DOI:
10.1039/D1RA03415D
(Paper)
RSC Adv., 2021,
11, 20164-20172
Halogen-free ionic liquids as high performance extractants for phenols separation†
Received
30th April 2021
, Accepted 21st May 2021
First published on 4th June 2021
Abstract
As precious chemical raw materials, phenols can be applied to produce pharmaceuticals, new materials, engineering products, and so on. The separation of phenols from oil mixtures shows great economic value. In this work, five halogen-free ionic liquids (HFILs) were designed and employed to separate phenols from simulated oils, and all of them showed excellent separation performance. Among the HFILs, 1-ethyl-3-methylimidazolium acetate ([Emim][Ac]) showed the highest separation efficiency of 98.6% for phenol, and achieved a minimum ultimate content of 1.96 g dm−3. The calculated distribution coefficient of phenol reached a high value of 431.8. The separation process could be finished within 3 min, and could be performed at normal temperature. It was also found that the HFILs could separate different types of phenols effectively. During separation, toluene was entrained in the HFIL, and an n-hexane treatment was used. After treatment, the toluene entrained in the HFIL after separation was largely removed, and the purity of the phenol was greatly improved. In addition, the HFILs could be easily regenerated by diethyl ether and reused 6 times without a decrease in separation efficiency. Meanwhile, the separation mechanism was explored by using FT-IR spectroscopy, and the FT-IR results indicated the existence of hydrogen bonds.
1. Introduction
Phenols are precious chemical raw materials, and are necessary raw materials for the production of pharmaceuticals, new materials, and engineering products.1,2 There is a growing need for phenols. For example, the demand for phenol is increasing with an average annual growth rate of more than 30% in China.3 Phenols are the main ingredients of the medium and low temperature pyrolysis oil of coal4,5 and the pyrolysis oil of biomass.6,7 It is of great economic value to separate phenols from these oil mixtures.
At present, NaOH elution is the only large-scale industrial separation method to separate phenols from oil mixtures, and the separation mechanism is shown in eqn (1) and (2). Based on the weak acidity of phenols, the addition of NaOH solution can separate phenols by the acid–base interaction between NaOH and phenols. Taking phenol as an example, the chemical reaction is shown in eqn (1). Then, the phenol product can be obtained by adding excess H2SO4 solution into sodium phenolate solution, as shown in eqn (2).
|
C6H5OH + NaOH → C6H5ONa + H2O
| (1) |
|
2C6H5ONa + H2SO4 → 2C6H5OH + Na2SO4
| (2) |
However, in the process of acid washing, a large amount of H
2SO
4 solution is used and cannot be regenerated. This greatly increases the cost of separation, and probably causes serious corrosion of metal containers. Meanwhile, a large amount of waste water containing phenols is produced and is hard to treat. Therefore, there is an urgent need for a novel environmentally friendly separation method.
Ionic liquids (ILs) have attracted much attention due to their extremely low vapor pressure, excellent solubility, and flexible design. ILs have been universally used in the separation of N-containing compounds,8–10 or S-containing compounds11–13 from mixtures. Recently, the separation of phenols from oils using ILs and IL analogues as separation media has emerged. Hou et al.14,15 designed six N-methylimidazole-based ionic liquids, and employed them to extract phenols from oil. The separation efficiency (SE) of phenol was as high as 99%. Xiong et al.16 designed an imidazolium-based poly IL, and employed it to adsorb phenols. Wu et al. designed and synthesized six imidazolium-based17 and trimethylamine-based18 dicationic ILs, and employed them to extract phenols. Both the poly IL and the dicationic ILs could separate over 90% phenols from oils. Also, Cesari et al.19 employed ILs to separate phenols from bio-oils in a two-step process. The extraction rate could be improved by increasing the stage number, and the extraction rate could reach over 80%.
As IL analogues, deep eutectic solvents (DESs) have been applied to separate phenols by many research groups. Wu et al.20,21 found for the first time that a series of inorganic salts could form DESs with phenols, and employed them to extract phenols. Among the salts, tetraethylammonium chloride showed a SE of over 99% for phenol, but the regeneration process was very difficult. Based on this result, Zhang et al.22 employed choline derivatives to separate 26 kinds of phenols with the highest SE of 94.7%. Jiao et al.23 employed an amide and its homologues to separate phenols by forming DESs with phenols, and obtained optimized experimental conditions. Also, this group employed imidazole and imidazole-based compounds to separate phenols by forming DESs,5 and the SE of phenols was higher than 90%.
The above methods show much superiority to the NaOH elution method, and effectively overcome its shortcomings. Unfortunately, as we can see, most of the separation agents contain the halogen anions Cl− or Br−. This may cause serious corrosion of machinery and containers.24,25 For example, Cl− can cause serious stress corrosion and pitting. Also, the corrosion caused by Br− is even more serious. Therefore, separation agents without halogen anions are expected to be designed. Despite this disadvantage, trials of separation via forming hydrogen bonds between separation agents and phenols have shown that this direction has much potential. Given the advantages of ILs, the problem of corrosion may be perfectly solved if we design halogen-free ILs (HFILs) that can separate phenols.
HFILs are ILs without halogen ions, and are well perceived by scientists.26,27 HFILs have been employed in many fields, especially in the absorption of NO,28 CO2,29,30 SO2,31 or H2S32 and the separation of organic compounds.10,33 HFILs tend to show better performances than normal ILs in the field of separation. In the structure of phenols, as we know, the O atom in the hydroxyl group shows strong electronegativity. The H atom connected to the O atom in the hydroxyl group is active, which may be the key to designing new separation agents. It is expected that it will be possible to design HFILs that can interact with this hydrogen. The aim of designing new separation agents is to find HFILs that can interact with this active H atom. For HFILs, an appropriate alkaline anion is important. Aside from halogens, the commonly used alkaline anions are the L-lactate anion, the trifluoromethanesulfonate anion, the dimethyl phosphate anion, the acetate anion, and the ethyl sulfate anion. In this way, the designed HFILs may interact with the active H atom in phenols. Thus, the problem of corrosion may be perfectly solved.
In this work, 1-ethyl-3-methylimidazolium L-lactate ([Emim][LLac]), 1-ethyl-3-methylimidazolium acetate ([Emim][Ac]), 1-butyl-3-methylimidazolium dimethyl phosphate ([Bmim][DMP]), 1-ethyl-3-methylimidazolium ethyl sulfate ([Emim][ES]), and 1-ethyl-3-methylimidazolium trifluoromethanesulfonate ([Emim][TFMS]) were designed and employed to separate phenols from simulated oil. The structures of the HFILs are shown in Scheme 1. Among the HFILs, [Emim][Ac] showed the highest separation efficiency of 98.6% for phenol. During separation, toluene was entrained in the HFIL, and an n-hexane treatment was used. After treatment, the toluene entrained in the HFIL after separation was largely removed, and the purity of the phenol was greatly improved. Meanwhile, the separation mechanism was explored by using FT-IR spectroscopy.
 |
| Scheme 1 The structures of the HFILs used in this experiment. | |
2. Experimental section
2.1. Chemicals
The separation agents employed in this work include [Emim][LLac], [Emim][Ac], [Bmim][DMP], [Emim][ES], and [Emim][TFMS]; their specifications are provided by the suppliers and indicated in Table S1 in the ESI file.† To prepare phenols-containing simulated oils, phenol, o-cresol, m-cresol, and 1,3-dihydroxybenzene were employed as the representative phenols, and toluene or n-hexane was employed as the oil. In addition, diethyl ether (DEE) was employed as the anti-extractant to regenerate the HFILs. Their specifications are also indicated in Table S1.† The above reagents were directly used as received without any further treatment or purification.
2.2. Preparation of simulated oils
Due to the complex composition of coal pyrolysis oil, an accurate analysis of the composition is difficult. Therefore, in this experiment, simulated oil was used to explore the separation conditions. Some common phenols were selected as the representative phenolic compounds, and toluene or n-hexane was selected as the representative oil. The preparation process of the simulated oils was carried out in a fume hood. For example, in the preparation process of the phenol + toluene mixture, 51.6075 g of phenol was added to a 1000 mL beaker containing a known amount of toluene. The phenol + toluene mixture was stirred thoroughly, and transferred to a 500 mL volumetric flask. Then, the solution was diluted with toluene to the volume of the flask, well mixed, and stored for later use. In this way, a phenol + toluene oil mixture containing 103.215 g dm−3 phenol was prepared. Oils with different specifications were prepared in the same way.
2.3. Separation process
The separation process was carried out in a fume hood to avoid harm caused by solvent volatilization. For the different oils, the separation processes were the same. The separation process was performed in a graduated tube. Firstly, a known amount (20 cm3) of oil mixture was added to the graduated tube. Then, an amount of HFIL with a known HFIL
:
phenols mole ratio was added to the graduated tube. The mixture in the graduated tube was well stirred (500 rpm, Shanghai Mei Yingpu Instrument and Meter Manufacturing Co., Ltd., Shanghai, China) and mixed at 298.2 K (±0.1 K) for a known period of time. After that, the mixture was left to stand for 15 min, and a clear boundary between the oil phase and the HFIL phase appeared. Finally, a separating funnel was employed to separate the oil phase from the HFIL phase, and the volumes were recorded as VU (oil phase) and VL (HFIL phase). Samples from the oil phase or the HFIL phase were taken for analysis.
2.4. Analytical methods
For the oil phase samples, a GC-2014 gas chromatograph (GC, Shimadzu, RTX-5 capillary column, flame ionization detector) was employed to analyze the component contents. An analytical program was employed as described in a previous report.18 The phenol and toluene contents were recorded as Cphe and Ctol, respectively. The separation efficiency of phenols was obtained using eqn (3). The distribution coefficients of the components were calculated by eqn (4). |
 | (3) |
|
 | (4) |
where VU and VL are the volumes of the oil phase and the HFIL phase, respectively, in dm3; V0 is the volume of the initial oil, and is 0.020 dm3; C0 is the initial phenol content in g dm−3; Cphe refers to the phenol content after reaching a separation equilibrium in g dm−3; and CU and CL in g dm−3 refer to the component contents in the oil phase and the HFIL phase, respectively, after reaching a phase equilibrium.
2.5. Regeneration of the HFILs
The HFIL phase (containing phenol and HFIL) obtained in the previous subsection was treated by adding an appropriate amount of DEE, and the regenerated HFIL was obtained. In this work, the regeneration process was also carried out in a fume hood. To regenerate the separation agents, DEE was added to a 500 mL beaker containing the HFIL phase. Then, the mixture was stirred for 40 min at a constant temperature by a magnetic stirrer (Shanghai Mei Yingpu Instrument and Meter Manufacturing Co., Ltd., Shanghai, China). After that, the mixture was left to stand for 15 min. The upper phase was DEE containing phenols, and was treated with a distillation process to obtain DEE and the phenol products. The obtained DEE was used in the next cycle. The lower phase was the regenerated HFIL, which was then stored in a vacuum oven to avoid moisture absorption. The regenerated HFILs were directly used in the next separation process.
2.6. Characterization
A Fourier transform infrared spectrometer (FT-IR) was employed to record the spectra of the phenols, the HFILs, and their mixtures for mechanism analysis. The spectrometer was a Bruker TENSOR II FT-IR spectrometer with a DTGS KBr detector, and the scanning region ranged from 4000 to 400 cm−1. In addition, a 400 MHz nuclear magnetic resonance spectrometer (Avance III, Bruker, Germany) with a Bruker 5 mm BBO probe was employed, in order to determine the 1H NMR spectra of the samples. Each of the samples was about 20 mg and dissolved in D2O. The sampling frequency was 16.
3. Results and discussion
3.1. Selection of HFILs
It was found that HFILs had the ability to effectively separate phenols from simulated oils. In this subsection, five HFILs (including [Emim][LLac], [Emim][TFMS], [Bmim][DMP], [Emim][Ac], and [Emim][ES]) were employed to separate phenol from oil. A HFIL
:
phenol mole ratio of about 1.5 was employed in this experiment. The phenol content in the oil was 103.215 g dm−3. The experiment was carried out at 298.2 K. The stirring time was 30 min. The separation process was conducted under the same conditions. The results are shown in Fig. 1.
 |
| Fig. 1 Influence of HFIL type on the separation process. Conditions: initial phenol content, 103.215 g dm−3; HFIL : phenol mole ratio, about 1.5; temperature, 298.2 K; stirring time, 30 min. | |
As can be seen from Fig. 1, the studied HFILs exhibit excellent separation performance for phenol. Under the studied conditions, the SEs of phenol are 98.2%, 93.7%, 98.0%, 98.6%, and 98.5% for [Emim][LLac], [Emim][TFMS], [Bmim][DMP], [Emim][Ac], and [Emim][ES], respectively. Fig. 2 shows the distribution coefficients of phenol and toluene for the different HFILs. As shown in Fig. 2, D of phenol are 328.2, 90.0, 230.6, 431.8, and 390.7 for [Emim][LLac], [Emim][TFMS], [Bmim][DMP], [Emim][Ac], and [Emim][ES], respectively. The distribution coefficients of phenol are three orders of magnitude higher than those of toluene. In conclusion, these HFILs can effectively separate phenol from simulated oil. Through comprehensive evaluation, [Emim][LLac] and [Emim][Ac] exhibited relatively high SE and D for phenol, and were selected as the optimum HFILs. They were employed to investigate the influence of different separation conditions on the separation process.
 |
| Fig. 2 The distribution coefficients of phenol and toluene for different HFILs. Conditions: initial phenol content, 103.215 g dm−3; HFIL : phenol mole ratio, about 1.5; temperature, 298.2 K; stirring time, 30 min. | |
3.2. Influence of stirring time on the separation process
The influence of stirring time on the separation process was thoroughly studied, and the stirring time was varied from 1 to 20 min (1, 2, 3, 5, 10, and 20 min). A HFIL
:
phenol mole ratio of about 1.5 and a simulated oil with the initial phenol content of 103.215 g dm−3 were employed. The experiment was performed at 298.2 K. The results are shown in Fig. 3.
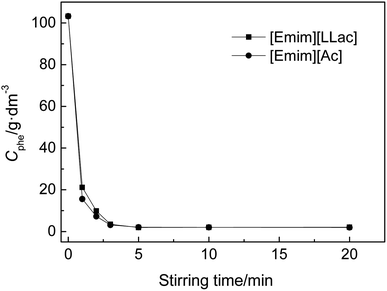 |
| Fig. 3 The influence of stirring time on the separation process. Conditions: initial phenol content, 103.215 g dm−3; HFIL : phenol mole ratio, about 1.5; temperature, 298.2 K; separation agents, [Emim][LLac] and [Emim][Ac]. | |
As shown in Fig. 3, the phenol content sharply decreases with an increase in stirring time from 0 to 3 min. As the stirring time further increases from 3 to 20 min, the phenol content stays nearly constant. When the separation system reached separation equilibrium, the phenol content in the oil reached the minimum ultimate content for phenol (MUCP). As can be seen in Fig. 3, the MUCPs are 2.06 g dm−3 for [Emim][LLac] and 1.96 g dm−3 for [Emim][Ac]. These results indicate that the separation of phenol from oil needs a period of time to reach separation equilibrium. In the following experiments, a stirring time of 20 min was selected as a suitable time for phenol separation.
3.3. Influence of temperature on the separation process
The influence of separation temperature on the separation process was thoroughly investigated. The temperature was varied from 273.2 to 333.2 K (273.2, 298.2, 303.2, 313.2, 323.2, and 333.2 K). A HFIL
:
phenol mole ratio of about 1.5 and a simulated oil with the initial phenol content of 103.215 g dm−3 were employed. The separation agents [Emim][LLac] and [Emim][Ac] were employed. The results are shown in Fig. 4.
 |
| Fig. 4 The influence of temperature on the separation process. Conditions: initial phenol content, 103.215 g dm−3; HFIL : phenol mole ratio, about 1.5; stirring time, 20 min; separation agents, [Emim][LLac] and [Emim][Ac]. | |
As shown in Fig. 4, the SE of phenol exhibits a tiny decrease as the temperature increases from 273.2 K to 333.2 K. For [Emim][LLac] as separation agent, the SE of phenol decreases from 98.0% to 96.5%. For [Emim][Ac] as separation agent, the SE of phenol decreases from 98.2% to 96.6%. Generally, the separation temperature has a very slight influence on the SE. This slight influence may be due to the decrease in interaction between phenol and HFIL as the temperature increases. Thus, extra heat exchange in the oil mixture is unnecessary, and room temperature is a good choice. Thus, the temperature in the following experiments was set to 25 °C.
3.4. Influence of HFIL
:
phenol mole ratio on the separation process
The HFIL
:
phenol mole ratio has a very important influence on phenol separation, since the amount of HFIL added to the oil directly influences the SE of phenol. An appropriate HFIL amount can ensure high SE of phenol, and improve the utilization rate of HFIL. In this subsection, the HFIL
:
phenol mole ratio was varied from 0 to about 1.5. A simulated oil with the initial phenol content of 103.215 g dm−3 and a temperature of 25 °C were employed. The separation agents [Emim][LLac] and [Emim][Ac] were employed. The results are shown in Fig. 5.
 |
| Fig. 5 The influence of HFIL : phenol mole ratio on the separation process. Conditions: initial phenol content, 103.215 g dm−3; temperature, 298.2 K; stirring time, 20 min; separation agents, [Emim][LLac] and [Emim][Ac]. | |
As shown in Fig. 5, both [Emim][LLac] and [Emim][Ac] exhibit excellent separation ability for phenol. For these two HFILs, as the HFIL
:
phenol mole ratio increases from 0 to about 0.6, the SE of phenol increases rapidly from 0 to over 95%. The main reason is that the HFIL can interact with phenol more and more as we continuously add HFIL to the oil. The phenol content in the oil decreases at the same time. As the HFIL
:
phenol mole ratio further increases from 0.6 to 1.5, the SE of phenol shows a slow increase from 95.3% to 98.2% for [Emim][LLac], and from 96.5% to 98.6% for [Emim][Ac]. As shown in eqn (3), high SE indicates low phenol content in the oil. Therefore, it is difficult to obviously improve the SE because of the low phenol content in the oil. The MUCPs are 2.0 g dm−3 and 1.6 g dm−3 for [Emim][LLac] and [Emim][Ac], respectively. The slow increase in SE may be because a new phase equilibrium is reached between the HFIL and the oil mixture with the continuous addition of HFIL. The amounts of phenol separated by the HFILs during separation are listed in Table S2 in the ESI file.†
3.5. Influence of initial phenol content on the separation process
Since different kinds of oil mixtures may have various contents, it is necessary to investigate the influence of the initial phenol content on the separation process. It is expected that the HFILs can be employed to separate phenol from oil even if the initial phenol content is different. In this subsection, oils with various phenol contents (50.126 g dm−3, 103.215 g dm−3, and 200.012 g dm−3) were employed, and [Emim][Ac] was selected as the separation agent. The results are shown in Fig. 6.
 |
| Fig. 6 The influence of initial phenol content on the separation process. Conditions: temperature, 298.2 K; stirring time, 20 min; separation agent, [Emim][Ac]; initial phenol contents, 50.126, 103.215, and 200.012 g dm−3. | |
As can be seen in Fig. 6, as the [Emim][Ac]
:
phenol mole ratio increases from 0 to about 0.6, the phenol content sharply decreases. As the [Emim][Ac]
:
phenol mole ratio further increases from 0.6 to about 1.2, the phenol content shows a slight decrease. Interestingly, even if the initial phenol content is different, the MUCPs are almost the same (about 1.8 g dm−3). Similar results have been reported in previous studies.20,21 Therefore, the initial phenol content in the oil mixture has little influence on the separation process, and HFILs can be employed to separate phenol from oils with various phenol contents.
3.6. Influence of phenol type on the separation process
The composition of real coal pyrolysis oil is extremely complex. There are 75 kinds of phenols found in the medium and low temperature coal pyrolysis oil of Northern Shaanxi (China).34 Therefore, the separation of other phenols is particularly important. In this subsection, a simulated oil mixture containing 25.0 g dm−3 phenol, 25.0 g dm−3 o-cresol, 25.0 g dm−3 m-cresol, and 25.0 g dm−3 1,3-dihydroxybenzene (shown as DHB) was used, and toluene was employed as the oil. [Emim][Ac] was employed as the separation agent, and an [Emim][Ac]
:
phenols mole ratio of 1.50 was used. The influence of phenol type on the separation process is shown in Fig. 7.
 |
| Fig. 7 The influence of phenol type on the separation process. Conditions: initial phenol content, 103.215 g dm−3; HFIL : phenol mole ratio, about 1.50; temperature, 298.2 K; stirring time, 20 min; separation agent, [Emim][Ac]. | |
As shown in Fig. 7, [Emim][Ac] shows high separation ability for the studied phenols. For the different types of phenols, the SEs of the phenols are around or over 90% when using [Emim][Ac] as the separation agent. After separation, the phenol contents remaining in the simulated oil are 1.3, 1.7, 2.2, and 3.0 g dm−3 for phenol, o-cresol, m-cresol, and 1,3-dihydroxybenzene, respectively. According to calculations, the total SE of the phenols can reach as high as 93.1%. Hence, the HFILs have great potential for the separation of phenols from real oil mixtures.
3.7. Separation of phenol from n-hexane
Besides aromatic hydrocarbons, there are also aliphatic hydrocarbons in coal pyrolysis oil. Hence, the separation of phenols from aliphatic hydrocarbons is also of much importance. In this subsection, phenol and n-hexane were selected to prepare the simulated oil, and the phenol content was 10.0 g dm−3. [Emim][Ac] was employed as the separation agent. The SE of phenol as a function of the [Emim][Ac]
:
phenol mole ratio is shown in Fig. 8.
 |
| Fig. 8 SE of phenol as a function of [Emim][Ac] : phenol mole ratio. Conditions: initial phenol content, 10 g dm−3; oil, n-hexane; temperature, 298.2 K; stirring time, 20 min; separation agent, [Emim][Ac]. | |
As shown in Fig. 8, the SE of phenol sharply increases as the [Emim][Ac]
:
phenol mole ratio increases from 0 to about 0.5. Under the studied conditions, the maximum SE of phenol can reach as high as 93.1%. The MUCP is low at 0.7 g dm−3. In this experiment, although the initial phenol content in the oil was low, at 10.0 g dm−3, [Emim][Ac] still exhibited excellent separation performance.
3.8. Entrainment of toluene and removal method
The purity of a product determines its value. In this work, we should not only pursue high SE of phenol, but also try to improve the purity of the phenol product. It can be seen from Fig. 2 that toluene is present, even though D has a small value, which indicates that toluene is entrained in the HFILs. In order to clarify this, we define the parameter E = mtoluene/(mtoluene + mphenol), where mtoluene and mphenol are the masses of toluene and phenol in the HFIL after separation, respectively. Hence, by analyzing E for the ionic liquid, we can infer the purity of the separated phenol products. For [Emim][Ac] as separation agent, a plot of E as a function of [Emim][Ac]
:
phenol mole ratio is shown in Fig. 9.
 |
| Fig. 9 E as a function of [Emim][Ac] : phenol mole ratio. Conditions: initial phenol content, 103.215 g dm−3; separation agent, [Emim][Ac]; temperature, 298.2 K; stirring time, 20 min. | |
As shown in Fig. 9, E decreases with an increase in [Emim][Ac]
:
phenol mole ratio. Under the studied conditions, the minimum E is 0.21, which indicates that much toluene is entrained in the HFIL during separation.
To remove the toluene and improve the purity of the phenol, we added n-hexane to [Emim][Ac] after separation. According to previous literature,35 an n-hexane
:
[Emim][Ac] volume ratio of 5.0 was used. After being well stirred and mixed, the mixture was left to stand for 15 min, and a clear boundary between the [Emim][Ac] phase and the n-hexane phase was observed. A sample of the n-hexane phase was analyzed by GC, and the results are shown in Fig. S1 in the ESI file.† A standard sample of toluene was also analyzed by GC. The peak at 2.47 min has exactly the same retention time as the peak for the standard sample of toluene. This result indirectly proved that some toluene was entrained in the HFIL after separation. Also, a sample was taken from the [Emim][Ac] phase. Through GC analysis, it is found that E significantly decreases to 0.042, which indicates that the entrained toluene is mostly removed. In this way, the purity of the separated phenols can be improved a lot.
3.9. Regeneration and recycling of HFILs
The regeneration and recycling of HFILs is of great significance to reduce the separation cost, save resources and protect the environment. In this work, DEE can be used to effectively regenerate HFILs based on the solubility difference between HFILs and phenol in DEE. A toluene + phenol simulated oil mixture containing 103.215 g dm−3 phenol was used. [Emim][LLac] and [Emim][Ac] were employed as the separation agents, and a HFIL
:
phenol mole ratio of 1.50 was used. The SE of phenol was calculated through eqn (3) to evaluate the separation ability of the regenerated HFILs. The influence of cycle number on the separation process is shown in Fig. 10.
 |
| Fig. 10 The influence of cycle number on the separation process. Conditions: initial phenol content, 103.215 g dm−3; temperature, 298.2 K; stirring time, 20 min; separation agents, [Emim][LLac] and [Emim][Ac]. | |
As can be seen in Fig. 10, the regenerated HFILs still present very high SE for phenol. After six cycles, the SE of phenol remains almost the same as that of phenol separated for the first time. To further illustrate the reusability of the HFILs, the 1H NMR spectra of the regenerated HFILs were recorded. The 1H NMR spectra of the original and regenerated HFILs are shown in Fig. 11. As shown in Fig. 11, the 1H NMR spectra of the original and regenerated HFILs are identical (the peaks at δ = 4.7 ppm are the H peaks of H2O in D2O), which indicates that the structure of the regenerated HFIL is the same as that of the original HFIL. The above description indicates that the studied HFILs can be regenerated without changing in structure, and can be reused without an obvious decrease in the SE of phenol.
 |
| Fig. 11 1H NMR spectra of the fresh and regenerated HFILs. Conditions: initial phenol content, 103.215 g dm−3; separation agents, [Emim][LLac] and [Emim][Ac]; solvent, D2O; mass, about 20 mg; sampling frequency, 16. | |
3.10. Mechanism of phenol separation
In this work, phenols can be effectively separated from simulated oils with high SE of phenol because the interactions between HFILs and phenols are much stronger than those between toluene or n-hexane and phenols. It is speculated that the interactions between HFILs and phenols may be hydrogen bonds. FT-IR spectroscopy is an effective method to study hydrogen bonds.36 Hence, the interactions between HFILs and phenol were analyzed and studied by FT-IR spectroscopy. Fig. 12 shows the FT-IR spectra of phenol, HFILs, and their mixtures. The band information is listed in Table S4 in the ESI file.†
 |
| Fig. 12 FT-IR spectra of (a) phenol, [Emim][LLac], and their mixture; (b) phenol, [Emim][Ac], and their mixture. Conditions: HFIL : phenol mole ratio, about 0.5. | |
As shown in Fig. 12, the absorption peak for the ν-OH stretching vibration (–OH in phenol) appears at 3322 cm−1. With [Emim][LLac] as separation agent, as shown in Fig. 12(a), that ν-OH stretching vibration is observed at about 3200 cm−1 for the [Emim][LLac] + phenol mixture (the peak for the ν-OH stretching vibration moves to lower wavenumber). This is because of the formation of hydrogen bonds between [Emim][LLac] and phenol, which decreases the density of the bonding electron cloud. Similarly, for [Emim][Ac] as separation agent, as shown in Fig. 12(b), the peak for the ν-OH stretching vibration shifts to a lower wavenumber of 3111 cm−1. The above results indicate the existence of hydrogen bonds between the HFIL and phenol after separation.
3.11. Comparison between this method and other methods
Compared to the halogen ion-containing separation agents (quaternary ammonium salts,21,37 dicationic ionic liquids,17,18 imidazolium-based ionic liquids15) proposed in previous literature, the HFILs contain no halogen ion, and cause no serious corrosion to metallic containers or equipment. When compared to the amide compounds proposed by Jiao et al.,23 and the inner salts proposed by Yao et al.,24 the present HFILs show much higher SE of phenol, and higher D of phenol. Compared to amino acid ionic liquids,33 the studied HFILs have a much easier operation process. We make a comparison of this method with other methods in terms of C0, SE, and MUCP, as shown in Table S3 in the ESI file.† In addition, in this work, the entrainment of toluene and a method to improve the purity of the phenol product in the separation process were discussed. After treatment, the toluene entrained in the HFIL after separation was largely removed, and the purity of the phenol was greatly improved. This is rarely discussed in other work.
As the HFILs can absorb water easily, the presence of water has a bad effect on phenol separation (as shown in Fig. S2 in the ESI file,† with an increase in the water to [Emim][Ac] mass ratio from 0 to 1.09, the phenol content in the oil after separation increases gradually from 2.0 to 20.7 g dm−3). Also, the HFILs used in this work are slightly more expensive than some other separation agents. As a new kind of separation agent, the market demand for HFILs will greatly increase as the applications of ionic liquids are greatly expanded. Also, we believe the price of HFILs will gradually decrease with progress in production technology.
4. Conclusions
In this work, five HFILs were designed and employed to separate phenols from simulated oil, and all of them showed excellent separation performance. Of the five HFILs, [Emim][Ac] showed the highest SE of 98.6% and the highest D of 431.8 for phenol. A MUCP of 1.96 g dm−3 was obtained. The separation could be finished within 3 min, and could be performed at normal temperature. During separation, toluene was entrained in the HFIL, and an n-hexane treatment was used. After treatment, the toluene entrained in the HFIL after separation was largely removed, and the purity of the phenol was greatly improved. In addition, the HFILs could be easily regenerated by diethyl ether and reused 6 times without a decrease in SE. Meanwhile, the FT-IR results indicated the existence of hydrogen bonds.
Abbreviations
IL | Ionic liquids |
DES | Deep eutectic solvent |
SE | Separation efficiency |
D | Distribution coefficient |
HFIL | Halogen-free ionic liquid |
[N2222][OH] | Tetraethylammonium hydroxide |
[Emim][LLac] | 1-Ethyl-3-methylimidazolium L-lactate |
[Emim][Ac] | 1-Ethyl-3-methylimidazolium acetate |
[Bmim][DMP] | 1-Butyl-3-methylimidazolium dimethyl phosphate |
[Emim][ES] | 1-Ethyl-3-methylimidazolium ethyl sulfate |
[Emim][TFMS] | 1-Ethyl-3-methylimidazolium trifluoromethanesulfonate |
DEE | Diethyl ether |
GC | Gas chromatography |
C0 | Initial phenol content |
Cphe | Phenol content detected by GC |
VU | The volume of the oil phase |
VL | The volume of the HFIL phase |
CL | The component contents in the HFIL phase |
CU | The component contents in the oil phase |
E | mtoluene/(mtoluene + mphenol), where mtoluene and mphenol are the masses of toluene and phenol in the HFIL after separation |
MUCP | Minimum ultimate content for phenol |
Conflicts of interest
There are no conflicts to declare.
Acknowledgements
We sincerely thank Professors Hua Sun and Huijian Shang for their help. This work is financially supported by the Scientific Research Foundation for the Introduction of Talents of Hebei University of Science and Technology (81/1181381).
References
- T. T. Jiao, M. M. Gong, X. L. Zhuang, C. S. Li and S. J. Zhang, J. Ind. Eng. Chem., 2015, 29, 344–348 CrossRef CAS.
- H. H. Schobert and C. Song, Fuel, 2002, 81, 15–32 CrossRef CAS.
- G. H. Zhang and H. J. Sun, Chem. Ind., 2014, 32, 33–35 Search PubMed.
- K. Erdmann, T. Mohan and J. G. Verkade, Energy Fuels, 1996, 10, 378–385 CrossRef CAS.
- T. T. Jiao, C. S. Li, X. L. Zhuang, S. S. Cao, H. N. Chen and S. J. Zhang, Chem. Eng. J., 2015, 266, 148–155 CrossRef CAS.
- J. H. Li, C. Wang and Z. Y. Yang, J. Anal. Appl. Pyrolysis, 2010, 89, 218–224 CrossRef CAS.
- Z. Shah, R. C. Veses, M. A. Ceschi and R. D. Silva, Mod. Chem. Appl., 2017, 5, 1–8 CrossRef.
- Y. Fan, D. X. Cai, S. Zhang, H. Wang, K. Guo, L. Zhang and L. Yang, Sep. Purif. Technol., 2019, 222, 92–98 CrossRef CAS.
- L. Zhang, X. Bing, Z. Cui, J. A. Labarta and Y. Wang, ACS Sustainable Chem. Eng., 2020, 8, 5662–5673 CrossRef CAS.
- Y. A. Ji, Y. C. Hou, S. H. Ren and W. Z. Wu, Sep. Purif. Technol., 2021, 258, 117997 CrossRef CAS.
- H. S. Butt, K. C. Lethesh and A. Fiksdahl, Sep. Purif. Technol., 2020, 248, 116959 CrossRef CAS.
- X. C. Chen, S. Yuan, A. A. Abdeltawab, S. S. Al-Deyab, J. W. Zhang, L. Yu and G. R. Yu, Sep. Purif. Technol., 2014, 133, 187–193 CrossRef CAS.
- Z. Kai, H. M. Li, S. H. Ren, W. Z. Wu and Y. Y. Bao, J. Chem. Eng. Data, 2017, 62, 2708–2712 CrossRef.
- Y. C. Hou, W. Peng, C. M. Yang, S. Y. Li and W. Z. Wu, J. Chem. Ind. Eng., 2013, 64, 118–123 Search PubMed.
- Y. C. Hou, Y. H. Ren, W. Peng, S. H. Ren and W. Z. Wu, Ind. Eng. Chem. Res., 2013, 52, 18071–18075 CrossRef CAS.
- J. L. Xiong, H. Meng, Y. Z. Lu and C. X. Li, Chem. J. Chin. Univ., 2014, 35, 2031–2036 CAS.
- Y. A. Ji, Y. C. Hou, S. H. Ren, C. F. Yao and W. Z. Wu, Energy Fuels, 2017, 31, 10274–10282 CrossRef CAS.
- Y. A. Ji, Y. C. Hou, S. H. Ren, C. F. Yao and W. Z. Wu, Fuel Process. Technol., 2018, 171, 183–191 CrossRef CAS.
- L. Cesari, L. Canabady-Rochelle and F. Mutelet, Sep. Purif. Technol., 2019, 209, 528–534 CrossRef CAS.
- K. Pang, Y. C. Hou, W. Z. Wu, W. J. Guo, W. Peng and K. N. Marsh, Green Chem., 2012, 14, 2398–2401 RSC.
- W. J. Guo, Y. C. Hou, W. Z. Wu, S. H. Ren, S. D. Tian and K. N. Marsh, Green Chem., 2013, 15, 226–229 RSC.
- Y. Zhang, Z. Y. Li, H. Y. Wang, X. P. Xuan and J. J. Wang, Sep. Purif. Technol., 2016, 163, 310–318 CrossRef CAS.
- T. T. Jiao, X. L. Zhuang, H. Y. He, C. S. Li, H. N. Chen and S. J. Zhang, Ind. Eng. Chem. Res., 2015, 54, 2573–2579 CrossRef CAS.
- C. F. Yao, Y. C. Hou, S. H. Ren, W. Z. Wu, K. Zhang, Y. A. Ji and H. Liu, Chem. Eng. J., 2017, 620–626 CrossRef CAS.
- J. J. Zhu, C. F. Zhu and W. J. Wei, Mater. Prot., 2007, 40, 71–73 CAS.
- L. Qi, W. Jiang, H. Fu, C. Hua and X. Li, Appl. Catal., A, 2007, 328, 83–87 CrossRef.
- R. Gusain, S. Dhingra and O. P. Khatri, Ind. Eng. Chem. Res., 2016, 55, 856–865 CrossRef CAS.
- Y. Sun, S. H. Ren, Y. C. Hou, K. Zhang and W. Z. Wu, Ind. Eng. Chem. Res., 2019, 58, 13313–13320 CrossRef CAS.
- Q. W. Yang, Z. P. Wang, Z. B. Bao, Z. G. Zhang, Y. W. Yang, Q. L. Ren, H. B. Xing and S. Dai, ChemSusChem, 2016, 9, 806–812 CrossRef CAS PubMed.
- H. Yu, Y. T. Wu, Y. Y. Jiang, Z. Zhou and Z. B. Zhang, New J. Chem., 2009, 33, 2385–2390 RSC.
- K. Zhang, S. H. Ren, X. Yang, Y. C. Hou, W. Z. Wu and Y. Y. Bao, Chem. Eng. J., 2017, 327, 128–134 CrossRef CAS.
- B. Wang, K. Zhang, S. H. Ren, Y. C. Hou and W. Z. Wu, RSC Adv., 2016, 6, 101462–101469 RSC.
- Y. A. Ji, Y. C. Hou, S. H. Ren, C. F. Yao and W. Z. Wu, Energy Fuels, 2018, 32, 11046–11054 CrossRef CAS.
- R. C. Wang, M. Sun, Q. X. Liu, Y. X. Ma, G. Feng, L. Xu and X. X. Ma, J. China Coal Soc., 2011, 36, 664–669 CAS.
- Y. A. Ji, Y. C. Hou, S. H. Ren, C. F. Yao and W. Z. Wu, Fuel Process. Technol., 2017, 160, 27–33 CrossRef CAS.
- N. Asprion, H. Hasse and G. Maurer, Fluid Phase Equilib., 2001, 186, 1–25 CrossRef CAS.
- Y. C. Hou, J. Kong, Y. H. Ren, S. H. Ren and W. Z. Wu, Sep. Purif. Technol., 2017, 174, 554–560 CrossRef CAS.
Footnote |
† Electronic supplementary information (ESI) available. See DOI: 10.1039/d1ra03415d |
|
This journal is © The Royal Society of Chemistry 2021 |
Click here to see how this site uses Cookies. View our privacy policy here.