DOI:
10.1039/D1RA00789K
(Paper)
RSC Adv., 2021,
11, 14475-14483
Evaluation of BaCo0.4Fe0.4Zr0.2−xNixO3−δ perovskite cathode using nickel as a sintering aid for IT-SOFC
Received
29th January 2021
, Accepted 8th April 2021
First published on 16th April 2021
Abstract
In this research work, BaCo0.4Fe0.4Zr0.2−xNixO3−δ (x = 0, 0.01, 0.02, 0.03, 0.04) perovskite cathode material for IT-SOFC is synthesized successfully using a combustion method and sintered at low temperature. The effects of nickel as a sintering aid on the properties of BaCo0.4Fe0.4Zr0.2O3−δ are investigated through different characterization methods. The addition of nickel increased the densification and grain growth at a lower sintering temperature 1200 °C. XRD analysis confirms a single phase of BaCo0.4Fe0.4Zr0.2O3−δ, and an increase in crystalline size is observed. SEM micrographs show formation of dense microstructure with increased nickel concentration. TGA analysis revealed that BaCo0.4Fe0.4Zr0.2−xNix cathode materials are thermally stable within the SOFC temperature range, and negligible weight loss of 2.3% is observed. The bonds of hydroxyl groups and metal oxides are confirmed for all samples through FTIR analysis. The highest electrical properties are observed for BaCo0.4Fe0.4Zr0.2−xNix (x = 0.04) due to increased densification and electronic defects compared to other compositions. The maximum power density of 0.47 W cm−2 is obtained for a cell having cathode material BaCo0.4Fe0.4Zr0.2−xNix (x = 0.02) owing to its permeable and well-connected structure compared to others.
1 Introduction
In the last decade, rapid urbanization and industrialization along with population growth have led to an exponential increase in energy demand. Traditional energy resources like coal, gas, and petroleum are used to fulfill humankind's energy needs. The extensive use of these energy resources is not only creating a negative impact on the environment by the emission of harmful gases but also causing their depletion at a rapid pace.1,2 Researchers are devoting a lot of their efforts to develop highly efficient, cost-effective, and eco-environment-friendly alternative energy resources. Among different energy resources, fuel cells have the potential in fulfilling these requirements. The solid oxide fuel cell (SOFC), among other types, is mostly preferred owing to its elevated energy conversion efficiency, inherent simplicity, less noise, fuel diversity, and insignificant by-products.3,4 The drawback of SOFC is its high operating temperature which causes little chemical stability leading to high maintenance and production cost.5 High temperature also causes a thermal mismatch with other components. However, SOFC operating temperature significantly decreased (from 1000 °C to 400 °C) in the past decade, by developing new and innovative materials without affecting their conductivity. However, efforts are still needed to create materials that can further reduce its operating temperature.6–8
In SOFC, cathode must have adequate porosity and high electronic conductivity for better oxygen reduction reaction (ORR).9 At the cathode, the overall molecule used for the electrochemical reaction is O2 (diatomic species) and it converts into an electro-active ion through one or more processes, and this reaction typically occurs near the TPBs.10 Micro-pattern and composition of materials used for electrolyte and cathode can also influence the TPB aspects and distribution.11,12
Recently perovskite cathode materials gained significant importance due to their considerable oxide ion conductivity and excellent electronic conductivity, makes them mixed ionic-electronic conductors and have great significance as cathode material.13,14 Perovskite has the formula ABO3±δ, where δ indicates the excess or deficiency of the oxygen, and A-cation is a metal with charge +2 or +3 larger than B-cation having charge +4 or +3. The positive valances of A and B cations are six and exist as “A2+B4+O3, A1+B5+O3 or A3+B3+O3”. Electrical conductivity and electrocatalytic performance of perovskites cathode material can be enhanced by using dopants at A and B sites of the structure.15 In perovskite cathode materials, the A site is comprised of the rare and alkaline earth metals that is La, Ba, Ca, or Sr, while B site consists of transition metals such as Mn, Ni, Co, or Fe, etc. B-site cations, therefore, give the catalytic mechanism.16 Barium zirconate and barium cerate both have perovskite structures. Barium cerate as a perovskite material is preferred because of its high storage capacity of oxygen vacancies and high conductivity compared to barium zirconate.17
The perovskites cathode material doped with rare-earth elements like Sr, Ce, and Co, etc., have shown tremendous advantages over conventional cathodes.14 These cathode materials provide better matching thermo-mechanical performance with electrolytes and show mixed ionic and electronic conductivity.18,19 Therefore, perovskite-type MIECs having a composition of ABO3 are best for oxygen permeability because of their excellent ionic and electronic conductivity over a different range of temperature.20 Cobalt-based perovskite material is the most suitable material in the family of MIEC materials. The substitution in cobalt-based perovskite structure from A or B site helps obtain materials that have good structural stability and high oxygen permeability.
To use a sintering aid, it is crucial that dopant can increase the point defects, and it can also enhance the transportation of ions or electrons to promote sintering.21,22 Nickel is considered as to be fast diffuser and it enhances the sintering rate of the ceramic powders. It was also reported that during sintering the addition of nickel suppresses the coarsening process of grains to some extent.23 The substitution of nickel in BCFZ not only helps in reducing the sintering temperature but it also increases the oxygen concentration and permeability at an intermediate temperature which is favourable for the transportation of O2 ions in bulk electrode, therefore resulting into enhanced electrocatalytic performance. Furthermore, it also reduces the reactivity of the electrolyte with the cathode and lead to the excellent performance of the SOFC.24
In current work, nickel is used as a sintering aid in BCFZ to observe the effect of sintering aid on sintering temperature, crystal structure, surface morphology, grain size and shape, temperature effects, conductivity, and electrochemical performance. A series of BaCo0.4Fe0.4Zr0.2−xNixO3−δ (x = 0, 0.01, 0.02, 0.03, 0.04) perovskite cathode materials were synthesized through cost and time effective auto-combustion method.
2 Experimentation of samples
BaCo0.4Fe0.4Zr0.2−xNixO3−δ (x = 0, 0.01, 0.02, 0.03, 0.04) perovskite cathode materials were synthesized through auto-combustion method for IT-SOFC. The precursor materials used for the synthesis of BaCo0.4Fe0.4Zr0.2−xNixO3−δ were Ba (NO3)3 (Sigma Aldrich, > 98%), Co(NO3)2·6H2O (Sigma Aldrich, > 98%), Ni(NO3)·6H2O (Sigma Aldrich, > 98%), Zr(NO3)4·5H2O (Sigma Aldrich, > 98%) and Fe(NO3)2·9H2O (Sigma Aldrich, > 98%). The homogenous solution was prepared by adding a stoichiometric amount of these materials in de-ionized water under constant stirring and heating at 80 °C. Oxalic acid as a chelating agent was used for auto combustion. The obtained solution was then continuously stirred and heated at 120 °C until gel formation took place. The gel was then placed within the oven at 120 °C for auto ignition, and BaCo0.4Fe0.4Zr0.2−xNix cathode powder was obtained, which was sintered at 1200 °C for 4 hours. The fine powder was obtained through grinding. Pellets of BaCo0.4Fe0.4Zr0.2−xNixO3−δ powder were prepared by the hydraulic press at a pressure of 300 MPa.
Different characterization techniques were employed to observe the structural improvement of BCFZ perovskite cathode material cells using NiO as a sintering aid. XRD was used for structural analysis, and crystallite size was determined using the Scherer equation. The surface morphology of synthesized cathode materials was observed through SEM (HITACHI S-3000H). Weight loss was followed by thermo-gravimetric analysis (TGA Q500). FTIR analysis was used to investigate the functional groups and presence of metal oxide in the cathode material. Four probe DC methods were employed to determine the conductivities of the samples. The relation between conductivity and temperature was determined by the Arrhenius equation given by,25
|
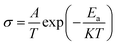 | (1) |
The electrochemical performance is evaluated by fabricating five anode supported button cells having configuration BaCo0.4Fe0.4Zr0.2−xNixO3−δ/SDC/Ni-SDC. The cathode slurry was printed on the SDC and was calcined at 1000 °C for 4 hours. Each button cell is prepared in the form circular disk with a diameter of 16 mm and thickness of 0.5 mm. The silver paste is used on both cathode and anode to collect current and is then treated at 500 °C for 1 hour. The humidified hydrogen (∼3% H2O) is provided at the anode as a fuel with a flow rate of 50 mL min−1, and at cathode, ambient air as an oxidant is used.
3 Result and discussion
3.1 Surface morphology
Fig. 1(a–e) shows the SEM micrographs of BaCo0.4Fe0.4Zr0.2−xNixO3−δ cathode materials. It is clear from the micrographs that BaCo0.4Fe0.4Zr0.2−xNixO3−δ structure becomes dense and less porous with increased content of nickel. Composition (x = 0) shows the least dense structure while composition (x = 0.04) shows the most dense structure. It can be deduced from SEM micrographs that pores reduced because nickel melted during sintering and diffused into the lattice of host Zr4+, and it also acted as a sintering aid due to its high surface energy.26 The increased concentration of Ni in BaCo0.4Fe0.4Zr0.2−xNixO3−δ also resulted into increased particle size and agglomeration which lead to further densification and grain growth.27,28 BaCo0.4Fe0.4Zr0.2−xNixO3−δ for (x = 0.01, 0.02) exhibit moderate porous structure and well-connected network along with increased TPB compared to other compositions, which is favorable for the enhanced electrochemical performance of cathode.29 It can also be deduced from these micrographs that microstructures of BaCo0.4Fe0.4Zr0.2−xNixO3−δ cathode materials became more compact and less permeable even at 1200 °C. Therefore, for these compositions, the sintering temperature can be further lowered to avoid agglomeration and to obtain porous and well-connected structures. The lowering of sintering temperature will make the synthesis process more cost-effective.30 The SEM analysis validates the fact that NiO played its role as a sintering aid and resulted in increased densification of BCFZ at much lower sintering temperatures.
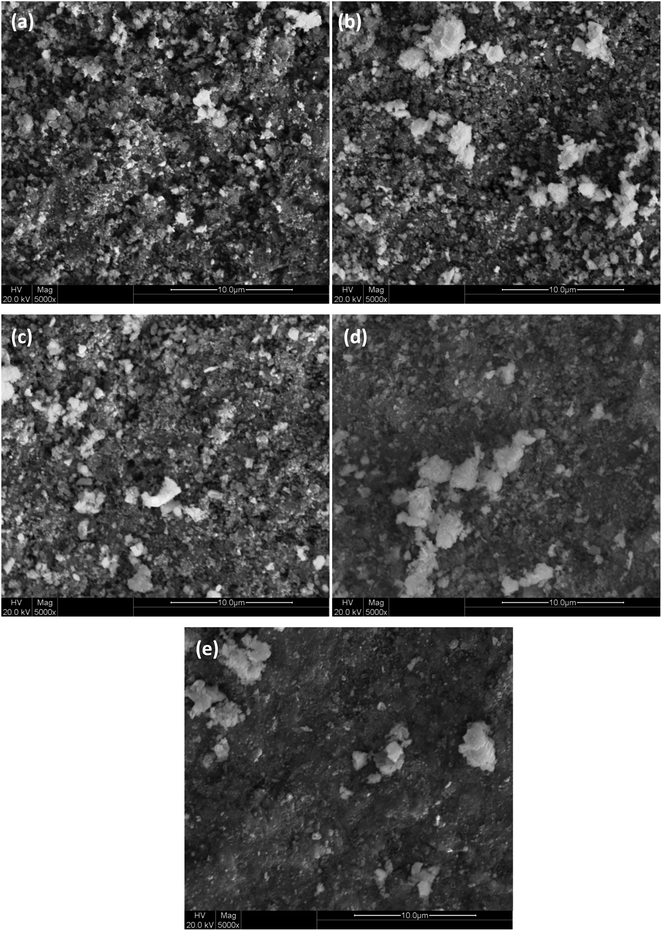 |
| Fig. 1 Surface morphology of BaCo0.4Fe0.4Zr0.2−xNixO3−δ, x = (a) 0, (b) 0.01, (c) 0.02, (d) 0.03 and (e) 0.04. | |
3.2 Structural study
Fig. 2 represents the XRD spectra of BaCo0.4Fe0.4Zr0.2−xNixO3−δ cathode materials within a 2θ range of 20°-70°. Single-phase perovskite planes (210), (111), (002), (110), (114), (400), (−322) and (003) are observed for all samples (JCPDS 75-0227, BCFZ). The sintering temperature is an important factor for the formation of perovskite phases because doped and undoped material shows the same crystal structure.31 The dominant phases before doping were monoclinic due to the zirconia, whereas doping of a small amount of nickel oxide suppressed the monoclinic structure and tetragonal phases get enhanced.32 Defect chemistry and the hydroxylation degree are the main aspects that dominate the properties of tetragonal structure of ZrO2. The phase change and stability of tetragonal phase is strongly dependent upon the dopant used. In the current work, the formation of the tetragonal phase depends upon the concentration of the nickel added. The small particle size of the nickel compared to the zirconia increases the reactivity and led to the stabilization of the tetragonal phase. The addition of nickel suppresses the monoclinic phases and enhances the tetragonal phase.33 It can be further deduced that after doping of nickel up to 4 mol%, the perovskite structure remains intact, which is also in agreement with the reported results. However, the secondary phase of BaO is observed for all samples while the NiO phase is observed for BaCo0.4Fe0.4Zr0.2−xNixO3−δ. The existence of BaO phase can be ascribed to low sintering temperature as researchers have reported that high sintering temperature can result in the volatilization of BaO.1
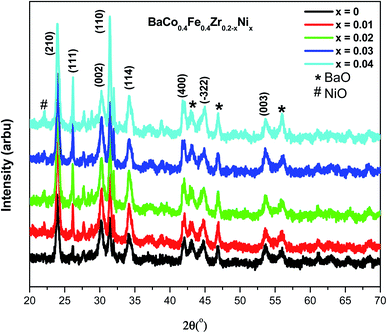 |
| Fig. 2 XRD spectra of BaCo0.4Fe0.4Zr0.2−xNixO3−δ. | |
It is also clear from the spectra that besides the NiO phase's appearance due to nickel, peak shifting also occurred for the samples doped with nickel. Fig. 3 represents the peak shifting of the (210) plane of BaCo0.4Fe0.4Zr0.2−xNixO3−δ. It can be observed that plane moved to a higher angle with an increased ratio of nickel. The increased concentration of nickel within BaCo0.4Fe0.4Zr0.2−xNixO3−δ disturbed the perovskite structure symmetry due to disparity in the ionic radii of host and dopant that resulted in peak shifting towards the higher angle.34 The shifting toward a higher angle can be ascribed to the small ionic radius of Ni2+ ions (1.62 Å) compared to Ba2+ (2.78 Å) and Zr4+ (2.16 Å) that resulted in the shrinkage of lattice parameter and led to a decreased unit cell.35
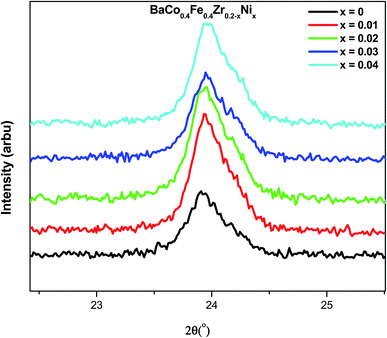 |
| Fig. 3 Magnified plane (210) peak BaCo0.4Fe0.4Zr0.2−xNixO3−δ. | |
XRD spectra further reveal that the intensity of peaks increased with the augmented concentration of nickel because nickel improved the sinterability of BaCo0.4Fe0.4Zr0.2−xNixO3−δ.36 When NiO doped at B-position in the perovskite structure, there is a reduction of oxygen vacancies which resulted in shrinkage of lattice and increased the intensity of the peaks.
The crystallite size was determined by the Debye–Scherrer formula.35
|
 | (2) |
Table 1 shows that crystallite size increased with increased concentration of nickel which can be attributed to an increase in grain growth and aggregation. The increased concentration of nickel resulted in increased nucleation of crystallites and enhanced grain growth. Earlier reported results also confirm the same behavior when nickel is used as sintering aid.37,38
Table 1 Crystalline Size of BaCo0.4Fe0.4Zr0.2−xNixO3−δ
Cathode materials (BaCo0.4Fe0.4Zr0.2−xNixO3−δ) |
x = 0 |
x = 0.01 |
x = 0.02 |
x = 0.03 |
x = 0.04 |
Crystallite size (nm) |
32 |
34 |
42 |
45 |
60 |
3.3 FTIR analysis
Fig. 4 shows the FTIR transmittance spectra of BaCo0.4Fe0.4Zr0.2−xNixO3−δ cathode material in a range of 4000–600 cm−1.
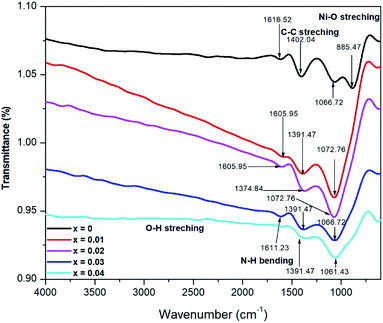 |
| Fig. 4 FTIR spectra of BaCo0.4Fe0.4Zr0.2−xNixO3−δ. | |
The peaks around 1600 cm−1 show N–H bindings due to the amines group, while peaks at 1400 cm−1 represent the C–C stretching in the rings due to aromatics compounds and water adsorption.39 These peaks get broader with increased concentration of nickel in BaCo0.4Fe0.4Zr0.2−xNixO3−δ. Peak shifting is also observed, which can be attributed to the shrinkage of lattice parameter, decreased unit cell volume, and trapping effects of charges between host Zr4+ and nickel dopant.40 The shifting of peaks can also be related to the structural disorder and stresses that are produced due to the difference in ionic radii dopant Ni and host Zr4+, therefore, resulting in displacement and tilting of zirconium oxide structure.41 Stability and structure disorder are inversely proportional to each other.42 Also due to this difference, the metal oxide bonds which change the internal motion of molecules, resulted in increased bond length for cathode materials.43,44
3.4 Thermal analysis
Fig. 5 shows the TGA plot of BaCo0.4Fe0.4Zr0.2xNxO3−δ in a range from room temperature to 850 °C. A minimal weight loss of about 2.3% is observed from 100 °C to 140 °C approximately. This weight loss is due to the evaporation of water present within the sample due to ambient moisture. No weight loss is observed beyond 140 °C because the thermal analysis is done after sintering; therefore, metal nitrates and residual compounds were already decomposed. It is also clear that no thermal process decomposition or evaporation occurred within the SOFC operating temperature range, which depicts that it is thermally stable for SOFC operating temperature.45
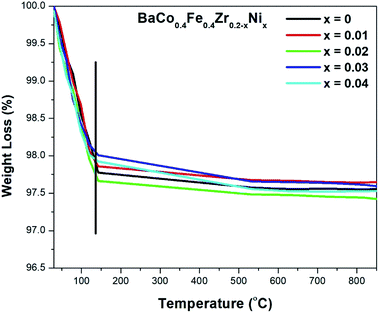 |
| Fig. 5 Thermogravimetric analysis (TGA) curves of BaCo0.4Fe0.4Zr0.2−xNixO3−δ. | |
3.5 Conductivity
Fig. 6 depicts the Arrhenius plot between ln
σT and 1/T for BaCo0.4Fe0.4Zr0.2−xNixO3−δ cathode material within the temperature range of 500–900 °C.
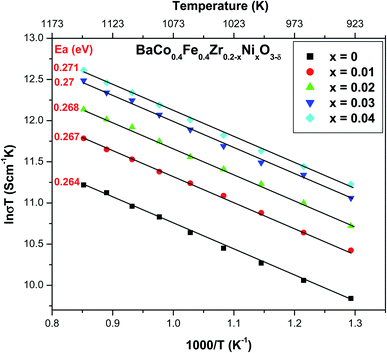 |
| Fig. 6 Arrhenius plot of BaCo0.4Fe0.4Zr0.2−xNixO3−δ. | |
It can be observed from the figure that electronic conductivity increased with the increased concentration of NiO. When NiO doped by decreasing the zirconium concentration, the ions of zirconium reduced in host BaCo0.4Fe0.4Zr0.2−xNixO3−δ, which produces distortion in the lattice of host materials.46
The materials' conductivity depends upon two parameters mobility of charge carriers and their concentration.47 Charge carriers mainly depend upon occupied and available sites. They are also dependent upon the energy gap and grain shape obtained after the sintering process.25 Porosity reduces, and grain size increases at higher sintering temperatures resulting in increased charge carriers' fraction.48,49 For metal oxide cathodes, there is molecular oxygen adsorption, and diffusion at the surface of the electrode, and oxygen ions transfer from TPB to electrolyte, and electronic conductivity increases at electrodes. Therefore, BaCo0.4Fe0.4Zr0.2−xNixO3−δ (x = 0.04) exhibited better conductivity compared to other compositions. The high concentration of nickel (x = 0.04) resulted in increased electronic defects and increased grain size, thus forcing the electron to transfer from one grain to another through conduction hopping.50 It can also be deduced that increased grain size leads to the oxygen permeation flux which caused the faster rate of diffusion of oxygen ions by grain boundaries thus enhancing the surface reaction rate. The activation energy for ranges from 0.26–0.27 eV which is comparable to the cathode materials sintered at higher temperature. The low activation energy makes BaCo0.4Fe0.4Zr0.2−xNixO3−δ cathode suitable for intermediate temperature SOFC. Moreover, activation energy is also linked directly to the grain growth.51 The obtained conductivity for the nickel BCFZ sintered at low temperature 1200 °C is much better than because nickel acted as sintering aid.
4 Electrochemical performance
The electrochemical performance of five button cells having configuration (BaCo0.4Fe0.4Zr0.2−xNixO3−δ/SDC/Ni-SDC) is evaluated at temperatures 600 °C, 500 °C and 400 °C. Fig. 7(a–c) gives the I–V and power density curves of button cells. It can be observed that the maximum power density of 0.47 W m−2 was observed for perovskite cathode material having nickel composition (x = 0.02) at 600 °C and OCV of 0.86 V. The power density observed for cells having cathode with concentration (x = 0, 0.01, 0.03, 0.04) were 0.29 W m−2, 0.31 W m−2, 0.40 W m−2 and 0.34 W m−2. The similar pattern is observed at 500 °C and 400 °C i.e. cells having cathode with nickel composition (x = 0.02) exhibited maximum power density while minimum power density is observed for composition (x = 0).
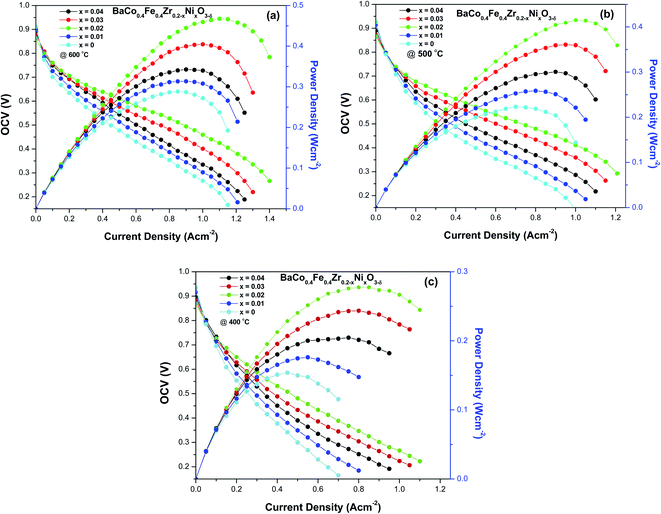 |
| Fig. 7 (a–c) Electrochemical performance of BaCo0.4Fe0.4Zr0.2−xNixO3−δ. | |
It was evident from SEM micrographs that cathode material with nickel concentration (x = 0.02) had moderate porosity and well-networked structure compared to other compositions therefore cell with a cathode having a nickel composition (x = 0.02) exhibit good performance compared to other cells. It can also be observed although cathode (x = 0.04) had the highest electronic conductivity compared to other compositions, but due to its dense structure, lesser gas diffusion occurred therefore reduced the oxygen reduction reaction at the cathode and decreasing its electrochemical performance.24 The obtained electrochemical performance confirms that BaCo0.4Fe0.4Zr0.2−xNixO3−δ (x = 0.02) perovskite cathode material is the best composition at low sintering temperature that can be used as suitable cathode material for application in IT-SOFCs.
Based on the better electrochemical performance of cell having composition (x = 0.02), its stability is observed for the 10 hour operation shown in Fig. 8. It can be observed that the cell has shown no apparent degradation with the passage of time at intermediate temperature. The addition of nickel as sintering in cathode will not have significant effect on degradation of cell performance because unlike anode where hydrocarbon is fed which significantly decreases the performance of cell due to carbon coking or sulphur poisoning, air or oxygen is fed at cathode.
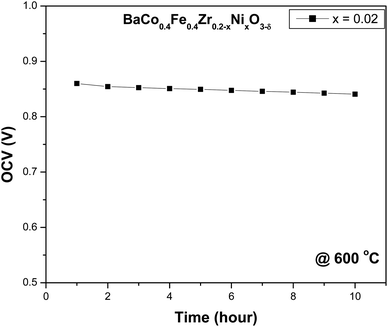 |
| Fig. 8 Stability of BaCo0.4Fe0.4Zr0.2−xNixO3−δ (x = 0.02) cell. | |
5 Conclusion
The BaCo0.4Fe0.4Zr0.2−xNix perovskite cathode material using nickel as sintering aid was successfully synthesized using a cost-effective auto combustion method. BaCo0.4Fe0.4Zr0.2−xNixO3−δ showed improved sinterability and conductivity at low sintering temperature (1200 °C) with nickel as a sintering aid. Morphological studies confirmed that densification steadily with increased content of nickel and BaCo0.4Fe0.4Zr0.2−xNixO3−δ (x = 0.04) exhibited denser structure compared to other compositions. From structural analysis, increased crystallite size was observed with increased concentration of nickel content and presence of a secondary phase of BaO was attributed to lower sintering. Thermal stability within the SOFC operating temperature range was observed for all compositions. The highest conductivity of BaCo0.4Fe0.4Zr0.2−xNixO3−δ (x = 0.04) was attributed to increased grain size and electronic defects that resulted in the enhanced surface reduction reaction. The peak power density of 0.47 W cm−2 was obtained for a cell having BaCo0.4Fe0.4Zr0.2−xNix (x = 0.02) cathode at 600 °C, due to its moderate porosity compared to other composition that led to better diffusion of gas and increased electrochemical reaction at the TPB. Therefore, BaCo0.4Fe0.4Zr0.2−xNixO3−δ perovskite cathode material with the composition (x = 0.02) sintered at a sintering temperature of 1200 °C can be a promising candidate for IT-SOFC.
Conflicts of interest
There are no conflicts to declare.
Acknowledgements
We would like to acknowledge Laser and Optronics Center (Department of Physics), UET, Lahore, Pakistan for their support.
References
- M. Irshad, et al., Evaluation of BaZr0.8X0.2 (X = Y, Gd, Sm) proton conducting electrolytes sintered at low temperature for IT-SOFC synthesized by cost effective combustion method, J. Alloys Compd., 2020, 815, 152389 CrossRef CAS.
- M. Benamira, L. Thommy, F. Moser, O. Joubert and M. T. Caldes, New anode materials for IT-SOFC derived from the electrolyte BaIn0.3Ti0.7O2.85 by lanthanum and manganese doping, Solid State Ionics, 2014, 265, 38–45 CrossRef CAS.
- M. Irshad, et al., Electrochemical evaluation of mixed ionic electronic perovskite cathode LaNi1−xCoxO3−δ for IT-SOFC synthesized by high temperature decomposition, Int. J. Hydrogen Energy, 2021, 46(17), 10448–10456 CrossRef CAS.
- M. Benamira, et al., Structural and Electrical Properties of Gadolinia-doped Ceria Mixed with Alkali Earth Carbonates for SOFC Applications, ECS Trans., 2019, 7(1), 2261–2268 CrossRef.
- M. Irshad, et al., Evaluation of densification effects on the properties of 8 mol% yttria stabilized zirconia electrolyte synthesized by cost effective coprecipitation route, Ceram. Int., 2021, 47(2), 2857–2863 CrossRef CAS.
- D. K. Niakolas, M. Daletou, S. G. Neophytides and C. G. Vayenas, Fuel cells are a commercially viable alternative for the production of ‘clean’ energy, Ambio, 2016, 45(1), 32–37 CrossRef PubMed.
- M. Irshad, et al., A Brief Description of High Temperature Solid Oxide Fuel Cell's Operation, Materials, Design, Fabrication Technologies and Performance, Appl. Sci., Mar. 2016, 6(3), 75 Search PubMed.
- M. Benamira, et al., Enhancing oxygen reduction reaction of YSZ/La2NiO4+δ using an ultrathin La2NiO4+δ interfacial layer, J. Alloys Compd., 2018, 746, 413–420 CrossRef CAS.
- F. Ramadhani, M. A. Hussain, H. Mokhlis and S. Hajimolana, Optimization strategies for Solid Oxide Fuel Cell (SOFC) application: A literature survey, Renewable Sustainable Energy Rev., 2017, 76, 460–484 CrossRef.
- A. M. Abdalla, et al., Nanomaterials for solid oxide fuel cells: A review, Renewable Sustainable Energy Rev., 2018, 82, 353–368 CrossRef CAS.
- L. Yang, Z. Liu, S. Wang, Y. Choi, C. Zuo and M. Liu, A mixed proton, oxygen ion, and electron conducting cathode for SOFCs based on oxide proton conductors, J. Power Sources, 2010, 195(2), 471–474 CrossRef CAS.
- A. Endo, Cathodic reaction mechanism of dense La0.6Sr0.4CoO3 and La0.81Sr0.09MnO3 electrodes for solid oxide fuel cells, Solid State Ionics, 2000, 135(1–4), 353–358 CrossRef CAS.
- S. Imashuku, T. Uda, Y. Nose, G. Taniguchi, Y. Ito and Y. Awakura, Dependence of Dopant Cations on Microstructure and Proton Conductivity of Barium Zirconate, J. Electrochem. Soc., 2009, 156(1), B1 CrossRef CAS.
- J. Sunarso, S. S. Hashim, N. Zhu and W. Zhou, Perovskite oxides applications in high temperature oxygen separation, solid oxide fuel cell and membrane reactor: a review, Prog. Energy Combust. Sci., 2017, 61, 57–77 CrossRef.
- M. Burriel, G. Garcia, J. Santiso, J. A. Kilner, R. J. Chater and S. J. Skinner, Anisotropic oxygen diffusion properties in epitaxial thin films of La2NiO4+δ, J. Mater. Chem., 2008, 18(4), 416–422 RSC.
- G. J. la O, R. F. Savinell and Y. Shao-Horn, Activity Enhancement of Dense Strontium-Doped Lanthanum Manganite Thin Films under Cathodic Polarization: A Combined AES and XPS Study, J. Electrochem. Soc., 2009, 156(6), B771 CrossRef CAS.
- N. Mahato, A. Banerjee, A. Gupta, S. Omar and K. Balani, Progress in material selection for solid oxide fuel cell technology: A review, Prog. Mater. Sci., 2015, 72, 141–337 CrossRef CAS.
- K.-Y. Park, Y. Seo, K. B. Kim, S.-J. Song, B. Park and J.-Y. Park, Enhanced proton conductivity of yttrium-doped barium zirconate with sinterability in protonic ceramic fuel cells, J. Alloys Compd., 2015, 639, 435–444 CrossRef CAS.
- A. Weber and E. Ivers-Tiffée, Materials and concepts for solid oxide fuel cells (SOFCs) in stationary and mobile
applications, J. Power Sources, 2004, 127(1–2), 273–283 CrossRef CAS.
- N. Laosiripojana, W. Wiyaratn, W. Kiatkittipong, A. Arpornwichanop, A. Soottitantawat and S. Assabumrungrat, Reviews on Solid Oxide Fuel Cell Technology, Eng. J., Feb. 2009, 13(1), 65–84 Search PubMed.
- S. Hossain, et al., Highly dense and chemically stable proton conducting electrolyte sintered at 1200 °C, Int. J. Hydrogen Energy, 2018, 43(2), 894–907 CrossRef CAS.
- C. Sun, R. Hui and J. Roller, Cathode materials for solid oxide fuel cells: a review, J. Solid State Electrochem., 2010, 14(7), 1125–1144 CrossRef CAS.
- B. B. Panigrahi, N. S. Reddy, A. Balakrishnan, M. C. Chu, S. J. Cho and J. J. Gracio, Nickel assisted sintering of Ti3SiC2 powder under pressureless conditions, J. Alloys Compd., 2010, 505(1), 337–342 CrossRef CAS.
- T. Kida, A. Yamasaki, K. Watanabe, N. Yamazoe and K. Shimanoe, Oxygen-permeable membranes based on partially B-site substituted BaFe1−yMyO3−δ (M = Cu or Ni), J. Solid State Chem., 2010, 183(10), 2426–2431 CrossRef CAS.
- B. Wang, L. Bi and X. S. Zhao, Exploring the role of NiO as a sintering aid in BaZr0.1Ce0.7Y0.2O3−δ electrolyte for proton-conducting solid oxide fuel cells, J. Power Sources, 2018, 399, 207–214 CrossRef CAS.
- Y.-L. Huang, A. M. Hussain, C. Pellegrinelli, C. Xiong and E. D. Wachsman, Chromium Poisoning Effects on Surface Exchange Kinetics of La0.6Sr0.4Co0.2Fe0.8O3−δ, ACS Appl. Mater. Interfaces, 2017, 9(19), 16660–16668 CrossRef CAS PubMed.
- E. Omari, S. Makhloufi and M. Omari, Preparation by Sol–Gel Method and Characterization of Co-doped LaNiO3 Perovskite, J. Inorg. Organomet. Polym. Mater., 2017, 27(5), 1466–1472 CrossRef CAS.
- J. S. A. Carneiro, R. A. Brocca, M. L. R. S. Lucena and E. Nikolla, Optimizing cathode materials for intermediate-temperature solid oxide fuel cells (SOFCs): Oxygen reduction on nanostructured lanthanum nickelate oxides, Appl. Catal., B, 2017, 200, 106–113 CrossRef CAS.
- B. Babu, C. V. Reddy, J. Shim, R. V. S. S. N. Ravikumar and J. Park, Effect of cobalt concentration on morphology of Co-doped SnO2 nanostructures synthesized by solution combustion method, J. Mater. Sci.: Mater. Electron., 2016, 27(5), 5197–5203 CrossRef CAS.
- J. R. Smith, et al., Evaluation of the relationship between cathode microstructure and electrochemical behavior for SOFCs, Solid State Ionics, 2009, 180(1), 90–98 CrossRef CAS.
- X. Lu, Y. Ding and Y. Chen, Ba0.5Sr0.5Zn0.2Fe0.8O3−δ–BaCe0.5Zr0.3Y0.16Zn0.04O3−δ composite cathode for proton-conducting solid oxide fuel cells, J. Alloys Compd., 2009, 484(1–2), 856–859 CrossRef CAS.
- Y. Yamazaki, R. Hernandez-Sanchez and S. M. Haile, High Total Proton Conductivity in Large-Grained Yttrium-Doped Barium Zirconate, Chem. Mater., 2009, 21(13), 2755–2762 CrossRef CAS.
- M. Mamivand, M. A. Zaeem, H. El Kadiri and L. Q. Chen, Phase field modeling of the tetragonal-to-monoclinic phase transformation in zirconia, Acta Mater., 2013, 61(14), 5223–5235 CrossRef CAS.
- F. Shen and K. Lu, Perovskite-type La0.6Sr0.4Co0.2Fe0.8O3, Ba0.5Sr0.5Co0.2Fe0.8O3, and Sm0.5Sr0.5Co0.2Fe0.8O3 cathode materials and their chromium poisoning for solid oxide fuel cells, Electrochim. Acta, 2016, 211, 445–452 CrossRef CAS.
- L. Gao, et al., Antimony-doped Bi0.5Sr0.5FeO3−δ as a novel Fe-based oxygen reduction electrocatalyst for solid oxide fuel cells below 600 °C, J. Mater. Chem. A, 2018, 6(31), 15221–15229 RSC.
- F. Liang, Z. Wang, Z. Wang, J. Mao and J. Sunarso, Electrochemical Performance of Cobalt-Free Nb and Ta Co-Doped Perovskite Cathodes for Intermediate-Temperature Solid Oxide Fuel Cells, ChemElectroChem, 2017, 4(9), 2366–2372 CrossRef CAS.
- L. Gao, M. Zhu, T. Xia, Q. Li, T. Li and H. Zhao, Ni-doped BaFeO3− perovskite oxide as highly active cathode electrocatalyst for intermediate-temperature solid oxide fuel cells, Electrochim. Acta, 2018, 289, 428–436 CrossRef CAS.
- Y. Xia, et al., A novel cobalt-free cathode with triple-conduction for proton-conducting solid oxide fuel cells with unprecedented performance, J. Mater. Chem. A, 2019, 7(27), 16136–16148 RSC.
- M. Qian and G. B. Schaffer, Sintering of aluminium and its alloys, in Sintering of Advanced Materials, Elsevier, 2010, pp. 291–323 Search PubMed.
- X. Jiang, F. Wu and H. Wang, Yb-Doped BaCeO3 and Its Composite Electrolyte for Intermediate-Temperature Solid Oxide Fuel Cells, Materials, 2019, 12(5), 739 CrossRef CAS PubMed.
- N. Madoui and M. Omari, Synthesis and Electrochemical Properties of LaCr1−xCoxO3 (0 ≤ x ≤ 0.5) via Co-precipitation Method, J. Inorg. Organomet. Polym. Mater., 2016, 26(5), 1005–1013 CrossRef CAS.
- S. M. de Lima and J. M. Assaf, Synthesis and Characterization of LaNiO3, LaNi(1−x)FexO3 and LaNi(1−x)CoxO3 Perovskite Oxides for Catalysis Application, Mater. Res., 2002, 5(3), 329–335 CrossRef CAS.
- S. Tao and J. T. S. Irvine, Conductivity studies of dense yttrium-doped BaZrO3 sintered at 1325 °C, J. Solid State Chem., 2007, 180(12), 3493–3503 CrossRef CAS.
- E. Gilardi, et al., Effect of Dopant–Host Ionic Radii Mismatch on Acceptor-Doped Barium Zirconate Microstructure and Proton Conductivity, J. Phys. Chem. C, 2017, 121(18), 9739–9747 CrossRef CAS.
- A. A. Shah, S. Ahmad and A. Azam, Investigation of structural, optical, dielectric and magnetic properties of LaNiO3 and LaNi1−xMxO3 (M = Fe, Cr & Co; x = 5%) nanoparticles, J. Magn. Magn. Mater., 2020, 494, 165812 CrossRef CAS.
- Y.-P. Fu, H.-C. Wang and J. Ouyang, Electrical conduction behaviors and mechanical properties of Cu doping on B-site of (La0.8Ca0.2)(Cr0.9Co0.1)O3−δ interconnect materials for SOFCs, Int. J. Hydrogen Energy, 2011, 36(20), 13073–13082 CrossRef CAS.
- C. Nityanand, W. B. Nalin, B. S. Rajkumar and C. M. Chandra, Synthesis and physicochemical characterization of nanocrystalline cobalt doped lanthanum strontium ferrite, Solid State Sci., 2011, 13(5), 1022–1030 CrossRef CAS.
- R. V. Wandekar, B. N. Wani and S. R. Bharadwaj, Crystal structure, electrical conductivity, thermal expansion and compatibility studies of Co-substituted lanthanum strontium manganite system, Solid State Sci., 2009, 11(1), 240–250 CrossRef CAS.
- Z. Wang, et al., A high performance cathode for proton conducting solid oxide fuel cells, J. Mater. Chem. A, 2015, 3(16), 8405–8412 RSC.
- M. A. Siddiqui, V. S. Chandel, M. Shariq and A. Azam, Dielectric and spectroscopic analysis of cobalt doped potassium hexatitanate (K2Ti6O13) ceramics, Mater. Sci., 2013, 31(4), 555–560 CAS.
- M. Shang, J. Tong and R. O'Hayre, A promising cathode for intermediate temperature protonic ceramic fuel cells: BaCo0.4Fe0.4Zr0.2O3−δ, RSC Adv., 2013, 3(36), 15769 RSC.
|
This journal is © The Royal Society of Chemistry 2021 |
Click here to see how this site uses Cookies. View our privacy policy here.