DOI:
10.1039/D0MA00818D
(Paper)
Mater. Adv., 2021,
2, 736-742
The hydrogen storage properties of MgH2–Fe7S8 composites
Received
20th October 2020
, Accepted 19th November 2020
First published on 21st November 2020
Abstract
Nanostructured Fe7S8 was successfully synthesized and its catalytic effect on hydrogen absorption/desorption performance of MgH2 is systemically discussed. The MgH2 + 16.7 wt% Fe7S8 composite prepared by ball-milling method offers a striking catalytic activity for hydrogenation kinetics, and also reduces the initial decomposition temperature for MgH2. The composite of MgH2–Fe7S8 can absorb 4.000 wt% of hydrogen within 1800 s at 473 K, which is about twice that of pristine MgH2 (1.847 wt%) under the same conditions. The onset hydrogen release temperature of Fe7S8-modified MgH2 is 420 K, which is 290 K lower than that of additive-free MgH2 (710 K). Meanwhile, the doped sample could release 4.403 wt% of hydrogen within 1800 s at 623 K as compared to 2.479 wt% of hydrogen by MgH2. The activation energy for MgH2–Fe7S8 is about 130.0 kJ mol−1, approximately 36 kJ mol−1 lower than that of MgH2. The hydriding process of MgH2 + 16.7 wt% Fe7S8 follows the nucleation and growth mechanism. The prominent hydrogen storage performances are related to the reactions between MgH2 and Fe7S8. The newly formed MgS and Fe in the ball-milling process present a co-catalytic effect on the hydrogen storage performance of MgH2.
1. Introduction
The global environmental issues related to the excessive emission of greenhouse gases and burning of fossil materials have driven us to center our attention on alternative energy sources that can be extensively developed and widely used.1–4 Meanwhile, hydrogen energy is deemed as one of the most potential and ideal energy alternatives on account of its high energy density and clean and environmentally friendly nature.5–8 However, the practical application and popularization of hydrogen is still hindered by numerous complicated technical hurdles. In recent years, solid-state storage materials have been receiving worldwide attention as ideal hydrogen storage media. Among them, magnesium hydride (MgH2), which has a high hydrogen storage capacity, excellent reversibility and abundant availability, is regarded as one of the most marvelous candidates for potential hydrogen storage.9–12 Unfortunately, the widespread practical application of MgH2 is retarded by sluggish dynamic performance and high thermodynamic operating temperature.
Various attempts covering mechanical alloying,13,14 nano-structuring,15 and catalyst doping16–20 have been made by numerous groups to enhance the thermodynamic and hydrogen absorption and desorption properties. Among the above-mentioned modified systems, doping MgH2 with catalysts has been considered as an efficient way to boost the properties of MgH2.21–23 Especially, the transition metal iron (Fe) and its compounds have attracted considerable interest due to their pronounced catalytic effect on MgH2. Yan et al.15 observed a lower onset dehydrogenation temperature for the MgH2–10 wt% FeB/CNTs composite; the modified composites could start to release hydrogen at about 196 °C and absorb 6.2 wt% of H2 at 150 °C within 10 min. Chen et al.24 found that doping MgH2 with 5 wt% Fe nanosheets reduced the onset desorption temperature, and hydrogen could be released at 182.1 °C and absorbed at 75 °C by the composite. Gattia et al.25 reported that Fe and its oxides are suitable catalysts for hydrogen storage as they drastically speed up the reaction kinetics.
In addition to iron and its compounds, sulfide compounds also showed remarkable catalytic activities for the improvement of sorption kinetics and thermodynamic properties of MgH2. Jia et al.26 discovered that MgH2 with 16.7 wt% of MoS2 additive showed outstanding hydrogenation/dehydrogenation properties and the hydrogenation activation energy of the modified composites was determined to be 87.19 ± 4.48 kJ mol−1, lower than that of the pure MgH2 (111.03 ± 3.41 kJ mol−1). WS2 was also found to promote the hydrogenation/dehydrogenation behavior of MgH2 by Wang et al.27 Our previous work reported that the hydrogen intake/uptake performance of MgH2 was greatly influenced by nano-structured polysulfides containing iron (Fe3S4 and FeS2).28,29 The polysulfide containing iron ion is a kind of compound in polyvalent states, which can be approximately considered by the compound of ferrous sulfide and iron sulfide. Multi-valent catalysts also showed great potential in enhancing de-/hydrogenation kinetics of MgH2 as reported by Xie and co-workers.30 Meanwhile, the excellent hydrogen storage behavior of MgH2 might be related to the unstable Fe2+. Fe7S8 is also a polysulfide containing iron; multi-valent and unstable Fe2+ exist in Fe7S8, which might contribute to the enhancement of the hydrogen storage capacity of MgH2.
Given the encouraging results mentioned above, in this work, Fe7S8 was successfully synthesized and its catalytic effectiveness toward hydrogen adsorption/desorption of MgH2 was systemically investigated. Besides, the corresponding catalytic mechanism of Fe7S8 to the enhancement of hydrogen properties of the pristine MgH2 was also presented based on the information reflected by hydrogen absorption/desorption kinetics, phase compositions and microstructure observations.
2. Experimental
2.1 Synthesis of Fe7S8
1 mmol FeSO4·7H2O and 2 mmol thiourea were added to a solvent composed of triethylenetetramine and deionized water (the ratio of the components of the solvent was 1
:
2) and stirred for 1 h by magnetic stirring until the solution was homogenized. The solution was then transferred into a Teflon autoclave and maintained at 140 °C for 24 h. After cooling down to room temperature naturally, the precipitate was gathered by centrifugation and washed with distilled water and absolute alcohol several times. The obtained precipitate was dried in a vacuum oven at 80 °C for 6 h. The precursor [Fe18S25](TETA)14 was finally prepared.
0.1 g precursor [Fe18S25](TETA)14 and 15 ml oleylamine were added into a boiling flask and promptly heated to 90 °C in a vacuum atmosphere. To protect the sample from oxidation, argon was introduced into the boiling flask as a protective gas after the vacuum was stopped. The sample was then quickly heated to 260 °C and kept warm for 8 h. After the reaction was complete and the temperature of the boiling flask decreased to room temperature, extra 40 ml alcohol was introduced into the flask under mechanical stirring for about 10 min and the solution was further aged for 2 h. Fe7S8 was successfully synthesized and could be separated after the aged solution was centrifuged and washed with absolute alcohol.
2.2 Synthesis of MgH2–Fe7S8 composites
MgH2 was synthesized by the method of hydrogen combustion from commercial magnesium powder. Magnesium was hydrogenated at 400 °C with a hydrogen pressure of 4 MPa for 10 h. The obtained powder was then ball-milled at 350 rpm for 2 h. The target MgH2 was successfully prepared after hydrogenating the sample one more time at 400 °C under 4 MPa hydrogen pressure for 10 h.
MgH2–Fe7S8 composite was synthesized through the ball-milling method by mechanical milling of MgH2 and Fe7S8 with a weight ratio of 5
:
1. To reduce the increasing temperature, the milling process was launched at a speed of 350 rpm and ball-milled in one direction for 0.5 h and paused for about 0.25 h, unceasingly starting in another direction for 0.5 h. The ball-to-sample weight ratio was 20
:
1. To prevent the sample from oxygen and vapor, all samples were handled in an air-filled glove box.
2.3 Characterization
X-ray diffraction (XRD) was performed on a SmartLab high-resolution X-ray diffractometer (made by Rigaku Company) with Cu Kα radiation at 40 kV, 40 mA. The scanning speed was 4° min−1 in the range of 10° to 80°. Scanning electron microscopy (SEM) was employed to observe the microstructure and morphology of the formed sample. The hydrogen absorption/desorption behavior in relation to temperature for the composite of MgH2–Fe7S8 and non-additive MgH2 was determined in a pressure–composition–temperature (PCT) apparatus. The sample was gradually heated from room temperature to the set temperature, which was kept constant during the whole experiment. Temperature–programmed–desorption (TPD) was used to investigate the initial desorption temperature for the composite of MgH2–Fe7S8 and MgH2 free-additive. All the tested composites were heated from room temperature to 770 K at a heating rate of 10 K min−1. Differential scanning calorimetry (DSC) was performed from 200 K to 770 K at various heating rates: 5 K min−1, 10 K min−1, 15 K min−1, and 20 K min−1.
3. Results and discussion
3.1 Characteristics of the prepared nano-structured Fe7S8
XRD pattern of the as-synthesized Fe7S8 in Fig. 1a exhibits dominant diffraction peaks at 2θ = 29.9°, 33.8°, 43.9°, 53.1°, 57.3°, 64.8°, and 71.2° matching well with the Fe7S8 phase, in accordance with the data reported in JCPDS PDF 33-0664. As can be seen from Fig. 1b, the prepared sample presents the morphology of two-dimensional hexagonal sheets with a thickness of approximately 20 nm and a diameter of around 250 nm. Based on XRD and SEM results, nano-structured Fe7S8 was successfully fabricated.
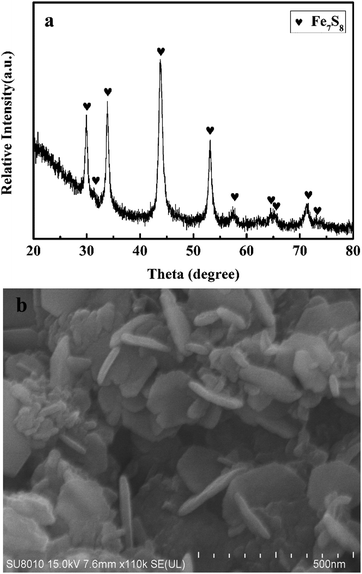 |
| Fig. 1 (a) XRD pattern of the as-synthesized Fe7S8 (b) SEM image of the as-synthesized Fe7S8. | |
3.2 Catalytic effectiveness of the fabricated Fe7S8 for the dehydrogenation/hydrogenation kinetics of MgH2
The catalytic role of the as-synthesized Fe7S8 in the dehydrogenation/hydrogenation kinetics of MgH2 was studied by using TPD isothermal dehydrogenation/hydrogenation measurements. The TPD curves of MgH2 and MgH2 + 16.7 wt% Fe7S8 composite at a heating rate of 10 K min−1 are shown in Fig. 2. As observed, the Fe7S8 doped MgH2 sample shows a striking effect of reducing the onset desorption temperature of MgH2. The prepared MgH2 commences to release hydrogen at approximately 710 K, whereas the onset desorption temperature for Fe7S8-modified MgH2 presents a remarkable decrease to 420 K, which is 290 K lower than that of additive-free MgH2. As for the pristine MgH2, the full desorption capacity is about 4.45 wt%. After introducing nano-Fe7S8 into MgH2, the desorbed content is increased and the maximum yield for the desorption process is nearly 5.72 wt%. Based on TPD measurements, the lower initial desorption temperature and the maximum desorption yield reveal that the introduced nano-Fe7S8 into MgH2 could successfully boost the desorption properties of MgH2.
 |
| Fig. 2 Thermal decomposition curves of MgH2 and MgH2 + 16.7 wt% Fe7S8 composite. | |
Isothermal dehydrogenation experiments were conducted at 623 K to further compare the effect of the doped Fe7S8 on the desorption kinetics process in MgH2; the relative curves for MgH2 with and without additives in the desorption process are presented in Fig. 3. It is evident that with the increase in temperature, the hydrogen desorption properties of MgH2 and MgH2 + 16.7 wt% Fe7S8 are enhanced. MgH2 + 16.7 wt% Fe7S8 composite exhibits much faster kinetics than that of pristine MgH2. The MgH2 + 16.7 wt% Fe7S8 sample could release 1.515 wt% H2 in 1800 s at 573 K. In contrast, the pure MgH2 only liberated 0.250 wt% H2 in the same time period. When the temperature increases to 623 K, the additive-free MgH2, which could only desorb 2.479 wt% of hydrogen in 1800 s at 623 K, shows worse desorption properties than the doped sample. MgH2 + 16.7 wt% Fe7S8 composite could liberate 4.403 wt% of hydrogen within 1800 s under identical conditions. As compared to non-additive MgH2, the dopant Fe7S8 promotes the dehydrogenation kinetics.
 |
| Fig. 3 Dehydrogenation properties of MgH2 and MgH2 + 16.7 wt% Fe7S8 composite at 573 K, 623 K. | |
The Kissinger's method31 was performed to further understand the enhanced dehydrogenation process for MgH2 and MgH2–Fe7S8 composites; the apparent activation energy (Ea) of those two composites were estimated by the Arrhenius equation described as below:
where
α is the heating rate (K min
−1),
Tm is the peak temperature for the maximum desorption rate (K), and
R is the gas constant of 8.314 J (mol
−1 K
−1).
Fig. 4a and b display DSC curves of MgH
2 and MgH
2–Fe
7S
8 composites, respectively, at various heating rates. From the slope of the fitted line in
Fig. 4c, the slope for the two samples were obtained as −19.95 and −15.64, while the corresponding apparent activation energy
Ea for MgH
2 was approximately 165.9 kJ mol
−1. It can be noticed that the apparent activation energy
Ea of MgH
2–Fe
7S
8 was decreased to 130.0 kJ mol
−1, which is lower by about 36 kJ mol
−1 than that of MgH
2. The reduced apparent activation energy demonstrated above gives the indication that the dopant Fe
7S
8 contributes to decreasing the energy barrier during the desorption process of MgH
2, which is directly responsible for the superior improvement of the dehydrogenation properties. In a recent literature,
25 activation energies for milled MgH
2 + 5 wt% Fe, MgH
2 + 5 wt% Fe
2O
3 and MgH
2 + 5 wt% Fe
3O
4 calculated using the Kissinger plot were 220.69 kJ mol
−1, 231.90 kJ mol
−1 and 304.45 kJ mol
−1, respectively, which indicates that the addition of Fe
7S
8 may show superior catalytic effect compared to that of some other additives.
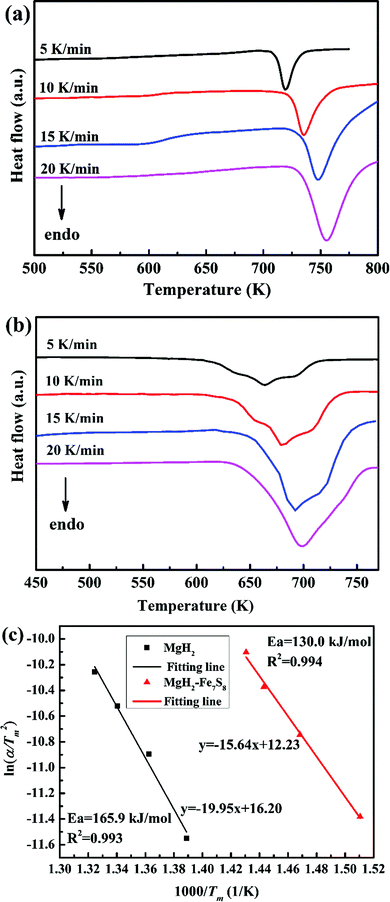 |
| Fig. 4 DSC curves of (a) pure MgH2 and (b) MgH2 + 16.7 wt% Fe7S8 composites with a heating rate of 5 K min−1, 10 K min−1, 15 K min−1. (c) The corresponding Kissinger plots for the hydrogen desorption reaction for MgH2 and MgH2 + 16.7 wt% Fe7S8 composites at various heating rates. | |
In addition to the hydrogen desorption behavior, the modified impact of Fe7S8 on the hydrogen uptake performance on MgH2 was also investigated by reabsorbing the dehydrogenated MgH2 and MgH2–Fe7S8 composites under 3 MPa of H2. Fig. 5 presents the hydrogenation curves of MgH2 and MgH2–Fe7S8 composite at 473 K and 523 K, respectively. It can be clearly seen that the dehydrogenated MgH2 sample only absorbs 1.847 wt% of hydrogen within 1800 s at 473 K, whereas the dehydrogenated MgH2 catalyzed by Fe7S8 composite shows higher hydrogen absorption ability under the same conditions, with an absorption capacity of 4.000 wt%. When the temperature sharply increases to 523 K, the hydrogen absorption ability of both dehydrogenated MgH2–Fe7S8 composite and additive-free MgH2 presents an obvious rise. The amount of hydrogen uptake increases to 3.915 wt% for pristine MgH2 within 1800 s, while that of the Fe7S8 doped composite reaches 4.804 wt%.
 |
| Fig. 5 Hydrogenation properties of (a) MgH2 at 473 K; (b) MgH2 + 16.7 wt% Fe7S8 composite at 473 K; (c) MgH2 at 523 K; (d) MgH2 + 16.7 wt% Fe7S8 composite at 523 K. | |
The hydrogenation mechanism can usually be explained by comparing the hydrogen absorption rate curves with the rate equations for MgH2 + 16.7 wt% Fe7S8 and MgH2 composites. The Avrami–Erofeev equation, eqn (2), is usually employed to fit the hydrogenation absorption process, which gives a strong idea for the nucleation and growth processes.
where
α is the reacted fraction,
k is the rate constant, and
m is the order of the reaction.
Fig. 6 shows the fitted hydrogenation kinetic curves of MgH
2 and MgH
2 + 16.7 wt% Fe
7S
8 composites at 523 K. It is obvious that there is a great difference between the fitted curve and the normalized curve for MgH
2 without additives. However, this similar phenomenon does not appear in the composite of MgH
2–Fe
7S
8, which is consistent with the experimental data. The fitted curves in
Fig. 6 demonstrate that the reaction mechanism of MgH
2–Fe
7S
8 composite conforms to nucleation and growth processes. Besides,
m represents the order of reaction; the rate-controlling steps for the hydrogen uptake process are connected with the value of
m. It has been reported that the values of
m for the one-dimensional diffusion process and the three-dimensional interfacial reaction are assigned as 0.620 and 1.070, respectively.
32 As for MgH
2 without the catalyst,
m is 0.9265 at 523 K, which is pretty close to 1.070. For the doped MgH
2–Fe
7S
8 composite, the value of
m was 0.4212, which approaches 0.620. Therefore, the rate-controlling steps of MgH
2 during the hydrogenation process changes from the three-dimensional interfacial reaction to the one-dimensional diffusion process, which is relevant to the addition of Fe
7S
8.
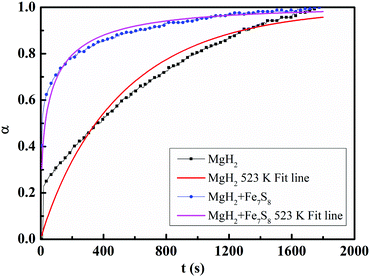 |
| Fig. 6 Fitted hydrogenation kinetic curves of MgH2 and MgH2 + 16.7 wt% Fe7S8 composites at 523 K under the pressure of 3 MPa. | |
3.3 Structural characterization and catalytic effect mechanism of MgH2–Fe7S8 composite
Fig. 7 presents SEM images of MgH2 and MgH2–Fe7S8 composite after the re-hydrogenation process. It is obvious that the particle size of pristine MgH2 is much bigger than that of MgH2–Fe7S8 composite; some of the particles in pristine MgH2 are agglomerated and inhomogeneous. The particles in the Fe7S8 added MgH2 have a loose structure and are highly dispersed, while the particles of additive-free MgH2 aggregate into large clusters and become tough. Xie et al.33 and Varin et al.34 reported that the decreased particle size and loose structure could boost the rates of dehydrogenation-hydrogenation, which indicates that the added Fe7S8 can not only help to decrease the particle size but also serve as an inhibitor to limit the formation of large clusters and result in favourable hydrogen kinetics.
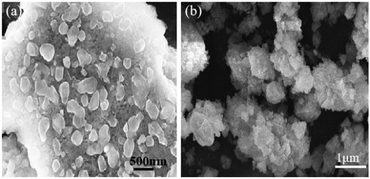 |
| Fig. 7 SEM images of (a) MgH2, (b) MgH2–Fe7S8 composite after the re-hydrogenation process. | |
To further elaborate on the catalytic mechanism related to the striking hydrogen absorption/desorption kinetics and thermodynamic properties of MgH2–Fe7S8 composite, XRD analysis was employed to characterize the phase structure of the doped composite at different stages. Fig. 8 shows the XRD patterns of MgH2–Fe7S8 composites that were collected at the ball-milling and de/hydrogenation stages. In the XRD pattern of the composite at the ball-milling stage, the main diffraction peak assigned to MgH2 appears accompanied by some new phases of Mg2FeH6, MgS, and Fe. In the XRD pattern of the composite at the hydrogenation stage, all the diffraction peaks are very intense due to hydrogenation. After the re-hydrogenation procedure, the major diffraction peaks assigned to Fe, Mg2FeH6 and MgS are still present. The appearance of new phases of Mg2FeH6, MgS and Fe indicates the reaction of MgH2 and Fe7S8 during the ball-milling/re-hydrogenation stage. The reactions can be summarized as follows:
| 8MgH2 + Fe7S8 → 7Fe + MgS + 8H2 | (1) |
| Fe + 2MgH2 + H2 → Mg2FeH6 | (2) |
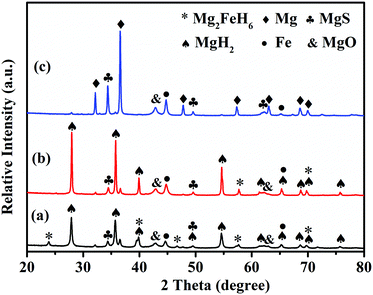 |
| Fig. 8 XRD patterns of MgH2–Fe7S8 composites at the (a) ball-milling (b) hydrogenation (c) dehydrogenation stages. | |
To confirm the possibility of the reaction between MgH2 and Fe7S8, the total change ΔGθ was calculated. The standard ΔfHθm for MgH2, Fe7S8, and MgS is −75.3, −824.2, and −346 kJ mol−1, and ΔfGθm are −35.9, −742.2, and −341.8 kJ mol−1, respectively. The total change ΔGθ for reaction (1) is −1705.0 kJ mol−1, whereas ΔGθ for MgH2 is −35.9 kJ mol−1; this confirms the possibility of occurrence of reaction (1) from the thermodynamic potentials, and the dopant Fe7S8 is conducive to the hydrogen absorption/desorption process.
In the XRD pattern of the composite at the dehydrogenation stage, the dominant diffraction peak belongs to Mg, implying that Mg2FeH6 and MgH2 produced in the hydrogenation process have completely decomposed. Some weak peaks corresponding to MgO are found during the whole stage, which is ascribed to the oxidation of Mg in the test operation process. The existing equation in the hydrogen release stage is as follows:
| Mg2FeH6 → Fe + 2Mg + 3H2 | (4) |
The formation of the intermediate phase of Mg2FeH6 has shown a striking catalytic role in the hydrogen sorption behavior. Xiao et al.35 reported that the Mg2FeH6@MgH2 core–shell sample exhibited faster hydrogen desorption kinetics, releasing more than 5.0 wt% H2 within 50 min at 280 °C. Apart from the Mg2FeH6–MgH2 system, Mg2FeH6 combined with NaBH436 composite has boosted dehydrogenation properties, while the dehydriding temperature of NaBH4 was reduced by at least 150 K when combined with Mg2FeH6. The enhancement of the dehydriding properties of LiBH4 was also confirmed by Li et al.37 Mg2FeH6 is a hydrogen-storage material, which has an excellent ability for hydrogen uptake/release performance.38 As an intermediate, Mg2FeH6 can uptake and liberate hydrogen. Therefore, the produced Mg2FeH6 plays a critical role in the improvement of the hydrogen storage properties.
The schematic diagram for the catalytic mechanism of Fe7S8 during the hydrogenation/dehydrogenation processes on MgH2 is shown in Fig. 9. During the hydrogenation process, the phases of Fe, MgH2 and H2 are generated by the formation of the intermediate phase of Mg2FeH6. In the dehydrogenation stage, Mg2FeH6 produces Mg and Fe. It is suggested that Fe as an active species exists in the whole dehydrogenation/hydrogenation process together with the newly formed MgS. Apart from that, from our previous investigation, the hydrogen absorption/desorption performance of the MgH2 + Fe and MgH2 + MgS systems is inferior to that of the in situ formed system.29 Therefore, the newly produced Fe and MgS during the ball-milling stage may co-catalyze the hydrogen storage performance of the MgH2–Fe7S8 system.
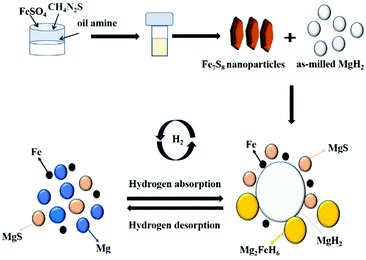 |
| Fig. 9 Schematic diagram of the catalytic mechanism of Fe7S8 during the hydrogenation/dehydrogenation processes on MgH2. | |
4. Conclusions
Nano-Fe7S8 was successfully fabricated and its catalytic effect on the hydrogen storage performance of MgH2 was systemically investigated. The isothermal hydrogen absorption/desorption measurement shows that the dehydrogenated MgH2 catalyzed by Fe7S8 composite has the hydrogen absorption capacity of 4.000 wt% within 1800 s at 473 K; only 1.847 wt% hydrogen could be absorbed by MgH2 under the same conditions. During the dehydrogenation process, MgH2 + 16.7 wt% Fe7S8 composite could release 4.403 wt% of hydrogen within 1800 s at 623 K as compared to 2.479 wt% of hydrogen by MgH2. The onset desorption temperature for Fe7S8-modified MgH2 is 420 K, lower than that of additive-free MgH2 (710 K). The hydriding process of MgH2 + 16.7 wt% Fe7S8 follows the nucleation and growth mechanism. The activation energy Ea of MgH2–Fe7S8 is about 130.0 kJ mol−1, approximately 36 kJ mol−1 lower than that of MgH2. The striking catalytic effect of Fe7S8 on the hydrogen storage performance of MgH2 is related to the reactions between MgH2 and Fe7S8. The newly formed MgS and Fe during the ball-milling process present a co-catalytic effect on the hydrogen storage performance of MgH2.
Conflicts of interest
There are no conflicts to declare.
Acknowledgements
This work was financially supported by the Natural Science Foundation of Hebei Province of China (No. E2019415036); Science and Technology Project of Hebei Education Department (BJ2020043); Science and Technology Support Plan of Qinhuangdao Science and Technology Bureau (201805A010); Doctoral Foundation of Hebei University of Environmental Engineering (201805)
Notes and references
- Z. W. Ma, J. X. Zou, D. Khan, W. Zhu, C. Z. Hu, X. Q. Zeng and W. J. Ding, J. Mater. Sci. Technol., 2019, 35, 2132–2143 CrossRef.
- M. Liu, S. Zhao, X. Xiao, M. Chen, C. Sun, Z. Yao, Z. Hu and L. Chen, Nano Energy, 2019, 61, 540–549 CrossRef CAS.
- X. Xie, C. Ni, B. Wang, Y. Zhang, X. Zhao, L. Liu, B. Wang and W. Du, J. Alloys Compd., 2020, 816, 152634 CrossRef CAS.
- Z. Shao, Y. Li, C. Liu, W. Ai, S.-P. Luo and Q. Liu, Nat. Commun., 2020, 11, 591 CrossRef CAS.
- J. Du, Z. Lan, H. Zhang, S. Lu, H. Liu and J. Guo, J. Alloys Compd., 2019, 802, 660–667 CrossRef CAS.
- X. Yao, C. Wu, A. Du, J. Zou, Z. Zhu, P. Wang, H. Cheng, S. Smith and G. Lu, J. Am. Chem. Soc., 2007, 129, 15650–15654 CrossRef CAS.
- L. Dan, L. Hu, H. Wang and M. Zhu, Int. J. Hydrogen Energy, 2019, 44, 29249–29254 CrossRef CAS.
- Z. Cao, L. Ouyang, H. Wang, J. Liu, L. Sun, M. Felderhoff and M. Zhu, Int. J. Hydrogen Energy, 2016, 41, 11242–11253 CrossRef CAS.
- M. Liu, X. Xiao, S. Zhao, S. Saremi-Yarahmadi, M. Chen, J. Zheng, S. Li and L. Chen, Int. J. Hydrogen Energy, 2019, 44, 1059–1069 CrossRef CAS.
- Y. Zheng, K. Li, H. Wang, D. Tian, Y. Wang, X. Zhu, Y. Wei, M. Zheng and Y. Luo, Appl. Catal., B, 2017, 202, 51–63 CrossRef CAS.
- H.-J. Lin, J. Matsuda, H.-W. Li, M. Zhu and E. Akiba, J. Alloys Compd., 2015, 645, S392–S396 CrossRef CAS.
- G. Gizer, J. Puszkiel, M. V. C. Riglos, C. Pistidda, J. M. Ramallo-Lopez, M. Mizrahi, A. Santoru, T. Gemming, J. C. Tseng, T. Klassen and M. Dornheim, Sci. Rep., 2020, 10, 12 CrossRef.
- G. Liang, J. Huot, S. Boily, A. V. Neste and R. Schulz, J. Alloys Compd., 1999, 292, 247–252 CrossRef CAS.
- M. Y. Song, S. N. Kwon, S. H. Hong, C. G. Park, S. H. Baek, H. S. Kim, D. R. Mumm and J. S. Bae, Catal. Today, 2007, 120, 281–286 CrossRef CAS.
- S. Gao, X. Wang, H. Liu, T. He, Y. Wang, S. Li and M. Yan, J. Power Sources, 2019, 438, 227006 CrossRef CAS.
- J. Zhang, L. He, Y. Yao, X. J. Zhou, L. P. Yu, X. Z. Lu and D. W. Zhou, Renewable Energy, 2020, 154, 1229–1239 CrossRef CAS.
- F. A. H. Yap, N. N. Sulaiman and M. Ismail, Int. J. Hydrogen Energy, 2019, 44, 30583–30590 CrossRef.
- N. H. Idris, N. S. Mustafa and M. Ismail, Int. J. Hydrogen Energy, 2017, 42, 21114–21120 CrossRef CAS.
- N. A. Ali, N. H. Idris, M. F. M. Din, N. S. Mustafa, N. A. Sazelee, F. A. H. Yap, N. N. Sulaiman, M. S. Yahya and M. Ismail, RSC Adv., 2018, 8, 15667–15674 RSC.
- N. A. Sazelee, N. H. Idris, M. F. Md Din, M. S. Yahya, N. A. Ali and M. Ismail, Results Phys., 2020, 16, 102844 CrossRef.
- M. Ismail, M. S. Yahya, N. A. Sazelee, N. A. Ali, F. A. H. Yap and N. S. Mustafa, J. Magnes. Alloys, 2020, 8, 832–840 CrossRef.
- T. B. Andres, M. Z. Luis and M. Marcos, Int. J. Hydrogen Energy, 2020, 45, 27421–27433 CrossRef.
- N. A. Ali, N. H. Idris, M. F. M. Din, M. S. Yahya and M. Ismail, J. Alloys Compd., 2019, 796, 279–286 CrossRef CAS.
- L. Zhang, L. Ji, Z. Yao, N. Yan, Z. Sun, X. Yang, X. Zhu, S. Hu and L. Chen, Int. J. Hydrogen Energy, 2019, 44, 21955–21964 CrossRef CAS.
- D. M. Gattia, M. Jangir and I. P. Jain, J. Alloys Compd., 2019, 801, 188–191 CrossRef CAS.
- Y. Jia, S. Han, W. Zhang, X. Zhao, P. Sun, Y. Liu, H. Shi and J. Wang, Int. J. Hydrogen Energy, 2013, 38, 2352–2356 CrossRef CAS.
- J. S. Wang, W. Zhang, Y. Cheng, D. D. Ke and S. M. Han, J. Wuhan Univ. Technol., Mater. Sci. Ed., 2015, 30, 670–673 CrossRef CAS.
- W. Zhang, Y. Cheng, D. Han and S. Han, Energy, 2015, 93(pt 1), 625–630 CrossRef CAS.
- W. Zhang, G. Xu, Y. Cheng, L. J. Chen, Q. Huo and S. Y. Liu, Dalton Trans., 2018, 47, 5217–5225 RSC.
- L. S. Xie, J. S. Li, T. B. Zhang and L. Song, Mater. Charact., 2017, 133, 94–101 CrossRef CAS.
- H. E. Kissinger, Anal. Chem., 1957, 29, 1702–1706 CrossRef CAS.
- J. S. Pedersen, J. Appl. Crystallogr., 1994, 27, 595–608 CrossRef.
- L. Xie, Y. Liu, Y. T. Wang, J. Zheng and X. G. Li, Acta Mater., 2007, 55, 4585–4591 CrossRef CAS.
- R. A. Varin, T. Czujko, E. B. Wasmund and Z. S. Wronski, J. Alloys Compd., 2007, 432, 217–231 CrossRef CAS.
- X. Xiao, C. Xu, J. Shao, L. Zhang, T. Qin, S. Li, H. Ge, Q. Wang and L. Chen, J. Mater. Chem. A, 2015, 3, 5517–5524 RSC.
- G. Q. Li, M. Matsuo, S. Deledda, B. C. Hauback and S. Orimo, Mater. Trans., 2014, 55, 1141–1143 CrossRef CAS.
- G. Li, M. Matsuo, S. Deledda, R. Sato, B. Hauback and S.-I. Orimo, Mater. Trans., 2013, 54, 1532–1534 CrossRef CAS.
- Y. Wang, F. Cheng, C. Li, Z. Tao and J. Chen, J. Alloys Compd., 2010, 508, 554–558 CrossRef CAS.
Footnote |
† Both authors contributed equally to this work. |
|
This journal is © The Royal Society of Chemistry 2021 |
Click here to see how this site uses Cookies. View our privacy policy here.