DOI:
10.1039/D1RA03738B
(Paper)
RSC Adv., 2021,
11, 27620-27626
A self-matting waterborne polyurethane coating with admirable abrasion-resistance
Received
13th May 2021
, Accepted 29th July 2021
First published on 17th August 2021
Abstract
Due to the paradox between abrasion-resistance and extinction, the development of a self-matting waterborne polyurethane (SMWPU) coating accompanied by excellent abrasion-resistance is still a challenge. Herein, a kind of hydroxyalkyl-terminated polysiloxane modified SMWPU was prepared and employed for matting leather/synthetic leather finishing. Simultaneously, the influences of hydrophilic chain extender and polysiloxane loadings on the matting effect and abrasion resistance of the coating were investigated in detail. The results indicated that the gloss of the coating was closely related to the hydrophilic chain extender content, and a stable emulsion and optimal matting effect could be achieved when a 1.6 wt% (based on solid content) hydrophilic chain extender was employed. With the introduction of polysiloxane, the silicon element content on the coating surface increased from 0% to 9.26%, just as expected, and an enhanced abrasion resistance of the coating was obtained. Specifically, the coating weight loss ratio was reduced from 2.36 wt% to 0.41 wt%, and obvious surface damage did not occur after 500 abrasions. Although the surface roughness and matting effect of the coating decreased slightly due to the introduction of silicone, the gloss of the modified coating was less than 1.5° (60° incidence angle), still exhibiting an excellent matting effect. Another interesting result was the elevation of anti-hot-pressing, compared with that of the unmodified one, and the gloss of the modified coating showed no changes under a 10 MPa, 150 °C hot-pressing condition.
1. Introduction
As a coating material, most waterborne polyurethanes generally present a high gloss, which meets the requirements of various market applications, such as leather/synthetic leather finishing, textile laminating, wood coating and car exterior paint, and so on. The gloss of the coating, which determines the aesthetic appearance and additional value of the final products, is often divided into four categories, as shown in Table 1. In recent years, with the changes of the aesthetic concept, matting coating is becoming more and more popular for consumers.1,2 Actually, as a high matting coating for leather and synthetic leather, the gloss of the coating should be less than 1.5° (60° incidence angle).
Table 1 Coating gloss classification (60° incidence angle)
Classification |
Extinction |
Egg shell light |
Semi-gloss |
High gloss |
Coating gloss (°) |
<5 |
5–30 |
30–90 |
>90 |
As is well-known, the gloss of the coating depends on the surface roughness.3 As depicted in Fig. 1, the rough surface will cause diffuse reflection at multiple angles, which will reduce the intensity of the reflected light, thus causing a low-gloss surface.4
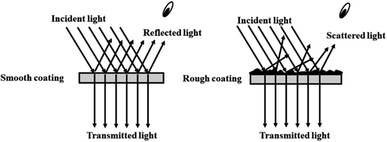 |
| Fig. 1 Effect of surface roughness on coating gloss and transparency. | |
Waterborne polyurethane (WPU) is a type of widely used coating material for leather/synthetic leather manufacture. Generally, WPU latexes with large particle sizes are more likely to form a rough coating surface during the drying process,5,6 which will impart the desirable coating matting effect. In our previous work, a type of self-matting WPU with a 6–7 μm particle size was prepared and used for a matte leather finishing, and we found the surface roughness and the matting effect increased rapidly with the increase of the latex particle size; when the particle size is in the range of 6–7 μm, the lowest gloss of the coating (<0.5°) can be achieved.7 Furthermore, T. Trezza, J. et al. described the relationship between the surface roughness (Rq) and the reflected light intensity (R) in accordance with the Bennet–Porteus rough surface reflection model.8
|
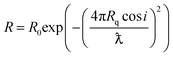 | (1) |
here,
R is the sample reflectance of a rough surface,
R0 is the reflectance from an optically smooth surface of the same material, and
Rq is the root-mean-square roughness (nm). Therefore, the key issue for constructing a matte coating is to increase the roughness of the coating surface, so as to form diffuse reflection on the surface of the coating.
To construct the rough surface, the traditional method is to add organic or inorganic matting powder to the WPU coating. However, these matting powders are always prone to sedimentation, which leads to some problems, such as decreasing the stability of the emulsion and worsening the adhesion of the coating.9 Comparatively, developing a self-matting waterborne polyurethane (SMWPU), in which the matting effect originates from its characteristic structure, rather than by means of the addition of matting powder, is suggested to be an efficient way to solve the above problems. For example, Yeyun Meng et al. prepared a soybean oil-based self-matting waterborne polyurethane coating, and the gloss of the coating reached 3.3° at 60°.10
In addition to extinction, the leather coating is often required to have good abrasion resistance. Similarly, in order to improve the abrasion resistance of the coating, the most convenient way is also by adding a variety of organic or inorganic additives (such as nano SiO2, liquid paraffin and organic silicon additives, etc.) into the coating. Among them, polysiloxane, due to its excellent properties such as a high and low temperature resistance, hydrophobicity, and abrasion resistance, has been commonly used as a type of abrasion resistance elevators for coatings.11 Wuhou Fan et al. reported a kind of polyurethane-organosilicone composite by incorporating nano SiO2 into polyurethane physically,12 and they found the composite coating showed enhanced abrasion resistance. But, unfortunately, the problem of poor compatibility still exists in this kind of physical blending system. Hence, how to chemically combine polysiloxane with WPU to improve their compatibility became a research hotspot. For example, Lee Won-Ki et al. reported a kind of hydroxyl-terminated polydimethylsiloxane covalently modified polyurethane. The chemical incorporated Si–O–Si chain segments endowed the polyurethane with a slight phase-separation and remarkable promotion in scratch resistance and abrasion endurance.13 However, these methods mentioned above cannot simultaneously impart the coating abrasion-resistant and matting effect, so the development of a self-matting waterborne polyurethane (SMWPU) coating accompanied by excellent abrasion-resistance is still a challenge.
Herein, a series of abrasion-resistant self-matting waterborne polyurethane (ARSMWPU) was prepared by covalently incorporating hydroxyalkyl-terminated polysiloxane into the self-matting waterborne polyurethane. The effects of the hydrophilic chain extender and polysiloxane loadings on the surface roughness, surface gloss, and abrasion resistance together with anti-hot pressing were systematically investigated. As expected, the chemical bonding between polysiloxane and SMWPU increased their compatibility, the migration of the polysiloxane side chain enhanced the surface enrichment of the –Si–O–Si- segments, which imparted a self-matting coating with superior abrasion-resistance and anti-hot pressing, simultaneously meeting the requirements of a high matting effect and wear resistance of the leather and synthetic leather coating.
2. Experimental
2.1 Materials
Polycarbonatediol (PCDL; Mn = 2000 g mol−1) and non-ionic hydrophilic chain extender (Ymer N120; Mn = 1000 g mol−1) were supplied by Shen Lan New Material Co. (Zhejiang, China). Acetone, diethylenetriamine (DETA), triethylamine (TEA) and 1,4-cyclohexanedimethanol (CHDM) were purchased from Aladdin (Shanghai, China). As the hydrophilic chain extender, 2,2′-bis (hydroxymethyl) butyric acid (DMBA) was supplied by Adamas (Shanghai, China). The bismuth acid catalyst, trimethylolpropane (TMP) and diethylenetriamine were obtained from Kelong Chemical Engineering Co. Ltd (Chengdu, China). Isophorone diisocyanate (IPDI) and hexamethylene-1,6-diisocyanate trimer (N3900) were obtained from Bayer Co. Ltd (Germany). Hydroxyalkyl-terminated polysiloxane was obtained from Chen Guang Research Institute of Chemical Industry (Chengdu, China). All the chemicals were used after dehydration.
2.2 Synthesis of ARSMWPU
The abrasion-resistant self-matting waterborne polyurethane (ARSMWPU) was synthesized as described in Scheme 1. Briefly, the hydroxyalkyl-terminated polydimethylsiloxane, isophorone diisocyanate (IPDI), polycarbonatediol (PCDL, Mn = 2000), trimethylolpropane (TMP), Ymer N120 and 0.1 wt‰ bismuth acid catalyst were added into a three-neck flask fitted with a mechanical stirrer and a thermometer. The reaction was carried out under a nitrogen atmosphere at 85 °C for 2 h until the theoretical amount of residual –NCO groups was reached. Subsequently, 1,4-cyclohexanedimethanol (CHDM) and 2,2′-bis-(hydroxymethyl) butyric acid (DMBA) were added into the reaction and continued to react at 55 °C for 3 h. After the prepolymer was neutralized by triethylamine (TEA), a large amount of deionized water was fed into the vessel to obtain a certain solid content ARSMWPU emulsion. Finally, a post chain-extending reaction was carried out by diethylenetriamine at 45 °C for 2 h, and acetone was removed from the emulsion by vacuum distillation (Table 2).
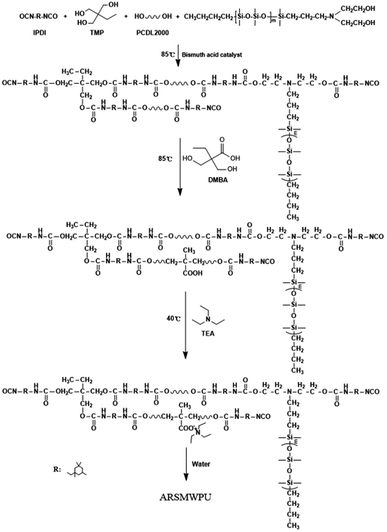 |
| Scheme 1 The synthesis of ARSMWPU. | |
Table 2 The raw material composition of WPU
Sample |
Polysiloxane content (wt%) |
SMWPU-0 |
0 |
ARSMWPU-1 |
0.6 |
ARSMWPU-2 |
1.2 |
ARSMWPU-3 |
1.8 |
ARSMWPU-4 |
2.4 |
ARSMWPU-5 |
3.0 |
2.3 Preparation of abrasion-resistant self-matting waterborne polyurethane films
ARSMWPU films with a thickness of about 1.0 mm were obtained by casting ARSMWPU dispersions on polytetrafluoroethylene plates at ambient temperature for three days and then vacuum-drying at 100 °C for 2 h. Before characterization, all the films were placed in a desiccator at room temperature. For data acquisition, all the binding energies (BE) were calibrated based on the hydrocarbon C 1s peak set at 284.6 eV. The CasaXPS program was adopted to deconvolve the XPS signals using a Shirley-type baseline for separating different species of the same element. The content of total organic carbon (TOC) was measured by combustion in an Apollo 9000 TOC/TN auto analysis system (Tekmar-Dohrmann, United States).
2.4 Preparation of wear-resistant self-matting leather
An amount of ARSMWPU emulsion, 0.5 wt% water-based thickener, 0.03 wt% water-based levelling agent and 0.1 wt% crosslinking agent were mixed together, and the viscosity of slurry was controlled to 800–1000 mPa s. The slurry was coated on the surface of leather or synthetic leather by an automatic coating machine with the amount of 20–30 g m−2, and then was dried at 120 °C for 60 s.
2.5 Measurements
Fourier transform infrared (FTIR) spectra were collected on an IS10 FTIR spectrometer (Thermo Scientific, United States) using KBr pellets over the wavenumber range from 4000 cm−1 to 400 cm−1. The particle size of the WPU dispersions was measured using a Malvern 2000 Mastersizer (Malvern Instruments, United Kingdom). A scanning electron microscope (SEM) micrograph of the WPU film was acquired using a FEI Apreo SEM (Thermo Scientific, United States) with an acceleration voltage of 15 kV. The sample was sputter-coated with a conductive gold layer before examination. And the equipped Energy Dispersive X-ray (EDX) spectrometer was used for qualitative and quantitative elemental analysis of the chars. X-ray photoelectron spectroscopy (XPS) was carried out using an ESCALAB 250XI spectrometer (Thermo Scientific, United States), with Al Kα excitation radiation under ultrahigh-vacuum conditions. A three-dimensional surface morphology observation of the WPU films was performed using Atomic Force Microscopy (AFM) (SPM-9500, Japan). The scanning rate was 1 Hz. The gloss of the coating was measured with a German REFO gloss meter at 60°, and the coating was prepared according to the reference,14 that is, the WPU was coated on the surface of black glass and dried. A Martindale abrasion tester (Darong textile instrument, China) was adopted to test the mass loss ratio of the leather coating after abrasion according to the ISO 12947-3:1998 standard. The mass loss ratio φ (wt%) was calculated according to formula (2): |
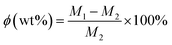 | (2) |
where M1–M2 is the mass loss before and after the abrasion test of the leather.
The morphology of the leather coating in the Martindale wear test was observed by a FEI Apreo SEM (Thermo Scientific, United States) with an acceleration voltage of 15 kV. The hot pressing test was measured by using a CYYB-15 Knurlier (Zhongda Machinery, China) at 150 °C with a pressure of 10 MPa for 30 s.
3. Results and discussion
3.1 Effect of hydrophilic group content on the latex particle size and coating gloss
As mentioned above, the coating gloss is closely associated with surface roughness, which is fundamentally determined by the particle size of waterborne polyurethane.15 As shown in Fig. 2, with an increasing DMBA (hydrophilic chain extender) content from 1.4 wt% to 1.7 wt%, the particle size of the WPU latex decreased from 11.23 μm to 1.27 μm. As a result, the gloss of the coating increased from 0.3° to 0.7° continuously, and a sharp increase of the coating gloss occurred when the DMBA content is over 1.7 wt%. The surface morphology of the WPU film changed with the content of hydrophilic groups, which can be directly observed by SEM. As shown in Fig. 3 and 4, when the DMBA content is in the range of 1.4–1.6 wt%, a large amount of spherical particles with a size scale from 7.51 μm to 1.72 μm occurred on the coating surface and formed a roughness surface. This roughness surface is suggested to contribute to the coating's outstanding matting effect. Further increasing the DMBA content to above 1.7 wt%, the latex particle size of the WPU decreased (Fig. 2) and the spherical particles of the coating surface disappeared to give a smooth surface (Fig. 3), which markedly decreased the matting effect.
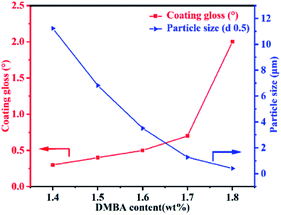 |
| Fig. 2 Effect of DMBA content on the WPU latex particle size (μm) and coating gloss (°). | |
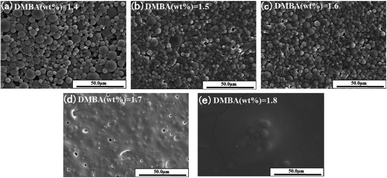 |
| Fig. 3 SEM of WPU film surfaces with various DMBA contents: (a) 1.4 wt%, (b) 1.5 wt%, (c) 1.6 wt%, (d) 1.7 wt% and (e) 1.8 wt%. | |
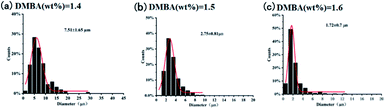 |
| Fig. 4 Particle size statistics of the WPU film surfaces with various DMBA contents: (a) 1.4 wt%, (b) 1.5 wt% and (c) 1.6 wt%. | |
3.2 Structure of polysiloxane modified SMWPU
The FTIR spectra of the hydroxyalkyl-terminated polysiloxane is depicted in Fig. 5a. The peaks at 3327 cm−1 (–OH), 1024 cm−1 (–Si–O–Si–) and 804 cm−1 (Si–CH3, Si–CH2) are observed. Fig. 5b is the FTIR spectrum of SMWPU-0; 3342 cm−1 and 1538 cm−1 belong to the stretching vibration absorption peak and the bending vibration absorption peak of N–H in the urethane bond, respectively; 1725 cm−1 should be ascribed to the stretching vibration absorption peak of the carbonyl group (C
O). The vibration absorption peaks of –CH2 and –CH3 occur at 2860 cm−1 and 2954 cm−1, revealing that the –NCO has reacted with –OH of polysiloxane and formed a carbamate bond (–NH–COO–). In Fig. 2c and d, the vibration absorption peak of the Si–O–Si bond at 1024 cm−1 and the vibration absorption peak of the C–H bond in Si–CH3 at 804 cm−1 also indicating that polysiloxane has been successfully incorporated into the polyurethane macromolecule chains.16,17 Notably, ARSMWPU-5 has a stronger C–H bond vibration absorption peak in Si–CH3 at 804 cm−1 than that of ARSMWPU-1, representing that more polysiloxane was introduced into WPU.
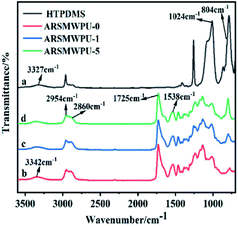 |
| Fig. 5 (a) FTIR spectra of hydroxyalkyl-terminated polysiloxane, (b) FTIR spectra of ARSMWPU-0. (c) FTIR spectra of ARSMWPU-1, (d) FTIR spectra of ARSMWPU-5. | |
As an abrasion-resistance elevator, polysiloxane should be uniformly dispersed in a self-matting waterborne polyurethane coating. Fig. 6 presents an EDX C, N, and O, Si-mapping comparison of ARSMWPU. Among these, the C, O, and N elements mainly come from WPU, and the Si element comes from polysiloxane. It can be seen from Fig. 6a that with a polysiloxane loading less than 1.2 wt%, the C, N, O and Si elements are homogeneously distributed in ARSMWPU. Whilst when the polysiloxane loading increases to above 1.8 wt%, the polysiloxane is concentrated on the surface of the film, and an uneven distribution is observed. Further increasing the amount of polysiloxane to 2.4 wt%, the polysiloxane segments aggregate in the WPU film and produce obvious microphase separation.
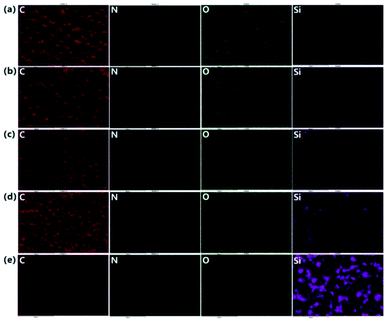 |
| Fig. 6 EDX mapping of the ARSMWPU SE mode, 15 kV: (a) ARSMWPU-1 (0.6 wt%), (b) ARSMWPU-2 (1.2 wt%), (c) ARSMWPU-3 (1.8 wt%), (d) ARSMWPU-4 (2.4 wt%), (e) ARSMWPU-5 (3.0 wt%). | |
In order to further confirm the migration of the polysiloxane side-chain, XPS was performed to reveal the surface chemical composition variation of polysiloxane modified SMWPU. The characteristic signals of carbon (C 1s), nitrogen (N 1s) oxygen (O 1s) and silicon (Si 2p) of the ARSMWPU samples and corresponding surface chemical composition are presented in Fig. 7. With the increase of polysiloxane content, the peak intensity of silicon (Si 2p) peak gradually increases. As can be seen from the data, the surface silicon content increases from 0.0% to 9.26% with an increase of polysiloxane from 0 wt% to 3.0 wt%. During the film forming process, the polysiloxane side-chains will migrate onto the surface of film due to its low surface energy; this result is highly consistent with our molecular design.
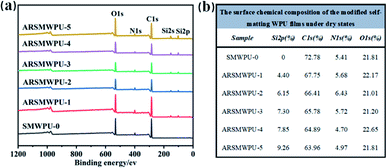 |
| Fig. 7 (a) XPS spectra of the ARSMWPU, (b) the surface chemical composition of the modified self-matting WPU films. | |
3.3 Effect of polysiloxane loading on the surface morphology and gloss of coating
The surface morphology of coating is one of the important indicators for describing the gloss of leather coatings. The effect of different polysiloxane contents on the surface morphology and gloss of ARSMWPU is presented in Fig. 8.
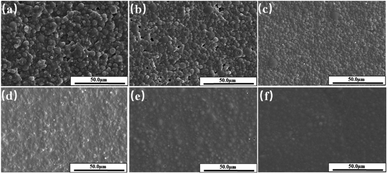 |
| Fig. 8 SEM of WPU film surfaces with various polysiloxane contents: (a) SMWPU-0 (0.0 wt%); (b) ARSMWPU-1 (0.6 wt%); (c) ARSMWPU-2 (1.2 wt%); (d) ARSMWPU-3 (1.8 wt%); (e) ARSMWPU-4 (2.4 wt%) and (f) ARSMWPU-5 (3.0 wt%). | |
For ARSMWPU-1 and ARSMWPU-2, similar spherical particles with different sizes are stranded on the film surface, which indicates that a small amount of polysiloxane has a slight effect on the surface morphology of the WPU coating. However, as the content of polysiloxane increases, the microspheres on the surface gradually become smaller and the rough surface of the WPU film becomes smoother, which should be ascribed to the migration of polysiloxane side chains onto the coating surface.18,19
AFM can be also used to observe the variation of the three-dimensional morphology of the ARSMWPU film surface. From AFM observations (Fig. 9), some parameters, such as height distribution and root-mean-square roughness (Rq), can be obtained and used to evaluate the roughness of coating surface:20,21
|
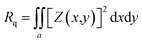 | (3) |
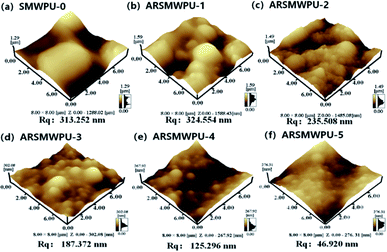 |
| Fig. 9 Three-dimensional AFM images of WPU film surfaces with various polysiloxane contents: (a) SMWPU-0 (0.0 wt%); (b) ARSMWPU-1 (0.6 wt%); (c) ARSMWPU-2 (1.2 wt%); (d) ARSMWPU-3 (1.8 wt%); (e) ARSMWPU-4 (2.4 wt%) and (f) ARSMWPU-5 (3.0 wt%). | |
Compared with the control sample SMWPU-0, the Rq values of the ARSMWPU samples with polysiloxane side chains show a decreasing tendency, which means the roughness of all the samples tends to decrease. For ARSMWPU-1 and ARSMWPU-2 with a small amount of polysiloxane, the Rq values show a slight decrease, so the gloss of the coating remains below 1.0°, showing a good matting effect as described in Table 3 and Fig. 10. With a further increase of polysiloxane content, the Rq decreases rapidly to 46.920 nm. As a result, the gloss of the coating increases from 0.8° for ARSMWPU-2 to 2.3° for ARSMWPU-5; correspondingly, a deteriorated matting effect of leather coating was observed. This result is in good consistency with the SEM conclusions.
Table 3 Effect of different polysiloxane content on gloss (60°) of WPU coating
Sample |
Coating gloss (°) |
SMWPU-0 |
0.5 |
ARSMWPU-1 |
0.6 |
ARSMWPU-2 |
0.8 |
ARSMWPU-3 |
1.2 |
ARSMWPU-4 |
1.5 |
ARSMWPU-5 |
2.3 |
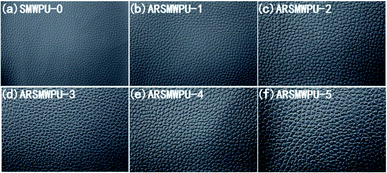 |
| Fig. 10 Effect of different polysiloxane contents modifying self-matting WPU on gloss of the leather coating. | |
3.4 Abrasion-resistance of self-matting leather coating
As for the SMWPU coated leather, its abrasion resistance can be reflected in two aspects: degree of damage and change in gloss of the coating surface after abrasion. Generally, the Martindale test method was carried out to evaluate the damage degree of the coating with reference to ISO 12947-3:1998.22 As shown in Fig. 11, the weight loss ratio of the coating is reduced from 2.36 wt% to 0.41 wt% with increasing polysiloxane content, indicating that the introduction of polysiloxane can efficiently increase the wear resistance of the coating. Fig. 12a presents microscope images of SMWPU-0 before (0 times) and after 500 abrasions; it can be seen that the microspheres on the coating surface almost disappear after abrasion. Under the same wearing conditions, the matte microspheres of ARSMWPU-4 still remained on the coating surface. This should be attributed to the lubricating effect of polysiloxane side chains enriched on the surface, which improves the abrasion resistance of the coating.23
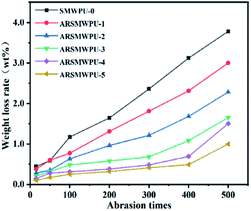 |
| Fig. 11 Effect of different polysiloxane contents on the abrasion resistance of leather coating. | |
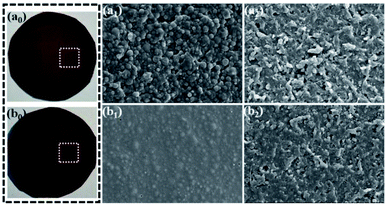 |
| Fig. 12 Digital images of (a0) SMWPU and (b0) ARSMWPU-4 coated leather after 500 abrasions; SEM images before and after 500 abrasions. (a1) SMWPU-0 (before) and (a2) SMWPU-0 (after); (b1) ARSMWPU-4 (before) and (b2) ARSMWPU-4 (after). | |
Another indicator for abrasion resistance is the gloss variation before and after wearing. As shown in Fig. 12(a0), (b0) and 13, the coating gloss of the control sample (SMWPU-0) tends to increase as the amount of abrasion resistance increases, whilst the coating gloss of polysiloxane modified samples show no or little changes even after 500 abrasions.
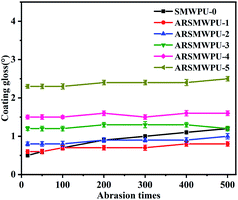 |
| Fig. 13 Effect of different polysiloxane content on the wear resistance of leather coating gloss. | |
3.5 Anti-hot pressing of matted leather coating
Hot pressing is a commonly used process in leather manufacturing. In general, hot pressing often causes the coating to brighten, especially for matted leather coating. As shown in Table 4, the coating gloss of the control sample (SMWPU-0) increases from 0.5° to 1.2° after hot pressing. However, the gloss of the polysiloxane modified self-matting leather coating is almost unchangeable after hot-pressing; this gloss stability in hot-pressing can be ascribed to the enhanced heat resistance caused by the introduction of silicone chain segments.24
Table 4 Change of coating gloss before and after hot pressing testa (60°)
Sample |
Before hot pressing (°) |
After hot pressing (°) |
Hot pressing: 10 MPa and 150 °C for 30 s. |
SMWPU-0 |
0.5 |
1.2 |
ARSMWPU-1 |
0.6 |
0.9 |
ARSMWPU-2 |
0.8 |
1.0 |
ARSMWPU-3 |
1.2 |
1.2 |
ARSMWPU-4 |
1.5 |
1.6 |
ARSMWPU-5 |
2.3 |
2.3 |
4. Conclusions
A kind of abrasion-resistant self-matting waterborne polyurethane (ARSMWPU) was prepared by covalently incorporating hydroxyalkyl-terminated polysiloxane into waterborne polyurethane, and the factors which influence the abrasion-resistance and matting effect were discussed. The results indicate that the hydrophilic group content is the key parameter to determine the particle size of the WPU latex and, in turn, the surface roughness and gloss of the coating are mostly dependent on the particle size of the WPU latex. When the DMBA content was less than 1.6 wt%, a large latex particle size, rough surface and outstanding matting effect can be achieved. With further increases in the DMBA content to above 1.7 wt%, the particle size of WPU latex decreased to 1.27 μm, and a relatively smooth surface and a weakened matting effect were obtained. The introduction of the polysiloxane side-chain can efficiently enhance the abrasion resistance of SMWPU without largely sacrificing the matting effect of the coating. The weight loss ratio of the coating decreased rapidly after 500 abrasions while the gloss of the coating showed little increase, from 0.5° to 0.8°. Moreover, the presence of a polysiloxane side-chain can endow the coating with excellent hot-pressing resistance. Under the conditions of 10 MPa and 150 °C hot pressing, the gloss of the unmodified coating shows a rapid increase whilst the modified one shows almost no change.
Conflicts of interest
The authors declare no conflict of interest.
Acknowledgements
We are grateful for financial support from the National Key Research and Development Program of China (Project No: 2017YFB0308600) and the Key Research and Development Program of Shandong Province (Project No: 2019JZZY010355). We also appreciate Wang Hui from the Analytical & Testing Center of Sichuan University for her help with the SEM characterization and Wang Zhonghui (College of Biomass Science and Engineering, Sichuan University) for her great help in the AFM characterization.
References
- T. Xie, W. Kao, L. Sun, J. Wang, G. Dai and Z. Li, Prog. Org. Coat., 2020, 142, 105569 CrossRef CAS.
- W. Fan, J. Wang and Z. Li, Polym. Test., 2021, 99, 107072 CrossRef CAS.
- G. N. Manvi and R. N. Jagtap, J. Dispersion Sci. Technol., 2010, 31, 1376–1382 CrossRef CAS.
- S. Zhang, Z. Chen, M. Guo, H. Bai and X. Liu, Colloids Surf., A, 2015, 468, 1–9 CrossRef CAS.
- X. Hu, X. Zhang and L. Jin, Int. J. Polym. Sci., 2015, 468, 1–8 CrossRef.
- A. Dang, S. Ojha, C. M. Hui, C. Mahoney, K. Matyjaszewski and M. R. Bockstaller, Langmuir, 2014, 30, 14434–14442 CrossRef CAS PubMed.
- Z. Sun, H. Fan, Y. Chen and J. Huang, Polym. Int., 2018, 67, 78–84 CrossRef CAS.
- T. A. Trezza and J. M. Krochta, J. Appl. Polym. Sci., 2001, 79, 2221–2229 CrossRef CAS.
- C. Sow, B. Riedl and P. Blanchet, J. Coat. Technol. Res., 2011, 8, 211–221 CrossRef CAS.
- Y. Meng, P. Lv, Q. Liu, B. Liao and W. Q. Liu, New J. Chem., 2019, 43, 19193–19199 RSC.
- Z. Sun, J. Wen, W. Wang, H. Fan, Y. Chen, J. Yan and J. Xiang, Prog. Org. Coat., 2020, 146, 105744 CrossRef CAS.
- W. Fan, W. Du, Z. Li, N. Dan and J. Huang, Prog. Org. Coat., 2015, 86, 125–133 CrossRef CAS.
- D.-B. Park, D. H. Kim and W.-K. Lee, Mol. Cryst. Liq. Cryst., 2020, 707, 94–100 CrossRef CAS.
- H. Ma, Y. B. Liu, J. B. Guo, T. B. Chai, S. B. Jing, Y. C. Zhou, L. D. Zhong and J. E. Deng, Prog. Org. Coat., 2020, 139, 105441 CrossRef CAS.
- Y. Qian, F. Dong, L. Guo, X. Xu and H. Liu, Prog. Org. Coat., 2021, 153, 106137 CrossRef CAS.
- Y. Zhang, R. Lin, Y. Shi, H. Li, Y. Liu and C. Zhou, Polym. Bull., 2019, 76, 5517–5535 CrossRef CAS.
- A. M. Mikhailova, M. Tamboura and Q. J. Meng, J. Coat. Technol. Res., 2013, 10, 97–108 CrossRef CAS.
- F. A. Zhang and C. L. Yu, J. Coat. Technol. Res., 2007, 4, 289–294 CrossRef CAS.
- H. Yahyaei, M. Mohseni and H. Ghanbari, J. Inorg. Organomet. Polym., 2015, 25, 1–8 CrossRef.
- P. F. Smith, I. Chun, G. Liu, D. Dimitrievich and G. J. Vancso, Polym. Eng. Sci., 1996, 36, 2129–2134 CrossRef CAS.
- A. M. Rabea, M. Mohseni, I. Tehran and S. M. Mirabedini, J. Coat. Technol. Res., 2011, 8, 497–503 CrossRef CAS.
- J. Liu, X. Jiao, F. Cheng, Y. Fan, Y. Wu and X. Yang, Prog. Org. Coat., 2020, 144, 105673 CrossRef CAS.
- Y. Zhang, R. Lin, H. Li, Y. Shi and C. Zhou, Int. J. Adhes. Adhes., 2020, 102, 102654 CrossRef CAS.
- C. A. Xu, Z. Qu, Z. Tan, B. Nan and L. Liang, Polym. Test., 2020, 86, 106485 CrossRef CAS.
|
This journal is © The Royal Society of Chemistry 2021 |
Click here to see how this site uses Cookies. View our privacy policy here.