DOI:
10.1039/D0NJ00870B
(Paper)
New J. Chem., 2021,
45, 123-130
Synthesis and properties of a bio-based PVC plasticizer derived from lactic acid
Received
22nd February 2020
, Accepted 19th November 2020
First published on 20th November 2020
Abstract
A novel green plasticizer, acetylated lactic acid 1,6-hexane diester (ALHD), was successfully synthesized based on L-lactic acid, a renewable organic acid from corn starch. Its chemical structure was characterized using FTIR, 1H NMR and matrix-assisted laser desorption/ionization time of flight mass spectrometry (MALDI-TOF-MS). The plasticizing effects of ALHD as an alternative substitute for commercial plasticizer acetyl tributyl citrate (ATBC) in poly(vinyl chloride) (PVC) were investigated in detail. The results show that the PVC films plasticized using ALHD have better organic solvent resistance and food mimic migration stability than ATBC. After 24 hours of extraction in cyclohexane and petroleum ether, the weight loss of PVC sample S5 plasticized using pure ALHD was reduced by 83.6% and 77.5%, respectively, compared to that of PVC sample S1 plasticized with pure ATBC. Furthermore, after 72 hours of migration in activated carbon, the weight loss of PVC sample S5 decreased by 44.0% compared to that of PVC sample S1, which indicated that ALHD had excellent volatility and migration stability. The elongation at break of the PVC pieces increased from 644.65% to 802.15% as the content of ALHD improved, showing an increase of 24.4%. The mechanical property analysis showed that, with the replacement of ALHD in the place of ATBC, the PVC blends exhibited better flexibility and elasticity.
Introduction
Poly(vinyl chloride) is one of the most useful materials due to its excellent mechanical and thermal stability, and has been widely used for numerous applications, such as medical instruments, children's toys, food packaging, infant supplies and others.1–5 PVC has a hard and brittle character due to the interaction among the PVC chains, which restricts chain motility. In order to enhance PVC properties and decrease the processing temperature, a suitable plasticizer needs to be added to PVC.6–8 However, external plasticizers are usually not chemically bonded to PVC polymer chains; this makes them easy to leach from the product into the surrounding media. Therefore, in view of maintaining public health and preventing related adverse effects, we need to study the exposure of these compounds.9–13
Many plasticizers are used to improve the performance of PVC. Among these commercial plasticizers, phthalate based plasticizers play an important part,14–16 and phthalate esters are a class of these plasticizers. They contribute to more than 80% of the total market share of PVC plasticizers.17–21 The phthalate ester group has a lot of members that are of industrial significance, such as dibutylphthalate (DBP), di-2-ethylhexyl phthalate (DOP), di-sec-octyl phthalate (DCP), butyl benzyl phthalate (BBP), diamyl phthalate (DPP), diisobutyl phthalate (DIBP), diisobutyl phthalate (DIDP), diisopentyl phthalate (DIPP) and so on; a comparison of the molecular structures of different plasticizers is shown in Fig. 1. All the phthalate members have very similar chemical and physical characteristics. However, research studies have shown that phthalates may increase the incidence of asthma, bronchitis and cancer. In addition, they are toxic to the human reproduction system and endogenous hormones.22–24 Therefore, the European Union's REACH act prohibits the use of phthalate plasticizers in PVC products such as children's toys, food packaging, medical devices and monitoring and control instruments. The use of non-toxic and biodegradable alternatives to replace phthalates has become an inevitable trend.25–27 Currently, hundreds of plasticizers obtained from renewable bio-based resources have been commercially used, such as epoxy soybean oil plasticizer,28,29 epoxidized glycidyl ester of ricinoleic acetic ester,30 epoxidized tung oil derivatives,31 polyester plasticizer based on glyceryl, epoxidized vegetable oil,32 isosorbide diester plasticizer and cardanol-based plasticizer33–35 and “acetylated” plasticizers.37–39 An example of an incumbent “acetylated” plasticizer is Grindsted Soft-N-Safe™ (acetylated monoglyceride of hydrogenated castor oil).
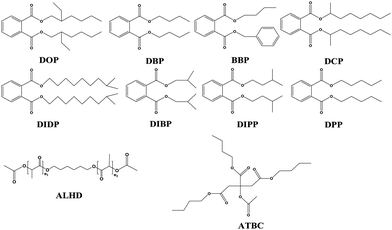 |
| Fig. 1 Comparison of molecular structures of different plasticizers. | |
L-Lactic acid is an organic acid refined by the biological fermentation of corn starch. It is colorless, transparent and slightly viscous. It is a good renewable biomass source. In addition, due to its left-handed characteristics, it has excellent bio-melting properties, has no toxic side effects on the human body, and can be directly metabolized. The lactic acid molecule contains both a hydroxyl group and a carboxyl group, and the self-polymerization is caused by the interaction of an intermolecular group at a normal temperature. Therefore, a large amount of strongly polar lactate groups is present in the plasticizer prepared from lactic acid as the raw material. Studies have shown that the PLA plasticized with glyceryl lactate had a lower glass-transition temperature and a better ductility.36 The research on lactic acid-based PVC plasticizer is still a very innovative field, and there are few reports.
In this study, a novel lactate was synthesized through two steps of esterification and acetylation from L-lactic acid and 1,6-hexanediol to plasticize PVC (Fig. 1). The obtained plasticizer is either used by itself or also blended with a commercial plasticizer; for the latter, the obtained plasticizer is blended with the commercial plasticizer ATBC in different proportions and added to the PVC. A wide range of PVC film properties, such as migration behavior, mechanical properties and thermal stability were investigated. Research shows that ALHD is a highly effective plasticizer with excellent compatibility with PVC. This study proves that traditional PVC plasticizers of citrates and phthalates can be replaced by lactic acid esters, which are a green plasticizer without a benzene ring.
Experimental
Materials
L-Lactic acid used in this study was kindly supplied by Jindan Co. (Henan, China). 1,6-Hexanediol was purchased from Macklin Co. (shanghai, China). Calcium–zinc heat stabilizers (Industrial grade) were supplied by Qilu Petrochemical Engineering Co. for PVC manufacturing (Shandong China). ATBC was purchased from Aladdin Co. (shanghai, China). PVC powder (P-440, emulsion grade) with an average degree of polymerization of 1100–1150, apparent density of 0.58 g mL−1, and whiteness of 81% (160 °C, 10 min) was obtained from Chlor-Alkali Chemical Industry Co. (Shanghai, China).
Preparation of ALHD
To a 250 mL three-necked flask equipped with a magnetic stirrer, reflux condenser and thermometer, L-lactic acid (36.03 g), 1,6-hexanediol (23.63), p-toluenesulfonic acid (0.54 g), and cyclohexane (9.00 mL) were charged. The mixture was slowly heated to 130 °C and maintained at that temperature. The acid value of the reaction system no longer decreases, marking the end of the reaction. After the reaction, reduced pressure distillation was carried out to remove the residual cyclohexane and low boiling point impurities. Next, 44.92 g (0.44 mol) of acetic anhydride was slowly added to the reaction system; the dropping rate was controlled to ensure that the reaction temperature did not exceed 80 °C. The reaction was terminated after 4 hours. Acetic acid and excess acetic anhydride were removed by vacuum distillation. The crude product was neutralized using a 10% NaHCO3 solution and washed with water. After standing and layering, the water is distilled off under reduced pressure to obtain a refined ALHD product. The synthetic route of ALHD is shown in Fig. 2.
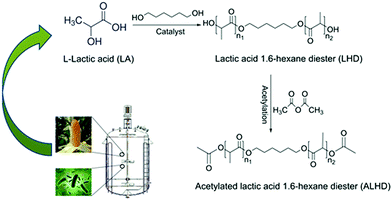 |
| Fig. 2 The synthetic routes of ALHD (n1 + n2 = 1–7). | |
Preparation of plasticized PVC test specimens
A series of plasticized PVC samples were prepared with different compositions as shown in Table 1. Firstly, PVC powder, plasticizers and thermal stabilizers (the mass ratio: CaSt2/ZnSt2 = 2/1) were mixed using a Shanghai Meiyingpu D2025W model mechanical agitator. The mechanical stirring speed was 600 rpm, and the blade used a PTFE spiral stirring rod. The blends were wet after 10 min of mixing at room temperature (15–25 °C). Secondly, the mixture was compounded into a homogeneous mixture at 160 °C for 5 min using a double-roll mill (Yunxin Co., China). Finally, the films were made using a Carver 3969 mini hot press (Wabash, IN) at 180 °C for 2 min. The thickness of all PVC test specimens is 1 mm.
Table 1 Samples of the PVC films
Component (phr) |
S1 |
S2 |
S3 |
S4 |
S5 |
PVC(g) |
100.0 |
100.0 |
100.0 |
100.0 |
100.0 |
ALHD(g) |
0.0 |
15.0 |
30.0 |
45.0 |
60.0 |
ATBC(g) |
60.0 |
45.0 |
30.0 |
15.0 |
0.0 |
Thermal stabilizers(g) |
3.0 |
3.0 |
3.0 |
3.0 |
3.0 |
Characterizations
Fourier transform infrared (FTIR) analysis was carried out using a Nexus spectrometer (Nicolet Co., USA). The samples were scanned from 4000 cm−1 to 500 cm−1.
The 1H NMR spectrum of the compounds in deuterated chloroform-m (CDCl3) was recorded using a Bruker 400 MHz spectrometer (Bruker Co., Switzerland).
Thermogravimetric analysis (TGA) was conducted using an 1100SF TG instrument (Mettler-Toledo Co., Switzerland). Pure plasticizers and PVC samples were heated from 50 °C to 600 °C under N2 atmosphere at a heating rate of 20 °C min−1.
DMA was measured according to a DMA Q800 (TA Instruments Co., US). Test method: the PVC test piece was cut into a rectangular test strip of 30 mm × 5 mm, and a tensile mold was used for testing. Test conditions: Vibration frequency is 1 Hz, and test temperature range is −40 °C to 60 °C.
Mechanical properties were measured according to GB/T1040.1-2006 using an electronic tensile testing machine (Kailiqiang Co., China). All the samples with a gauge length of 10 mm were stretched at an extension rate of 50 mm min−1 for the tensile test.
Volatility tests were carried out using the activated carbon method according to ASTM D1203-67. 3 pieces of PVC sample of different formulas of 40 mm × 60 mm × 1 mm were prepared, and the samples were placed in a crucible containing activated carbon. The crucible was placed in a convection oven at a temperature of 70 °C for 24 h, 48 h and 72 h. Then, the samples were removed, brushed and reweighed. Volatility (%) was determined by the difference in weight.
Migration tests were evaluated according to GB/T 3830-2008. The test conditions were restricted to a temperature of 30 ± 1 °C. The PVC specimens were immersed in three different solvents (anhydrous ethanol, cyclohexane and petroleum ether). The sample was removed after a certain period of time. Using filter paper to dry the liquid on both sides of the sample, and then dry it thoroughly using a convection oven (Shanghai Shengxin Technology Co., China). After the sample is naturally cooled to room temperature in a desiccator, its mass is weighed. The extraction loss is calculated according to eqn (1): Weight loss = [((m1 − m2)/m1)] × 100%, where m1 = initial weight of test specimen, and m2 = final weight of test PVC specimen.
Overall migration to food simulants was performed in the light of GB 5009.156-2016. The immersion method was similar to that of the migration tests. Migration rate (%) was determined using high performance liquid chromatography/HPLC (Waters Co., USA), with a Hedera ODS-2-C18 chromatographic column. Standard curves were carried out in ethanol for the analysis of the migrated plasticizers after overall migration tests.
Attenuated total reflection (ATR) analysis was conducted using a Nicolet 6700 spectrometer (Thermo Fisher Scientific, US). The samples were scanned from 4000 cm−1 to 500 cm−1.
Results and discussion
Characterization
Fig. 3 shows the infrared image of the raw material oligomeric lactic acid and the product ALHD. It can be seen from the infrared spectrum of oligolactic acid that the broadband peak at 3409 cm−1 is the characteristic peak of hydroxyl groups (–OH), and 2993 cm−1 is the characteristic peak of methyl groups (–CH3) in 2-hydrox-ypropionic acid. As for ALHD, 2859 cm−1 is the characteristic absorption peak of methylene (–CH2) in 1,6-hexanediol, thereby confirming the successful occurrence of the esterification reaction. 1742 cm−1 is the stretching vibration absorption of carbonyl (C
O). The new peak at 1236 cm−1 is due to the presence of C–O bonds on the acetate after acetylation. Moreover, the hydroxyl (–OH) peak at 3409 cm−1 completely disappeared, which proved that the target product was successfully synthesized.
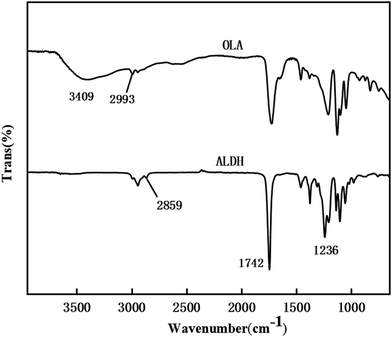 |
| Fig. 3 FT-IR spectra of (a) OLA and (b) ALHD. | |
Fig. 4 displays the 1H NMR spectrum of ALHD. In Fig. 4(a), the multiple peaks around 1.47–1.58 ppm were assigned to methyl (–CH3) of the number 1 carbon atom. The peaks at 4.4 ppm were signals of hypomethyl protons of the number 2 carbon atom. The peaks at 5.2 ppm were signals of the hydroxyl proton (–OH) of the number 4 carbon atom. The multiple peaks around 6.45–6.85 ppm were attributed to the carboxyl proton (–COOH) of the number 3 carbon atom. In Fig. 4(b), the multiple peaks around 1.39–1.67 ppm were assigned to methyl (–CH3) and methylene protons (–CH2–) of number 3, 5, and 6 carbon atoms. The peaks at 2.06–2.15 ppm were signals of methyl protons (–(OC)–CH3) of the number 1 carbon atom. The multiple peaks around 4.06–4.21 ppm were attributed to the methylene protons (–CH2–CH2–O–) of the number 4 carbon atom. The peaks at 5.05–5.17 ppm were the sign of hypomethyl protons of the number 2 carbon atom. Therefore, the data of hydrogen nuclear magnetic resonance can be reasonably matched with the theoretical structure of ALHD, which proves that the reaction product is exactly the required acetylated lactic acid 1,6-hexane diester.
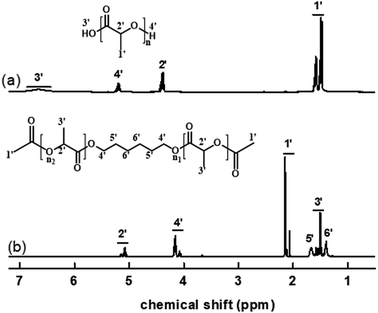 |
| Fig. 4
1H NMR spectrum of ALHD. | |
MALDI-TOF-MS was recorded, as shown in Fig. 5. It can be seen from the figure that there are seven molecular mass peaks with the same interval between 200 and 800. The interval was calculated to be 72, which was consistent with the relative molecular mass of a polylactic acid molecule C3H4O2. In addition, the difference between the actual measured value and the theoretical calculated value is less than 0.2.
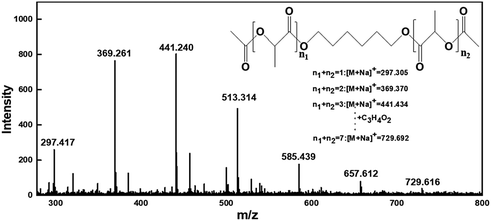 |
| Fig. 5 MALDI-TOF-MS of ALHD. | |
Therefore, the finally obtained product was a mixed product having different molecular weights.
Extraction resistance and volatility stability
Fig. 6 shows the extraction resistance and volatility stability of PVC samples with different formulations. In Fig. 6(a)–(c), the PVC test pieces were tested for resistance to extraction in cyclohexane, absolute ethanol and petroleum ether. It can be clearly observed that the weight loss of PVC films immersed in different solvents followed the order of S1 > S2 > S3 > S4 > S5. As ALHD gradually replaced ATBC, the extraction resistance of the PVC test pieces was significantly improved. This result might be explained by the fact that a large number of lactate groups on the ALHD interact with the polar parts of the PVC chain, which means better compatibility between the ALHD and the PVC matrix. In addition, the weight loss of ALHD plasticized PVC films was quite low in cyclohexane and petroleum ether. By comparing the polarities of several solvents, it was found that cyclohexane and petroleum ether were less polar than absolute ethanol. This result can be explained by considering that the lactic acid-based environmentally friendly plasticizer ALHD was less resistant to extraction in more polar solvents.
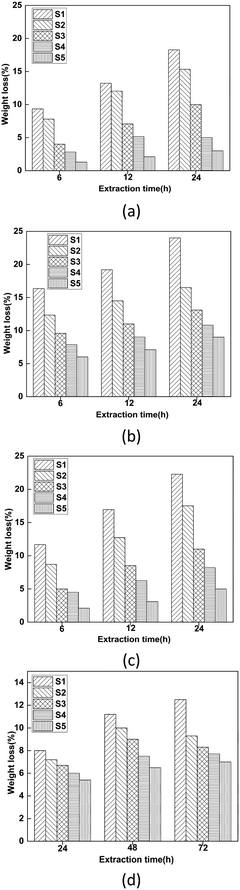 |
| Fig. 6 Weight losses of PVC films after extraction resistance and volatility stability testing. | |
In Fig. 6(d), the PVC test pieces were tested for volatility stability in activated carbon. It can be clearly observed that the weight loss of PVC films followed the order of S5 < S4 < S3 < S2 < S1, which was consistent with the result in the liquid solvents. It showed that ALHD had better volatilization stability and compatibility with PVC molecules than that of the commercially available environmental plasticizer ATBC. As a result, ALHD could give PVC films long-term stability and reduce the diffusion into contact materials.
Migration stability for food simulants
The migration stability of PVC films with different formulas to food simulants was explored and is shown in Fig. 7. Distilled water, 4% by volume acetic acid, 50% by volume ethanol and isooctane were used as simulants for aqueous, acidic, alcoholic and fatty foods. It can be clearly observed that all of the PVC films displayed poorer migration resistance in 50% ethanol and isooctane than in distilled water. Moreover, ALHD showed greater migration resistance in 50% ethanol and isooctane than acetylated tributyl citrate (ATBC). This result can be explained by considering that the molecular polarity of ALHD was greater than that of ATBC, making it difficult to migrate into weakly polar solvents and good solvents of esters. As a result, this is consistent with the conclusion of previous extraction resistance and volatility stability.
 |
| Fig. 7 Migration stability of PVC films to food simulants. (a) Distilled water, (b) 4%(v/v) acetic acid, (c) 50%(v/v) ethanol, (d) isooctane. | |
Mechanical properties
The mechanical properties of the PVC samples with different plasticizer ratios including elongation at break, tensile strength, and Young's modulus are shown in Fig. 8 and Table 2. It can be seen from Fig. 8 that there is a nonlinear part in the curve. If only the Young's modulus at the time of fracture was compared, there was a large error. Therefore, in Table 2 we show the results of the apparent modulus at 100% and 300% elongation for all experiments. It can be seen that the percentage elongation of PVC films followed the order of S4 > S5 > S3 > S2 > S1. With the gradual replacement of ATBC by ALHD, the elongation at break of the PVC test pieces increased significantly. Moreover, when the formula S4 (ALHD and ATBC ratio is 3
:
1) reached the maximum value, taking into consideration the standard deviations of the tensile measurements, there was a general trend for increasing proportions of ALHD (in the plasticizer composition) to yield greater tensile elongation. The pure ALHD plasticized test piece exhibited higher tensile strength than the pure ATBC plasticized test piece. All samples exhibited strain softening during the tensile testing. As the ATBC was replaced by ALHD, the apparent modulus decreased.
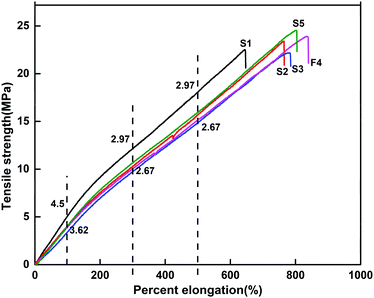 |
| Fig. 8 Selected tensile stress–strain curves of the different PVC films. | |
Table 2 Mechanical properties of the different PVC films
PVC films |
Tensile properties |
Elongation at break (%) |
Max tensile strength (MPa) |
Apparent modulus at 100% (MPa) |
Apparent modulus at 300% (MPa) |
Young's modulus |
S1 |
644.65 ± 10.2 |
22.51 ± 0.2 |
4.50 ± 0.1 |
2.97 ± 0.2 |
3.49 ± 0.1 |
S2 |
763.82 ± 8.5 |
23.41 ± 0.5 |
3.85 ± 0.2 |
2.75 ± 0.0 |
3.06 ± 0.1 |
S3 |
779.66 ± 7.6 |
22.19 ± 0.3 |
3.62 ± 0.0 |
2.67 ± 0.1 |
2.85 ± 0.2 |
S4 |
833.82 ± 15.3 |
23.92 ± 0.2 |
3.81 ± 0.1 |
2.71 ± 0.1 |
2.87 ± 0.0 |
S5 |
802.15 ± 11.0 |
24.53 ± 0.1 |
3.92 ± 0.1 |
2.89 ± 0.2 |
3.06 ± 0.2 |
These results indicate that ALHD plasticized PVC test pieces maintained better strength during straining than ATBC plasticized test pieces due to the presence of more polar groups and ester-based bonds in the molecular structure. The new plasticizer ALHD gave PVC products better toughness and strength; therefore, it can be used as either a primary or secondary plasticizer.
Thermal stability and DSC analysis
Thermal stability of the plasticizers and PVC specimens was researched using TGA and the obtained data are shown in Fig. 9 and Table 3. Table 3 displays the values of Ti (i.e. the initial decomposition temperature), T10% and T50% (i.e. the temperature at which the PVC sample lost 10% and 50% of its original mass), and Tp1 and Tp2 (i.e. the maximum weight loss temperature rate). As shown in Fig. 9(a), ATBC illustrated higher thermal stability, and the characteristic data also proved this fact. Fig. 9(b) showed that the thermal degradation of the plasticized PVC samples was a two-step procedure, which was consistent with the literature report. In the first step, the weight loss was mainly due to the decomposition of the plasticizers and the dechlorination of PVC to release HCl gas. In the second step, the polymer was cracked to form crosslinked compounds. Unlike pure plasticizers, it was observed that the Ti, T10%, T50% and Tp1 of the PVC films showed little change when ATBC was gradually replaced by ALHD. The results show that in spite of ATBC and ALHD exhibiting different thermogravimetry characteristics, the plasticized PVC specimens made with these plasticizers or their mixtures did not exhibit any apparent differences in thermogravimetry testing.
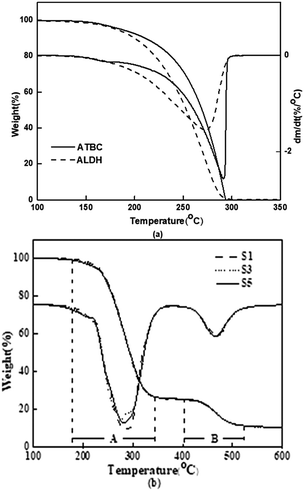 |
| Fig. 9 TGA curves of (a) ATBC and ALHD. (b) PVC films with different plasticizers. | |
Table 3 TGA data of plasticizers and PVC films with different plasticizers
Sample |
T
i (°C) |
T
10% (°C) |
T
50% (°C) |
T
p1 (°C) |
T
p2 (°C) |
ATBC |
156.0 |
210.7 |
269.3 |
291.3 |
— |
ALHD |
148.2 |
199.7 |
253.4 |
276.2 |
— |
S1 |
168.0 |
244.7 |
293.7 |
293.7 |
467.3 |
S3 |
156.8 |
244.3 |
294.3 |
274.6 |
469.2 |
S5 |
153.7 |
242.3 |
294.3 |
283.7 |
463.0 |
Dynamic mechanical analysis (DMA) of the PVC films with different formulas is illustrated in Fig. 10. It can be clearly seen that, as the ALHD content increased, the Tg gradually decreased from 14.3 °C to 7.0 °C. This result may be explained by considering that ALHD can create more free volume in the polymer.
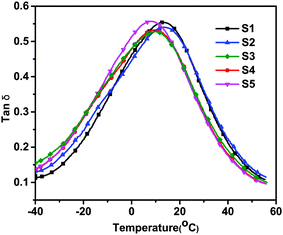 |
| Fig. 10 Tan (δ) for the PVC films with different plasticizers. | |
Fourier attenuated total reflection infrared analysis
Five different formulations of PVC test pieces were characterized using Fourier attenuated total reflection infrared, and the result is shown in Fig. 11. The interaction between the plasticizer and PVC chains was studied based on some characteristic peaks. In the spectra of the S1 and S5 test pieces (Fig. 11(a)), the peaks around 1739 cm−1 and 689 cm−1 were attributed to the carbonyl bond (C
O) of the plasticizers and the carbon–hydrogen bond (C–H) of the PVC chains, respectively. After adding the plasticizer into the PVC formulations, it was discovered that the carbonyl absorption peak in the plasticizers reduced the frequency of several wave numbers. The C
O frequency of ATBC shifted from 1745.8 cm−1 to 1738.0 cm−1, and the C
O frequency of ALHD shifted from 1745.6 cm−1 to 1739.1 cm−1, which means that both of the plasticizers have good interaction with the PVC chains. On the other hand, as shown in Fig. 11(b), as ALHD gradually replaced ATBC, the vibration absorption peak of C–H (PVC) gradually increased from 682.7 cm−1 to 688.4 cm−1, and the peak width and intensity gradually increased. Hooke's law states that the force constant is proportional to the vibration frequency. As the ALHD content increased, the C–H (PVC) vibration absorption peak frequency gradually enhanced. This phenomenon indicated that ALHD plasticizer had stronger interaction with the PVC chain.
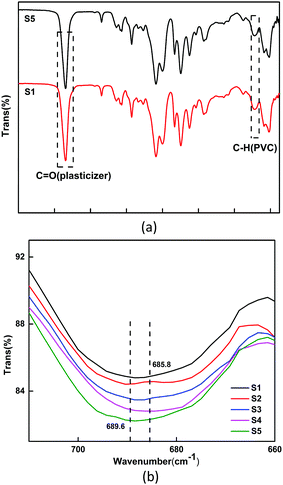 |
| Fig. 11 FTIR spectra of PVC films with different plasticizers. | |
Conclusions
In this study, a green plasticizer ALHD based on lactic acid was synthesized and incorporated into PVC blends. The properties of ALHD were studied and compared with those of the commercial plasticizer ATBC. Extraction resistance and volatility stability tests found that the PVC films plasticized using ALHD displayed higher extraction resistance in petroleum ether, cyclohexane and anhydrous ethanol and lower volatility in contact with activated carbon. The glass transition temperature (Tg) of PVC films decreased gradually from 14.3 °C to 7.0 °C when ATBC was replaced with ALHD. The DMA and tensile tests showed a significant enhancement of the plasticizing efficiency and flexibility of PVC films plasticized using ALHD. This phenomenon indicated that ALHD endued PVC products with higher processability compared to ATBC.
In addition, ALHD displayed better compatibility with the PVC matrix compared to ATBC. This study replaced traditional citrate and phthalate PVC plasticizers with a benzene-free green plasticizer, bridging the gap between conventional and alternative plasticizers in plastics additives.
Conflicts of interest
There are no conflicts to declare.
Acknowledgements
The authors are grateful for the financial support from International Joint Laboratory of Jiangnan University, the Fundamental Research Funds for the Central Universities (Grant No. JUSRP51623A) and the open fund of Jiangsu Key Laboratory for Biomass Energy and Materials (Grant No. JSBEM201906).
Notes and references
- Y. A. El-Shekeil, S. M. Sapuan, M. Jawaid and O. M. Al-Shuja’a, Mater. Des., 2014, 58, 130–135 CrossRef CAS.
- Y. Yang, J. Huang, R. Zhang and J. Zhu, Mater. Des., 2017, 126, 29–36 CrossRef CAS.
- P. Yang, J. Yan, H. Sun, H. Fan, Y. Chen, F. Wang and B. Shi, RSC Adv., 2015, 5, 16980–16985 RSC.
- P. Jia, M. Zhang, L. Hu and Y. Zhou, Korean J. Chem. Eng., 2016, 33, 1080–1087 CrossRef CAS.
- J. Bao, M. Wang, X. Ning, Y. Zhou, Y. He, J. Yang, X. Gao, S. Li, Z. Ding and B. Chen, J. Toxicol. Environ. Health, Part A, 2015, 78, 325–341 CrossRef CAS.
- I. N. Unar, S. A. Soomro and S. Aziz, Pak. J. Anal. Environ. Chem., 2010, 11, 7 Search PubMed.
- H. Hosney, B. Nadiem, I. Ashour, I. Mustafa and A. El-Shibiny, J. Appl. Polym. Sci., 2018, 135, 46270 CrossRef.
- H. C. Erythropel, S. Shipley, A. Börmann, J. A. Nicell, M. Maric and R. L. Leask, Polymer, 2016, 89, 18–27 CrossRef CAS.
- J. A. Tickner, T. Schettler, T. Guidotti, M. McCally and M. Rossi, Am. J. Ind. Med., 2011, 39, 100–111 CrossRef.
- F. Chiellini, M. Ferri, A. Morelli, L. Dipaola and G. Latini, Prog. Polym. Sci., 2013, 38, 1067–1088 CrossRef CAS.
- B. Yin and M. Hakkarainen, J. Appl. Polym. Sci., 2011, 119, 2400–2407 CrossRef CAS.
- C. J. Hines, N. B. Hopf, J. A. Deddens, M. J. Silva and A. M. Calafat, Int. Arch. Occup. Environ. Health, 2012, 85, 317–325 CrossRef CAS.
- P. Jia, L. Hu, G. Feng, C. Bo, J. Zhou, M. Zhang and Y. Zhou, RSC Adv., 2017, 7, 897–903 RSC.
-
J. Murphy, Additives for plastics handbook., Elsevier, 2001, pp. 6–7 Search PubMed.
- M. Rahman and C. S. Brazel, Prog. Polym. Sci., 2004, 29, 1223–1248 CrossRef CAS.
- T. Fierens, K. Servaes, M. Van Holderbeke, L. Geerts, S. De Henauw, I. Sioen and G. Vanermen, Food Chem. Toxicol., 2012, 50, 2575–2583 CrossRef CAS.
- J. Chen, Z. Liu, J. Jiang, X. Nie, Y. Zhou and R. E. Murray, RSC Adv., 2015, 5, 56171–56180 RSC.
- T. Zheng, Z. Wu, Q. Xie, J. Fang, Y. Hu, M. Lu, F. Xia, Y. Nie and J. Ji, J. Cleaner Prod., 2018, 186, 1021–1030 CrossRef CAS.
-
G. Wypych, Handbook of plasticizers., ChemTec Publishing, 2004, pp. 7–66 Search PubMed.
- I. Omrani, A. Ahmadi, A. Farhadian, H. K. Shendi, N. Babanejad and M. R. Nabid, Polym. Test., 2016, 56, 237–244 CrossRef CAS.
- P. A. Clausen, Z. Liu, V. Little, J. Kofoed-Sørensen and P. Wolkoff, Environ. Sci. Technol., 2012, 46, 909–915 CrossRef CAS.
- L. Yu, H. X. Li, J. Y. Guo, Y. Q. Huang, H. Wang, M. Talukder and J. L. Li, Environ. Pollut., 2019, 251, 984–989 CrossRef CAS.
- Y. Ito, M. Kamijima and T. Nakajima, Environ. Health Prev. Med., 2019, 24, 47 CrossRef.
-
V. Suteau, L. Gourdin, C. Briet, P. Rodien and M. Munier, 21st European Congress of Endocrinology., 2019, p. 63 Search PubMed.
- J. Chen, Y. Wang, J. Huang, K. Li and X. Nie, ACS Sustainable Chem. Eng., 2018, 6, 642–651 CrossRef CAS.
- J. Chen, X. Nie and J. Jiang, Polym. Int., 2018, 67, 269–275 CrossRef CAS.
- J. Chen, X. Li, Y. Wang, K. Li, J. Huang, J. Jiang and X. Nie, J. Taiwan Inst. Chem. Eng., 2016, 65, 488–497 CrossRef CAS.
- C. Bueno-Ferrer, M. C. Garrigós and A. Jiménez, Polym. Degrad. Stab., 2010, 95, 2207–2212 CrossRef CAS.
- B. I. Chaudhary, B. D. Nguyen, P. Smith, N. Sunday, M. Luong and A. Zamanskiy, Polym. Eng. Sci., 2015, 55, 634–640 CrossRef CAS.
- J. Chen, K. Li, Y. Wang, J. Huang, X. Nie and J. Jiang, Polymers, 2017, 9, 640 CrossRef.
- P. Jia, Y. Ma, H. Xia, M. Zheng, G. Feng, L. Hu, M. Zhang and Y. Zhou, ACS Sustainable Chem. Eng., 2018, 6, 13983–13994 CrossRef CAS.
- B. Chieng, N. Ibrahim, Y. Then and Y. Loo, Molecules, 2014, 19, 16024–16038 CrossRef.
- Y. Yang, Z. Xiong, L. Zhang, Z. Tang, R. Zhang and J. Zhu, Mater. Des., 2016, 91, 262–268 CrossRef CAS.
- C. Cui, Z. Zhang, Q. Zeng and B. Chen, RSC Adv., 2016, 6, 108180 RSC.
- P. Yang, J. Yan, H. Sun, H. Fan, Y. Chen, F. Wang and B. Shi, RSC Adv., 2015, 5, 16980–16985 RSC.
- H. Z. Li, S. C. Chen and Y. Z. Wang, Ind. Eng. Chem. Res., 2014, 53, 17355–17361 CrossRef CAS.
-
B. Nielsen, F. V. Sparso and J. K. Kristiansen, US Pat., 6734241, 2004 Search PubMed.
-
B. Nielsen, F. V. Sparso and J. K. Kristiansen, US Pat., 6949597, 2005 Search PubMed.
-
B. I. Chaudhary, K. Schiller and M. Meerbote, US Pat., 9422418, 2016 Search PubMed.
|
This journal is © The Royal Society of Chemistry and the Centre National de la Recherche Scientifique 2021 |
Click here to see how this site uses Cookies. View our privacy policy here.