DOI:
10.1039/D2RA03364J
(Paper)
RSC Adv., 2022,
12, 20886-20896
Comparative evaluation of thermal and emission performances for improved commercial coal-fired stoves in China
Received
30th May 2022
, Accepted 16th June 2022
First published on 20th July 2022
Abstract
The extensive use of traditional cooking stoves to meet daily cooking and heating requirements has highlighted the serious problem of indoor and outdoor air pollution. This study evaluates seven improved coal-fired space-heating and cooking stoves and compares them with a widely used stove of an older design, selected as a baseline reference. The seven stoves were selected from a range of candidate improved stoves submitted by manufacturers for testing as part of the air quality improvement in the Hebei Clean Air Project, Hebei Province, China. Stove performance was evaluated when burning raw coal and coal briquettes during the high and low power stages respectively. All seven improved cooking stoves surpassed the baseline stove in combined heating and cooking thermal and emission performance. Among the improved cooking stoves, Model 2-TL was found to have the highest average thermal efficiency, 87.2 ± 0.5%, when burning coal briquettes at high and low power. The lowest emission of PM2.5 was 0.94 ± 0.5 mg MJNET−1, CO 0.55 ± 0.28 g MJNET−1, and CO/CO2 1.1 ± 0.6%, respectively. It is concluded that the use of these improved heating and cooking stoves should be promoted for daily cooking and heating requirements. This strategy will not only save fuel to the benefit of the household, but widespread adoption could contribute to significant reductions of CO and PM2.5 emissions in Hebei Province.
1 Introduction
Nearly three billion individuals in developing nations depend on solid fuels, particularly biomass, for their cooking, heating, and even lighting necessities.1,2 More than 80% of China's population lives in rural areas, and 95% of them use coal, wood and other biomass for cooking and heating.3–5 Though household heating with biomass and coal is common in northern China, the contribution of space heating stoves to ambient air pollution has not been well studied.6
The extensive use of and dependence on conventional cooking stoves is the prime reason for the perilous quality of indoor air.7,8 Indoor air pollution (IAP) is a complex mixture of solid particles, liquid droplets and gases which, when inhaled, causes or exacerbates respiratory ailments.9,10 IAP has been attributed to be a factor in 3 to 7 million premature deaths annually, with the attribution of cardiorespiratory illness being a major factor.11–13 Studies have demonstrated that lung cancer could in large part be related to the burning of solid fuels in poorly ventilated homes for space heating and cooking14,15 The products of incomplete combustion of fuel in traditional stoves have more global warming potential than carbon-dioxide.16,17 Due to inefficient traditional stoves and low-quality fuel, a high level of smoke is produced as a result of incomplete combustion.18,19 Depending on the fuel composition, there is the possibility of releasing flue gases with a high concentration of SOx (sulfur oxides) and NOx (nitrogen oxides) due to the impracticality of adding desulphurization and denitrification equipment to a domestic stove. The adoption of improved cooking stoves in rural households can reduce black carbon (BC) by 47%.20 In Hebei Province of China, air contamination in the southern urban areas is significantly worse than in the north. Particulate matter (PM) is the most noteworthy air pollutant, with SO2 and NOx also being significant.21 Coal-fired industrial and residential boiler emissions are the key drivers of air pollution control measures being implemented in the Beijing, Tianjin and Hebei Province (BTH) region. China plans to replace most residential coal stoves in northern China with clean heating devices by 2021 in response to severe air pollution. The replacement of coal stoves began in the BTH region and is spreading throughout northern China. It is beneficial for both air quality and public health to remove coal stoves, as well as reducing greenhouse gas emissions.22 Emissions of SO2, PM, PM10 (coarse PM with aerodynamic diameter ≤ 10 μm), and PM2.5 (fine PM with aerodynamic diameter ≤ 2.5 μm) from coal-fired residential and industrial boilers in 2012 were respectively, 9 × 105 tons, 3 × 105 tons, 3 × 105 tons, 1 × 105 tons and 0.8 × 105 tons.23
Coal has been the most significant energy source of China, and in the near future it will be a prime energy source in other developing nations. However, its improper utilization is closely related to serious concerns about air pollution.24,25 At present, improperly combusted coal is the primary contributor to air pollution appearing in the form of a heavy smog in numerous urban areas, often called a “haze”.26,27 Haze remediation measures have included the adoption of district heating systems and conversion of residential biomass stoves to liquefied petroleum gas (LPG).28
The incomplete combustion of biomass has also been a source of indoor pollution.29–32 The pollution created by burning biomass badly in traditional stoves includes carbon monoxide, PM2.5 and black carbon.33 These health and environmental challenges can be reduced by using modern, efficient stoves with greatly reduced emission factors.34,35 In the rural regions of developing nations, the general population appreciates “low-quality” inexpensive coal to meet their everyday cooking and warming requirements because of cost.36,37
This paper reports the results of an investigation into the performance of seven modern commercial coal stoves and compares their performance with an older baseline stove. This information could be useful as evidence-based policy support for planning the air quality management. This was done using an online (real-time) stove performance testing system. The measured data were used to calculate the total pollutant mass discharged using a test method used previously to assess the performance of clean stoves in China and abroad. Seven commercially available stoves were compared to the baseline model while burning two fuels: semi-coked coal briquettes and Shenmu raw coal. All these stoves were coal-fired low-pressure boilers (LPB) with integrated cooking and water heating suited to the requirements of rural households in Hebei Province, China.
2 Materials and methods
A clean stove promotion project has been undertaken as part of the Hebei Clean Air Project. An assessment of the performance of candidate stoves was carried out at the Biomass Stove Testing Laboratory at China Agricultural University. Seven commercial improved stoves were anonymized with the labels 1-TL, 2-TL, 3-TL, 4-TL, 5-TL, 6-FL, 7-FL and the “Baseline” stove (Table 1). They were tested using raw coal with an average size of 40–60 mm and semi-coked coal briquettes with an average size of 50 mm. Their thermal efficiency and emissions were assessed. The baseline stove had been in continuous use for about ten years. The baseline data were used to characterize current household heating requirements. During these tests, measurements were recorded every 10 seconds and stored on a computer for analysis.
Table 1 Details and identification of stoves used in the study
Stove ID number |
Identification |
Type |
Base |
Baseline stove |
Top loading, handmade, more than ten years old, no secondary air supply hole for low power running, one burner |
1-TL (top load) |
Small orange |
Top loading, commercial ICS, one burner, primary air supply for high and low power |
2-TL (top load) |
Light orange grey |
Top loading, commercial ICS, one burner, primary and secondary air supply for high and low power |
3-TL (top load) |
Blue with two pots |
Top loading commercial ICS, two burners, primary and secondary air supply for high and low power |
4-TL (top load) |
Big orange |
Top loading commercial ICS, one burner, primary air hole in ash removal door and secondary air on the upper side of the ash chamber supply for high and low power |
5-TL (top load) |
Big green |
Top loading commercial ICS, one burner, primary air hole in ash removal door and secondary air supply with the external holes in the combustion chamber for high and low power |
6-FL (front load) |
Grey |
Front loading commercial ICS, one burner, primary air hole in ash removal door for high and low power |
7-FL (front load) |
Small green |
Front loading commercial ICS, one burner, primary air supply hole for high and low power in ash removal door |
A gas analyzer (MRU MGA5/Vario Plus, Germany) was used to measure the concentrations of gases taken directly from the flue. A non-dispersive infrared (NDIR) sensor was used for measuring the concentration of CO2 gas in ppm, the rest (O2, CO, NOx, SO2) using electrochemical cells. The temperatures measured with K-type thermocouples are logged every one second. An ultrasonic flowmeter was used to measure the heating water flow rate through the heat exchanger in litres per second. The particulate matter was measured by a DustTrak DRX aerosol monitor (Model 8533) (mg m−3). The DustTrak has internal zero calibration and simultaneously reports PM1, PM2.5, PM4 and PM10. The stove was set on an electronic mass balance and all instrument functions were checked in advance. The stove testing system is shown in Fig. 1. The fire was ignited with pre-weighed paper and wood and small pieces of coal. The experiment included a total of 48 tests: triple replications were made for each of 16 stove–fuel combinations.
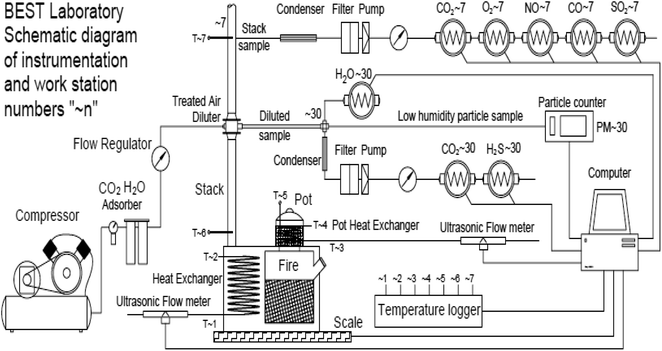 |
| Fig. 1 Schematic diagram of the online testing system with work station ∼numbers (the H2O is a RH sensor. The ∼30 and ∼7 etc. are work stations numbers as indicated on the drawing). | |
2.1 Fuel preparation
Two fuels were used: semi-coked briquettes and raw coal. The briquettes are claimed to be a “low smoke fuel”. The raw coal was broken into smaller pieces approximately 40–60 mm by hammering to mimic typical user behavior. In the countryside, fuel markets typically sell oviform and oblate spheroidal coal briquettes with a diameter of ≈50 mm and raw coal ranging from 40 to 60 mm across. The replacement of “low-grade” coal with either semi-coked coal or biomass briquettes is claimed to be an effective method for mitigating SO2 emissions.38
The calorific value, moisture content, volatile matter fraction and elemental composition were analyzed by Northern China Electric Power University using the methods in the relevant Chinese national and industrial standards: Agricultural Standard of the People's Republic of China (NY/T 1881.1-2010) National Standard of the People's Republic of China (GB/T 28731-2012) – (GB/T 28734-2012).
2.2 Stove testing and test procedure
The laboratory at the China Agricultural University has equipment to dilute and dehydrate the sample of products of incomplete combustion prior to measurement across a wide range of concentrations. The dilution ratio can be varied from 3
:
1 to 100
:
1 as required, to keep the concentration within the operating limits of the DustTrak DRX aerosol monitor (0.001–150 mg m−3) (Fig. 1). After ignition, the dilution remains constant during each test to avoid errors. The variable dilution system overcomes the limitation of fixed dilution systems in that the systematic “error” is overcome through the use of a dilution and humidity monitoring apparatus that simultaneously overcomes the problems created by fixed dilution systems and variable stack humidity. The instrument was calibrated in the fashion described. That calibration is maintained by the correct use of the variable dilution system. The flue gases are diluted by air containing nearly no CO, CO2 or water vapor (dew point < −60 °C). The use of this specially prepared dilutant preserves the calibrated accuracy of the optical measurement system even if the humidity of the source particles varies widely. The humidity is controlled (by adjusting the dilution if necessary) in a typical range of 15–30%. The dilution rate is calculated per 10 seconds by comparing the concentration of CO2 before and after dilution, factoring for ambient CO2. Diluted and undiluted flue gases and diluted particle measurements are recorded using a data acquisition system. Of the more than 120 approved models commonly available in Hebei Province, 8 were selected; one being the baseline product as shown in Fig. 2.
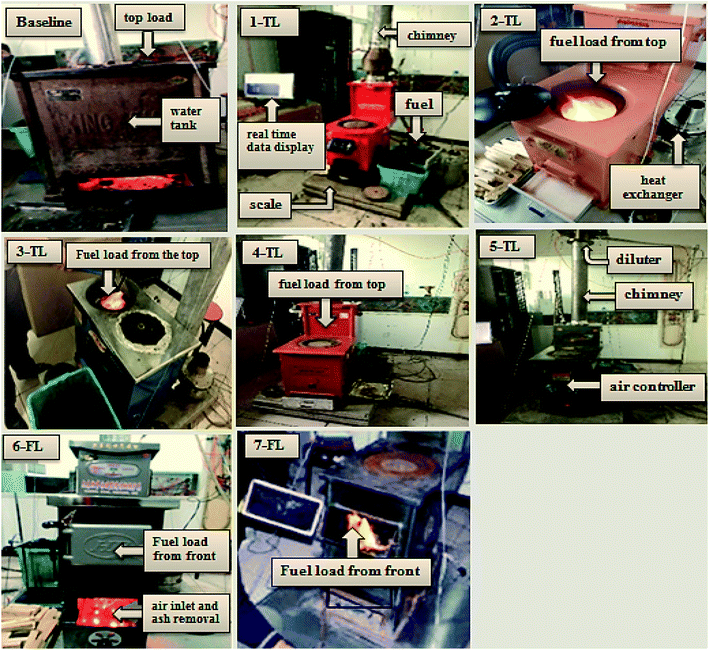 |
| Fig. 2 Stoves used in the current study with different feeding method and design. | |
Instrument measurements were recorded every 10 seconds and included: mass change of the system, inlet and outlet water temperature in the space heating heat exchanger and the cooking pot heat exchanger, the flow rate of the coolant in each, the temperature of the uncirculated water in the cooking vessel, PM and trace gas emissions, ambient and diluted gas humidity, numerous other temperatures and the ambient air pressure. During the high power test, the flow of coolant through the space heating heat exchanger was adjusted for high and low power to maintain an output temperature of approximately 50 ± 20 °C. Without monitoring this variable, the cooling water might boil at high power which does not happen in typical use. On the other hand, having a low ΔT (change in temperature) on the heat exchanger reduces the accuracy of calculated results. The concentrations of trace gases H2, SO2, NO, CO, CO2, O2 were measured directly from flue while in the diluter measurements included CO2, H2O, H2S. The calculated outputs include the heating and cooking efficiency, emission rates and the combined cooking and heating efficiency were performed according to Beijing Municipal Standard (DB11/T 540-2008). The fire was set according to the manufacturer's instructions.
2.3 Calculations
An adequate quantity of fuel sufficient for the entire experiment was estimated using the following formula: |
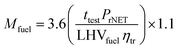 | (1) |
where: Mfuel is the mass of the fuel set aside [kg]; 3.6 converts J s−1 to kJ h−1; ttest is the testing duration [h]; PrNET is rated heating power [kWNET]; LHVfuel is Lower Heating Value of the fuel as received (AR) [MJ kg−1]; ηtr is the rated high power thermal efficiency [%]; the factor of 1.1 is due to the 10% safety margin so as not to run out before the test ends.
If the rated thermal efficiency was not available, but the stove had passed the Beijing Municipal Standard (DB11/T 540-2008), a default thermal efficiency value of 60% was assumed based on the fact that the stove had been allowed to enter the market.
The stoves performance parameters were calculated using the equations listed below.
Q1, the heat gained by the space heating heat exchanger was calculated using eqn (2).
|
 | (2) |
|
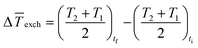 | (3) |
where
Cp,w is the specific heat capacity of water [J g
−1];
T1 is the heat exchanger inlet temperature [°C];
T2 is the heat exchanger outlet temperature [°C];
mexch is the mass of the heat exchanger [g];
mw,exch is the mass of the water in the heat exchanger [g];

is the change in average temperature of the water in the heat exchanger [°C]. The rated heating power (
PrNET) was calculated using the
eqn (4):
|
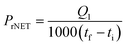 | (4) |
where
tf and
ti are final and initial time [s], respectively.
The heat gained by the cooking pot (Q2) and its uncirculated contents are calculated using the eqn (5) as follows:
|
ΔT5 = (T5)tn+1 − (T5)tn
| (6) |
where Δ
T5 is change in temperature of the cooking pot and its uncirculated contents, the term (
n + 1) −
n is the measurement interval of 10 seconds.
The heat gained (Q3) by the coolant flowing through the cooking pot heat exchanger (tube), the heat exchanger tube, and the coolant contained within that tube is calculated by eqn (7).
|
 | (7) |
|
 | (8) |
where

is the change in the average temperature of the tube and the coolant contained in the tube. The total heat gained (
Q4) by the cooking system during the test period was calculated using (
eqn (9)) as follows:
|
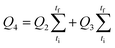 | (9) |
The total useful heat (Qt) delivered is the sum of the space heating and cooking energy is given in MJ by eqn (10) as follows:
|
 | (10) |
The total chemical energy (Ut) available from the fuel fed into the stove during the test in given in MJ by eqn (11) as follows:
|
Ut = BQnet,var + B0Qnet,var1
| (11) |
where
B is the mass of fuel fed [kg];
Qnet,var is the LHV of the fuel as received [MJ kg
−1];
B0 is the mass of kindling material [kg];
Qnet,var1 is the LHV of the kindling materials as received [MJ kg
−1].
The percentage of useful heat delivered by the stove Qt divided by the total heat available from the fuel fed Ut, indicates the fraction of energy utilization. Before starting the test, the pre-weighed fuel was placed in a container on a platform that was larger than the stove to adequately limit such possible drying. The space between the stove and the fuel was about 15 cm, which didn't affect moisture and prevented the fuel from drying out during use. The test continued for 16 hours from ignition to the end, and the cooking phase was started three hours after ignition. The time was noted before and after the cooking phase in order to separately calculate the cooking efficiency. The change in mass was determined from the scale data which enables the determination of the fuel mass consumed during each of multiple space heating and cooking phases. The thermal efficiency (ηc) of cooking was calculated as a percentage using eqn (12). The space heating efficiency (ηh) was calculated as a percentage using eqn (13). The overall system efficiency (ηt) for cooking and heating was calculated using eqn (14).
|
 | (12) |
|
 | (13) |
|
 | (14) |
The PM2.5 emission factor (EFPM2.5) was calculated in mg MJNET−1 using eqn (15).
|
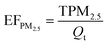 | (15) |
where TPM
2.5 is the total mass of PM emitted [mg] which is calculated using (
eqn (16));
Qt is the total useful heat energy (
eqn (10)) [MJ].
|
TPM2.5 = PM2.5DrVdil∼1
| (16) |
where TPM
2.5 is the total mass of PM
2.5 reported during the sampling interval [mg];
Dr is the dilution ratio between the stack sample and the diluter sample and is estimated using
eqn (17).
Vdil∼1 is the volume of emissions in the stack [m
3], including excess air, created by the mass of fuel burned as given by
eqn (18).
|
 | (17) |
|
Vdil∼1 = VstoΔmfuelλ
| (18) |
where Δ
mfuel is the change in mass of fuel fed [kg];
Vsto is the stoichiometric volume gases produced by the combustion of 1 kg of fuel (AR) [m
3];
λ is the total air demand factor providing both used and unused oxygen. The CO emission factor was calculated using
eqn (19) |
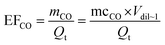 | (19) |
where
mCO is the mass of CO emitted during the sampling interval [g]; mc
CO is the mass concentration of CO [g m
−3]. The

is converted into CO
ppm(v) using
eqn (20) |
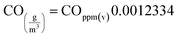 | (20) |
where 0.0012334 is the conversion factor.
The fuel saving was calculated using (eqn (21)).
|
Fuel savings = [1 − (base efficiency/improved efficiency)] ×100
| (21) |
2.4 Apparatus
A catalogue of test indicators, instruments and testing principles is given in Table 2. In order to evaluate the performance of the stoves, sixteen hour tests were first conducted combining China's relevant standard methods with observed local behaviors. The test sequence comprises various stages informed by observing the cooking and heating behavior of rural consumers in Hebei Province, China. The details of this protocol are provided in Table 3.
Table 2 Description of test indicators, equipments and testing principlea
Test indicators |
Unit |
Equipment |
Precision |
Measuring range |
Test principle |
Note: NDIR = non-dispersive infra-red; MV = measured value; FS = full scale reading; EC = electrochemical. |
Fuel mass loss |
g |
Straw FCN-V10 |
±0.1% |
30–600 kg |
Double beam sensor electronic scale |
Flue gas (O2, CO2, CO, NOx, SO2) concentration |
ppm |
MRU Vario Plus |
±0.1% |
O2, CO2, CO, NOx, SO2 = 0–10 000 vol% EC |
CO2 used NDIR, others use EC sensors |
CO2 = 0–30% (NDIR) |
Particulate matter |
mg m−3 |
DustTrak DRX Aerosol Monitor 8533 Desktop |
±0.1% of reading of 0.001 mg m−3, whichever is greater |
0.001–150 mg m−3 |
Light scattering; simultaneously reporting size-segregated mass fraction concentrations corresponding to PM1.0, PM2.5, respirable, PM10 and total PM |
Analysis of flue gas concentration of diluents: CO2, H2O, H2S |
ppm |
DP00112/DP00118 |
±2% FS |
0–30 000 ppm |
CO2 using NDIR, H2S using EC sensors, H2O using a humidity sensor |
TESTO 6681+6614 |
Determination of water flow |
ml s−1 |
TUF-2000P |
±1% |
0 ± 10 m s−1 |
Ultrasonic flow measurement |
Temperature |
°C |
Thermocouple |
±0.2 °C |
−270 to 1260 °C |
Thermocouple thermo electromotive force |
Table 3 Description of >16 hour test including ignition and end stages
Testing stage |
Duration (h) |
Purpose |
Reason |
Ignition and adjustments |
Depends on the ignition |
Start the ignition and adjust the stove accurately |
The test begins with ignition of the fuel and with a burning period of approximately 30 minutes while the stove is adjusted for best performance. Because the stove is kept burning over the entire heating season, ignition occurs only once, hence the ignition phase and the fuel burnout phase are not included when comparing and evaluating stoves in this context |
High power |
2 |
Cooking breakfast |
The purpose of the high power after ignition is to make breakfast within two hours and also for space heating |
Low power |
10 |
Space heating |
The fully loaded stove is run at low power for 10 hours for space heating. Stove power is adjusted by controlling the inlet air |
Cooking and heating at high power |
1 |
Cooking dinner |
After 10 h low power, the stove was run at high power for evening cooking purposes for one hour duration |
High power |
3 |
Space heating |
After cooking the stove is operated on high power for three hours to warm the room for comfortable sleep for the household |
End stage |
Depends on the fuel burning |
Test end |
Ending process depends on the fuel burned completely after the three hour high power phase |
3 Results and discussion
3.1 Analyses of the fuels
Both fuels were analysed for their elemental composition, moisture content, volatile matter fraction and higher heating value (HHV) (Table 4). The moisture content of raw coal was higher than that of semi-coked briquettes. The volatiles content of the semi-coked coal briquettes was low. The nitrogen content of the briquette was higher than that of the raw coal.
Table 4 Industrial analysis and elemental analysis of fuela
Content |
Raw coal |
Briquette coal |
Note: ar = as received; M = moisture content; A = ash content; V = volatile matter content; FC = fixed carbon content; C = carbon content; H = hydrogen content; N = nitrogen content; Qnet = lower calorific value; S = sulfur content; O = oxygen content. |
Mar/% |
9.04 |
3.5 |
Aar/% |
5.7 |
15.7 |
Var/% |
27.14 |
10.2 |
FCar/% |
58.14 |
70.6 |
Qnet,ar/MJ kg−1 |
17.41 |
25.89 |
Car/% |
67.5 |
60.3 |
Har/% |
4.5 |
4.1 |
Nar/% |
0.9 |
0.84 |
Sar/% |
0.4 |
0.33 |
Oar/% |
20.4 |
18.2 |
3.2 Thermal performance
The test results show that for each fuel-stove-use pattern, all stoves except the baseline and 5-TL met the thermal efficiency requirement (≥60%) of the relevant standard (DB11/T 540-2008). The thermal and emissions performance indicators are presented in Table 5 according to the relevant standard (DB11/T 540-2008). The thermal efficiencies for all eight stoves are presented in Fig. 3. The results show that the new, project-approved stoves had much higher thermal efficiencies than the baseline stove. The thermal efficiency of the baseline stove was poor, even though sometimes it had good combustion efficiency. The failure to perform is due to the low heat exchange surface area per rated kW compared with the new stoves. The average baseline stove efficiency was 48.8 ± 1.4% burning coal briquettes and 38.5 ± 2.8% burning raw coal. The average fuel savings, calculated using eqn (21) for each stove and then averaged, was 44%. Stove 2-TL was found to be the most efficient (87.2 ± 0.5%) burning briquettes and 62.9 ± 0.6% burning raw coal. The least efficient stove was the 5-TL with an average thermal efficiency of 61.2 ± 3.2% and 52.6 ± 4.2% burning coal briquettes and raw coal respectively. Despite these low values, stove 5-TL will still save 1/3rd of the fuel compared with the baseline stove. Previously, mixed results have been reported with some authors finding no significant differences between some stoves and fuel types.8
Table 5 Thermal and emissions performance indicators according to the Chinese testing method (Beijing Municipal Standard, DB11/T 540-2008)
|
Unqualified |
Qualified |
Exceeding requirement |
Thermal performance |
Cooking power (kW) |
Pc < 11.3 |
Pc ≥ 11.3–50 |
Pc ≤ 50 |
Thermal efficiency (%) |
ηc ≥ 60 |
ηc ≥ 60–65 |
ηc ≥ 65 |
![[thin space (1/6-em)]](https://www.rsc.org/images/entities/char_2009.gif) |
Emission performance |
Smoke mass concentration (mg m−3) |
<10 |
10–30 |
<30 |
NOx (mg m−3) |
<150 |
150–150 |
<150 |
CO (%) |
<0.2 |
0.2–2.0 |
<2.0 |
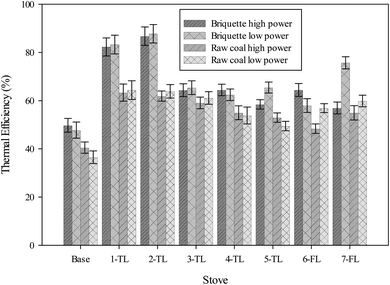 |
| Fig. 3 Thermal efficiency of various stoves using briquettes and raw coal. The error bars indicate the standard deviation (±SD) of three replications. | |
3.3 Emission measurement
3.3.1 Particular matter (PM2.5). The emission performance results (Fig. 4) show that the average (for high and low power) PM2.5emitted from the baseline stove was 9.4 ± 0.4 mg MJNET−1 burning raw coal while burning semi-coked briquettes it was 2.5 ± 0.4 mg MJNET−1. Stove 2-TL was better for raw coal: 1.1 ± 0.6 mg MJNET−1 but significantly worse for burning briquettes: 5.2 ± 0.6 mg MJNET−1. All the improved stoves produced less PM2.5 than the baseline model with stove 6-FL emitting the least: 1.0 ± 0.7 mg MJNET−1 while burning briquettes followed by 4-TL at 1.6 ± 0.6 mg MJNET−1 and 3-TL at 1.1 ± 0.3 mg MJNET−1.
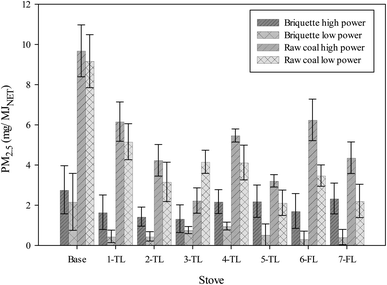 |
| Fig. 4 PM2.5 emission performance of improved stove in comparison to baseline. | |
The average PM2.5 emissions when burning raw coal for the other stoves were 3-TL: 3.2 ± 1.0, 1-TL: 5.2 ± 0.6, 5-TL: 2.7 ± 0.5 and 6-TL: 6.5 ± 0.3 mg MJNET−1. Li et al.39 reported that in China, the average emission of PM2.5 declined some 92% when semi-coke briquettes were used as fuel in traditional stoves. This study shows that a 40 ± 1.1% reduction can be achieved by replacing the baseline stove with a Model 2-TL while continuing to burn raw coal. A similar variation in combustion quality between high and low power has been reported for the same types of fuel.40
3.3.2 CO/CO2 ratio. The lower the CO/CO2 ratio, the more complete the combustion of carbon. The CO/CO2 ratios during high power for the baseline and 5-TL stoves burning coal briquettes (Fig. 5) were almost equivalent: 7.4 ± 0.7% versus 7.1 ± 0.8%, respectively. The stove 2-TL, the best performing stove on this metric, scored a CO/CO2 ratio of 1.1 ± 0.3%, burning coal briquettes and 1.4 ± 0.4% burning raw coal. The average CO/CO2 ratios for stoves burning raw coal were all higher than when burning briquettes: 1-TL: 3.1 ± 0.5%, 3-TL: 3.5 ± 0.5%, 4-TL: 3.7 ± 1.1%, and 5-TL: 6.4 ± 0.5%. Burning briquettes, the scores were, 1-TL: 3.1 ± 0.5%, 3-TL: 3.5 ± 0.5%, 4-TL: 3.7 ± 1.1%, and 5-TL: 6.4 ± 0.5%. Stoves 6-FL and 7-FL had better performance than the baseline stove during high power operation (2.3 ± 0.6% and 1.6 ± 0.3%, respectively), but were worse (3.7 ± 0.6% and 3.7 ± 1.1%, respectively) when operated at low power. Interestingly, these two stoves were also superior to all the others when burning raw coal during both high and low power operation. It is observed that all stoves operating at high power had relatively good CO/CO2 ratios but the combustion quality deteriorated as the burn rate and combustion temperatures decreased. A similar variation in coal combustion quality between high and low power has been reported by reference 41 and for other types of fuel like wood or kerosene42 and the inverse for ethanol gel.43
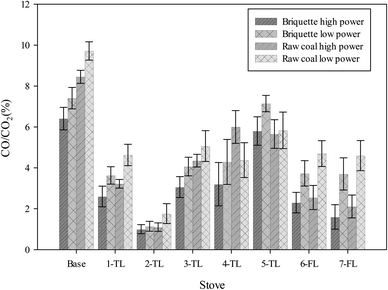 |
| Fig. 5 CO/CO2 ratio of the improved stove in comparison to the baseline stove with briquettes and raw coal during high power and low power. | |
3.3.3 CO emission factor. Fig. 6 shows that the CO emission factors for all improved stoves are lower than the baseline value. The maximum values (8 ± 0.6 and 7.1 ± 0.6 g MJNET−1) were obtained during high and low power operation when burning raw coal in the baseline stove. The minimum emission factors (1.66 ± 0.44 and 0.55 ± 0.28 g MJNET−1) during low and high power operation, respectively, were achieved by stove 2-TL. Overall, the stoves performed better than the baseline product when burning briquettes. Even the baseline stove gave lower emissions burning briquettes at low and high power than for raw coal. In an earlier study,44 the CO concentration of 0.07 mg m−3 when burning “clean” briquettes was significantly lower than when burning the raw coal 4.25 mg m−3, though we hasten to add that the testing methodology was different. In another study,45 the CO emission factor was reported to be between 1200 and 3200 mg MJ−1 (fuel) for wood stoves and between 92 and 270 mg MJ−1 (fuel) for pellet stoves, again using a different method. Similar findings with a little variation have been reported in a previous study conducted in the BTH region by Cui et al.46 Together, these studies indicate that more modern stoves have better combustion quality.
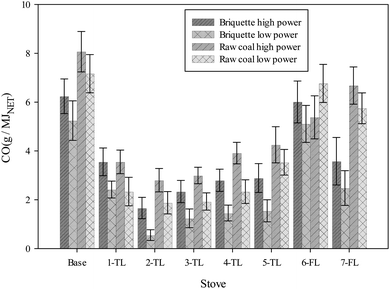 |
| Fig. 6 Emission factors of CO from the improved stoves using briquettes and raw coal in comparison to the baseline stove. | |
3.4 Overall performance
The overall thermal efficiency improvement, fuel saving and emission reduction performance comparison (Table 6) shows that the maximum thermal improvement and fuel saving 44 ± 1.1% and 78.6 ± 0.3% was obtained for the 2-TL stove with coal briquette, the maximum reduction in emissions of PM2.5 63.0 ± 1.9% and CO 42.2 ± 0.4% with briquette coal was also achieved for this model. It was found that the firepower of stove 2-TL varied significantly with fuel type (86.7 ± 0.8% high power with coal briquettes and 61.9 ± 1.1% high power with raw coal). This demonstrates that the context of use – stove + fuel + operating sequence – strongly affects the performance.
Table 6 Thermal improvement and estimated reduction in emission of various stovesa
Stoves |
Thermal efficiency (%) |
Thermal improvement (%) |
Fuel saving (%) |
PM2.5 (mg MJNET−1) |
Est. PM2.5 reduction (%) |
CO (g MJNET−1) |
Est. CO reduction (%) |
Briq. coal |
Raw coal |
Briq. coal |
Raw coal |
Briq. coal |
Raw coal |
Briq. coal |
Raw coal |
Briq. coal |
Raw coal |
Briq. coal |
Raw coal |
Briq. coal |
Raw coal |
Note: Thermal and emissions performance indicators are shown in Table 5. Est. = estimated. |
Baseline |
48.8 ± 1.4 |
38.5 ± 2.8 |
— |
— |
— |
— |
2.5 ± 0.4 |
9.7 ± 1.3 |
— |
— |
5.7 ± 1.2 |
7.6 ± 1.3 |
— |
— |
1-TL |
82.8 ± 0.5 |
64.4 ± 0.6 |
69.6 ± 0.4 |
66.2 ± 0.2 |
41.0 ± 1.2 |
40.0 ± 1.9 |
1.0 ± 0.6 |
6.2 ± 1.1 |
58 ± 1.4 |
37.4 ± 0.8 |
3.5 ± 0.8 |
5.6 ± 0.9 |
38.6 ± 0.7 |
24.4 ± 0.7 |
2-TL |
87.2 ± 0.5 |
62.9 ± 1.0 |
78.6 ± 0.3 |
63.2 ± 0.4 |
44.0 ± 1.1 |
38.7 ± 1.6 |
0.9 ± 0.5 |
5.1 ± 0.9 |
63 ± 1.9 |
47.5 ± 0.7 |
3.3 ± 0.5 |
4.8 ± 0.7 |
42.2 ± 0.4 |
36.9 ± 0.4 |
3-TL |
64.8 ± 0.5 |
60.1 ± 1 |
67 ± 0.3 |
55.0 ± 0.4 |
24.7 ± 1.8 |
35.9 ± 1.9 |
1.1 ± 0.3 |
6.5 ± 1.2 |
56 ± 0.7 |
33 ± 0.9 |
4.1 ± 1.1 |
5.3 ± 0.8 |
28 ± 0.9 |
30.3 ± 0.6 |
4-TL |
63.4 ± 1.0 |
54.4 ± 0.6 |
65.5 ± 0.5 |
42.0 ± 0.2 |
23.0 ± 1.3 |
29.2 ± 1.6 |
1.6 ± 0.6 |
5.8 ± 0.9 |
36 ± 1.4 |
40.3 ± 0.7 |
3.7 ± 0.8 |
5.9 ± 1.1 |
35.1 ± 0.7 |
22.5 ± 0.8 |
5-TL |
61.9 ± 3.4 |
51 ± 1.7 |
55.0 ± 1.7 |
32.4 ± 0.6 |
21.2 ± 1.6 |
24.5 ± 1.7 |
1.4 ± 0.8 |
6.2 ± 1.2 |
44 ± 1.9 |
36.1 ± 0.9 |
3.9 ± 0.9 |
5.4 ± 0.8 |
31.6 ± 0.8 |
29 ± 0.6 |
6-FL |
61.2 ± 3.2 |
52.6 ± 4.2 |
51.7 ± 1.6 |
35.0 ± 1.5 |
20.2 ± 1.2 |
25.9 ± 2.0 |
1.0 ± 0.7 |
5.9 ± 1.1 |
59 ± 1.5 |
39.2 ± 0.8 |
4.7 ± 1.2 |
5.7 ± 0.9 |
17.6 ± 1 |
25 ± 0.7 |
7-FL |
66.4 ± 9.3 |
57.4 ± 2.4 |
72.2 ± 4.6 |
49.0 ± 0.8 |
26.6 ± 2.1 |
32.9 ± 2.4 |
1.6 ± 1.1 |
5.4 ± 1.0 |
36 ± 2.6 |
44.4 ± 0.8 |
3.5 ± 1.0 |
6.1 ± 1.2 |
38.6 ± 0.8 |
38.6 ± 0.8 |
The absolute values for this study differ from others, which can be attributed to differences in the experimental design, the fuels, the testing method and the calculations and metrics employed. Unfortunately, our findings are not directly comparable with other results. In a previous study,47 the results showed improved stove reduced emissions of CO 22%, CO2 28% and PM2.5 27% in comparison to a traditional stove.
Previously, mixed results have been reported with some authors finding no significant differences between some stove and fuel types48–50 while others51,52 reported that improved stoves had significantly better thermal efficiency and reduced emissions similar to our results.
4 Conclusions
This study was conducted to investigate the thermal efficiencies and emissions of seven dual-function cooking and heating stoves burning semi-coked coal briquettes and raw coal. A comparison was also made between the improved stoves and a traditional baseline stove. Sixteen hour tests were conducted to evaluate the thermal and emissions performance. The results show that in general, all the improved stoves were better than the baseline stove but not on all metrics in all cases. The commercially produced model 2-TL stove had the highest thermal efficiency (87.2 ± 0.5%) and the lowest emissions of PM2.5 0.94 ± 0.5 mg MJNET−1 and CO 1.1 ± 0.6 g MJNET−1, when burning 50 mm briquettes.
It is concluded that with respect to these improved stove designs, semi-coked coal briquettes produce better performance. The improved stoves had higher thermal efficiencies and lower specific emissions on all metrics, contributing to a cleaner environment, saving fuel expenses, and improving the health of the general population, as well as offering greenhouse gas mitigation co-benefits.
Conflicts of interest
There are no conflicts to declare.
Acknowledgements
This study was supported by the National Natural Science Foundation of China (Grant No. 51806242); the Chinese Universities Scientific Fund (No. 2019TC010); Agricultural Product Quality Inspection Bureau, Ministry of Agriculture and Rural Affairs, China, Agricultural Industry Standard Development Project – “Determination method of major atmosphere pollutants from rural household stoves” (No. 181721301092371112); the Innovation and Entrepreneurship program Yantai Economic & Technological Development Area (2020CYRC2); and Project of Hebei Energy Conservation Inspection and Monitoring Center – “Assessment on the effect of clean space heating replacement in Hebei Province”. We also appreciate for the supports from the Key Laboratory of Clean Production and Utilization of Renewable Energy, Ministry of Agriculture and Rural Affairs, China; National Center for International Research of BioEnergy Science and Technology, Ministry of Science and Technology, China; National First-Class Discipline of Agricultural Engineering; Beijing Municipal Key Discipline of Biomass Engineering; and appreciation to the support for some consumables from Beijing Kunhe Environmental Technology, Co., Ltd.
References
- G. Bensch and J. Peters, J. Health Econ., 2015, 42, 44–63 CrossRef PubMed.
- International Energy Agency (IEA), World energy outlook, Paris: International Energy Agency, 2011 Search PubMed.
- W. Qu, Z. Yuan, M. Qu and M. Ikram, Iran, J. Public Health, 2015, 44, 625–638 Search PubMed.
- G. F. Shen, R. Xing, Y. S. Zhou, X. Q. Jiao, Z. H. Luo, R. Xiong, W. X. Huang, Y. L. Tian, Y. C. Chen, W. Du, H. Z. Shen, H. F. Cheng, D. Q. Zhu and S. Tao, Sustainable Horiz., 2022, 1, 100010 CrossRef.
- G. F. Shen, R. Xiong, Y. L. Tian, Z. H. Luo, B. Jiangtulu, W. J. Meng, W. Du, J. Meng, Y. C. Chen, B. Xue, Y. H. Wang, J. Duan, F. G. Duo, L. Fan, T. Z. Huang, T. Z. Ju, F. G. Liu, S. X. Li, X. L. Liu, Y. G. Li, M. Wang, Y. Nan, B. Pan, Y. F. Pan, L. Z. Wang, E. Zeng, C. Zhan, Y. L. Chen, H. Z. Shen, H. F. Cheng and S. Tao, Natl. Sci. Rev., 2022, nwac050 CrossRef.
- J. Liao, A. Z. Jin, A. Z. Chafe, A. Pillarisetti, T. Yu, M. Shan, X. Yang, H. Li, G. Liu and K. R. Smith, Atmos. Environ., 2017, 165, 62–72 CrossRef CAS.
- E. T. Gall, E. M. Carter, M. C. Earnest and B. Stephens, Am. J. Publ. Health, 2013, 103, 67–72 CrossRef PubMed.
- R. Ahmad, Y. G. Zhou, N. Zhao, A. Abbas, G. Li, P. Raman, C. Pemberton-Pigott, M. Sultan and R. J. Dong, Fresenius Environ. Bull., 2019, 28, 9835–9842 CAS.
- N. Bruce, P. Perez and R. Albalak, Bull. World Health Organ., 2000, 78, 1080–1092 Search PubMed.
- Z. H. Luo, L. Zhang, G. Li, W. Du, Y. C. Chen, H. F. Cheng and S. Tao, Atmos. Res., 2021, 248, 105247 CrossRef CAS.
- M. M. Pier and F. Massimo, Int. J. Environ. Res. Publ. Health, 2017, 14, 1048 CrossRef PubMed.
- G. Yang, Y. Wang, Y. X. Zeng, G. F. Gao, X. F. Liang, M. G. Zhou, X. Wan, S. C. Yu, Y. H. Jiang, M. Naghavi, T. Vos, H. D. Wang, A. D. Lopez and C. J. L. Murray, Lancet, 2013, 381, 1987–2015 CrossRef.
- G. Hoek, R. M. Krishnan, R. Beelen, A. Peters, B. Ostro, B. Brunekreef and J. D. Kaufman, Environ. Health, 2013, 12, 43 CrossRef CAS PubMed.
- J. Lissowska, A. Bardin-Mikolajczak, T. Fletcher, D. Zaridze, N. Szeszenia-Dabrowska, P. Rudnai, E. Fabianova, A. Cassidy, D. Mates, I. Holcatova, V. Vitova, V. Janout, A. Mannetje, P. Brennan and P. Boffetta, Am. J. Epidemiol., 2005, 162, 326–333 CrossRef PubMed.
- W. J. Seow, W. Hu, R. Vermeulen, H. D. Hosgood III, G. S. Downward, R. S. Chapman, X. He, B. A. Bassig, C. Kim, C. Wen, N. Rothman and Q. Lan, Chin. J. Cancer, 2014, 33, 471–475 CAS.
- M. A. Jeuland and S. K. Pattanayak, PLoS One, 2012, 7, e30338 CrossRef CAS PubMed.
- G. Li, X. Bai, S. H. Huo and Z. G. Huang, IET Renew. Power Gener., 2020, 14, 959–967 CrossRef.
- N. Zhao, B. W. Li, D. Y. Chen, R. Ahmad, Y. Zhu, G. Li, Z. P. Yu, J. Li, E. L. Wang, S. Yun, H. Yoon, I. Yoon, Y. G. Zhou, R. J. Dong, H. Wang, J. X. Cao, J. He and X. X. Ju, Waste Manag., 2020, 104, 20–32 CrossRef CAS PubMed.
- K. Jiang, B. Fu, Z. H. Luo, R. Xiong, Y. T. Men, H. Z. Shen, B. G. Li, G. F. Shen and S. Tao, Environ. Pollut., 2022, 306, 119378 CrossRef CAS PubMed.
- W. S. Zhang, Z. F. Lu, Y. Xu, C. Wang, Y. F. Gu, H. Xu and D. G. Streets, Atmos. Environ., 2018, 176, 158–170 CrossRef CAS.
- L. Wang, Y. Jing, Z. Pu, Z. Xiu, W. Zhe, Z. Fen, S. Jie and C. M. Chen, Open J. Air Pollut., 2013, 2, 47–55 CrossRef.
- H. Liu and D. I. Mauzerall, Energy Econ., 2020, 90, 104844 CrossRef.
- H. Wang, Y. Lei, X. Chen, J. He and L. Gao, J. Environ. Res. Sci., 2015, 28, 1510–1517 CAS.
- Y. Hao, Q. Zhang, M. Zhong and B. Li, J. Clean. Prod., 2015, 108, 944–954 CrossRef CAS.
- G. Li, Z. T. Lu, J. Zhang, H. Li, Y. G. Zhou, A. M. I. Zayan and Z. G. Huang, Int. J. Agric. Biol. Eng., 2020, 13, 241–246 Search PubMed.
- B. Xu and B. Lin, J. Clean. Prod., 2015, 112, 1454–1463 CrossRef.
- J. F. Zhang and J. M. Samet, J. Thorac. Dis., 2014, 7, 3–13 CrossRef.
- H. Li, S. Yang, J. Zhang and Y. Qian, J. Clean. Prod., 2015, 112, 1350–1359 CrossRef.
- R. Ahmad, Y. G. Zhou, H. Li, N. Zhao, A. Abbas, M. Sultan, P. Raman and R. J. Dong, Fresenius Environ. Bull., 2021, 30, 4365–4372 CAS.
- N. Zhao, B. W. Li, R. Ahmad, F. Ding, Y. G. Zhou, G. Li, A. M. I. Zayan and R. J. Dong, Case Stud. Therm. Eng., 2021, 28, 101484 CrossRef.
- Z. G. Huang, J. Zhang, M. M. Pan, Y. H. Hao, R. C. Hu, W. B. Xiao, G. Li and T. Lyu, Biochem. Eng. J., 2020, 179, 108330 CrossRef.
- G. Li, R. C. Hu, N. Wang, T. L. Yang, F. Z. Xu, J. L. Li, J. H. Wu, Z. G. Huang, M. M. Pan and T. Lyu, J. Clean. Prod., 2022, 355, 131768 CrossRef CAS.
- P. Wilkinson, K. R. Smith, M. Davies, H. Adair, B. G. Armstrong, M. Barrett, N. Bruce, A. Haines, I. Hamilton, T. Oreszczyn, I. Ridley, C. Tonne and Z. Chalabi, Lancet, 2009, 374, 1917–1929 CrossRef.
- H. Z. Shen, Z. H. Luo, R. Xiong, X. Liu, L. Zhang, Y. Li, W. Du, Y. C. Chen, H. F. Cheng, G. F. Shen and S. Tao, Environ. Int., 2021, 157, 106841 CrossRef CAS PubMed.
- C. Venkataraman, G. Habib, A. Eiguren, H. Miguel and K. Friedlander, Science, 2005, 307, 1454–1456 CrossRef CAS PubMed.
- S. Ahmad and J. A. P. Oliveira, J. Clean. Prod., 2015, 94, 130–136 CrossRef.
- N. Zhao, B. W. Li, H. Li, G. Li, R. C. Wu, Q. Hong, P. Mperejekumana, S. Liu, Y. G. Zhou, R. Ahmad, A. M. I. Zayan, C. Pemberton-Pigott and R. J. Dong, Environ. Res., 2021, 94, 110683 CrossRef PubMed.
- H. E. S. Mestl, K. Aunan, J. Fang, H. M. Seip, J. M. Skjelvik and H. Vennemo, J. Clean. Prod., 2005, 13, 57–70 CrossRef.
- Q. Li, X. H. Li, J. K. Jiang, L. Duan, S. Ge, Q. Zhang, J. G. Deng, S. X. Wang and J. M. Hao, Sci. Rep., 2016, 6, 19306 CrossRef CAS PubMed.
- R. Ahmad, A. Abbas, W. Jufei, H. Li, M. Sultan, B. Li, S. M. Nyambura and X. J. Pan, Environ. Sci. Pollut. Res., 2021, 28, 58135–58141 CrossRef CAS PubMed.
- R. Ahmad, Y. G. Zhou, N. Zhao, C. Pemberton-Pigott, H. J. Annegarn, M. Sultan, R. J. Dong and X. X. Ju, Int. J. Agric. Biol. Eng., 2019, 12, 160–167 Search PubMed.
- O. Adetona, Z. Li, A. Sjödin, L. C. Romanoff, M. A. Villalobos, L. L. Needham, D. B. Hall, B. E. Cassidy and L. P. Naeher, Environ. Int., 2013, 53, 1–8 CrossRef CAS PubMed.
- J. Robinson, C. Pemberton-Pigott and H. Annegarn, 2018, available online: http://www.newdawnengineering.com/website/library/Papers+Articles/SeTAR/SeTAR%20HPT%20Multistove%20comparison,%20Robinson%20et%20al%20FINAL.xlsx.
- J. Wang, H. H. Lou, F. Yang and F. Cheng, J. Clean. Prod., 2016, 134, 447–455 CrossRef CAS.
- L. S. Bäfver, B. Leckner, C. Tullin and M. Berntsen, Biomass Bioenergy, 2011, 35, 3648–3655 CrossRef.
- M. Cui, Y. Xu, B. Yu, L. Liu, J. Li and Y. Chen, Sci. Total Environ., 2022, 83, 155529 CrossRef PubMed.
- F. Mamuye, B. Lemma and T. Woldeamanuel, Sustainable Environ. Res., 2018, 28, 32–38 CrossRef CAS.
- J. Liu, D. L. Mauzerall, Q. Chen and T. Zhu, Environ. Sci., 2016, 113, 7756–7761 CAS.
- J. Granderson, J. S. Sandhu, D. Vasquez, E. Ramirez and K. R. Smith, Biomass Bioenergy, 2009, 33, 306–315 CrossRef.
- J. P. McCracken and K. R. Smith, Environ. Int., 1998, 24, 739–747 CrossRef.
- A. Edwin, T. Erika, W. Jin, S. David and M. Vijay, Energy Sustainable Dev., 2010, 14, 172–185 CrossRef.
- D. Ludwinski, K. Moriarty and B. Wydick, Environ. Dev. Sustain., 2011, 13, 657–676 CrossRef.
Footnote |
† Riaz Ahmad and Yuguang Zhou contributed equally to this work. |
|
This journal is © The Royal Society of Chemistry 2022 |
Click here to see how this site uses Cookies. View our privacy policy here.