DOI:
10.1039/D1RA02852A
(Paper)
RSC Adv., 2021,
11, 18797-18808
Ultrafast conversion of carcinogenic 4-nitrophenol into 4-aminophenol in the dark catalyzed by surface interaction on BiPO4/g-C3N4 nanostructures in the presence of NaBH4†
Received
12th April 2021
, Accepted 18th May 2021
First published on 25th May 2021
Abstract
The heterogeneous catalytic conversion of pollutants into useful industrial compounds is a two-goals at once process, which is highly recommended from the environmental, economic, and industrial points of view. In this regard, design materials with high conversion ability for a specific application is required to achieve such a goal. Herein, the synthesis conditions for the fabrication of BiPO4 nanorod bundles supported on g-C3N4 nanosheets as heterojunction composites was achieved using a facile ex situ chemical deposition for the reductive conversion of carcinogenic 4-nitrophenol (4-NP) into 4-aminophenol (4-AP). To better understand the mechanistic reduction pathways, BiPO4/g-C3N4 composites with varying ratios where obtained. The morphology and structure of BiPO4/g-C3N4 composites were checked using several methods: XRD, FE-SEM, HRTEM, XPS, and FT-IR, and it was found that hexagonal phase BiPO4 nanorod bundles were randomly distributed on the g-C3N4 nanosheets. Overall, the reduction ability of BiPO4/g-C3N4 composites was far better than bare BiPO4 and g-C3N4. A total reductive conversion of 4-NP at a concentration of 10 mg L−1 into 4-AP was found with 50% BiPO4/g-C3N4 composite within only one minute of reaction. Moreover, the presence of reducing agent (NaBH4) enhanced the kinetic rate constant up to 2.914 min−1 using 50% BiPO4/g-C3N4, which was much faster than bare BiPO4 (0.052 min−1) or g-C3N4 (0.004 min−1). The effects of some operating parameters including the initial concentration of 4-NP and catalyst dosage were also evaluated during the experiments. BiPO4/g-C3N4 showed great stability and recyclability, wherein, the catalytic reduction efficiency remains the same after five runs. A plausible 4-NP reduction mechanism was discussed. The high catalytic activity with the good stability of BiPO4/g-C3N4 make it a potential candidate for the reduction of nitroaromatic compounds in real wastewaters.
1. Introduction
Petrochemical and pesticide manufacturing industries discharge huge amounts of nitroaromatic compounds, e.g., nitrophenols, which are known as potential environmental hazards to human health because of their high degree of carcinogenic risk and non-biodegradability in the aquatic or/and soil environments.1,2 Many efforts have been made to remove nitrophenols from the environment using different physicochemical or photonic techniques.3–7 Of these, the reduction of nitrophenol is a great strategy as it achieves two goals at the same time, including the removal of toxic compound from the medium, plus the production of aminophenol as a valuable compound for industrial use such as in pharmaceutical and drug processing.8 Therefore, the intensification of green technologies for enhanced and selective reduction of nitrophenol into aminophenol has received much attention recently due to the important environmental and economic impact.9,10 In this regard, over the last decades, semiconductor catalysts have attracted wide attention for removing environmental pollutants or/and converting them into useful compounds for industrial use.11,12 Numerous semiconductor materials with appropriate physicochemical or/and photochemical properties have been widely developed and used for the catalytic and photocatalytic transformation of compounds.13,14
g-C3N4 has been considered as one of the most successful π-conjugated polymers over the last decades, due to its high stability, good absorption in the visible light and photoefficiency.15 Owing to the existence of the lamellar structure, g-C3N4 is always well-crystallized, allowing the transfer of charges.16 In view of its unique structure, and photochemical characteristics, g-C3N4 has been widely employed in various fields, for instance, removal of pollutants from water or air,17 reduction of hazardous metals,18 water splitting,19 hydrogen evolution.20 Therefore, g-C3N4 as a metal-free material is identified to be a “sustainable develop” catalyst. Regardless, the photocatalytic effectiveness of g-C3N4 is still limited due to several issues including the fast recombination of electron/hole charges and low adsorption capacity.21,22 To limit the recombination of charges and enhance the catalytic ability of g-C3N4, the surface modification though metal doping23 or non-metal doping processes24 were extensively reported. In terms of 4-nitrophenol reduction, Pd, Ag, Au doped g-C3N4 have been utilized to improve the catalytic activity of 4-nitrophenol reduction.25–28 On top of that, the combination of g-C3N4 with other semiconductors to form heterojunction systems which gives a range of synergistic benefits, wherein, the interfacial charge-transfer (IFCT) is the key advantage as it can enhance significantly the yield of long lifetime of separated redox charge carriers.29,30 For a successful construction of a heterojunction systems, the semiconductors should be properly chosen. In recent decades, the scientific community has addressed widely the application of bismuth based nanomaterials such as BiOBr, Bi2S3, BiPO4, BiVO4, Bi2WO6, Bi2O2CO3 in different catalytic applications thanks to their appropriate physicochemical and photonic characteristics.31–36 In particular, BiPO4 as a new bismuth salt catalyst, which has been developed for the first type by Zhu's group, has been revealed as promising candidate in semiconductor catalysis due to its highly photocatalytic efficiency under UV light which was found to be superior that TiO2 (P25, Degussa) towards the oxidation of dyes.37 However, the catalytic performance of BiPO4 has been greatly restricted. Like other semiconductors, a lot research has been carried out on BiPO4 to improve its (photo)-catalytic efficiency and visible light response. One of the used strategies is the combination of BiPO4 with other semiconductors to get multifunctional heterojunctions with combined options, which could enhance the surface interactions, charges transfer and better visible light response.38–40 Other ways have been also reported including surface hybridization with π-conjugated materials,41–43 creation of surface oxygen vacancies,44,45 and phase junction system.46,47 The combination of g-C3N4 with BiPO4 has been proved to be very successful due to the excellent interfacial interaction between the two nanostructured materials in terms of high yield of separated charged and enhanced (photo)-catalytic reactions.48–50 However, the catalytic reduction application and mechanism of heterojunction BiPO4 with g-C3N4 have not been thoroughly investigated.
In this work, we report the fabrication of BiPO4 nanorod bundles/g-C3N4 nanosheets composite architectures with ultrafast catalytic efficacy towards the reduction of 4-nitrophenol. As far as we know, this is the first investigation on the use of BiPO4/g-C3N4 to initiate the reduction of 4-NP in dark condition. The catalytic efficiencies bare BiPO4 and g-C3N4 were studied as well for the purpose of comparison. Additionally, the effect of different BiPO4:g-C3N4 ratios on the catalytic effectiveness was checked. The effect of some operating parameters such as the initial concentration of 4-NP and catalyst amount on the catalytic performance was studied. The stability of BiPO4/g-C3N4 composite and the feasible mechanistic pathway for the catalytic reduction of 4-NP were addressed.
2. Experimental
All chemicals and characterization instruments were reported in the ESI.†
2.1 Synthesis of BiPO4 nanorod bundles
The details of the synthesis of BiPO4 were reported in our previous study.51 Typically, 1.94 g of Bi(NO3)3·5H2O and 0.5 g CTAB were stirred in 40 mL dimethyl sulfoxide. Then 0.524 g (NH4)2HPO4 dissolved in 40 mL of water was dropped into the previous solution under vigorous stirring for 1 h. After the formation of precipitate, the solid was recovered with centrifugation, and then washed with water and ethanol, and finally it was dried for 6 h at 90 °C.
2.2 Synthesis of g-C3N4 nanosheets
g-C3N4 was synthesized through the direct hearting of mixture of melamine and urea (5
:
5 g) at 600 °C in a muffle furnace for 2 h with 2 °C min−1 heating rate. The obtained yellow solid was ground.
2.3 Synthesis of BiPO4 nanorod bundles/g-C3N4 nanosheets
To develop BiPO4/g-C3N4 heterojunction photocatalyst, the ex situ route was adopted, as shown in Scheme 1, the growth of BiPO4 nanorod bundles within sheets of g-C3N4 was obtained. In details, 0.5 g of g-C3N4 was mixed with 50 mL methanol and stirred for 1 h. Different amounts of BiPO4 was ultrasonically dispersed into g-C3N4 suspension for 10 min and complete stirring for 1 h to denote as 10% BiPO4/g-C3N4, 30% BiPO4/g-C3N4, 50% BiPO4/g-C3N4, and 70% BiPO4/g-C3N4 samples. Finally, the composites were washed with water and dried for 6 h at 90 °C.
 |
| Scheme 1 Diagram representation for the synthesis and structure of BiPO4/g-C3N4 heterojunction. | |
2.4 Catalytic reduction test of 4NP
The catalytic behavior was investigated towards the reductive conversion of 4-nitrophenol into 4-aminophenol in the presence of NaBH4. First, 50 mL of an aqueous solution of 4-nitrophenol (10 ppm) was mixed with NaBH4 (16 mM), which leads to form a strong yellow solution. Then, 25 mg of the catalyst was added in dark to yellow solution and the reaction was performed until the solution became colorless. A 3 mL aliquots were taken at different time intervals, and the solid suspension was removed via centrifugation. The concentration of compounds was followed by the use of UV-vis spectrophotometer. The recycling of BiPO4/g-C3N4 was carried out to check the stability. For this, the catalyst was recovered after the reaction, and the washed with double distilled water and dried at 90 °C for subsequent tests.
3. Results and discussion
3.1 Characterization
Fig. 1 illustrates the XRD patterns of bare BiPO4, g-C3N4, and BiPO4/g-C3N4 hybrid composites. The diffraction peaks of BiPO4 at 2-theta angles 14.7°, 20.1°, 25.5°, 29.5°, 31.3°, 41.9°, and 48.7° which corresponding to the crystal orientations of (100), (101), (110), (200), (102), (211), and (212) planes of BiPO4. These diffraction peaks correspond to JCPDS card no. 15-0766.52 It can be seen from the diffraction peaks that BiPO4 is a hexagonal phase (HBIP, space group: P3121). g-C3N4 pattern shows an intense peak at 2θ = 27.7° corresponding to its crystal plane (002) of stacking conjugated aromatic system, while the peak at 12.9° is due to the tristriazine units.53 The diffraction peaks of g-C3N4 from mixture of urea and melamine is more intense than as prepared by urea as shown in Fig. S1.† No other peaks or impurities are observed, implying that the final products of BiPO4 and g-C3N4 are of pure phases. The diffraction pattern of BiPO4/g-C3N4 shows that the composite is composed of the hexagonal phase BiPO4 and g-C3N4. The intensity of diffraction peaks of BiPO4 are gradually strengthen with increasing BiPO4 content. Consequently, the above results confirm the successful formation BiPO4/g-C3N4 heterojunction.
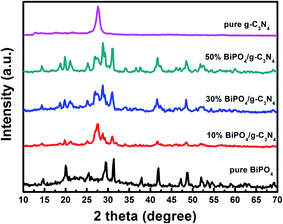 |
| Fig. 1 Powder XRD patterns of pure BiPO4, g-C3N4, 10% BiPO4/g-C3N4, 30% BiPO4/g-C3N4, and 50% BiPO4/g-C3N4. | |
The surface morphologies of bare BiPO4, g-C3N4, 30% BiPO4/g-C3N4, and 50% BiPO4/g-C3N4 catalysts were characterized by FE-SEM. As depicted in Fig. 2, the diameter of nanorod bundles in BiPO4 was found to be 300 nm, and lengths of 800 nm (Fig. 2a). Whereas the g-C3N4 displayed a typical sheet-like morphology with several crystallites (Fig. 2b). After the heterojunction was successfully formed in 30% BiPO4/g-C3N4, and 50% BiPO4/g-C3N4 samples, the agglomeration of BiPO4 could be observed by the insertion of BiPO4 nanorods bundles in the inter sheets of g-C3N4 (Fig. 2c and d), which implies that the g-C3N4 sheets are coated with BiPO4 nanorods bundles.
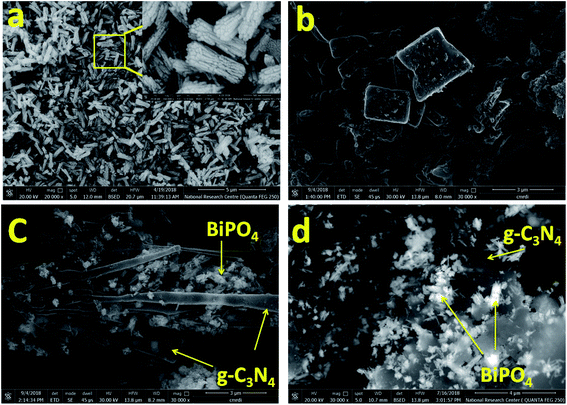 |
| Fig. 2 FE-SEM images of BiPO4 (a), g-C3N4 (b), and 30% BiPO4/g-C3N4 (c), and 50% BiPO4/g-C3N4 (d). | |
The TEM image (Fig. 3a) revealed that BiPO4 was composed of nanorods with diameter ranging from 30 to 40 nm. HRTEM (Fig. 3b) showed that BiPO4 nanorod bundles have a lattice fringe spacing of 0.349 nm, which can be indexed to (110) crystal plane of BiPO4 (JCPDS card no. 15-0766). The SAED pattern (Fig. 3c) confirmed the polycrystalline nature of the material due to the presence of concentric ring shape like. The TEM images shown in Fig. 3d indicated that BiPO4 nanorod bundles are bonded to g-C3N4 nanosheets. HRTEM (Fig. 3e) shows a fringe spacing of 0.350 nm due to (110) crystal planes of BiPO4. In addition, the polycrystalline phase was observed in SAED pattern (Fig. 3f). It can be seen from TEM images (Fig. 3g) that g-C3N4 has an unsmooth surface, which could boost the catalytic reaction by offering a higher surface area or/and favorizes the immobilization of other semiconductor nanoparticles. From the results of materials characterization, it can be concluded that the BiPO4 nanorod bundles was successfully immobilized on the g-C3N4 nanosheets to form heterojunction system.
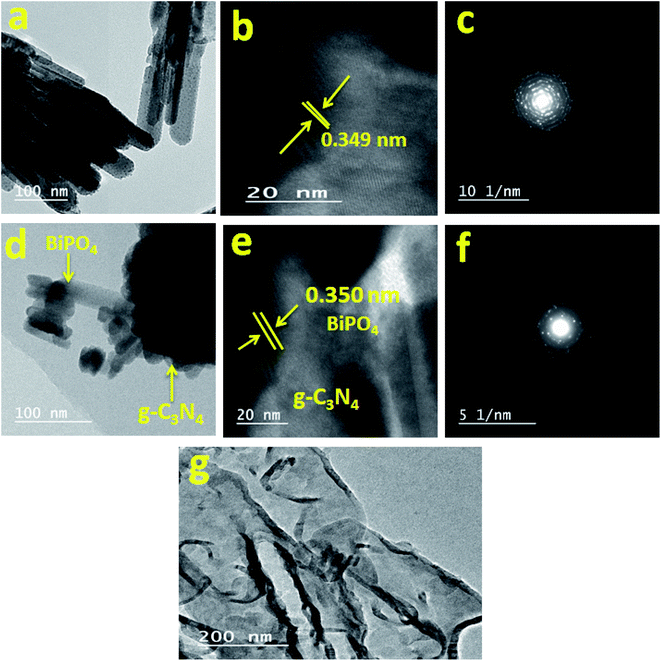 |
| Fig. 3 TEM, HRTEM images and SEAD pattern of BiPO4 (a, b, and c, respectively), BiPO4/g-C3N4 hybrid structure (d, e, and f, respectively), and TEM image of g-C3N4 (g). | |
The chemical oxidation state of BiPO4/g-C3N4 hybrid structure was verified using XPS analysis. Fig. 4a illustrates the full scan survey which indicate the presence of Bi, P, O, C and N elements, implying the successful heterojunction of BiPO4 and g-C3N4. The high resolution Bi 4f, P 2p, O 1s, C 1s, and N 1s are shown in Fig. 4b–f. The binding energies peaks at 159.81 eV and 165.11 eV (Fig. 4b) are due to the Bi 4f7/2 and Bi 4f5/2 levels in BiPO4, respectively.54 The Bi 4f7/2 and Bi 4f5/2 peaks showed a splitting of 5.3 eV which confirms that Bi atoms have a valence state of +3.55 The characteristic peak of P 2p can be found at 133.7 eV (Fig. 4c), which ascribed to the P5+ in BiPO4.56 In Fig. 4d, the peaks at 529.85, 531.61 and 533.66 eV correspond to O2− bonded to Bi, surface bound and adsorbed oxygen, respectively.57 The two peaks in C 1s spectra appeared at 284.34 and 287.37 eV are due to the sp2 bonded carbon atoms such as carbon–carbon bonding (C–C), and carbon–nitrogen double bond (C
N), respectively (Fig. 4e).58,59 The high resolution N 1s XPS spectra in Fig. 4f is divided into four bands with energies of 398.26, 400.39, 401.76 and 404.11 eV correspond to C–N
C, N–(C)3 groups, and (C)2–N–H, respectively.50,60 The XPS data is an accordance with XRD, FE-SEM, and TEM analysis.
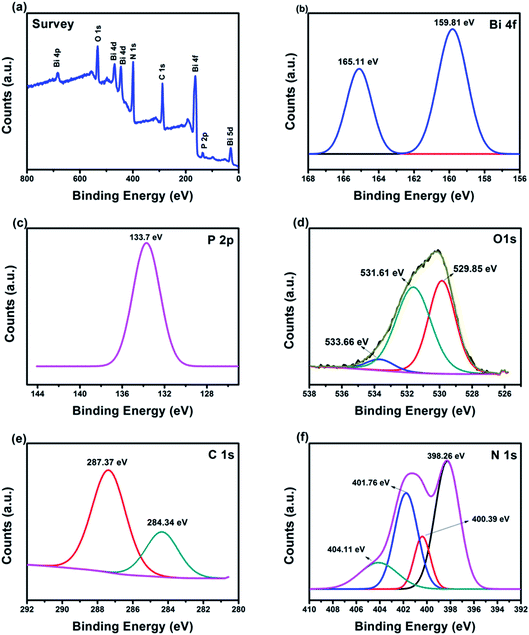 |
| Fig. 4 XPS spectra of BiPO4/g-C3N4, (a) survey spectra, (b) Bi 4f, (c) P 2p, (d) O 1s, (e) C 1s, (f) N 1s. | |
FTIR spectra of bare semiconductors and BiPO4/g-C3N4 composites are shown in Fig. 5. In terms of BiPO4, bending vibration peaks due to PO4 group are detected at 587 and 534 cm−1. The band at 974 cm−1 is assigned to PO4 stretching vibration.41 The band at 3495 cm−1 corresponds to hydroxyl stretching vibration groups of the surface adsorbed or/and structure water molecules in BiPO4. δ(H–O–H) bending vibrations can be observed also at 1602 cm−1. g-C3N4 spectrum shows a large band at 3155 cm−1 as a result of stretching vibration in NH and NH2 groups.61 The heptazine heterocyclic ring stretching vibrations in g-C3N4 units were appeared at 1200–1650 cm−1. In addition, the peaks at 1310 and 1629 cm−1 correspond respectively to the stretching vibrations of C–N and C
N.61 The characteristic peak at about 800 cm−1 could be assigned to the triazine units.62 For BiPO4/g-C3N4 samples, the entire characteristic peaks of (PO4) group (bending, stretching vibration) in BiPO4 are gradually strengthen with increasing BiPO4 content, implying that the BiPO4 and g-C3N4 are of harmonious coexistence.
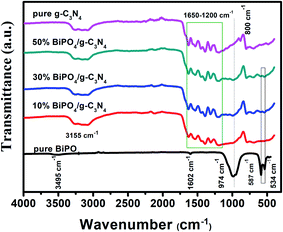 |
| Fig. 5 FT-IR spectra of pure BiPO4, g-C3N4, 10% BiPO4/g-C3N4, 30% BiPO4/g-C3N4, and 50% BiPO4/g-C3N4. | |
3.2 4-NP catalytic reduction
The catalytic performances of as-prepared catalysts towards the reduction of 4-NP to 4-AP in the presence of NaBH4 are shown in Fig. 6. The maximum absorption peak of aqueous solution of 4-NP (Fig. 6a) is shown at 318 nm but after addition of NaBH4 the peak shifted to 400 nm with a color conversion from light yellow to strong yellow due to NaBH4 converted 4-nitrophenol to 4-nitrophenolate.63,64 The coexistence of these two peaks indicates the copresence of 4-nitrophenol and nitrophenolate during the equilibrium, which is due to 4-nitrophenol self-ionization.10 In terms of g-C3N4, no significant reduction was observed for pure g-C3N4 in presence of NaBH4 (Fig. 6b). As seen in Fig. 6c–f, when 0.5 g L−1 of BiPO4/g-C3N4 composite was added to the reaction medium, a fast disappearance of yellow color was found, and a quick decrease in the peak intensity of 400 nm, and at the same time the characteristic peak of 4-AP at 300 nm was appeared, reflecting the reduction reaction.65 Time consumed for reduction of 4-NP is 12, 4, 1, and 20 min for 10% BiPO4/g-C3N4, 30% BiPO4/g-C3N4, 50% BiPO4/g-C3N4, and 70% BiPO4/g-C3N4, respectively. In addition, bare BiPO4 showed similar spectral tendency within 45 min (Fig. 6g). The order of the catalytic performances was as follows 50% BiPO4/g-C3N4 > 30% BiPO4/g-C3N4 > 10% BiPO4/g-C3N4 > 70% BiPO4/g-C3N4 > BiPO4 > g-C3N4. Increasing percentage of BiPO4 to 70% may cover surface of g-C3N4 and decreased the catalytic reduction of 4-NP. The enhancement of catalytic performance ability could be attributed to the synergistic heterojunction effect between BiPO4 and g-C3N4 nanosheets, high electrical conductivity, and enlarged reaction active sites.
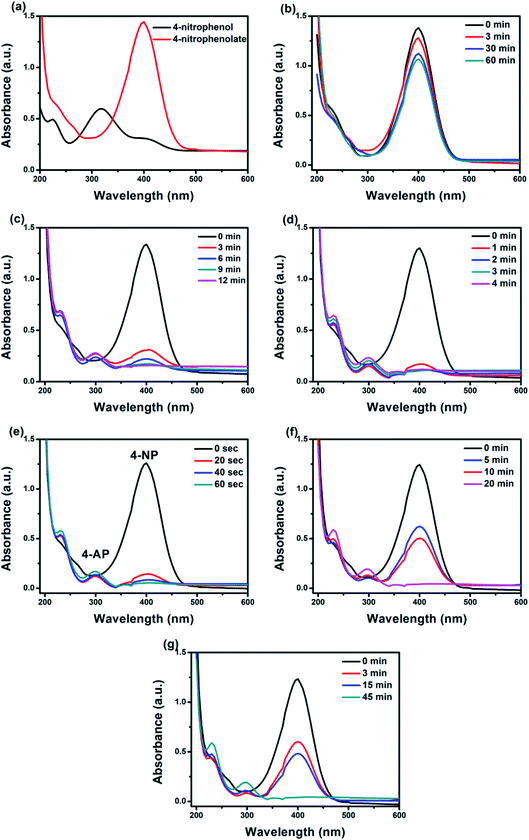 |
| Fig. 6 UV-vis spectral changes of 4-NP before and after adding NaBH4 solution (a); the successive reduction of 4-NP to 4-AP in presence of pure g-C3N4 (b), 10% BiPO4/g-C3N4 (c), 30% BiPO4/g-C3N4 (d), 50% BiPO4/g-C3N4 (e), 70% BiPO4/g-C3N4 (f) and pure BiPO4 (g). ([4-NP] = 10 mg L−1, [catalyst] = 0.5 g L−1). | |
The reduction conversion kinetics of 4-NP were studied by the first-order simplification of Langmuir–Hinshelwood (L–H), using the following equation:66
where
A0 and
At are absorbance of 4-NP in solution at times 0 and
t, respectively, and
k is the first-order rate constant (min
−1). The
kapp value is obtained from a liner plot of ln(
At/
A0)
versus time (
t), as shown in
Fig. 7e. The rate constant values was 0.004, 0.052, 0.186, 0.677, and 2.914 min
−1 for pure g-C
3N
4, BiPO
4, 10% BiPO
4/g-C
3N
4, 30% BiPO
4/g-C
3N
4, 50% BiPO
4/g-C
3N
4, and 70% BiPO
4/g-C
3N
4, respectively as shown in
Fig. 7e and
Table 1. It is clear the increase of the amount of BiPO
4 in the composite leads to increase proportionally the rate constant of the reduction reaction. Therefore, 50% BiPO
4/g-C
3N
4 sample gives the highest
k value which was 728.5 and 56 times superior than the values recorded for g-C
3N
4 and BiPO
4, respectively. The impact of temperature on reduction of 4-NP was further investigated using 50% BiPO
4/g-C
3N
4. The
kapp values improved with the increase in temperature due to increasing diffusion rate of reactant molecules (
Table 2).
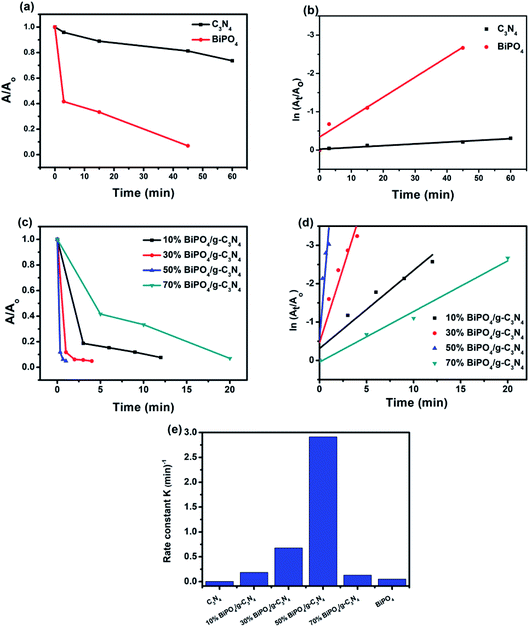 |
| Fig. 7 Reduction rate of 4-NP over different catalysts (a and c); corresponding linear transform ln(A/A0) = f(t) of the 4-NP reduction kinetics curves (b and d); comparison of the rate constant value for the reduction of the 4-NP over different catalysts (e). ([4-NP] = 10 mg L−1, [catalyst] = 0.5 g L−1). | |
Table 1 The kapp values for the reduction of 4-nitrophenol with and without catalysts in the presence of NaBH4
S. No. |
Catalyst |
Kapp (min−1) |
1 |
C3N4 |
0.004 |
2 |
10% BiPO4/g-C3N4 |
0.186 |
3 |
30% BiPO4/g-C3N4 |
0.677 |
4 |
50% BiPO4/g-C3N4 |
2.914 |
5 |
70% BiPO4/g-C3N4 |
0.13 |
6 |
BiPO4 |
0.052 |
7 |
Without catalyst |
0.001 |
Table 2 Impact of temperature on kapp values for the reduction of 4-nitrophenol ([4-NP] = 30 mg L−1, [catalyst] = 0.5 g L−1)
S. No. |
Temperature (K) |
Kapp (min−1) |
1 |
298 |
1.1 |
2 |
303 |
1.25 |
3 |
308 |
3.50 |
4 |
313 |
4.67 |
5 |
318 |
5.24 |
The turnover number (TON) and the turn over frequency (TOF) of 50% BiPO4/g-C3N4 heterojunction have been further investigated to show the catalytic efficiency of the catalyst. The TON of catalyst is the number of 4-NP molecules that can convert into products using 1 g of catalyst, while TOF is calculated as TON/time. The concentration of 4-NP and dosage of catalyst are 7.18 × 10−5 M, 0.025 g, respectively. The TOF was found to be 0.249 molecules per g.s for 50% BiPO4/g-C3N4 heterojunction using the following equation:64
where
mi is the initial number of moles nitrophenol,
X is the conversion of 4-NP,
x is the molecular weight of 4-NP,
W is the mass of catalyst used in the reaction (g), and
t is the reaction time (h).
3.2.1 Effect of initial concentration of 4-NP. The effect of initial concentration of 4-NP on the catalytic efficiency rate using 50% BiPO4/g-C3N4 catalyst was carried by varying the concentration from 10 to 70 mg L−1, and the obtained results as shown in Fig. 8a. Interestingly, 50% BiPO4/g-C3N4 was able to reduce all 4-NP solutions at concentrations from 10 to 70 mg L−1 reflecting the highly efficiency of such a catalyst towards this 4-NP reduction. At lower concentration, superior constant rate was recorded due to the availability of large number of catalytic sites per a given amount of 4-NP moles. And vice versa, the higher the concentration, the lower the rate constant (Fig. 8b) fitting pseudo-first-order reaction, due to the high competition of 4-NP molecules on the limited sites. In addition, the number of molecules adsorbed at the surface of the BiPO4/g-C3N4 heterojunction increases with the increase in the concentration of 4-nitrophenol and hence, the surface becomes saturated by 4-nitrophenol molecules. This leads to a decrease in concentration of BH4− ions approaching the surface of the BiPO4/g-C3N4 heterojunction, hence lowering the rate of hydrogen transfer from BH4− ion to the 4-nitrophenol molecule. This confirms that the BiPO4/g-C3N4 catalyzed reduction of nitrophenol occurs according to the L–H mechanism.
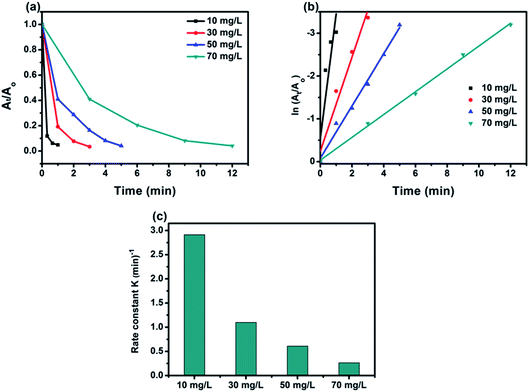 |
| Fig. 8 Effect of initial concentration on reduction rate of 4-NP (a); corresponding linear transform ln(At/A0) = f(t) of the 4-NP reduction kinetics curves (b); comparison of the rate constant value for the reduction of the 4-NP over initial different concentration (c). ([4-NP] = 10–70 mg L−1, [catalyst] = 0.5 g L−1). | |
3.2.2 Effect of catalyst amount. We also investigated the effect of catalyst dosage (0.012–0.05 g) on the reduction 4-NP (70 mgL−1). As seen in Fig. 9, with the increase of catalyst dosage, the removal efficiency of 4-NP improved markedly. With further increase to 0.05 g, the reduction efficiency value is 99% within 5 min for 4-NP reduction. The 50% BiPO4/g-C3N4 composite (0.05 g) exhibited the highest rate constant of 0.58 min−1 compared with 0.025 g (0.26 min−1), and 0.012 g (0.18 min−1) catalyst dosage as shown in Fig. 9c. As above-discussed, the relationship between the active sites on the surface of the catalyst and 4-NP molecules is very significant in terms of reaction kinetics. The use of higher amount of catalyst is required to proceed a faster reduction reaction at high 4-NP concentration.
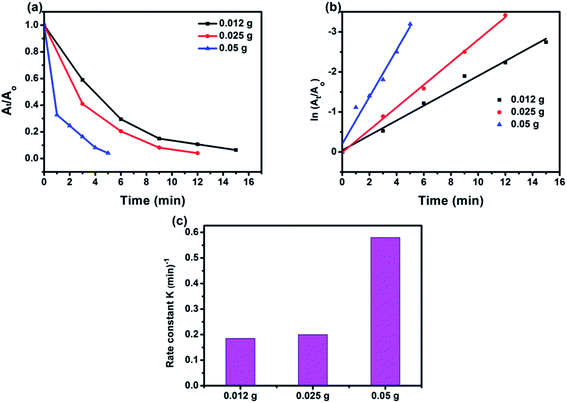 |
| Fig. 9 Reduction rate of 4-NP over catalyst amount (a); corresponding linear transform ln(At/A0) = f(t) of the 4-NP reduction kinetics curves (b); comparison of the rate constant value for the reduction of the 4-NP over catalyst amount (c). ([4-NP] = 70 mg L−1, [catalyst] = 0.012–0.05 g in 50 mL [4-NP]). | |
3.3 Feasible mechanism for 4-NP reduction
Overall, the obtained results showed that the bare g-C3N4 has very low catalytic efficiency towards the reduction of 4-NP from one side, and from another side, BiPO4/g-C3N4 catalysts exhibited ultrafast catalytic reductive conversion of 4-NP, compared to bare BiPO4. In addition, the higher amount BiPO4 in the composite, the faster reduction kinetics. These results lead to deduce that BiPO4 plays an important key especially when it is bonded to g-C3N4 nanosheets. The Langmuir–Hinshelwood (LH) model was proposed as mechanism for our reaction. The plausible mechanism for the 4-NP in the presence of NaBH4 and BiPO4/g-C3N4 is shown in Scheme 2. NaBH4 undergoes an ionization and produce BH4− species, which adsorb on the catalyst surface, followed by BO2− species generation as a result of self-hydrolysis. Simultaneously, adsorbed BH4− species can induce the transfer of active hydrogen species to form hydride complex. Afterwards, such active hydrogen species react with nitro groups to reduce them into amino groups, as reported in previous studies.66,67 The produced aminophenol is released from the surface of the catalyst to the medium. The catalytic reduction activity of BiPO4/g-C3N4 composites were significantly enhanced compared with bare BiPO4 and g-C3N4 due to addition of BiPO4 nanorod bundles immobilized on the g-C3N4 nanosheets to form heterojunction system may form more active surface-hydrogen species, suggesting higher yield of 4-NP reduction. In addition, the conductive g-C3N4 can transfer electrons and H˙ radicals from the adsorbed BH4− to 4-NP through the catalytic BiPO4 nanorod bundles more readily, resulting in the production of 4-AP. Furthermore, the heterojunction of BiPO4/g-C3N4 renders all active sites readily accessible that can significantly facilitate the rapid transport and diffusion of hydrogen radicals and electrons, resulting in the enhanced catalytic reduction on 4-NP. The efficiency of BiPO4/g-C3N4 towards the reduction of 4-NP was comparatively listed in Table 3 with the recent previous reported catalysts for 4-NP reduction. The value of rate constant was calculated to be 2.914 min−1 for 50% BiPO4/g-C3N4 nanocomposite that is much better than other nanocomposites, as shown in Table 3.
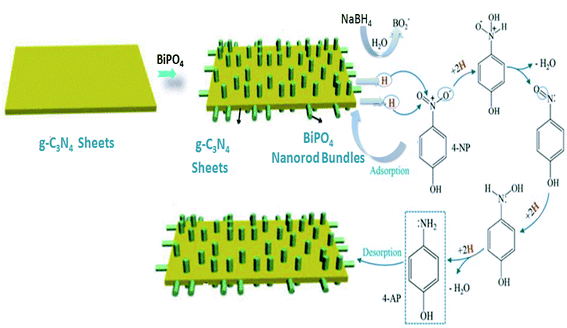 |
| Scheme 2 The plausible mechanism for the catalytic reduction of 4-NP by BiPO4/g-C3N4 composite using NaBH4 as a reducing agent. | |
Table 3 The comparison of present work with the recent literature of catalytic reduction of 4-NP to 4-AP using various catalysts with its reaction conditions
Catalyst |
Conc. of 4-NP (mol dm−3) |
Conc. of NaBH4 (mol dm−3) |
Amount of catalyst (g L−1) |
Time (min) |
Rate constant (min−1) |
Number of cycles |
Ref. |
g-C3N4/CuS |
1.26 × 10−2 |
0.5 |
3.3 |
50 |
0.0411 |
5 |
68 |
Au@g-C3N4 |
0.01 |
0.1 |
1 |
10 |
0.109 |
10 |
69 |
Au/CeO2@g-C3N4 |
0.12 × 10−3 |
0.04 |
0.5 |
0.6 |
6.36 |
5 |
27 |
g-C3N4/Bi2S3 |
0.03 |
0.2 × 10−3 |
0.01 |
60 |
0.016 |
5 |
70 |
Cu@g-C3N4 |
0.13 × 10−3 |
1.64 × 10−5 |
5 |
25 |
1.11 |
4 |
71 |
N/graphene |
0.1 × 10−3 |
0.04 × 10−3 |
1.5 |
18 |
0.029 |
3 |
72 |
Ag/g-C3N4/V2O5 |
0.01 |
0.5 |
5 |
60 |
0.373 |
3 |
73 |
50% BiPO4/g-C3N4 |
7.18 × 10−5 |
16 × 10−3 |
0.5 |
1 |
2.914 |
5 |
This work |
3.4 Stability evaluation
Recycling of any heterogeneous catalyst has a significant role, especially for the economic and environmental points of view. The catalytic performance of BiPO4/g-C3N4 catalyst was checked five times in a row towards the reduction of 4-NP under the same conditions (50 mg L−1, and 25 mg 50% BiPO4/g-C3N4). As shown in Fig. 10, the reduction rate was slightly decreased from 98% to 95%, after five times recycling. The results demonstrated that the as-prepared 50% BiPO4/g-C3N4 heterojunction was comparably stable under the studied conditions, which is an advantage of using the catalysts for industrial applications.
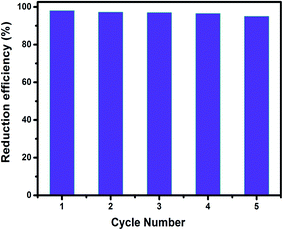 |
| Fig. 10 Cyclic runs for the reduction of 4-NP on 50% BiPO4/g-C3N4 heterojunction in the presence of NaBH4. ([4-NP] = 50 mg L−1, [catalyst] = 0.5 g L−1). | |
4. Conclusions
Highly efficient and stable BiPO4 nanorod bundles supported on g-C3N4 sheets composites with variable BiPO4 loadings were developed using ex situ chemical deposition. The as synthesized composites showed superior catalytic activities towards reduction of 4-NP to 4-AP in wastewater, unlike bare g-C3N4 and BiPO4. It was found that the increasing BiPO4 loading enhanced catalytic reduction of 4-NP. The 50% BiPO4/g-C3N4 sample performed the highest rate constant for 4-NP reduction which was 728.5 and 56 times superior than the values for g-C3N4 and BiPO4, respectively. The mechanism for high-efficient catalytic activity have been discussed. In addition, the synthesized BiPO4/g-C3N4 heterojunction does not show a significant reduce in its catalytic efficiency during the five times recycling tests. Therefore, the BiPO4/g-C3N4 composite indicated the potential application for removing the hazardous wastes such as p-nitrophenol from the environment as a whole.
Conflicts of interest
There are no conflicts to declare.
Acknowledgements
We acknowledge the financial support from Helwan University and the Central Metallurgical Research and Development Institute (CMRDI).
References
- T. Begildayeva, S. J. Lee, Y. Yu, J. Park, T. H. Kim, J. Theerthagiri, A. Ahn, H. J. Jung and M. Y. Choi, J. Hazard. Mater., 2020, 409, 124412 CrossRef PubMed.
- Z. Zhu, L. Tao and F. Li, J. Hazard. Mater., 2014, 279, 436–443 CrossRef CAS PubMed.
- Z. Xiong, H. Zhang, W. Zhang, B. Lai and G. Yao, Chem. Eng. J., 2019, 359, 13–31 CrossRef CAS.
- Q. Chen, C. Ma, W. Duan, D. Lang and B. Pan, J. Cleaner Prod., 2020, 271, 122550 CrossRef CAS.
- M. I. Din, R. Khalid, Z. Hussain, T. Hussain, A. Mujahid, J. Najeeb and F. Izhar, Crit. Rev. Anal. Chem., 2020, 50, 322–338 CrossRef CAS PubMed.
- A. A. Pradhan and P. R. Gogate, Chem. Eng. J., 2010, 156, 77–82 CrossRef CAS.
- M. T. Qamar, M. Aslam, I. M. I. Ismail, N. Salah and A. Hameed, ACS Appl. Mater. Interfaces, 2015, 7, 8757–8769 CrossRef CAS PubMed.
- S. R. Thawarkar, N. D. Khupse and A. Kumar, ChemistrySelect, 2017, 2, 6833–6843 CrossRef CAS.
- A. Hernández-Gordillo, A. G. Romero, F. Tzompantzi and R. Gómez, Appl. Catal., B, 2014, 144, 507–513 CrossRef.
- M. A. Koklioti, T. Skaltsas, Y. Sato, K. Suenaga, A. Stergiou and N. Tagmatarchis, Nanoscale, 2017, 9, 9685–9692 RSC.
- M. Zhang, X. Su, L. Ma, A. Khan, L. Wang, J. Wang, A. S. Maloletnev and C. Yang, J. Hazard. Mater., 2021, 403, 123870 CrossRef CAS PubMed.
- P. Kar, K. Shukla, P. Jain, G. Sathiyan and R. K. Gupta, Nano Mater. Sci., 2020, 3, 25–46 CrossRef.
- O. L. Stroyuk and S. Y. Kuchmy, Theor. Exp. Chem., 2020, 56, 143–173 CrossRef CAS.
- C. Liu, J. Li, Y. Li, W. Li, Y. Yang and Q. Chen, RSC Adv., 2015, 5, 71692–71698 RSC.
- K. Hu, M. Yao, Z. Yang, G. Xiao, L. Zhu, H. Zhang, R. Liu, B. Zou and B. Liu, Nanoscale, 2020, 12, 12300–12307 RSC.
- C. Pan, J. Xu, Y. Wang, D. Li and Y. Zhu, Adv. Funct. Mater., 2012, 22, 1518–1524 CrossRef CAS.
- A. Mishra, A. Mehta, S. Basu, N. P. Shetti, K. R. Reddy and T. M. Aminabhavi, Carbon, 2019, 149, 693–721 CrossRef CAS.
- C. Lu, P. Zhang, S. Jiang, X. Wu, S. Song, M. Zhu, Z. Lou, Z. Li, F. Liu, Y. Liu, Y. Wang and Z. Le, Appl. Catal., B, 2017, 200, 378–385 CrossRef CAS.
- X. Chen, R. Shi, Q. Chen, Z. Zhang, W. Jiang, Y. Zhu and T. Zhang, Nano Energy, 2019, 59, 644–650 CrossRef CAS.
- M. Wu, J.-M. Yan, X. Tang, M. Zhao and Q. Jiang, ChemSusChem, 2014, 7, 2654–2658 CrossRef CAS PubMed.
- P. Su, J. Zhang, K. Xiao, S. Zhao, R. Djellabi, X. Li, B. Yang and X. Zhao, Chin. J. Catal., 2020, 41, 1894–1905 CrossRef CAS.
- D. Masih, Y. Ma and S. Rohani, Appl. Catal., B, 2017, 206, 556–588 CrossRef CAS.
- X. Liu, R. Ma, L. Zhuang, B. Hu, J. Chen, X. Liu and X. Wang, Crit. Rev. Environ. Sci. Technol., 2020, 51, 751–790 CrossRef.
- L. Zhou, H. Zhang, H. Sun, S. Liu, M. O. Tade, S. Wang and W. Jin, Catal. Sci. Technol., 2016, 6, 7002–7023 RSC.
- K. Gu, X. Pan, W. Wang, J. Ma, Y. Sun, H. Yang, H. Shen, Z. Huang and H. Liu, Small, 2018, 14, 1–8 Search PubMed.
- P. Fageria, S. Uppala, R. Nazir, S. Gangopadhyay, C. H. Chang, M. Basu and S. Pande, Langmuir, 2016, 32, 10054–10064 CrossRef CAS PubMed.
- M. Kohantorabi and M. R. Gholami, Appl. Phys. A: Mater. Sci. Process., 2018, 124, 1–17 CrossRef CAS.
- Y. Y. Liu, Y. H. Zhao, Y. Zhou, X. L. Guo, Z. T. Chen, W. J. Zhang, Y. Zhang, J. Chen, Z. M. Wang, L. T. Sun and T. Zhang, Nanotechnology, 2018, 29, 315702 CrossRef CAS PubMed.
- W. J. Ong, Front. Mater., 2017, 4, 1–10 Search PubMed.
- J. Wen, J. Xie, X. Chen and X. Li, Appl. Surf. Sci., 2017, 391, 72–123 CrossRef CAS.
- Y. Sang, X. Cao, G. Dai, L. Wang, Y. Peng and B. Geng, J. Hazard. Mater., 2020, 381, 120942 CrossRef CAS PubMed.
- Y. Li, H. Wang, L. Huang, C. Wang, Q. Wang, F. Zhang, X. Fan, M. Xie and H. Li, J. Alloys Compd., 2020, 816, 152665 CrossRef CAS.
- X. Ren, K. Wu, Z. Qin, X. Zhao and H. Yang, J. Alloys Compd., 2019, 788, 102–109 CrossRef CAS.
- S. Li, J. Chen, S. Hu, H. Wang, W. Jiang and X. Chen, Chem. Eng. J., 2020, 402, 126165 CrossRef CAS.
- R. A. Geioushy, S. M. El-Sheikh, A. B. Azzam, B. A. Salah and F. M. El-Dars, J. Hazard. Mater., 2020, 381, 120955 CrossRef CAS PubMed.
- L. Cheng, X. Hu and L. Hao, Ultrason. Sonochem., 2018, 44, 137–145 CrossRef CAS PubMed.
- C. Pan and Y. Zhu, Catal. Sci. Technol., 2015, 5, 3071–3083 RSC.
- Y. Liu, W. Yao, D. Liu, R. Zong, M. Zhang, X. Ma and Y. Zhu, Appl. Catal., B, 2015, 163, 547–553 CrossRef CAS.
- H. Lin, H. Ye, S. Chen and Y. Chen, RSC Adv., 2014, 4, 10968 RSC.
- Y. Liu, P. Zhang, H. Lv, J. Guang, S. Li and J. Jiang, RSC Adv., 2015, 5, 83764–83772 RSC.
- Y. Zhang, B. Shen, H. Huang, Y. He, B. Fei and F. Lv, Appl. Surf. Sci., 2014, 319, 272–277 CrossRef CAS.
- P. Hu, J. Niu, M. Yu and S. Y. Lin, Chin. J. Anal. Chem., 2017, 45, 357–362 CAS.
- J. Li, H. Yuan and Z. Zhu, Appl. Surf. Sci., 2016, 385, 34–41 CrossRef CAS.
- Y. Lv, Y. Zhu and Y. Zhu, J. Phys. Chem. C, 2013, 117, 18520–18528 CrossRef CAS.
- Y. Zhu, Q. Ling, Y. Liu, H. Wang and Y. Zhu, Appl. Catal., B, 2016, 187, 204–211 CrossRef CAS.
- Y. Zhiu, Y. Liu, Y. Lv, Q. Ling, D. Liu and Y. Zhu, J. Mater. Chem. A, 2014, 2, 13041–13048 RSC.
- Y. Guo, P. Wang, J. Qian, J. Hou, Y. Ao and C. Wang, Catal. Sci. Technol., 2018, 8, 486–498 RSC.
- Y. Wang, W. Luo, W. Jiang, Z. Wei and Y. Zhu, Mater. Today Adv., 2019, 1, 100006 CrossRef.
- D. Long, Z. Chen, X. Rao and Y. Zhang, ACS Appl. Energy Mater., 2020, 3, 5024–5030 CrossRef CAS.
- X. Zou, C. Ran, Y. Dong, Z. Chen, D. Dong, D. Hu, X. Li and Y. Cui, RSC Adv., 2016, 6, 20664–20670 RSC.
- A. B. Azzam, S. M. El-Sheikh, R. A. Geioushy, B. A. Salah, F. M. El-Dars and A. S. Helal, RSC Adv., 2019, 9, 17246–17253 RSC.
- X. Zou, C. Ran, Y. Dong, Z. Chen, D. Dong, D. Hu, X. Li and Y. Cui, RSC Adv., 2016, 6, 20664–20670 RSC.
- Z. Li, S. Yang, J. Zhou, D. Li, X. Zhou, C. Ge and Y. Fang, Chem. Eng. J., 2014, 241, 344–351 CrossRef CAS.
- M. H. Fulekar, A. Singh, D. P. Dutta, M. Roy, A. Ballal and A. K. Tyagi, RSC Adv., 2014, 4, 10097–10107 RSC.
- S. M. El-Sheikh, A. B. Azzam, R. A. Geioushy, F. M. El Dars and B. A. Salah, J. Alloys Compd., 2021, 857, 157513 CrossRef CAS.
- L. She, G. Tan, H. Ren, J. Huang, C. Xu and A. Xia, RSC Adv., 2015, 5, 36642 RSC.
- J. Zhao, Q. Han, J. Zhu, X. Wu and X. Wang, Nanoscale, 2014, 6, 10062–10070 RSC.
- R. Djellabi, B. Yang, K. Xiao, Y. Gong, D. Cao, H. M. A. Sharif, X. Zhao, C. Zhu and J. Zhang, J. Colloid Interface Sci., 2019, 553, 409–417 CrossRef CAS PubMed.
- J. Xia, J. Zhao, J. Chen, J. Di, M. Ji, L. Xu, Z. Chen and H. Li, J. Photochem. Photobiol., A, 2017, 339, 59–66 CrossRef CAS.
- Q. Liang, J. Jin, C. Liu, S. Xu, C. Yao and Z. Li, J. Mater. Sci.: Mater. Electron., 2018, 29, 2509–2516 CrossRef CAS.
- H. Sun, G. Zhou, Y. Wang, A. Suvorova and S. Wang, ACS Appl. Mater. Interfaces, 2014, 6, 16745–16754 CrossRef CAS PubMed.
- J. Gao, J. Wang, X. Qian, Y. Dong, H. Xu, R. Song, C. Yan, H. Zhu, Q. Zhong, G. Qian and J. Yao, J. Solid State Chem., 2015, 228, 60–64 CrossRef CAS.
- M. T. Shah, A. B. Sirajuddin, A. Ahmed, P. Abdullah, A. Muhammad, M. Saman, R. Khattak and A. Ali, Microsyst. Technol., 2017, 23, 5745–5758 CrossRef CAS.
- S. R. Thawarkar, B. Thombare, B. S. Munde and N. D. Khupse, RSC Adv., 2018, 8, 38384–38390 RSC.
- G. Wu, X. Liang, L. Zhang, Z. Tang, M. Al-Mamun, H. Zhao and X. Su, ACS Appl. Mater. Interfaces, 2017, 9, 18207–18214 CrossRef CAS PubMed.
- Y. Fu, P. Xu, D. Huang, G. Zeng, C. Lai, L. Qin, B. Li, J. He, H. Yi, M. Cheng and C. Zhang, Appl. Surf. Sci., 2019, 473, 578–588 CrossRef CAS.
- D. Ayodhya and G. Veerabhadram, J. Mol. Struct., 2019, 1186, 423–433 CrossRef CAS.
- D. Ayodhya and G. Veerabhadram, FlatChem, 2019, 14, 100088 CrossRef.
- T. B. Nguyen, C. P. Huang and R. an Doong, Appl. Catal., B, 2019, 240, 337–347 CrossRef CAS.
- D. Ayodhya and G. Veerabhadram, Environ. Technol., 2019, 42, 826–841 CrossRef PubMed.
- S. Huang, Y. Zhao and R. Tang, RSC Adv., 2016, 6, 90887–90896 RSC.
- P. V. R. K. Ramacharyulu, S. J. Abbas, S. R. Sahoo and S. C. Ke, Catal. Sci. Technol., 2018, 8, 2825–2834 RSC.
- H. S. EL-Sheshtawy, H. M. El-Hosainy, K. R. Shoueir, I. M. El-Mehasseb and M. El-Kemary, Appl. Surf. Sci., 2019, 467–468, 268–276 CrossRef CAS.
Footnote |
† Electronic supplementary information (ESI) available. See DOI: 10.1039/d1ra02852a |
|
This journal is © The Royal Society of Chemistry 2021 |
Click here to see how this site uses Cookies. View our privacy policy here.