DOI:
10.1039/D2RA01494G
(Paper)
RSC Adv., 2022,
12, 11906-11912
Metal chloride anion based ionic liquids: synthesis, characterization and evaluation of performance in hydrogen sulfide oxidative absorption†
Received
7th March 2022
, Accepted 1st April 2022
First published on 19th April 2022
Abstract
Three metal chloride anion based ionic liquids (MCABILs) were synthesized and characterized for high conversion of hydrogen sulfide (H2S). The MCABILs were synthesized via metathesis reaction and characterized by chemical spectroscopy such as FTIR, UV-Vis and CHNS elemental analysis. Then, the performance of those ionic liquids in H2S conversion was evaluated at various temperatures and atmospheric pressure. The results indicated remarkable efficiency of metal chloride anion based ionic liquids in H2S conversion. MCABILs managed to reach over 90% conversion efficiency at temperature as low as 50 °C, despite operating at atmospheric pressure. This occurs due to their high oxidation capability. The regeneration experiment indicated that all MCABILs can be recycled easily. Taken together, the research findings highlight the synthesis, characterization and high efficiency of MCABILs in promoting faster H2S conversion as a catalyst.
1. Introduction
H2S is a colorless gas that exists naturally,1 and is very toxic2 and highly flammable. Its harmful effects towards living organisms are visible at 10 ppm (ref. 3) and become fatal after exceeding 500 ppm.4 H2S is also highly corrosive to carbon steel.5 Thus, H2S removal is very crucial for economic and safety reasons. Absorption, adsorption and conversion are common desulphurization technologies. LO-CAT and Claus process are most outstanding as they are capable of converting H2S into sulfur with excellent efficiency.6 However, they consume a lot of energy and face catalyst deactivation. Consequently, sulfur production output is lowered and cost increased.7 Ionic liquids (ILs) are salts with melting point lower than the water boiling point and have emerged as promising green solvents for desulphurization.8 ILs are designer solvents because their physicochemical properties are tunable by changing the cation and anion.9 Hence, they can be designed specifically for desulphurization. Recently, many studies were targeting H2S conversion into sulfur using ILs.10–14 Since there are unlimited possible combinations, evaluation for most efficient ILs would be very tedious and costly if carried out experimentally.15,16 The chances to discover and select new ILs would be complicated. Thus, every potential IL must undergo a thorough and systematic screening.
This work is a continuation study of screening potential ILs for direct conversion of H2S by Conductor-like Screening Model for Real Solvents (COSMO-RS).17 COSMO-RS screening was conducted to predict the thermodynamic properties of ILs for H2S conversion without requiring any prior experimental data. Based on COSMO-RS prediction, economical and safety reasons, three MCABILs were selected for synthesis from 300 screened.17 Various studies have discovered potential Room-Temperature Ionic Liquids (RTILs) application for H2S conversion,18,19 nonetheless, it is discovered that their capacity and solubility for H2S are still poor at low pressure.20–23 Thus, this study was performed using Task Specific Ionic Liquids (TSILs) which is MCABILs that were improved24,25 and capable of promoting faster H2S conversion to sulfur.11,26 Three selected ILs were; trihexyl(tetradecyl)phosphonium tetrachlorogallate, [P66614][GaCl4], trihexyl(tetradecyl)phosphonium tetrachloroferrate, [P66614][FeCl4] and trihexyl(tetradecyl)phosphonium trichlorostannate, [P66614][SnCl3].
2. Materials and methods
2.1. Materials
Trihexyl(tetradecyl)phosphonium chloride, [P66614][Cl] of 95% purity was purchased from Sigma-Aldrich. The metal chlorides used for this work were gallium(III) chloride, iron(III) chloride and tin(II) chloride. Gallium(III) chloride, GaCl3 of 99.999% purity, anhydrous iron(III) chloride, FeCl3 of 97% purity and tin(II) chloride, SnCl2 of 98% purity were also purchased from Sigma-Aldrich. All chemicals used are analytical grade and require no purification.
2.2. Synthesis of MCABILs
Three MCABILS were synthesized by metathesis reaction of [P66614][Cl] with GaCl3, FeCl3 an SnCl2 to produce trihexyltetradecylphosphonium tetrachlorogallate, [P66614][GaCl4], trihexyltetradecylphosphonium tetrachloroferrate, [P66614][FeCl4] and trihexyltetradecylphosphonium trichlorostannate, [P66614][SnCl3]. [P66614][GaCl4] was synthesized by metathesis reaction according to Fig. 1.
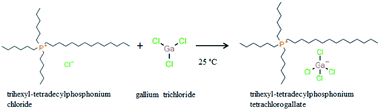 |
| Fig. 1 Reaction mechanism for synthesis of trihexyl(tetradecyl)phosphonium tetrachlorogallate, [P66614][GaCl4]. | |
P66614Cl and GaCl3 were reacted in round bottom flask with stirrer to ensure uniform heating and perfect mixing at 25 °C for 24 h. The product was filtered and washed with deionized water to remove unwanted salt and impurities. To minimise water content and volatiles to lowest possible values, the synthesized MCABILs underwent rotary evaporation at 70 °C in vacuum condition for several days. The procedure were repeated with [P66614][FeCl4] and [P66614][SnCl3].
[P66614][GaCl4] formed was a dark red liquid. The yield obtained was 99.0% and the water content was measured at 11 ppm. CHNS analysis calculated (found); C: 55.27 (55.24), H: 9.86 (9.89), N: 0 (0), S: 0 (0).
[P66614][FeCl4] was formed was a dark black liquid. The yield for [P66614][FeCl4] was 96.7% and the water content was obtained at 17 ppm. CHNS analysis calculated (found); C: 56.40 (56.38), H: 10.06 (10.09), N: 0 (0), S: 0 (0).
[P66614][SnCl3] was obtained as a golden yellow colour liquid. The product yield was 90.3% and the water content was found to be at 25 ppm. CHNS analysis calculated (found); C: 54.22 (54.19), H: 9.67 (9.71), N: 0 (0), S: 0 (0).
2.3. Characterization instruments
CHNS elemental analysis was performed using Leco-CHNS-932 Analyzer. FT-IR spectra of the samples were collected by Fourier transfrom infrared Thermo Nicolet is5 spectrometer. TGA curve was obtained by PerkinElmer thermogravimetric analyzer, Pyris V-3.81. DSC curve was collected by DSC Q2000 V24.11 Build 124 (Universal V4.5A TA Instruments). Density was determined by density meter DA-645 (Kyoto Electronics Manufacturing). Viscosity was obtained by AMVn Anton Paar micro viscometer. The water content analyses were conducted by V30 Mettler Toledo coulometric Karl Fischer titrator.
2.4. H2S absorption measurement
H2S absorption measurement was conducted at atmospheric pressure and various temperatures at 25 °C, 50 °C, 75 °C and 100 °C as depicted in Fig. 2. Raw materials inlet into the system consists of three gas path way and the gas flow rate was controlled by the flow meter and mass flow controller. A gas mixture of oxygen and 100 ppm concentration of H2S was passed through the 25 mL stainless steel reactor in which the MCABILs were loaded. N2 gas was used as the carrier gas and purging gas to ensure all the system is free of H2S before and after the reaction happened. The reaction temperature was between room temperature until 100 °C and regulated by the heating mantel around the reactor. The concentration of H2S at both inlet and outlet gas was detected by H2S gas analyzers. The residual H2S gas was absorbed by the concentrated NaOH solution in the scrubber tanks. In this test, a maximum 10 ppm of the initial concentration of H2S was defined as the breakthrough concentration.
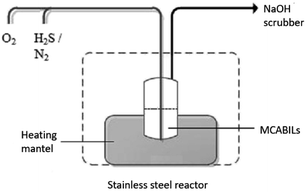 |
| Fig. 2 Schematic diagram for H2S oxidative absorption experimental set up. | |
3. Results and discussion
3.1. FT-IR spectra of MCABILs
The infrared spectra of [P66614][GaCl4], [P66614][FeCl4] and [P66614][SnCl3] display several peaks at 1465 cm−1, 1410 cm−1, 1110 cm−1 and 720 cm−1 associated with P–C stretching vibration as depicted in Fig. 3. The broad peak that exists in region between 2960 cm−1 to 2850 cm−1 are assigned to aliphatic moieties of C–H stretching vibration. The bands located at 985 cm−1 and 810 cm−1 are attributed to CH
CH bending vibrations. A single peak at 1375 cm−1 is associated with CH2–CH3 stretching vibration, while the peak at 1210 cm−1 is corresponded to C–H bending vibration. Based on spectra analysis, there is no presence of alkyl halides, C–Cl bond. Hence, this confirms the structure of MCABILs as shown in Fig. S1–S3.†
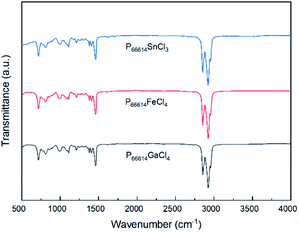 |
| Fig. 3 FTIR spectra of MCABILs: [P66614][GaCl4], [P66614][FeCl4] and [P66614][SnCl3]. | |
3.2. Density and viscosity of MCABILs
Fig. 4(a) and (b) show the density and viscosity of MCABILs, respectively. The densities varied from 0.98139 to 1.05059 g cm−3 and in reported range of 0.9 to 1.7 g cm−3.27 No significant decrease in viscosity was observed after the temperature reached 60 °C.28 The viscosity and density of MCABILs decrease as the temperature increases. At 20 °C, MCABILs exhibited viscosity between 543.11 to 880.42 cP and density between 0.98139 and 1.00274 g cm−3 as shown in Tables S1 and S2.† Since MCABILs possess lower viscosity and density at higher temperature, they can be excellent catalysts for direct H2S conversion.
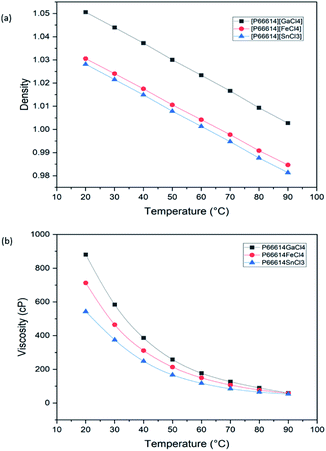 |
| Fig. 4 The relationship between (a) density and (b) viscosity versus temperature for all MCABILs. | |
3.3. TGA and DSC analysis of MCABILs
Fig. 5(a) and (b) represent the TGA and DSC curves of MCABILs, respectively. Thermal stability for each ILs was reported as thermal onset and decomposition temperatures in Table S3.† The decomposition temperature has appeared at 480.34 °C, 478.57 °C and 468.77 °C for [P66614][GaCl4], [P66614][FeCl4] and [P66614][SnCl3], respectively. These ILs display high thermal stability and [P66614][GaCl4] being the most stable. They were fully decomposed at a high temperature of 500 °C because phosphonium based ILs are very stable thermally.29 Since each MCABILs possesses Tonset higher than 400 °C, it is concluded that each of them is very stable ILs thermally.30 The melting point for each MCABILs are shown in Table S4.† The melting points of MCABILs increases as the molecular weight (MW) of the anions increases. An increase in MW of the anions side chains resulted in stronger intermolecular reaction which contributes to the rise in melting points. Since they share similar cation, the melting points only vary slightly.
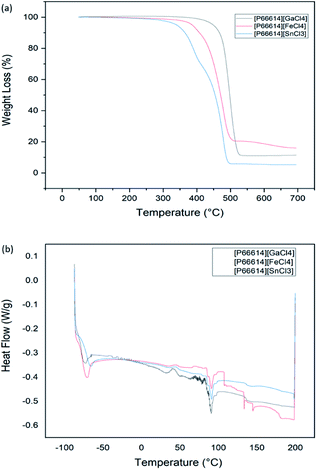 |
| Fig. 5 (a) TGA and (b) DSC profiles of MCABILs. | |
3.4. H2S removal performance of MCABILs
As depicted in Table 1, the efficiencies of H2S removal for all three MCABILs increased to over 90% within 360 min (6 h) at 100 °C. This indicates high performance and H2S conversion capabilities in those ILs. Among all three MCABILs, P66614GaCl4 demonstrated a lower H2S absorption capability compared to the other two MCABILs. Ding et al.26 designed a series of TSILs containing metal chelate cations for SO2 capture. The results indicated that SO2 solubility increases with the increase of metal ion radius and decreasing acidity due to alkali metal ion. According to Wang & Zhang,31 metal containing ILs are capable of absorbing H2S efficiently under certain pressure. They also stated that the metal anions acidity plays an important factor for H2S absorption.
Table 1 Desulfurization performance of MCABILs after 6 h
Ionic liquids |
Percentage of H2S removal after 6 h at 100 °C (%) |
P66614GaCl4 |
92.23 |
P66614FeCl4 |
93.51 |
P66614SnCl3 |
97.54 |
In this work, H2S absorption was performed in dynamic conditions and the partial pressure was also relatively low. However, the MCABILs were still able to perform well while maintaining high efficiency of H2S removal at relatively low pressure. The H2S conversion percentages were calculated using eqn (1):
|
 | (1) |
where,
xH2S,in and
xH2S,out are the concentration of H
2S at the inlet and outlet, respectively.
Fig. 6 depicted the FT-IR spectra of MCABILs before and after H2S conversion. Since it does not show any significant difference, that means no chemical reaction between H2S and ILs molecules have occurred. The presence of metal chlorides in the ILs matrix enhance the desulfurization abilities of pure ILs which have low physical and chemical solubility of H2S.
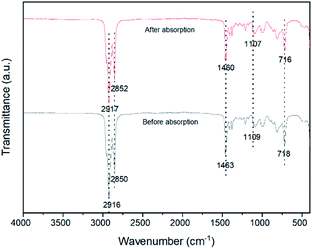 |
| Fig. 6 FT-IR spectra of MCABILs before and after H2S absorption | |
3.5. Mechanism of absorption
The reaction mechanism of H2S oxidative absorption in this research involves redox reaction between MCABILs and H2S. A study conducted by DeBerry et al.32 revealed that Fe(III)Cl4− was reduced to Fe(III)Cl4− during H2S oxidation in DMSO. In this work, the metal chloride anions in the ILs was reduced while H2S is being oxidized simultaneously. By combining the present work with research conducted by Nguyen et al.,33 the complete reaction mechanism for absorptive oxidation by one of the MCABILs is depicted as eqn (2) and (3). |
[P66614]GaCl4 + H2S → ([P66614]GaCl3)* + S8 + HCl
| (2) |
|
([P66614]GaCl3)* + HCl → [P66614]GaCl4H
| (3) |
The reaction began with the reduction of {P66614]GaCl4 into ([P66614]GaCl3)* by H2S. ([P66614]GaCl3)* was an intermediate species that reacted with HCl instantaneously to form [P66614]GaCl4H. The hydrogen ion in [P66614]GaCl4H is most likely to react with Cl− in MCABILs to form HCl, resulting in a strong acidic environment. The regeneration of MCABILs was performed by bubbling N2 gas through the catalyst for approximately 3 h.
3.6. Factors affecting H2S removal performance of the MCABILs
3.6.1. Effects of absorption temperature. The H2S conversion performance for one of MCABILs, P66614FeCl4 at different temperatures is shown in Fig. 7. The result reported a higher conversion at higher temperature. This demonstrates that the conversion of H2S is an endothermic reaction, which is supported by literature.34 Since it is an endothermic process, it limits the thermodynamic conversion at lower temperature.
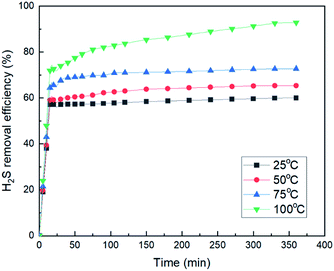 |
| Fig. 7 Desulfurization performance of MCABILs, P66614FeCl4 at different temperature. | |
However, since MCABILs were designed specifically to perform excellently at low temperature and pressure, MCABILs still can achieve high conversion as high as 90% at 50 °C and 1 atm. At higher temperature, the conversion of H2S in MCABILs is much higher. It can be concluded that the performance of MCABILs is optimum at higher temperature.
3.6.2. Effects of viscosity of MCABILs. Tables 2 and 3 shows the desulfurization performance of MCABILs with respect to their viscosity at 50 °C and 100 °C, respectively. Among all three MCABILs, P66614GaCl4 demonstrated a lower H2S conversion at lower temperature. This is because P66614GaCl4 has the highest viscosity followed by P66614FeCl4 and P66614SnCl3. It is very viscous at lower temperature and unable to perform the conversion efficiently. Meanwhile, P66614SnCl3 which possess a low viscosity at lower temperature showed a remarkable performance in H2S conversion. Hence, lower viscosity ILs are the best choice for H2S conversion.
Table 2 Desulfurization performance and viscosity of MCABILs at 50 °C after 6 h
Ionic liquids |
Viscosity (cp) |
Conversion (%) |
[P66614][GaCl4] |
258.37 |
65.35 |
[P66614][FeCl4] |
213.41 |
69.03 |
[P66614][SnCl3] |
167.17 |
91.75 |
Table 3 Desulfurization performance and viscosity of MCABILs at 100 °C after 6 h
Ionic liquids |
Viscosity (cp) |
Conversion (%) |
[P66614][GaCl4] |
59.43 |
92.23 |
[P66614][FeCl4] |
57.96 |
93.51 |
[P66614][SnCl3] |
53.42 |
97.54 |
3.6.3. Effects of reaction with time. Fig. 8 shows the percentage of H2S conversion into elemental sulfur with respect to reaction time, using P66614FeCl4. At the beginning, the reaction was rather slow because of mixing and dispersion of H2S, O2 and ILs phases. For example, conversion of H2S into elemental sulfur by P66614FeCl at 100 °C and 1 bar. The obtained results were 79.07%, 83.69%, 86.4%, 88.94%, 91.25% and 92.83% at 60, 120, 180, 240, 300 and 360 min respectively. The conversion rate increases with time because of the increase in mass transfer between the mixture gases of H2S and O2 and the catalyst, metal chloride anion based ILs and completed after a certain period of time.
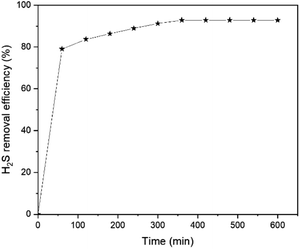 |
| Fig. 8 The effect of reaction time on H2S conversion using MCABILs, P66614FeCl4 at 100 °C. | |
Liu and Wang35 reported that as the reaction was prolonged until 10 h, the percentage of H2S conversion in PMo10V2/BmimCl decreases to below 75% which demonstrated that PMo10V2/BmimCl is only acting as solvent. Meanwhile, MCABILs maintains a high conversion percentage above 90% until 600 min without any performance drop and signifies its role as a catalyst for desulfurization reaction.
The experimental results indicated that the percentage of conversion (%) increases with increasing reaction time. As the reaction reaches 360 min, the conversion percentage of H2S has reached its peak at 93.51% and remain stagnant afterwards until reaches 600 min. Hence, 360 min can be deduced as the optimum reaction time for conversion of H2S into elemental sulfur.
3.7. Comparison of desulfurization performance for MCABILs
As shown in Fig. 9, all MCABILs with phosphonium cations demonstrated a high rate of desulfurization, reaching above 90% during 6 h of reaction at 100 °C. The performance of all MCABILs at 50 °C were also depicted in Fig. 10. Comparatively, the performance of MCABILs at lower temperature were a bit lower compared to their performance at 100 °C. This is probably due to higher viscosity of MCABILs at lower temperature.
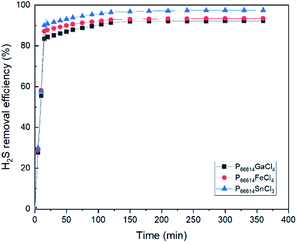 |
| Fig. 9 Comparison of desulfurization performance of MCABILs at 100 °C for 6 h. | |
 |
| Fig. 10 Comparison of desulfurization performance of MCABILs at 50 °C for 6 h. | |
Since MCABILs consist of similar cation, it is concluded that the metal chloride anions and their oxidation number play a significant role in affecting the desulfurization performance. MCABILs were playing role as catalysts for the removal of H2S through absorptive oxidation. Comparatively, they are more stable and efficient compared to the conventional ILs reported36,37 under similar operating conditions.
Among three MCABILs, P66614SnCl3 is the best catalyst for H2S absorptive oxidation with removal rate of 97.54%. The sequence of H2S removal efficiencies of MCABILs are in the following order of [P66614][SnCl3] > [P66614][FeCl4] > [P66614][GaCl4]. The efficiencies of MCABILs for H2S removal increased as the viscosity of MCABILs decreased. As a result, P66614SnCl3 demonstrated the best desulfurization performance.
3.8. Regeneration performance of MCABILs
MCABILs can be regenerated by flowing N2 at 200 mL min−1 for 30 min at 50 °C. The MCABILs used to study regeneration process was [P66614][FeCl4]. The regeneration performance of MCABILs was depicted in Fig. 11. The efficiency of H2S removal was observed after the absorption took place for 3 h. The rates of H2S removal for the studied MCABILs were found to be higher than 90% within 5 cycles thus, signifying an outstanding regeneration performance of MCABILs for H2S removal.
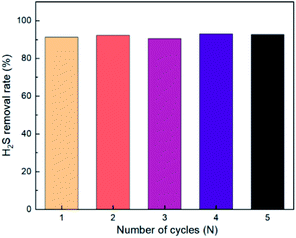 |
| Fig. 11 Regeneration performance of MCABILs, P66614FeCl4. | |
4. Conclusions
The contribution of this paper is twofold; to report the synthesis and characterization of three new MCABILs via combination of trihexyl(tetradecyl)phosphonium cation with metal chloride-anions and to evaluate their performance in H2S conversion. The yields for all ionic liquids were obtained in range of 90% to 99%. The synthesized ILs exist as liquid at room temperature and very stable thermally, possessing high decomposition temperatures ranging between 468.77 °C and 480.34 °C. Overall, MCABILs show desirable physical properties which make them excellent catalysts for absorptive oxidation of H2S. Those MCABILs also shown a remarkable desulfurization performance with over 90% efficiency at atmospheric pressure and can be regenerated for multiple usage.
Abbreviations
CHNS | Carbon, hydrogen, nitrogen, sulphur |
DSC | Differential scanning calorimetry |
FT-IR | Fourier transformed infrared |
H2S | Hydrogen sulfide |
ILs | Ionic liquids |
MCABILs | Metal chloride anion based ionic liquids |
RTILs | Room temperature ionic liquids |
TGA | Thermogravimetric analysis |
TSILs | Task specific ionic liquids |
Author contributions
Muhammad Syahir Aminuddin: conceptualization, methodology, investigation, writing – original draft. Mohamad Azmi Bustam: supervision, validation. Bawadi Abdullah: supervision, funding acquisition, validation, writing – review & editing.
Conflicts of interest
There are no conflicts to declare.
Acknowledgements
The authors acknowledge the funding for research work from Yayasan Universiti Teknologi PETRONAS (YUTP) under the YUTP-FRG Scheme (015LC0-263), Universiti Teknologi PETRONAS (UTP).
Notes and references
- E. Total, Sour Gas, A History of Expertise, Group, 2007, vol. 24 Search PubMed.
- A. J. Kidnay, W. R. Parrish and D. G. McCartney, Fundamentals of natural gas processing, CRC Press, 2019 Search PubMed.
- P. C. Database, Hydrogen sulfide, https://pubchem.ncbi.nlm.nih.gov/compound/Hydrogen-sulfide, accessed September 4, 2020 Search PubMed.
- O. S. a. H. Administration, Safety and Health Topics/Hydrogen Sulfide, https://www.osha.gov/SLTC/hydrogensulfide/hazards.html, accessed September 4, 2020 Search PubMed.
- M. Shahid and M. Faisal, Arabian J. Sci. Eng., Sect. A, 2009, 34, 179 CAS.
- M. J. Goodwin, O. M. Musa and J. W. Steed, Energy Fuels, 2015, 29, 4667–4682 CrossRef CAS.
- M. Abdul Aziz and A. Mithani, Holistic Approach in Managing Challenges of Mature Offshore Carbonate Gas Fields with High CO2 and H2S Content in Sarawak Gas Operations, Society of Petroleum Engineers, Malaysia, 2017 Search PubMed.
- K. Huang, X. Feng, X.-M. Zhang, Y.-T. Wu and X.-B. Hu, Green Chem., 2016, 18, 1859–1863 RSC.
- X. Wang, S. Zeng, J. Wang, D. Shang, X. Zhang, J. Liu and Y. Zhang, Ind. Eng. Chem. Res., 2018, 57, 1284–1293 CrossRef CAS.
- D. Shang, X. Liu, L. Bai, S. Zeng, Q. Xu, H. Gao and X. Zhang, Curr. Opin. Green Sustainable Chem., 2017, 5, 74–81 CrossRef.
- B. Guo, E. Duan, Y. Zhong, L. Gao, X. Zhang and D. Zhao, Energy Fuels, 2011, 25, 159–161 CrossRef CAS.
- Y. Ma, X. Liu and R. Wang, J. Hazard. Mater., 2017, 331, 109–116 CrossRef CAS PubMed.
- M. Li, J. Guan, J. Han, W. Liang, K. Wang, E. Duan and B. Guo, J. Mol. Liq., 2015, 209, 58–61 CrossRef CAS.
- J. Wang and R. Ding, Inorganics, 2018, 6, 11 CrossRef.
- A. Shojaeian, J. Mol. Liq., 2017, 229, 591–598 CrossRef CAS.
- S. Aparicio, M. Atilhan and F. Karadas, Ind. Eng. Chem. Res., 2010, 49, 9580–9595 CrossRef CAS.
- M. S. Aminuddin, Z. Man, M. A. Bustam Khalil and B. Abdullah, E3S Web Conf., 2021, 287, 02003 CrossRef CAS.
- J.-G. Lu, Y.-F. Zheng and D.-L. He, Sep. Purif. Technol., 2006, 52, 209–217 CrossRef CAS.
- P. K. Mohapatra, Dalton Trans., 2017, 46, 1730–1747 RSC.
- O. Brettschneider, R. Thiele, R. Faber, H. Thielert and G. Wozny, Sep. Purif. Technol., 2004, 39, 139–159 CrossRef CAS.
- Y. Zhao, J. Gao, Y. Huang, R. M. Afzal, X. Zhang and S. Zhang, RSC Adv., 2016, 6, 70405–70413 RSC.
- H. Sakhaeinia, A. H. Jalili, V. Taghikhani and A. A. Safekordi, J. Chem. Eng. Data, 2010, 55, 5839–5845 CrossRef CAS.
- M. Han and R. M. Espinosa-Marzal, ACS Appl. Mater. Interfaces, 2019, 11, 33465–33477 CrossRef CAS PubMed.
- C. Chiappe and C. S. Pomelli, in Ionic Liquids II, Springer, 2017, pp. 265–289 Search PubMed.
- C. Wang, Y. Guo, X. Zhu, G. Cui, H. Li and S. Dai, Chem. Commun., 2012, 48, 6526–6528 RSC.
- F. Ding, J. Zheng, Y. Chen, K. Chen, G. Cui, H. Li and C. Wang, Ind. Eng. Chem. Res., 2014, 53, 18568–18574 CrossRef CAS.
- J. O. Valderrama and K. Zarricueta, Fluid Phase Equilib., 2009, 275, 145–151 CrossRef CAS.
- P. Wasserscheid and T. Welton, Ionic liquids in synthesis, John Wiley & Sons, 2008 Search PubMed.
- H. F. Almeida, J. A. Lopes-da-Silva, M. G. Freire and J. A. Coutinho, J. Chem. Thermodyn., 2013, 57, 372–379 CrossRef CAS.
- Y. Cao and T. Mu, Ind. Eng. Chem. Res., 2014, 53, 8651–8664 CrossRef CAS.
- J. Wang and W. Zhang, Energy Fuels, 2014, 28, 5930–5935 CrossRef CAS.
- G. Srinivas, S. C. Gebhard and D. W. DeBerry, Hybrid sulfur recovery process for natural gas upgrading, National Energy Technology Laboratory (NETL), Pittsburgh, PA, Morgantown, WV, 2001 Search PubMed.
- M. D. Nguyen, L. V. Nguyen, E. H. Jeon, J. H. Kim, M. Cheong, H. S. Kim and J. S. Lee, J. Catal., 2008, 258, 5–13 CrossRef CAS.
- M. L. Samaniego, M. D. G. de Luna, D. C. Ong, M.-W. Wan and M.-C. Lu, Energy Fuels, 2019, 33, 1098–1105 CrossRef CAS.
- X. Liu and R. Wang, Fuel Process. Technol., 2017, 160, 78–85 CrossRef CAS.
- M. H. Ibrahim, M. Hayyan, M. A. Hashim and A. Hayyan, Renewable Sustainable Energy Rev., 2017, 76, 1534–1549 CrossRef CAS.
- A. W. Bhutto, R. Abro, S. Gao, T. Abbas, X. Chen and G. Yu, J. Taiwan Inst. Chem. Eng., 2016, 62, 84–97 CrossRef CAS.
|
This journal is © The Royal Society of Chemistry 2022 |
Click here to see how this site uses Cookies. View our privacy policy here.