DOI:
10.1039/D1RA05435J
(Paper)
RSC Adv., 2021,
11, 27607-27619
Low temperature NH3-SCR performance and mechanism of Mn and Fe supported CeCO3F-monazite catalysts†
Received
15th July 2021
, Accepted 3rd August 2021
First published on 13th August 2021
Abstract
The group has shown that Baiyun Ebo rare earth concentrate has excellent performance in NH3-SCR denitrification when used as a carrier, where rare earth elements are mainly present in cerium fluorocarbon ore (CeCO3F) and monazite (CePO4) mineral phases. In this paper, a new low-temperature NH3-SCR catalyst of Mn–Fe/CeCO3F-monazite was prepared by an impregnation method, using synthetic CeCO3F and purified monazite as carriers. By exploring its denitrification performance and mechanistic analysis, it provides theoretical guidance for the use of rare earth concentrates as low-temperature NH3-SCR catalysts. Our previous studies have determined the optimum loading of Fe, so this paper needs to be investigated for the optimum doping ratio of the active substance Mn. The results of the activity tests, XRD and BET have determined that the best denitrification rate and catalytic performance was achieved at a ratio of Mn
:
Ce of 1
:
5. The denitrification activity of the different catalysts was investigated by loading Fe, Mn and Fe and Mn together. The results obtained by means of experimental analyses such as XRD, SEM, BET and activity tests showed that the composite catalyst loaded with Fe and Mn at the same time, had the highest activity and its denitrification rate could reach 94.8% at 250 °C. This is mainly attributed to the fact that the interaction of Fe, Mn can promote the dispersion of each other on the carrier surface, which greatly improves the specific surface area of the catalyst. The introduction of Fe and Mn increases the acidic sites and the amount of acid on the catalyst surface, which results in the formation of a large number of oxygen vacancies and the presence of more oxygen species on the catalyst surface, which facilitate the migration of oxygen. The new catalyst was investigated by Fourier transform infrared (FTIR) spectroscopy to characterise the adsorption and transformation behaviour of the reactive species on the surface of the catalyst, and to investigate the reaction mechanism. The results showed that the entire reaction process followed the L–H mechanism, with the gaseous NO adsorption and activation on the catalyst surface generating bidentate nitrate, bridging nitrate species and NH3/NH4+ species as the main intermediate species involved in the reaction, both of which underwent redox reactions on the catalyst surface to produce N2 and H2O. The above results indicated that the CeCO3F-monazite carrier has excellent performance, and provided a theoretical basis for the high-value utilization of rare earth concentrates.
1. Introduction
The production of NOx from coal, diesel and gasoline causes a number of environmental problems such as photochemical smog and ozone depletion.1 Therefore NOx reduction and removal is imperative. The commercial V2O5-WO3(MoO3)/TiO2 catalyst for the selective catalytic reduction (SCR) of NH3 from NOx is a widely used technology for the removal of NOx from coal combustion.2 However, problems such as the toxicity of V2O5 and the narrow activity temperature window (320–400 °C) remain.3,4 Therefore, we need to develop efficient and environmentally friendly catalysts for low temperature NH3-SCR.
In recent years, rare earth element catalysts have been widely studied in the field of NH3-SCR due to their abundant storage capacity as well as their stable properties, which not only have good catalytic activity but also good tolerability. Wang et al.5 used a hydrothermal method to load different rare earth oxides (La, Ce, Pr, Nd) onto activated semi-coke (ASC) to prepare low temperature (150–300 °C) selective catalytic reduction (SCR) catalysts for NH3 to NO. The results showed that the best performance of the CeO2-loaded catalysts was due to the doping of rare earth elements which effectively promoted the increase of oxygen vacancy concentration. The high concentration of oxygen vacancies not only facilitated the formation of lattice oxygen, but also the adsorption of O2 and the further oxidation of NO. The lattice oxygen initially oxidised the NO to NO2, which facilitated the subsequent reduction reaction to proceed rapidly. Jie Fan6 et al. evaluated the effect of cerium or lanthanum on the hydrothermal stability of copper-SAPO-3 catalysts. The results showed that the nitrogen oxide conversion of aged cerium or lanthanum modified Cu-SAPO-34 remained above 93%. This is because the introduction of cerium or lanthanum effectively slowed down the dealumination process, and inhibited the aggregation of copper species on Cu-SAPO-34 during hydrothermal ageing, further maintaining a relatively large specific surface area and uniform pore size distribution. At the same time, the redox properties of Cu-SAPO-34 were enhanced and the surface acidic sites were stabilised, further facilitating the adsorption and activation of the reactants.
Baiyun Ebo rare earth minerals are rich in rare earth elements and have been used to good effect in the preparation of NH3-SCR catalysts. There has been some progress in the preparation of denitrification catalysts directly from minerals (rare earth concentrates, rare earth tailings), which contain not only many rare earth elements, but also some transition metals, which can significantly improve the denitrification efficiency. Meng Zhaolei7 et al. used Fe2O3 loaded on Baiyun Ebo rare earth concentrate by impregnation method, and the denitrification rate could reach more than 80% at 350 °C. The catalyst surface became rough and porous, which increased the specific surface area; and most of the Fe2O3 was embedded on the rare earth concentrate in a highly dispersed or amorphous form, which formed a small portion of FeCeO composite oxide. Zhang8 et al. prepared catalysts by using roasted weak acid-weak base leaching method for the denitrification of rare earth concentrates. The denitrification rate was up to 92.8% at 400 °C. The results showed that the Ce7O12 content in the active fraction increased and was more uniformly distributed. The specific surface area increased and the exposure of active sites increased. Wang Jian9 et al. used different microwave roasting temperatures to treat the tailings, resulting in a denitrification rate of up to 96.1% at 400 °C. This has guiding significance for the efficient use of rare earth tailings. However, the current research on catalysts prepared using rare-earth concentrates and rare-earth tailings has focused on medium and high temperatures, and there has been no relevant research on their low temperature NH3-SCR performance.
From the process mineralogy of Baiyun Ebo rare earth concentrates,10 it can be obtained that the rare earth minerals are mainly dominated by Ce elements. Ce based catalysts have excellent low temperature catalytic properties, and many researchers have used CeO2 as a carrier to improve the performance of NH3-SCR. Zhang Runduo11 et al. prepared LaMnO3, LaMnO3/TiO2 and LaMnO3/CeO2 catalysts to investigate the effect of the carrier on the catalytic performance of NH3-SCR, and the results showed that the best low-temperature catalytic performance was achieved with CeO2 as the carrier. The main reason is that at temperatures less than 200 °C, the interaction between LaMnO3 and CeO2 facilitates the movement of lattice oxygen, which can promote partial oxidation of NO to NO2, allowing the NO reduction reaction to proceed according to the fast NH3-SCR reaction. Yao Xiaojiang12 prepared a series of MnOx/CeO2 catalysts by adjusting the solvents (deionised water, anhydrous ethanol, acetic acid, oxalic acid solution). The MnOx/CeO2 catalysts prepared with oxalic acid solution as the solvent showed over 80% NO conversion in the range of 100–250 °C and good low temperature sulphur and water resistance. The rare earth elements in rare earth concentrates are mainly found in cerium fluorocarbon and monazite, with Ce elements accounting for more than 38% of the total. As purified cerium fluoride ore is currently unavailable, I13 have used a hydrothermal method to synthesise cerium fluoride ore, which is highly compatible with the mineral phase of cerium fluoride ore in the concentrate. Natural monazite ore can be obtained from the Baiyun Ebo. So this experiment will use the synthesized fluorocerium cerium ore and purified monazite ore together as a carrier, loaded with Mn and Fe active substances, and provide theoretical guidance significance for the use of rare earth minerals of dolomite as a denitrification catalyst carrier by exploring its excellent performance and mechanism as a low-temperature denitrification catalyst carrier.
2. Experimental methods
2.1. Materials and methods
In this paper, CeCO3F was synthesised by hydrothermal method using cerium nitrate as raw material, mixed with sodium bicarbonate and sodium fluoride. The synthesized CeCO3F was mixed with monazite ore purified from dolomite concentrate as a carrier and loaded with Mn and Fe in a certain ratio. The surface properties and denitrification activity were tested to determine the best catalyst. The chemical reagents used in the experiments were: Ce(NO3)3·6H2O (mass fraction), analytical purity, Tianjin Comio Chemical Reagent Co. NaHCO3, analytical purity, Tianjin Windship Chemical Reagent Technology Co. NaF, analytical purity, Tianjin Windship Chemical Reagent Technology Co. Monazite ore is monazite ore obtained from the purification of Baiyun Ebo concentrate.
2.2. Preparation of the catalyst
The hydrothermal method was used to synthesize CeCO3F. A certain amount of Ce(NO3)3·6H2O was placed in 100 mL of PTFE liner at room temperature, and a certain amount of NaF and NaHCO3 was dissolved in 80 mL of distilled water. The mixed solution was poured into the PTFE liner and put into an autoclave at 120 °C under atmospheric pressure and stirred and heated for 2 h for hydrothermal reaction. After cooling, the mixture is filtered and dried at 110 °C to obtain synthetic cerium fluorocarbon ore. The synthetic cerium fluorocarbon ore and a certain amount of monazite ore were then mixed and impregnated at room temperature for 24 h, filtered and dried to obtain CeCO3F-monazite carrier. It was divided into several portions and loaded with Mn according to the molar ratio of Ce in the carrier, and 50% Mn(NO3)2 solution was added dropwise to the carrier in the ratio of Ce
:
Mn = 2
:
1, Ce
:
Mn = 5
:
1, Ce
:
Mn = 8
:
1, respectively. It was transferred to 100 mL of distilled water and macerated for 24 h. The solution was filtered and dried at 110 °C. Finally, the sample was microwave roasted at 500 °C for 5 min to obtain the catalyst loaded with Mn. In the same way, Fe2O3 was added to the carrier in the ratio of Ce
:
Fe = 5
:
1, then the solution was impregnated for 24 h, filtered and dried, and roasted at 500 °C for 5 minutes to obtain catalysts loaded with Fe. The catalyst was tested for catalytic performance and the optimum Mn loading and Fe loading were selected, which will be loaded onto the carrier in the ratio of Mn
:
Fe = 1
:
1.
2.3. Testing of catalytic performance
The experiments were carried out in a reaction apparatus with quartz tubes for testing the activity of the catalyst NH3-SCR. The reaction apparatus consists of a gas mixing tank – flow meter, standpipe furnace, quartz tube, Fourier infrared spectroscopy flue gas analyser and computer data acquisition system. The standpipe furnace was heated by a silicon-molybdenum rod model 1800 with a rated temperature of 1600 °C and an internal diameter of 20 mm and a length of 1.2 m from Nanjing Boynton Instrument Technology Co. The Fourier infrared spectroscopy (FTIR) flue gas analyser and data acquisition system were manufactured in Finland, and the model number was GASMET-DX4000. The simulated gas components were as follows: NH3 500 ppm, NO 500 ppm, O2 at a volume fraction of 3% of the total, N2 as the equilibrium gas, a total gas flow of 100 mL min−1, an air velocity of approximately 8000 h−1 g−1 and a catalyst dosage of 0.6 g for each test.
Firstly, the test equipment and controls such as the gas cylinder valve are opened and a constant gas flow rate in the empty tube is carried out so that the gas flow in the gas path is constant and the gas content detected by the flue gas analyser is stable. Then the quartz wool and catalyst are placed in the quartz tube and warmed up to test the denitrification activity of the catalyst in the temperature range of 100 °C to 400 °C. The denitration data is recorded at 50 °C intervals and the constant temperature time at each temperature point is 15 min. The content of the gas measured by the flue gas analyser during this time is the NOx content of the treated virtual flue gas.
The formula for calculating the denitration rate of the catalyst treated by the activity test is:
η is the NO removal rate; (NO)in is the percentage of NO detected after smoothing the inlet of the flue gas simulation system; (NO)out is the percentage of NO detected by the flue gas analyser at the outlet test of the flue gas simulation system.
2.4. Characterisation of the catalysts
XRD diffractometer type D8 ADVANCE, BRUKER, Germany; angle of, range 10° to 80°. Observation of the surface structure and morphology of the catalyst using a field emission scanning electron microscope type 500 AMCS, Carl Zeiss, Germany. Simulated flue gas denitrification unit (including flowmeter, heating furnace, Beijing Pioid Electronic Technology Co., Ltd; Laoying 3022 comprehensive flue gas analyser, Laoshan Institute of Applied Technology, Qingdao). Programmed temperature rise desorption (TPD) and programmed temperature rise reduction (TPR) were carried out on a chemisorption instrument (from Beijing Peod Electronic Technology Co., Ltd.) with a thermal conductivity detector (TCD). A 0.2 g sample of catalyst was purged under N2 atmosphere for 10 min prior to the experiment and dehydrated at a constant temperature of 200 °C for 30 min, followed by NH3 adsorption at 100 °C for one hour. Finally the catalyst was ramped up from 50 °C to 600 °C at a rate of 10 °C min−1. For H2-TPR, the catalyst samples were ramped up from 50 °C to 800 °C at a rate of 10 °C min−1.
3. Results and discussion
3.1. Experiments on the optimum Mn loading
3.1.1 Testing of the catalytic performance. Our previous pre-experimental results showed that, the best catalytic performance was obtained by loading Fe2O3 onto CeCO3F plus monazite at a ratio of 5
:
1 Ce
:
Fe. Therefore, in this paper, only the catalyst loaded with Fe alone was tested for denitrification performance. The results showed that the catalyst loaded with Fe alone gave a NOx conversion of 79% at 250 °C. In order to investigate the optimum loading of synthetic CeCO3F plus monazite loaded Mn, the denitrification activity was tested and the results are shown in Fig. 1. It can be seen from the figure that before 150 °C, the catalyst activity was relatively low for different percentages of Mn loadings, stabilising within 10%. After 150 °C, the catalytic performance of the catalysts improved significantly due to the interaction between Mn and Ce, which showed good catalytic activity. The denitrification rate of the three catalysts began to rise rapidly, reaching the highest rate at 400 °C, with the denitrification rate of the Ce
:
Mn ratio of 5
:
1 reaching 58%. As the temperature continued to increase, the catalytic activity of the catalysts started to decrease and as this ratio showed a more excellent catalytic performance, a doping ratio of 5
:
1 Ce
:
Mn was determined as the optimum loading ratio.
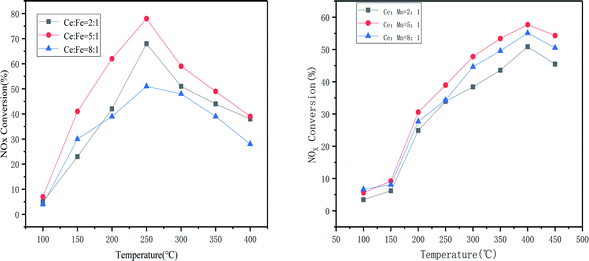 |
| Fig. 1 NH3-SCR activity of CeCO3F-monazite loaded with different proportions of Mn and Fe (reaction conditions: 500 ppm NO, 500 ppm NH3, 3% O2, N2 as equilibrium gas). | |
3.1.2 Structural characteristics (XRD). Fig. 2 showed XRD patterns of different ratios of Mn loaded by the synthesis of CeCO3F plus natural monazite. From the figure, it can be observed that in all three catalysts loaded with different ratios of Mn, obvious diffraction peaks of cerium fluorocarbon can be observed and the intensity of the diffraction peaks is strong, which not only indicates a good synthesis effect, but also a good stability of the synthesised CeCO3F without decomposition after microwave roasting. From the figure, MnOx species such as Mn3O4, Mn2O3 and MnO2 can also be observed. Compared with the catalysts with Ce
:
Mn of 2
:
1 and 8
:
1, the diffraction peaks of MnOx species on the 5
:
1 catalyst are relatively weak, which indicates that the dispersion of MnOx species on the catalyst gradually becomes better and the Mn species are mainly dispersed on the catalyst surface in amorphous form,14 not only that, there are more species of MnOx species on its surface, and the interconversion between Mn ions is beneficial to improve the redox performance. As can be seen from the cell parameters in Table 1, the differences in grain size and crystalline spacing between the three are not significant. However, the catalyst with a Ce
:
Mn of 5
:
1 has a smaller spacing and size, indicating a relatively good dispersion of the carrier and active components, which is consistent with the activity test results. It was also observed that the diffraction peaks of cerium fluorocarbon also tended to fade and decrease compared to the other two catalysts, suggesting that the 5
:
1 catalyst was the best sample for the Mn loading.
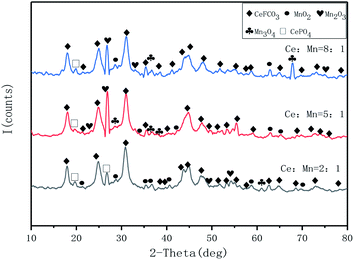 |
| Fig. 2 XRD pattern of CeCO3F-monazite loaded with different proportions of Mn. | |
Table 1 Physical structure properties of the catalysts
Catalysts |
D (nm) |
Crystallite dimension |
Ce : Mn = 2 : 1 |
5.014 |
177 |
Ce : Mn = 5 : 1 |
5.142 |
147 |
Ce : Mn = 8 : 1 |
4.990 |
423 |
3.2. The best active substances
3.2.1 Test of catalytic performance. The catalysts were loaded individually according to the optimum Mn and Fe loading ratios that had been determined, and then both were loaded simultaneously according to the same Mn and Fe ratios. As shown in Fig. 3.
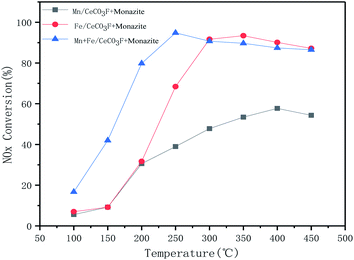 |
| Fig. 3 NH3-SCR activity of Mn and Fe loaded at the same time and NH3-SCR activity of Optimum proportion of separate load Mn, Fe. (Reaction conditions: 500 ppm NO, 500 ppm NH3, 3% O2, N2 as equilibrium gas) | |
The catalysts loaded with Fe alone showed very good activity in the range of 250 °C to 350 °C, up to 93%. This also indicated that the loading of Fe could better interact with the carrier to improve the catalytic activity. The catalysts loaded with both Mn and Fe reached 94.8% denitrification at 250 °C. Not only did they have good denitrification rates, but they also widened the temperature window and moved towards lower temperatures, with a decreasing trend in catalytic activity when the temperature exceeded 350 °C. This is due to the oxidation of ammonia gas, which can produce NO and NO2 gas at higher temperatures.16–18 The higher activity in the catalyst may lead to a rapid decrease in NOx conversion at higher temperatures due to the increased redox capacity.19 The increase in temperature provides energy that allows for enhanced interactions between Mn, Fe and Ce, thus facilitated conversion of NO and accelerated reduction of NO by NH3. At higher temperatures, the movement and collisions of reacting molecules increase, so activity is enhanced in the low temperature range, however, the NH3 oxidation side reaction (consumption of NH3 reductant to produce N2O, NO and NO2) is the dominant reaction at higher temperatures, resulting in reduced catalytic activity.18,20 Fig. 4 shows the stability of the catalytic activity of Mn + Fe/CeCO3F + monazite at 250 °C. It is clear that the catalyst can maintain the best denitrification effect at the appropriate temperature for a constant 15 h, which indicated that the denitrification performance is stable and not easily deactivated.
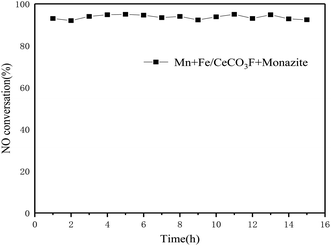 |
| Fig. 4 Stability tests of the catalyst. | |
3.2.2 Structural characteristics (XRD). When loaded with Mn and Fe at the same time. As shown in the figure, only weak MnO2 diffraction peaks were detected at 47.2°, 52.8° and 57.6°, which indicated that the Fe doping favoured a high degree of dispersion of the MnOx species on the catalyst, while the intensity of the Fe oxide diffraction peaks was also very weak, which indicated a good dispersion of the Fe oxide species on the catalyst surface (Fig. 5).
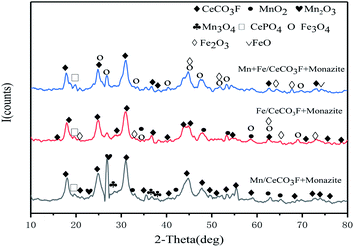 |
| Fig. 5 XRD pattern of Mn and Fe loaded at the same time and Mn and Fe with separate loads. | |
In comparison with the catalyst loaded with Fe only, it can be clearly observed that the diffraction peak of Fe oxide is stronger than that of the catalyst loaded with both Mn and Fe, but the diffraction peak of cerium fluoride is significantly weaker than that of the catalyst loaded with Mn, which indicated that the doping of Fe can better promote the dispersion of the carrier, and the interaction between Fe and Ce is stronger than that between Mn and Ce. The catalysts loaded with Mn and Fe at the same time can have stronger interactions between the two, promoting each other's dispersion on the catalyst surface and thus improving the catalytic activity. From the cell parameters in Table 3, it can be seen that the composite catalysts loaded with both Mn and Fe have the largest grain surface spacing and a significant variation in grain size can be observed. Compared to the other catalysts, it has the smallest grain size, which also indicated that both manganese oxides and iron oxides were well loaded onto the catalyst surface.21,23 This is further evidence of the good dispersion of the two, which fully exploits each other's catalytic activity and facilitates the NH3-SCR reaction.
Table 3 Physical structure properties of the catalysts
Catalysts |
D (nm) |
Crystallite dimension |
Mn/CeCO3F + monazite |
5.142 |
147 |
Fe/CeCO3F + monazite Mn + Fe/CeCO3F + monazite |
5.290 |
140 |
5.833 |
131 |
3.2.3 Surface physical properties. The enhanced pore capacity pore size in the BET data facilitates the diffusion of the reaction medium and the entry and exit of gases, which increase the reaction rate of the catalyst.22 The very large specific surface area and pore size of the Fe-only loaded catalysts indicate that the Fe loading has better catalytic activity than the Mn loading alone, which is consistent with the XRD results. The specific surface area and pore volume pore size are the largest when loaded with both Mn and Fe, which can reach 28.92 m2 g−1. This indicates that Mn and Fe are well dispersed on the surface of the carrier, and their interaction can promote the dispersion of each other on the surface of the carrier, which is more conducive to the adsorption of reactive gases on the surface of the catalyst, and promote the SCR denitration reaction (Table 4).
Table 4 The BET data of Samples
Samples |
Surface area (m2 g−1) |
Pore volume (ml g−1) |
Pore size (nm) |
Mn/CeCO3F + monazite |
21.82 |
0.1252 |
35.36 |
Fe/CeCO3F + monazite |
27.16 |
0.1375 |
35.76 |
Mn + Fe/CeCO3F + monazite |
28.92 |
0.1399 |
36.52 |
3.2.4 Surface topography. Scanning electron microscopy was used to observe the surface structure of the catalyst. The graph showed that the catalyst with the optimum Mn loading had the active components distributed on the surface of the carrier in very fine particles and had a flat surface structure with slightly larger pores, which was consistent with the BET results. The catalyst loaded with Fe only has a better dispersion on the surface of the carrier, and the various types of material on the surface of the carrier are interspersed with each other, increasing the specific surface area. At the same time the catalyst loaded with Mn and Fe showed a large number of cracks on the surface, which may be due to the interaction of both Mn and Fe on the surface of the carrier, and prompt the conversion of large particles into smaller particles, which increased the number of active sites, these properties make this catalyst favourable to the adsorption and desorption behaviour of the gas. In addition, the microwave heating makes the surface of the particles show more cracks, and the characteristics of the microwave uniform heating makes the catalyst molecules oscillate, which increases the specific surface area of the catalyst and facilitates the improvement of denitrification efficiency (Fig. 6).
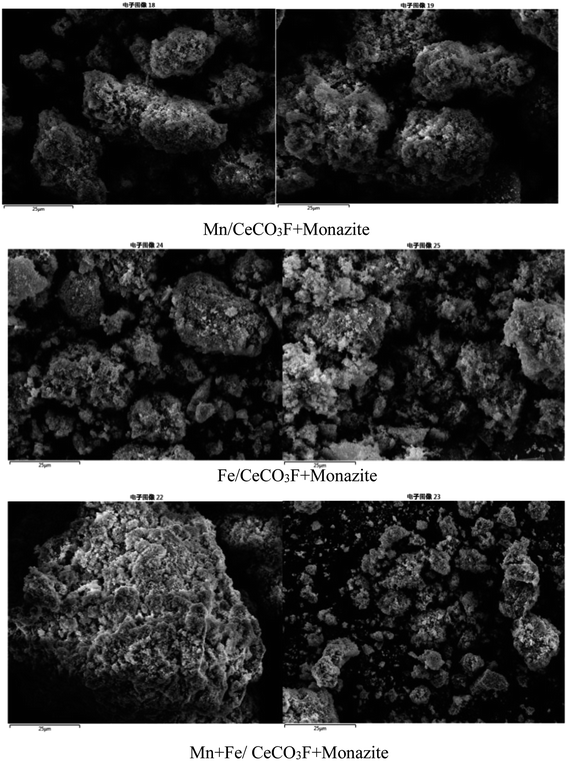 |
| Fig. 6 SEM diagram of Mn and Fe loaded at the same time and Mn, Fe separate load. | |
3.2.5 Reduction and desorption performance of catalyst. In order to investigate the low temperature redox capability of the catalyst, it was characterised for H2-TPR. It is well known that the redox properties of catalysts are a key factor in the oxidation of NO to NO2 and can facilitate the fast SCR reaction [NO + NO2 + 2NH3 → 2N2 + 3H2O] (Fig. 7).23
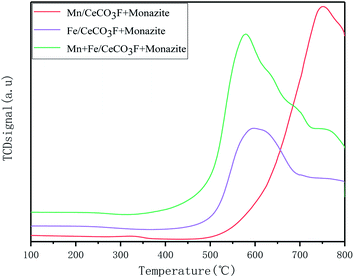 |
| Fig. 7 H2-TPR graph with Mn and Fe loaded at the same time and Mn and Fe loaded separately. | |
Stronger redox properties not only increase the oxidation rate of NO to NO2 conversion but also improve the oxidation reaction activity. As can be seen from the figure, for the catalyst loaded with Mn has a higher H2 reduction peak between 450 °C and 780 °C, which can be attributed to the process of MnO2/Mn2O3 → Mn3O4 → Mn.24–26 Due to the large variety of MnOx species, the reaction process can be interconverted, which facilitates the redox reaction.27 The reduction peaks in the high temperature section of the catalyst loaded with Mn at 700–780 °C, as obtained from the literature, can also be attributed to the reduction of the catalyst bulk phase CeO2.22,28 The catalysts loaded with both Fe and Mn showed reduction peaks at 575 °C, 690 °C and 760 °C, respectively, with the reduction peak at 575 °C attributed to the superposition of the reduction of Mn3O4 to MnO and the reduction of surface Ce4+ to Ce3+.22 The reduction peak at 690 °C can be attributed to FeO → Fe.29 And when loaded with Fe and Mn at the same time, the position of the reduction peak moved towards the lower temperature compared to the other two catalysts. From Table 5 it can be seen that the area of their reduction peaks is the largest. This is probably due to the increase in reduction potential of the active component, the formation of oxygen vacancies and the appearance of more oxygen species on the surface, which facilitates the migration of oxygen and thus enhances the activation reaction of the catalysts, which indicated that the loading of Mn and Fe has greatly improved the redox properties of the catalysts. For the catalyst loaded with Fe only, a reduction peak appeared at 588 °C, which was attributed to the conversion of Fe3+ → Fe2+,30 and the position of the reduction peak was at a lower temperature compared to the other catalysts, making it easier for the redox reaction to take place, but slightly less redox-friendly than the catalysts loaded with both Mn and Fe.
Table 5 H2-TPR Suction and desorption curve peak area
In varying proportions |
Mn/CeCO3F + monazite |
Fe/CeCO3F + monazite |
Mn + Fe/CeCO3F + monazite |
Onset temperature (T/°C) |
476 |
445 |
348 |
Peak temperature (T/°C) |
748 |
599 |
571 |
Peak area |
3085.57 |
4924.24 |
7936.72 |
In addition to the redox properties, another key factor in NO removal is the adsorption and activation of NH3 on the NH3-SCR catalyst.31 The desorption peaks in the TPD curves correspond to the surface acidic sites of the catalysts. From the figure, it can be seen that when loaded with both Mn and Fe, this catalyst shows two strong desorption peaks at 164 °C and 275 °C, which correspond to the Brønsted acid site and the Lewis acid site, respectively. The peak areas were significantly larger than the other two, as shown in Table 6, which indicated that this catalyst had the highest amount of acid and reflected the fact that it had the most acid sites and stronger adsorption of NH3 than the other catalysts, which indicated better denitrification activity in the low temperature range. The catalyst loaded with only Fe also has peaks at 185 °C attributed to the desorption of weakly acidic sites, and 280 °C attributed to the desorption of moderately acidic sites. It follows that the low temperature peaks on the catalyst surface are associated with NH4+ on the Brønsted acidic sites and the high temperature peaks are associated with NH3 on the Lewis acidic sites (Fig. 8).
Table 6 NH3-TPD Suction and desorption curve peak area
In varying proportions |
Mn/CeCO3F + monazite |
Fe/CeCO3F + monazite |
Mn + Fe/CeCO3F + monazite |
Peak temperature (T/°C) |
180, 475 |
185, 280 |
164, 275 |
Peak area |
76.90 |
63.94 |
112.32 |
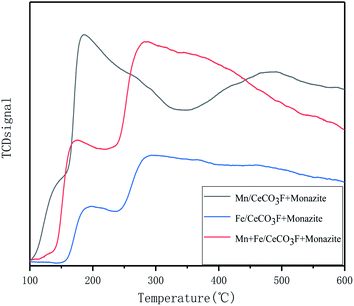 |
| Fig. 8 NH3-TPD graph with Mn and Fe loaded at the same time and Mn and Fe loaded separately. | |
To explore the adsorption behaviour of NOx on the catalyst surface, the catalyst was characterised for NO-TPD and the formation of surface NOx species is an important step in the NH3-SCR reaction (Fig. 9).
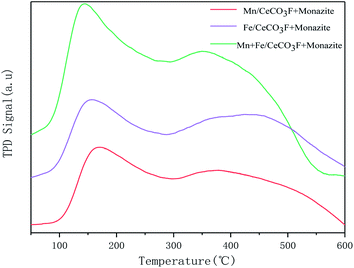 |
| Fig. 9 NO-TPD graph with Mn and Fe loaded at the same time and Mn and Fe loaded separately. | |
It has been reported in the literature that low temperature desorption peaks near 100 °C correspond to physical and weak chemisorption of NO. The desorption peaks near 300 °C correspond to the desorption of mono-ligand nitrate or nitrite, and those above 300 °C correspond to the decomposition of double-ligand or bridged nitrate.32–35 As can be seen from the figure, the catalyst loaded with Mn showed a desorption peak in the range of 100–250 °C. The NO-TPD reflects both the amount of NO adsorbed on the catalyst surface and the desorption temperature of NO on the catalyst surface, both of which can indirectly reflect the catalytic reactivity of the catalyst.34,36 When Mn and Fe were loaded simultaneously, two very obvious desorption peaks appeared in the range of 100–500 °C. The area of the desorption peaks was the largest compared to the other two catalysts, and the location of the desorption peaks was also in the low temperature section, and the peak width and peak height also changed significantly. The effect was also changed, which indicated that the combined effect of Mn and Fe increased the adsorption capacity of the catalysts on NO, which resulted in a large amount of NO adsorption on the catalyst surface and increased the amount of acid and active sites on the catalyst surface. When only Fe was loaded, the area, peak position and intensity of the desorption peaks were similar to those of the Mn loading alone, which also indicated that there is no difference in the facilitation of NO adsorption by the catalyst between Mn and Fe loading alone, and when the two load together interact, they have a greater advantage to the catalyst for selective catalytic reduction of NOx (Table 7).
Table 7 NO-TPD Suction and desorption curve peak area
In varying proportions |
Mn/CeCO3F + monazite |
Fe/CeCO3F + monazite |
Mn + Fe/CeCO3F + monazite |
Peak temperature (T/°C) |
164, 389 |
153, 441 |
141, 358 |
Peak area |
274.63 |
276.13 |
384.17 |
3.3. In situ infrared analysis and reaction mechanism research
In order to investigated the types of adsorbed species on the catalyst surface and the role of each adsorbed species on the NH3-SCR reaction, as well as its reaction mechanism under different temperature conditions, the Mn + Fe/CeCO3F + monazite composite catalysts were investigated in situ in the IR mechanism.
3.3.1 In situ infrared spectra of adsorption of NH3 and NO + O2 over time at 250 °C. In order to investigate the effect of the catalyst on the activation performance of NH3 adsorption at low temperatures, this experiment investigated the variation of NH3 adsorption with time at 250 °C, and the results are shown in Fig. 10. From the figure, it can be seen that the catalyst surface showed obvious infrared absorption peaks at 1109 cm−1, 1192 cm−1, 1293 cm−1, 1698 cm−1 and 1826 cm−1, where the absorption peaks at 1109 cm−1 were attributed to NH4+ species adsorbed on the Brønsted acidic site on the catalyst surface,35 and the absorption peaks at 1192 cm−1, 1293 cm−1, 1698 cm−1 and 1593 cm−1 were attributed to NH3 species adsorbed on the Lewis acidic site.36,37 It can be seen that the predominant NH3 adsorption site on the catalyst surface is the Lewis acidic site, with a small number of Brønsted acidic sites. Previous studies have shown that the presence of Brønsted acidic sites has a facilitative effect on the NH3-SCR reaction.38 The adsorption of the two acidic sites indicates that the acidic sites are abundant on the catalyst surface and that the NH3 species and NH4+ species adsorbed on the catalyst surface are more stable with time.
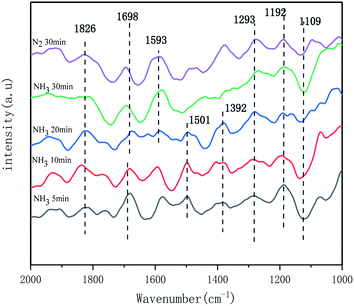 |
| Fig. 10 In situ infrared spectra of NH3 adsorbed by the catalyst at 250 °C. | |
The catalyst surface showed infrared absorption peaks at 1501 cm−1, 1392 cm−1, with the peak at 1392 cm−1 attributed to the deformation vibration of the N–H bond in the NH4+ adsorbed by the Brønsted acid centre on the catalyst surface,39,41 and the absorption peak at 1501 cm−1 attributed to the amide (–NH2) species, but the surface species gradually disappeared with increasing time, which indicated unstable adsorption.
To further investigated the effect of the catalyst on the NO adsorption and activation performance, the in situ IR spectra of NO + O2 adsorption over time at 250 °C were also examined. As shown in Fig. 11, the infrared absorption peaks at 1937 cm−1, 1834 cm−1, and 1818 cm−1 were attributed to the weak adsorption species of NO formed on the catalyst surface,40 and the adsorption species did not change much with increasing time, which indicated that it was more stable. The IR peak at 1115 cm−1 was attributed to the even secondary nitrate species [–(N2O2)2−], the peak at 1211 cm−1 to the bridged nitrate species and 1310 cm−1 to the bidentate nitrate species. And the adsorbed species did not decrease with increasing time and N2 purging. The peak at 1632 cm−1 was attributed to the weakly adsorbed NO2 species on the catalyst surface. According to the literature,40,42 NO2 is an important intermediate species for the occurrence of fast SCR reactions under low temperature conditions. And the large number of adsorbed species on the catalyst surface indicates a very good activation capacity for NO adsorption.
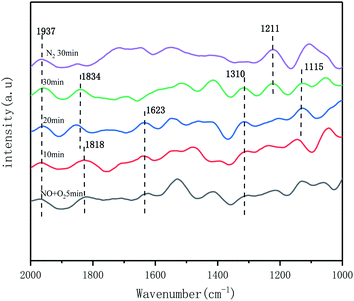 |
| Fig. 11 NO + O2 adsorption in situ infrared spectra of the catalyst at 250 °C. | |
3.3.2 In situ infrared spectra of NH3 and NO + O2 adsorbed species on the catalyst surface under different temperature conditions. In this experiment, the adsorption and activation of NH3 on the catalyst surface at different temperatures was investigated by in situ IR spectroscopy, and the presence of NH3 species on the catalyst surface at different temperatures was studied. As shown in Fig. 12, it is evident that the catalyst is present on the surface mainly in the form of NH3 and NH4+. The catalyst shows infrared absorption peaks at 1431 cm−1, 1516 cm−1 and 1597 cm−1, where the absorption peak at 1431 cm−1 is attributed to NH4+ species adsorbed on the Brønsted acidic site on the catalyst surface,37 and the absorption peak at 1516 cm−1 is attributed to the splitting of the bidentate nitrate due to the adsorption of NH3 species by oxygen oxidation on the catalyst surface.41 The absorption peak at 1597 cm−1 is attributed to liganded NH3 species adsorbed on the Lewis acidic site on the catalyst surface. This shows that the main adsorption and activation sites for NH3 species on the catalyst surface are the Brønsted acid site and the Lewis acid site. As the temperature increases, the absorption peak at 1431 cm−1 gradually decreases and almost disappears at 250 °C, indicated that the NH4+ species adsorbed on the Brønsted acid site on the catalyst surface are unstable and prone to thermal decomposition and desorption. However, the IR absorption peak at 1597 cm−1 did not change significantly with increasing temperature, which indicated that the NH3 species adsorbed on the Lewis acid site on the catalyst surface were more stable, and only the NH3 species on the Lewis acid site could be detected in the high temperature section, which suggested that the adsorption of NH3 by the catalyst in the high temperature section was mainly carried out on the Lewis acid site.
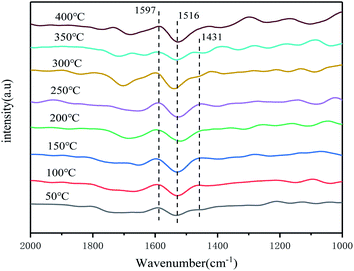 |
| Fig. 12 In situ infrared spectra of NH3 adsorption by the catalyst at different temperatures. | |
The adsorption and activation processes of NO + O2 species on the catalyst surface under different temperature conditions were subsequently investigated by in situ infrared spectroscopy, to discuss the forms and changes of NOx species present on the catalyst surface under different temperature conditions. From Fig. 13, it can be seen that IR absorption peaks appeared on the catalyst surface at 1407 cm−1, 1499 cm−1 and 1536 cm−1, where all three peaks can be attributed to monodentate nitrate species,39,42 and the IR absorption peak at 1617 cm−1 was attributed to bridged nitrate species.38 As the temperature increased, the peaks of monodentate nitrate species at 1407 cm−1, 1499 cm−1, and bridged nitrate at 1617 cm−1 gradually decreased, which indicated that the adsorbed species on the catalyst surface began to undergo desorption and pyrolysis reactions, and the main active sites in the low temperature section were occupied by bridged nitrate and some of the monodentate nitrate. However, the monodentate nitrate species at 1536 cm−1 is more stable in the high temperature stage, which indicated that it has good thermal stability and occupies the active sites in the high temperature section. Therefore, it can be inferred that the NH3-SCR reaction on the catalyst surface may follow different reaction paths due to different reaction temperatures.
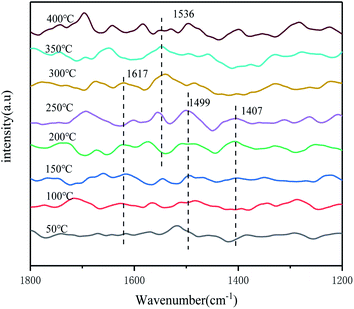 |
| Fig. 13 In situ infrared spectra of NO + O2 adsorption by the catalyst at different temperatures. | |
3.3.3 In situ infrared spectra of reaction of NH3 and NO + O2 pre-adsorbed species on the catalyst surface at 250 °C. To further investigate the NH3-SCR reaction mechanism of the catalyst, in situ IR spectroscopy of the catalyst was carried out at 250 °C under different reaction conditions. Firstly, NH3 gas was passed into the IR reaction cell containing the catalyst for 60 min, prior to which N2 was used as a supplementary gas to pre-treat the catalyst at 200 °C for 30 min, then the NH3 gas was stopped and purged with N2 for 10 min, after which NO + O2 gas was then passed into the reaction cell. The changes in the IR spectrum were observed as shown in Fig. 14. First, the adsorption peak due to gaseous NH3 appears at 1762 cm−1 after the passage of NH31h.39 The absorption peaks at 1517 cm−1 and 1363 cm−1 were attributed to the adsorption of the ammonia dehydrogenation product NH3+ at the Brønsted acidic site and to the deformation movement of the mid-N-H bond in NH4+.39 The peaks at 1280 cm−1, 1612 cm−1 and 1679 cm−1 belong to NH3 species adsorbed at Lewis acidic sites.39,43,44 The abundant acidic sites on the catalyst surface may have been provided by the dropwise addition of manganese nitrate solution in addition to the carrier itself. After a subsequent purge of N2 for 10 min, followed by the passage of NO + O2 atmosphere for 5 min it was observed that the peaks belonged to NH3 species at 1679 cm−1 and NH4+ species at 1363 cm−1 decreased, which indicated that both the Brønsted acidic site and the Lewis acidic site played a role. As the NO + O2 pass time increased, absorption peaks appeared on the catalyst surface for the monodentate nitrate species (1280 cm−1 and 1517 cm−1), the bridged nitrate (1612 cm−1), and the bidentate nitrate species (1700 cm−1) produced at 20 min pass time. The peak at 1762 cm−1 was attributed to the telescopic motion of N
O. The presence of O2 facilitated the conversion of NO. The peaks at 1920 cm−1 and 1842 cm−1 belong to NO species in the weakly adsorbed state on the catalyst surface.39 The monodentate nitrate species at 1517 cm−1 disappears after 10 min and is less stable, while the intensity of the other NOx peaks gradually increases, which also indicates that both adsorbed NH3 and NH4+ species are involved in the low temperature SCR reaction and react with the NOx species produced.
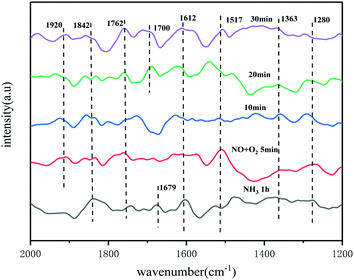 |
| Fig. 14 In situ infrared spectra of NO + O2 reacting with preadsorbed NH3 species on the catalyst surface at 250 °C. | |
Fig. 15 showed an in situ IR spectrum of the reaction of NH3 with pre-adsorbed NO + O2 species at 250 °C. At 250 °C temperature, when NO + O2 was introduced into the reaction cell system for 60 min, the appearance of distinct monodentate nitrate species (1263 cm−1, 1389 cm−1, 1500 cm−1),45 bridged nitrate species (1591 cm−1), and bidentate nitrate species (1678 cm−1) can be observed on the catalyst surface. The IR absorption peak at 1799 cm−1 is attributed to the stretching motion of the N
O bond, and the peak at 1918 cm−1 is attributed to the weakly adsorbed species formed by NO on the catalyst surface. With the passage of NH3, a significant weakening trend occurred for monodentate nitrate, bidentate nitrate and bridged nitrate species. The absorption peak disappeared at 10 min with increasing time of NH3 introduction for all nitrate species. This also indicated that the nitrate species on the catalyst surface were partially involved in the reaction. With further passage of NH3, NH3 species adsorbed on the Lewis acidic site (1263 cm−1) and NH4+ species adsorbed on the Brønsted acidic site appeared on the catalyst surface (1530 cm−1, 1708 cm−1).35 The peaks at 1624 cm−1 and 1878 cm−1 belong to the active intermediate NH2 after dehydrogenation of NH3, while the peaks at 1799 cm−1 and 1389 cm−1 belong to the adsorption peak formed by gaseous NH3 and the deformation vibration of the N–H bond in the NH4+ adsorbed at the Brønsted acid centre of the catalyst, respectively. The peak intensity is also more stable with increasing time, and some of the peaks show an enhancement trend. It can be concluded that the catalyst surface follows the L-H mechanism, where the nitrate species and NH3/NH4+ species on the catalyst surface are the main intermediate species involved in the reaction, both of which undergo redox reactions on the catalyst surface to produce N2 and H2O. The catalytic mechanism is shown in Fig. 16.
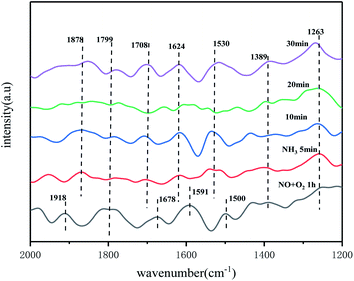 |
| Fig. 15 In situ infrared spectra of NH3 reacting with preadsorbed NO + O2 species on the catalyst surface at 250 °C. | |
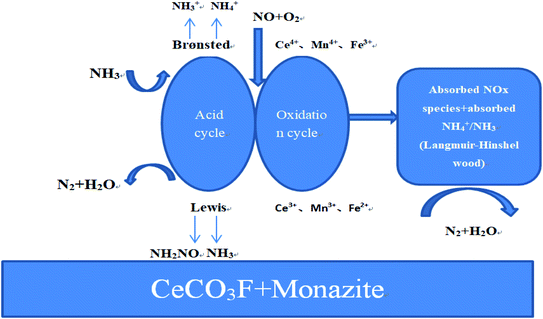 |
| Fig. 16 L–H reaction mechanism of Mn + Fe/CeCO3F-monazite. | |
4. Conclusion
In this experiment, CeCO3F was synthesised by hydrothermal method, and the synthesised CeCO3F was mixed with natural monazite ore as a carrier and loaded with Mn and Fe using the impregnation method. The optimum loading was determined by adding different ratios of amounts and the results showed that the best denitrification performance was achieved when Ce
:
Mn was 5
:
1. The load ratio is 1
:
1 for Fe
:
Mn, it was found that the composite catalyst supported by Fe and Mn at the same time showed excellent catalytic performance for denitrification, and the denitrification rate reached 94.8% at 250 °C. The loading of Mn and Fe played a very critical role in enhancing the catalytic activity, and their interaction promoted the dispersion of each other on the carrier surface, greatly increasing the specific surface area of the composite catalyst. Impregnation with manganese nitrate solution increased the acidic sites and the amount of acid. Microwave roasting resulted in the formation of more oxygen vacancies on the catalyst surface, which facilitated the migration of oxygen. In situ infrared spectroscopy was used to investigate the adsorption and activation properties of a new Mn–Fe/CeCO3F-monazite catalyst for NO and NH3 species, as well as the species and reaction behaviour of intermediate species in the NH3-SCR reaction. The results showed that the NH3-SCR reaction process occurring on the catalyst surface mainly follows the L–H mechanism. The bidentate nitrate and bridging nitrate species generated by the adsorption activation of gaseous NO on the catalyst surface and the NH3/NH4+ species generated by NH3 at the Lewis acidic site and Brønsted acidic site on the catalyst surface are the main intermediate species involved in the reaction, which undergo redox reactions to generate N2 and H2O on the catalyst surface. The excellent performance of CeCO3F-monazite carriers provides a theoretical basis for the use of Baiyun Ebo rare earth minerals as denitrification catalyst carriers and high value utilization.
Conflicts of interest
There are no conflicts to declare.
Acknowledgements
This study was financially supported by Natural Science Foundation of Inner Mongolia (Grant No. 2019ZD13), National Natural Science Foundation of China (Grant No. 51866013). Thanks for Start-up Funds for Talent Introduction and Scientific Research of Institutions in Inner Mongolia Autonomous Region.
References
- F. Luck and J. Roiron, Selective catalytic reduction of NOx emitted by nitric acid plants, Catal. Today, 1989, 4(2), 205–218 CrossRef CAS.
- L. J. Alemany, F. Berti, G. Busca, G. Ramis, D. Robba, G. P. Toledo and M. Trombetta, Characterization and composition of commercial V2O5-WO3-TiO2 SCR catalyst, Appl. Catal., B, 1996, 10(4), 299–311 CrossRef CAS.
- K. J. Lee, P. A. Kumar, M. S. Maqbool, K. N. Rao, K. H. Song and H. P. Ha, Ceria added Sb-V2O5/TiO2 catalysts for low temperature NH3-SCR: Physico-chemical properties and catalytic activity, Appl. Catal., B, 2013, 142–143, 705–717 CrossRef CAS.
- F. D. Liu, H. He, C. B. Zhang, W. P. Shan and X. Y. Shi, Mechanism of the selective catalytic reduction of NOx with NH3 over environmental-friendly iron titanate catalyst, Catal. Today, 2011, 175(1), 18–25 CrossRef CAS.
- J. P. Wang, Z. Yan, L. L. Liu, Y. Y. Zhang, Z. T. Zhang and X. D. Wang, Low-temperature SCR of NO with NH3 over activated semi-coke composite-supported rare earth oxides, Appl. Surf. Sci., 2014, 309, 1–10 CrossRef CAS.
- J. Fan, P. Ning, Y. C. Wang, Z. X. Song, X. Liu, H. M. Wang, J. Wang, L. Y. Wang and Q. L. Zhang, Significant promoting effect of Ce or La on the hydrothermal stability of Cu-SAPO-34 catalyst fo NH3-SCR reaction, Chem. Eng. J., 2019, 369, 908–919 CrossRef CAS.
- Z. L. Meng, B. W. Li, J. Y. Fu, C. Zhu and W. F. Wu, Research on NH3-SCR denitrification performance of Fe2O3 mineral catalytic materials supported by rare earth concentrates, Chin. J. Bioprocess Eng., 2020, 08–19, 1–10 Search PubMed.
- K. Zhang, J. H. Zhu, S. N. Zhang, N. Li, H. J. Luo, B. W. Li, Z. W. Zhao, G. Jinang and W. F. Wu, Influence of Impurity Dissolution on Surface Properties and NH3-SCR Catalytic Activity of Rare Earth Concentrate, Minerals, 2019, 9(4), 246 CrossRef CAS.
- J. Wang, Z. J. Gong, B. W. Li, G. D. Xu and W. F. Wu, Mineral analysis of rare earth tailings and the effect of microwave roasting on its catalytic denitrification performance, Mater. Rev., 2020, 34(16), 16072–16076 Search PubMed.
- Z. H. Zhu, Z. F. Yang and Q. W. Wang, Research on Process Mineralogy of Bayan Obo Rare Earth Concentrate, Nonferrous Met., 2019,(006), 1–4 Search PubMed.
- R. D. Zhang, W. Yang, N. Luo, P. X. Li, Z. G. Lei and B. H. Chen, Low-temperature NH3-SCR of NO by lanthanum manganite perovskites: Effect of A-/B-site substitution and TiO2/CeO2 support, Appl. Catal., B, 2014, 146, 94–104 CrossRef CAS.
- X. J. Yao, T. T. Kong, L. Chen, S. M. Ding, F. M. Yang and L. Dong, Enhanced low-temperature NH3 -SCR performance of MnOx/CeO2 catalysts by optimal solvent effect, Appl. Surf. Sci., 2017, 420(31), 407–415 CrossRef CAS.
- N. Li, S. H. Zhang, H. Li, J. J. Wang, K. Zhang and W. F. Wu, Study on the microstructure and denitration performance of synthesized CeCO3F, J. Chin. Rare Earth Soc., 2020, 38(5), 610–616 Search PubMed.
- T. Boningari, P. R. Ettireddy, A. Somogyvari, Y. Liu, A. Vorontsov, C. A. McDonald and P. G. Smirniotis, Influence of elevated surface texture hydrated titania on Ce-doped Mn/TiO2 catalysts for the low-temperature SCR of NOx under oxygen-rich conditions, J. Catal., 2015, 325, 145–155 CrossRef CAS.
- P. J. Gong, J. L. Xie, D. Fang, F. He, F. X. Li and K. Qi, Enhancement of the NH3 -SCR property of Ce-Zr-Ti by surface and structure modification with P, Appl. Surf. Sci., 2020, 505 Search PubMed.
- H. F. Chen, Y. Xia, H. Huang, Y. P. Gan, X. Y. Tao, C. Liang, J. M. Luo, R. Y. Fang, J. Zhang, W. K. Zhang and X. S. Liu, Highly dispersed surface active species of Mn/Ce/TiW catalysts for high performance at low temperature NH3-SCR, Chem. Eng. J., 2017, 330, 1195–1202 CrossRef CAS.
- G. Ramis, L. Yi, G. Busca, M. Turco, E. Kotur and R. J. Willey, Adsorption, Activation, and oxidation of ammonia over SCR catalysts, J. Catal., 1995, 157(2), 523–535 CrossRef CAS.
- R. D. Zhang, W. Yang, N. Luo, P. X. Li, Z. G. Lei and B. H. Chen, Low-temperature NH3-SCR of NO lanthanum manganite perovskites: effect of A-/B-site substitution and TiO2/CeO2 support, Appl. Catal., B, 2014, 146, 94–104 CrossRef CAS.
- G. Y. Zhou, B. C. Zhong, W. H. Wang, X. J. Guan, B. C. Huang, D. Q. Ye and H. J. Wu, In situ DRIFTS study of NO reduction by NH3 over Fe-Ce-Mn/ZSM-5 catalysts, Catal. Today, 2011, 175, 157–163 CrossRef CAS.
- X. J. Yao, K. L. Ma, W. X. Zou, S. G. He, J. B. An, F. M. Yang and L. Dong, Influence of preparation methods on the physicochemical properties and catalytic performance of MnOx-CeO2 catalysts for NH3-SCR at low temperature, Chin. J. Catal., 2017, 38(1), 146–159 CrossRef CAS.
- M. Xue. Research on low-temperature SCR denitration performance and molding preparation of MnOx-CeO2 composite catalyst, Northwest University, 2019 Search PubMed.
- N. L. Qiao, Y. X. Yang, Q. L. Liu, H. Q. Song, G. Z. Yu and M. S. Luo, The effect of the physical and chemical properties of the support on the denitration performance of manganese-cerium catalyst NH3-SCR, J. Fuel Chem. Technol., 2018, 46(06), 733–742 CAS.
- E. Tronconi, I. Nova and C. Ciardelli, Redox features in the catalytic mechanism of the “standard” and “fast” NH3-SCR of NOx over a V-based catalyst investigated by dynamic methods, J. Catal., 2007, 245(1), 1–10 CrossRef CAS.
- Y. Xiong, C. J. Tang, X. J. Yao, L. Zhang, L. L. Li, X. B. Wang, Y. Deng, F. Gao and L. Dong, Effect of metal ions doping (M=Ti4+, Sn4+) on the catalytic performance of MnOx/CeO2 catalyst for low temperature selective catalytic reduction of NO with NH3, Appl. Catal., A, 2015, 495, 206–216 CrossRef CAS.
- X. F. Tang, Y. G. Li, X. M. Huang, Y. D. Xu, H. Q. Zhu, J. G. Wang and W. J. Shen, MnOx-CeO2 mixed oxide catalysts for complete oxidation of formaldehyde: Effect of preparation method and calcination temperature, Appl. Catal., B, 2006, 62(3–4), 265–273 CrossRef CAS.
- Z. Wang, G. L. Shen, J. Q. Li, H. D. Liu, Q. Wang and Y. F. Chen, Catalytic removal of benzene over CeO2-MnOx composite oxides prepared by hydrothermal method, Appl. Catal., B, 2013, 138–139, 253–259 CrossRef CAS.
- B. Q. Jiang, Preparation of Mn/TiO series low-temperature SCR denitrification catalyst and its reaction mechanism, Zhejiang University, 2008 Search PubMed.
- D. Fang, J. Xie, H. Hu, H. Yang, F. He and Z. Fu, Identification of MnO x species and Mn valence states in MnOx/TiO2 catalysts for low temperature SCR, Chem. Eng. J, 2015, 271, 23–30 CrossRef CAS.
- X. B. Huang, P. Wang, J. C. Tao and Z. S. Xi, CeO2 modified Mn-Fe-O composite and its NH3-SCR denitration catalytic performance, J. Inorg. Mater., 2020, 35(05), 573–580 CrossRef.
- S. S. R. Putluru, L. Schill, A. D. Jensen, B. Siret, F. Tabaries and R. Fehrmann, Mn/TiO2 and Mn-Fe/TiO2 catalysts synthesized by deposition precipitation—promising for selective catalytic reduction of NO with NH3 at low temperatures, Appl. Catal., B, 2015, 165, 628–635 CrossRef CAS.
- C. J. Tang, L. Dong and H. L. Zhang, Ceria-based catalysts for low-temperature selective catalytic reduction of NO with NH3, Catalysis science & technology, 2016 Search PubMed.
- F. D. Liu, H. He, Y. Ding and C. B. Zhang, Effect of manganese substitution on the structure and activity of iron titanate catalyst for the selective catalytic reduction of NO with NH3, Appl. Catal., B, 2009, 93(1), 194–204 CrossRef CAS.
- Z. H. Lian, F. Liu, H. He, X. Shi, J. Mo and Z. Wu, Manganese–niobium mixed oxide catalyst for the selective catalytic reduction of NOx with NH3 at low temperatures, Chem. Eng. J., 2014, 250(1), 390–398 CrossRef CAS.
- J. H. Zhu, Study on the removal of impurities from rare earth concentrates and its NH3-SCR denitration performance, Inner Mongolia University of science and technology, 2019 Search PubMed.
- G. Ramis and M. A. Larrubia, An FT-IR study of the adsorption and oxidation of N-containing compounds over Fe2O3/AhO3 SCR catalysts, J. Mol. Catal. A: Chem., 2004, 215(1–2), 161–167 CrossRef CAS.
- D. K. Sun, Q. Y. Liu, Z. Y. Liu, G. Q. Gui and Z. G. Huang, Adsorption and oxidation of NH3 over V2O5/AC surface, Appl. Catal., B, 2009, 92(3–4), 462–467 CrossRef CAS.
- L. Zhu, Z. P. Zhong, H. Yang, C. H. Wang and L. X. Wang, DeNOx performance and characteristic study for transition metals doped iron based catalysts, Korean J. Chem. Eng., 2017, 34(4), 1229–1237 CrossRef CAS.
- E. Borfecchia, K. A. Lomachenko, F. Giordanino, H. Falsig, P. Beato, A. V. Soldatov, S. Bordiga and C. Lamberti, Revisiting the nature of Cu sites in the activated Cu-SSZ-13 catalyst for SCR reaction, Chem. Sci., 2015, 6(1), 548–563 RSC.
- Y. J. Liao, Y. P. Zhang, Y. X. Yu, J. Li, W. Q. Guo and X. L. Wang, In situ infrared study on the mechanism of MnOx/WO3/TiO2 low temperature selective catalytic reduction of NOx, CIESC J., 2016, 67(12), 5033–5037 Search PubMed.
- M. Bendrich, A. Scheuer, R. E. Hayes and M. Votsmeier, Unified mechanistic model for standard SCR, fast SCR, and NO2 SCR over a copper chabazite catalyst, Appl. Catal., B, 2018, 222, 76–87 CrossRef CAS.
- X. J. Yao, R. D. Zhao, L. Chen, J. Du, C. Y. Tao, F. M. Yang and L. Dong, Selective catalytic re-duction of NOx by NH3 over CeO2 supported on TiO2: Comparison of anatase, brookite, and rutile, Appl. Catal., B, 2017, 208, 82–93 CrossRef CAS.
- L. L. Li, W. Tan, X. Q. Wei, Z. X. Fan, A. N. Liu, K. Guo, K. L. Ma, S. H. Yu, C. Y. Ge, C. J. Tang and L. Dong, Mo doping as an effective strategy to boost low temperature NH3-SCR performance of CeO2/TiO2 catalysts, Catal. Commun., 2018, 114, 10–14 CrossRef CAS.
- Z. Liu, Y. Yi, J. Li, S. I. Woo, B. Wang, X. Cao and Z. Li, A superior catalyst with dual redox cycles for the selective reduction of NOx by ammonia, Chem. Commun., 2013, 49, 7726–7728 RSC.
- K. Liu, F. Liu, L. Xie, W. Shan and H. He, DRIFTS study of a Ce-W mixed oxide catalyst for the selective catalytic reduction of NOx with NH3, Catal. Sci. Technol., 2015, 5, 2290 RSC.
- N. Z. Yang, R. T. Guo, Q. S. Wang, W. G. Pan, Q. L. Chen, C. Z. Lu and S. X. Wang, Deactivation of Mn/TiO2 catalyst for NH3-SCR reaction: effect of phosphorous, RSC Adv., 2016, 6(14), 11226–11232 RSC.
Footnote |
† Electronic supplementary information (ESI) available. See DOI: 10.1039/d1ra05435j |
|
This journal is © The Royal Society of Chemistry 2021 |
Click here to see how this site uses Cookies. View our privacy policy here.