DOI:
10.1039/D2RA02944H
(Paper)
RSC Adv., 2022,
12, 19225-19231
Insights into the effects of synthesis techniques and crosslinking agents on the characteristics of cellulosic aerogels from Water Hyacinth
Received
10th May 2022
, Accepted 27th June 2022
First published on 1st July 2022
Abstract
Aerogel cellulose materials were synthesised from Water hyacinth and different crosslinkers, such as kymene and a mixture of polyvinyl alcohol (PVA) and glutaraldehyde (GA). The effects of using a magnetic stirrer and ultrasonic methods were investigated. The results show that materials prepared using ultrasonic methods have higher porosity and lower density. The thermal conductivity of the synthesised aerogel cellulose could be as low as 0.0281 W m K−1, showing the good heat insulation performance of this material. Absorption capacity was tested using diesel oil (DO), and the highest capacities of 58.82 and 52.03 g g−1 of DO were found with kymene and PVA + GA as crosslinkers, respectively. The reusability of the materials was tested. After 10 cycles, the DO absorption capacity was 62.8% of the value of the first cycle for the aerogel cellulose sample with kymene as the crosslinker and 72.7% for the sample with PVA + GA as the crosslinking agent.
Introduction
Many papers have been published on the synthesis and application of cellulose aerogel materials made from different materials: rice straw, banana tree,1,2 corn,3 cotton fibre,4 sugarcane bagasse,5 calamus manan,6 corn straw,7 palm fruit bunches,8 potato tubers,9 paper waste,10 durian shell,11 cotton,12 and wood.13,14 Cellulose aerogel materials and their modified forms are widely used in many different fields, such as heavy metal adsorption,15 dye adsorption,16 waste gas treatment, soundproofing,17 absorbents for oils,18 energy storage,7 and thermal insulation materials.19 Water hyacinth (WH) is a highly developed aquatic organism that grows in many tropical countries, including Vietnam. WH grows rapidly on the surface of rivers and canal systems, obscuring the water surface, and thus destroying water ecosystems as well as impeding water traffic. According to a previous study,20 the cellulose content of WH is up to 50% of its raw weight. Therefore, it is considered to be a promising source for the preparation of aerogel cellulose and extracted materials, which could be applied in many different fields. When synthesising aerogel materials, after processing to remove lignin and hemicellulose, cellulose is combined with polymers to create crosslinks and reinforce the porous structure, making it more durable with very high porosity. In the cellulose chain, functional groups can form crosslinks to separate cellulose circuits. The cellulose aerogel structure mainly depends on the number and nature of the crosslinks produced in the polymer chains. Two types of crosslinking can be found. Physical crosslinking consists of weak binding forces, such as van der Waals forces, hydrophobic or electronic bonds, and hydrogen bonds. Chemical crosslinking is based on covalent or ionic bonds, giving stable Feng structures, suitable porosity, and high stability in cellulose.21 Different polymers can be used to make materials with different physical and chemical properties. Methyltrimethoxysilane (MTMS) 2% by weight in cellulose nanofibre (CNF)/aqueous suspension has been used to form chemical crosslinks in cellulose aerogel structures.22 Silanols form hydrogen bonds with cellulose hydroxyl groups, which then, under heating conditions, form covalent –Si–OC– bonds and create cellulose aerogels with a stable porous structure.23 A solvent NaOH/thiourea/H2O system with the help of ethanol has also been used.24 Further, graphene oxide (GOS) sheets have been used to provide physical crosslinking in the structure of cellulose aerogels.25 Recently, polyvinyl alcohol (PVA) and kymene10,25–27 have been used to form crosslinks in the structure of aerogel cellulose materials.
The synthesis process is affected by both the stirring method and the temperature used. Mechanical stirring or an ultrasonic28 method are important in facilitating the incorporation of polymer molecules into fibres in the suspension, thus promoting the formation of cellulose aerogel structures with high porosity and stability. This result is due to the formation of a network of siloxane polymer (–Si–O–Si–) and three-dimensional oligomers that interact with cellulose through hydrogen bonding.23
In this study, WH was used as the raw material to synthesise aerogel cellulose. Both kymene and PVA with glutaraldehyde (GA) were used to form crosslinks, and their effect on the physical–chemical properties of aerogel cellulose was examined. The structural properties of the product were compared using ultrasonic and mechanical stirring methods in the synthesis process. The results from this study indicate differences between crosslinking agents as well as in the technical efficiency of material synthesis methods. It can be confirmed that cellulose aerogel materials have potential application in different fields.
Results and discussion
Material characterisation
The FTIR spectra of cellulose from WH (CW) and samples synthesised from WH cellulose (Fig. 1) show that cellulose has strong absorbance at 3340 cm−1 (–O–H stretching), 2896 cm−1 (–CH– symmetric stretching), and 1050 cm−1 (vibration of pyranose ring ether).27 After crosslinking, the O–H variation peak at 3340 cm−1 becomes broad and weaker.29 The FTIR spectra of all the samples have a peak at 1652 cm−1, which represents a typical amide C
O and absorbed H2O molecules.16,18 However, the ratio of peak intensity of 1652 cm−1 to others (such as 1055 cm−1 for the C–O stretching vibration of the cellulose backbone, which is not affected by the chemical modification) is remarkably low after crosslinking, showing that crosslinks are formed in the aerogel cellulose materials.26 In addition, a new weak peak arises at around 1550 cm−1 that can be assigned to the N–H bending of amide, as in the reported work.19 This result suggests that crosslink agents are indeed bonded to the aerogel material after heat treatment.
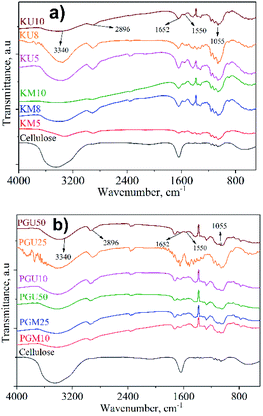 |
| Fig. 1 FTIR spectra of cellulosic aerogel samples synthesised from WH with kymene (a) and the mixture of PVA + GA (b). | |
The results for density and porosity are shown in Fig. 2 and 3, respectively, for aerogels made with kymene as the crosslinking agent using magnetic stirring (KM) and ultrasonics (KU) and with PVA + GA (PGM and PGU). Materials synthesised with kymene have a lower density (the lowest values are for KU8 and KM8 at 0.012 and 0.013 g cm−3, respectively) and a higher porosity (the highest values are for KU8 and KM8 at 99.2 and 99.3%, respectively) than materials made with PVA + GA. These materials have the lowest density at 0.015 and 0.017 g mL−1 and the highest porosity at 98.9 and 98.5% for PGU25 and PGM25, respectively. Kymene can form both self-crosslinking through its epichlorohydrin groups and external crosslinking with cellulose, increasing the mechanical strength, particularly the wet strength, of the aerogels.25 The results of DM Hai10 also show that aerogel cellulose materials have high porosity values with kymene as the crosslinking agent (98.1 to 99.4%). PVA can make a matrix material to form a 3D interconnected continuous network with hydrogen bonding and chemical crosslinking. Aerogel synthesised using PVA for crosslinking is neither mechanically strong nor highly compressible. Previously published results show that the porosity of this kind of product is 97.7–98.7%.27
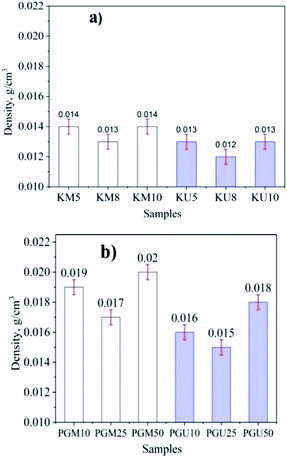 |
| Fig. 2 The density of aerogel cellulose from WH with kymene (a) and a mixture of PVA + GA (b) with an ultrasonic method and magnetic stirring. | |
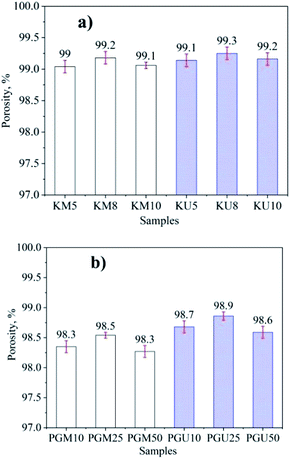 |
| Fig. 3 The porosity of aerogel cellulose from WH with kymene (a) and the mixture of PVA + GA (b) in two cases of ultrasonic assistance and magnetic stirring. | |
It can be seen that with both crosslinking agents, the products made with ultrasonic assistance have higher porosity and lower density compared to those made with magnetic stirring. However, the different values for kymene products are lower than those for PVA + GA. These results can be explained by the effect of ultrasonic energy separating the cellulose chains, facilitating dispersion of the crosslinking agents. Mechanical stirring does not separate the cellulose blocks, creating local agglomeration and poor dispersion of crosslinking agents.30 Because kymene has a low viscosity, it diffuses more readily in the cellulose mixture. Thus, ultrasonic assistance only has a promoting effect, reducing the interaction time between kymene and cellulose, and diffusion is not significantly increased compared with magnetic stirring. The mixture of PVA + GA has a much higher viscosity, so its ability to diffuse into cellulose is limited, meaning that ultrasonic assistance has a greater effect, increasing the diffusion capacity of the mixture into cellulose and leading to a marked increase in the interaction between the crosslinking agents and cellulose.31,32 Thus, the aerogel cellulose is more porous and more stable than with magnetic stirring.
The results also show that when the concentration of crosslinking agents is low, the density of the material is high. These density values increase with increased concentration of crosslinking agents but then decrease if the concentration of crosslinking is increased further. The reverse trend was seen with the porosity of the synthesized materials. When the concentration of the crosslinking agents is low, more cellulose blocks are created because of the saturation of cellulose in water; high density and low porosity material is formed. Increasing the concentration of the crosslinking agents increases the ability to create cellulose aerogel structures and thus increases porosity and reduces density.33,34 However, if the concentration of the crosslinking agents is increased further, blocks of these compounds form, decreasing porosity and increasing density.
Fig. 4 shows the structure and morphology of the aerogels investigated by SEM characterization. The SEM images show that the aerogel cellulose samples have the same uniform porous structure as the corresponding aerogels in previous reports.17,26,34,35 The results shown in Fig. 2 confirm that material with PVA + GA crosslinkers has a higher porosity than material with kymene.27 At the same time, material synthesised by the ultrasonic method has a higher porosity than material synthesised by magnetic stirring.31,32
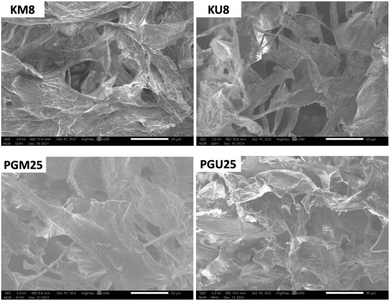 |
| Fig. 4 SEM images of aerogel samples. | |
The results of tests of the thermal conductivity of the aerogel material samples are presented in Fig. 5 and show that when density decreases and porosity increases, thermal conductivity also increases; these are the same findings as.34 It can be also observed that materials prepared with ultrasonic assistance have lower thermal conductivity compared to those prepared by magnetic stirring; this is because they have higher porosity, as shown in Fig. 2. The lowest thermal conductivity values obtained for the aerogels were 0.0281 and 0.0283 W m−1 K−1, corresponding to samples KU8 and PGU25, respectively. The obtained results show that the porosity and density of materials are correlated. For thermal conductivity, besides depending on porosity and density, it also depends on the nature of crosslinkers including polyvinyl alcohol + glutaraldehyde (PVA + GA) or Kymene (K).
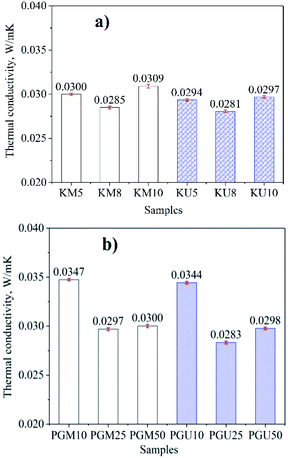 |
| Fig. 5 Thermal conductivity of aerogel cellulose materials with kymene (a) and a mixture of PVA and GA (b) as crosslinkers, by ultrasonic and magnetic stirrer methods. | |
Oil absorption capacity and the effects of stirring method with different crosslinking agents
The results show that the synthesised samples of all the cellulosic aerogels prepared using kymene and PVA + GA have high hydrophobicity, with a high water contact angle (141–142°) and have the ability to selectively adsorb oil in water (illustrated in Fig. 6). The absorption capacity for DO of cellulosic aerogel prepared using magnetic stirring and ultrasonic assistance in the synthesis processes with kymene and PVA + GA as crosslinking agents is shown in Fig. 7.
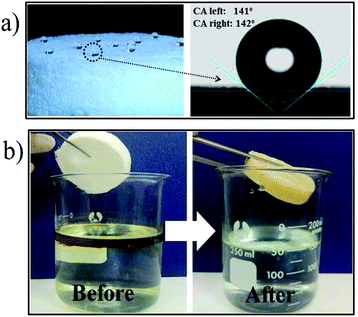 |
| Fig. 6 Images of hydrophobicity and water contact angles (a) and the selective absorption of oil in water (b) aerogel cellulose materials with kymene as crosslinker. | |
 |
| Fig. 7 Effects of magnetic stirrer and ultrasonic assistance methods on DO absorption capacity (g g−1) with kymene (a) and PVA + GA (b) as crosslinking agents. | |
With both crosslinking agents, the oil absorption capacity of the products using ultrasonic assistance is higher than when using the stirring method. However, with kymene as the crosslinking agent, the different values are not as clear as with the mixture of PVA + GA; this is because of the different viscosity of these agents and their dispersion into the cellulose block under the effect of stirring methods, as explained above. In addition, the results show that with kymene, the absorption capacity of aerogel cellulose is significantly higher than with PVA + GA. These results can be explained by the density and porosity values shown in Fig. 2 and 3, with changes in absorption capacity occurring when the concentration of crosslinking agents is altered. The highest absorption capacities of 58.8 and 52.0 g g−1 of DO correspond to samples KU8 and PGU25, respectively.
Reusability of materials
Samples KM8, KU8 and PGM25, PGU25 were used to test reusability with DO absorption. The testing process was carried out over 10 cycles and, after 3 min submergence in DO, the samples were compressed by 30 N of load. The results of the absorbing-releasing testing cycle are shown in Fig. 8. There was a significant deterioration in oil absorption capacity of sample KU8, from 58.8 g g−1 in cycle 1 to 42.9 g g−1 in the second cycle. However, from the second cycle to the tenth cycle, absorption capacity did not change a great deal, reaching 36.94 g g−1 in the last cycle, which equates to 62.8% of the highest value. The same trend was seen with the other samples (KM8, PGM25, and PGU25), as shown in Fig. 8. When PVA + GA is used as the crosslinking agent, even the highest absorption capacity is lower than for kymene; however, after the second cycle, absorption capacity is still 80% of the highest value, and after the tenth cycle, is still 72.7% of the highest value. The large drop in absorption capacity after the first cycle is the result of a massive structural collapse after compression, which leads to a huge loss of pores as the medium for retaining DO; however, the structure is then fairly stable for continuing cycles.36,37 In addition, kymene can produce better crosslinking, and so products have higher porosity and absorption capacity in the first absorption cycle. On the other hand, PVA + GA can form stronger crosslinks inside the aerogel cellulose product, meaning that the product undergoes less deformation when being compressed, with less decrease in absorption capacity. These results will be confirmed in future testing for compressive stress.
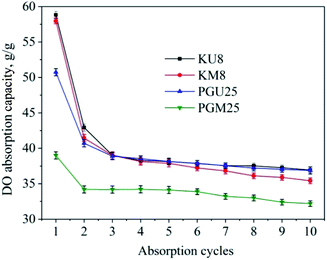 |
| Fig. 8 The absorption capacity changing of aerogel materials with ten absorption cycles. | |
Experimental
Materials
WH was collected from the Saigon River, District 12, Ho Chi Minh City, Vietnam. It was cut into small pieces and finely ground to a size less than 1 mm. It was then washed and dried in air. Glutaraldehyde (GA, HiMedia, 50%), polyvinyl alcohol (PVA, Merck, 99%), hydrogen peroxide (H2O2, Xilong, 30%), sodium hydroxide (NaOH, Xilong, 99%), sulphuric acid (H2SO4, Xilong, 98%), and kymene (KM, Solenis 5574) were used without further purification.
Preparation of aqueous gel of cellulose from WH
Dried WH fibres 2% w/w were mixed with a solution of NaOH solution 2% w/w to remove lignin and hemicellulose. The mixture was heated in a microwave (AEM-G2135W; AQUA) for 20 minutes to increase removal effectiveness. H2O2 aqueous solution of 17 vol% was added into the cool microwave-treated mixture with pH adjusted to around 11 using NaOH before being heated in the microwave for a further 10 minutes. As soon as the mixture was cooled to room temperature, it was filtered and washed with distilled water to attain a pH of 7.0. The pre-treated material was dried at 70 °C for 24 hours and stored for analysis and aerogel synthesis.
Preparation of aerogel cellulose from WH
Preparation of aerogel cellulose from WH with kymene as the crosslinker. Three samples of 100 mL solution of 1% w/w cellulose fibres after treatment with water were stirred to form a homogeneous solution. Then, 0.05, 0.075, and 0.1 mL of kymene binding agent were added and stirred with a magnetic stirrer at the stirring speed of 800 rpm for 1 hour to create samples KM5, KM8, and KM10, respectively. The same process was repeated for three other samples, but magnetic stirring was replaced by an ultrasonic method, for 15 minutes, creating samples KU5, KU8, and KU10, respectively. The six samples were placed in a refrigerator for 24 hours and sublimated at −70 °C on a TPV-50F dryer (China) to produce aerogels. Then, the cellulose aerogel materials were placed in an oven at 120 °C for 2 hours to increase the crosslinking of kymene in the aerogel cellulose product.
Preparation of aerogel cellulose from WH with PVA and GA as the crosslinker. As in the previous process, six samples of 100 mL solution 1% w/w of cellulose fibres were divided into two groups and mixed with water for at least 1 hour to form a homogeneous solution. In this process, to form the crosslinking in the aerogel structure, a solution of PVA (5% w/w in water) was added to the mixture at a ratio of PVA to cellulose of 4
:
3. The solution was stirred for 1 hour before adding 0.1 mL of 1% H2SO4 and 0.10, 0.25, and 0.50 mL of GA (25% w/w in water). The first group of three samples was prepared with magnetic stirring at the stirring speed of 800 rpm for another 1 hour to obtain samples PGM10, PGM25, and PGM50, respectively. The second group was prepared using ultrasonic stirring for 15 minutes to obtain samples PGU10, PGU25, and PGU50, respectively. All the samples were placed in a refrigerator for 24 hours and sublimated at −70 °C on a TPV-50F dryer (China) to produce aerogel cellulose materials Fig. 9.
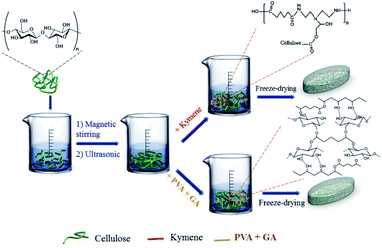 |
| Fig. 9 The structure model of aerogel materials formed with different crosslinkers. | |
Characterization
The density of the aerogel cellulose samples was determined by eqn (1):20 |
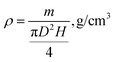 | (1) |
where, D is the diameter (cm), H is the height (cm) and m is the mass of the sample (g).
While the porosity of aerogel materials (P) is determined by eqn (2):20
|
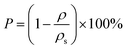 | (2) |
where,
ρ is the density of the aerogel sample after drying (g cm
−3) and
ρs is the density of the initial solid amount (g cm
−3).
A scanning electron microscope (SEM, Hitachi, S-4800) was used to examine the surface morphology and pore structure of the samples. In addition, the functional groups in the aerogel cellulose samples were determined through Fourier Transform Infrared (FT-IR) results performed on a Bruker Tensor 27 instrument (Bruker, Germany) with a scan range of 400 to 4000 cm−1 and a scan speed of 1 time/s within 30 times. Thermal conductivity tests were performed using a C-Therm TCi Thermal Conductivity Analyzer (C-Therm Technologies, Canada) using a modified transient plane source method with a spiral heater enclosed by a guard ring in ambient conditions.
Absorption capacity and reusability
The absorption capacity of the aerogel cellulose samples was tested according to ASTM F726-06. Dried samples were weighed and immersed in DO for 2 hours to reach equilibrium. Then, the aerogel cellulose samples were lifted from the oil-filled beaker with a stainless steel mesh basket, air-dried for 30 seconds, and reweighed. The oil absorption capacity of the sample was calculated according to eqn (3):20 |
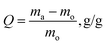 | (3) |
where, mo and ma are the mass of the aerogel cellulose sample before and after absorption. The same process was used to test the reusability and oil recovery of the aerogel cellulose materials for 10 cycles. The sample was squeezed to remove absorbed oil and dried in air for 30 minutes after each cycle.
Conclusions
Water hyacinth was used as raw material to synthesise aerogel cellulose with kymene and a mixture of PVA and GA as crosslinkers, with ultrasonic and magnetic stirring methods. The lowest thermal conductivity found was 0.0281 W m−1 K−1, showing high potential for application as a heat insulation material. The results show that aerogel celluloses using kymene as the crosslinker and synthesised with ultrasonic assistance have high porosity and low density, and also have high absorption capacity. The absorption capacity after 10 cycles of the sample with PVA and GA did not change as much as that of the kymene sample, at 72.7% and 62.8%, respectively. The results confirm that aerogel cellulose as a “green” material produced from WH can be used as absorption materials and also has the potential to be used in many industrial fields.
Author contributions
Thi Thuy Van Nguyen: conceptualization, methodology, resources, writing-original draft, validation, investigation, formal analysis. Goh Xue Yang: methodology, validation, investigation, formal analysis. Anh N. Phan: conceptualization, methodology, writing–review & editing, supervision, project administration, funding acquisition. Tri Nguyen: conceptualization, methodology, resources, writing-original draft, investigation, formal analysis. Thanh Gia Thien Ho: methodology, resources, writing- original draft, validation, investigation, formal analysis. Son Truong Nguyen: methodology, validation, investigation, formal analysis. Ha Ky Phuong Huynh: conceptualization, methodology, writing–review & editing, supervision, project administration, funding acquisition.
Conflicts of interest
There are no conflicts to declare.
Acknowledgements
The authors would like to thank The Royal Academy of Engineering (FF\1920\1\45), The Royal Society (ICA\R1\191220), and the Academy of Medical Sciences Global Challenges Research Fund Networking scheme (GCRFNGR3\1506), UK for their financial support.
Notes and references
- P. Lu and Y.-L. Hsieh, Carbohydr. Polym., 2012, 87, 564–573 CrossRef CAS PubMed.
- M. M. Ibrahim, W. K. El-Zawawy, Y. Jüttke, A. Koschella and T. Heinze, Cellulose, 2013, 20, 2403–2416 CrossRef CAS.
- S. Jantip and P. Suwanruji, Adv. Mater. Res., 2011, 332, 1781–1784 Search PubMed.
- J. Wang and S. Liu, Sep. Purif. Technol., 2019, 221, 303–310 CrossRef CAS.
- Z. N. T. Mzimela, L. Z. Linganiso, N. Revaprasadu and T. E. Motaung, Mater. Res., 2018, 21 Search PubMed.
- R. R. Rizkiansyah, S. Mardiyati and R. Suratman, AIP Conf. Proc., 2016, 1725, 020071 CrossRef.
- D. Li, Y. Wang, Y. Sun, Y. Lu, S. Chen, B. Wang, H. Zhang, Y. Xia and D. Yang, Carbon, 2018, 137, 31–40 CrossRef CAS.
- Y. C. Ching and T. S. Ng, BioResources, 2014, 9, 6373–6385 Search PubMed.
- A. Dufresne, D. Dupeyre and M. R. Vignon, J. Appl. Polym. Sci., 2000, 76, 2080–2092 CrossRef CAS.
- J. Feng, S. T. Nguyen, Z. Fan and H. M. Duong, Chem. Eng. J., 2015, 270, 168–175 CrossRef CAS.
- Y. Wang, L. Zhu, F. Zhu, L. You, X. Shen and S. Li, J. Taiwan Inst. Chem. Eng., 2017, 78, 351–358 CrossRef CAS.
- F. Liebner, A. Potthast, T. Rosenau, E. Haimer and M. Wendland, Holzforschung, 2008, 62, 129–135 CAS.
- W. Chen, H. Yu, Q. Li, Y. Liu and J. Li, Soft Matter, 2011, 7, 10360–10368 RSC.
- J. Bhandari, H. Mishra, P. K. Mishra, R. Wimmer, F. J. Ahmad and S. Talegaonkar, Int. J. Nanomed., 2017, 12, 2021 CrossRef CAS PubMed.
- M. Czikkely, E. Neubauer, I. Fekete, P. Ymeri and C. Fogarassy, Water, 2018, 10, 1377 CrossRef CAS.
- W. Wei, H. Hu, X. Ji, Z. Yan, W. Sun and J. Xie, Water Sci. Technol., 2018, 78, 402–414 CrossRef CAS PubMed.
- M. Kaya and A. Tabak, J. Polym. Environ., 2020, 28, 323–330 CrossRef CAS.
- P. Munier, K. Gordeyeva, L. Bergström and A. B. Fall, Biomacromolecules, 2016, 17, 1875–1881 CrossRef CAS PubMed.
- W. Guo, X. Wang, P. Zhang, J. Liu, L. Song and Y. Hu, Carbohydr. Polym., 2018, 195, 71–78 CrossRef CAS PubMed.
- T. T. V. Nguyen, N. Tri, B. A. Tran, T. Dao Duy, S. T. Nguyen, T.-A. Nguyen, A. N. Phan, P. Mai Thanh and H. K. P. Huynh, ACS Omega, 2021, 6, 26130–26139 CrossRef CAS PubMed.
- S. Zhou, P. Liu, M. Wang, H. Zhao, J. Yang and F. Xu, ACS Sustainable Chem. Eng., 2016, 4, 6409–6416 CrossRef CAS.
- M. Zanini, A. Lavoratti, L. K. Lazzari, D. Galiotto, M. Pagnocelli, C. Baldasso and A. J. Zattera, Cellulose, 2017, 24, 769–779 CrossRef CAS.
- B. Zhang, C. Huang, H. Zhao, J. Wang, C. Yin, L. Zhang and Y. Zhao, Polymers, 2019, 11, 2063 CrossRef CAS PubMed.
- S. Acharya, S. Liyanage, P. Parajuli, S. S. Rumi, J. L. Shamshina and N. Abidi, Polymers, 2021, 13, 4344 CrossRef CAS PubMed.
- W. Zhang, Y. Zhang, C. Lu and Y. Deng, J. Mater. Chem., 2012, 22, 11642–11650 RSC.
- Q. Zheng, Z. Cai and S. Gong, J. Mater. Chem. A, 2014, 2, 3110–3118 RSC.
- X. Gong, Y. Wang, H. Zeng, M. Betti and L. Chen, ACS Sustainable Chem. Eng., 2019, 7, 11118–11128 CrossRef CAS.
- L.-Y. Long, Y.-X. Weng and Y.-Z. Wang, Polymers, 2018, 10, 623 CrossRef PubMed.
- W. Wang, X. Jin, Y. Zhu, C. Zhu, J. Yang, H. Wang and T. Lin, Carbohydr. Polym., 2016, 140, 356–361 CrossRef CAS PubMed.
- A. H. Idrisi and A.-H. I. Mourad, J. Alloys Compd., 2019, 805, 502–508 CrossRef CAS.
- A. Simon, L. Penpenic, N. Gondrexon, S. Taha and G. Dorange, Ultrason. Sonochem., 2000, 7, 183–186 CrossRef CAS PubMed.
- S. Sumitomo, H. Koizumi, M. A. Uddin and Y. Kato, Ultrason. Sonochem., 2018, 40, 822–831 CrossRef CAS PubMed.
- J. J. Shi, L. B. Lu and J. Y. Zhang, Adv. Mater. Res., 2013, 773, 487–491 CAS.
- P. Gupta, B. Singh, A. K. Agrawal and P. K. Maji, Mater. Des., 2018, 158, 224–236 CrossRef CAS.
- O. Laitinen, T. Suopajärvi, M. Österberg and H. Liimatainen, ACS Appl. Mater. Interfaces, 2017, 9, 25029–25037 CrossRef CAS PubMed.
- Q. Liao, X. Su, W. Zhu, W. Hua, Z. Qian, L. Liu and J. Yao, RSC Adv., 2016, 6, 63773–63781 RSC.
- D. Wu, L. Fang, Y. Qin, W. Wu, C. Mao and H. Zhu, Mar. Pollut. Bull., 2014, 84, 263–267 CrossRef CAS PubMed.
|
This journal is © The Royal Society of Chemistry 2022 |
Click here to see how this site uses Cookies. View our privacy policy here.