DOI:
10.1039/D0RA10164H
(Paper)
RSC Adv., 2021,
11, 8846-8856
Scale-up experiments of SO2 removal and the promoting behavior of NO in moving beds at medium temperatures
Received
2nd December 2020
, Accepted 12th February 2021
First published on 26th February 2021
Abstract
The dry flue gas desulfurization (FGD) method was studied, which is a part of the integrated removal of multi-pollutants at medium temperatures. Although dry flue gas treatment is a simple and effective method, it is still a highly empirical-led application technology. A superior desulfurization adsorbent, fine powder of NaHCO3 (hereinafter called fine NaHCO3), was selected by scale-up experiments. A deep understanding of the reaction process and mechanism is then explored, which helps the further optimization of dry desulfurization. Based on the multi-factor experiments for NaHCO3, the effect mechanism of NO on desulfurization using NaHCO3 is also proposed. The conversion of SO32− → SO42− is promoted by the existence of NO. Therefore, a slight decline can be found. According to the influences of the SO2 concentration and the residence time, it is concluded that the diffusion of SO2 into the channel of NaHCO3 is the rate-limiting step. Impressively, the reaction process of reactants was clearly studied by in situ FTIR spectroscopy to determine the whole process. Moreover, the recycling of NaHCO3 is the main direction for reducing adsorbent consumption in the next step. The predictable insights are beneficial for profoundly understanding the gas composition synergetic interaction for the SO2 removal by the dry treatment using NaHCO3.
1 Introduction
The combustion of fossil fuels (e.g., coal, petroleum, flammable gases, etc.) is widely used for human activities and in industries,1–3 which cause the generation of gas pollutants such as sulfur dioxide, nitrogen oxides, particulate matters, heavy metals, and organic matter.4–10 Limestone-based wet flue gas desulfurization (Ca-WFGD) and ammonia-based selective catalytic reduction (NH3-SCR) denitrification are simultaneously used in the pollutant control system in power plants.10–12 However, huge investment and operating costs, complicated system and secondary pollution have attracted considerable attention.13,14 Dry simultaneous control technologies are promisingly investigated without large water assumptions and low secondary pollution.15–27
Among the dry integrated multi-pollutant removal technologies, the carbon-based catalyst-integrated removal technology was widely studied,28,29 particularly in the sintering flue gas industry.30 Activated coke/activated carbon is used as a dry adsorbent. The adsorption tower is placed downstream of the precipitator. More than 98% SO2 and sulfur trioxide (SO3), 30% to 60% NOx, 90% mercury and 50% particulate matter31 will be captured in the system. The process involves three stages of adsorption, activated coke regeneration and by-product recovery, as shown in Fig. 1.
 |
| Fig. 1 Multi-pollutant integrated removal process using activated coke.32 | |
Besides, high-energy electron activation oxidation technologies33–37 and photo-catalysis technologies have been attempted,38–41 but these technologies are challenging to achieve high denitrification efficiency and lower the cost.
Under the condition of medium temperatures (200–500 °C) for the multi-pollutant integrated removal, the temperature zone is a suitable range for selective catalytic reduction (SCR), which is beneficial for the synergistic removal of SO2 and NOx. It has caused intense concerns in the industry. The schematic diagram of the integrated removal of multi-pollutants at the medium temperature zone is shown in Fig. 2. The integrated removal of multiple pollutants is realized by a single system. This broad market prospect system is more conducive to the comprehensive utilization of fly ash and owns the advantages of a high degree of system integration, a significant reduction in pollutant control costs, and no wastewater discharge.42
 |
| Fig. 2 Schematic diagram of the integrated removal of multi-pollutants at medium temperatures. | |
The adsorbents researched under medium-temperature conditions involve copper oxide (CuO), sodium bicarbonate (NaHCO3), and calcium adsorbents. Most research studies concentrated on removing single pollutants or synergistically removing SO2 and NO. However, most of them were experimental studies in a fixed bed, lacking research data on desulfurization in bench systems and moving beds.
Herein, we select the appropriate desulfurizer from different kinds of adsorbents and systematically reveal influences on dry desulfurization in scale-up experiments for flue injection to achieve multi-pollutant integrated removal. Surprisingly, a removal efficiency of more than 98% was achieved by fine NaHCO3. It is worth mentioning that in situ FTIR spectroscopy was used to better integrate the influence mechanism in the removal process. Suitable desulfurization conditions for the bench system were discussed, which lays the foundation for the next step of SO2, NOx and dust removal in practical engineering applications.
2 Experimental method
2.1 Experimental device
Based on the moving bed reactor, the multi-pollutant integrated removal test bench was designed. The whole experimental system is shown in Fig. 3. Insulation cotton was used for keeping the temperature drop with a reasonable range constant in the reaction zone.
 |
| Fig. 3 Schematic diagram of the temperature desulfurization test bench. | |
The simulated flue gas entered the heater after passing through the mixing device, and the simulated flue gas flow rate varied from 50 to 68 m3 h−1, depending on the specific situation. The flue gas was heated to the required temperature by the electric heating tube in the heater. Then, the flue gas entered the reaction zone. The feeding device was arranged at the heating zone outlet, and the entire feeding device was sealed. The feeding direction was perpendicular to the gas flow direction, ensuring uniform mixing of the feed and the flue gas. The whole reaction zone was 11.4 m in length, and the inner diameter of the reaction pipe section was 50 mm, which ensured sufficient reaction time.
The reacted flue gas entered the cyclone dust collector for dust removal, and then the induced air blower was used to provide power to the whole system. After the draft fan was induced, part of the flue gas was introduced into the flue gas analyzer to measure the flue gas component concentration following the reaction, and the rest of the flue gas was discharged into the atmosphere after the tail gas treatment. The temperature of the reaction zone was set at the desired temperature on the temperature control panel, and the flue gas flow was controlled by the flow controller.
2.2 SO2 adsorption experiment
The simulated flue gas was a mixture of air, SO2, NO, and so on. Pure SO2 and air were mixed uniformly in the mixing device and the SO2 concentration was controlled to achieve the required conditions. Pure NO was also mixed in the mixing device and the NO concentration was controlled to achieve the required condition. The water vapor was first generated by evaporation. In addition, its concentration was controlled by the knob. Then, it was introduced into the mixing device and then vaporized after heating. CO2 was supplied directly from the cylinder and introduced into the mixing device. The draft fan powered the cycle of the entire process. The SO2 removal efficiency was calculated in combination with the initial SO2 concentration and that of the outlet. The adsorbents to be screened were: sodium carbonate (Na2CO3), sodium bicarbonate (NaHCO3), magnesium hydroxide (Mg(OH)2), magnesium oxide (MgO), and calcium hydroxide (Ca(OH)2).
First, adsorbent screening was finished on the self-made experimental bench. Then, the one with the best performance was carried out to explore the SO2 removal effect on different factors on the experimental bench.
The factors that needed to be explored were temperature, residence time, sodium-to-sulfur ratio, the particle size of the desulfurizer and flue gas composition. The flue gas components consisted of SO2, CO2, NOx, water vapor and so on. The temperature was adjusted by the heating zone. The residence time was adjusted by the air volume of the experimental system. The sodium-to-sulfur ratio was adjusted by the amount of materials added, and the SO2 concentration was controlled by the volume flow of SO2 entering the air mixture device. NOx, water vapor, CO2, etc., were respectively controlled by the flow meter. The particle size of the desulfurizer was adjusted by adsorbents of different particle sizes.
2.3 Product characterization experiment
X-ray diffraction (XRD) patterns were acquired using an X-ray diffractometer (D8 advance XRD diffractometer, Swiss Buker Company) between 10° and 90° at a rate of 10° min−1. The thermogravimetric test was carried out using a Netzsch thermogravimetric analyzer under the flow of nitrogen at a heating rate of 10 °C min−1. A BET analyzer was made by American Quantatech Co. The ion chromatograph was produced by Thermo. The particle size was measured using a NKT6100-B dry and wet integrated laser particle size analyzer manufactured by Shandong Nikeite Analytical Instrument Co., Ltd.
The in situ FTIR spectra were recorded using a Frontier FTIR Spectrometer, from PerkinElmer, USA. The instrument was equipped with a 10 cm demountable gas cell and a highly sensitive MCT detector. The total gas flow rate in the experiment was fixed at 200 mL min−1. Two groups of FTIR experiments were carried out. Before each experiment, the samples were pretreated at 200 °C under the flow of N2 (200 mL min−1) for 30 min to remove physically adsorbed water, and then, the background spectra were recorded at 200 °C under N2 flow, which should be deducted from the spectra of samples. Both samples in each group were investigated at 200 °C in a flow of required composition of the gas (200 mL min−1) maintaining for demanded time, as shown in Table 1.
Table 1 Test procedures for in situ FTIR spectroscopy
Test procedures for in situ FTIR |
Conditions |
Group 1 |
Group 2 |
Pretreatment |
30 min with N2 |
30 min with N2 |
Step 1 |
20 min with 700 × 10−6 SO2/N2 |
20 min with 450 × 10−6 NO/N2 |
N2 purging |
30 min with N2 |
30 min with N2 |
Step 2 |
20 min with 700 × 10−6 SO2 + 21% O2/N2 |
20 min with 700 × 10−6 SO2 + 450 × 10−6 NO/N2 |
N2 purging |
30 min with N2 |
30 min with N2 |
Step 3 |
20 min with SO2 + 21% O2 + 8% H2O (gas)/N2 |
20 min with 700 × 10−6 SO2 + 450 × 10−6 NO + 21% O2/N2 |
N2 purging |
|
30 min with N2 |
Step 4 |
|
20 min with 700 × 10−6 SO2/N2 |
2.4 Parameter definition
For the sake of understanding a few special concepts, some parameters are defined as follows:
(1) Ratio of material to SO2 (M/S): the ratio of the molar amount of the added material to the molar amount of SO2. The following ratios of calcium to sulfur, sodium to sulfur, and magnesium to sulfur are collectively referred to as the ratio of material to sulfur. Their definitions are as follows.
Calcium-to-sulfur ratio (Ca/S): the molar amount of calcium hydroxide added to the reaction zone to the molar amount of sulfur dioxide in the flue gas;
Sodium-to-sulfur ratio (Na2/S): the molar amount of sodium carbonate or half of sodium bicarbonate added to the reaction zone to the molar amount of sulfur dioxide in the flue gas;
Magnesium-to-sulfur ratio (Mg/S): the molar amount of magnesium oxide added to the reaction zone to the molar amount of sulfur dioxide in the flue gas.
(2) Theoretically, when Ca/S = 1 of calcium hydroxide, calcium hydroxide can be completely reacted with SO2, like the magnesium oxide and sodium carbonate are. However, when NaHCO3 is used, 1 mol can be completely reacted with 0.5 mol of SO2. Therefore, Na2/S is introduced for NaHCO3 to intuitively express the results.
(3) When calculating the desulfurization efficiency under different conditions, the desulfurization efficiency value in the stable range of desulfurization efficiency is used, and the desulfurization efficiency calculation formula is as follows:
|
 | (1) |
where
η is the Ca(OH)
2 desulfurization efficiency;
C1 and
C2 are the actual concentrations measured by the flue gas analyzer at the moment of
t1 and
t2, respectively, mg m
−3;
C0 is the initial SO
2 concentration, mg m
−3; and
Q is the mixed flue gas flow rate, L min
−1.
Because the flow rate of flue gas entering the flue gas analyzer is constant, formula (1) can be simplified as follows:
|
 | (2) |
3 Results and discussions
3.1 Desulfurization effects for different adsorbents
Using a self-made experimental system, the adsorbents selected were Mg(OH)2, MgO, Na2CO3, NaHCO3 and Ca(OH)2. The flue gas flow rate was controlled at 50 m3 h−1; the inlet SO2 concentration was set as 2000 mg m−3, and the desulfurization efficiency for different adsorbents at different temperatures is shown in Fig. 4.
 |
| Fig. 4 Desulfurization efficiency for different adsorbents with temperature changing (the number on the label represents the temperature, °C). | |
As shown in Fig. 4, the best SO2 removal efficiency is exhibited by NaHCO3 at both 300 °C and 400 °C, followed by Ca(OH)2, Na2CO3, MgO and Mg(OH)2. Under any conditions, slight changes in the desulfurization efficiency by Na2CO3, MgO, Mg(OH)2 are shown, while the removal efficiencies by NaHCO3 and Ca(OH)2 grow by the increased M/S ratio. Comparing the desulfurization efficiencies of the same materials at different temperatures, the desulfurization efficiency of NaHCO3 presents a slight decrease through enhanced temperature, while the graph shows a sharp rise in the efficiency for Ca(OH)2. At the same time, it was found that Ca(OH)2, Mg(OH)2 and MgO were easily adhesive to the pipe, which were very hygroscopic. However, NaHCO3 exhibited better gas-phase spatial dispersion. According to the above-mentioned analysis, NaHCO3 was selected as the optimum adsorbent to carry out the following experiments.
3.2 Influence of different flue gas compositions on SO2 removal
Porous and highly active sodium carbonate is produced by decomposed NaHCO3 above 50 °C, as shown in Fig. 5. This process is called the popcorn effect,43 and a porous sponge-like structure is formed. SO2 is diffused and adsorbed on the surface of sodium carbonate. Compared with the diffraction peaks before the reaction, the crystal form changes after the reaction can be found, and the characteristic peaks of Na2SO3 appear.
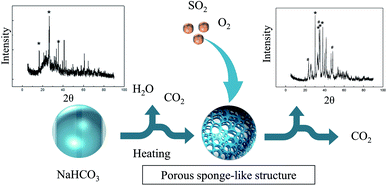 |
| Fig. 5 Schematic of desulfurization using NaHCO3 (where symbol * represents the characteristic peak of sodium carbonate and symbol # represents the characteristic peak of sodium sulfite). | |
The main reactions are listed as follows:
|
4NaHCO3 → 2Na2CO3 + 2CO2 + 2H2O
| (3) |
|
2NaHCO3 + SO2 → Na2SO3 + H2O + 2CO2
| (4) |
|
4NaHCO3 + 2SO2 + O2 → 2Na2SO4 + 4CO2 + 2H2O
| (5) |
It can be seen from Fig. 6a that the efficiency is decreased with the increase in the concentration of CO2. When the Na2/S is 2, the SO2 removal efficiency is decreased from 30% to 22% at a concentration of CO2 from 0 to 15%, and the SO2 removal efficiency is reduced from 57% to 47% when the Na2/S is 4. The active sites in the porous sponge-like structure can be occupied by CO2 diffused, thereby hindering the combination with SO2. As shown in Fig. 6b, the removal efficiency is strengthened when water vapor is introduced into the pipe. When the Na2/S is 4, the SO2 removal efficiency is expanded from 41.5% without water vapor to 70% containing water vapor. Similar trends are also demonstrated as the sodium-to-sulfur ratio is 2. More importantly, as shown in Fig. 6h and j, the amount of CO32− remaining in the sample without water vapor is higher than that with water vapor. It is indicated that the amount of Na2CO3 remaining in the sulfated samples can be decreased by the addition of water vapor and the sulfation efficiency can be improved when more Na2CO3 is utilized. Different hypotheses have been proposed around the influence mechanism of water vapor on calcination and sulfation recently.44–49 One hypothesis50 is that the solid-state diffusion can be enhanced by water vapor, which consolidates the calcination reaction rate. Herein, this hypothesis can be used to explain the results shown in Fig. 6h and j. The sulfation rate of Na2CO3 in the diffusion-controlled stage is enhanced by water vapor. Both the decomposition and sulfation reaction would be intensified by water vapor.
 |
| Fig. 6 (a) Effect of CO2 on SO2 removal. (b) Effect of water vapor on the removal of SO2 (water vapor content: (1%)). (c) Effect of NO on SO2 removal (NO concentration was 300 mg m−3). (d) XRD results of the desulfurization product. (e) XRD results of the desulfurization product under a condition with CO2. (f) XRD results of the desulfurization product under a condition with water vapor. (g) XRD results of the desulfurization product under a condition with NO. (h) Content of the desulfurization product. (i) Content of the desulfurization product under a condition with CO2. (j) Content of the desulfurization product under a condition with water vapor. (k) Content of the desulfurization product under a condition with NO (where symbol * represents the characteristic peak of sodium carbonate and symbol # represents the characteristic peak of sodium sulfite) (temperature: inlet temperature of the reaction zone was 220 °C, the outlet temperature of the reaction zone was 180 °C; the air flow rate was 50 m3 h−1; Na2/S were 2 and 4 respectively; SO2 concentration was 2000 mg m−3). | |
It can be seen from Fig. 6c that the desulfurization efficiency is decreased with the introduction of NO. The Fig. 6k reveals that the introduction of NO contributes to the formation of SO42−. Interestingly, Fig. 6g reveals that no characteristic peak of NO32− is observed, which is consistent with the phenomenon in other studies.51 Hou et al.51 found no NO3− was shown in the FTIR and XRD analyses as a result of low concentrations. He also found a higher desulfurization rate caused by NO. However, only a slight decline in the desulfurization rate is observed in our experiments. This may be caused by the production of nitrate or nitrite species. This can be proved by the appearance of other contents in Fig. 6k, which is determined later by in situ FTIR results. The facilitating effect of the conversion to sulfate was subsequently confirmed by in situ infrared characterization. According to the results, NO can be reacted with NaHCO3, thereby inhibiting the reaction between SO2 and NaHCO3, while the conversion to SO42− can be promoted by the formation of NO3−. The reaction in our hypothesis is as follows, which still needs further confirmation:
|
2NaHCO3 + SO2 → Na2SO3 + H2O + CO2
| (6) |
|
4NaHCO3 + 4NO + O2 → 4NaNO3 + 2CO2 + 2H2O
| (7) |
|
2NaNO3 + SO2 → Na2SO4 + 2NO + O2
| (8) |
Notably, in Fig. 6g, two peaks (marked with the red symbol) appear at a specific location, which is not observed in the other three figures (Fig. 6d–f). The first peak represents SO42− to emphasize that the content of SO42− is higher than that of products under other conditions. The second one contributes to CO32−. It can be observed from Fig. 6d–g that characteristic peaks of NaHCO3 and Na2SO3 are observed, indicating insufficient oxidation. At the same time, the characteristic peak of Na2CO3 at θ = 56.996 disappears, while a strong characteristic peak is exhibited here in the samples with NO.
3.3 Influence of different factors on SO2 removal
The continual growth of the desulfurization efficiency with the increase in SO2 concentration is depicted in Fig. 7a, and the efficiency (4 of Na2/S) is two times as high as that of 2. This could be attributed to the low probability of collision. In collision theory, the actual reaction rate is decided by the effective collision. The probability of effective collision is determined by two factors: (1) the appropriate path orientation and (2) the number of activated molecules. With the increase in concentration, the number of activated molecules is raised (at a constant temperature, the percentage of activated molecules is not changed), which leads to an elevating reaction rate. A high SO2 concentration can give rise to a large number of activated molecules. In addition, the increase in Na2/S contributed to the growing probability of the appropriate path orientation. This result shows that the rate-limiting step is SO2 diffusion into the surface of NaHCO3, which is consistent with the inhibition by CO2 and the promotion by water vapor.
 |
| Fig. 7 (a) Effect of SO2 concentration on SO2 removal. (b) Effect of temperature on SO2 removal. (c) Effect of residence time on SO2 removal (reaction conditions: temperature: inlet temperature of the reaction zone was 220 °C, the outlet temperature of the reaction zone was 180 °C; air volume flow rate: 50 m3 h−1; Na2/S was 2 and 4, respectively; SO2 concentration: 2000 mg m−3). | |
As shown in Fig. 7b, the temperature of 100–200 °C has a promoting effect on the desulfurization efficiency and is inhibited at 200–400 °C. NaHCO3 is gradually decomposed from 50 °C. More channels for SO2 diffusion are exhibited. NaHCO3 at 260 °C is decomposed completely,52 so the effect of temperature on efficiency is limited. After the temperature reached 300 °C, it was inhibited due to the sintering process. As shown in Fig. 7c, when the Na2/S is 4, the residence time changes from 1.4 s to 1.8 s, and the SO2 removal efficiency is slightly added from 44% to 52.5%, which is comparable to that used as the Na2/S is 2.
Based on the formula (3)–(5), the draft fan was selected to control the residence time by controlling the air flow rate.
|
 | (10) |
where
Q is the flue gas flow rate, m
3 h
−1;
A is the pipe cross-sectional area, m
2;
v is the flue gas velocity, m s
−1;
t is the flue gas residence time in the reaction zone, s;
l is the reaction zone length, m;
r is the radius of reaction zone pipe, m.
It is worth mentioning that the efficiency is not improved immediately by the increasing residence time, which demonstrates a slight decline at first. It can contribute to the control mode of residence time. The elevation in residence time is not enough to resist the decrease in molecular diffusion due to the lower wind speed. Until the reaction time is long enough, the efficiency is enhanced as expected.
3.4 Effect of the particle size of NaHCO3 on the removal of SO2
Two different sizes of NaHCO3 were used in the experiment, and the results are shown in Fig. 8.
 |
| Fig. 8 Differential pore volume versus pore size diameter and cumulative pore volume for fine NaHCO3 and NaHCO3. | |
BET results of two kinds of NaHCO3 are listed in Table 2, and the pore volume distribution results are depicted in Fig. 8.
Table 2 BET analysis results
Materials |
Specific surface area (m2 g−1) |
Adsorption average pore size by BJH method (nm) |
Fine NaHCO3 |
111.04 |
4.933 |
NaHCO3 |
28.435 |
7.444 |
Fine NaHCO3 was produced by grinding from NaHCO3. As shown in Fig. 9a, fine NaHCO3 presents better efficiency. In addition, the particle size of fine NaHCO3 is smaller than that of NaHCO3. In addition, a larger volume on fine NaHCO3 is illustrated on the smaller pore parameters than NaHCO3 in Fig. 8, which is beneficial to mixing uniformly with SO2. In Table 1, it manifests the higher specific surface area of 111.04 m2 g−1 for fine NaHCO3 than that for NaHCO3 of 28.435 m2 g−1, and the adsorption average pore size is reduced by the BJH method. A similar case researched by Walawska et al.53 identified similar conclusions that both smaller particle size and larger specific surface area were responsible for the higher conversion and instantaneous efficiency. Fig. 9b shows a weight loss process between 50 °C and 80 °C and a weight loss process between 80 °C and 130 °C. It is known that the first weight loss process is the separation of bound water in the sample. The second one is the decomposition of NaHCO3 with a low utilization rate of NaHCO3. The high utilization of NaHCO3 will be studied next. The high utilization of fine NaHCO3 is proved by Fig. 9c and d.
 |
| Fig. 9 (a) Desulfurization effect of NaHCO3 and fine NaHCO3 at 200 °C. (b) Thermogravimetric analyses of desulfurization products using fine NaHCO3 (N2 as a carrier, heating rate: 10 °C min−1, maximum temperature: 800 °C). (c) Content of the desulfurization product of fine NaHCO3. (d) Content of the desulfurization product of NaHCO3 (reaction conditions: temperature: inlet temperature of the reaction zone was 220 °C, the outlet temperature of the reaction zone was 180 °C; air flow rate was kept at 50 m3 h−1; SO2 concentration was set at 2000 mg m−3). | |
3.5 Reaction intermediates and mechanism
Fig. 10a–c show the in situ FTIR spectra of SO2 adsorption at 200 °C under different conditions. Several bands at 1377, 1344 and 978 cm−1 are observed, respectively. The band at 978 cm−1 represents the stretching vibration of surface-coordinated bisulfite and/or sulfite.54 The bands at 1377 and 1344 cm−1 can be attributed to the asymmetric and symmetric stretching vibrations of SO2 species combined by chemical adsorption.55 These results indicate that the participation of oxygen and water vapor has no noticeable effect on the oxidation of SO2, which is consistent with the experimental results.
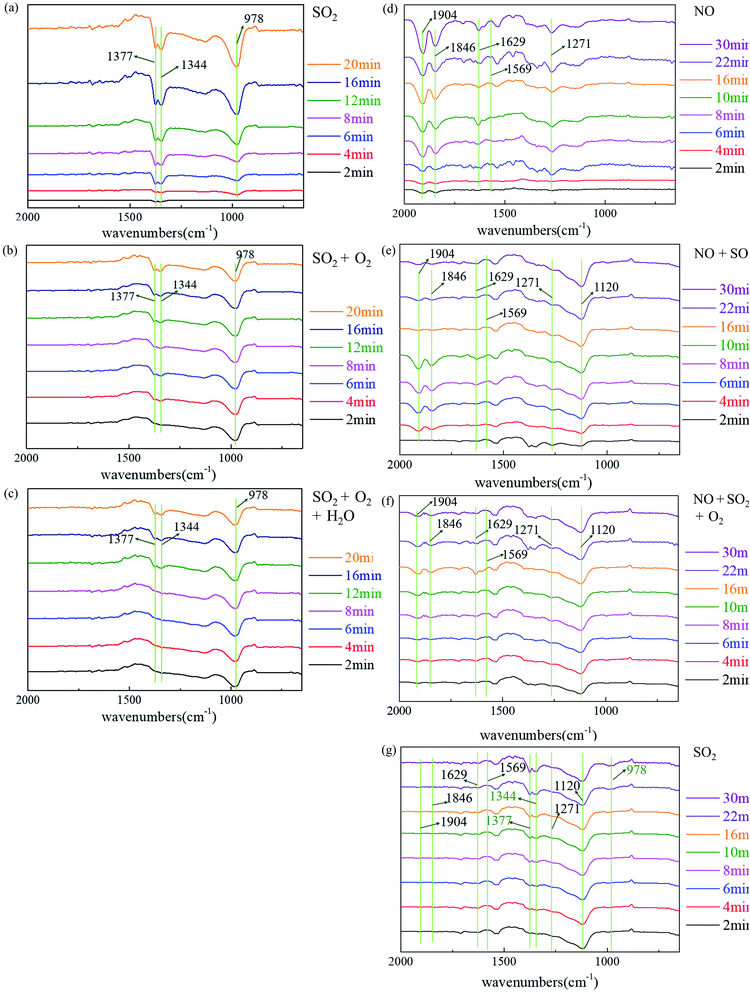 |
| Fig. 10 In situ FTIR spectra of (a) 700 × 10−6 SO2 adsorption, (b) 700 × 10−6 SO2 + 21% O2 adsorption and (c) 700 × 10−6 SO2 + 21% O2 + 8% water vapor adsorption on NaHCO3. In situ FTIR spectra of (d) 450 × 10−6 NO adsorption, (e) 700 × 10−6 SO2 + NO adsorption, (f) 450 × 10−6 NO + 700 × 10−6 SO2 + 21% O2 adsorption and (g) 700 × 10−6 SO2 on NaHCO3. | |
Fig. 10d–g shows the in situ FTIR spectra with NO on NaHCO3 at 200 °C under different conditions. After introducing only NO into the IR cell, the bands at 1904, 1846, 1629, 1569 and 1271 cm−1 are observed, respectively. These bands at 1904, 1846, 1629 and 1271 cm−1 all represent nitrite species,56–58 while the band at 1569 is assigned to the nitrate species.59 Notably, after the introduction of SO2 and NO, the band at 1120 appears, which indicates that sulfate is formed.60 No obvious bands representing SO32− appear. In addition, the bands representing NO almost vanish after 10 min, which indicates a similar evolution process after SO2, O2 and NO introduction. After purging with N2 and only SO2 introduced, bands at 1120 still exit. Meanwhile, the bands at 1377, 1344 and 978 cm−1 appear, which indicates that the formation of sulfate is promoted by NO. In addition, the band at 1569 cm−1 does not vanish, illustrating the stable presence of nitrate species, which was proposed above.
4 Conclusions
In summary, desulfurization by NaHCO3 was systematically studied by scale-up experiments. These results indicated that the diffusion of SO2 into the channel of NaHCO3 was the rate-limiting step. Meanwhile, the role of NO in promoting sulfate formation was confirmed and its reaction mechanism was proposed. Increasing the ratio of sodium to sulfur and the residence time would have a promotive effect on desulfurization efficiency. However, more attention should be paid to material waste and high costs. The efficient utilization of NaHCO3 such as material recycling and the addition of additives to promote the decomposition of sodium bicarbonate will be the next direction. In the practical application process, increasing the flow rate to improve the residence time will be a more effective way. However, due to site constraints, empty tower circulation and other ways can promote the reaction effect. Fine sodium bicarbonate could effectively enhance the reaction rate and improve the desulfurization effect. This work may inspire further development of dry integrated multi-pollutant removal with a clear explanation for different factors on desulfurization.
Author contributions
Shuangchen Ma: revised the manuscript, supervision. Xuan Bie: draft writing and editing. Chunqin Gong: methodology and some experimental data collection. Baozhong Qu: designed some experiments and conducted some characterizations of samples. Daokuan Liu: conducted some characterizations of the samples.
Conflicts of interest
There are no conflicts to declare.
Acknowledgements
This research is funded by the Foundation of Key R&D Program of Hebei Province (18273708D) and the Fundamental Research Funds of the Central University of North China Electric Power University (2018QN086).
References
- R. L. Hao, Y. M. Mao, X. Z. Mao, Z. Wang, Y. P. Gong, Z. L. Zhang and Y. Zhao, Cooperative removal of SO2 and NO by using a method of UV-heat/H2O2 oxidation combined with NH4OH-(NH4)2SO3 dual-area absorption, Chem. Eng. J., 2019, 365, 282–290 CrossRef CAS.
- R. L. Hao, X. Z. Mao, Z. Wang and Y. Zhao, A Novel Method of Ultraviolet/NaClO2–NH4OH for NO removal: mechanism and kinetics, J. Hazard. Mater., 2019, 368, 234–242 CrossRef CAS.
- Y. Shan, W. Yang, Y. Li and Y. X. Liu, Preparation of microwave-activated magnetic bio-char adsorbent and study on removal of elemental mercury from flue gas, Sci. Total Environ., 2019, 697, 134049 CrossRef CAS.
- C. Y. Su, R. Xu, J. L. Hu and C. L. Shao, Photocatalytic Process of Simultaneous Desulfurization and Denitrification of Flue Gas by TiO2-polyacrylonitrile nanofibers, Environ. Sci. Technol., 2013, 47, 11562–11568 CrossRef CAS.
- Y. Wang, X. Han and Y. X. Liu, Removal of carbon monoxide from simulated flue gas using two new fenton systems: Mechanism and Kinetics, Environ. Sci. Technol., 2019, 53, 10387–10397 CrossRef CAS.
- Q. Zhou, J. X. Yang, M. M. Liu and Y. Liu, Toxicological risk by inhalation exposure of air pollution emitted from China's municipal solid waste incineration, Environ. Sci. Technol., 2018, 52, 11490–11499 CAS.
- G. Sharma, S. B. Pallavi, H. Hakkim and B. P. Chandra, Gridded emissions of CO, NOx, SO2, CO2, NH3, HCl, CH4, PM2.5, PM10, BC, and NMVOC from open municipal waste burning in India, Environ. Sci. Technol., 2019, 53, 4765–4774 CrossRef CAS.
- J. C. Xu, J. Zhang and Y. Yu, Characteristics of vapor condensation on coal-fired fine particles, Energy Fuels, 2016, 303, 1822–1828 CrossRef.
- Y. G. Adewuyi and N. Y. Sakyi, Simultaneous absorption and oxidation of nitric oxide and sulfur dioxide by aqueous solutions of sodium persulfate activated by temperature, Ind. Eng. Chem. Res., 2013, 52, 11702–11711 CrossRef CAS.
- Q. Wang, Y. Miyake and M. Tokumura, Effects of characteristics of waste incinerator on emission rate of halogenated polycyclic aromatic hydrocarbon into environments, Sci. Total Environ., 2018, 625, 633–639 CrossRef CAS.
- Y. Zhao, T. X. Guo and Z. Y. Chen, Simultaneous removal of SO2 and NO using M/NaClO2 complex absorbent, Chem. Eng. J., 2010, 160, 42–47 CrossRef CAS.
- B. Wu and Y. Q. Xiong, A novel low-temperature NO removal approach with ˙OH from catalytic decomposition of H2O2 over La1−xCaxFeO3 oxides, J. Chem. Technol. Biotechnol., 2018, 93, 43–53 CrossRef CAS.
- J. H. Park, J. W. Ahn, K. H. Kim and Y. S. Son, Historic and futuristic review of electron beam technology for the treatment of SO2 and NOx in flue gas, Chem. Eng. J., 2019, 355, 351–366 CrossRef CAS.
- A. G. Chmielewski, E. Zwolińska, J. Licki, Y. X. Sun, Z. Zimek and S. Bułka, A hybrid plasma-chemical system for high-NOx flue gas treatment, Radiat. Phys. Chem., 2018, 144, 1–7 CrossRef CAS.
- P. Hoffmann, C. Roizard, F. Lapicque, S. Vénot and A. Maire, Process for the Simultaneous Removal of SO2 and NOx Using Ce(IV) Redox Catalysis, Process Saf. Environ. Prot., 1997, 75, 43–53 CrossRef CAS.
- B. M. Obradović, G. B. Sretenović and M. M. Kuraica, A dual use of DBD plasma for simultaneous NOx and SO2 removal from coal-combustion flue gas, J. Hazard. Mater., 2011, 185, 1280–1286 CrossRef.
- Y. X. Liu, Y. Shan and Y. Wang, Novel simultaneous removal technology of NO and SO2 using a semi-dry microwave activation persulfate system, Environ. Sci. Technol., 2020, 54(3), 2031–2042 CrossRef CAS.
- X. Zhou, H. X. Yi and X. L. Tang, Thermodynamics for the adsorption of SO2, NO and CO2 from flue gas on activated carbon fiber, Chem.
Eng. J., 2012, 200–202, 399–404 CrossRef CAS.
- Y. Zhao and J. Han, Simultaneous SO2 and NO removal from flue gas based on TiO2 photocatalytic oxidation, Environ. Technol., 2009, 30, 555–1563 Search PubMed.
- J. H. Yoon, H. W. Park and D. W. Park, Simultaneous oxidation and absorption of NOx and SO2 in an integrated O3 oxidation/wet atomizing system, Energy Fuels, 2016, 3043, 289–3297 CrossRef.
- G. Y. Xie, Z. Y. Liu, Z. P. Zhu and Q. Y. A. Liu, Simultaneous removal of SO2 and NOx from flue gas using a CuO/Al2O3 catalyst sorbent: II. Promotion of SCR activity by SO2 at high temperatures, J. Catal., 2004, 224, 42–49 CrossRef CAS.
- E. Kowsari and S. Abdpour, Investigation performance of rod-like ZnO/CdO composites, synthesized in ionic liquid medium as photocatalytic for degradation of air pollutants (SO2 and NOx), Optik, 2016, 127, 11567–11576 CrossRef CAS.
- S. P. Cui, R. L. Hao and D. Fu, Integrated method of non-thermal plasma combined with catalytical oxidation for simultaneous removal of SO2 and NO, Fuel, 2019, 246, 365–374 CrossRef CAS.
- Y. Yang, R. Whiddon and Z. H. Wang, Investigation of NO removal with ozone deep oxidation in Na2CO3 solution, Energy Fuels, 2019, 335, 4454–4461 Search PubMed.
- H. M. Yang, H. Liu and H. Wu, Photochemical removal of gaseous elemental mercury in a dielectric barrier discharge plasma reactor, Plasma Chem. Plasma Process, 2012, 32, 969–977 CrossRef CAS.
- J. H. Ye, J. Shang, H. Song, Q. Li and T. Zhu, Generation of reactive oxygen species in simulated flue gas under vacuum ultraviolet radiation, Chem. Eng. J., 2013, 232, 26–33 CrossRef CAS.
- L. Luo, Y. Y. Guo and T. Y. Zhu, Adsorption species distribution and multicomponent adsorption mechanism of SO2, NO, and CO2 on commercial adsorbents, Energy Fuels, 2017, 3110, 11026–11033 CrossRef.
- Y. J. Li, X. L. Zhang, H. F. Lin, F. Q. Yu, Z. H. Chen, C. M. Li, Z. E. Liu, J. Yu and S. Q. Gao, The simultaneous removal of SO2 and NO from flue gas over activated coke in a multi-stage fluidized bed at low temperature, Fuel, 2020, 275, 117862 CrossRef CAS.
- L. Yang, L. Yao, Y. T. Liu, X. Zhao, X. Jiang and W. J. Jiang, Bimetallic and polymetallic oxides modification of activated coke by one-step blending method for highly efficient SO2 removal, Energy Fuels, 2020, 34, 7275–7283 CrossRef CAS.
- Z. Hu, H. Zhou, W. Zhang and S. Wu, The influence of the porous structure of activated coke for the treatment of gases from coal combustion on its mechanical strength, Processes, 2020, 8, 900 CrossRef CAS.
- J. M. Rosas, R. Ruiz-Rosas, J. Rodríguez-Mirasol and T. Cordero, Kinetic study of SO2 removal over lignin-based activated carbon, Chem. Eng. J., 2017, 307, 707–721 CrossRef CAS.
- ReACT reduces emissions and water use, https://www.powermag.com/react-reduces-emissions-and-water-use/, 2010, vol. 6, p. 1 Search PubMed.
- B. K. Saikia, A. M. Dutta and B. P. Baruah, Feasibility studies of de-sulfurization and de-ashing of low grade medium to high sulfur coals by low energy ultrasonication, Fuel, 2014, 123, 12–18 CrossRef CAS.
- X. H. Dong, Z. Wang and Y. Zhao, Elemental mercury removal by a method of ultraviolet-heat synergistically catalysis of H2O2 halide complex, Environ. Sci. Technol., 2019, 53, 8324–8332 CrossRef.
- B. Wu and Y. Q. Xioang, Enhancement of NO absorption in ammonium-based solution using heterogeneous Fenton reaction at low H2O2 consumption, Korean J. Chem. Eng., 2016, 33, 3407–3416 CrossRef CAS.
- X. M. Huang, J. Ding and Q. Zhong, Catalytic decomposition of H2O2 over Fe-based catalysts for simultaneous removal of NOx and SO2, Appl. Surf. Sci., 2015, 30, 66–72 CrossRef.
- Y. X. Liu, Y. Wang and Q. Wang, Simultaneous Removal of NO and SO2 using vacuum ultraviolet light (VUV)/heat/peroxymonosulfate (PMS), Chemosphere, 2018, 190, 431–441 CrossRef CAS.
- Y. X. Liu and Q. Wang, Novel process on simultaneous removal of nitric oxide and sulfur dioxide using vacuum ultraviolet (VUV)-activated O2/H2O/H2O2 system in a wet VUV-spraying Reactor, Environ. Sci. Technol., 2016, 50, 12966–12975 CrossRef CAS.
- R. L. Hao, X. Z. Mao, Z. Qian, Y. Zhao, L. D. Wang, B. Yuan, K. M. Wang, Z. H. Liu, Q. Meng and J. Crittenden, Simultaneous removal of SO2 and NO using a novel method of ultraviolet irradiating chlorite-ammonia complex, Environ. Sci. Technol., 2019, 53, 9014–9023 CrossRef CAS.
- R. L. Hao, Z. Wang, X. Z. Mao, B. Yuan and Y. Zhao, Elemental mercury removal by a novel advanced oxidation process of ultraviolet/chlorite-ammonia: mechanism and kinetics, J. Hazard. Mater., 2019, 374, 120–128 CrossRef CAS.
- Y. X. Liu, Y. Wang and Z. Y. Liu, Oxidation removal of nitric oxide from flue gas using UV photolysis of aqueous hypochlorite, Environ. Sci. Technol., 2017, 51, 11950–11959 CrossRef CAS.
- S. C. Ma, X. Bie, X. Huang, Y. Sun, K. X. Chen and Z. P. Zhu, Desulfurization experiment analysis based on control of multiple pollutants in flue gas at medium temperature, Chem. Ind. & Eng. Pro., 2017, 37(S1), 210–217 Search PubMed.
- J. Mareček, K. Mocek and E. Erdös, Kinetics of the reaction between the solid sodium carbonate and the gaseous sulfur dioxide. IV: effect of the gas phase composition and of temperature in an integral Fixed-Bed reactor, Collect. Czech. Chem. Commun., 1970, 35, 154–164 CrossRef.
- V. Manovic and E. J. Anthony, Steam reactivation of spent CaO based sorbent for multiple CO2 Capture Cycles, Environ. Sci. Technol., 2007, 41, 1420–1425 CrossRef CAS.
- R. T. Symonds, D. Y. Lu, A. Macchi, R. W. Hughes and E. J. Anthony, CO2 capture from syngas via cyclic carbonation/calcination for a naturally occurring limestone: modeling and bench-scale testing, Chem. Eng. Sci., 2009, 64, 3536–3543 CrossRef CAS.
- P. Sun, J. R. Grace, C. J. Lim and E. J. Anthony, An investigation of attempts to improve cyclic CO2 capture by sorbent hydration and modification, Ind. Eng. Chem. Res., 2008, 47, 2024–2032 CrossRef CAS.
- R. H. Borgwardt, Calcium oxide sintering in atmospheres containing water and carbon dioxide, Ind. Eng. Chem. Res., 1989, 28, 493–500 CrossRef CAS.
- S. K. Bhatia and D. D. Perlmutter, Effect of the product layer on the kinetics of the CO2-lime reaction, AIChE J., 1983, 29, 79–86 CrossRef CAS.
- D. Mess, A. F. Sarofim and J. P. Longwell, Product layer diffusion during the reaction of calcium oxide with carbon dioxide, Energy Fuels, 1999, 13, 999–1005 CrossRef CAS.
- V. Manovic and J. E. Anthony, Carbonation of CaO-based sorbents enhanced by steam addition, Ind. Eng. Chem. Res., 2010, 49, 9105–9110 CrossRef CAS.
- B. Hou, H. Qi and C. F. You, Dry desulfurization in a circulating fluidized bed (CFB) with chain reactions at moderate temperatures, Energy Fuels, 2005, 19, 73–78 CrossRef CAS.
- Z. Q. Tan, G. P. Niu, Q. Qi, M. W. Zhou, B. H. Wu and W. Yao, Ultralow emission of dust, SOx, HCl, and NOx using a ceramic catalytic filter tube, Energy Fuels, 2020, 34, 4173–4182 CrossRef CAS.
- B. Walawska, A. Szymanek, A. Pajdak and M. Nowak, Flue gas desulfurization by mechanically and thermally activated sodium bicarbonate, Polish J. Chem. Technol., 2014, 16(3), 56–62 CAS.
- L. Zhao, X. Y. Li, C. Hao and L. C. Raston, SO2 adsorption and transformation on calcined NiAl hydrotalcite-like compounds surfaces: an in situ FTIR and DFT study, Appl. Catal. B-Environ., 2012, 117–118, 339–345 CrossRef CAS.
- C. Sun, N. Zhao, Z. Zhuang, H. Wang, Y. Liu, X. Weng and Z. Wu, Mechanisms and reaction pathways for simultaneous oxidation of NOx and SO2 by ozone determined by in situ IR measurements, J. Hazard. Mater., 2014, 274, 376–383 CrossRef CAS.
- C. D. Craver, The coblentz society desk book of infrared spectra, DTIC document, 1977 Search PubMed.
- H. M. Wang, P. Ning, Y. Q. Zhang, Y. P. Ma, J. F. Wang, L. Y. Wang and Q. L. Zhang, Highly efficient WO3–FeOx catalysts synthesized using a novel solvent-free method for NH3-SCR, J. Hazard. Mater., 2020, 388, 121812 CrossRef CAS.
- J. Fan, P. Ning, Y. C. Wang, Z. X. Song, X. Liu, H. M. Wang, J. Wang, L. Y. Wang and Q. L. Zhang, Significant promoting effect of Ce or La on the hydrothermal stability of Cu-SAPO-34 catalyst for NH3-SCR reaction, Chem. Eng. J., 2019, 369, 908–919 CrossRef CAS.
- L. Lietti, M. Daturi, V. Blasin-Aubé, G. Ghiotti, F. Prinetto and P. Forzatti, Relevance of the Nitrite Route in the NOx Adsorption mechanism over Pt-Ba/Al2O3 NOx storage reduction catalysts investigated by using operando FTIR spectroscopy, ChemCatChem, 2011, 4, 55–58 CrossRef.
- S. F. Weng, Fourier transform infrared spectroscopy analysis, Chemical Industry Press, China, 2010 Search PubMed.
|
This journal is © The Royal Society of Chemistry 2021 |
Click here to see how this site uses Cookies. View our privacy policy here.