DOI:
10.1039/D1RA01720A
(Paper)
RSC Adv., 2021,
11, 18171-18178
The synthesis of nanocarbon-poly(ricinoleic acid) composite as a lubricant additive with improved dispersity and anti-wear properties
Received
4th March 2021
, Accepted 2nd May 2021
First published on 19th May 2021
Abstract
Herein, a nanocarbon-poly(ricinoleic acid) composite as a lubricant additive with excellent oil-solubility and dispersity was synthesized using nanocarbon spheres (CNSs) and ricinoleic acid via a “one-pot” approach. The prepared composite was characterized via Fourier transform infrared spectrometry (FTIR), thermogravimetric analysis (TG), Raman spectroscopy (Raman) and X-ray diffraction (XRD). Scanning electron microscopy (SEM) showed that there was no obvious aggregation after surface modification of CNSs. Results demonstrated that the dispersion stability of the composite anti-wear additive in base lubricating oil was significantly optimized. The prepared nanocarbon-poly(ricinoleic acid) composite showed significantly improved stability and dispersity in base lubricating oil for 3 months without obvious precipitation. Tribological tests indicated that the composite lubricant additive exhibited an improved anti-wear performance and better wear resistance than pure CNS additives. The friction coefficients with the composite anti-wear additive dropped from 0.052 to 0.027, which was reduced by 48.1% compared with that of the TMT base lubricating oil. Furthermore, the composite additive is desirable for efficient anti-wear properties in base lubricating oil. The synergistic effect between modified CNSs and poly(ricinoleic acid) significantly improved the wear resistance of the base oil.
1 Introduction
Nanocarbon additives applied in lubrication systems can enhance the tribological properties of the lubricating oil by improving its extreme pressure, anti-wear and anti-friction performance.1,2 They can increase the efficiency of machines and prolong the service life of parts, which has great development potential.3,4 Nanocarbon spheres (CNSs) have the characteristics of large specific surface area, high dispersion, large surface energy and high hardness, which show a more obvious effect under the conditions of high temperature and overloading.5,6 It is worth noting that the amount of CNSs is quite small when used as a lube oil additive.7,8 Compared with the traditional extreme pressure and anti-wear additives, CNSs have a less negative impact on the environment.9,10
As an anti-wear additive, nanocarbon particles can reduce the friction coefficient on the wear surface by forming a thin film layer.11 Furthermore, they can also play a role in filling and repairing the friction surface.12,13 In recent years, many scientists have conducted extensive studies and reported the wear resistance of carbon nanomaterials. Kumar et al.14 investigated the friction behavior of different grades of polyalphaolefin oil (PAO) modified with COOH-functionalized multi-walled carbon nanotubes (MWCNTs). The experimental results showed that the presence of multi-walled carbon nanotubes could effectively enhance the anti-wear performance of the base lubricating oil. Also, MWCNTs exhibited better anti-wear properties than friction properties. The literature also discusses the possible reasons for the improved friction and wear properties. Gu et al.16 proposed the grafting of a poly(ethylene imine) (PEI) nanolayer on the surface of carbon spheres (CS) to improve the friction and wear properties of traditional lubricating oils. CS-PEI showed good dispersion stability in engine oil. The steel substrates lubricated by CS-PEI showed clearly improved properties, with a significant reduction in the friction and wear (15–42%). The tribological mechanism was demonstrated by scanning electron microscopy and energy-dispersive X-ray spectroscopy. Mou et al.15 designed and synthesized a series of novel polyelectrolyte-functionalized carbon dots (CDs-PEI-X) via a facile and reversible phase transfer method based on the protonation reaction and anion exchange process executed on the surface of polyethylenimine-grafted CDs (CDs-PEI). The hydrophobic CDs-PEI-X displayed excellent dispersibility and long-term stability in PEG200 base lubricating oil and exhibited excellent lubricity, outstanding load-bearing capacity, long service life, and remarkable operational stability under the boundary lubrication regime. However, although many research groups have modified the surface of nanocarbon materials to improve their dispersion stability in lubricating oil, the insolubility and difficulty in achieving a stable dispersion of inorganic powder still restrain their application in lubricating oil.16 Therefore, it is very interesting and also urgent to increase the oil solubility of CNSs in lubrication oil. It is worth noting that the effects of CNSs on the properties of base lubricating oil still need further investigation for their industrial application.17
Castor oil is a type of oil with low volatility, non-irritation and non-drying properties, and the characteristics of high viscosity, low acid value, high temperature resistance, non-oxidation and non-solidification.18,19 As a natural and green lubricant, it is widely used in the fields of mechanical lubricants and brake oils.20 Ricinoleic acid is the key component of castor oil fatty acids, which is often used to prepare surfactants, plasticizers and lubricating oil additives.21 Poly(ricinoleic acid) itself produced by polymerization is an oil-soluble lubricant with excellent performance. As a surfactant, it can effectively improve the dispersion stability of nanoparticles in the oil phase. In addition, as a lubricant additive, poly(ricinoleic acid) can improve the anti-wear property, low temperature fluidity and biodegradability of base lubricating oil.22 The dispersion stability of CNSs in base lubricating oil can be improved by physical and chemical synchronization action.
Thus, to increase the oil solubility and improve the dispersion stability of modified CNSs in lubricating oils, herein, CNSs were initially purified using sulfuric acid and nitric acid. Then, the surface of the CNSs was connected with long alkyl chains via modification with ricinoleic acid. The tribological behavior of the modified CNSs with composite anti-wear additives was investigated in trimellitate (TMT) base lubricating oil as well as their viscosity, pour point, acid value and thermal behavior.
2 Experimental
2.1 Materials
The CNSs used in this study were purchased from Xifeng Co. Ltd. (Urumqi, China) with a purity of ≥95%. Organic solvents and sulfuric acid and nitric acid were purchased from Chemical Reagent Factory (AR, Shanghai, China). Ricinoleic acid was purchased from Guangzhou Langfeng Chemical Co., Ltd (Industrial Grade, Guangzhou, China). TMT was purchased from Shandong Ruijie New Materials Co. Ltd. (Industrial Grade, Liaocheng, China), which was used as the base lubricant in the experiment. The ZnO catalyst was purchased from Beilianchem Co., Ltd (Tianjin, China) with AR grade. All chemicals were used without further purification.
2.2 Synthesis of composite anti-wear additives
In the experiment, pre-prepared CNSs were purified by immersing them in a 1
:
3 mixture of concentrated HNO3 and H2SO4 and refluxing for 2 h. Then the samples were dried at 60 °C after filtering and washing with deionized water until neutral pH was reached. Then the CNSs were modified with ricinoleic acid was as follows: the oxidized CNSs were mixed with ricinoleic acid in a ratio of 1
:
80. Then 0.3% ZnO as the catalyst was added to the reaction system, which was stirred and fitted with a vacuum distillation device for 8 h at 200 °C. Subsequently, the reaction mixture was cooled to obtain the modified CNS composite anti-wear additive. It should be noted that ZnO itself is a solid anti-wear agent, but its content was so low, it did not need to be removed. The composite anti-wear additive was dispersed uniformly by sonication in 50 °C water bath for 20 min. The modified CNS composite anti-wear additive was added to TMT base oil in a certain proportion, then the nano-lubricating oil was obtained by ultrasonic dispersion at room temperature for 15 min. Fresh nano-lubricating oil was prepared for each measurement and was used immediately to avoid possible agglomeration or sedimentation.
To characterize the modified CNS composite anti-wear additive, the modified CNSs and poly(ricinoleic acid) were separated by filtration. Then, the ZnO catalyst was removed using 10% (v/v) HCl. The products were further extracted with CH2Cl2 and deionized water several times to remove the poly(ricinoleic acid) and HCl. Subsequently the modified CNSs were dried at 60 °C in a vacuum drying oven overnight, which were characterized via FTIR, TG, Raman spectroscopy and XRD. The polymerization degree of poly(ricinoleic acid) was calculated using the acid value. The modification mechanism of CNSs is shown in Fig. 1.
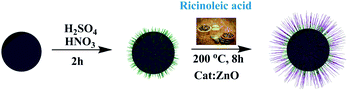 |
| Fig. 1 Modification mechanism of CNSs. | |
2.3 Material characterization
The infrared spectrum of CNSs was recorded on a DIGILAB FTS 3000 Fourier transform-infrared (FTIR) spectrophotometer (Digilab Inc., Boston, MA, USA) with a KBr pellet in the range of 400 to 4000 cm−1 at room temperature. The morphology of CNSs was imaged via scanning electron microscopy (SEM) on a JSM-5600 LV scanning electron microscope (Japan Electron Optics Laboratory Co., Ltd. Tokyo, Japan) with an acceleration voltage of 20 kV. Thermogravimetric analysis (TGA) was carried out on a PerkinElmer TGA-7 analyzer PE TG/DTA 6300 instrument (PerkinElmer Inc., Boston, MA, USA) over the temperature range of 40–800 °C at an air flow rate of 50 mL min−1 at a heating rate of 10 °C min−1. The powder X-ray diffraction (XRD) patterns of the CNSs were measured on an XRD analyzer (D8-Advance, Bruker AXS, Karlsruhe, Germany) equipped with a diffracted-beam monochromator with Cu Kα radiation (50 kV, 40 mA) in the 2θ range of 10° to 70° with a step size of 0.05°. EDS of the friction surfaces was carried out on an Energy Spectrum Analyser (X-flash 5010, Bruker, Karlsruhe, Germany).
2.4 Performance tests
The tribology tests were performed on a four-ball friction tester (Xiamen Tenkey Co., Ltd. Xiamen, China) at different concentrations of CNSs in base lubricating oil. The measurements were performed at 75 °C with a speed of 1200 rpm for 60 min under the load of 60 kgf.
The kinematic viscosity variations in the nano-lubricant were measured at 40 °C and 100 °C with different concentrations of CNSs. The kinematic viscosity was measured on a JSR1104 kinematic viscosimeter (JinShi Petrochemical Instrument Co., Ltd. Jinshi, China) according to the ASTM D445 standard. The viscosity index was measured according to the ASTM D2270 standard.
The pour point was measured according to the ASTM D97 standard, which was conducted on a JSR0805 inclinometer (JinShi Petrochemical Instrument Co., Ltd. Jinshi, China).
The change in acid value was used to judge the degree of polymerization of ricinoleic acid. The acid value was measured according to the GB/T264 standards (China) and the tests were carried out with KOH standard solution titration.
3 Results and discussion
3.1 Polymerization of ricinoleic acid
The theoretical acid value of ricinoleic acid is 187.9 mg KOH per g. Herein, the degree of polymerization was judged based on the acid value. |
 | (1) |
where C is the concentration of potassium hydroxide standard solution, mol L−1; V is the consumption of potassium hydroxide standard solution volume, mL; m is the sample weight, g; M is the molar mass of sample, g mol−1 and n is the number moles of sample, mol.
The theoretical acid value of 4-poly(ricinoleic acid) is 50.82 according to formula (1), which is very close to the acid value of 49.21 obtained from the experiment. The experimental results show that when 0.3% ZnO as the catalyst was added to the reaction system, which was stirred and fitted with a vacuum distillation device for 8 h under 200 °C, the product was 4-poly(ricinoleic acid). Poly(ricinoleic acid) itself is an excellent oil-soluble lubricant with good solubility in both paraffinic and cycloalkyl base lubricating oils. Due to its unique properties as a surfactant, poly(ricinoleic acid) is mainly used as a lubricating additive in micro-emulsions and semi-synthetic metalworking fluids, and is especially suitable for rolling oil, emulsified, semi-synthetic and synthetic cutting fluids for aluminum processing. Poly(ricinoleic acid) can help CNSs be stably dispersed in the oil phase by van der Waals attraction force. Furthermore, the composite anti-wear system of poly(ricinoleic acid) and CNSs can provide an enhance wear reduction performance for the base lubricating oil.
3.2 Morphological analysis
The dispersion of CNSs in synthetic ester lubricants is very difficult even after sonication treatment. This is due to the high specific surface area and small diameter of CNSs, and strong van der Waals attraction force between CNSs, resulting in the easy agglomeration of large CNSs. Thus, to improve the dispersion stability of CNSs in the organic phase as a lubricating oil, it is usually necessary to modify them by physical or chemical methods. Herein, the method of surface chemical modification was employed to improve the dispersion stability of CNSs in lubricating oil. The ricinoleic acid molecules have long hydrocarbon chains, which can limit the van der Waals interaction between CNSs and attract the ester bonds in lubricants, thus effectively improving the dispersion stability of CNSs. SEM was employed to detect the structure and morphology of the modified CNSs compared with the unmodified CNSs. The SEM images of the unmodified and modified samples are shown in Fig. 2.
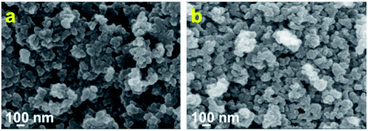 |
| Fig. 2 SEM images of CNSs. (a) Unmodified CNSs and (b) modified CNSs. | |
The SEM investigation showed that there was no agglomeration after modification with ricinoleic acid. Also, the average diameter of CNSs was still in the range of 40–60 nm. Thus, the experimental results indicate that the morphology and particle size of CNSs did not change significantly by grinding after modification.
3.3 FTIR analysis
The variation in the characteristic absorption peaks in the spectra can be used to infer the effectiveness of the functional groups on the surface of CNSs, which can provide proof to identify whether the modification process was successful. The infrared spectra of the CNSs are shown in Fig. 3. As can be seen in Fig. 3a, there is no obvious absorption, which implies that the structure of the raw material contains no functional groups. Compared with the unmodified CNSs, the FTIR spectrum of the modified CNSs shows the presence of many groups on the surface of CNSs, where the absorption peak at 3742 cm−1 is attributed to the hydroxyl group from the terminal of poly(ricinoleic acid) on the surface of CNSs. The characteristic peaks observed at 2920 cm−1 and 2860 cm−1 are attributed to the –CH3 and –CH2 stretching mode, respectively. The new peak observed at about 1728 cm−1 is attributed to –C
O. In addition, the absorption peaks of –C–H and –C–O– are located at 1470 cm−1 and 1240 cm−1, respectively. These results are consistent with the literature.23 Thus, all the results confirm the successful coating of CNSs with ricinoleic acid.
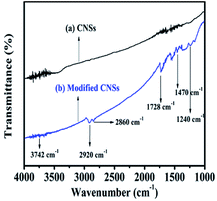 |
| Fig. 3 FTIR spectra of (a) unmodified CNSs and (b) modified CNSs. | |
3.4 Raman analysis
The Raman spectrum of the modified CNSs showed the D band at 1327 cm−1 and G band at 1608 cm−1 in Fig. 4. The G band is produced by the graphite base, where a graphite layer is formed by the intact structure of hexagons. The new peak of the G′ band was observed at about 2700 cm−1, which is mainly due to the structural defects in CNSs caused by the organic-modified acid treatment.24 The results also indicate that the method of modifying CNSs by ricinoleic acid is feasible.
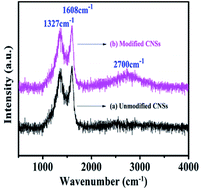 |
| Fig. 4 Raman spectra of (a) unmodified CNSs and (b) modified CNSs. | |
3.5 XRD analysis
Fig. 5a and b show the X-ray diffraction patterns of the unmodified and modified CNSs, respectively. The intense peaks at around 26.4° and 42° are associated with the characteristic peaks of the (002) and (100) planes of CNSs. The slight increase in the intensity of the diffraction peak at about 10° is related to the intense oxidation of CNSs. Thus, the XRD characterization results indicate the successful surface modification of CNSs.24
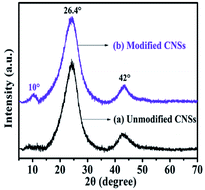 |
| Fig. 5 XRD patterns of (a) unmodified CNSs and (b) modified CNSs. | |
3.6 TG analysis
The TG curves of poly(ricinoleic acid), unmodified and modified CNSs are shown in Fig. 6. The initial slope in the degradation profiles of the modified CNSs can be attributed to the loss of poly(ricinoleic acid) from the sample in the temperature range of 251 °C to 518 °C. The second mass loss of CNSs in the temperature range of 542 °C to 603 °C is due to the decomposition of CNSs. The temperature curves of decomposition are consistent with poly(ricinoleic acid) and unmodified CNSs, which provide a basis for our assumption.
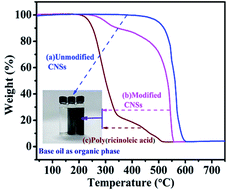 |
| Fig. 6 TG curves of (a) unmodified CNSs, (b) modified CNSs, (c) poly(ricinoleic acid); and dispersion stability test in the inset. | |
The experimental results show that the process of coating CNSs with ricinoleic acid was successful. The results also provide a qualitative assessment of the performance of the dispersion stability for the unmodified and modified CNSs in the base lubricating oil. After ultrasonic treatment with 0.025 (wt%) unmodified CNSs and 0.025 (wt%) modified CNSs {with 0.5% (wt%) poly(ricinoleic acid)}, TMT with modified CNSs was stable and no precipitation phenomenon was observed for 30 days. On the contrary, the unmodified CNSs were obviously precipitated after 7 days. Thus, the dispersion of CNSs in the base lubricating oil was greatly improved.
3.7 Lubrication performance test of nano-lubricant
3.7.1 Effect of poly(ricinoleic acid) concentration on TMT lubrication performance. Table 1 shows the effect of the concentration of poly(ricinoleic acid) on the lubrication performance of TMT. Compared with the base lubricating oil, the kinematic viscosity and viscosity index of the lubricant had a little promotion with an increase in poly(ricinoleic acid) concentration, but this effect was very limited. However, the addition of poly(ricinoleic acid) had the opposite effect on the acid value and pour point of the base lubricating oil. This is due to the carboxyl groups in the structure of poly(ricinoleic acid) and its relatively high freezing point. When the content of poly(ricinoleic acid) was 0.5 wt%, the performance of the base oil was relatively less affected. The acid value of the base oil increased from 0.25 to 0.78, the kinematic viscosity (40) increased from 69.72 to 70.66, the kinematic viscosity (100) increased from 8.77 to 9.21, and the pour point increased from −45 °C to −43 °C. Therefore, the optimum dosage of poly(ricinoleic acid) was set at 0.5% (wt%).
Table 1 Effect of poly(ricinoleic acid) concentration on TMT lubrication performance
Property |
Concentration of poly(ricinoleic acid) in base lubricating oil (wt%) |
0 |
0.5 |
1.0 |
2 |
Acid value (mg KOH per g) |
0.25 |
0.78 |
1.00 |
1.53 |
Kinematic viscosity (40 °C, mm2 s−1) |
69.72 |
70.66 |
72.12 |
74.39 |
Kinematic viscosity (100 °C, mm2 s−1) |
8.77 |
9.21 |
9.39 |
9.66 |
Viscosity index |
101 |
106 |
107 |
109 |
Pour point (°C) |
−45 |
−43 |
−41 |
−39 |
3.7.2 Anti-wear property. The nano-lubricating oil was tested for its tribological behavior on a four-ball friction tester at a speed of 1200 rpm for 1 h. The test conditions were set as 75 °C under a load of 60 kgf. The test steel balls needed to be cleaned by anhydrous ethanol and petroleum ether to remove surface stains and oil samples before and after testing. Then test steel balls were used for SEM and EDS surface analysis. The friction behaviors of CNSs at different concentrations in TMT are shown in Fig. 7.
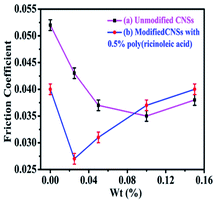 |
| Fig. 7 Anti-friction property tests. | |
In the absence of CNSs, the friction coefficient of the base lubricating oil with 0.5% (wt%) poly(ricinoleic acid) decreased from 0.052 to 0.040, which was reduced by 23.1% compared with that of the base lubricating oil. When the unmodified CNSs were present alone, the coefficient of friction dropped from 0.052 to 0.043, which was reduced by 17.3%, and the lowest friction coefficient of 0.035 was obtained with the concentration of 0.1 wt%, which was reduced by 32.7% compared with that of the base lubricating oil. For the composite anti-wear additive, the friction coefficient decreased rapidly during the early stage of the test, and the lowest friction coefficient of 0.027 was obtained with the concentration of 0.025 wt% modified CNSs and 0.5 wt% poly(ricinoleic acid). The friction coefficients were reduced nearly by 48.1% compared with that of the base lubricating oil. The composite anti-wear additive exhibited a better anti-wear effect than the unmodified CNSs acting alone, and the amount of modified CNSs used was less.
It is speculated that this phenomenon may be attributed to the adsorption capacity of poly(ricinoleic acid) on the metal surface and CNSs exhibited the effect of “ball bearing”, which could provide much easier shear, slide and roll between the two mating wear surfaces.25 Also, CNSs could easily fill into the mating wear surfaces during the wear process.26 In addition, the CNSs on the wear surface could serve as spacers to prevent rough contact between the wear surfaces.27 The experimental results show that the composite anti-wear additive could effectively improve the utilization of CNSs and significantly improve the wear resistance of the base lubricating oil.
Fig. 8 shows the morphologies of the worn surfaces lubricated by the base lubricating oil, base lubricating oil with 0.5 wt% poly(ricinoleic acid), 0.025 wt% unmodified CNSs, 0.025 wt% modified CNSs, and 0.5 wt% poly(ricinoleic acid) under the condition of 60 kgf to 1200 rpm for 60 min. Compared with the base lubricating oil (a), the worn surfaces of (d) were much smoother and smaller in size. The minimum AWSD varied from 897.1 to 770.0 μm at a concentration of 0.025 wt% modified CNS composite anti-wear additive, and the wear loss decreased by about 14.2%. It can be seen clearly in c3 and d3 that CNSs were embedded in the scratches, which play a role in decreasing the abrasion and repairing wear defects.28
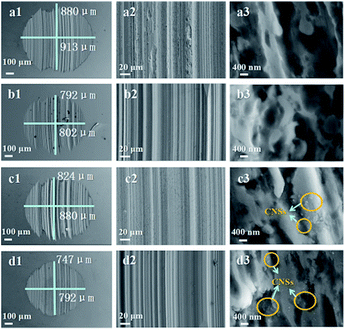 |
| Fig. 8 SEM images of wear scar. (a) Base lubricating oil, (b) base lubricating oil with 0.5 wt% poly(ricinoleic acid), (c) 0.025 wt% unmodified CNSs, and (d) 0.025 wt% modified CNS composite anti-wear additive. | |
EDS analysis was carried out to confirm the existence of CNSs on the friction surface, as shown in Fig. 9. Compared with the carbon element on the worn surface lubricated by the base lubricating oil, the carbon content on the friction surface of the nano-lubricating oil increased from 7.33% to 8.41%. The increase in the content of carbon was caused by the insertion of CNSs into the wear marks.
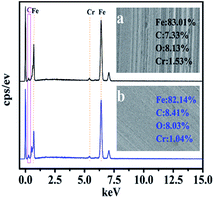 |
| Fig. 9 EDS analysis on the wear surface. (a) Lubricated with base lubricating oil and (b) lubricated with CNS composite anti-wear additive. | |
3.7.3 Dispersion stability behaviors. The main methods for testing the dispersion stability of nanoparticles in lubricating oil are the sedimentation method, spectrophotometry method, particle size analysis method and zeta potential method. The sedimentation method can truly reflect the dispersion stability of CNSs in liquid medium and the operation is simple. Therefore, the dispersion stability of CNSs in the base oil was measured using the sedimentation method in this experiment. The variation trend in the friction coefficient was used as an auxiliary means to test the dispersion stability of CNSs. The dispersion stability behaviors of the composite anti-wear additive was investigated over 3 months by comparison of its precipitation and variation in friction coefficient. The experiment results are exhibited in Fig. 10 and 11.
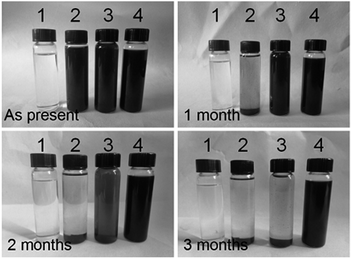 |
| Fig. 10 Images of dispersion stability test. (1) Base lubricating oil, (2) unmodified CNSs in base lubricating oil, (3) modified CNSs in base lubricating oil and (4) composite anti-wear additive in base lubricating oil. | |
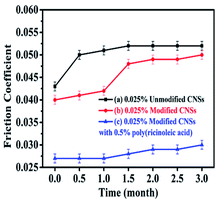 |
| Fig. 11 Analysis of the variation in friction coefficient with time. (a) 0.025 wt% unmodified CNSs, (b) 0.025 wt% modified CNSs and (c) 0.025 wt% modified CNS composite anti-wear additive. | |
Fig. 10 shows that the agglomeration of the unmodified CNSs occurred obviously in about 7 days and the unmodified CNSs were completely deposited at the bottom of the sample bottle after one month. The modified CNSs did not precipitate obviously in one month and maintained good dispersion stability in the base lubricating oil. However, precipitation began to occur within 2 months. The composite anti-wear additive could maintain no obvious precipitation phenomenon in the oil phase for 3 months.
Fig. 11 compares the friction coefficient curves of the unmodified CNSs, modified CNSs, and composite anti-wear additives as a function of time. The experimental results show that the wear resistance of the unmodified CNSs varied sharply after 0.5 month, and the friction coefficient increased from 0.043 to 0.050. The friction coefficient of the modified CNSs did not change significantly in the first 1 month, and it increased from 0.040 to 0.048 after 1.5 months. The composite anti-wear additive showed excellent stability in the anti-wear test within 3 months, where its friction coefficient only increased from 0.027 to 0.030. Thus, the experimental results prove that the composite anti-wear system was significantly optimized in both dispersion stability and anti-wear properties.
The mechanism of optimization the dispersion stability of CNSs can be attributed to the following aspects, as shown in Fig. 12.
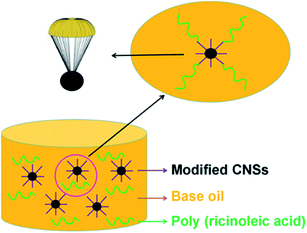 |
| Fig. 12 Mechanism of modified CNS dispersion stability behaviors. | |
(1) Oil-soluble long chain groups were grafted on the surface of the modified CNSs, which increased their dispersion stability.
(2) Poly(ricinoleic acid) itself is a commonly used surfactant, which can form a completely dispersed emulsion by reducing the surface tension of the oil phase, thereby significantly improving the dispersion stability of the CNSs in the base lubricating oil.
(3) The composite anti-wear additive can effectively optimize the amount of CNSs used and reduce the probability of sedimentation of CNSs due to agglomeration.
3.7.4 Effect of modified CNSs concentration on TMT lubrication performance. The effect of composite anti-wear additive concentration on the lubrication performance of the base lubricating oil is shown in Table 2. The experimental results show that there was no obvious relationship between CNS concentration and the acid value of the lubricating oil. This is due to the fact that the modified CNSs were neutral, and their addition amount was very small. Therefore, the results show that CNSs had no effect on the acid value of oil at a low concentration. The kinematic viscosity of the nano-lubricants had a decreasing trend with an increase in the concentration of CNSs. The lubricating oil is a typical Newtonian fluid, and thus there was internal friction between the flowing liquid layers; meanwhile, there was frictional resistance between the fluid and the tube wall.29 The addition of CNSs reduced the friction resistance of the base lubricating oil and tube wall through the effect of “ball bearing”, and the CNSs located between the oil layers caused the fluid layers to move fast.30,31 However, the addition of CNSs had no effect on the viscosity index of the base lubricating oil. There was no obvious relationship between pour point and the concentration of CNSs. Thus, the results indicate that CNSs had no effect on the pour point of the oil at a low concentration.
Table 2 Effect of modified CNS concentration on TMT lubrication performance
Property |
Content of modified CNSs in base lubricating oil |
0% |
0.025% |
0.05% |
0.1% |
Acid value (mg KOH per g) |
0.25 |
0.25 |
0.25 |
0.25 |
Kinematic viscosity (40 °C, mm2 s−1) |
70.66 |
70.36 |
70.31 |
69.17 |
Kinematic viscosity (100 °C, mm2 s−1) |
9.21 |
9.24 |
9.19 |
9.08 |
Viscosity index |
106 |
107 |
106 |
106 |
Pour point (°C) |
−43 |
−43 |
−43 |
−43 |
4 Conclusions
The method of modifying CNSs was proved to be feasible via FTIR spectroscopy, Raman spectroscopy, TG and XRD. The results showed that the composite anti-wear additive exhibited excellent friction-reduction and dispersion stability behaviors as a synthetic ester additive in the base lubricant. By adjusting the amount of CNSs and ricinoleic acid, different proportions of nanocomposite anti-wear additives could be obtained via a one-pot method. With the help of poly(ricinoleic acid), the modified CNSs could remain stable in TMT without obvious precipitation for more than 3 months. In addition, the composite additives could reduce the usage of CNSs and provided more efficient anti-wear properties for the base lubricating oil. The improvement in dispersion stability solves an important problem in the application of nanocarbon materials in the lubricant industry.
Author contributions
Conceptualization, Wumanjiang Eli and Shuzhe Guan; methodology, Shuzhe Guan and Xuanchi Liu; software, Xuanchi Liu; validation, Xuanchi Liu; formal analysis, Shuzhe Guan; investigation, Xuanchi Liu; resources, Shuzhe Guan; data curation, Shuzhe Guan and Xuanchi Liu; writing-original draft preparation, Shuzhe Guan; writing-review & editing, Shuzhe Guan; visualization, Wumanjiang Eli; supervision, Wumanjiang Eli; project administration, Shuzhe Guan; funding acquisition, Shuzhe Guan. All authors contributed substantially to the work reported.
Conflicts of interest
There are no conflicts of interest to declare.
Acknowledgements
The work was financially supported by Scientific Research Projects of Education Department of Xinjiang Uygur Autonomous Region (No. XJEDU-2020Y040). Xinjiang Tianshan Youth Talents Program (2020Q081). Doctoral research start-up fund of Xinjiang Institute of Engineering (No. 2020 xgy052302).
References
- S. Shahnazar, S. Bagheri and S. B. Abd Hamid, Int. J. Hydrogen Energy, 2016, 41(4), 3153–3170 CrossRef CAS.
- I. Braceras, I. Ibáñez and S. Dominguez-Meister, et al., Friction, 2020, 8(02), 235–245 CrossRef.
- L. Shuwei, Z. Chenhui and O. Eryilmaz, et al., Sci. China: Technol. Sci., 2016, 12(59), 5–13 Search PubMed.
- A. K. Sharma, et al., Friction, 2019, 97(02), 65–80 Search PubMed.
- S. Singh, X. Chen and C. Zhang, et al., J. Tribol., 2020, 142(12), 1–23 CrossRef.
- L. Cai, Z. Qi and J. Xu, et al., J. Chem., 2019, 1–9 Search PubMed.
- Z. Hu, X. Fan and C. Chen, Friction, 2020, 1–13 Search PubMed.
- C. Yang, X. Hou and Z. Li, et al., Appl. Surf. Sci., 2016, 388(part_A), 497–502 CrossRef CAS.
- A. Kayvani Fard, T. Rhadfi and G. McKay, et al., Chem. Eng. J., 2016, 293, 90–101 CrossRef CAS.
- B. Chen, S. Liang and S. Lu, et al., J. Tribol., 2019, 141(5), 052004 CrossRef CAS.
- B. Zareh-Desari and B. Davoodi, J. Cleaner Prod., 2016, 135, 1198–1209 CrossRef CAS.
- X. Wang, H. Sato and K. Adachi, Friction, 2021, 9(3), 598–611 CrossRef CAS.
- X. Sun, Y. Ding and B. Zhang, et al., Chem. Commun., 2015, 51(44), 9145–9148 RSC.
- H. Kumar and A. P. Harsha, J. Tribol., 2020, 142(8), 1–34 CrossRef.
- Y. Gu, J. Fei and X. Zheng, et al., Tribol. Int., 2021, 153, 106652 CrossRef CAS.
- Z. Mou, B. Zhao and B. Wang, et al., ACS Appl. Mater. Interfaces, 2021, 13(7), 8794–8807 CrossRef CAS PubMed.
- M. E. Makowiec and T. A. Blanchet, Wear, 2017, 374–375, 77–85 CrossRef CAS.
- G. Phalak, D. Patil and V. Vignesh, et al., Ind. Crops Prod., 2018, 119, 9–21 CrossRef CAS.
- Y. Wang, Z. Wan and L. Lu, et al., Tribol. Int., 2018, 124, 10–22 CrossRef CAS.
- S. Bhaumik, R. Maggirwar and S. Datta, et al., Appl. Surf. Sci., 2018, 449, 277–286 CrossRef CAS.
- P. Ghosh, M. Hoque and G. Karmakar, Polym. Bull., 2018, 75(2), 501–514 CrossRef CAS.
- Q. Shanhua, C. Xuliang and L. Liguo, et al., J. Tribol., 2016, 138(1), 014501–014505 CrossRef.
- J. Raisin, F. Nicolas and V. Philoppe, et al., Tribol. Int., 2019, 133(3), 136–151 CrossRef CAS.
- R. K. Singh, A. R. Dixit and A. K. Sharma, et al., Int. J. Surf. Sci. Eng., 2018, 12(3), 207–227 CrossRef CAS.
- S. K. Easwaran and P. Jawahar, J. Balk. Tribol. Assoc., 2018, 24(4), 700–717 CAS.
- A. Erdemir and J. M. Martin, Curr. Opin. Solid State Mater. Sci., 2018, 22(6), 243–254 CrossRef CAS.
- M. Hemmat Esfe, M. Afrand and S. H. Rostamian, et al., Exp. Therm. Fluid Sci., 2017, 80, 384–390 CrossRef CAS.
- A. Kumar, D. K. Chouhan and P. S. Alegaonkar, et al., Compos. Sci. Technol., 2016, 127, 79–87 CrossRef CAS.
- J. Wu, X. Huang and B. Kim, et al., Compos. Sci. Technol., 2018, 162, 86–92 CrossRef CAS.
- M. Ahmadi and M. H. Siadati, J. Alloys Compd., 2018, 769, 713–724 CrossRef CAS.
- A. Ponnuruthiyil Shaji, M. A. Shaik and B. R. Golla, J. Appl. Polym. Sci., 2019, 136(23), 136–149 CrossRef.
|
This journal is © The Royal Society of Chemistry 2021 |
Click here to see how this site uses Cookies. View our privacy policy here.