DOI:
10.1039/D2RA04455B
(Paper)
RSC Adv., 2022,
12, 31585-31595
Synthesis of a porous SiO2–H3BO3–V2O5–P2O5 glassy composite: structural and surface morphological behaviour for CO2 gas sensing applications†
Received
19th July 2022
, Accepted 19th October 2022
First published on 3rd November 2022
Abstract
The present work mainly focuses on the fabrication of a porous glass 40SiO2–35H3BO3–19V2O5–6P2O5 via a melt-quenching technique. The structural, morphological, and sensing behaviour of the glass sample was investigated successfully. The calculated density and molar volume of the fabricated glass are 2.4813 ± 0.124 g cm−3 and 35.7660 ± 1.708 cm3 mol−1. XRD, SEM and TEM analyses confirmed the amorphous nature of the glass. FTIR results revealed the O–H bond formations, which indicate that the presence of water molecules is probably due to the porous nature of the glass. Further, BET analysis confirmed the mesoporous nature of the glass sample with a mean pore diameter of 7 nm. The sensing response of the synthesized glass at 1000 ppm concentration of CO2 was found to be 3.05 with a response time 22.6 s and recovery time 25.8 s. Hence, this porous glass can be easily synthesized, is affordable, and was found to be useful for CO2 gas sensing applications.
Introduction
The demand for better and industrialized surroundings has led to an extreme evolution of harmful gases, and the excessive use of natural resources has resulted in increased air pollution. The need to upgrade and enhance man-made resources for coming generations is increasing day by day, which in turn causes a lot of pollution in the atmosphere.1 Carbon dioxide (CO2) is one of the most common toxic gases present in the atmosphere, and the emission from automobiles, greenhouse gases, and industrial plants is the major source of CO2 emission. The excessive release of CO2 has a direct impact on the increased temperature, leading to global warming. To control the toxic harmful gases and to prevent the deterioration of the atmosphere, we need to keep pollution levels in check. This led to the discovery of gas sensors that help reduce air pollution by keeping track of harmful gases, such as CO, CO2, NO2, methane, in the atmosphere, thus preventing the adverse effects of pollution on all natural beings. The first ever gas sensor was developed in the early 1980s based mainly on household or non-professional purposes such as gas leakage, humidity sensors, and car fuel leakage systems.2,3 Gradually, the demand for gas sensors increased for various other applications such as air pollutants, volatile organic compounds (VOCs), fire detection, industrial implants, breath analysers, and many more, which led to the advancement of gas sensors in domestic as well as industrial fields.4–10
Recently, porous glass has attracted increasing attention due to its unique properties such as porous structure, chemical and thermal stability, and very reactive surface.11,12 The porous structure of glass provides a large surface area with various active pore sites to adsorb and desorb gas, which elevates the sensing ability of the sensor, thus making it an excellent gas sensor for many applications.13–15 There is often a discussion as to why only porous materials are considered for gas sensing application over non-porous materials. A non-porous material has a weak sensing response, low selectivity, and requires a high temperature process for the gas sensing mechanism and therefore not suitable for gas sensor applications. Many researchers came forward to present a comparative study of gas sensing properties on porous and non-porous materials having the same composition. Du et al. carried out a detailed ethanol gas sensing measurement on porous SnO2 and non-porous SnO2 microflowers and revealed that the sensing response for porous SnO2 (3.05) showed way better results than non-porous SnO2 (1.5).16 Song et al. synthesized porous ZnO microflowers and non-porous ZnO microflowers by a hydrothermal method and revealed that the response for porous ZnO showed 1.8 times better response results than non-porous ZnO.17
Usually, semiconducting metal oxides (SMOs) are preferred for gas sensing. However, it has been revealed in recent research that amorphous materials can also provide excellent gas sensing output due to the availability of large surface area, easy fabrication, and require low temperatures for manufacturing amorphous composites. Many research works have proven that amorphous substances like glass can be used for CO2 gas sensing applications. Sophia et al. demonstrated that when applied voltage and polarisation voltage flow is balanced, a standard soda-lime glass (Sailing Boat Lab, China) can achieve prominent CO2 gas sensing properties. The sensing response was found to be 0.43 for the highest concentration of CO2 (5000 ppm).19 Kumar et al. synthesized a multiwalled carbon nanotube (MWCNT) thin film by using the chemical vapor deposition (CVD) technique for CO2 gas sensing applications. The sensing response for the synthesized MWCNT gas sensor was found to be 2.1 at 5000 ppm of CO2.20 Recently, Kim et al. investigated the gas sensing properties of pure and Pd-, Pt-, and Au-functionalized soda-lime glasses. The functionalized glasses were prepared via the UV-irradiation method for different precursors. The gas sensing results revealed that at a temperature of 350 °C, the gas sensing response for pure soda-lime glass was 1.379 for 5000 ppm concentration of CO2 gas.21 More recently, Ali et al. synthesized amorphous molybdenum trioxide (MoO3−x) films using the thermal evaporation technique. The MoO3−x thin film deposited on a 650 nm thick glass substrate revealed a relatively high response and recovery time, and the sensor response at 200 °C was recorded to be 2.826.22 Various amorphous and porous materials have been analysed for CO2 gas sensing applications. However, not much research has been done on porous glass, which can emerge as a potential contender for gas sensors due to its unique porous morphology and amorphous nature. This study revealed that the synthesized glass showed way better sensing results than many crystalline materials, thus opening a new field for glass applications.
Various metal oxides are being used for glass synthesis, like SiO2, H3BO3, V2O5, etc. Silicon dioxide (SiO2) is the main constituent for glass fabrication, and it is widely used as a glass former. SiO2 basically enhances the electrical, dielectric, and thermal properties of the synthesized glass. Boric acid (H3BO3) is commonly used as a fluxing agent for glass preparation. Some oxides used in the glass preparation have relatively high melting temperatures, e.g., SiO2 (melting temperature ∼1713 °C); thus, the inclusion of H3BO3 in such oxide glass compositions allows the glass to melt at a lower temperature. Phosphorus pentoxide (P2O5) is an extensively used material for glass fabrication because it has unique properties like low melting point and high thermal and chemical stability, making it an efficient sensing material. Besides these oxides, vanadium pentoxide (V2O5) has attained a lot of attention in the field of sensor technology due to its high stability and chemical resistance and offers low-cost fabrication for sensors.3,23–25
Herein, our main focus is to synthesize a glass 40SiO2–35H3BO3–19V2O5–6P2O5 (SHVP6) via the melt-quenching technique, which is commonly used for glass preparation and is quite affordable and easy to operate. The structural and morphological properties of this synthesized glass are analyzed in detail. We know that the porous structure helps in elevating the sensing ability of the gas sensor. Therefore, the porous morphology of the synthesized glass indicated the possible gas sensing application. Hence, this porous glass is subjected to carbon dioxide (CO2) gas sensing, and a detailed gas sensing analysis is performed to study different parameters like sensor response, response time, and selectivity of porous glass SHVP6.
Experimental
Fabrication of glass sample
Melt-quenching technique (MQT) is widely used for glass preparation. High quality chemical reagents used to fabricate 40SiO2–35H3BO3–19V2O5–6P2O5 glass were SiO2 (Himedia 99.5%), H3BO3 (Himedia 99.5%), V2O5 (Sigma-Aldrich 98%), and P2O5 (Sigma-Aldrich 98%). Appropriate amounts of given chemicals were weighed in an electronic balance, and a batch of 25 g was mixed together with the help of a mortar and pestle with acetone as a mixing medium for 2 h. This mixture was then poured into an alumina crucible and kept in a programmable furnace at 1400 °C with a heating rate of 5 °C min−1. The prepared melt was left in the furnace for an additional 30 min (soaking time) so as to properly homogenize. This melt was then taken out from the furnace and was poured onto an aluminium mould and immediately quenched with the help of an aluminium plate for residual stress removal within the fabricated glass. The sample was then kept in a pre-heated muffle furnace at 400 °C with a heating rate of 5 °C min−1 for 4 h. The fabricated glass samples were taken out of the furnace after cooling to room temperature. The prepared glass was taken out when the furnace was cooled to room temperature (30 °C).7,26 The schematic diagram for glass preparation is shown in Fig. 1(a).
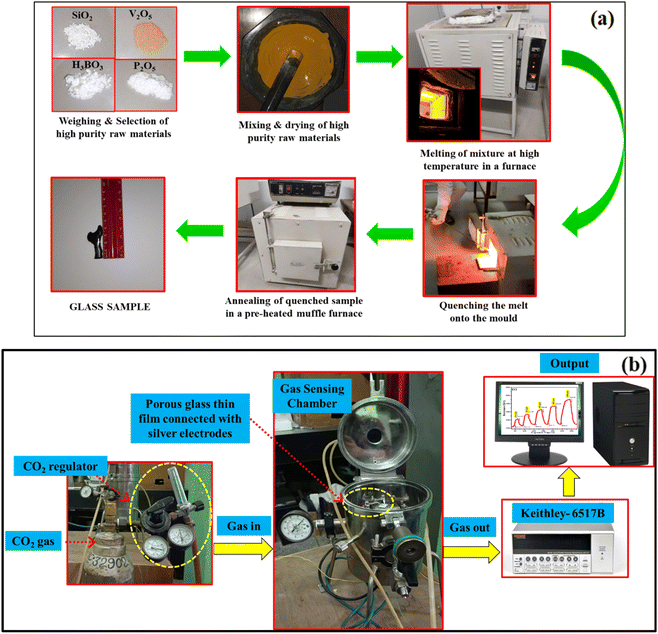 |
| Fig. 1 (a) Schematic diagram for the fabrication of glass sample via the melt-quenching technique, (b) schematic diagram of CO2 gas sensing setup. | |
Device fabrication and CO2 sensor fabrication
To prepare a thin film of porous glass sample, the method employed was as follows: a homogeneous solution was prepared by dissolving the synthesized SHVP6 porous glass in hydrofluoric acid (HF); the solution was prepared using ultra-sonification. This solution was then drop-coated on a glass substrate of dimensions 1 × 1 cm2 and dried at 70 °C on a hot plate. A specially designed gas chamber was used to analyse the characteristics of CO2 gas sensing. The sensing film was mounted on the sample holder, and silver electrodes were connected to the surface of the sensing film and dried at 60 °C. The inlet of the gas chamber is connected to a measuring unit: CO2 regulator, which is used to measure the accurate concentration of the CO2 gas that flows inside the chamber. The leads from the outer end of the gas chamber were connected to the Keithley electrometer 6517B for estimating the electrical resistance of the gas sensing film. A schematic diagram for the gas sensing setup is shown in Fig. 1(b), and the gas sensing measurement was carried out at room temperature (32 °C and 60% RH).27
XRD of the porous glass sample
The synthesized samples were ground for 1.5 h to make a fine powder. To analyze the amorphous nature of the synthesized samples, the XRD pattern of this powdered sample was recorded within a 2θ range of 10°–70° with scanning @ 5° min−1 using a Rigaku Ultima IV XRD machine having a monochromatic CuKα radiation (λ = 1.54 Å) that functioned at 40 kV and tube current at 40 mA.
Density and molar volume
The density of the porous glass was calculated with the help of Archimedes' principle. Irregular shaped glass samples were used to analyse the density of the synthesized porous glass. The measurement was performed with the help of an electronic balance having readability up to 0.0001 mg, and distilled water was used as a liquid medium. To obtain accurate results, the density measurement was repeated three times, and the average value was taken into consideration. The density of the synthesized porous glass was calculated by using the formula given below:7 |
 | (1) |
where, ρw is the density of distilled water (ρw = 1), W1 is the weight of an empty density bottle, W2 is the weight of a density bottle with a porous glass sample, W3 is the weight of density bottle with distilled water and porous glass sample, and W4 is the weight of the density bottle with distilled water. On the other hand, the molar volume (Vm) of the porous glass sample was calculated using the formula given in eqn (2) |
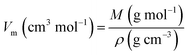 | (2) |
where Vm represents the molar volume of the porous glass sample, M represents the molar mass, and ρ is the density of the porous glass sample.7
Brunauer–Emmett–Teller (BET) measurements
To analyse the surface area, pore size, and surface porosity of a powdered porous glass sample, BET is performed. This analysis reveals the significant properties and importance of the sample in the field of sensor technology. Micrometrics (Gemini VII 2390t) surface area analyser at an adsorption temperature of 77 K was used to determine the pore size, surface area, and porosity of the porous glass sample.
FT-IR and Raman spectroscopy measurements
FT-IR spectroscopy is used to study the structural information of the synthesized sample. To analyse and record the FTIR spectra of the synthesized porous glass, a fine powder of SHVP6 glass and KBr (Potassium bromide) is mixed with the help of a mortar and pestle to make a fine powder and then pressed to form a thin circular pellet using a hydraulic press machine. These thin pellets were used to record the FTIR spectrum through an IRAffinity-IS FTIR (SHIMADZU-01020) within the wavenumber range of 400 to 4000 cm−1. Further, the recorded spectra of the SHVP6 porous glass displayed numerous transmittance bands in different wavenumber regions. Raman spectra were recorded using a MicroRaman setup (Renishaw, UK) that was furnished with 1800 lines per mm diffraction grating within the wavenumber range of 0–1200 cm−1.
Scanning and transmission electron microscopy
To study the surface morphology of the synthesized glass sample, SEM was performed. The surface of the glass sample was polished using different silicon carbide (SiC) powders (mesh number: 120, 600, and 800) to obtain a plain surface. The porous glass was further polished using emery paper (grade 2000, 2500, 3000, and 3500) and then rubbed on a soft blazer cloth using a diamond paste of particle size 1–6 μm along with Hifin fluid ‘OS’. The polished glass sample was then washed with double distilled water to remove any debris from the surface and then placed in an electric oven for 1 h to dry. To avoid any charge accumulation, a sputtering unit is used, Auto Fine Coater JEOL (Model: JEC-3000FC) is used to spread thin gold films on the surface of the glass sample. The polished sample was mounted on a copper stub with the help of a carbon tape, and SEM images were recorded at different magnifications with the help of SEM-Model: JSM-7610 F, Make: JEOL Ltd Japan.26 The TEM images and diffraction patterns were recorded with the help of TEM (JEOL, Model: JEM 2100). A small quantity of finely powdered sample was taken and kept in an isopropyl alcohol bath for about 30 min. The sample for TEM analysis was prepared by casting a few drops of sample on the grid and left to dry in a vacuum overnight.28
Energy dispersive spectroscopy (EDS) measurements
To evaluate the elemental constituents present in the synthesized porous glass, EDS was performed. This technique is quite useful in quantitative as well as qualitative studies. In this technique, a selected area/spot of the porous glass was scanned, and the presence of elements was examined and recorded. Thus, the EDS spectrum reveals the desired elemental information about the synthesized porous glass sample.26
Results and discussion
Density and molar volume of the porous glass
The density and molar volume of the prepared glass sample are 2.4813 ± 0.124 g cm−3 and 35.7660 ± 1.708 cm3 mol−1, respectively. The density of the synthesized glass SHVP6 is found to be less than the standard density of SiO2 (2.65 g cm−3) and the density of V2O5 (3.36 g cm−3). The density of the glass sample was calculated using the Archimedes principle. The decrease in the density of the prepared glass is probably due to the presence of voids/holes in the structural arrangement of the SHVP6 glass, thus indicating the porous nature of SHVP6 glass.7
X-ray diffraction analysis
The XRD analysis of the synthesized glass 40SiO2–35H3BO3–19V2O5–6P2O5 is shown in Fig. 2. The XRD analysis shows diffused peaks with short-range order, confirming the amorphous nature of the prepared glass.26 The absence of sharp peaks depicts that the prepared sample has no major phase formation or grain boundaries, which is further confirmed by the TEM characterization discussed later in this paper.
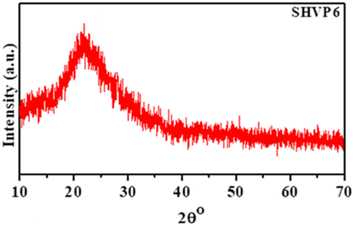 |
| Fig. 2 XRD pattern of porous glass sample SHVP6. | |
Fourier transform infra-red spectroscopy
A FTIR spectrum for the synthesized glass SHVP6 is shown in Fig. 3(a), and a series of transmittance peaks have been observed in the range of 400–4000 cm−1. Multiple peaks have been observed in the low wavenumber region (fingerprint region), and the low intensity peak at 443 cm−1 corresponds to the Si–O rocking vibration, indicating the presence of SiO2 within the glass sample. Another low intensity transmittance peak at 547 cm−1 corresponds to the vibration of the V–O bond. Also, a weak intensity transmittance peak at 650 cm−1 is assigned to the wagging vibrations of Si–H bonding. The low wavenumber region is mainly comprised of silicate bonds, and this might be due to the highest content of SiO2 present in the glass composition.29–31 Another low intensity peak at 1195 cm−1 shows the asymmetric stretching vibration of PO2.32 A broad peak at 1456 cm−1 is observed, which indicates the characteristics of –O– vibrations.33 Peaks at 1622 cm−1, 2926 cm−1, and 3215 cm−1 are assigned to the stretching vibration of O–H bonds inside the porous glassy network. The presence of O–H bonding is probably due to the porous nature of the synthesized glass and also due to the high hygroscopicity of P2O5.34,35,37
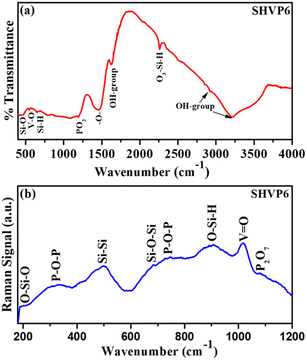 |
| Fig. 3 (a) FTIR spectrum of the SHVP6 porous glass, (b) Raman spectrum of the SHVP6 porous glass. | |
Raman spectroscopy
Fig. 3(b), shows the Raman spectrum of the synthesized porous glass, weak intensity peaks at 187 cm−1, 498 cm−1, and 684 cm−1 correspond to the bending vibration of O–Si–O bond, Si–Si vibration, and symmetric stretching vibration of Si–O–Si, respectively. These peaks indicate the presence of SiO2 within the glassy matrix, which is in good agreement with the.
FTIR spectroscopic analysis.38,40 The weak intensity peaks at 336 cm−1 correspond to vibrations of the pyrophosphate group through a P–O–P linkage.39 A sharp peak is observed at 1018 cm−1, indicating the vibration of V
O; this strong vibration peak indicates that these vanadium species also interact with water molecules to form hydrated species of V2O5, and this reaction is probably due to the porous nature of the synthesized glass sample, which is discussed later in this paper.43 The detailed peaks and their respective vibrational bonding of FTIR and Raman spectra are shown in Table 1.29–44
Table 1 Peak assignment for FTIR and Raman spectra with their respective wave number
FTIR wavenumber (cm−1) |
Vibration type |
References |
Raman wavenumber (cm−1) |
Vibration type |
References |
443 |
Si–O rocking vibration |
29 |
187 |
O–Si–O bending vibration |
38 |
547 |
V–O vibration |
30 |
336 |
PO3 deformation vibration |
39 |
650 |
SiO4 bending vibration |
31 |
498 |
Si–Si vibration |
40 |
1195 |
PO2 asymmetric stretching vibration |
32 |
684 |
Si–O–Si symmetric stretching |
38 |
1456 |
–O– vibration |
33 |
745 |
P–O–P symmetric stretching |
41 |
1622, 2926 |
O–H group |
26, 34 and 35 |
905 |
O–Si–H bending/P–O–P asymmetric stretching vibration |
38 and 42 |
2260 |
O3–Si–H stretching vibration |
36 |
1018 |
V O vibration |
43 |
3215 |
O–H group |
37 |
1078 |
P–O symmetric stretching vibration |
44 |
Scanning electron microscopy and elemental analysis
Fig. 4 shows a high magnification SEM image of the synthesized glass, and the image clearly shows distinct spherical pores having varied pore sizes randomly spread across the surface of the glass sample (indicated by green circles). The average pore diameter of these pores ranges from 0.167–0.322 μm, which are embedded on the glassy matrix as shown in Fig. 4 (indicated by blue dotted lines). Since the pore diameter varied significantly, we can only indicate that the synthesized glass is porous in nature; therefore, TEM microscopy will be discussed later in this paper to analyse the porous as well as amorphous nature of the fabricated glass in a more detailed manner. This pore formation is possibly due to the high temperature manufacturing of the glass, which is synthesized at a temperature of 1400 °C. At high temperatures, the boric acid (H3BO3) present in the glass decomposes as shown in eqn (3): |
 | (3) |
 |
| Fig. 4 High-magnification SEM micrograph of glass sample. | |
The reaction gives out metaboric acid (HBO2) along with the release of water molecules from the glass melt,45,46 thus generating pores on the surface of the glass sample.
Further, there is no visible grain or grain boundary, thus confirming the amorphous nature of the glass, which is in good agreement with the XRD results.
Further, the elemental mapping was performed on a low magnification SEM image, as shown in Fig. S1(a),† to study the distribution of elements on the surface of the prepared glass sample. Fig. 5(a) shows the average distribution of elements on the surface of the glass, the distribution of elemental composition of this homogeneous mixture is further shown in Fig. 5(b)–(e) where 18% of oxygen (indicated by light green color), 26% of vanadium (indicated by purple color), 32% of phosphorus (indicated by dark green color), and 24% of silicon (indicated by light beige color), respectively. The mapping results reveal that phosphorus and vanadium have major contributions to the glass formation. The pie chart (Fig. S1(b)†) shows the elemental distribution of components in the synthesized glass.
 |
| Fig. 5 (a) Average elemental mapping of porous glass, SEM-EDS elemental mapping: (b) O-18%, (c) V-26%, (d) P-32%, (e) Si-24%. | |
Energy dispersive spectroscopy (EDS) is performed to determine the elemental distribution of elements present on the surface of the porous glass (Fig. 6). The EDS spectrum of the synthesized glass further confirmed the presence of elemental composition (average) of silicon (Si), oxygen (O), vanadium (V), and phosphorus (P) along with some impurities like aluminium (Al). The impurity (Al) present in the synthesized glass sample was probably due to the use of aluminium crucible for the high temperature melting process. The weight percentage of vanadium (V) is 32.56%, phosphorus (P) is 15.71%, silicon (Si) is 9.04%, and aluminium (Al) is 0.73%. The graph suggests that the weight percentage of oxygen (O) is 41.96% due to the contribution of oxides in the preparation of the glass sample26
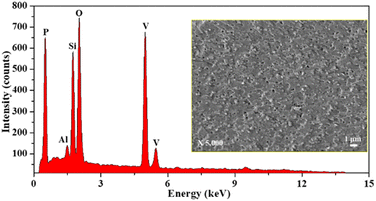 |
| Fig. 6 EDS spectrum of the porous glass sample SHVP6. | |
Transmission electron microscopy
Since the SEM micrograph records the morphology of the sample surface, TEM analysis is performed to study the morphology of the glass sample more closely. Fig. 7(a) shows the TEM image of SHVP6 glass, the overlapped spherical pores spread across the glass sample indicate that the fabricated glass has porous morphology, and these pores have an average pore diameter of 33.42 nm, which is in good agreement with the SEM results.
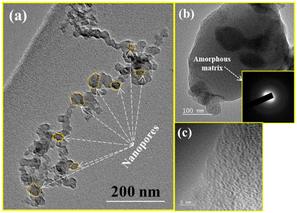 |
| Fig. 7 TEM micrographs of the glass sample: (a) overlapped spherical pores of average pore diameter 33.42 nm, (b) TEM micrograph and SAED-pattern (inset) and (c) and HR-TEM-image of SHVP6 porous glass. | |
The TEM image of SHVP6 glass is shown in Fig. 7(b), and petal-like dark region can be seen in the high-resolution TEM image, which shows a magnified pore. The TEM image reveals the presence of petal-like dark regions; these darker regions (petal-like structure) probably correspond to V-rich zones owing to their high density (6.11 g cm−3), while the lighter regions correspond to (Si, P, O, H) rich zones.47
The inset in Fig. 7(b) shows a selected area electron diffraction (SAED) pattern, and the SAED pattern clearly depicts the diffused rings confirming the amorphous nature of the porous glass.48 Fig. 7(c) shows an HR-TEM image, and no lattice fringe or grain boundaries were observed, which confirms that the fabricated glass is amorphous in nature. These results are consistent with the XRD as well as SEM analysis, which also confirm the amorphous nature of the synthesized porous glass.
Brunauer–Emmett–Teller (BET) analysis
The SEM and TEM analyses indicate the porous morphology of the fabricated glass, and therefore, BET and BJH analysis was performed to confirm the porous nature of the synthesized glass SHVP6. To calculate the specific surface area of the porous sample via physical adsorption technique of gas molecules on the surface of the porous sample, Brunauer–Emmett–Teller (BET) analysis was performed. The total surface area Stotal and the specific surface area SBET are given by |
 | (4) |
where, St is the total surface area of the sample, νm is the monolayer absorbed gas volume, N is the Avogadro's number (6.02 × 1023 molecules per mol), S is the cross-sectional area of adsorbed gas molecule, V is the molar volume of the adsorbed gas |
 | (5) |
SBET is the specific area, and ‘a’ is the mass of the sample.
The calculated surface area of the synthesized glass is 70.8 m2 g−1, and the large surface area also indicates the amorphous nature of the sample.11,49 The total pore volume and mean pore diameter of the SHVP6 glass is found to be 0.1288 cm3 g−1 and 7.2799 nm, respectively. The nitrogen adsorption–desorption curve of the SHVP6 glass is shown in Fig. 8(a), and the graph indicates Type-IV isotherm, which further reveals that the synthesized glass is porous in nature. The mean pore diameter reveals a lot of information about the pores present; if the mean pore diameter is greater than 50 nm, then the sample has macroporous nature, if the mean pore diameter lies between 2–50 nm then the sample has mesoporous nature, and if the mean pore diameter is less than 2 nm then the sample has microporous nature. The synthesized SHVP6 glass has a mean pore diameter of 7 nm, which lies within the range of 2–50 nm, thus confirming that the fabricated porous glass is mesoporous in nature and is in good agreement with SEM and TEM results.50 The BJH (Barrett–Joyner–Halenda) plot is used to measure the pore-size distribution of the synthesized glass sample. The average pore diameter of the SHVP6 glass is 1.66 nm, as shown in Fig. 8(b), which confirms the presence of pores within the glassy matrix. Since the prepared glass is mesoporous in nature, the mesoporous surface area (aP) and mesoporous volume (VP) are 65.666 m2 g−1 and 0.1224 cm3 g−1, respectively.51 These results are in good agreement with each other and the porous nature of the synthesized glass provides a possible pathway for the target gas, which indicates that the fabricated glass can be used for gas sensing applications. Therefore, gas sensing was performed to analyse various parameters in detail.
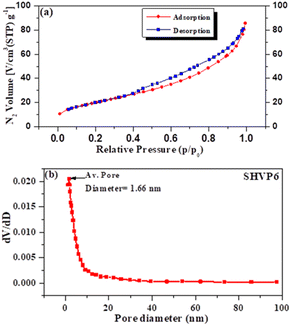 |
| Fig. 8 (a) Nitrogen adsorption–desorption curve of porous glass sample SHVP6. (b) Pore size distribution of the glass sample by BJH method. | |
Gas sensing properties of porous glass
The CO2 gas sensor works on the phenomena of adsorption (ads) and desorption. The variation in electrical resistance of the sensing film occurred due to the adsorption/desorption of CO2 gas on the sensing surface. The parameters taken into consideration to study the sensing properties of CO2 gas for SHVP6 porous glass are sensing response, response time, and recovery time with a concentration range of 200–1000 ppm (parts per million) at room temperature. The CO2 sensing graphs recorded at different concentrations of 200, 400, 600, 800, and 1000 ppm with exposure time are shown in Fig. 9(a), and it can be observed that at 200 ppm concentration, the resistance in air (Ra) is 115.919 MΩ and the resistance of the glass film suddenly increases when exposed to CO2 gas inside the chamber and becomes constant at 214.115 MΩ. Afterwards, CO2 gas is released by opening the outlet of the gas chamber. Other CO2 gas concentrations were recorded in a similar manner, and the respective curves were plotted.
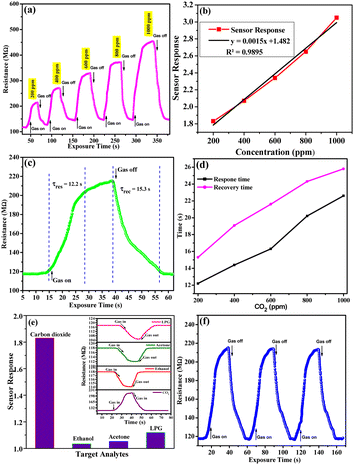 |
| Fig. 9 CO2 gas sensing characteristics of porous glass, (a) CO2 sensing curves for different concentrations, (b) sensor response curve with various concentration of CO2, (c) transit sensor response curve for 200 ppm of CO2, (d) response and recovery time graphs with different concentrations, (e) selectivity graph at 200 ppm of gas analysts, (f) repeatability graph at 200 ppm of CO2. | |
The sensing response of the gas sensor is defined as:
|
 | (6) |
where,
Ra is the resistance in air and
Rg is the resistance of the glass film in the presence of CO
2 gas.
The sensing response of glass film for different concentrations of CO2 (200–1000 ppm) is calculated using eqn (8) and plotted in Fig. 9(b). As the concentration of CO2 increases, the sensing response increases, as indicated by the linear curve. With the help of this calibrated linear curve (linear fit curve), the sensitivity of the sensing device can be calculated by the IUPAC definition (sensitivity = sensor response/concentration). The sensitivity of the sensing device was found as 0.0091 sensor response/ppm. It is observed that the interaction between the adsorbed oxygen species and CO2 molecules deteriorates at low concentrations. On increasing the concentration of CO2 inside the gas chamber, the molecules are adsorbed by the porous film of SHVP6 glass, thus increasing the resistance of the film. The minimum sensor response of the SHVP6 porous glass is found to be 1.83 for 200 ppm of CO2 and the maximum sensor response is 3.05 for 1000 ppm of CO2 as shown in Table S2.† The response time (Tres) is defined as the time required by the sensor to attain maximum resistance when gas is exposed inside the chamber, whereas the time required by the sensor to come back to its initial state when gas is removed from the gas chamber is the recovery time (Trec). The sensor response, response time, and recovery time were calculated by the transits sensor response graph for porous glass SHVP6 film for various concentrations of CO2 gas.52 The transits response graph at 200 ppm concentration of CO2 is shown in Fig. 9(c), and the response time and recovery time are found to be 12.2 s and 15.3 s, respectively. Similarly, for other concentrations of CO2 at 400, 600, 800, and 1000 ppm, response and recovery time are calculated as shown in Fig. 9(d). To further check the selectivity of the SHVP6 sensing film with respect to other target analytes like acetone, ethanol, and LPG, comparative data against sensing response is shown in Fig. 9(e). Here, the sensing responses for acetone, ethanol, LPG, and CO2 are 0.32, 0.53, 0.98, and 1.83, respectively, at 200 ppm concentration. Also, the selectivity curve for various target analytes is shown in Fig. 9(e) (inset). The curve shows that the resistance increases in the case of CO2 gas, while in the case of other target analytes, the resistance decreases. This analysis further confirms the oxidising nature of CO2 gas and that the synthesized sample is an n-type material. The sensing response of CO2 with respect to the other target analytes is relatively higher. The ability to produce the same output after an interval of time for the same parameters is known as the reproducibility of the gas sensor. The repeatability of the sensor is a key parameter, and it can be defined as the same output over one measurement. The repeatability curve at 1000 ppm of sensing film is shown by three consecutive cycles, and it is observed that the measurement is almost 98% repeatable (Fig. 10(a)). Also, the long-term stability of a sensor is a vital parameter and is defined as the ability to reproduce the same measurement after a time interval. The long-term stability curve of SHVP6 sensing film was examined after 15 days’ time interval at 1000 ppm, as shown in Fig. 10(b). The sensor response of the sensing curve is calculated using eqn (8) and plotted in Fig. 10(c). As the number of days increases, the sensor response decreases because the presence of moisture weakens the interaction of the CO2 sensing film. The error bar in the sensor response is shown in Fig. 10(c) and suggests minor changes in sensor response.
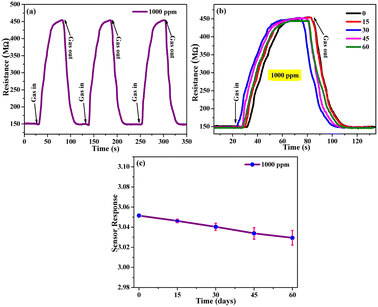 |
| Fig. 10 (a) Sensing characteristics at 1000 ppm of CO2 showing, (b) long-term stability curve at 1000 ppm and (c) sensor response graph at 1000 ppm of CO2. | |
To analyse the gas sensing in detail, various parameters have been calculated, viz., sensitivity, the limit of quantification (LOQ), and the limit of detection (LOD). The sensitivity of the SHVP6 porous glass was calculated using the linear-square fit method and straight-line formula; y = mx + c, where y is the sensitivity of the sensing device, m is the response, and c is the CO2 gas concentration. The correlation plot between CO2 gas concentration and sensing response of the SHVP6 porous glass is shown in Fig. 9(b), which indicates y = 0.0015x + 1.482 and R2 = 0.9895, which reveals the fabricated SHVP6 porous glass is 98% sensitive. The limit of detection is defined as the lowest amount of analyte in the synthesized sample, which can be detected but not necessarily quantified under specified conditions. However, the limit of quantification is the lowest concentration of an analyte in the synthesized sample that can be quantitatively determined with acceptable precision and accuracy under specified conditions. The LOD and LOQ values were calculated using the following equations;
|
 | (7) |
|
 | (8) |
where SD is the standard deviation of response. The calculated values of LOD and LOQ were found to be 292 ppm and 886 ppm, respectively. These results reveal that the synthesized porous glass sensor is quite stable with excellent CO
2 gas sensing properties.
23,53
We also performed the effect of humidity in the presence of CO2 gas at 200 ppm. Humidity inside the gas chamber was measured with the help of a hygrometer placed inside the gas chamber, and the humidity increased gradually from 20% to 80%, and their respective sensor response was recorded. Fig. 11 shows the sensing response curve of a porous glass film in the presence of relative humidity. Relative humidity present inside this gas chamber was controlled with the help of potassium sulfate (K2SO4) solution, which acts as a humidifier. Hence, we conclude that porous glass film shows a decrease in the sensing response when humidity increases. This decrease in sensing response might be due to the increased amount of water molecules in the synthesized sample when humidity is increased. A comparative study of CO2 gas at different concentrations with respect to previously reported literature is tabulated in Table 2.20,22–25,54–57
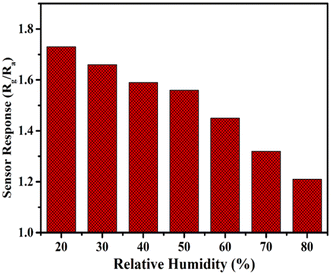 |
| Fig. 11 Relative humidity graph of CO2 gas sensor. | |
Table 2 Comparative study of CO2 gas sensor: materials, synthesis process, CO2 concentrations, operating temperature, response and recovery time, sensor response
Materials |
Synthesis process |
Concentration (ppm) |
Temperature (°C) |
Response time (s) |
Recovery time (s) |
Sensor response |
References |
Al2O3–V2O5 |
Co-precipitation |
600 |
673 |
— |
— |
1.00 |
20 |
Standard soda-lime glass |
— |
5000 |
350 |
— |
— |
0.43 |
22 |
MWCNT |
DLICVD* |
5000 |
30 |
30.2 |
49.6 |
2.1 |
23 |
Pure soda-lime glass |
— |
5000 |
350 |
— |
— |
1.379 |
24 |
MoO3−x thin film |
Thermal evaporation |
— |
200 |
∼180 |
∼180 |
2.826 |
25 |
Ag–BaTiO3–CuO |
Thin film deposition |
5000 |
250 |
900 |
600 |
1.28 |
54 |
Al/ZnO |
Screen printing |
1000 |
250 |
25 |
110 |
2.873 |
55 |
Random CNT |
CVD |
500 |
RT |
385 |
421 |
2.19 |
56 |
Aligned CNT |
CVD |
500 |
RT |
33 |
46 |
2.08 |
56 |
NdFeO3 |
Sol–gel |
1000 |
200 |
407 |
100 |
1.39 |
57 |
SHVP6 |
MQT |
200 |
RT |
12.2 |
15.3 |
1.83 |
Present work |
SHVP6 |
MQT |
1000 |
RT |
22.6 |
25.8 |
3.05 |
Present work |
Gas sensing mechanism
The gas sensing mechanism of metal oxides is explained by the adsorption/desorption surface phenomena. Usually, the electrical resistance increases or decreases depending on the nature of the material (n-type or p-type). Generally, the electrical resistance in n-type semiconductors increases after the interaction of oxidizing gases, whereas the resistance is the opposite for reducing gases. Since the CO2 gas is oxidizing in nature and it interacts with n-type materials, the resistance should increase. The oxygen present in air gets adsorbed on the surface of the porous glass film even before exposure to CO2 gas, and the trapped electrons from the conduction band (CB) result in the formation of oxygen species such as O−2, O−, and O2−, which depends upon temperature. The possible reactions can be explained as follows: |
O2(gas) + e−(CB) → O−2(ads) (>100 °C)
| (10) |
|
O−2(ads) + e−(CB) → 2O−(ads) (200–300 °C)
| (11) |
|
2O−(ads) + 2e−(CB) → 2O2−(ads) (<300 °C)
| (12) |
At room temperature, O−2 is formed at the surface of the sensing film and creates an electronic depletion layer, which eventually forms a region known as the depletion region and this depletion region acts as a potential barrier. When the resistance of the porous glass sensing film increases and reaches a saturation point, the adsorption resistance of the porous glass reaches a constant value. When the CO2 gas reacts with these oxygen species, due to the oxidizing nature of CO2, the electrons are transferred to CO2 molecules and form metastable (CO32−) complexes on the surface of the sensing film. The formation of (CO32−) complexes results in the reduction of the conductivity of the sensing film, which increases the depletion region. Hence, there is a sudden increase in the resistance, which depends upon the concentration of CO2. The possible reactions are as follows:
|
2CO2 + O2(ads)− + 3e− → 2CO3(ads)2−
| (13) |
|
2CO3(ads)2− → CO2 + 3e−
| (14) |
when the flow of CO
2 is turned off, the (CO
32−) complexes become CO
2 and the electrons are released from the sensing film, which comes back to its initial state. In the present work, we have observed an enhanced sensing response due to the unique porous morphology, which forms a reactive surface for CO
2 detection, and the mesopores present within this amorphous glassy composite provide a large surface area for CO
2 gas sensing
18.
Conclusion
In this study, a porous glass 40SiO2–35H3BO3–19V2O5–6P2O5 was prepared using the melt-quenching technique. X-ray diffraction confirmed the amorphous nature of the glass. SEM and TEM analysis confirmed that the synthesized glass has amorphous nature and revealed the presence of pores within the glassy matrix. BET analysis further confirmed that the pores generated within the fabricated glass are mesoporous, having a mean pore diameter of 7 nm. The porous structure of the glass sample tends to elevate the reactive surface, which increases the sensing response of the CO2 gas. The sensing response of the porous glass was found to be 3.05 at 1000 ppm of CO2 gas. Thus, we can say that the unique morphology of this glass provides good sensing ability and opens new ways to fabricate a better gas sensor using porous-amorphous materials with a relatively large surface area using an easy and low-cost fabrication process.
Author contributions
The manuscript was written with the joint contribution of ZF, CRG, and AS under the supervision of CRG. Synthesis, spectroscopic experiments, and sample analysis were performed by ZF and SKA. Sensing experiments were performed by AS and BCY, and the basic calculations were analyzed and calculated by ZF, AS, and AAK. The manuscript was reviewed and approved by all the authors. CRG and AS came up with the idea and topic of the manuscript.
Conflicts of interest
There are no conflicts to declare.
Acknowledgements
The authors are thankful to the Head, Department of Chemistry, University of Lucknow, for extending the FTIR facility and also to Prof. Atul Khanna for providing the Raman measurements at the Department of Physics, Guru Nana Dev University, Amritsar, Punjab India. The Manuscript communication number (IU/R & D/2022-MCN0001619) is allotted from Integral University, Lucknow.
Notes and references
- Z. Yunusa, M. N. Hamidon, A. Kaiser and Z. Awang, Sens. Trans., 2014, 168(4), 61–75 Search PubMed.
- N. Yamazoe, Sens. Actuators, B, 2005, 108, 2–14 CrossRef CAS.
- N. Yamazoe and K. Shimanoe, Sens. Actuators, B, 2009, 138, 100–107 CrossRef CAS.
- A. Singh, S. Sikarwar, A. Verma and B. C. Yadav, Sens. Actuators, A, 2021, 332, 11312 CrossRef.
- S. Deng, X. Liu, N. Chen, D. Deng, X. Xiao and Y. Wang, Sens. Actuators, B, 2016, 233, 615–623 CrossRef CAS.
- K. Arshak, E. Moore, G. M. Lyons, J. Harris and S. Clifford, Sens. Rev., 2004, 24(2), 181–198 CrossRef.
- Z. Fatima, C. R. Gautam, A. Singh, S. K. Avinashi, Shweta, B. C. Yadav and A. A. Khan, J. Mater. Sci.: Mater. Electron., 2022, 33, 1192–1210 CrossRef CAS.
- S. Dhall, B. R. Mehta, A. K. Tyagi and K. Sood, Sensors International, 2021, 2, 100116 CrossRef.
- P. Gouma, K. Kalyanasundaram, X. Yun, M. Stanácevi and L. Wang, IEEE Sens. J., 2010, 10(1), 49–53 CAS.
- R. Singh, A. K. Yadav and C. R. Gautam, J. Sens. Technol., 2011, 1(4), 116–124 CrossRef CAS.
- C. R. Gautam, D. Chakravarty, A. Gautam, C. S. Tiwary, C. F. Woellner, V. K. Mishra, N. Ahmad, S. Ozden, S. Jose, S. Biradar, R. Vajtai, R. Trivedi, D. S. Galvao and P. M. Ajayan, ACS Omega, 2018, 3, 6013–6021 CrossRef CAS PubMed.
- D. Enke, F. Janowski and W. Schwieger, Microporous Mesoporous Mater., 2003, 60, 19–30 CrossRef CAS.
- A. Markovi, D. Stoltenberg, D. Enke, E. U. Schlünder and A. Morgenstern, J. Membr. Sci., 2009, 336, 17–31 CrossRef.
- T. Tanaka, A. Guilleux, T. Ohyama, Y. Y. Maruo and T. Hayashi, Sens. Actuators, B, 1999, 56, 247–253 CrossRef CAS.
- L. D. Gelb and K. E. Gubbins, Langmuir, 1998, 14, 2097–2111 CrossRef CAS.
- L. Du, Y. Li, S. Li, H. Li, L. Li, Y. Cheng and H. Duan, J. Mater. Sci.: Mater. Electron., 2018, 29, 244–250 CrossRef CAS.
- L. Song, H. Yue, H. Li, L. Liu, Y. Li, L. Dua, H. Duan and N. I. Klyui, Chem. Phys. Lett., 2018, 699, 1–7 CrossRef CAS.
- N. Rajesh, J. C. Kannan, T. Krishnakumar, A. Bonavita, S. G. Leonardi and G. Neri, Ceram. Int., 2015, 41(10), 14766–14772 CrossRef CAS.
- K. V. Sopiha, J. H. Kim, S. S. Kim and P. Wu, Sens. Actuators, B, 2018, 266, 344–353 CrossRef CAS.
- U. Kumar and B. C. Yadav, J. Taiwan Inst. Chem. Eng., 2019, 96, 652–663 CrossRef CAS.
- J. Y. Kim, A. Mirzaei, J. H. Kim, J. H. Lee, H. W. Kim and S. S. Kim, Sens. Actuators, B, 2019, 296, 126673 CrossRef CAS.
- H. M. Ali, E. K. Shokr, Y. A. Taya, S. A. Elkot, M. F. Hasaneen and W. S. Mohamed, Sens. Actuators, A, 2022, 335, 113355 CrossRef CAS.
- Shweta, P. Dixit, A. Singh, S. K. Avinashi, B. C. Yadav and C. R. Gautam, J. Non-Cryst. Solids, 2022, 583, 121475 CrossRef CAS.
- M. El-Hezzat, A. Atbir, M. Abid, L. Montagn and F. Méar, Solid State Sci., 2021, 118, 106666 CrossRef CAS.
- T. Ishihara, K. Shiokawa, K. Eguchi and H. Arai, Sens. Actuators, 1989, 19, 259–265 CrossRef CAS.
- Z. Fatima, A. Hussain, C. R. Gautam, Shweta, P. Singh, A. Ahmed, G. Singh and M. K. Singh, J. Asian Ceram. Soc., 2020, 8, 1108–1126 CrossRef.
- A. Singh and B. C. Yadav, Surf. Interfaces, 2022, 34, 102368 CrossRef CAS.
- C. R. Gautam, C. S. Tiwary, S. Jose, G. Brunetto, S. Ozden, S. Vinod, P. Raghavan, S. K. Biradar, D. S. Galvao and P. M. Ajayan, ACS Nano, 2015, 22, 12088–12095 CrossRef PubMed.
- D. E. V. Valerdi, J. A. L. López, J. C. López, G. G. Salgado, A. B. Lara and N. D. E. Torres, Nanoscale Res. Lett., 2014, 9, 422 CrossRef PubMed.
- I. Asif, S. Ali, S. Shahzadi and S. Mahmood, J. Chin. Chem. Soc., 2007, 54, 23–30 CrossRef CAS.
- M. Th. P. Ledent and P. Tarte, Spectrochim. Acta, Part A, 1973, 29, 1007–1016 CrossRef.
- X. Li, A. Lu and H. Yang, J. Non-Cryst. Solids, 2014, 389, 21–27 CrossRef CAS.
- M. Uğurlu, Microporous Mesoporous Mater., 2009, 119, 276–283 CrossRef.
- W. Wang, H. Li, Y. Guo, Q. Sun and C. Chen, J. Adv. Ceram., 2012, 1, 283–289 CrossRef CAS.
- C. R. Gautam and A. K. Yadav, Opt. Photonics J., 2013, 3, 1–7 CrossRef.
- M. A. Butturi, M. C. Carotta, G. Martinelli, L. Passari, G. M. Youssef, A. Chiorino and G. Ghiotti, Solid State Commun., 1997, 101, 11–16 CrossRef CAS.
- C. R. Gautam, A. K. Yadav and A. K. Singh, ISRN Ceram., 2012, 2012, 428497 Search PubMed.
- C. Marcolli and G. Calzaferri, J. Phys. Chem. B, 1997, 101, 4925–4933 CrossRef CAS.
- C. Ivascu, A. T. Gabor, O. Cozar, L. Daraban and I. Ardelean, J. Mol. Struct., 2011, 993, 249–253 CrossRef CAS.
- E. V. Jelenkovic, K. Y. Tong, Z. Sun, C. L. Mak and W. Y. Cheung, J. Vac. Sci. Technol., A, 1997, 15, 2836 CrossRef CAS.
- P. Y. Shih, S. W. Yung and T. S. Chin, J. Non-Cryst. Solids, 1998, 224, 143–152 CrossRef CAS.
- A. K. Yadav and P. Singh, RSC Adv., 2015, 5, 67583–67609 RSC.
- C. Wang, G. Deo and I. E. Wachs, J. Catal., 1998, 178, 640–648 CrossRef CAS.
- C. Andronache, Mod. Phys. Lett. B, 2010, 24, 2007–2014 CrossRef CAS.
- C. D. Blasi, C. Branca and A. Galgano, Polym. Degrad. Stab., 2007, 92, 752–764 CrossRef.
- X. Wu, R. Su, Y. Zhu and Z. Huang, RSC Adv., 2019, 9, 4203 RSC.
- Y. Shen, J. C. Jiang, P. Zeman, V. Šímová, J. Vlček and E. I. Meletis, Sci. Rep., 2019, 9, 3603 CrossRef CAS PubMed.
- J. Paillier, C. Mickel, P. F. Gostin and A. Gebert, Mater. Charact., 2010, 61, 1000–1008 CrossRef CAS.
- M. Naderi, Progress in Filtration and Separation, Academic Press, 2015, pp. 585–608 Search PubMed.
- C. Sriwong, C. Phrompet, W. Tuichai, A. Karaphun, K. Kurosaki and C. Ruttanapun, Sci. Rep., 2020, 10, 11077 CrossRef CAS PubMed.
- S. Kwon, H. Hwang and Y. Lee, Crystals, 2019, 9(10), 528 CrossRef CAS.
- A. Singh, S. Sikarwar and B. C. Yadav, Mater. Res. Express, 2021, 8, 045013 CrossRef CAS.
- H. Zhang, J. Feng, L. Li, Y. Jiang and J. Feng, RSC Adv., 2019, 9, 5967 RSC.
- J. Herrán, G. G. Mandayo, I. Ayerdi and E. Castãno, Sens. Actuators, B, 2008, 129, 386–390 CrossRef.
- A. Patil, C. Dighavkar and R. Borse, J. Optoelectron., 2011, 13, 1331–1337 CAS.
- Y. Wang, K. Zhang, J. Zou, X. Wang, L. Sun, T. Wang and Q. Zhang, Carbon, 2017, 117, 263–270 CrossRef CAS.
- Y. Chen, D. Wang, H. Qin, H. Zhang, Z. Zhang, G. Zhou, C. Gao and J. Hu, J. Rare Earths, 2019, 37, 80–87 CrossRef CAS.
|
This journal is © The Royal Society of Chemistry 2022 |
Click here to see how this site uses Cookies. View our privacy policy here.