental perspective and ensure the security of raw material supply. Currently, pyrometallurgical processing is one of the efficient routes to recycle value metals from spent LIBs.17,18 Copper, cobalt and nickel can be enriched in an alloy and then recovered after the smelting process but lithium transfers to the slag and is currently not well recovered.17,19 Lithium can often present as an aluminate mineral phase in many slag types, such as those from the Umicore process and those based on Li2O–Al2O3–SiO2–CaO slags.19–22
LiAlO2 has attracted much attention compared to spodumene, an essential lithium-bearing industrial mineral because it has a higher lithium content and does not require high-temperature roasting for crystal transformation. Improving the separation efficiency between LiAlO2 and its common gangue mineral melilite solid solution (melilite s.s.)23 via mineral processing approaches is highly beneficial for the subsequent hydrometallurgical process and is essential for improving the pyrometallurgical recovery path for lithium-ion batteries. Previous research has shown that LiAlO2 can be floated by certain fatty acids/fatty acid soap such as sodium oleate, naphthenic acid, and commercial collector Flotinor FS-2, FS-100, and SM-15 produced by Clariant.20,23
Oleic acid and its saponification product, sodium oleate, are widely utilized collectors in industrial flotation practice and in fundamental research.24 Naphthenic acid is comprised of mixed saturated aliphatic and alicyclic carboxylic acids which contain monocyclic ring, dual ring, or alkyl side chain.25,26 As a by-product of petroleum refining, it is broadly available, and therefore inexpensive compared to oleic acid. In addition, because of its similar properties to that of fatty acids,26 naphthenic acid can also be treated as a possible substitute for oleic acid or in combination with oleic acid in flotation. Currently it has been used in many flotation studies, such as scheelite27 or hematite28 flotation. Flotinor FS-2 is a commercial collector based on a mixture of saturated and unsaturated carboxylic acids29,30 and is used in flotation studies of different oxide minerals,29,31 sulfide minerals,32 and even industrial wastes.30
However, when these conventional flotation chemicals are used for flotation, there is a particular risk of polluting the environment. Therefore, the use of new green flotation chemicals is crucial for constructing a circular economy. An alternative process by reducing the needed amount of flotation chemicals via a pre-functionalization has been recently reported by our groups.23
In this paper, ILs were evaluated for the first time in the flotation of LiAlO2 and its gangue mineral melilite s.s. Firstly, reagent screening experiments for single mineral flotation against LiAlO2 and melilite s.s. were carried out for seven ILs. From these, IL-1 with an imidazolium cation and a bromide anion and IL-7 with a pyridinium cation and a bromide anion were selected for further flotation experiments (dosage, pH). Flotation experiments were also conducted using naphthenic acid, a conventional fatty acid-based collector, and FS-2, a commercial collector in order to compare the results with the ILs. Moreover, the effects of different counter-anions in the ILs on the flotation were evaluated. Finally, a pre-functionalization was also explored with modified cholesterol derivatives, comparing the effect of cholesterylsulfate and cholesterylphosphate on the flotation of LiAlO2 and melilite s.s. This study is vital for further optimizing lithium recovery from the pyrometallurgical recycling path of lithium-ion batteries and the flotation of primary minerals such as aluminosilicates.
2. Materials and methods
2.1. Experimental materials
LiAlO2 (Sigma-Aldrich) and melilite s.s. were employed for flotation experiments. The under 63 μm sieve product of LiAlO2, was used for flotation tests. After grinding, the melilite ore, which came from Vata de Sus, Hunedoara, Romania, was further sieved and the product under 63 μm sieve was sampled and also employed for flotation. The chemical analysis (Table 1) and the X-ray powder diffraction measurement were performed on the sample. According to the XRD analysis (see ESI, p. S1†), besides the main phase melilite s.s., there are also some impurities such as merwinite, wollastonite, and calcite.
Table 1 Chemical composition of melilite s.s.
|
Content, % |
Na2O |
0.2 |
MgO |
4.1 |
Al2O3 |
15.99 |
SiO2 |
27.49 |
P2O5 |
0.02 |
Cl |
0.08 |
K2O |
0.02 |
CaO |
31.88 |
TiO2 |
0.409 |
MnO |
0.04 |
Fe2O3 |
3.06 |
The used ILs are listed in Table 2 and are abbreviated as IL-1 to IL-7. These ILs were synthesized according to literature procedures. IL-1,33 IL-5 and IL-7,34 IL-3 and IL-4,35 IL-2 (ref. 36) and IL-6a37 and IL-6b.38
FS-2 (Clariant), naphthenic acid (Fluka) and pine oil (American Cyanamid) were purchased from commercial courses. Naphthenic acid was saponified by adding NaOH to obtain sodium naphthenate.
2.2. Methods
2.2.1. Microflotation. A modified Hallimond tube (Fig. 1) produced by HI-ALOQUIMICA, Brazil, was used to perform flotation tests. The modified Hallimond tube consists of three parts and it is easy to disassemble them for cleaning. The air can flow into the tube through a piece of porous glass (medium-pore fritted glass) installed in the bottom part. In addition, a small magnetic stirrer bar was placed at the bottom to stir the slurry. The IL screening experiments were conducted at natural pH and ambient temperature and the sample amount for each test was 2 grams. Firstly, the slurry was stirred in a beaker for 1 minute, then the conditioning time was also 1 minute after the reagents were added. The slurry was then transferred to a Hallimond tube for flotation. The airflow rate of each test was controlled to be around 2.1 ± 0.2 L h−1, and the rotation speed was controlled to be 500 rpm. The flotation time lasted for 3 min.
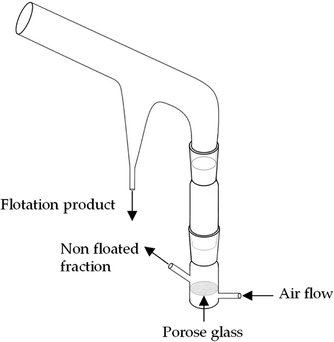 |
| Fig. 1 Sketch of the modified Hallimond tube.23 | |
In further flotation experiments, IL-1 and IL-7, the two ionic liquids with the highest LiAlO2 yields in the screening tests, were selected for flotation tests at three different pHs: natural pH, pH 7 ± 0.2, and pH 9 ± 0.2. The pH was stabilized with a Britton–Robinson buffer consisting of 0.04 M boric acid, 0.04 M phosphoric acid and 0.04 M acetic acid and the desired pH was achieved by adding 0.2 M NaOH.
The collector dosages for LiAlO2 flotation were 0 g t−1, 50 g t−1, 100 g t−1, 150 g t−1, 200 g t−1, 250 g t−1 and 300 g t−1. According to our previous research, the yield of LiAlO2 is much higher than that of melilite s.s. at the same amount of sodium oleate.23 Therefore, in this paper, higher dosages of collectors (0 g t−1, 300 g t−1, 500 g t−1, 1000 g t−1 and 2000 g t−1) were selected for melilite s.s.
After flotation, the froth product and the pulp product were weighed separately. The flotation effect was compared by the yield of the froth product. The difference in yield of the same collector for different minerals forms the basis for selective flotation separation. The greater the difference, the better the separation efficiency to be expected.
The pre-functionalized samples were not treated with collectors.
2.2.2. Analytical methods. ATR-IR-spectra were recorded on an Alpha-T IR (Bruker) with a platinum ATR-unit and diamond crystal. Vibrations are given in cm−1.
3. Results and discussions
3.1. Ionic liquids screening
Through the screening of the seven ILs, it was observed that IL-1, 2, 3, 4, 5, 7 had a significant collecting effect on LiAlO2 compared to the flotation tests without the collector. Their collecting ability on melilite s.s. was much weaker than that of LiAlO2. The IL-1, 2, 3 contained an imidazolium cation, while IL-5, 7 contained a pyridinium cation. The anion in IL-1, 5, 7 was bromide, while IL-2, 4 had a methanesulfonate anion. IL-6 was not available for screening tests because it was difficult to dissolve in water.
The principle of micro-flotation reagents screening was that the collection ability of the reagents for LiAlO2 and melilite s.s. should be considered at the same time. The flotation yield of the reagent for LiAlO2 should be as high as possible, yet its flotation yield for melilite s.s. should be the opposite.
Since IL-1 and IL-7 contributed to a high yield of about 40% for the flotation of LiAlO2, and the difference in yield was reflected in the flotation of melilite s.s., these two reagents were further investigated in subsequent flotation experiments (Fig. 2).
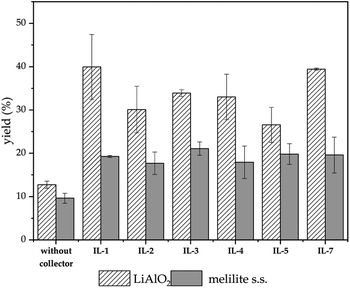 |
| Fig. 2 Screening tests for different ionic liquids. | |
3.2. Effects of conventional collectors and ILs on the flotation of LiAlO2 and melilite s.s.
At natural pH, which is 11, the flotation yields of both conventional fatty acid-based collectors against LiAlO2 were better than those of IL-1 and IL-7. The highest yield of 66.9% for LiAlO2 flotation was obtained with the collector FS-2 when the dosage was 250 g t−1.
The flotation yields of both fatty acid collectors against melilite s.s. were similarly larger than those of IL-1 and IL-7 at natural pH. FS-2 and naphthenic acid flotation yields against melilite s.s. were close to 53% when the collector dosage was 2000 g t−1. The lower performance of the ionic liquids may be explained due their lower hydrophobic character compared to the applied conventional collectors (Fig. 3).
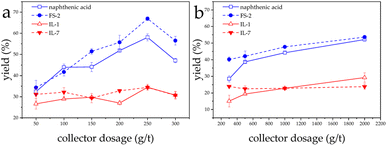 |
| Fig. 3 Effect of collector dosage on flotation of LiAlO2 (a) and melilite s.s. (b) using different collectors at natural pH. | |
At pH 9 both conventional collectors have higher flotation recovery than IL-1 and IL-7 for LiAlO2. The yields of LiAlO2 ranged between 38.8% and 45.1% when FS-2 was used and dropped to 31.3–43.6% when naphthenic acid was employed.
A similar trend was observed in the flotation of melilite s.s. The yields were much lower when using IL-1 and IL-7 than conventional collectors. With FS-2, the yields ranged from 40.8% to 43.5% and when naphthenic acid was used, the yields of melilite s.s. ranged from 39.3% to 46.2% (Fig. 4).
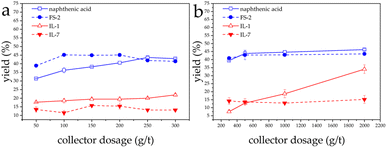 |
| Fig. 4 Effect of collector dosage on flotation of LiAlO2 (a) and melilite s.s. (b) using different collectors at pH 9. | |
The flotation yields of both conventional collectors against LiAlO2 were not satisfactory at pH 7, ranging from 39% to 42.2%. Nevertheless, ILs remained less effective than conventional collectors for LiAlO2. The yields were between 28.4% and 31.5% when IL-2 was used, and the yield of IL-7 was even below 25%.
For melilite s.s. flotation, both conventional collectors also showed higher yields at pH 7 than IL-1 and IL-7. Yields of melilite ranged between 22.2% and 43.8% when FS-2 was applied. With naphthenic acid melilite s.s. was isolated between 41.8% and 51.5% (Fig. 5). Obviously, the natural pH of LiAlO2 at 11 is needed to have a sufficient amount of deprotonated carboxylic acids present in the system. This explains the strong influence of the pH values on the carboxylic acid collector. The presence of carboxylate leads to a stronger interact with these collectors with the surface of the mineral.
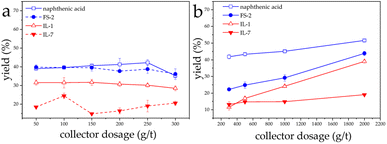 |
| Fig. 5 Effect of collector dosage on flotation of LiAlO2 (a) and melilite s.s. (b) using different collectors at pH 7. | |
After being treated with different collectors, the IR-spectra of LiAlO2 displayed a new band at 1360–1380 cm−1. The appearance of this new band might be due to chemisorption according to our previous research (Fig. 6).23
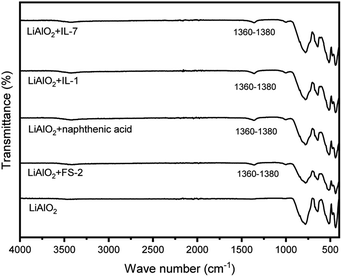 |
| Fig. 6 FT-IR measurement of LiAlO2 treated with different collectors at natural pH. | |
3.3. Comparation of bromide and chloride
Different anions in ILs can influence their viscosity39 which thus can affect the flotation yield. Therefore, it was decided to perform flotation experiments with two different anions, Br− and Cl−, to compare their effects on the flotation yield. As shown in Fig. 7, when the cation in the IL was 1-ethyl-3-methylimidazolium (EMIM), the two anions did not have a great influence on the flotation yield and the yield of LiAlO2 was very close. However, when the cation in the ionic liquid was 1-methyl-3-octylimidazolium (OMIM), the anion Cl− had a higher yield of LiAlO2 than Br−. This is interesting since that harder anion leads to a better result. It would have been reasonable to assume that the softer anion is superior, because the overall IL would be more hydrophobic. It could be that the harder chloride anions could form more easily a layer over the LiAlO2 surface due to the better interaction with the hard Li and Al ions present on the surface of the mineral compared to the softer bromide anion. The anion layer could then bind the lipophilic OMIM cation easier on the surface layer.
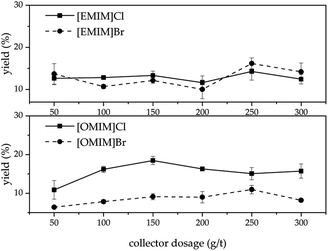 |
| Fig. 7 Effect of Br− and Cl− in ionic liquids on flotation yield. | |
3.4. Mixture of ILs and conventional collector
When specific flotation reagents are mixed in certain proportions, a synergistic effect can occur with the flotation effect better than that of a single reagent.40 For example, Xu et al. reported a mixed anionic and cationic collector for the flotation of spodumene, where the anionic collector was sodium oleate, and the cationic collector was dodecyl trimethyl ammonium chloride (DTAC). After adding the mixed collector in the artificially mixed mineral system, the Li2O grade increased to 5.57%. If only sodium oleate was used, the Li2O grade decreased to 4.13%.40 Bayat et al. tried a mixture of three cationic collectors, AERO 3030C, AERO 801 and AERO 825, for the feldspar flotation and the mixed collector exhibits better selectivity than the single one. The trace elements of the main impurity, Ti and Fe-content in the concentrates, are lower than that with the single collector.41 Xu et al. reported a mixed anionic and non-ionic collector for the separation of spodumene and feldspar in an artificial mixed mineral micro-flotation, where the anionic collector was sodium oleate, and the non-ionic collector was dodecyl succinimide. The mixed collectors achieve a Li recovery of 82.67%, which is higher than the single collector used (68.11% recovery).42
The flotation yields were not satisfactory when a single IL as a collector was used. It may be because the carbon chain length of the ionic liquid was not long enough. ILs are generally not surface active, but when the number of hydrophobic alkyl carbon chain atoms on the IL exceeds 8, the ionic liquid can be more surface-active.43 Therefore, the next was to mix the IL with a fatty acid-based collector.
By mixing conventional collectors with ILs for flotation, the yield of the combination of naphthenic acid and IL-1 for LiAlO2 at natural pH was higher than that of IL-1 alone but slightly lower than that of naphthenic acid. The yield of the combination of naphthenic acid and IL-1 for melilite s.s. at natural pH was much lower than that of the single collector naphthenic acid and also lower than that of IL-1. The yield difference between LiAlO2 and melilite s.s. reached about 35% for this collector mixture. The flotation yield difference between LiAlO2 and melilite s.s. at natural pH with naphthenic acid was only about 18%. At pH 7, the yield difference between LiAlO2 and melilite s.s. reached 21% with the mixed collectors. The difference in flotation yield between LiAlO2 and melilite s.s. at pH 7 using naphthenic acid was about 6%. At pH 9, the yield difference between LiAlO2 and melilite s.s. reached about 19% with the mixed collectors. The flotation yield difference between LiAlO2 and melilite s.s. at pH 9 using naphthenic acid was about 3.5% (Fig. 8).
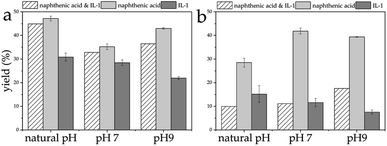 |
| Fig. 8 Flotation yield of LiAlO2 (a) and melilite s.s. (b) by mixed collector – naphthenic acid and IL-1 at different pH. | |
Another collector combination, FS-2 and IL-1 showed a similar trend. The yield of the combination of FS-2 and IL-1 collector for LiAlO2 at natural pH was higher than that of the IL-1, but lower than that of naphthenic acid. The yield difference between LiAlO2 and melilite s.s. reached about 31% for this mixed collector. The difference in flotation yield between LiAlO2 and melilite s.s. at natural pH with FS-2 was about 17%. At pH 7, the yield difference between LiAlO2 and melilite s.s. reached about 35% with the mixed collectors. The difference in flotation yield between LiAlO2 and melilite s.s. pH 7 was about 14% using FS-2. At pH 9, the yield difference between LiAlO2 and melilite s.s. reached about 7% with these mixed collectors. The difference in flotation yield between LiAlO2 and melilite s.s. at pH 9 using FS-2 was about 19% (Fig. 9).
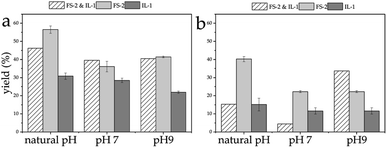 |
| Fig. 9 Flotation yield of LiAlO2 (a) and melilite s.s. (b) by mixed collector – FS-2 and IL-1 at different pH. | |
3.5. Pre-functionalized cholesterol
Since IL-6 was insoluble in water, LiAlO2 and melilite s.s. were pre-functionalized with cholesterylsulfate and cholesterylphosphate in advance. The advantage of this method is that the materials can be pre-treated in advance, making it unnecessary to continue adding the collector in the subsequent flotation.23
Through flotation experiments, a difference in the flotation yield of LiAlO2 and melilite s.s. after the pretreatment effect of cholesterylsulfate, about 25%, as shown in Table 3. LiAlO2 and melilite s.s. after cholesterylphosphate pretreatment showed their strong hydrophobicity (Table 3).
Table 2 Applied ionic liquids
IL |
Structure and name |
IL |
Structure and name |
1 |
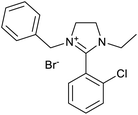 |
5 |
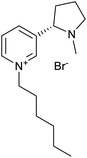 |
3-Benzyl-2-(2-chlorophenyl)-1-ethyl-4,5-dihydro-1H-imidazol-3-ium bromide |
(S)-1-Hexyl-3-(1-methylpyrrolidin-2-yl)pyridin-1-ium bromide |
2 |
 |
6a/6b |
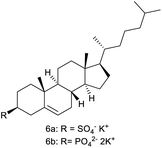 |
1,3-Bimethyl-2-phenyl-4,5-dihydro-1H-imidazol-3-ium-(7,7-dimethyl-2-oxobicyclo[2.2.1]heptan-1-yl)methanesulfonate |
6a: potassium-(3S,8S,9S,10R,13R,14S,17R)-10,13-dimethyl-17-((R)-6-methylheptan-2-yl)-2,3,4,7,8,9,10,11,12,13,14,15,16,17-tetradecahydro-1H-cyclopenta[a]phenanthren-3-yl sulfate(potassium cholesterylsulfate) |
6b: phosphate(potassium cholesterylphosphate) |
3 |
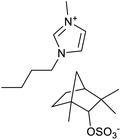 |
7 |
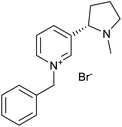 |
1-Butyl-3-methyl-1H-imidazole-3-ium-1,3,3-trimethylbicyclo[2.2.1]heptan-2-yl sulfate |
(S)-1-Benzyl-3-(1-methylpyrrolidin-2-yl)pyridin-1-ium bromide |
4 |
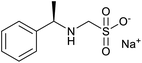 |
|
|
Sodium-(R)-((1-phenylethyl)amino)methanesulfonate |
Table 3 Flotation yield of cholesterylsulfate pre-functionalized LiAlO2 (a) and melilite s.s. (b)
Pre-functionalized samples |
|
Yield, % |
LiAlO2 |
Chol. + SO4 |
53.51 |
Melilite s.s. |
Chol. + SO4 |
28.49 |
4. Conclusions
Different ILs were investigated for the first time in the flotation of LiAlO2 and its gangue mineral melilite s.s. A significant influence of the hardness of the counter anions chloride and bromide of the ILs in the flotation process was observed. Furthermore, it was possible to apply ILs as additives with known collectors in order to increase the selectivity of the flotation process significantly. This study is vital for the further optimization of lithium recovery from the pyrometallurgical recycling path of lithium-ion batteries and the flotation of primary minerals such as aluminosilicates.
Conflicts of interest
There are no conflicts to declare.
Acknowledgements
We acknowledge Thomas Schirmer from Department of Mineralogy, Geochemistry, Salt Deposits, Institute of Disposal Research for the XRD analysis. We thank Petra Sommer, Heike Grosse, and Maike Gamenik from the IFAD Institute of Mineral and Waste Processing, Recycling and Circular Economy Systems for the elemental analysis.
Notes and references
- P. Wasserscheid and T. Welton, Ionic liquids in synthesis, Wiley-VCH, Weinheim, 2003 Search PubMed.
- Y. Tong, H. Yang, J. Li and Y. Yang, Extraction of Au(III) by ionic liquid from hydrochloric acid medium, Sep. Purif. Technol., 2013, 120, 367–372 CrossRef CAS.
- D. Chen, X. OuYang, Y. Wang, L. Yang and C. He, Liquid–liquid extraction of caprolactam from water using room temperature ionic liquids, Sep. Purif. Technol., 2013, 104, 263–267 CrossRef CAS.
- A. Berthod, M. J. Ruiz-Ángel and S. Carda-Broch, Recent advances on ionic liquid uses in separation techniques, J. Chromatogr. A, 2018, 1559, 2–16 CrossRef CAS PubMed.
- R. Li, C. Marion, E. Espiritu, R. Multani, X. Sun and K. E. Waters, Investigating the use of an ionic liquid for rare earth mineral flotation, J. Rare Earths, 2021, 39, 866–874 CrossRef CAS.
- H. Sahoo, S. S. Rath, B. Das and B. K. Mishra, Flotation of quartz using ionic liquid collectors with different functional groups and varying chain lengths, Miner. Eng., 2016, 95, 107–112 CrossRef CAS.
- M. Muntzeck, F. Pippert and R. Wilhelm, Tetraalkylammonium-based ionic liquids for a RuCl3 catalyzed C–H activated homocoupling, Tetrahedron, 2020, 76, 131314 CrossRef CAS.
- M. V. Mancini, N. Spreti, P. Di Profio and R. Germani, Understanding mercury extraction mechanism in ionic liquids, Sep. Purif. Technol., 2013, 116, 294–299 CrossRef CAS.
- J. G. Huddleston, H. D. Willauer, R. P. Swatloski, A. E. Visser and R. D. Rogers, Room temperature ionic liquids as novel media for ‘clean’ liquid–liquid extraction, Chem. Commun., 1998, 1765–1766 RSC.
- M. Muntzeck and R. Wilhelm, Influence of Ionic Liquids on an Iron(III) Catalyzed Three-Component Coupling/Hydroarylation/Dehydrogenation Tandem Reaction, Int. J. Mol. Sci., 2016, 17, 860–868 CrossRef PubMed.
- M. Freemantle, Designer solvents – ionic liquids may boost clean technology development, Chem. Eng. News, 1998, 76, 32–37 CrossRef.
- H. Sahoo, S. S. Rath and B. Das, Use of the ionic liquid-tricaprylmethyl ammonium salicylate (TOMAS) as a flotation collector of quartz, Sep. Purif. Technol., 2014, 136, 66–73 CrossRef CAS.
- H. Sahoo, S. S. Rath, S. K. Jena, B. K. Mishra and B. Das, Aliquat-336 as a novel collector for quartz flotation, Adv. Powder Technol., 2015, 26, 511–518 CrossRef CAS.
- D. Azizi, F. Larachi and M. Latifi, Ionic-liquid collectors for rare-earth minerals flotation case of tetrabutylammonium bis(2-ethylhexyl)-phosphate for monazite and bastnäsite recovery, Colloids Surf., A, 2016, 506, 74–86 CrossRef CAS.
- M. Keersemaker, in Suriname revisited [electronic resource], ed. M. Keersemaker, Springer, Cham, 2020, pp. 69–82 Search PubMed.
- A. Vanderbruggen, J. Sygusch, M. Rudolph and R. Serna-Guerrero, A contribution to understanding the flotation behavior of lithium metal oxides and spheroidized graphite for lithium-ion battery recycling, Colloids Surf., A, 2021, 626, 127111 CrossRef CAS.
- Rückgewinnung von Lithium aus Li-Ionen-Traktionsbatterien – Entwicklungen im Rahmen des LiBRi-Projektes, ed. T. Elwert, D. Goldmann and T. Schirmer, TK-Verlag, 2011, vol. 4 Search PubMed.
- T. Schirmer, H. Qiu, H. Li, D. Goldmann and M. Fischlschweiger, Li-Distribution in Compounds of the Li2O-MgO-Al2O3-SiO2-CaO System—A First Survey, Metals, 2020, 10, 1633 CrossRef CAS.
- T. Elwert, D. Goldmann, T. Schirmer and K. Strauss, Phase Composition of High Lithium Slags from the Recycling of Lithium Ion Batteries, World Metall.–ERZMETALL, 2012, 65, 163–171 CAS.
- Challenges and research needs in the flotation of synthetic metal phases, ed. A. Haas, T. Elwert, D. Goldmann and T. Schirmer, GDMB Verlag GmbH, Clausthal-Zellerfeld, 2018 Search PubMed.
- T. Schirmer, H. Qiu, D. Goldmann, C. Stallmeister and B. Friedrich, Influence of P and Ti on Phase Formation at Solidification of Synthetic Slag Containing Li, Zr, La, and Ta, Minerals, 2022, 12, 310 CrossRef CAS.
- A. Wittkowski, T. Schirmer, H. Qiu, D. Goldmann and U. E. A. Fittschen, Speciation of Manganese in a Synthetic Recycling Slag Relevant for Lithium Recycling from Lithium-Ion Batteries, Metals, 2021, 11, 188 CrossRef CAS.
- H. Qiu, J. Kersebaum, A. Wollmann, N. Feuge, A. Haas, D. Goldmann and R. Wilhelm, Improvement of the froth flotation of LiAlO2 and melilite solid solution via pre-functionalization, Sci. Rep., 2021, 11, 20443 CrossRef CAS PubMed.
- S. M. Bulatovic, Handbook of flotation reagents. Chemistry, theory and practice, Elsevier, Amsterdam, Oxford, 2007 Search PubMed.
- J. V. Headley and D. W. McMartin, A review of the occurrence and fate of naphthenic acids in aquatic environments, J. Environ. Sci. Health, Part A: Toxic/Hazard. Subst. Environ. Eng., 2004, 39, 1989–2010 CrossRef PubMed.
- D. Wang, Flotation Reagents: Applied Surface Chemistry on Minerals Flotation and Energy Resources Beneficiation, Springer Singapore, Singapore, 2016 Search PubMed.
- N. Kupka and M. Rudolph, Froth flotation of scheelite – A review, Int. J. Min. Sci. Technol., 2018, 28, 373–384 CrossRef CAS.
- K. Quast, Literature review on the use of natural products in the flotation of iron oxide ores, Miner. Eng., 2017, 108, 12–24 CrossRef CAS.
- O. Kangal, A. A. Sirkeci and A. Güney, Flotation behaviour of huntite (Mg3Ca(CO3)4) with anionic collectors, Int. J. Miner. Process., 2005, 75, 31–39 CrossRef CAS.
- B. Breitenstein, T. Elwert, D. Goldmann, A. Haas, T. Schirmer and V. Vogt, Froth Flotation of Copper and Copper Compounds from Fine Fractions of Waste Incineration Bottom Ashes, Chem. Ing. Tech., 2017, 89, 97–107 CrossRef CAS.
- Clariant Mining Solutions, Beneficiation of Frequently Occurring Minerals, Clariant, https://www.clariant.com/-/media/Files/Business-Units/OMS/Clariant-Chart-Benefication-of-Frequently-Occuring-Minerals-2020-EN.pdf, accessed, 29 September 2022 Search PubMed.
- F. May, S. Hamann, A. Quade and V. Brüser, Froth flotation improvement by plasma pretreatment of sulfide minerals, Miner. Eng., 2017, 113, 95–101 CrossRef CAS.
- V. Jurcik and R. Wilhelm, Imidazolinium salts as catalysts for the aza-Diels-Alder reaction, Org. Biomol. Chem., 2005, 3, 239–244 RSC.
- T. Heckel, A. Winkel and R. Wilhelm, Chiral ionic liquids based on nicotine for the chiral recognition of carboxylic acids, Tetrahedron: Asymmetry, 2013, 24, 1127–1133 CrossRef CAS.
- A. Winkel and R. Wilhelm, New Chiral Ionic Liquids Based on Enantiopure Sulfate and Sulfonate Anions for Chiral Recognition, Eur. J. Org. Chem., 2010, 2010, 5817–5824 CrossRef.
- A. Winkel and R. Wilhelm, New chiral ionic liquids based on imidazolinium salts, Tetrahedron: Asymmetry, 2009, 20, 2344–2350 CrossRef CAS.
- J. Goto, K. Suzaki and T. Nambara, Synthesis of conjugated cholesterol and cholestanols, Chem. Pharm. Bull., 1979, 27, 1926–1931 CrossRef CAS.
- H. A. C. Montgomery, J. H. Turnbull and W. Wilson, 882. Some cholesteryl phosphates, J. Chem. Soc., 1956, 4603 RSC.
- C. Xia and Z. Li, Task specific ionic liquids (in chinese), Chemical Industry Press, Beijing, 2018 Search PubMed.
- L. Xu, Y. Hu, J. Tian, H. Wu, Y. Yang, X. Zeng, Z. Wang and J. Wang, Selective flotation separation of spodumene from feldspar using new mixed anionic/cationic collectors, Miner. Eng., 2016, 89, 84–92 CrossRef CAS.
- O. Bayat, V. Arslan and Y. Cebeci, Combined application of different collectors in the floatation concentration of Turkish feldspars, Miner. Eng., 2006, 19, 98–101 CrossRef CAS.
- L. Xu, F. Jiao, W. Jia, Z. Pan, C. Hu and W. Qin, Selective flotation separation of spodumene from feldspar using mixed anionic/nonionic collector, Colloids Surf., A, 2020, 594, 124605 CrossRef CAS.
- Y. Hu, J. Han and R. Guo, Influence of the Alkyl Chain Length of the Imidazole Ionic Liquid-Type Surfactants on Their Aggregation Behavior with Sodium Dodecyl Sulfate, Langmuir, 2020, 36, 10494–10503 CrossRef CAS PubMed.
|
This journal is © The Royal Society of Chemistry 2022 |
Click here to see how this site uses Cookies. View our privacy policy here.