DOI:
10.1039/D0RA10528G
(Paper)
RSC Adv., 2021,
11, 7502-7510
Organic/inorganic double solutions for magnesium–air batteries
Received
15th December 2020
, Accepted 2nd February 2021
First published on 15th February 2021
Abstract
In order to limit the anode corrosion and improve the battery activity, magnesium–air batteries with organic/inorganic double solutions (0.5 M Mg(ClO4)2–N,N-dimethylformamide (DMF)/0.6 M NaCl–H2O, 0.5 M Mg(ClO4)2–acetonitrile (AN)/0.6 M NaCl–H2O) were prepared. The discharge performance, discharge morphology, and corrosion performance of magnesium anode were researched. Results obtained show that organic electrolytes separate the anode from the aqueous electrolyte, thus improving the anode utilization rate. Due to the NaCl electrolyte used in the air cathode side, batteries show higher discharge voltages. As an example, a better discharge performance has been observed in Mg(ClO4)2–DMF/NaCl–H2O double electrolytes at 1 mA cm−2 discharge. This is attributed to there being no obvious absorption of corrosion products on the anode surface. The results of the discharge morphology and electrochemical impedance spectroscopy agree well with the discharge performance. The magnesium anode discharge mechanism is different for different solutions.
1 Introduction
Mechanically rechargeable magnesium–air batteries have a high theoretical energy density (3910 W h kg−1) and a high theoretical voltage (3.09 V). Magnesium–air batteries are inexpensive options for applications that require ultrahigh energy densities.1–3 There is a commercial concern in them as conversion devices, such as off-grid power supplies, long-range drones and electric vehicles.4,5 The batteries use oxygen in air as the cathode, and the magnesium anode serves as the only active component.6,7 When the magnesium anode is consumed, the battery continues to discharge by replacing the magnesium anode. Unfortunately, magnesium is a reactive metal and easy to corrode in aqueous solutions. This decreases the anode utilization rate. Magnesium may react with water (reaction (1)), and not produce any current for the circuit.8,9
Many papers have focused on reducing the anode corrosion by alloying the magnesium anode,4,10 and adding corrosion inhibitors in solution to passivate the magnesium surface.11–13 However, Mg2+ cannot penetrate the passivating surface film and corrosion products layer, which obviously inhibits the magnesium dissolution necessary for the magnesium–air battery discharge.14,15 In addition to alloying and adding corrosion inhibitors, another method is to use an organic electrolyte system.16,17 According to reports about magnesium corrosion in organic electrolytes,18–20 the potential of magnesium in dimethylformamide is 2.47 V versus Ag/Ag+.21 Further, people have investigated the behavior of the magnesium electrode in hexakis (methanol)–dinitrate complex electrolyte22 and basic electrochemical behavior of Mg2+/Mg couple in organic electrolytes.23,24
In this work, organic/inorganic double electrolytes were tested as an alternative method. The double electrolytes consist of an organic electrolyte and an inorganic aqueous electrolyte. The cathodic reaction takes place between the cathode and inorganic electrolyte for the air electrode (reaction (2)), whereas the anodic reaction proceeds between the magnesium electrode and organic electrolyte (reaction (3)). The organic electrolyte, which is immiscible with the inorganic electrolyte, has the function to separate the magnesium anode from the corrosive inorganic electrolyte.
|
Mg + 2H2O → Mg(OH)2 + H2
| (1) |
|
O2 + 2H2O + 4e− → 4OH−
| (2) |
In this paper, N,N-dimethylformamide (DMF: C3H7NO) and acetonitrile (AN: C2H3N) were selected as the organic solvents. They are good solvents for many substances.25,26 Inorganic salts are difficult to dissolve in organic solvents, but Mg(ClO4)2 is soluble in N,N-dimethylformamide and acetonitrile organic solvents.27 Therefore, Mg(ClO4)2 was selected as an ionophore to transport Mg2+. As the most common electrolyte for the magnesium–air battery, 0.6 M NaCl aqueous solution was used as a cathode electrolyte to keep the battery discharge activity. For the magnesium alloy, aluminum is the most important alloying element. The corrosion is affected strongly by the aluminum content and microstructure. Aluminum is a major alloying element that inhibits corrosion by forming a dense Al2O3 protective layer on the alloy surface.9 The aluminum element in the magnesium alloy can form a β-phase (Mg17Al12) if the aluminum content is more than a solid solubility in the α-Mg matrix (maximum solubility is 12.7 wt% at the eutectic temperature 437 °C). Song15 indicated that the β-phase can serve as an anode barrier to inhibit the corrosion expansion of the α-matrix. As a continuation of earlier research activities,7,28 Mg–6 wt% Al alloy was selected as the anode material.
Fig. 1a illustrates a schematic of a magnesium–air battery with organic/inorganic double solutions. In organic solution, ClO4− plays a charge carrier role. The transfer of Mg2+ is accomplished by ion pair ClO4− diffusion. ClO4− transports Mg2+ from the anode into the aqueous solution. In the NaCl aqueous solution, Mg2+ moves to the cathode and forms Mg(OH)2 coupled with OH−. Mg2+ migration forms a current. The structures of the organic reagents DMF and AN are presented in Fig. 1b.
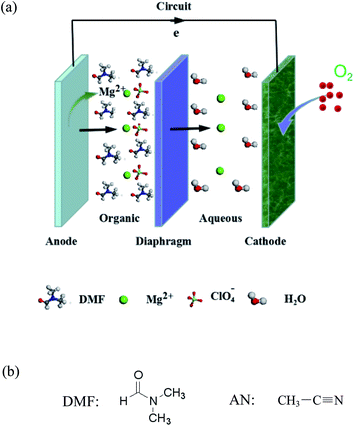 |
| Fig. 1 Schematic of the magnesium–air battery with organic/inorganic double electrolytes (a), and structures of N,N-dimethylformamide (DMF) and acetonitrile (AN) (b). | |
2 Experiments
2.1 Material preparation
Commercially pure magnesium and aluminum ingots (99.99%) were used to prepare the Mg–6 wt% Al alloy as the anode material. The ingots were melted under a mixed atmosphere of CO2 and SF6 in an induction furnace at 750 °C ± 5 °C. After continuous stirring for 5 min, the molten alloy was poured into a preheated cast iron mold. The actual composition of the alloy was determined by direct reading spectrometry (GS1000, Germany). It contains 5.96 wt% Al, 0.001 wt% Mn, 0.002 wt% Fe, and the rest was Mg. DMF, AN, NaCl, and Mg(ClO4)2 of analytical grade were purchased from Aladdin. NaCl had no further treatment before its utilization. DMF, AN, and Mg(ClO4)2 were dried 24 h before use. All weighing and preparation of 0.5 M Mg(ClO4)2–DMF and 0.5 M Mg(ClO4)2–AN organic electrolytes were carried out in glove boxes under a highly pure argon atmosphere.
2.2 Electrochemical test
The electrochemical property was tested by a CHI660E equipment with a three-electrode system. The sample of the Mg–6 wt% Al alloy was the working electrode with an exposed area of 1 cm2. The saturated calomel electrode (SCE) and graphite rod were used as the reference electrode and counter electrode, respectively. Test solutions included 0.6 M NaCl aqueous electrolyte, 0.5 M Mg(ClO4)2–DMF, and 0.5 M Mg(ClO4)2–AN organic electrolytes. Electrochemical impedance spectroscopy (EIS) was conducted with a 5 mV sine perturbation from 100 kHz to 0.1 Hz after the working electrode was stable for 1000 s in solution. Potentiodynamic polarization was measured at a scan rate of 1 mV s−1 after the sample was stable for 1000 s in the electrolyte. Additionally, the ionic conductivity of different solutions was investigated by the FE38 standard conductivity gauge (Mettler Toledo Instruments Co. Ltd., Switzerland).
2.3 Corrosion test
For the corrosion test, samples of dimension ø 11.3 mm × 5.0 mm were immersed in electrolytes for 5 h. The corrosion products were cleaned out in a solution (200 g L−1 CrO3 + 10 g L−1 AgNO3) at 80 °C for 5 min. Weight measurements were made before and after the immersion test to determine the corrosion rate, which is calculated using the following formula: |
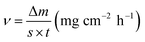 | (4) |
Here, v is the corrosion rate (mg cm−2 h−1); Δm is the weight loss (mg); s is the sample surface area (cm2); and t is the immersion time (h).
2.4 Cell assembly and discharge test
Magnesium–air cells with a single electrolyte and organic/inorganic double electrolytes were assembled. Single electrolytes included 0.6 M NaCl aqueous solution, 0.5 M Mg(ClO4)2–DMF organic solution, and 0.5 M Mg(ClO4)2–AN organic solution. The organic/inorganic double electrolytes were 0.5 M Mg(ClO4)2–DMF/0.6 M NaCl–H2O and 0.5 M Mg(ClO4)2–AN/0.6 M NaCl–H2O. A 20 μm thick hydrophilic treated polypropylene (PP) membrane with a pore diameter <0.1 μm was used as the diaphragm. Polypropylene (PP) as the diaphragm has good alkali resistibility, chemical stability, and high air permeability.29,30 The Mg–6 wt% Al sample with an exposed area of 1 cm2 acted as the anode. The commercial air cathode with the MnO2 catalyst was purchased (Changzhou Youteke New Energy Science and Technology, LTD, China). It also had an exposed area of 1 cm2. Magnesium–air cells were discharged at constant currents of 0.5 mA cm−2, 1 mA cm−2, and 2 mA cm−2 for 120 min using a LAND-CT2001A system at room temperature (25 °C ± 5 °C). The anode discharge morphologies before and after cleaning discharge products were analyzed using scanning electron microscopy (SEM
:
JSM-5610LV) with energy-dispersive X-ray spectroscopy (EDS). The discharge products were cleaned out with a solution of 200 g L−1 CrO3 and 10 g L−1 AgNO3 at 80 °C for 5 min. The anode weights before and after discharge were measured to calculate the anode utilization rate according to the formulas (5) and (6): |
 | (5) |
Here, η is the anode utilization rate (%), W is the theoretical mass loss, and W0 is the actual mass loss.
|
 | (6) |
Here, Q is the actual current capacity, Q = 2 h × (0.5, 1, 2) mA, and Q0 is the theoretical current capacity (A h kg−1), Q0 = 2219 A h kg−1 × 0.94 + 2980 A h kg−1 × 0.06 = 2265 A h kg−1.
The anode energy density was calculated using the formula (7):
|
 | (7) |
Here,
E is the energy density (W h kg
−1),
U is the average operating voltage (V),
I is the discharge current density (A cm
−2),
t is the discharge time (h), and
W0 is the actual mass loss (kg).
All of these experiments were repeated at least three times to gauge their reproducibility.
3 Results and discussion
3.1 Potentiodynamic polarization and corrosion
Fig. 2 exhibits the potentiodynamic polarization curves of Mg–6 wt% Al in 0.6 M NaCl electrolyte, 0.5 M Mg(ClO4)2–DMF electrolyte, and 0.5 M Mg(ClO4)2–AN electrolyte. The corresponding corrosion parameters are listed in Table 1. The anodic branch does not exhibit Tafel characteristics, and is not as steep as the cathodic branch in Fig. 2. The anodic polarization curves are complicated. Consequently, the Tafel extrapolation for the exchange current density (jcorr) calculation can be extrapolated from the cathodic branch to the corrosion potential of the polarization curve.31 It can be seen that the alloy shows a lower corrosion rate, a lower exchange current density (jcorr), a higher polarization resistance (Rp), and a more positive corrosion potential (Ecorr) in 0.5 M Mg(ClO4)2–DMF electrolyte and 0.5 M Mg(ClO4)2–AN electrolyte than in 0.6 M NaCl electrolyte. This indicates that the organic electrolytes can largely decrease the corrosion rate of the alloy, but the alloy becomes slightly less electrochemically active.
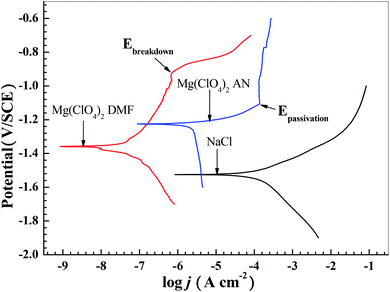 |
| Fig. 2 Polarization curves of the Mg–6 wt% Al alloy in 0.6 M NaCl solution, 0.5 M Mg(ClO4)2–DMF solution, and 0.5 M Mg(ClO4)2–AN solution. | |
Table 1 Corrosion parameters of Mg–6 wt% Al alloy in 0.6 M NaCl solution, 0.5 M Mg(ClO4)2–DMF solution, and 0.5 M Mg(ClO4)2–AN solution
Solutions |
Ecorr/V vs. SCE |
jcorr/mA cm−2 |
Rp/Ω cm2 |
Corrosion rate/mg cm−2 h−1 |
Conductivity rate/ms cm−1 |
NaCl–H2O |
−1.525 |
7.55 × 10−3 |
2.28 × 102 |
0.73 |
51.8 |
Mg(ClO4)2–DMF |
−1.358 |
1.37 × 10−6 |
6.63 × 105 |
0.03 |
21.3 |
Mg(ClO4)2–AN |
−1.225 |
5.11 × 10−6 |
5.48 × 104 |
0.05 |
17.6 |
In contrast to the polarization curves of the alloy in two organic electrolytes, Ecorr of the alloy in Mg(ClO4)2–DMF electrolyte is more negative than in the Mg(ClO4)2–AN electrolyte, showing that the alloy in the Mg(ClO4)2–DMF electrolyte possesses a higher activity than in the Mg(ClO4)2–AN electrolyte. The Jcorr of the alloy in the Mg(ClO4)2–DMF electrolyte is lower than in the Mg(ClO4)2–AN electrolyte, manifesting that the alloy in the Mg(ClO4)2–DMF electrolyte possesses a lower corrosion rate than in the Mg(ClO4)2–AN electrolyte. This agrees with the corrosion rate and polarization resistance Rp in Table 1.
3.2 Battery discharge
Fig. 3 exhibits the discharge curves of the magnesium–air batteries in a single electrolyte and organic/inorganic double electrolytes at 0.5 mA cm−2, 1 mA cm−2 and 2 mA cm−2. Table 2 presents the discharge parameters of these batteries. Fig. 3a shows the discharge curves at 1 mA cm−2 in single electrolytes, including NaCl–H2O, Mg(ClO4)2–DMF, and Mg(ClO4)2–AN electrolytes. The cell average voltage in the NaCl electrolyte is higher than that in organic electrolytes due to the lower conductivity rates of the organic electrolytes (Table 1). The cell voltage drops with increasing discharge time in organic electrolytes. This may be a result of the formation of the adsorption layer on the alloy surface.32 The anodic utilization rate in the NaCl electrolyte is lower than in both organic electrolytes (Table 2). This is because the alloy violently reacts with water in the NaCl aqueous electrolyte according to reaction (1), producing a large amount of hydrogen. The portion of the alloy consumed in the hydrogen evolution reaction does not proceed to an electricity-producing reaction for the circuit. The Cl− ions can penetrate the protective Mg(OH)2 film on the alloy electrode surface, and thus promotes corrosion.31,33 Adopting the Mg(ClO4)2–DMF electrolyte and Mg(ClO4)2–AN electrolyte results in a higher anodic utilization rate compared with using the NaCl electrolyte. This might be attributed to the DMF and AN anions adsorbing the anode surface, and there being no water molecules attacking the anode. Using Mg(ClO4)2–DMF and Mg(ClO4)2–AN as electrolytes led to higher anodic utilization rates of 85% and 79%, indicating that DMF and AN have an effect of suppressing the corrosion of the magnesium anode. In general, the lower the ionic conductivity rate, the higher the polarization resistance, as can be seen from Table 1. The higher polarization resistance will lead to a strong corrosion resistance, so the anode has a higher utilization rate. The anode utilization rates in organic solutions are higher than in NaCl–H2O solution.
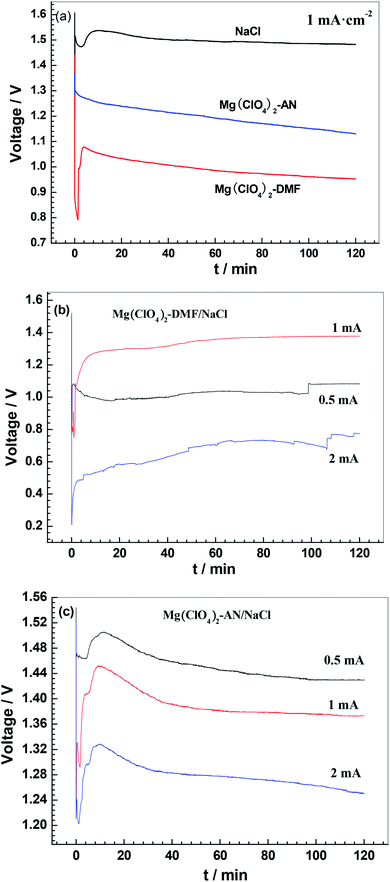 |
| Fig. 3 Discharge curves of the magnesium–air batteries: (a) in single solution at 1 mA cm−2, (b) in 0.5 M Mg(ClO4)2–DMF/0.6 M NaCl solutions at 0.5 mA cm−2, 1 mA cm−2 and 2 mA cm−2, (c) in 0.5 M Mg(ClO4)2–AN/0.6 M NaCl solutions at 0.5 mA cm−2, 1 mA cm−2 and 2 mA cm−2. | |
Table 2 Discharge performance of magnesium–air batteries in 0.6 M NaCl solution, 0.5 M Mg(ClO4)2–DMF/0.6 M NaCl solutions, and 0.5 M Mg(ClO4)2–AN/0.6 M NaCl solutions at 0.5 mA cm−2, 1 mA cm−2, and 2 mA cm−2
Solutions |
Discharge current/mA cm−2 |
Average operating voltage/V |
Anodic utilization/% |
Energy density/W h kg−1 |
Capacity density/mA h g−1 |
NaCl |
1 |
1.494 |
27 |
905 |
606 |
Mg(ClO4)2–DMF |
1 |
0.986 |
85 |
1933 |
1960 |
Mg(ClO4)2–AN |
1 |
1.192 |
79 |
1917 |
1606 |
Mg(ClO4)2–DMF/NaCl |
0.5 |
1.036 |
51 |
1070 |
1033 |
Mg(ClO4)2–DMF/NaCl |
1 |
1.358 |
76 |
1950 |
1436 |
Mg(ClO4)2–DMF/NaCl |
2 |
0.700 |
80 |
1799 |
2570 |
Mg(ClO4)2–AN/NaCl |
0.5 |
1.445 |
47 |
1103 |
763 |
Mg(ClO4)2–AN/NaCl |
1 |
1.381 |
52 |
1463 |
1059 |
Mg(ClO4)2–AN/NaCl |
2 |
1.278 |
73 |
1803 |
1411 |
However, hydrogen evolution caused by the reaction between the magnesium anode and water is not the only reason for the decreased anodic utilization rate. Another reason is that galvanic corrosion between the magnesium matrix and the second phase leads to the dissolution of the magnesium matrix,34 as shown in Fig. 4d and f. Therefore, in both organic electrolytes, the anode utilization rates are lower than 100%.
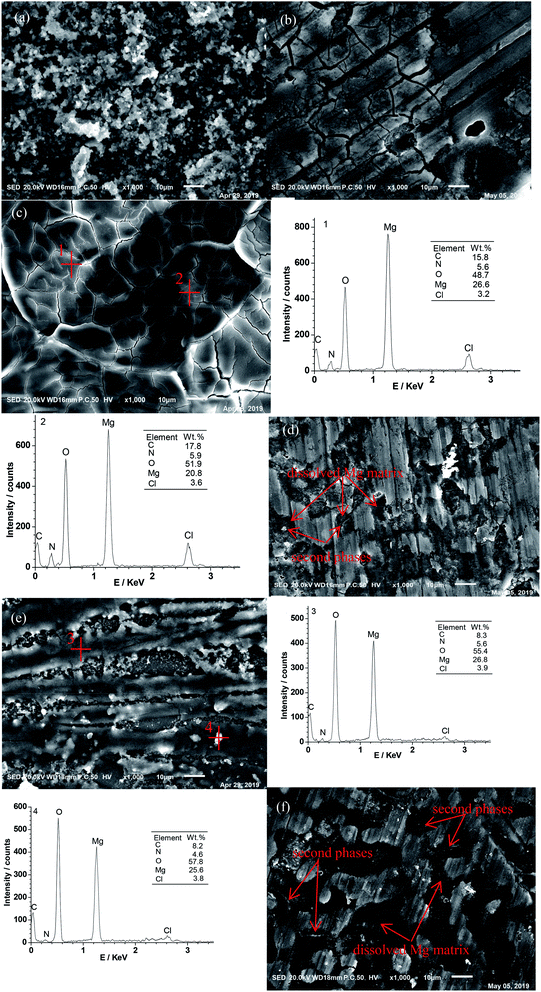 |
| Fig. 4 SEM of the Mg–6 wt% Al alloy after discharge in different solutions before cleaning out the corrosion product: 0.6 M NaCl (a), 0.5 M Mg(ClO4)2–DMF/0.6 M NaCl–H2O (c), 0.5 M Mg(ClO4)2–AN/0.6 M NaCl–H2O (e), and after cleaning out the corrosion product: 0.6 M NaCl (b), 0.5 M Mg(ClO4)2–DMF/0.6 M NaCl–H2O (d), 0.5 M Mg(ClO4)2–AN/0.6 M NaCl–H2O (f), energy spectral analysis of post 1 and 2 of (c), and post 3 and 4 of (e). | |
Fig. 3b and c show the discharge curves of the magnesium–air batteries with double electrolytes, namely Mg(ClO4)2–DMF/NaCl–H2O and Mg(ClO4)2–AN/NaCl–H2O. In these batteries, the anodic reaction proceeds in an organic electrolyte, whereas the cathodic reaction proceeds in 0.6 M NaCl–H2O electrolyte, because the anode contacts with the organic electrolyte, and the air cathode contacts with the NaCl aqueous electrolyte. On the one hand, the organic electrolyte suppresses the anode corrosion. On the other hand, the NaCl aqueous electrolyte can improve the ionic conductivity rate. Therefore, the anodic utilization rates in double electrolytes are in between those of a single organic solution and single NaCl solution (Table 2). It is visible in Fig. 3b that when the discharge starts, the voltage increases slowly as the magnesium electrode activates slowly. At 1 mA cm−2, the average operating voltage, anodic utilization rate, and energy density in the Mg(ClO4)2–DMF/NaCl–H2O solutions are 1.358 V, 76%, and 1950 W h kg−1, respectively. The comprehensive discharge performance of the battery at 1 mA cm−2 is superior to that at 0.5 mA cm−2 and 2 mA cm−2 discharge.
In Fig. 3c, the voltage decreases slowly with increasing discharge time. This indicates that there is a competition between the surface adsorption layer and alloy electrode dissolution, with the surface adsorption layer dominating. The surface adsorption layer may be organic magnesium salts and contain O, Mg, Cl, C, and N elements (energy spectral analysis of posts 3 and 4 in Fig. 4e), such as Mg(N
C
CH2) (reaction (8)) in the acetonitrile electrolyte. As a result of the surface layer existence, Mg2+ cannot pass through this layer. So, the magnesium anode dissolution reaction can only proceed when the surface layer breaks down.
|
2CH3CN + Mg → Mg(N2 C CH2) + H2
| (8) |
The magnesium–air battery with Mg(ClO4)2–DMF/NaCl–H2O double electrolytes has a better discharge performance than that with Mg(ClO4)2–AN/NaCl–H2O (Table 2). This may be due to the different performances of DMF and AN. This result is in accordance with the higher activity of the alloy in Mg(ClO4)2–DMF solution, in contrast to that in the Mg(ClO4)2–AN solution. The conductivity rate of the Mg(ClO4)2–DMF electrolyte is higher than that of the Mg(ClO4)2–AN electrolyte (Table 1). The polarization curve of the alloy in the Mg(ClO4)2–DMF electrolyte (Fig. 2) shows a passivation section in the anode branch. When the alloy contacts with organic solutions, complicated reactions take place. These reactions result in the formation of a surface adsorption layer. However, the over potentials of several tens of millivolts are enough to break down the adsorption layer.32 Then, the current increases sharply. The corresponding potential is the breakdown potential (Ebreakdown). The polarization curve of the alloy in the Mg(ClO4)2–AN electrolyte also shows a passivation section and a signal passivation potential (Epassivation) in the anode branch (Fig. 2). However, with increasing potential, the current shows almost no change, and Ebreakdown does not appear. This indicates that the adsorption layer is difficult to break down in the Mg(ClO4)2–AN electrolyte. At present, there are few studies on the magnesium–air battery with double solutions. Magnesium–air batteries with butyl butyrate-20 wt% [BMIM][TFSI]/10 wt% Mg(TFSI)2–H2O double solutions were reported by Wu Zr et al.35 At 0.6 mA cm−2 discharge, the magnesium–air battery showed 91.6% anodic utilization rate, 2020 mA h g−1 capacity density, and 0.7 V operating voltage. Due to the different double solution systems, paper35 showed the lower operating voltage, but a higher anodic utilization rate and capacity density. However, the ionic liquid [BMIM][TFSI] was very expensive.
3.3 Discharge morphology
Fig. 4 presents the SEM images of the Mg–6 wt% Al anodes after discharge at 1 mA cm−2 in NaCl–H2O electrolyte, Mg(ClO4)2–DMF/NaCl–H2O electrolytes, and Mg(ClO4)2–AN/NaCl–H2O electrolytes. Images without cleaning discharge products are shown in Fig. 4a, c and e, whereas images with discharge products being cleaned out are shown in Fig. 4b, d and f. The anode surface is covered by thick discharge products after discharge in the NaCl electrolyte (Fig. 4a). Fig. 5 shows the XRD analysis of the Mg–6 wt% Al alloy after discharge in 0.6 M NaCl solution without cleaning out the discharge product. It mainly contains Mg(OH)2 and NaCl. This indicates that the main discharge products are Mg(OH)2 in NaCl electrolyte, and the NaCl phase in XRD is the dried up NaCl electrolyte. After cleaning the discharge products, some cracks and pits are visible (Fig. 4b). This illustrates that a serious local corrosion took place, which leads to a lower anodic utilization rate in the NaCl solution (Table 2). Many turtle shell-shapes with little cracks are visible on the anode surface after discharge in 0.5 M Mg(ClO4)2–DMF/NaCl–H2O solutions (Fig. 4c). The turtle shell-shaped cracks indicate that the discharge products easily break down. After cleaning out, some shallow corrosion pits and scratches made by abrasive paper are visible on the anode surface (Fig. 4d). This means that the anode corrosion occurs very little in the Mg(ClO4)2–DMF/NaCl–H2O solutions. The anode discharged in 0.5 M Mg(ClO4)2–AN/NaCl–H2O solutions (Fig. 4e) has fewer discharge products and scratches on its surface, and some shallow pitting and scratches are observed clearly after cleaning out (4f). The discharge products in Mg(ClO4)2–DMF/NaCl–H2O and Mg(ClO4)2–AN/NaCl–H2O are too little to collect, and cannot be determined using XRD. Fig. 4c and e show the EDS analysis on the corroded surface of the alloy after discharge. The discharge products at positions 1 and 2, positions 3 and 4 all contain O, Mg, Cl, C, and N elements in Mg(ClO4)2–DMF/NaCl–H2O and Mg(ClO4)2-AN/NaCl–H2O solutions. The O, Mg, and Cl elements may be the dried up Mg(ClO4)2 electrolyte. The C and N elements indicate that DMF and AN react with the alloy, or adsorb on the alloy surface. In contrast, there is no H element on the alloy surface. This is because the H element has only one extranuclear electron, and it is not possible to detect it by EDS.
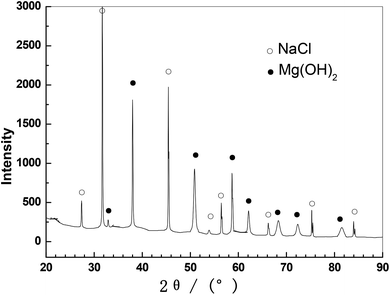 |
| Fig. 5 XRD of the Mg–6 wt% Al alloy after discharge in 0.6 M NaCl solution without cleaning out the discharge product. | |
Comparing the discharge morphologies in Fig. 4, one can see that the anode is severely corroded in the NaCl electrolyte, while the anode is only slightly corroded in the organic/NaCl double solutions. As a consequence, the batteries have a higher anodic utilization rate and a higher energy density in the organic/NaCl double solutions (Table 2). As a comparison of the anode discharge images produced in the two double solutions (see Fig. 4c and e), only a thin layer of discharge products with cracks can be seen on the anode surface after discharge in the Mg(ClO4)2–DMF/NaCl–H2O electrolytes (Fig. 4c). In contrast, obvious discharge products can be seen after discharge in the Mg(ClO4)2–AN/NaCl–H2O electrolytes (Fig. 4e). This indicates that the anode discharged in the Mg(ClO4)2–DMF/NaCl electrolytes has less corrosion than the one discharged in the Mg(ClO4)2–AN/NaCl–H2O electrolytes. In Fig. 4d and f, some shallow pitting corrosion is visible on the anode surfaces. The shallow pitting corrosion is believed to be due to the dissolution of the magnesium matrix, which can result from the galvanic corrosion between the magnesium matrix and the second phases of the magnesium alloy.36,37 There are some grey and white precipitated phases and some shallow corrosion pits due to the dissolved magnesium matrix observed in Fig. 4d and f. Galvanic corrosion has occurred between the precipitated phases and magnesium matrix. The magnesium matrix is dissolved as an anode. The precipitated phases as cathodes are not eroded. However, due to the dissolution of the magnesium matrix surrounding the precipitated phases, this causes some precipitated phases to fall off.
3.4 EIS
Fig. 6a presents the electrochemical impedance spectra of Mg–6 wt% Al in the NaCl electrolyte. Two capacitive arcs appear at high frequency and at medium frequency, respectively, and an inductive arc appears at lower frequency. The fitted curves match well with the experimental data (Fig. 6a). An equivalent circuit is shown in Fig. 6a, containing Rs, Rt and CPEt, Rf and CPEf, R1 and L1.38,39 Rs is the solution resistance. The high frequency capacitive arc is because of the Mg–Mg2+ reaction. Equivalent components contain Rt (charge transfer resistance) and CPEt (double-layer capacitance). The controlling step is the charge transfer process. The medium frequency capacitive arc is due to the absorption of the corrosion products on the anode surface. CPEf and Rf are the capacitance and resistance of the absorption layer, respectively. The lower frequency inductive arc is due to the local corrosion on the anode surface, as shown in Fig. 4b.40–42 L1 and R1 are the inductance and resistance of the corrosion reaction (reaction (1)), respectively. According to Fig. 6a, the anode corrosion occurs mainly via magnesium dissolution (Mg–Mg2+) and local corrosion in the NaCl electrolyte.
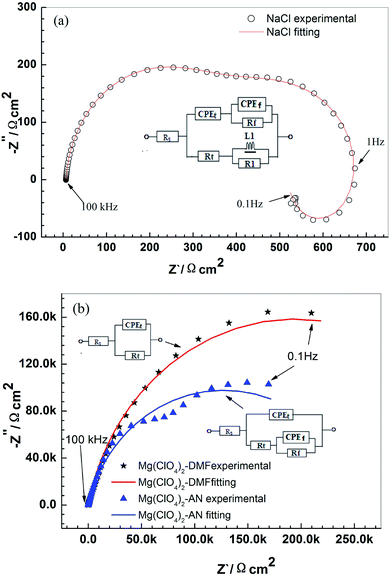 |
| Fig. 6 EIS spectra of the Mg–6 wt% Al alloy in 0.6 M NaCl solution (a), 0.5 M Mg(ClO4)2–DMF solution, and 0.5 M Mg(ClO4)2–AN solution (b). | |
The EIS of the alloy in the Mg(ClO4)2–DMF electrolyte and Mg(ClO4)2–AN electrolyte is shown in Fig. 6b. There is only a capacitive arc at high frequency in the Mg(ClO4)2–DMF electrolyte. An equivalent circuit according to Fig. 6b contains Rs, Rt and CPEt. Then, the anode corrosion occurs mainly via magnesium dissolution (Mg–Mg2+) in the Mg(ClO4)2–DMF electrolyte. Two capacitive arcs appear at high frequency and at medium frequency in the Mg(ClO4)2–AN electrolyte, respectively. An equivalent circuit is shown in Fig. 6b, containing Rs, Rt and CPEt, Rf and CPEf. Anode corrosion occurs mainly via magnesium dissolution (Mg–Mg2+) and the absorption of corrosion products in Mg(ClO4)2–AN electrolyte. From Fig. 6b for the anode discharged in organic electrolytes, the inductive arc as a symbol of local corrosion is too slight to appear in EIS (Fig. 6b). This shows that the local corrosion is slight in organic electrolytes. For the anode tested in the Mg(ClO4)2–DMF electrolyte, a medium frequency capacitive arc as a symbol of the absorption of corrosion products does not appear. This manifests that there is no absorption layer in the Mg(ClO4)2–DMF electrolyte, and the alloy has a higher activity in the Mg(ClO4)2–DMF electrolyte than in the Mg(ClO4)2–AN electrolyte. The results of EIS agree well with the discharge morphology in Fig. 4.
Table 3 shows the fitting values obtained by ZSimpwin software, according to the equivalent circuit. Rt of 392.6 Ω cm2, 3.89 × 105 Ω cm2, and 6.28 × 103 Ω cm2 are gained for tests in the NaCl electrolyte, Mg(ClO4)2–DMF electrolyte, and Mg(ClO4)2–AN electrolyte, respectively. Rt in organic electrolytes is much large than that in NaCl electrolyte. This indicates a lower corrosion rate in the organic electrolytes than in NaCl electrolyte. The result is consistent with the corrosion rate in Table 1 and the discharge morphology in Fig. 4.
Table 3 EIS simulated values of Mg–6 wt% Al alloy in 0.6 M NaCl solution, 0.5 M Mg(ClO4)2–DMF solution, and 0.5 M Mg(ClO4)2–AN solution
Solutions |
NaCl |
Mg(ClO4)2/DMF |
Mg(ClO4)2/AN |
Rs/Ω cm2 |
6.5 |
21.7 |
12.17 |
CPEt/Ω−1 cm−2 s−1 |
7.92 × 10−6 |
3.32 × 10−6 |
2.34 × 10−6 |
nt/0 < n < 1 |
0.9 |
0.87 |
0.90 |
Rt/Ω cm2 |
392.6 |
3.89 × 105 |
6.28 × 103 |
CPEf/Ω−1 cm−2 s−1 |
2.28 × 10−4 |
— |
1.46 × 10−6 |
Nf/0 < n < 1 |
0.8 |
— |
0.70 |
Rf/Ω cm2 |
122.6 |
— |
2.53 × 105 |
L1/H cm2 |
42.56 |
— |
— |
R1/Ω cm2 |
213.7 |
— |
— |
4 Conclusions
Based on the results obtained in this study, the following conclusions can be drawn for magnesium–air batteries with organic/inorganic double electrolytes:
(1) Using organic electrolytes to separate the anode from the corrosive aqueous electrolyte can improve the anodic utilization rate.
(2) A better discharge performance can be achieved for magnesium–air batteries with 0.5 M Mg(ClO4)2–DMF/0.6 M NaCl–H2O double electrolytes.
(3) A higher discharge voltage can be obtained when using the aqueous NaCl electrolyte in the air cathode side.
Conflicts of interest
There are no conflicts of interest to declare.
Acknowledgements
This work was supported by the Chinese 1000 Plan for High Level Foreign Experts (grand no. WQ20154100278), and the National Natural Science Foundation (grant no. U1804146).
References
- F. W. Richey, B. D. McCloskey and A. C. Luntz, Mg anode corrosion in aqueous electrolytes and implications for Mg–air batteries, J. Electrochem. Soc., 2016, 163, A958–A963 CrossRef CAS
. - N. N. Xu, Q. Nie, L. Y. Q. Luo, C. Z. Yao, Q. J. Gong, Y. Y. Liu, X. D. Zhou and J. L. Qiao, Controllable hortensia-like MnO2 synergized with carbon nanotubes as an efficient electrocatalyst for long-term metal–air batteries, ACS Appl. Mater. Interfaces, 2019, 1, 578–587 CrossRef
. - Z. Ma, D. R. Farlane and M. Kar, Mg Cathode Materials and Electrolytes for Rechargeable Mg Batteries: A Review, Batteries Supercaps, 2019, 2, 1–14 CrossRef
. - Q. Zhang, J. Chen and Q. A. Li, Strength stability of aging hardened Mg-10Y-1.5Sm alloy, Rare Met. Mater. Eng., 2018, 47(3), 799–802 CrossRef
. - Y. P. Wu, Z. F. Wang, Y. Liu, G. F. Li, S. H. Xie, H. Yu and H. Q. Xiong, AZ61 and AZ61-La alloys as anodes for Mg–air battery, J. Mater. Eng. Perform., 2019, 28, 2006–2016 CrossRef CAS
. - A. P. Shyma, S. Palanisamy, N. Rajendhran and R. Venkatachalam, Enhanced discharge capacity of Mg–air battery with addition of water dispersible nano MoS2 sheet in MgCl2 electrolyte, Ionics, 2019, 25, 583–592 CrossRef
. - Y. Q. Li, J. L. Ma, G. X. Wang, F. Z. Ren, Y. J. Zhu, Y. F. Song and J. L. Zhang, Effect by adding Ce and In to Mg–6Al Alloy as anode on performance of Mg–air batteries, Mater. Res. Express, 2019, 6, 066315 CrossRef CAS
. - X. Liu, J. L. Xue and S. Z. Liu, Discharge and corrosion behaviors of the alpha-Mg and beta-Li based Mg alloys for Mg–air batteries at different current densities, Mater. Des., 2018, 160, 138–146 CrossRef CAS
. - A. Pardo, M. C. Merino, A. E. Coy, F. Viejo, R. Arrabal and S. Feliú, Influence of microstructure and composition on the corrosion behaviour of Mg/Al alloys in chloride media, Electrochim. Acta, 2008, 53, 7890–7902 CrossRef CAS
. - X. Liu, J. L. Xue and D. Zhang, Electrochemical behaviors and discharge performance of the as-extruded Mg-1.5 wt% Ca alloys as anode for Mg–air battery, J. Alloys Compd., 2019, 790, 822–828 CrossRef CAS
. - Y. C. Zhao, G. S. Huang, G. L. Gong, T. Z. Han, D. B. Xia and F. S. Pan, Improving the intermittent discharge performance of Mg–air battery by using oxyanion corrosion inhibitor as electrolyte additive, Acta Metall. Sin., 2016, 29, 1019–1024 CrossRef CAS
. - J. L. Zhang, J. L. Ma, G. X. Wang, Y. Q. Li and A. A. Volinsky, Electrochemical performance of 1-ethyl-3-methylimidazolium bis(trifluoromethylsulfonyl) imide ionic liquid as electrolyte for primary Mg air batteries, J. Electrochem. Soc., 2019, 166, A1103–A1106 CrossRef CAS
. - S. Y. Liew, J. C. Juan, C. W. Lai, G. T. Pan, T. C. K. Yang and T. K. Lee, An eco-friendly water-soluble graphene-incorporated agar gel electrolyte for magnesium–air batteries, Ionics, 2019, 25, 1291–1301 CrossRef CAS
. - N. G. Wang, Y. C. Mu, W. H. Xiong, J. C. Zhang, Q. Li and Z. C. Shi, Effect of crystallographic orientation on the discharge and corrosion behaviour of AP65 magnesium alloy anodes, Corros. Sci., 2018, 144, 107–126 CrossRef CAS
. - G. L. Song and A. Atrens, Corrosion mechanisms of magnesium alloys, Adv. Eng. Mater., 1999, 1, 11–18 CrossRef CAS
. - A. R. Polu and R. Kumar, Preparation and characterization of PEG–Mg(CH3COO)2–CeO2 composite polymer electrolytes for battery application, Bull. Mater. Sci., 2014, 37(2), 309–314 CrossRef CAS
. - D. Lu, H. Q. Liu, T. Huang, Z. X. Xu, L. Ma, P. Yang, P. R. Qiang, F. Zhang and D. Q. Wu, Magnesium ion based organic secondary batteries, J. Mater. Chem. A, 2018, 6, 17297–17302 RSC
. - M. A. Deyab, Decyl glucoside as a corrosion inhibitor for magnesiumeair battery, J. Power Sources, 2016, 325, 98–103 CrossRef CAS
. - Y. S. He, Q. Li, L. L. Yang, C. R. Yang and D. S. Xu, Electrochemical-conditioning-free and water-resistant hybrid AlCl3/MgCl2/Mg(TFSI)2 electrolytes for rechargeable magnesium batteries, Angew. Chem., 2019, 58, 7615–7619 CrossRef CAS
. - H. J. Lee, J. Shin and J. W. Choi, Intercalated water and organic molecules for electrode materials of rechargeable batteries, Adv. Mater., 2018, 30 SI Search PubMed
. - R. Manjuladevi, S. Selvasekarapandian, M. Thamilselvan, R. Mangalam, S. Monisha and P. C. Selvin, A study on blend polymer electrolyte based on poly(vinyl alcohol)–poly (acrylonitrile) with magnesium nitrate for magnesium battery, Ionics, 2018, 24, 3493–3506 CrossRef CAS
. - E. Sheha and M. El-Deftar, Magnesium hexakis(methanol)–dinitrate complex electrolyte for use in chargeable magnesium batteries, J. Solid State Electrochem., 2018, 22, 2671–2679 CrossRef CAS
. - C. S. Li, Y. Sun, F. Gebert and S. L. Chou, Current progress on rechargeable magnesium–air battery, Adv. Energy Mater., 2017, 7, SI Search PubMed
. - N. Wang, Y. N. NuLi, S. J. Su, J. Yang and J. L. Wang, Effects of binders on the electrochemical performance of rechargeable magnesium batteries, J. Power Sources, 2017, 341, 219–229 CrossRef CAS
. - M. Konni, A. S. Dadhich and S. B. Mukkamala, Solvent induced surface modifications on hydrogen storage performance of ZnO nanoparticle decorated MWCNTs, Sustainable Energy Fuels, 2017, 2, 466–471 RSC
. - L. Yang, J. S. Dordick and S. Garde, Hydration of enzyme in nonaqueous media is consistent with solvent dependence of its activity, Biophys. J., 2004, 87, 812–821 CrossRef CAS
. - O. R. Brown and R. Mcuntyre, The magnesium and magnesium amalgam electrodes in aprotic organic solvents:a kinetic study, Electrochim. Acta, 1985, 30, 627–633 CrossRef CAS
. - Y. F. Song, J. L. Ma, Y. Q. Li, G. X. Wang, C. H. Qin and H.-R. Stock, Effects of second phases in anode materials on discharge performance of Mg–air batteries, Ionics, 2019, 25, 5899–5906 CrossRef CAS
. - L. Stano, M. Stano and P. Durina, Separators for alkaline water electrolysis prepared by plasma-initiated grafting of acrylic acid on microporous polypropylene membranes, Int. J. Hydrogen Energy, 2020, 45, 80–93 CrossRef CAS
. - A. Ratner, R. Beaumont and I. Masters, Dynamic Mechanical Compression Impulse of Lithium-Ion Pouch Cells, Energies, 2020, 13, 2105, DOI:10.3390/en13082105
. - J. R. Li, Q. T. Jiang, H. Y. Sun and Y. T. Li, Effect of heat treatment on corrosion behavior of AZ63 magnesium alloy in 3.5% sodium chloride solution, Corros. Sci., 2016, 111, 288–301 CrossRef CAS
. - D. Aurbach, Y. Gofer, A. Schechter, O. Chusid, H. Gizbar, Y. Cohen, M. Moshkovich and R. Turgeman, A comparison between the electrochemical behavior of reversible magnesium and lithium electrodes, J. Power Sources, 2001, 97–98, 269–273 CrossRef CAS
. - M. Deng, D. Hoche, S. V. Lamaka, D. Snihirova and M. L. Zheludkevich, Mg–Ca binary alloys as anodes for primary Mg–air batteries, J. Power Sources, 2018, 396, 109–118 CrossRef CAS
. - J. L. Ma, G. X. Wang, Y. Q. Li, C. H. Qin and F. Z. Ren, Electrochemical Investigations on AZ Series Magnesium Alloys as Anode Materials in a Sodium Chloride Solution, J. Mater. Eng. Perform., 2019, 28, 2883–2870 Search PubMed
. - Z. J. Wang, Y. Q. Niu and Z. Wu, et al., Double liquid electrolyte for primary Mg batteries, J. Power Sources, 2014, 247, 840–844 CrossRef
. - J. L. Ma, Y. Zhang, M. S. Ma, C. H. Qin, F. Z. Ren and G. X. Wang, Corrosion and discharge performance of a magnesium aluminum eutectic alloy as anode for magnesium–air batteries, Corros. Sci., 2020, 4, 108695 CrossRef
. - S. M. Li, H. Q. Qian and L. Qin, The analysis of the volume ratio of oxide on the alloy, Corros. Sci. Prot. Technol., 1999, 11(5), 284–289 Search PubMed
. - J. L. Ma, J. B. Wen, Q. A. Li and Q. Zhang, Electrochemical polarization and corrosion behavior of Al–Zn–In based alloy in acidity and alkalinity solutions, Int. J. Hydrogen Energy, 2013, 38, 14896–14902 CrossRef CAS
. - J. L. Ma, F. Z. Ren, W. H. Li, G. X. Wang, Y. Xiong, Y. Q. Li and J. B. Wen, Electrochemical performance of melt-spinning Al–Mg–Sn based anode alloys, Int. J. Hydrogen Energy, 2017, 42, 11654–11661 CrossRef CAS
. - J. L. Ma, Y. Zhang, C. H. Qin, F. Z. Ren and G. X. Wang, Effects of polystyrene sulfonate/graphene and Mn3O4/graphene on property of aluminum(zinc)–air batteries, Int. J. Hydrogen Energy, 2020, 45, 13025–13034 CrossRef CAS
. - Y. Yang, F. Scenini and N. Stevens, et. al., Relationship between the inductive response observed during electrochemical impedance measurements on aluminium and local corrosion processes, Corros. Eng., Sci. Technol., 2019, 54, 1521591, DOI:10.1080/1478422X.2018.1521591
. - D. Mareci, G. Bolat and J. Izquierdo, et. al., Electrochemical characteristics of bioresorbable binary MgCa alloys in Ringer's solution: Revealing the impact of local pH distributions during in vitro dissolution, Mater. Sci. Eng., C, 2016, 60, 402–410 CrossRef CAS
.
|
This journal is © The Royal Society of Chemistry 2021 |
Click here to see how this site uses Cookies. View our privacy policy here.