DOI:
10.1039/D1RA04115K
(Paper)
RSC Adv., 2021,
11, 31807-31816
Barium promoted Ni/Sm2O3 catalysts for enhanced CO2 methanation
Received
27th May 2021
, Accepted 14th September 2021
First published on 27th September 2021
Abstract
Low temperature CO2 methanation is a favorable pathway to achieve high selectivity to methane while increasing the stability of the catalysts. A Ba promoted Ni/Sm2O3 catalyst was investigated for CO2 methanation at atmospheric pressure with the temperature ranging from 200–450 °C. 5Ni–5Ba/Sm2O3 showed significant enhancement of CO2 conversion particularly at temperatures ≤ 300 °C compared to Ni/Sm2O3. Incorporation of Ba into 5Ni/Sm2O3 improved the basicity of the catalysts and transformed the morphology of Sm2O3 from random structure into uniform groundnut shape nanoparticles. The uniformity of Sm2O3 created interparticle porosity that may be responsible for efficient heat transfer during a long catalytic reaction. Ba is also postulated to catalyze oxygen vacancy formation on Sm2O3 under a reducing environment presumably via isomorphic substitution. The disappearance of a high temperature (∼600 °C) reduction peak in H2-TPR analysis revealed the reducibility of NiO following impregnation with Ba. However, further increasing the Ba loading to 15% formed BaNiO3–BaNiO2.36 phases which consequently reduced the activity of the Ni–Ba/Sm2O3 catalyst at low temperature. Ni was suggested to segregate from BaNiO3–BaNiO2.36 at high temperature thus exhibiting comparable activity with Ni/Sm2O3 at 450 °C.
Introduction
Carbon dioxide is a naturally occurring gas occupying ∼0.04% of air in the atmosphere. CO2 is produced from natural processes such as biomass decomposition, or human activities that are associated with the burning of fossil fuel. Primary consumption of fossil fuel as an energy provider results in the rising level of CO2 in the atmosphere. This greenhouse gas contributes to global warming, which ultimately caused a devastating impact to the environment in particular through extreme climate change.1 Current analysis by the UNEP (United Nations Environment Programme) indicated that the global temperature was expected to elevate by more than 2 °C by 2050, and more than 4 °C by 2100.2 Over the years, scientists have investigated multiple approaches to overcome the issue of CO2 emission. Carbon capture and utilization (CCU) has gain worldwide attention as a method to control CO2 emission via conversion of CO2 into useful products such as urea and fuel.3
Since CO2 is continuously emitted from industrial processes, the conversion of CO2 to methane (CH4) was identified as an ideal route to recycle the most oxidative carbon compound into active carbon species.4 Catalytic hydrogenation of CO2 with hydrogen gas produced CH4 and water, which was discovered by Paul Sabatier in 19022 and referred to as the Sabatier reaction or CO2 methanation (eqn. (1)).
|
CO2 + 4H2 ⇌ CH4 + 2H2O, ΔH298 K = −165 kJ mol−1
| (1) |
Since CO2 methanation is an exothermic reaction, production of methane favors a lower reaction temperature. However as a stable molecule, catalyst was required for the reaction to achieve optimum rate. Competing reactions such as carbon formation (eqn (2)) and reverse-water-gas-shift (RWGS) (eqn (3))5 occurred predominantly at high temperatures. High temperature reaction also caused coke deposition that eventually contributed to the deactivation of catalysts.
|
CO2 + 2H2 ⇌ C + 2H2O, ΔH298 K = −90.1 kJ mol−1
| (2) |
|
CO2 + H2 ⇌ CO + H2O, ΔH298 K = 41.2 kJ mol−1
| (3) |
Metal oxides such as Al2O3, TiO2, ZrO2 and CeO2 were commonly investigated as metal supports for Ni-based catalysts.6 Rare earth element was generally used as promoter to enhance CO2 methanation primarily due to the high cost of obtaining the element. Sm2O3 was often investigated as promoter for various catalytic reaction such as water gas shift reaction,7 ammonia synthesis,8 and photocatalytic removal of organic pollutants.9 As promoter in Co/CeO2 catalysts, samarium improved the reducibility of Ce4+ by facilitating the electron transfer from Co to CeO2 and enhanced the surface oxygen vacancies.7 Sm2O3 was reported to enhance Ni dispersion, reduced coke deposition, hence enhanced both stability and activity of Ni/SBA-15 catalyst.10 Ni exhibited high selectivity towards CH4 and inexpensive, in comparison to noble metals.5 The use of alkali and rare earth oxides as promoter further increased the metal-support interaction and metal dispersion.5 However, Ni was easily sintered during rapid temperature increase and exothermic nature of the methanation reaction. Coke deposition onto the active sites of Ni-based catalysts also caused premature deactivation.11 W. J. Lee et al.12 stated that highly dispersed Ni particles can be achieved by essentially enhancing the surface defects of the support.
This research aimed to investigate the ability of rare earth metal oxide, Sm2O3, as active catalyst for CO2 methanation reaction. The potential of Sm2O3 as support for CO2 methanation was relied on its basic properties and redox potential, which was ideal to enhance CO2 adsorption and dissociation. However, studies on Sm2O3 as catalysts support for CO2 methanation was rarely reported. Muroyama et al. showed utilization of Ni/Sm2O3 as catalyst produced a higher CH4 yield when compared to Al2O3, ZrO2, CeO2 and La2O3, although the catalysts showed deactivation within 5 h of the reaction.13 The formation of Sm2O3 xerogel via epoxide addition method showed high activity and thermal stability of Ni/Sm2O3, however 39 wt% of Ni was required to ensure such performances.14 In this work, Ni–Ba/Sm2O3 was investigated as catalysts for CO2 methanation reaction to enhance the activity and the stability of the catalysts. Ba as alkali earth metal was introduced as promoter to enhance the basicity of the catalysts and to improve CO2 adsorption and dissociation.15 Ba showed a high affinity towards CO2 to form carbonate, which was a highly important step towards CO2 decomposition at mild temperatures.16 To our knowledge, studies on the effect of Ba as promoter to enhance Ni/Sm2O3 activity has not yet been reported. Ni–Ba/Sm2O3 catalysts was synthesized using wet impregnation method at variation of Ba loading while using 5 wt% of Ni. The enhanced activity was correlated with the basicity, reducibility and morphology of the catalysts determined using FE-SEM, HRTEM, XRD, H2-TPR, CO2-TPD and XPS analysis.
Results
XRD analysis
Fig. 1a showed the XRD analysis of Sm2O3, 5Ni/Sm2O3 and 5Ni–xBa/Sm2O3 at different Ba loading (x = 5%, 10% and 15%) after calcination in air at 500 °C. The main characteristic peaks of Sm2O3 were observed at 2θ = 28.2°, 32.7°, 46.9° and 55.6° which were indexed to (222), (400), (440) and (622) accordingly (JCPDS 043-1029). Following impregnation with Ni and Ba, some of the Sm2O3 diffraction peaks were disappeared. As seen in Fig. 1b, narrow angle XRD analysis showed NiO peaks on 5Ni/Sm2O3 and 5Ni-xBa/Sm2O3 at 2θ = 38.9° and 42.0°, indexed at (111) and (200) respectively (JCPDS 004-0835), proving that NiO nanoparticles were formed following calcination at 500 °C. However, at 10% of Ba loading, BaNiO3 peak was observed at 2θ = 18.8°, 36.8° and 42.3° (JCPDS 072-0403).17 Increasing the Ba loading to 15%, BaNiO2.36 peaks appeared at 2θ = 21.9°, 38.3°, 48.9° and 50.4° corresponded to (110), (020), (220), (131), (310) and (240) planes respectively (JCPDS 072-0403). BaNiO3 was reported as less stable than BaNiO2.36, which will be decomposed gradually at higher temperatures.18
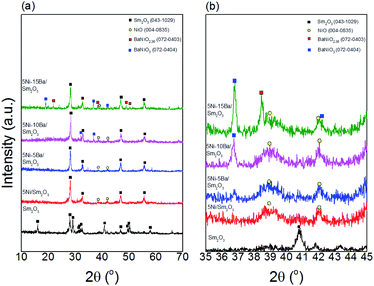 |
| Fig. 1 (a) Wide and (b) narrow angle XRD patterns of pure Sm2O3, 5Ni/Sm2O3 and 5Ni–xBa on Sm2O3 with different Ba loading after calcination at 500 °C. | |
N2 adsorption–desorption analysis
The textural properties of 5Ni/Sm2O3 and 5Ni–xBa/Sm2O3 were analyzed using N2 adsorption–desorption (Fig. 2a). The isotherms of the catalysts were categorized as Type III isotherm with H3-hysteresis loop, according to IUPAC isotherm classification. The H3 loop was related to the adsorbed multi-layer metastability and delayed capillary condensation which occurs in slit-shaped macropores resulted from a low level of pore curvature and flexibility of the aggregate structure.19,20 The increase of Ba loading slightly enhanced the surface area of the catalysts. 5Ni/Sm2O3 showed 9 m2/g, and the surface area was enhanced 14 m2 g−1 for 5Ni–10Ba/Sm2O3. However, the surface area was reduced to 12 m2 g−1 on 5Ni–15Ba/Sm2O3 presumably due to the formation of BaNiO2. Hysteresis loop presence at high relative pressure (p/po > 0.7) implied a broad pore size distribution, comprising both meso- and macropores in the catalysts structure.21 Pore size distribution analysis (Fig. 2b) showed the formation of mesopores on 5Ni–5Ba/Sm2O3 catalyst. A broad pore distribution was observed on 5Ni–5Ba/Sm2O3 with a slight enhanced of pore volume compared to 5Ni/Sm2O3. The data summarized in Table 1 indicated the pore volume was increased to 0.050 cm3 g−1 in 5% Ba loading compared to 0.040 cm3 g−1 in 5Ni/Sm2O3 catalyst.
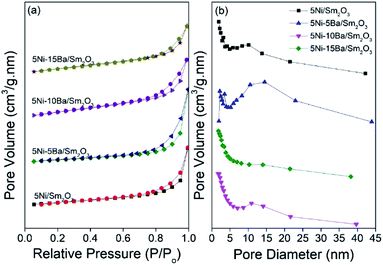 |
| Fig. 2 (a) Nitrogen adsorption–desorption isotherms and (b) pore size distribution of 5Ni/Sm2O3 and 5Ni–xBa/Sm2O3, x = 5%, 10% and 15% after calcination at 500 °C. | |
Table 1 Textural properties of 5Ni/Sm2O3 and 5Ni–xBa/Sm2O3, x = 5%, 10% and 15% Ba loading
Catalyst |
SBET (m2 g−1) |
Pore volume (cm3 g−1) |
Pore size (nm) |
TH2 desorption (°C) |
H2 uptakea (mmol gcat−1) |
CO2 uptakeb (μmol gcat−1) |
H2 consumption obtained from H2-TPR profiles. The amount of adsorbed CO2 was determined from CO2-TPD. N.D – not determined. |
Sm2O3 |
13 |
N.D |
N.D |
410 |
0.74 |
6.9 |
5Ba/Sm2O3 |
N.D |
N.D |
N.D |
526, 555, 863 |
15.8 |
13.2 |
5Ni/Sm2O3 |
9 |
0.0419 |
2, 11 |
412, 516, 635 |
34.5 |
10.0 |
5Ni–5Ba/Sm2O3 |
9 |
0.0532 |
3, 15 |
373, 443, 552 |
40.9 |
18.3 |
5Ni–10Ba/Sm2O3 |
14 |
0.0414 |
— |
386, 538 |
97.9 |
16.5 |
5Ni–15Ba/Sm2O3 |
12 |
0.0342 |
— |
495 |
59.8 |
6.9 |
Morphology analysis
Surface morphology of 5Ni/Sm2O3 and 5Ni–xBa/Sm2O3 catalysts were characterized using FESEM-EDX and HRTEM analysis. Fig. 3a displayed the morphology of 5Ni/Sm2O3 after calcination in air at 500 °C for 3 hours. The SEM image showed a non-uniform crystallites structure with no apparent pattern on the morphology. Following addition of 5% Ba on Ni/Sm2O3, the morphology was significantly changed into interconnected uniform nanoparticles resembled to a groundnut-like structure. The presence of uniform pores was observed from the interaction between particles in 5Ni–5Ba/Sm2O3 catalyst (Fig. 3b). The addition of Ba significantly reduced the size of crystallites to be within nanoscale length. However, following impregnation with 15% of Ba loading, the uniform groundnut-like structures disappeared and turned into non-uniform crystallites. The uniform porosity was no longer visible as the amount of Ba increased to 15% loading (Fig. 3c). The formation of non-uniform morphology of 5Ni–15Ba/Sm2O3 may be associated with the formation of BaNiO3–BaNiO2.36 phases as shown in XRD analysis. EDX analysis was carried out to study the Ni and Ba dispersion on Sm2O3. EDX mapping (Fig. 3d) of 5Ni–5Ba/Sm2O3 showed Ni and Ba particles were evenly dispersed on Sm2O3 surface. The homogeneous dispersion can promote synergetic effect between Ni and Ba to improve CO2 adsorption and to increase catalytic activity.
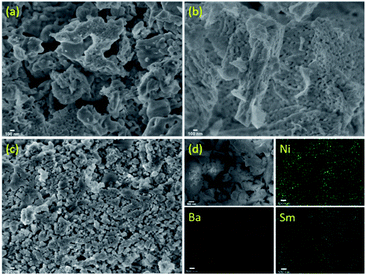 |
| Fig. 3 FESEM images of 5Ni–xBa/Sm2O3 at (a) 0% Ba, (b) 5% Ba, (c) 15% Ba and (d) EDX mapping of 5Ni–xBa/Sm2O3 at 5% Ba after calcination. | |
HRTEM analysis of 5Ni–5Ba/Sm2O3 in Fig. 4a and b showed homogeneous dispersion of NiO nanoparticles. The average NiO particle diameter was determined at approximately 3.5 ± 0.5 nm. The interplanar spacing of NiO nanoparticles was measured at 0.21 nm corresponded to (111) plane (16). The interplanar spacing determined at 0.31 nm was in a good agreement with the Sm2O3 (222) (d222 = 3.142 Å) plane.22 HRTEM analysis of 5Ni–15Ba/Sm2O3 (Fig. 4c and d) estimated the diameter of NiO nanoparticles as 4.5 ± 0.4 nm with interplanar spacing at 0.21 nm. The presence of BaNiO2.36 was evident from 0.28 nm crystal plane adjacent to Sm2O3.23
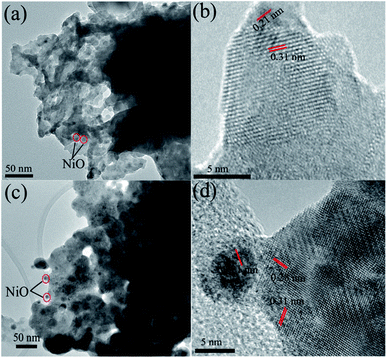 |
| Fig. 4 HRTEM analysis of 5Ni–5Ba/Sm2O3 (a and b) and 5Ni–15Ba/Sm2O3 (c and d) after calcination in air at 500 °C. | |
H2-TPR analysis
H2-TPR analysis of the catalysts provided information on the reducibility of NiO and the metal support interaction (Fig. 5). In general, α-type NiO species peak was located at low-temperature region (300–500 °C) signifying bulk NiO particles. β-Type NiO peak can be seen at mild-temperature region (500–700 °C) demonstrating a weak interaction between NiO and support. Meanwhile a high temperature peak >700 °C was assigned to γ-type NiO species with strong interaction with the support.24–26 Sm2O3 only showed a very low H2 uptake (0.74 mmol gcat−1) suggesting the high stability of Sm2O3 which only slightly reduced to SmO. Following impregnation with 5% Ba on Sm2O3, sharp TPR peaks appeared at 526 °C and 555 °C, and a small peak at much higher temperatures, 863 °C. The amount of H2 uptake was increased to 15.2 mmol gcat−1. The H2 TPR analysis of 5Ba/Sm2O3 was compared with H2 TPR analysis of BaO, which indicated BaO stability under reducing environment. The reduction of Sm2O3 upon Ba addition could be due to migration of Ba2+ to Sm2O3 lattice. The close interaction between Ba2+ and Sm3+ enhanced the reducibility of Sm3+ to Sm2+ thus promoting the formation of oxygen vacancy. The hypothesis was postulated from the behaviour of CeO2 system when doped with cation with a lower charge such as Co2+ that leads to charge compensation.27 This charge compensation mechanism from isomorphic substitution of Ba2+ in Sm3+ enhanced the formation of surface oxygen vacancies.
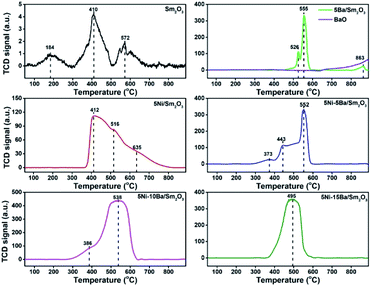 |
| Fig. 5 H2-TPR profiles of 5Ni/Sm2O3, 5Ba/Sm2O3, BaO, and 5Ni–xBa/Sm2O3 at different Ba loading. The catalysts were calcined in air at 500 °C prior to the analysis. | |
All Ni catalysts showed the reduction peaks were formed within α- and β-type ranges and shifted to the lower temperatures with the addition of Ba. 5Ni/Sm2O3 showed a broad reduction peaks at 412 °C, with shoulder peaks at 516 °C and 635 °C. The broad reduction peak formation suggested multiple interaction of NiO species with the Sm2O3 support.26 Large NiO particles required a long reduction time and high temperatures in order to ensure complete reduction into its metallic state, hence displayed a broad reduction peak at high temperature region.21 The H2-TPR profile of 5Ni–5Ba/Sm2O3 showed the appearance of small reduction peak at 373 °C, followed with a broad peak started at 443 °C. A sharp reduction peak at 552 °C showed a similar feature as 5Ba/Sm2O3. Impregnation with 5Ni–5Ba on Sm2O3 also showed the disappearance of NiO reduction peak at 635 °C which implied the incorporation of Ba into 5Ni/Sm2O3 improved the reducibility of NiO nanoparticles. The volume of H2 consumption was also significantly enhanced with increasing Ba loading presumably due to the combination of H2 consumption for NiO reduction and the formation of oxygen vacancies on Ba/Sm2O3. However, the amount of H2 uptake was reduced to 59.8 mmol gcat−1 on 5Ni–15Ba/Sm2O3 presumably due to the formation of BaNiO3–BaNiO2.36 phases restricting the evolution of oxygen vacancies.
CO2-TPD analysis
Surface basicity and distribution of basic sites of 5Ni-xBa/Sm2O3 catalysts at different Ba loadings were determined using CO2-TPD as shown in Fig. 6. CO2 is a weak Lewis acid that can adsorb on the catalysts to distinguish the types and the strengths of basic sites. The CO2 desorption peak at temperature below 100 °C was corresponded to CO2 interaction with a weak basic site on the catalysts surface. This feature was negligible on all catalysts. CO2-TPD analysis of Sm2O3 showed the CO2 desorption peaks centered at 172 °C and 363 °C that were associated with the medium interaction between CO2 molecules and moderate basic sites. The peaks formed in the medium basic site region also indicated the formation of carbonate species on the catalysts surface.28,29 These carbonate species, specifically monodentate carbonate were susceptible towards hydrogenation to form CH4.30 Following impregnation of Sm2O3 with 5% Ba, the amount of CO2 uptake was enhanced from 6.9 μmol gcat−1 on Sm2O3 to 13.2 μmol gcat−1 on 5Ba/Sm2O3. The CO2 desorption peak also slightly shifted to lower temperatures. The results clearly showed the presence of Ba enhanced surface basicity of Sm2O3. No peak associated with the strong interaction between CO2 molecules and basic sites was observed at temperature above 500 °C.21,31 Ni/Sm2O3 also showed enhanced CO2 uptake at 10.9 μmol gcat−1. Synergy between Ni, Ba and Sm2O3 was further evidenced on the increase of desorption peak at 150 °C for 5Ni–5Ba/Sm2O3 compared to 5Ni/Sm2O3 and 5Ba/Sm2O3. The amount of adsorbed CO2 was quantified based on the deconvoluted peak and tabulated in Table 1. The results clearly indicated the addition of Ba into Ni/Sm2O3 tremendously improved the surface basicity of the catalysts through the formation of a new basic sites originating from the Ba.32,33 5Ni–5Ba/Sm2O3 demonstrated the highest CO2 uptake at 16.5 μmol gcat−1. The role of Ba to provide the additional basic sites was further consolidated by the reduction of CO2 uptake on 5Ni–15Ba/Sm2O3 at 6.9 μmol gcat−1. The formation of BaNiO3–BaNiO2.36 as evidenced by the XRD analysis reduced the ability of Ba to increase the surface basicity of the catalyst.
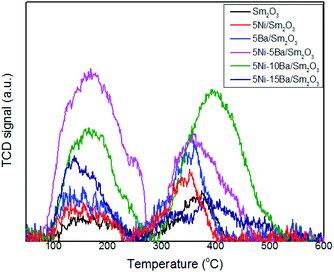 |
| Fig. 6 CO2-TPD profiles of 5Ni/Sm2O3, 5Ba/Sm2O3 and 5Ni–xBa/Sm2O3 with different Ba loading at x = 5%, 10%, 15%. | |
XPS analysis
XPS analysis is a surface analysis method that provided the information of the outer layer of heterogeneous catalysts responsible for catalytic reaction. XPS analysis was conducted following air calcination at 500 °C and reduction at 450 °C (Fig. 7). The presence of Ni and Sm were observed on 5Ni/Sm2O3 and 5Ni–5Ba/Sm2O3, although Ni 3d signal appeared significantly low in intensity due to the low Ni loading. Analysis of O1s XPS spectra between 5Ni/Sm2O3 and 5Ni–5Ba/Sm2O3 indicated the presence bulk lattice oxygen. There were no significant differences on the O1s signal following Ba addition. The Sm 3d XPS signal showed doublet peaks appeared at 1083.8 eV and 1150 eV corresponded to Sm3+ species.34 Ni was analyzed at 856.1 eV and 861.8 eV originated from NiO. However, the Ni0 at 853.1 eV was absent presumably due to the surface oxidation of Ni0 when the catalyst was exposed to air during the transfer process for XPS measurement.35 There were no significant differences on the XPS signal of Sm 3d following impregnation with Ba suggesting that no alteration of Sm3+ oxidation states. The presence of surface oxygen vacancies on Sm2O3 following impregnation with Ba cannot be deduced from the XPS analysis due to the absence of Sm2+ peak generally appeared at binding energy ∼1095.9 eV and 1121.3 eV.36,37 XPS also confirmed that dissolution of Ni or Ba into Sm2O3 lattice did not take place on the 5Ni–5Ba/Sm2O3 catalysts even after reduction at 450 °C.
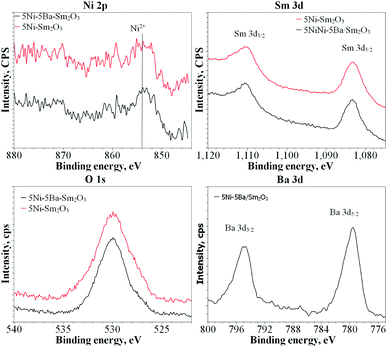 |
| Fig. 7 Ni 2p, Sm 3d, O 1s and Ba 3d XPS spectra of 5Ni/Sm2O3 and 5Ni–5Ba/Sm2O3 after reduction at 450 °C. | |
Catalytic activity
The activity of 5Ni/Sm2O3 and 5Ni–xBa/Sm2O3 on the variation of Ba loading was investigated at 200–450 °C (Fig. 8). No activity was observed at 200 °C, and all the catalysts showed CO2 conversion at 250 °C with 100% selectivity to methane. Increasing the temperature to 300 °C significantly enhanced the conversion of CO2. 5Ni–5Ba/Sm2O3 showed the highest CO2 conversion at 38.9% followed with 5Ni–10Ba/Sm2O3 at 29%. The conversion was significantly higher than 5Ni/Sm2O3 with only 20% at 300 °C. 5Ni–15Ba/Sm2O3 was less active than 5Ni/Sm2O3 at temperature below 350 °C presumably due to the formation of BaNiO2. Evidently, as the amount of Ba loading increased to 10% and 15%, the CO2 conversions were comparable with 5Ni/Sm2O3 at 400 °C and 450 °C. Reaction at 450 °C showed 72.7% of CO2 conversion on 5Ni–5Ba/Sm2O3, which was slightly higher than 5Ni/Sm2O3, 5Ni–10Ba/Sm2O3 and 5Ni–15Ba/Sm2O3 at ∼66.8%. It is apparent that the addition of Ba enhanced the activity of Ni catalysts at temperature below 350 °C. Meanwhile at temperature above 400 °C, the reaction was dictated by the thermodynamic of the reaction thus restricting the catalytic performances of all the catalysts. It is also interesting to note that all the 5Ni/Sm2O3 and 5Ni–xBa/Sm2O3 catalysts exhibited 100% selectivity to methane. When the Ni–Ba/Sm2O3 catalysts were compared with the results previously reported on Ni/metal oxides (Table 2), it is apparent that Ni–Ba/Sm2O3 selectively transformed CO2 to methane and prevented CO formation. The activity of 5Ni–5Ba/Sm2O3 was further investigated for 28 h to show the stability of the catalysts (Fig. 9). The conversion was observed at 39% with 100% selectivity towards methane, with similar conversion was observed up to 28 h.
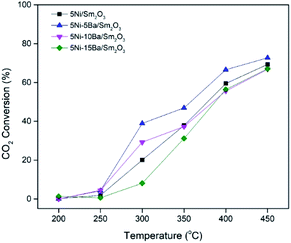 |
| Fig. 8 CO2 conversion for 5Ni/Sm2O3 and 5Ni–xBa/Sm2O3 at x = 5%, 10%, 15%. The catalysts was pre-reduced in situ under H2 for 3 h at 450 °C. | |
Table 2 Catalytic performance comparison among various Ni-based catalysts prepared using wet impregnation as CO2 methanation catalysts
Catalysts |
Reaction condition |
XCO2 (%) |
SCH4 (%) |
Reference |
5Ni/Sm2O3 |
450 °C, 1 bar |
69.3 |
100 |
This work |
5Ni–5Ba/Sm2O3 |
450 °C, 1 bar |
72.7 |
100 |
This work |
5Ni–10Ba/Sm2O3 |
450 °C, 1 bar |
66.8 |
100 |
This work |
5Ni–15Ba/Sm2O3 |
450 °C, 1 bar |
67.0 |
100 |
This work |
5Ni/NaY-DM |
400 °C, 1 bar |
67 |
94 |
39 |
5Ni/MSN |
300 °C, 1 bar |
64.1 |
99.9 |
40 |
10Ni/SiO2 |
400 °C, 1 bar |
73.2 |
98.7 |
41 |
10Ni/MgO |
400 °C, 1 bar |
28.9 |
9.0 |
10Ni/SiO2 + 10Ni/MgO |
400 °C, 1 bar |
66.5 |
96.8 |
10Ni/CeO2 |
350 °C, 1 bar |
79.1 |
76.5 |
42 |
5Ni/CZimp |
350 °C, 1 bar |
59.8 |
97.3 |
30 |
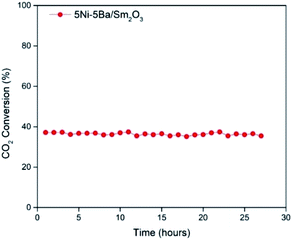 |
| Fig. 9 Catalytic stability of 5Ni–5Ba/Sm2O3 catalysts at 300 °C for 28 h. | |
Fig. 10 summarized the effect of reduction temperature on the activity of 5Ni/Sm2O3 and 5Ni–5Ba/Sm2O3 in order to further elucidate the role of Ba in enhancing Ni activity. These studies also provided insight into the importance of reducing the catalysts prior to the reaction, to ensure the catalysts gained high catalytic activity. Reduction at 250 °C showed the CO2 conversion of 5Ni/Sm2O3 was significantly lower in comparison to 5Ni–5Ba/Sm2O3. 5Ni/Sm2O3 was only active at 350 °C, to give 9.2% of CO2 conversion. The result was indirect contrast to 5Ni–5Ba/Sm2O3, in which 7.9% conversion was analysed at 300 °C following pre-reduction at 250 °C and increased to 28.4% at 350 °C. When the reaction temperature was further increased to 450 °C, the conversion was enhanced to give 49% for 5Ni/Sm2O3 and 59% for 5Ni–5Ba/Sm2O3. Following reduction at 450 °C, no methane was produced at 200 °C but significant conversion was observed at 250 °C for both catalysts. 5Ni–5Ba/Sm2O3 showed 4.3% conversion at 250 °C meanwhile Ni/Sm2O3 only showed 1.9% of CO2 conversion. Increasing the reaction temperature to 300 °C, further increased CO2 conversion of 39% on Ba promoted catalysts compared to reduction at 250 °C with only 7.7%. When 5Ni/Sm2O3 was reduced at 600 °C, the catalysts achieved 24% of CO2 conversion at 300 °C, slightly higher than 5Ni/Sm2O3 reduced at 450 °C. Fully reduction of NiO at 600 °C according to H2-TPR analysis (Fig. 5) was suggested to improve 5Ni/Sm2O3 activity. However, reduction of 5Ni–5Ba/Sm2O3 at 600 °C reduced the CO2 conversion. H2-TPR analysis of 5Ni–5Ba/Sm2O3 showed the catalyst was fully reduced at temperature below 500 °C, thus high temperature reduction may cause particle sintering.38 Nevertheless, all the catalysts showed 100% selectivity towards CH4. The results obtained on the effect of reduction temperature is highly important to show the role of Ba in improving the activity of Ni catalysts particularly for CO2 methanation at low temperature.
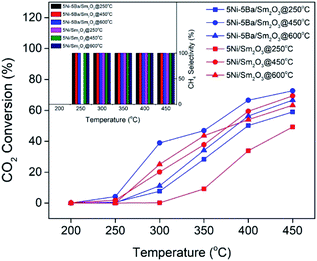 |
| Fig. 10 CO2 conversion and selectivity of 5Ni/Sm2O3 and 5Ni–5Ba/Sm2O3 at different reduction temperature. | |
Discussions
The effect of Ba on Ni/Sm2O3 activity was observed particularly when the reaction was carried out at temperature below 300 °C. The activity of most nickel catalysts for CO2 methanation was reported to have insignificant increment at the temperature above 350 °C mainly due to the thermodynamic restriction.43 Reaction at temperatures above 400 °C showed the gap between CO2 conversions on 5Ni–5Ba/Sm2O3 and 5Ni/Sm2O3 were only slightly varied. At low temperature, the methanation was restricted by kinetic due to the stability of CO2.44 The results proved the synergy between Ni,Ba and Sm2O3 for CO2 conversion at mild temperatures. The combination of increased basicity, surface oxygen vacancies, NiO reducibility and interparticle meso-porosity of 5Ni–5Ba/Sm2O3 enhanced the activity and stability of 5Ni–xBa/Sm2O3 catalyst. It is also interesting to note that, 5Ni–5Ba/Sm2O3 exhibited 100% selectivity towards methane even when the reaction was carried out at 450 °C. Sm2O3 is a rare earth metal oxide, with mild basicity and redox properties which is ideal for CO2 adsorption and hydrogenation. Barium as alkali earth metal promoter further enhanced the basicity of the catalysts evidenced by the increase of adsorbed CO2 volume determined using CO2-TPD. There is a possibility that introduction of Ba2+ in Sm2O3 enhanced the mobility of oxygen species consequently facilitated the formation of oxygen vacancies on reducible metal oxides.45 The presence of surface oxygen vacancies during catalytic reaction promotes CO2 activation and dissociation.46 Although the XPS analysis showed no evidence of Sm2+ species, there is a possibility that Sm2O3 as redox active metal oxide, to be responded with the changes of oxidation states under reducing environment, alternating between Sm3+ to Sm2+.34 CO2 adsorbed on the metal oxide surface to form monodentate or bidentate carbonate species depending on the oxygen vacancies within the vicinity of Ni nanoparticles.28 Furthermore, the presence of surface oxygen vacancies on Sm2O3 following the addition of Ba enhanced the hydrogenation of carbonate into formate intermediates.28 Formate intermediate will further undergo C–O dissociation and hydrogen insertion to form methane, thus preventing decomposition into CO.28
However at higher Ba loading (15%), the formation of BaNiO3–BaNiO2.36 was observed after calcination at 500 °C. BaNiO2.36 is a stable crystalline phase resulting from the oxidation of Ba and Ni precursors to form zig-zag chains of Ni2+ ion.47 The average oxidation states of Ni in BaNiO2 is 2+, and it is interchangeable to 4+ under oxygen at high temperature to form BaNiO3.17 Since it was crucial for Ni to be in its reduction state in order to catalyze hydrogen dissociation in CO2 methanation reaction,48 the formation of BaNiO3–BaNiO2.36 reduced the activity of 5Ni–15Ba/Sm2O3. Furthermore, BaNiO3–BaNiO2.36 inhibited the contribution of Ba as the additional basic sites evidenced by the CO2-TPD analysis thus resulting in a low catalytic activity at temperature below 350 °C. However, as the temperature was increased to 450 °C, there is a possibility that NiO segregating from BaNiO3–BaNiO2.36 under the presence of H2. Although we have no evidence on the segregation of NiO from BaNiO2 during reaction at 450 °C, the comparable activity with Ni/Sm2O3 implied such processes may occur in situ under the flow of reactant gases.
Impregnation of barium also altered the morphology of Sm2O3 to form uniform particles within ∼100 nm of size with interparticle porosity. It is suggested that partial dissolution of Sm2O3 during impregnation changed the morphology, which was essential to improve the uniformity of nanoparticles. The formation of uniform nanoparticles with interparticle porosity may be beneficial to facilitate carbon dioxide adsorption and diffusion in order to react with the dissociated H atom on Ni sites to form CH4.5,49 Porosity was also improved the heat transfer capacity that allowed the catalysts to overcome the heat released during the exothermic reaction.50
Experimental
Catalysts preparation
All the catalysts were prepared using wetness impregnation method. Nickel(III) nitrate hexahydrate was obtained from Emsure, 99.0%, barium nitrate from Emsure, 99.0%, samarium oxide from Aldrich, 99%. 5Ni–xBa/Sm2O3 catalysts were prepared with different Ba loading, and x = 5 wt%, 10 wt% and 15 wt%. The amount of Ni was kept at 5 wt% relative to the weight of Sm2O3. Ba(NO3)2, Ni(NO3)2 and Sm2O3 were weighed accordingly and physically mixed, which later then dissolved in 10 mL of distilled water. The mixture was stirred continuously for 3 h at 60 °C to ensure thorough dispersion. The catalysts were dried at 200 °C for 2 hours and then calcined at 500 °C for 3 hours in air atmosphere with a heating rate of 10 °C min−1.
Catalyst characterization
Field Emission Scanning Electron Microscope (JSM-7610F equipped with EDX) was used to investigate the surface morphology of the catalysts. Energy Dispersive X-ray analysis was carried out to determine the Ni and Ba dispersion onto Sm2O3. The morphological analysis at micro and nano-scales resolution was carried out using high-resolution field emission transmission electron microscopy (HRTEM) Tecnai G2 F20 STWIN at 200 kV. Prior to the analysis, the catalyst was ground and dispersed in water, and the suspension was dropped on the TEM grid and leave to dry at ambient condition. X-ray powder diffraction (Shimadzu XRD-700 X-ray Diffractometer) was carried out to analyze the crystalline structure of the catalysts by utilizing Cu-Kα radiation at λ = 1.54 Å, with operating conditions of 60 kV and 50 mA. The scanning angle range, 2θ, was 10–70° with a scan rate of 2° min−1. The crystalline structure size was calculated using Scherrer's equation (eqn (4)). |
 | (4) |
where D is the crystallite size (nm), λ is the wavelength of X-ray (0.15406 nm), θ is the peak position (radians), k is Scherrer constant and β is the FWHM (radians).
Surface area, average pore volume and pore diameter of 5Ni/Sm2O3 and 5Ni–xBa/Sm2O3 at different Ba loading were determined using N2 adsorption at 77 K (Micromeritics ASAP 2020). The samples were degassed under carbon degassing conditions for 2 hours at 300 °C. Brunauer–Emmett–Teller (BET) equation was used to calculate the surface area and Barret–Joyner–Halenda (BJH) equation for pore volume and diameter calculation. The pore volume was determined based on three different measurement with standard deviation was measured at 8.91 × 10−5. X-ray photoelectron spectra (XPS) were recorded on a Kratos Axis Ultra-DLD XPS spectrometer with a monochromatic Al kα source (75–150 W) and analyser pass energies of 160 eV (for survey scans) or 40 eV (for detailed scans). The XPS data was analysed using CASA XPS software and all the samples were calibrated by adjusting the C 1s position to 284.5 eV. H2 temperature-programmed reduction (Quantachrome ChemBET Pulsar TPR/TPD, equipped with TCD) was performed to study the reducibility of the catalyst. Catalyst was pre-treated in N2 stream with flow of 75 mL min−1 at 100 °C for 1 hour and cooled down to 40 °C. The catalysts were heated to 900 °C with a heating rate of 10°C min−1 in a 5% H2/N2 gas mixture with a flow rate of 75 mL min−1. CO2 temperature-programmed desorption was conducted to study the surface basicity and basic sites distribution of the catalysts. Catalysts were heated to 600 °C for 1 hour under 5% H2/N2 gases, which later cooled to room temperature under He flow. Catalyst was exposed to CO2 gas stream for 30 minutes and then flushed out with He for 1 hour. TPD was finally carried out from 40–600 °C with a heating rate of 10 °C min−1.
Catalytic activity
CO2 methanation reaction was conducted in a stainless-steel plug flow reactor at atmospheric pressure and reaction temperature ranging from 200 to 450 °C. 0.5 g of catalyst was placed in a tubular fixed bed reactor and reduced in situ with H2 gas (99.9%) with flow rate of 20 mL min−1 at 450 °C for 3 h. The catalyst was cooled down to room temperature and CO2/H2/N2 (15%/60%/25%) gases at 20 mL min−1 were flowed in the reactor. The gas effluent from the reactor was analyzed by GC (Shimadzu GC-2014 with TCD detector). Reaction temperature was increased by 50 °C every hour and the gas were sampled using GC. CO2 conversion (eqn (5)), CH4 selectivity (eqn (6)) and CO selectivity (eqn (7)), and CH4 yield (eqn (8)) were calculated according to the previous method (ref. 48) as follows: |
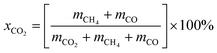 | (5) |
|
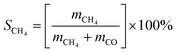 | (6) |
|
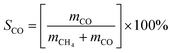 | (7) |
where xCO2(%) is the CO2 conversion, SCH4(%) is the CH4 selectivity, SCO(%) is the CO selectivity, YCH4(%) is the CH4 yield and m is the number of moles of the gases.
Conclusions
The activity of Ni–Ba/Sm2O3 catalysts was investigated to enhance CO2 methanation at moderate reaction temperatures. 5Ni–5Ba/Sm2O3 demonstrated a higher CO2 conversion with 100% CH4 selectivity in comparison to 5Ni/Sm2O3. The effect of increasing Ba loading on 5Ni/Sm2O3 exhibited the changes of porosity and uniformity of the catalysts structure, and the reducibility of NiO. Ba as promoter also enhanced the number of basic sites and surface oxygen vacancies, and transformed the non-uniform aggregates Sm2O3 into uniform size nanoparticles. The basicity originated from Ba promoter enhanced CO2 adsorption meanwhile the porosity facilitated the heat transfer process during catalytic reaction which consequently increased the catalytic stability. However, further increasing the Ba loading to 15% destroyed the uniform nanostructure and porosity of the catalysts, due to the formation of BaNiO3–BaNiO2.36 phases thus reducing the catalytic performance at low temperatures.
Conflicts of interest
There are no conflicts to declare.
Acknowledgements
The authors would like to acknowledge UBD University Research Grant for funding this research (UBD/RSCH/URC/RG(b)/2019/012).
Notes and references
- T. R. Anderson, E. Hawkins and P. D. Jones, CO2, the greenhouse effect and global warming: from the pioneering work of Arrhenius and Callendar to today's Earth System Models, Endeavour, 2016, 40(3), 178–187, DOI:10.1016/j.endeavour.2016.07.002.
- W. Li, H. Wang, X. Jiang, J. Zhu, Z. Liu and X. Guo, et al., A short review of recent advances in CO2 hydrogenation to hydrocarbons over heterogeneous catalysts, RSC Adv., 2018, 8(14), 7651–7669, 10.1039/C7RA13546G.
- R. M. Cuéllar-Franca and A. Azapagic, Carbon capture, storage and utilisation technologies: A critical analysis and comparison of their life cycle environmental impacts, J CO2 Util., 2015, 9, 82–102 CrossRef.
- N. M. Martin, P. Velin, M. Skoglundh, M. Bauer and P. A. Carlsson, Catalytic hydrogenation of CO2 to methane over supported Pd, Rh and Ni catalysts, Catal. Sci. Technol., 2017, 7(5), 1086–1094, 10.1039/C6CY02536F.
- J. Ashok, S. Pati, P. Hongmanorom, Z. Tianxi, C. Junmei and S. Kawi, A review of recent catalyst advances in CO2 methanation processes, Catal. Today, 2020, 356, 471–489, DOI:10.1016/j.cattod.2020.07.023.
- K. Stangeland, D. Kalai, H. Li and Z. Yu, CO2 Methanation: The Effect of Catalysts and Reaction Conditions, Energy Procedia, 2017, 105(1876), 2022–2027 CrossRef CAS.
- P. Tepamatr, N. Laosiripojana, T. Sesuk and S. Charojrochkul, Effect of samarium and praseodymium addition on water gas shift performance of Co/CeO2 catalysts, J. Rare Earths, 2020, 38(11), 1201–1206, DOI:10.1016/j.jre.2019.12.003.
- Z. Chunhui, Z. Yifeng and L. Huazhang, Effect of samarium on methanation resistance of activated carbon supported ruthenium catalyst for ammonia synthesis, J. Rare Earths, 2010, 28(4), 552–555, DOI:10.1016/S1002-0721(09)60152-6.
- S. Singh, P. Kaur, V. Kumar, K. B. Tikoo and S. Singhal, Traversing the advantageous role of samarium doped spinel nanoferrites for photocatalytic removal of organic pollutants, J. Rare Earths, 2020 DOI:10.1016/j.jre.2020.12.008.
- Z. Taherian, M. Yousefpour, M. Tajally and B. Khoshandam, A comparative study of ZrO2, Y2O3 and Sm2O3 promoted Ni/SBA-15 catalysts for evaluation of CO2/methane reforming performance, Int. J. Hydrogen Energy, 2017, 42(26), 16408–16420 CrossRef CAS.
- X. L. Wang, M. Yang, L. J. Zhu, X. N. Zhu and S. R. Wang, CO2 methanation over Ni/Mg@MCM-41 prepared by in situ synthesis method, J. Fuel Chem. Technol., 2020, 48(4), 456–465, DOI:10.1016/S1872-5813(20)30020-7.
- W. J. Lee, C. Li, H. Prajitno, J. Yoo, J. Patel and Y. Yang, et al., Recent trend in thermal catalytic low temperature CO2 methanation: A critical review, Catal. Today, 2021, 368, 2–19, DOI:10.1016/j.cattod.2020.02.017.
- H. Muroyama, Y. Tsuda, T. Asakoshi, H. Masitah, T. Okanishi and T. Matsui, et al., Carbon dioxide methanation over Ni catalysts supported on various metal oxides, J. Catal., 2016, 343, 178–184, DOI:10.1016/j.jcat.2016.07.018.
- J. Ilsemann, A. Sonström, T. M. Gesing, R. Anwander and M. Bäumer, Highly Active Sm2O3–Ni Xerogel Catalysts for CO2 Methanation, ChemCatChem, 2019, 11(6), 1732–1741 CrossRef CAS.
- N. A. Sholeha, S. Mohamad, H. Bahruji, D. Prasetyoko, N. Widiastuti and N. A. Abdul Fatah, et al., Enhanced CO2 methanation at mild temperature on Ni/zeolite from kaolin: Effect of metal-support interface, RSC Adv., 2021, 11(27), 16376–16387 RSC.
- A. Bansode, B. Tidona, P. R. Von Rohr and A. Urakawa, Impact of
K and Ba promoters on CO2 hydrogenation over Cu/Al2O3 catalysts at high pressure, Catal. Sci. Technol., 2013, 3(3), 767–778 RSC.
- A. M. Arévalo-López, M. Huvé, P. Simon and O. Mentré, The hidden story in BaNiO3 to BaNiO2 transformation: Adaptive structural series and NiO exsolution, Chem. Commun., 2019, 55(26), 3717–3720 RSC.
- M. Liu, Z. Wang, M. Liu, X. Li, K. Blinn and S. Lai, et al., Understanding the phase formation and compositions of barium carbonate modified NiO-yttria stabilized zirconia for fuel cell applications, Int. J. Hydrogen Energy, 2015, 40(45), 15597–15604, DOI:10.1016/j.ijhydene.2015.09.092.
- Z. A. Alothman, A review: Fundamental aspects of silicate mesoporous materials, Materials, 2012, 5(12), 2874–2902 CrossRef CAS.
- K. S. W. Sing and R. T. Williams, Physisorption hysteresis loops and the characterization of nanoporous materials, Adsorpt. Sci. Technol., 2004, 22(10), 773–782 CrossRef CAS.
- C. Italiano, J. Llorca, L. Pino, M. Ferraro, V. Antonucci and A. Vita, CO and CO2 methanation over Ni catalysts supported on CeO2, Al2O3 and Y2O3 oxides, Appl. Catal., B, 2020, 264, 118494 CrossRef CAS.
- B. T. Sone, E. Manikandan, A. Gurib-Fakim and M. Maaza, Sm2O3 nanoparticles green synthesis via Callistemon viminalis' extract, J. Alloys Compd., 2015, 650, 357–362, DOI:10.1016/j.jallcom.2015.07.272.
- M. Retuerto, F. Calle-Vallejo, L. Pascual, P. Ferrer, Á. García and J. Torrero, et al., Role of lattice oxygen content and Ni geometry in the oxygen evolution activity of the Ba–Ni–O system, J. Power Sources, 2018, 404(September), 56–63, DOI:10.1016/j.jpowsour.2018.09.098.
- A. Quindimil, U. De-La-Torre, B. Pereda-Ayo, A. Davó-Quiñonero, E. Bailón-García and D. Lozano-Castelló, et al., Effect of metal loading on the CO2 methanation: A comparison between alumina supported Ni and Ru catalysts, Catal. Today, 2020, 356, 419–432 CrossRef CAS.
- C. Jiménez-González, Z. Boukha, B. De Rivas, J. J. Delgado, M. Á. Cauqui and J. R. González-Velasco, et al., Structural characterisation of Ni/alumina reforming catalysts activated at high temperatures, Appl. Catal., A, 2013, 466, 9–20, DOI:10.1016/j.apcata.2013.06.017.
- C. Lv, L. Xu, M. Chen, Y. Cui, X. Wen and C. e. Wu, et al., Constructing highly dispersed Ni based catalysts supported on fibrous silica nanosphere for low-temperature CO2 methanation, Fuel, 2020, 278, 118333 CrossRef CAS.
- K. Polychronopoulou, A. A. Alkhoori, A. M. Efstathiou, M. A. Jaoude, C. M. Damaskinos and M. A. Baker, et al., Design Aspects of Doped CeO2 for Low-Temperature Catalytic CO Oxidation: Transient Kinetics and DFT Approach, ACS Appl. Mater. Interfaces, 2021, 13(19), 22391–22415 CrossRef CAS PubMed.
- S. Wang, Q. Pan, J. Peng and S. Wang, In situ FTIR spectroscopic study of the CO2 methanation mechanism on Ni/Ce0.5Zr0.5O2, Catal. Sci. Technol., 2014, 4(2), 502–509 RSC.
- M. J. Kim, J. R. Youn, H. J. Kim, M. W. Seo, D. Lee and K. S. Go, et al., Effect of surface properties controlled by Ce addition on CO2 methanation over Ni/Ce/Al2O3 catalyst, Int. J. Hydrogen Energy, 2020, 45(46), 24595–24603, DOI:10.1016/j.ijhydene.2020.06.144.
- P. A. U. Aldana, F. Ocampo, K. Kobl, B. Louis, F. Thibault-Starzyk and M. Daturi, et al., Catalytic CO2 valorization into CH4 on Ni-based ceria-zirconia. Reaction mechanism by operando IR spectroscopy, Catal. Today, 2013, 215, 201–207, DOI:10.1016/j.cattod.2013.02.019.
- K. Zhao, W. Wang and Z. Li, Highly efficient Ni/ZrO2 catalysts prepared via combustion
method for CO2 methanation, J CO2 Util., 2016, 16, 236–244 CrossRef CAS.
- A. Quindimil, U. De-La-Torre, B. Pereda-Ayo, J. A. González-Marcos and J. R. González-Velasco, Ni catalysts with La as promoter supported over Y- and BETA- zeolites for CO2 methanation, Appl. Catal., B, 2018, 238(April), 393–403, DOI:10.1016/j.apcatb.2018.07.034.
- D. Wierzbicki, R. Debek, M. Motak, T. Grzybek, M. E. Gálvez and P. Da Costa, Novel Ni-La-hydrotalcite derived catalysts for CO2 methanation, Catal. Commun., 2016, 83, 5–8 CrossRef CAS.
- G. K. Hodgson, S. Impellizzeri, G. L. Hallett-Tapley and J. C. Scaiano, Photochemical synthesis and characterization of novel samarium oxide nanoparticles: Toward a heterogeneous Brønsted acid catalyst, RSC Adv., 2015, 5(5), 3728–3732 RSC.
- H. Bahruji, M. Bowker, P. R. Davies, J. Kennedy and D. J. Morgan, The importance of metal reducibility for the photoreforming of methanol on transition metal-TiO2 photocatalysts and the use of non-precious metals, Int. J. Hydrogen Energy, 2015, 40(3), 1465–1471, DOI:10.1016/j.ijhydene.2014.11.097.
- T. D. Nguyen, D. Mrabet and T. O. Do, Controlled self-assembly of Sm2O3 nanoparticles into nanorods: Simple and large scale synthesis using bulk Sm2O3 powders, J. Phys. Chem. C, 2008, 112(39), 15226–15235 CrossRef CAS.
- T. D. Nguyen, C. T. Dinh and T. O. Do, Monodisperse samarium and cerium orthovanadate nanocrystals and metal oxidation states on the nanocrystal surface, Langmuir, 2009, 25(18), 11142–11148 CrossRef CAS PubMed.
- M. Aghayan, D. I. Potemkin, F. Rubio-Marcos, S. I. Uskov, P. V. Snytnikov and I. Hussainova, Template-Assisted Wet-Combustion Synthesis of Fibrous Nickel-Based Catalyst for Carbon Dioxide Methanation and Methane Steam Reforming, ACS Appl. Mater. Interfaces, 2017, 9(50), 43553–43562 CrossRef CAS PubMed.
- N. A. Sholeha, L. Jannah, H. N. Rohma, N. Widiastuti, D. Prasetyoko and A. A. Jalil, et al., Synthesis of zeolite NaY from dealuminated metakaolin as Ni support CO2 hydrogenation to methane, Clays Clay Miner., 2020, 68(5), 513–523 CrossRef.
- M. A. A. Aziz, A. A. Jalil, S. Triwahyono, R. R. Mukti, Y. H. Taufiq-Yap and M. R. Sazegar, Highly active Ni-promoted mesostructured silica nanoparticles for CO2 methanation, Appl. Catal., B, 2014, 147, 359–368 CrossRef CAS.
- M. Guo and G. Lu, The effect of impregnation strategy on structural characters and CO2 methanation properties over MgO modified Ni/SiO2 catalysts, Catal. Commun., 2014, 54, 55–60, DOI:10.1016/j.catcom.2014.05.022.
- S. Tada, T. Shimizu, H. Kameyama, T. Haneda and R. Kikuchi, Ni/CeO2 catalysts with high CO2 methanation activity and high CH4 selectivity at low temperatures, Int. J. Hydrogen Energy, 2012, 37(7), 5527–5531, DOI:10.1016/j.ijhydene.2011.12.122.
- F. Ocampo, B. Louis, L. Kiwi-Minsker and A. C. Roger, Effect of Ce/Zr composition and noble metal promotion on nickel based CexZr1−xO2 catalysts for carbon dioxide methanation, Appl. Catal., A, 2011, 392(1–2), 36–44, DOI:10.1016/j.apcata.2010.10.025.
- I. Champon, A. Bengaouer, A. Chaise, S. Thomas and A. C. Roger, Carbon dioxide methanation kinetic model on a commercial Ni/Al2O3 catalyst, J CO2 Util., 2019, 34(March), 256–265, DOI:10.1016/j.jcou.2019.05.030.
- A. G. Bhavani, W. Y. Kim and J. S. Lee, Barium substituted lanthanum manganite perovskite for CO2 reforming of methane, ACS Catal., 2013, 3(7), 1537–1544 CrossRef CAS.
- H. Gu, J. Ding, Q. Zhong, Y. Zeng and F. Song, Promotion of surface oxygen vacancies on the light olefins synthesis from catalytic CO2 hydrogenation over Fe[sbnd]K/ZrO2 catalysts, Int. J. Hydrogen Energy, 2019, 44(23), 11808–11816, DOI:10.1016/j.ijhydene.2019.03.046.
- M. Matsuda, K. Katsumata, I. Watanabe and K. Nagamine, μSR measurements of BaNiO2, Hyperfine Interact., 1997, 104(1–4), 97–103 CrossRef CAS.
- W. L. Vrijburg, G. Garbarino, W. Chen, A. Parastaev, A. Longo and E. A. Pidko, et al., Ni-Mn catalysts on silica-modified alumina for CO2 methanation, J. Catal., 2020, 382, 358–371, DOI:10.1016/j.jcat.2019.12.026.
- S. B. Ubale, T. T. Ghogare, V. C. Lokhande, T. Ji and C. D. Lokhande, Electrochemical behavior of hydrothermally synthesized porous groundnuts-like samarium oxide thin films, SN Appl. Sci., 2020, 2(4) CAS.
- L. Dou, C. Yan, L. Zhong, D. Zhang, J. Zhang and X. Li, et al., Enhancing CO2 methanation over a metal foam structured catalyst by electric internal heating, Chem. Commun., 2019, 56(2), 205–208 RSC.
|
This journal is © The Royal Society of Chemistry 2021 |
Click here to see how this site uses Cookies. View our privacy policy here.