DOI:
10.1039/D1RA06510F
(Paper)
RSC Adv., 2021,
11, 33788-33797
Recovery of Zn and Ge from zinc oxide dust by ultrasonic-H2O2 enhanced oxidation leaching
Received
29th August 2021
, Accepted 27th September 2021
First published on 15th October 2021
Abstract
Zn and Ge were selectively extracted from zinc oxide dust (ZOD) by the ultrasonic-H2O2 (UH) combined oxidation-leaching process. In the leaching process, the effects of the dosage of H2O2 (6–29.5 mL), ultrasonic power, initial acidity (100–200 g L−1), liquid/solid mass ratio (4–8
:
1), leaching temperature (50–90 °C), and leaching time (30–240 min) on the leaching rates of Zn and Ge were studied. The experimental results showed that the ultrasonic power and the dosage of H2O2 have the greatest influence on the leaching rates of Zn and Ge. The results showed the optimum conditions as: ultrasonic power 200 W, the dosage of H2O2 14.8 mL, initial acidity 160 g L−1, liquid/solid mass ratio 7
:
1, leaching time 60 min, stirring speed 400 rpm, leaching temperature 60 °C, and the leaching rate of Zn and Ge reaches 99.61% and 88.29%, respectively. The leaching rates of Zn and Ge by UH were 7.86% and 5.65% higher than that by conventional leaching (CL), respectively. The experimental results showed that UH leaching technology can improve the rates of Zn and Ge from ZOD, reduce the leaching temperature, save the production cost, solve the problem of low leaching rates of Zn and Ge in ZOD treatment technology, and realize the resource, reduction and harmless treatment of ZOD.
1. Introduction
Germanium is a very important strategic resource, which has been widely used in many fields, including aerospace, optical fiber communication, semiconductor, photocell, electronic equipment, and biomedicine.1–3 It is estimated that the content of germanium in the crust is in the range of 1–7 ppm, but it is difficult to extract because of its strong dispersion and is concentrated only in some minerals.4 All germanium products are extracted from smelting residue, and the main raw material of germanium produced in China is lead-zinc smelting residue.5–7 In zinc-lead smelting, most germanium in zinc and lead concentrate is retained in zinc leaching residue and lead smelting residue, respectively. ZOD is obtained from the pyrometallurgical process, which is mainly obtained by fuming zinc-leaching residue in a rotary kiln or lead smelting slag in fuming furnace.8,9 The ZOD thus obtained usually contains 500–1000 g t−1 germanium, which is an important secondary resource for Ge production in China.10
At present, the CL process of recovering germanium from ZOD is leaching the dust with sulfuric acid as solvent, dissolving germanium and zinc in the solution, separating them from insoluble PbSO4 and other impurities, and then separating and extracting Zn and Ge from the solution. However, the data of enterprises and laboratories show that the recovery rates of Zn and Ge are only 80–90% and 60–85%, respectively, with the CL process.11–13 Researchers have studied many enhanced leaching methods to improve the leaching rates of Zn and Ge. Wang studied microwave alkaline roasting combined with water-soluble ZOD, and the leaching rate of Ge was 97.38%.14 It is found that in the appropriate temperature range, microwave calcination can cause the fragmentation of large particles in ZOD, reducing the particle size of ZOD, improve the size uniformity, and make some insoluble phases disappear, which is conducive to the leaching of germanium. However, due to the high economic cost and strict equipment requirements, and the process is not suitable for commercial use. The sulfur affinity of germanium makes it enriched in some sulfides in lead-zinc ores, such as sphalerite (ZnS) and galena (PbS). Germanium enters the sphalerite lattice as isomorphism, which is the biggest feature of germanium enrichment in sulfides.15,16 The results of Nigel et al.17 show that Ge is preferentially incorporated into iron-rich sphalerite or coexisting sphalerite and wurtzite. Jiang confirmed that germanium in ZOD mainly exists in galena, lead oxide, and other minerals.18 However, ZnS and PbS in ZOD cannot be leached in the leaching process without oxidant, which may be one of the main reasons for Ge loss.
Ultrasonic technology is a kind of advanced oxidation technology developed recently.19 Ultrasonic waves stimulate cavitations in chemical compounds resulting in the formation of strong and active radicals such as OH˙, H˙, and H2O2. These free radicals have strong oxidizing properties and can quickly oxidize sulfides. These radicals may react with collapsing bubbles and form new molecular structures, or radicals may be transformed into a state whereby the inner liquid becomes active. Water sonolysis produces hydroxyl and hydrogen active radicals.20,21 Ultrasonic technology have cavitation effect, the thermal effect, and mechanical stirring effect.22 At present, ultrasonic technology is often used as a mineral-enhanced leaching method to improve the leaching rate of valuable metals in minerals.
For example, ultrasonic technology is used to improve the leaching rate of Cu in tailings, the removal of chromium from polymetallic sludge, the extraction of CO from waste lithium-ion batteries, and the extraction of silver from solid waste residue.23–26 Ultrasonic technology has obvious advantages in improving the recovery rate of valuable metals in minerals. Barrera Godinez et al.27 studied the ultrasonic-assisted leaching of pellets from EAF dust treated by two kilns using acidified calcium chloride. They proved that ultrasonic is beneficial to improve zinc recovery from dust in an arc furnace. Zhang et al.28 studied the comparative study of ultrasonic enhancement and CL on the germanium-leaching rate. They found that the recovery of germanium can reach 92.7% under the optimum conditions of ultrasonic enhanced leaching (reaction temperature 80 °C and 40 min). The maximum-leaching rate of Ge in CL is only 83.35%, and the leaching time of CL is 100 min. Jiang et al.29 studied the method for recovering cobalt and lithium from waste lithium-ion battery by ultrasonic-assisted leaching. They have proved that ultrasonic leaching has a higher leaching rate under the same conditions than through CL.
Based on this background, the main purpose of this research work was to study the UH combined oxidation-leaching process leaching of ZOD in a laboratory-scale device and under atmospheric pressure conditions, careful study of the ultrasonic hydrogen peroxide-enhanced acid leaching process, and to optimize the leaching conditions and improve the leaching rates of Zn and Ge. Therefore, the effects of ultrasonic power, the dosage of H2O2, leaching temperature, leaching time, liquid/solid mass ratio, and initial acidity on the leaching rates of Zn and Ge were studied. This study has the significance of sustainable development for the effective use of solid waste resources, reducing waste generation, and improving production efficiency.
2. Experiments
2.1. Materials and methods
The ZOD collected from a zinc smelter in Yunnan Province of China was produced by the pyrometallurgical process of zinc-leaching residue. The ZOD sample was prepared at 105 °C to remove moisture and ground to 200 μm. In addition, all other reagents used for leaching experiments and chemical analysis are analytically pure (purity greater than 99.9%). Deionized water was used in all experiments. Table 1 lists the XRF quantitative analysis results of ZOD. ZOD is mainly composed of 49.65 wt% Zn, 15.92 wt% Pb, 4.70 wt% S, 3.02 wt% Fe, 0.99 wt% As, 620.4 g t−1 Ge and 0.58 wt% Si. ZOD is a light gray powder, and the main phases are PbSO4, PbS, and ZnS (Fig. 1).
Table 1 Main chemical composition of ZOD
Element |
Zn |
Pb |
S |
Fe |
As |
Ge |
Si |
Content, wt% |
49.65 |
15.92 |
4.70 |
3.02 |
0.99 |
620.4 g t−1 |
0.58 |
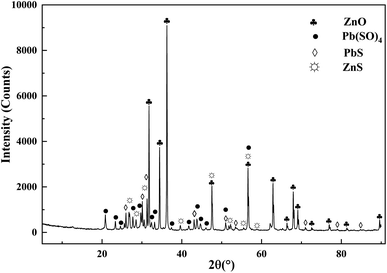 |
| Fig. 1 XRD pattern of ZOD. | |
2.2. Leaching experimental
Fig. 2 shows the flowchart of the leaching experimental device. The leaching experiment of ZOD was conducted in a 250 mL flask. During the experiment, the flask was placed in a constant temperature magnetic stirrer. The H2SO4 (100–200 g L−1) solution was added to the flask, and intelligent ultrasonic equipment with an ultrasonic frequency of 19.5 kHz was used to enhance oxidation leaching with a strong oxidant hydrogen peroxide. The reflux condenser was equipped to prevent the evaporation of the solution. A lid was used on the container to ensure sealing. After the solution was heated to the preset temperature (50–90 °C), the ZOD sample was weighed according to the predetermined liquid/solid mass ratio (4–8
:
1), then it was added to the solution, H2O2 (6–29.5 mL) was added slowly. The ultrasonic equipment was turned on, and then leaching was performed for 30–240 min at a stirring speed of 400 rpm. After the reaction, the mixture was filtered and precipitated. After washing and drying, the concentrations of Zn and Ge in the filtrate and leaching residue were analyzed.
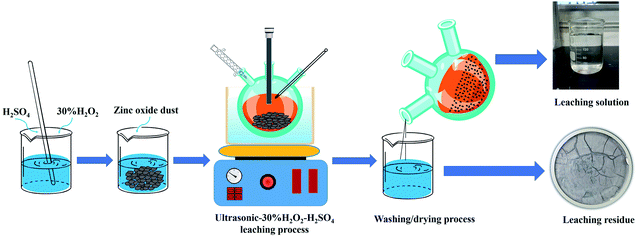 |
| Fig. 2 Schematic of the leaching experimental setup. | |
2.3. Analysis and characterization
X-ray fluorescence (XRF) spectrometry was used to analyze the chemical compositions of the concentrate. To know the phase composition of ZOD and leaching residue, they were analyzed using X-ray diffraction (XRD, Philips pw1825). The surface microstructure of leaching residue was analyzed using a scanning electron microscope and an energy spectrometer (EDS) with the equipment model Nova-NanoSEM-450. EPMA-1720 series electron microprobes (15 kV and 10 nA) were used to determine the distribution of main elements in the leaching residue. Further, an inductively coupled plasma spectrometer (PlasmaQuant PQ9000) was used to analyze the elemental content of Zn and Ge in the solution sample. The contents of zinc and germanium in minerals and solutions were determined using inductively coupled plasma atomic emission spectrometry.
The leaching rate of metal was calculated using eqn (1):
|
 | (1) |
where
λMe (%) is the leaching rate of the metal,
θMe (g L
−1) is the concentration of a metal ion in the leaching solution,
V (L) is the volume of the leaching solution,
θ0Me is the metal content of ZOD, and
m (g) is the mass of the ZOD.
3. Results and discussion
3.1. Effect of dosage of H2O2 on metal-leaching rate
To explore the effect of the dosage of H2O2 on the leaching rates of Zn and Ge in ZOD, the following experiments were designed. The leaching rates of Zn and Ge are shown in Fig. 3, when the initial acidity concentration was 160 g L−1, the leaching temperature was 90 °C, the stirring speed was 400 rpm, the liquid/solid mass ratio was 5
:
1, and the dosage of H2O2 was 6–29.5 mL. It can be seen from Fig. 3 that the amount of hydrogen peroxide has little effect on the leaching rate of zinc. The leaching rate of Ge first increased and then decreased with the increase in the dosage of H2O2, reaching the maximum value of 81.48% at 14.8 mL. The implied decrease in the leaching rate can be explained in terms of the concentration of hydrogen peroxide being too high. Hydrogen peroxide also acts as a hydroxyl radical scavenger, producing the much less reactive
radical. This effect becomes significant at higher hydrogen peroxide concentrations, leaving less hydroxyl radical available for the oxidation of compounds.30,31 Therefore, with the increase in hydrogen peroxide concentration, the oxidation process weakens, and the leaching rate decreases. When H2O2 peroxide is excessive, it reacts with ferrous to oxidize ferrous to ferric. Ferric will hydrolyze to form Fe(OH)3 colloid, which may precipitate leached germanium and cause germanium loss. Therefore, the optimal dosage of H2O2 is 14.8 mL.
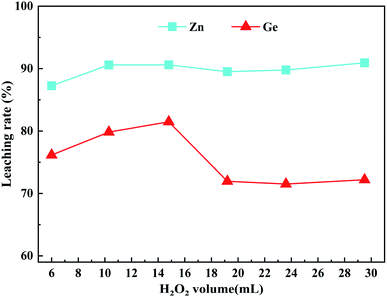 |
| Fig. 3 Effect of dosage of H2O2 on metal-leaching rate. | |
3.2. Effect of leaching time on metal-leaching rate
For industrial applications, increasing leaching time will greatly increase the economic cost. Therefore, it is very important to determine the optimal leaching time for the industrialization of this method. To explore the effect of leaching time on the leaching rates of Zn and Ge in ZOD, according to the above experiments, the optimal dosage of H2O2 is 14.8 mL, the initial acidity is 160 g L−1, the leaching temperature is 90 °C, the stirring speed is 400 rpm, and the liquid/solid mass ratio is 5
:
1. The leaching rates of Zn and Ge are obtained in this time range as shown in Fig. 4. As the leaching time was increased from 30 min to 60 min, the leaching rate increased rapidly, and the leaching rates of Zn and Ge reached the maximum after 60 min, which was 90.6% and 81.48%, respectively. This indicates that a 60 min reaction is sufficient to extract most of the Zn and Ge from ZOD. The rapid increase in the leaching rate is because the hydroxyl radical is short-lived, if an extremely potent oxidizing agent, which can oxidize mineral through hydrogen abstraction, electrophilic addition, or electron-transfer reactions is used, a higher reaction rate can be achieved in the early stage of leaching.32 Considering the leaching rate and the production cost, the optimal leaching time is 60 min.
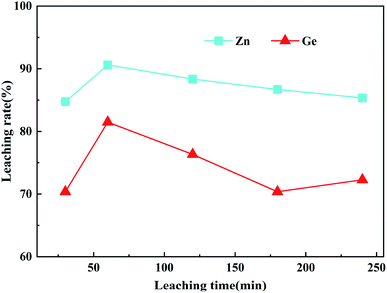 |
| Fig. 4 Effect of leaching time on metal-leaching rate. | |
3.3. Effect of initial acidity on metal leaching rate
The effect of initial acidity on the leaching rates of Zn and Ge was studied by changing the initial acidity between 100–200 g L−1 under the conditions of fixed optimal dosage of H2O2 (14.8 mL), leaching temperature (90 °C), leaching time (60 min) and stirring speed (400 rpm). Fig. 5 shows that the extraction of Zn and Ge from ZOD is strongly dependent on the concentration of H2SO4. The leaching rate increases with increases in H2SO4 dosing until 160 g L−1. When the concentration of H2SO4 is 160 g L−1, the leaching rates of Zn and Ge reach the highest value, which is 90.6% and 81.48%, respectively. With a further increase of H2SO4 concentration, the leaching rates of Zn and Ge decrease. This may be due to the high concentration of H2SO4 at the beginning of the experiment, so the reaction speed is fast, which leads to the formation speed of PbSO4, CaSO4, and other substances, making them cover the ZOD surface, resulting in the reduction of the contact area between H2SO4 and zinc-containing substances, or the failure of sulfuric acid to further react with germanium containing compounds such as germanium oxide and germanium dioxide in the dust, resulting in the decrease of zinc and germanium-leaching rate. Therefore, the optimal initial acidity in the following test is 160 g L−1.
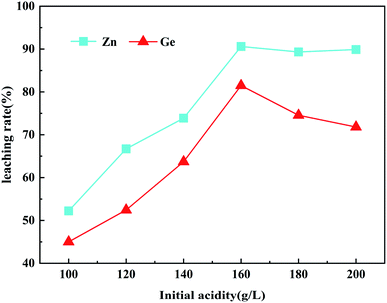 |
| Fig. 5 Effect of initial acidity on the metal-leaching rate. | |
3.4. Effect of liquid/solid mass ratio on metal leaching rate
The effect of liquid/solid mass ratio from 4
:
1 to 8
:
1 on the leaching rates of Zn and Ge was studied under the conditions of optimal H2O2 dosage of 14.8 mL, leaching time of 60 min, initial acidity of 160 g L−1, fixed leaching temperature of 90 °C, and stirring speed of 400 rpm. It can be seen from Fig. 6 that the leaching rates of Zn and Ge increase with the increase of the liquid/solid mass ratio. When the liquid/solid mass ratio is 8
:
1, the leaching rate of Zn reaches a maximum of 96.63%. When the liquid/solid mass ratio is 7
:
1, the leaching rate of Zn is 95.65%, and the leaching rate of Ge reaches the maximum value of 85.90%. When the liquid/solid mass ratio is 8
:
1, the leaching rate of Zn is 96.63%, but the leaching rate of Ge drops to 84.64%. If you continue to increase the liquid/solid mass ratio, Ge begins to decrease, and increasing the liquid/solid mass ratio will also increase the cost of leaching. Studies have shown that an appropriate increase in the liquid/solid mass ratio helps to promote the mass transfer process at the solid–liquid interface.33,34 With the increase of the liquid/solid mass ratio, the higher the final acidity of the leaching solution, a large amount of iron will be leached into the solution, and the high concentration of iron ions in the leaching solution will have a greater impact on the recovery of germanium in the subsequent process. Therefore, considering the cost and iron ion, the best liquid/solid mass ratio is 7
:
1.
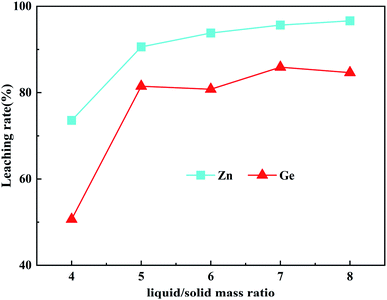 |
| Fig. 6 Effect of liquid/solid mass ratio on the metal-leaching rate. | |
3.5. Effect of leaching temperature on the metal-leaching rate
To explore the influence of leaching temperature on the leaching rates of Zn and Ge in ZOD, the following experiments were designed to explore the factors. According to the above experiments, the optimal dosage of H2O2 was selected as 14.8 mL, the liquid/solid mass ratio was 7
:
1, the leaching time was 60 min and the initial acidity was 160 g L−1, and the fixed stirring speed was 400 rpm, and the leaching temperature changed from 50 °C to 90 °C. The leaching rates of Zn and Ge obtained in this temperature range are shown in Fig. 7. When the temperature reached 60 °C, the leaching rates of zinc and germanium were 95.47% and 84.82%, respectively. When the temperature continued to rise to 90 °C, the leaching rates of zinc and germanium reached the maximum values of 95.65% and 85.90%, respectively. The leaching rate of zinc and germanium at a temperature of 60 °C and 90 °C is not much different. Studies by Kida et al.31 have shown that the decomposition rate of hydrogen peroxide increases with the increase of temperature. Higher temperatures cause hydrogen peroxide to rapidly lose its oxidability. After adding hydrogen peroxide, the leaching process could achieve good results even under low temperature and no pressure conditions. Considering the metal-leaching rate and economic cost comprehensively, 60 °C is selected as the best leaching temperature.
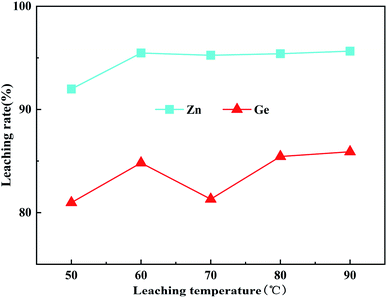 |
| Fig. 7 Effect of leaching temperature on the metal-leaching rate. | |
3.6. Effect of combined ultrasonic process and H2O2
When the aqueous solution is irradiated with ultrasound in the presence of H2O2, the ultrasound will generate hydroxyl radicals through cavitation. Hydroxyl radicals have a high oxidation potential and can quickly oxidize sulfides; however, hydroxyl radicals have a short lifespan and tend to combine with each other to form H2O2.35,36 Nikfar et al.30 have shown that ultrasound assistance will promote H2O2 to decompose more hydroxyl radicals.
To explore the optimal conditions of the UH peroxide-combined process, in the presence of hydrogen peroxide, and to study the effect of ultrasonic power on the leaching rate of Zn and Ge in ZOD, the following experiment was designed: according to the above experiment, the optimal dosage of H2O2was 14.8 mL, the liquid/solid mass ratio was 7
:
1. The stirring speed was 400 rpm, the leaching temperature was 60 °C, the leaching time was 60 min, and the initial acidity was 160 g L−1. The leaching experiment was conducted by using ultrasonic equipment with an ultrasonic frequency of 19.5 kHz and ultrasonic power varying from 100 W to 600 W.
It can be seen from Fig. 8 that with the increase of ultrasonic power, the leaching rates of Zn and Ge begin to increase, reaching the maximum value when the ultrasonic power is 200 W, and the maximum-leaching rates of Zn and Ge are 99.61% and 88.29%, respectively. When the ultrasonic power is less than 200 W, the leaching rates of Zn and Ge decrease, which may be due to the low intensity of ultrasonic energy in the solution, which cannot produce a good mechanical effect and cavitation effect, and the low ultrasonic power is not enough to produce strong oxidizing hydroxyl radicals.29 When ultrasonic power was 200 W, the leaching rates of Zn and Ge were the highest, which may be due to the synergistic effect of 200 W ultrasonic power with hydrogen peroxide and sulfuric acid in the leaching solution under the current acidic conditions, which can enhance the leaching rates of Zn and Ge, especially when the ultrasonic power is 200 W, this may be due to the stronger cavitation effect of 200 W ultrasonic wave and the encapsulated germanium ions, which make the decomposition rate of germanium increase sharply.
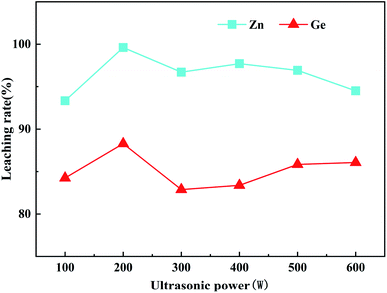 |
| Fig. 8 Effect of ultrasonic power on the metal-leaching rate. | |
When the ultrasonic power exceeds 200 W, the leaching rate begins to decrease. Many researchers have also encountered a situation where high ultrasound power causes a decrease in output. Jiang et al.29 studied changing ultrasonic power without changing the concentration of hydrogen peroxide and found that the ultrasonic power was too high, but did not observe the decomposition of H2O2. After an exhaustive literature review, it can be concluded that the negative effects of high-power ultrasound in this experiment may be due to the following two reasons. Zhang et al.28 found that the coalescence of bubbles generated by cavitation is a reaction under high ultrasound power. The main reason for the weakening. Daryabor et al.37 reported that due to the action of ultrasound, the cycle time of compression and decompression becomes very short, so liquid molecules will not separate to form voids under very high power. Therefore, ultrasonic cavitation cannot work. Therefore, the best ultrasonic power is 200 W.
Under the optimized condition of CL (liquid/solid mass ratio is 7
:
1, stirring speed is 400 rpm, leaching temperature is 60 °C, leaching time is 60 min, initial acidity is 160 g L−1), the influence of hydrogen peroxide oxidation process and UH peroxide combined process on metal leaching rate was studied.
As shown in Fig. 9, the use of hydrogen peroxide alone is better than that of conventional leaching. Compared with the process used alone, the combined process is more effective in improving the leaching rate of zinc and germanium. This is because of the synergistic effect of these two mechanisms on oxidation. These mechanisms include ultrasonic cavitation and hydrogen peroxide oxidation. During the research process, the number of hydroxyl radicals affected the oxidation rate of the substance. In terms of the number of free radicals, the combined system is more than the ultrasonic or hydrogen peroxide single system, and the rate of the combined oxidation system is higher than that of the single system.38,39
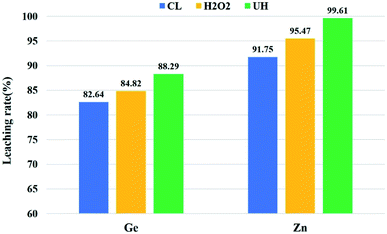 |
| Fig. 9 Under the best conditions, the comparison of the effects of the conventional (CL), H2O2 and combined processes (UH). | |
3.7. Characterization of leaching residue
CL leaching residue was obtained under the conditions of leaching temperature 60 °C, initial acidity 160 g L−1, liquid/solid mass ratio 7
:
1, leaching time 60 min. The leaching rates of Zn and Ge were 91.75% and 82.64%, respectively. The UH leaching residue was obtained at 200 W ultrasonic power and 14.8 mL H2O2 based on CL. The leaching rates of Zn and Ge were 99.61% and 88.29%, respectively.
Table 2 lists the XRF quantitative analysis results of UH leaching residue. After chemically dissolving the leaching residue, inductively coupled plasma emission spectrometry (ICP-OES) was used to determine the germanium content in the leaching residue. The Ge content was 72.65 g t−1. The UH leaching residue is mainly composed of 45.41 wt% Pb, 0.55 wt% Zn, 12.22 wt% S, 2.58 wt% Fe, 0.30 wt% As, 0.23 wt% K, 1.93 wt% Si, 1.23 wt% Al, and 72.65 g t−1 Ge. Comparing and observing the chemical composition of ZOD in Table 1, the content of zinc and germanium in the UH leaching residue was significantly reduced, and the content of lead was significantly increased, indicating that most of the Zn and Ge were leached and lead was enriched. The UH leaching residue is mainly lead-silver slag with a Pb content of as high as 45.41 wt%, which can be returned to lead smelting enterprises as raw materials for lead smelting.
Table 2 Main chemical composition of UH leaching residue
Element |
Pb |
Zn |
S |
Fe |
As |
K |
Si |
Al |
Content, wt% |
45.41 |
0.55 |
12.22 |
2.58 |
0.30 |
0.23 |
1.93 |
1.23 |
The XRD patterns of the leaching residues are shown in Fig. 10. The compositions of the two leach residues are the same, and they are mainly composed of PbSO4 and a small amount of PbS and ZnS. By observing the diffraction peaks of PbS and ZnS, it can be found that the diffraction peaks of PbS and ZnS in UH leaching residue are fewer than those in CL leaching residue, which indicates that UH leaching technology can effectively leach most PbS and ZnS, while PbSO4 still exist, which indicates that UH leaching technology has no leaching effect on PbSO4.
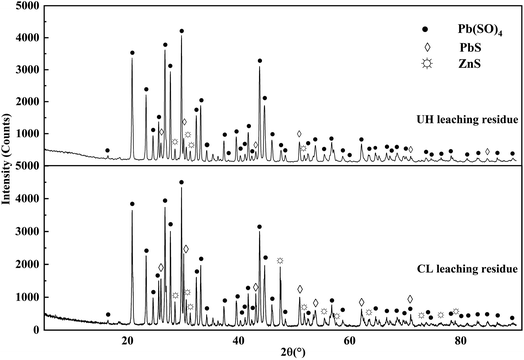 |
| Fig. 10 XRD pattern of characterization of the leaching residue. | |
To intuitively understand the leaching residue, the CL-leaching residue (Fig. 11a) and UH leaching residues (Fig. 11b–e) were analyzed using SEM and EDS (Tables 3 and 4). The morphology of leach residues from the two samples is similar, and they all contain tetragonal, rod-shaped, spherical, and near-spherical particles. There are many spherical structures in the leaching residue, which are mainly composed of lead but contain a small number of other metal elements. Jiang40 and others classified this spherical structure as Pb-based spheres containing impurity elements (such as zinc and sulfur). During the leaching process, PbO (or Pb) on the surface of the Pb-based ball is transformed into PbSO4, which forms a shielding layer to block the reaction between sulfuric acid and the material in the ball, resulting in a variety of metals remaining in the leaching residue. The Pb-based ball prevents the leaching of Zn and Ge, and then Zn and Ge enter the leaching residue, resulting in the loss of Zn and Ge. It can be seen from the results in Table 4 and Fig. 11 that Ge is detected at point 5 of the spherical structure, while the absence of Ge in other regions indicates that Ge is mainly wrapped by Pb-based spheres. This is consistent with the results of Jiang et al.40 By observing CL leaching residue (Fig. 11a) and UH leaching residue (Fig. 11b–e), it was found that the spherical structure of UH is leaching more residue, and the spherical structure is mainly composed of PbSO4, PbS, and SiO2, which indicates that the spherical Pb-based shell is formed during the leaching process of coating or capture Zn and Ge, which may be the main reason for the low zinc-leaching rate. In conclusion, ZnS and PbS are partially leached under UH leaching technology, while PbSO4, SiO2, and ZnFe2O4 are difficult to leach.
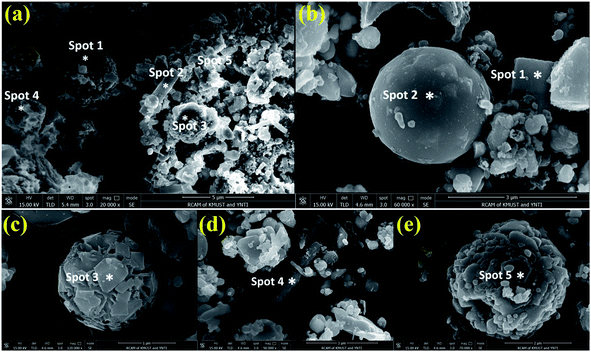 |
| Fig. 11 SEM images of different leaching residues: (a) CL leaching residue, (b–e) UH leaching residue. | |
Table 3 Contents of main elements in designated areas in EDS analysis results of CL leaching residue
Item |
Spot 1, wt% |
Spot 2, wt% |
Spot 3, wt% |
Spot 4, wt% |
Spot 5, wt% |
Zn |
1.4 |
42.0 |
10.7 |
3.2 |
6.4 |
Pb |
19.1 |
4.5 |
0.8 |
30.5 |
15.8 |
O |
76.6 |
44.1 |
84.3 |
61.8 |
74.3 |
S |
2.9 |
9.1 |
0.2 |
4.6 |
3 |
Si |
— |
0.1 |
— |
— |
— |
Fe |
— |
0.1 |
4.0 |
— |
0.5 |
Main phase |
PbSO4, PbS |
PbSO4, PbS, ZnS |
PbSO4, ZnS |
PbSO4, PbS |
PbSO4, PbS, ZnS |
Other phases |
ZnS |
SiO2, ZnFe2O4 |
ZnFe2O4 |
ZnS |
ZnFe2O4 |
Table 4 Contents of main elements in designated areas in EDS analysis results of UH leaching residue
Item |
Spot 1, wt% |
Spot 2, wt% |
Spot 3, wt% |
Spot 4, wt% |
Spot 5, wt% |
Zn |
56.01 |
14.1 |
26.7 |
47.8 |
5.46 |
Pb |
7.8 |
11.1 |
22.4 |
20.1 |
72.3 |
O |
9.7 |
45.3 |
31.0 |
10.2 |
15.0 |
S |
26.4 |
— |
4.2 |
21.9 |
6.52 |
Si |
— |
25.5 |
12.0 |
— |
0.08 |
Fe |
— |
3.9 |
3.7 |
— |
0.54 |
Ge |
— |
— |
— |
— |
0.09 |
Main phase |
ZnS |
SiO2, PbO |
PbSO4, PbS, ZnS |
ZnS |
PbSO4, PbS |
Other phases |
PbSO4, PbS |
ZnFe2O4 |
SiO2, ZnFe2O4 |
PbSO4, PbS |
ZnS, SiO2, GeO2, ZnFe2O4 |
Fig. 12 shows BSE image (a) and EPMA element image ((b) and (c)) of CL leaching residue, BSE image (d) and EPMA element image ((e) and (f)) of UH leaching residue. The element distribution of zinc and sulfur is almost the same, which indicates that the zinc-bearing minerals of the two leaching residues are all ZnS. By observing (b), (c), (e) and (f) in Fig. 12, it is found that the brightness of Zn and S elements in Fig. 12b and e is reduced, indicating that part of ZnS composed of Zn and S is leached. It shows that UH leaching technology can leach part of ZnS and improve the leaching rates of Zn and Ge.
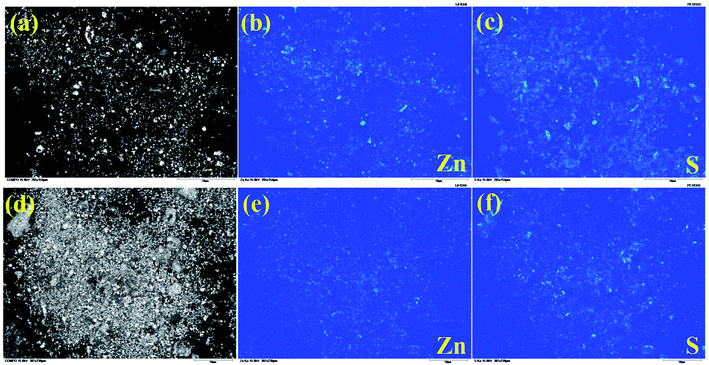 |
| Fig. 12 BSE image (a) and EPMA element image (b and c) of CL leaching residue and BSE image (d) and EPMA element image (e and f) of UH leaching residue. | |
4. Conclusions
(1) Ultrasonic-H2O2(UH) combined oxidation-leaching process is a new method to extract Zn and Ge from ZOD. High efficient leaching of Zn and Ge from ZOD can be achieved by the combination of ultrasonic and hydrogen peroxide enhanced oxidation. The results show that the optimum leaching conditions are as follows: ultrasonic power 200 W, the dosage of H2O2 14.8 mL, initial acidity 160 g L−1, liquid/solid mass ratio 7
:
1, leaching time 60 min, stirring speed 400 rpm, leaching temperature 60 °C, the leaching rates of Zn and Ge reached 99.61% and 88.29%, respectively, which is 7.86% and 5.65% higher than those for CL. The problem of low leaching rates of Zn and Ge from ZOD was solved.
(2) On one hand, ultrasonic technology was used for obtaining evenly dispersion of hydrogen peroxide in the solution, reducing the particle size of the soot, strengthening the contact area between hydrogen peroxide and ZOD, and improve the oxidation efficiency and reaction rate. On the other hand, using the cavitation effect and chemical effect of ultrasonic to accelerate the decomposition of hydrogen peroxide to produce hydroxyl radicals (OH˙) with stronger oxidizing ion than hydrogen peroxide, and its thermal effect makes the reaction medium temperature rise, which accelerates the decomposition rate of hydrogen peroxide, to save the dosage of H2O2, increasing the reaction rate, oxidizing and decomposing sulfide, and improving the leaching rates of Zn and Ge.
(3) In this process, hydrogen peroxide was used to oxidize, no new impurity ions are introduced, and no harmful components are left in the leaching solution after leaching, which has no adverse effect on the subsequent process. The decomposition product of hydrogen peroxide is water, which is friendly to the environment.
Nomenclature
ZOD | Zinc oxide dust |
UH | Ultrasonic-H2O2 |
CL | Conventional leaching |
Author contributions
Conceptualization and supervision: H. Xia; investigation: C. Xin, Q. Zhang, and W. Zhang; characterization: C. Xin; project administration: H. Xia; writing-original draft: C. Xin; review and editing: H. Xia; funding acquisition: H. Xia and L. Zhang. All authors have read and agreed to the published version of the manuscript.
Conflicts of interest
The authors declare that they have no known competing financial interests or personal relationships that could have appeared to influence the work reported in this paper.
Acknowledgements
This work was supported by the General Project of National Natural Science Foundation of China (51974141), Yunnan Province Basic Research Special Key Project (No. 202001AS070009), Special Fund Projects of Central Government Guiding Local Science and Technology Development (No. 202107AA110002), Yunnan Ten Thousand Talents Plan Industrial Technology Talents Project (No. 2019-1096), Yunnan Ten Thousand Talents Plan Young & Elite Talents Project (No. 2018-73).
References
- J. K. Wang, and A. P. He, Modern germanium metallurgy, Metallurgical Industry Press, Beijing, 2005 Search PubMed.
- L. Zhang and Z. Xu, A critical review of material flow, recycling technologies, challenges and future strategy for scattered metals from minerals to wastes, J. Cleaner Prod., 2018, 202, 1001–1025 CrossRef.
- K. Kuroiwa, S. I. Ohura, S. Morisada, K. Ohto, H. Kawakita and Y. Matsuo, Recovery of germanium from waste solar panels using ion-exchange membrane and solvent extraction, Miner. Eng., 2014, 55, 181–185 CrossRef CAS.
- F. A. Torralvo, C. Fernández-Pereira, E. G. Villard, Y. Luna, C. Leiva, L. Vilches and R. Villegas, Low environmental impact process for germanium recovery from an industrial residue, Miner. Eng., 2018, 128, 106–114 CrossRef.
- R. R. Moskalyk, Review of germanium processing worldwide, Miner. Eng., 2004, 17, 393–402 CrossRef CAS.
- F. Liu, Z. Liu, Y. Li, Z. Liu, Q. Li and L. Zeng, Extraction of gallium and germanium from zinc refinery residues by pressure acid leaching, Hydrometallurgy, 2016, 313–320 CrossRef.
- R. Höll, M. Kling and E. Schroll, Metallogenesis of germanium—A review, Ore Geol. Rev., 2007, 30, 145–180 CrossRef.
- J. Su, Discussion on the technological process of comprehensive recovery of germanium from carbonate lead zinc oxide ore, Nonferrous Met., 1974, 12, 6–10+5 Search PubMed.
- Z. X. Li, C. Y. Wang, X. M. Yin and M. Z. Gao, Extraction of germanium and zinc from germanium-bearing zinc oxide dust, Nonferrous Met., 2017, 09, 45–47+53 Search PubMed.
- T. Zhang, T. Jiang and Z. Liu, Recovery of Ge (IV) from synthetic leaching solution of secondary zinc oxide by solvent extraction using tertiary amine (N235) as extractant and trioctyl phosphate (TOP) as modifier, Miner. Eng., 2019, 136, 155–160 CrossRef CAS.
- W. Q. Fu, D. J. Yang, W. Zou, J. C. Liu, X. B. Mu and Z. B. Zhai, Study on high-efficient leaching of zinc and germanium from zinc oxide dust bearing germanium with atmospheric-pressure leaching process, Nonferrous Met., 2018, 08, 48–51 Search PubMed.
- J. L. Li, M. Mao and L. F. Yu, Improving germanium recovering technology in zinc hydrometallurgy, Yunnan Metallurgy, 2011, 40, 40–45 Search PubMed.
- Y. Q. Yang, C. Y. Wang, W. J. Yang, W. H. Yuan and P. Xing, Study of leaching of indium, germanium and zinc from zinc calcining, Nonferrous Met., 2014, 07, 11–13 Search PubMed.
- W. K. Wang, Recovery of germaniu m from zinc oxide dust containing germanium by microwave roasting, Kunming University of Science and Technology, 2013 Search PubMed.
- V. V. Seredin, From coal science to metal production and environmental protection: A new story of success, Int. J. Coal Geol., 2012, 90, 1–3 CrossRef.
- M. Frenzel, M. P. Ketris and J. Gutzmer, On the geological availability of germanium, Miner. Deposita, 2014, 49, 471–486 CrossRef CAS.
- C. Nigel, E. Barbara, C. Cristiana, G. Kalotina, H. Daryl, W. Timothy, R. Nick, P. Allan, G. Chen and J. Bernt, Distribution and Substitution Mechanism of Ge in a Ge-(Fe)-Bearing Sphalerite, Minerals, 2015, 5, 117–132 CrossRef.
- T. Jiang, T. Zhang, F. Ye and Z. Liu, Occurrence state and sulfuric-acid leaching behavior of germanium in secondary zinc oxide, Miner. Eng., 2019, 137, 334–343 CrossRef CAS.
- I. Hua, R. H. Hoechemer and M. R. Hoffmann, Sonolytic Hydrolysis of p-Nitrophenyl Acetate: The Role of Supercritical Water, J. Phys. Chem., 1995, 99, 2335–2342 CrossRef CAS.
- M. N. Ingale and V. V. Mahajani, A novel way to treat refractory waste: Sonication followed by wet oxidation (SONIWO), J. Chem. Technol. Biotechnol., 2010, 64, 80–86 CrossRef.
- Y. G. Adewuyi, Sonochemistry in Environmental Remediation. 1. Combinative and Hybrid Sonophotochemical Oxidation Processes for the Treatment of Pollutants in Water, Environ. Sci. Technol., 2015, 39, 3409–3420 CrossRef PubMed.
- U. Neis, Ultrasound in water, wastewater and sludge treatment, Water, 2000, 21, 36–39 Search PubMed.
- J. Zhang, A. X. Wu and X. S. Chen, Experimental research in leaching of copper-bearing tailings enhanced by ultrasonic treatment, Int. J. Min. Sci. Technol., 2008, 18, 98–102 CAS.
- P. Zhang, Y. Ma and F. Xie, Impacts of ultrasound on selective leaching recovery of heavy metals from metal-containing waste sludge, J. Mater. Cycles Waste Manage., 2013, 15, 530–538 CrossRef CAS.
- L. Li, X. J. Zhai, X. X. Zhang, J. Lu and K. Amine, Recovery of valuable metals from spent lithium-ion batteries by ultrasonic-assisted leaching process, J. Power Sources, 2014, 262, 380–385 CrossRef CAS.
- M. S. Oncel, M. Ince and M. Bayramoglu, Leaching of silver from solid waste using ultrasound assisted thiourea method, Ultrason. Sonochem., 2005, 12, 237–242 CrossRef PubMed.
- J. A. Barrera-Godinez, T. J. OKeefe and J. L. Watson, Effect of ultrasound on acidified brine leaching of double-kiln treated EAF dust, Miner. Eng., 1992, 5, 1365–1373 CrossRef CAS.
- L. B. Zhang, W. Q. Guo, J. H. Peng, G. Lin and X. Yu, Comparison of ultrasonic-assisted and regular leaching of germanium from by-product of zinc metallurgy, Ultrason. Sonochem., 2016, 31, 143–149 CrossRef CAS PubMed.
- F. Jiang, Y. Chen, S. Ju, Q. Zhu, L. Zhang, J. Peng, X. Wang and J. D. Miller, Ultrasound-assisted Leaching of Cobalt and Lithium from Spent Lithium-ion Batteries, Ultrason. Sonochem., 2018, 88–95 CrossRef CAS PubMed.
- E. Nikfar, M. H. Dehghani, A. H. Mahvi, N. Rastkari and V. K. Gupta, Removal of Bisphenol A from aqueous solutions using ultrasonic waves and hydrogen peroxide, J. Mol. Liq., 2016, 213, 332–338 CrossRef CAS.
- M. Kida, S. Ziembowicz and P. Koszelnik, Removal of organochlorine pesticides (OCPs) from aqueous solutions using hydrogen peroxide, ultrasonic waves, and a hybrid process, Sep. Purif. Technol., 2018, 192, 457–464 CrossRef CAS.
- K. Ikehata and M. G. El-Din, Aqueous pesticide degradation by hydrogen peroxide/ultraviolet irradiation and Fenton-type advanced oxidation processes: a review, J. Environ. Eng. Sci., 2006, 5, 81–135 CrossRef CAS.
- S. Aydogan, A. Aras and M. Canbazoglu, Dissolution kinetics of sphalerite in acidic ferric chloride leaching, Chem. Eng. J., 2005, 114, 67–72 CrossRef CAS.
- S. H. Zhang, T. Li, B. C. Zhu and Z. B. Zhu, Gas–liquid mass transfer in three-phase mechanical agitated reactor, J. Chem. Ind. Eng., 2005, 56, 200–226 Search PubMed.
- N. Min, Q. Wang and G. Qiu, Enhancement of ultrasonically initiated emulsion polymerization rate using aliphatic alcohols as hydroxyl radical scavengers, Ultrason. Sonochem., 2008, 15, 222–226 CrossRef PubMed.
- A. B. Pandit, P. R. Gogate and S. Mujumdar, Ultrasonic degradation of 2:4:6 trichlorophenol in presence of TiO2 catalyst, Ultrason. Sonochem., 2001, 3, 227–231 CrossRef.
- M. Daryabor, A. Ahmadi and H. Zilouei, Solvent extraction of cadmium and zinc from sulphate solutions: Comparison of mechanical agitation and ultrasonic irradiation, Ultrason. Sonochem., 2017, 34, 931–937 CrossRef CAS PubMed.
- M. R. Samarghandi, J. Nouri, A. R. Mesdaghinia, A. H. Mahvi, S. Nasseri and F. Vaezi, Efficiency removal of phenol, lead and cadmium by means of UV/TiO2/H2O2 processes, Int. J. Environ. Sci. Technol., 2007, 4, 19–25 CrossRef CAS.
- E. Naffrechoux, S. Chanoux, C. Petrier and J. Suptil, Sonochemical and photochemical oxidation of organic matter, Ultrason. Sonochem., 2000, 4, 255–259 CrossRef.
- T. Jiang, T. Zhang and Z. Liu, Pb-based aggregate, Ge-galena coexistence, and Ge-anglesite coprecipitate—limitations and an improvement of germanium recovery from secondary zinc oxide via H2SO4 leaching, Hydrometallurgy, 2020, 200, 105543 CrossRef.
|
This journal is © The Royal Society of Chemistry 2021 |
Click here to see how this site uses Cookies. View our privacy policy here.